lancer S8E V3 Series Manual

www.lancerbeverage.com
S8E V3 Hi-Carb Superchiller
230V / 50Hz
Installation, Operation &
Service Manual

S8E V3 Hi-Carb Superchiller 230V / 50Hz
www.lancerbeverage.com Page 2 of 27
Hoshizaki Lancer reserve the right to change specifications without notice. Part No: 68000021
Images are for illustration purposes only as product may vary. No 043-3 – 19 December 2019
This page is intentionally left blank

S8E V3 Hi-Carb Superchiller 230V / 50Hz
www.lancerbeverage.com Page 3 of 27
Hoshizaki Lancer reserve the right to change specifications without notice. Part No: 68000021
Images are for illustration purposes only as product may vary. No 043-3 – 19 December 2019
Table of contents
1. Specifications and Features ................................................................................................4
1.1 Models ...........................................................................................................................4
1.2 Specifications.................................................................................................................4
1.3 Product Features ...........................................................................................................4
1.4 Options...........................................................................................................................4
2. Superchiller Safety Information ..........................................................................................4
2.1 Safety Instructions .........................................................................................................4
2.2 Recognise Safety Alert Symbols...................................................................................5
2.3 Operating .......................................................................................................................5
2.4 Service & Maintenance .................................................................................................5
2.5 Carbon Dioxide (CO2)...................................................................................................6
3. Installation..............................................................................................................................6
3.1 Receiving .......................................................................................................................6
3.2 Unpacking......................................................................................................................6
3.3 Selecting a Location ......................................................................................................6
3.4 Mounting Superchiller....................................................................................................6
3.5 Connecting Python ........................................................................................................7
3.6 Connecting to water supply...........................................................................................7
3.7 Connecting to CO2 supply ............................................................................................8
3.8 Filling unit with water .....................................................................................................8
3.9 Electrical Connection.....................................................................................................8
3.10 Plumbing the drain and CO2 exhaust...........................................................................8
3.11 Commissioning ..............................................................................................................8
3.12 Purge System ................................................................................................................9
3.13 Sanitise System.............................................................................................................9
4. Scheduled Maintenance .......................................................................................................9
4.1 Daily ...............................................................................................................................9
4.2 Quarterly ........................................................................................................................9
4.3 Half Yearly .....................................................................................................................9
4.4 Yearly.......................................................................................................................... 10
4.5 Sanitisation of Beverage System ............................................................................... 10
5. Postmix Circuit Diagram ................................................................................................... 11
5.1 Single Carbonator Superchiller (3 pumps)................................................................. 11
5.2 Twin Carbonator Superchiller (4 pumps) ................................................................... 12
5.4 Twin Carbonator Superchiller (5 pumps) ................................................................... 13
6. Electrical Circuit Diagram ................................................................................................. 14
6.1 Refrigeration Wiring Diagram..................................................................................... 14
6.2 Postmix Wiring Diagram............................................................................................. 15
7. Airflow Diagram.................................................................................................................. 16
8. Trouble Shooting................................................................................................................ 17
8.1 Refrigeration ............................................................................................................... 17
8.2 Troubleshooting – Postmix......................................................................................... 18
9. Hydra Icebank Control Go/No Go Test............................................................................ 20
10. Hydra Carbonator Level Control Test.............................................................................. 21
11. Assembly Diagrams & Parts List ..................................................................................... 22
11.1 Postmix Spare Parts List ............................................................................................ 22
11.2 Postmix Assembly Diagram ....................................................................................... 23
11.3 Refrigeration Spare Parts List .................................................................................... 24
11.4 Refrigeration Assembly Diagram ............................................................................... 25
12. Certificate of Warranty....................................................................................................... 26
13. Manufacturer’s Checklist .................................................................................................. 27

S8E V3 Hi-Carb Superchiller 230V / 50Hz
www.lancerbeverage.com Page 4 of 27
Hoshizaki Lancer reserve the right to change specifications without notice. Part No: 68000021
Images are for illustration purposes only as product may vary. No 043-3 – 19 December 2019
1. Specifications and Features
1.1 Models
S8E23LA V3 Lancer S8E Superchiller with 3 pumps, single Carbonator
S8E94LA V3 Lancer S8E Superchiller with 4 pumps, dual Carbonator
S8E95LA V3 Lancer S8E Superchiller with 5 pumps, dual Carbonator
1.2 Specifications
Voltage 230 Volts
Frequency 50 Hz
Max Current Draw Refrig 15 Amps / Postmix 10 Amps
Ambient Temperature 2 - 40°C
Heat Rejection 6346 Watts
Dimensions
Width 1300 mm
Depth 685 mm
Height 815 mm
Weight 3 pump 4 pump 5 pump
Shipping 210 kg 221kg 232kg
Empty 190 kg 201kg 212kg
Operating 372 kg 383kg 394kg
Refrigerant 1000 grams R134a x 2
Ice bank Weight 75 kg
Water Bath Capacity 180 litres
Construction Stainless Steel
Compressor Danfoss x 2
Agitator Motor 12W, 230 VAC 1 Phase
Condenser Motor 20W, 230 VAC 1 Phase
Ice bank Control Electronic
Carbonation Level Control Electronic
Drink Capacity Continuous 473ml (16 oz) drinks below 4.4°C at 4
drinks per minute with 40°C ambient, syrup inlet
temperature and 32°C water inlet temperature.
1.3 Product Features
The Lancer Superchiller is an Australian designed and manufactured remote refrigerated unit
designed to refrigerate and distribute post-mix (soft drinks) as well as maintaining the product
temperature through the python and dispenser.
1.4 Options
•
Adjustable Legs (79232218) – height with legs approx 960mm.
•
Casters (79602411) – height with casters approx. 921mm.
2. Superchiller Safety Information
2.1 Safety Instructions
For your personal safety, and that of others working around you please read, understand, and
follow thoroughly all safety instructions included in this manual and on the Superchiller.
•
Review all applicable OSH (Occupational Safety & Health) regulations.
•
Review all applicable Beverage Dispensing Gas Standards

S8E V3 Hi-Carb Superchiller 230V / 50Hz
www.lancerbeverage.com Page 5 of 27
Hoshizaki Lancer reserve the right to change specifications without notice. Part No: 68000021
Images are for illustration purposes only as product may vary. No 043-3 – 19 December 2019
•
Learn how to operate the Superchiller and use the controls properly.
•
Do not allow untrained personnel to operate the machine.
•
Ensure that the Superchiller is maintained according to service manual instructions.
•
Do not allow any unauthorised modifications to the machine.
2.2 Recognise Safety Alert Symbols
The safety alert symbol precedes Warning and Caution notes throughout this manual. To
prevent personal injury or damage to the machine these alerts must be strictly adhered too.
Warning Alerts to a potentially hazardous situation that if not avoided CAN result
in death, serious injury.
Caution Alerts to a potentially hazardous situation that if not avoided MAY result
in injury or equipment damage.
2.3 Operating
Warning
Superchillers are intended for indoor operation only; do not operate
outside unless suitably protected by a weatherproof enclosure. This
appliance is not suitable for installation in an area where a water jet could
be used.
Caution
This appliance is not intended for use by persons (including children)
with reduced physical, sensory or mental capabilities, or lack of
experience and knowledge, unless they have been given supervision or
instruction concerning use of the appliance by a person responsible for
their safety. Children should be supervised to ensure that they do not
play with the appliance.
2.4 Service & Maintenance
Caution Installation of Superchiller and service work should only be performed by fully
trained & certified Electrical, Plumbing, & Refrigeration Technicians.
Warning Carbonator contains CO2gas and water under pressure. De-pressurise before
performing any work on the system.
Warning ALL WIRING AND PLUMBING MUST CONFORM TO LOCAL AND
NATIONAL CODES.
Warning SUPERCHILLER MUST BE ISOLATED FROM ELECTRICAL SUPPLY
BEFORE COMMENCING ANY SERVICE OR MAINTENANCE WORK.

S8E V3 Hi-Carb Superchiller 230V / 50Hz
www.lancerbeverage.com Page 6 of 27
Hoshizaki Lancer reserve the right to change specifications without notice. Part No: 68000021
Images are for illustration purposes only as product may vary. No 043-3 – 19 December 2019
2.5 Carbon Dioxide (CO2)
Warning
The Superchiller uses a CO
2
(Carbon Dioxide) supply. CO
2
is a heavier
than air, colourless, non-combustible gas with a faintly pungent odour.
Personnel exposed to high concentrations of CO2gas will experience
tremors, which are followed rapidly by loss of consciousness and
suffocation.
If a CO2gas leak is suspected, immediately ventilate the contaminated
area before attempting to repair the leak.
3. Installation
Warning
To avoid personal injury or damage, do not attempt to lift a Superchiller
without help.
Use of a mechanical lift is recommended.
(NOTE: Empty S8E Superchiller weight: 212kg)
3.1 Receiving
Each unit is completely tested under operating conditions and thoroughly inspected before
shipment. At time of shipment, the carrier accepts the unit and any claim for damage(s) must
be made with the carrier. Upon receiving units from the delivering carrier, carefully inspect
shipping crate for visible indication(s) of damage. If damage exists, have carrier note damage
on bill of landing and file a claim with the carrier.
3.2 Unpacking
Caution
The use of gloves is recommended to protect hands from potential injury
from sharp edges. The Superchiller must always be handled in a vertical
position.
Carefully unpack the Lancer S8E Superchiller from the shipping carton, remove the wooden
base.
If appropriate, assemble legs to unit by carefully tilting (tilt should not be more than 45°).
Inspect unit for concealed damage and if evident, notify delivering carrier and file a claim
against the carrier.
3.3 Selecting a Location
Warning
Superchillers are intended for indoor operation only; do not operate
outside unless suitably protected by a weatherproof enclosure.
This appliance is not suitable for installation in an area where a water jet
could be used.
Caution
The Superchiller is not suitable for use in subfreezing temperatures.
To prevent damage to the water supply line, turn off and drain unit when
air temperature is below zero.
•The S8E Superchiller should be located in a well-ventilated, firm, level location close to
dispenser, water and electrical supplies, with easy access for servicing
•Ensure sufficient clearance around Superchiller to allow good fresh air circulation through
the condenser – allow at least 200mm at rear and sides.
•Installation should only be performed by a qualified and competent technician.
3.4 Mounting Superchiller
•Install on a flat, level surface using adjustable legs or casters (Optional).
•Fix to supporting structure using 4 x ¾” BSW bolts screwed into base supports.

S8E V3 Hi-Carb Superchiller 230V / 50Hz
www.lancerbeverage.com Page 7 of 27
Hoshizaki Lancer reserve the right to change specifications without notice. Part No: 68000021
Images are for illustration purposes only as product may vary. No 043-3 – 19 December 2019
Caution
Superchiller operational weight is 394kg; ensure that all supporting
structures are certified for this loading by a registered Mechanical
Engineer.
Supporting structure must be securely fixed to floors or walls.
3.5 Connecting Python
Connect Python to Chiller and Dispenser.
Caution
NOTE: The S8E Superchiller is rated to operate with a maximum of
90m of python connected at 32°C.
Exceeding manufacturer’s ratings may cause damage to the
Superchiller and void warranty.
Connect the Python to Chiller and Dispenser.
Refer to Python and Dispenser specifications for connection data.
Superchiller can be supplied with 4 or 5 pumps, dual carbonator, or 3 pumps single carbonator;
python should be connected to Chiller as follows:
5 Pump 4 Pump 3 Pump
SODA
RETURN A
WATER
RETURN
SODA
RETURN B SODA
RETURN A
SODA
RETURN B SODA
RETURN A
WATER
RETURN
SODA
SUPPLY A
WATER
SUPPLY
SODA
SUPPLY B SODA
SUPPLY A
SODA
SUPPLY B SODA
SUPPLY A
WATER
SUPPLY
Important: Ensure lines from python to Superchiller connections are insulated to prevent
condensation.
Note: For additional Soda reserve on short python lengths used in high volume accounts, it
may be necessary to extend the soda circuit by connecting the 2 spare lines in the python onto
the soda return line (i.e. double pass of soda circuit out and back from dispense point to soda
return).
3.6 Connecting to water supply
•Using appropriate tubing and fittings connect a 10mm water supply line from Superchiller
carbonator pump inlet to a filtered, regulated water supply. (See Postmix circuit diagram
page 11-13). Installation in accordance with AS/NZS 3500.1 and AS/NZS 3500.2.
•Turn on water supply, check for leaks, adjust water regulator to 172-275kpa.
S
O
D
A
S
U
P
P
L
Y
S
O
D
A
R
E
T
U
R
N
1
0
m
m
'
U
'
B
E
N
D
P
Y
T
H
O
N

S8E V3 Hi-Carb Superchiller 230V / 50Hz
www.lancerbeverage.com Page 8 of 27
Hoshizaki Lancer reserve the right to change specifications without notice. Part No: 68000021
Images are for illustration purposes only as product may vary. No 043-3 – 19 December 2019
•Purge the carbonator of air by lifting the relief valve until water discharges from the CO2
exhaust port. For dual carbonators, repeat this operation for each carbonator.
Caution Maximum water supply pressure to be 275 kpa.
Normal operating water temperature should be within 7°C to 32°C.
3.7 Connecting to CO2 supply
Warning
As carbon dioxide (CO2) displaces oxygen; prevention of CO2leaks is
paramount. If a leak is suspected, immediately ventilate the
contaminated area, before attempting repairs.
•Connect CO2 supply line from regulator to gas inlet on carbonator. (See Postmix circuit
diagram page 11 – 13 for details)
•Adjust CO2 Regulator supplying Carbonator to 550 kpa.
•Turn on CO2 supply.
3.8 Filling unit with water
Remove Superchiller lid and fill water bath until water flows out overflow tube.
NOTE: Do not use water supplied from newly installed carbon filter as ice bank control
operation will be adversely affected.
3.9 Electrical Connection
•This unit requires a separate 10 amp (Postmix) and a 15amp (Refrigeration) power
supplies.
•Check the name plate on the machine for electrical supply requirements. Use only the
power supply specified on the name plate.
Warning If the supply cord is damaged, it must be replaced by the manufacturer,
its service agent or similarly qualified persons in order to avoid a hazard.
Warning
To avoid possible fatal electric shock or serious injury the Superchiller
must be electrically grounded.
Electrical Connection Must Be Made In Accordance With The
Appropriate Local Codes And Regulations.
Use of an RCD is recommended.
3.10 Plumbing the drain and CO2 exhaust
The 19mm overflow drain tube exiting from the base of the tank should be plumbed to a
suitable drain, installation in accordance with AS/NZS 3500.1 and AS/NZS 3500.2.
The 6mm barb labelled as CO2 EXHAUST should be plumbed to an outside safe area.
3.11 Commissioning
•Unplug carbonator and recirculation pumps power supply leads from electrical box located
under lid.
•Connect Superchiller power supply lead to an appropriate 3 pin socket outlet and switch on.
Compressors, condenser fans and agitator motors should all operate.
•When Superchiller ice bank is fully formed (approx. 4 hours) the compressors and
condenser fans will cycle off, but the agitators will run continuously (unit has cycled off).
•After Superchiller has cycled off, reconnect carbonator and recirculation pumps.

S8E V3 Hi-Carb Superchiller 230V / 50Hz
www.lancerbeverage.com Page 9 of 27
Hoshizaki Lancer reserve the right to change specifications without notice. Part No: 68000021
Images are for illustration purposes only as product may vary. No 043-3 – 19 December 2019
3.12 Purge System
Progressively activate each dispensing valve or Bargun connected to the Superchiller systems
until an uninterrupted flow of soda, water (where applicable), and syrup pours from each
dispenser.
3.13 Sanitise System
Prepare sanitising solution:
Prepare sanitising solution in accordance with the manufacturer’s written recommendations
and safety guidelines.
Sanitising BIB System
•Remove all disconnects from BIB containers.
•Immerse all disconnects in warm water and clean using a nylon bristle brush. Rinse with
clean water.
•Prepare sanitising solution according to manufacturer’s instructions.
•Attach sanitising fittings to BIB disconnects, if sanitising fittings are not available cut fittings
from empty BIB bags.
•Immerse all sanitising fittings with attached BIB disconnects in bucket of sanitising solution.
Operate all dispensing valves until the sanitising solution flows from the valve. Allow
sanitiser to remain in lines for fifteen (15) minutes.
•Immerse all sanitising fittings with attached BIB disconnects in bucket of clean water.
Operate all dispensing valves until all sanitiser has been flushed from the system.
•Remove sanitising fittings from BIB disconnects and re-connect disconnects to appropriate
BIB's. Operate dispensing valves until syrup flows freely.
4. Scheduled Maintenance
The following Superchiller routine maintenance should be performed at the intervals listed.
4.1 Daily
Cleaning/Sanitising
The Superchiller supplies soda water to the dispensing valves/barguns. To ensure optimum
drink quality and system performance at all times please follow cleaning and sanitising
procedures for the dispensing valves/barguns recommended by the valve/bargun
manufacturer.
Checking CO2 Supply
Ensure that the contents gauge on the CO2 Regulator reads higher than 1400kpa on the dial. If
it does not, then the CO2 cylinder is empty and must be changed using safe working practices.
Warning
To avoid personal injury and/or property damage, always secure the
CO2cylinder with a safety chain to prevent it from falling over; and use
appropriate protective equipment (as defined in Clause 3.3.2 of AS
5034) to handle cylinders.
Should the valve become accidentally damaged or broken off, a CO2
cylinder can cause serious personnel injury.
4.2 Quarterly
The Superchiller should be connected to a filtered water supply. To ensure optimum drink
quality and system performance, supply water filters should be replaced every 3 months.
4.3 Half Yearly
•Remove & Clean condenser filters on the Superchiller. When the environment is dirty and
dusty, the interval between cleaning the filters may need to be reduced. Clean condenser
with low pressure compressed air. When using compressed air always direct air from the
fan side through condenser. Remove all dust and foreign particles from refrigeration deck.

S8E V3 Hi-Carb Superchiller 230V / 50Hz
www.lancerbeverage.com Page 10 of 27
Hoshizaki Lancer reserve the right to change specifications without notice. Part No: 68000021
Images are for illustration purposes only as product may vary. No 043-3 – 19 December 2019
Caution When using compressed air always wear safety glasses.
•Check that the water is level with the top of the overflow tube. Add water if necessary.
•Open carbonator relief valve to purge CO2 and check leakage, close relief valve after
checking.
4.4 Yearly
Water bath and recirculation pump inspection.
•Isolate Superchiller from power supply by switching off at socket.
•Thaw the bank of ice formed in the tank. Empty the water from the tank with a suction pump
or drainage pipe.
•Inspect coils and agitator in water bath for algae or slime accumulation. Clean as necessary
using a soft brush, rinse with clean water.
•Check recirculation pump strainers for accumulation, replace if necessary.
•Fill tank with clean water until water flows out the overflow tube.
•Switch on power supply and check ball position in flow indicator section of strainer. If ball
indicates flow is less than 5 litres per minute, replace pump.
•Commission and purge system as per clause 6.11 and 6.12.
4.5 Sanitisation of Beverage System
To maintain optimum quality of dispensed product each Superchiller and its associated
beverage system components must be thoroughly cleaned and sanitised annually.
Prepare sanitising solution
Prepare sanitising solution in accordance with the manufacturer’s written recommendations
and safety guidelines.
Sanitising BIB System
•Remove all disconnects from BIB containers.
•Immerse all disconnects in warm water and clean using a nylon bristle brush. Rinse with
clean water.
•Prepare sanitising solution according to manufacturer’s instructions.
•Attach sanitising fittings to BIB disconnects, if sanitising fittings are not available cut fittings
from empty BIB bags.
•Immerse all sanitising fittings with attached BIB disconnects in bucket of sanitising solution.
Operate all dispensing valves until the sanitising solution flows from the valve. Allow
sanitiser to remain in lines for fifteen (15) minutes.
•Immerse all sanitising fittings with attached BIB disconnects in bucket of clean water.
Operate all dispensing valves until all sanitiser has been flushed from the system.
•Remove sanitising fittings from BIB disconnects and re-connect disconnects to appropriate
BIB's. Operate dispensing valves until syrup flows freely.

S8E V3 Hi-Carb Superchiller 230V / 50Hz
www.lancerbeverage.com Page 11 of 27
Hoshizaki Lancer reserve the right to change specifications without notice. Part No: 68000021
Images are for illustration purposes only as product may vary. No 043-3 – 19 December 2019
5. Postmix Circuit Diagram
5.1 Single Carbonator Superchiller (3 pumps)

S8E V3 Hi-Carb Superchiller 230V / 50Hz
www.lancerbeverage.com Page 12 of 27
Hoshizaki Lancer reserve the right to change specifications without notice. Part No: 68000021
Images are for illustration purposes only as product may vary. No 043-3 – 19 December 2019
5.2 Twin Carbonator Superchiller (4 pumps)
5.3
SODA RELIEF
VALVE
SODA RELIEF
VALVE

S8E V3 Hi-Carb Superchiller 230V / 50Hz
www.lancerbeverage.com Page 13 of 27
Hoshizaki Lancer reserve the right to change specifications without notice. Part No: 68000021
Images are for illustration purposes only as product may vary. No 043-3 – 19 December 2019
5.4 Twin Carbonator Superchiller (5 pumps)
SODA RELIEF
VALVE
SODA RELIEF
VALVE

S8E V3 Hi-Carb Superchiller 230V / 50Hz
www.lancerbeverage.com Page 14 of 27
Hoshizaki Lancer reserve the right to change specifications without notice. Part No: 68000021
Images are for illustration purposes only as product may vary. No 043-3 – 19 December 2019
6. Electrical Circuit Diagram
6.1 Refrigeration Wiring Diagram

S8E V3 Hi-Carb Superchiller 230V / 50Hz
www.lancerbeverage.com Page 15 of 27
Hoshizaki Lancer reserve the right to change specifications without notice. Part No: 68000021
Images are for illustration purposes only as product may vary. No 043-3 – 19 December 2019
6.2 Postmix Wiring Diagram

S8E V3 Hi-Carb Superchiller 230V / 50Hz
www.lancerbeverage.com Page 16 of 27
Hoshizaki Lancer reserve the right to change specifications without notice. Part No: 68000021
Images are for illustration purposes only as product may vary. No 043-3 – 19 December 2019
7. Airflow Diagram

S8E V3 Hi-Carb Superchiller 230V / 50Hz
www.lancerbeverage.com Page 17 of 27
Hoshizaki Lancer reserve the right to change specifications without notice. Part No: 68000021
Images are for illustration purposes only as product may vary. No 043-3 – 19 December 2019
8. Trouble Shooting
8.1 Refrigeration
TROUBLE
CAUSE
REMEDY
Compressor will not
start.
Power Failure.
High Pressure/temperature switch
activated.
LED on Ice Bank Control board
illuminated.
Ice bank control faulty contacts not
closing.
Check start mechanism components.
Thermal overload faulty, open circuit,
compressor seized.
Check for blown fuse, supply cord pulled
out or supply outlet turned off.
Turn chiller “off” at supply socket then
“on” again to reset controller.
Check Ice bank control using Procedure
on page 20. Replace if defective.
If faulty, replace e.g. capacitors, start
relays.
Replace compressor, check condenser,
check power supply, evacuate system
and if necessary fit burnout drier to
industry standards.
Compressor short
cycling on thermal
overload (frequent
starting and stopping
of the compressor
while ice bank control
contacts remain
closed).
Dirty condenser.
Restricted air flow over unit.
Low supply voltage.
Defective thermal overload.
Check wiring connections.
Fan motor bearings tight or seized.
Clean condenser of all lint and dirt.
Check for air restriction to condenser.
Check with voltmeter.
Replace compressor.
Tighten if loose.
Replace motor(s)
Product too warm
Ice bank control defective
(permanently open circuit).
Low refrigerant charge.
Check agitator motor, seized or fused.
Check Ice bank control using procedure
on page 20.
Replace control or probe if defective.
Leak check, repair leak, charge with
correct amount of refrigerant.
Replace if not working.
Compressor runs too
long or doesn’t cycle.
Location too hot.
Superchiller overloaded.
Loss of refrigerant.
Condenser clogged.
Fan not operating.
Relocate or improve ventilation.
Use larger model or reduce python
length.
Leak check and repair.
Clean off dust, lint, grease, etc.
Remove obstruction or replace motor.

S8E V3 Hi-Carb Superchiller 230V / 50Hz
www.lancerbeverage.com Page 18 of 27
Hoshizaki Lancer reserve the right to change specifications without notice. Part No: 68000021
Images are for illustration purposes only as product may vary. No 043-3 – 19 December 2019
8.2 Troubleshooting – Postmix
TROUBLE
CAUSE
REMEDY
Rusty appearance
and/or metallic taste to
water.
Poor water supply - contaminated.
Carbon filter required.
CO
2
gas or water
escapes from
pressure relief valve.
(Observed
from CO2exhaust)
CO
2
pressure too high.
Pump motor will not stop.
Inadequate water supply.
Lines too small or restricted.
Check CO
2
pressure relief valve. Bleed
gas by opening and closing the relief
valve - set CO2 to 550 kpa.
Check carbonator control using
procedure on page 21.
Replace control or probe if defective.
If strainer and filter are clear and line
valves are fully open, noisy pump
operation indicates insufficient water
supply. Minimum water supply is 172 kpa
flowing pressure.
Poor carbonation
(low CO2volume).
Flooded carbonator.
Dirty water supply.
CO2 pressure too low.
Poor quality paper cups.
Dirty or greasy glasses.
Improperly drawn drink.
Check carbonator control using
procedure on page 21.
Replace control or probe if defective.
Check filters.
Check CO2 pressure at regulator. Should
be set between 550 kpa. CO2 inlet check
valve stuck, shut or blocked, repair or
replace.
Purchase better quality cups.
Wash all glasses.
Open faucet all the way and draw
against side of glass or cup.
Pump leaks from shaft
seal.
Worn pump seals.
Misaligned or damaged motor and
pump facings.
Replace pump.
Realign or file flat.
Pump will not run.
Power failure or low voltage.
Carb pump hi temp LED on icebank
control board illuminated.
Faulty low pressure switch (if fitted).
Defective motor.
Locked up pump. Motor has cut out
on overload.
Carbonator flooded – filled completely
with water.
Check fuses. Check power supply.
Check for icebank growth into product
coils, defrost and turn off chiller at supply
socket and turn on again to reset.
Ensure of adequate water supply. Switch
should close above 172 kpa. Replace if
defective.
Replace motor.
Replace pump.
Check mains water pressure - must be at
least 135 kpa lower than CO2 (install
water pressure regulator if necessary)
Check CO2 regulator.
Check carbonator control using
procedure on page 21. Replace control
or probe if defective.

S8E V3 Hi-Carb Superchiller 230V / 50Hz
www.lancerbeverage.com Page 19 of 27
Hoshizaki Lancer reserve the right to change specifications without notice. Part No: 68000021
Images are for illustration purposes only as product may vary. No 043-3 – 19 December 2019
Carbonator empty - faulty
Carbonator probe or control.
Low water supply pressure.
Excessive CO2 Pressure.
Check carbonator control
Using procedure on page 21.
Replace control or probe if defective.
A minimum of 172 kpa water supply
pressure is required
Check function & setting of CO2
regulator.
Faucet delivers CO2
gas continuously.
Carbonator pump will not run due to
power failure or low voltage.
Pump water supply restricted.
Carbonator pump will not run due to
excessive carbonator CO2pressure.
Faulty low pressure switch.
Defective Carbonator motor.
Locked up pump. Motor has cut out
on overload.
Carbonator empty – faulty control
board or level probe.
Carb pump hi temp LED on icebank
control board illuminated.
Check fuses. Check power supply.
Ensure clean mains water supply tap is
open or replace filters.
Check Carbonator CO2pressure
regulator for creeping. It should be set at
550 kpa.
Ensure adequate water supply (minimum
pressure 172 kpa flowing pressure).
Pressure switch is set to open below 35
kpa and reset at 172 kpa.
Check operation by plugging into
circulation pump socket momentarily.
Replace motor if necessary.
Replace pump.
Check carbonator control using
procedure on page 21.
Replace control or probe if defective.
Check for icebank growth into product
coils, defrost and turn off chiller at supply
socket and turn on again to reset.

S8E V3 Hi-Carb Superchiller 230V / 50Hz
www.lancerbeverage.com Page 20 of 27
Hoshizaki Lancer reserve the right to change specifications without notice. Part No: 68000021
Images are for illustration purposes only as product may vary. No 043-3 – 19 December 2019
9. Hydra Icebank Control Go/No Go Test
This is a test to simulate the building and erosion of the icebank; to determine if the icebank control is
operating correctly. The test assumes that all other components in the refrigeration system (e.g. high
pressure cut-out reset) are in an operational condition.
Warning
230VAC is present on terminals N, A, ON 1, ON 2 terminals.
Work should only be performed by fully trained & certified
Electrical, Plumbing & Refrigeration Technicians.
1.
Remove the ice bank probe connections from
terminals J5, J6, J7.
2.
Connect alligator jumper to terminals J5, J6, J7. Ice
bank control relay should close and refrigeration
system start.
(Simulates water covering all probes)
3.
With refrigeration system operating (ice bank control
relay energised) remove alligator jumper from
terminal J6. Refrigeration system should continue to
operate.
(Simulates ice growth over green probe. Water still
contacting red and black probes)
4.
With refrigeration system operating, remove alligator
lead from terminal J5.
Refrigeration system should stop.
(Simulates ice growth over black probe only)
This manual suits for next models
3
Table of contents
Other lancer Chiller manuals
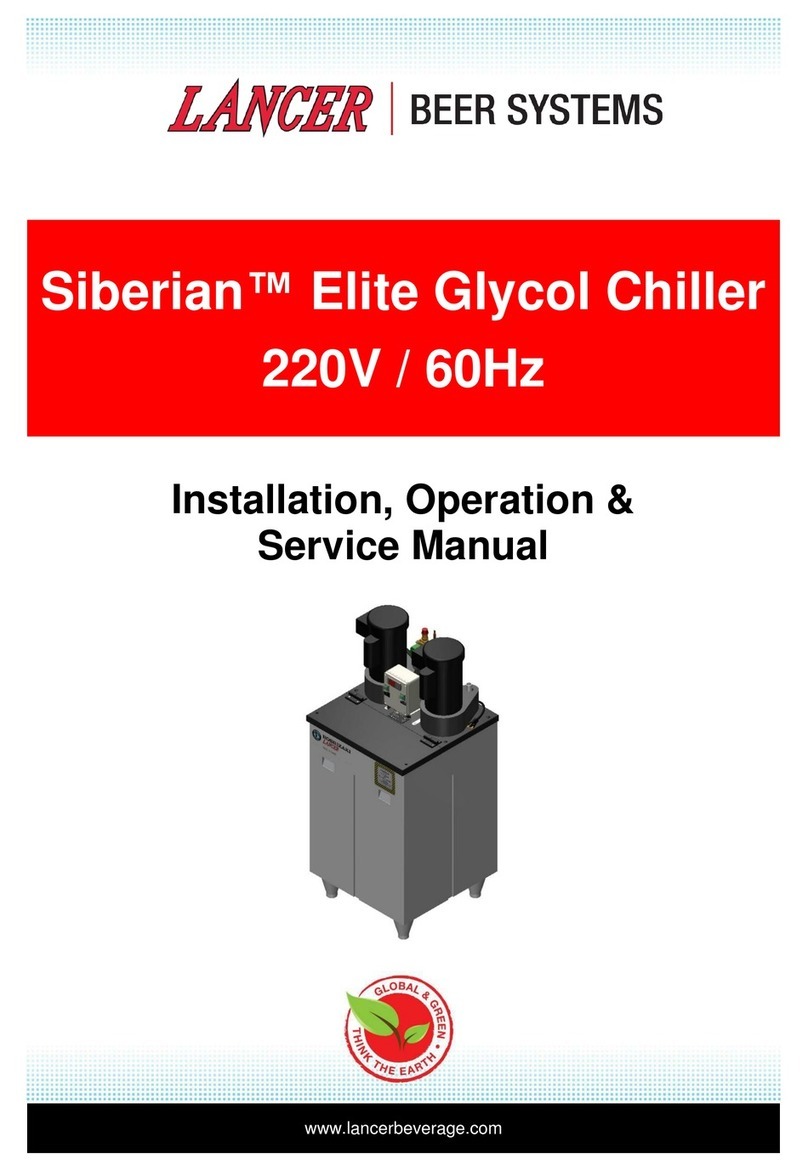
lancer
lancer Siberian Elite Series Manual
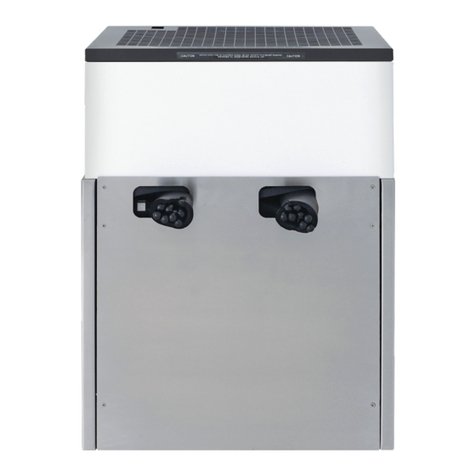
lancer
lancer SERIES 1500 POSTMIX User manual
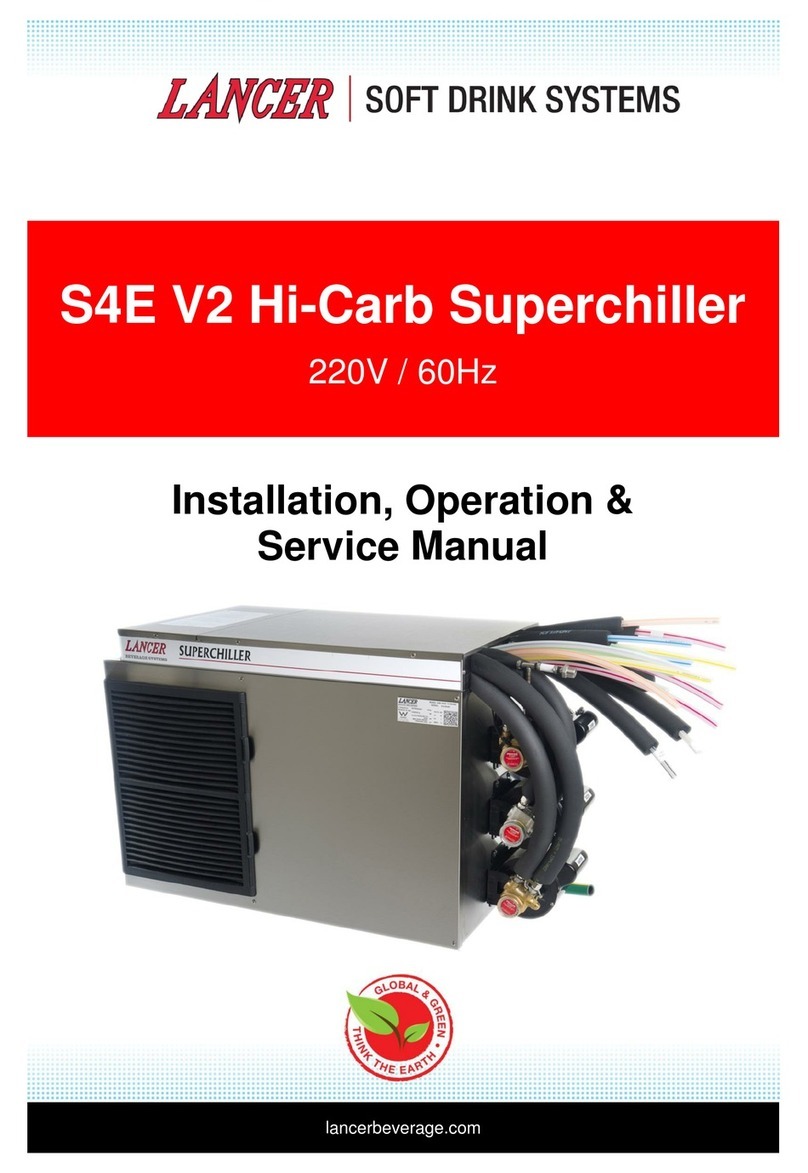
lancer
lancer S4E V2 Hi-Carb Superchiller Manual
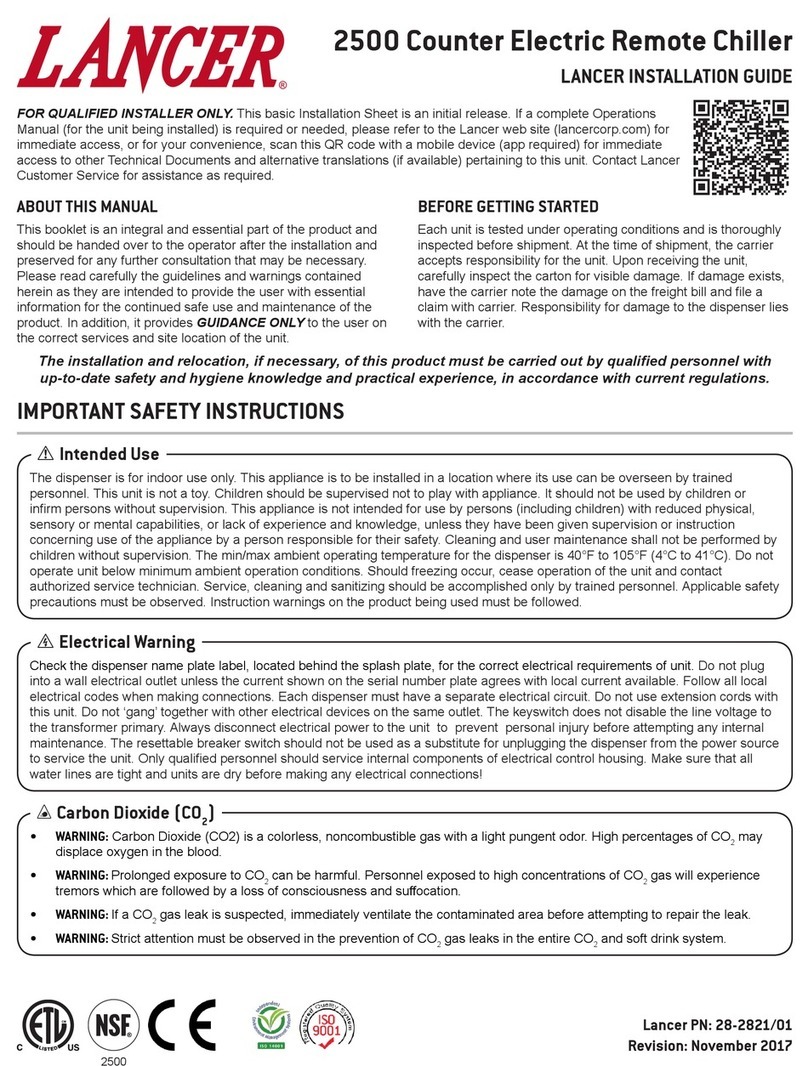
lancer
lancer 2500 REMOTE series User manual
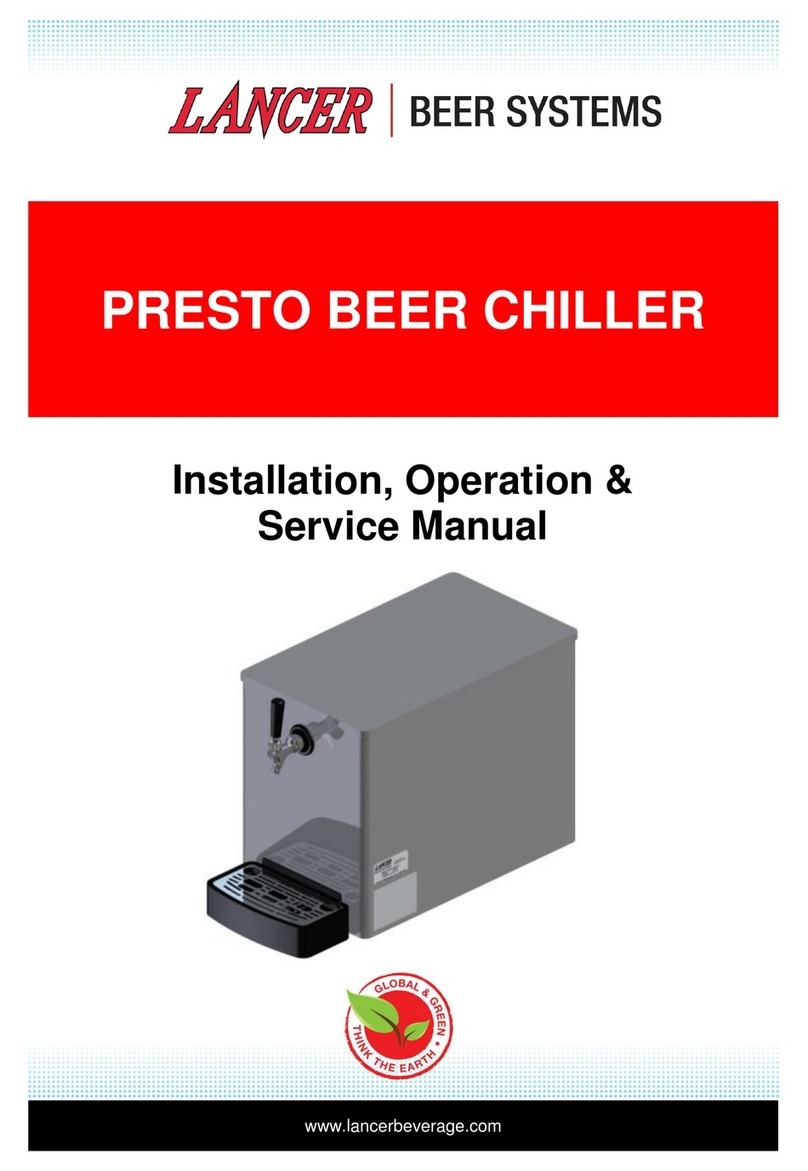
lancer
lancer PRESTO Manual
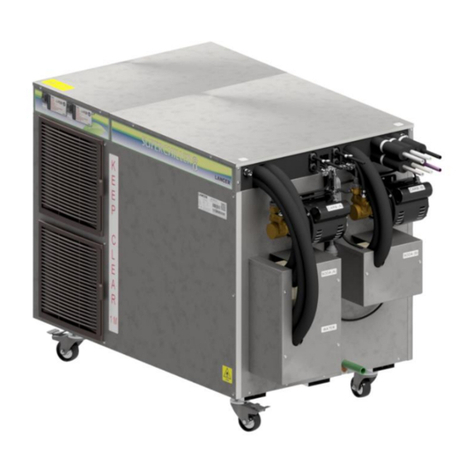
lancer
lancer S8H Manual

lancer
lancer LP2 Superchiller Manual
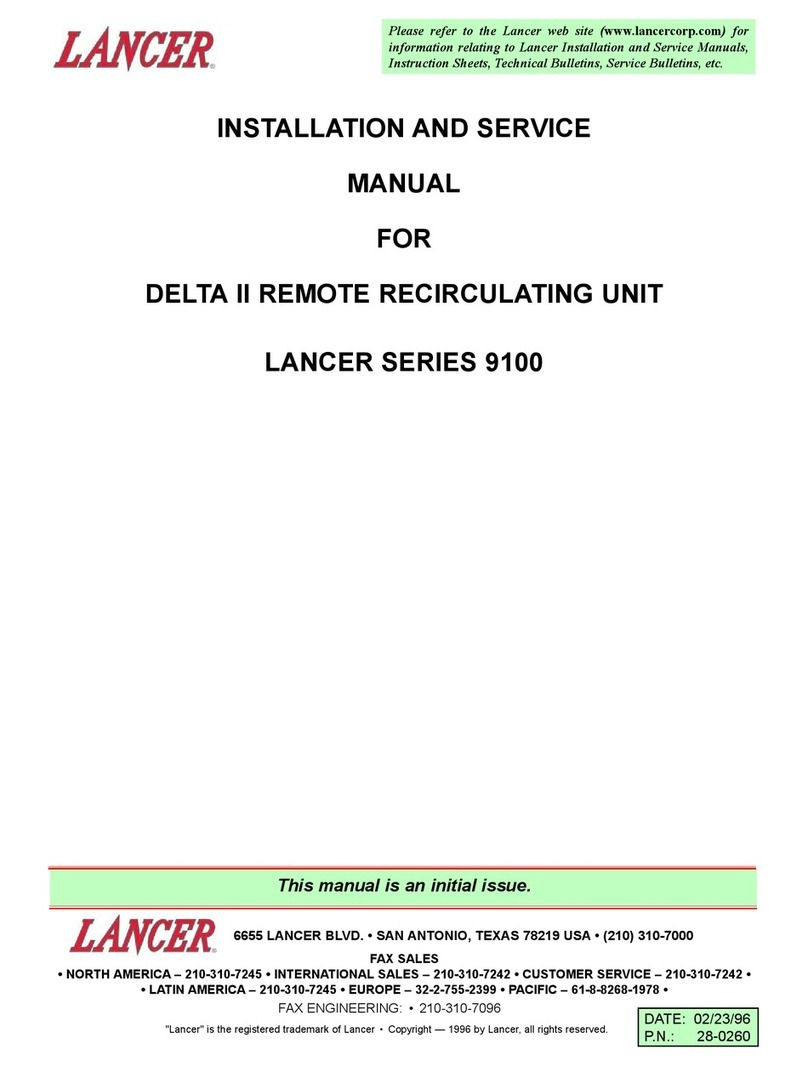
lancer
lancer DELTA II 9100 Series Manual

lancer
lancer Hi-Carb Superchiller S2H Manual
Popular Chiller manuals by other brands
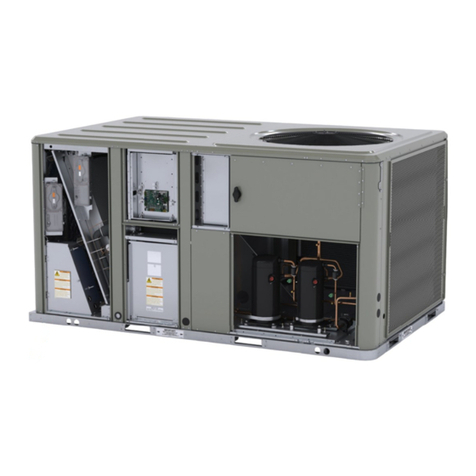
Trane
Trane FIAECON003 Series installation instructions

Daikin
Daikin FWW Series Technical manual

Liebert
Liebert Process Fluid Chiller PS120A Specification sheet
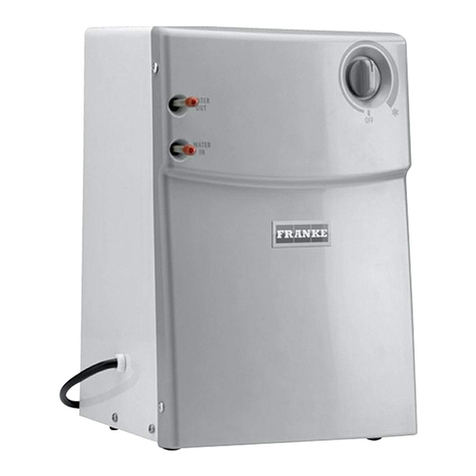
Franke
Franke KER1P Installation and operating instructions

Polar Refrigeration
Polar Refrigeration GL001 instruction manual

Aquacal
Aquacal TropiCool TC500 Brochure & specs