KMT C 370 SA-V Installation and operation manual

Model C 370 SA-V
Clk
SEMI-AUTOMATIC CIRCULAR CUTOFF SAW
WITH INFINITELY VARIABLE BLADE SPEEDS
OPERATORS MANUAL
PARTS LIST
Kalamazoo Machine Tool
6700 Quality Way
Portage, Michigan 49002
Phone (269) 321-8860
FAX (269) 321-8890

2
TABLE OF CONTENTS
Specifications 3
Installation 5
Electrical Connection 6
Air Connection 7
Blade Installation 8
Setup Adjustments 9
Controls & Setup 11
Operating the Machine 12
Blade speeds 16
Blade Selection 17
Other Sawing Notes
Maintenance
Parts Illustrations

3
SPECIFICATIONS
Model C 370 SA-V
Drive Motor 4 HP, TEFC
Spindle RPM 13-76 RPM, Infinitely Variable
Blade Data
Max diam 14 1/2" (370mm)
Spindle diam 40mm
Pin diameter 10mm
Pin locations 63mm
Max Vise Opening 7"
Work Height 36"
Power Requirements
208-220-230 volts - 20 amps
440-460 volts - 12 amps
3 phase
60 cycles
Air Connection 3 CFM 60-100 PSI
Coolant Capacity 3.5 Gal (15 lit)
Gearbox Capacity-main 1 Gal (5.5 lit)
Hydraulic Capacity 45 oz (1.6 lit)
SAFETY INSTRUCTIONS
TO THE OWNER OR SUPERVISOR
You must remember that this machine is designed to cut metal with a sharp tool, and you are responsible to see
that the machine is in top operating condition and that it is operated IN A SAFE MANNER!
YOU MUST:
1. Make sure the machine is properly installed, anchored to floor, and electrical installation is proper.
2. Be sure you are familiar with all operating, safety, and applications information before operating this
machine or turning it over to one of your employees.
3. See that all who operate this machine are properly trained and fully aware of all safety practices.
4. Be aware of all unsafe practices that may occur. (See operator safety precautions and applications
information)
5. Insist on proper personal protective equipment and practices.
6. Maintain all factory installed safety devices and insure that these are never removed or altered or
restricted in any way.
7. Insure that your operators have a safe and orderly work area, with adequate light and operating room.
8. Be certain that your machinery receives responsible and competent maintenance and that your
machinery is inspected on a regular basis.
YOU ARE RESPONSIBLE

4
SAFETY INSTRUCTIONS
TO THE MACHINE OPERATOR
You must read and understand all operating, safety,
and applications information before attempting
to use this machine.
1. Always wear proper eye protection.
2. Never operate machine unless all guards are in place.
3. Never insert hands or arms into or near cutting area while machine is running.
4. Never load or unload machine while blade is running.
5. Never wear loose clothing, long sleeves, gloves, jewelry, or any other items that may be caught.
Confine long hair.
6. Adequately support stock on both sides of machine to prevent falling.
7. Always disconnect power at source when performing maintenance or making adjustments, other than
those necessary for the normal operation of machine.
8. Keep cutting area clear of tools or other loose objects.
9. Before starting a sawing cycle, be sure vise is securely clamped and machine set-up is correct.
10. Never use this machine to cut workpieces larger than the stated capacity.
11. Never modify a blade to fit arbor.
12. Never use a blade larger than the machine is designed for.
13. When cutting very short pieces, make sure they do not jam between the blade and the slot in the
tabletop.
14. Be aware that the pneumatic vises close automatically and to KEEP HANDS CLEAR!
15. Be aware of the possible sawing problems (see APPLICATIONS section of this book)
16. CAUTION: If blade becomes jammed, immediately turn off power, loosen vise, extract workpiece
from blade, and inspect blade for cracks or broken teeth.
ALWAYS OPERATE MACHINE SAFELY, USING COMMON SENSE AND ALERTNESS

5
INSTALLATION
We recommend that you follow these instructions closely
and report any problems to your distributor
Select an installation site that is clear of traffic and obstructions, suitable for proper machine operation and
maintenance, including adequate light and clearance. Machine may be transported via sling from ‘’eye” bracked
as illustrated.
The first step after uncrating your machine is to see that all items are present and that there is no apparent
damage to any part of the machine.
Checklist of items
C 370 SA-V Machine Operators manual
Wrenches One HSS Sawblade
Swiveling Handle
Note: Most of above items located in machine base. Open access door by
unlatching latch in lower LH corner of door.
Your machine has been carefully packed and has preservative applied to
all metal surfaces to protect it during transit and storage. It is recommended that all of these surfaces be cleaned
at this time.
Check to insure that the gear reduction head contains the proper amount of oil. See section on Maintenance
(Gearbox), for proper oil level.
Mix coolant to approximately 10:1 with water for most sawing applications. . For Stainless Steal use a 5:1
mixture. For unusual materials, consult the manufacturer for additional coolant recommendations. Pour coolant
into the water in order to mix properly, then pour coolant into the coolant tank in the base of the machine.
Never use straight cutting oil!
Caution:
Ensure the removable chip tray is in the proper position
before you operate machine or pour in the coolant. The
removable chip tray slides easily into place and will drop into
place when in correct position.
Failure to observe this will allow coolant to flow into base
instead of into the reservoir.
Also note that a full chip tray is heavy. You must be prudent
to dispose of chips before the chip ban becomes too heavy.
View of chip tray and coolant reservoir.
Exact details may vary from various models.

6
ELECTRICAL CONNECTION
Only a qualified electrician should do electrical connections!
Make sure your power supply matches the machine.
Note: Machine is supplied with isolation transformer to match your operating voltage.
All machines operate at 400 volts, and you must have the correct transformer to operate on your power supply.
Voltage may be changed at isolation transformer.
It is recommended that the machine is on a circuit that is properly fused, and the machine must be properly
grounded to comply with OSHA and state electrical codes. If your machine is installed in an area subject to
voltage spikes or high variations you will need to install a Line Reactor rated at 11 amps.
Next, check the machine for proper rotation. If rotation is not correct, change any two of the three power leads at
point of connection.
Note: Yellow & Green Wires are Ground
Foot Pedal Connection
Note that on the back of the operators console you will find a female plug receptacle. If you desire to operate with
a footswitch, you may wire into the plug at this point. Use of a foot pedal will then actuate a semi-automatic
sawing cycle (same as pushing “cycle start” button)
WIRE SIZES
The machine must be serviced by adequate wire or a severe loss of power may occur, leading to poor
machine performance. We recommend:
Length of conductor Wire Gauge Size
50' or less #14
100" or less #12
100-150" #10
150 or longer NOT RECOMMENDED

7
AIR CONNECTION
Connect air line to connector at rear of machine as shown:
Note: Shop air should be between 80-110 PSI. Air volume
required, approx. 2-3 cfm.
FURTHER SUGGESTIONS:
Your air supply will certainly contain some moisture which is unavoidable in any plant air supply. The volume of
water vapor may amount to 5-6 gallons per day in the worst conditions. This water can rust the internal parts of
air tools, controls, and cylinders. It is for this reason that we suggest the installation of an air dryer in the line
(connection line 6), which will provide DRY AIR to your machine, eliminating unnecessary downtime due to
breakdowns, maintenance, and cleaning of rust, scale, and moisture.
Water in your machines operating system or cylinders is not covered under
warranty!

8
BLADE INSTALLATION
Please refer to the section on BLADE SELECTION to select proper blade.
Saw frame should be positioned as illustrated. Spindle bolt & coolant nozzle should
be in line as shown at right.
Loosen coolant nozzle with hex wrench as illustrated, and move to left to allow
installation of blade.
Loosen socket cap screw on front of blade guard with hex wrench, slide removable
guard up until it releases, and remove guard. This will allow removal of plexiglass
cover.
-Remove spindle bolt, spring washer, and flange (items 1 thru 3).
-Insure that the spindle, outer flange, and blade are clean and free of dirt
and oil.
-Mount the blade with the teeth pointing in the direction
of the arrow
- Mount the flange, spring washer (high side to the outside, seated
properly) and the locking bolt.
Important: Prior to finally tightening the bolt, rotate the blade backwards so
that the backlash is removed from between the driving pins and the holes in
the blade.
-Check to see blade brush bristles are just touching sawblade teeth adjust if
necessary.
-Reinstall the blade guard.
The blade guard assembly is also adjustable, and may require adjustment when
changing blade diameter sizes. If not in proper adjustment, it may prevent the
saw frame from its' full travel up or down. Loosen the two SHCS at rear and
adjust as necessary.

9
Optional Minimal Lubrication System
The optional minimal lube system is illustrated and a separate
manual describing it’s use and maintenance is enclosed with this
manual.
Note: The device has a life time warranty if you use original
Unist lubricant
Always use caution installing the blade so as not to damage the
nozzles.
The system has an on/off slide valve located on the input
assembly. It is the chrome cylindrical mechanism see at right,
and sliding it in & out will stop or allow air flow to the system.
The standard flood system may be used in place of it if desired,
and you will find it packed in the coolant reservoir in the base of
machine.
If you wish to use the flood coolant system, simply remove the
minimal lubrication spray nozzle and replace with the flood
nozzle that comes with the flood system.
Upon replacing the spray mist nozzle, make sure to align the
nozzle with the sawblade to prevent damage.

10
Blade Coming Loose
In the unlikely event that your blade comes loose occasionally or frequently, please read the following.
Installing the blade correctly is the most important place to start, but there may be a combination of factors
involved so we'll try to cover all of them.
Follow correct blade selection. If the proper blade for the work to be done is not selected, excessive vibration will
occur, and if the blade wasn't properly installed initially, vibration will contribute to the loosening.
It is also important to make sure that all of the surfaces are clean and free of chips before you attempt to mount
the blade, otherwise you cannot properly tighten the blade.
Next you must be certain to put the spring washer on correctly, as illustrated, making sure the machined head of
the spindle bolt fits correctly into the spring washer. The spring washer is what keeps the spindle bolt tight.
Next make sure that the backlash is removed between the drive pins and the holes in the blade. The holes must
be larger than the pins or you wouldn't be able to get the blade on, and you must therefore remove any backlash.
If you don't, the machine will do it for you (violently) when the blade contacts the workpiece, and you may get
damage.
Please note that it is not necessary to use excessive force to tighten the spindle bolt. The spring washer is what
does the work.
Blade Direction & Tightening
You will note that the blade rotation is the opposite of inexpensive pivoting-type cold saws. For the experienced
machinist, you will recognize the concept of ‘climb cutting’.
The rotation of our machine causes the blade to force the workpiece down, into the table top. Opposite rotation
would allow the sawframe to self-feed and/or lift the workpiece.
CAUTION: Operating this drive in the wrong direction will cause damage to the gearbox!
Also note that the bolt has to tighten in the opposite direction that the spindle turns. The reason is because the
startup torque of the drive is such that if you have it tighten in the same direction the startup torque would begin to
loosen it.
Vise Adjustment
The vise assembly adjusts laterally in the front "T" slot to allow clamping support as
close to the blade as possible. This is important for minimum vibration while
sawing. Adjust by loosening adjustable handle and position as desired.
Adjust the anti-burr device on the cutoff side of the blade so the device supports the
workpiece as closely to the blade as possible. Note that the disc springs ensure a
constant clamping on the material, despite the materials' irregular shapes.
BLADE CLEANING BRUSH
Proper utilization of the blade cleaning brush will keep chips from being carried
around in the teeth of the blade and re-entering the cut. This can cause blade
breakage and poor blade life.
The blade cleaning brush should be adjusted so the tips of the brush are just lightly
riding on the gullets of the teeth. If the brush rides too hard against the teeth, the
brush will wear prematurely.
Adjust brush assembly as illustrated at right, with hex wrench as shown.

11
Variable Vise Clamping Pressure
Vise clamping pressure may be adjusted to prevent
distortion of tubing or structural materials. Adjustment is
made at the regulator on the machine base (inside door)
and registered on gauge. Adjust for maximum pressure
without distortion.
Caution: Pressure must be sufficient to prevent material
from turning in the vise, or damage to blade may occur.
Note that the knob is a locking knob. To unlock, pull out.
To lock, push in.
POWER UP
The power disconnect switch is located at
end of machine. Push RH button to power
up machine.
Push the yellow System Start button (to the left of disconnect switch), and it will
illuminate.
Nothing will operate if the yellow button is not on.
View of display when power is on
Start Pneumatics
Push F3
Operator Functions
Sawframe raise & lower
Sawvise clamp & unclamp
The lower 4 buttons in this group are not used

12
Operating the machine
Quick Start Operation
POWER ON SWITCH
SYSTEM START BUTTON
F3 - PNEUMATIC START
CLAMP SAWVISE ON MATERIAL
CLOSE FEED SPEED VALVE
PUSH CYCLE START
ADJUST COOLANT VALVE
OPEN FEED SPEED VALVE UNTIL
YOU REACH DESIRED RATE
BLADE SPEED Increase ADecrease V
Up & down arrows, for blade speed increase/decrease
The machine display will read as illustrated at the right
Blade Effo 2.4 is the amperage of the drive motor
Blade velo Blade rpm
ARC lowering indicates the sawframe is moving down
Detailed Explanation
Operation is quick and simple. We suggest you run a test cycle to set
your blade speed, downfeed rate, blade brush, and coolant flow.
Raise sawframe to the starting position desired via the UP arrow (top
left)
When the sawblade clears the workpiece as shown, clamp your
material in the sawvise to make sure the workpiece is securely
clamped.
Push the Cycle Start button to start sawing cycle.
The sawblade will make one cut and return automatically to the
starting position.

13
Function Keys
Only 3 Function Keys are utilized on this machine
F3 - Activate the pneumatic system. This will allow the sawframe UP and DOWN
functions and the sawvise CLAMP and UNCLAMP functions
F4 -Function button F4 is the key for the coolant control.
Push F4 to change the coolant from ON (continuously) OFF (never on) or ON for
cycling (coolant on only during the sawing cycle)
F5 - Function button F5 is the key to preset the blade speed

14
Sawframe Travel Limits
If your sawframe does not go HIGH enough or LOW enough and you wish to change the settings,
proceed as follows.
To make the sawframe go to a lower cutoff point that it is currently performing, first run
the sawframe completely down.
Next,push both of the DOWN arrows as illustrated, and the
sawframe will go lower.
When satisfied that the cutoff point is what you need, push
ENTER and the down arrow as illustrated and you will see
the display read ARC LOW SAVED
From this point forward the sawframe cutoff point will remain
the same until you change it.
To make the sawframe go higher that it is currently performing, first run the sawframe completely up as
far as it will go.
If it is not high enough for you, push both of the UP arrows and the sawframe will go
higher
When satisfied that blade top point is what you need, push ENTER and the UP arrow as illustrated and
you will see the display read ARC HIGH SAVED
You may then lower the sawblade to the desired starting point and each sawing cycle will be repeated.

15
Display messages & solutions
Check the yellow emergency button on startup side of operator console.
If you interrupt a cut by pushing the Cycle Stop button it may be
necessary to restart the system.
Push F3 to restart pneumatic system.
Check air support
User Parameters
Customized parameters may be utilized as desired. To access, push ENTER + F6
Enter the code 0000
01 - Language, select 1 of 5 languages
Push ENTER button to scroll through the various languages Note: English is ING
Scroll down through the list of parameters with the 'down'
arrow shown at right
02 - Blade thickness - may changed to match your blade
thickness (keft removal) Enter number and decimal at keypad
03 - Hydraulic timeout - may be adjusted to shut down hydraulic system after set level of idle activity,
adjustable in minutes. Enter time in minutes at keypad
04 - Blade shut off - blade can be set to run continually or shut off when cycling
05 - Sawframe travel - Semi-automatic operation only; shut off at bottom of cut or shut off when
sawframe reaches top
09 - Unit of measure - Chose between inch or metric

16
RECOMMENDED SPINDLE SPEEDS
300 & 315 BLADE
350 & 370 BLADE350 & 370 BLADE
MATERIAL
RPM
RPMRPM
Free Cutting, Low Carbon Steels
1108-1115-1117-1119-1212
20-40
16-3516-35
1018-1020-1010
Medium Carbon Steels
1132-1137-1140-1145-1151
17-30
13-2213-22
High Carbon Steel
1040-1060
13-20
13-1813-18
Various Alloys
Light Mild Steel Structurals
tubes, pipes, etc. up to 0.060"
20-40
16-3516-35
Medium Mild Steel Structurals
tubes, pipes, etc.up to 0.375"
17-30
13-2213-22
Stainless Steels - Solids
13-18
13-1613-16
Stainless Steels - Tubes
16-20
14-2014-20
Castiron
22-26
20-3020-30
Copper
60-76
50-7050-70
Brass
76
76
Bronze
24-36
22-3422-34
Aluminum
76
76
CAUTION: DO NOT USE SPINDLE SPEEDS LOW ER THAN 13 RPM!
Choosing Blade Speed Information
Your machine has blade speeds infinitely variable from 13-89 RPM.

17
Blade Selection
Blade Size
Your machine came equipped with one 350mm sawblade (14”). It is possible to use smaller (300mm) or larger
(370mm) sawblades under certain conditions.
Blade Toothpitch
Refer to chart to locate the type of material (solid or structural) and size of material you want to cut.
Locate material to be cut, and follow straight down to the row labeled “toothpitch” to find recommended toothpitch

18
Locate recommended blade from list
Special Sawblade Grinds
All standard blades are ground for use on mild steels.
Blades to be used on stainless steels (or other hard materials) should be designated with an “SS” after the part
number (ex: 1404 SS) These blades may also be used on mild steels
Blades to be used on aluminum or other non-ferrous materials should be dsignated with an “AL after the part
number (ex: 1410 AL) These blades may not be used on steels.
Overloading
The machine is equipped with a thermal motor protector in case of overload. This device is built into the machine
main power disconnect, and is adjustable. If machine frequently goes into overload, you may adjust the
amperage to a slightly higher setting by removing cover and turning adjusting screw.

19
1
3
2
EMERGENCY BLADE REVERSE
In case the blade should get stuck in the workpiece for any reason (overfeeding, broken blade, etc) you must be
able to extract the blade from the workpiece. First, push EMERGENCY STOP button.
Your machine is equipped with a reversing switch, located near the main power disconnect switch.
Normal Operation Reversed
Normal operating position is as shown at left. Reversing direction is as shown at right.
If blade is stuck in the workpiece, turn selector switch to right and push “cycle” button. Blade will reverse rotation
and sawframe will raise.
If selector switch is not in correct position, machine will not work and you will receive an error message: BLOC
Angle Cutting
In your tool kit you will find a 25mm round bar that is threaded on one end,
and this is to be mounted into the RH side of the sawframe column.
This will assist swiveling the sawframe for making miters.
Your machine will make angle cuts from 0-45° left, and 0-60° right. Two
stops (1&2) serve as positive stops for quickly stopping accurately at 45°.
These may be removed to go to settings beyond zero or 45 °.
To set an angle, first loosen lever (3). Swivel the saw frame until the
graduation desired on the swiveling plate matches the indicator on the
base. Relock handle.
It may be necessary to remove anti-burr device when miter cutting, as
failure to do so may result in interference with the blade.
IMPORTANT NOTE: When angle sawing, it is important to note the
capacity limitations, as it is not possible to cut pieces as wide as you can at
90°.
Vise Adjustment
The vise assembly adjusts laterally in the front "T" slot to allow clamping
support as close to the blade as possible. This is important for minimum
vibration while sawing. Adjust by loosening adjustable handle and position as
desired.
Adjust the anti-burr device on the cutoff side of the blade so the device supports
the workpiece as closely to the blade as possible. Note that the disc springs
ensure a constant clamping on the material, despite the materials' irregular
shapes.

20
VARIABLE SPEED DRIVE
The A/C drive is located in an enclosure on machine COLUMN, at rear.
-Open cover of operators console, and you will see in the upper right hand
corner the A/C drive, labeled ALTIVAIR
When you turn on power, you will see the rdy message. If the rdy message
does not appear, the drive is dead and must be replaced.
When the drive has a problem, instead of rdy you will see most likely one of
the following:
OLF - which means the drive has been overloaded for some reason
(reassess how you are using the machine)
OSF - which means the supply voltage is too high (check your voltage)
USF - which means the supply voltage is too low (check your voltage)
The most frequent problems with machines are voltage too high,
voltage too low, and overloading the drive.
Table of contents
Popular Saw manuals by other brands

Chicago Electric
Chicago Electric 65570 Owner's manual & safety instructions

DeWalt
DeWalt DW728 instruction manual

BN Products
BN Products BNCE-30-24V Operation & instruction manual
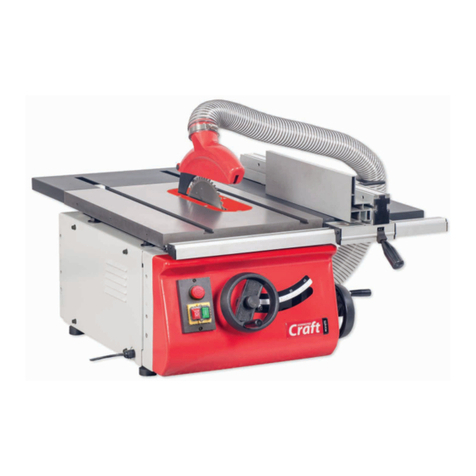
Axminster Craft
Axminster Craft AC216TS Original instructions
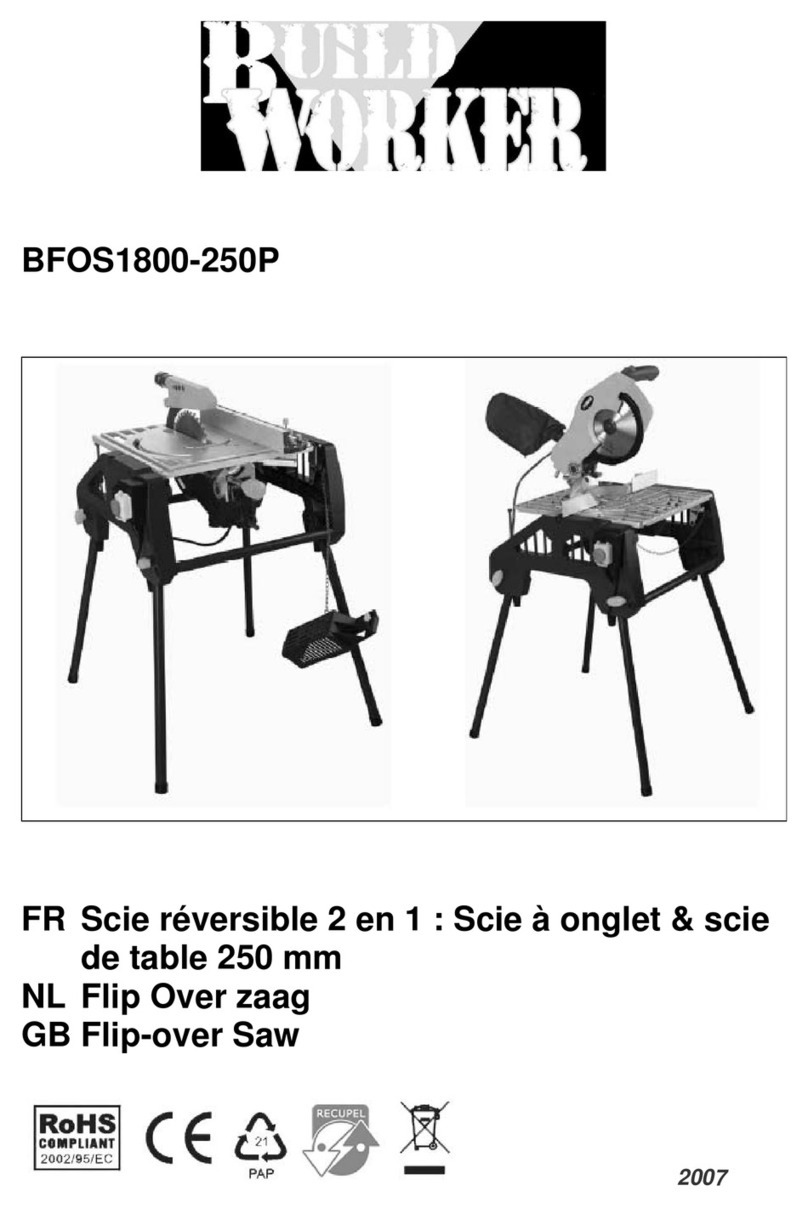
Build Worker
Build Worker BFOS1800-250P manual

Jet
Jet HBS-1321VS operating instructions
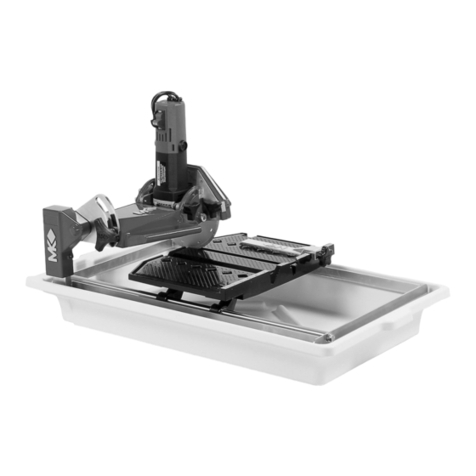
MK Diamond Products
MK Diamond Products MK-370 EXP Owner's manual & operating instructions
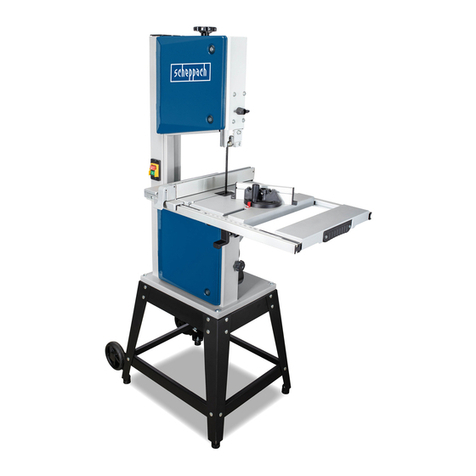
Scheppach
Scheppach HBS300XWB Translation from the original instruction manual
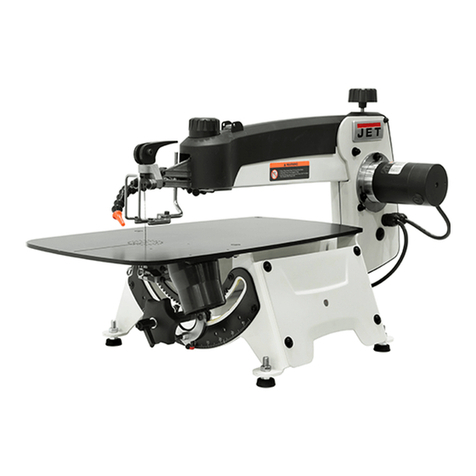
Jet
Jet JWSS-18B Operating instructions and parts manual
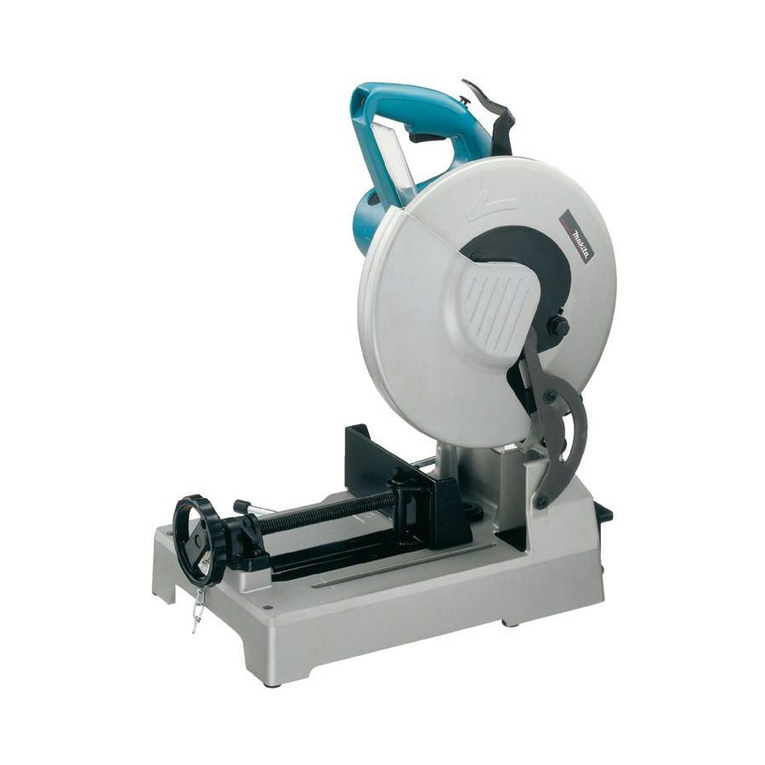
Makita
Makita LC1230 instruction manual
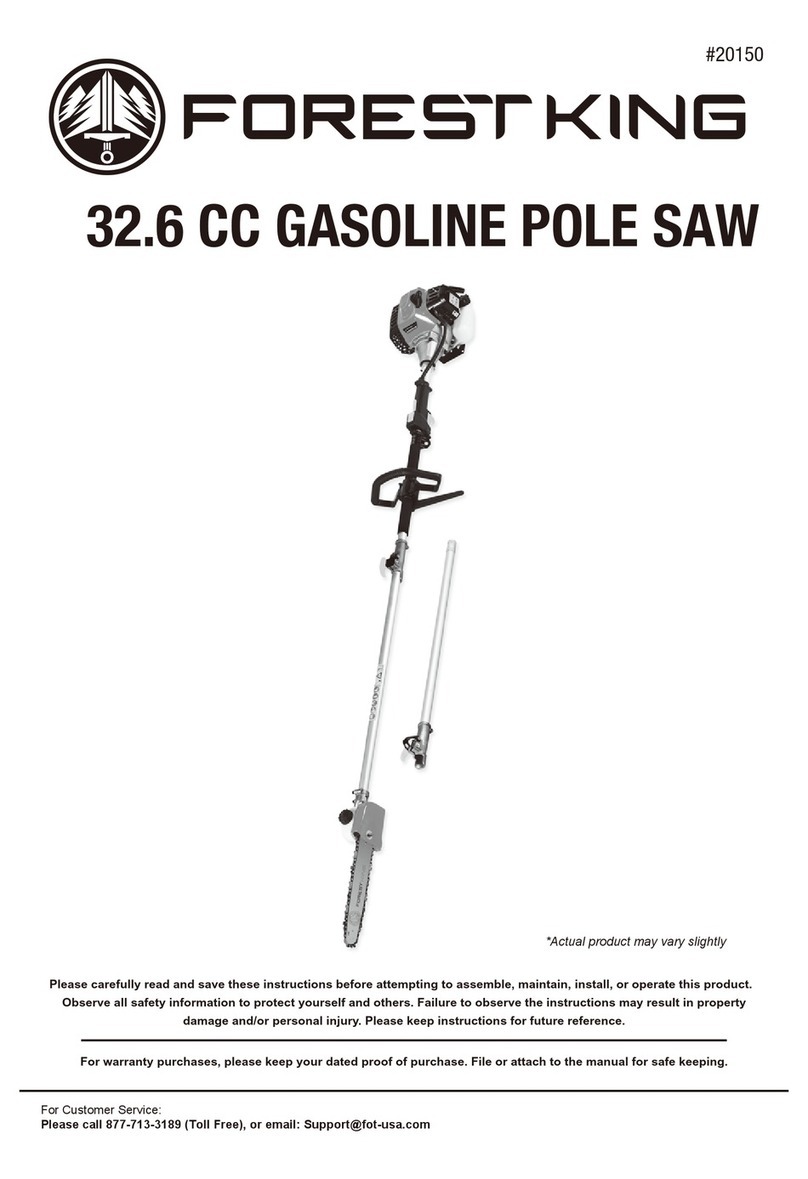
Forest King
Forest King 20150 manual

GÜDE
GÜDE GKS 1100 P manual