MAK M20 User manual

Total Index
Book A, B and C
A0.01
-
en / 31.10.2001 AA020014 1/2
Ĺ
Engine operating instructions A0
Total Index Book A, B and C A0.01
Introduction A0.02
Safety instructions A0.03
Technical engine data A1
Governor-data A1.04
Working pressures of auxiliary equipment A1.05
Temperatures of operating media A1.06
Torsional vibration calculation A1.09
Acceptance Test Records A1.10
Operating instructions A3
Table of contents A3.01
Introduction A3.02
Safety instructions A3.03
Instructions for heavy fuel operation A3.04
Initial operation A3.05
Operational supervision A3.06
Removal from operation A3.07
Danger of frost A3.08
Running-in A3.10
Fault tracing A3.11
Emergency operation A3.12
Operating media A4
Table of contents A4.01
Introduction A4.02
Safety instructions A4.03
Regulations and care A4.05
Maintenance A5
Table of contents A5.01
Introduction A5.02
Safety instructions A5.03
Tools A6
Table of contents A6.01

Introduction
A0.02
M20-M601C
en / 27.07.2000 AA000024 1/1
Ĺ
The present operating instr ctions incl de notes and g idelines for proper handling of the engine
plant. It is matched with the eq ipment condition and the type of f el sold.
Since the type of f el sed considerably infl ences the service life of the components, the Caterpil-
lar / MaK after-sales service has to be cons lted when it is req ired to change from destillate f el
operation to heavy f el oil operation, in order to ens re an expert retrofit of the engine plant and to
exchange the necessary doc mentation. When changing over from heavy f el oil operation to
destillate operation, the Caterpillar / MaK after-sales service sho ld also be cons lted for a longer
period of time so that a doc mentation with extended maintenance intervals can be made available.
With regard to operation and maintenance of the engine incl ding the necessary work to be carried
o t, the operating instr ctions are s bdivided into the following chapters:
A1 Technical engine data
A3 Operating instructions
A4 Fuels
A5 Maintenance
A6 Tools
With the respective information contained in the individ al chapters, the technical personnel is able
to maintain the engine in s ch a manner that regarding its o tp t, reliability, economy and service
life optim m operating res lts can be achieved.
If yo need f rther information or if yo have any other q estions, we kindly ask yo to contact o r
department service technology.
The operating instr ctions do not release the personnel in charge of this engine plant from their
d ty to take care. The recognized r les of technology are to be observed, taking into acco nt
overriding reg lations, observance of the general safety meas res and locally applicable accident
prevention reg lations. Data or explanations ass med to be the basic knowledge of trained techni-
cal and engine room personnel, are not contained.
Caterpillar / MaK is not responsible for damage ca sed by improper operation and maintenance.
These operating instr ctions are only intended for o r c stomers. All rights reserved for this doc -
ment. All technical data contained in these operating instr ctions m st neither be reprod ced, distri-
b ted nor tilized for competitive p rposes or disclosed to third parties witho t o r express approval.
Postal address: Caterpillar Motoren GmbH & Co. KG, P.O. Box 9009, D-24157 Kiel
Telephone: +49(0)431- 3995-01 (chief operator)
Telefax: +49(0)431-3995-2010(after-sales service only)
http://www.mak-global.com

Safety instructions
A0.03
M20-M601C
en / 19.02.1996 AA000370 1/1
Ĺ
Personnel entrusted with work on the engine/plant must have read the
operating instructions and in particular the pages on safety instructions
which precede the chapters before beginning work. In order to eliminate
danger which may constitute a risk of life and limb of the user or of third
parties, all safety regulations which are marked with the ĭĭ
ĭĭ
symbol have
to be observed in all cases.
Technical instructions and/or operations to be strictly observed are
marked in the documents with attention. They warn of possible damage
to the machinery or to other material property.
Note refers to special information on appropriate use and work to be
carried ou
California / USA
Proposition 65 Warning
Diesel engine exhaust and some of its constituents are known to the
state of California to cause cancer, birth defects, and other reproductive
harm.

Working pressures of auxiliary equipment
A1.05
M20
en / 28.03.2000 TD000033 1/1
Ĺ
Lubricating oil
- at the last main bearing 4,0 - 4,5 bar
at rated engine speed
Cooling water
- min. feed head at p mp inlet 4 m. water ga ge 2,5 - 5,0 bar
Fuel at injection pump inlet
- Distillate f el 3,0 - 5,0 bar
- Heavy f el 4,0 - 5,0 bar
Injection nozzle opening pressure
- take the applicable fig res from the acceptance test records (
A1.10
)
Control air
7,5 bar
Starting air
7,5 bar

Temperatures of operating media
A1.06
M20
en / 13.07.1999 TD000036 1/1
Ĺ
Lubricating oil
- engine inlet 60 - 65 °C
- temperat re rise at rated o tp t 10 - 14 °C
Cooling water
- engine o tlet 65 - 80 °C
- temperat re rise at rated o tp t 7 - 10 °C
Charge air
see also
A3.06.05.nn
- engine inlet 45 - 60 °C
Distillate fuel
40 - 50 °C *1
Fuel before injection pumps
(see diagram) *1
Permissible injection viscosity must be set on the viscothermic device to enable a kinematic viscosity of 10 - 12
mm
2
/s (cSt) to be reached before the injection pumps, corresponding to a dynamic viscosity of 9 - 11 mPas (di-
stillate fuel below 10 mm
2
/s or 9 m Pas).
The heavy fuel specifications defined by
Caterpillar / MaK
(e.g. RHM 35 (~ IF 380) give the heavy fuel tempe-
rature before engine starting.
*1However, the maximum temperature at injection pumps must not exceed 155 °C!

Table of contents
A3.01
-
en / 31.10.2001 AA020023 1/3
Ĺ
Operating instructions A3
Table of contents A3.01
Introd ction A3.02
Safety instr ctions A3.03
Instr ctions for heavy f el operation A3.04
Instr ctions for heavy f el operation
F el system A3.04.07.00
Instr ctions for heavy f el Operation
Care and s pervision / Engine f el A3.04.07.01
Instr ctions for heavy f el operation
L bricating oil system A3.04.08.00
Instr ctions for heavy f el Operation
Care and s pervision / L bricating Oil A3.04.08.01
Initial operation
Engine A3.05.00
Initial operation
F el system A3.05.07.00
Initial operation
L bricating oil system A3.05.08.00
Initial operation
Cooling water system A3.05.09.00
Initial operation
Starting air system A3.05.11.00
Initial operation
General performance testing A3.05.15.00
Commissioning
P tting into operation/starting A3.05.18.00
Initial operation
P tting into service/starting A3.05.18.02
Initial operation
P tting into service/loading A3.05.18.03
Initial operation
P tting into service/loading A3.05.18.04
Operational s pervision
Engine A3.06.00
Monitoring
Intake air temperat re A3.06.05.00
Operational s pervision
Exha st system/s percharging A3.06.06.00
Monitoring of operation
Exha st system/Firing press re A3.06.06.01
Operational s pervision
Exha st system/s percharging A3.06.06.02
Operational s pervison

Table of contents
A3.01
-
en / 31.10.2001 AA020023 2/3
Ĺ
Exha st system/s percharging A3.06.06.03
Operational s pervision
F el system A3.06.07.00
Operational s pervision
Changing the type of f el A3.06.07.01
Operational s pervision
L bricating oil system A3.06.08.00
Operational s pervision
Cooling water system A3.06.09.00
Operational s pervision
Partial load operation A3.06.18.00
Removal from operation
Engine A3.07.00
Removal from operation
Placing o t of service/stopping A3.07.18.01
Decommissioning
Decommissioning/Stopping A3.07.18.02
Danger of frost
Engine A3.08.00
Danger of frost
Antifreeze protection A3.08.01.00
Preservation
Engine A3.09.00.00
Preservation
Short term preservation A3.09.01.00
Preservation
Long term preservation A3.09.02.00
Preservation
Depreservation A3.09.03.00
R nning-in
Engine A3.10.00
R nning-in
Engine A3.10.01.00
Fa lt tracing
Engine A3.11.00
Fa lt tracing
Introd ction A3.11.18.00
Fa lt tracing
Remedial meas res A3.11.18.02
Emergency operation
Engine A3.12.00
Emergency operation
With a defective t rbocharger A3.12.01.00
Emergency operation
With a defective t rbocharger A3.12.01.01

Introduction A3.02
M20-M601C
en / 12.02.1996 AA000295 1/2
Ĺ
Contained herein are certain points regarding the initial operation, the ass rance of a reliable
service as well for overcoming the need for long periods of non operation, th s ens ring a rapid
ret rn to service.
For any working data mentioned in this book, please bear the following in mind:
It is possible for the engine power to be limited before reaching its f ll performance capacity,
to meet special req irements. Thereby in compliance with DIN ISO 3046 we differentiate
between:
• Maximum continuous power
this is the maxim m permissible o tp t for this type of engine.
• Rated power
this is indicated on the acceptance test records for yo r engine.
• Full stop power
this is the power o tp t limited by a restrictor on the injection p mp racks.
Unless otherwise indicated, o r information always refers to the maxim m contin o s power and if
this is nknown to the operator he sho ld make inq iries to the man fact rer.
The power is limited by a restrictor at the f el injection p mp control shaft d ring the test bed r n
and normally at rated power and speed. Any other arrangements can be seen from the acceptance
test records (A1.10).
Attention:
When using heavier fuel grades independent on the density of the fuel, the rated power
will be reached at a fuel rack position that is accordingly lower. As such, the limiting
position must also be accordingly lower. This is especially the case after a change of fuel
from that of an essentially higher density as it is the case when changing from distilled
fuel to heavy oil. The alteration of the fuel rack position may only be carried out by
personnel who have received permission to do this from Caterpillar / MaK !

Introduction A3.02
M20-M601C
en / 12.02.1996 AA000295 2/2
Ĺ
The operators have to work with the necessary care and to keep to the safety notes. The existing
protection and safety devices m st not be removed nor changed, and any damage detected m st be
immediately reported. Safety devices may only be changed in special cases by personnel who have
received permission to do this from MaK.
The preparations for the first start p are made by the MaK service engineer, who will explain the
plant to the engine room staff in detail. Detail q estions are to be settled on site from the operating
instr ctions and explanations sho ld be noted down in the instr ctions. After commissioning the
engine, all important data and work sho ld be recorded in either the engine log book or in o r ship
management system DIMOS.
Please observe the data and recommendations in yo r operating instr ctions together with the
maintenance and servicing meas res recommended by s. They are the basis for a long sef l life
with a constant degree of economy for yo r engine installation.
Attention:
After every cleaning of the engine with fat solvent detergents all metallic blank patts must
be protected again slightly with an oil film!
Special care must be taken to ensure that all bearing points affected by the cleaning are
thoroughly lubricated afterwards!

Safety instructions A3.03
M20-M601C
en / 15.01.1998 AA000338 1/2
Ĺ
Safety instructions
The Caterpillar / MaK engine has been built in accordance with state-of-the-art standards and the
recognized safety regulations.
Nevertheless, in the case of improper operation
• physical or life-threatening danger to the operator or others
• damage to the unit and other valuable objects
• a reduction in the economy of the unit.
The service personnel must possess the corresponding qualification and authorization (qualifica-
tion certificate) for the engine system in operation.
Before the initial operation of special systems, the service personnel must be fully aquainted with
the characteristic features therein.
An introduction to the system specifications, requirements/characteristics can be carried out in the
training center of Caterpillar / MaK. For the operators of the system this is a necessary requirement
to the order.
General safety instructions
During all operational and service measures the relevant pointers in the prevention of accident
regulations of the particular employee's liability insurance association or equivalent institution, are
to be observed, for example:
• Observe all fire-warning and fire-fighting procedures!
• Operating elements of the emergency-off device are to be free acessible!
Further valid is the following:
• Unauthorized modifications and changes to the system can impair the safety! Alteration may
only be carried out by personnel with received permission to do so from Caterpillar / MaK!
• Avoid any work procedures which may affect the safety!
• Only operate the engine if all protection facilities, e.g. detachable protection facilities, linings,
heat insulation, extractors are available and functional!
• Check the engine/plant at least once per shift for damage and defects which can be
recognized from the outside! If any changes occur (including changes of the operational
behaviour), this must be reported immediately to the competent person! Stop the engine/
plant immediately and secure it if necessary against restart! Damages and faults should be
rectified immediately!
• Stop and secure the engine/plant immediately against restart in the case of functional
disorders! Malfunctions should be rectified immediately!

Safety instructions A3.03
M20-M601C
en / 15.01.1998 AA000338 2/2
Ĺ
Remote control
The engine remote control of seegoing ships and inland ships will be constructed according to the
safety regulations of the classification society.
Inland ships must also observe the relevant customary safety recommendations!
Safety measures for local control of the engine
Before the start:
• Check the system for defects, check lamps!
- defective instruments, operating controls, control lights
• Clean up spillages of fuel and oil!
• Protection guards must be in operation position and operative!
• Hearing protection must be worn!
• Before putting the engine into operation, ensure that there is no danger to persons by the
starting engine/plant!
• Move operational controls to neutral position and/or minimum position (r.p.m. potentiome-
ter with locking facility)!
Starting:
• Check the instrument readings!
• Do not switch off extractors and ventilators while the engine is running!
Attention:
In no case the starting air shut-off valve must be closed during engine
operation.
California / USA
Proposition 65 Warning
• Diesel engine exhaust and some of its constituents are known to the state of California to
cause cancer, birth defects, and other reproductive harm.

Instructions for heavy fuel operation A3.04
M20-M601C
en / 10.12.1997 AA000291 1/1
Ĺ
The instr ctions stated below are to be stringently observed, as the readiness for service and
operational reliability of the engine system d ring high extremes of se, req ires perfect f el and
depends pon optimal concentrations and monitoring s pervision.
• Fuel system A3.04.07.nn
• Lubricating oil system A3.04.08.nn

Instructions for heavy fuel operation
F el system
A3.04.07.00
M20-M601C
en / 10.12.1997 BA000004 1/1
Ĺ
Fuel system
The evermore intensive tilization of cr de oils by modern processing is the reason the portion of
the resid al oils (heavy f el) has become smaller and the portion of the in the resid al oils
remaining contaminating matter has, however, increased.
The disting ishing properties of s ch resid al oils are their high viscosity and their density as well
as the increased portion of chemical compo nds with s lph r, vanadi m, sodi m and cat fines etc.
The remainig contaminating matters infl ence the operation of the “heavy f el engine”! Optim m
treatment of the f el and an intensive s pervision of the plant are therefore a precondition for
economical operation of “heavy f el engines”.
For information abo t heavy fuel quality and for instr ctions and maintenace see section
A4.05.07.nn.
Table of contents
Other MAK Engine manuals
Popular Engine manuals by other brands

Rotax
Rotax 915 iSc 3 A installation manual
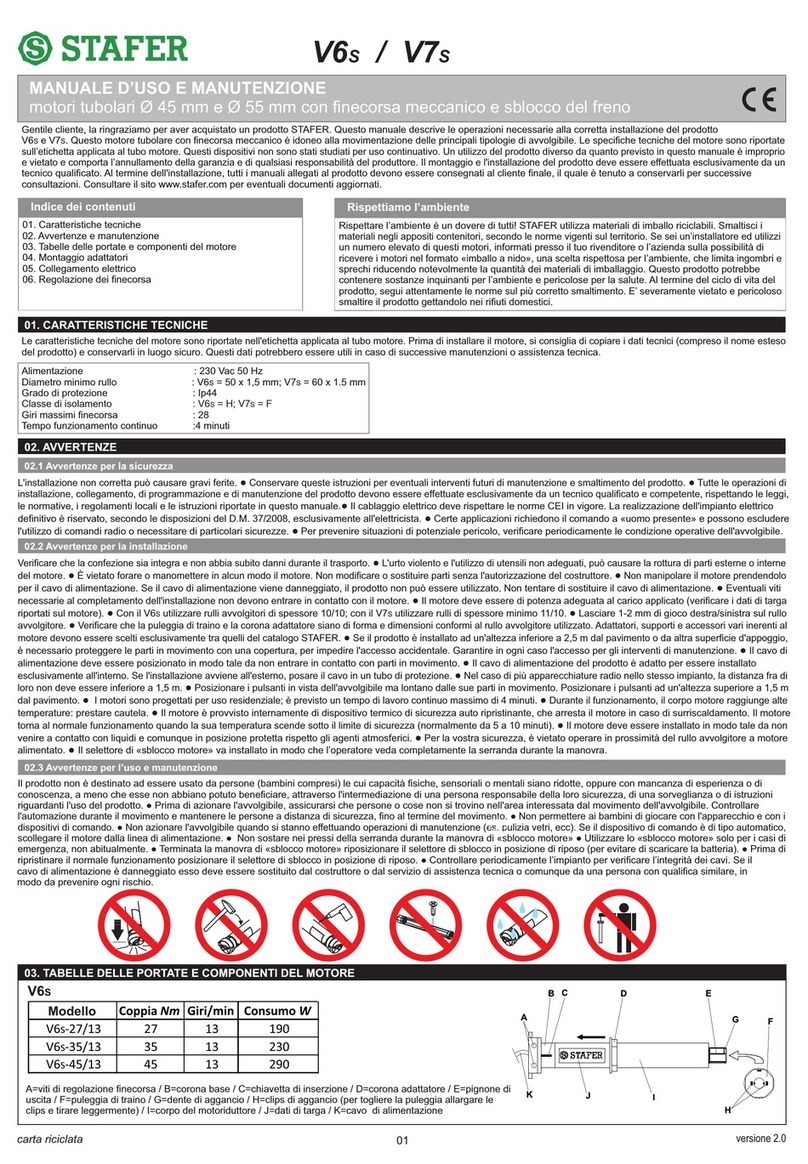
Stafer
Stafer V6S-27/13 user manual
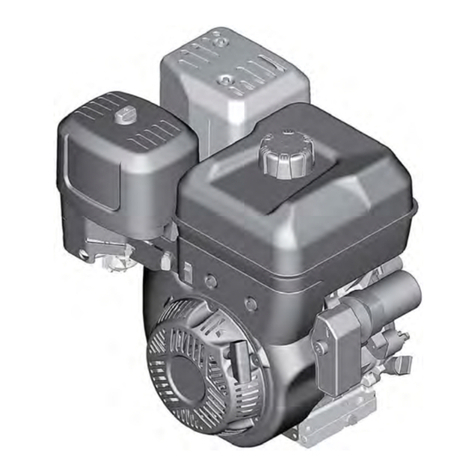
Briggs & Stratton
Briggs & Stratton 190000 Series Operator's manual
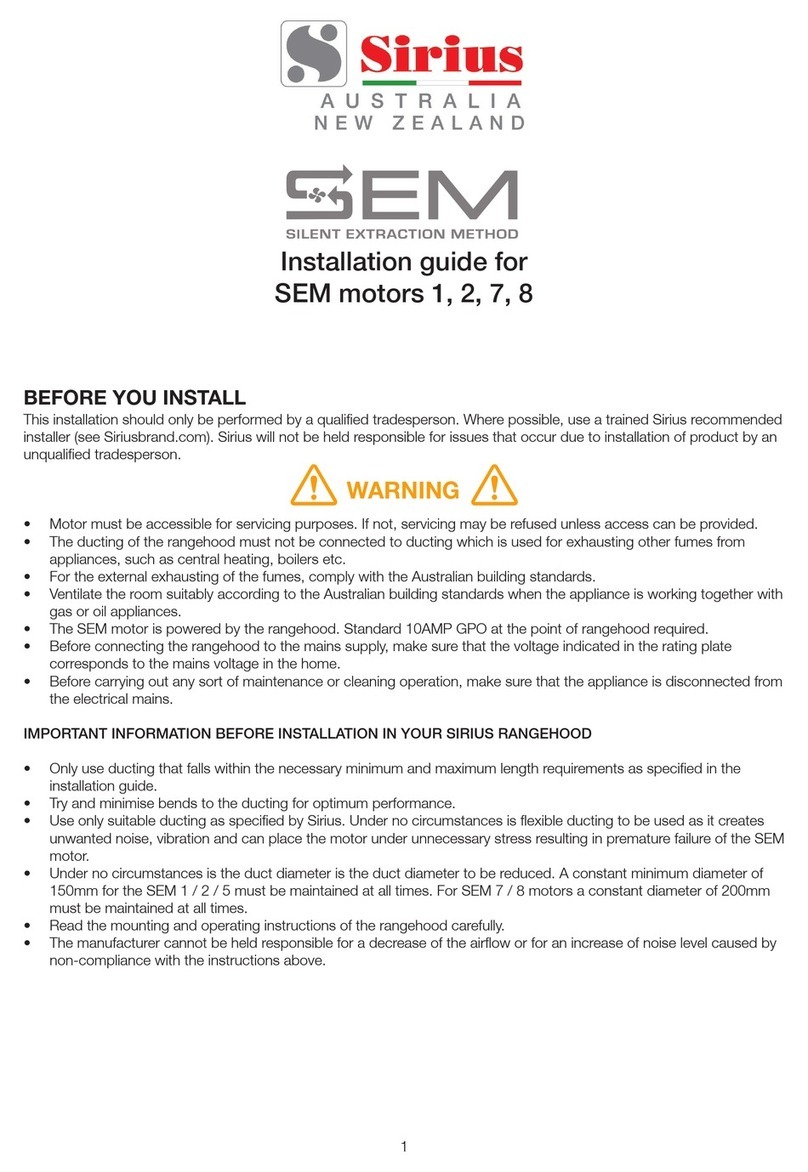
Sirius Satellite Radio
Sirius Satellite Radio SEM1 Installation guides
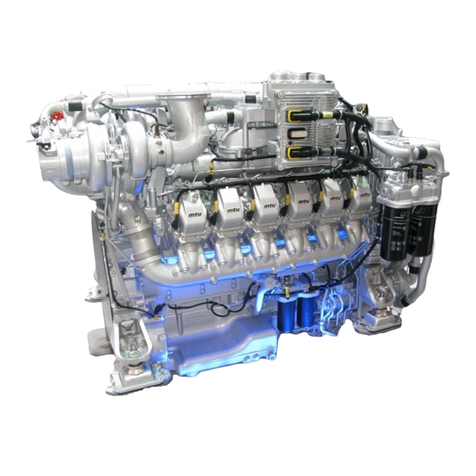
MTU
MTU 12V 2000 C66 operating instructions

Continental Refrigerator
Continental Refrigerator LTSIO-520-AE Overhaul manual