LIMBACH L 2000 Series User manual

Installation Manual
L 1700
L 2000
and
L 2400 Series
Limbach Flugmotoren GmbH & Co. KG
Kotthausener Str. 5
53639 Königswinter
Germany
Tel.: 02244 / 9201 - 0
Fax: 02244 / 9201 - 30
Part-No. 905.170.010.000
Edition: 01.03.99
Limbach Flugmotoren GmbH & Co. KG
Flugmotoren

TABLE OF CONTENTS
1INTRODUCTION 1-1
1.1.1 Title 1-1
1.1.2 Foreword 1-1
1.1.3 Applicability 1-1
1.1.4 Copyright 1-1
2MEASUREMENTS 2-1
2.2.1 Definitions 2-1
3COOLING 3-1
3.3.1 Description 3-1
3.3.1.1 L 2000 and Series Engines 3-1
3.3.1.2 L 2400 EF Engine 3-2
3.3.1.2.1 Cylinder Cooling 3-4
3.3.1.2.2 Cylinder-Head Cooling 3-4
3.3.1.2.3 Oil Cooling 3-5
3.3.1.2.4 Technical Data 3-5
3.3.1.2.5 Generator Cooling 3-6
4FUEL SYSTEM 4-1
4.4.1 Requirements 4-1
4.4.1.1 L 2000 Series Engines 4-2
4.4.1.1.1 Connection Diagram 4-2
4.4.1.1.2 Carburetor System 4-2
4.4.1.2 L 2400 EF Engine 4-3
4.4.1.2.1 Components 4-3
4.4.1.2.2 Description 4-3
5ELECTRICAL SYSTEM 5-1
5.5.1 Description 5-1
5.5.2 L 2000 Series Engines 5-1
5.5.3 L 2400 EF Engine 5-2
5.5.3.1 Description 5-2
5.5.3.2 Connection of the Engine Electrics 5-4
5.5.3.2.1 Mounting of the ECU and wiring loom 5-4
5.5.3.2.2 Connection of the wiring loom 5-4
5.5.3.2.3 Connection of the Relay-box (MCU) 5-4
5.5.3.2.4 MCU- test 5-4
5.5.3.2.5 MCU and emergency battery test 5-5
5.5.3.3 Engine Instruments 5-5
5.5.3.3.1 Instrument calibration 5-5
Flugmotoren
1
Prepared by: J. B. Meyer Replaces edition from: 10.03.86 Page: 1-1
Checked by: Edition: 01.03.1999 Reg. Number:
Installation Manual
L 1700, L2000 and L 2400 Series

5.5.3.3.2 Connection of RPM indicatorwith 9-Pin connector 5-6
5.5.3.3.3 Connection of RPM-Indicator with Generator-pickup 5-7
5.5.3.3.4 Oil pressure and oil temperature 5-7
5.5.3.3.5 EGT, coolant temperature and coolant level warning lamp 5-8
5.5.3.3.6 Status Indicator 5-9
5.5.3.4 Fuel Pumps 5-9
5.5.3.5 Connections for the Instruments/Panel 5-9
5.5.3.6 Ignition System 5-10
5.5.4 Requirements 5-10
5.5.4.1 L 2000 Series Engines 5-10
5.5.4.2 L 2400 EF Engine 5-11
6ENGINE MOUNT 6-1
7EXHAUST SYSTEM 7-1
7.7.1 General 7-1
7.7.2 L 2400 EF 7-3
8PROPELLERS 8-1
8.8.1 L 2000 Series Engines 8-1
8.8.1.1 L 2400 EF Engine 8-1
9VIBRATIONS 9-1
10 COWLING 10-1
10.10.1 L 2000 and Series 10-1
10.10.2 L 2400 EF Engine 10-1
10.10.2.0.1 Air Inlet 10-1
10.10.2.0.2 Air Ducting 10-1
10.10.2.0.3 Air Outlet 10-1
10.10.3 Engine Breather 10-2
11 Literature 11-1
Flugmotoren
Installation Manual
L 1700, L 2000 and L 2400 Series 1
Prepared by: J. B. Meyer Replaces edition from: 10.03.86 Page: 1-2
Checked by: Edition: 01.03.1999 Reg. Number:

Flugmotoren
1
Prepared by: J. B. Meyer Replaces edition from: 10.03.86 Page: 1-1
Checked by: Edition: 01.03.1999 Reg. Number:
Installation Manual
L 1700, L2000 and L 2400 Series

1INTRODUCTION
1.1 Title
The title of this manual is:
Installation Manual for the LIMBACH L 1700, L 2000 and L 2400 Series Engines.
1.2 Foreword
This manual describes the requirements for the installation of the LIMBACH aircraft engines.
The manual contains the mandatory requirements and also a number of recommendations and
guidelines. This manual is for use by aircraft designers.
LIMBACH Flugmotoren cannot forsee all engineering aspects related to the specific aircraft in
-
stallation situation. Therefore this manual is to be used as an assistance in the engine installation
design. National airworthyness regulations may override or contradict the information given in
this manual. In such cases you should contact LIMBACH Flugmotoren for guidance, in certain
cases your aviation authorities may waive their requirements or procedures if a reasonable expla-
nation is given.
1.3 Applicability
This manual is applicable to all engines of the following types: LIMBACH L 1700, L 2000, L
2400.
The chapters are divided up into L 2000 and series and L 2400 EF engine headings.
L 2000 and series represents all L 1700, L 2000 and L 2400 EB engines, which are air-cooled and
supplied with conventional carburetors and magneto-ignition systems.
L 2400 EF is described especially because of it´s electronic engine management system with
electronic ignition, fuel injection and liquid-cooled cylinder heads.
1.4 Copyright
This manual is protected by German and international copyright. This book or parts thereof, may
not be reproduced in any form without permission.
Flugmotoren
1
Prepared by: J. B. Meyer Replaces edition from: 10.03.86 Page: 1-1
Checked by: Edition: 01.03.1999 Reg. Number:
Installation Manual
L 1700, L2000 and L 2400 Series

2MEASUREMENTS
The dimensions of the different engine series are given in the applicable installation drawings.
They also contain the location and size of the engine interfaces (all dimensions are given in milli
-
meters).
2.1 Definitions
Following an illustration indicating the cylinder designation, direction of rotation etc.
Flugmotoren
2
Prepared by: J. B. Meyer Replaces edition from: 10.03.86 Page: 2-1
Checked by: Edition: 01.03.1999 Reg. Number:
Installation Manual
L 1700, L2000 and L 2400 Series
1
3
2
4
front
rear
top
bottom
rotation
right left
Fig.: 2-1

3COOLING
3.1 Description
3.1.1 L 2000 and Series Engines
The L 1700, L 2000 and the L 2400 EB series engines are air cooled. For safe operation, a cowl-
ing and baffle system is required. The air that enters the inlets (A) must be guided through the
finned passages of both the cylinders and the cylinder heads. The heated air then exits through the
cowling exit (E). The exit opening should be approximately twice the size of the inlet. The en
-
gine requires air at approximately 1000 liters/second at a pressure drop of between 200.0 mm and
300.0 mm of water (standard atmospheric pressure). Baffles (B) must be fitted correctly to
achieve the optimum cooling performance. The baffles should touch the cooling fins of the en-
gine and must be sealed (S) against the cowling and the engine. To obtain the correct fit at the
propeller is more difficult but must also be achieved with care. Openings, the size of the palm of
the hand, can be observed in this area which reduces the cooling performance.
The engine is designed for downdraft cooling. Do not use updraft cooling.
Flugmotoren
3
Prepared by: J. B. Meyer Replaces edition from: 10.03.86 Page: 3-1
Checked by: Edition: 01.03.1999 Reg. Number:
Installation Manual
L 1700, L2000 and L 2400 Series
A
E
S
S
O
B
B
C
H
M
X
Fig.: 3-1Typical Engine Installation

For pusher- and/or fuselage-installation behind cockpit it must be ensured that the inlets are not
blocked due to unsymmetric flight attitude
A typical engine installation is shown in Fig. 3-1. To obtain the maximum cooling performance,
the upper plenum must be as large as possible.
The shape and size of the inlet and exhaust openings must be designed not to exceed the tempera
-
ture limits (refer to the operating manual) under worst case conditions (full power climb at the
lowest permitted speed).
For the maximum reliability and safety, it is not recommended to exceed a cylinder-head temper-
ature of 160° C at high-power cruise.
The engine has an oil cooler (O) which must be positioned correctly and is the responsibility of
the aircraft designer. It is possible to drain the oil from the oil cooler at regular intervals. The oil
cooler must have a separate duct for the cooling air. This air is directed through the chamber of
the upper plenum (cold section) of the engine cowling to the oil cooler. There is also a venting
outlet. To assure a sufficient oil temperature during winter operation, it could be useful to reduce
the effective inlet surface of the oil cooler by using an aluminum shielding. Other changes to the
fins and/or the oil cooler are not permitted.
For cabin and carburetor heating a heat muff (M) around the exhaust may be used. It also helps
to cool the exhaust, which may reacht temperatures of more than 800 °C. Use ducting hose (H) to
attach the heat muff to an opening in the cowling. The heated air may then be supplied to the car
-
buretor or to the cabin. Make sure that you have a proper exit (X) to the outside in case the cabin
heating is switched off and that the duct (X) does not block the cooling air exit (E)
Caution: Use a carbon monoxide warning device to protect the crew from a defictive heating system!
Note: The cooling system will absorb power, which is no longer available for flight propulsion. A well
designed cooling system will minimize these losses and increase the flight performance and/or
lower the fuel consumption.
It is very important that all of the components in the cooling system are installed carefully.
For more information see Technical Bulletin 44 in it´s current edition.
3.1.2 L 2400 EF Engine
The cooling system of the L 2400 EF engine consists of 4 different sub-systems. The general sys-
tem layout is shown in Fig. 3-2:
•liquid cooled cylinder-heads
•direct air-cooled cylinders
•oil cooling
•direct air-cooled generator
The major portion (70%) of the engine heat is dissipated by the cylinder-head cooling syst em.
The cylinders are cooled with air, the oil mainly removes the heat caused by friction from the en
-
gine (5%). The cooling system is not designed for continuos operation at full power when the
aircraft is on the ground. During flight the flow of air increases considerably and the cooling
property also increases considerably.
The cylinder head is designed so that the liquid coolant, a water/ethylene-glycol mixture, flows
through the passages in the cylinder head under pressure. A pump circulates the liquid coolant
through the pipes (CO) to a radiator (R). The coolant is the returned to the coolant pump through
a pipe (CR). Cooling air (AR)flows through the matrix of the radiator which cools the liquid cool-
ant. A sealed duct to the cowling is ncessary to ensure full flow through the radiator. The syst em
Flugmotoren
3
Prepared by: J. B. Meyer Replaces edition from: 10.03.86 Page: 3-2
Checked by: Edition: 01.03.1999 Reg. Number:
Installation Manual
L 1700, L2000 and L 2400 Series

Flugmotoren
3
Prepared by: J. B. Meyer Replaces edition from: 10.03.86 Page: 3-3
Checked by: Edition: 01.03.1999 Reg. Number:
Installation Manual
L 1700, L2000 and L 2400 Series
Fig.: 3-2L 2400 EF Cooling System Layout

has an expansion vessel (X) to receive the residue of the heated coolant. The expansion vessel has
a pressure cap and a vent (XV) to atmosphere to prevent excessive build-up of pressure.
A thermostat is not included in this system1because the temperature of the air-cooled cylinder
wall, a major factor governing cylinder wear, is reached very quickly. To prevent the cylinder
head from reaching an operating temperature which may be too low, in winter months, it is rec
-
ommended that the airframe manufacturer include an aerodynamic radiator blind in the design.
This will also reduce the surface drag.
The crankshaft drives the coolant pump through a pulley-wheel/belt system. A tensioning adjust
-
ment arm and jockey wheel tensions the drive-belt.
A more recent design features of cylinder-cooling is the use of units made from composite mate-
rials. This consists of two funnel shaped units connected to the front of the engine cowling. The
air (AC) flows directly to the cylinders and eliminates the requirement for the air baffles to cool
the engine. This design is more efficient and it is recommended to embody this in the design of
the aircraft. Use a seal of 170.163.500.000 to avoid the loss of cooling-air between the funnels
and cowling.
Note The airframe manufacturer might decide to include a water-to-oil heat exchanger in preference to
the separate components. They are very compact and are used in several types of automobiles.
This eliminates the need for the cooling ducting which is to be found in the conventional cooling
system. LIMBACH-Flugmotoren do not recommend this practice. The use of individual items is
recommended for safety. If a component fails, it will not eliminate the complete system and will
allow the aircraft to return safely, possibly on reduced power.
3.1.2.1 Cylinder Cooling
The cylinder cooling requires only 25% of the amount of air necessary for cooling a conventional
air-cooled engine installation. Pressure cooling is required for the cylinders.
The engines are delivered with the cooling-air ducts, for cylinder cooling, already attached. The
cooling air enters two inlets and is effectively directed, by the cooling-air ducts, to the surface of
the cylinder. The interface of the cowling to the cooling-air ducts must be sealed.
3.1.2.2 Cylinder-Head Cooling
The cylinder-head cooling consists of the following components (Fig.:3-2):
Pos. Item Description
Coolant pump installed on engine
CO,R Coolant pipes partially installed on engine
missing parts are customer
supplied items
CO,R Coolant hoses included in the installation kit,
missing parts are customer
supplied items
RRadiator (cooler) included in the installation kit
XExpansion vessel with pressure
cap included in the installation kit
Thermostat optional
Flugmotoren
3
Prepared by: J. B. Meyer Replaces edition from: 10.03.86 Page: 3-4
Checked by: Edition: 01.03.1999 Reg. Number:
Installation Manual
L 1700, L2000 and L 2400 Series
1A thermostat is optionally available on special request

The airflow to the radiator must be independent of the airflow to the cylinders, with careful de
-
sign it may be possible to use a common outlet. The size of the radiator is dependent on the aero-
dynamic conditions such as air-speed during climb, position of installation and design of the air
inlet and outlet.
The recommended
sizes of the radia
-
tor are based on an
air-speed of 40 m/s
and a temperature
difference of 60° C
between the cool
-
ant and ambient
air.
The size of the ra-
diator may be re-
duced if there is an
increase in air ve
-
locity and/or cool
-
ant temperature.
However, for
safety reasons, a
maximum temper-
ature of 110° C
must not be ex
-
ceeded.
The pipes for the cooling water have a diameter of 25 mm and the mixture is 50% glycol for frost
and corrosion protection. There are two bleed lines from the outlets from the engine to the expan-
sion vessel. The angle of installation of the radiator is 45° and is installed on the brackets of the
engine mounts. Flexible hoses permit the engine to move in relation to the engine mounts (engine
is installed in rubber anti-vibration blocks). Make sure that the outlet for the cooling air is of an
adequate size . Install the expansion vessel at the highest point (for bleeding).
3.1.2.3 Oil Cooling
Oil cooling (Fig.: 3-3) requires another radiator or heat exchanger, which can be slightly larger
than required because of the thermostat. The oil cooler is delivered within the installation kit.
The oil cooler may be attached directly to the cowling and the cooling air is provided through an
NACA inlet (N) and a Duct (D) to the oil cooler (O). The cooler must be sealed against the duct
with an elastic seal (S) to prevent an air bleed to the inside of the engine cowling. The air bleed
would cause a disturbance of the pressure differential which is used to operate the air-based por-
tion of the cooling system. The warm air exiting from the cooler must pass through the main
cooling air exit. Be sure to dimension it accordingly.
Note: The duct (D) must also be sealed towards the cowling. Keep in mind that the installation situa-
tion may change with manufacturing tolerances which may be very large with all dependencies
considered. Also consider that the enduser may not always fit the cowling correctly and that the
sealing should function in such cases also. Inspection of the seals should be included as an item
in your maintanance documentation.
Flugmotoren
3
Prepared by: J. B. Meyer Replaces edition from: 10.03.86 Page: 3-5
Checked by: Edition: 01.03.1999 Reg. Number:
Installation Manual
L 1700, L2000 and L 2400 Series
D
O
S
In Out
N
Fig.:3-3Oil Cooler Installation L 2400 EF (Sample)

3.1.2.4 Technical Data
Coolant flow (liquid cooling) approx. 0.1 m3/min. @3000
rpm
Max. coolant temperature 110° C
Size of radiator approx. 4,5 dm2
Air-speed ahead of the radiator approx. 40 m/s
Max. pressure in the cooling
system 1.2 bar
Air flow over cylinders approx. 0.2 m3/s / 0.17 kg/s
Size of oil cooler approx. 2.0 dm2
3.1.2.5 Generator Cooling
On the rear of the generator is a cooling cap to prevent overheating of the diode plate. A wire re-
inforced hose of diameter 25 mm supplies pre-cooling air to the oil cooler at the NACA inlet.
Flugmotoren
3
Prepared by: J. B. Meyer Replaces edition from: 10.03.86 Page: 3-6
Checked by: Edition: 01.03.1999 Reg. Number:
Installation Manual
L 1700, L2000 and L 2400 Series

4FUEL SYSTEM
4.1 Requirements
The fuel system has to be designed for all types of fuel as given in the operating manual and there
should also be a good chemical resistance to cleaning materials. An hazardous operating condi-
tion may occur when fuel tanks are used which are made of composite material and observe the
surface sealing and also the adhesion. New lead-free fuels contain an alcoholic dissolvent. Both a
fuel filter and a water trap should be provided at a suitable location. No particles larger than 7-10
µm must be allowed to pass through the filter.
Depending on the design of the fuel system and the ambient temperature, vapor locks may occur.
These create a severe power loss. In some aircraft it may be possible that the pilot may not ob-
serve any indication of this during taxiing and the take-off run. The operating manual of the air
-
craft must contain an indication of this fact. The probability of vapor locks is minimized if the
instructions on the connection diagram are followed. The electrical fuel pump must be placed at
the coolest position in the system. In order to reduce the fire hazard, only minimum quantity of
fuel is to be contained forward of the firewall.
Flugmotoren
4
Prepared by: J. B. Meyer Replaces edition from: 10.03.86 Page: 4-1
Checked by: Edition: 01.03.1999 Reg. Number:
Installation Manual
L 1700, L2000 and L 2400 Series
V2
P2
V1
S1
F1
F2
V3
P2 F5
T1
T2
W1
Fig. 4-1Fuel System Diagram, Engines with Carburetors

4.1.1 L 2000 Series Engines
The filter must have a capacity of between 0.15 liters and 0.25 liters. A suitable filter is available
under the part number 201.090.015.000.
The L 2000 series engines are provided with a positive displacement mechanical pump which is
sufficient for normal use. For additional safety, an electrical fuel pump should be connected in
line to the mechanical pump (diagram). The electrical pump is mandatory if MOGAS fuel is
used.
4.1.1.1 Connection Diagram
Fig. 4-1illustrates a sample fuel system. The layout may vary with aircraft and national airwor-
thiness requirements. The designations of the diagram symbols are as follows:
F1 Fuel filter
F2 Water trap
F5 Tank filter
P1 Mechanical fuel pump
P2 Electrical fuel pump
T1 Fuel tank
T2 Tank vent
S1 Fuel pressure indicator (optional)
V1 Carburetor
V2 Carburetor (only twin carb models )
V3 Fuel cock
W1 Firewall
4.1.1.2 Carburetor System
LIMBACH engines in general
are equipped with constant de-
pression carburetors. Therefore
the pressure of the intake-air
must be at the same level as the
air pressure for the float cham
-
bers ventilation and for a work
-
ing altitude correction. Never
use a direct pressure air supply
for the intake because this
would give a very inconstantly
lean mix ratio. A carburetor
heating system is recommended
to prevent carburetor icing (Fig.
Flugmotoren
4
Prepared by: J. B. Meyer Replaces edition from: 10.03.86 Page: 4-2
Checked by: Edition: 01.03.1999 Reg. Number:
Installation Manual
L 1700, L2000 and L 2400 Series
1
2
345
1
6789
10
Fig.4-2Sample Carburetor Preheat System L 2000 EA (Single
Carburetor) series

4-2and Fig. 4-3). Please note
the fuel tray (item 10) which is
located below the carburetor to
prevent fuel from dripping onto
hot engine components.
Position of the notch in gasket
(1) is also very important to en-
sure the function of the carbure-
tor. Check the air filter flange
of the carburetor and make sure
that the openings are not cov
-
ered with the gasket.
Flugmotoren
4
Prepared by: J. B. Meyer Replaces edition from: 10.03.86 Page: 4-3
Checked by: Edition: 01.03.1999 Reg. Number:
Installation Manual
L 1700, L2000 and L 2400 Series
Fig. 4-3Sample Carburetor Preheat System L 2000 EB1AA (Twin
Carburetor) Series

4.1.2 L 2400 EF Engine
4.1.2.1 Components
The fuel pipes must be so routed as to avoid heating of the fuel. The L 2400 EF engine has elec-
tric fuel pumps which provide the required injection pressure and the delivery output is approxi-
mately 100 l/h. This is well above the maximum consumption of 30 l/h. The pressure regulator
controls the injection pressure. Fuel not injected into the cylinders flows from the pressure regu
-
lator back into the tank (loop circuit). The fuel system, downstream of the pumps, operates at a
pressure of 2.5 bar. The material of the fuel lines, internal diameter 6.0-8.0 mm, is to be compati-
ble with the type of fuel used. Suitable fuel lines are available on request.
4.1.2.2 Description
Fuel is supplied to the injection nozzles (F1-F4) by a loop circuit which prevents the formation of
gas bubbles. The tank(s) (T1) also provides the function of the radiator1. The fuel flows from the
tanks to the active pump (P1 or P2), from the pump to the filters (F1-F4), to the injection nozzles
Flugmotoren
4
Prepared by: J. B. Meyer Replaces edition from: 10.03.86 Page: 4-4
Checked by: Edition: 01.03.1999 Reg. Number:
Installation Manual
L 1700, L2000 and L 2400 Series
L1 S1
L2
L4
T1
T2
F5
F2
F1 F3
V1
V2
V3
P2
P1
L3
R2
W1
Fig. 4-4Fuel System Schematic L 2400 EF
1The fuel tank should have some extra volume to allow for expansion of the fuel and to provide some extra space for
separation of air bubbles.

Installation Manual
L 1700, L2000 and L 2400 Series
4, 2, 1 and 3, from the injection nozzles to the pressure sensor (S1) and then to the pressure regu
-
lator (R2). The unused fuel flows back into the tanks. The electric driven pumps, arranged in par-
allel and the separator(s) (F3, F4), are to be located at the lowest possible position in the fuel
system (Fig. 4-4). The fuel lines uses must be pressure resistant to a design pressure of 3 bar and
to a limit pressure of min. 6 bar. They must be protected with fire resistant sleeves. Also the fuel
lines must be chemically resistant against aviation and automotive fuel, alcohol (metha nol) and
engine oil.
Item Component Remark Position
F1-F4 Fuel injection Engine
T1 Tank Airframe/wings
T2 Tank vent
F1, F2 Filter 7.0 um, with replacement and
inspection facility Firewall / airframe
F3, F4 Water
separator(s) main fuel/feed auxiliary system if
specified firewall
F5 Tank Filter Tank
L1 Fuel line Crossover line to cylinder banks Engine
L2 Fuel line Return to fuel pressure regulator Engine to firewall
L3 Fuel line Pressure line from pump(s) Firewall/engine
P1, P2 Fuel pumps electrically driven; main and
auxiliary system Firewall / airframe
S1 Fuel pressure
sensor connect between cross-over line
and pressure regulator. firewall
V1-V3 Shut-off valve(s) main fuel/feed auxiliary and
return lines if specified Airframe
R2 Pressure
regulator connect manifold pressure,
cross-over and return line firewall
4.2 Airfilter
An air filter (A) (see Fig.:3-2) should be used to protect the engine from dust and dirt. The air
filter duct has been optimized for the engine and should not be changed, because the power might
be reduced. The air filter must be provided with cool air from the outside. An enclosure for the
air filter that is attached to the cowling has proven to be practical. A drain vent in the air filter
enclosure provides protection from water accumulation in the cell of the air filter. An internal
vane prevents the ingress of water.
Flugmotoren
4
Prepared by: J. B. Meyer Replaces edition from: 10.03.86 Page: 4-5
Checked by: Edition: 01.03.1999 Reg. Number:

5ELECTRICAL SYSTEM
5.1 Description
The power output of the starter largely depends on both the size of the battery and the
cross-section of the cable. The starter will draw a current of up to 300A.
Caution: Be aware of a possible fire hazard when installing the starter cable.
5.2 L 2000 Series Engines
The L 2000 series engines have a 12V electrical system for both the starter and the alternator,
a 24 V System is available on request. Observe the wiring diagram.
Recommended figures for the battery capacity are 12V/28Ah and a cross-section for the starter
cable 16mm².
According to your installation, these figures may vary considerably.
Flugmotoren
5
Prepared by: J. B. Meyer Replaces edition from: 10.03.86 Page: 5-1
Checked by: Edition: 01.03.1999 Reg. Number:
Installation Manual
L 1700, L2000 and L 2400 Series
GND (31b)
G2 G3
N1
H1
F1
H1
S2
F1
G1
+P1 S1
V1
K1
F2
C1
Y1
P2
P3
P4
P5
P6
F6 F5 F4 F3
B4 B3
B2
G4
S3
E1..E4
M1
B1
30
31 50
B+ D+
D+
DF
D-
31
W
31
B+
D-
D+
DF
(Exc)
+
+
- -
+
-
+
-
tegt tcht
Bus +12V
A
M
npoil toil
Fig. 5-1Sample Wiring Diagram for L 2000 Series

A ground cable from the engine to the battery is required. It should have at least the same cross
section as the starter cable and should be attached to one of the starter mounting bolts.
Warning: If the magneto switch is be set to the “ON” position (for example circuit testing) beware of
the “Hot-Engine”condition especially if the propeller is attached. The battery must not dis
-
charge with the magneto switch in the “ON” position.
5.3 L 2400 EF Engine
5.3.1 Description
The L 2400 EF engine has a 12V electrical system for the engine electrics, the starter, the pumps
and the generator. The engine is equipped with an electronic engine management system that pro-
vides full control of the fuel and ignition requirements of the engine throughout the complete op-
erational envelope. Mixture control, due to the ambient conditions, is automatic.
The information required to calculate the fuel flow and ignition advance is given in two basic ta
-
bles with 16 x 16 fields. This gives a total of 256 individual values for each of the two functions.
Engine speed and throttle angle are used to address the information given in the tables. Engine re-
quirements for operating conditions that do not exactly correspond to the table entries are interpo-
lated. Additional inputs give information on air temperature, air pressure and engine temperature.
They are used to adjust the values in the basic table to the requirements for non-standard environ
-
mental conditions. The Engine Control Unit (ECU) is the electronic brain.
Warning: Function of the engine management system is dependent on the availability of electrical
power.
Unlike conventional engines with magnetos, the L 2400 EF engine will not function without a
12V power source. To provide operational behavior similar to the conventional engines that most
pilots may be familiar with, a back-up system is essential. This is provided by the emergency
switch and the relay box (MCU). It should ensure a supply of the electrical power for the engine
function for a minimum period of twenty minutes after the loss of power from the main electrical
system.
The emergency switch is included in the circuit in case the fuel pump or a sensor cases to func
-
tion. In the emergency operational mode, the second fuel pump replaces the previously active
pump, the second speed sensor replaces the previously active speed sensor. The sensors rev ert to
a permanently set resistance. The engine can be started with the emergency switch in the “Emer-
gency operation“ position, providing that the main switch is in the “ON“ position and the main
battery functions correctly. The housing has a diameter of 53.0 mm. The emergency switch does
not influence the electrical power supply/period of operation.
The relay box has the function to supply the engine with electrical power from the main batt ery,
generator and the emergency battery. The nominal current is 12V. There is a 9 Amp. consump
-
tion for engine operation. Because the operation of the engine is dependent on the functional op-
eration of the electrical power supply, the emergency battery and appropriate switching inside the
relay-box (MCU) is necessary. No electrical power flows from the emergency battery into the air-
craft network but the battery can be continually charged. The generator provides the syst em with
13.5-14.0V.
5.3.2 Connection of the Engine Electrics
5.3.2.1 Mounting of the ECU and wiring loom
The ECU should be mounted with shock mounts. For example 1 Barrymount GE 21-03-05 may
be used at the backside and 2 Flex-Loc Q-6 at the front.
Flugmotoren
5
Prepared by: J. B. Meyer Replaces edition from: 10.03.86 Page: 5-2
Checked by: Edition: 01.03.1999 Reg. Number:
Installation Manual
L 1700, L2000 and L 2400 Series

Flugmotoren
Installation Manual
L 1700, L 2000 and L 2400 Series 5
Prepared by: J. B. Meyer Replaces edition from: 10.03.86 Page: 5-3
Checked by: Edition: 01.03.1999 Reg. Number:
Fig. 5-2Block Diagram L 2400 EF Electrical System
This manual suits for next models
2
Table of contents
Other LIMBACH Engine manuals
Popular Engine manuals by other brands

MVVS
MVVS 3007L 80 IRS operating instructions

Fiamma
Fiamma Polar White 08318-01P Installation and usage instructions

MTHTrains
MTHTrains F-3 POWERED B-UNIT Engineer's guide
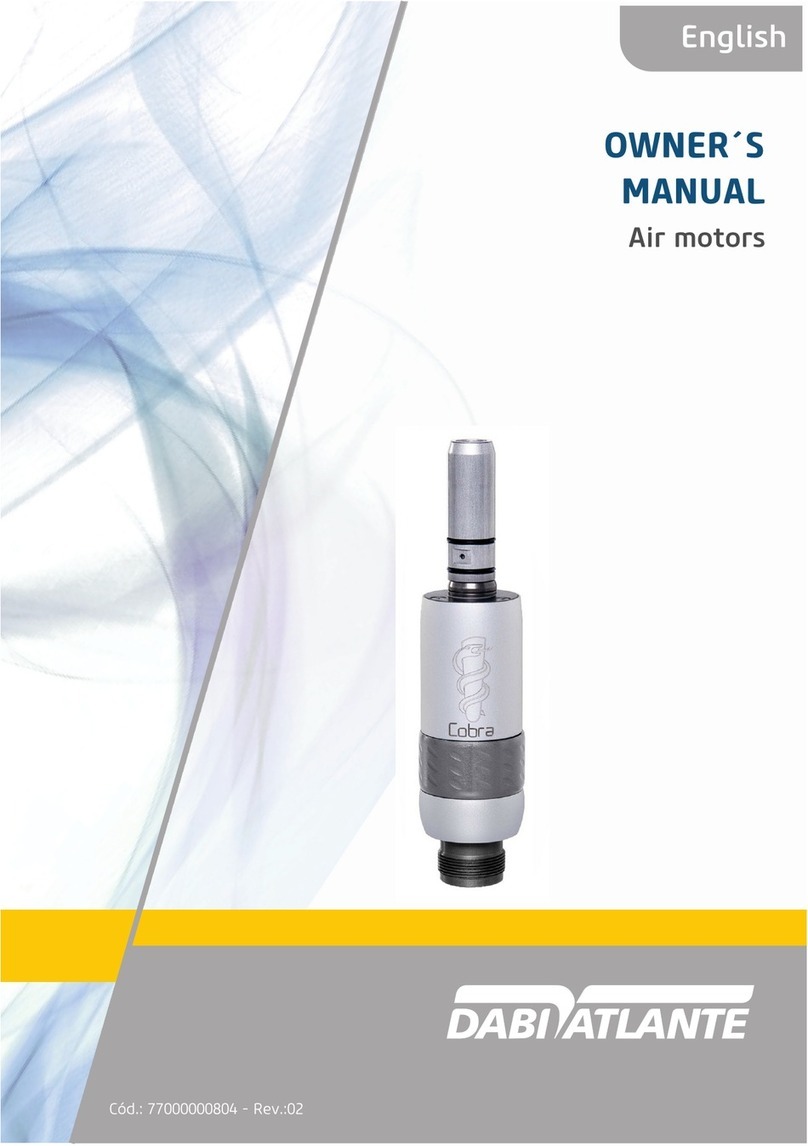
Dabi Atlante
Dabi Atlante MICROMOTOR INTRA 32 MM-C SPRAY TB owner's manual
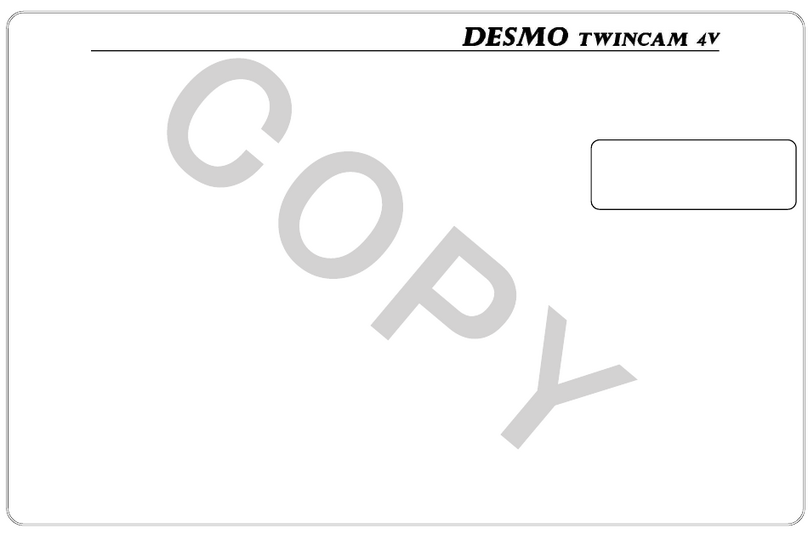
Takegawa
Takegawa DESMO TWINCAM 4V manual
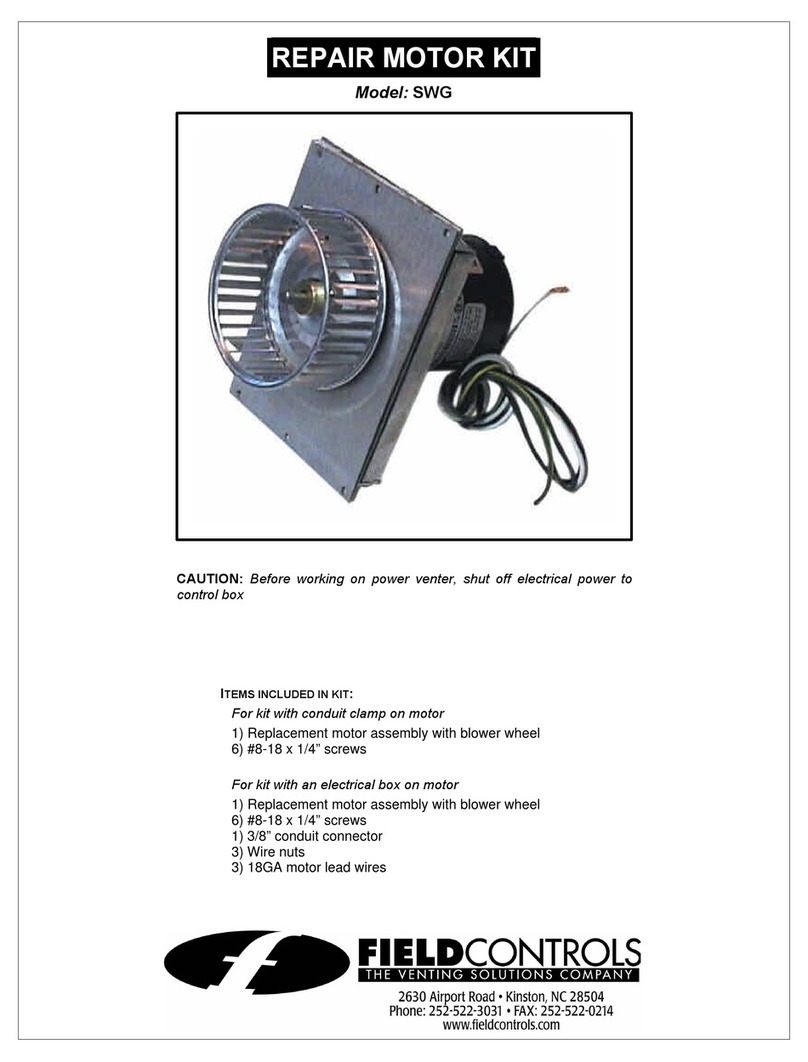
Field Controls
Field Controls SWG Removal and installation