Lamtec F 200 K Guide

Technical documentation F 200 K Compact flame detector
Sensors and systems
for industrial flame monitoring
• Compact casing with integrated flame
sensor and switching amplifier
• Sensitivity adjustment in multiple steps
• Digital circuit design for flame evaltion
• LED status indicator
• 24 V DC operating voltage
• Dual-channel system with electronic self-
monitoring
• LED bar flame intensity indicator and
4 (0) ... 20 mA measuring output
• Selectable trend indicator allowing opti-
mum adjustment to the flame direction

- 2 -
Table of Contents
1 General remarks ..........................................................................................................4
1.1 Allow for compliance with the Equipment Safety Act ................................................................................. 4
2 Safety instructions ......................................................................................................5
3 Operating instructions ................................................................................................6
3.1 Application .................................................................................................................................................. 6
3.2 Purpose intended ....................................................................................................................................... 6
3.3 Design......................................................................................................................................................... 6
3.4 Mode of operation....................................................................................................................................... 7
3.5 Basic circuit diagram .................................................................................................................................. 8
4 Technical parameters..................................................................................................9
4.1 Characteristics............................................................................................................................................ 9
4.2 Operating conditions................................................................................................................................... 9
5 Selection criteria........................................................................................................11
6 Installation and assembly instructions....................................................................12
6.1 Assembly / Basic instructions ................................................................................................................... 12
6.2 Installation ................................................................................................................................................ 13
6.2.1 External installation .................................................................................................................................. 14
6.2.2 Device connection .................................................................................................................................... 14
7 Instructions on commissioning and maintenance .................................................14
7.0 Display and operational controls .............................................................................................................. 14
7.0.1 Intensity indicator including the “Adjust“ function / section 9.1 + 9.2, items 3 and 6................................ 15
7.0.2 Sensitivity range - indication / section 9.2 items 10 and 11 .................................................................... 15
7.0.3 Operating state - indication / sections 9.1 + 9.2, items 1 and 2 .............................................................. 15
7.0.4 Sensitivity – Switch/ sections 9.1 + 9.2, items 4 and 5 ........................................................................... 16
7.0.5 Frequency – Switch / section 9.2, item 6.................................................................................................. 16
7.0.6 Service – Switch Serv. / section 9.1 + 9.2, item 6 ................................................................................ 16
7.0.7 Adjust – Switch / section 9.1 + 9.2, item 6 ............................................................................................... 16
7.0.8 Start-up suppression - Potentiometer / sections 9.1 + 9.2, item 9 ........................................................... 16
7.0.9 Measuring points / section 9.1 + 9.2, items 7 and 8................................................................................ 16
7.1 Commissioning ......................................................................................................................................... 16
7.1.1 General remarks....................................................................................................................................... 17
7.1.2 Preparative measures .............................................................................................................................. 17
7.1.3 Adjustment................................................................................................................................................ 18
7.1.4 Checking the flame shut-down on fault .................................................................................................... 20
7.1.5 Fault on flame detection ........................................................................................................................... 20
7.1.6 Faults during ignition ................................................................................................................................ 21
7.1.7 Faults during operation............................................................................................................................. 22
7.2 Troubleshooting........................................................................................................................................ 20
7.3 Commissioning flow chart......................................................................................................................... 22
7.4 Maintenance ............................................................................................................................................. 23
7.4.1 General remarks....................................................................................................................................... 24
7.4.2 Instructions on troubleshooting ................................................................................................................ 24

- 3 -
8 Guarantee and delivery terms.................................................................................. 23
9 Layout of the operational controls .......................................................................... 24
9.1 F 200 K1 … (in the state as delivered)..................................................................................................... 24
9.2 F 200 K2 … (Ex-proof), (in the state as delivered) .................................................................................. 25
10 Dimensional drawings .............................................................................................. 26
10.1 F 200 K … and F 200 K Compact Flame Detectors... Z2 (hazardous area II)......................................... 26
10.2 F 200 K2 … Compact Flame Detector Ex (hazardous area I) ................................................................. 27
10.3 Connection housing FG 24 Ex ................................................................................................................. 27
11 Pin configuration....................................................................................................... 28
11.1 F 200 K1 … .............................................................................................................................................. 28
11.2 F 200 K2 ... (Ex) ....................................................................................................................................... 29
12 Examples of application ........................................................................................... 30
12.1 Interconnection with Etamatic .................................................................................................................. 30
12.2 Interconnection with FMS......................................................................................................................... 30
13 Accessories............................................................................................................... 31
13.1 FN 20 mains supply unit........................................................................................................................... 31
13.1.1 Purpose .................................................................................................................................................... 33
13.1.2 Technical parameters............................................................................................................................... 33
13.1.3 Pin configuration....................................................................................................................................... 35
13.2 Adjustable holding devices....................................................................................................................... 36
13.2.1 FS 19-10 (for IR and UV, without ball-and socket-joint, with purge air connection) ................................ 38
13.2.2 FS 20-10 (for IR and UV, with ball-and socket-joint and purge air connection)....................................... 38
13.2.3 FV 19-10 (for IR and UV, without socket-and-ball-joint, with purge air connection) ................................ 39
13.2.4 FV 20-10 (for IR and UV, with ball-and-socket-joint and purge air connection)....................................... 39
13.2.5 FS 50 (without ball-and-socket-joint and cooling air housing) ................................................................. 40
13.2.6 FS 51 (with ball-and-socket joint and cooling air housing)....................................................................... 41
13.3 Installation in the cooling air housing ....................................................................................................... 40
14 EG Certificate of Conformity.................................................................................... 41
15 EC Prototype testing certificate............................................................................... 42
16 TÜV Certificate .......................................................................................................... 43

- 4 -
1 General remarks
1.1 Allow for compliance with the Equipment Safety Act
The Equipment Safety Act provides the following:
Comply with the operating instruction!
Proceed as instructed by this technical documentation
(Printed matter no. DLT 7620-04D-0001).
Make sure to only use the equipment for the purpose as described herein.
Operation to be carried out by qualified staff only. The equipment may only be oper-
ated and maintained by persons capable of properly doing so based on their knowl-
edge and qualification level.
Liability for proper functioning of the equipment will be transferred to the owner
or operator by law.
Liability for proper functioning of the equipment will be transferred to the owner or op-
erator by law if the equipment is improperly operated, maintained or repaired by per-
sons that do not have the knowledge required, or if the equipment is handled in a way
not complying with the purpose intended.
LAMTEC GmbH & Co KG shall not be held liable for any damage caused by non-
compliance with the instructions given in this manual. The warranty and liability condi-
tions of LAMTEC GmbH & Co KG shall not be extended by the instructions as given
hereinafter.
Any reference to laws, regulations and standards shall be subject to the legislation of
the Federal Republic of Germany.

- 5 -
2 Safety instructions
This operator manual uses the following symbols to mark important safety instructions
to be complied with by the user. In the following sections, this symbols appear in texts
at places where the information is required. Make sure to comply with these safety in-
structions, in particular note the warnings.
WARNING
marks possible risks for persons, especially emanating from electrical equipment.
WARNING
makes reference to possible risks for persons if system components are handled im-
properly.
CAUTION!
makes reference to dangers for system components or to a possible deterioration of
the equipment's operability.
NOTE:
comprises additional information of importance for the user on the system or system
components, and provides additional hints.
This appears in instructive texts to indicate that something has to be done.
In this context, we remind the operator to comply with the accident prevention regula-
tions in connection with all activities, and to do its best to avoid injury to persons and
damage to property in way as circumstances will allow.

- 6 -
3 Operating instructions
3.1 Application
These operating instruction apply to the F 200 K compact flame detector.
The devices comply with the following standards and rules:
DIN EN 230
DIN EN 298
DIN VDE 0116
97/23/EG (directive on pressurised equipment)
90/396/EWG (directive on gas equipment)
DIN EN 60730, part 1 and IEC 801, part 5 (leakage paths and sparking-distance in air
as well as interference susceptibility)
Product identification no.: CE- 0085 BO 0005
3.2 Purpose intended
In single-burner and multiple-burner furnaces, the flame detector performs a high-
safety monitoring of the burner flames. When the flame goes out, the safe control
state “Flamme out“ is reached.
The flame detector is mainly used in large-scale power plants, thermal power stations
and chemical plants as well as for monitoring furnaces which are operated from
- OIL
- GAS
- BIO-MASS
- DUST COAL
- CHEMICALS AND OTHER WASTE PRODUCTS.
3.3 Design
The compact-type flame detector is composed of a cylindrical casing comprising a
light incidence aperture that is in line with the axis a processing status indicator on its
rear side as well as operational controls, which can be accessed there when removing
the cover.
When closed the flame detector complies with the requirements of IP 67 protection
degree.
The detector is installed at the burner by optionally using the FS 19, FV 19, FS 20, FV
20 adjustable holding devices or with an air-cooled housing of the FS 50 or FS 51
types.
The detector consists of the following functional units:
- Sensor unit providing for digitalisation of the flame signal
- digital frequency evaluation
- Self-monitoring
- Switching amplifier
The device is connected through an integrated standard plug and using the a connec-
tion cable required for this (8 pins, static screen,
cable type LiYCY 8x1x0,5 mm²) with coupler.

- 7 -
The cable provides for the following connections:
- Infeed of auxiliary energy
- Connection of the operational earthing FPE
- Connection of external power circuits to a failsafe change-over contact to control
the control states "Flame out" and "Flame in"
- Connection of the intensity measurement output
- Connection for an external sensitivity change-over, only for F 200 K2
- Connection of the screen via the plug enclosure
The layout of the operational controls is represented in section 10.
3.4 Mode of operation
The compact flame detector converts the flame radiation pulses of the burner flame
into electrical signals. These representative signals are routed to an electronic
changeover switch, which alternately applies them to one of the independently work-
ing processing channels, where the signals are digitised. This reduces the initial signal
quantity to the information "pulse period" (information carrier: pulse frequency of the
flame radiation). The digitised signals are compared with the related reference signals
by means of a digital frequency evaluation unit. This makes sure that only those flame
signals that are within the pre-selected frequency transmission range will be included
in a continued processing, irrespective of their original amplitude. A control switch (for
the F 200 K2 only) located below the removable cover allows to change the lower fre-
quency limit if required. After evaluation, the flame signal is routed to the switching
amplifier, which also controls the related shut-down time. A safe monitoring of the
antivalent control states as well as the response and shut-down periods is performed
at the output of the signal processing channels, before an activation of the output re-
lays at the end of each signal processing channel is carried out. Antivalence faults and
deviation in time delays going beyond the admissible limit values result in the control
state "Flame out". The control states “Flame out“ and “Flame in“ are indicated on the
rear side of the device by means of a red and/or green LED, the change-over between
the two signal processing channels being indicated by pulsation of the green LED dur-
ing the “Flame in“ control state. Moreover, one or two six-step control switches provide
for a sensitivity adjustment to adapt the system to the flames to be monitored, this be-
ing indicated by means of a six-step chain of green LEDs designed to be the device's
flame intensity indicator.
Miscellaneous
Self-monitoring principle
Signal processing is carried out by means of two transmission channels working inde-
pendently of each other and alternately triggered. The output levels are permanently
checked for antivalence within a given time grid.
Parameter adjustment, furnace type →Monitoring equipment
The turning knob controls of the F 200 K1 / F 200 K2 compact flame detectors allow to
set 6 to 12 sensitivity levels, the F 200 K version providing an increased sensitivity
level in range II. A six-step green LED indicator indicates the evaluated flame intensity
on the rear side of the device. The transmission range of the digital flame frequency
evaluation allows for signal passage between10 ... 190 Hz (F 200 K1) and/or 10 / 30 /
45 ... 190 Hz (F 200 K2).

- 8 -
3.5 Basic circuit diagram
Intensity remote
indicator
Visual intensity
indicator
GND
GND GND
Self-
monitoring
Monitoring
cycle
Output relay
cycl
e
safe de-coupling safe de-coupling
digital band pass digital band pass
1
0/20/30...190 Hz
Switching amplifier
channel A
Switching amplifier
channel B
Channel A Channel B
Detector
Flame sensor
Stabilisation
U
BCycle
Switch-over
contact
1...6 7...1
21...6 7...1
2
Sensitivity
selector switch
0/4...20mA
Output
contacts
10/20/30...190 Hz

- 9 -
4 Technical parameters
4.1 Characteristics
The compact flame detector is available in 2 basic versions, apart from an ex-proof enclosure type with several
spectral varieties (IR / UV).
Design type F 200 K1... F 200 K2... (Ex)
Sensitivity range 1 sensitivity range
6 levels
2 sensitivity range
increased sensitivity in
range II, can externally be
switched over,
6 levels each
Frequency range 10 ... 190 Hz 10/30/45 ... 190 Hz,
can be adjusted on the device
Signals lying in the mains frequency range or its multiples are suppressed for 50 Hz
mains generally. For 60 Hz application, please indicate separately in your order form.
The related stop ranges are changed in factory. The compact flame detector is ac-
cordingly marked by a type plate.
4.2 Operating conditions
Input parameters
Auxiliary energy, input
- Supply voltage 24 V DC ± 20%, protection class III
- Power consumption ≤4 W
spectral radiation range and sight angle
- F 200 K1 UV-1 and F 200 K2 UV-1 (Ex) 260 ... 400 nm about 8°
- F 200 K1 UV-2 and F 200 K2 UV-2 (Ex) 210 ... 380 nm about 8°
- F 200 K1 IR-2 and F 200 K2 IR-2 (Ex) 850 … 1200 nm about 50°
- F 200 K1 IR-1 and F 200 K2 IR-1 (Ex) 1200 ... 2800 nm about 60°
Response sensitivity 25 mV AC
Range remote switch-over (F 200 K2 only) floating contact, can be controlled by
means of the supply voltage (refer to section 12.2)
- Control current about 10 mA
Output parameters
Output contact Chang-over contact (floating)
- admissible switching voltage 48 V DC max., protection class II
(250 V AC by mains supply FN 20)
6 V AC/DC min.

- 10 -
- admissible switching current 0.5 A maximally
10 mA minimally, at a limit
load of 50 mA
- Switching capacity 0.1 W minimally
30 W maximally
- Internal fuses, 500 mA slow IEC and/or
750 mA slow UL
- Safety period "Operation" t VOff ≤1 s and/or ≤3 s,
factory set
- Start-up delay t VOn ≈1 s and/or ≈3 s
Measuring output for intensity
- Output continuous current 4 (0 )... 20 mA, there is no insulation
of potential towards the supply
voltage
- Maximum working resistance 220 Ω
- Floating DC voltage 6.6 V
- Basic error ±2 %
Dynamic characteristics
Self-monitoring cycle t CYCLE ca. 3.0 s for safety period
t
VOff ≤1 s
t
CYCLE ca. 7.0 s for safety period
t
VOff ≤3 s
Cable length LiYCY 8x1x0.5
Coupling part with standard cable length 3 m
(is also available in variable length if the customers requires so)
Extension of more than 3 m with LiYCY 8x1x0.5 to 50 m
Extension of more than 3 m with LiYCY 8x1x1.0 to 100 m
Extension of more than 3 m with LiYCY 8x1x2.5 to 250 m
Taking into account the electrical basic conditions, it also possible to bridge major dis-
tances using smaller cable core sections. An important criterion is the compliance with
the supply voltage limits at the compact flame detector, and thus the voltage drop in
supply voltage coming through the supply line.
Technical stressability
Operating mode DB
Creepage distances and clearances DIN EN 60730 part 1
Interference susceptibility DIN EN 60730-1, EN 61000-4
Emitted interference DIN EN 55011/A1
Radio interference suppression
The output contacts of the flame detector have no radio interference suppression. The
user is required to take the appropriate radio interference suppression measures on
the basis of the overall installation design. In order to ensure the required safety, carry
out the installation circuitry in such a way as to avoid shorting-out of the contacts by
defective components of the interference suppression unit.
Climatic stressability
Installation category Temp. min. - 20 °C
max. +60 °C
rel. air humidity 80 % at 35 °C

- 11 -
Vibration fatigue limit
according to EN 298, section. 6.5.2.2.2 2 g
function tested 5 g
Protection type IP 67; in closed state
Mass 0.6 kg
Storage conditions (in original packing)
Storage location closed premises
Air temperature - 40 ... +70 °C
Air humidity max. 80% at 35 °C
Transport conditions (in original packing)
Type of transport in closed holds
Air temperature - 40 ... + 70 °C
Temperature - humidity - coupling max. 80% at 35 °C
Wear and tear parts n o n e
5 Selection criteria
Type Spectral range Application - Fuel type
F 200 K1 UV-1 260 ... 400 nm Oil, gas
F 200 K2 UV-1 (Ex)
F 200 K1 UV-2 210 ... 280 nm Oil, gas (special gasses such as
F 200 K2 UV-2 (Ex) refinery and blast furnace gases)
F 200 K1 IR 2 850 … 1200 nm Monitoring of combustion chambers
F 200 K2 IR-2 (Ex) and burn edges (coal, wood)
F 200 K1 IR-1 1200 ... 2800 nm Oil, gas, wood, coal, furnaces with
F 200 K2 IR-1 (Ex) heavy flue gas recirculation, waste
gasses with yellowish colour with-
out UV radiation and/or screening
of the UV portions by vapour, dust
etc.

- 12 -
6 Installation and assembly instructions
6.1 Assembly / Basic instructions
The radiation emitted by a flame contains a pulsating portion (flickering). This results
from the processes, which occur during combustion, the oscillation frequency (flame
frequency) of which is used for monitoring. The compact flame detector is installed at
the burner at the viewing port provided for this and using the appropriate adjustable
holding device. Make sure that the burner flame remains perfectly visible through-
out the "Operation range of the furnace". To install a simple selective monitoring
device, the viewing port should be located in such a manner that the flame sensor de-
tects the flame root (near the burner mouth) of the burner flame to be monitored, and
that it cannot directly look into an adjacent flame or a flame located on the opposite
side. This is also of special importance as to background flames (coal, wood, waste).
The compact flame detector:
-is to be aligned in such a way as to cover the first third of the flame for single mo-
nitoring.
- has to cover the flame root area for a simple selection during the "Flame in" control
state (area of high flame frequencies), and during the "Flame out" state to only de-
tect the residual radiation caused by the "off-shoots" of the other flames in the
combustion chamber (area of low flame frequencies) or by reflection.
- If possible avoid to arrange the compact flame detector in parallel with the flame
axis, since in this position, a flame rupture can hardly be detected.
In order to reach a high availability and a high selection quality, it is very important to
place the compact flame detector at the appropriate location.
Make sure in every case that the aperture angle for the UV solutions is only about 8°.
That's why we recommend to use the FS 20 and/or FV20 adjustable holding device
(ball-and-socket joint), unless already in place. A correct alignment is of paramount
importance in particular in such cases where there is an additional viewing tube in-
side the burner or where the visibility of the flame is considerably restricted. The instal-
lation site must be easily accessible to allow a perfect observation of the visual opera-
tional controls even during operation of the furnace. When replacing the compact
flame detector, make sure to install a device having the same identification marking.
Make sure that the maximum admissible ambient temperature of 60 °C is not ex-
ceeded at the installation site. This applies in particular to radiant heat.
For the installation of an extension cable on site, make sure to use a separate,
shielded extensionable. Moreover, provide for good continuity of the shield and
make sure that the shield and functional earthing (FPE) are connected properly.
We recommend to lay the supply cable, including extension cable, on separate cable
trays to keep mains and control lines as well as high-energy power lines and equip-
ment separated from each other (e.g. ignition lines, ignition transformer, electrical mo-
tors, contactor). Moreover, avoid any parallel cable routing together with mains cables
in trays.
CAUTION!
Very high levels of electromagnetic radiated noise may result in sporadic problems in
flame detection, or may even avoid proper detection at all.

- 13 -
6.2 Installation
6.2.1 External installation
Output contacts
The flame detector ready for operation delivers the "Flame in" or "Flame out" status
message to a floating output contact. Further signal processing has to be carried out
by the controller adapted to the related furnace.
To guarantee a high safety level make sure when installing the output contacts to lay
out the circuitry of the radio interference suppression system to be provided by the
user in such a manner as to avoid shorting-out of the contacts due to faulty compo-
nents of the radio interference suppression unit.
Remote switch-over of sensitivity
The remote switch-over may only be effected by using a floating contact via the 24V
supply of the flame detector.
Intensity remote display (4 / 0 - 20 mA current loop)
Only potential-free devices may be connected complying with the requirements for
protective low voltage (SELV) (safe insulation according to DIN EN 50178).
6.2.2 Device connection
Refer to pin configuration section11

- 14 -
7 Instructions on commissioning and maintenance
7.0 Display and operational controls
Represented in section 9
7.0.1 Intensity indicator including the “Adjust“ function / section 9.1 + 9.2, items 3 and 6
Intensity indication is effected by means of a roaming light dot in 6 levels. The indica-
tion is delayed in accordance with switch-off time (1s and/or 3s) and fulfils 2 functions.
1. Display of the evaluated intensity / basic setting
The Adjust switch has to be in the OFF position. The flame signal that has already
been analysed for amplitude and frequency is displayed. For a well recognised
flame signal, the display in normal state shows the maximum position (uppermost
green LED). There might be a signal rupture in the green LED row for a short pe-
riod depending the behaviour of the flame to be monitored. If such signal rupture
occur very frequently, this may result, however, in a switch-off during a prolonged
operation.
2. Display of the unevaluated intensity (direct signal at the probe element)
The Adjust switch has to be in the ON position in any case. The function of the
Serv. switch is not active in this case. The direct flame signal is now shown at the
probe element without evaluation of the flame frequency. The Adjust function is
used to align the compact flame detector to the maximum of the flame radiation
using a ball-and-socket joint (refer to section 7.1.3). Normally, the display should
be in the green LED row. If the flame is stable, a reliable operation may be possible
in this function even if the two upper yellow LEDs light up. This display mode only
represents the trend of the orientation at a good accuracy, thus it is no exact
measuring device.
7.0.2 Sensitivity range - indication / section 9.2 items 10 and 11
This display type only exists in the F 200 K2 execution type. The display shows the
sensitivity ranges I or II activated by external selection. The range I (normal sensitivity)
is mainly used for high flame intensities, while range II (higher sensitivity) is used for
weaker flame intensities.
7.0.3 Operating state - indication / sections 9.1 + 9.2, items 1 and 2
The red LED shows the Flame OUT operating state, the green LED showing the
Flame IN state. In the “Flame in“ state, the green LED shows a pulsating intensity at
the rhythm of the self-monitoring cycle (1.5 s and/or 3 s). If the green LED is not pul-
sating, this may be due to a e.g. excessive interference radiation (EMV) or to a defect
of the compact flame detector. (refer to 7.1.2 and 7.2)

- 15 -
7.0.4 Sensitivity – Switch/ sections 9.1 + 9.2, items 4 and 5
Depending on the solution type (F 200 K1 or F 200 K2), there are 1 or 2 sensitivity se-
lector switches. The sensitivity selector switches can be set in 6 steps. The switches
serve to adapt the device to the existing flame intensity. (refer to 7.1.3)
7.0.5 Frequency – Switch / section 9.2, item 6
The frequency switches are only included in the F 200 K2 solution.
They are used to set the lower frequency limits of the digital filters. This allows to im-
prove the selectivity in flame detection. In the F 200 K1 solution, only the lower fre-
quency limit of 10 Hz is factory-set principally. (refer to 7.1.3)
7.0.6 Service – Switch Serv. / section 9.1 + 9.2, item 6
The Serv. service switch serves to suppress the indication during start-up and star-
ting time of the flame detector. In the state as delivered, the Serv. is in the ON posi-
tion. This function does not display any short flame signals of other radiation sources
(e.g. adjacent burners or background fire), which are not to result in a switch-on of the
flame detector.
For commissioning it is recommendable to set the Serv. switch to OFF. Short
flame signal of other sources are thus indicated even during the start-up phase. This
information is important for a probably required change of the start-up suppression
setting (refer to 7.1.3).
7.0.7 Adjust – Switch / section 9.1 + 9.2, item 6
The Adjust switch serves to feed in the unevaluated flame intensity (direct signal at
the probe element) on the intensity display of the compact flame detector. The activa-
tion of the Adjust switch (ON position) suppresses the function of the Serv. switch
(refer to 7.1.3).
7.0.8 Start-up suppression - Potentiometer / sections 9.1 + 9.2, item 9
The potentiometer serves to vary the setting of the start-up (switch-on) behaviour of
the flame detector. This setting has an influence on the switch-on behaviour of the
flame detector with regard to the flame to be monitored. (refer to 7.1.3)
7.0.9 Measuring p>YAX Coints / section 9.1 + 9.2, items 7 and 8
These measuring points serve to directly measure the flame signals at the probe ele-
ment and can be used to determine the optimal alignment, apart from intensity indica-
tion. (refer to 7.1.3).

- 16 -
7.1 Commissioning
7.1.1 General remarks
Check the compact flame detector for correct positioning on the burner. Before switch-
ing on the supply voltage, check the connections on the basis of the pin configuration as
specified herein. Refer to section 12.
The switches of the compact flame detector as delivered are set according to section
10, unless otherwise agreed. The potentiometer for start-up suppression is set to 50 %.
“Flame out" state
After switching on the auxiliary energy, the flame detector is ready for operation after
approximately 5 s. The following display has to be shown:
- Display "Flame out" LED “red“ lights up
- Sensitivity range I or II LED “yellow“ lights depending on
external pre-selection f. range I or II
(for F 200 K2 only)
“Flame in" state
To check the monitoring parameters, install the compact flame detector in the speci-
fied mounting place before starting the operation of the furnace. If the flame burns
naturally, the display should change as follows:
LED „red“ goes out
LED „green“ lights up, changing its radiation intensity antivalently to
the cycle rhythm of the self-monitoring system
Intensity indicator (lighting point) should reach 100%
7.1.2 Preparative measures
Checking the flame detector function
The flame detector can be checked for proper functioning without any burning flame.
1. Carry out the complete electrical installation of the flame detector and connect it to
the supply voltage.
A LAMTEC test emitter of the FFP 02 type (IR + UV) can be used as an auxiliary
means for flame simulation.
2. Simulation of a flame radiation in front of the flame detector's viewing port. This
can be done using a lighter or any other type of a modulated-light source (don't
use the mains frequency) having a sufficiently high intensity. For example, you
can modulate in a sufficient way the light of a lamp by moving your fingers splayed
out in front of the light source and the flame detector. However, start-up suppres-
sion requires a stable signal to do this. If necessary and if the signal is not suffi-
cient, the Serv. switch (section 9) should be set to OFF in order to make the re-
action to the simulated flame signal visible.
The flame detector has to switch on its output contacts if the flame signal is simulated
for a sufficient period of time. This is shown by the extinction of the red LED and the
pulsating light of the green LED. The 6-level intensity indicator lights up.

- 17 -
If no flame signal is delivered in spite of an apparently correct functioning, check the
output contact (refer to 7.2).
Alignment
IR- flame detectors should be installed / aligned in such a way that possible reflec-
tions form the combustion chamber are already largely suppressed by constructive
measures. A ball-and-socket joint for the alignment of the sensor to the flame is nor-
mally not required, since the optics of the flame detector is characterised by a wide
viewing angle.
UV- flame detectors should generally be used with one ball-and-socket joint only,
since the optics of the flame detector has a narrow viewing angle. That's why an opti-
mum alignment towards the flame is of utmost importance.
.
Optics
There are no special requirements for locking discs or similar components when using
IR- flame detectors. Small accumulations of dirt due to dust and similar materials are
mainly not critical for flame detection.
In UV- flame detectors, the requirements to locking discs are more strict. Make sure
to use a material that lets UV light pass (e.g. quartz) without problems. They are al-
ready contained in the LAMTEC-UV adjustable holding device (FS 19, FS 20, FV 19
and FV 20). Small accumulations of dust, water etc. are considerably more likely to
lead to problems in flame detection than IR radiation.
7.1.3 Adjustment
Sensitivity
If for the 1st burner start, there is no reaction, the sensitivity switch (flame amplitude)
can be set towards the right-hand stop position to allow a stable flame detection. The
positions 1 – 6 and/or 7 – 12 are allocated to the internal amplification of the flame
signal. Position 1 and/or 7 means lowest amplification / sensitivity as well as 6 and/or
12 highest amplification / sensitivity in the related sensitivity range.
Caution!
Make sure to react otherwise in a sufficient way to a flame not burning correctly or an
extinguishing flame next to the flame detector until successful switch-off test will have
been carried out.
After having carried out a correct burner adjustment, reduce the sensitivity again to
such an extent as to allow for a stable and safe operation. The measurable signals
should have at least 2 to 3 times the switching threshold value of 25 mV AC to al-
low a reliable recognition.
Alignment with adjustment function
To allow an optimum alignment of the compact flame detector towards the flame
(maximum flame amplitude), the intensity indicator of the device can be used by
activating the “Adjust“ function switch. The activation of the “Adjust“ switch
(ON position) suppresses the function of the Serv. switch. The intensity indicator
now represents flame amplitude detected. If the intensity has already been set to
maximum in this function, reduce the sensitivity of the active sensitivity switch to such
a level that a reaction of the intensity indicator can be noticed, in order to find the best
possible view to the flame by alignment. After having completed the adjustment work
and/or before optimisation set the Adjust switch back to OFF.

- 18 -
Measuring points
Apart from the Adjust function, the measuring points (section 10) of the device can be
used. This allows to continuously measure the unevaluated intensity.
Use a commercial potential-free measuring device, such as a manual multimeter
complying with EN 61010-1 (safe insulation), and having a measuring resistance
> 5 MΩ.
The trigger threshold for the F 200 K is at ≥25 mV AC , while the measured sig-
nal voltage can amount to maximally 3 V AC.
To allow an optimal suppression of reflections, the measured values should be
clearly below the specified value of 25 mV AC of the response threshold after burner
switch-off.
Frequency setting
An adaptation to the burner flame can additionally be effected in the F 200 K2 (ex-
proof) as to the lower frequency limit (section 9.2, item 6). This frequency allows no
remote switch-over. Generally, a low frequency limit means a higher availability, how-
ever a reduction of the selectivity.
3 levels are provided for.
The setting (changeover to another frequency range) has always to be carried out for
both processing channels A and B in an identical way.
Moreover, always make sure that only one frequency range in ON position is selected
each time.
Start-up suppression
If on burner start, there are short flame pulses in the set transmission range due to in-
tense background fire and/or adjacent burners, thus likely to cause problems with
burner start ( light emitted by other sources ), a change of start-up suppression ac-
cording to the technological circumstances can be used to suppress the undesired
flame pulses.
The start-up suppression function (refer to section 7.0.8, separately adjustable) allows
to suppress short pulse rates, which may occur on burner start in connection with the
fan operation (pre-ventilation) and background fire. The values can be set between 0
and 100 % at a continuous start-up delay of 1s, i.e. that short pulse rates that may re-
sult in extraneous light signalling during the burner start phase, but don't represent no
continued flame signal, are excluded from evaluation (suppressed) with differently in-
tensive ways. When 0% has been set, the flame detector is activated even on im-
proper flame signals, at a setting of 100% however, an activation requires very proper
and stable flame signals.
In case of improperly starting flames, an excessive start-up suppression impedes a
timely recognition of the flame.
The devices are delivered with start-up suppression of 50 % factory pre-set 50 % and
the Serv. switch pre-set to the ON position (deactivated).
Carry out resetting according to the requirements as follows:
(cf. the representation of the operational controls in section 10)
- Set the Serv. switch to the OFF position, this allowing to make the pulses visible
during the start-up time via the devices' intensity indicator
- Set the start-up suppression (section 10, item 9) according to the amplitude of the
pulse rates between 0 and 100 %
After completion of the settings and/or optimisation, reset the Serv. switch to the ON
position.

- 19 -
Caution!
However, this setting operation should only be used if the alignment of the flame
sensor, as well as sensitivity and frequency settings as to reliability have fully been
used.
7.1.4 Checking the flame shut-down on fault
Simulate a flame rupture or flame extinction. To this end, shut off the fuel supply to the
burner to be monitored by the flame detector. Check that the signal for shutting-off the
safety valve is triggered off within the period of TS< 1 s (on safety period “Operation“ at
tVOff = 1 s) after extinction of the flame.
LED „red“ lights
LED „green“ dark
For the IR compact flame detectors of the F 200 K1(2) IR-1 and/or F 200 K1(2) IR -2
types, take into account the special reflection effects caused by the combustion
chamber. Consequently, switch-off tests have to be carried out when the boiler has
the operating temperature. In particular, make sure that the sensitivity of the compact
flame detector is increased only to such a value required to safely and reliably monitor
the flame throughout the operating range of the burner.
7.1.5 Fault on flame detection
Check this function according to section 7.1.2.
1. Interference
Generally, interference becomes apparent by the fact that the intensity indicator of the
device may indicate 100 %, but the green LED (“Flame in“) doesn't light up. Or, the
green LED lights up for a moment, but then it doesn't change its intensity according to
the cycle rhythm and goes out again. This is a cycle synchronisation fault (signal in
both evaluation channel present at the same time). This may chiefly be due to the in-
terference emission of the ignition transformer during ignition.
- Check the shielding and FPE for proper connection to the F 200 K
- Carry out a proper grounding of the ignition transformer
- Check the cables for laying and if required untangle / separate them spa-
tially
2. Excessive temperatures
Make sure that the maximum admissible ambient temperature of 60 °C is not ex-
ceeded at the installation site. In case temperatures are expected to be higher, take
appropriate cooling measures (e.g. cooling air enclosure FS 50 or FS 51, section
14.3). Moreover, make sure that the flame detector casing doesn't heat up beyond this
temperature value due to the impact of the heat radiated by the boiler. Overheating
will result in a sensitivity loss in the first line, or will cause damage to the sensor ele-
ments and with it may result in a total failure of the system.

- 20 -
7.1.6 Faults during ignition
Faults occurring during ignition may have 4 causes.
1. In case of additionally monitoring the pilot flame, the pilot flame may not suffi-
ciently be detected.
Check the pilot flame for stable operation
Check that the pilot flame is sufficiently visible within the viewing scope of the
compact flame detector, and change pilot burner adjustment if required.
Realign the flame detector and check for cleanness of the viewing port
Measure the flame radiation captured by the compact flame detector (section
7.1.4), and optimise alignment if required.
Increase sensitivity if required.
2. Interference
Refer to section 7.1.5
3. If the flame has trouble to start-up, a timely recognition of the flame may be ham-
pered by an excessive start-up suppression.
4. Defect in the device
7.1.7 Faults during operation
Faults occurring during operation may have 3 causes.
1. The main flame may not sufficiently be detected.
- Check the main flame for stable operation - provide for visibility throughout the
operating range
- Check the compact flame detector for proper alignment and make sure that
the viewing port
- Measure the flame radiation detected by the compact flame detector (section
7.1.4), optimise alignment if required
- Increase the sensibility if required
2. Interference refer to section 7.1.5
3. Defect on the device
7.2 Troubleshooting
on apparently immaculate functioning according to the indicator elements
1. Check the output contact fuse and the contact
- Disconnect the flame detector from the supply voltage
- Check the normally-closed output contact at the 1st clamping point behind the
flame detector between the brown (BR) and the white (WH) connection wire
(avoid low-resistance continuity check – fuse 500 mA)
- Connect the flame detector to the supply voltage
- Check with simulated flame between the brown (BR) and the green (GN) con-
nection wire
Table of contents
Other Lamtec Security Sensor manuals
Popular Security Sensor manuals by other brands
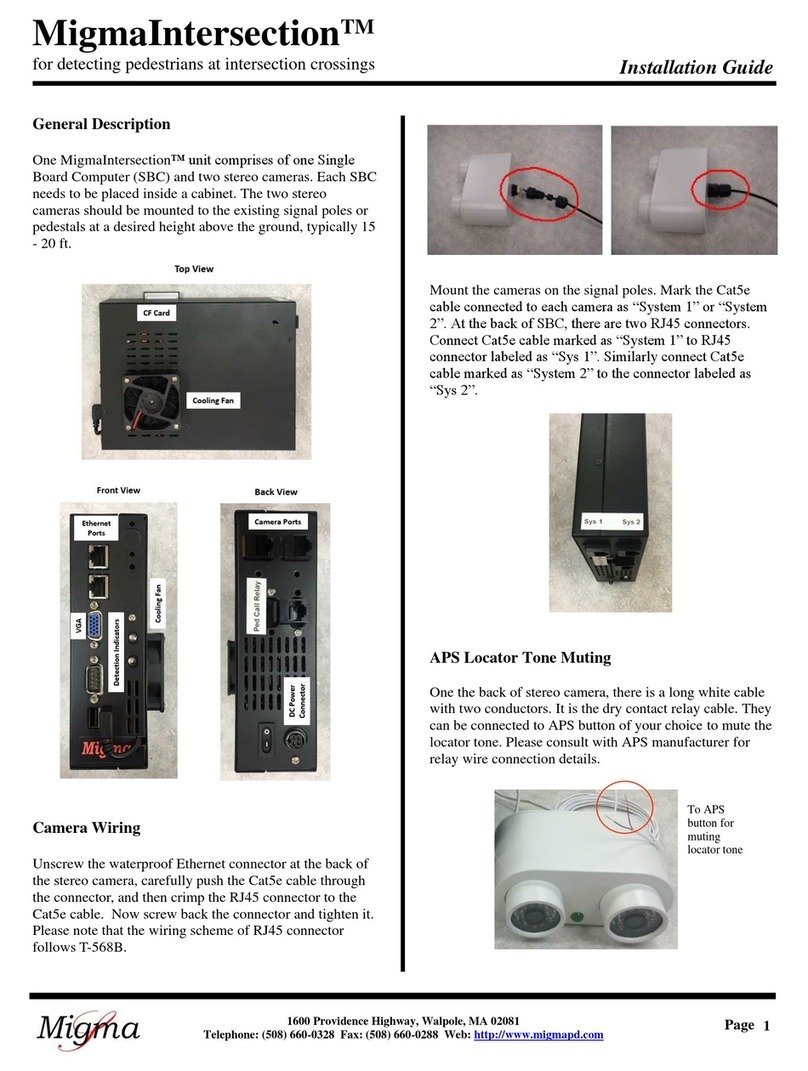
Migma
Migma MigmaIntersection installation guide
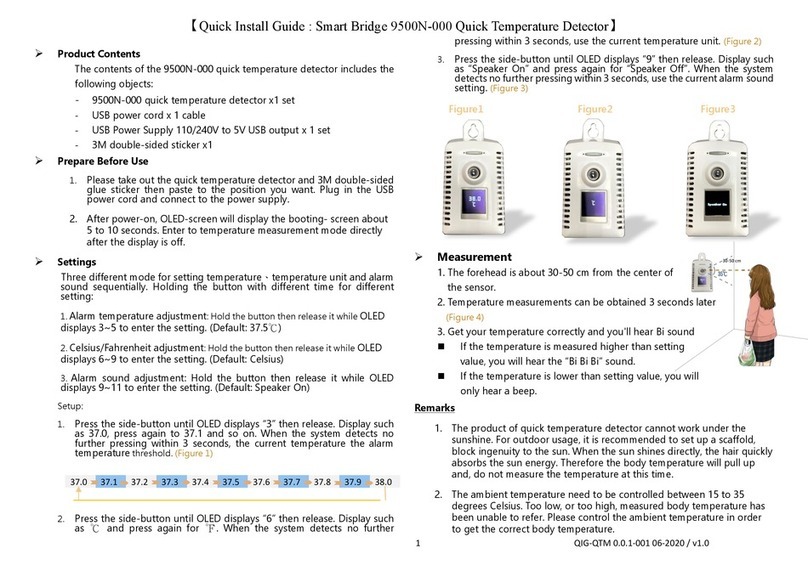
Smart Bridge
Smart Bridge 9500N-000 Quick install guide

Robertshaw
Robertshaw 365A instruction manual

Polimaster
Polimaster PM1704 Operation manual
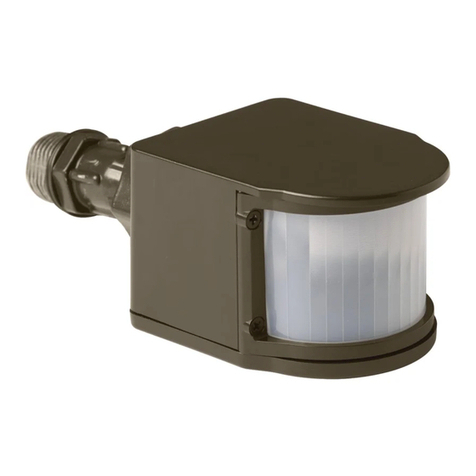
Progress Lighting
Progress Lighting P6345 Series Assembly/installation instructions

schmersal
schmersal BNS 16 operating instructions