INTORQ BFK455-25 Quick guide

INTORQ BFK455-25
Spring-applied brake with electromagnetic release
Translation of the Original Operating Instructions
setting the standard
www.intorq.com

Document history
Material number Version Description
33008102 1.0 07/2019 SC First edition
Legal regulations
Liability
¾
The information, data and notes in these Operating Instructions are up to date at the time of printing.
Claims referring to drive systems which have already been supplied cannot be derived from this in-
formation, illustrations and descriptions.
¾
We do not accept any liability for damage and operating interference caused by:
– inappropriate use
– unauthorised modifications to the product
– improper work on or with the drive system
– operating errors
– disregarding the documentation
Warranty
Notice
The warranty conditions can be found in the terms of sale and delivery from INTORQ
GmbH & Co. KG.
¾
Warranty claims must be made to INTORQ immediately after the defects or faults are detected.
¾
The warranty is void in all cases when liability claims cannot be made.
INTORQ | BA 14.0215 | 07/2019 2

Spring-applied brakes of type BFK455-25
Version without hand-release Version with hand-release
Product key
Product group: Brakes
Product family: Spring-applied brake
Type: 455
Size: 25
INTORQ B FK
Not coded: Connection voltage, hub bore hole, options
Checking the delivery
After receipt of the delivery, check immediately whether the items delivered match the accompanying pa-
pers.
INTORQ does not accept any liability for deficiencies claimed subsequently.
¾
Claim visible transport damage immediately to the deliverer.
¾
Claim visible deficiencies or incomplete deliveries immediately to INTORQ GmbH & Co. KG.
INTORQ | BA 14.0215 | 07/2019 3

Contents
Spring-applied brakes of type BFK455-25............................................................................................................... 3
1 General information................................................................................................................................................... 6
1.1 Using these Operating Instructions ...................................................................................................................... 6
1.2 Conventions in use............................................................................................................................................... 6
1.3 Safety instructions and notices ............................................................................................................................ 6
1.4 Terminology used................................................................................................................................................. 7
1.5 Abbreviations used............................................................................................................................................... 8
2 Safety instructions................................................................................................................................................... 10
2.1 General safety instructions................................................................................................................................. 10
2.2 Disposal ............................................................................................................................................................. 10
3 Product description ................................................................................................................................................. 11
3.1 Proper and intended usage................................................................................................................................ 11
3.1.1 Standard applications ............................................................................................................................ 11
3.2 Layout ................................................................................................................................................................ 11
3.2.1 Basic module ......................................................................................................................................... 12
3.3 Function ............................................................................................................................................................. 12
3.4 Braking and release ........................................................................................................................................... 13
3.5 Release monitoring ............................................................................................................................................ 13
3.6 Project planning notes........................................................................................................................................ 13
3.7 Optional configuration ........................................................................................................................................ 13
3.7.1 Hand-release (optional) ......................................................................................................................... 13
3.7.2 Optional encapsulated design ............................................................................................................... 13
4 Technical specifications.......................................................................................................................................... 14
4.1 Possible applications of the INTORQ spring-applied brake ............................................................................... 14
4.2 Rated data.......................................................................................................................................................... 14
4.3 Switching times .................................................................................................................................................. 16
4.4 Friction work / operating frequency .................................................................................................................... 18
4.5 Electromagnetic compatibility............................................................................................................................. 19
4.6 Emissions........................................................................................................................................................... 19
4.7 Labels on product............................................................................................................................................... 20
INTORQ | BA 14.0215 | 07/2019 4

5 Mechanical installation............................................................................................................................................ 22
5.1 Design of end shield and shaft........................................................................................................................... 22
5.2 Tools .................................................................................................................................................................. 23
5.3 Preparing the installation.................................................................................................................................... 23
5.4 Installing the hub onto the shaft ......................................................................................................................... 24
5.5 Brake mounting .................................................................................................................................................. 25
5.6 Cover ring assembly .......................................................................................................................................... 30
5.7 Mounting the hand-release (retrofitting) ............................................................................................................. 31
6 Electrical installation ............................................................................................................................................... 37
6.1 Electrical connection .......................................................................................................................................... 38
6.2 Bridge/half-wave rectifier (optional).................................................................................................................... 39
6.2.1 Assignment: Bridge/half-wave rectifier – brake size.............................................................................. 39
6.2.2 Technical specifications......................................................................................................................... 40
6.2.3 Permissible current load at ambient temperature.................................................................................. 40
7 Commissioning and operation ............................................................................................................................... 41
7.1 Function checks before initial commissioning .................................................................................................... 41
7.1.1 Brake with micro-switch......................................................................................................................... 41
7.2 Commissioning................................................................................................................................................... 42
7.3 During operation................................................................................................................................................. 42
8 Maintenance and repair........................................................................................................................................... 43
8.1 Wear of spring-applied brakes ........................................................................................................................... 43
8.2 Inspections ......................................................................................................................................................... 44
8.2.1 Maintenance intervals............................................................................................................................ 44
8.3 Maintenance....................................................................................................................................................... 44
8.3.1 Release / voltage................................................................................................................................... 45
8.3.2 Checking the air gap.............................................................................................................................. 45
8.3.3 Checking the rotor thickness ................................................................................................................. 46
8.3.4 Replacing the rotor ................................................................................................................................ 46
8.4 Spare parts list ................................................................................................................................................... 47
9 Troubleshooting and fault elimination................................................................................................................... 48
INTORQ | BA 14.0215 | 07/2019 5

General information
INTORQ | BA 14.0215 | 07/2019 6
1 General information
1.1 Using these Operating Instructions
¾
These Operating Instructions will help you to work safely with the spring-applied brake with electro-
magnetic release. They contain safety instructions that must be followed.
¾
All persons working on or with electromagnetically released spring-applied brakes must have the Oper-
ating Instructions available and observe the information and notes relevant for them.
¾
The Operating Instructions must always be in a complete and perfectly readable condition.
1.2 Conventions in use
This document uses the following styles to distinguish between different types of information:
Spelling of numbers Decimal separator Point The decimal point is always used. For ex-
ample: 1234.56
Page reference Underscore, orange _____
Reference to another page with additional
information
For example: Conventions in use,Page6
Symbols
Wildcard □
Wildcard (placeholder) for options or selec-
tion details
For example: BFK455-25-□□ =
BFK455-25-10
Notice Important notice about ensuring smooth op-
erations or other key information.
1.3 Safety instructions and notices
The following icons and signal words are used in this document to indicate dangers and important safety
information:

General information
INTORQ | BA 14.0215 | 07/2019 7
Structure of safety notices:
CAUTION
Icon
Indicates the type of danger
Signal word
Characterizes the type and severity of danger.
Notice text
Describes the danger.
Possible causes
List of possible consequences if the safety notices are disregarded.
Protective measures
List of protective measures required to avoid the danger.
Danger level
DANGER
DANGER indicates a hazardous situation which, if not avoided, will result in death or seri-
ous injury.
WARNING
WARNING indicates a potentially hazardous situation which, if not avoided, could result in
death or serious injury.
CAUTION
CAUTION indicates a hazardous situation which, if not avoided, could result in minor or
moderate injury.
NOTICE
Notice about a harmful situation with possible consequences: the product itself or sur-
rounding objects could be damaged.
1.4 Terminology used
Term In the following text used for
Spring-applied brake Spring-applied brake with electromagnetic release
Drive system Drive systems with spring-applied brakes and other drive com-
ponents

General information
INTORQ | BA 14.0215 | 07/2019 8
1.5 Abbreviations used
Letter symbol Unit Designation
FRN Rated frictional force
I A Current
IHA Holding current, at 20 °C and holding voltage
ILA Release current, at 20 °C and release voltage
INA Rated current, at 20 °C and rated voltage
MANm Tightening torque of fastening screws
Mdyn Nm Braking torque at a constant speed of rotation
MKNm Rated torque of the brake, rated value at a relative speed of rotation of 100
rpm
nmax rpm Maximum occurring speed of rotation during the slipping time t3
PHW Coil power during holding, after voltage change-over and 20 °C
PLW Coil power during release, before voltage change-over and 20 °C
PNW Rated coil power, at rated voltage and 20 °C
Q J Quantity of heat/energy
QEJMax. permissible friction energy for one-time switching, thermal parameter of
the brake
QRJ Braking energy, friction energy
QSmax JMaximally permissible friction energy for cyclic switching, depending on the
operating frequency
RmN/mm2Tensile strength
RNOhms Rated coil resistance at 20 °C
Rzμm Averaged surface roughness
Sh1/h Operating frequency: the number of switching operations evenly spread over
the time unit
Shue 1/h Transition operating frequency, thermal parameter of the brake
Shmax 1/h Maximum permissible operating frequency, depending on the friction energy
per switching operation
sLmm Air gap: the lift of the armature plate while the brake is switched
sLN mm Rated air gap
sLmin mm Minimum air gap
sLmax mm Maximum air gap
sHL mm Air gap for hand-release
t1ms Engagement time, sum of the delay time and braking torque: rise time t1 = t11
+ t12
t2ms Disengagement time, time from switching the stator until reaching 0.1 MK

General information
INTORQ | BA 14.0215 | 07/2019 9
Letter symbol Unit Designation
t3ms Slipping time, operation time of the brake (according to t11) until standstill
t11 ms Delay during engagement (time from switching off the supply voltage to the
beginning of the torque rise)
t12 ms Rise time of the braking torque, time from the start of torque rise until reach-
ing the braking torque
tue s Overexcitation period
U V Voltage
UHV DC Holding voltage, after voltage change-over
ULV DC Release voltage, before voltage change-over
UNV DC Rated coil voltage; in the case of brakes requiring a voltage change-over, UN
equals UL

Safety instructions
INTORQ | BA 14.0215 | 07/2019 10
2 Safety instructions
2.1 General safety instructions
¾
Never operate INTORQ components when you notice they are damaged.
¾
Never make any technical changes to INTORQ components.
¾
Never operate INTORQ components when they are incompletely mounted or incompletely connected.
¾
Never operate INTORQ components without their required covers.
¾
Only use accessories that have been approved by INTORQ.
¾
Only use original spare parts from the manufacturer.
Keep the following in mind during the initial commissioning and during operation:
¾
Depending on the degree of protection, INTORQ components may have both live (voltage carrying),
moving and rotating parts. Such components require the appropriate safety mechanisms.
¾
Surfaces can become hot during operation. Take the appropriate safety measures (to ensure contact/
touch protection).
¾
Follow all specifications and information found in the Operating Instructions and the corresponding
documentation. These must be followed to maintain safe, trouble-free operations and to achieve the
specified product characteristics.
¾
The installation, maintenance and operation of INTORQ components may only be carried out by quali-
fied personnel. According to IEC 60364 and CENELEC HD 384, skilled personnel must be qualified in
the following areas:
– Familiarity and experience with the installation, assembly, commissioning and operation of the
product.
– Specialist qualifications for the specific field of activity.
– Skilled personnel must know and apply all regulations for the prevention of accidents, directives,
and laws relevant on site.
2.2 Disposal
The INTORQ components are made of various differing materials.
¾
Recycle metals and plastics.
¾
Ensure professional disposal of assembled PCBs according to the applicable environmental regula-
tions.

Product description
INTORQ | BA 14.0215 | 07/2019 11
3 Product description
3.1 Proper and intended usage
3.1.1 Standard applications
INTORQ components are intended for use in machinery and facilities. They may only be used for pur-
poses as specified in the order and confirmed by INTORQ. The INTORQ components may only be oper-
ated under the conditions specified in these Operating Instructions. They may never be operated beyond
their specified performance limits. The technical specifications (refer to Technical specifica-
tions,Page14) must be followed to comply with the proper and intended usage. Any other usage is con-
sider improper and prohibited.
3.2 Layout
The BFK455-25 spring-applied brake is a double-disc brake with four friction surfaces. The braking torque
is applied through two separate braking circuits, both electrical and mechanical, via several compression
springs in the form of friction locking. The brake circuits are released electromagnetically. Due to its divi-
sion into two brake circuits, the brake is particularly suitable for applications such as lift systems and
stage/platform technology. The brake can be selected based on the rated torque for one brake circuit. The
second brake circuit meets the requirement for redundancy (refer to Rated data for coil power,Page15).
The division of the brake circuits is done using two separate armature plates with their corresponding com-
pression springs and electromagnetic coils. Each brake circuit can be operated individually due to the sep-
arate supply lines for each stator and armature plate (siehe Switching suggestions for the
BFK455-25,Page38).
Each brake circuit has a micro-switch which monitors the switching state of the spring-applied brake. Us-
ing the associated switching device, the supply voltage (AC voltage) is rectified and, when the brake is re-
leased, lowered after a short period of time. This results in a reduction of the average electrical power of
the brake.
The stator is designed to comply with heat class F. The limit temperature of the coils is 155 °C. The
BFK455-25 spring-applied brake is designed for a maximum duty cycle of 60 % with holding current reduc-
tion.
Size Rated torque
[Nm]
EC-type examination certificate
Directive 2014/33/EC
25
2 x 800
EU-BD 10772 x 1200
2 x 1500

Product description
INTORQ | BA 14.0215 | 07/2019 12
3.2.1 Basic module
Fig.1: Design of a BFK455-25 spring-applied brake
ATappet BArmature plate CComplete rotor
DFlange EGear teeth FCompression springs
GCoil
3.3 Function
This brake is an electrically releasable spring-applied brake with two rotating brake discs (rotors) that are
equipped on both sides with friction linings. In its de-energized state, the rotor is clamped with braking
force applied by pressure springs between the armature plate and a counter friction surface. This corres-
ponds to a fail-safe functionality.
The brake torque applied to the rotor is transferred to the input shaft via a hub that has axial gear teeth.
The brake can be used as a holding brake, as an operating brake, and as an emergency stop brake for
high speeds.
The asbestos-free friction linings ensure a safe braking torque and low wear.

Product description
INTORQ | BA 14.0215 | 07/2019 13
3.4 Braking and release
During the braking procedure, the inner and outer springs use the armature plate to press the rotor (which
can be shifted axially on the hub) against the friction surface. The asbestos-free friction linings ensure high
braking torque and low wear. The braking torque is transmitted between the hub and the rotor via gear
teeth.
When the brakes are applied, an air gap (sL) is present between the stator and the armature plate. To re-
lease the brake, the coil of the stator is energised with the DC voltage provided. The resulting magnetic
flux works against the spring force to draw the armature plate to the stator. This releases the rotor from the
spring force and allows it to rotate freely.
3.5 Release monitoring
The spring-applied brake has a micro-switch for each braking circuit to monitor the switching state. When
the brake is released, the micro-switches toggle. This means that it is possible to prevent the drive from
being operated when the brake is closed. The micro-switches can be connected as both normally open
and also normally closed.
To check that the micro-switches function correctly, we recommend testing the switching status (refer to
table 6) in both the released and applied braking states.
3.6 Project planning notes
¾
When designing a brake for specific applications, torque tolerances, the limiting speeds of the rotors,
the thermal resistance of the brake, and the effect of environmental influences must all be taken into
account.
¾
The brakes are dimensioned in such a way that the specified rated torques are reached safely after a
short run-in process.
¾
However, as the organic friction linings used do not all have identical properties and because environ-
mental conditions can vary, deviations from the specified braking torques are possible. These must be
taken into account in the form of appropriate dimensioning tolerances. Increased breakaway torque is
common in particular after long downtimes in humid environments where temperatures vary.
¾
If the brake is used as a pure holding brake without dynamic load, the friction lining must be reactiv-
ated regularly.
3.7 Optional configuration
3.7.1 Hand-release (optional)
To temporarily release the brake when there is no electricity available, a hand-release function is available
as an option. The hand-release function can be retrofitted.
3.7.2 Optional encapsulated design
This design not only prevents the penetration of spray water and dust, but also the spreading of abrasion
particles outside the brake. This is achieved by the following enclosures:
¾
A cover ring over the armature plate and rotor.

Technical specifications
INTORQ | BA 14.0215 | 07/2019 14
4 Technical specifications
4.1 Possible applications of the INTORQ spring-applied brake
¾
Degree of protection:
– The brake is designed for operation under the environmental conditions that apply to IP54 protec-
tion. Because of the numerous possibilities of using the brake, it is still necessary to check the func-
tionality of all mechanical components under the corresponding operating conditions.
¾
Ambient temperature:
– -20 °C to +40 °C (Standard)
¾
Humidity: no restrictions
– In the event of condensation or moisture formation: provide for appropriate ventilation of the brakes
to ensure that the friction pairs will dry quickly.
¾
Ambient temperature:
– -5 °C to +40 °C
¾
At high humidity and low temperature:
– Take the steps necessary to protect the armature plate and rotor from freezing.
¾
Protect the electrical connections against any contact or touching.
4.2 Rated data
s
LN
s
LN
Fig.2: Dimensions
Size Rated torque Air gap Permissible
wear distance
Rotor thickness Mass per
stator
sLN
+0.22/-0.02 sLmax Min. Max. m
[Nm] [mm] [mm] [mm] [mm] [mm] [kg]
25
2 x 800
0.3 0.6 0.3 12.7 13 352 x 1200
2 x 1500
Tab.1: Rated data for air gap specifications

Technical specifications
INTORQ | BA 14.0215 | 07/2019 15
Size Screw hole circle Fastening screws DIN 912 Minimum thread depth Tightening torque
MA
Diameter Thread without
flange
with flange without
flange
with
flange1)
without
flange
with
flange1)
[mm] [mm] [mm] [mm] [mm] [Nm] [Nm]
25 282 M12 6 x M12x190 6 x M12x200 25 22.5 105 105
Tab.2: Rated data: screw kit for brake assembly onto flange
1) Flange only permissible for max. 2 x 1000 Nm
CAUTION
¾
The screws for the different brake attachment variants have different strength grades
and may have special surface coatings. In order to guarantee a secure screw connec-
tion, use ONLY the proper screws from INTORQ!
¾
It is very important to comply with the minimum thread depth of the end shield (refer to
Rated data: screw kit for brake assembly onto flange,Page15).
¾
If the required thread depth is not maintained, the fastening screws may run onto the
root. This has the effect that the required pre-load force is no longer established. The
brake is no longer securely fastened!
Size Voltage Power Coil resistance Current
Release ±10% Hold ±10% Brake release Brake hold
ULUHPNPHRN
±5% IL
[V DC] [V DC] [W] [W] [Ω] [A]
25
160 80 2 x 236 2 x 59 2 x 108.5 2 x 1.48
205 103 2 x 178.1 2 x 1.15
2 x 425 2 x 106 2 x 98.9 2 x 2.07
Tab.3: Rated data for coil power

Technical specifications
INTORQ | BA 14.0215 | 07/2019 16
4.3 Switching times
The switching times listed here are guide values which apply to DC switching with rated air gap sLN, warm
coil and standard characteristic torque. The switching times given are mean values and subject to vari-
ations. The engagement time t1 is approximately 5 times longer for AC switching.
t
t
M
t2
t12
t11
t1
Mdyn
U
0.1Mdyn
Fig.3: Operating/switching times of the spring-applied brakes
t1Engagement time t11 Delay time during engagement
t2Disengagement time (up to M = 0.1 Mdyn)t12 Rise time of the brake torque
Mdyn Braking torque at a constant speed of rotation UVoltage
Size Rated
torque
Max.
perm.
switch-
ing en-
ergy
Transitional
operating
frequency
Switching times Max.
speed
Engaging Disengaging
MKQEShue t10
1) t90
1) t11.AC
2) t1.AC
2) t2ab@sLN
3) t2ab@sLmax
3) nmax
5)
[Nm] [J] [1/h] [ms] [ms] [ms] [ms] [ms] [ms] [rpm]
25
2 x 800
240000 7.5 0.085 0.250 0.400 1.400 0.288 0.480 1150
2 x 1200 0.360 0.600 600
2 x 1500 0.068 0.181 0.330 1.155 0.240 0.400
Tab.4: Switching energy - operating frequency - switching times
1) Switching times according to type examination certificate are based on the rated torque t50 = (t10 + t90) / 2
2) Switching times refer to steady braking torque.
3) Venting times under unfavorable conditions (240 switching operations per hour, 60% DC, 40 °C ambient temperature)
4) Brake supplied with overexcitation (release voltage / holding voltage = 2 / 1)
5) Max. speed according to type examination certificate (for higher speeds, please first contact the manufacturer)

Technical specifications
INTORQ | BA 14.0215 | 07/2019 17
Engagement time
The transition from a brake-torque-free state to a holding-braking torque is not free of time lags.
For emergency braking, short engagement times for the brake are absolutely essential. The DC-side
switching in connection with a suitable spark suppressor must therefore be provided.
NOTICE
Connect the spark suppressors in parallel to the contact. If this is not admissible for safety
reasons (e.g. with hoists and lifts), the spark suppressor can also be connected in parallel
to the brake coil.
¾
If the drive system is operated with a frequency inverter so that the brake will not be de-energized be-
fore the motor is at standstill, AC switching is also possible (not applicable to emergency braking).
¾
The specified engagement times are valid for DC switching with a spark suppressor.
– Circuit proposals: refer to DC switching at mains – fast engagement.
Notice
Spark suppressors are available for the rated voltages.
Disengagement time
The disengagement time is the same for DC-side and AC-side switching. The specified disengagement
times always refer to control using INTORQ rectifiers and rated voltage.

Technical specifications
INTORQ | BA 14.0215 | 07/2019 18
4.4 Friction work / operating frequency
Friction work Q [J]
R
Operating frequency Sh[h ]
-1
Fig.4: Friction work as a function of the operating frequency
The permissible operating frequency Shmax depends on the amount of heat QR (refer to Figure Friction
work / operating frequency,Page18). At a pre-set operating frequency Sh, the permissible amount of
heat is QSmax.
Notice
With high speeds of rotation and switching energy, the wear increases strongly, because very
high temperatures occur at the friction surfaces for a short time.

Technical specifications
INTORQ | BA 14.0215 | 07/2019 19
4.5 Electromagnetic compatibility
Notice
The user must ensure compliance with EMC Directive 2014/30/EC using appropriate controls
and switching devices.
NOTICE
If an INTORQ rectifier is used for the DC switching of the spring-applied brake and if the
operating frequency exceeds five switching operations per minute, the use of a mains filter
is required.
If the spring-applied brake uses a rectifier of another manufacturer for the switching, it
may become necessary to connect a spark suppressor in parallel with the AC voltage.
Spark suppressors are available on request, depending on the coil voltage.
4.6 Emissions
Heat
Since the brake converts kinetic energy as well as mechanical and electrical energy into heat, the surface
temperature varies considerably, depending on the operating conditions and possible heat dissipation. Un-
der unfavourable conditions, the surface temperature can reach 130 °C.
Noise
The loudness of the switching noise during engaging and disengaging depends on the air gap "sL" and the
brake size.
Depending on the natural oscillation after installation, operating conditions and the state of the friction sur-
faces, the brake may squeak during braking.
Others
The abrasion of the friction parts produces dust.

Technical specifications
INTORQ | BA 14.0215 | 07/2019 20
4.7 Labels on product
There is a packaging label on the package. The name plate is glued to the outer surface of the brake.
Fig.5: Packaging label
INTORQ Manufacturer
33006670 ID number
BFK455-25 Type (refer to Product key,Page3 )
Bar code
SPRING-APPLIED BRAKE Designation of the product family
205/205 V DC Rated voltages of both braking circuits
1500/1500 NM Rated torque
Pieces Qty. per box
425/425 W Rated powers for both braking circuits
26.04.18 Packaging date
Anti-rust packaging: keep friction surface free of
grease! Addition
CE mark
Fig.6: Name plate (example)
INTORQ Manufacturer
BFK455-25 Type (refer to Product key,Page3 )
205/205 V DC Rated voltages of both braking circuits
425/425 W Rated powers for both braking circuits
No. 33006670 ID number
1500/1500 NM Rated torque
26.04.18 Date of manufacture
CE mark
Table of contents
Other INTORQ Spring Applied Brake manuals
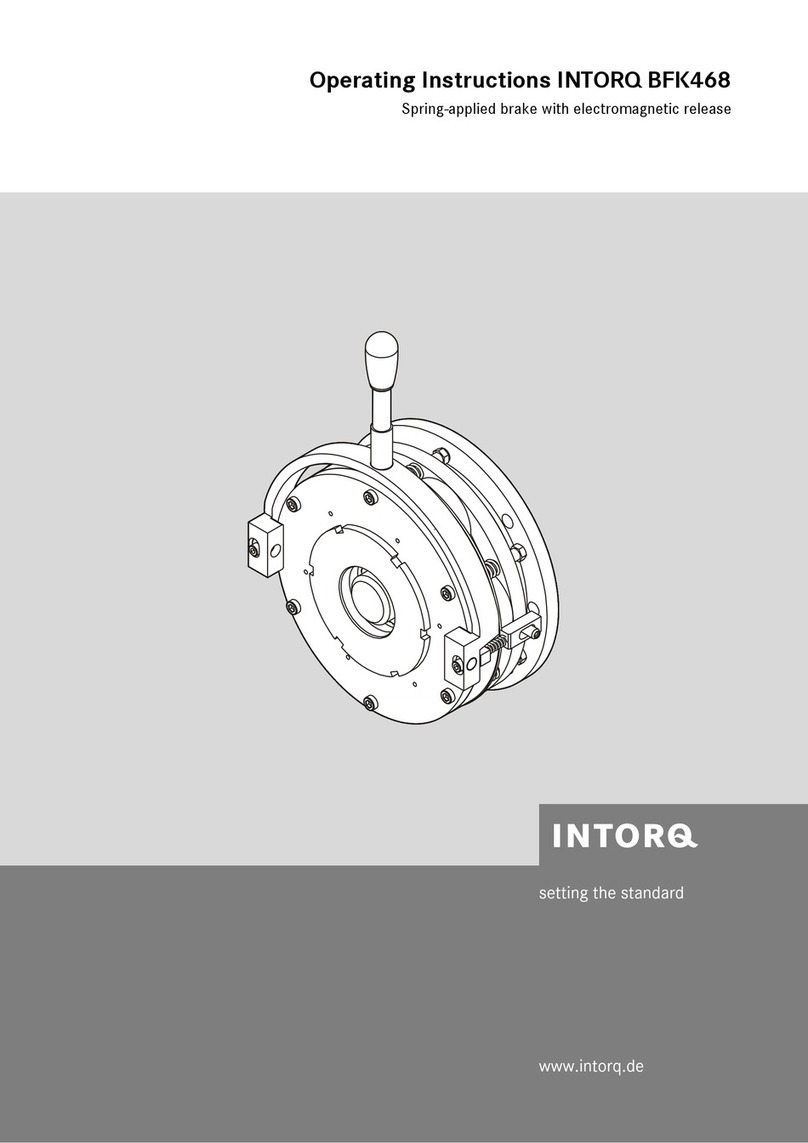
INTORQ
INTORQ BFK468 User manual
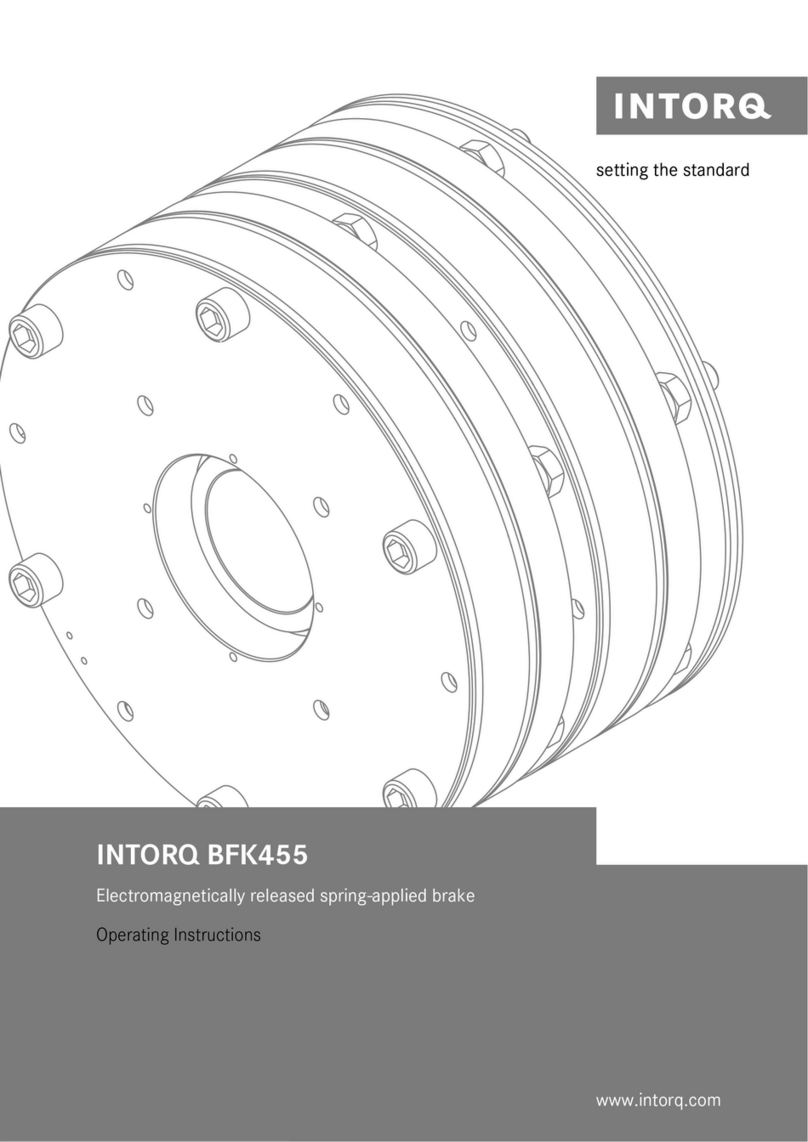
INTORQ
INTORQ BFK455 User manual
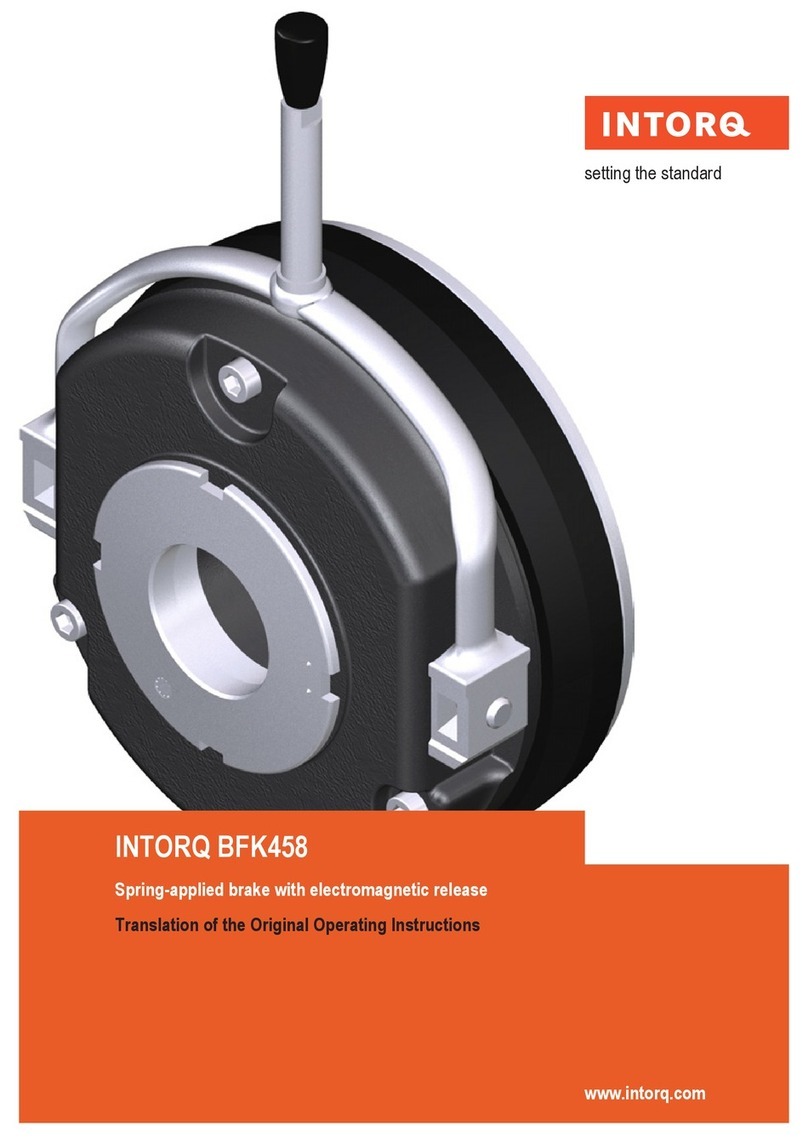
INTORQ
INTORQ BFK458 User manual
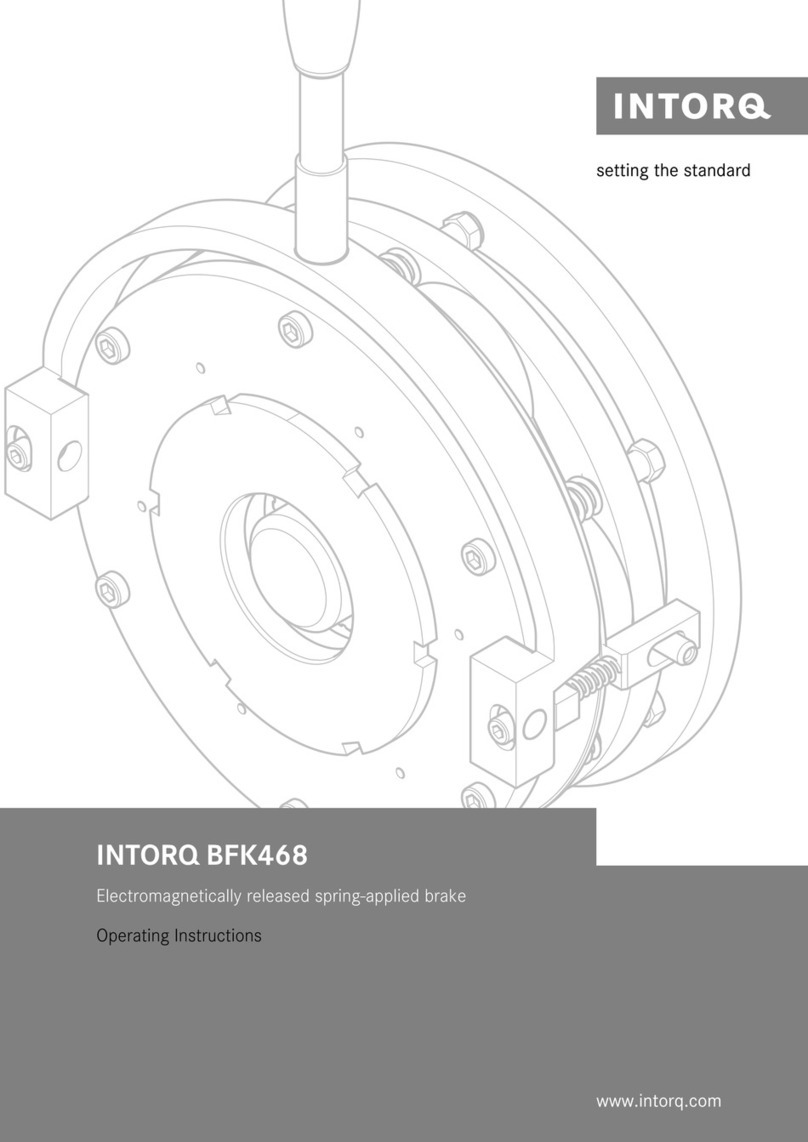
INTORQ
INTORQ BFK468 User manual
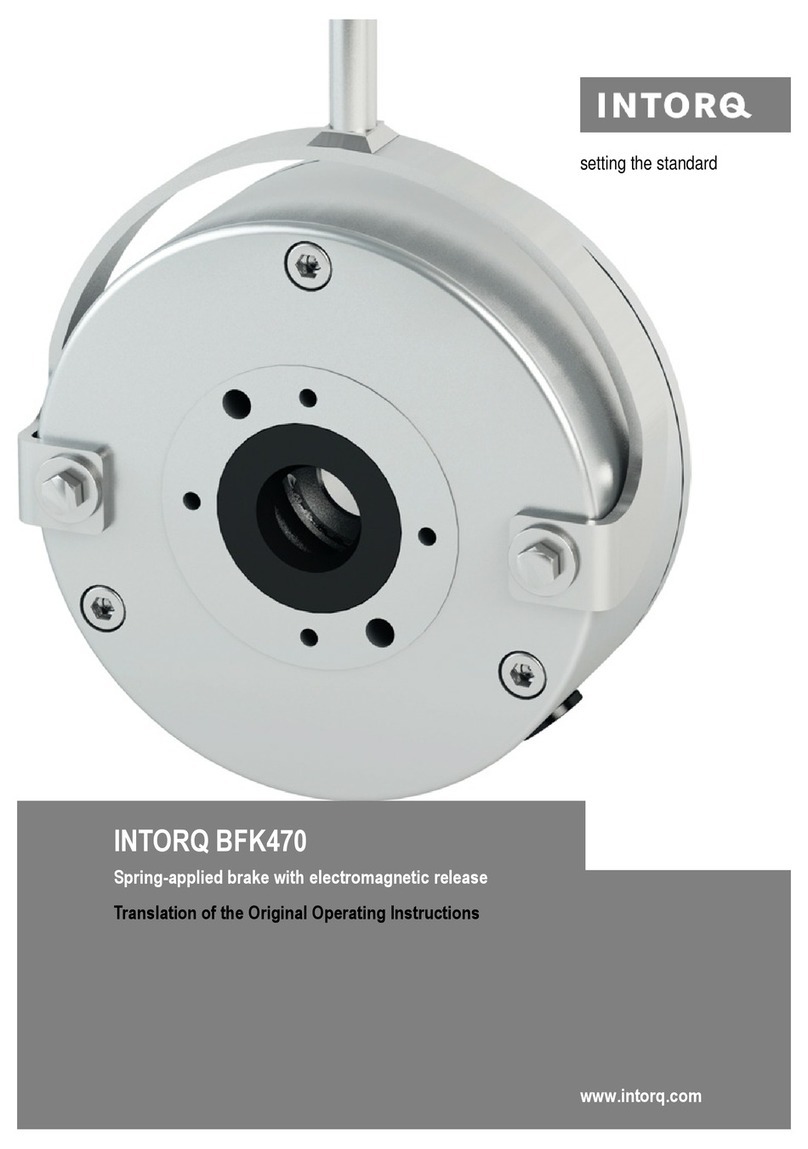
INTORQ
INTORQ BFK470 Series Quick guide
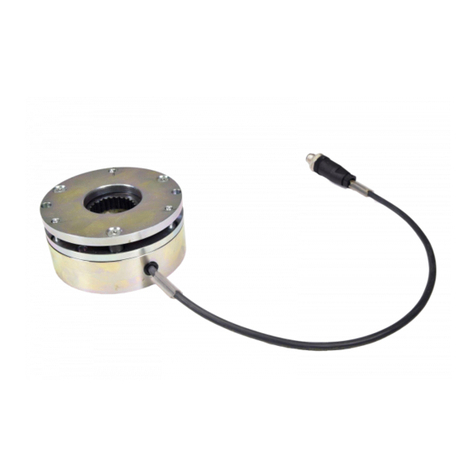
INTORQ
INTORQ BFK457 Series User manual
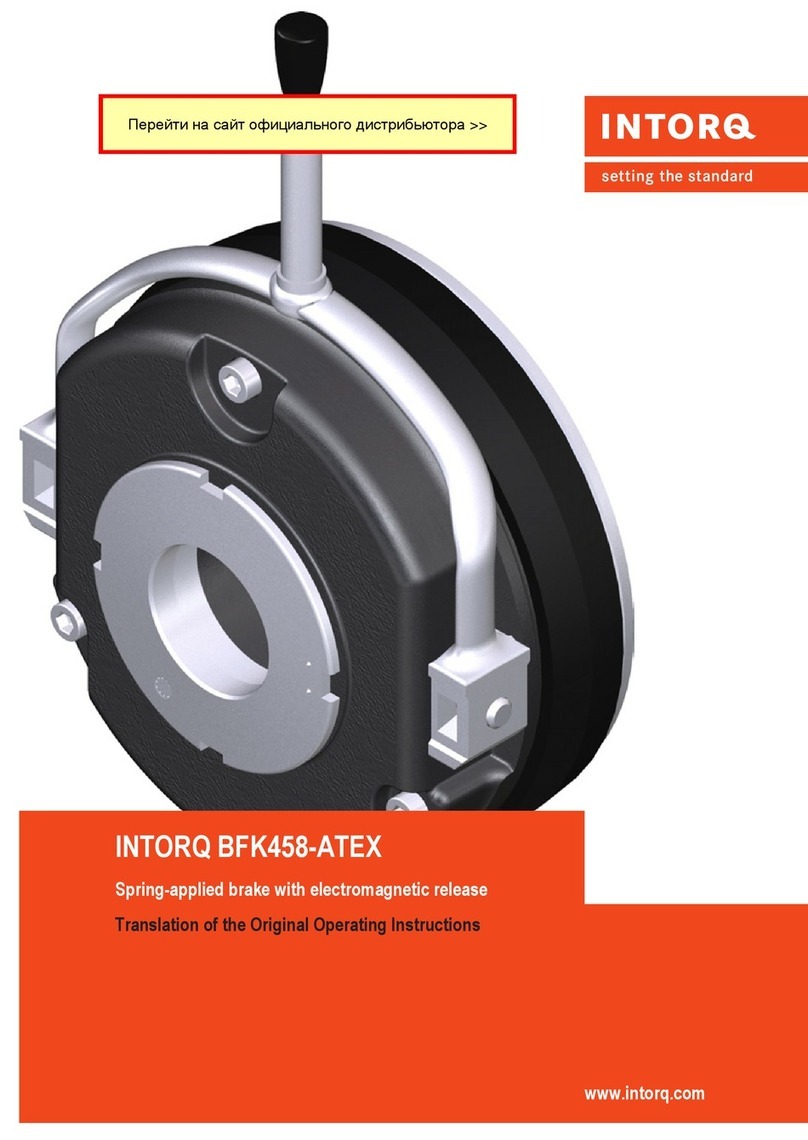
INTORQ
INTORQ BFK458-ATEX Quick guide
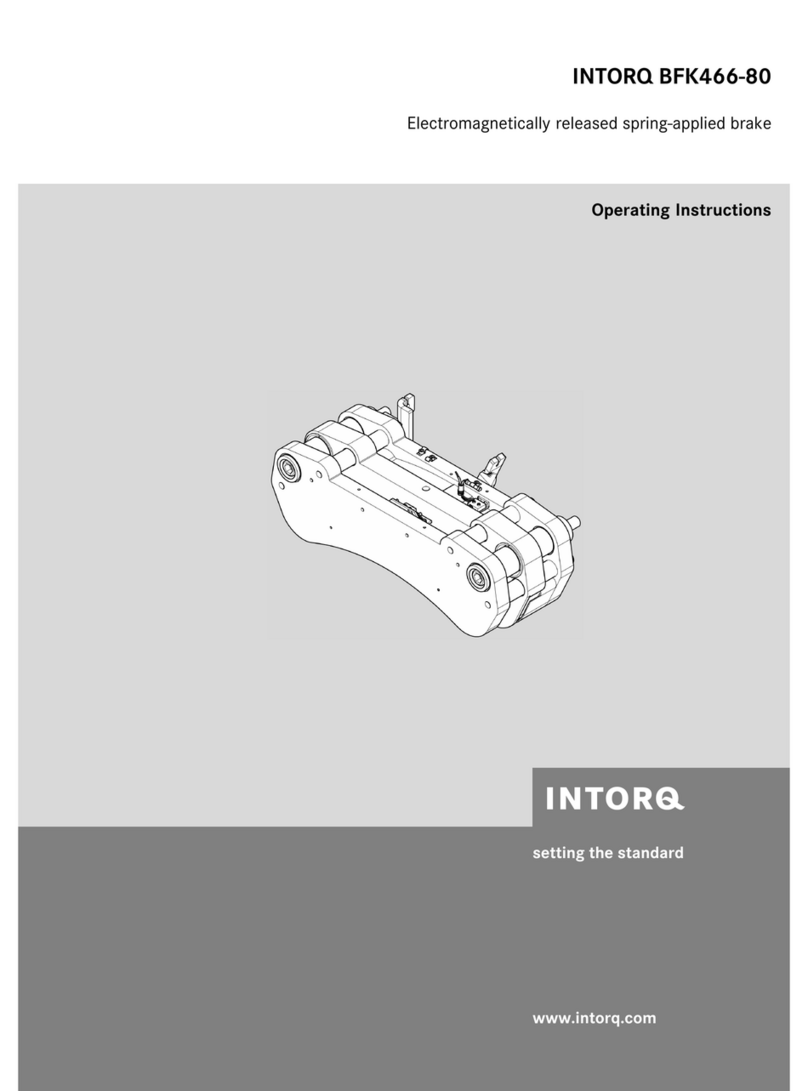
INTORQ
INTORQ BFK466-80 User manual

INTORQ
INTORQ BFK471-25 Quick guide
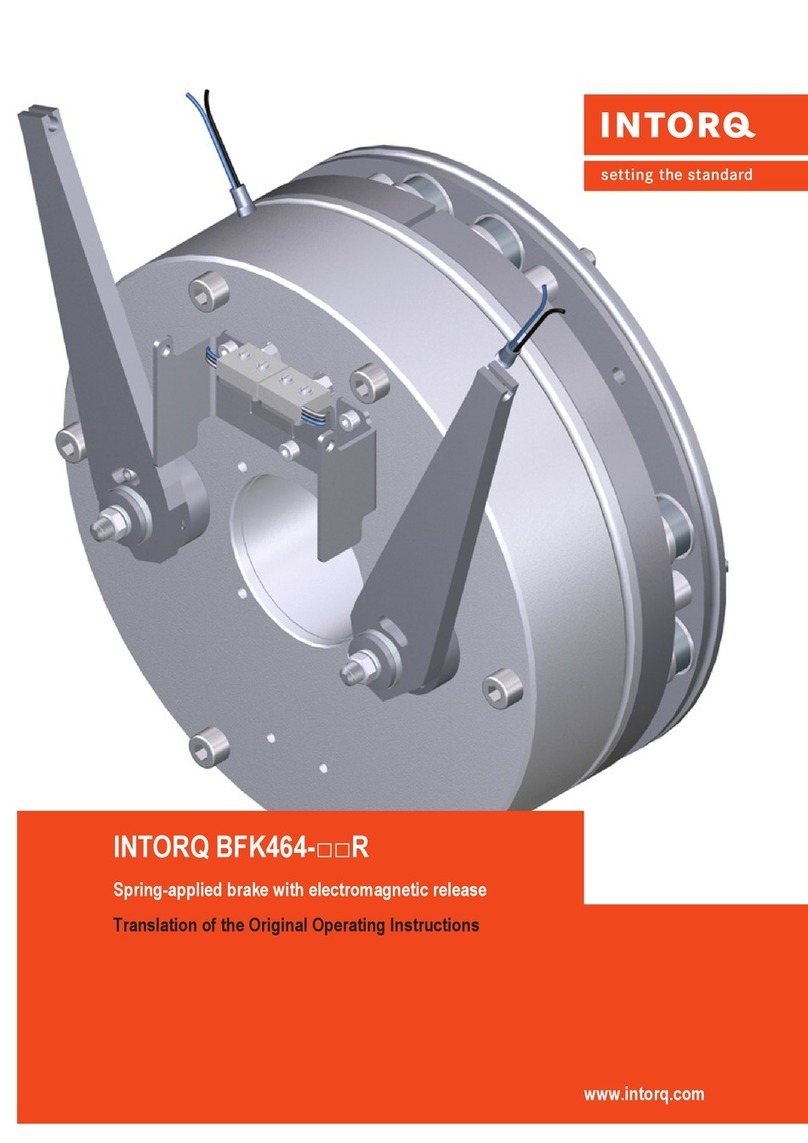
INTORQ
INTORQ BFK464-R Series Quick guide