Klingenburg KR4 User manual

·KLINGENBURG
·KLINGENBURG
Rotor controllers
Type KR4 and KR7
Rotation controller for regenerative
heat exchangers
ENERGY RECOVERY

·KLINGENBURG 2
3
4
5
6
7
8
9
10
11
13
14
17
18
19
Table of Contents
General
What can the controller do?
Functions of the KR4 and KR7 basic controllers
Functions of the KR4 Z and KR7 Z controllers
with additional functions
Technical specifications KR4 / KR7 and KR4 Z / KR7 Z
Motor data
Terminal configurations of the KR4 / KR7 controllers
Terminal configurations of the KR4 Z / KR7 Z controllers
Hooking up KR4 und KR7 basic controllers
Hooking up KR4 Z und KR7 Z controllers
with additional functions
Ordering a controller
Putting in operation KR4 und KR7 basic controllers
Putting in operation KR4 Z und KR7 Z
controllers with additional functions
Summary of features
Safety and Warning Instructions
Page

·KLINGENBURG 3
General
The efficiency of regenerative heat exchangers can be adjusted
by means of the rotor speed.
The rotor speed can be adjusted by means of the KR controller
across the complete control range. For further performance
features see page 4.
The new KR controller is the fourth generation of a series of
controllers for regulating regenerative heat exchangers
developed by our company since 1979. Developments in
modern processing technology and our wish to make the
operating controls as simple as possible provided the impetus
for an extensive development programme.
Only two types are required for all rotor sizes:
KR4 = 400 Watt
rotor diameters smaller than 3760 mm
KR7 = 750 Watt
rotor diameters larger than 3760 mm
The KR controllers represent the latest standards for rotor
technology.
The controller is housed in an extruded aluminium case which
improves heat dissipation and increases mechanical stability.
The case also ensures good electric screening. More space
was provided for the wiring and the new configuration of the
terminals makes it easier to hook up the controller.
And of course all new industry standards have been taken into
account. The radio shielding incorporates the latest technology.
The rotor drive is effected through three-phase alternating
current motors which can be operated up to a rotor diameter of
1919 mm direct from the mains. Furthermore, an acceleration
and deceleration ramp must be utilised for the gears.
So, for the optimum control of the drive, the rotor controller KR
is required.

·KLINGENBURG 4
What can the controller do?
The KR4 and KR7 control units and their central component,
the frequency inverter, permit you to fully adjust the rotor
speed for the entire permissible range.
These control units can be utilised worldwide.
(With supply voltage 230V ~)
When designing these control units, all known regulations were
taken in consideration.
Quality features
·Latest processor technology
·CE conformity
·Casing IP 54
·Short-circuit-proof output
·EN 55011 tested
·EN 61000-3 tested
·EN 61000-4-2 tested
·EN 61000-4-4 (Burst) tested
·EN 61000-4-5 (Surge) tested
·EN 61800-3 tested
·Each single module is tested repeatedly
·exchangable info sheet
Optional features
The following functions can be selected by means of the
extended Z-controller:.
·Summer operation including display of function *)
-Enthalpy comparison
-Temperature comparison
-Temperature switching over
·supply air temperature control *)
·sequence switching register including function display
In this case the controller bears the model number KR4 Z or
KR7 Z. See page 13 for order codes.
*) The corresponding sensors must be installed for the control
features marked with an asterisk.
Performance features
·6 detailed fault display
·Thermal protection including function display
·Starting and running out switching
·Menu controlled programming
·Clear text display via LCD display
·Three push-button operation
·External control signal processing
·Self-cleaning function
·Rotor operation control *)

·KLINGENBURG 5
Functions of the KR4 and KR7 basic controllers
Self-cleaning operation
One result of the constant air flow in regenerative heat
exchangers is a very beneficial self-cleaning effect. As a result,
cleaning is not required in most cases. In case of doubt, please
consult us.
At times when the ventilation unit is running but the rotor
function itself is not required, it is still expedient to activate the
rotor periodically. The cleaning cycle can be set for 20, 40, 60,
80 or 100 minutes. In this manner smaller dirt deposits can be
cleaned away.
Speed display
You can calculate the speed of the rotor from the frequency.
80 Hz corresponds to approximately 10 rpm.
Rotation monitor
As the rotor turns, the rotation is monitored by a magnetic
proximity switch mounted inside the rotor case. A magnet
which is mounted on the circumference of the rotor reports the
rotation movement back to the controller. In case of a rotor
operation fault, e.g. the V-belt comes off, the fault contact
switches over from S1 to S2. The following error message then
appears on the display.
KR4 = 400 Watt forrotordiameterssmallerthan3760mm
KR7 = 750 Watt forrotordiametersbiggerthan3760mm
The electronics function test checks motor current and processor
operation. After starting the motor it checks the functions of the
motor.In addition it verifies for short circuits or earth faults.
In case of a fault the fault contact switches over from S1 to S2.
The error message appears on the display. (see page 16)
Example:
Operation mode: Manual operation
In manual operation mode you can determine by depressing
the selection push-button a fixed rotational speed.
Operation mode: External operation
By evaluation of a external control signal (0 - 20 mA, 4 - 20 mA or
0-10 V) the rotational speed is justified.
Hardware err:EXX
If the rotor stops turning, the reaction time of the controller will
vary between 0.5 and 3 minutes, depending upon the speed of
the rotor beforehand. The controller renews operation once the
error message has been acknowledged by pressing the three
buttons on the controller.
The function of the rotation monitor is not active at frequencies
£10 Hz.
The rotation monitor is a component of the basic controller. If
you require this function, you must order the magnetic
proximity switch and the installation set that comes with it
(KR4 R or KR7 R).
Runcontrol error

·KLINGENBURG 6
Functions of KR4 Z and KR7 Z controllers
with additional functions
1. Setting supply air temperature
The supply air temperature can be set to a value between 10-
40°C. The rotor speed increases and decreases until the
desired temperature is reached or until the rotor reaches its
minimum / maximum speed. A temperature sensor type PT
1000 is required in order to regulate the supply air temperature
(200 mm resp. 2000 mm).
Other temperature ranges require a special order.
2. Sequence switch
The sequencer is a change-over switch which allows you, e.g.,
to operate a downstream heat source in sequence with the
rotor. It ensures that the heating is switched on only if the rotor
is already turning. In this manner, you can be sure that the
heating is only being used as a residual heater. The heating
activation value is set under the menu item "Activation value". It
can be set to a value between 5- 100 % in 5%-steps. In the
center of the display a "#" indicates that the sequence switch
is activated.
3. Summer mode, Cooling mode
As you well know, your rotary heat exchanger is not only the
ideal solution for recuperating heat; it can also be used as a
"cooler". If the exhaust air in summer is cooler than the outer
air, the rotor can be used as a cost-saving cooling unit. By
running the rotor at full speed, it is possible to pre-cool the
outer air. The KR Z automatically tests whether the conditions
merit operating in summer mode. You can choose from
different versions of the summer operating mode:
3.1 Temperature comparison mode
In the temperature comparison mode, the KR Z decides when
to switch the rotor to cooling mode by comparing the
temperature of the outer air with that of the exhaust air. If the
exhaust air is cooler than the outer air, then the rotor can use
the outer air to cool the supply air. Two temperature sensors
are required for the temperature comparison mode.
3.2 Enthalpy comparison mode
In the enthalpy comparison mode, the KR Z decides when to
switch the rotor to cooling mode by comparing the total heat
content of the outer air with that of the exhaust air. If the
enthalpy of the outer air is higher than that of the exhaust air,
then the rotor can use the outer air to cool the incoming air.
Two enthalpy sensors are required for the enthalpy comparison
mode.
3.3 Outer temperature measurement
This method uses an adjustable reference value to decide
when to change over to summer mode. It is also referred to as
the change-over mode. When the outside temperature
surpasses the set value, the rotor switches to cooling mode.
The rotor then runs at maximum speed. The change-over mode
requires a temperature sensor to measure the outside
temperature.
The extended version with independent sensor evaluation bears
the number KR4 Z or KR7 Z.
The “Z” controler is extended by the following functions.
·Supply air temperature control
·sequence switch-heat register
·Summer operation mode

·KLINGENBURG 7
128
40
180
40
207
230
260
265
218
23 21 21 16 16
1616
21
21
23
£ 1419
1420-2379
2380-3759
³3760
90
180
370
750
230/400
230/400
230/400
230/400
0,37
0,60
1,20
2,00
F
F
F
F
IP 54
IP 54
IP 54
IP 54
0,64
1,05
2,07
3,46
(230 V) (400 V)
Technical specifications
KR4/KR7 and KR4 Z/KR7 Z
Motor data
DimensionsType KR4 KR7
Output: 0,4 kW 0,75 kW
Fuse: 6,3 A 10 A
Supply voltage: 220-240 V
Weight: 3200 g 3500 g
Operating temperature: -10°C - + 40°C
When operating temperatures
are below 0 °C, we recommend
that the motors be left off when the
power is first turned on to allow
the controller to warm up.
Supply air temperature: 10°C - 40°C
Other temperature ranges can
be specially ordered.
System of protection: IP 54
Output frequency: 0 - 80 HZ
Frequency resolution: 0,08 Hz
Control signals: 0 - 10 V, 0 - 20 mA, 4 - 20 mA
Fault contact: 230 V, 1 A
Power cord: A shielding power cord must
be used in all cases and if
longer than 15m, additional main
suppression filter should be
installed. Please ask for more
information.
Motor data
Rotor diameter
[mm]
Performance
[W]
Supply voltage
[V]
Max. current consumption [A] Isolation class Type of protection

·KLINGENBURG 8
{
{
0 - 10 Volt
0 - 20 mA
4 - 20 mA
PE
PE
PE
N
L1
S3
S2
S1
{
{
W
V
U
{
+
+
-
-
10
8
7
6
5
4
3
2
1
9
{
{
Terminal configuration of the KR4 / KR7 controller
black
brown
blue
Thermal protection relay - motor
control unit release
(potential free contact)
Rotation monitor
Three-phase motor
(3x230 Volt)
Error message
During operation S1 and S3 closed
By occurring of defects or net failure
S2 and S3 closed
Mains (230 Volt) 50 - 60 Hz
There is a supply voltage
of 24 V on the contacts 5, 7, 9
10 Volt power supply
External control signal 0 - 10 V, 0 - 20 mA
Jumper

·KLINGENBURG
+
-
10
8
7
6
5
4
3
2
1
9
{
9
{
{
0 - 10 Volt
0 - 20 mA
4 - 20 mA
26
24
23
22
21
20
19
18
17
25
-
S
+
-
S
+
-
+
-
S
{
{
{
{
PE
PE
PE
N
L1
S3
S2
S1
{
{
W
V
U
{
{
16
15
14
{
13
12
11
Terminal configuration of the KR4 Z / KR7 Z controller
black
brown
blue
Thermal protecton relay - motor
Rotation monitor
External control signal 0 - 10 V, 0 - 20 mA
Three-phase motor
(3x230 Volt)
Mains (230 Volt)
50 - 60 Hz
There is a supply voltage
of 24 V on the contacts 5, 7, 9
There is a supply voltage
of 10 V on the contacts 17, 20
10 Volt power supply for
sensor (e.g. enthalpy sensor)
Summer mode
Sequence switch
External control signal
0 - 10 V, 0 - 20 mA
Supply air sensor
Exhaust air sensor
Outside air sensor
Jumper
Error message
During operation S1 and
S3 closed. By occurring of
defects or net failure S2
and S3 closed
control unit release
(potential free contact)

·KLINGENBURG
N
L1
S3
S2
S1
3
2
+
-
V
U
W
0 - 20 mA
4 - 20 mA
0 - 10 Volt
3
7
8
3
9
10
10
5
4
6
-
+
S
{
0 - 10 Volt
{
0 - 20 mA
4 - 20 mA
Hooking up KR4 and KR7 basic controllers
1. Power supply
Both the KR4 and KR7 models must be hooked up to a 230 V
power supply.
2. Hooking up the fault contact
In the normal operating conditions, S1 is connected with S3. In
case of a fault or when the device is voltage free, S2 is
connected with S3.
3. Motor connection
In order to avoid interference from the connecting wires to the
motor, it is necessary to install each of these separately in a
shielded cable. The KR4 and KR7 frequency inverter from
Klingenburg operate with an output voltage of 3 x 230 V. This
must be taken into account when wiring the terminal board on
the motor. Using standard motors 230/400 V they have to be
installed in delta connection.
4. External control signal inputs
Control signal connection
The KR can process the following signals:
Hook up the control signal to terminals 2 and 3.
For a control signal of 0 - 20 mA or 4 - 20 mA, the pins must
be jumped as illustrated below.
For a control signal of 0 - 10 V, the pins must be jumped as
illustrated below.
5. Connecting the rotation monitor
The rotation sensor must be hooked up to terminals 4, 5 and 6.
6. Controller release (Enable)
The controller release is driven over terminals 7 and 8 on the
control terminal strip. The contact used to connect the
controller release must be voltage free.
7. Thermal protection relay - motor
The thermal protection relay must be connected using shielded
wire in order to protect the motor from excessive overheating
when running at low speeds. The warranty is voided if the
thermal protection relay for the motor is not connected.
blue
brown
black

·KLINGENBURG
17
18
19
20
21
22
S
-
S
-
{
{
17
18
19
20
21
22
S
-
{
+
S
-
{
+
11
12
13
18
19
S
-
{
11
Hooking up KR4 Z and KR7 Z basic controllers
with installed options board
In case of the Z-Controller the connections must be made as
follows:
1. Summer mode, Cooling mode
1.1 Temperature comparison “B”
The 200 mm long outside air and exhaust air rod sensors are
connected to terminals 18 and 19 (outside air sensor) and 21
and 22 (exhaust air sensor) as shown in the following
illustration.
The sensors must be installed as illustrated. When ordering, this
function is indicated by the letter "B" (see page titled "Ordering
controllers").
Mounting the sensor:
1.2 Enthalpy comparison “C”
The 200 mm long outside air and exhaust air rod sensors are
connected to terminals 17, 18, and 19 (outside air sensor) and
20, 21 and 22 (exhaust air sensor) as shown in the following
illustration.
The sensors must be installed as illustrated. When ordering,
this function is indicated by the letter "C" (see "Orders" page).
Mounting the sensor:
1.3 Outside temperature measurement “D”
(summer change-over mode)
The 200 mm long outside air and exhaust air rod sensors are
connected to terminals 18 and 19 (outside air sensor) on the
options board as shown in the following illustration. When
operating in summer mode, the summer mode relay switches
from contact 13/11 to 13/12
The temperature sensor must be installed in the outside air.
When ordering, this function is indicated by the letter "D" (see
page titled "Ordering controllers”).
Mounting the sensor:
Outside air
Exhaust air
Outer air
Exhaust air
Outside air
Exhaust air
Outside air
Exhaust air sensor
Outside air sensor
Exhaust air sensor
Summer mode
Outer air sensor

·KLINGENBURG
{
0 - 20 mA
4 - 20 mA
{
0 - 10 Volt
26
25
+
-
24
23
S
-
16
15
14
12
2. Sequence switch
The sequencer must be set in accordance with the activation
value. The sequencer contact can support a maximum of 230
V and 1 A.
3. Connecting the supply air sensor “A”
The 200 mm resp. 2000 mm long supply air sensor type PT
1000 must be conncted to the terminals 23 and 24 as
illustrated.
The temperature sensor should be installed behind the rotary
heat exchanger on the supply air side. When ordering, this
function is indicated by the letter "A" (see page titled "Ordering
controllers").
Mounting the sensor:
4. External control signal inputs
In the case of basic controllers with an installed options board,
the external control signal input is located at the terminals 25
and 26.
In order to process a signal of 0-20 mA or 4 20 mA, the two
pins must be jumped as illustrated.
In order to process a signal of 0-10 Volt, the two pins must be
jumped as illustrated.
Outside air
Exhaust air

·KLINGENBURG
KR 4 R
7
Z A B
C
D
13
Ordering a controller
The KR controllers for regenerative heat exchangers are
available in two sizes:
KR4 = 400 Watt und KR7 = 750 Watt
The basic controller can be upgraded using an options board.
Certain functions require additional sensors (see
below).
Basic controller:
Control signal inputs
Speed display
Fault output
Intermittent operation
Motor thermal protection
Rotation monitor
Additonal functions:
Sequence switch
Supply air temperature control
Summer mode
- basic controller
- controller output
- rotation monitor *)
- additional functions
- supply air temperature control
- summer mode
Additional functionsBasic controller
*) see basic controllerr
Sample order KR4 R Z A B
Basic controller, output 400 Watt
Rotation monitor
using temperature comparison
using enthalpy comparison
using outside temperature
measurement
Required additional sensors for optional features
Supply air temperature control
-1 sensor in the supply air
Summer mode using temperature comparison
-2 sensors
Summer mode using enthalpy comparison
-2 sensors
Summer mode using outside temperature measurement
-1 sensor
·
·
·
·
Summer mode
using temperature comparison
Supply air temperature control
Independent control with sensors,
sequence switch

·KLINGENBURG 14
Putting in operation of control units KR4 / KR7
All functions on the KR controller can be accessed using the
three keys. The left-hand and the right-hand keys are used to
select options. The centre key is used to confirm entries.
Programming is initiated by pressing all three keys
simultaneously.
1. Commissioning
Once turned on, the display shows
If the following messages appears,
then the system must be checked according to the message
display.
Begin by pressing all three keys at the same time. After about 5
sec. the display shows the message
After that, the following message appear
After the motor has come to a complete stop, the controller
guides you through the menu items.
Guide to menu items
You can set the display language to either English or German.
To change the display language, use the selection keys
Confirm your choice with the Enter push-button.
After that, the following message appears:
As before, you select by means of the selection push-buttons
and confirm by depressing the” Enter” push-button.
Corresponding to your selection, the control unit leads you
through the series of inquiries “Manual operation” or “External
operation”, as described in the following.
Manual operation
The display shows:
By depressing the selection push-button, a frequency can be
determined. At 80 Hz, the rotor will run a standard 10 rpm.
Attention: Contact with
live elements even after
the power supply has
been cut can be life
threatening. Please
wait 15 minutes!
Motor stop!
SF:00 Hz IF:00HZ
Hardware err:EXX
Contr. blocked!
Motor temp!
Deutsch
English
Manual operation
External drive
Please wait!
Man. frequ: 00Hz
Push-buttons for selection
Enter push-button

·KLINGENBURG 15
External operation
After having determined “External operation”, the following
display is shown:
The Control Unit is pre-set to 5%, in spite of this it is possible
that an unwanted running of the rotor could be caused on
account of interference voltages. By increasing this voltage
rate, this can definitively be prevented. Acknowledgement is
carried out by depressing the Enter push-button. The following
display then appears:
In case “Cleaning on” is selected, the value is pre-set to 20
minutes.
The cleaning run is set in a cyclic mode between 40, 60, 80
and 100 minutes. The cleaning run ensures that the rotor
revolves regularly by half a rotation when the control signal is
set to 0 V for a prolonged period of time. The control unit must,
however, be released. By multiple depressing of the selection
loads, the intervals will change. Confirm by depressing the
Enter push-button.
Manual Operation / External Operation
The rotation of the rotor can be supervised by means of the
rotation monitor. In case you have ordered a control unit with
the option rotation monitor, you will select
In case the Control Unit is not equipped with a rotation monitor,
you will select
The ON/OFF switching of the rotation monitor is effected via the
selection push-buttons, the confirmation by means of the Enter
push-button.
During operation correct running is shown by the following
display:
Start point: 05%
Cleaning on
Cleaning off
Clean int 40min
Runcontrol on
Runcontrol off
SF:80Hz IF:80Hz
In order to accept the changes that have been entered at last, it
is necessary to store them.
In order to store the data, depress the “Enter” push-button.
By depressing the selection push-buttons instead of the
“ENTER” push-button, the changes that have been entered at
last are deleted and the previous menu items are active again.
The control unit returns into its normal operation mode.
In the case of manual operation, the display shown is as
follows:
In order to start or to stop the controller in the case of manual
operaton, depress the “ENTER” push-button. Th e se le ct ed
rotational speed is justified.
In the case of external operation, the display shown is as
follows:
Store data?
Stored!
Not stored!
HF: Hz IF: Hz
Runcontrol
SF: Hz IF: Hz
Attention: Contact with
live elements even after
the power supply has
been cut can be life
threatening. Please
wait 15 minutes!

·KLINGENBURG 16
SF:00Hz IF:00Hz
01: Excess current (motor / rotor blocked;
short circuit between U, V, W)
05: Overload (Control unit / motor overloaded)
09: Mains undervoltage
14: Earth fault
15: Excessive voltage in network
21: Excessive temperature at the power output
stage, ambient temperature too high; control
unit overloaded
99: Software error
The control unit is again ready for operation as soon as the
trouble has been acknowledged by interruption of the mains
voltage or by simultaneous pushing of the three push-buttons.
Unit is blocked
Motor exc. temp.
Running check
Hardware err:EXX
Attention: Contact with
live elements even after
the power supply has
been cut can be life
threatening. Please
wait 15 minutes!
Troubleshooting
Correct running and operation is shown by the following
display
If, however, the following display is showing
you will have to check the defect according to the following
list.
Hardware err:E01
SF:00Hz IF:00Hz
Trouble shooting for the basic contol unit KR4 / KR 7
- Check fuse / Mains voltage
- Control unit is not enabled (ext. potential free contact closed)
- Check the thermal protective contact
- Connect thermal protective contact at the control Unit.
-
During operation with rotation monitor:
- Check distance of magnetic switch to the rotor
- Check connection of the magnetic switch at the
control Unit
- Check if V belt has come off
- Check V belt tension
During operation without rotation monitor:
- Alter programming of the Control Unit
(See Description of the item rotation monitor)
- Check position of jumper according to the
requirements
- Check if control unit signal is effective
- Check connection control signal at the control unit
on contacts 5, 7 and 9 against ground (contacts 3 or 4)
supply voltage of 24 V must exist.
If not: check trip line

·KLINGENBURG 17
Putting in operation control units with
additional functions KR4 Z und KR7 Z
The leading through the menu items is the same as for
controllers KR4 / KR7.
After the items “Manual operation” and “External operation”
appears in addition:
After confirmation the following menu item appears:
After adjusting the selected value between 0 an 40 °C and
confirming entry with the Enter push-button, go to the menu
item “Summer mode”
Summer mode
When selecting the summer operating mode, you can select
among “Summer mode off”, “Summer temperature
comparison”, “Summer enthalpy comparison” and “Outside air
temperature measurement”.
If you select “Summer mode off”, the program will go to the
menu item “Sequencer activation value” after you press the
Enter push-button.
If you select one of the summer operation modes and confirm
your entry with the Enter push-button, the following message
appears:
The selected temperature activates the summer operation and
can be set in 1°C increments in a range from 18 - 42°C. After
you have entered the desired reference temperature and
confirmed with the Enter push-button, the following menu item
will appear:
After confirmation continue as described for the controller KR4
/ KR 7.
Trouble shooting / Trouble shooting for the controller with
additional functions KR4 Z und KR7 Z
In case of the Z-controller, please note these additional search
points.
Nature of problem: Action:
Supply air control does Check sensor and connection.
not reply On the contacts 1, 17 and 20
against ground has to be a
supply voltage of 10 V.
No summer operation Check controller programming
mode and connections
Please ensure that you state model and serial numbers of the
rotary heat exchanger when making enquiries about your
controller or its components.
Input temp.regul
Setpoint: °C
Summerfunct. off
Summerswitch on
Summer Temp.comp
Summer Enth.comp
Setpoint: °C
Switchpoint: x%
Attention: Contact with
live elements even after
the power supply has
been cut can be life
threatening. Please
wait 15 minutes!

·KLINGENBURG 18
Summary of features
Basic controller KR4
KR4 = 400 Watt
for rotor diameters smaller than 3760 mm
KR controller as frequency inverter with control unit
Processor technology
3 touch key with display for programming settings and
showing function and arror messages
IP 54 - aluminium case
External signal inputs
Fault indicator
Intermittent operation
Thermal protection relays
Optional:
Rotation monitor with sensor => KR4 R
·
·
·
·
·
·
·
·
·
·
Basic controller KR7
KR7 = 750 Watt
for rotor diameters greater than or equal to 3760 mm
KR controller as frequency inverter with control unit
Processor technology
3 touch key with display for programming settings and
showing function and error messages
IP 54 - aluminium case
External signal inputs
Fault indicator
Intermittent operation
Thermal protection relays
Optional:
Rotation monitor with sensor => KR7 R
·
·
·
·
·
·
·
·
·
·
Controller with additional functions KR4 Z
KR4 = 400 Watt
for rotor diameters smaller than 3760 mm
KR controller as frequency inverter with control unit
Processor technology
3 touch key with display for programming settings and
showing function and arror messages
IP 54 - aluminium case
External signal inputs
Fault indicator
Intermittent operation
Thermal protection relays
Sequence switch
Optional:
Rotation monitor with sensor => KR4 RZ
Supply air temperature control - 1 sensor
Summer mode: temperature comparison - 2 sensors
Summer mode enthalpy comparison - 2 sensors
Summer mode: outside air temperature measurement
·
·
·
·
·
·
·
·
·
·
·
·
·
·
·
- 1 sensor
Controller with additional functions KR7 Z
KR7 = 750 Watt
for rotor diameters greater than or equal to 3760 mm
KR controller as frequency inverter with control unit
Processor technology
3 touch key with display for programming settings and
showing function and error messages
IP 54 - aluminium case
External signal inputs
Fault indicator
Intermittent operation
Thermal protection relays
Sequence switch
Optional:
Rotation monitor with sensor => KR7 RZ
Supply air temperature control - 1 sensor
Summer mode: temperature comparison - 2 sensors
Summer mode enthalpy comparison - 2 sensors
Summer mode: outside air temperature measurement
- 1 sensor
·
·
·
·
·
·
·
·
·
·
·
·
·
·
·

·KLINGENBURG 19
Safety and Warning Instructions
Please read the Product manual carefully and observe all safety
and warning instructions, before the installation and putting into
operation of the frequency transformer. Keep this Product
Manual always at your finger tips in the vicinity of the frequency
inverter.
Definition of the instructions:
In the case of non-observance of these instructions,
death, severe injuries or considerable damage may occur.
In the case of non-observance of these instructions,
slight injuries or damage may be incurred.
Warning!
Attention!
General
During operation ensure that the power supply is
constant.
·This frequency inverter generates dangerous electric voltages
and controls rotating components that may become
dangerous. In the case of non-observance of the instructions
in this Manual, death, severe injuries or considerable damage
may be incurred.
·The installation, putting into operation and maintenance of
these drives is permitted to be undertaken only by technically
suitable persons who are completely familiar with the mode
of operation of the equipment and of the machine.
·The devices are equipped with intermediate circuit capacitors
which have dangerously high voltage rates even after having
been disconnected from the mains. You must wait at least
fifteen (15) minutes after having disconnected the voltage
before you can open the device and start working. It is
important to note that no live components are contacted.
·The earthing safety measures serve only the protection of the
frequency inverter and not for the protection of persons.
Three-phase frequency transformers are - according to VDE
0160 - not allowed to be connected with current-operated
earth-leakage circuit breakers because in the case of a
possible direct current component (direct current load). In the
case of such trouble the sensitivity of the current-operated
earth-leakage circuit breaker is reduced. As a protective
measure, the regulations of VDE 0160 are to be observed.
Earth the frequency inverter at the connection
provided for this purpose.
Do not come into contact with your hands or objects
components within the enclosure - when the device is
connected to the mains or if the intermediate circuit is still not
discharged. Do not work at the wires and do not check any
signals as long as the device is connected to the mains.
Warning!
Warning!
Warning!
Be particularly careful when the automatic restarting device is
activated. Install on the mains side a swit which is inactivated in
the case of a mains failure and which can be switched on when
voltage becomes available again only by manual operation, in
order to prevent injuries through uncontrolled restarting of the
frequency transformer after a mains failure. Earth the frequency
transformer at the corresponding connection.
Make sure that the input voltage complies with the
voltage stated on the type plate of the machine. Influences of the
environment, such as high temperatures, air humidity are to be
avoided in the same way as dust, oil and aggressive gases.The
place of installation should be a well ventilated location not
exposed to direct sun rays. Install the device at a vertical, fire-
resistant wall which does not transmit any vibrations. Do not
connect any mains voltage to the terminals U/T1, V/T2, W/T3.
·Please contact the manufacturers of the motors or machines
when standard motors with frequencies >60 Hz are to be
operated.
·All frequency transformers are tested regarding voltage
resistance and insulation resistance measurements. Insulation
resistance measurements are allowed to be carried out, e.g. in
the scope of inspections, only between the power terminals
and the ground. Do not carry out any insulation resistance
measurements at the control terminals.
·Enter the operation signals START / STOP via the control
terminals or the control panel and not by switching the mains
or motor contactor. Do not install any capacitors or excess
voltage distribution-type arresters into the motor input lines.
In order to safeguard safe and reliable functioning of
your Klingenburg Frequency inverter, all applicable safety
regulations, e.g. accident prevention regulations, VDE
regulations, etc. must be strictly observed. On account of the
fact that these regulations are differently handled in various
countries, the user is required to observe the requirements which
are applicable in his case. Klingenburg GmbH cannot warrant the
user from the duty to exactly follow the latest safety regulations
applicable in his case.
·The technical data and descriptions in this Operation Manual
have been compiled according to our best knowledge. Product
improvements are introduced all the time - Klingenburg GmbH
reserves the right, for this reason, to carry out such alterations
without prior notification.
·The instructions in this Operation Manual have been compiled
with great care. Should, in spite of everything, defects or
damage be incurred through the utilization of these
instructions, then Klingenburg GmbH cannot be held
responsible for any damage of this type.
Warning!
Attention!

·KLINGENBURG 21
We reserve the right to introduce technical changes and
alterations without prior notice /06-2003
Klingenburg GmbH
Boystrasse 115
D-45968 Gladbeck/Germany
Telephone +49 - 20 43 - 96 36 - 0
Telefax +49 - 20 43 - 7 23 62
E-Mail: [email protected]
www.klingenburg.de
Other manuals for KR4
1
This manual suits for next models
3
Table of contents
Other Klingenburg Controllers manuals
Popular Controllers manuals by other brands
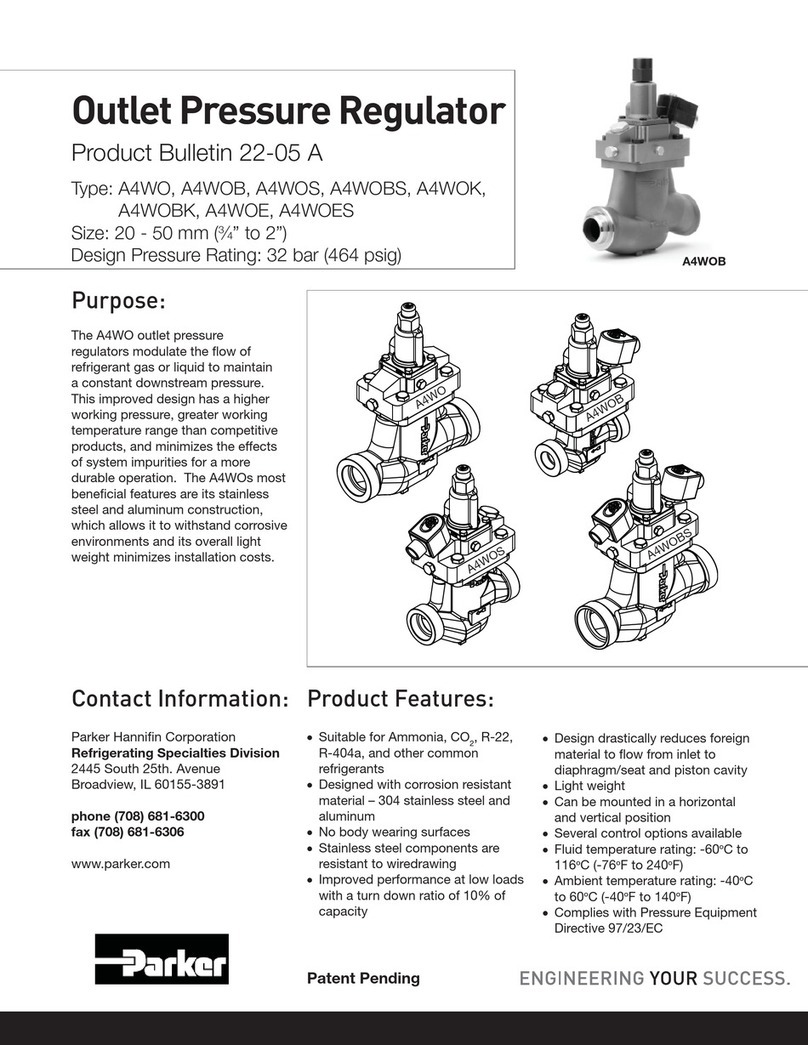
Parker
Parker A4WO Product bulletin
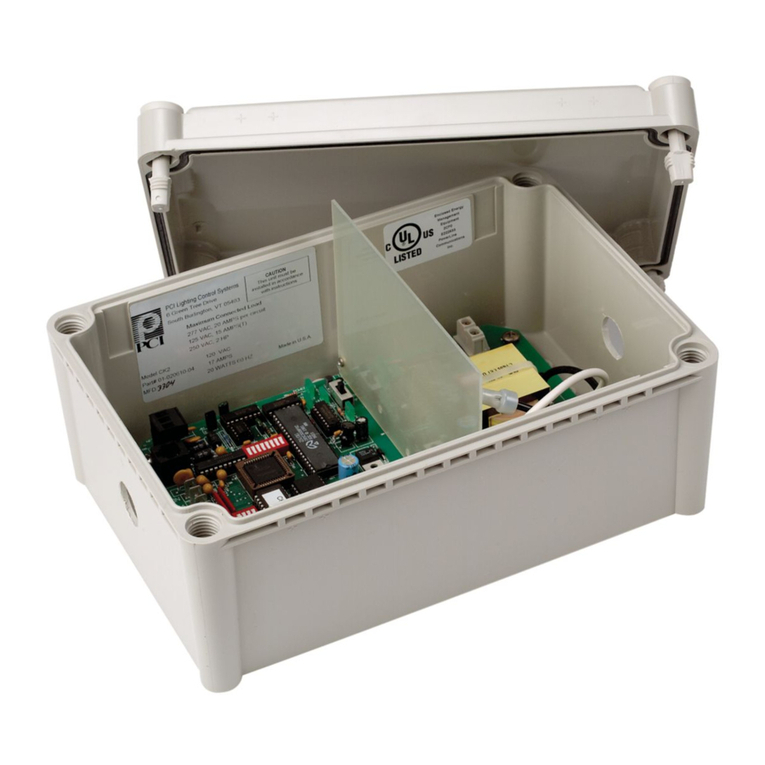
Greengate
Greengate ControlKeeper 2 CK2-120-NC Installation sheet
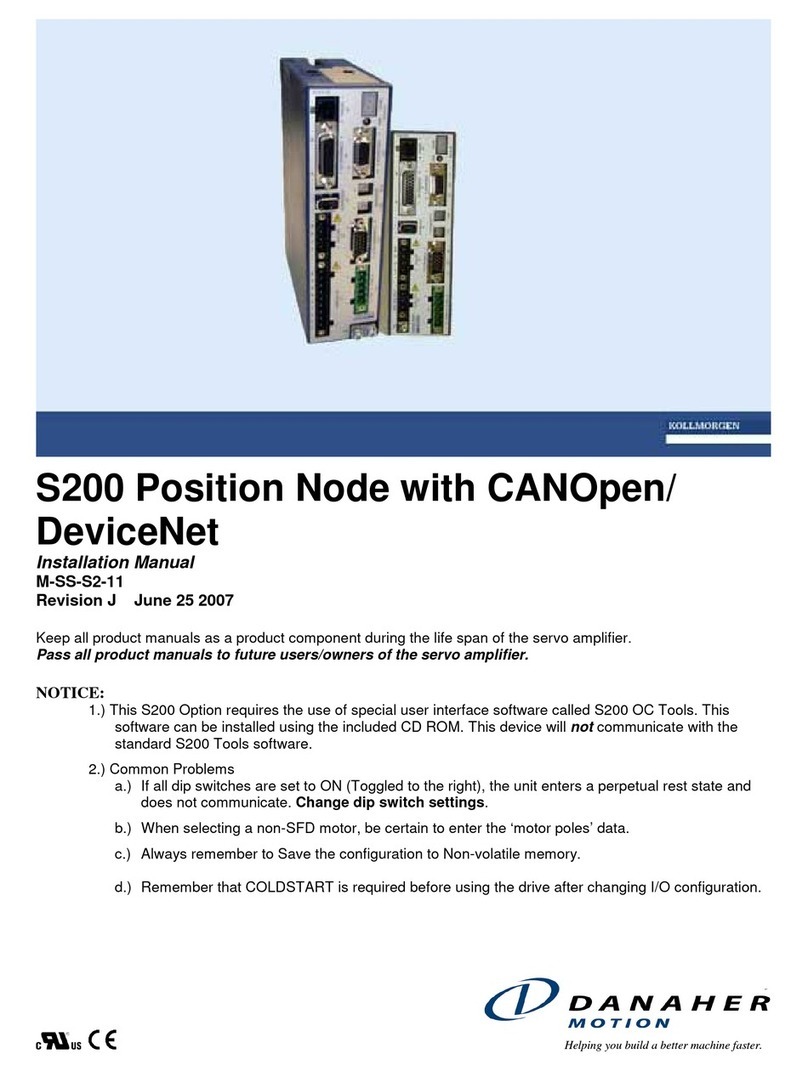
Danaher Motion
Danaher Motion S20630 installation manual
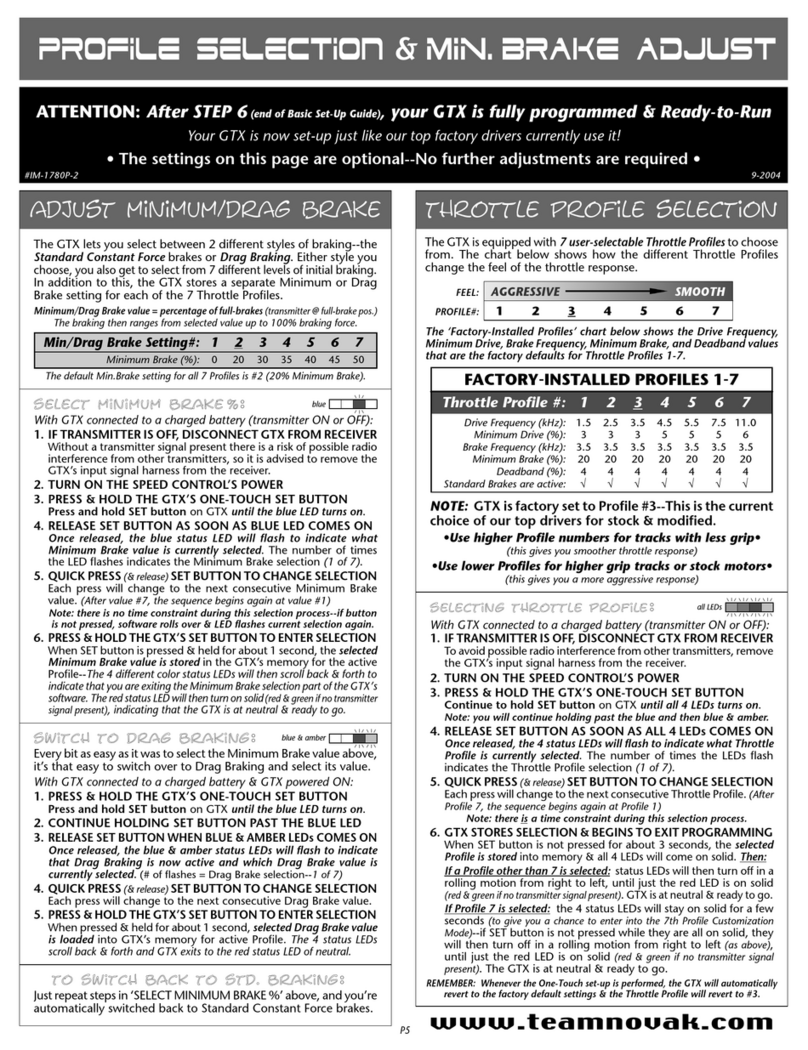
NOVAK
NOVAK GTX - PROFILE SELECTION & MIN BRAKE... manual
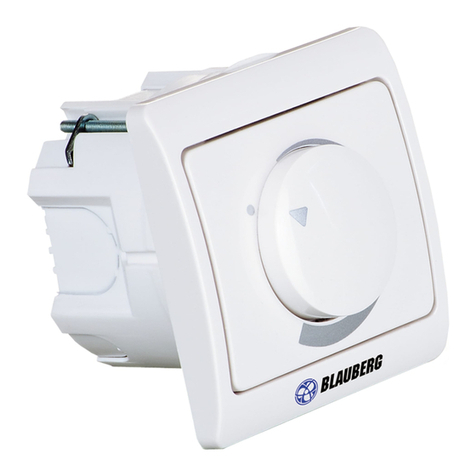
BLAUBERG
BLAUBERG CDT E/0-10 manual
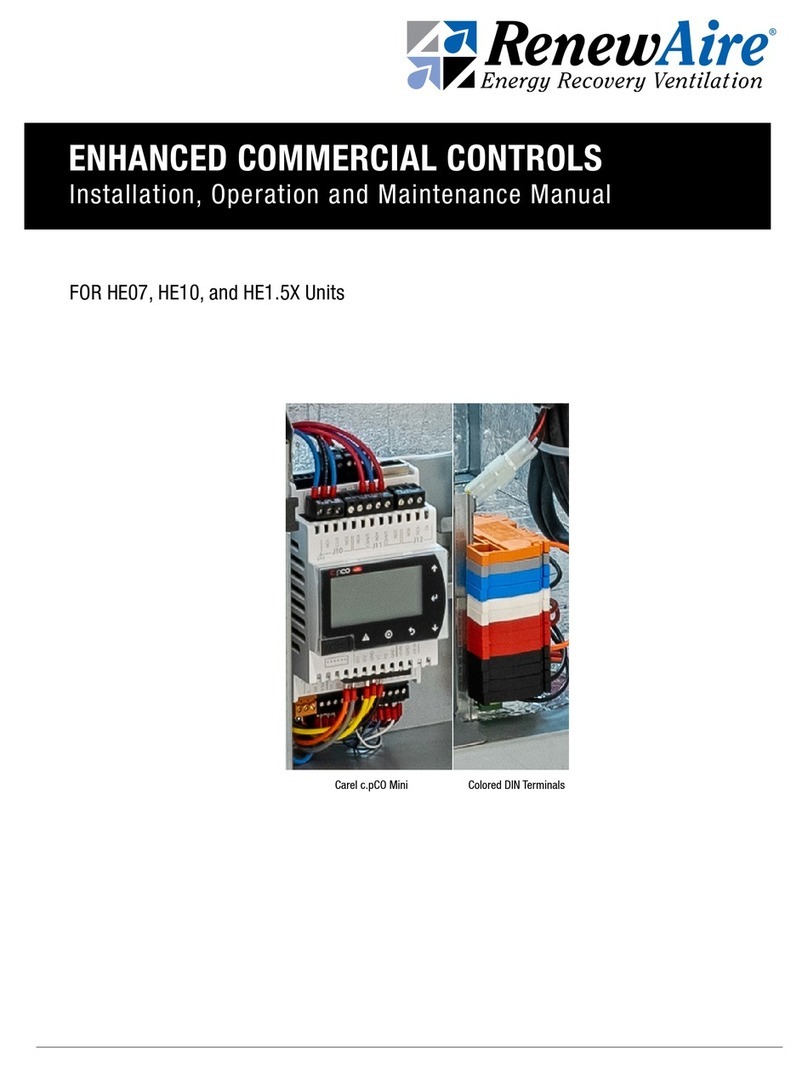
RenewAire
RenewAire HE07 Installation, operation and maintenance manual
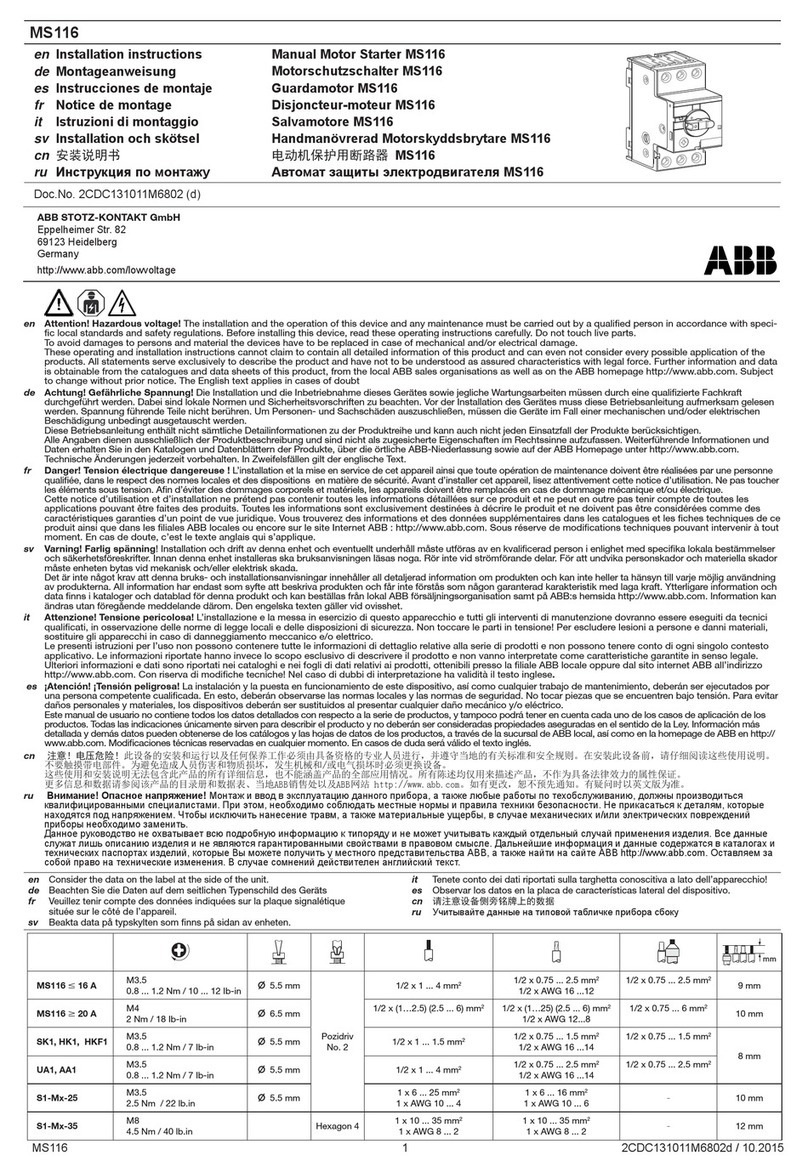
ABB
ABB MS116 installation instructions

Copley Controls
Copley Controls Xenus XSL user guide

Regada
Regada MO 3.4 Installation, service and maintenance instructions

Comunello Automation
Comunello Automation SHOWIN S45 3FC instruction manual

inTouch R&B
inTouch R&B HVAC Minder installation instructions
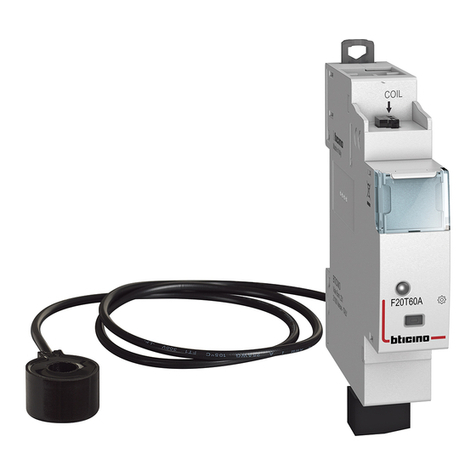
Bticino
Bticino F20T60A manual