IBM 729 Guide

r'=I
.
.
.
v
e
cdi
c.cr
IBM WiC;t
D
.
P
:'Cf`:DE.PT..-PRINTE:DriN
UNiTED KINGDOM

72•9;;OPER'A.T*
G FEA-7UR~5."
DIFFERENT MODELS
'IECCRC OEiEIiT
~E1TlJJMCIE-
-/EL EEOEIIC-
TAPE UNITS
729 RELAY
729 NOR
729 NORLAY
This chart shows the various character rates,
densities and speeds of the 729 transistorised
tape drives
TAPE
TRANSPORT
PROLAY ASSEMBLY AND STOP CAPSTAN
LUBRICATION(may be performed on-line)
Every three months lubricate the nylon pulley
shafts with IBM 6. Mark the position and direction
of rotation of the pulleys before removal.
Every four months on Mod IV and VI or
Every six months on Mod II and V lubricate the
Sintered bronze prolay parts with IBM 6 oil.
VISUAL INSPECTION&OPERATIONAL CHECK
Every four months on Mod IV and VI or
Every six months on Mod II and V mark the pos-
itions of the prolay arm assembly and armatures
and remove. Replace the set screws on the moving
pulley and armature pivots. Make sure the
residual plastic strips are mounted as shown in
the picture.
CAUTION! The removal and replacement of the
prolay arm assembly must be performed with
power OFF to avoid damaging the plastic strips.
1

Next check the start and stop timings. If these
are incorrect, carry out mechanical adjustments
to obtain:
. 005 to . 006" forward drive gap
. 006 to. 008" forward stop gap
. 005 to . 006" backward drive gap
. 004 to . 005" backward stop gap
After completing the mechanical adjustments,
carry out dynamic gap adjustments:
1.
Use P5 to set drive current to 4 Amps. This
corresponds to 2 volts on-
TB11 between 8 & 9 on 729 RELAY
TB11 between 3 & 8 on 729 NOR
(Note:on some relay type machines the reading
must be 4 volts-refer to EC 729 WTC 57)
2.
Use P4 to adjust the neutral current to give
2. 7± 2 volts on -
TB11 between 6 & 7 for 729 NORLAY
TB11 between 3 &
7
for 729 NOR
3.
Bring P6 and P7 to zero by turning counter-
clockwise.
4.
Use an HD tape and adjust the start and stop
times to obtain a correct envelope.
5.
Adjust to obtain the following timings:
Amplitude
0-100% 100% 100%-0
729I1 & V
forward and
backward start
3ms
forward stop
1. 5ms 2. 3ms
backward stop
0. 9ms 1. 8ms
729IV
&
VI
forward and
backward start
3ms
forward stop
0. 9ms 2. 3ms
backward stop
0. 9ms 1. 8ms
DRIVE CAPSTAN
Count five troubles may be caused by a glazed
rubber capstan. This may be replaced in the
field by using a special tool P/N 8019875.
Refer to SA/WTC 275.
2

.
PEAS
!'H_t.MP
L
IFI_R •'NCVEFCRM
'
Ei
, Nc.~w~
,
~~s
nv[~ ~='oee CeI,e411,4t a+ a:
t+r+.0 ;.
'VACUUM. COLUMN. MI tell AMC' TARE IN
,
COLUMN{ SN
ITCH
3
!E4!
I*
FMPitC i>&
0t
;
,
Reading troubles may be caused by substantial
play of the forward capstan bearing. This play
creates vibrations which result in read bus
variations or a wavy rear edge on track C of
the tape. To check this play, examine the
variation of the read buses at the fifth peak
after starting. The variation must not exceed
0.7 microseconds..
LUBRICATION
Every three months saturate the oil tubes of the
capstan motor with IBM 6 oil. Pour a thin film
of oil on the capstan motor shaft and wipe the
capstan to keep it perfectly clean.
VACUUM COLUMNS
Intermittent troubles which are difficult to
detect may result from noise caused by the
column switch contacts. The.capacitors at the
contact terminals must be kept in perfect
condition.
VISUAL INSPECTION&OPERATIONAL CHECK
Every four months on Mod IV and VI or
Every six months on Mod II and V check the
vacuum switches and tape in column switches
for incorrectly adjusted or dirty contacts.
Also check that the column switch RC filters
are in good condition A defective RC filter
has a deformed capacitor and a burnt resistor.

READ/WRITE HEAD
Two types of read/write head are in use on
729's, 800 B. P. I. and 55.6 B. P. I. These heads
have rounded pole pieces to avoid noise when
reading or writing.
A deeply grooved head surface indicates that
the head is worn out and will give a weak and
unreliable signal (15 my or less). This will
make the skew and asymmetry adjustments
difficult.
Be careful when inspecting two 729 machines
simultaneously. Do not interchange the head
covers as this would interfere with the locking
of the head in the low position.
TAPE
AP
A'1.1
,
AHErL
!
OaßABCT
.;dfl6
4
TA PE
HEAD
ASSEMBLY
The approach angle of the tape to the head is
critical. Incorrect positioning of the head could
cause trapping of air bubbles between the tape
and head. These bubbles will raise the head and
cause read and write errors.
Never remove the tape cleaner blade assembly;
its position affects the approach angle.

111111111111111111h1111
Next use the appropriate master skew tape to
check the read skew as follows:
master skew tape
P/n 432154
P/n 433153
tape head
556 BPI
800 BPI
tape units
7293 7291V
729V 729VI
max read skew
(microseconds)
2.3
1. 5
0.25
O. 25
■
■
1111111
■
11
:-..
1111111111111111
. .
IRE
"
Aiiii:SIN
: t
~
s~ien~
ag
ems
I4•T.`
W:1
-. -~~~
■
5
LUBRICATION
Every four months
on Mod IV and VI or
Every six months
on Mod II and V, lubricate
the felt pads and links with IBM 8 oil. Lubricate
the head raising gear with IBM 17 grease.
VISUAL INSPECTION & OPERATIONAL CHECK
Every four months
on Mod IV and VI or
Every six months
on Mod II and V check the
read and write conditions:
First use the preamplifier calibration tape,
P/N 432152 and check the read bus levels to
obtain the following readings:
8 volts for Mod II and IV (556 B. P. I. head)
9 volts for Mod V and VI (too B. P. I. head)
Cheek the asymmetry on 729V and VI using good
quality tape such as HD, and refer to SA WTC
159 (128). After adjusting the read bus and
asymmetry off-line they must be checked at the
output of the read register in TAU on line.
REMEMBER to check the skew adjustments
after adjusting the asymmetry,

Check that the write skew does not exceed:
2. 3 microsec for the 729 II
1.5 microsec for the 729 IV
0. 25 microsec for the 729 V and VI
REMEMBER to check the asymmetry after
altering the skew adjustment.
ERASE HEAD
Every twelve months check the erase head for
good operation and correct positioning.
H - SHIELD
Every twelve months check that the H-shield is
correctly positioned with its centre to the right
of the centre head laminations.
TAPE CLEANER BLADE
Every twelve months check the condition of the
blade. When replacing a worn tape cleaner blade,
the ground jumper must be installed over and not
under it to avoid altering the approach angle.
Similarly, an incorrect position of the tape
cleaner blade assembly may alter the approach
angle so do not remove this assembly.
PHOTOSENSING ASSEMBLY
Bad sensing of the load point and end of tape
reflective spots may be caused by worn out or
incorrectly positioned photocells. The photocell
slot must be parallel to the tape.
VISUAL INSPECTION&OPERATIONAL CHECK
Every six months check the lamp sockets for
good contact , otherwise noise may be generated.
6

REEL. p'i?IVE. ASSEMBLY
.TAKE UP ßvtECHA
.
iJISPA
.
t
lighten i,io
much
`,pCCIfICOtiGflS)
.
.
_....,...~.:
Finatair
,
TAKE UP MECHANISM & TAKE UP MOTORS
LUBRICATION
Every four months on Mod IV and VI or
Every six months on Mod II and V lubricate the
take up mechanism shaft with IBM 17 grease.
VISUAL INSPECTION & OPERATIONAL CHECK
Every twelve months make a visual inspection of
the tape take up motor and head take up motor.
REEL CLUTCH & REEL BRAKE
The clutch shaft locknut is tightened in the plant
with a torque wrench. Do not overtighten after
replacing the magnetic powder or the shaft may
become deformed.
LUBRICATION
Every four months on Mod IV and VI or
Every six months on Mod II and V lubricate the
stop clutch gears with IBM 17 grease.
REEL DRIVE &
TAKE-UP
MECHANISM
VISUAL INSPECTION & OPERATIONAL CHECK
Every four months on Mod IV and VI or
Every six months on Mod II and V inspect and
adjust the brakes as follows:
a) Partial right brake adjustment
1.
Place full reel on right hub
2.
If right reel is full, turn reel over with
file protect ring outside.
3.
Disconnect HS rewind motor and trip
mercury switch.
4.
Depress load rewind and reset switches
sequentially.
5.
Check partial right brake for 600 1
.
200
grams tension. Adjust with Pl for 720
NOR and NORLAY, and P3 for the 729
RELAY.

b) Tape wrinkling adjustment
i) With special tool P/N 8018462
1.
Depress the unload and load rewind
switches in succession.
2.
Adjust by means of P3 for 729 NOR and
NORLAY or P8 for 729 RELAY to
disengage the knurled disc of the tool.
.
This gives about 200 grams of tape
wrinkling.
ii) With gram gauge
Proceed as above, adjusting P3 or P8 to
obtain 200 grams on the right reel.
c
)
HS rewind adjustment
1.
Connect the HS rewind motor
2.
Disconnect the take up motor
3.
Release the mercury switch
4.
perform the HS rewind operation
When the reels stop at the end of the HS rewind
operation, check that the thickness of the
tape on the right reel is about ;" (5 to 6 mm)
Make sure the tape is tight between the pulley
idlers, without looping above the left vacuum
column. If the tape is not tight, adjust P2,
controlling the partial left brake.
d)
Mechanical brake adjustment
Check with power OFF for pressure of
about
X
70 grams between the shoe and the
brake. Wipe all grease from the stop
clutch braking surface.
Weak pressure of the mechanical brake is
indicated if the reels slowly rotate in load
status.
e)
Check the condition of belts, brushes and
clutch commutator rings. Check the
magnetic clutch for powder leaks.
REMEMBER that intermittent troubles may be
caused by noise originating from bad brushes
or incorrect brush pressure on the commutator
rings.
REEL DRIVE MOTORS & HS REWIND MOTOR
VISUAL INSPECTION & OPERATIONAL CHECK
Every twelve months
visually inspect:
1.
The condition of the reel drive motors
and their belts.
2.
The HS rewind motor-make sure that
the coupling is not loose on the shaft.
ö
Printed in United Kingdom

THE
BASE
FRONT DOOR ASSEMBLY
a) Cable doors (old style)
To change a spring of a cable door:
1.
First remove cable from pulley:
2.
Unscrew spring from negator spring
assembly and remove drum assembly.
3.
Unwind the old spring from the drum
and wind the new spring onto the drum.
4.
Attach the spring to the negator spring
assembly and replace drum assembly on
axle. Ensure the flange is facing the
mounting bracket to avoid spring
breakage later.
5.
Replace cable following reference
manual procedure.
b) Magnetic latch door
To improve the operation of the magnetic
latch door scrape the paint from the inside
bracket surface.
To replace a spring on a magnetic latch door,
hold the spring in place with a short-handled
screwdriver.
9

RELAY TIMER
VISUAL INSPECTION
Every twelve months check the relays,
particularly the DP relay as its contacts are a
source of noise.
BLOWERS AND FILTERS
Several types of electronic gate blowers
.
are in
use, so when changing a blower, check the
direction of rotation and airflow. This is shown
by arrows on the blower.
LUBRICATION
Every twelve months lubricate blowers which
have the grease nipples, with IBM 17 grease.
VISUAL INSPECTION
Check the general condition of the blowers.
Every twelve months change the filter, taking
care to install the new filter correctly.
11

Table of contents
Popular Microscope manuals by other brands
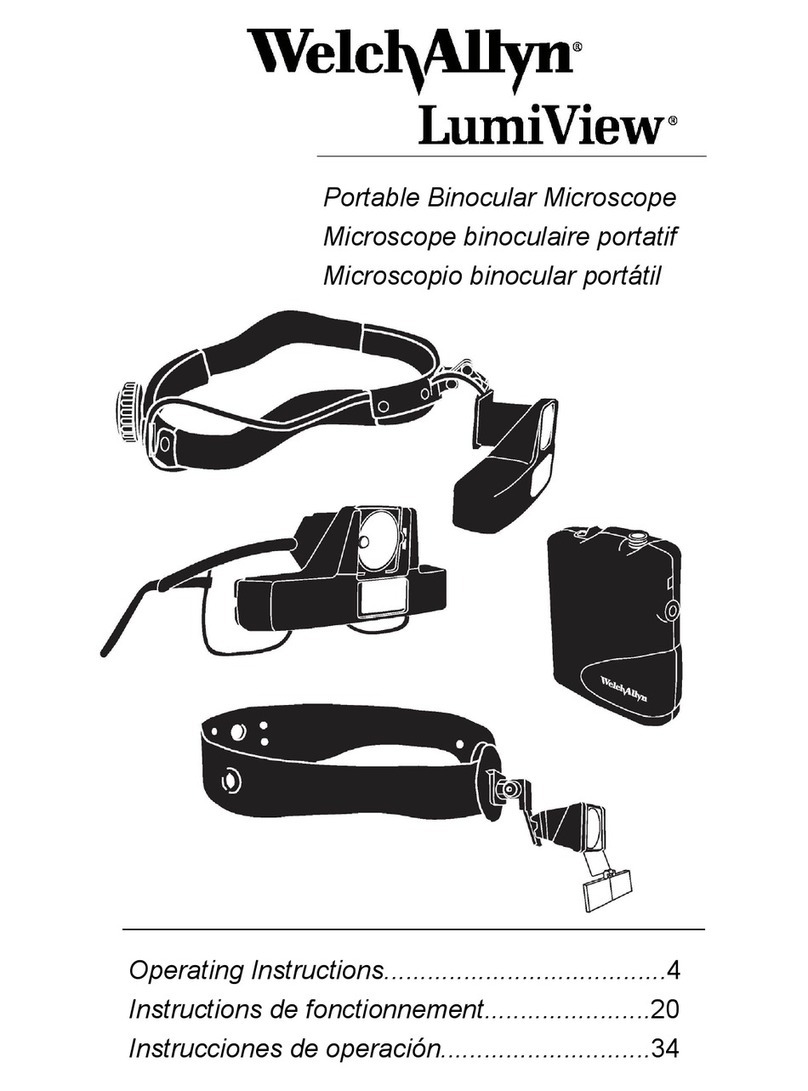
Welch Allyn
Welch Allyn LumiView Series operating instructions
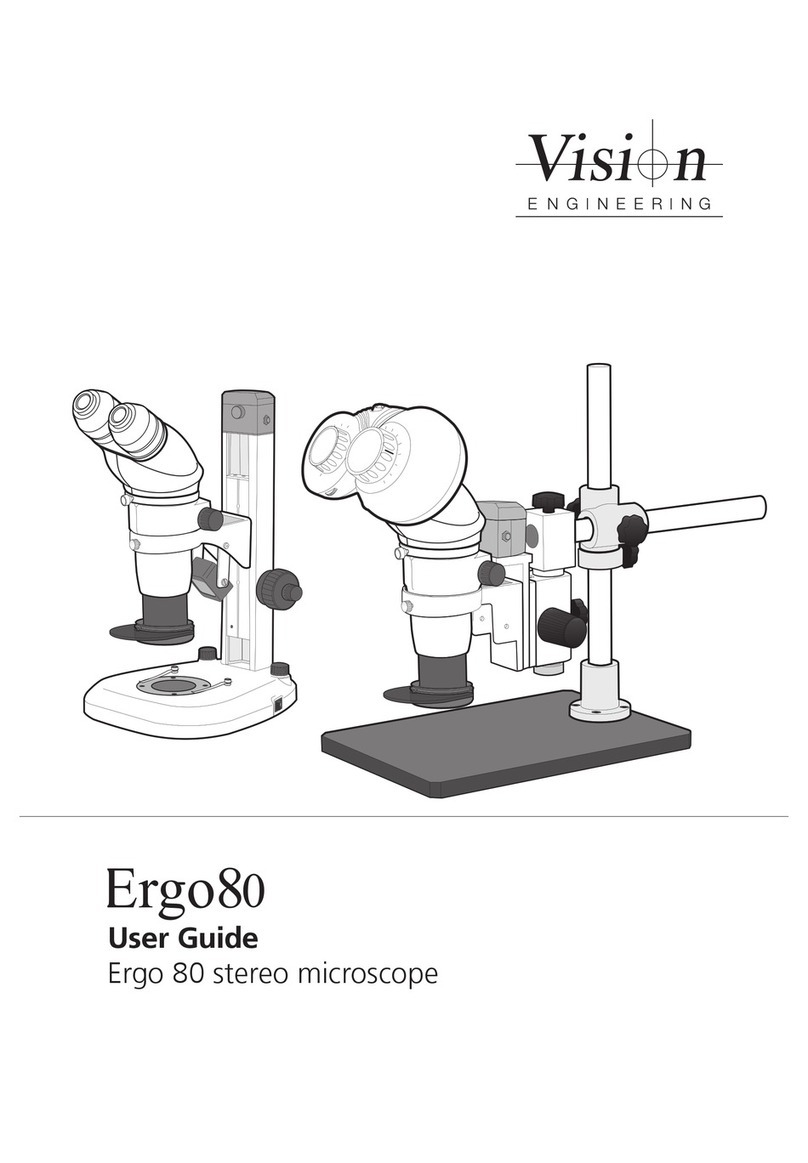
Vision Engineering
Vision Engineering Ergo 80 user guide

Nikon
Nikon SMZ1500 instructions

DANA
DANA DI-100F user manual
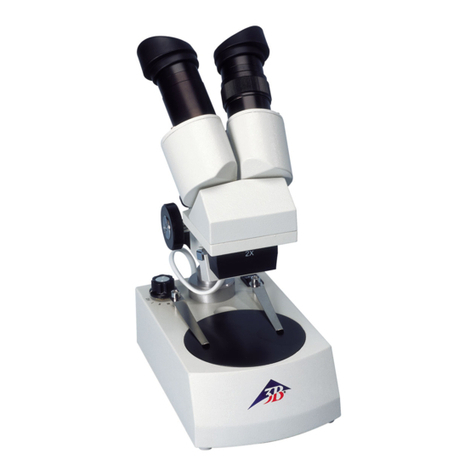
3B SCIENTIFIC PHYSICS
3B SCIENTIFIC PHYSICS 115 V, 50/60 Hz instruction manual

Bresser
Bresser Biolux ICD 20x operating instructions