Makita GA7050 Manual

Model No.
Description
CONCEPT AND MAIN APPLICATIONS
P 1/ 8
Standard equipment
Optional accessories
Note: The standard equipment for the tool shown above may vary by country.
GA7050/ GA9050
Models GA7050 and GA9050 are developed as easy-to-control
2000W class angle grinder, featuring compact and lightweight
tool design achieved by employing:
Newly developed, compact and lightweight motor (Type S-82)
Down-sized gear housing and main handle
Especially in compactness, the products are unrivalled;
the overall length of 432 mm (17'') is the shortest among the 2000W
class models available in the global market as of February 2010.
Wheel size is:
180mm (7'') for Model GA7050
230mm (9'') for Model GA9050
Lock nut wrench 35 ......... 1
Side grip 36 ...................... 1
Dimensions: mm (")
Width (W)
Height (H)
Length (L)
Model No. GA7050 GA9050
432 (17)
200 (7-7/8) 250 (9-7/8)
132 (5-3/16)
Vibration absorbing side grip
Toolless quick adjustable wheel cover
Toolless lock nut
Dust cover attachment
GA7050: Accessories for 180mm angle grinder
GA9050: Accessories for 230mm angle grinder
Net weight*3 : kg (lbs)
Power supply cord: m (ft)
Continuous Rating (W)
Cycle (Hz) Input Output Max. Output (W)
50/ 60
50/ 60
50/ 60
50/ 60
50/ 60
2,000
---
2,000
2,000
2,000
900
900
1,100
1,100
1,100
2,900
2,900
3,600
3,600
3,600
GA7050 GA9050
6,6008,500
No
No
Yes
180 (7)
22.23 (7/8)
230 (9)
2.0 (6.6)*1 / 2.5 (8.2)*2
4.5 (9.9) 4.7 (10.4)
Specification
Voltage (V)
110
120
220
230
240
19
15
9.6
9.2
8.8
Current (A)
Specification
Soft start feature
Anti-restart function
Double insulation
No load speed: min-1= rpm.
Wheel size: mm (") Diameter
Model No.
Hole diameter
Angle Grinders 180mm (7'')/ 230mm (9'')
PRODUCT
TECHNICAL INFORMATION
*1 for Brazil, Australia
*2 for all countries except the two listed above
*3 Weight according to EPTA-Procedure 01/2003, with Side grip, Wheel cover, Inner flange, Lock nut
L
H
W

P 2/ 8
Repair
[1] NECESSARY REPAIRING TOOLS
[2] LUBRICATIONS
[3] DISASSEMBLY/ASSEMBLY
[3]-1. Armature, Spiral bevel gear (small), Ball bearing 6201DDW, ball Bearing 6000DDW
Fig. 1
Item No.
Apply Makita grease SG.No.0 to the following portions designated with the black triangle to protect parts
and product from unusual abrasion.
Description Portion to lubricate
Code No. Description Use for
1R005 Retaining ring pliers RT-2N Removing Retaining ring (INT) R-32 from Gear housing
1R004 Retaining ring pliers ST-2 Removing Ring spring 13 from Spindle
1R252 Round bar for arbor 30-100
1R258 V-block Assembling Felt ring 16 to Gear housing
Assembling large Spiral bevel gear to Spindle
1R269 Bearing extractor Assembling / Disassembling Ball bearings
1R165 Ring spring setting tool B
4
4Gear housing complete Apply approx. 35g grease to Gear room.
Model No. No load speed: min-1
GA7050 8,500
6,600
Spiral bevel gear 10A Spiral bevel gear 38
Spiral bevel gear 49Spiral bevel gear 10B
GA9050
Small spiral bevel gear
(Gear on Armature shaft)
Large spiral bevel gear
(Gear on Spindle)
Diameter: 23.5mm
Diameter: 18.5mm
Number of teeth: 38
Number of teeth: 49
Each model has different gears as illustrated below, and they are not interchangeable.
23.5mm
18.5mm
CAUTION: Repair the machine in accordance with “Instruction manual” or “Safety instructions”.

P 3/ 8
Repair
[3] DISASSEMBLY/ASSEMBLY
[3]-1. Armature, Spiral bevel gear (small), Ball bearing 6201DDW, Ball bearing 6000DDW
DISASSEMBLING
Fig. 2
Separate Gear housing complete
from Motor housing complete
together with Armature assembly.
Separate Bearing box from Gear
housing complete by removing
four M5x16 Hex socket head bolts.
Carbon brush
Armature assembly
Bearing box
Gear housing complete
Motor housing
complete
5x35 Tapping screw (4pcs.)
Brush holder cap
Locking M7 Hex nut with wrench,
turn Armature clockwise by hand.
Wrench for locking M7 Hex nut
M7
Hex nut
Armature can be pulled off.
Do not lose M7 Hex nut.
Small spiral
bevel gear
M7 Hex nut
Armature
Fig. 3
Note
If the work is very difficult due to the seizing
of Small spiral bevel gear, spray lubricant
between Armature shaft and Small spiral
bevel gear. And then turn and pull Armature
while holding Small spiral bevel gear with
pliers and a cloth.
Remove Retaining ring (INT)
R-32 with 1R005 from Gear
housing complete.
Fig. 4 Fig. 5
Retaining
ring (INT)
R-32
Assemble Armature assembly and Small spiral bevel gear. Tighten
M7 Hex nut provisionally by turning clockwise. (Refer to Fig. 3.)
Ball bearing 6201DDW can be
removed together with Armature
by tapping the end of Gear housing
complete with a plastic hammer.
Felt ring 16 can be removed
together with Armature.
Remove Carbon brushes. And then,
remove four 5x35 Tapping screws.
Ball bearing 6201DDW
M7 Hex nut Small spiral
bevel gear
(1) Disassemble Armature assembly and Small spiral bevel gear as illustrated in Figs. 2 and 3.
(2) Disassemble Ball bearing 6201DDW as illustrated in Figs. 4 and 5.
M5x16 Hex socket
head bolt (4pcs.)
(3) Disassemble Armature section as illustrated in Fig. 6.
Remove M7 Hex nut and Small spiral bevel gear again. Ball bearing 6201DDW can be removed by hand.
Remove Rubber ring 26 from Ball bearing 6000DDW by hand.
Insert the jaws of 1R269 between Ball bearing 6000DDW and Insulation washer, and remove Ball bearing 6000DDW.
Fig. 6
Ball bearing 6000DDW
Ball bearing
6201DDW
Note: Do not mistake the directions of
Insulation washer and Rubber ring 26
when setting them in place.
Fan 80Small spiral bevel gear
Felt ring 16
M7 Hex nut Ball bearing 6201DDW Rubber ring 26
Insulation washer

P 4/ 8
Repair
[3] DISASSEMBLY/ASSEMBLY
[3]-1. Armature, Spiral bevel gear (small), Ball bearing 6201DDW, Ball bearing 6000DDW (cont.)
ASSEMBLING
Assemble Gear housing section by setting Felt ring 16, Ball bearing 6201DDW and Retaining ring (INT) R-32 in place of
Gear housing complete in accordance with the following steps.
(1) Set Felt ring 16 in place as illustrated in Fig. 7 when disassembling Ball bearing 6201DDW.
Fig. 7
Felt ring 16
1R258 (1set/2pcs.)
Felt top
portion
Steel cup
portion
1R252
Cross-section of the bottom
of the bearing room
1R252
Felt ring 16
Flat washer
as a jig
O ring 31 in Gear housing
complete
Note: If O ring 31 has damage,
replacing it is required.
0.5mm
Put a Flat washer (illustrated above) temporarily on Felt ring 16.
Then press down the Flat washer with arbor press and 1R252
carefully to move the Flat washer to only 0.5mm downwards.
Remove the Flat washer after setting Felt ring 16 in place.
Bottom step in Gear housing complete
26mm in outer diameter
0.5mm in
thickness
Flat washer as a jig
Hold Gear housing complete with two V-blocks,
and pressfit Felt ring 16 into the hole of Gear
housing complete so that the felt top portion and
the bottom step of Gear housing complete is in line.
Fig. 8
Armature with Ball
bearing 6201DDW Armature
(2) Assemble Ball bearing 6201DDW to Armature temporarily. After setting Ball bearing 6201DDW in place of Gear
housing complete, pull off Armature. Then, fit Retaining ring (INT) R-32 into the groove of Gear housing
complete to secure Ball bearing 6201DDW. (Fig. 8)
(3) Assemble Armature and small Spiral bevel gear to Gear housing complete by reversing the step shown in Fig. 3.
(4) Assemble Gear housing complete to Motor housing, And assemble Bearing box section to Gear housing complete.
Retaining
ring R-32
1R005
Ball bearing
6201DDW
Groove for
Retaining
ring (INT)
R-32

P 5/ 8
Repair
[3] DISASSEMBLY/ASSEMBLY
[3]-2. Large spiral bevel gear, Ball bearing 608ZZ, Ball bearing 6202DDW
DISASSEMBLING
1R269
Remove Bearing box from
Gear housing complete.
Remove Ball bearing 608ZZ with 1R269.
Remove Spindle complete by pressing with Arbor press.
Ball bearing 6202DDW in Bearing box has a damage in this step.
Do not reuse Ball bearing 6202DDW after removal of Spindle complete.
Ball bearing
608ZZ
M5x16 Hex socket
head bolt (4pcs.)
Ring spring 13
1R004
Spindle complete
Bearing box
Turn table of Arbor press Turn table of Arbor Press
Slotted screwdriver
Enlarging the clearance of Ring spring 13
with 1R004, lift up the opposite side
with slotted screwdriver.
Ring spring 13 can be removed.
Fig. 9
Fig. 10R
Correct setting The following wrong settings causes deforming.
Fig. 10F
Fig. 11
Large spiral bevel gear
Bearing box
Remove Bearing retainer by
unscrewing three M4x16 Pan
head screws.
(1) Large spiral bevel gear can be disassembled as illustrated in Figs. 9, 10R and 11.
Ball bearing
6202DDW
The brim portion of Bearing
box is received with Turn table
of arbor press.
Labyrinth ring portion of Spindle
complete is received with
Turn table of arbor press.
Receive the cylindrical portion of Bearing
box with Turn table of arbor press.
Cylindrical portion
Bearing
retainer
M4x16 Pan head
screw (3pcs.)

1R165
Large spiral bevel gear
P 6/ 8
Repair
[3] DISASSEMBLY/ASSEMBLY
[3]-2. Large spiral bevel gear, Ball bearing 608ZZ, Ball bearing 6202DDW (cont.)
DISASSEMBLING
ASSEMBLING
(2) Ball bearing 6202DDW can be disassembled as illustrated in Fig. 12A or Fig. 12B.
Reverse the disassembling step shown in Fig. 11, 10R and 9.
Note: 1) Do not deform the labyrinth ring of Spindle complete when pressfitting Spindle complete to Ball bearing
6202DDW. (Fig. 13)
2) Putting Large spiral bevel gear on 1R165, press Spindle into arbor hole of Large spiral bevel gear with Arbor
press. (Fig. 14)
Fig. 12A Fig. 12B
Fig. 13
If it is difficult to remove as illustrated
in Fig. 13A, remove Ball bearing
6202DDW with the appropriate
diameter round bar and Arbor press.
Remove Ball bearing 6202DDW by striking Bearing box
against Work table.
Ball bearing
6202DDW
Bearing box
Round bar
Ball bearing 6202DDW
Labyrinth ring
of Spindle complete
Fig.14

P 7/ 8
Repair
[3] DISASSEMBLY/ASSEMBLY
[3]-3. Shaft lock mechanism
DISASSEMBLING
Fig. 15
Fig. 17 Fig. 18
ASSEMBLING
(1) Remove Gear housing complete from Motor housing.
Remove Bearing box from Gear housing complete as illustrated in Fig. 2.
(2) Remove Armature from Gear housing complete as illustrated in Fig. 3.
(3) Shaft lock mechanism can be disassembled as illustrated in Figs. 15 and 16.
Put Gear housing complete on
Turn table of arbor press as
illustrated right.
Insert 1R268 from the small hole
on Pin cap, and tap 1R268 with
Plastic hammer to push out
Shoulder pin 11 through the
U-groove of the turn table.
Release 1R268 from Pin cap carefully so that
Pin cap would not be slung by Compression
spring 12.
Shoulder pin 11
U-groove of turn table
of arbor press
Pin cap
Note: Do not reuse Pin cap.
Removal of Shoulder pin 11 damages
the inside surface of Pin cap, producing
plastic dust.
Pin cap
Compression
spring 12
Pin cap
Compression
spring 12
Fig. 16
(1) Be sure to use a new Pin cap for replacement and to remove all the plastic dust on Shoulder pin 11. (Fig. 17)
(2) Assemble the parts for Shaft lock mechanism as illustrated in Fig. 18.
Plastic dust
O ring 7
Shoulder pin 11
Shoulder pin 11
Make sure that O ring 7 is
mounted to Shoulder pin 11
illustrated below.
Assemble Compression spring 12
and Pin cap by pressing them to
Shoulder pin 11.
Insert Shoulder pin 11
through the hole of Gear
housing complete.
1R268

Circuit diagram
Wiring diagram
P 8/ 8
Fig. D-1
Noise suppressor (if used)
Brown lead wire is used
for some countries.
Fig. D-2
Fig. D-3
Blue lead wire is used
for some countries.
Pass Field lead wire (white) through this hook.
White
Color index of lead wires' sheath
Black
Field viewed from
Commutator side
BHB
BHA
Wiring in Motor housing
on Commutator side
Fix Field lead wire (black) with this Lead wire holder.
Motor housing
viewed from
Commutator
installation side
Do not make any
sags of Lead wires
in Motor housing.
Wiring in Handle
complete (L)
Power supply cord
Lead wires of
Power supply cord
Rib
Receptacles have to be connected
to Switch as illustrated.
Pass Field Lead wires (black, white)
through Sponge sheet and fix them
with lead wire holder here.
Sponge sheet
Noise suppressor
(if used)
Put Lead wires of power supply
cord between Switch and Rib.
Other manuals for GA7050
9
This manual suits for next models
1
Table of contents
Other Makita Grinder manuals

Makita
Makita 9566CR User manual

Makita
Makita DGA506Z User manual
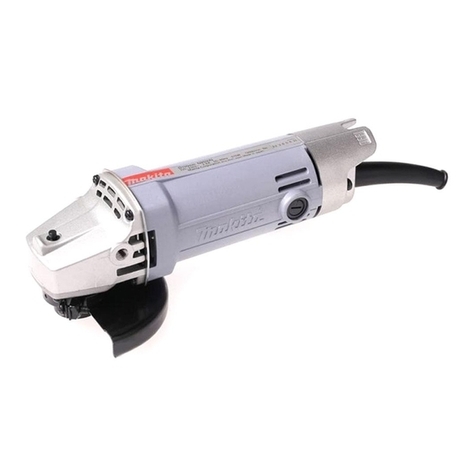
Makita
Makita N9500N User manual

Makita
Makita GA4030 User manual

Makita
Makita 9565CVL User manual

Makita
Makita DGA700 User manual
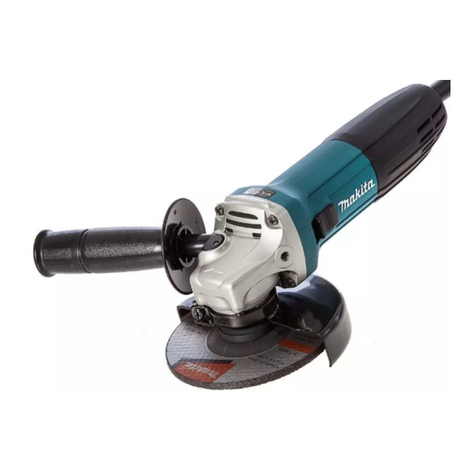
Makita
Makita GA5030RSP1 User manual

Makita
Makita GA003G User manual
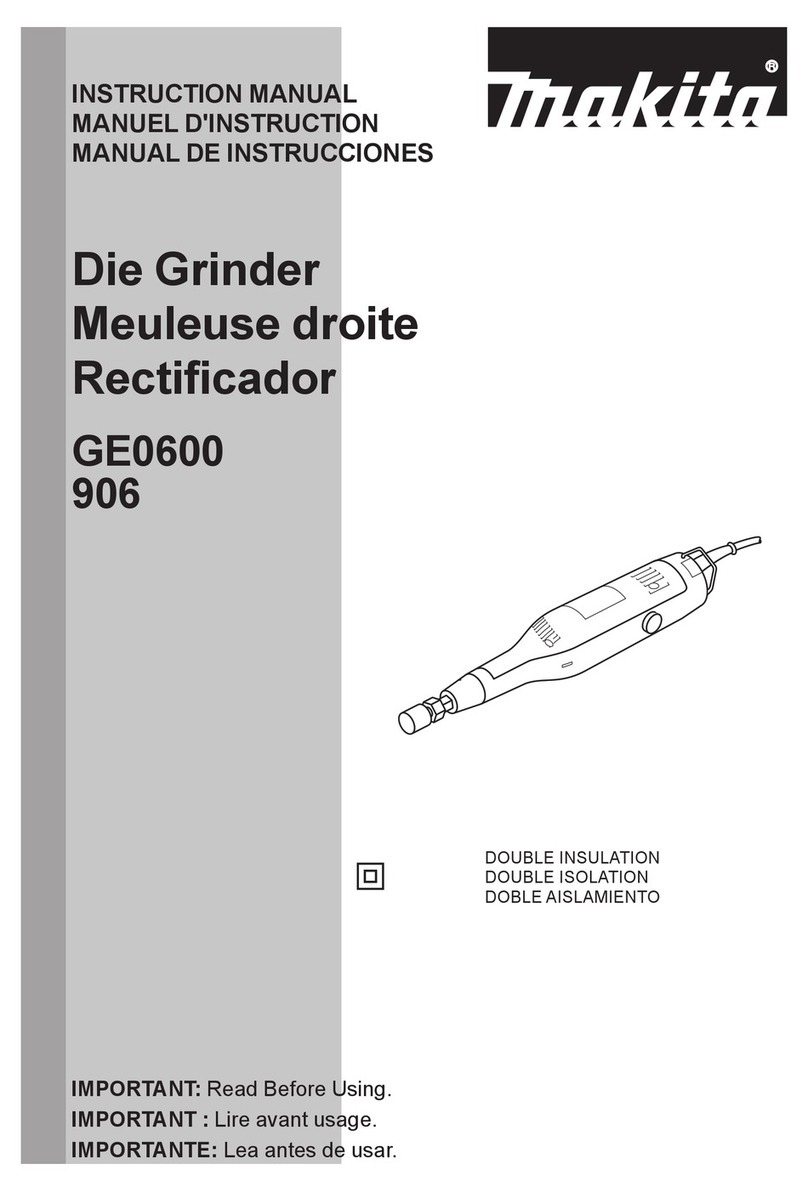
Makita
Makita ge0600 User manual
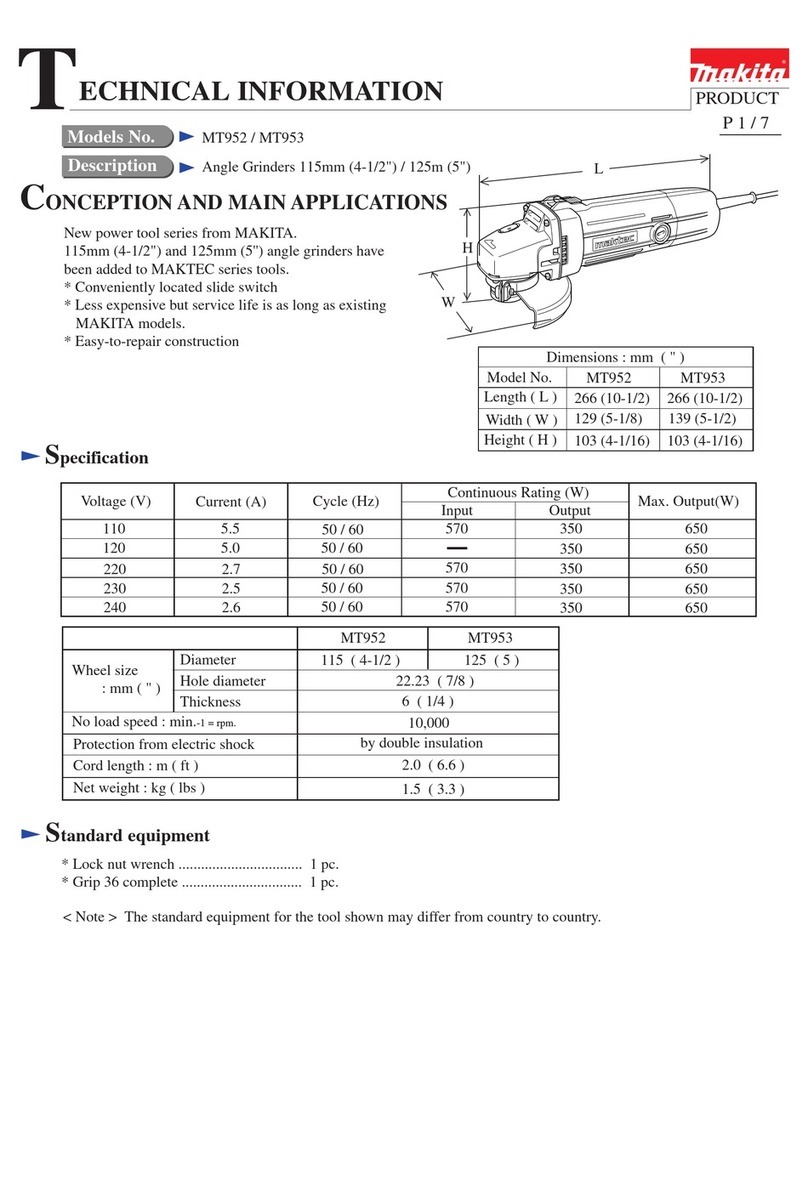
Makita
Makita MT952 Manual

Makita
Makita 9501B User manual

Makita
Makita DGA505RTJ User manual

Makita
Makita 9565CR User manual
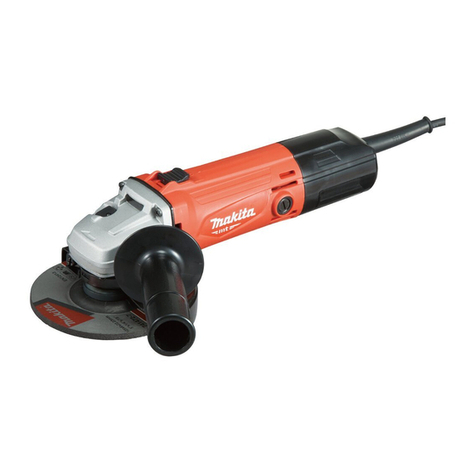
Makita
Makita M9502R User manual

Makita
Makita 9560CV User manual

Makita
Makita 9564P User manual

Makita
Makita 9047L User manual
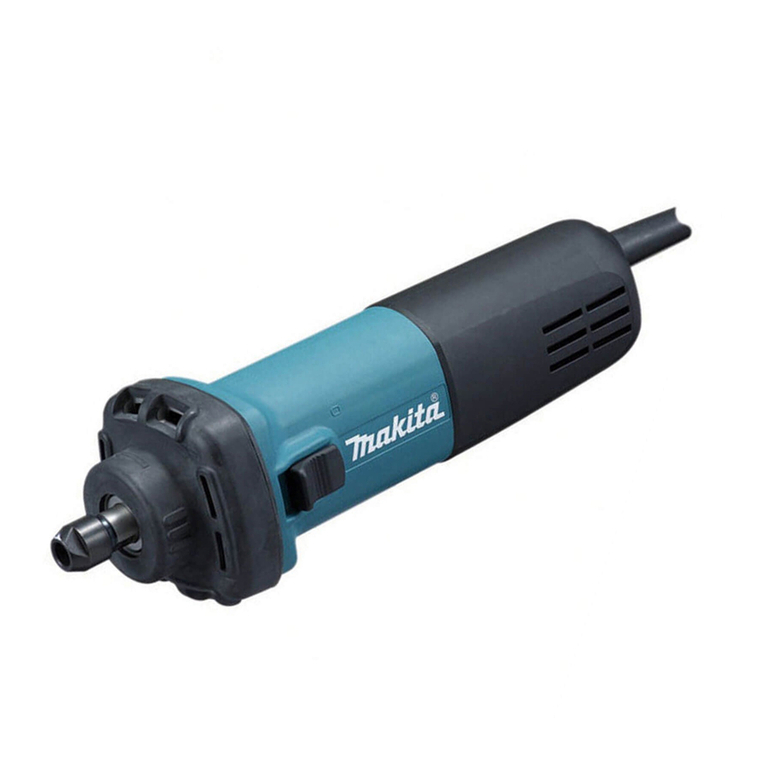
Makita
Makita GD0602 User manual
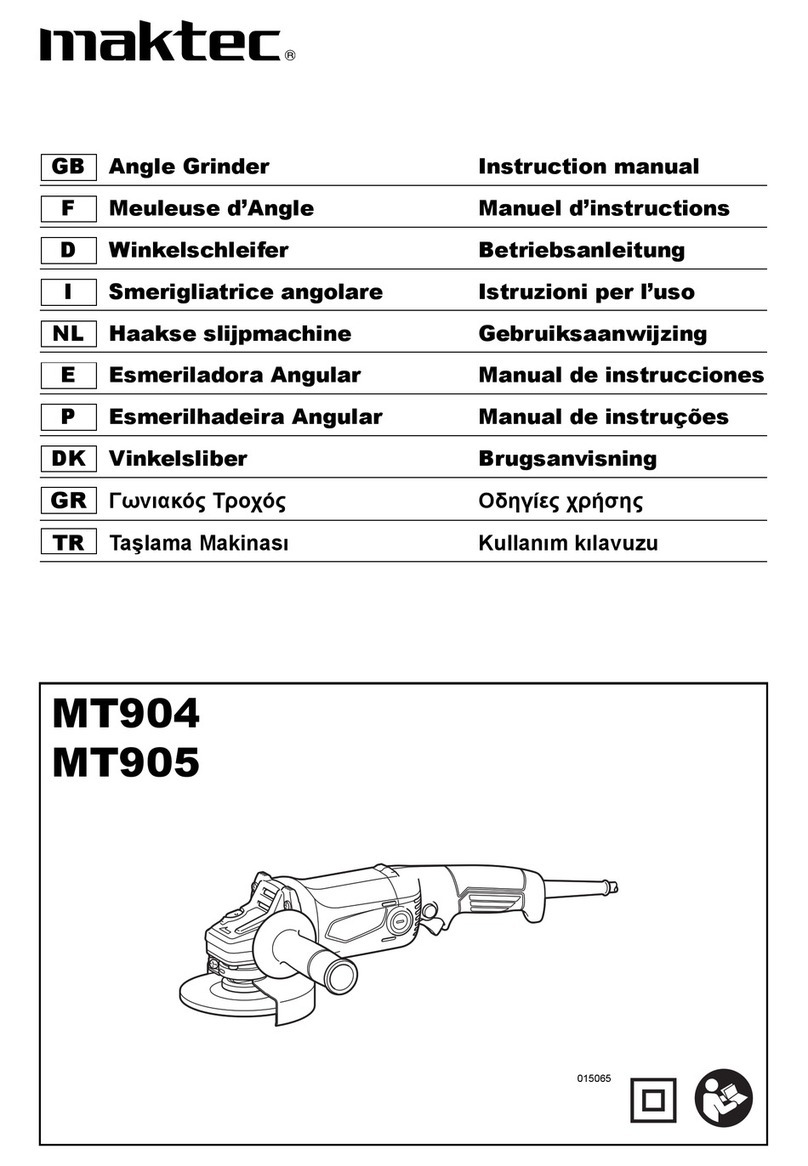
Makita
Makita Maktec MT904 User manual

Makita
Makita GA011G User manual