Kidde FENWAL 35-71 Series User manual

FEATURES
n
3 Enclosure Configurations
n
Case and Cover - dust and foreign object protection
n
Open Board with Stand-offs - saves space and cost
n
Potted - protection for washdown and exteme vibration
n
Full-time power option
n
Integral Blower Relay
n
2 Wiring Options – 1/4” quick connects and multi-pin connector
n
2 Trial For Ignition Options - 1 and 3 trial
n
4 Trial For Ignition Times - 4, 7, 10 and 15 seconds
(customized timings available)
n
2 Flame Sense Options – single spark and sense
and remote sense
n
Diagnostic LED - 3 error codes for accurate troubleshooting
n
Flame Current Test Pins - instant access to circuit
for troubleshooting
n
Polarity Insensitive – reduces chance of miswiring
APPLICATIONS
n
Construction and Agriculture Heaters
n
Crop Dryers
n
Ceramic and Black Body Infrared Heaters
n
Commercial Cooking Equipment
n
Any 120 VAC Gas Burner Application under 400K BTU
DESCRIPTION
The 35-71 is a 120 VAC direct spark ignition control with
blower relay for controlling a gas valve, controlling and
monitoring combustion air-flow and igniting LP or natural gas
for construction heaters, infrared heaters, crop dryers,
commercial cooking equipment and gas burner applications
that provide a 120 VAC operating signal.
The microprocessor circuit design provides precise, repeatable
timing sequences for ignition times and purge times (pre-,
inter- and post-) as well as multiple tries for ignition, 1 hour
automatic reset and flame sensing during pre-, inter- and post-
purge. The control continually monitors the pressure switch,
thermostat and main burner flame to ensure safe system
operation. The on-board diagnostics with LED output provide
assistance with troubleshooting to ensure safe and efficient
burner operation.
Agency Certifications
Recognized under the Component Program of Underwriters Laboratories
Inc., UL 372, UL 1998 Software
Design certified by CSA International, CAN C22.2 #199-M89
and ANSI Z21.20 Automatic Ignition Systems
SERIES 35-71
120 VAC Direct Spark Ignition Control with
Combustion Blower Relay - Microprocessor Based
THE TOTAL SOLUTION FOR
GAS IGNITION CONTROL
Fenwal offers a complete range of ignition
control products including:
nIgnition Controls
nSpark and Flame Sense Electrodes
nSpark and Flame Sense Cables
nWiring harnesses
Designed, developed and
manufactured by Fenwal,
these components integrate
seamlessly providing
maximum system performance.
Getting Started - Samples
To ensure proper system design and operation, Fenwal provides
sample ignition controls, high-voltage wires and electrodes for trial
and evaluation at no charge. To get you started quickly, Fenwal has
identified our most popular ignition controls, see Page 8. Whether
it is an individual control, complete start-up kit or customized control,
Fenwal is ready to provide your gas ignition solution.
Fenwal Ignition Development Center
Send your equipment to us and we’ll design, install and qualify a
control to meet your exact application requirements. Fully equipped
and staffed with trained technicians, the Fenwal Ignition Development
Center has proven extremely beneficial for many customers focused
on product quality and reducing time-to-market for their appliances.
35-71-01
Series 35-71, 120 VAC Direct Spark Ignition Control Page 1
www.fenwalcontrols.com 1-800-FENWAL-1

Start up - Heat Mode
120 VAC is supplied to the L1 terminal, either from a thermostat or other control
device. When this occurs the control will power up and perform a self-check
routine and if selected, begin a pre-purge. Following the pre-purge, the gas valve
is energized and sparks commence until flame is detected or the Trial for Ignition
(TFI) period expires.
When flame is detected, the spark is shut off and the gas valve and combustion blow-
er remain energized. The thermostat, pressure switch and main burner
flame are constantly monitored to ensure that the system is functioning properly.
When the thermostat is satisfied and the demand for heat ends, the gas valve
is de-energized immediately and a post-purge is initiated (optional) and the
flame is extinguished. When the post purge is complete, the combustion blower
is de-energized.
System Response to Flame Failures
Fenwal controls are configured with several options for managing loss of flame.
Failure during TFI Period
SINGLE TRIAL MODEL
Should the burner fail to light or flame is not detected during the
TFI period, the gas valve is de-energized and the control will go into
lockout mode.
MULTI TRIAL MODEL
Should the burner fail to light or flame is not detected during the
first TFI period, the gas valve is de-energized and the control will
attempt two additional ignition trials with inter-purge. If these
attempts are unsuccessful, the control will go into lockout mode.
Failure of Established Flame -Two Options
There are two methods for re-starting the burner after loss of established flame.
The Re-ignition option is the default configuration for re-establishing flame and
does not need to be specified when ordering. If the Recycle option is desired,
please specify this when ordering so that a special part number is assigned to
the control by Fenwal.
RE-IGNITION
If the established flame signal is lost, the control responds and begins
sparking within 0.8 seconds of loss of flame. This is considered the first
re-ignition attempt. The spark will be energized for the duration of the
TFI period in an attempt to re-light the burner. If flame is re-established,
normal operation resumes.
SINGLE TRIAL MODEL
If the burner does not light after the first re-ignition attempt, the
control will de-energize the gas valve and go into lockout mode.
MULTI TRIAL MODEL
If the burner does not light after the first re-ignition attempt, the inter-
purge sequence is completed between the next two attempts to re-light
the burner. If the burner fails to light after the third attempt, the control
will de-energize the gas valve and go into lockout mode.
RECYCLE
If the established flame signal is lost, the control responds
by shutting off the gas valve within 0.8 seconds.
SINGLE TRIAL MODEL
The control will begin the ignition cycle with the pre-purge cycle,
if a pre-purge cycle is programmed into the control. Controls without
pre-purge immediately commence sparking for one TFI period. If flame
is re-established, normal operation resumes. If the burner fails to light
after the first try, the control will de-energize the gas valve and go into
lockout mode.
MULTI TRIAL MODEL
The control will begin the ignition cycle with the inter-purge sequence
and attempt three tries for ignition including inter-purges. If flame is
re-established, normal operation resumes. If the burner fails to light
after the third try, the control will de-energize the gas valve and
go into lockout mode.
NOTE: The Recycle feature option requires a special part number that
is determined by contacting Fenwal.
Combustion Air Flow Monitoring
In normal operation, the control monitors the combustion air flow by reading
the pressure switch (PSW) input to confirm that the blower is operating in the
proper sequence. Initially, the control checks the PSW input to be sure that
it is open. Once the blower is energized and the PSW closes the control
proceeds to trial for ignition.
If during a call for heat 120 VAC power is present at the PSW input prior to
the blower being energized, the control will wait 30 seconds, for the condition
to change. Possible reasons for this condition includes a stuck or mis-wired
pressure switch, or the blower is spinning down and keeping the switch closed.
If the condition does not change, an airflow fault will be declared and the LED
will flash the one flash pattern.
If the combustion blower is energized and the PSW does not close within
30 seconds, an airflow fault will be declared and the LED will flash the one-
flash pattern. The blower will remain energized until the condition changes.
If the PSW signal is lost while the burner is firing, the control will immediately
de-energize the gas valve and the combustion blower will remain on. If the
call for heat remains and the PSW signal returns within 30 seconds, the control
will restart with the pre-purge period. If the PSW input does not return within
30 seconds, the blower remains on and LED will flash the one-flash code
indefinitely. If the PSW closes, the LED stops flashing and the control resumes oper-
ation with the pre-purge function.
Lockout Mode (On-Board Safety System)
After single or multiple attempts to light the burner have failed or flame is not estab-
lished, the control automatically enters lockout mode. The control will not open the
gas valve unless there is intervention by the user or one hour has
passed depending on the model chosen. See Lockout Recovery.
Lockout Recovery - Two Options
There are two options for recovering from lockout mode. When selecting
the control, please specify one of the following methods for lockout recovery.
1. Thermostat/ Power Off Reset- requires the user to reset the thermostat below
ambient temperature or remove the 120 VAC power supply for 5 seconds.
The control will start the ignition sequence and attempt to light the burner again.
2. Automatic Reset - After one hour, if the thermostat is still calling for heat, the
control will automatically start the ignition sequence and attempt to light the
burner again.
Benefits of Full Time Power
1. Separate 120 VAC input for ignition control operation and combustion blower
operation. Allows high current to feed the blower directly rather than have it
pass through the thermostat.
2. Sense flame even with zero second pre-purge to provide safe operation.
Control will monitor flame presence immediately upon a call for ignition.
3. Post purge blower operation to clear the combustion chamber and remove
remaining heat when the call for heat has ended.
4. If a flame is detected during pre-, inter- or post-purge, the combustion
blower will be energized. Should the main valve later close and the flame
signal disappear, the combustion blower will be de-energized.
Page 2 Series 35-71, 120 VAC Direct Spark Ignition Control
SEQUENCE OF OPERATION / FLAME RECOVERY/ SAFETY LOCKOUT
www.fenwalcontrols.com 1-800-FENWAL-1

TROUBLESHOOTING GUIDE
LED Indication
Steady on
1 Flash
2 Flashes
3 Flashes
Fault Mode
Internal Control Failure
Airflow Fault
Flame Fault**
Ignition Lockout Fault
MOUNTING AND WIRING
The 35-71 is not position sensitive and can be mounted vertically or
horizontally. The control may be mounted on any surface and fastened
with #6 sheet metal screws. Secure the control in an area that will
experience a minimum of vibration and remain below the maximum
ambient temperature of 80°C (175°F).
All connections should be made with UL approved, 105°C rated, 18 gauge,
stranded, .054” thick insulated wire. Refer to the appropriate wiring
diagram when connecting the 35-71 to other components in the system. High
voltage spark cables and control wiring harnesses are detailed on
Pages 5 and 6.
Series 35-71, 120 VAC Direct Spark Ignition Control Page 3
1/4”
3/16”
1/4”
3/16”
3/16”
1/4”
1/4”
1/4”
3/16”
1/4”
Alarm
Valve Power
Pressure Switch
120 VAC Neutral
Valve Neutral
120 VAC Input (Hot)
Inducer Output
Thermostat Input
Burner Ground
Remote Flame Sensor
Flame Sense Test Pins
NC
V1
PSW
L2
V2
L1
IND
TH
B.GND
S1*
FC+, FC-
11
10
9
8
7
6
4
3
2
1
Blue
Brown
Orange
White
Yellow
Black
White/Black
Red
Purple
Gray
TERMINAL DESCRIPTION
MULTI-PIN
CONNECTOR
P/N: AMP 1-644615-1
QUICK
CONNECT
TERMINAL
SIZE
Terminal Designations
PIN
LOCATION
WIRE
COLOR
2 Pin Header
(AMP P/N: 640383-2, Molex P/N: 26-60-2020)
CAUTION: Label all wires prior to disconnection when servicing the
control. Wiring errors can cause improper and dangerous operation.
A functional checkout of a replacement is necessary to prevent porperty
damage and/or personal injury or death.
*On controls configured for single spark and sense with quick connects,the S1
terminal is removed. On controls configured for single spark and sense with
multi-pin connector, leave S1 wire, pin 1, color gray unconnected.
Input Power
Input Current Drain
Gas Valve Rating
Combustion Blower Rating
Operating Temperature
Flame Sense Voltage
Flame Sense Current
Flame Failure Response Time
Type of Gas
Spark Rate
Moisture Resistance
Size (LxWxH)
Weight
102 to 138 VAC, 50/60 Hz
350mA @ 120 VAC, 60 Hz
1.5A @ 120 VAC
3.0 FLA @ 120 VAC
-40°F to +175°F, -40°C to +80°C
120 VAC
1.0 microamp minimum
0.8 seconds maximum
Natural, LP and manufactured
Line frequency (50/60 Hz)
Conformal coated to operate to 95% R.H.
See drawings on Page 8
Integral stand-offs: 7.1 oz
Potted: 14.3 oz Case and Cover: 10.1oz
SPECIFICATIONS
The LED will flash on for 0.2 seconds then off for 0.2 seconds to indicate an
error condition. The pause time between error codes will be 2.5 to 3.0 seconds.
During power-up, the LED will light for one second and then turn off to indicate
normal operation.
ON-BOARD DIAGNOSTICS
** May indicate either that a flame was detected during pre-, inter- or post-purge,
or that there is a flame sensing error.
WARNING: Operation outside specifications could result in failure of
Fenwal product and other equipment with injury to people and damage
to property and even death.
PIN LAYOUT
FULL TIME POWER
NO FULL TIME POWER
Single
Spark
and
Sense
Remote
Sense
On controls without full time
power the TH terminal is not
used and L1 becomes the
T’stat or control device input.
www.fenwalcontrols.com 1-800-FENWAL-1
Symptom
Control will not start up
Gas Valve on and
no spark during TFI
Spark on and gas valve
off
Flame during TFI but no
flame sense after TFI
Call for ignition, but
combustion blower
doesn't start up
Pressure switch operating
properly, but no TFI after
purge period
Recommended Actions
A. Check for 120VAC at L1 and/ or TH
B. Check fuse/ circuit breaker
C. Check thermostat on and set above ambient
D. Red LED steady on. Reset power. Replace
control if LED remains on.
A. Shorted electrode - re-establish 1/8" gap
B. Check that bracket is making a solid
ground connection
C. Check connection at each end of high
voltage cable
A. Check for 120VAC at V1
B. Check wiring to V1 and V2
C. Valve coil malfunction
A. Check that the spark electrode/ flame
sensor are in the flame
B. Poor ground at the burner
C. Low flame current - check flame current
using test pins on the control
A. Check for 120VAC at L1 and TH
B. Check for 120VAC at IND, should be on if
pressure switch is operating properly
C. Check that the pressure switch has been
wired properly
D. Pressure switch failed off or on (1 LED Flash)
E. Check blower fan assembly
A. Flame was detected during purge period
(2 LED Flashes)
B. Check for 120VAC at L1 and TH
C. Check for 120VAC at IND, should be on
if pressure switch is operating properly

+
-
HIGH TEMP
MATERIAL
CSA rated at 2500°F
Steel Cu Flashed
Nickel Plated Steel
Nickel Plated Steel
Alumina
Alumina
Spring Steel
Kanthal APM
Kanthal APM
Kanthal APM
ACCESSORIES
Proper Electrode Location
Proper location of the electrode assembly is important for
optimum system performance. It is recommended that the
electrode assembly be mounted temporarily using clamps or other
suitable means to check the system before permanently mounting
the assembly. The electrode assembly should be located so that
the tips are inside the flame envelope and about 1/2 inch (10 mm)
above the base of the flame. See Figures 3a and 3b.
CAUTIONS:
1. Ceramic insulators should not be in or close to the flame.
2. Electrodes should have a gap spacing of 0.125± 0.031 inch
(3.12 ± 0.81 mm). If this spacing is not correct, the assembly
must be replaced or adjusted (see troubleshooting)
3. Exceeding the temperature limits can cause
nuisance lockouts and premature electrode failure.
4. Electrodes must be placed where they are not exposed
to the appliance user in normal operation.
Flame Sensing
Flame sensing is achieved using the principal of flame
rectification. Flame rectification relies on the current passing
from ground through the flame to the sense rod. The minimum
flame current necessary to keep the system operating is
1.0 microamperes.
SINGLE SPARK AND SENSE
Figure 3a
REMOTE FLAME SENSE
Figure 3b
ITEM
#
1
2
3
4
5
6
7
8
9
DESCRIPTION
Mounting Bracket
1/4” Q.C. High Voltage Terminal
3/16” Q.C. Flame Sense Terminal
Spark, H.V. Ceramic Tube
Sense Electrode Ceramic Tube
Press Ring
Flame Sense Electrode
Ground Rod
Spark Electrode, High Voltage
STANDARD
MATERIAL
CSA rated at 1800°F
Steel Cu Flashed
Nickel Plated Steel
Nickel Plated Steel
L-3 Steatite
L-3 Steatite
Spring Steel
Kanthal D
Kanthal D
Kanthal D
#
!
1
2
3
4
6
7
5
8
9
TYPICAL SPARK ELECTRODE
WITH INTEGRAL REMOTE FLAME SENSE
Page 4 Series 35-71, 20 VAC Direct Spark Ignition Control
Figure 4
FLAME CURRENT CHECK: SINGLE SPARK & SENSE AND
REMOTE SENSE
To measure flame current, disconnect the input voltage, and attach
the leads from a DC current meter with a microampere range to
FC+ and FC- terminals to the 35-70 flame sense test pins per
Figure 4. Reconnect the input voltage and initiate a
call for heat. After sparking is complete and the flame is
established the meter should read 1.0 microamperes DC or
higher. If meter reads below "0" on the scale, meter leads are
reversed. Disconnect power and reconnect meter leads
for proper polarity.
www.fenwalcontrols.com 1-800-FENWAL-1

Electrode Assemblies
With over 1,000 configurations of spark electrodes and flame sense rods, Fenwal has a design for almost any application. The latest
state-of-the-art wire forming and assembly equipment is used to accurately and efficiently produce high quality electrodes that deliver the
hottest spark. The "Universal" electrodes depicted below are just a sampling of the 1,000 electrode styles available. These electrodes
are designed for on-site customization. Cut and bend these to fit your application and then send the formed electrode back for Fenwal to
detail or send us a print and we will provide you with a quote and samples.
Part Number: 22-100000-593
Part Number: 22-100001-076
Part Number: 22-100001-117
Part Number: 22-100001-025
SINGLE SPARK AND SENSE WITH INTEGRAL FLAME SENSE ELECTRODES
SINGLE SPARK AND SENSE ELECTRODES
Series 35-71, 120 VAC Direct Spark Ignition Control Page 5
www.fenwalcontrols.com 1-800-FENWAL-1
(FLAME SENSE
ELECTRODE)
(HIGH VOLTAGE
ELECTRODE)
(FLAME SENSE
ELECTRODE)
(HIGH VOLTAGE
ELECTRODE)

Control Wire Harness
Select the proper harness (6 or 7 PIN) based on flame sense choice. Once the terminal configuration is determined, complete the part num-
ber by replacing the last two digits (“XX”) with the length in inches (“L” dimension). Standard wire lengths are 12, 18, 24, 30, 36, 48, and 60
inches. Example: 05-129892-118 = 18 inches. For other lengths, please contact Fenwal.
SPECIFICATIONS: Voltage Rating Agency Rating Temperature Rating Diameter Jacket Material
All Wires 600 V UL/CSA Listed 105°C (221°F) 18 gage stranded PVC
Gray Only 600 V UL/CSA Listed 200°C (392°F) 18 gage stranded PVC
Electrode Assemblies continued
REMOTE SENSE
Part Number: 05-129864-7XX
Part Number: 05-129864-8XX
Part Number: 22-100001-080
Part Number: 22-100001-110
Part Number: 05-129864-4XX Part Number: 05-129864-3XX
SINGLE SPARK SENSE
REMOTE FLAME SENSE ELECTRODES
To make your own harness select AMP connector housing P/N: 1-770849-1 and AMP housing terminal P/N: 770522-1
To make your own harness select AMP connector housing P/N: 1-770849-1 and AMP housing terminal P/N: 770522-1
1/4” FEMALE Q.C. -
FULLY INSULATED
Page 6 Series 35-71, 120 VAC Direct Spark Ignition Control
1/4” FEMALE Q.C. -
FULLY INSULATED
www.fenwalcontrols.com 1-800-FENWAL-1
1.094 +.015

Series 35-71, 120 VAC Direct Spark Ignition Control Page 7
www.fenwalcontrols.com 1-800-FENWAL-1
1. SILICONE RUBBER SUPRESSION TYPE: Resistive carbon coated fiberglas core prevents spark energy radiation from interfering with
other electronic systems. Select this wire type for applications where wire lengths are less than 36” and noise is a major concern.
SPECIFICATIONS: Voltage Rating Agency Rating Temperature Rating Diameter Jacket Material
25 KVDC SAE J2031 200°C (392°F) 7mm (.27”) Silicone Rubber
over Fiberglas Braid
Part Number: 05-129608-0XX Part Number: 05-129608-2XX Part Number: 05-129608-6XX
1/4” FEMALE Q.C. WITH SILICONE RUBBER BOOT
RIGHT ANGLE SPARK PLUG
WITH SILICONE RUBBER BOOT
High Voltage Ignition Wire - 3 Types
Part Number: 05-127613-2XX Part Number: 05-129865-0XX Part Number: 05-125948-0XX
Part Number: 05-129867-0XX
Delivering the 15K to 25K volts of spark energy from the ignition control to the electrode is a vital element of an ignition system.
There are 3 material options and multiple terminal configurations available. Shown are the most popular versions offered by Fenwal.
To ensure maximum spark energy, it is recommended that the ignition wires not be longer than 36”. Longer lengths are available
and should be evaluated on the appliance to determine if there is sufficient spark energy to consistently light the burner under
all conditions. Once the wire type and terminal configurations are determined, complete the part number by replacing the last two
digits (“XX”) with the length in inches (“L” dimension). Standard wire lengths are 12, 18, 24, 30, 36, 48 and 60 inches.
Example: 05-129608-018 = 18 inches. For other lengths, please contact Fenwal.
1/4” FEMALE Q.C. -
FULLY INSULATED
BOTH ENDS
1/4” FEMALE Q.C.
BOTH ENDS
RIGHT ANGLE SPARK PLUG WITH
SILICONE RUBBER BOOT
1/4” FEMALE Q.C.
TERMINATIONS SAME AS TYPE 1
Part Number: 05-129866-0XX Part Number: 05-129866-1XX
3/16”FEMALE Q.C.
FULLY INSULATED
1/4”FEMALE Q.C.
FULLY INSULATED
1/4” FEMALE Q.C. FULLY INSULATED
BOTH ENDS
2. SILICONE RUBBER COPPER CONDUCTOR TYPE: Low resistance copper conductor transmits maximum spark energy. Select this
type when maximum energy or longer wire lengths are required and noise is not a major concern.
SPECIFICATIONS: Voltage Rating Agency Rating Temperature Rating Diameter Jacket Material
25 KVDC UL Type 3257 250°C (482°F) 7mm (.27”) Silicone Rubber
3. TEFLON INSULATED TYPE: Low resistance copper conductor transmits maximum spark energy. Select this type
for applications that have tight clearances and sharp bend radii.
SPECIFICATIONS: Voltage Rating Agency Rating Temperature Rating Diameter Jacket Material
25 KVDC UL Type 1911 250°C (482°F) 2mm (.08”) Teflon
4. FLAME SENSE WIRES: Spark electrodes with integral remote sense rod, i.e. 22-100001-076, have a 3/16” male q.c..
Please choose flame sense wire 05-129866-0XX. For remote flame sense rods , i.e. 22-100001-080, choose flame sense
wire part number 05-129866-1XX.
SPECIFICATIONS: Voltage Rating Agency Rating Temperature Rating Diameter Jacket Material
600 V UL/CSA Listed 200°C (392°F) 18 gage stranded PVC

Inter-purge
Time (seconds)
0
l
30
l
l
l
l
60
l
Post
Purge
Assemblies
8 = Assemblies (may consist of control, high voltage ignition wire,
electrode and harness)
Non-Standard Configurations
9 = Non Standard Configuration
A 9 in this location of the part number (i.e. 35-725 -113) identifies this
configuration as a non-standard design. The part number does not follow the
part numbering system. The 9XX is a sequential part number assigned by Fenwal.
Consult factory for operating characteristics of this control.
Enclosure Configurations
and Wiring Options
2 = Potted Multi-Pin Connector (Figure 4)
3 = Case and Cover Multi-Pin Connector (Figure 6)
4 = Integral Stand-off’s Multi-Pin Connector (Figure 5)
5 = Case and Cover Quick Connect (Figure 3)
6 = Integral Stand-off’s Quick Connect (Figure 2)
7 = Potted Quick Connect (Figure 1)
Case
l
l
l
l
Multi-
Pin
l
l
l
Auto
MOST COMMON CONFIGURATIONS
Fenwal offers any option variation listed in the above part number scheme along with customized configurations to meet your exact application
requirements. Because of the numerous options available, models not listed in the table below are made to order. For quick-ship samples and
quick-ship orders, please select a model from the table below. All controls listed below are Full Time Power Models.
HOW TO ORDER
901
Trial for Ignition
Time (TFI)
1 = 4 seconds
3 = 7 seconds
5 = 10 seconds
7 = 15 seconds
Pre-Purge
Time
0 = None
1 = 15 seconds
2 = 30 seconds
5 = 5 seconds
Inter-Purge
Time
0 = None
1 = 15 seconds
2 = 30 seconds
Number of Ignition Trials,
Flame Sense Method and Lock Out Reset Method
0 = 1 try, single spark and sense Thermostat / power off reset
1 = 1 try, remote sense Thermostat / power off reset
2 = 1 try, single spark and sense Automatic reset
3 = 1 try, remote sense Automatic reset
5 = 3 try, single spark and sense Thermostat / power off reset
6 = 3 try, remote sense Thermostat / power off reset
7 = 3 try, single spark and sense Automatic reset
8 = 3 try, remote sense Automatic reset
X X X
35 - 71 5 - X X X
400 MAIN STREET, ASHLAND, MA 01721
TEL: (508) 881-2000
FAX: (508) 881-6729
www.fenwalcontrols.com
These instructions do not purport to cover all the details or variations in the equipment
described, nor do they provide for every possible contingency to be met in connection with
installation, operation and maintenance. All specifications subject to change without notice.
Should further information be desired or should particular problems arise which are not covered
sufficiently for the purchaser’s purposes, the matter should be referred to KIDDE-FENWAL,
Inc., Ashland, Massachusetts.
P/N 35-70-01 6/30/01
or
POTTED INTEGRAL STAND-OFF
Flame Sense
Method
Stand
Off
Potted
l
l
Q.C.
l
l
l
1
l
l
3
l
l
l
l
Single
l
l
l
Remote
l
l
l
Thermostat/
Power - off
l
l
l
l
l
l
0 15
l
l
l
l
30 5
l
l
47
l
l
l
l
l
10
l
15
35-715510-505
35-715325-113
35-715526-113
35-715331-503
35-715725-113
35-715226-113
Figure 1 Figure 2
Page 8 Series 35-71, 120 VAC Direct Spark Ignition Control
CASE AND COVER
Figure 3
or
0
l
l
15
l
l
l
l
30
Figure 4 Figure 5 Figure 6
© 2001 Kidde-Fenwal, Inc. Printed in U.S.A. CP
Combustion Blower Control,
Post-purge time and Power Options
0 = 0 second post-purge and no full-time power
1 = 0 second post purge with full-time power
2 = 30 second post purge with full-time power
3 = 60 second post purge with full-time power
Pre-purge Time
(seconds)
Lockout Reset
Method
Number of
Ignition Trials
Wiring
Enclosure Type
Ignition Control
Part Number
Trial for Ignition
Time (seconds)
www.fenwalcontrols.com 1-800-FENWAL-1
requires individual 120VAC inputs for blower and the thermostat which allows higher current to
feed the combustion blower without having the high current pass through the thermostat
requires single 120 VAC input for both blower and thermostat/ control device
This manual suits for next models
6
Table of contents
Other Kidde Controllers manuals
Popular Controllers manuals by other brands
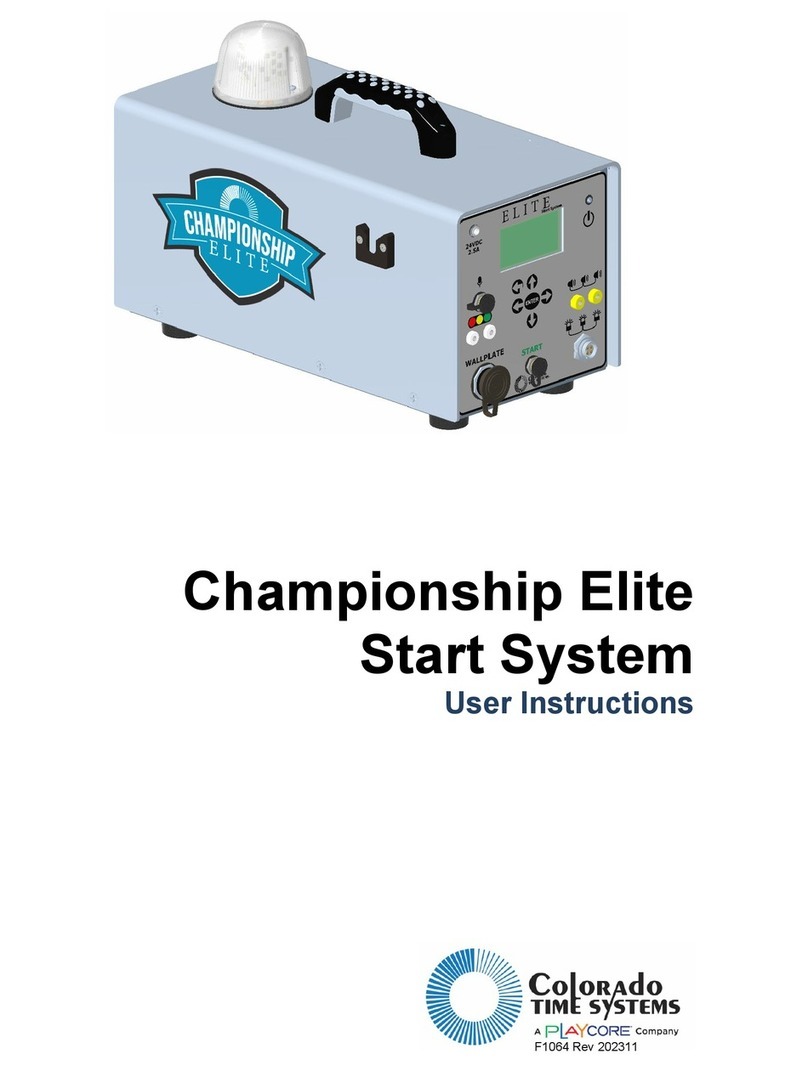
Playcore
Playcore Colorado Time Systems Championship Elite Start... User instructions
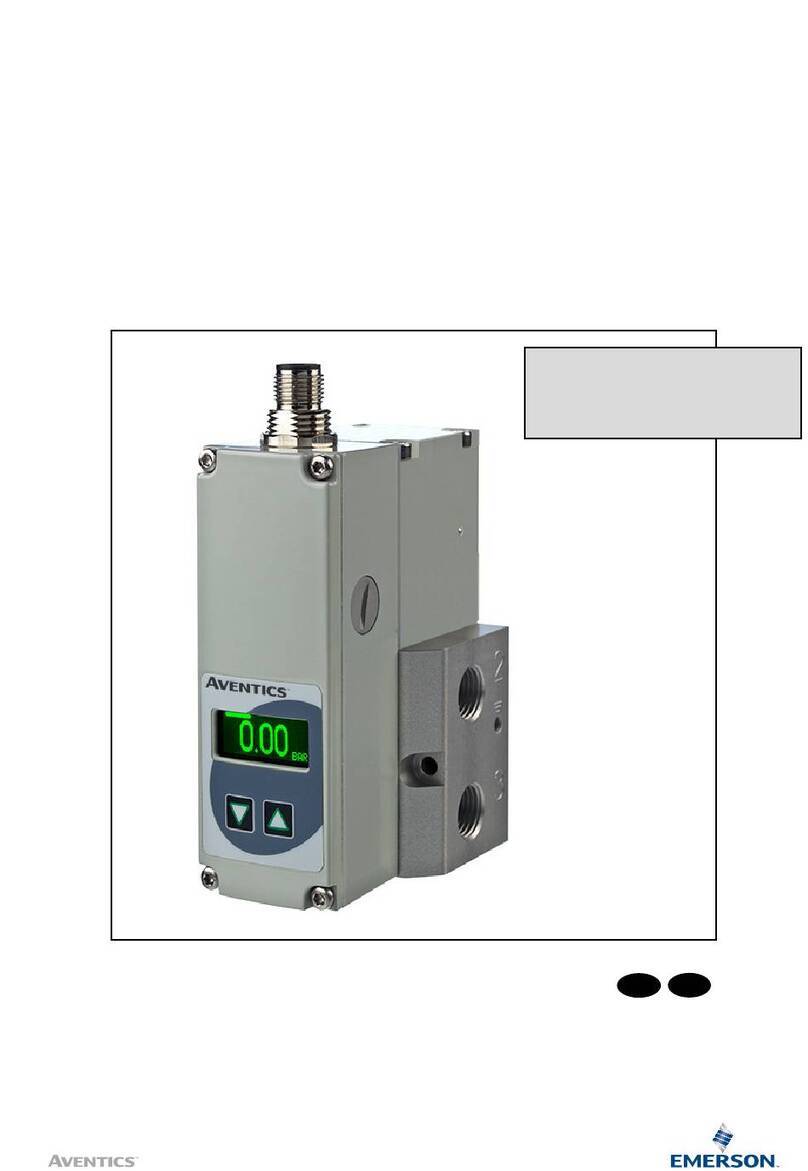
Emerson
Emerson Aventics 617 Series installation manual
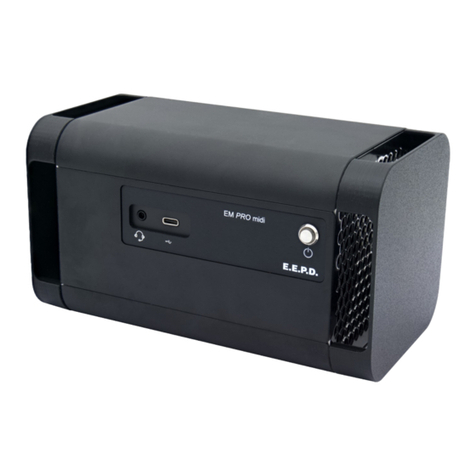
EEPD
EEPD EM PRO midi E Device Reference Manual
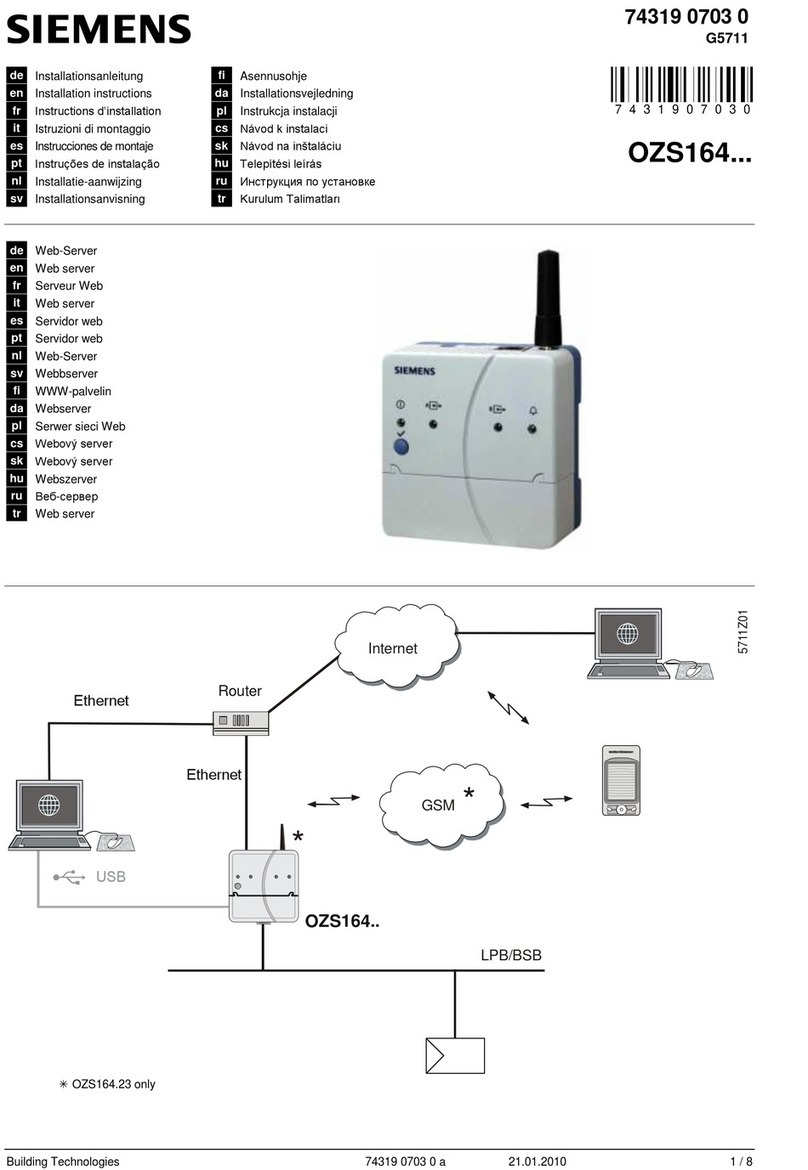
Siemens
Siemens OZS164 series installation instructions
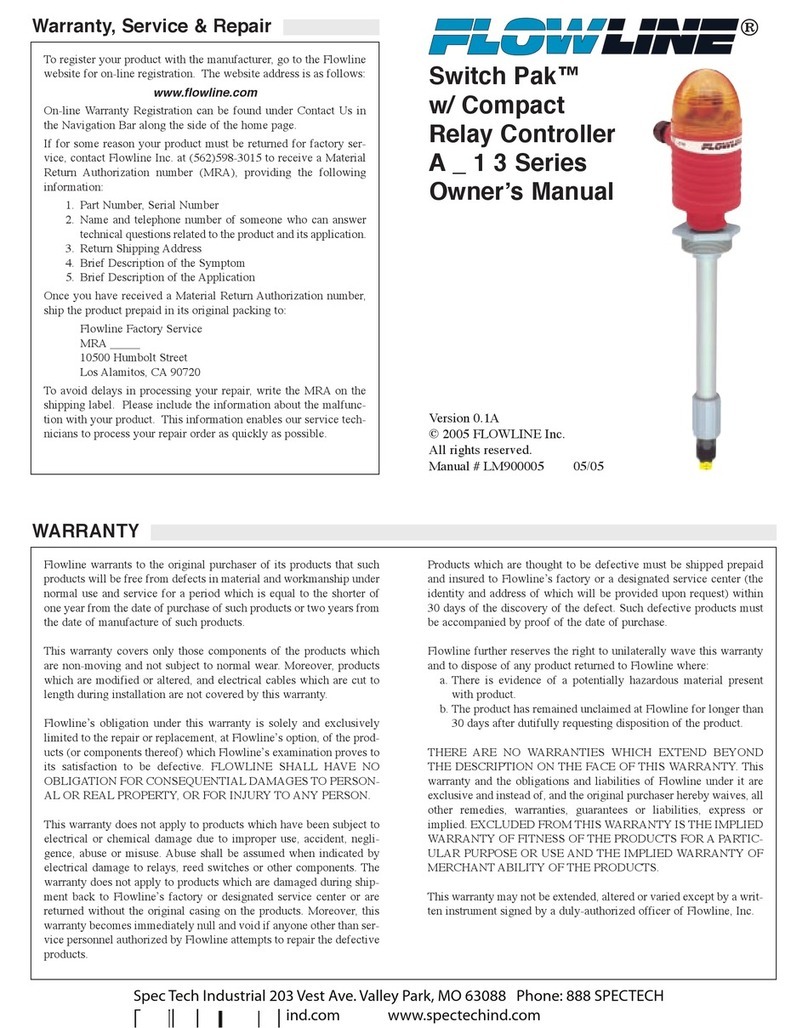
FlowLine
FlowLine Switch Pak A*13 series owner's manual

Soyal
Soyal AR-716E user guide
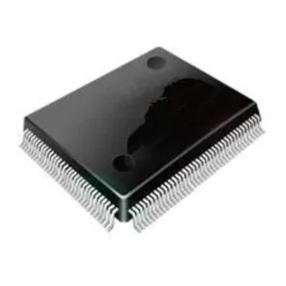
NXP Semiconductors
NXP Semiconductors MK30DX64VMC7 Reference manual
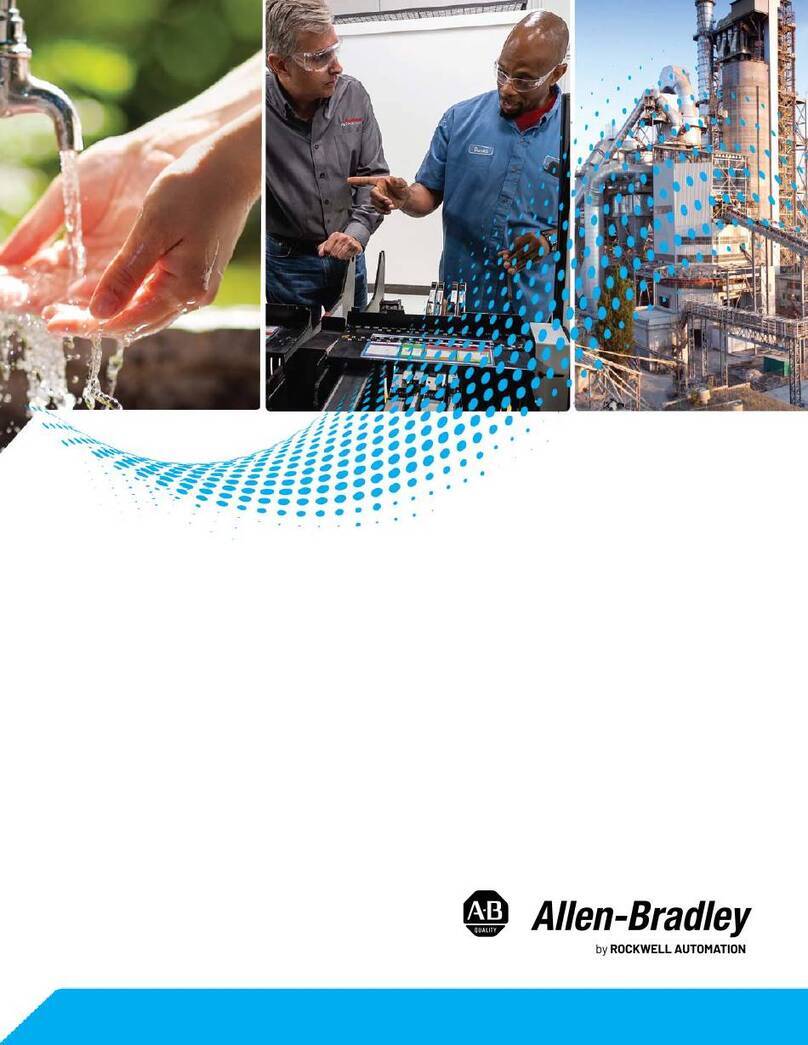
Rockwell Automation
Rockwell Automation Allen-Bradley Micro820 user manual
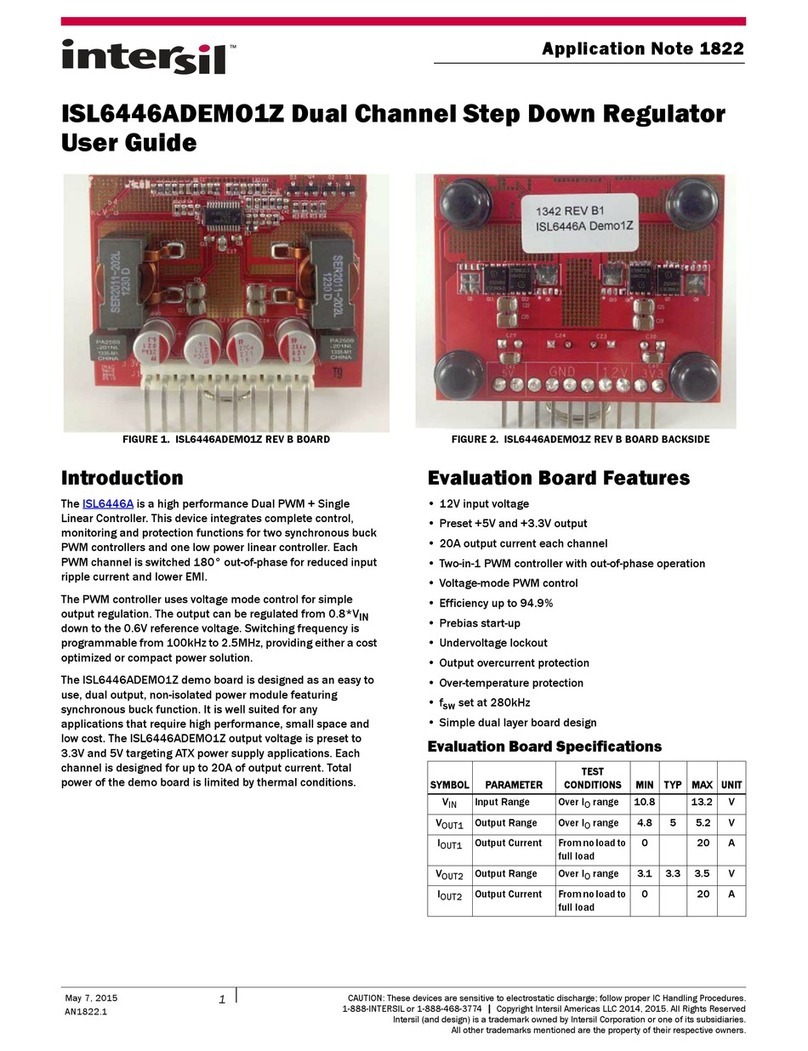
Intersil
Intersil ISL6446ADEMO1Z user guide
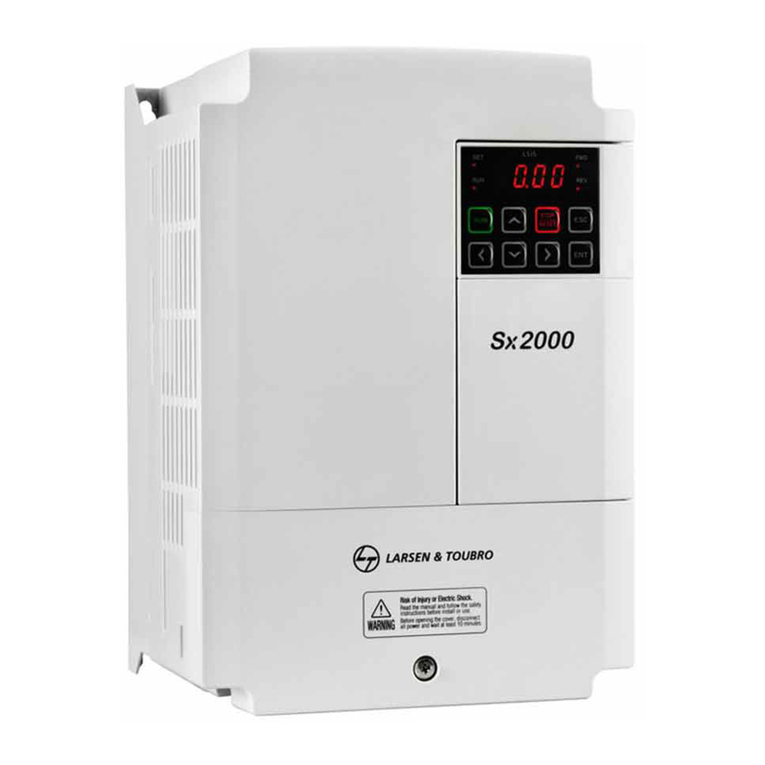
Larsen & Toubro
Larsen & Toubro C*2000 Series user manual
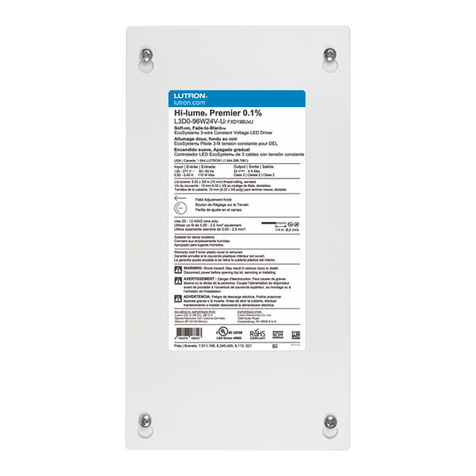
Lutron Electronics
Lutron Electronics LHD0-96W24V-U UL Installation

Vimar
Vimar EIKON 20593 manual