JUMA PA-100D User manual

JUMA PA100-D
Operation Manual
(Firmware Version 1.05c - 24 October 2011)
Adrian Ryan - 5B4AIY

Table Of Contents
FrontPanelControls.........................................................1
ControlDescription..........................................................2
PWR................................................................2
UP/DOWN...........................................................2
DISPLAY/CONFIG....................................................2
OPER...............................................................2
AUTO. .............................................................3
BAND+.............................................................3
UserConfigurationMode. ....................................................3
AutoBandDetect......................................................3
JUMA-TRX2...................................................4
FT-817........................................................4
F-Sense........................................................4
SerialProtocol........................................................4
SerialSpeed..........................................................4
LCDBacklighting.....................................................5
LCDContrast.........................................................5
SWRTripLimit.......................................................5
TemperatureUnitSelection..............................................5
FanControl. .........................................................6
Normal........................................................6
Low. .........................................................6
Medium.......................................................6
High..........................................................6
Over-TemperatureLimit................................................6
FanCut-InTemperature.................................................6
BandUnits...........................................................7
SystemConfiguration&Calibration.............................................7
VoltageCalibration....................................................8
CurrentCalibration. ...................................................8
OutputPowerCalibration...............................................9
BeepLength.........................................................10
PollingTime.........................................................10
PowerSampleAveraging...............................................11
ResetDefaults.......................................................11
SerialTestMode...........................................................12
AnnexA..................................................................17
JumaPA100DAlarmSystem.................................................17
i

HighSWR..........................................................17
HighCurrent. .......................................................17
Over-Temperature....................................................18
Over-Voltage..............................................................18
Over-Voltage(Adjust).................................................18
Under-Voltage.............................................................18
Under-Voltage(Adjust)................................................19
Low-voltage(FinalLimit)..............................................19
ii

JUMA PA-100D OPERATING MANUAL
5B4AIY Firmware Version: 1.05c
The PA-100D is a companion 100W all-band linear amplifier primarily intended for the Juma
TRX-2 all-band 10W transceiver, but can also be used with almost any low-power
transceiver.
This document describes the operation and setup of this equipment using firmware version
1.05c, software modifications and changes made by Adrian Ryan, 5B4AIY.
The revised firmware incorporates a number of changes to enhance the utility of this
amplifier. These instructions assume that you have already performed the necessary setup and
calibration steps.
The enhancements are:
1. User selectable temperature units of either Centigrade or Fahrenheit.
2. User selectable frequency/band units of either MHz or metres.
3. User selectable fan control option
4. Enhanced alarm facility
5. Enhanced serial test facility.
6. Improved resolution and accuracy of voltage, current and power displays
7. Power Sample Averaging
8. Minor user interface modifications.
Front Panel Controls
Juma PA100D Front Panel
1

Control Description
PWR
This button is used to power-up and power-down the amplifier, as well as several secondary
functions. To power up the amplifier, briefly press the button. The display will illuminate and
a sign-on message will be displayed:
JUMA-PA100 1.05c
OH2NLT OH7SV
After a short delay, the main screen will be displayed, as shown above.
This button now has assigned to it the cancel alarms function, which takes priority. This is to
make the alarm system consistent with the Juma TRX-2, whose alarms are cancelled with this
button. In the event an alarm cannot be cancelled, press and hold this button for an emergency
shutdown. No user settings will be saved, the power latch signal will be immediately
dropped.
UP/DOWN
These buttons are used to increment/decrement the various user settings, depending upon the
current operating mode. In the normal mode, these buttons alter the gain settings of the
amplifier, as shown by the G1 – G4 indicators on the display. G1 is the lowest gain, and the
gain can be increased in 1dB steps. In fact, the “gain” changes are simply an attenuator being
switched in and out of circuit, but it is convenient to think of this in terms of overall gain.
DISPLAY/CONFIG
This button has two functions. In the normal mode it allows the user to display a number of
internal parameters. From the normal display, a single push will show the current output
power. The next push will display the SWR, followed by the supply voltage, the amplifier
current, and finally the temperature in either EC or EF.
If the button is pressed and held, this will invoke the User Configuration mode, which is fully
covered in a later section. To exit from the User Configuration mode, press and hold the
button until a beep is heard, whereupon the normal display will return.
OPER
This button is used to place the amplifier in either the standby mode or the operate mode. In
previous versions of the firmware it was also used to cancel alarms, this function has now
been moved to the PWR button.
With this firmware revision the amplifier will always power up in the standby mode as a
precaution, except when the System Setup is selected, when it will power up in the operate
state.
In the standby mode the signal path is straight through, with neither filters nor attenuation
present. A connected transceiver will be able to transmit and receive directly to the connected
antenna. The metering functions of the amplifier will operate to show the output power and
SWR, although at low power levels the accuracy is somewhat reduced.
2

Press this button to select the operate mode. In this mode the amplifier will be fully
functional.
If this button is pressed and the power switch operated to turn the amplifier on, the flash
writer will be invoked. This is used with the Ingenia loader program to update the firmware.
For further details, please see the article on the Juma website which covers this procedure.
AUTO
This button is used to select either the manual or automatic band selection, in conjunction
with the BAND+ and BAND!buttons.
The current selection is displayed on the lower line of the display. To use the manual mode,
press the button to select M on the lower line, and use the BAND+ or BAND!button to
select an amateur band from 160m – 10m. This will select the appropriate low-pass output
filter, but exercise care, as inadvertent selection of the wrong filter could damage the
amplifier. For example, selecting the 80m band filter when transmitting on the 40m or higher
band at high power levels could seriously damage the filters.
It is preferable to use the AUTO band select mode, if possible. In this mode there are three
detection possibilities, selected via a setting in the User Configuration mode. Please refer to
this section for details concerning the use.
BAND+
There is a secondary function to this button. By pressing and holding this button and then
powering up the amplifier, the factory defaults can be reloaded. Previously this was assigned
to the OPER button, but also assigned to this button at power up is the flash writer. As it can
be a little disconcerting to see this prompt, the default reload function has been moved.
Release the BAND+ button and the display will prompt you for a selection, either press the
BAND+ to reload the default settings, or the BAND!button to abort and continue.
User Configuration Mode
This mode is used to setup the various options and settings for proper operation of this
amplifier. To select this mode, press and hold the DISPLAY/CONFIG button until you hear a
long beep, and the screen will change to reflect this mode. The various settings are changed
with the UP/DOWN buttons
To move from one menu item to the next, briefly press the DISPLAY/CONFIG button. To
exit, press and hold the button until a long beep is heard.
Auto Band Detect
Default: JUMA-TRX2
3

This governs the operation of the AUTO feature. There are three selections:
a. JUMA-TRX2. This mode should be selected when the amplifier is connected to the
Juma TRX2 transceiver. It relies on the presence of a serial data link between the
amplifier and the transceiver. The transceiver’s RS-232 port mode should be set to
JUMA TRX2, and port speeds must be the same. The default of 9600 Baud is
satisfactory. If this mode is selected, the following RS-232 selection will also be
forced to the JUMA-TRX2 setting.
b. FT-817 This setting will allow automatic band detection when connected to a Yaesu
FT-817 or similar transceiver with the appropriate accessory cable. This transceiver
outputs a stepped DC voltage which can be detected by the amplifier and used to
automatically select the correct band. The rear accessory BAND socket should be
used.
c. F-Sense With this mode selected, the incoming RF signal from the transceiver is
measured in frequency, and the result used to select the correct low-pass filters. No
connections other than the RF cable and the PTT line are required. To use this mode,
select the TUNE mode on the connected transceiver and inject between 2 – 10 watts.
The amplifier will detect the signal and select the appropriate filter automatically.
Serial Protocol
Default: JUMA-TRX2
This allows the selection of either the JUMA-TRX2 protocol for automatic band selection, or
the Test Mode. Note that the JUMA-TRX2 mode is automatically selected and cannot be
changed if the similar mode is selected in the Auto Band Detect menu. The test mode allows
the user to perform various low-level tests, as well as obtain a dump of the current internal
configuration and calibration values.
Serial Speed
Default: 9600 Baud
This sets the communications speed for the RS-232 port and can be set from 1200 Baud –
115200 Baud. The other parameters are fixed at 8 data bits, 1 stop bit, no parity.
4

LCD Backlighting
Default: 300
Set the level you wish for the display illumination using the UP/DOWN buttons. Note the a
setting of 0 will turn the backlighting off. The range is from 0 – 1100.
LCD Contrast
Default: 2000
Adjust with the UP/DOWN buttons for a suitable display. The range is from 0 – 3500.
SWR Trip Limit
Default: 3.0
Adjust with the UP/DOWN buttons over a range from 1.0 – 10.0, a default setting of 3.0 is
recommended.
Temperature Unit Selection
Default: Celsius
Using the UP/DOWN buttons select either EC or EF. Note that if the units are changed, then
the following menu settings for the alarm and fan cut-in temperatures will be automatically
preset at their respective default values in the new scale.
5

Fan Control
Default: Normal
This is a new feature. Some users prefer the cooling fan to operate all the time irrespective of
the heat sink temperature. Use the UP/DOWN buttons to select one of the following modes.
Normal: In this mode the fan operation is entirely determined by the heat-sink
temperature.
Low: In this mode, the fan will run continuously at the low speed, but will switch to
the medium or high speed in response to the heat-sink temperature.
Medium: The fan will run at medium speed, but will switch to high speed in response to
heat-sink temperature.
High: The cooling fan will operate at high speed all the time.
Over-Temperature Limit
Default : 70EC/160EF
Using the UP/DOWN buttons, select a suitable limit. The range is from 50EC – 100EC or
120EF – 212EF.
Fan Cut-In Temperature
Default: 40EC/104EF
Using the UP/DOWN buttons, select a suitable temperature for the cooling fan to start. The
range is from 0EC – 80EC, or 32EF – 170EF.
When the heat-sink temperature reaches the cut-in point, the fan will start at low speed,
assuming the normal mode of operation has been selected in the previous menu.
6

When the heat-sink temperature has risen to 5EC/10EF higher than the preset cut-in
temperature, the fan speed will increase to the medium setting. If the temperature rises by
10EC/20EF above the cut-in temperature, the fan will run at its maximum speed.
Although the range of cut-in temperatures are from 0EC – 80EC, or 32EF – 160EF, the actual
maximum cut-in temperature will be determined by the Over-Temperature Limit setting. The
actual maximum permissible cut-in temperature will always be 20EC/40EF lower than the
Over-Temperature Limit setting, or 80EC/160EF.
Although a zero temperature setting may seem somewhat odd, its purpose is to allow you to
quickly verify that the fan operates in response to temperature. As an example, assume room
temperature is 25EC, if you reduce the cut-in temperature to 25EC you should hear the fan start
at low speed. Reduce the setting to 20EC, and the fan should run at medium speed. Reduce it
to 15EC, and the fan should run at its maximum speed. Reset the temperature to the desired
setting when done.
Note: The fan drop-out temperature is 2EC/4EF lower than the cut-in temperature. This
hysteresis prevents “fan twitch” whereby the fan blades “twitch” when the cut-in
temperature is close to room temperature.
Band Units
Default: MHz
This is a new feature. Using the UP/DOWN buttons select either MHz, or metres.
To exit and save the current settings, press and hold the DISPLAY/CONFIG button until a
long beep is heard.
System Configuration & Calibration
To calibrate the amplifier, connect a suitable transceiver to provide a drive signal, and ensure
that it is connected to a dummy load. In the Service Mode, the amplifier will power-up in the
operate mode.
This section covers the system calibration settings which are only infrequently changed. To
enter this mode, press and hold the PWR button until the following screen is displayed:
7

Release the button and the calibration menu screens can be selected by briefly pressing the
DISPLAY/CONFIG button.
Voltage Calibration
Default: 5250
Limits : 4750 – 5750
The measurement system of the amplifier has been modified to obtain increased resolution and
precision.
The voltage measurement section is the most precise, as its sample voltage is obtained directly
from a precision potential divider formed by R27/R28 on the control board, and this voltage is
directly sampled by the A-D convertor.
Measure the input voltage at the amplifier’s power connector with a precision 4-digit digital
multimeter, and using the UP/DOWN buttons alter the calibration factor so that the displayed
voltage matches as closely as possible the measured value.
It should be possible to arrive at a display that matches within ±1 digit in the least significant
figure – in the display above, if the measured value was 13.84V, then you should be able to
adjust the display to read between 13.83 – 13.85.
Note that as with all digital sampling systems there is an inherent quantisation uncertainty of
±1 in the last digit.
The display is a direct sample of the A-D convertor’s output, no averaging takes place, and
thus you will see significant jitter at some calibration settings. When the display is used with
the amplifier in its normal mode, the voltage displayed is the result of a 16-sample average,
and is thus much less prone to jitter. The non-averaged value shown here allows you to adjust
the calibration for both the most accurate and the most stable display.
Current Calibration
Default: 2520
Limits : 1500 – 4000
The current sense is obtained from a precision 0.005Ωcurrent shunt resistor, R7, in series with
the main power bus. The voltage developed across this shunt is processed by IC1, a MAX4373
8

high-side current sense amplifier/convertor and the scaled voltage is measured by the A-D
convertor. The nominal scale factor is 100mV/A.
The most accurate method of calibrating the ammeter is to use a clip-on DC ammeter and a
precision digital multimeter. Alternatively, if you have access to a precision high-current shunt
you can connected this in series with your supply and measure the shunt voltage. If neither of
these means is available but your power supply has an accurate digital ammeter, then this can
be used as the reference.
Inject a suitable drive signal, wait for the current reading to stabilise, then using the
UP/DOWN buttons adjust the calibration factor to obtain a match as close as possible to the
reference measured value.
This measurement is less accurate than the voltmeter for a number of reasons. First, although
the current shunt is principally the current shunt resistor, in addition there is the contact
resistance of the four solder pads.
The varying construction techniques as well as differing types of solder will all add a varying
contact resistance which will affect the calibration. In addition, at high currents the resistor
will dissipate a certain amount of power which will cause heating, adding a further uncertainty
to the measurement. Thus, although the resolution of the ammeter is 0.1A, the accuracy will
probably not be better than ±0.5A at the nominal output power of the amplifier.
Output Power Calibration
Default: 1200
Limits: 750 – 1500
The RF output power is measured from the DC output voltage obtained from a dual directional
coupler on the main board. This measurement is probably the least accurate.
Because power is proportional to the square of the voltage, any errors or differences in
construction will be magnified when the A-D output is squared to perform the power
calculation. Equally, the output voltage of the diodes is only reasonably linear at fairly high
powers, as the output power is reduced the accuracy will degrade.
In order to calibrate this measurement, either you will need access to a fairly accurate RF
power meter, or you can use an accurate directional coupler and an oscilloscope. In my case I
had access to both methods, and was thus able to confirm the relative accuracy of both
methods.
The power meter method is by far the easiest. Inject a suitable RF drive signal, wait for the
output power reading to stabilise, and using the UP/DOWN buttons adjust the calibration
9

factor to obtain the closest possible agreement between the display and the measurement
reference.
To use the direction coupler/oscilloscope method, connect the output of the amplifier to the
directional coupler with as short a piece of co-ax as possible, and connect the output of the
directional coupler to a high-power 50Ωdummy load. Connect the oscilloscope to the
directional coupler’s coupled port and terminate the input to the oscilloscope with a 50Ωfeed-
through termination.
If it is a digitising oscilloscope, set it up to measure the RMS voltage at the input. With a
!30dB coupler, at 100W the coupled port will provide a 100mW signal into the feed-through
termination. This will give a 6.3V p-p signal into the oscilloscope. Measure the amplitude of
the signal, and calculate the coupled power level. Taking into account the coupler loss, adjust
the calibration for the best match.
If you do not have access to either of these pieces of test equipment, then the default
calibration value will be accurate enough for most purposes – this is the least accurate of the
measurements, and is really intended as an indication of output power rather than a precision
measurement.
Beep Length
Default: 50mS
Limits : 0 – 100
Using the UP/DOWN buttons, adjust for the desired time. Note that a time of 0 will disable
the beeper, no audio annunciator tones will then be generated.
Polling Time
Default: 8.0 Seconds
Limits : 0 – 30
Using the UP/DOWN buttons adjust for the desired polling rate. This is the time interval that
will elapse between the PA-100D query attempts to the Juma TRX2. If you are using the
TRX2, then any band changes or transmit status changes are conveyed via the serial port, but
in addition the PA100D will also query the TRX2. Setting the rate to 0 will disable polling.
10

Power Sample Averaging
Default: 1
This feature was added at the request of an amateur who was using the amplifier as the driver
stage of a high-power linear.
When operating CW there were occasions when there would be a transient high SWR alarm
caused by the finite time it took for the transmit/receive relays to operate. Although internally
the amplifier requires two successive samples to assert the high SWR alarm, because the
overall measurements are performed very quickly this was not long enough to ensure that a
transient would be ignored, but a steady-state condition would not.
This feature can also be used when using separate transmit and receive antennas where the
relay operating time might also provoke a transient alarm.
Power averaging was added to smooth out such transients. The number of samples can be set
from 1 (no sampling) to 8. Bear in mind that each sample adds about 4mSec to the time it
takes to register the power, and that two successive averaged samples are required to recognise
a high SWR condition. At 8 sample averaging the total recognition time for a high SWR
would thus be about 60mSec.
Use this feature at your own risk, and with caution. If you require more than about 6 samples
to smooth the transient, then consider an alternative method of using the linear.
This feature is NOT required for normal operation, and the sample count should be left at its
default value of 1.
Reset Defaults
The final page allows you to reset to the factory defaults. To do so, press and hold the OPER
button until you hear a beep, the factory defaults will then have been restored. (See also the
use of the BAND+ button.)
Note that you can only reset the factory defaults from this menu page! To save the current
calibration values, briefly press the DISPLAY/CONFIG button to return to the first page, and
briefly press the OPER button, the current values will be saved, and the system will return to
normal operation.
11

Serial Test Mode
The amplifier has an enhanced serial test feature that can be useful for a number of test
purposes. To use this feature, in the User Configuration mode, ensure that the Auto Band
detect is set to something other than JUMA-TRX2. If this latter mode is selected, then the
serial port mode is automatically configured as JUMA TRX2, and cannot be altered.
In the Serial Port mode, select Test Mode, and set the speed to a suitable value, 9600 Baud is
usually satisfactory.
Connect your PC running a terminal program to the amplifier via a serial port or a USB to RS-
232 convertor if your computer is not equipped with a normal RS-232 port.
Enter the letter I (Capital I) on the terminal, and the amplifier should respond as shown below:
Software version: 1.05c, Copyright Juha Niinikoski OH2NLT
Additional features and modifications - Adrian Ryan 5B4AIY
~~~~~~~~~~~~~~[COMMAND TABLE]~~~~~~~~~~~~~~
I Help - (This Screen)
A ADC Channel Dump
a Test Alarm System
b LCD Bar Graph Test, ESC to exit
C Clear Factory Default reset counter
D Dump System & User Settings
E Dump EEPROM contents
f Toggle Frequency Sense On/Off
t Buzzer Sound Test
W Write ASCII to LCD, ESC to exit
w Write HEX to LCD, 1B to exit
c Continuous SPI write
Z Divide-By-Zero Trap
This “Help” display can also be obtained by entering ?, H, or h.
Enter D, and the following display will be obtained:
System Calibration Settings
Battery Voltage Factor : 5288
PA Current Factor : 2650
Power Meter Factor : 1089
Beep Length Time : 50 mS
Serial Link Polling : 8.00 Seconds
PWR Measurement Samples: 1
Over-Voltage Trip : 2799 = 14.80V
Under-Voltage Trip : 2081 = 11.00V
User Configuration Settings
LCD Contrast : 2000
LCD Backlighting : 300
RS-232 Port Mode : Test Mode
RS-232 Port Speed : 9600 Baud
Frequency Sense Mode : Frequency Sense
SWR Trip Limit : 3.00
Temperature Units : Celsius
Fan Speed Control : Normal
Temperature Alarm Limit: 70C
Fan Start Temperature : 40C
Current Amplifier State: Standby
12

Band Select : Manual
Band Display Units : Metres
Your settings will, naturally, be somewhat different.
Enter A, and the following display will be obtained:
ADC 9 = 925 Scaled: 1.129V 12.256 Amps
ADC 10 = 2585 Scaled: 3.156V 13.669 Volts
ADC 11 = 0 Scaled: 0.000V 0 Out-Of-Band
ADC 12 = 68 Scaled: 0.083V 0.1 Watts (Reverse)
ADC 13 = 2979 Scaled: 3.271V 78.2 Watts (Forward)
ADC 14 = 523 Scaled: 0.639V 32 Celsius
This displays the output and scaled values from the Analogue to Digital convertor in the
microprocessor.
The display shows the ADC channel number, the raw value, the scaled equivalent input
voltage, and the actual display that would be obtained, also scaled by the calibration factor to
the measurement unit.
For example, the first line shows the output from ADC channel 9. The raw value is 925, which
corresponds to an input voltage of 1.129V. This corresponds to a current of 12.26 amps when
scaled with the calibration factor of 2650 obtained from the previous dump. The actual
calculation is:
I = ADC * Calibration Factor / 200,000Amps
= 925 * 2650 / 200,000
= 2,451,250 / 200,000
= 12.26 Amps
The second line shows that the output of ADC channel 10. The raw value is 2585,
corresponding to an input voltage of 3.156V, and the scaled display reading would be 13.67V.
The actual calculation is:
V = ADC * Calibration Factor / 1,000,000
= 2585 * 5288 / 1,000,000
= 13,669,480 / 1,000,000
= 13.67V
The third line shows the output of ADC channel 11. This channel is used with a Yaesu FT-817
transceiver or similar, and represents the band select voltage. I have simulated the actual
13

voltages and confirmed that when the Auto Band Select is set to Yaesu 817, the appropriate
amateur band filters are selected. The voltage thresholds are:
BAND VOLTAGE
1.8MHz – 160m 0.33V
3.5MHz – 75/80m 0.67V
7.0MHz – 40m 1.00V
10.0MHz – 30m 1.33V
14.0MHz – 20m 1.67V
18.0MHz – 17m 2.00V
21.0MHz – 15m 2.33V
24.0MHz – 12m 2.67V
28.0MHz – 10m 3.00V
The tolerance is ±100mV. Note that voltages below 0.23V and above 3.1V are invalid. If the
input voltage is below 0.23V, then the Out-Of-Band selection is made. Above 3.1V and the
unknown selection will be made corresponding to the 28MHz filter.
The next line shows the output from ADC channel 12, the reverse power channel used for
SWR calculations.
The next line shows the output from ADC channel 13, the forward power channel. The
calculation for both the forward and reverse power is the same, and uses the same calibration
factor. In this case the forward power raw value is 2679 corresponding to an input voltage of
3.271V.
The calculation is:
P = ( ( ( ADC * ADC ) / 10 ) * Calibration Factor ) / 10,000,000
= ( ( ( 2679 * 2679 ) / 10 ) * 1089 ) / 10,000,000
= ( ( 7,177,041 ) / 10 ) * 1089 ) / 10,000,000
= 781,579,764 / 10,000,000
= 78.2W
The last line of the display shows the output from ADC channel 14, the temperature
measurement channel.
14

It shows that the raw output was 523, corresponding to an input voltage of 0.639V. In this case
there is no software calibration factor. The design of the temperature measurement system
takes advantage of the accurately known change of base-emitter voltage of a silicon transistor
with temperature. The transistor is Q3, a BD139, mounted on the backplate of the power
amplifier. It is fed with a constant current, and is used both as a temperature sensor and a
temperature compensated voltage source to provide the bias current to the output transistors.
As the temperature of the heat-sink increases the base-emitter voltage will fall. The base-
emitter voltage of the output transistors will also fall, and if no temperature compensation
were applied, a constant bias voltage would cause their collector currents to increase. This
would result in increased dissipation, and even higher heat-sink temperatures, with a resultant
further reduction in base-emitter voltage, and eventually thermal runaway. With the
temperature compensated bias voltage from Q3, the collector currents of the output transistors
are stabilised, and thermal runaway prevented.
From the theory of silicon diodes, it is known that the temperature characteristic of a silicon
diode junction is such that the forward voltage of the diode will change by about !2mV/EC.
Thus, in the temperature sense amplifier A1-B, the potentiometer is used to adjust the offset
voltage and calibrate the sensor, and the negative change in DC output voltage is amplified by
the x10 DC gain of the inverting amplifier giving approximately +20mV/EC over a range from
0EC – 100EC, with an input voltage range to the ADC of 0 – 2V.
The reference voltage for the A-D convertor is the +5V logic supply, and thus at a 2V input the
convertor output will be 2 / 5 * 4096 = 1638. The scaling factor used is 4000, and thus the
calculation is:
T = ( ( 2 / 5 ) * 4096 ) * 4000 / 65536
= 0.4 * 4096 * 4000 / 65536
= 100EC
The potentiometer is used to calibrate the system, and all that is required is to measure the
heat-sink temperature, and adjust the potentiometer to suit. In practice, leave the amplifier to
acquire the ambient temperature by letting it sit for an hour or so, use an accurate digital
thermometer, and adjust the potentiometer as required.
For the Fahrenheit scale, the conversion is:
T = ( ( ( 2 / 5 ) * 4096 ) * 7200 ) / 65536 ) + 32
T = ( 0.4 * 4096 * 7200 / 65536 ) + 32
T = ( 1638.4 * 7200 / 65536 ) + 32
T = ( 11,796,480 / 65536 ) + 32
15

T = 180 + 32
T = 212EF
Entering the letter t will invoke the buzzer sound test:
Sound Test
Enter Frequency (100 - 5000Hz): 500
Data Value: 7372
Enter duration (mS): 1500
Enter the letter E and a dump of the EEPROM contents will be obtained:
Dump EEPROM contents
0000 0000 0000 0000 0000 0000 0000 0000 0000
0010 0000 0000 0000 0009 0000 07D0 012C 0001
0020 0003 012C 0001 0000 0046 001E 0000 0000
0030 0001 F565 FFFF FFFF FFFF FFFF FFFF FFFF
0040 0A5A 0000 14A8 0000 0441 0000 0441 0000
0050 0032 1F40 0001 0003 0AEF 0821 A5F6 FFFF
0060 FFFF FFFF FFFF FFFF FFFF FFFF FFFF FFFF
0070 FFFF FFFF FFFF FFFF FFFF FFFF FFFF FFFF
0080 FFFF FFFF FFFF FFFF FFFF FFFF FFFF FFFF
0090 FFFF FFFF FFFF FFFF FFFF FFFF FFFF FFFF
00A0 FFFF FFFF FFFF FFFF FFFF FFFF FFFF FFFF
00B0 FFFF FFFF FFFF FFFF FFFF FFFF FFFF FFFF
00C0 FFFF FFFF FFFF FFFF FFFF FFFF FFFF FFFF
00D0 FFFF FFFF FFFF FFFF FFFF FFFF FFFF FFFF
00E0 FFFF FFFF FFFF FFFF FFFF FFFF FFFF FFFF
00F0 0000 FFFF FFFF FFFF FFFF FFFF FFFF FFFF
Last success code = 7F
It is beyond the scope of this manual to explain the mapping of the EEPROM. If you are
curious, you will need to read the source code, with particular reference to the file:
pa100_eeprom.h which shows how the data values are mapped. The first 25 words are
used by the user setup contents, and the 26 word is the checksum. As an example, note the
th
checksum A5F6 at word 26.
This information is mainly of use to those wishing to modify the software, to verify that their
EEPROM changes have been accomplished correctly.
16

Annex A Juma PA100D Alarm System
The PA100D was provided with an alarm system that would warn the user of over-current,
over-temperature, and high SWR conditions. This has now been enhanced with the provision
of over-voltage, and under-voltage alarms.
The alarm system can be tested using the serial test facility described previously. Enter the
letter a and you will be prompted to enter a 1, 2, 3 ,4 , 5, or 6. 1 corresponds to a high SWR
alarm, 2 an over-current alarm, 3 an over-temperature alarm, 4 an over-voltage alarm, 5 a
battery pre-limit warning alarm, and 6 a battery final limit alarm.
High SWR
The SWR notification will blink and will be accompanied by a loud beep. To acknowledge
and cancel any alarm, briefly press the OPER button.
The limit at which the alarm is triggered is adjustable from the System Setup & Calibration
menu from 1.0 – 10.0
Whilst a setting of 1.0 might seem strange, it is there to allow you to safely test the alarm. If
you set the threshold to 1.0, and then save the setting and return to normal operation, with the
amplifier connected to a dummy load, if the transmitter is keyed the alarm will be triggered.
Release the PTT switch or key, and press the PWR button to cancel the alarm.
Switch the amplifier off and reselect the System Setup & Calibration menu and restore the
threshold to a suitable value, 3.0 is recommended.
High Current
The amplifier is fitted with a high-side current sense amplifier and over-current trip, the
MAX4373. It is independent of the measurement system and will provide a fast-acting trip in
the event that the input current exceeds 24A. The alarm will latch and will force the amplifier
to the standby state.
17
Other manuals for PA-100D
1
Table of contents
Other JUMA Amplifier manuals
Popular Amplifier manuals by other brands
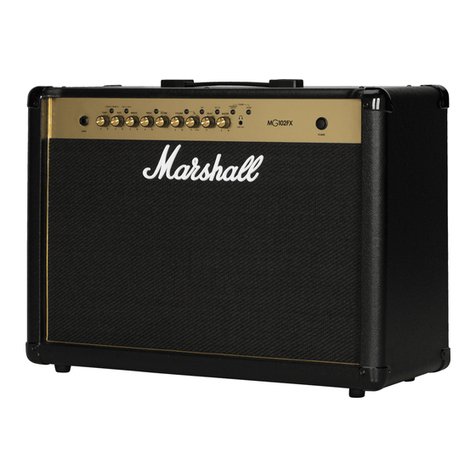
Marshall Amplification
Marshall Amplification MG GOLD SERIES owner's manual
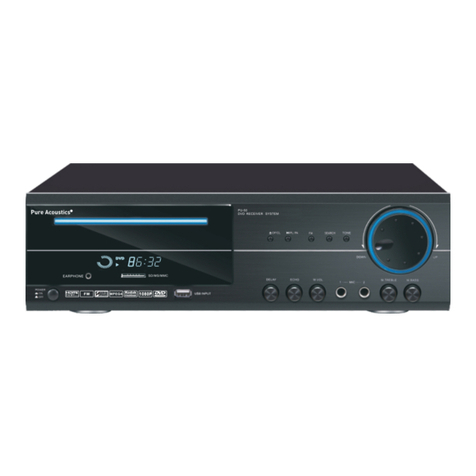
Pure Acoustics
Pure Acoustics PU-50 user manual
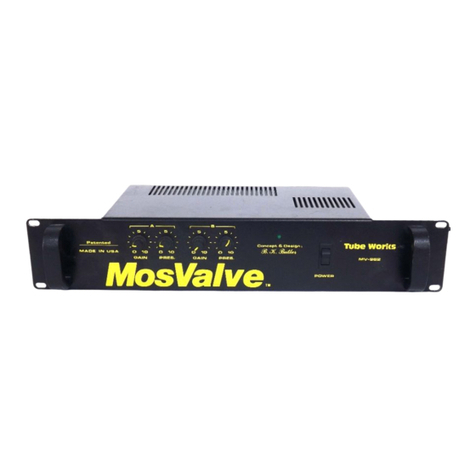
Tube Works
Tube Works MosValve 962 Operation Notes
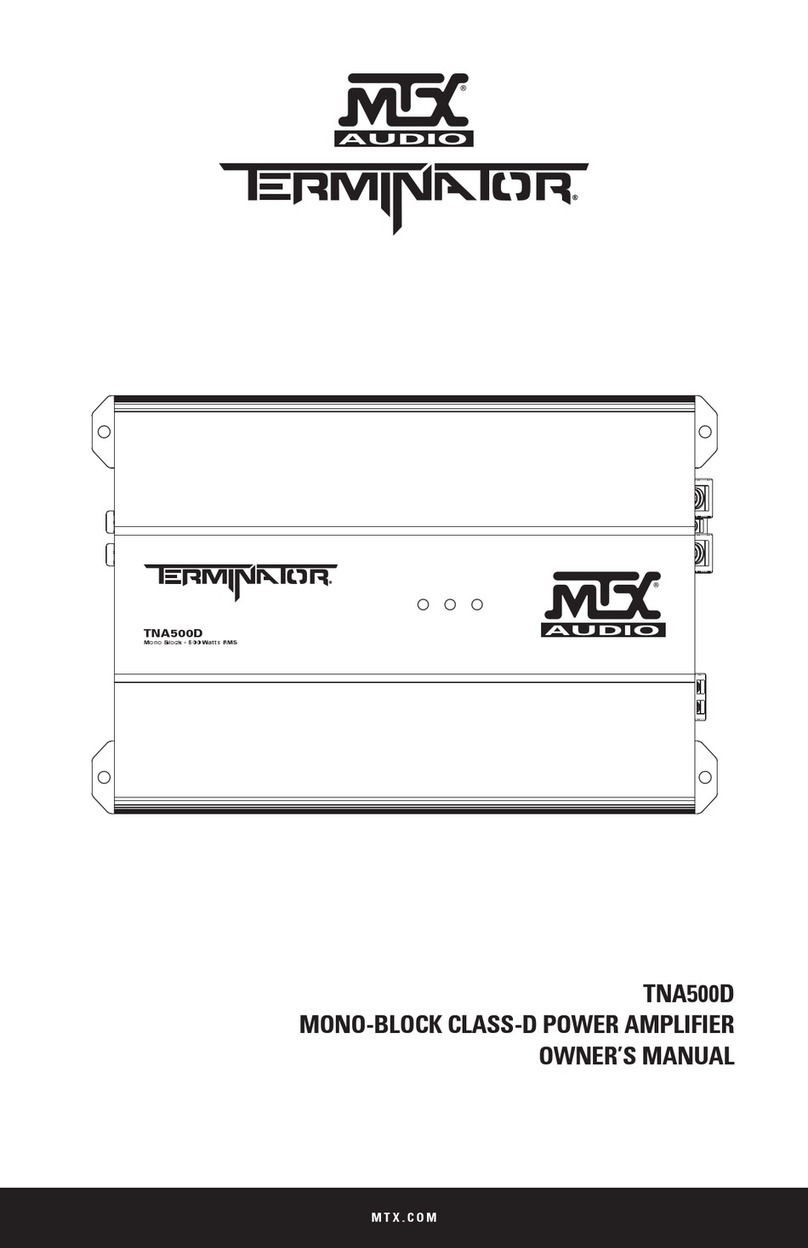
MTX
MTX TERMINATOR TNA500D owner's manual
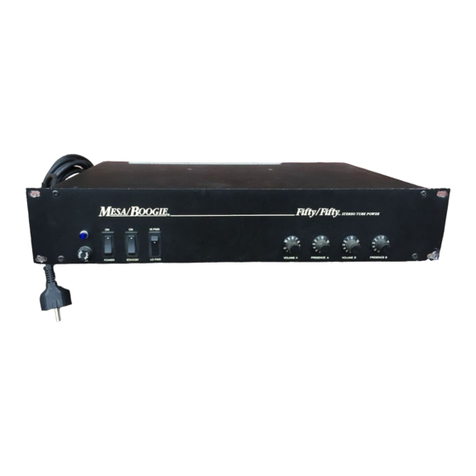
Mesa/Boogie
Mesa/Boogie Three Channel Dual & Triple Rectifier Solo... operating manual
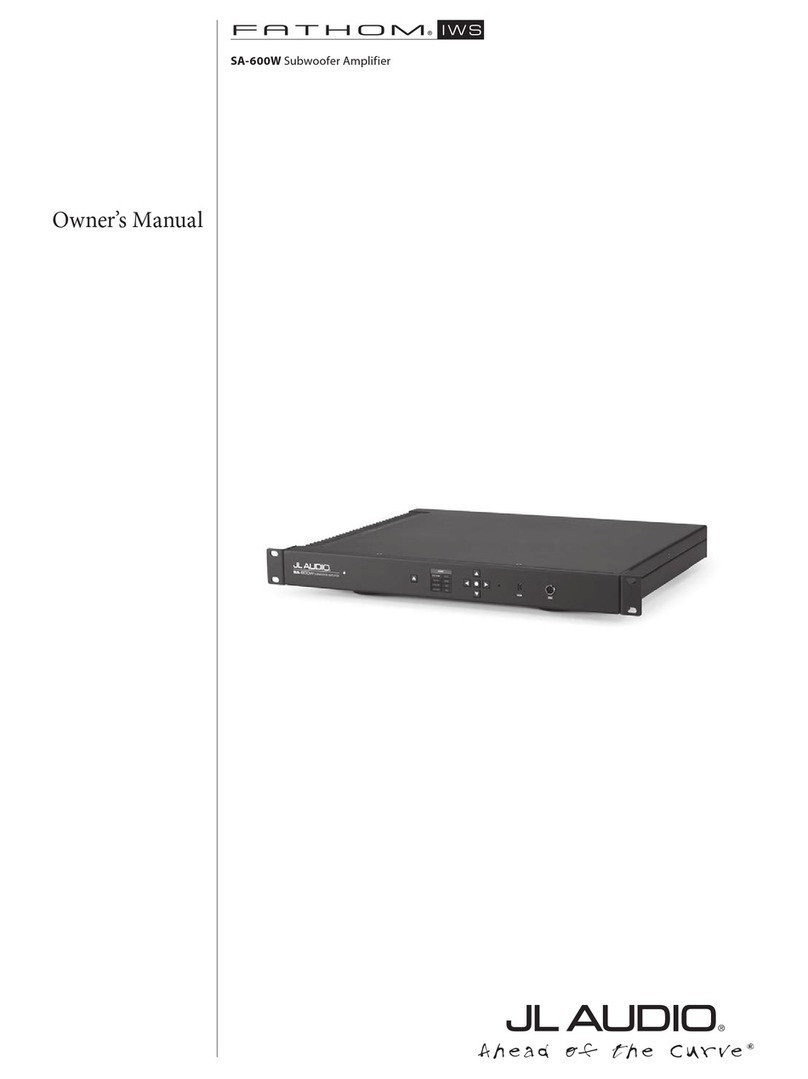
JL Audio
JL Audio Fathom SA-600W owner's manual