Integral Solutions EPS-100 User manual

ESD Hardware Option Manual
Integral Solutions Int'l
– EPS-100 –
August 22, 2013
Copyright 2003-2013 Integral Solutions Int'l
All rights reserved
Integral Solutions Int'l
3000 Olcott St
Santa Clara, CA 95054
Phone: (408) 653-0300 Web: http://www.us-isi.com/
Fax: (408) 653-0309 E-mail: isi@us-isi.com
While every effort has been made to verify the accuracy of the information contained in this publication, this publication may contain
technical and/or typographical errors. Please contact Integral Solutions Int’l to report any errors in this publication.

Contents
1.
HARDWARE DESCRIPTION 3
2.
INSTALLATION 4
3.
MAINTENANCE 5
4.
CHARGE DEVICE MODEL (CDM) 6
4.1
MECHANICAL ALIGNMENT 6
4.2
MONITORING WAVEFORM 7
4.3
ESD STANDARD 8
4.4
CALIBRATION 10
4.5
CDM OPERATION 12
5.
MACHINE MODEL (MM) 13
5.1
MECHANICAL ALIGNMENT 13
5.2
MONITORING WAVEFORM 14
5.3
ESD STANDARD 15
5.4
CALIBRATION 16
5.5
MM OPERATION 17
6.
HUMAN BODY MODEL (HBM) 18
6.1
MONITORING WAVEFORM 18
6.2
ESD STANDARD 19
6.3
CALIBRATION 20
6.4
HBM OPERATION 21
7.
ESD SWEEP TEST 22
8.
BAR ESD STRESS OPTION 23
8.1
BAR ESD OPTION INSTALLATION 23
8.2
MONITORING THE WAVEFORM ON BAR HBM/MM 25
8.3
CHANGING THE WAVEFORM MODULE 27
8.4
SOFTWARE CONTROL DIAGRAM 28
8.5
ESD PROBE CARD PIN-OUT 28
9.
HIGH FIELD ESD STRESS OPTION 29
10.
CONTACT INFORMATION 29
11.
TABLE OF FIGURES 30

EPS-100 Manual Integral Solutions Int’l
August 22, 2013
Page 3
1. Hardware Description
ESD Hardware Option is designed as an add-on to ISI QST-200x testers to study sensitivity of magneto-
resistive heads to electro static discharge. ESD stress can only be done at HGA level and can be run in either
standalone mode or as part of QST test.
ESD option consists of EPS-100 and waveform module. EPS-100 is a power supply, capable of producing +/-
100V with 0.003V resolution. It is universal for all waveform modules. Due to calibration for more precise HBM
and MM amplitude, the waveform module may require voltages slightly higher than 100, which is not supported by
EPS-100. Therefore the maximum HBM and MM firing voltage is +/-90V.
Waveform module is responsible for producing a pulse of a known shape (using one of the standard ESD
models) and switching the head from stressing to testing. There are three standard types of waveform modules:
Charge Device Model (CDM), Human Body Model (HBM), and Machine Model (MM). Newer waveform modules
are located directly on the 2xHGA cartridge in close proximity to the head, and are called cartridge-style. Such
modules can be run standalone or mounted on 2x tooling directly for testing.
Older type module is an add-on to QST that has two 6-pin cables running to standard QST 2xHGA cartridge,
and is called a box-style module. HBM and MM box-style waveform modules do not support any AC measurements.
These modules are no longer manufactured, however EPS-100 supports them as well. A special adapter board for
EPS-100 is required to run the box-style waveform modules.
HBM and MM modules are universal for any flex design; custom mechanics that are required for different
heads are located on the cartridge. So HBM and MM waveform modules can be freely interchanged on one
cartridge. CDM waveform module on the other hand requires unique mechanical configuration for each flex design,
and cannot be mounted on HBM/MM cartridge.
EPS option was designed to work with the automated ESD Sweep test. The test uses EPS to generate controlled
ESD transients and measures head parameters between the pulses to find ESD failure threshold (voltage). Any QST-
200x test, including AC measurements, can be used to characterize the head and find the ESD failure threshold. QST
test requires a QST-200x and either 2xHGA tooling (for cartridge style waveform modules) or 8xHGA tooling for
box-style. To enable this test, add ESDApp.Application to Quasi97
Selected Modules and enable it.
!Important!
It is not recommended to expose any waveform module to magnetic fields higher than 250Oe. When running
QST tests with waveform module close to the magnet, make sure that magnetic field from the QST magnet does not
cause field near waveform modules to exceed 200Oe.
On standard 2-pole HSA/HGA magnet the module is physically inside the magnet so 250Oe limit applies.
However, other magnet design (for example 4-pole or 15K high field) can go to higher fields without affecting the
waveform module due to smaller field leakage in the perimeter. For example QST-2002HF Tester and QST-2002
with Quad-Pole HGA Magnet can go to higher fields.
!Important!
The diodes on Gen2 2xHGA cartridges must be removed in order to work properly with Machine Model (MM)
and Human Body Model (HBM) ESD modules. So the “MR Clamping During Write” feature is not supported by the
HBM/MM Gen2 type cartridges. User must remember the fact that the QST-2002 tester cannot recognize if the
diodes are present or not, so “MR Clamping During Write” even though available in software, will not work. The
diode protection still exists on the 2xHGA GEN2 interface board, using programmable clamping voltage, but it is
enabled in both write and read modes.
!Important!
On Gen2 2xHGA type cartridges, for HBM and MM, the DC cable makes a slight impact on the waveform with
higher resistance read heads. While it is recommended to have it for higher accuracy measurement, it has negative
impact on the amplitude of the HBM waveform (HBM peak on 500ohm reader is ~5% higher with the DC ribbon
cable because of additional capacitance). In order to avoid this phenomena, the DC ribbon cable between the
cartridge and HGA connector board can be removed. In this case the cartridge needs to be reworked as follows:
1) On HGA connector board - remove the R5 and R7.
2) On the G2 2x Universal Cartridge board, install 0ohm resistors on R5-R10.

EPS-100 Manual Integral Solutions Int’l
August 22, 2013
Page 4
2. Installation
1. Install the NI-DAQ PCI-6503 in one of available PCI slots in the computer.
2. Connect EPS-100 to the NI-Daq card using a 50-pin ribbon cable.
3. Connect the waveform module to the EPS-100 using 26-pin cable.
4. Plug in EPS-100 power supply to a standard 115VAC outlet.
5. Turn on the PC, and run Quasi97. Go to FileHardware Config. Add one line item, select for
module type EPS100Lib.clsHOption, * in the instance column and ESD Option in the function
column.
6. Select a setup file. In the Add-InsSelected modules, enable ESDApp.application.
7. ESD option is ready. You can fire single pulses from FileHardwareConfigEPS100Lib User
menu, or run an ESD Sweep test.
If you are installing the EPS-100 option on the new PC, you need to install the NIDAQmx 9.7 software. The
NIDaqmx Core link is available on www.us-isi.com – this is the bar minimum required to run.
There is also an option to install full version of NIDAQmx. This can be downloaded from National Instruments
website. If installing full NIDAQ version, then following must be done:
1) Select the following options.
2) After Installing the NI-DAQ software, run “Measurement and Automation Explorer” from your Desktop.
3) Go to "Devices and Interfaces", click "View"-->"Refresh".

EPS-100 Manual Integral Solutions Int’l
August 22, 2013
Page 5
4) The new PCI-6503 card should appear on the list. Click on the PCI-6503 card, then "Properties" - the
software will verify the card.
5) After than close Measurement and Automation Explorer and Start Quasi97.
F
Fi
ig
gu
ur
re
e
2
2-
-1
1
–
–
M
Me
ea
as
su
ur
re
em
me
en
nt
t
a
an
nd
d
A
Au
ut
to
om
ma
at
ti
io
on
n
E
Ex
xp
pl
lo
or
re
er
r
The 50pin ribbon cable with the choke between QST Universal Interface and 2xHGA tooling is to reduce
AC noise on 2xHGA ESD option. It should be used if ESD Option is installed, and does not have any effect on
standard non-ESD cartridgees.
2xHGA Gen2 Users:
For CDM ESD test, you should have a special cartridge that does not have DC cables and connectors
installed. The CDM cable splits into 2 AC cables (write and read) that should be connected to the back of the
cartridge.
For MM/HBM ESD test, you should reuse the non-ESD cartridge. You have to disconnect the 4 AC cables,
then install a shim and put on the ESD waveform module. Then connect the waveform module to the cartridge via
Y-type AC cable. Then connect the waveform module to the Connector board via 1" Y-Type AC cable. The DC
cables should remain connected.
3. Maintenance
Approximated lifetime of the relay on DCDM modules is 100,000 cycles. HBM and MM modules are less
sensitive to a small change of capacitance in the relay, and will work longer without changing it. Performance of
your waveform module should be monitored periodically, and, if necessary, the module should be sent back to ISI
for relay replacement or calibration. Follow calibration procedures to ensure performance of your ESD Stress
system.
There is a 100mA SLO-BLO fuse on the AC input.

EPS-100 Manual Integral Solutions Int’l
August 22, 2013
Page 6
4. Charge Device Model (CDM)
4.1 Mechanical Alignment
According to CDM standard, the head’s suspension must be grounded. In most cases suspension holder serves
that purpose, while in other, the suspension is pressed against CDM chassis by flex clamp.
Unlike HBM or MM modules, CDM cartridge requires the flex to be directly connected to the board. That is
why mechanical alignment of CDM cartridge may be counterintuitive. The pads on the flex must be facing the
board, so for some cases, the head will be mounted ABS side up. The head will still be kept horizontal (90°to the
transverse field).
F
Fi
ig
gu
ur
re
e
4
4-
-1
1
C
CD
DM
M
M
Me
ec
ch
ha
an
ni
ic
ca
al
l
A
Al
li
ig
gn
nm
me
en
nt
t
Up/Down head reconfiguration involves changing the flex guide and realigning the suspension holder.
Align the suspension holder so that the head’s flex is on the centerline of the CDM tooling and the lies on the 2(4)
pogo pins.
Usually ISI ships two flex guides for Up/Down heads: user needs to remove the two screws holding the
flex guide and change it. Head’s flex should always lie on the 2(4) pogo pins, on the centerline of CDM tooling. If
screws from the flex guide are missing the user should remove the pins and put them into different pinholes to match
head type.
CDM cartridge can support heater, but a special cable should be used (that connects to pins 3 and 4 of the Write
port on the 2xCartridge). Use "Static Test"."Aux Point Test" to measure resistance of the heater in ESD and non-
ESD configuration.
Note for 4-Pole magnet applications
On DCDM the flex is centered, but the suspension (and therefore HGA) is pivoted. This means there may be an
offset (top view) of both the UP and DN sliders, and each may be at an angle (mirror image top view). The offset
user can manually compensate by moving the magnet left or right. However, the angle will be an issue. For
Transverse testing this is no problem, assuming the MR itself is centered in the gap. But for rotating fields the head
will see different result than if the head was placed perpendicular into the gap.
So for Quad-Pole and HGA-only magnets user must ensure that the MR-element is within the uniform zone of
the magnet gap. Secondly, Transverse-only field is recommended if the suspension is at any angle to the magnet
other than 90degrees.
Suspension
Holder
Flex Guide
Flex Clamp

EPS-100 Manual Integral Solutions Int’l
August 22, 2013
Page 7
4.2 Monitoring Waveform
CDM waveform module charges the head to desired voltage and then grounds it, which creates a very fast
current transient from the charge accumulated on the head. The pulse is very fast with the rise time up to 500pS and
pulse width up to 1nS. The screenshot below is 5V CDM pulse, fired into a real head.
F
Fi
ig
gu
ur
re
e
4
4-
-2
2
M
Mo
on
ni
it
to
or
ri
in
ng
g
C
CD
DM
M
P
Pu
ul
ls
se
e
(
(f
fi
ir
re
ed
d
i
in
nt
to
o
r
re
ea
al
l
h
he
ea
ad
d)
)
The shape and amplitude of the pulse you see on the screenshot is
going to depend on the electrical properties (capacitance) of the head.
The CT-6 probe comes standard with CDM cartridge and should
be ready for monitoring the waveform. Simply connect the CT-6
current probe from CDM waveform module to the oscilloscope.
If CT-6 is not installed, we recommend sending it to ISI. If that is
not possible, here is the procedure on how to do it:
Separate the waveform module from the 2x cartridge, by
removing 4 screws that are not covered in black.
Fix the waveform module as shown on the picture (right).
Push the CT-6 probe through the opening on the bottom, up
towards the copper wire.
Unsolder the copper wire on the right end. Insert wire through the
CT-6 probe and re-solder.
Mount DCDM waveform module back on the cartridge.
F
Fi
ig
gu
ur
re
e
4
4-
-3
3
C
CD
DM
M
C
CT
T-
-6
6

EPS-100 Manual Integral Solutions Int’l
August 22, 2013
Page 8
4.3 ESD Standard
The standard shown here applies to pulses produced by ISI DCDM waveform modules and should treated as
such. The values should be used for verification of the CDM waveform module device with 5pF and 12pF
calibration capacitors.
-200
-100
0
100
200
300
-2
-1
0
1
2
3
4
5
6
Time (ns)
Current (mA)
t
r
t
d
I
p2
I
p3
I
P1
F
Fi
ig
gu
ur
re
e
4
4-
-4
4
C
CD
DM
M
S
St
ta
an
nd
da
ar
rd
d
1
1
Ip1 can be estimated as 11mA/V CDM for 5pF capacitor and 13mA/V CDM for 12pF at 10V CDM or higher.
The real peak current at lower voltages (such as 1V CDM) is around 8mA/V and 12mA/V for 5pF and 12pF
capacitors. Use the following table to verify performance of your CDM module.
Ip1 / CDM Voltage Nominal Minimum Maximum
5pF Calibration Capacitor
1 8.2 6.6 9.8
10 104.5 83.6 125.4
20 215.6 172.5 258.7
12pF Calibration Capacitor
1 10.4 8.3 12.5
10 130.9 104.7 157.0
20 268.2 214.6 321.8
Other parameters can be checked at 10V CDM:
Symbol 5pF 12pF
Rise Time (10% – 90% of Ip1) t
r
<0.5 ns <0.6 ns
Width at 50% of Ip1 t
d
700 ps 1000 ps
2
Max 2
nd
peak Ip
2
<50% Ip
1
<50% Ip
1
Max 3
rd
peak Ip
3
<25% Ip
1
<25% Ip
1
The values above were measured using LeCroy LC574A 1Ghz oscilloscope. We expect that faster oscilloscope
would show slightly higher amplitude and smaller pulse width.
1
Figure taken from Standardized Direct Charge Device ESD Test For Magneto resistive Recording Heads II.
Lydia Baril, Tim Cheung, Albert Wallash.
2
The waveform rise time and width is overall 5% higher at bar CDM then on 2xHGA, because calibration
capacitor is mounted in different location.

EPS-100 Manual Integral Solutions Int’l
August 22, 2013
Page 9
The following plot shows real 20V CDM discharge on 5pF calibration capacitor.
F
Fi
ig
gu
ur
re
e
4
4-
-5
5
C
CD
DM
M
W
Wa
av
ve
ef
fo
or
rm
m
(
(5
5p
pF
F
C
Ca
ap
pa
ac
ci
it
to
or
r)
)

EPS-100 Manual Integral Solutions Int’l
August 22, 2013
Page 10
4.4 Calibration
Use one of the calibration capacitors to verify the CDM waveform. Turn on the EPS-100. If running Quasi97
software then exit from it and run EPS-100 application. Also remove the CDM cartridge from the 2xHGA tooling.
To install a calibration board, remove the HGA flex clamp and flex guide for Up/Down Heads from the
cartridge. Pull out a pin from plastic base (where you put in the flex of HGA); the HGA clamp along with the spring
should come out. If flex guide is held by two screws then remove them and pull out the flex guide. If flex guide is
glued then remove the locating pins from it. You should have a cartridge with 2 or more uncovered pogo pins.
F
Fi
ig
gu
ur
re
e
4
4-
-6
6
C
CD
DM
M
C
Ca
ar
rt
tr
ri
id
dg
ge
e
C
Ca
al
li
ib
br
ra
at
ti
io
on
n
Put the calibration board on top of the pogo pins. The calibration capacitor board should reside on two reader
pogo pins and contact the CDM chassis on the sides. So when installing it make sure that the two MR pogo pins do
contact the metal portion of the disk capacitor and writer pins do not. There are two methods of locating the
calibration capacitor:
If there is a pinhole before pogo pin 1, insert the pin that you removed earlier in that hole through the calibration
board (use the pin to guide the calibration board to the proper location).
If a guide hole (or a pin) is not available then use an ohmmeter to locate the calibration board. To do that, restart
EPS-100 software; connect the ohmmeter to pins 1 and 2 of J2 connector, and continuously measure resistance
while moving the calibration capacitor until you get less than 1 Ohm. After that, check resistance between pins 2 and
3 to make sure that R+ and W- are not connected.
Put 2 screws with washers on two sides of the calibration board to hold it in place and to connect the topside of
the board with the CDM chassis. Fire a 1, 10 and 20V pulses and verify the amplitude, pulse width and rise time
against CDM standard.

EPS-100 Manual Integral Solutions Int’l
August 22, 2013
Page 11
BlazerX5 version of the CDM waveform module has pogopins on the other side of the board. For verification of
the waveform, the module has to be mounted on the support plate and the calibration disk should be mounted on a
shim, as shown on the picture below.
F
Fi
ig
gu
ur
re
e
4
4-
-7
7
B
Bl
la
az
ze
er
rX
X5
5
C
CD
DM
M
C
Ca
al
li
ib
br
ra
at
ti
io
on
n
1 CDM Waveform Module
2 Support Plate
9 Calibration Disk
10 Special Shim
12 Screw
13 Flat washer

EPS-100 Manual Integral Solutions Int’l
August 22, 2013
Page 12
4.5 CDM O eration
The following block diagram is provided for better understanding of the operation of the waveform module. It is
created to show the charge device model ESD standard. The actual waveform module circuit may be slightly
different.
F
Fi
ig
gu
ur
re
e
4
4-
-8
8
C
CD
DM
M
B
Bl
lo
oc
ck
k
D
Di
ia
ag
gr
ra
am
m
To fire pulse:
1) S1-UP, S2-DN, S3-UP
2) wait 100mS
3) S1-DN
To test:
1) S1-DN, S2-UP, S3-DN

EPS-100 Manual Integral Solutions Int’l
August 22, 2013
Page 13
5. Machine Model (MM)
5.1 Mechanical Alignment
MM cartridge does not require a special mechanical alignment. It connects to the board with pogo pins on the
cartridge through a short cable. The waveform module can be connected to only one head at a time. In the case
where cartridge has two pogo-pin boards for up and down heads, connect the cable from one or the other board to
the waveform module.
F
Fi
ig
gu
ur
re
e
5
5-
-1
1
M
MM
M
/
/
H
HB
BM
M
M
Me
ec
ch
ha
an
ni
ic
ca
al
l
A
Al
li
ig
gn
nm
me
en
nt
t
To switch from MM to HBM, simply remove the two screws on the topside of the waveform module and
disconnect three cables from it (EPS-100 cable, QST and pogo-pin board connection). The waveform module should
come off and you can install another one (HBM or MM) in its place.
On 2xHGA Gen2 HBM/MM ESD cartridges do support heater testing (the aux bias current goes though the DC
cables). Use "Static Test"."Aux Point Test" to measure resistance of the heater in ESD and non-ESD configuration.

EPS-100 Manual Integral Solutions Int’l
August 22, 2013
Page 14
5.2 Monitoring Waveform
To monitor current going through the head install a CT-1 probe on the wire going from J4 Pin2 on the cartridge-
style waveform module to the FIC board. For the box-style modules mount CT-1 on the wire going from pin2 of
“HEAD” connector on waveform module.
F
Fi
ig
gu
ur
re
e
5
5-
-2
2
M
Mo
on
ni
it
to
or
ri
in
ng
g
M
MM
M
P
Pu
ul
ls
se
e
The following screenshot shows a 10V discharge into 500Ohm resistor.
F
Fi
ig
gu
ur
re
e
5
5-
-3
3
M
MM
M
5
50
00
0Ω
Ω
D
Di
is
sc
ch
ha
ar
rg
ge
e

EPS-100 Manual Integral Solutions Int’l
August 22, 2013
Page 15
5.3 ESD Standard
Machine Model charges a 200pF capacitor and fires the accumulated charge into the head. The standard shown
here applies to pulses produced by ISI MM waveform modules and should treated as such.
Voltage Level (V) 10
Positive I
PEAK
for Short, I
PS1
(mA) 150 – 200
Current at 100ns for 500
Ω
I
100
(mA) 7.25 +/- 20%
Maximum Positive I
PEAK
for 500
Ω
I
PR
(mA) I
100
* 4.5
Maximum Ringing Current, I
R
(mA) I
PS1
* 30%
Resonance Frequency for Short, FR (1/t
fr
) (MHz) 11–15
F
Fi
ig
gu
ur
re
e
5
5-
-4
4
S
Sh
ho
or
rt
t
a
an
nd
d
5
50
00
0Ω
Ω
M
MM
M
S
St
ta
an
nd
da
ar
rd
d
3
3
3
Figure Taken from EIA/JEDEC Standard. Test Method A115-A. Electrostatic Discharge Sensitivity Testing
Machine Model (HBM). Revision EIA/JESD22-A115.

EPS-100 Manual Integral Solutions Int’l
August 22, 2013
Page 16
5.4 Calibration
To verify calibration of the machine module, mount a CT-1 probe to monitor the ESD pulse. Connect a 0Ω
resistor instead of the head and fire a 10V pulse. Verify the peak amplitude and ringing frequency against that in the
MM spec. Connect a 500Ωresistor and fire a 10V pulse. Check that amplitude and current at 100nS conforms to
Machine Module specification.
F
Fi
ig
gu
ur
re
e
5
5-
-5
5
N
Ne
ew
w-
-S
St
ty
yl
le
e
M
MM
M-
-H
HB
BM
M
C
Ca
al
li
ib
br
ra
at
ti
io
on
n
The picture above shows the cartridge-style machine module prepared for calibration. See HBM calibration for
a picture of box-style waveform module calibration. Note that the same ESD waveform specification applies to both
cartridge and box – style MM.
F
Fi
ig
gu
ur
re
e
5
5-
-6
6
M
MM
M
1
10
0V
V
D
Di
is
sc
ch
ha
ar
rg
ge
e
i
in
nt
to
o
a
a
0
0O
Oh
hm
m
R
Re
es
si
is
st
to
or
r

EPS-100 Manual Integral Solutions Int’l
August 22, 2013
Page 17
5.5 MM O eration
The following block diagram is provided for better understanding of the operation of the waveform module. It is
created to show the machine model ESD standard. The actual waveform module circuit may be slightly different.
F
Fi
ig
gu
ur
re
e
5
5-
-7
7
M
MM
M
B
Bl
lo
oc
ck
k
D
Di
ia
ag
gr
ra
am
m
To fire pulse:
1) S2-Right, S1-Right, S3-Up
2) wait 100mS
3) S2-Left
To test device:
1) S3-DN

EPS-100 Manual Integral Solutions Int’l
August 22, 2013
Page 18
6. H man Body Model (HBM)
6.1 Monitoring Waveform
Capturing the waveform of HBM pulse requires the same setup as on Machine Model. To monitor current going
through the head install a CT-1 probe on the wire going from J4 Pin2 on the cartridge-style waveform module to the
FIC board. For the box-style modules mount CT-1 on the wire going from pin2 of “HEAD” connector on waveform
module.
F
Fi
ig
gu
ur
re
e
6
6-
-1
1
M
Mo
on
ni
it
to
or
ri
in
ng
g
H
HB
BM
M
P
Pu
ul
ls
se
e
HBM/MM ESD catridge do support heater testing (the aux bias current goes though the DC cables). Use "Static
Test"."Aux Point Test" to measure resistance of the heater in ESD and non-ESD configuration
F
Fi
ig
gu
ur
re
e
6
6-
-2
2
H
HB
BM
M
5
50
0V
V
w
wi
it
th
h
5
50
00
0O
Oh
hm
m
R
Re
es
si
is
st
to
or
r

EPS-100 Manual Integral Solutions Int’l
August 22, 2013
Page 19
6.2 ESD Standard
Human Body Model charges 100pF capacitor and fires accumulated charge through the 1500Ωresistor into the
head. The standard shown here applies to pulses produced by ISI HBM waveform modules and should treated as
such.
Voltage Level (V) 7 50
I
P0
Ω
(MR) for Short (mA) 4.2 – 5.15 30 – 36.7
I
P500
Ω
(MR) for 500
Ω
(mA) 2.63 – 4.2 18.75 – 30
V
PEAK
(on R1)
4
for Short
(I
PEAK
*1500/1000) (V) 6.3 – 7.7 45 – 55
V
PEAK
(on R1) for 500
Ω
(I
PEAK
*(1500+500)/1000) (V) 5.25 – 8.4 37.5 – 60
Rise Time for Short (t
r
) (nS) 2 – 10
Rise Time for 500
Ω
(nS) 5 – 25
Decay Time for Short (t
d
) (nS) 130 – 170
Decay Time for 500
Ω
(nS) 160 – 240
Ringing Current (I
R
) (mA) 15% of I
PS
F
Fi
ig
gu
ur
re
e
6
6-
-3
3
S
Sh
ho
or
rt
t
a
an
nd
d
5
50
00
0O
Oh
hm
m
H
HB
BM
M
S
St
ta
an
nd
da
ar
rd
d
5
5
4
R1 is 1500ΩResistor in series with the MR head inside the HBM waveform Module. Vpeak is directly
proportional to Ipeak, and the formula can be used to calculate real HBM voltage applied.
5
Figure Taken from EIA/JEDEC Standard. Test Method A114-A. Electrostatic Discharge Sensitivity Testing
Human Body Model (HBM). Revision EIA/JESD22-A114.

EPS-100 Manual Integral Solutions Int’l
August 22, 2013
Page 20
6.3 Calibration
To verify calibration of the human body module, mount a CT-1 probe to monitor the ESD pulse. Connect a 0Ω
resistor instead of the head and fire a 7V and 50V pulse. Verify the peak amplitude, rise and decay times against the
HBM spec. Connect a 500Ωresistor and fire a 7 and 50V pulses. Verify the waveform characteristics with the spec.
F
Fi
ig
gu
ur
re
e
6
6-
-4
4
O
Ol
ld
d-
-S
St
ty
yl
le
e
M
MM
M-
-H
HB
BM
M
C
Ca
al
li
ib
br
ra
at
ti
io
on
n
The screenshot above shows the box-style HBM prepared for calibration. See MM calibration for screenshot of
cartridge-style waveform module calibration. Note that the same ESD waveform specification applies to both box
and cartridge – style HBM.
F
Fi
ig
gu
ur
re
e
6
6-
-5
5
R
Re
ea
al
l
H
HB
BM
M
D
Di
is
sc
ch
ha
ar
rg
ge
e
o
on
n
0
0O
Oh
hm
m
r
re
es
si
is
st
to
or
r
Table of contents
Popular Computer Hardware manuals by other brands
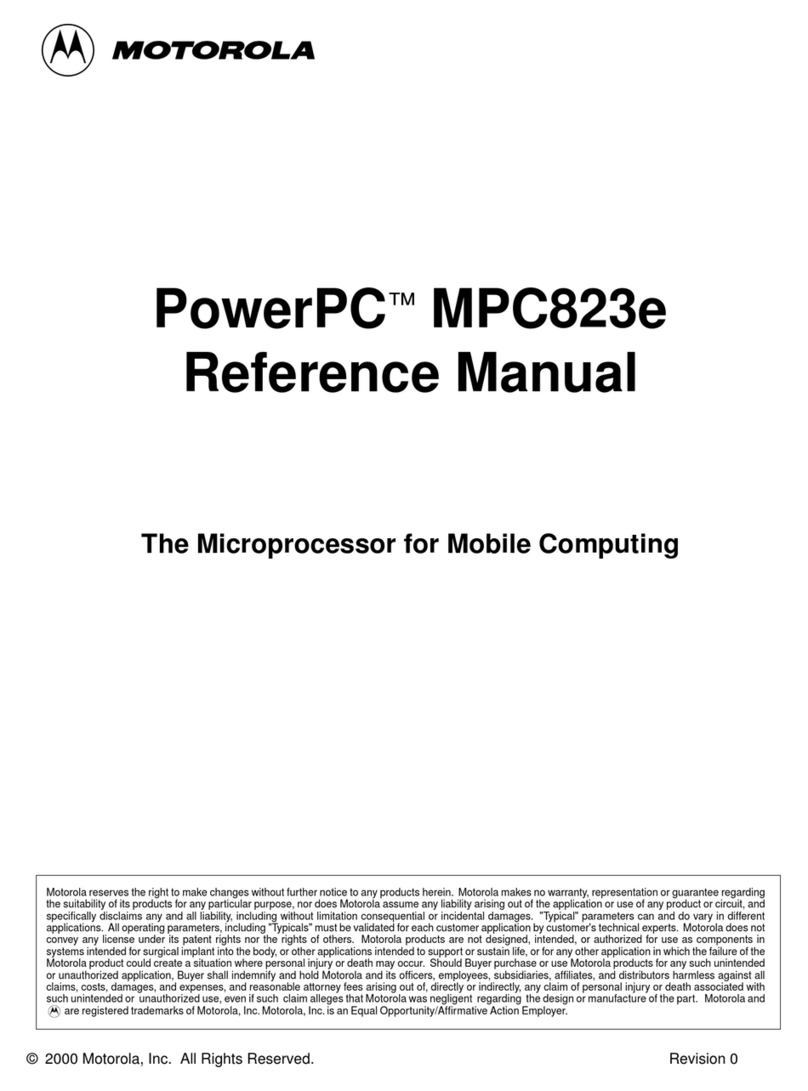
Motorola
Motorola MPC823e Reference manual
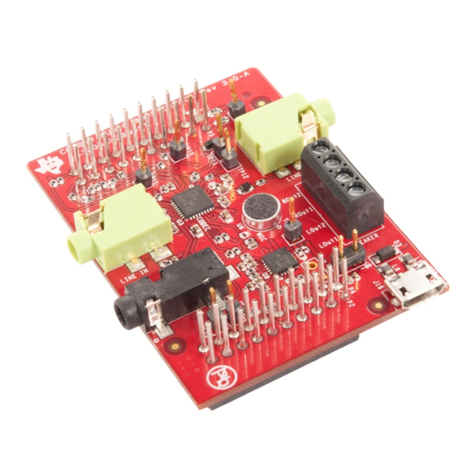
Texas Instruments
Texas Instruments SimpleLink CC3200 Wi-Fi user guide
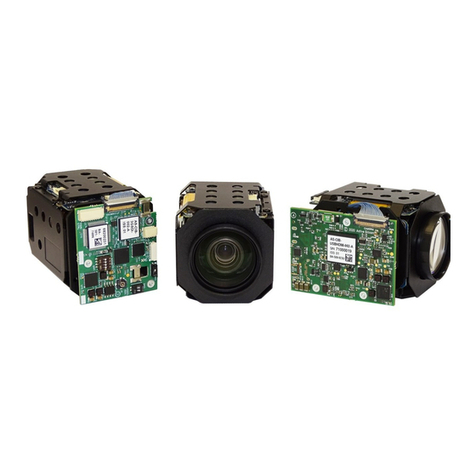
Active Silicon
Active Silicon AS-CIB-3GSDI-002-EVAL-B quick start guide
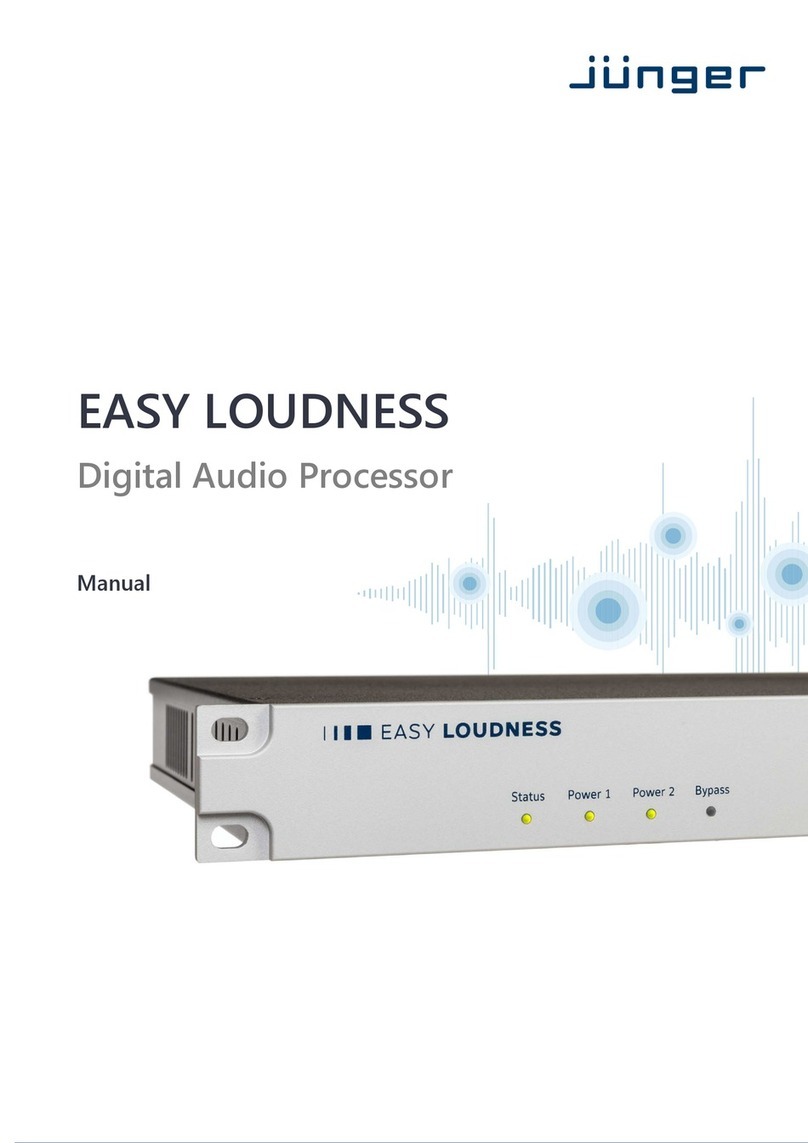
junger
junger EASY LOUDNESS manual

Albatron
Albatron MBFastTrak133 "Lite" user manual
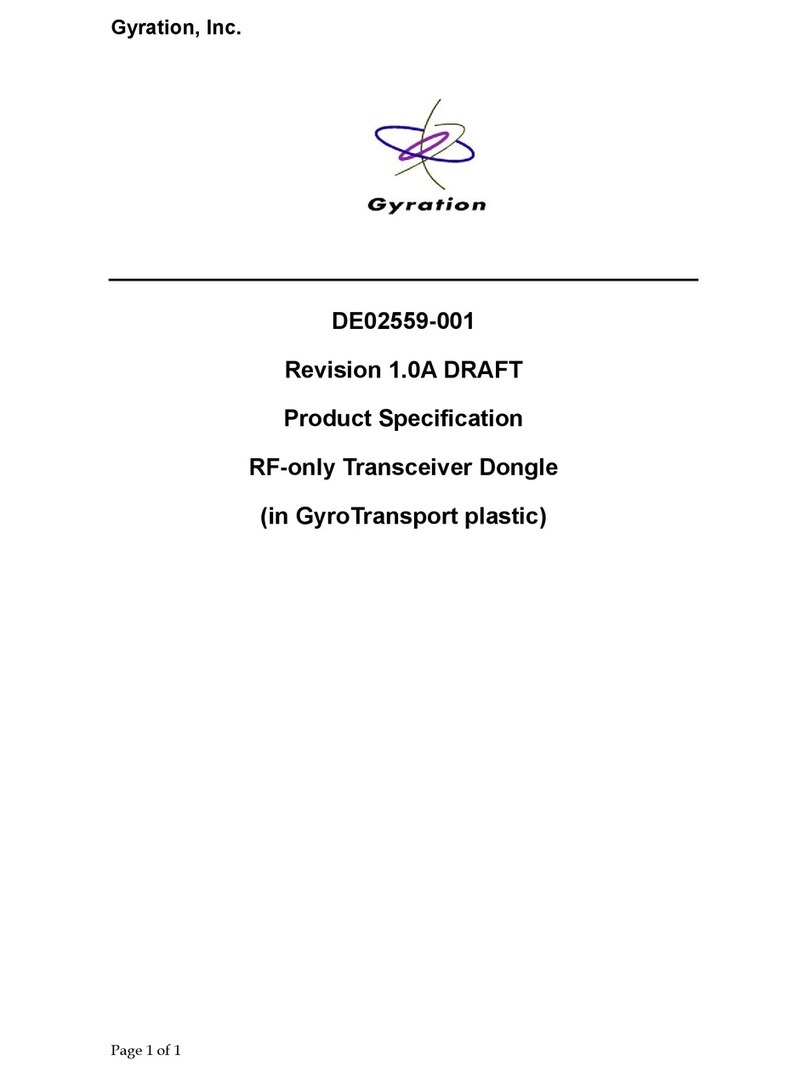
Gyration
Gyration DE02559-001 Product specification