imPower RB003 User manual

1
Installation
Guide
www.imPowerDealer.com

2 3
2 3
Marathon Electric oers a full line of motors for the pool, spa and bath markets.
Poolside contractors prefer our pool and spa motors for their quick installation,
long life and easy serviceability.
Marathon designs motors for a variety of pool and spa applications, including
above-ground pool, in-ground pool, commercial pool, variable-speed, heat
pumps and all other standard applications.
Our variable speed products consume up to 85% fewer watts than standard PSC
induction motors. This not only saves the Earth's precious resources, but also
saves the consumer hundreds of dollars per year in energy costs.
Why Choose Marathon Electric?
Our fast response to customer questions, unmatched engineering expertise
and the delivery speed that comes with maintaining a large inventory makes
Marathon Electric ideally suited to meeting our customers' needs. In addition
Marathon's focus on innovation keeps our customers on the leading edge of
technology.
Marathon Electric
100 East Randolph St.
Wausau, WI 54402
800-683-9144
www.imPowerDealer.com
The information in this document is subject to change without notice.

2 3
2 3
Table of Contents
Safety Considerations 4
Introduction 6
Operation 7
Removing the Existing Motor from Pump 8
Topside Interface Overview 9
Single Speed Connection with Timer 10
Two Speed Connections with Timer 13
Automation Controller Signal Line Connection 16
Automatic Reduced Speed Selection 20
Software Error Code Matrix 22
Troubleshooting Guide 24
Please read the entire instruction manual before
starting the installation.

4 5
4 5
Safety Considerations
The following denitions are used as safety considerations on the imPower motor
and in this manual. Please read and observe all of these safety concerns.
SAFETY
SYMBOLS
Installation and service of this motor should be attempted only by trained service
technicians familiar with the imPower Installation Guide.
This motor should be installed in accordance with accepted practices and
installation instructions, and in compliance with all national and local codes.
- 1 -
Safety Considerations
The following definitions are used as safety considerations on the
Evergreen IM motor and in this manual. Please read and observe all
of these safety concerns.
SAFETY
SYMBOLS
Installation and service of this motor should be attempted only by
trained service technicians familiar with the Evergreen instructions
and training manual.
This motor should be installed in accordance with accepted practices
and installation instructions, and in compliance with all national and
local codes.
REG7232_EvergreenIM_Reprint.indd 1 4/28/10 2:05:19 PM
- 1 -
Safety Considerations
The following definitions are used as safety considerations on the
Evergreen IM motor and in this manual. Please read and observe all
of these safety concerns.
SAFETY
SYMBOLS
Installation and service of this motor should be attempted only by
trained service technicians familiar with the Evergreen instructions
and training manual.
This motor should be installed in accordance with accepted practices
and installation instructions, and in compliance with all national and
local codes.
REG7232_EvergreenIM_Reprint.indd 1 4/28/10 2:05:19 PM
- 1 -
Safety Considerations
The following definitions are used as safety considerations on the
Evergreen IM motor and in this manual. Please read and observe all
of these safety concerns.
SAFETY
SYMBOLS
Installation and service of this motor should be attempted only by
trained service technicians familiar with the Evergreen instructions
and training manual.
This motor should be installed in accordance with accepted practices
and installation instructions, and in compliance with all national and
local codes.
REG7232_EvergreenIM_Reprint.indd 1 4/28/10 2:05:19 PM
• Disconnectpowerbeforeinstalling,servicing,orrepairingelectrical
components including motors. Observe all warning notices posted on the
existing equipment, imPower motor, and in these installation instructions.
It is also a good practice to conrm power is disconnected with a meter.
• TheimPowermotorcanbeusedtoreplaceinductionmotors.Proper
wiring selection and installation is critical to provide proper operation and
maintain the proper operation of the in-ground pool pump system
in which it is used.
• Alwayskeephandsandclothingawayfrommovingparts.
• Neverattempttomeasurethetemperatureriseofamotorbytouch.
Temperature rise must be measured by thermometer, resistance, imbedded
detector or thermocouple.
• Operationofamotoratlevelsinexcessofitsnameplateratingmayresultin
re, damage to equipment or serious injury to personnel.

4 5
4 5
- 1 -
Safety Considerations
The following definitions are used as safety considerations on the
Evergreen IM motor and in this manual. Please read and observe all
of these safety concerns.
SAFETY
SYMBOLS
Installation and service of this motor should be attempted only by
trained service technicians familiar with the Evergreen instructions
and training manual.
This motor should be installed in accordance with accepted practices
and installation instructions, and in compliance with all national and
local codes.
REG7232_EvergreenIM_Reprint.indd 1 4/28/10 2:05:19 PM
Safety Considerations (continued)
The following denitions are used as safety considerations on the imPower motor
and in this manual. Please read and observe all of these safety concerns.
SAFETY
SYMBOLS
- 1 -
Safety Considerations
The following definitions are used as safety considerations on the
Evergreen IM motor and in this manual. Please read and observe all
of these safety concerns.
SAFETY
SYMBOLS
Installation and service of this motor should be attempted only by
trained service technicians familiar with the Evergreen instructions
and training manual.
This motor should be installed in accordance with accepted practices
and installation instructions, and in compliance with all national and
local codes.
REG7232_EvergreenIM_Reprint.indd 1 4/28/10 2:05:19 PM
- 1 -
Safety Considerations
The following definitions are used as safety considerations on the
Evergreen IM motor and in this manual. Please read and observe all
of these safety concerns.
SAFETY
SYMBOLS
Installation and service of this motor should be attempted only by
trained service technicians familiar with the Evergreen instructions
and training manual.
This motor should be installed in accordance with accepted practices
and installation instructions, and in compliance with all national and
local codes.
REG7232_EvergreenIM_Reprint.indd 1 4/28/10 2:05:19 PM
- 1 -
Safety Considerations
The following definitions are used as safety considerations on the
Evergreen IM motor and in this manual. Please read and observe all
of these safety concerns.
SAFETY
SYMBOLS
Installation and service of this motor should be attempted only by
trained service technicians familiar with the Evergreen instructions
and training manual.
This motor should be installed in accordance with accepted practices
and installation instructions, and in compliance with all national and
local codes.
REG7232_EvergreenIM_Reprint.indd 1 4/28/10 2:05:19 PM
• Forsafety,BuyerorUsershouldprovideprotectiveguardsoverallshaft
extensionsandanymovingapparatusmountedthereon.TheUseris
responsible for checking all applicable safety codes in his area and
providingsuitableguards.Failuretodosomayresultinbodilyinjury
and/or damage to equipment.
• Improperinstallation,adjustment,alternation,service,maintenance,
or use of a motor other than for its intended application or in excess of its
nameplate rating can cause explosion, re, electrical shock, or other
conditions that may cause personal injury, death, or property damage.
Consult a qualied installer, service agency, or your distributor or branch
for information or assistance. The qualied installer or agency must use the
supplied or recommended parts when installing or servicing this product.
• Useofthewiresprovidedwithorrecommendedinthiskitisrequiredfor
proper operation of the motor. Should additional wires be needed, use
equivalent size wire gauge and rated insulation.
• Makesurethemotorisproperlysecuredandalignedbeforeoperation.

6 7
6 7
Introduction
The imPower motor is a permanent magnet alternating current (PMAC) electroni-
cally commutated motor (ECM), leveraging over 20 years of ECM technical and
manufacturing experience. The PMAC machine is inherently more eciency
than its induction counterpart, resulting in energy consumption savings of up to
85%. This imPower motor is designed to safely replace existing full-rated pool
lterpumpmotorsratedat3/4HP1.65SForup-ratedmotorsat1.0HP1.25SF.
This motor also features three selectable speeds either through the use of the
patent pending auto speed switch feature, top panel push buttons, external
multi-speed timers, or through external automation controls.
RB003
ModelNumber 5SME29DFT001
Voltage: 208-230V (±10%)
Flange: Square
HP: 1.0
ServiceFactor: 1.25
High Speed 3450 RPM
Medium Speed 2600 RPM
Low Speed: 1725 RPM
Temp Rating: -40C to +55C
Weight: 11 lbs
RB053
ModelNumber 5SME29DFT002
Voltage: 208-230V (±10%)
Flange: Round/C-Face
HP: 1.0
ServiceFactor: 1.0
High Speed 3450 RPM
Medium Speed 2600 RPM
Low Speed: 1725 RPM
Temp Rating: -40C to +55C
Weight 11 lbs
The installation manual enables a technician, certied by their local/state agency/
board, to install, service, repair, and maintain the imPower motor.

6 7
6 7
Operation
imPower motors are congured with Constant Speed, meaning they simply maintain
the speed (RPM) they are congured for in each application. This reduces the eect
lter cleanliness and product load have on the operation of the motor, unlike
traditional induction motors. The motor only uses the power (current) necessary to
operate at its programmed speed, and has the ability to automatically increase or
decrease power to maintain that speed.
imPower motors turn on and o with application of line voltage. This is critical to its
eectiveness with all existing line-power cuto timers and automation controllers.
Start up
During start up, motor current is slowly applied to motor windings. This provides a
controlled smooth start up. The motor/pump will accelerate to the high speed level
of 3450 rpm in approximately 6-8 seconds. Once started, the motor is programmed to
operate on high speed for two minutes to assure a proper prime is achieved, during
which time no attempt to change speeds will be recognized. Only after this two-min-
ute cycle will a change speed signal be accepted.
If no speed change signal is received by the motor after the two-minute prime cycle,
the motor will remain on high speed for a total of two hours, then automatically turn
down to one of the two reduced speeds. The factory default reduced speed setting
is “low” (1725 rpm), though this can be modied to “medium”(2600 rpm) if the ow/
pressure at low is deemed insucient for operation of certain poolside equipment/
features. The modication of the reduced speed automatic turn-down is found on
page 20 of this guide, titled“Automatic Reduced Speed Selection”.
Stall Detect (Locked Rotor Protection)
This feature protects the motor from external obstructions in the event it does not
achieve high speed operation within 15 seconds of applying voltage or if the RPM
drops below 500 RPM during operation. The imPower is programmed with a hard
fault feature such that the motor will automatically shut down if a stall detect fault
is registered. Power at the timer or automation controller must be removed and
reapplied after one minute of “dwell” time to restart the motor.
Overload Protection (Over-Current or Over-Temperature)
The imPower motor is specied with a series of sensors that continuously monitor the
temperature of critical internal components as well as the current owing through the
electronics. The motor will automatically shutdown if either limit is exceeded. Like the
stall detection, the timer or controller power must be removed, though it is recom-
mended that the motor power stay removed for at least 15 minutes to allow the motor
to cool and/or to determine the cause of the overload condition.

8 9
8 9
Remove the Existing Motor from Pump
Step 1: Loosen and remove the screws holding the seal plate to the pump
housing. Pull the seal plate / motor assembly from the pump housing.
Step 2: Remove the screws holding the diuser to the seal plate and remove it.
Step 3: After conrming that the power has been shut o, remove the electrical
connections from the existing motor. Remove the conduit and connec-
torfromthemotor.Note:theconduitandconnectorwillbere-used.
Step 4: To remove the impeller lock the shaft by placing a wrench or a athead
screwdriverattheopeningintherear.Note:Donotreusetheseal
from the existing motor when installing the imPower motor. Remove
the screws holding the seal plate onto the motor.
Step 5: Remove the pump motor by removing the four bolts holding the motor
to the seal plate of the pump. Also remove the stationary portion of the
seal from seal plate.
- 1 -
Safety Considerations
The following definitions are used as safety considerations on the
Evergreen IM motor and in this manual. Please read and observe all
of these safety concerns.
SAFETY
SYMBOLS
Installation and service of this motor should be attempted only by
trained service technicians familiar with the Evergreen instructions
and training manual.
This motor should be installed in accordance with accepted practices
and installation instructions, and in compliance with all national and
local codes.
REG7232_EvergreenIM_Reprint.indd 1 4/28/10 2:05:19 PM
When servicing the pool pump lter motor, always disconnect the main power
from the unit. It is also good practice to conrm the power is o with a meter.

8 9
8 9
Topside Interface Overview
The topside interface on the imPower motor provides functionality to change
amongst three distinct preset speeds via either a button press or by a remote
timer / automation controller. Green display LED’s will light to indicate the
currently selected speed as well as to indicate power is applied to the motor. A
red Error LED is also included to show a fault identied by the on-board diagnostic
system.
The following are the LED lights that will shine in each normal operational
condition.
This condition is present:
1. Directly after energizing the motor
2. After selecting high speed via a button
press
3. After selecting high speed via a timer or
automation controller
This condition is present
1. After selecting medium speed via a but-
ton press
2. After selecting medium speed via an
automation controller
3. After two hours of high speed operation
if the factory default automatic speed
selection was changed to medium (refer
to page 20)
This condition is present
1. After selecting low speed via a button
press
2. After selecting low speed via an automa-
tion controller
3. After two hours of high speed operation
if the factory default automatic speed
selection was changed to medium (refer
to page 20)
Notes:
1. The red Error LED will blink once after power is applied to the motor. This
indicates the internal self-check has returned normal results.
Figure 1
Figure 2
Figure 3

10 11
10 11
Single Speed Connection with Timer
These steps as outlined below are for connection of the imPower motor to a single
speed timer.
Step 1: Remove the three screws holding the top control enclosure onto the
motor. Carefully lift the top panel and turn it over to expose the inside
of the terminal box.
Step 2: Run the L1, L2, and GROUND wires from the conduit cable through the
threaded opening on the right side of the connection box.
Step 3: Connect the L1 to the terminal block opening directly across from the
ORANGEwire(refertoFigure6).
Step 4: Connect L2 to the block opening directly across from the WHITE wire
(refertoFigure6).
Step 5: Connect the ground to the block
opening directly across from the
GREEN/YELLOW wire (refer to
Figure6).
Step 6: Screw in the conduit connector into
the terminal box on the right side of
the terminal box (shaft facing away
from you).
Always disconnect the main power from the unit prior to servicing the pool
pump lter motor. It is also good practice to conrm the power is o with a
voltage meter
- 1 -
Safety Considerations
The following definitions are used as safety considerations on the
Evergreen IM motor and in this manual. Please read and observe all
of these safety concerns.
SAFETY
SYMBOLS
Installation and service of this motor should be attempted only by
trained service technicians familiar with the Evergreen instructions
and training manual.
This motor should be installed in accordance with accepted practices
and installation instructions, and in compliance with all national and
local codes.
REG7232_EvergreenIM_Reprint.indd 1 4/28/10 2:05:19 PM
Figure 4 Figure 5
Figure 6

10 11
10 11
Step 7: Carefully fold the extra wires inside the terminal box and place the top
control panel back on top of the terminal box.
Step 8: Tighten the three screws into the terminal box while applying light
pressure to the top control enclosure.
Step 9: Replace and tighten the screws to mount the seal plate onto the motor.
Step 10: Put a NEW pump seal into the seal plate and onto the motor shaft.
Handle and lubricate seal per manufacturer’s specications.
Step 11: Replace the impeller. Make sure that the impeller can spin freely in the
housing.
Step 12: Replace the diuser.
Step 13: Replace and tighten the bolts that retain the motor/seal plate assembly
to the pump.
Step 14: Connect the appropriately sized ground conductor to the supplied
grounding/bonding lug.
Step 15: Open the inlet and outlet valve.
Step 16: Reapply power and allow motor to accelerate to high speed and
operate there for at least two minutes to assure adequate pump
prime has been established.
Notes:
1. In this type of connection, the motor will operate on high speed for
2 hours, followed by an automatic turn-down to a reduced speed. As
noted in the “Operation” section of this manual, the factory default
reduced speed setting is“low” (1725 rpm), though this can be modied
to “medium” (2600 rpm) if the ow/pressure at low is deemed insucient
for operation of certain poolside equipment/features. The modication
of this reduced speed automatic turn-down is found on page 20 of this
guide, titled“Automatic Reduced Speed Selection”
2. The selectable on-time of the timer should be adjusted so the pool can
meet the total number of turns as required by local/state regulations.

12 13
12 13
3. The user can override the operational speed currently running via the
buttons on the top control panel after the mandatory initial two-minute
prime cycle. The override will continue until the timer removes power or
another button is pressed. The standard operation identied in
Note1canberesumedifthepoweristurnedoatthetimerand
turned back on.
Extended Functionality
The imPower motor also has the ability
to operate on high speed for only the
mandatory two-minute pump priming
cycle before changing to low speed until
power is removed. Simply change the
connection description noted above by
moving the incoming L1 to the terminal
block across from the Red lead (refer to
Figure7)toactivatethisfeature.Note
that the automatic reduced speed
function dened on Page 20 of this guide
does not apply with this feature.
Figure 7

12 13
12 13
- 1 -
Safety Considerations
The following definitions are used as safety considerations on the
Evergreen IM motor and in this manual. Please read and observe all
of these safety concerns.
SAFETY
SYMBOLS
Installation and service of this motor should be attempted only by
trained service technicians familiar with the Evergreen instructions
and training manual.
This motor should be installed in accordance with accepted practices
and installation instructions, and in compliance with all national and
local codes.
REG7232_EvergreenIM_Reprint.indd 1 4/28/10 2:05:19 PM
Always disconnect the main power from the unit prior to servicing the pool
pump lter motor. It is also good practice to conrm the power is o with a
voltage meter.
Two Speed Connections with Timer
If you had a single speed motor prior to this installation, you will need to run a
newconduitwithfourconductors(HighSpeed,LowSpeed,Neutral,andGround)
and proceed through the following steps to properly operate the motor with the
multi-speed timer. Proceed to step 5 if a multi-speed timer is already installed and
operating a two-speed induction motor.
Step 1: Remove the caution / instruction cover from the front of the timer,
exposingthescrewterminalsunderneath(refertoFigure8).
Step 2: Connect the L1 and L2 incoming power leads into the two left-most
screw terminals . The timer is connected for 240V from the factory, so
no internal timer changes are required.
Step 3: Connect a jumper lead of at least 18AWG size between the L1 terminal
and the Line-side of Circuit 1. Connect a second jumper lead between
the Load-side of Circuit 1 and the Line-side of Circuit 2 as illustrated
above.
Step 4: Connect the L2 lead of the new four-conductor conduit to the same
screwterminalastheincominglineL2,theHighSpeedBlackleadto
the Line-side of Circuit 1, and the Low Speed Red lead to the Load-side
of Circuit 2.
Figure 8 Figure 9

14 15
14 15
Step 5: Remove the three screws holding the top control enclosure onto the
motor. Carefully lift the top panel and turn it over to expose the inside
of the terminal box.
Step 6: RuntheHighSpeedBlack,LowSpeedRed,L2,andGroundwiresfrom
the conduit cable through the opening on the right side of the motor.
Step 7: Connect the wire for Circuit 1 from the timer to the opening directly
acrossfromtheBLACKwireontheterminalblock(refertoFigure10).
Step 8: Connect the wire for the Circuit 2 from the timer to the opening directly
acrossfromtheREDwireontheterminalblock(refertoFigure10).
Step 9: Connect the L2 to the opening directly across from the WHITE wire on
theterminalblock(refertoFigure10).
Step 10: Connect the ground to the opening directly across from the GREEN/
YELLOWwireontheterminalblock(refertoFigure10).
Step 11: Screw in the conduit connector into the terminal box on the right side
of the terminal box.
Step 12: Carefully fold the extra wires inside the terminal box and place the top
control panel back on top of the terminal box.
Step 13: Tighten the three screws into the terminal box while applying light
pressure to the top control enclosure.
Step 14: Replace and tighten the screws to mount the seal plate onto the motor.
Step 15: Put a NEW pump seal into the seal plate and onto the motor shaft.
Handle and lubricate seal per manufacturer’s specications.
Figure 10

14 15
14 15
Step 16: Replace the impeller. Make sure that the impeller can spin freely in the
housing.
Step 17: Replace the diuser.
Step 18: Replace and tighten the bolts that retain the motor/seal plate assembly
to the pump.
Step 19: Connect the appropriately sized ground conductor to the supplied
grounding/bonding lug.
Step 20: Open the inlet and outlet valve.
Step 21: Reapply power and allow motor to accelerate to high speed and
operate there for at least two minutes to assure adequate pump prime
has been established.
Notes:
1. This connection allows the high speed and low speed to be operated
at any duration set by the multi-speed timer. At no point will the motor
automatically turn down to the selected reduced speed. The two-minute
prime cycle is still operation at initial start-up. The timer should be set
so that the pool can meet the total number of turns as required by local/
state regulations.
2. The user can override the operational speed currently running via the
buttons on the top control panel after the mandatory initial power-up
two-minute prime cycle. The override will continue until the motor is
either powered o by the multi-speed timer or a new speed is requested
by the multi-speed timer. At anytime, another speed can also be se-
lected via the top side control panel buttons.
3. In this type of connection, the motor will operate on high speed and
a reduced speed as dened by the multi-speed timer programming.
As noted in the“Operation” section of this manual, the factory default
reduced speed red lead setting is “low” (1725 rpm), though this can be
modied to “medium” (2600 rpm) if the ow/pressure at low is deemed
insucient for operation of certain poolside equipment/features. The
modication of this reduced speed automatic turn-down is found on
page 20 of this guide, titled“Automatic Reduced Speed Selection”.

16 17
16 17
Automation Controller Signal Line Connection
The steps as outlined below are for connection of the imPower motor to an auto-
mationcontroller.TheoptionallowvoltagecableconnectionkitP/N391-200-01
(15’cord)orP/N391-200-02(25’cord)willberequired.
Step 1: Remove the three screws holding the top control enclosure onto the
terminal box. Carefully lift the top panel and turn it over to expose the
inside of the terminal box.
Step 2: Run L1, L2, and GROUND wires from the conduit cable through the
open on the right side of the motor (shaft facing away from you).
Step 3: Connect L1 from the automation
controller to the opening directly
across from the BLACK wire on the
terminalblock(refertoFigure11).
Step 4: Connect the L2 / White to the
opening directly across from the
WHITE wire on the terminal block
(refertoFigure11).
Step 5: Connect the ground to the opening directly across from the GREEN/
YELLOWwireontheterminalblock(refertoFigure11).
Step 6: Screw in the conduit connector into the terminal box on the right side
of the terminal box (shaft facing away from you).
Step 7: Remove the small threaded black
plug on the rear of the terminal box.
Step 8: Pull the cable through the low
voltage conduit connector con-
tained within the kit and tighten
the connector into the appropriate
terminal box threaded hole. Run the
low voltage cable to the automation
control box.
- 1 -
Safety Considerations
The following definitions are used as safety considerations on the
Evergreen IM motor and in this manual. Please read and observe all
of these safety concerns.
SAFETY
SYMBOLS
Installation and service of this motor should be attempted only by
trained service technicians familiar with the Evergreen instructions
and training manual.
This motor should be installed in accordance with accepted practices
and installation instructions, and in compliance with all national and
local codes.
REG7232_EvergreenIM_Reprint.indd 1 4/28/10 2:05:19 PM
Always disconnect the main power from the unit prior to servicing the pool
pump lter motor. It is also good practice to conrm the power is o with a
voltage meter.
Figure 11
Figure 12

16 17
16 17
Step 9: Plugtheconnectorendofthelowvoltagecable(P/N391-200-01or
P/N391-200-02)intotheconnectorontheundersideofthetopcontrol
enclosureasseeninFigure13.
Step 10: Carefully fold the extra wires inside the terminal box and place the top
control panel back on top of the terminal box and tighten the three
topside enclosure screws.
Step 11: Carefully pull the low voltage cable to reduce the amount of excess
cable inside the connection box. Tighten the connector nut.
Step 12: The connection of the low voltage
wires at the automation controller
should be to the HOT side of the
auxiliary/AUXrelays(redandblack
wire on the top side of the relay).
Depending on the manufacturer of
the automation controller, you may
need to remove the cover plate on
these relays to gain access to the
terminals.
Note: The pictures shown in this section are
provided for illustrative purposes only.
The actual conguration of the auto-
mation controller at installation site
may be dierent than what is shown.
Refer to the controller operations
manual for proper identication of
AUXrelays.
Figure 13 Figure 14
Figure 15
Figure 16

18 19
18 19
Step 13: Wire the low voltage cable to the automation controller. The speed
connectionsandtheircorrespondingleadcolorsareshowninFigure
17. The (+) marking denotes the positive side controller connection
and the (-) denotes the negative side controller connection.
High Speed:
BLACK(+)
WHITE (-)
Medium Speed:
BROWN(+)
BLUE(-)
Low Speed:
RED (+)
GREEN(-)
Step 14: Replace any access panels on the controller that were removed.
Step 15: Replace and tighten the screws to mount the seal plate onto the motor.
Step 16: Put a NEW pump seal into the seal plate. Handle and lubricate seal per
manufacturer’s specications.
Step 17: Replace the impeller. Make sure that the impeller can spin freely in the
housing.
Step 18: Replace the diuser.
Step 19: Replace and tighten the bolts that retain the motor/seal plate assembly
to the pump.
Step 20: Connect the appropriately sized ground conductor to the supplied
grounding/bonding lug.
Step 21: Open the inlet and outlet valve.
Step 22: Reapply power and allow motor to accelerate to high speed and oper-
ate there for at least two minutes to assure adequate pump prime has
been established.
Figure 17

18 19
18 19
Notes:
1. The automation controller allows for the programmable operation of
all three speeds. The motor will start on high speed for each speed
selection and operate through its two-minute prime cycle before
reacting to any controller inputs. The on time and speeds should be set
so that the pool can meet the total number of turns as required by local/
state regulations.
2. The user can override the operational speed currently being set by the
automation controller via the buttons on the top control panel. The
override will continue until either the power is removed by the
automation controller or a new speed is requested by the automation
controller. Other than the initial start-up prime cycle, a change in speed
can be initiated at any time via the top side control panel buttons.

20 21
20 21
Automatic Reduced Speed Selection
The imPower motor has been programmed with a feature called the Automatic
Reduced Speed Selection function that allows for the maximum energy savings
via multi-speed operation despite using a standard single-speed timer. This
feature also applies to a multi-speed timer where the Circuit 2 speed can either be
assigned to medium or low speed.
The reduced default speed is factory set to switch to low speed operation after the
initial two-hour high speed operational period. However, it can be modied to
medium speed as required by minimum ow / pressure requirements of various
pool-side equipment / features as dened by manufacturer specications. The
default speed should only be modied during the rst two minutes of applying
power to the unit.
Please follow all local/state regulations regarding pool motor and timer speed
settings when choosing default reduced speed operation.
Step 1: Allow the pump to achieve prime if starting the system for the rst time.
Step 2: Turn power to the motor o at the timer / controller once pump prime
is reached. Also turn power o to the motor if prime was previously
reached and now motor/pump are operating as dened by the timer.
Step 3: Turn the motor on after allowing the motor to sit for at least 30 sec-
onds. Ensure that HIGH speed / Circuit 1 is being commanded if using a
multi-speed timer.
Step 4: After allowing the motor to come
to full speed, press and hold the
high and medium buttons simulta-
neouslyasshowninFigure18until
the low speed LED indicator light
begins to blink and then release.
Step 5: The low speed LED will continue to
blink for three seconds to indicate a
modication to the automatic
reduced speed turndown is being requested. After a brief pause, a sec-
ond series of LED blinks will indicate the new default setting has been
set to either medium speed (medium speed LED blinks) or low speed
(low speed led blinks).
Step 6: Turn the motor o, wait 30 seconds, turn back on to activate new setting.
Figure 18
This manual suits for next models
3
Table of contents
Popular Engine manuals by other brands

Regal
Regal Century V-GREEN 165 user manual
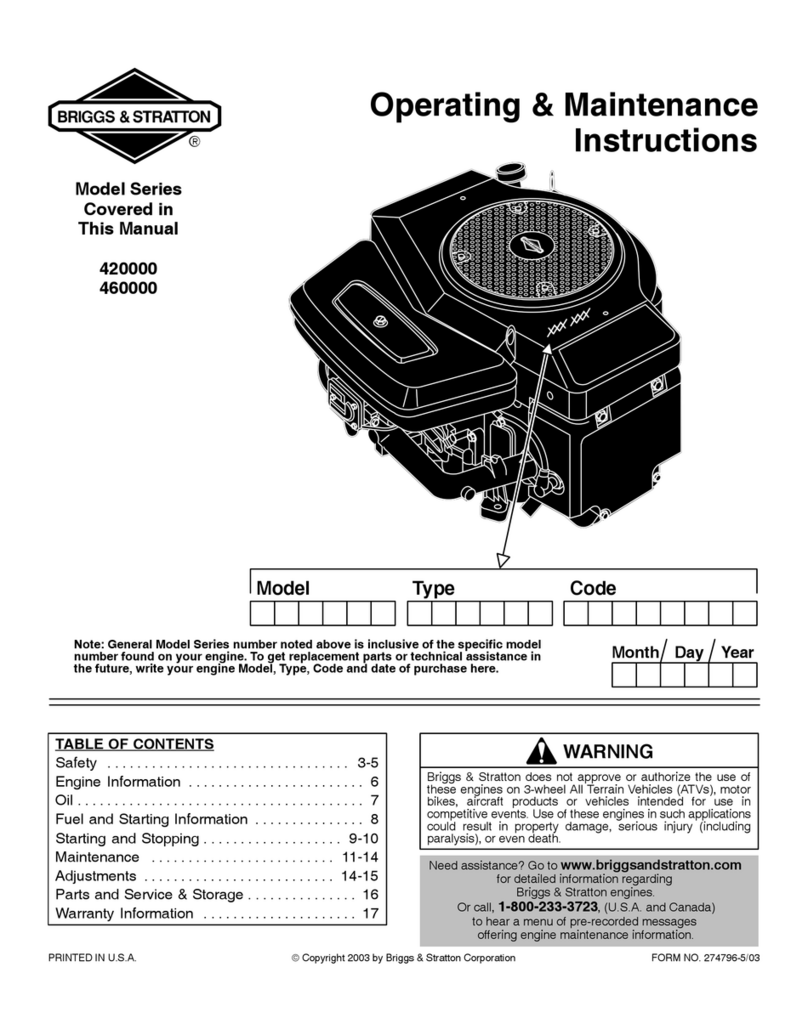
Briggs & Stratton
Briggs & Stratton 420000 Series Operating and maintenance instructions
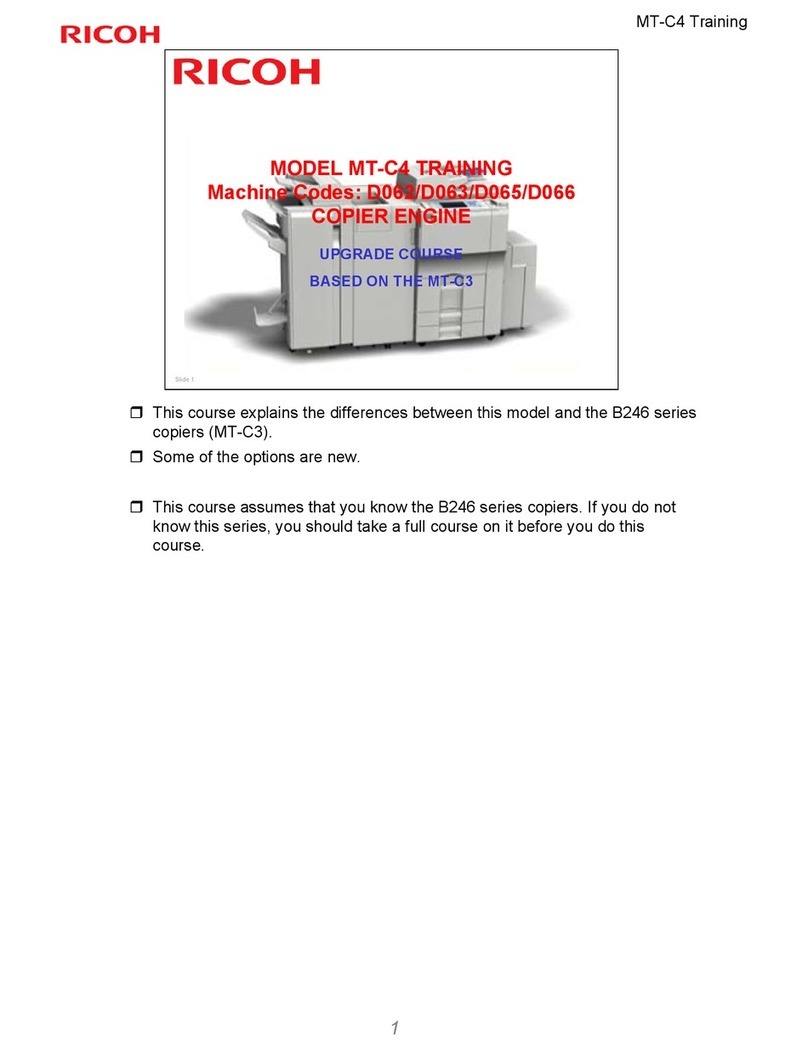
Ricoh
Ricoh MT-C4 manual

Yaroslavl
Yaroslavl ???-236 Maintenance manual

Shindaiwa
Shindaiwa DGW310MC Owner's and operator's manual
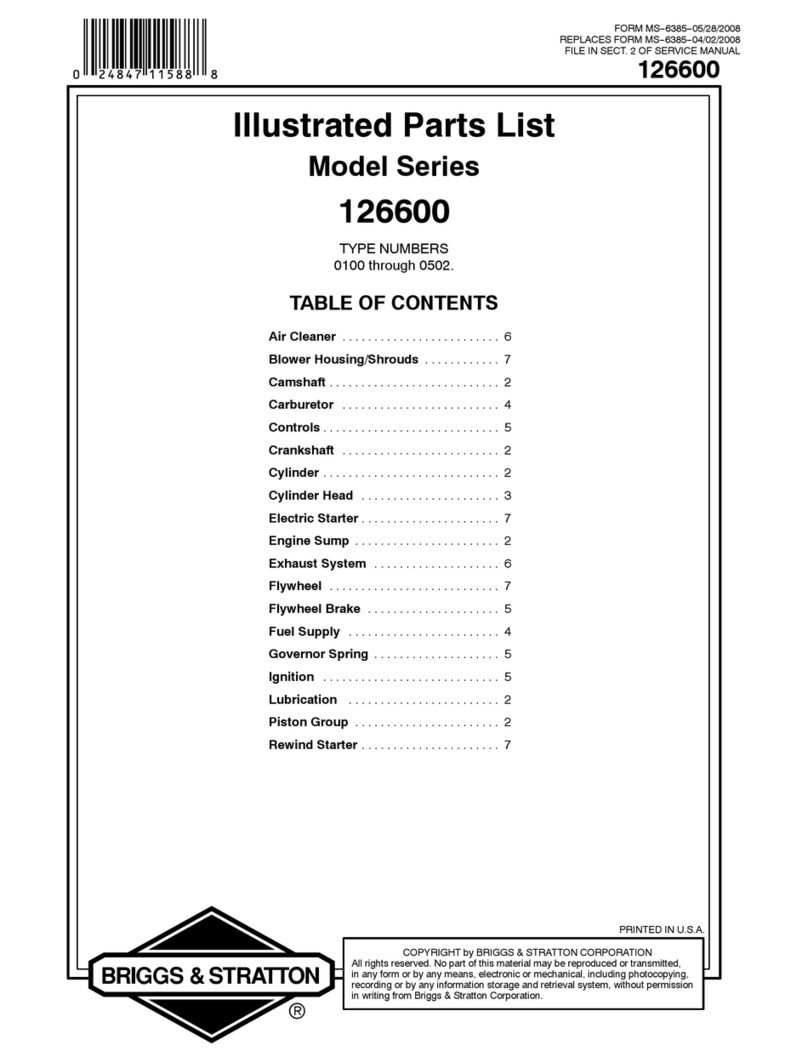
Briggs & Stratton
Briggs & Stratton 126600 specification
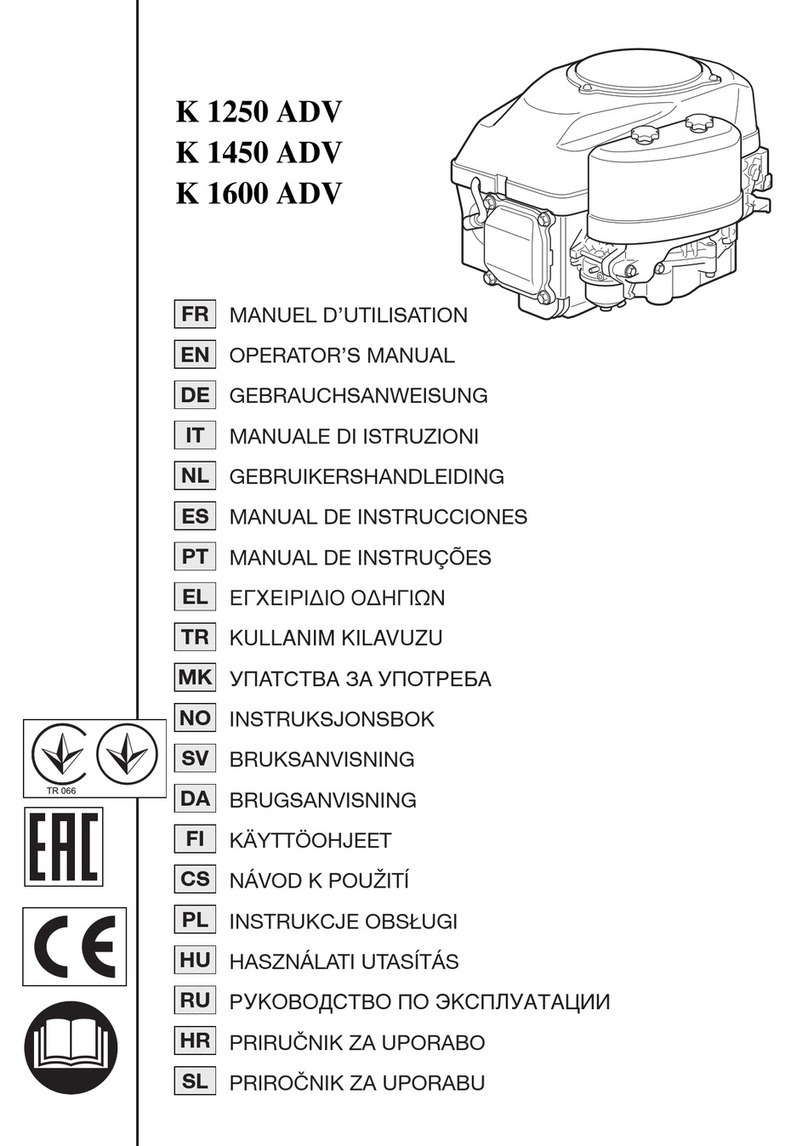
EMAK
EMAK K 1250 ADV Operator's manual

Briggs & Stratton
Briggs & Stratton 11000B Operator's manual
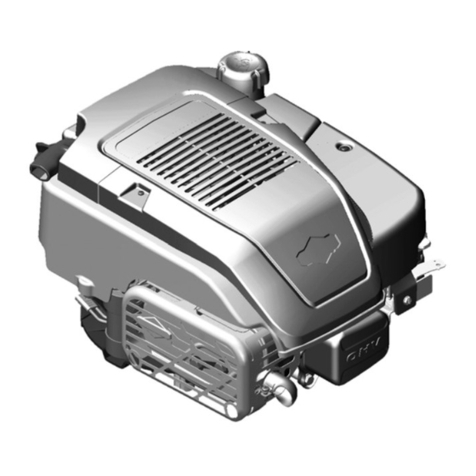
Briggs & Stratton
Briggs & Stratton PROFESSIONAL SERIES 110000 Operator's manual

Volvo Penta
Volvo Penta D8 2020 Operator's manual

Sears
Sears 143.996706 Operator's manual
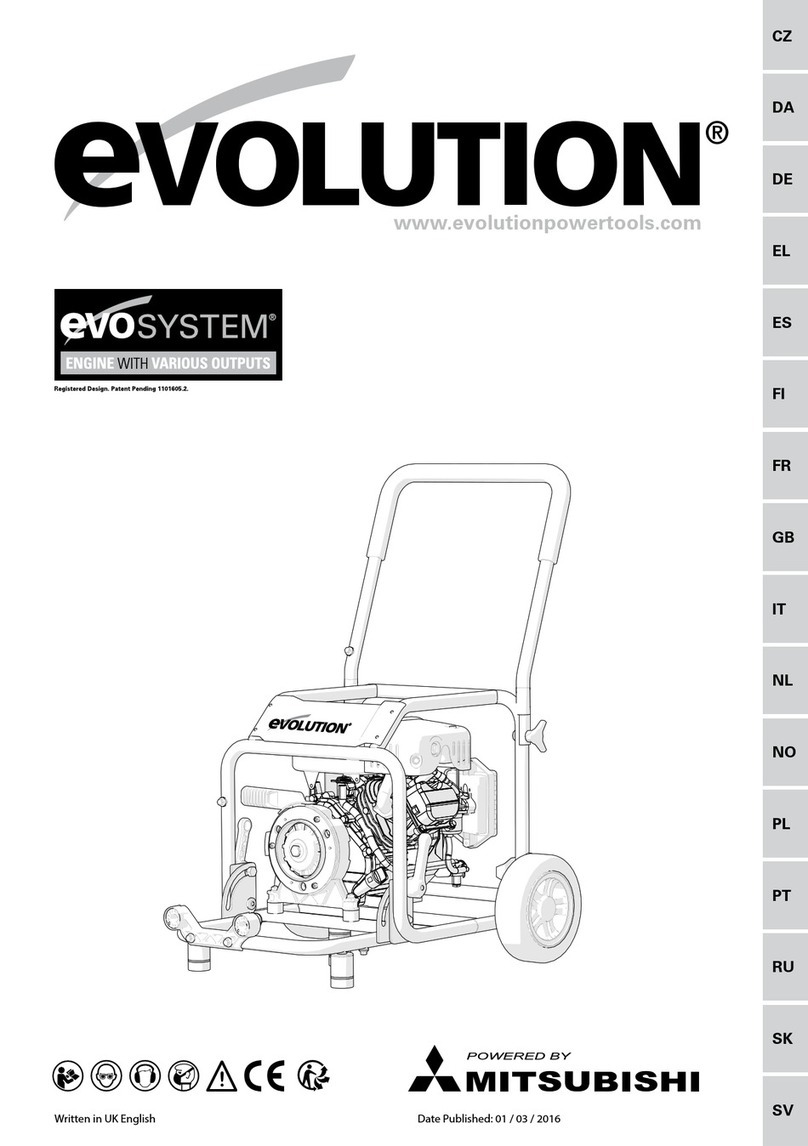
Evolution
Evolution EVOMITS Original manual