JUMO mTRON T User manual

JUMO mTRON T
Measuring, Control, and Automation System
CODESYS OPC Server
B 705001.5.1
Operating Manual
2014-10-14/00625938


3
Contents
1 Introduction . . . . . . . . . . . . . . . . . . . . . . . . . . . . . . . . . . . . . . . . . . . . . . . . . . . . .5
1.1 Available technical documentation . . . . . . . . . . . . . . . . . . . . . . . . . . . . . . . . . . . . . . . . . . . . . . . . 5
1.1.1 General information . . . . . . . . . . . . . . . . . . . . . . . . . . . . . . . . . . . . . . . . . . . . . . . . . . . . . . . . . . . . 5
1.1.2 Base units . . . . . . . . . . . . . . . . . . . . . . . . . . . . . . . . . . . . . . . . . . . . . . . . . . . . . . . . . . . . . . . . . . . 5
1.1.3 Input/output modules . . . . . . . . . . . . . . . . . . . . . . . . . . . . . . . . . . . . . . . . . . . . . . . . . . . . . . . . . . . 5
1.1.4 Special modules . . . . . . . . . . . . . . . . . . . . . . . . . . . . . . . . . . . . . . . . . . . . . . . . . . . . . . . . . . . . . . 6
1.1.5 Operating, visualization, recording . . . . . . . . . . . . . . . . . . . . . . . . . . . . . . . . . . . . . . . . . . . . . . . . 6
1.1.6 Power supply units . . . . . . . . . . . . . . . . . . . . . . . . . . . . . . . . . . . . . . . . . . . . . . . . . . . . . . . . . . . . 6
1.2 Safety information . . . . . . . . . . . . . . . . . . . . . . . . . . . . . . . . . . . . . . . . . . . . . . . . . . . . . . . . . . . . . 7
1.2.1 Warning symbols . . . . . . . . . . . . . . . . . . . . . . . . . . . . . . . . . . . . . . . . . . . . . . . . . . . . . . . . . . . . . . 7
1.2.2 Note signs . . . . . . . . . . . . . . . . . . . . . . . . . . . . . . . . . . . . . . . . . . . . . . . . . . . . . . . . . . . . . . . . . . . 7
1.2.3 Intended use . . . . . . . . . . . . . . . . . . . . . . . . . . . . . . . . . . . . . . . . . . . . . . . . . . . . . . . . . . . . . . . . . 8
1.2.4 Qualification of personnel . . . . . . . . . . . . . . . . . . . . . . . . . . . . . . . . . . . . . . . . . . . . . . . . . . . . . . . 8
1.3 System requirements . . . . . . . . . . . . . . . . . . . . . . . . . . . . . . . . . . . . . . . . . . . . . . . . . . . . . . . . . . 9
1.4 Brief description . . . . . . . . . . . . . . . . . . . . . . . . . . . . . . . . . . . . . . . . . . . . . . . . . . . . . . . . . . . . . . . 9
2 Installation . . . . . . . . . . . . . . . . . . . . . . . . . . . . . . . . . . . . . . . . . . . . . . . . . . . . . .11
2.1 Automatic installation . . . . . . . . . . . . . . . . . . . . . . . . . . . . . . . . . . . . . . . . . . . . . . . . . . . . . . . . . 11
2.2 Manual installation, registration, and deinstallation . . . . . . . . . . . . . . . . . . . . . . . . . . . . . . . . . . . 11
3 Configuration and testing . . . . . . . . . . . . . . . . . . . . . . . . . . . . . . . . . . . . . . . . . .13
3.1 Configuring the symbols in the programming system . . . . . . . . . . . . . . . . . . . . . . . . . . . . . . . . . 13
3.2 Changing device names . . . . . . . . . . . . . . . . . . . . . . . . . . . . . . . . . . . . . . . . . . . . . . . . . . . . . . . 15
3.3 Configuring the OPC server . . . . . . . . . . . . . . . . . . . . . . . . . . . . . . . . . . . . . . . . . . . . . . . . . . . . 16
3.4 Testing the OPC server . . . . . . . . . . . . . . . . . . . . . . . . . . . . . . . . . . . . . . . . . . . . . . . . . . . . . . . . 18
3.5 Visualization of other objects . . . . . . . . . . . . . . . . . . . . . . . . . . . . . . . . . . . . . . . . . . . . . . . . . . . . 24

Contents
4

5
1 Introduction
1.1 Available technical documentation
The documents specified below are available for the measuring, control, and automation sys-
tem.
1.1.1 General information
1.1.2 Base units
1.1.3 Input/output modules
Product Type of documentation No. Printed PDF file
Measuring,
control, and
automation system
Data sheet T 705000 - X
System manual1
1Accessory subject to charge
B 705000.0 X -
Setup program manual B 705000.6 - X
System description2
2Includes an overview of the purpose and content of all documents
B 705000.8 - X
Product Type of documentation No. Printed PDF file
Central
processing unit Data sheet T 705001 - X
Operating manual B 705001.0 - X
Modbus interface description B 705001.2.0 - X
PROFIBUS-DP interface description B 705001.2.3 - X
Installation instructions B 705001.4 X X
CODESYS OPC server
operating manual B 705001.5.1 - X
Product Type of documentation No. Printed PDF file
Multichannel
controller module Data sheet T 705010 - X
Operating manual B 705010.0 - X
Installation instructions X X
Relay module
4-channel Data sheet T 705015 - X
Operating manual B 705015.0 - X
Installation instructions B 705015.4 X X
Analog
input module
4-channel
Data sheet T 705020 - X
Operating manual B 705020.0 - X
Installation instructions B 705020.4 X X
Analog
input module
8-channel
Data sheet T 705021 - X
Operating manual B 705021.0 - X
Installation instructions B 705021.4 X X

1 Introduction
6
1.1.4 Special modules
1.1.5 Operating, visualization, recording
1.1.6 Power supply units
Digital input/
output module
12-channel
Data sheet T 705030 - X
Operating manual B 705030.0 - X
Installation instructions B 705030.4 X X
Product Type of documentation No. Printed PDF file
Product Type of documentation No. Printed PDF file
Router module Data sheet T 705040 - X
Installation instructions B 705040.4 X X
Product Type of documentation No. Printed PDF file
Multifunction
panel 840 Data sheet T 705060 - X
Operating manual B 705060.0 - X
Modbus interface description B 705060.2.0 - X
Installation instructions B 705060.4 X X
Operating panels Data sheet T 705065 - X
Product Type of documentation No. Printed PDF file
24 V power supply
units Data sheet T 705090 - X
Operating instructions QS5.241 X -
Operating instructions QS10.241 X -

7
1 Introduction
1.2 Safety information
1.2.1 Warning symbols
1.2.2 Note signs
DANGER!
This symbol indicates that personal injury caused by electrical shock may occur if the re-
spective precautionary measures are not carried out.
WARNING!
This symbol in connection with the signal word indicates that personal injury may occur if the
respective precautionary measures are not carried out.
CAUTION!
This symbol in connection with the signal word indicates that damage to assets or dataloss
will occur if the respective precautionary measures are not taken.
CAUTION!
This symbol indicates that components could be destroyed by electrostatic discharge
(ESD = Electro Static Discharge) if the respective cautionary measures are not taken.
Only use the ESD packages intended for this purpose to return device inserts, assembly
groups, or assembly components.
READ DOCUMENTATION!
This symbol – placed on the device – indicates that the associated device documentation
has to be observed. This is necessary to recognize the kind of the potential hazards as
well as the measures to avoid them.
NOTE!
This symbol refers to important information about the product, its handling, or additional
use.
REFERENCE!
This symbol refers to further information in other sections, chapters, or manuals.
FURTHER INFORMATION!
This symbol is used in the tables and refers to further information in connection with the
table.
&
DISPOSAL!
This device and the batteries (if installed) must not be disposed in the garbage can after
use! Please ensure that they are disposed properly and in an environmentally friendly
manner.

1 Introduction
8
1.2.3 Intended use
The measuring, control, and automation system is intended for use in an industrial environ-
ment, as specified in the technical data of the individual modules of the system. Use for any
other purpose is considered contrary to the intended use.
The modules have been manufactured in compliance with applicable standards and guidelines
as well as the applicable safety regulations. Nevertheless, personal injury or material damage
may occur in the event of improper use.
To avoid risks, the modules may only be used:
• for the intended use
• when in good order and condition
• when taking into account the technical documentation provided
Even if a module is used correctly and according to the intended use, it may still pose applica-
tion-related risks, for example as the result of missing safety devices or incorrect settings.
To avoid incorrect settings, this manual contains relevant safety information and warnings.
These must be complied with.
1.2.4 Qualification of personnel
This document contains the information required to ensure that the measuring, control, and au-
tomation system described is used as intended.
It is intended for technically qualified personnel who have received special training and have
the appropriate knowledge in the field of automation technology (measurement and control
technology).
Understanding and technically correct observance of the safety information and warnings con-
tained in the supplied technical documentation are prerequisites for safe startup as well as
safety during operation. Only qualified individuals have the required technical knowledge to in-
terpret and put into practice the safety information and warnings used in this document in any
given situation.

9
1 Introduction
1.3 System requirements
The CODESYS OPC server is supported by the measuring, control, and automation system
from system version 01 onwards.
The system version is determined using the compatibility index of the base unit. Further infor-
mation on the compatibility index:
Setup program manual (B 705000.6)
1.4 Brief description
OPC (OLE for Process Control) is a standardized interface for accessing process data. It is
based on the Microsoft® standard COM/DCOM and was developed for the data access re-
quirements in automation technology. In this area it is used predominantly for reading and re-
cording control values.
OPC clients may be visualization tools and programs for operating data logging. OPC servers
are typically provided for PLC systems and fieldbus cards.
The CODESYS OPC server is a program part of the CODESYS PLC programming system.
The CODESYS OPC server
• is within the scope of delivery of the CODESYS development environment and is free,
• consists of the server and an OPC configurator,
• requires a symbol configuration in CODESYS and offers all variables which are available in
the symbol configuration.
The PLC programming system can be downloaded from the JUMO website www.jumo.de at
SUPPORT/SERVICES > DOWNLOAD > SOFTWARE DOWNLOAD > REMAINING SOFTWARE
(file size approx. 400 MB).
NOTE!
For operation as CODESYS OPC server, on the system side the extra code "PLC according
to IEC 61131-3 (CODESYS V3)", code 224 is required.

1 Introduction
10

11
2 Installation
More detailed information on installing the CODESYS OPC servers V3 is available in the COD-
ESYS OPC server user manual, which is installed alongside the OPC server.
CODESYS_OPC_Server_V3_User_Guide.pdf, chapter 3
If only the OPC server is required, only the following features should be selected and installed
at the time of installation:
• CODESYS Gateway
• CODESYS OPC Server 3
2.1 Automatic installation
The CODESYS OPC server V3 is supplied with the setup program of the measuring, control,
and automation system. During installation all files necessary for OPC communication are in-
stalled and the OPC server is automatically registered as a COM server.
Depending on whether the complete development environment or only the CODESYS OPC
server is to be installed on the PC, close attention must be paid when selecting features at the
time of installation.
2.2 Manual installation, registration, and deinstallation
In addition to automatic installation, it is possible to register the OPC server manually, either as
a COM server or as a service. This also applies for deinstallation.
Simultaneous installation and registration
The command WinCODESYSOPC /RegServer registers the OPC server as a COM server.
During this, the current location of the file "WinCODESYSOPC.exe" is always used as the path.
Access can therefore only be from a local path.
Registration as a service
The command WinCODESYSOPC /Service installs the executable file "WinCODESYS-
OPC.exe" as a Windows system service. Once this has been started, the service remains ac-
tive until the system is shut down. Communication with the configured PLCs continues. The
service is also installed at the current location in this case.
Deinstallation
The command WinCODESYSOPC /UnRegServer deletes all entries of the OPC server from
the Windows registry. The installed files are not deleted.
NOTE!
To use the CODESYS OPC server V3 on a PC with the WINDOWS VISTA operating system1
it is strongly recommended that you start the OPC client in compatibility mode for WINDOWS
XP1SP2 and with extended administrator rights. This ensures that the values are continu-
ously updated.
1WINDOWS VISTA and WINDOWS XP are registered trademarks of Microsoft Corporation.

2 Installation
12

13
3 Configuration and testing
3.1 Configuring the symbols in the programming system
Configuration of the symbols takes place in three steps, which are summarized below. More
detailed information is available in the CODESYS OPC server user manual.
CODESYS_OPC_Server_V3_User_Guide.pdf, chapter 5.1 ("V3 interface")
Step 1: Adding symbol configuration
Select the CPU application object in the device tree (right mouse click) and add symbol config-
uration:
CPU (70.5001) > PLC LOGIC > APPLICATION > ADD OBJECT > SYMBOL CONFIGURATION
If necessary, change the description and add the symbol configuration by clicking the "Open"
button.

3 Configuration and testing
14
Step 2: Configuring symbols
Double-clicking SYMBOL CONFIGURATION opens the following dialog.
Execute the "Build" command to allow variables to be selected:
Select the entry "Unconfigured from Project" in the "View" menu:
Select the required variables:

15
3 Configuration and testing
In the symbol configuration the access rights for each selected variable can be changed. To do
this, in the "Access Rights" column click on the symbol next to the variables in question. The
access rights change each time the mouse is clicked:
Step 3: Logging in
When logging into the PLC the application is compiled and loaded.
3.2 Changing device names
In the measuring, control, and automation system the device name is assigned automatically.
It is composed of the MAC address and the description of the device family. This name is not
suitable for use with the CODESYS OPC server and must be changed.
The change is carried out in CODESYS in the configuration of the CPU:
Communication settings >Open context menu for the relevant CPU in the network path (right
mouse click) >Change device name
Symbol Access right
read+write
write-only
read-only

3 Configuration and testing
16
3.3 Configuring the OPC server
Configure the OPC server according to the CODESYS OPC server user manual.
CODESYS_OPC_Server_V3_User_Guide.pdf, chapter 6
During configuration, the PLC name must be entered in the "CoDeSys address of PLC" dialog.
Click the "Edit" button to open the dialog:
Enter the name of the system‘s CPU (here: "mTRON_T_OPC"):

17
3 Configuration and testing
Alternatively the address from the communication settings can be used (here: "001.B02E"):

3 Configuration and testing
18
3.4 Testing the OPC server
The OPC server should be tested using an OPC client.
In the following description the free OPC DA Data Access Client from Kassl GmbH is used
(www.kassl.de/opc/download.shtml).
Establishing a connection to the OPC server
After the OPC client has been started the connection to the OPC server must be established:
FILE > CONNECT TO SERVER...
To do this, select "CoDeSysOPCDA-Server" from the list of available OPC servers:

19
3 Configuration and testing
Shortly afterwards the OPC client is connected to the OPC server. The server state changes
from "not connected" to "running", and the connected PLC is displayed in the path window:
Selecting and displaying variables
Open the path using the mouse until the variables required for the tests (OPC items) appear:

3 Configuration and testing
20
Click on the "Inspector" tab and add a group to display individual variables and to edit if neces-
sary:
Enter Groupname and UpdateRate and confirm by clicking "Ok":
The new group appears in the left part of the window:
Other manuals for mTRON T
8
Table of contents
Popular Server manuals by other brands
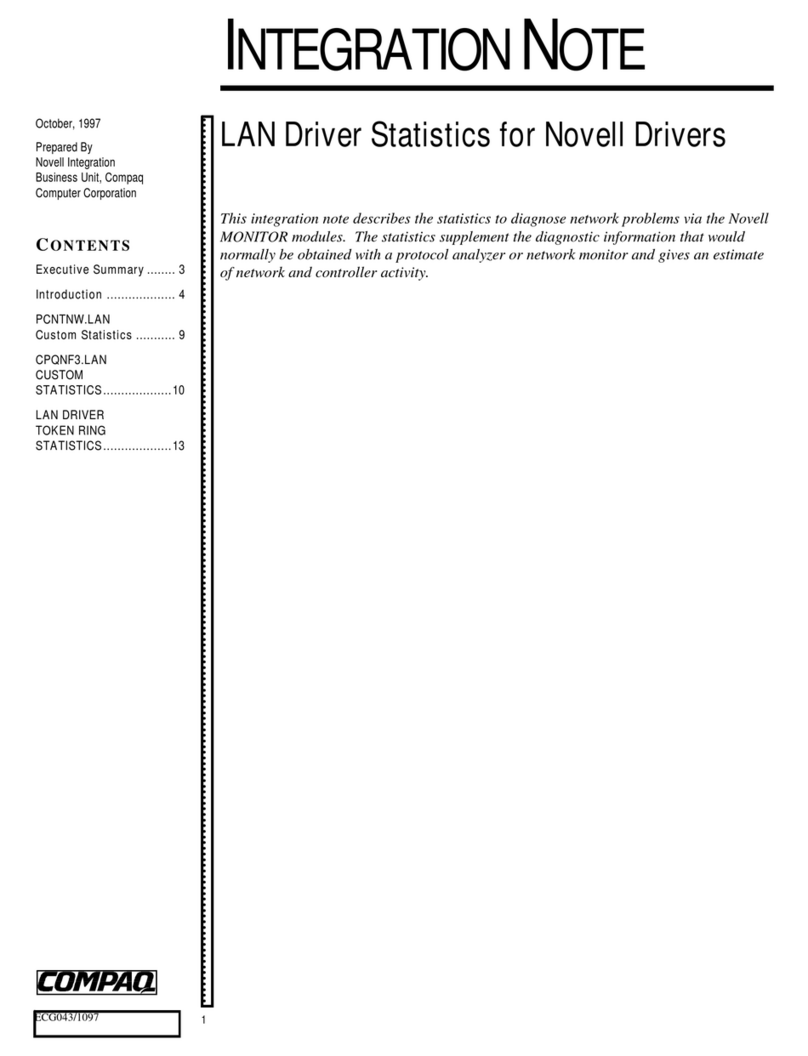
Compaq
Compaq 108164-003 - ProLiant - 800 Integration notes
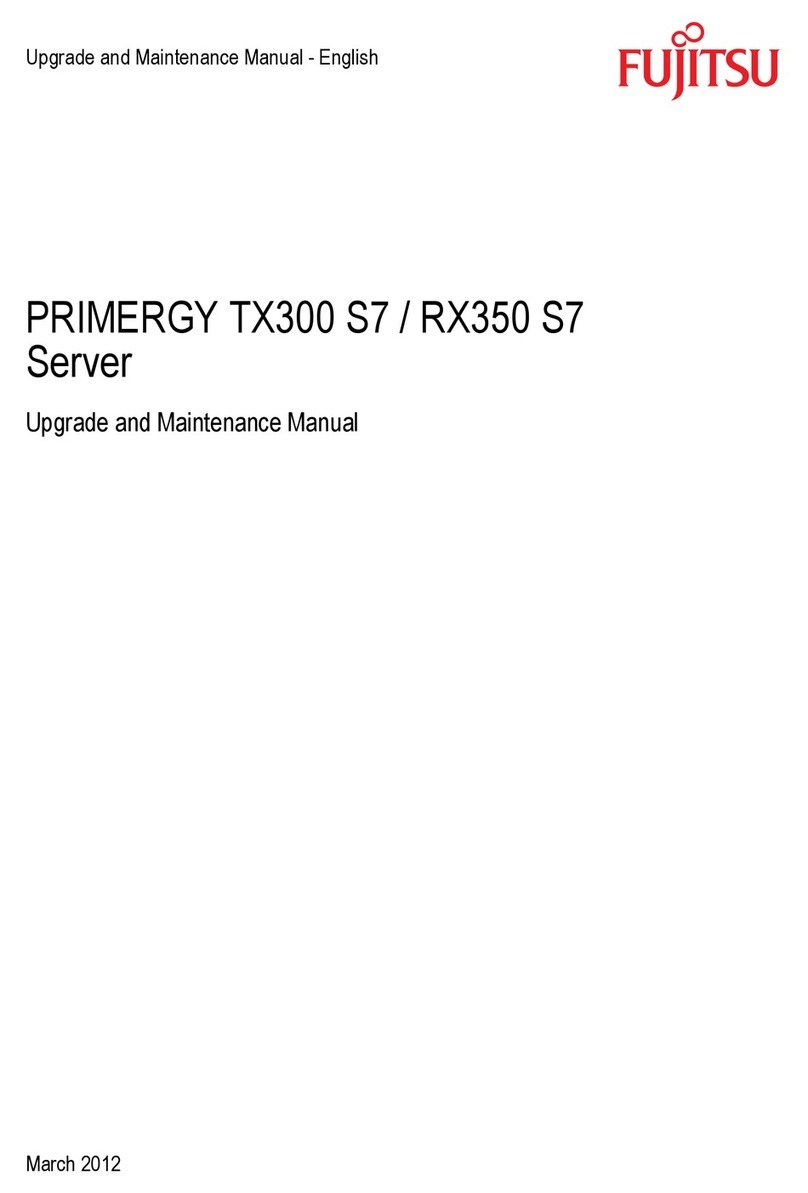
Fujitsu
Fujitsu PRIMERGY TX300 S7 Upgrade and maintenance manual
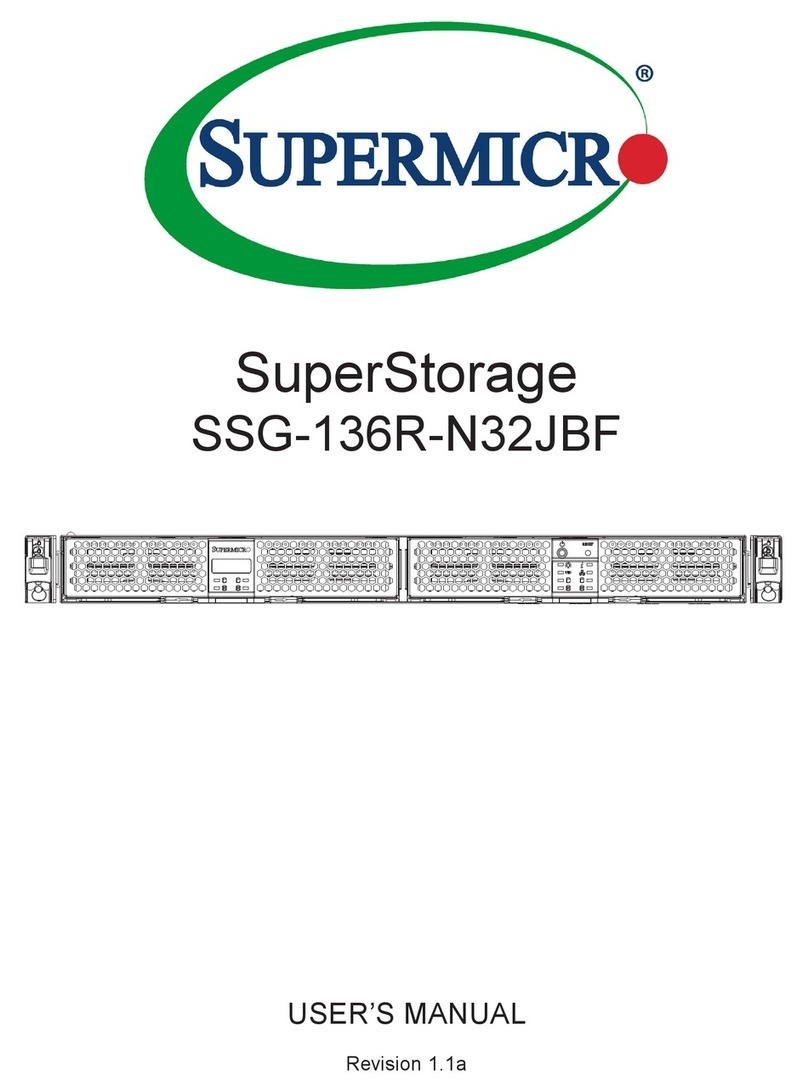
Supermicro
Supermicro SuperStorage SSG-136R-N32JBF user manual

Intervoice
Intervoice Neoware m100 - Mobile Thin Client installation guide

HP
HP HP3000/9x9KS I/O Upgrade Manual
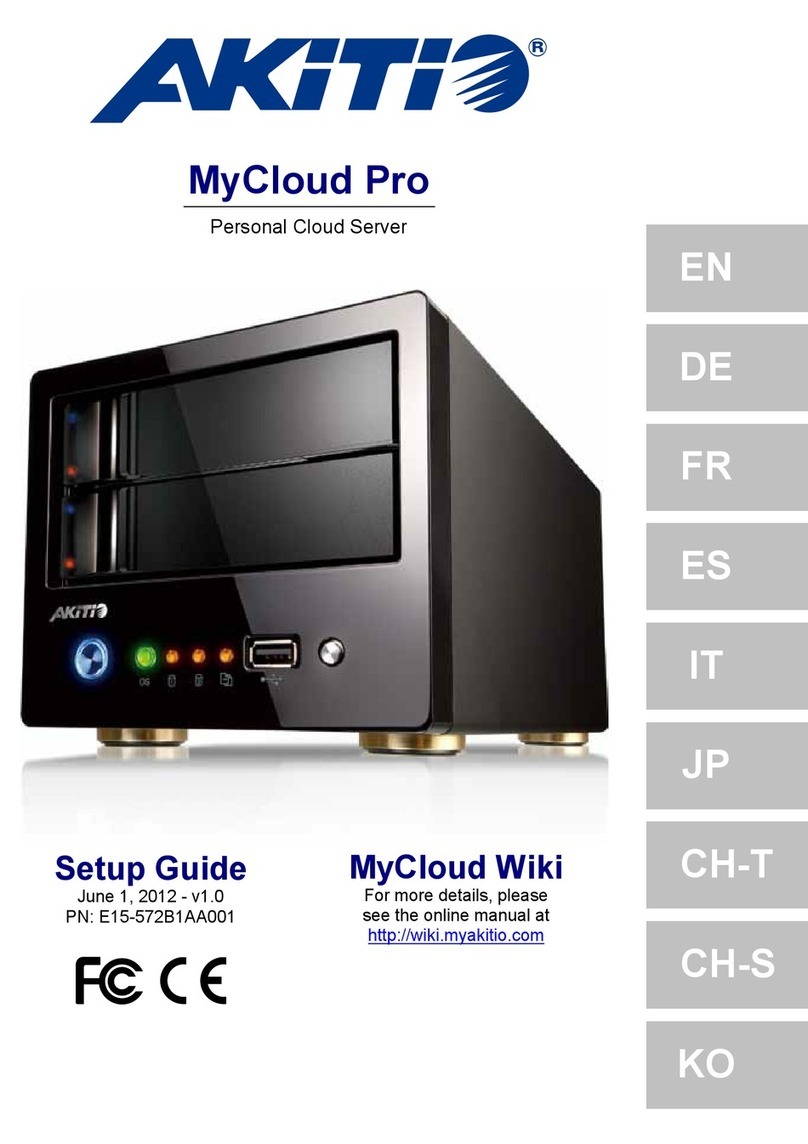
Akitio
Akitio MyCloud Pro Setup guide