LG MULTI V WATER MINI Installation and operation manual

ENGINEERING MANUAL
Variable Refrigerant Flow
Water-Source Units
4.4 Tons

A summary list of safety precautions is on page 3.
For continual product development, LG Electronics U.S.A., Inc. reserves the right to change specifications without notice.
© LG Electronics U.S.A., Inc.
PROPRIETARY DATA NOTICE
This document, as well as all reports, illustrations, data, information, and
other materials are the property of LG Electronics U.S.A., Inc., and are
disclosed by LG Electronics U.S.A., Inc. only in confidence.
This document is for design purposes only.
To access additional technical documentation such as submittals,
indoor unit engineering manuals, installation, service, product
data performance, general best practice, and building ventilation
manuals, as well as whitepapers, catalogs, LATS software
programs, and more, log in to www.lghvac.com.

TABLE OF SYMBOLS
DANGER
This symbol indicates an imminently hazardous situation which, if not avoided, will result in death or serious injury.
This symbol indicates a potentially hazardous situation which, if not avoided, could result in death or serious injury.
CAUTION
This symbol indicates a potentially hazardous situation which, if not avoided, may result in minor or moderate injury.
This symbol indicates situations that may result in equipment or property damage accidents only.
This symbol indicates an action that should not be performed.
TABLE OF CONTENTS
Unit Nomenclature����������������������������������������������������������������������������������������������������������������������������������������������������������������������������������������������������������4
LG Air Conditioner Technical Solution (LATS) ���������������������������������������������������������������������������������������������������������������������������������������������������������5-6
Rrefrigerant Charge Worksheet ������������������������������������������������������������������������������������������������������������������������������������������������������������������������������������7
Water Source Product Data ��������������������������������������������������������������������������������������������������������������������������������������������������������������������������������������8-20
Mechanical Specications ............................................................................................................................................................................................9
Product Features and Benets...................................................................................................................................................................................10
General Data .............................................................................................................................................................................................................. 11
Electrical Data ............................................................................................................................................................................................................ 11
Dimensions.................................................................................................................................................................................................................12
Wiring Diagram...........................................................................................................................................................................................................13
Refrigerant Flow Diagrams....................................................................................................................................................................................14-16
Acoustic Data .............................................................................................................................................................................................................17
Accessories ...........................................................................................................................................................................................................18-20
Performance Data����������������������������������������������������������������������������������������������������������������������������������������������������������������������������������������������������21-33
Cooling Capacity ...................................................................................................................................................................................................22-27
Heating Capacity ................................................................................................................................................................................................. 28-33-
Correction Factors ��������������������������������������������������������������������������������������������������������������������������������������������������������������������������������������������������34-36
Electrical Connections��������������������������������������������������������������������������������������������������������������������������������������������������������������������������������������������37-40
Power Wiring and Communication Cable..............................................................................................................................................................38-39
DIP Switch Settings for Use With Gen4 Indoor Units.................................................................................................................................................40
Water Circuit Installation ����������������������������������������������������������������������������������������������������������������������������������������������������������������������������������������41-57
Water Circuit Design..............................................................................................................................................................................................42-43
Piping System Specications ................................................................................................................................................................................44-47
Flow Switches and Solenoid Valves ......................................................................................................................................................................48-49
Variable Water Flow Control Kit (Required Accessory)..........................................................................................................................................50-57
Refrigerant Piping Design ��������������������������������������������������������������������������������������������������������������������������������������������������������������������������������������58-64
Piping Limitations .......................................................................................................................................................................................................59
Pipe Sizing.............................................................................................................................................................................................................60-62
Placement Considerations.....................................................................................................................................................................................63-64

Due to our policy of continuous product innovation, some specifications may change without notification.
©LG Electronics U.S.A., Inc., Englewood Cliffs, NJ. All rights reserved. “LG” is a registered trademark of LG Corp.
4|INTRODUCTION
MULTI V Water Mini Unit Engineering Manual
058 G A
Type
N = Heat Pump
Electrical Ratings
G = 208–230V / 60Hz / 1Ø
053 = 52,900
Condenser
W = Water Source
Family
AR = Multi V (Refrigerant R410A)
2
Basic Function = A
Generation
2 = Second
Water Source Units (WSU)
AR W N
UNIT NOMENCLATURE
Water Mini Unit
Nominal Cooling Capacity in Btu/h

Due to our policy of continuous product innovation, some specifications may change without notification.
©LG Electronics U.S.A., Inc., Englewood Cliffs, NJ. All rights reserved. “LG” is a registered trademark of LG Corp. INTRODUCTION | 5
Introduction
LG AIR CONDITIONER
TECHNICAL SOLUTION (LATS)
Figure 1: Example of LATS CAD2.
LG Air Conditioner Technical Solution (LATS) Software
A properly designed and installed refrigerant piping system is critical to the optimal performance of LG air-conditioning systems. To assist
engineers, LG offers, free of charge, LG Air Conditioner Technical Solution (LATS) software—a total design solution for LG air conditioning
systems.
To reduce the risk of designing an improper applied system or one that will not operate correctly, LG requires that LATS software be used on all projects.
Formats
LATS is available to LG customers in three user interfaces: LATS HVAC, LATS CAD2, and LATS REVIT. All three LATS formats are available
through www.myLGHVAC.com, or contact an LG Sales Representative.
LATS HVAC is a Windows®-based application that aids engineers in designing LG Variable Refrigerant Flow (VRF), Multi F / Multi F MAX,
Single-Zone, and Energy Recovery Ventilator (ERV) systems.
*Windows® is a registered mark of Microsoft®Corporation.
LATS CAD2 combines the LG LATS program with AutoCAD®software**. It permits engineers to layout and validate LG Multi V Variable
Refrigerant Flow (VRF), Multi F / Multi F MAX, Single-Zone, and En-
ergy Recovery Ventilator (ERV) systems directly into CAD drawings.
LATS Revit integrates the LG LATS program with Revit®software**.
It permits engineers to layout and validate Multi V VRF systems
directly into Revit drawings.
**AutoCAD®and Revit®are both registered marks of Autodesk, Inc.
Features
All LG product design criteria have been loaded into the program,
making LATS simple to use: double click or drag and drop the com-
ponent choices. Build systems in Tree Mode where the refrigerant
system can be viewed. Switch to a Schematic diagram to see the
electrical and communications wiring.
LATS software permits the user to input region data, indoor and
outdoor design temperatures, modify humidity default values, zoning, specify type and size of outdoor units and indoor units, and input air
flow and external static pressure (ESP) for ducted indoor units.
The program can also:
•Import building loads from a separate Excel file.
•Present options for outdoor unit auto selection.
•Automatically calculate component capacity based on design
conditions for the chosen region.
•Verify if the height differences between the various system
components are within system limits.
•Provide the correct size of each refrigerant piping segment and LG
Y-Branches and Headers.
•Adjust overall piping system length when elbows are added.
•Check for component piping limitations and flag if any parameters
are broken.
•Factor operation and capacity for defrost operation.
•Calculate refrigerant charge, noting any additional trim charge.
•Suggest accessories for indoor units and outdoor units.
•Run system simulation.
Features depend on which LATS program is being used, and the type of system being designed.

Due to our policy of continuous product innovation, some specifications may change without notification.
©LG Electronics U.S.A., Inc., Englewood Cliffs, NJ. All rights reserved. “LG” is a registered trademark of LG Corp.
6|INTRODUCTION
MULTI V Water Mini Unit Engineering Manual
LG AIR CONDITIONER
TECHNICAL SOLUTION (LATS)
Figure 2: Example of a LATS Tree Diagram.
LATS Generates a Complete Project Report
LATS software also generates a report containing project design parameters, cooling and heating design data, system component perfor-
mance, and capacity data. The report includes system combination ratio and refrigerant charge calculations; and provides detailed bill of
material, including outdoor units, indoor units, control devices, accessories, refrigerant pipe sizes segregated by building, by system, by pipe
size, and by pipe segments. LATS can generate an Excel GERP report that can imported into the LG SOPS pricing and ordering system.
Proper Design to Install Procedure
LG encourages a two report design-to-install-procedure. After the
design engineer determines building / zone loads and other details,
the engineer opens the LATS program and inputs the project’s infor-
mation. When the design is complete, the “Auto Piping” and “System
Check” functions must be used to verify piping sizes, limitations, and
if any design errors are present. If errors are found, engineers must
adjust the design, and run Auto Piping and System Check again.
When the design passes the checks, then the engineer prints out
a project “Shop Drawing” (LATS Tree Diagram) and provides it to
the installing contractor. The contractor must follow the LATS Tree
Diagram when building the piping system, but oftentimes the design
changes on the building site:
•Architect has changed location and/or purpose of room(s).
•Outdoor unit cannot be placed where originally intended.
•Structural elements prevent routing the piping as planned.
•Air conditioning system conflicts with other building systems
(plumbing, gas lines, etc.).
The contractor must mark any deviation from the design on the Shop Drawing, including as-built straight lines and elbows. This “Mark Up”
drawing must be returned to the design engineer or Rep, who must input contractor changes into the LATS file. (Copy the original LATS soft-
ware file, save and rename as a separate file, and modify all piping lengths by double-clicking on each length and editing information.) Like
the shop drawing, the Auto Piping and System Check must also be run on this new “As Built” drawing. The design engineer or Rep must then
provide the final As Built file to the contractor. The Mark Up version must be compared to the As Built version for:
•Differences in pipe diameter(s). If incorrect diameters have been installed, the piping must be changed out. If pipe diameters have changed,
check to see if Y-Branches will also need to be changed.
•Changes to outdoor unit and indoor unit capacities. Capacities changes will impact line length changes.
•Additional refrigerant charge quantity (“Trim Charge”). Trim charge will change if piping lengths and diameters change. The As Built version
must reflect installed piping lengths to ensure correct trim charge.
All documents submitted by the contractor, as well as the Shop Drawing and the As Built Drawing files must be provided for commissioning
purposes. Model and serial numbers for all system components must also be submitted. If the steps previously detailed are not followed, and
all documents are not provided to the commissioning agent, the project runs the risk of not being commissioned and any warranty LG offers
on the equipment not being activated.
Any eld changes, such as re-routing, shortening or lengthening a pipe segment, adding or eliminating elbows and/or ttings, re-sizing,
adding, or eliminating indoor units, changing the mounting height, or moving the location of a device or tting during installation must be
done with caution and ALWAYS VERIFIED in LATS SOFTWARE BEFORE supplies are purchased or installed. Doing so will lead to a more
protable installation, reduce the potential for rework, and will reduce the potential for multiple visits to the job site to complete the system
commissioning.

Due to our policy of continuous product innovation, some specifications may change without notification.
©LG Electronics U.S.A., Inc., Englewood Cliffs, NJ. All rights reserved. “LG” is a registered trademark of LG Corp. INTRODUCTION | 7
Introduction
REFRIGERANT CHARGE WORKSHEET
System R410A Refrigerant Charge Calculator (lbs.)
Table 1: System Refrigerant Charge Calculator (lbs.).
1CF (Ref.) = Correction Factor for Refrigerant Charge.
2For refrigerant charge purposes, consider only the liquid line; ignore the vapor line(s).
System Tag or ID:
Job Name: __________________________________________
Project Manager: ____________________________________ Date: ______________
Line # Description Chassis I.D. Size Quantity CF (Ref.)1Total (lbs.)
1 Linear feet of 1/4" liquid line tubing2— — 0.015
2 Linear feet of 3/8" liquid line tubing2— — 0.041
3 Linear feet of 1/2" liquid line tubing2— — 0.079
4 Linear feet of 5/8" liquid line tubing2— — 0.116
5 Linear feet of 3/4" liquid line tubing2— — 0.179
6 Linear feet of 7/8" liquid line tubing2— — 0.238
7 Linear feet of 1" liquid line tubing2— — 0.323
8 Standard + Art Cool Mirror SJ, SK 5k to 15k 0.53
9 Standard + Art Cool Mirror SJ, SK 18k to 24k 0.62
10 Standard SV 30k to 36k 1.01
11 Art Cool Gallery SF 9k to 12k 0.22
12 1-Way Cassette TU 7k to 12k 0.44
13 1-Way Cassette TT 18k to 24k 0.64
14 2-Way Cassette TS 18k to 24k 0.75
15 4-Way 2' x 2' Cassette TR 5k to 7k 0.40
16 4-Way 2' x 2' Cassette TR 9k to 12k 0.55
17 4-Way 2' x 2' Cassette TQ 15k to 18k 0.71
18 4-Way 3' x 3' Cassette TN 7k to 24k 0.88
19 4-Way 3' x 3' Cassette TM 28k to 36k 1.08
20 4-Way 3’ x 3’ Cassette TM 42k to 48k 1.41
21 High Static Ducted M1 7k to 24k 0.57
22 High Static Ducted M2 7k to 24k 0.77
23 High Static Ducted M2 28k to 42k 1.15
24 High Static Ducted M3 28k to 54k 1.35
25 High Static Ducted B8 36k to 96k 2.20
26 Low Static Ducted, Low Static Ducted Bottom Return L1 5k to 9k 0.31
27 Low Static Ducted, Low Static Ducted Bottom Return L2 12k to 18k 0.42
28 Low Static Ducted, Low Static Ducted Bottom Return L3 21k to 24k 0.55
29 Vertical / Horizontal Air Handling Unit NJ 12k to 30k 1.04
30 Vertical / Horizontal Air Handling Unit NJ 36k 1.57
31 Vertical / Horizontal Air Handling Unit NK 42k to 54k 2.00
32 Floor Standing CE (U) 7k to 15k 0.37
33 Floor Standing CF (U) 18k to 24k 0.82
34 ADDITIONAL Refrigerant Charge Required (Sum of lines 1 – 33)
35 Water Source Unit Factory Refrigerant Charge ARWN053GA2 52,900 2.2
36 Total System Charge: Sum of Additional Refrigerant Charge Required and Total Factory Refrigerant Charge

WATER SOURCE
PRODUCT DATA
Mechanical Specifications on page 9
Product Features and Benefits on page 10
General Data on page 11
Electrical Data on page 11
Dimensions on page 12
Wiring Diagram on page 13
Refrigerant Flow Diagrams on page 14
Acoustic Data on page 17
Accessories on page 18

PRODUCT DATA | 9
Product Data
Due to our policy of continuous product innovation, some specifications may change without notification.
©LG Electronics U.S.A., Inc., Englewood Cliffs, NJ. All rights reserved. “LG” is a registered trademark of LG Corp.
MECHANICAL SPECIFICATIONS
Multi V™ Water Mini Units
Multi V™ Water Mini Units
General
The LG Multi V Water Mini system consists of a water source unit,
one or more indoor units, integrated system controls, and intercon-
necting field-provided refrigerant pipe containing various fittings
including Y-branch and Header kits supplied by LG. LG components
are manufactured in a facility that meets or exceeds International
Organization for Standardization (ISO) 9001 and 14001. The units
are listed by Intertek (ETL) and bear the ETL label, and are certified
to AHRI Standard 1230.
Frame
The frame is constructed with galvanized steel and finished with
baked enamel paint.
Casing
The water-source unit case is constructed from 20-gauge metal,
and is cleaned and finished with baked enamel finish. Paint color is
“warm gray.”
Refrigeration System
The refrigeration system consists of a single refrigerant circuit and
uses R410A refrigerant. The water source unit is provided with
factory installed components, including a refrigerant strainer, check
valves, accumulator, hot gas bypass valve, four-way reversing valve,
electronic expansion valve (EEV), high and low side charging ports,
service valves, and interconnecting piping. The unit comes factory
charged with R410A refrigerant.
Refrigeration Oil Control
The refrigeration oil level in the compressor is maintained using
a control system. The water source unit microprocessor is
programmed to flush the refrigerant piping for a minimum period
of three (3) minutes after three (3) hours of compressor operation.
Compressor
The water source units are equipped with one hermetic, digitally
controlled, inverter driven, rotary compressor, which is manufactured
by LG. The frequency inverter is capable of providing a modulation
range from 30Hz–100Hz. The compressor motor is suction gas-
cooled and has an acceptable voltage range of ±10% of nameplate
voltage. The compressor is equipped with a crankcase heater.
An external pressure sensor and an external temperature sensor are
provided to protect the compressor from damage caused by over /
under temperature or over / under pressure conditions. The com-
pressor is provided with a positive displacement oil pump providing
sufficient oil film on all bearing surfaces across the entire inverter
modulation range. The compressor refrigerant oil is polyvinyl ether
(PVE) having no hygroscopic
properties. The compressor is
wrapped with a heat resistant,
sound attenuating blanket and
mounted on rubber isolation
grommets.
Heat Exchanger
The water heat exchanger is a
stainless steel, type SUS316,
refrigerant / water plate heat
exchanger. The heat exchanger
requires a field-provided
50 mesh strainer and water
treatment to prevent scaling
inside the heat exchanger.
Closed loop condenser water
systems are recommended to
protect the factory mounted heat
exchanger.
Controls
Water source units are factory
wired with electrical control
components, printed circuit boards, thermistors, sensors, terminal
blocks, and lugs for power wiring. The control wiring circuit is low
voltage and includes a control power transformer, fuses, and inter-
connecting wiring harness with plug connectors. Microprocessor-
based algorithms provide component protection, soft-start capability,
and refrigerant system pressure and temperature control. The unit
is designed to provide continuous compressor operation with an
entering water temperature range of 23°F to 113°F for cooling mode,
and 23°F to 113°F for heating mode (Variable water flow control kit
[PRVC1] required for all entering water temperatures; one kit per
frame) (if entering water temperature falls below 42°F, glycol must
be added to the system). When the system is started, the connected
indoor units are automatically assigned an electronic address by the
water source unit’s microprocessor. Additionally, each indoor unit is
capable of accepting a manual assignment of a secondary address
that, if used, provides unit tag identification when integrating with LG
V-Net control devices.
The water source unit microprocessor is provided with a three-digit,
LED display that communicates active system information and /
or malfunction codes. The microprocessor has an algorithm that
actively verifies the operational condition of system sensors and
thermistors. A power conditioning circuit is provided and designed
to protect the unit’s inverter compressor and controls from phase
failure, over / under-voltage condition, and to prevent transmission of
power irregularities to the supply power source.
Figure 3: Multi V Water Mini Unit.
For indoor unit guide specications, visit www.lghvac.com.

10 |PRODUCT DATA
MULTI V Water Mini Unit Engineering Manual
Due to our policy of continuous product innovation, some specifications may change without notification.
©LG Electronics U.S.A., Inc., Englewood Cliffs, NJ. All rights reserved. “LG” is a registered trademark of LG Corp.
Quiet Operation and Integrated
Controls
Low Sound Levels
LG customers often ask if the unit is running after commissioning is
complete. When Multi V Water Mini units operate fully loaded, they
are one of the quietest levels in the industry. The sound is almost
undetectable during off-peak operation.
All rotating components are soft-started by the controller using a
digitally controlled inverter, which reduces undesirable noise caused
by compressors cycling on and off.
Comfort Control at its Best
Tight temperature control through precise load matching maximizes
the time that the indoor units remove moisture. This ensures
maximum comfort!
Precision Load Matching
Unlike traditional air conditioning control systems that use
thermostatic controls to maintain room temperatures, LG Multi V
controls continuously vary the indoor unit fan speed and
refrigerant flow. The water source unit responds by varying the
compressor speed as needed to meet the indoor unit’s demand. As
a result, the Multi V Water Mini system delivers precise space tem-
perature control without overshooting the set-point. Temperature drift
in the thermal zone is minimized, because the fan speed and
refrigerant volume are controlled together precisely matching the
load.
Advanced Compressor Technology
Oil Management
The oil injection mechanism ensures a reliable oil film on moving
parts even at the lowest speeds, which enables the inverter
compressor to safely operate at speeds as low as 30 Hz. The
following oil return system brings oil back to the compressor once
the oil leaves the compressor, so oil migration is no longer a
concern.
1. The compressor discharge is specially designed to minimize the
amount of oil leaving the compressor.
2. Oil return algorithms flush the oil from the system back to the
compressor.
Inverter Driven
The rotary compressor is optimized around the R410A model to
maximize compressor efficiency, which reduces power consumption
and lowers utility bills. The latest inverter technology allows the LG
Multi V Water Mini to precisely match the load, which prevents
constant cycling and results in tight temperature control and opti-
mized efficiency. Occupants remain comfortable while utility costs
are reduced.
Simplified Installation
Cooling and heating systems that use the LG Multi V Water Mini
simplify and reduce the mechanical and control system design time.
The designer no longer has to be concerned with interconnecting
chilled water piping or air distribution duct systems, or matching and
selecting chillers, fans, air handlers, or Variable Air Volume (VAV)
boxes.
System integration with existing building management systems
(based on BACnet®or LonWorks®) has never been easier. Because
all of the Multi V Water Mini system components are engineered and
provided by LG, the system components and controls come pre-
engineered and do not need any custom programming from third-
party contractors.
Operating Range and Size
Operating Range (4�4 Tons)
The water source unit can operate from 23°F–113°F entering water
temperature in cooling mode, and 23°F–113°F entering water
temperature in heating mode (if entering water temperature falls
below 42°F, glycol must be added to the system). Variable water flow
control kit [PRVC1] required for all entering water temperatures; one
kit per frame. The connected indoor unit combination ratio range is
30%–130%.
Compact Size
Water Mini units have a 20-5/8″ H x 13-1/8″ W cabinet. Multiple units
can be stacked using an independent racking system, giving back
valuable floor space.
PRODUCT FEATURES AND BENEFITS
Multi V™ Water Mini Units Entering water temperatures below 42 require ...WIL MEN-
TION glycol here. SEE OTHER SECTIONS FOR TEXT. see
page 45.

PRODUCT DATA | 11
Product Data
Due to our policy of continuous product innovation, some specifications may change without notification.
©LG Electronics U.S.A., Inc., Englewood Cliffs, NJ. All rights reserved. “LG” is a registered trademark of LG Corp.
GENERAL DATA
Specications / Electrical Data
Table 2: ARWN053GA2 Water Mini Unit Specications.
Unit Model Number 4.4 Ton
ARWN053GA2
Nominal Capacity / Input Power
Cooling Capacity (Btu/h)152,900
Cooling Input Power (kW) 3.2
Heating Capacity (Btu/h)161,400
Heating Input Power (kW) 3.5
Compressor
Type Inverter Rotary
Power Supply (volt/hz/phase)2208-230 / 60 / 1
MCA (A) 27
MOP (A) 45
System Data
Sound Pressure (dBA)354
Heat Rejected to Equipment Room (Btu/h) 512
Net Weight (lbs.) 168
Shipping Weight (lbs.) 181
Dimensions (W x H x D) 20-5/8 x 42-1/2 x 13-1/8
Max. Qty Indoor Units 9
Refrigerant Piping Connections4
Vapor Line OD (in.) 3/4 Braze
Liquid Line OD (in.) 3/8 Braze
Expansion Device Electronically Controlled (EEV)
Factory Refrigerant Charge (R410A [lbs.]) 2.2
Water Side
Heat Exchanger Stainless Steel Plate
Water Volume in Heat Exchanger (gal.) 0.2
Water Inlet/Outlet Connection Size (in) 1-1/4 FPT
Nominal Flow Rate Total (GPM) 15.9
Range of Flow (GPM) 8.3-19.9
Entering water temp. range (°F)– Cooling523-113
Entering water temp. range (°F)– Heating523-113
Total Heat of Rejection (Btu/h) 56,640
Total Heat of Absorption (Btu/h) 49,448
Pressure Drop (ft) 9.5
Maximum Water Pressure (psi) 640
ΔT (°F)67
1Rated capacity is certified under AHRI Standard 1230. Ratings are subject to change without notice.
Current certified ratings are available at www.ahridirectory.org.
2Power wiring is field provided, solid or stranded, and must comply with the applicable local and national
codes.
3Sound pressure levels are tested in an anechoic chamber under ISO 3745 standard.
4LG requires that LATS software be used on all projects to ensure correct line sizing. Designer must
verify the shop drawing design against the as built design using LATS. Contractor must also use LG
manufactured Y-Branch and Header Kits only.
5Variable water flow control kit (PRVC1) is required for all entering water temperatures (one kit per
frame). If entering water temperatures fall below 42°F, glycol must be added to the system.
6Value is calculated as follows: Δt = Total Heat of Rejection/(Nominal Flow Rate x 500).
7Communication cable between WSU to IDUs to be 18 AWG, 2-conductor, twisted, stranded, shielded.
Ensure the communication cable shield is properly grounded to the WSU chassis only. Do not
ground the WSU to IDUs communication cable at any other point. Wiring must comply with all ap-
plicable local and national codes.
Nominal Tons Unit Model No. Compressor Qty. Compressor Motor RLA MSC MCA MOP
4.4 ARWN053GA2 1 21.6 - 27 45
MCA = Minimum Circuit Ampacity.
MOP = Maximum Overcurrent Protection is calculated as follows: (Largest motor FLA x 2.25) + (Sum of other motor FLA) rounded down to the nearest standard fuse size.
Allowable voltage range is between 208–230 volts only (tolerance is 10%).
Maximum allowable voltage imbalance is 2%.
Table 3: ARWN053GA2 Water Mini Unit Electrical Data.

12 |PRODUCT DATA
MULTI V Water Mini Unit Engineering Manual
Due to our policy of continuous product innovation, some specifications may change without notification.
©LG Electronics U.S.A., Inc., Englewood Cliffs, NJ. All rights reserved. “LG” is a registered trademark of LG Corp.
ARWN053GA2
DIMENSIONS
H
S
ide View
F
ront View
Top View Isometric
L7
L
L
6
L5
L4
L
3
L1
L
L
2
V
apor
Li
ne
Liquid Line
C
apped Line
Wa
t
e
r
Ou
tl
et
Wa
t
e
r Inl
et
Z
X
Y
M
1
M2
W
D
W
D
H
L
1
L
2
L
3
L4
L
5
L
6
L7
L
8
M
1
M2
X
Y
Z
Figure 4: ARWN053GA2 Dimensions.

PRODUCT DATA | 13
Product Data
Due to our policy of continuous product innovation, some specifications may change without notification.
©LG Electronics U.S.A., Inc., Englewood Cliffs, NJ. All rights reserved. “LG” is a registered trademark of LG Corp.
WIRING DIAGRAM
83
ARWN053GA2
Figure 5: ARWN053GA2 Wiring Diagram.

14 |PRODUCT DATA
MULTI V Water Mini Unit Engineering Manual
Due to our policy of continuous product innovation, some specifications may change without notification.
©LG Electronics U.S.A., Inc., Englewood Cliffs, NJ. All rights reserved. “LG” is a registered trademark of LG Corp.
REFRIGERANT FLOW DIAGRAMS
Cooling Mode
EEV
Filter
EEV
Filter
IndoorHEXIndoor HEX
Fan
Indoor Unit Indoor Unit
Fan
Liquid
Gas
HEX
Temp
Liquid
Temp
Suction
Te mp
Hot Gas
Bypass
Valve
4 Way
Valve
Main
EEV
Low
Pressure
Sensor
Accumu
lator
Inv.
Comp.
High
Pressure
Switch
Discharge
Te mp
High
Pressure
Sensor
Check
Valve
Solenoid
Valve Strainer Thermistor
Remark
High
Pressure
Switch
S
High
Water In Water Out
Plate
Heat Exchanger
Pressure
Sensor SVC
Valve
Fusible
Plug
EEV
Fusible
Plug
High Te mperature High Pressure Gas
High Te mperature High Pressure Liquid
Low Te mperature Low Pressure Gas
S
Figure 6: ARWN053GA2—Cooling Mode.
ARWN053GA2

PRODUCT DATA | 15
Product Data
Due to our policy of continuous product innovation, some specifications may change without notification.
©LG Electronics U.S.A., Inc., Englewood Cliffs, NJ. All rights reserved. “LG” is a registered trademark of LG Corp.
Heating Mode
REFRIGERANT FLOW DIAGRAMS
Figure 7: ARWN053GA2—Heating Mode.
EE V
Filter
EEV
Filter
Indoor HEX
Indoor Unit
Indoor HEX
Indoor Unit
Fan Fan
Liquid
Gas
HEX
Temp
Liquid
Temp
Hot Gas
Bypass
Valve
4 Way
Valve
Main
EEV
Accumu
lator
Inv.
Comp.
High
Pressure
Switch
Discharge
Temp
High
Pressure
Sensor
High
Water In Water Out
Plate
Heat Exchanger
Suction
Temp
Low
Pressure
Sensor
Fusible
Plug
Check
Valve
Solenoid
Valve Strainer Thermistor
Remark High
Pressure
Switch
Pressure
Sensor SVC
Valve
Fusible
Plug
EEV
High Te mperature High Pressure Gas
High Te mperature High Pressure Liquid
Low Te mperature Low Pressure Gas
S
S
ARWN053GA2

16 |PRODUCT DATA
MULTI V Water Mini Unit Engineering Manual
Due to our policy of continuous product innovation, some specifications may change without notification.
©LG Electronics U.S.A., Inc., Englewood Cliffs, NJ. All rights reserved. “LG” is a registered trademark of LG Corp.
Oil Return Operation
REFRIGERANT FLOW DIAGRAMS
Figure 8: ARWN053GA2—Oil Return.
Filter Filter
Indoor Unit Indoor Unit
Fan Fan
Indoor HEX Indoor HEXEEV EEV
Liquid
Gas
HEX
Temp
Liquid
Temp
Suction
Temp
Hot Gas
Bypass
Valve
4 Way
Valve
Main
EEV
Low
Pressure
Sensor
Accumu
lator
Inv.
Comp.
High
Pressure
Switch
Discharge
Te mp
High
Pressure
Sensor
High
Water In Water Out
Plate
Heat Exchanger
Fusible
Plug
Check
Valve
Solenoid
Valve Strainer Thermistor
Remark High
Pressure
Switch
Pressure
Sensor SVC
Valve
Fusible
Plug
EEV
High Te mperature High Pressure Gas
High Te mperature High Pressure Liquid
Low Te mperature Low Pressure Gas
S
S
ARWN053GA2

PRODUCT DATA | 17
Product Data
Due to our policy of continuous product innovation, some specifications may change without notification.
©LG Electronics U.S.A., Inc., Englewood Cliffs, NJ. All rights reserved. “LG” is a registered trademark of LG Corp.
ACOUSTIC DATA
Measurement Location and Sound Pressure Levels
Model (208-230V/60Hz/1Ø) Sound Levels dB(A)
Cooling Heating
ARWN053GA2 52 54
3.3 feet
4.9 feet
Sound
Detector
Figure 9: Sound Level Measurement Location.
• Measurement taken 4.9′ above finished floor, and at a distance of 3.3′ from face of unit.
• Measurements taken with no attenuation and units operating at full load normal operating
condition.
• Sound level will vary depending on a range of factors such as construction (acoustic
absorption coefficient) of particular area in which the equipment is installed.
• Sound power levels are measured in dB(A)±3.
• Tested in anechoic chamber per ISO Standard 3745.
Table 4: Water Mini Unit Sound Levels.
Sound Pressure Levels
Cooling
Octave Band Center Frequency (Hz)
Octave Band Sound Pressure Level (0dB = 20μPa)
10
20
30
40
50
60
70
80
63 125 250 500 1000 2000 4000 8000
NC-15
NC-20
NC-25
NC-30
NC-35
NC-40
NC-45
NC-50
NC-55
NC-60
NC-65
Approximate
Hearing
Threshold
Octave Band Center Frequency (Hz)
Octave Band Sound Pressure Level (0dB = 20μPa)
10
20
30
40
50
60
70
80
63 125 250 500 1000 2000 4000 8000
NC-15
NC-20
NC-25
NC-30
NC-35
NC-40
NC-45
NC-50
NC-55
NC-60
NC-65
Approximate
Hearing
Threshold
Octave Band Center Frequency (Hz)
Octave Band Sound Pressure Level (0dB = 20μPa)
10
20
30
40
50
60
70
80
63 125 250 500 1000 2000 4000 8000
NC-15
NC-20
NC-25
NC-30
NC-35
NC-40
NC-45
NC-50
NC-55
NC-60
NC-65
Approximate
Hearing
Threshold
ARWN038GA2 ARWN048GA2 ARWN053GA2
Octave Band Center Frequency (Hz)
Octave Band Sound Pressure Level (0dB = 20μPa)
10
20
30
40
50
60
70
80
63 125 250 500 1000 2000 4000 8000
NC-15
NC-20
NC-25
NC-30
NC-35
NC-40
NC-45
NC-50
NC-55
NC-60
NC-65
Approximate
Hearing
Threshold
Octave Band Center Frequency (Hz)
Octave Band Sound Pressure Level (0dB = 20μPa)
10
20
30
40
50
60
70
80
63 125 250 500 1000 2000 4000 8000
NC-15
NC-20
NC-25
NC-30
NC-35
NC-40
NC-45
NC-50
NC-55
NC-60
NC-65
Approximate
Hearing
Threshold
Octave Band Center Frequency (Hz)
Octave Band Sound Pressure Level (0dB = 20μPa)
10
20
30
40
50
60
70
80
63 125 250 500 1000 2000 4000 8000
NC-15
NC-20
NC-25
NC-30
NC-35
NC-40
NC-45
NC-50
NC-55
NC-60
NC-65
Approximate
Hearing
Threshold
ARWN038GA2 ARWN048GA2 ARWN053GA2
Heating

18 |PRODUCT DATA
MULTI V Water Mini Unit Engineering Manual
Due to our policy of continuous product innovation, some specifications may change without notification.
©LG Electronics U.S.A., Inc., Englewood Cliffs, NJ. All rights reserved. “LG” is a registered trademark of LG Corp.
ACCESSORIES
Indoor Unit Y-Branches
Y-Branches
Models Pipe
ARBLN01621
Vapor Pipe
I.D. 3/4 (19.05)
O.D. 5/8 (15.88)
I.D. 1/2 (12.7)
I.D. 5/8 (15.88)
I.D. 5/8 (15.88)
I.D. 5/8 (15.88) I.D. 1/2 (12.7)
I.D. 1/2 (12.7)
11-1/2 (292)
11-1/16 (281)
2-15/16
(74)
2-3/4 (70)
1
1
Liquid Pipe
I.D. 1/2 (12.7)
2-3/4 (70)
I.D. 1/4 (6.35)
I.D. 1/4 (6.35)
I.D. 1/4 (6.35)
1
1
I.D. 3/8 (9.52)
I.D. 3/8 (9.52)
I.D. 9.52 (3/8)
O.D. 3/8 (9.52)
ARBLN03321
16-1/4 (413)
15-3/8 (390)
I.D. 3/4 (19.05)
I.D. 3/4 (19.05)
I.D. 3/4 (19.05) I.D. 1/2 (12.7)
I.D. 1/2
(12.7)
2-3/4 (70)
I.D. 5/8 (15.88)
I.D. 5/8 (15.88)
I.D. 1 (25.4)
I.D. 1 (25.4)
O.D. 1 (25.4)
3-1/8 (80) 4-5/16 (110)
3-1/4
(83)
12
3
3
O.D. 3/4 (19.05)
O.D. 3/4 (19.05)
1 2
I.D. 7/8 (22.2)
I.D. 7/8 (22.2)
I.D. 7/8 (22.2)
I.D. 28.58 (1-1/8)
I.D. 1/2 (12.7)
I.D. 1/2 (12.7)
I.D. 1/2 (12.7) (74)
2-15/16
13-1/16 (332)
12-5/8 (321)
I.D. 1/4 (6.35)
I.D. 1/4 (6.35)
I.D. 3/8 (9.52)
I.D. 3/8 (9.52)
I.D. 3/8 (9.52)
(Unit: Inch [mm])
Vapor Pipe Liquid Pipe
2-15/16
(74)
11-1/2 (292)
11-1/16 (281)
AJR54072929 AJR54072927
AJR54072930 AJR54072928

PRODUCT DATA | 19
Product Data
Due to our policy of continuous product innovation, some specifications may change without notification.
©LG Electronics U.S.A., Inc., Englewood Cliffs, NJ. All rights reserved. “LG” is a registered trademark of LG Corp.
ACCESSORIES
Unit: Inch
4 branch
ARBL054
7 branch
ARBL057
4 branch
ARBL104
7 branch
ARBL107
Models Vapor pipe Liquid pipe
14-3/16
21-1/4 21-1/4
4-3/4
I.D. 5/8
I.D. 1/2
I.D. 1/2
I.D. 5/8
I.D. 5/8
I.D. 3/4
4-3/4
14-3/16
I.D. 3/8
I.D. 3/8
I.D. 1/4
I.D. 1/4
I.D. 3/8
I.D. 1/2
5-15/16
5-15/16
5-15/16 5-15/16
5-15/16
15-3/4
6-5/16
I.D. 5/8
I.D. 1/2
I.D. 3/4
I.D. 5/8
I.D 7/8
I.D. 1-1/8 I.D. 1
4-3/4
4-3/4
4-3/4 4-3/4
4-3/4
4-3/4 4-3/4
4-3/4
I.D. 5/8
I.D. 1/2
I.D. 5/8
I.D. 1/2
I.D. 5/8
I.D. 3/4
4-3/4
I.D. 1/4
I.D. 3/8
I.D. 3/8
I.D. 1/2
6-5/16
22-7/8
I.D. 3/4
I.D. 5/8
ID15.88(5/8)
ID12.7(1/2)
I.D. 5/8
I.D. 1/2
I.D. 7/8
I.D. 1-1/8 I.D. 1
27-9/16
4-3/4
I.D. 1/4
I.D. 3/8
I.D. 3/8
I.D. 1/4
I.D. 3/8I.D. 1/2
5-15/16
5-15/16
5-15/16
4-3/4
4-3/4
14-3/16
I.D. 3/8
I.D. 3/8
I.D. 1/4
I.D. 1/4
I.D. 3/8
I.D. 1/2
Headers
Headers

20 |PRODUCT DATA
MULTI V Water Mini Unit Engineering Manual
Due to our policy of continuous product innovation, some specifications may change without notification.
©LG Electronics U.S.A., Inc., Englewood Cliffs, NJ. All rights reserved. “LG” is a registered trademark of LG Corp.
ACCESSORIES
LGMV
•Actual inverter compressor speed
•Target inverter compressor speed
•Actual outdoor fan speed
•Target outdoor unit fan speed
•Actual superheat
•Target superheat
•Actual subcooler circuit superheat
•Target subcooler circuit superheat
•Main EEV position
•Subcooling EEV position
•Inverter compressor current transducer
value
•Outdoor air temperature
•Actual high pressure/saturation temperature
•Actual low pressure/saturation temperature
•Suction temperature
•Inverter compressor discharge temperature
•Constant speed compressor discharge
temperature
•Front outdoor coil pipe temperature
•Back outdoor coil pipe temperature
•Liquid line pipe temperature
•Subcooler inlet temperature
•Subcooler outlet temperature
•Average indoor unit (IDU) pipe temperature
•Inverter compressor operation indicator
light
•Four-way reversing valve operation
indicator light
•Pressure graph showing actual low pres-
sure and actual high pressure levels
•Error code display
•Operating mode indicator
•Target high pressure
•Target low pressure
•PCB (printed circuit board) version
• Software
version
• Installer
name
•Model no.
of outdoor units
•Site name
•Total number of connected indoor units
•Communication indicator lights
•Indoor unit capacity
•Indoor unit operating mode
•Indoor unit fan speed
•Indoor unit EEV position
•Indoor unit room temperature
•Indoor unit inlet pipe temperature
•Indoor unit outlet pipe temperature
•Indoor unit error code
LG Monitoring View (LGMV) Diagnostic Software and Cable
LGMV software allows the service technician or commissioning agent to connect a computer USB port
to the outdoor unit main printed circuit board (PCB) using an accessory cable without the need for a
separate interface device. The main screen for LGMV shall allow user to view the following real time data
on one screen:
Additional screens can be accessed by tabs on the main screen:
1. Cycleview: Graphic of internal components including:
2. Graph: Full screen graph of actual high and low pressures and high and low pressure limits. A slid-
ing bar enables user to go back in time and view data.
3. Control IDU: Enables user to turn on all IDU’s default setpoints of 86°F in heat mode or 64°F in cool
mode.
4. Setting: Converts metric values to imperial values.
5. Making Data: Recording of real time data to a separate file created to be stored on the user’s computer.
6. Loading Data: Recorded data from a saved “.CSV” file can be loaded to create an LGMV session.
7. Electrical Data: The lower half of main screen is changed to show the following:
Figure 10: MV Cycleview.
•Compressors showing actual speeds
• EEVs
•Indoor Units
•Liquid injection valves
•Temperature and pressure sensors
•Four-way reversing valve
•Outdoor fans showing status and speeds
•Inverter compressor
- Amps
- Volts
- Power Hz
- Inverter control board fan Hz
•Constant compressor
- Current transducer value
- Phase
In lieu of connecting to the outdoor unit, user has the option to connect to the indoor unit with the use of a USB to RS-485 connector kit.
When connected through the indoor unit, user will not be able to record data.
This software can be used to both commission new systems and troubleshoot existing systems. LGMV data can be recorded to a “.CSV” file
and emailed to an LG representative to assist with diagnostic evaluations.
LGMV is available in dierent formats, including Mobile LGMV, which is an app for use on wireless devices. Contact your LG
Sales Representative for information about the dierent formats, and recommended system requirements for any version of
LGMV.
Table of contents
Other LG Air Compressor manuals
Popular Air Compressor manuals by other brands

Rolair
Rolair 6820K17D instruction manual
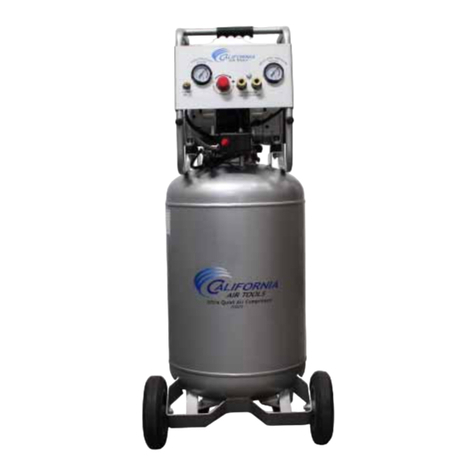
California Air Tools
California Air Tools 20020 owner's manual

Ingersoll-Rand
Ingersoll-Rand VHP600WCU Operating, Maintenance & Parts Manual
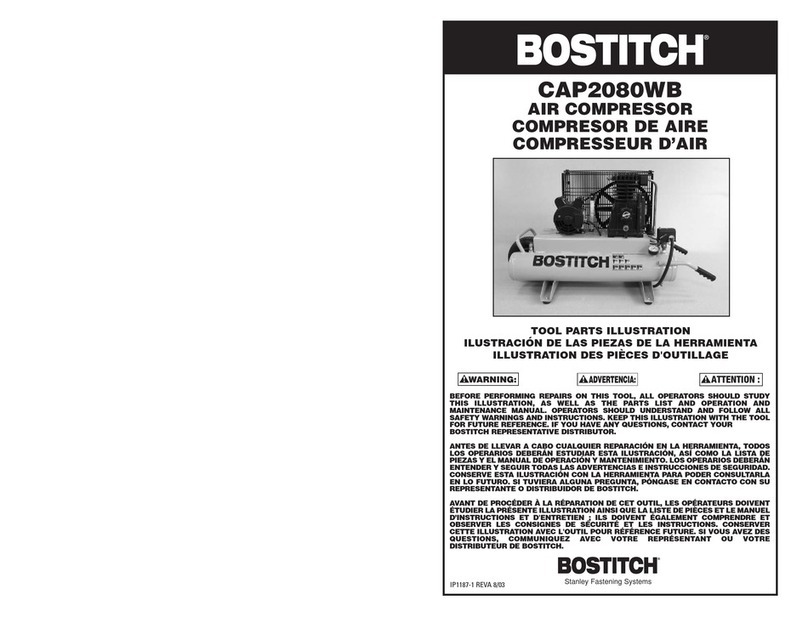
Bostitch
Bostitch CAP2080WB Assembly instructions
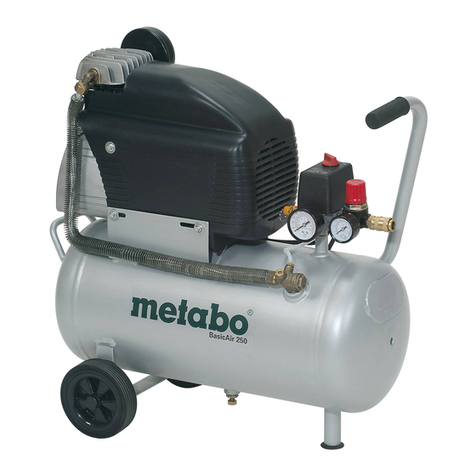
Metabo
Metabo BasicAir 250 Original operating instructions

Ingersoll-Rand
Ingersoll-Rand 2000 owner's manual
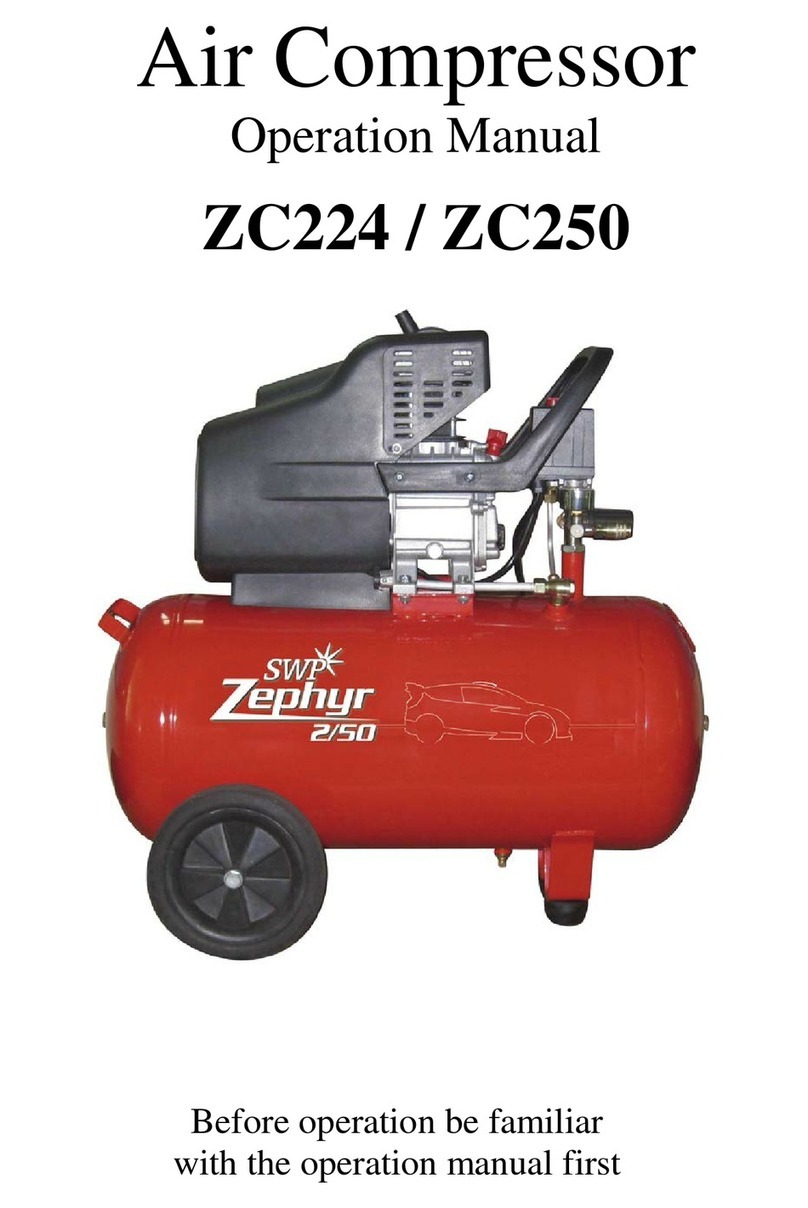
SWP
SWP ZC224 Operation manual
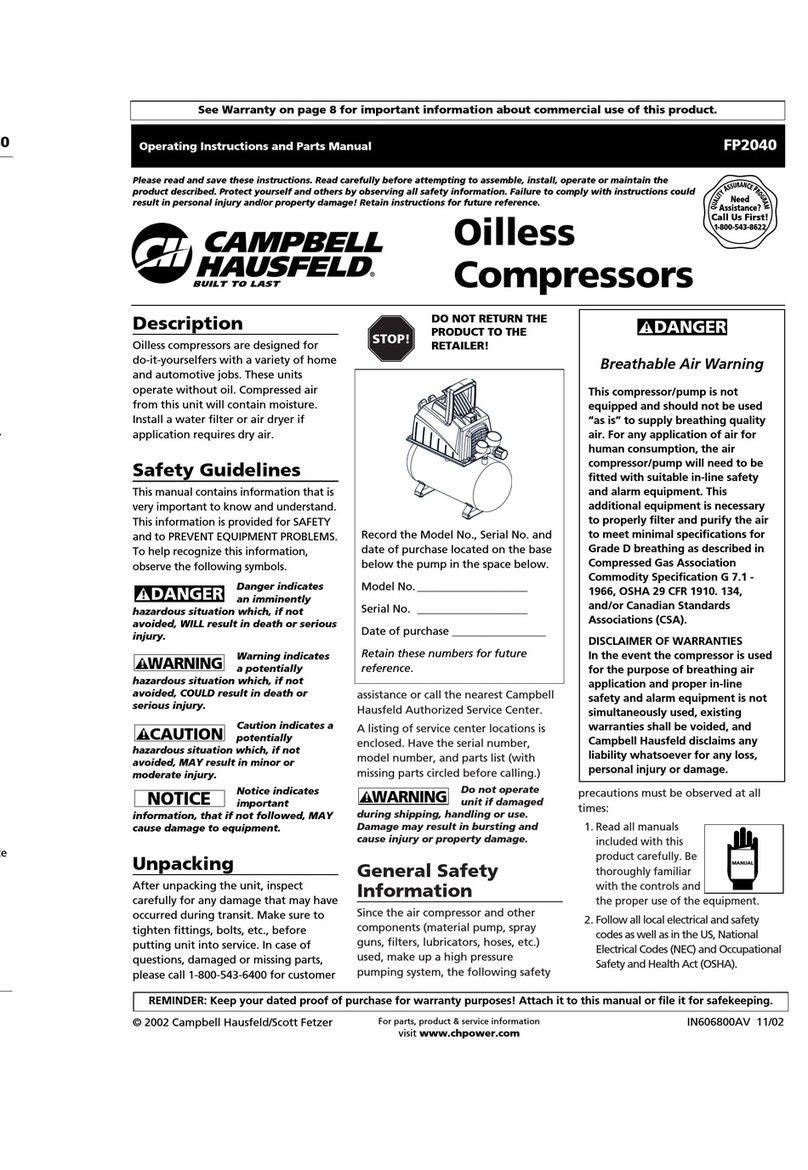
Campbell Hausfeld
Campbell Hausfeld FP2040 Operating instructions and parts manual

Bacharach
Bacharach eco-20202 user manual
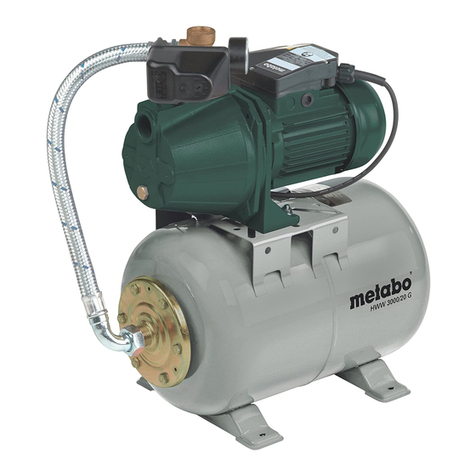
Metabo
Metabo HWW 3000/ 20 S operating instructions
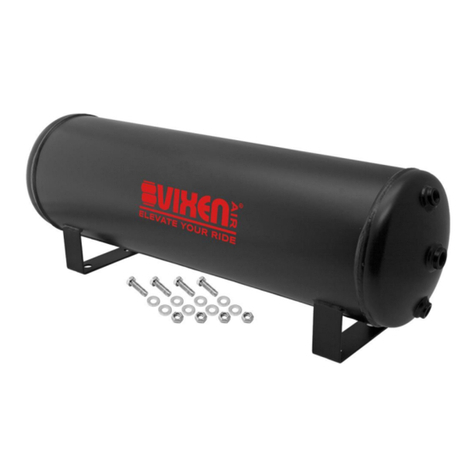
Vixen Air
Vixen Air VXT4100 installation guide
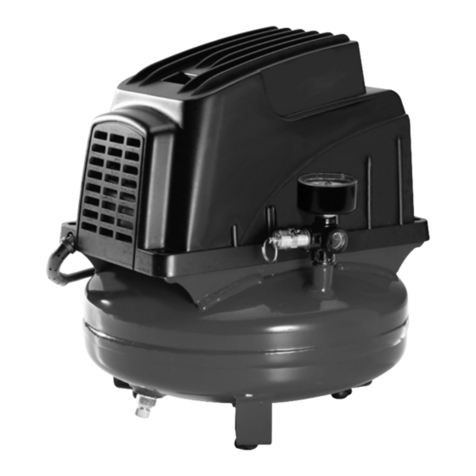
Campbell Hausfeld
Campbell Hausfeld FP2028999TT Operating instructions and parts manual