ICC DL6000 User manual

INDUSTRIAL
OWNERS
MANUAL
DL6000
/
D6000

INDUSTRIAL
OPERATORS
MANUAL

8.
9.
10.
CONTENTS
Introduction
Warranty
Safety
General
Operation
Service
Controls
and
Instruments
Identification
Operation
of
Controls
Engine
Start-up
and
Operation
Lubrication
and
Maintenance
Introduction
Time
Table
Service
Access
Panels
Engine
Lubrication
System
Fuel
System
Air
Intake
System
Exhaust
System
Electrical
System
Hydraulic
Oil
and
Filtering
System
Engine
and
Hydraulic
Cooling
System
Final
Drive
and
Brakes
Undercarriage
Adjustment
&
Wear
Attachments
Ioader
Removal
and Installation
Dozer Removal
and
Installation
Lubrication
Loader
Operating
Load
Capacities
General
Information
Machine
Cleaning
Procedures
Index

INTRODUCTION
Read
this
manual
carefully
to
learn how
to
operate
and
service
your
machine
correctly.
Failure
to
do
so
could
result
in
personal
injury
or
equipment
damage.
This
manual
should
be
considered
a
permanent
part
of
your
machine
and
should
remain
with
the
machine
when
you
sell
it.
Right-hand
and
left-hand
sides
are
determined
by
facing
in
the
direction
of
forward
travel.
Write
machine and
attachment
identification numbers in the
Identification
Section
of
this
page.
Your
dealer will need
these
numbers when
you
order
parts.
Also
file
the
identification
numbers in a
secure
place
off of
the
machine.
Accurately
recording
these
numbers will help
trace
the
machine
should
it
be
stolen.
The
identification numbers
for
the
crawler
are
located
inside the
operators
cab
in
the
upper
left
hand
corner.
There
are
also identification numbers
located
on
all attachments.
Warranty
1s provided as a
part
of ICC Mfg.
Co.'s
support
program for
customers
who
operate and
maintain
their
equipment as
described
in this manual. A
copy
of
the
warranty
statement
is
on
page
2 of
this
manual.
All
information
in
this
manual
are
based
on
the
latest
information
available
at
the
time
of
publication.
The
right
is
reserved
to
make
changes
at anytime
without
notice.
IDENTIFICATION
MODEL NO. SERIAL NO.
CRAWLER
DL6000
95-10018
ENGINE
TMD27
94081362
ATTACHMENT
120605
10011-L
DEALFR
NAME
PETRY
EQUIPMENT
ADDRESS
30
SOUTHVILLE
RD.,
SOUTHBOROUGH,
MA
01772
PHONE NO.

S
DIVISION
OF
TENAX
CORPORATION
WARRANTY
ICC
Mfg.
Co.
warrants
new
construction
equipment
therefor
sold
by
it
to
be
free
from
defective
materials
and
workmanship.
The
warranty
periods
are
6
months
or
600
hours
whichever comes
first
on
the
machine, and 12 months or 1200 hours whichever comes
first
on
the
power
train only.
The
power
train being the engine, drive pumps and
motors, implement
pump
and valve,
brakes
and final drives. ICC Mfg. Co. makes no
warranty with respect
to
allied equipment or accessories not manufactured by ICC
Mfg. Co. and
being
subject
to
warranty, if any,
provided
by their respective
manufactures
(such
as,
but
not limited to, engines, pumps, motors or like). The
warranty
described in
this
paragraph shall be in
1lieu
of all other warranties,
expressed or implied, including,
but
not limited to, any implied warranty or
merchantability
or
fitness
for
a
particular
purpose.
Upon
notification
to
ICC
Mfg.
Co.
within
the
above-stated
warranty
period
of
any
failure
to
conform
to
this
warranty,
and
upon
inspection
by
ICC
Mfg.
Co.
to
verify
said
nonconformity,
ICC
Mfg.
Co.
will
provide
a
new
part
or
a
repaired
part,
whichever
ICC
Mfg.
Co.
elects,
to
replace
the
part
found
to
be
defective,
along
with
the
labor
for
installation
of
such
new
or
repaired
part.
Such
parts
and
labor
will
be
provided
without
charge
to
the
Purchaser
during
normal
working
hours
at
a
place
of
business
of
an
ICC
Mfg.
Co.
dealer
or
other
establishment
authorized
by
ICC
Mfg.
Co.
to
effect
said
repairs or replacements, but Purchaser
shall
bear all costs of
transporting
the
product
to
and
from
such
place
of
business
or
establishment.
Correction of nonconformities, in
the
manner and for
the
period
of time provided
above, shall constitute fulfillment of all liabilities of ICC Mfg. Co. under this
contract.
THE
REMEDIES
OF
THE
USER
SET
FORTH
HEREIN
ARE
EXCLUSIVE,
WITHOUT
REGARD
TO
WHETHER
ANY
DEFECT
WAS
DISCOVERABLE
OR
LATENT
AT
THE
TIME
OF
DELIVERY
OF
THE
PRODUCT
TO
THE
PURCHASER.
The
essential
purpose of
this
exclusive
remedy
shall
be
to
provide
the
Purchaser
with
repair
or
replacement
of
parts
that
prove
to
be
defective
within
the
period
and
under
the
conditions
previously
set
forth.
This
exclusive
remedy
shall
not.
have failed of its essential purpose
(as
that
term
is
used
in the Uniform
Commercial Code) provided ICC Mfg. Co. remains willing
to
repair or replace
defective
parts
within a commercially reasonable time after
it
obtains actual
knowledge of
the
existence of a particular defect.
IN
NO
EVENT
SHALL
ICC
MFG.
CO.
BE
LIABLE
FOR
ANY
SPECIAL,
CONSEQUENTIAL,
INCIDENTAL
OR
INDIRECT
DAMAGES
WITH
RESPECT
TO
THIS
CONTRACT
OR
ANYTHING
DONE
IN
CONNECTION
THEREWITH,
OR
FOR
PROPERTY
DAMAGE
SUSTAINED
BY
A
PERSON
DESIGNATED
AS
A
THIRD
PARTY
BENEFICIARY
OF
A
SURVIVING
WARRANTY
UNDER
THE
LAW
OF
ANY
JURISDICTION.
ICC MFG.
Co.
1850 W. OLIVER AVENUE
INDIANAPOLIS, IN 46221
EFFECTIVE
April
1,
1995
1850
WEST OLIVER AVENUE
INDIANAPOLIS,
INDIANA
46221
317-638-8145
¢
FAX:
317-632-7482

SAFETY (GENERAL)
RECOGNIZE SAFETY SYMBOL
This
is
the
safety
alert
symbol.
If
you
see
this
symbol
in
the
operators manual or
on
your
machine,
be
alert
to
the
potential
for
personal
in
jury.
Follow
recommended precautions and
safe
operating
practices
as well as general safety
and
accident
prevention
regulations
in
order
to
avoid
accidents.
FOLLOW
SAFETY
INSTRUCTIONS
Carefully
read
all
safety
information
in
this
manual
and
on
your
machine
decals.
Learn how
to
operate the machine and the controls before starting
work.
Do
not
let
anyone
operate
without
instructions.
Keep
machine
in
proper
working condition. Unauthorized
modifications
to
the
machine
may
impair
the
function and/or safety and affect
machine
PREVENT
MACHINE RUNAWAY
Do
not
start
the
engine
by
shorting
across
the
starter
or
solenoid
terminals.
Never
start
engine
while
standing
on
the
ground.
Always
start
engine
from
operators
seat.
PREPARE
FOR
EMERGENCIES
Be
prepared
if a fire starts.
Keep
first
aid
kit
and
fire
extinguisher
handy.
Keep emergency phone numbers
for
doctors, ambulance service and fire department
near
the
phone.
WEAR
PROTECTIVE
CLOTHING
Wear
close fitting clothing and safety equipment appropriate for
job.
Wear
suitable hearing protection
to
protect
against objectionable
or
uncomfortable
loud
noises.
HANDLE FUEL SAFELY
-
AVOID FIRES
Handle
fuel with care.
Do
not refuel machine while smoking
or
when
near
an
open
flame
or spark.
Always
stop engine before refueling machine.
Fill
fuel tank outdoors.
Prevent
fires
by
keeping
machine
clean
of
trash,
grease
and
debris.
3-1
(Revised
4/25/95)

STORE
ATTACHMENTS
SAFELY
Stored
attachments
such
as
loaders
and
dozers
can
fall
and
cause
serious
injury.
Secure
stored attachments
to
prevent
falling.
Keep
children
and
bystanders away
from
storage
area.
RA
AR
SAFETY
(OPERATION)
CHECK
MACHINE
SAFETY
Always
check
the
ground
conditions
before
starting
work.
Check
general
operating
safety
of
the
machine
before
using.
DRIVING
THE
MACHINE
Before
moving
away,
always
check
immediate
vicinity
of
machine.
Always
adapt
your
ground
speed
to
meet
ground
conditions.
Reduce
your
ground
speed of the machine
when
driving
on
slopes or over
uneven
ground.
Avoid
holes, ditches
and
obstructions
which
may
cause
the
machine
to
top
over.
KEEP RIDERS OFF MACHINE
Only
allow
the
operator
on
the
machine.
USE SEAT BELT PROPERLY
The seat belt
must
be
used
to
operate the machine. Failure
to
do
so may cause
serious injury or death
from
an accident such as an overturn or a sudden stop.
ATWAYS
LOWER
ATTACHMENTS
Lower
all
attachments
to
the
ground
before
exiting
the
operators
cab.
When
carrying material in bucket, always
carry
bucket as low as possible.
PARKING
AND
LEAVING
MACHINE
Lower
mounted
attachments
to
the ground before leaving
the
tractor.
When
leaving
the
machine, shut-off engine and remove
main
switch key.
3-2
(Revised
4/25/95)

SAFETY
(SERVICE)
PRACTICE
SAFE
MAINTENANCE
USE
Understand
service
procedure
before
doing
work.
Never
work
on
machine while
it
is
moving
or
the
engine
is
running.
Securely
support
all machine
parts
that must be raised for service work.
Disconnect
battery
ground
cable
before
making
repairs
to
electrical
system
or
welding
on
machine.
GENUINE
ICC
MFG.
CO.
PARTS
ICC
Mfg.
Co.
replacement
parts
have
been
specifically
designed
for
ICC
Mfg.
Co.
Machines.
Other
parts
are neither
examined
nor released by ICC Mfg. Co. Use of such
parts
could
have
negative
effects
upon
the
machine
and
thereby
affect
its
safety.

CONTROLS
AND
INSTRUMENTS
IDENTIFICATION
Controls
A.
Travel
Control lever
B.
Throttle
Control
C.
Attachment
Control
Levers
Instruments
Hourmeter
shows number
of
engine operation hours.
Battery/voltmeter
C.
Fuel
gauge
shows
amount
of
fuel
in
tank.
D.
Warning
lights
are
visible indicators
that
there
is
aproblem
with
the
indicated system. The warning lights can be checked
by
turning
the
key
to
the
run position
and
depressing
the
preheat
button.
All
lights should
be
on.
D2
D1
Hydraulic
filter restriction
(see
Hydraulic 0il
and
Filter
D4
System
section
of
this
manual).
D2
Hydraulic
oil
temperature
light
will
indicate
that
hydraulic
oil
has
exceeded
190°F
(see
the
Hydraulic
Cooling
Systems
section
of
this
manual).
D3
Engine
water
temperature
light
will
indicate
that
the
engine
coolant has exceeded 200°F (see Engine Cooling
System
section
of
this
manual).
D4
Engine
pressure
light will indicate low oil pressure.
Shut
engine
off
immediately
(see
your
Continental
Engine
Manual).
E.
Starter
switch and key operates the starter motor.
F.
Iight
switch will operate optional work lights.
4
(Revised
4/25/95)

ENGINE
THROTTLE
CONTROL
The
engine
throttle
control
is
located
to
the
left
of
the
operator's
seat.
The
down
position
is
the
idle
speed.
The
more
the
control
is
pulled
up
the
more
the
engine
speed.
The
control
can
be
operated
by
pushing
the
red
button
down
and
moving
the
control
in
the
desired
position.
If
a
more
accurate
metering
of
the
engine
speed
is
required,
the
control
can
be
moved
by
turning
the
black
knob.
Clockwise
will
lower
the
engine
speed
and
counter—clockwise
will
increase
the
engine
speed.
x
TRAVEL
FUNCTION
All
travel
functions
are
controlled
by
a single joystick directional control
located
to
the
left
of
operator's
seat.
Forward
and
reverse
functions are
accomplished
by
pushing the
control
forward
for
forward
movement
and
pulling
the control
back
for
reverse
movement.
Right and
left
hand turns are
accomplished
by
moving
the
control
lever
in
direction
you
want
to
turn.
By
moving
the
control
lever
full
right
or
left,
the
machine
will
counterrotate
in
that
direction.
If
the
control
lever
is
moved
in
the
full
right direction
the
left
hand
track
will
rotate
in
the
forward
direction
and
the
right
hand
track
will
rotate in
the
reverse direction.
The
travel
speed
is
infinitely
variable and
is
controlled
with
the
same
joystick
control.
The
further
the
control
is
moved in
the
direction
of desired travel
the
faster
the
machine
will
travel.
NOTE:
More speed means
less
torque.
If
torque
1s
needed
move
the
control toward
neutral.
TRAVEL
FORWARD
REVERSE

5.
Neutral
can
be
located
by
simply
releasing
the
control.
Neutral
will
automatically
be
found.
6.
IMPORTANT:
As
a
safety
feature,
the
travel
system
will
not
function
if
the
seat
belt is not
used
properly
and
the
brake
is
ON.
DANGER: Unauthorized
modification
of this
system
can result in
serious
injury
or
death.
7. CAUTION:
This
machine is
extremely
maneuverable,
please
keep a lookout in
all
directions
when
operating.
ATTACHMENT
CONTROLS
1.
All
attachment
controls
(excluding
backhoe)
are
located
to
the
right
of
the
operator's
seat.
2.
The
function
of
these controls are as
follows:
JOY
STICK
CONTROL
LOADER
DOZER
FRONT
FRONT
BLADE
DOWN
ANGLE
RH
LH
BLADE
up
OPT.
.
TILT
HYD.
RIGHT
OPT.
HYD.
OPT.
HYD.
*Push
lever
in
full
forward
position
and
boom
function
will
allow attachment
to
float.
3.
IMPORTANT:
A
safety
system
has
been
integrated
into
the
boom
down
function.
The
boom
down
function
will not operate if the seat belt
is
not
in
use
Ah Unauthorized
modification
of
this
system
could result
in
serious
in
jury
or death.

4.
5.
All
safety
instructions
of
the
attachment
should
be
followed
when
operating
an
attachment
that
uses
the
optional
hydraulic
functions.
IMPORTANT:
If
machine is
equipped
with a loader attachment, a boom lock-up
mechanism
is
located
on
the
left
hand
boom
cylinder.
This
lock-up
should
be
used
any
time
the
loader
is
in
the
up
position
and
you
or
anybody is working
in
the area or under
the
loader attachment
or
its
arms
or
cylinders.
Simply
raise
the
loader
to
its
full
height,
pull
the
retaining
pin
to
allow
the
lock
to
lay
down
over
the
cylinder
rod
and
lower
the
attachment
down
against
the
lock.

ENGINE START-UP
AND
OPERATION
1. Prestart Check
a.
Engine
oil
level
should
be
between
marks
on
dipstick.
DO
NOT
start
engine
if
level
is
below
the
low
mark.
b.
Drain
water
from
water
separator
in
fuel
system.
Cc.
Check
engine
coolant level.
2.
Engine
Starting
a.
Set
engine throttle
at
one-third
to
one-half open.
b.
If
engine
is
cold,
preheat
engine
by
turning
switch
key
clockwise
to
run
position,
push
in
the
preheat
button
and
hold
for
seven
(7)
seconds.
c.
Turn
Starter
Switch
key
clockwise
to
start
position
and
release
when
engine
starts.
The
cranking
period
of
starter
should
not
exceed
10
seconds.
CAUTION:
Do
not
use
starting
fluid
to
aid
in
starting
the
engine.
The
use
of
starting fluid will cause permanent damage
to
your
engine and will
void
any engine warranties.
3.
Warm-up
Period
a.
Warm
engine before engaging a full load
to
the machine.
b.
Warm
engine
at about one-half
throttle
until
operating
temperature
has been
obtained.
4.
After
Engine
Start-Up
Checklist
a.
No
warning
lights
should
be
lit.
b.
Charge
system
showing
charge.
Cc.
Engine
noise normal.
d.
Exhaust
smoke
color:
No Color
or
light
blue
.... NORMAL
Black
ABNORMAL
White
ABNORMAL
e.
Check
for
leakage
in
all
fluid
Systems:
Engine
0il
Coolant
Fuel
Hydraulic
5.
Operating
Period
Checklist
a.
Operate
at
full
throttle.
b.
Monitor
gauges and warning lights.
Cc.
Engine noise.
d.
Exhaust
smoke
color
e.
leakage
of
fluids.
6.
Engine
Shutdown.
a.
Make
sure
all
control
levers
are
in
a
neutral
position.
b.
Let
engine cool down by operating it at a low idle
speed
for approximately
three
minutes.
c.
To
stop engine turn switch key
to
off
position.
For
further engine information see engine manufactures instruction
manual
or
call
authorized
engine
dealer.
6
(Revised
4/25/95)

LUBRICATION
AND
MAINTENANCE
INTRODUCT
ION
Although
this
machine has
been
designed
to
require a minimum of maintenance, a good
preventative
maintenance
program
is
still
the
best insurance aginst
downtime
and
costly repairs.
The following recommendations for
lubrication
and maintenance are
based
on
actual
hours of operation and moderate
working
conditions.
The machine is
equipped
with
a
hourmeter
that
shows
accumulated
hours
of
engine
operation.
Always
check
to
be
sure
hourmeter
is
operating.
The
fluid
and
lubricant
specifications
outlined
in
this
manual
are
required
to
maintain
validity of
your
machine warranty
and
the
integrity of
your
machine.
Any
variations
from
these
specifications
could
cause
premature
wear
or
failure.
CAUTION:
Do
not lubricate
or
adjust
tractor
while
engine
is
rumning
unless
recommended.
7-1

LUBRICATION
AND
MAINTENANCE
TIME TABLE
DAILY
Description
Remarks
Page
No
Engine
oil
level 7-5
Coolant
system level 7-11
Hydraulic
oil
level
7-10
Inspect
air
precleaner
7-7
Check
air
restriction
indicator
Replace
element
as
req.
7-7
Inspect radiator and cooler 7-12
Fill
fuel
tank
7-5
Check
voltmeter
7-9
Lubricate
all
grease
fittings
8-3
Check
track
tension
7-13
General
machine
inspection
Machine
clean-up
9
100
HOURS
Description
Remarks
Page
No.
Drain
fuel/water
separator
Drain
if
req.
7-6
Check
engine
belt
tension
7-11
Inspect
battery
and
terminals
7-9
200
HOURS
Description
Remarks
Page
No.
Replace engine
oil
and filter Replace
After
First 50
Hours
7-4
Inspect
all
hoses
Check
final
drive
oil
levels
7-12
Retorque
all
major
hardware
500
HOURS
Description
Remarks
Page
No.
Replace fuel filters
/-6
Clean
fuel
fill
strainer
7-7
Flush
and
refill
coolant
system
or
every
12
months
7-11
Check and adjust valve
tappets
see engine dealer
Replace
hydraulic
filters
7-10
Replace
hydraulic
oil
7-10
Replace
final
drive
oil
7-12
1200 HOURS
Description
Remarks
Page
No.
7-6
Clean fuel
primer
strainer
Check injection nozzles see
Pngine
dealer
7-2
(Revised
4/25/95)

To
make
maintenance
and
service
on
the
machine
as easy as
possible,
access
SERVICE
ACCESS
PANELS
panels
have
been
located
in
strategic
locations.
Hydraulic
Pump
and
Filter
Door.(Fig.
1)
a.
Rear
Cover
Plate.
(FIG.
3)
a.
b.
Ce
Located directly
under
front edge of
seat.
Unlock
by
using
master
key
supplied
with
machine.
Pull
top of door
toward
front of machine
and lift out.
Allows access
to
hydraulic pump,
filters, fuel fill
and
travel
control
cables.
FIGURE
1
2.
Hydraulic
Valve
and
Piping
Cover.
(FIG.
2)
a.
Located
under
the
right
hand
fender.
b.
To
remove
cover,
take
out
6
—
3/8xl
hexhead
capscrews.
Cc.
Allows access
to
hydraulic valve, hoses,
fittings,
and
boom lock solenoid.
FIGURE
2
on rear of
main
frame.
To
remove
take
out
2
-
3/8
x
1
1/4
hexhead capscrews.
Allows access
to
drive motors, brakes,
hoses, final drive bolts, and engine oil
drain
plug.
FIGURE
3
7-3
(Revised
4/25/95)

4.
Engine
Side
Panels.
(FIG.
4)
a.
Located
on
either
side
of
engine
enclosure.
b.
To
remove, unlock with master key,
slide forward and lift out.
Cc.
Allows access
to
engine
oil fill,
oil filters, air filters, fuel
filters
and
other
miscellaneous
engine accessories.
FIGURE 4
5.
Rear
Door.
(FIG.5)
a. Located on rear of machine.
b.
To
open, unlock with master key and
swing
open.
Cc.
Allows access
to
radiator and
hydraulic
oil
cooler.
WT
-—
FIGURE
5
NOTE:
Master
key
should
be
kept
with
machine
at
all
times.
Store
the
key
in
the
hydraulic pump and filter door.
ENGINE
LUBRICATION
SYSTEM
1.
Engine
0il
Selection
a. The quality of engine oil directly affects the engines performance and life.
b.
Use
one
of
the
following
API
oilclassifications:
Ch,
SE/CD,
SF/CD,
or
CG
c.
The
engine
viscosity
(Grade)
largely
affects
the
engine
start
ability,
performance, oil consumption, and life. Select the proper viscosity with
respect
to
the
atmospheric
temperature
(See
Chart
Below)
[Single
grade)
SAE
20,20W
SAE
40,50
Ambieni
TT
Toe we
TT
«22 SE
325)
J
[Multi-
grade]
5A
NOTE: DO NOT mix different brands or qualities of oil, as this will adversely
affect
the
original oil quality.
7-4
(Revised
4/25/95)

Engine
0il
Level
(Check
Daily).
(FIG.
1)
a.
Place
the machine
on
alevel surface.
b.
Remove
the
dipstick
out
from
the
crankcase
and
wipe
it
with
a
clean
towel.
Put
dipstick
back
into
engine
and remove gently.
Check
the
oil
level
on
the
dipstick.
It
should
be
between
the
upper
and
lower
3.
Engine
Oil
Filler.
a.
Filler
location is at
the
rear
end
of
the
cylinder
head cover.
b.
Caution
should
be taken
not
to
spill
oil
on
the
outside
of
the
engine.
Do
not spill
oil
on
the
exhaust
manifold
or
the
fan belt.
Engine
0il
and
0il
Filter
Element
Change.
(FIG
1)
The
engine
oil
change
and
oil
filter
element
change
must
be made
simul
taneously according
to
the
following
change
schedule.
a.
Change
interval:
Every
200
hours
of
operation
(50
hours
initially).
b.
Engine
oil
draining
-
wipe
clean
around
the
oil
filler
cap
so
no
foreign
particles
enter system. Remove filler
cap.
Cc.
Remove lower
panel
located at lower
rear
of
machine.
d.
Position
a drain
pan
under the
drain
plug
in
the
oil
pan
of
the
engine.
Remove
drain
plug
and
allow
the
oil
to
drain completely.
e. Use filter wrench
to
remove cartridge FIGURE 1
type
oil
filter
(located
on
left
hand
side
of
engine
compartment).
f.
Apply
a
thin
coat
of
engine
oil
to
the
O-ring
of
the
new
filter.
g.
Turn
in
the
new cartridge until
the
sealing face
is
fitted
against
the
O-ring. Use the filter wrench
to
turn in the cartridge an additional one
and
1/4
turn.
h.
Reinstall
drain
plug
and
fill
with
new
engine
oil.
Check
level
on
dipstick.
i.
Operate
engine
at
low
idle
to
check
for
leaks.
A
FUEL SYSTEM
Fuel
Selection
a.
Use
ASTM
D975
NO.
2D
(general
automotive
diesel
engine
fuel
oil)
or
equivalent.
b.
If
fuel other
than
the specified
is
used
engine
performance
will be lowered.
Cc.
Fuel
containing
dust
particles
or
water
may
cause
engine
failure.
7-5
(Revised
4/25/95)

Fuel
Filter/Water
Separator
(FIG.
2)
ae
b.
C.
d.
Always
fully
fill
tank.
The
fuel
tank
fill cap
is
located inside
the
door
located
in
front under
the
seat.
(FIG.
1)
FIGURE 1
in
front
right
hand
side
of
engine compartment.
Check
for
water
in
separator
every
100
hours.
To
drain
water
from
separator,
open
valve
on
bottom.
Be
sure
to
tighten
valve
when
finished.
Change
interval
-
500
hours.
Use
hand
pressure
to
remove
filter.
Thread new filter in
place
until
O-Ring
is
against sealing face.
Use
hand
to
turn
the
nut
an
additional
1/4
of
a
turn.
Bleed
air
after
element
change
is
completed.
FIGURE
2
4.
In-Line
Fuel
Filter
Change
(FIG.
3)
a.
Change
interval
—-
500
hours.
b.
Remove
old
filter
by
loosening
the
hose
clamps
on
both ends and pulling the
hoses
off
the
ends
of
the
filter.
Cc.
Install
the
new
filter
by
reversing
the
above procedure.
d.
Important:
This
filter
must
be
installed
in
the
proper
direction.
The
arrow
on
the filter should point
to
the hose from
the
engine's fuel pump.
FIGURE
3
IMPORTANT:
The
fuel
injection
pump
is
precisely
adjusted
and
sealed.
Do
not
break
the
seals.
The
manufacture
of
the
engine
does
not
warranty
the
claim
if
these
seals
have
been
broken.
7-6
(Revised
4/25/95)

6.
EE EE EEE
Fuel Tank Fill Strainer
a. Astrainer
is
located in the fill neck of the fuel tank.
b. Remove and clean
with
fuel
every
500
hours.
ATR INTAKE SYSTEM
Precleaner (FIG. 1)
a.
Inspect
daily
and
clean
as
required.
b. Replace cracked
or
broken bowls and
covers.
Check connection between precleaner
sleeve and
intake
tube
for possible
leaks.
IMPORTANT:
Failure
to
do
any
of
the
above
maintenance procedures will
shorten
the
life
of
the
air
cleaner element.
FIGURE
1
2.
Air
Cleaner
Service
Indicator
(FIG.
2)
a.
The
air
intake
system
is
equipped
with
a
Service
Signal
indicator
to
show
when
air
cleaner
service
is
required.
b. The indicator
is
located on
the
front
side
of
the
main
air
cleaner
assembly
and
should
be
inspected
daily.
C.
When air cleaner service
is
required the
indicator
will
show
in
orange.
After
service
has
been
completed,
reset
the
indicator by pushing
the
reset button on
top.
d. Inspect indicator regularly for damage.
FIGURE
2
Air
Cleaner
Maintenance
(FIG.
3)
a.
Air
cleaner
assembly
is
located
on
top
of the engine enclosure.
b. Clean rubber dust unloading valve once
every 50 hours. Replace if missing
or
damaged.
Cc.
Main element assembly should
be
changed
as service indicator dictates.
d.
The
safety
or
secondary
element
(the
small
inner
element)
should
be
changed
every
third
main
element
change.
FIGURE 3
7-7
(Revised
4/25/95)
This manual suits for next models
1
Table of contents
Popular Compact Loader manuals by other brands

Toro
Toro TXL 2000 Operator's manual
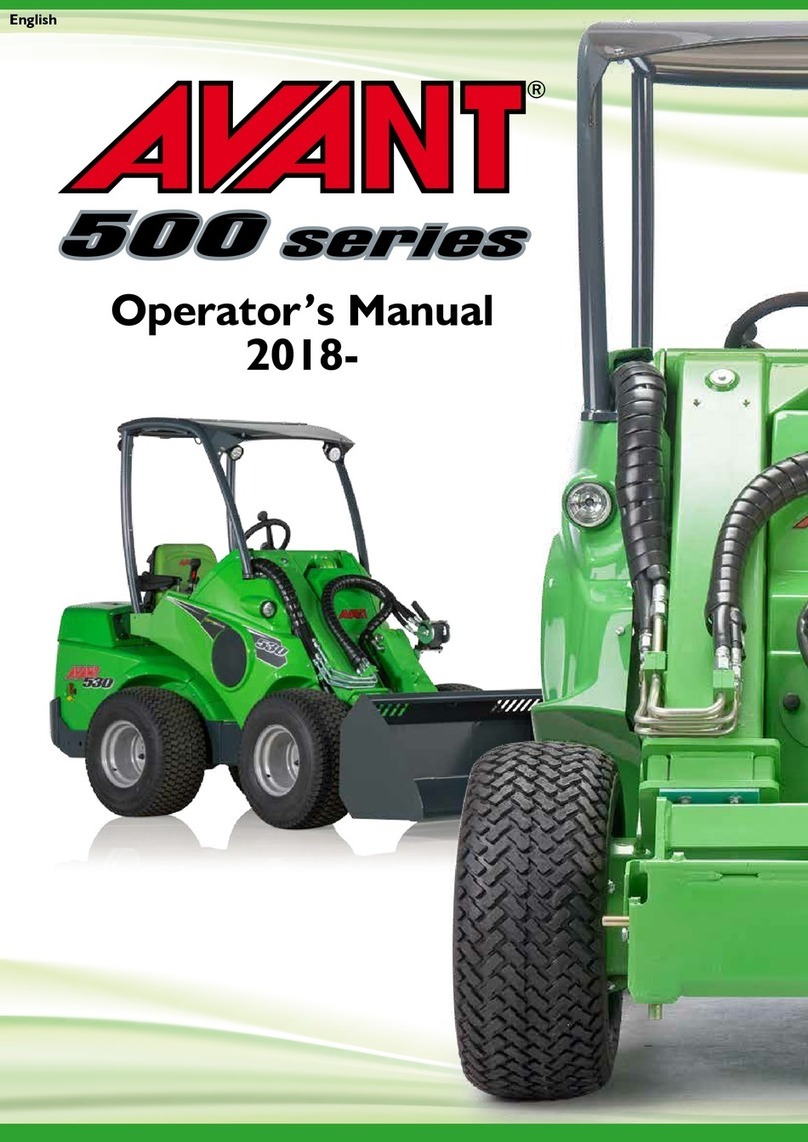
Avantco
Avantco 500 Series Operator's manual

Big Joe
Big Joe J1-192 Maintenance Repair Parts Manual
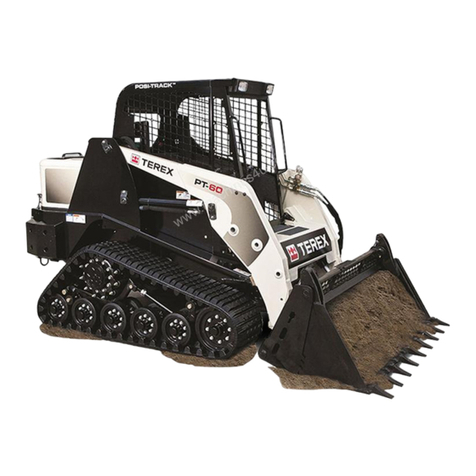
Terex
Terex PT-60 Operation and maintenance manual
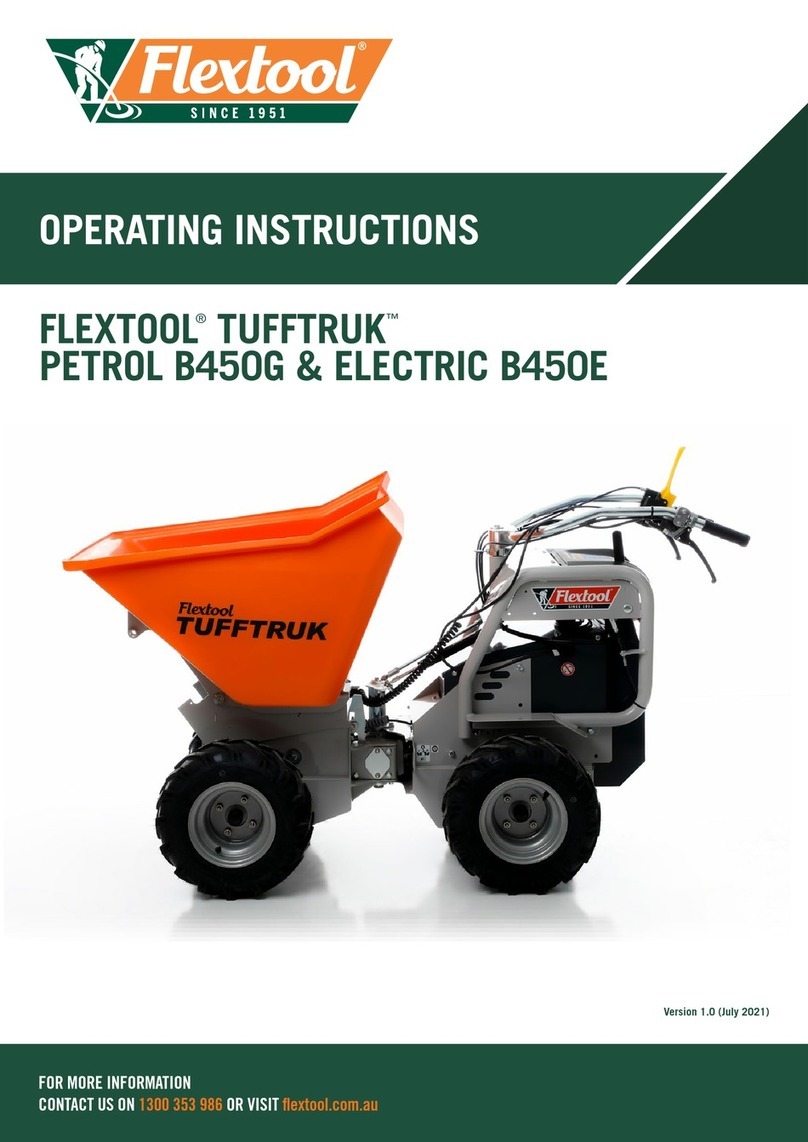
Flextool
Flextool TUFFTRUK B450G operating instructions
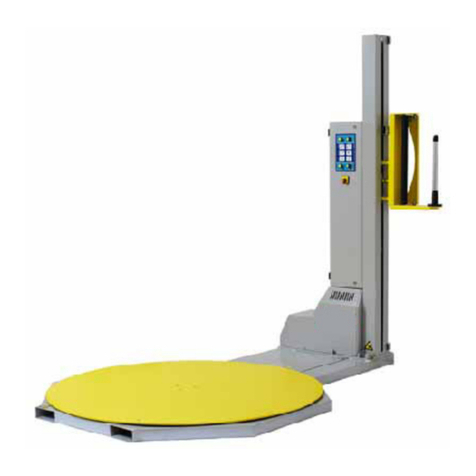
Messersi
Messersi Compact Loader Installation, use and maintenance manual