INTORQ BFK458-ATEX Quick guide

Document history
Material number Version Description
33007851 1.0 09/2019 SC First edition
Legal regulations
Liability
¾
The information, data and notes in these Operating Instructions are up to date at the time of printing.
Claims referring to drive systems which have already been supplied cannot be derived from this in-
formation, illustrations and descriptions.
¾
We do not accept any liability for damage and operating interference caused by:
– inappropriate use
– unauthorised modifications to the product
– improper work on or with the drive system
– operating errors
– disregarding the documentation
Warranty
Notice
The warranty conditions can be found in the terms of sale and delivery from INTORQ
GmbH & Co. KG.
¾
Warranty claims must be made to INTORQ immediately after the defects or faults are detected.
¾
The warranty is void in all cases when liability claims cannot be made.
INTORQ | BA 14.0217 | 09/2019 2

Spring-applied brakes of type BFK458-06...25
Design E Design N
Double spring-applied brake
INTORQ | BA 14.0217 | 09/2019 3

Product key
Product group: Brakes
Product family: Spring-applied brake
Type: 458
Size: 06, 08, 10, 12, 14, 16, 18, 20, 25
Design/type:
E - adjustable (brake torque can be reduced via torque adjustment ring)
N - not adjustable
L – not adjustable, long-life design
INTORQ B FK
Not coded: Connection voltage, hub bore hole, options
Checking the delivery
After receipt of the delivery, check immediately whether the items delivered match the accompanying pa-
pers.
INTORQ does not accept any liability for deficiencies claimed subsequently.
¾
Claim visible transport damage immediately to the deliverer.
¾
Claim visible deficiencies or incomplete deliveries immediately to INTORQ GmbH & Co. KG.
INTORQ | BA 14.0217 | 09/2019 4

Contents
Legal regulations ....................................................................................................................................................... 2
Warranty...................................................................................................................................................................... 2
Spring-applied brakes of type BFK458-06...25........................................................................................................ 3
Product key................................................................................................................................................................. 4
Checking the delivery................................................................................................................................................ 4
1 General information................................................................................................................................................... 8
1.1 Using these Operating Instructions...................................................................................................................... 8
1.2 Conventions in use............................................................................................................................................... 8
1.3 Safety instructions and notices ............................................................................................................................ 8
1.4 Terminology used................................................................................................................................................. 9
1.5 Abbreviations used............................................................................................................................................. 10
2 Safety instructions................................................................................................................................................... 12
2.1 General safety instructions................................................................................................................................. 12
2.2 Safety notices for use in potentially explosive areas.......................................................................................... 13
2.3 Disposal ............................................................................................................................................................. 13
3 Product description ................................................................................................................................................. 14
3.1 Proper and intended usage................................................................................................................................ 14
3.1.1 Standard applications............................................................................................................................ 14
3.2 Layout ................................................................................................................................................................ 15
3.2.1 Spring-applied brake as holding/parking brake ..................................................................................... 15
3.2.2 Spring-applied brake used as a holding brake with emergency-stop function and as an operating
brake................................................................................................................................................ 15
3.2.3 Basic module E...................................................................................................................................... 16
3.2.4 Basic module N ..................................................................................................................................... 17
3.2.5 Basic module L...................................................................................................................................... 17
3.2.6 Double spring-applied brake.................................................................................................................. 18
3.3 Function ............................................................................................................................................................. 18
3.4 Braking and release ........................................................................................................................................... 19
3.5 Brake torque reduction....................................................................................................................................... 19
3.6 Optional configuration ........................................................................................................................................ 19
3.6.1 Hand-release (optional)......................................................................................................................... 19
4 Project planning notes ............................................................................................................................................ 20
INTORQ | BA 14.0217 | 09/2019 5

5 Technical specifications.......................................................................................................................................... 21
5.1 General information............................................................................................................................................ 21
5.2 Possible applications of the INTORQ spring-applied brake ............................................................................... 22
5.3 Brake torques..................................................................................................................................................... 23
5.4 Rated data.......................................................................................................................................................... 24
5.5 Switching times .................................................................................................................................................. 29
5.6 Friction work / operating frequency.................................................................................................................... 31
5.7 Dust explosive atmosphere (zone 22: non-conductive dusts)............................................................................ 31
5.8 Gas explosive atmosphere (zone 2) .................................................................................................................. 33
5.9 Example calculation for the charts ..................................................................................................................... 36
5.10 Electromagnetic compatibility............................................................................................................................. 36
5.11 Emissions........................................................................................................................................................... 37
5.12 Hand-release...................................................................................................................................................... 37
5.13 Labels on product............................................................................................................................................... 38
5.14 ATEX marking.................................................................................................................................................... 40
6 Mechanical installation............................................................................................................................................ 41
6.1 Design of end shield and shaft........................................................................................................................... 42
6.2 Tools .................................................................................................................................................................. 43
6.3 Preparing the installation.................................................................................................................................... 43
6.4 Installing the hub onto the shaft ......................................................................................................................... 44
6.5 Mounting the brake ............................................................................................................................................ 45
6.6 Installing the friction plate (optional)................................................................................................................... 48
6.7 Mounting the flange............................................................................................................................................ 48
6.7.1 Mounting the flange without additional screws...................................................................................... 48
6.7.2 Installing the flange (variants: size 06 - 16)........................................................................................... 49
6.7.3 Installing the flange (variants: size 18 - 20)........................................................................................... 50
6.7.4 Installing the flange (variants: size 25) .................................................................................................. 51
6.8 Installing the double spring-applied brake.......................................................................................................... 52
6.9 Cover ring assembly .......................................................................................................................................... 53
6.10 Installing the shaft sealing ring........................................................................................................................... 54
6.11 Installing the hand-release (retrofitting).............................................................................................................. 55
INTORQ | BA 14.0217 | 09/2019 6

7 Electrical installation ............................................................................................................................................... 56
7.1 Electrical connection .......................................................................................................................................... 56
7.2 AC switching at the motor – extremely delayed engagement ............................................................................ 57
7.3 DC switching at the motor – fast engagement ................................................................................................... 58
7.4 AC switching at mains – delayed engagement .................................................................................................. 59
7.5 DC switching at mains – fast engagement......................................................................................................... 60
7.6 Minimum bending radius for the brake connection line...................................................................................... 61
7.7 Bridge/half-wave rectifier (optional).................................................................................................................... 61
7.7.1 Assignment: Bridge/half-wave rectifier – brake size.............................................................................. 62
7.7.2 Technical specifications......................................................................................................................... 62
7.7.3 Reduced switch-off times ...................................................................................................................... 63
7.7.4 Permissible current load at ambient temperature.................................................................................. 63
8 Commissioning and operation ............................................................................................................................... 64
8.1 Protect the electrical connections against any contact or touching.................................................................... 64
8.2 Function checks before initial commissioning .................................................................................................... 65
8.2.1 Function check of the brake .................................................................................................................. 65
8.2.2 Release / voltage control....................................................................................................................... 65
8.2.3 Testing the hand-release functionality................................................................................................... 66
8.3 Commissioning................................................................................................................................................... 67
8.4 Operation ........................................................................................................................................................... 68
8.4.1 Brake torque reduction (for the optional adjustable braking torque)...................................................... 69
8.4.2 Operating procedures............................................................................................................................ 69
9 Maintenance and repair........................................................................................................................................... 70
9.1 Wear of spring-applied brakes ........................................................................................................................... 70
9.2 Inspections......................................................................................................................................................... 72
9.2.1 Maintenance intervals............................................................................................................................ 72
9.3 Maintenance....................................................................................................................................................... 72
9.3.1 Checking the components..................................................................................................................... 73
9.3.2 Check the rotor thickness...................................................................................................................... 73
9.3.3 Checking the air gap.............................................................................................................................. 74
9.3.4 Release / voltage................................................................................................................................... 74
9.3.5 Adjusting the air gap.............................................................................................................................. 75
9.3.6 Replace rotor......................................................................................................................................... 75
9.4 Spare parts list ................................................................................................................................................... 77
10 Troubleshooting and fault elimination................................................................................................................... 80
INTORQ | BA 14.0217 | 09/2019 7

General information
INTORQ | BA 14.0217 | 09/2019 8
1 General information
1.1 Using these Operating Instructions
¾
These Operating Instructions will help you to work safely with the spring-applied brake with electro-
magnetic release. They contain safety instructions that must be followed.
¾
All persons working on or with electromagnetically released spring-applied brakes must have the Oper-
ating Instructions available and observe the information and notes relevant for them.
¾
The Operating Instructions must always be in a complete and perfectly readable condition.
1.2 Conventions in use
This document uses the following styles to distinguish between different types of information:
Spelling of numbers Decimal separator Point The decimal point is always used. For ex-
ample: 1234.56
Page reference Underscore, orange _____
Reference to another page with additional
information
For example: Conventions in use
Symbols
Wildcard □
Wildcard (placeholder) for options or selec-
tion details
For example: BFK458-□□ = BFK458-10
Notice Important notice about ensuring smooth op-
erations or other key information.
1.3 Safety instructions and notices
The following icons and signal words are used in this document to indicate dangers and important safety
information:

General information
INTORQ | BA 14.0217 | 09/2019 9
Structure of safety notices:
CAUTION
Icon
Indicates the type of danger
Signal word
Characterizes the type and severity of danger.
Notice text
Describes the danger.
Possible causes
List of possible consequences if the safety notices are disregarded.
Protective measures
List of protective measures required to avoid the danger.
Danger level
DANGER
DANGER indicates a hazardous situation which, if not avoided, will result in death or seri-
ous injury.
WARNING
WARNING indicates a potentially hazardous situation which, if not avoided, could result in
death or serious injury.
CAUTION
CAUTION indicates a hazardous situation which, if not avoided, could result in minor or
moderate injury.
NOTICE
Notice about a harmful situation with possible consequences: the product itself or sur-
rounding objects could be damaged.
1.4 Terminology used
Term In the following text used for
Spring-applied brake Spring-applied brake with electromagnetic release
Drive system Drive systems with spring-applied brakes and other drive com-
ponents

General information
INTORQ | BA 14.0217 | 09/2019 10
1.5 Abbreviations used
Letter symbol Unit Designation
FRN Rated frictional force
I A Current
IHA Holding current, at 20 °C and holding voltage
ILA Release current, at 20 °C and release voltage
INA Rated current, at 20 °C and rated voltage
MANm Tightening torque of fastening screws
Mdyn Nm Braking torque at a constant speed of rotation
MKNm Rated torque of the brake, rated value at a relative speed of rotation of 100
rpm
nmax rpm Maximum occurring speed of rotation during the slipping time t3
PHW Coil power during holding, after voltage change-over and 20 °C
PLW Coil power during release, before voltage change-over and 20 °C
PNW Rated coil power, at rated voltage and 20 °C
Q J Quantity of heat/energy
QEJMax. permissible friction energy for one-time switching, thermal parameter of
the brake
QRJ Braking energy, friction energy
QSmax JMaximally permissible friction energy for cyclic switching, depending on the
operating frequency
RmN/mm2Tensile strength
RNOhms Rated coil resistance at 20 °C
Rzμm Averaged surface roughness
Sh1/h Operating frequency: the number of switching operations evenly spread over
the time unit
Shue 1/h Transition operating frequency, thermal parameter of the brake
Shmax 1/h Maximum permissible operating frequency, depending on the friction energy
per switching operation
sLmm Air gap: the lift of the armature plate while the brake is switched
sLN mm Rated air gap
sLmin mm Minimum air gap
sLmax mm Maximum air gap
sHL mm Air gap for hand-release
t1ms Engagement time, sum of the delay time and braking torque: rise time t1 = t11
+ t12
t2ms Disengagement time, time from switching the stator until reaching 0.1 MK

General information
INTORQ | BA 14.0217 | 09/2019 11
Letter symbol Unit Designation
t3ms Slipping time, operation time of the brake (according to t11) until standstill
t11 ms Delay during engagement (time from switching off the supply voltage to the
beginning of the torque rise)
t12 ms Rise time of the braking torque, time from the start of torque rise until reach-
ing the braking torque
tue s Overexcitation period
U V Voltage
UHV DC Holding voltage, after voltage change-over
ULV DC Release voltage, before voltage change-over
UNV DC Rated coil voltage; in the case of brakes requiring a voltage change-over, UN
equals UL

Safety instructions
INTORQ | BA 14.0217 | 09/2019 12
2 Safety instructions
2.1 General safety instructions
¾
Never operate INTORQ components when you notice they are damaged.
¾
Never make any technical changes to INTORQ components.
¾
Never operate INTORQ components when they are incompletely mounted or incompletely connected.
¾
Never operate INTORQ components without their required covers.
¾
Only use accessories that have been approved by INTORQ.
¾
Only use original spare parts from the manufacturer.
Keep the following in mind during the initial commissioning and during operation:
¾
Depending on the degree of protection, INTORQ components may have both live (voltage carrying),
moving and rotating parts. Such components require the appropriate safety mechanisms.
¾
Surfaces can become hot during operation. Take the appropriate safety measures (to ensure contact/
touch protection).
¾
Follow all specifications and information found in the Operating Instructions and the corresponding
documentation. These must be followed to maintain safe, trouble-free operations and to achieve the
specified product characteristics.
¾
The installation, maintenance and operation of INTORQ components may only be carried out by quali-
fied personnel. According to IEC 60364 and CENELEC HD 384, skilled personnel must be qualified in
the following areas:
– Familiarity and experience with the installation, assembly, commissioning and operation of the
product.
– Specialist qualifications for the specific field of activity.
– Skilled personnel must know and apply all regulations for the prevention of accidents, directives,
and laws relevant on site.

Safety instructions
INTORQ | BA 14.0217 | 09/2019 13
2.2 Safety notices for use in potentially explosive areas
DANGER
Danger of explosion
Increased temperatures on the surfaces and in the friction gap can result when the max-
imum friction work and operating frequencies specified by INTORQ are exceeded. These
can lead to ignition.
¾
Operation is only permitted within the specified specifications.
¾
The characteristic curve for the friction work (in the sections Dust explosive atmosphere (zone 22: non-
conductive dusts),Page31 and Gas explosive atmosphere (zone 2),Page33) as a function of the
operating frequency must not be exceeded when in an explosive atmosphere or even in emergency-
stop mode.
¾
If the facility operator cannot ensure that the specified friction work and operating frequencies will be
complied with, then the temperatures defined on the ATEX name plate for the dust zone must be mon-
itored on the brake's magnet housing using a suitable temperature measurement mechanism. If there
is no available knowledge of the occurring temperatures, then INTORQ is no longer responsible for this
ATEX certification.
¾
In an explosive gas atmosphere, the resulting frictional heat in the friction gap created during the brak-
ing process creates a potential source of ignition. It is not possible here to measure the temperature
during braking operations. Thus, it is very important to comply with the specified values for the friction
work and operating frequencies. If the values for the actual friction work and operating frequencies are
not known, the brake must not be put into operation in this atmosphere.
2.3 Disposal
The INTORQ components are made of various differing materials.
¾
Recycle metals and plastics.
¾
Ensure professional disposal of assembled PCBs according to the applicable environmental regula-
tions.

Product description
INTORQ | BA 14.0217 | 09/2019 14
3 Product description
3.1 Proper and intended usage
3.1.1 Standard applications
INTORQ components are intended for use in machinery and facilities. They may only be used for purposes
as specified in the order and confirmed by INTORQ. The INTORQ components may only be operated under
the conditions specified in these Operating Instructions. They may never be operated beyond their specified
performance limits. The technical specifications (refer to Technical specifications) must be followed to com-
ply with the proper and intended usage. Any other usage is consider improper and prohibited.
3.1.1.1 ATEX
The following is required for safely operating the INTORQ spring-applied brakes BFK458 in hazardous
areas, device category 3, zone 2/22:
The INTORQ spring-applied brakes BFK458 described may only be used in normal operations within the
following areas:
¾
Where an explosive atmosphere caused by gases, vapors, mists or swirled up dust is not expected,
¾
Or where, if these conditions nevertheless occur, then the use under these conditions may only take
place rarely and for a short period of time in the sense of the ATEX guideline 2014/34/EU.
INTORQ spring-applied brakes must never be operated outside the performance limits corresponding to
ATEX brakes!
NOTICE
If the spring-applied brake shall be used as a holding/parking brake (refer to the name plate),
all braking torques listed in the BFK458 spring-applied brake catalog are permissible.
DANGER
Danger of explosion
Increased temperatures on the surfaces and in the friction gap can result when the max-
imum friction work and operating frequencies specified by INTORQ are exceeded. These
can lead to ignition.
¾
Operation is only permitted within the specified specifications.
The following must always be observed when installing ATEX brakes:
¾
The proper functioning and correct dimensioning of the brake must be ensured before it is put into op-
eration. The correct relation between the brake, motor, control and loads must be checked.
¾
If the switching times of the brake in conjunction with the control of the drive is not properly taken into
consideration, the rotational speed could increase when the motor is switched off. As a result, the brak-
ing procedure would be carried out at a much higher speed and higher friction work than assumed in
the preliminary design. This would result in higher temperatures, which would then pose a risk of igni-
tion.

Product description
INTORQ | BA 14.0217 | 09/2019 15
¾
Check if the rotor can be pushed when it is mounted on the hub. A sluggish heavy connection between
the rotor and hub can lead to a continuous slip of the rotor. This would increase the temperature at the
friction joint.
¾
Make sure that the air gap is properly and uniformly adjusted. An uneven air gap adjustment can lead
to continuous slip of the rotor and thus to increased temperatures.
¾
When installing and dismantling the brake, make sure that no solids fall into the friction gap.
¾
Careless assembly, disassembly or operations can lead to sparking. Do not use spark-generating
tools.
¾
Mount the brake so that it does not hit any rotating components. Ensure that there is sufficient clear-
ance to the fan hood and fan blade.
3.2 Layout
This chapter describes the variants, layout and functionality of the INTORQ BFK458 spring-applied brake.
The basic module E is adjustable (the braking torque can be reduced using the torque adjustment ring).
The special feature for basic module L (with an identical design) is the more durable materials (torque sup-
port, guide pins, toothed intermediate ring, friction lining and gear teeth). The double spring-applied brake
design is especially useful in redundant braking applications.
3.2.1 Spring-applied brake as holding/parking brake
If the spring-applied brake shall be used as a holding/parking brake, all braking torques listed in the
BFK458 spring-applied brake catalog and in the BA14.0186 Operating Instructions are permissible.
The spring-applied brake is identified as a holding brake by the additional notice ("Holding brake") that is
found on an additional name plate.
Example of this marking:
Haltebremse / holding brake
II 3G Ex ec IIC T4 Gc X
II 3D Ex tc IIIB 120°C Dc X
3.2.2 Spring-applied brake used as a holding brake with emergency-stop function and as an
operating brake
When using the spring-applied brake as a holding brake with emergency-stop functionality or as an oper-
ating brake in an explosive atmosphere, it is absolutely necessary to increase the degree of protection of
the brake. The following measures must be implemented:
¾
Use the brake with a cover ring (without a condensate drain hole) and consequently also with the IN-
TORQ flange/friction plate and the corresponding ring nut for attaching the cover ring (refer to the sec-
tion Cover ring assembly,Page53).
¾
Close the rear bore holes in the torque adjustment ring or in the magnet housing with a suitable radial
shaft seal or a sealing cover (refer to the section Installing the shaft sealing ring,Page54).
¾
Closing the hand vent holes using (for example) suitable plastic plugs and a suitable sealant.

Product description
INTORQ | BA 14.0217 | 09/2019 16
The following table shows the assignments for the ID numbers of the cover rings and the sealing covers
for the different sizes and the basic models N and E:
Size INTORQ ID number
Taper plug
Cover ring
Sealing cover Radial shaft seal
Basic Model N Basic module E
06 405194 398804 405719
Request the ID
number corres-
ponding to the
shaft diameter
from INTORQ.
GPN 605/1648
(from the manu-
facturer Pöppel-
mann)
08 405197 398805 390665
10 405198 379810 131444
12 405199 398802 76767
14 405201 398803 73355
16 405202 398801 73355
18 120591 381517 73356
20 120592 364510 73357
25 120593 379257 364510
Tab.1: ID number: Assignment of the cover rings and sealing covers for the basic models N and E
3.2.3 Basic module E
Fig.1: Design of the INTORQ BFK458 spring-applied brake: Basic module E (complete stator) + rotor + hub + flange
ATappet BTorque adjustment ring CStator
DSocket head cap screw EHand-release (optional) FSleeve bolt
GFlange HRotor IHub
JPressure spring KArmature plate

Product description
INTORQ | BA 14.0217 | 09/2019 17
3.2.4 Basic module N
Fig.2: Design of the INTORQ BFK458 spring-applied brake: Basic module N (complete stator) + rotor + hub + flange
AStator BSocket head cap screw CHand-release (optional)
DSleeve bolt ERotor FHub
GPressure spring HArmature plate IFlange
3.2.5 Basic module L
Description of the long-life design:
¾
Armature plate with low backlash and reinforced torque support
¾
Pressure springs with guide pins for protection against shearing forces
¾
Aluminum rotor with toothed intermediate ring: Low-wear friction lining and low-wear gear teeth.
The long-life design can be configured modularly for size 6 to size 12 in combination with the specified
rated torques. The specifications are as follows:
¾
The stator corresponds to the design N.
¾
Rear bores and extensions are not possible.

Product description
INTORQ | BA 14.0217 | 09/2019 18
3.2.6 Double spring-applied brake
Fig.3: Design of the INTORQ BFK458 spring-applied brake: Basic module N, doubled design with intermediate flange
AStator BSocket head cap screw CScrew for intermediate flange
DIntermediate flange EHand-release (optional) FSleeve bolt
GFlange HHub IRotor
JPressure spring KArmature plate
Notice
A version of the double spring-applied brake using HFC (high-friction coefficient) linings is not
permitted.
3.3 Function
This brake is an electrically releasable spring-applied brake with a rotating brake disc (rotor) that is
equipped on both sides with friction linings. In its de-energised state, the rotor is clamped with braking
force applied by pressure springs between the armature plate and a counter friction surface. This corres-
ponds to a fail-safe functionality.
The brake torque applied to the rotor is transferred to the input shaft via a hub that has axial gear teeth.
The brake can be used as a holding brake, as an operating brake, and as an emergency stop brake for
high speeds.
The asbestos-free friction linings ensure a safe braking torque and low wear.
To release the brake, the armature plate is released electromagnetically from the rotor. The rotor, shifted
axially and balanced by the spring force, can rotate freely.

Product description
INTORQ | BA 14.0217 | 09/2019 19
3.4 Braking and release
During the braking procedure, the inner and outer springs use the armature plate to press the rotor (which
can be shifted axially on the hub) against the friction surface. The asbestos-free friction linings ensure high
braking torque and low wear. The braking torque is transmitted between the hub and the rotor via gear
teeth.
When the brakes are applied, an air gap (sL) is present between the stator and the armature plate. To re-
lease the brake, the coil of the stator is energised with the DC voltage provided. The resulting magnetic
flux works against the spring force to draw the armature plate to the stator. This releases the rotor from the
spring force and allows it to rotate freely.
3.5 Brake torque reduction
For the basic module E, the spring force and thus the brake torque can be reduced by unscrewing the
central torque adjustment ring.
3.6 Optional configuration
3.6.1 Hand-release (optional)
To temporarily release the brake when there is no electricity available, a hand-release function is available
as an option. The hand-release function can be retrofitted.

Project planning notes
INTORQ | BA 14.0217 | 09/2019 20
4 Project planning notes
¾
When designing a brake for specific applications, torque tolerances, the limiting speeds of the rotors,
the thermal resistance of the brake, and the effect of environmental influences must all be taken into
account.
¾
The brakes are dimensioned in such a way that the specified rated torques are reached safely after a
short run-in process.
¾
However, as the organic friction linings used do not all have identical properties and because environ-
mental conditions can vary, deviations from the specified braking torques are possible. These must be
taken into account in the form of appropriate dimensioning tolerances. Increased breakaway torque is
common in particular after long downtimes in humid environments where temperatures vary.
¾
If the brake is used as a pure holding brake without dynamic load, the friction lining must be reactiv-
ated regularly.
¾
You must comply with all technical specifications in order to ensure trouble-free operations of the
ATEX brake. In particular, the user-specific dimensioning of the brake must be checked according to
the specified limits of the friction performance charts (refer to Technical specifications,Page21 ). If
the limit values from the friction performance charts are not adhered to, the brake and the friction sur-
face may overheat, which would lead to a risk of ignition. In such as case, the brake is no longer com-
pliant with the ATEX standards.
¾
The permissible operating frequency (number of switching operations) corresponding to the required
friction work is determined from the friction performance charts. The number of switching operations
must be evenly distributed over the course of one hour.
¾
The correct relation between the brake, motor, control and loads must be taken into account when di-
mensioning the brake.
¾
If the switching times of the brake in conjunction with the control of the drive is not properly taken into
consideration, the rotational speed could increase when the motor is switched off. As a result, the brak-
ing procedure would be carried out at a much higher speed and higher friction work than assumed in
the preliminary design. This would result in higher temperatures, which would then pose a risk of igni-
tion.
¾
Use only original INTORQ friction parts (flange and armature plate) and standard friction linings (ST)
for the ATEX brake.
¾
The brake is designed with one free cable end. This cable must be inserted into a suitable terminal box
(through a cable gland) in accordance with the ATEX directives.
¾
INTORQ's half-wave and bridge rectifiers and spark suppressors have not been designed for use in
potentially explosive atmospheres. If the use of these electrical components is necessary, they must
be installed within a control cabinet that is outside the explosive atmosphere.
¾
To temporarily release the brake when there is no electricity available, a hand-release function is avail-
able as an option. The hand-release function can be retrofitted; for this, the hand-release holes in the
magnetic housing of the brake must be closed.
¾
The use of a micro-switch for monitoring ventilation, wear and manual release is not permitted for
brakes that are used in an explosive atmosphere.
Table of contents
Other INTORQ Spring Applied Brake manuals
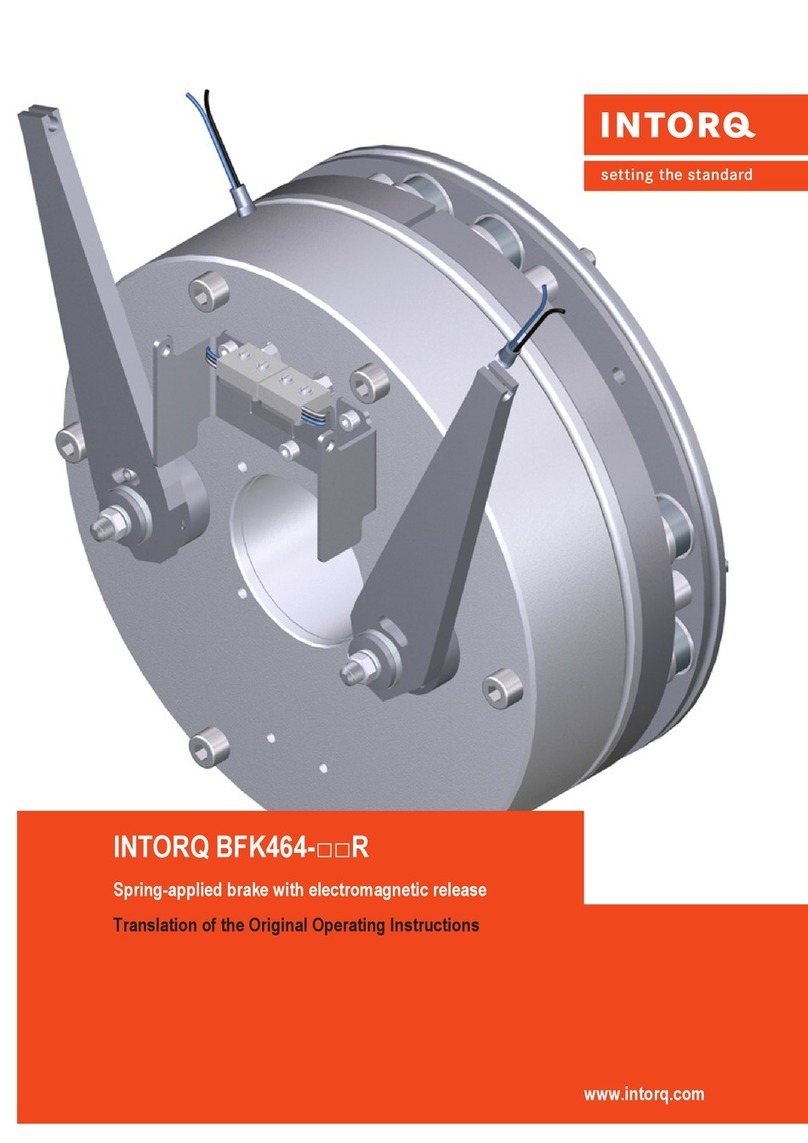
INTORQ
INTORQ BFK464-R Series Quick guide
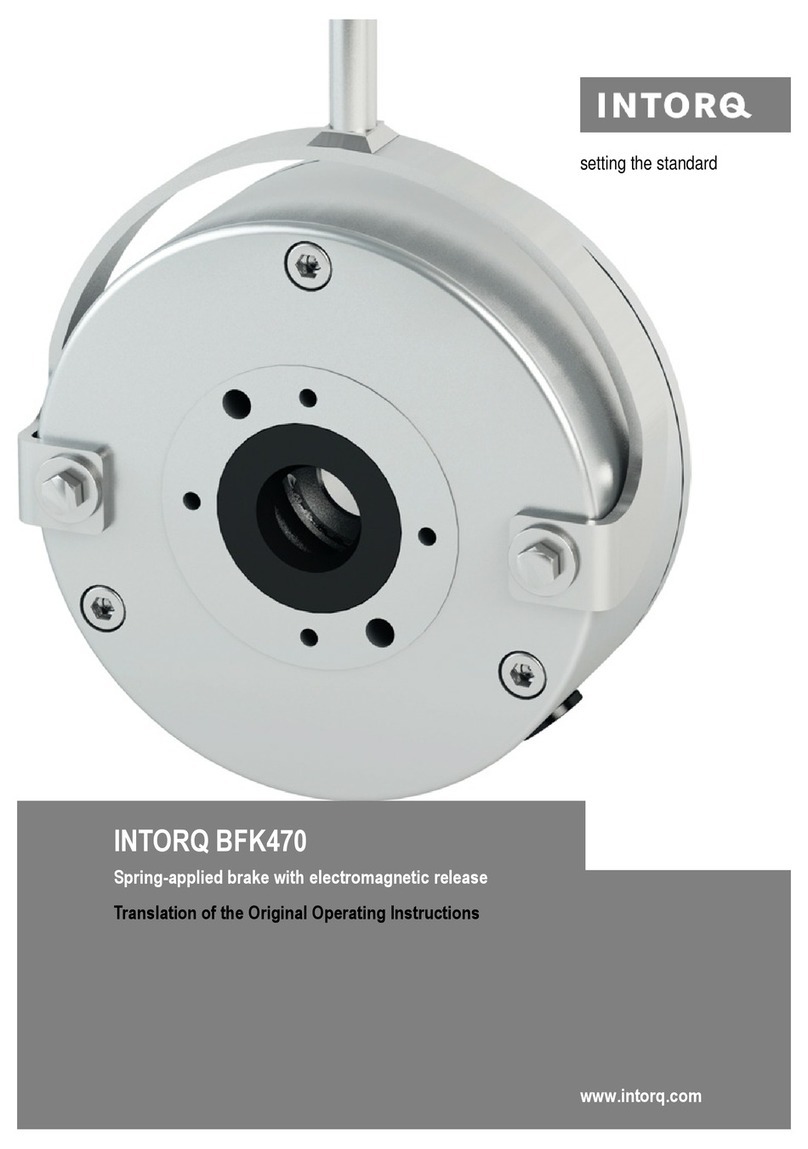
INTORQ
INTORQ BFK470 Series Quick guide
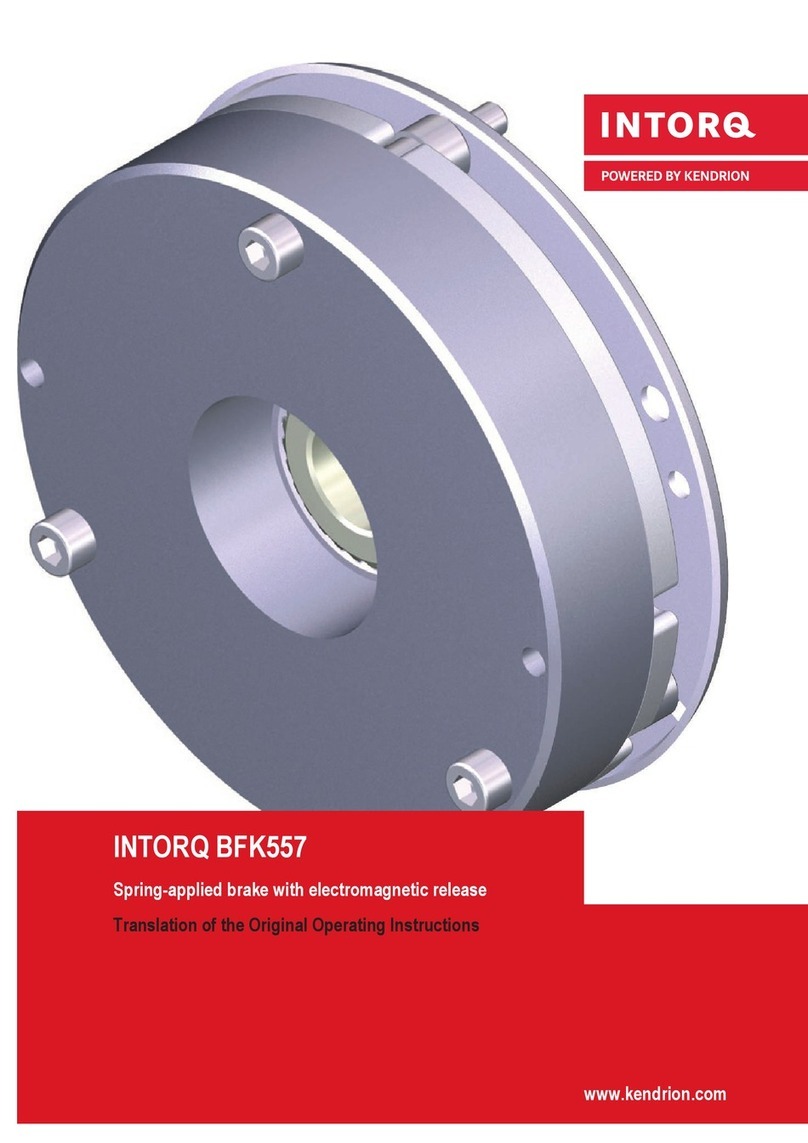
INTORQ
INTORQ BFK557 Quick guide
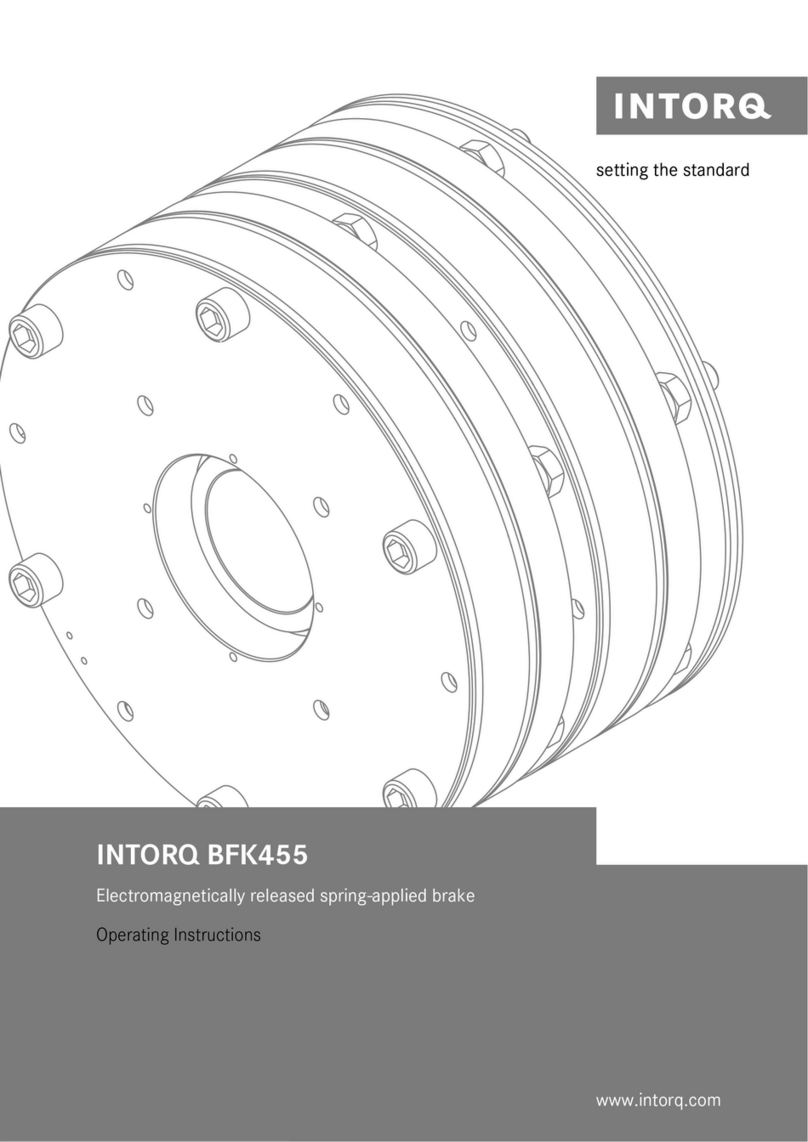
INTORQ
INTORQ BFK455 User manual

INTORQ
INTORQ 14.105 Series User manual

INTORQ
INTORQ BFK471-25 Quick guide
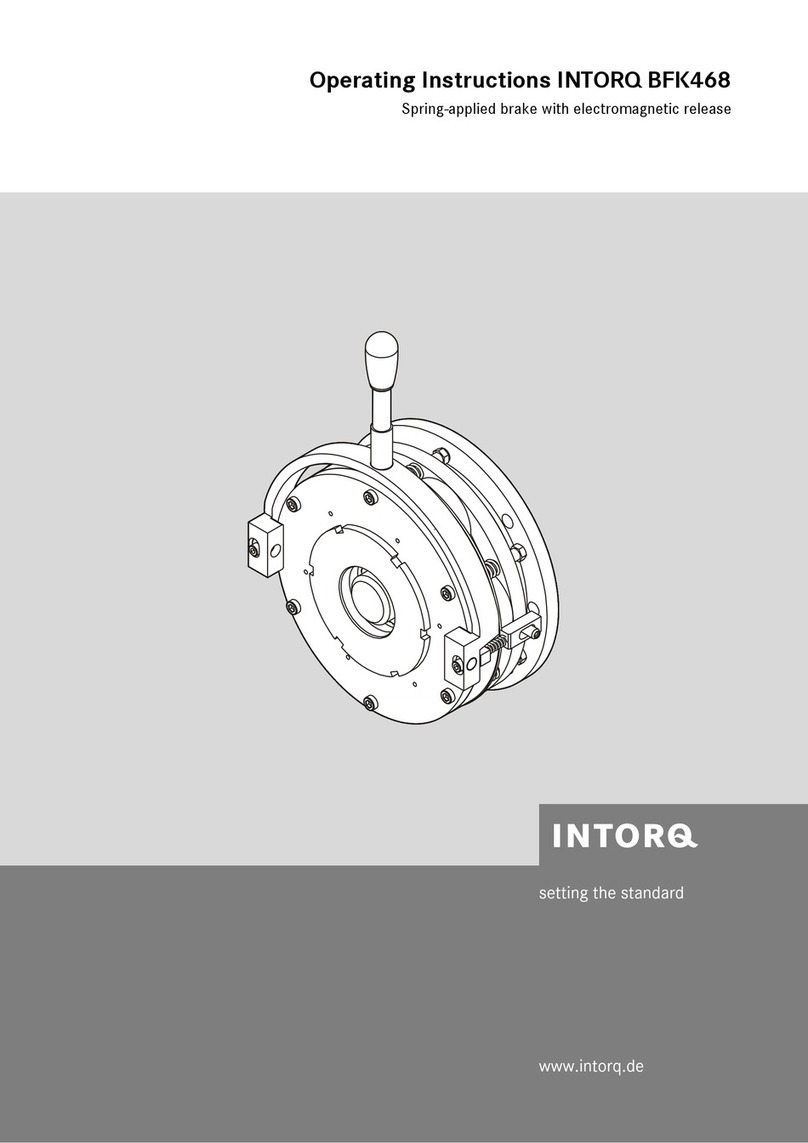
INTORQ
INTORQ BFK468 User manual
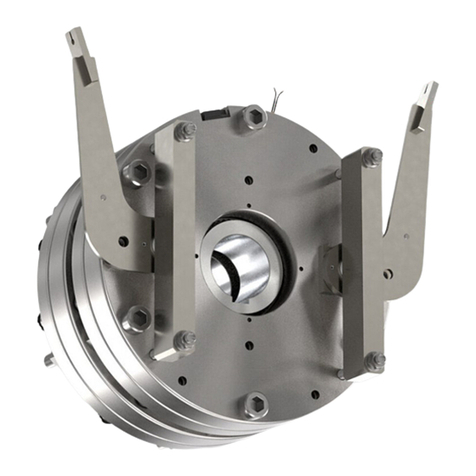
INTORQ
INTORQ BFK455-25 Quick guide
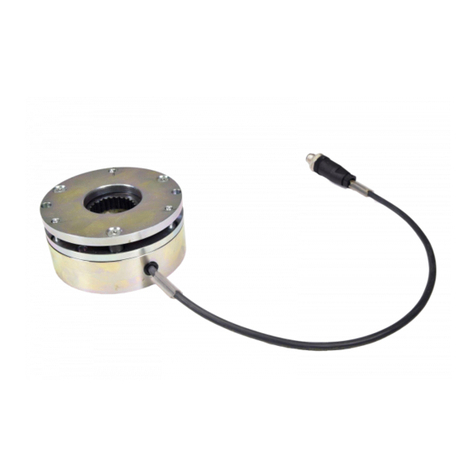
INTORQ
INTORQ BFK457 Series User manual
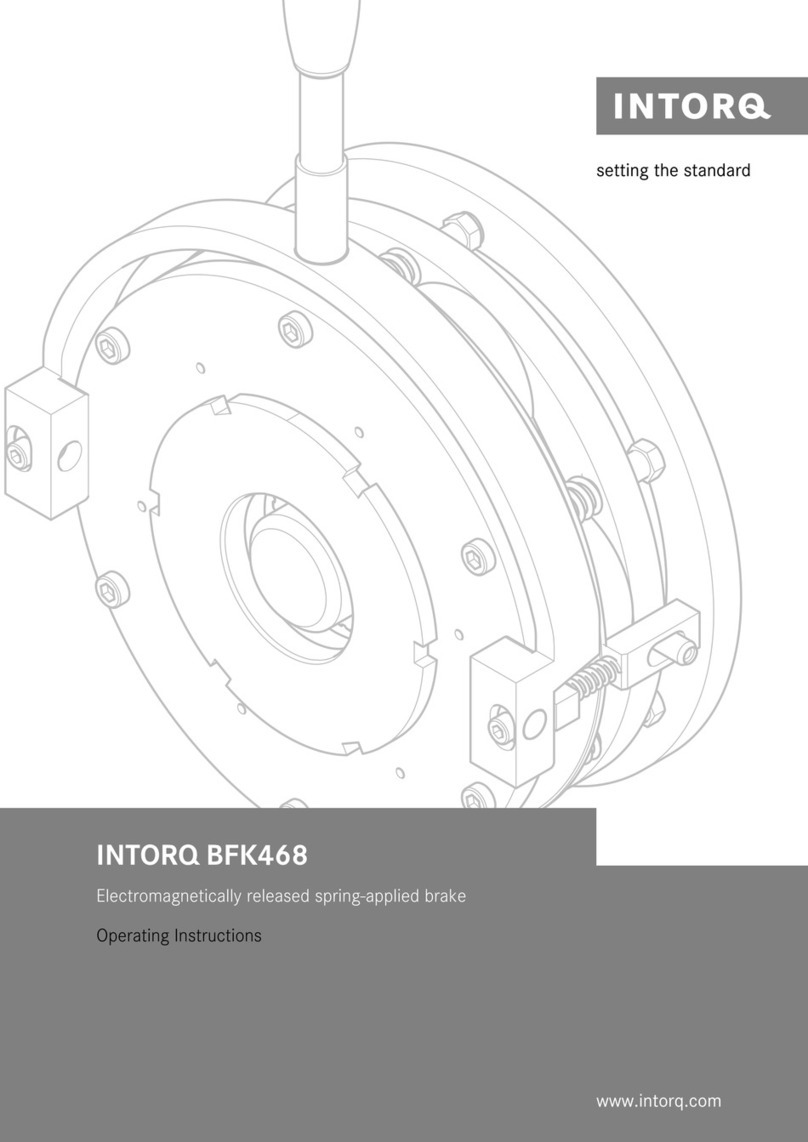
INTORQ
INTORQ BFK468 User manual