LMI Technologies Liquitron DC4000 Series User manual

1
Replaces same of Rev. E 11/99
1732. F 3/2013
Instruction Manual
Liquitron™ DC4000 Series
Conductivity Controller
For le reference, please record the following data:
Model No:
Serial No:
Installation Date:
Installation Location:
When ordering replacement parts for your LMI Controller or accessory, please include
the complete Model Number and Serial Number of your unit.
201 Ivyland Road
Ivyland, PA 18974 USA
TOLL FREE: (800) 564-1097
TEL: (215) 293-0401
FAX: (215) 293-0445
http://www.Imipumps.com
sales@novatech-usa.com
www.novatech-usa.com
Tel: (866) 433-6682 Fax: (866) 433-6684
Tel: (281) 359-8538 Fax: (281) 359-0084

4
Contents
1.0 Introduction.......................................................................................................................................5
2.0 Installation ........................................................................................................................................7
2.1 Mounting the Controller Enclosure .................................................................................... 7
2.2 Enclosure Mounting Dimensions .......................................................................................8
2.3 Electrical Wiring Information ..............................................................................................8
2.4 Terminal Strip Layout.........................................................................................................9
3.0 Operating the Controller.................................................................................................................16
3.1 Menu Overview................................................................................................................17
3.2 Conductivity .....................................................................................................................18
3.3 Set Point ..........................................................................................................................19
3.4 ∆ Differential.....................................................................................................................20
3.5 Low Alarm ........................................................................................................................21
3.6 High Alarm .......................................................................................................................22
3.7 Feed.................................................................................................................................23
3.8 Manual Outputs ...............................................................................................................24
3.9 Advanced Setup ..............................................................................................................25
3.10 Temperature.....................................................................................................................26
3.11 H2O Meter ........................................................................................................................27
3.12 Boiler................................................................................................................................28
4.0 Start-Up .........................................................................................................................................30
4.1 Cooling Tower Installation................................................................................................31
4.2 Pre-Start-Up Work Sheet.................................................................................................32
4.3 Boiler Installation .............................................................................................................32
4.4 Determining the Blowdown Requirement ........................................................................ 32
4.5 Timed Sampling Mode .....................................................................................................33
4.6 Continuous Sampling.......................................................................................................33
4.7 Boiler Installation Notes...................................................................................................33
4.8 Boiler Start-Up .................................................................................................................34
4.9 Timed Sample Start-Up ................................................................................................... 34
4.10 Continuous Sample Start-Up ...........................................................................................36
4.11 Closed Loop Installation Theory of Operation .................................................................36
4.12 Closed Loop Start-Up ......................................................................................................36
4.13 Closed Loop Installation Notes ........................................................................................37
5.0 Functional Instructions ...................................................................................................................37
5.1 Calibration........................................................................................................................37
6.0 Maintenance...................................................................................................................................39
6.1 Controller ......................................................................................................................... 39
6.2 Probe ...............................................................................................................................30
7.0 Troubleshooting..............................................................................................................................40
8.0 Factory Settings .............................................................................................................................41
9.0 Product Specications....................................................................................................................41
10.0 Product Exploded View .................................................................................................................. 42
11.0 Product Parts List...........................................................................................................................43
12.0 Warranty ........................................................................................................................................44

5
1.0 Introduction
The DC4000 is a microprocessor-based conductivity controller. It is designed for use in a variety of water treatment
applications requiring precise control of total dissolved solids and chemical feed. Among its many uses, the DC4000
will control conductivity and chemical feed in cooling towers, closed loop systems, and boilers.
LMI’s DC4000 Series of conductivity controllers allows the greatest programming exibility for cooling tower or boiler
system applications. This is accomplished through the use of an options menu that is easy to use.
BLEED or BLOWDOWN of system water by valve control can be based on several setpoint options:
• Conductivity setpoint
• Hysteresis delay (lower than setpoint) to avoid valve operation chattering
• Rising or Falling conductivity trip points
FEED of chemical (inhibitor) can be based on four (4) different methods:
• FEED at the same time system BLEEDS (lockout timer limits maximum FEED time)
• FEED time calculated as a percentage of total BLEED time
• FEED based on a timed cycle (pump is on for a percentage of this timed cycle)
• FEED based on ow meter input
ALARM indicators and relay outputs are energized based on the following conditions:
• HIGH conductivity set point is reached
• LOW conductivity set point is reached
• NO FLOW condition exists (ow switch must be installed)
The display is a 16-character backlit LCD (liquid crystal display) which is visible in all light conditions. A three-key
position membrane is used to enter data and settings (see Figure 1). The conductivity range is 0 - 20,000 µSiemens. The
units can be either µSiemens or PPM/TDS (total disolved solids). If the units displayed are PPM/TDS, the ratio of µS:
to: TDS can be selectively programmed.
All setpoints and parameter settings are retained permanently in a special nonvolatile computer chip memory, preventing
their loss due to a power outage. This nonvolatile memory chip allows the unit to be programmed before installation. No
battery powered backup is required.
Built in test circuits are provided to test each individual relay output wiring and to allow for quick eld service isolation
of faulty probe, circuit cards, pumps, or solenoid valves for ease of troubleshooting.
A display for temperature is also provided. The range is 32° F to 212° F [0° C to 100° C]. The display can be either
fahrenheit or centigrade. This reading also provides the basis for temperature compensation which is performed in all
modes except the boiler mode.
A 4-20 mA analog data (or control) output is provided. The conductivity reading that corresponds to minimum and maxi-
mum analog signals is fully programmable. This signal can be used to power chart recorders or other pumps and devices.

6
The controller operates in two (2) distinct modes, ‘SYSTEM RUN’ and ‘SYSTEM START-UP’ or 'PROGRAMMING
MODE'. The unit will be in the ‘SYSTEM RUN’ mode when it is rst turned on. The various program screen menus
are used to calibrate the unit, set the control and alarm points, set the inhibitor feed operating parameters, and manually
test the relays and wiring connections.
In the ‘SYSTEM RUN’ mode the DC4000 monitors the conductivity and activates the appropriate control or alarm relay
as necessary based on the set points entered in the ‘SYSTEM START-UP’ mode.
The DC4000 is packaged in a NEMA 12X, ame-retardant, molded TPE enclosure. When ordered, 115 VAC units
come fully wired to include input power cord and relay output pigtails to allow for simple installation. The unit can be
hardwired through conduit to the lower junction box portion of the enclosure when required. Hard wiring makes the
unit suitable for NEMA 4X applications.
ALARM indicator lights when
a warning condition occurs:
• high alarm set point
• low alarm set point
• loss of ow
BACKLIT
LCD
DISPLAY
FLOW indicator lights when
there is a loss of system ow.
Operates only if ow switch
is installed
BLEED indicator
lights when the
BLEED OFF or
BLOWNDOWN
output is energized
FEED indicator
lights when feed
(inhibitor) output
is energized
PUSH BUTTON UP AND
DOWN ARROW KEYS allow
scrolling through menu and
selection or changing of set
point values
PUSH BUTTON ENTER KEY
provides for menu selection
and/or acceptance of selected
values
POWER indicator
lights when power
is supplied to unit
Figure 1

7
Figure 2
2.0 Installation
2.1 Mounting the Controller Enclosure
The DC4000 conductivity controller is supplied with integral wall-mounting anges. It should be mounted with the
display at eye level on a vibration free surface. All accessibe mounting holes should be utilized. The maximum allow-
able temperature is 122° F [50° C]. This should be considered if installation is in a high-temperature location. Once
the DC4000 is wall mounted, the metering pumps may be located at any distance from the controller. The conductivity
probe should be placed as close to the controller as possible. Consult factory for distance over 30 ft [9 m]. Under 25 ft
[7.6 m] is recommended. Over 30 ft [7.6 m], the cable may need to be isolated or shielded.

8
Figure 3
2.3 Electrical Wiring Information
Toreducethe riskofelectrical shock,thecontrollermust bepluggedinto agroundedoutlet withratingsconforming to
the specications on the data nameplate. It must be connected to a viable ground circuit. DO NOT USE ADAPTERS
(see Figure 4)! All wiring must conform to required electrical codes.
The DC4000 conductivity controller is available in either 115 or 230 VAC 50/60 Hz. The 115 VAC version is supplied with
one (1) 6-foot grounded AC power cord and two (2) 12-inch output pigtails for plug-in connection of controlled devices.
A four-pin connector is provided for the temperature compensated (cooling tower mode) conductivity probe.
The DC4000 controller is provided with a voltage selector switch to allow the unit to be used with a 115 VAC or
230 VAC power source. To change the voltage selection, disconnect the unit from the power source and remove the
front keypad panel. The selector switch is located on the circuit board attached to the back panel. When switching
voltages ensure that power cord and pigtails are appropriately changed.
Figure 4
2.2 Enclosure Mounting Dimensions
When using the prewired unit, the enclosure is congured as NEMA 12X. If the unit is connected through watertight
conduit, the enclosure is congured as NEMA 4X.
The following clearances should be observed for proper mounting (see Figures 2 and 3).

9
2.4 Terminal Strip Layout - DC4000
To access the wiring connections inside of the conductivity controller:
1. Disconnect the unit from electrical power.
2. Remove the four (4) screws and the junction box cover on the lower half of the unit.
3. Consult the specic instructions below for the connections required.
AC Power Input
Hot: TB4-1
Neutral: TB4-2
Ground: TB4-3
Bleed / Blowdown / Control Relay Output
Hot (N.O.): TB3-1
Hot (N.C.): TB3-2
Neutral: TB3-4
Ground: To ground wire (twist connect) or GND post
Feed Output
Hot: TB2-2
Neutral: TB2-1
Ground: To ground wire (twist connect) or GND post
Alarm Output
Hot: TB2-4
Neutral: TB2-3
Ground: To ground wire (twist connect) or GND post
4 - 20 mAmp Output
( + ) TB6-1
( - ) TB6-2

10
2.4 Terminal Strip Layout - DC4000
Flowmeter Input
The inputs are reversible when the owmeter connection is a relay and has no polarity. Only use
owmeters that do not send power to the controller.
TB9-1
TB9-2
Flow Switch Input
This input can be used to connect a ow switch or other device providing a switch closure output.
If a device such as this is connected to the DC4000, it will serve to disable the controller outputs
when this switch is in the “OPEN” position.
This function can be used as a safety override to prevent controller/pump operation during loss of
ow. This can be programmed to operate in the [N.O.] or [N.C.] conguration.
The electrical wiring inputs are reversible since the ow switch connection has no polarity.
TB9-3
TB9-4
Thermistor Probe Input (If Hardwiring Cooling Tower Probe)
Run the thermistor probe wiring through the PG9 connector on the right side of the DC4000
controller junction box keeping the wires away from any 115/230 VAC cables that may cause
electrical interference.
Signal Output: TB7-1
Signal Return: TB7-2
Conductivity Probe (If Hardwiring Cooling Tower or Boiler Probe)
Run the conductivity probe wiring through the PG9 connector on the right side of the DC4000
controller junction box keeping the wires away from any 115/230 VAC cables that may cause
electrical interference.
Signal Output: TB7-3
Signal Return: TB7-4

11
Terminal Strip Layout and Wiring Diagram for Accessories
Wiring diagram for Boiler Applications with 1/2” Conduit connections
Dotted lines represent HARDWIRED Accesories
DC4000

12
Terminal Strip Layout and Wiring Diagram for Accessories
Wiring diagram for Boiler Applications with 1/2” Conduit connections
Dotted lines represent HARDWIRED Accesories
DC4000

13
Flowmeter Input DC4000
2.4 Terminal Strip Layout for CE-DC4000
To access the wiring connections inside of the conductivity controller:
1. Disconnect the unit from electrical power.
2. Remove the four (4) screws and the junction box cover on the lower half of the
unit.
3. Consult the specic instructions below for the connections required.
AC Power Input
Hot: TB2-1
Neutral: TB2-3
Ground TB4-1
Bleed / Blowdown / Control Relay Output
Hot (N.O.): TB5-1
Hot (N.C.): TB5-2
Neutral: TB1-1
Ground: To ground wire (twist connect) or GND post
Feed Output
Hot: TB6-1
Neutral: TB2-4
Ground: To ground wire (twist connect) or GND post
Alarm Output
Hot: TB6-2
Neutral: TB1-2
Ground: To ground wire (twist connect) or GND post
4-20 mAmp Output
( + ) TB9-1
( – ) TB9-2

14
Flowmeter Input
The inputs are reversible when the owmeter connection is a relay and has no polarity. Only use
owmeters that do not send power to the controller.
TB10-1
TB10-2
Flow Switch Input
This input can be used to connect a ow switch or other device providing a switch closure output. If a
device such as this is connected to the DC4000, it will serve to disable the controller outputs when this
switch is in the “OPEN” position.
This function can be used as a safety override to prevent controller/pump operation during loss of ow.
This can be programmed to operate in the [N.O.] or [N.C.] conguration.
The electrical wiring inputs are reversible since the ow switch connection has no polarity.
TB10-3
TB10-4
Thermistor Probe Input (If Hardwiring Cooling Tower Probe)
Run the thermistor probe wiring through the PG9 connector on the right side of the DC4000 controller
junction box keeping the wires away from any 115/230 VAC cables that may cause electrical
interference.
Signal Output: TB11-1
Signal Return: TB11-2
Conductivity Probe (If Hardwiring Cooling Tower or Boiler Probe)
Run the conductivity probe wiring through the PG9 connector on the right side of the DC4000
controller junction box keeping the wires away from any 115/230 VAC cables that may cause electrical
interference.
Signal Output: TB11-3
Signal Return: TB11-4

15
Terminal Strip Layout and Wiring Diagram for Accessories
Wiring Diagram for version only
Dotted lines represent HARDWIRED Accessories
CE-DC4000

16
3.0 Operating the Controller
The Conductivity Read Screen or “System Run”:
The normal operating display for the DC4000 Series Controller is the conductivity reading screen (as shown
above). This screen is referred to as “System Run” throughout this manual. The controller relay outputs can-
not be activated unless the unit is in the “System Run” or conductivity reading mode. The only exception is
when the unit is in the test mode.
After reviewing or changing the conductivity controller programming setpoints, the unit must be returned to
the “System Run” or conductivity reading screen to allow automatic control to proceed. There are three ways
to return to the “System Run” screen and mode:
1. Use the or keys to move through the various menus, and back to the “System Run” screen.
2. Push ANY two (2) keys simultaneously. This will return the unit immediately to the “System Run”
screen.
3. The unit will return to the “System Run” screen automatically after three (3) minutes if no keys
are pressed.
COND : ( µS) 1470

17
3.1 Menu Overview
When the “System Run” screen is displayed in the window, the unit automatically switches to the run/operate mode of
operation.
This “System Run” display line is the top menu page item. Pressing the or keys will move the display window
to another line item. When not in the “System Run” mode the outputs to the control relays are disabled. The following
is the order of items in the main menu:
CONDUCTIVITY
SET POINT
∆ DIFFERENTIAL
LOW ALARM
HIGH ALARM
FEED
MANUAL OUTPUT
ADVANCED SETUP
TEMPERATURE
H2O METER
BOILER
COND : ( µS) 1470
Only if selected in Ad-
vanced Setup Menu.
Only if Controller is in
Cooling Tower mode.

18
3.2 Conductivity
The“CONDUCTIVITY”screendisplaystheconductivityreadingsineither
µSiemens or PPM/TDS (parts per million/total dissolved solids). When the
controller is displaying this screen it is considered to be in the SYSTEM
RUN mode. This means that the pumps, solenoids, and alarm outputs will
be activated based on the controller’s programmed set points. When the
controller is in any other display screen all the outputs are disabled and
will not be energized.
Pressing the “ENTER” key when the “CONDUCTIVITY” screen is dis-
played accesses the calibration mode. From this “CALIBRATION” screen
the “UP” or “DOWN” keys can be pressed to change the conductivity
reading and adjust for inaccuracies. If calibration adjustment is attempted
beyond 50% of the probe conductivity reading, the controller will ash a
warning on the screen: “CALIBRATION LIMIT”. This alerts the operator
that the probe needs to be serviced.
If Controller is set up in Boiler mode the calibration limits
are: -90% and +400%.
COND : ( µS)3400
Conductivity Reading Screen
From Conductivity Screen....press Enter....to access Calibration
If Calibration is attempted
beyond limit..... .....a Calibration Limit
screen will appear.
CALIBRATION LIMIT
ENTER
ENTER
COND : ( µS)3400
CONDUCTIVITY
SET POINT
LOW ALARM
HIGH ALARM
FEED
MANUAL OUTPUT
ADVANCED SETUP
TEMPERATURE
H2O METER
∆ DIFFERENTIAL
BOILER
CAL : ( µS) 1700
CAL: ( µS) 3400

19
The “SET POINT” screen allows access to the conductivity value that
will energize the bleed output relay and allow for the opening of the bleed
valve. The output trip setting may be changed in this screen. The relay can
be programmed to respond to either rising or falling conductivity values
(see “ADVANCED MENU” options under “TRIP”).
Pressing “ENTER” from the main menu “SET POINT” screen accesses the
conductivity reading trip value and allows the value to be changed. The
value will have a ashing cursor indicating that it can be changed. Press the
“UP” or “DOWN” key to increase or decrease the value. Press “ENTER”
to save the value.
SET PT 3000
Set Point Screen
SET PT µS 3200
3.3 Set Point
CONDUCTIVITY
SET POINT
LOW ALARM
HIGH ALARM
FEED
MANUAL OUTPUT
ADVANCED SETUP
TEMPERATURE
H2O METER
∆ DIFFERENTIAL
BOILER

20
3.4 ∆ Differential
The “DIFFERENTIAL” or dead band setting allows for a hysteresis to be
programmedintotheconductivitytrippoint.Aprogrammedhysteresisvalue
prevents the bleed relay and solenoid from cycling on and off repeatedly
when the conductivity reading hovers around the trip set point. The value
enteredin the “DIFFERENTIAL” is the amountofconductivity, awayfrom
the trip “SET POINT”, that the bleed relay will shut off.
Press “ENTER” from this screen to change the value. The value will
have a ashing cursor indicating that it can be changed. Press the “UP” or
“DOWN” key to increase or decrease the value. Press “ENTER” to save
the “DIFFERENTIAL” value.
∆ DIFF 100
Differential or Dead Band
CONDUCTIVITY SET POINTS
FALLING SET POINT
RISING SET POINT
CONDUCTIVITY
SET POINT
LOW ALARM
HIGH ALARM
FEED
MANUAL OUTPUT
ADVANCED SETUP
TEMPERATURE
H2O METER
∆ DIFFERENTIAL
BOILER
∆ DIFF 100

21
3.5 Low Alarm
The “LOWALARM” screen allows programming of the Low Conductivity
reading that activates an alarm LED and output relay.
Press “ENTER” from “LOW ALARM” screen to change this value. The
setting will have a ashing cursor indicating that the value can be changed.
Press the “UP” or “DOWN” key to increase or decrease the setting. Press
“ENTER” to save the value.
LO ALARM 250
Low Conductivity Alarm Set Point
CONDUCTIVITY
SET POINT
LOW ALARM
HIGH ALARM
FEED
MANUAL OUTPUT
ADVANCED SETUP
TEMPERATURE
H2O METER
∆ DIFFERENTIAL
BOILER
LO ALARM 250

22
3.6 High Alarm
The “HIGH ALARM” screen allows programming of the High Con-
ductivity reading that activates an alarm LED and output relay.
Press “ENTER” from “HIGH ALARM” screen to change this value. The
setting will have a ashing cursor indicating that the value can be changed.
Press the “UP” or “DOWN” key to increase or decrease the setting. Press
“ENTER” to save the value.
HI ALARM 4000
High Conductivity Alarm Set Point
CONDUCTIVITY
SET POINT
LOW ALARM
HIGH ALARM
FEED
MANUAL OUTPUT
ADVANCED SETUP
TEMPERATURE
H2O METER
∆ DIFFERENTIAL
BOILER
HI ALARM 4000
Table of contents
Other LMI Technologies Controllers manuals
Popular Controllers manuals by other brands

Citronic
Citronic CD-2 owner's manual
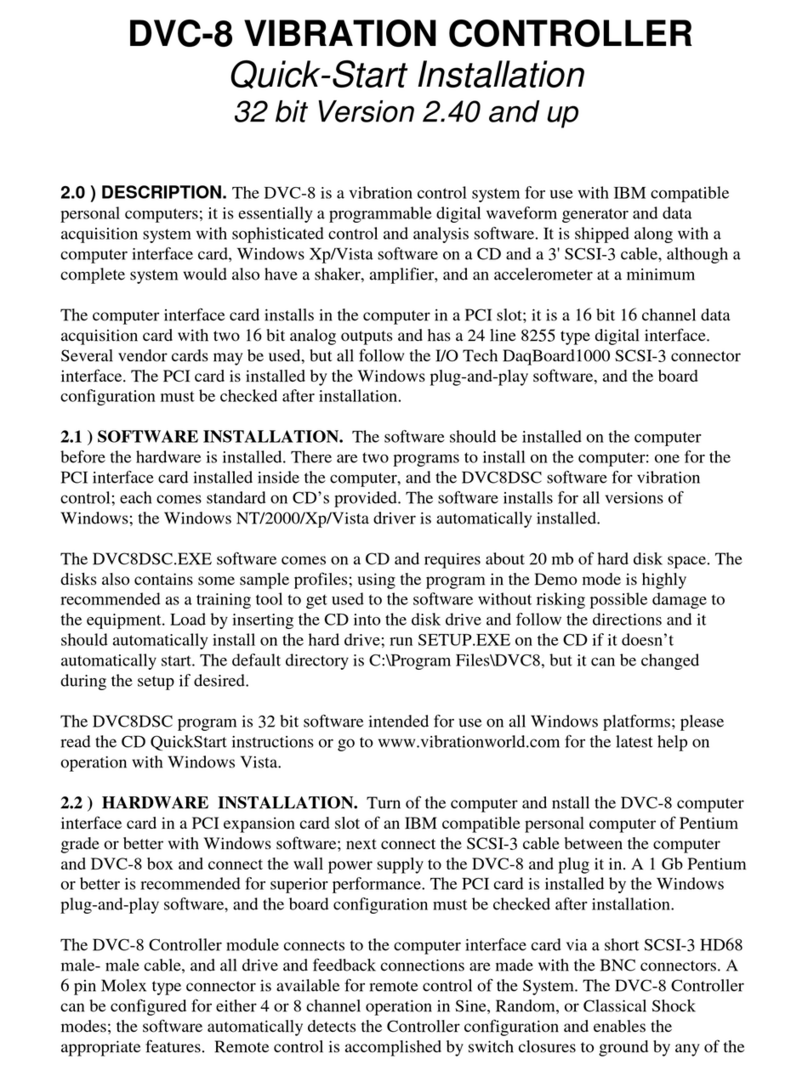
Vibration World
Vibration World DVC-8 Quick Start Installation
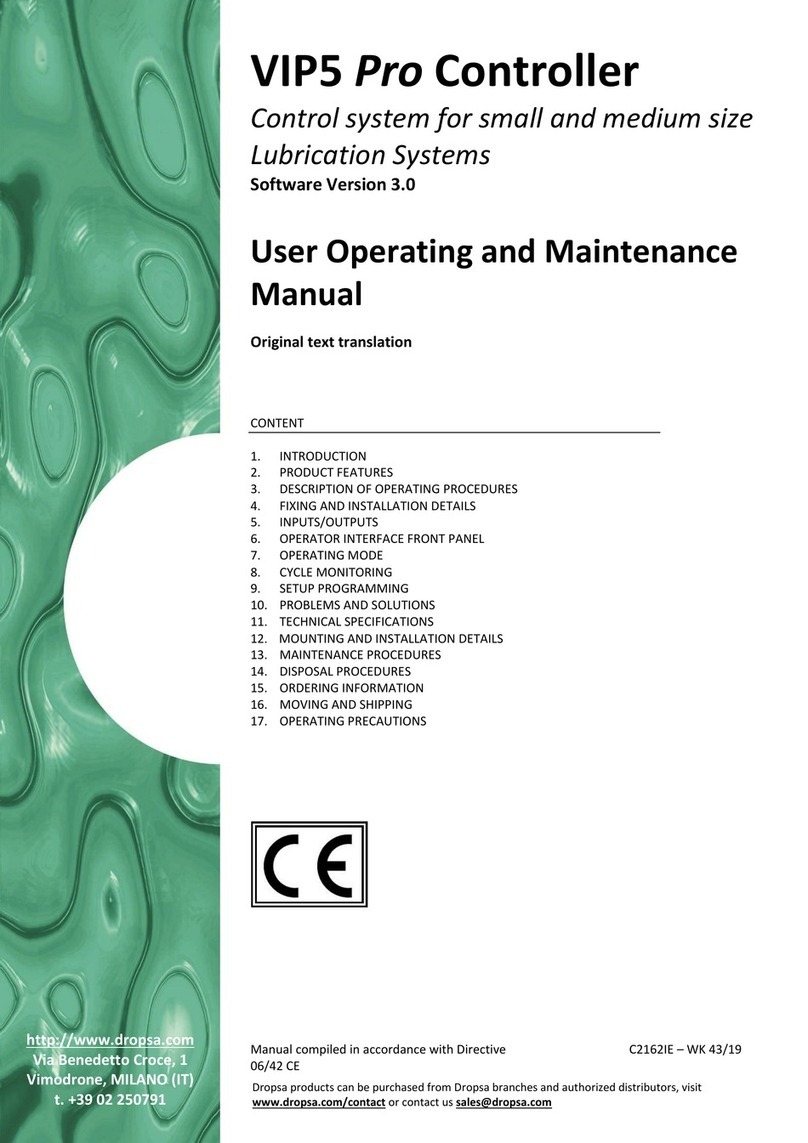
DROPSA
DROPSA VIP5 Pro User Operating and Maintenance Manual
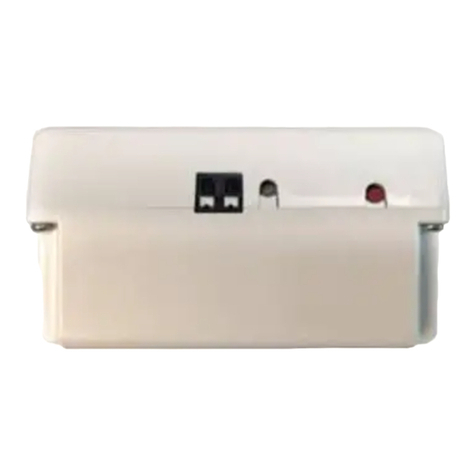
Douglas Lighting Controls
Douglas Lighting Controls BT-PP20-B installation manual
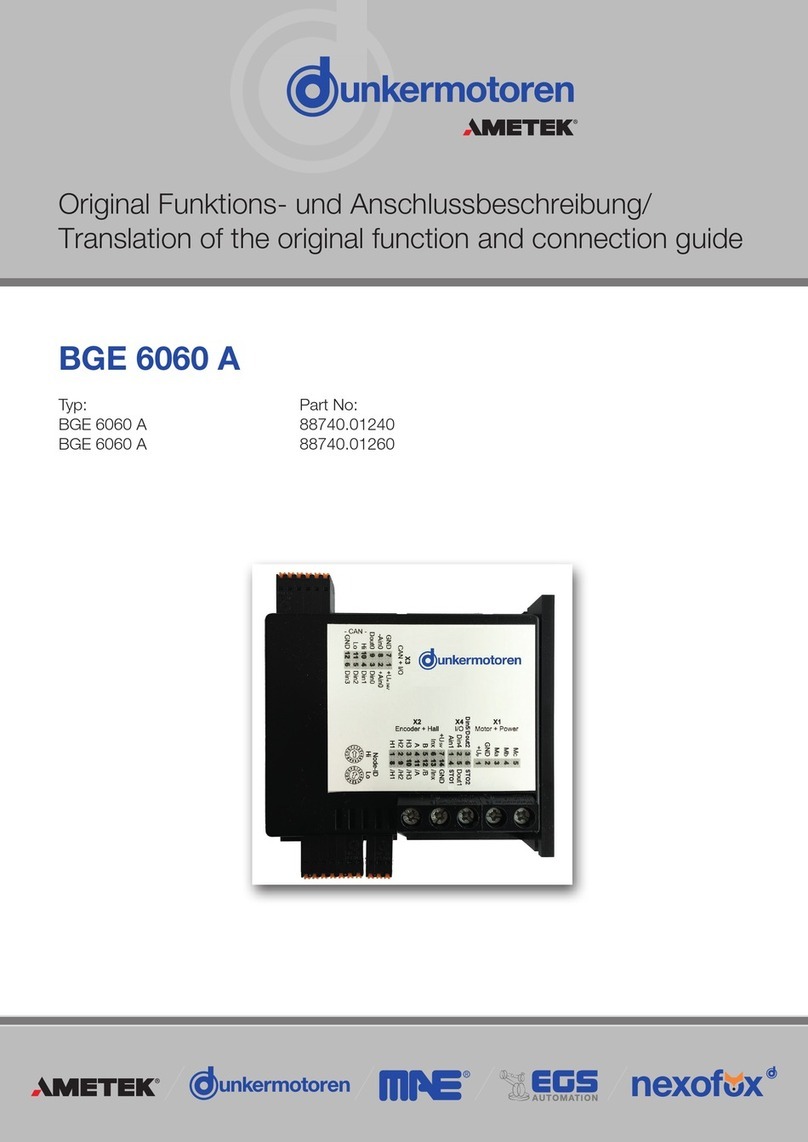
Ametek
Ametek dunkenmotoren BGE 6060 A Translation of the original function and connection guide
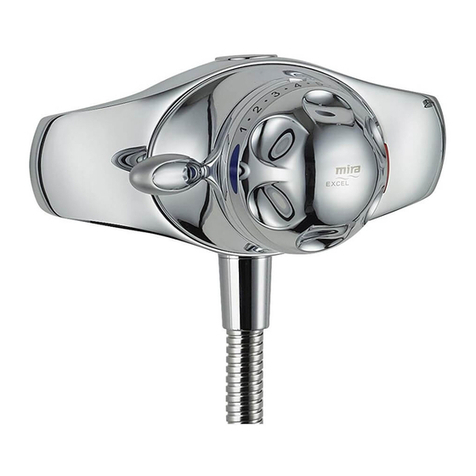
Mira
Mira Excel Installation & user guide