Masport CROMWELL User manual

1
CROMWELL
Installation &
Operations
Manual
THIS MANUAL CONTAINS IMPORTANT INFORMATION.
PLEASE KEEP IT IN A SAFE PLACE FOR FUTURE REFERENCE.
Manufactured in New Zealand by:
GLEN DIMPLEX NEW ZEALAND LIMITED
P.O. Box 58473, Botany, Manukau - 2163
Ph: 0800 666 2824
Fax: 09 274 8472
Email: sales@glendimplex.co.nz
Web: www.glendimplex.co.nz
1
st
Nov 2017 Part No. 598675 V1.1
*Glen Dimplex New Zealand Ltd reserves the right to change specifications, content of this manual or design of its product without prior notice.

2
CONTENTS
PAGE
1.0 INTRODUCTION 3
1.1 ITEMS SUPPLIED WITH THE FIRE 3
1.2
HANDLING AND TRANSPORT
3
1.3 WARNINGS
4
1.4 CAUTIONS 4
2.0 TECHNICAL SPECIFICATIONS 5
3.0 INSTALLATION OF THE FIRE 6
3.1 UNPACKING 6
3.2 POSITIONING 6
3.3 FLUE REQUIREMENTS 6
3.4 FLOOR PROTECTOR REQUIREMENTS 7
3.5 SEISMIC RESTRAINT 7
3.6 REDUCING CLEARANCES 8
4.0 PERMITTED FUELS 9
4.1 TESTING YOUR WOOD MOISTURE 9
4.2 RECOMMENDED FUEL LOG SIZES 9
5.0 OPERATIONAL SEQUENCE
10
5.1 BEFORE FIRST LIGHT-UP 10
5.2 COLD START-UP 10
5.3 STACK & LIGHT KINDLING 10
5.4 INTERMEDIATE LOAD 1 10
5.5 INTERMEDIATE LOAD 2 11
5.6 RE-FUELING 11
5.7 SHUT DOWN & RESTART 12
6.0 CLEANING AND MAINTENANCE 12
6.1 PERIODIC CLEANING & CHECK 12
6.2 ANNUAL MAINTENANCE 12
7.0 CROMWELL REPLACEMENT PARTS 16
8
.0
TROUBLESHOOTING: CAUSES & REMEDY
17
9
.0
CROMWELL
WARRANTY
19

3
1.0 Introduction
Congratulations!
You are the owner of a state-of-the-art Ultra Low Emission Burner “Masport
Cromwell” designed and developed by Glen Dimplex New Zealand. Thank you for purchasing a Masport
appliance.
CROMWELL burner is a new generation wood fire, designed to provide you with all the warmth and charm of
a fireplace, at the same time have negligible emissions with dramatically reduced impact on the environment.
Environment Canterbury has approved installation of this burner in all clean air zones that have been banned
for installation of a conventional wood burner. As it bears the Masport brand, it promises to provide you with
economy, safety, and efficiency.
To make the most of your appliance, it is important to install, operate and maintain the burner correctly.
Please read this installation and operations manual carefully before installing or operating your CROMWELL
fire. Please take time to understand the basic principles of this new burner which uses down draft
combustion technique.
Conventional Masport burner has a single firebox and uses triple combustion technique with preheated
combustion air. Injection of preheated air jets in different direction bombards the fire bed and creates a very
hot turbulent flame to burn most of the polluting particles at around 600~700
o
C. Though this is a clean way
of burning, some particulate and valuable heat energy escapes to atmosphere through an exhaust flue pipe.
Cromwell burner has a firebox with two combustion chambers and a heat exchanger at the rear of these two
chambers. Fuel is loaded and ignited in the top combustion chamber where primary combustion takes place.
After initial primary burning, when the overall burner is hot enough and sustained flue draft is created, flue
gases are directed downward into bottom combustion chamber by closing the damper in upper section of the
firebox. The exhaust gases passing through the red-hot embers get re-ignited and burns at temperatures
higher than 1000
o
C. The extreme hot temperatures and turbulence created while passing through ember
bed, burns almost all the particulate matter. Further, these hot gases pass through a heat exchanger to
extract maximum heat from the exhaust gases which creates a much lower temperature flue gas than the
conventional wood burners. Overall, the downdraft combustion technique is more effective and efficient way
of burning wood which give negligible emissions, returns maximum heat from the fuel burnt and reduces fuel
consumption.
1.1 Items supplied with the fire
- Cromwell Burner
- 600mm Cromwell/Mystique St/St Double Skin Flue Shield
- Accessory Pack – which contains
- 1 x Installation and Operations Manual
- 1 x ceramic block
1.2 Handling and Transport
The CROMWELL fire is heavy and tall in size with total weight of 155 kg.
Single person handling could cause injury, hence Masport recommends suitable handling equipment or two
persons while handling, both outside and inside the house.
Removing both top and bottom doors, Injector and ceramic block will help to reduce weight the weight and
will ease handling of fire during installation.
All precautions have been taken during designing of packaging so that the fire reaches customer’s house
without any damage. In case any damage is found while opening the fire, please report it to your dealer and
to Masport immediately before installing the fire.

4
1.3 Warnings
•The installation of Cromwell burner requires a building consent prior to installation commencing.
Check with your local Building Authority whether there are any extra requirements before
commencing installation.
•The Cromwell burner and flue system shall be installed in accordance with AS/NZS 2918:2001
and appropriate requirements of the relevant local building codes.
•Glen Dimplex highly recommends NZHHA trained SFAIT (Solid Fuel Appliance Installation
technician) installer for installation of Cromwell burner. Your dealer or heating specialist will be
able to help with recommendations as well as advice on permits/consents required for the
installation in your area.
•Please read carefully all the dimensions and recommendations provided on the technical
specification section of this manual. The dimensions given comply with required safety standard
AS/NZS 2918:2001.
•Safety and emissions performance of CROMWELL can be affected by altering the appliance hence no
modifications are allowed without written permission from the manufacturer.
•Please ensure that only components approved by Glen Dimplex New Zealand are used for the
installation, as substitutes may adversely affect performance and might nullify compliance with the
requirements of AS/NZS 2918 safety standard.
•Cromwell burner should be installed with a Masport flue system.
•Modifying the dimensional specification of components may result in hazardous conditions. Where
such action is considered, the manufacturer should be consulted in the first instance.
•Cromwell burner must be serviced at least once every 2 years from service agent trained and
authorized by Glen Dimplex New Zealand.
1.4 Caution
•This appliance is not intended for use by persons (including children) with reduced physical,
sensory, or mental capabilities, or lack of experience and knowledge, unless they have been
given supervision or instruction concerning use of the appliance by a person responsible for
their safety.
•Do not leave children un-attended near alighted fire and keep them well away from the fire
when in use. Supervise young children to ensure that they do not play with the appliance.
•Do not use flammable liquids or aerosols to start or rekindle the fire. Also, do not use such
flammable materials near this appliance when it is operating.
•Always keep clothing, firewood, furnishing and other combustible materials at a safe
distance from the fire.
•Do not attempt to open the bottom door when fire is in use.
•Do not touch any part of the fire other than the top door and the damper handle when in use
as all other parts can be extremely hot.
•Cracked/broken door glass, makes the installation unsafe. Do not operate the fire with
cracked glass.
•Do not attempt to clean or maintain the fire when in use or with hot embers in top or bottom
combustion chamber. Ensure that embers and all other parts of the fire have cooled down
completely before starting ash removal or other maintenance.
•Do not use the fire if there is a malfunction, a suspicion of breakage or unusual noises.
Contact your nearest Masport dealer or customer service team at Glen Dimplex New
Zealand.
•This appliance should always be operated & maintained as per instructions given in this
manual.
Failure to follow above warnings, cautionary measures
and instruction given in this installation and operation
manual will void the Masport warranty of this product.

5
2.0 Cromwell Technical Specifications
Cromwell fire has been tested and complies to following standards & tests:
Environment Canterbury’s Real-life test - Canterbury test method CM1
NZ National Environmental Test Standards - AS/NZS 4012:2014 & AS/NZS 4013:2014.
NZ National Environmental Safety Test
Standard
- AS/NZS 2918:2001
Overall Dimensions
4
68
mm Wide x 54
7
mm Deep x 11
8
8
mm High
Weight
155.0 kg
Test Method
Emissions mg/MJ
Emissions g/kg
Efficiency %
Real Life Test
Canterbury Method
35 mg/MJ 0.47 g/kg 67%
National Environment Standard
AS/NZS 4012/13:20
15
14 mg/MJ 0.20 g/kg 72.4%
Heat
Output
Power in kW
Minimum Average Output
6.8 kW
Maximum Average Output
8.8 kW
Peak Observed during Tests
13.3 kW
Flue Shield
600mm Long SS Masport Double Flue Shield
Flue System
Std 4.2M Long, 150mm Masport Flue System
Floor Protector Requirement
Ash Floor Protector
Clearances to Combustibles
:
Parallel Installation
Corner Installation
`
A
-
Rear Panel to Rear Wall
100
mm
C
-
Glass to Floor Protector
Front
300
mm
B-Cooktop Edge to Side Wall 360 mm E- Cooktop Corner to Wall 125 mm
C- Glass to Floor Protector Front
300 mm H- Flue Centre to Wall 375 mm
D- Floor Protector Side 138 mm L- Floor Protector Diagonal 1131 mm
F- Flue Centre to Rear Wall 344 mm M- Floor Protector Side 957 mm
G- Flue Centre to Side Wall 595 mm N- Flue Centre to Floor
Protector Front
601 mm
I- Floor Protector Front Edge 446 mm R- Flue Centre to Wall Corner 530 mm
J
-
Floor Protector Width
746
mm
WW
-
Overall Width of
Fire
470
mm
K
-
Floor Protector Depth
94
5
mm
DD
-
Overall Depth of Fire
54
5
mm
HH- Overall Height of Fire 1187 mm
Seismic Restraint - Cromwell shall be seismically restrained including floor protector. Use 8mm Dynabolts
for concrete floors or 8mm coach screws for wooden floors, of appropriate lengths.
(Refer Fig 3.5.1 for hole details)

6
3.0 Installation of Cromwell
3.1 Unpacking
Remove the shipping wooden crate and packing around the burner. Remove the packers and other loose pieces
from the firebox. Remove and discard the screws holding the wood fire to the shipping pallet. Using appropriate
lifting equipment, move the burner close to its installation position. Correct lifting procedures should be observed
to avoid injury while handling Masport Cromwell burner.
3.2 Positioning
Cromwell burner is tested to a parallel or corner wall configuration, with minimum distances to heat sensitive
materials in accordance with the AS/NZ 2918:2001 safety test standard. Determine the installation position for
your Cromwell fire only after considering the necessary clearances (See Technical Specifications on page 5 of
this manual) and checking the practicability of installing the flue system. No wall or other fixed object should be
closer to the front of the Cromwell burner than two meters. Regard heat resistant walls with heat sensitive surface
treatments (e.g. wallpaper or heat sensitive paints) as heat sensitive walls.
Any proposed deviation from the specified clearances or installation configurations should be discussed with a
registered “NZHHA” approved installer or GDNZ’s technical team, thus ensuring that progression thereafter is in
accordance with the guidelines in the AS/NZ 2918:2001 test standard and subsequently no compromise on
safety.
3.3 Flue Requirements
Standard 4.2M long, 150mm diameter Masport flue systems which has been tested and complies with the current
installation standard AS/NZS 2918:2001 Appendix F shall be used for Cromwell burner along with the 600mm
long, Masport St/St double skin flue shield. Clearances to combustible given on section 2.0 have been
determined during safety test which was carried out with standard parallel and corner installation configuration
with minimum 2.4m high ceiling.
If a flue exits out of the roof within 3 meters from the ridge, the outer shield shall be not less than 600mm above
the ridge. If the flue exits further than 3 meters out from the roof ridge then it must project at least 1000mm above
roof penetration. This dimension may need increasing to ensure that the top of the flue is at least 3 meters away
from the roof or other obstruction when measured horizontally.
The flue pipe shall extend not less than 4.2m above the top of the burner. Due to factors such as roof pitch,
predominant winds, nearby obstructions (i.e. trees, buildings) and fire placement, flue lengths and flue
terminations/cowls may vary. (Refer Figure 3.3.1) Additional components may be required to complete the
installation and meet all AS/NZS 2918:2001 guidelines for flue termination.
AS/NZS2918:2001 guidelines should be followed for any deviation to these standard configurations. Detailed
instructions for roof penetrations etc. are supplied along with the Masport flue kit. These must be followed
closely, including the minimum flue exit height from the top of the floor protector and the minimum exit height
above the roofline or roof ridge as detailed in the instructions.
Flue installations other than strictly vertical ones are possible. See AS/NZS 2918:2001 for information on non-
vertical flues and flues passing through walls and eaves.
The flue to the flue spigot and all other flue pipe joints should be sealed using firebox cement and Stainless-Steel
Rivets. Sealing all the joints is important for achieving desired performance of the Cromwell burner.
For flue heat shields other than the 600mm Masport Double Shield, the installation clearances will be in
accordance with the guidelines specified in AS/NZS 2918:2001 for an untested flue installation.

7
Figure 3.3.1
3.4 Floor Protector Requirements
Cromwell burner can be installed on any non-combustible ash floor protector with minimum dimensions given on
page 4 if this manual. Please note that the dimensions given are minimum and we recommend using slightly
larger floor protector size.
Please note that the Cromwell burner is heavy having total weight of 155 Kg. The floor and the materials used as
floor protector should be strong enough to bear this load. The minimum requirements for material to be used as
floor protectors on a combustible material are
- 6mm fibre cement board (e.g. Hardies Tile & Slate Underlay) plus 8mm ceramic tiles on a firm base.
- 4mm mild steel floor protector supplied by Glen Dimplex
- Or equivalent.
3.5 Seismic Restraint
Cromwell burner must be seismically restrained, including the floor protector. The Fig 3.5.1 gives the holes that
can be pre-drilled on the floor protector with respect to flue centre. We recommend a minimum 8mm DynaBolts
on concrete floor or 8mm coach screws or toggle fasteners for wooden floors of appropriate length.

8
Fig. 3.5.1
Two holes are located at the rear of the burner and the third one is in the front, under the firebox. T Front hole
can be accessed by removing the bottom front panel as shown in Fig 7.1
- Open the bottom chamber door
- Remove two screws that fasten bottom front panel to the firebox
- Lift upwards and tilt the panel to disengage from the firebox body.
- Lift and remove the bottom shield to access the front seismic hole.
3.6 Reducing Clearances
The clearances to combustible specified in section 2.0 of this manual, can be safely reduced by following
guidelines specified in AS/NZS 2918:2001 table 3.1 & 3.2.
- Heat shield should be made of non-combustible material like metal or masonry.
- Installed between burner and the combustible wall
- With an air gap behind it and vented top and bottom
- The shield should extend a minimum of 450mm beyond the top of the appliance and extend width-wise so
that unshielded rear clearance is maintained
Clearance factors for heat shield which is within 45 degrees of the vertical
Heat Shield Construction Minimum Air Gap Dimension
Clearance Factor
Single layer of continuous material 12mm 0.4
Single layer of continuous material 25mm 0.3
Two spaced layers of continuous material
12mm+12mm 0.2
Clearance factors for heat shield which is more than 45 degrees off the vertical
Heat Shield Construction
Minimum Air Gap Dimension
Clearance Factor
Single layer of continuous material 12mm 0.8
Single layer of continuous material 25mm 0.6

9
4.0 Permitted Fuels
The quality of the firewood you burn can have a considerable effect on performance of the CROMWELL burner.
Moisture content, tree species and log size are the main factors that affects the emissions that are produced by
any wood burner. We recommend that firewood with less than 25% moisture content be used.
If you are cutting your own firewood, only wood that has been air dried in a sheltered, well ventilated stack,
preferably for at least 12 months may be burned in CROMWELL. To ensure that the wood has a moisture
content of 25% or less, store it under a roof or protected against heavy rain. If you purchase firewood, buy
firewood that is well seasoned and having moisture level below 25%. We recommend “Good Wood” merchants
approved by your local council.
Under any circumstances do not burn coal, driftwood, treated or painted wood, highly resinous wood like
“Old Man’s Pine”, laminated plastics, plywood, chipboard, garbage, flammable fluids such as gasoline,
naphtha, engine oil, refuse, milk cartons, colored or printed paper. Use of such materials will invalidate
your warranty, as this may emit toxic, corrosive, and hazardous fumes when burned. They may also
cause a build-up of the toxic gas dioxin, which is damaging to the burner and the environment. Most
importantly, use of such materials will invalidate your warranty.
4.1 Testing Your Wood Moisture
There are number of ways to confirm if wood is dry enough.
- Wood moisture meter is the best way to check the moisture content of the wood fuel. Press the meter tip
into wood firmly into the long side of a split piece of wood and test it. The 15-20% percent moister
content is ideal.
- If you are purchasing firewood, ask for dry seasoned wood and get it tested from your wood merchant.
- Dry wood weighs much less than wet wood.
- Wet wood is hard to light and will emit moisture from the ends while burning.
- Two dry pieces banged together sound hollow, wet pieces sound solid and dull.
4.2 Recommended Log Sizes & Fire Starters
- A packet of matches or lighter
- A packet of firelighters. We recommend green firelighters made of wood waste
- Seasoned firewood about 220~250mm long in various sizes
o(2A) For kindling - 15-16 finely split, dry softwood (total 1.0 kg approximately)
o(2B) For intermediate 1 load – 4 pieces (total 1.2 kg, 300 g each approximately)
o(2C) For intermediate 2 loads – 4 pieces (total 2.5 kg, 625 g each approximately)
o(2D) For main load – 3 or more pieces (Total 3.0 kg, 1 kg each approximately)
4.2A
4.2B
4.2C
4.2D

10
5.0 Operational Sequence (For various steps refer images shown in the bracket)
5.1 Before First Light-up
- Make sure that the burner is correctly installed and signed off by an approved installer.
- All local council’s wood fire permission or permit requirements have been completed satisfactorily.
- Make sure that all the packing material has been removed from both the combustion chambers.
Please note that the special high temperature paint is used in the firebox that will emit some smoke as it cures
during initial two to three sessions of running. Ventilate the house during these initial burns. While curing the
surface heated paint softens, so do not touch hot surface during this process. Babies, small children, pregnant
women, elderly persons, persons subject to pulmonary hypersensitivity and pets should avoid exposure to this
smoke. Open doors and windows and use a fan, if necessary. After these initial burns, there should be no smoke.
5.2 Cold Start- up
-(5.2A) Make sure the bottom combustion chamber door is closed and ceramic block is sitting in place at the
rear of the chamber
-(5.2B) Set the damper handle to “OPEN” position
-(5.2C & 5.2D) Open the top combustion chamber and ensure that injector is oriented front-to-back i.e. rod on
the top of the injector are perpendicular to door opening or parallel to side of the firebox. Ensure the tabs on
top injector are firmly interlocked into slots of bottom injector and injector is not blocked with charcoals or ash.
5.2A 5.2B
5.2C 5.2D
5.3 Stack & Light Kindling
-(5.3A) Open the top combustion chamber & Load 4 pieces of kindling around & top of the downdraft injector.
-(5.3B) Place 2 firelighters as shown
-(5.3C) Load the remaining kindling over the firelighters in a crisscross stack formation
-(5.3D) Light the fire starters and close the door
5.3A 5.3B
5.3C
5.3D
5.4 Intermediate Load 1 (after 5~6 min after light up)
-(5.4A & 5.4B) In about 4-5 mins, kindling will be fully alight. Open the door, add 4 pieces of intermediate 1
load – approx. 1.2 kg and then close the door.
-Now onwards, always ensure that all fuel logs are loaded with “Front to Back” orientation with slightly at an
angle in the firebox.
-(5.4C & 5.4D) in about 10-12 mins, the intermediate load will be fully alight. Turn damper handle from “OPEN”
to “CLOSE”. This sets the burner into downdraft mode.
-In case the down draft is not working, keep the damper handle on “OPEN” for another 2-3 minutes.

11
5.4A 5.4B
5.4C
5.4D
5.5 Intermediate Load 2 & Door Operations (after 10~12 mins after starting up)
-(5.5A) Door will not open once damper handle is positioned on “CLOSE” because of safety interlock
mechanism.
-(5.5B) The downdraft flame in the bottom combustion chamber should look like this.
-When approx. 50% of the intermediated load 1 has burned down, Turn the damper handle to “OPEN” positions
-(5.5C) Open the top combustion chamber slowly, load 4 pieces of intermediate load 2 – approx. 2.5 kg and
close the door
-(5.5D) Turn the damper handle to “CLOSE” position to set the burner back into downdraft mode.
-Do not ever force to open the top chamber door when damper is in “CLOSE” position
-Please note if the bottom chamber flame is ‘pulsing’ or ‘puffing’ after closing the damper, open the damper for
another 1-2 mins and then close to return to downdraft mode.
5.5A 5.5B
5.5C
5.5D
Overall the above steps should take around 40-45 mins. This point on, the burner will be hot enough to run in the
downdraft mode for prolonged period.
5.6 Re-fueling
-(Burner can be refueled with bigger logs once the down-draft is fully established.
-(5.6A) As fuel burns away the down-draft flame will reduce. This is normal and flame will increase again when
more fuel is loaded.
-(5.6B) Turn damper handle to “OPEN” position, open the top combustion chamber.
-Use rake and level the ember bed. Particularly leaving good embers around the downdraft injector.
-(5.6C) Place the 2-3 large size logs weighing approximately 1 kg each on embers in Front-to-Back direction
and close the door
-(5.6D) Turn the damper handle to “CLOSE” position to set the burner back into downdraft mode.
5.6
A
5.6
B
5.6
C
5.6
D

12
5.7 Shut-down and Restart
-To shut down the burner, let the fire extinguish and leave the burner doors closed until it has cooled down
6.0 Cleaning and Maintenance
The following precautions must be taken prior to start any cleaning or maintenance activity:
-Make sure there are no embers in the top or bottom chamber and ashes have cooled down
completely. Also make sure that all panels of the burner are at room temperature.
6.1 Periodic Cleaning & Checks
Depending upon the usage certain parts or areas of the Cromwell burner will need cleaning every week or
fortnight.
6.1.1 Ash Removal
The downdraft burner creates considerably less ash compared to conventional wood burners. Depending upon
usage, ash removal will be required every week or as required.
-Open the top combustion chamber door and & remove the top downdraft injector by lifting vertically.
-Using a small brush, push accumulated ash into bottom chamber through injector hole.
-Open the bottom chamber door
-Insert a metal pan into the lower combustion chamber and using a small brush swap ash on to pan.
-Remove the metal pan with ash and empty it.
-Carefully put back the downdraft top injector back in place.
-Do not remove to the ceramic block during this regular ash removal process. Only make sure that it is in
place.
-Ensure that the ceramic block is pushed at the rear and held in place. Then close the bottom chamber door.
6.1.2 Cleaning the Glass
It will be necessary to clean the glass after long usage or when improper fuel is burnt. A dampened paper towel
newspaper with cool ash or a non-caustic oven cleaner can be used to clean the glass. Do not scrub using steel
products or abrasive material, as it can leave scratch marks on the glass and damage printing on the glass.
6.1.3 Cleaning the Panels
A soft dry cloth is sufficient to clean and maintain the finish of the panels. Household detergent or a damp cloth
must not be used as they may damage painted panels or give bad odors while running the fire.
6.1.4 Visual checks
-Make sure that the top downdraft injector is sitting properly with correct orientation in the top combustion
chamber. (Refer 5.2C)
-All boards in both the combustion chambers are in place and are in good condition.
-Make sure that the ceramic block in the bottom chamber is sitting properly in the bottom combustion
chamber. If the holes of this ceramic block appear to be filled with fly ash, remove it from the bottom chamber
and dust off using a soft brush.
6.2 Annual Maintenance
Cromwell burner must be serviced at least once every 2 years from a service agent
trained and authorized by Glen Dimplex New Zealand.
To ensure continuous safety, before each heating season, carry out checking and maintenance of various parts of
Cromwell, in following order:
1. Door and other seals 5. Top & Bottom combustion Chambers
2. Firebox lining boards & Ceramic Block 6. Top and Bottom Injector
3. Flue inspection and cleaning
4. Heat Exchanger cleaning
Bottom chamber door is for periodic maintenance only.
Open bottom door only when all parts of the burner have cooled down completely.
Top chamber door need to be opened,
to
open the bottom chamber door.

13
Further sections will describe the systematic process of carrying out servicing of different sections of the firebox,
flue, and the heat exchanger. Replace parts only with genuine GLEN DIMPLEX spare components
6.2.1 Door and Other Seals
Seals in following areas should be checked and if required will need replacement periodically depending upon
usage of the Cromwell burner.
1. Top combustion chamber door seal and tape seal behind glass
2. Bottom combustion chamber door seal and tape seal behind glass
3. Access plate for heat exchanger
6.2.2 Firebox Lining Boards & Ceramic Block
The vermiculite boards in your Cromwell burner are an important part of the burner to achieve clean and efficient
burn. These boards are likely to degrade with time and will need to be replaced accordingly. The life of the
boards will depend upon usage, type of fuel burnt and care taken during operations and maintenance. The
boards in both the top and bottom chambers are designed to hold them in place by interlocking into one another.
Due to high temperature in the fire box, the boards may crack with use and this is regarded as a normal
occurrence. If the boards crack but remain in place, it will not affect the performance of the fire and subsequently
can continue to be used. The boards should be replaced only when they are damaged enough that they no longer
remain interlocked in place and cannot perform their intended task. Refer Fig 6.1 for location and sequence of
assembly of boards in both the top and bottom combustion chamber.
The ceramic block placed in the bottom combustion chamber helps in minimizing fly ash entering the heat
exchanger and the main flue pipes. Placing ceramic block in the correct position is important for achieving clean
and efficient burning. After removing the boards and the ceramic block, remove all the ash from both chambers
using brush and pan.
Fig 6.1
The sequence for remove lining boards and ceramic block in both the combustion chamber is as follows:
Top Combustion Chamber
Bottom Combustion Chamber
a. Top Chamber Ash Glass
b. Downdraft Injector
c. Bottom Downdraft Injector
d. Bottom Board LH & RH
e. Rear Board
f. Side LH or RH
g. Top Baffle Board
h.
Remaining Side Board
i. Ceramic Block
j. Bottom Board
k. Side Board LH or RH
l. Front Top Board
m. Rear Top Board
n. Remaining Side Board
o. Rear Boards

14
6.2.3 Flue Inspection & Cleaning
Flue system should be checked and if needed be swept by a professional chimney sweep at least once a year
depending upon usage. Do not use chemical chimney cleaners. Check the flue sections nearest the firebox. If a
flue system is becoming excessively blocked or needs frequent cleaning, investigate the installation, fuel, and
operation of the burner with help of a professional.
4. Remove the injectors, ceramic block and boards from the bottom combustion chamber and keep them in
a safe place as per instruction in 6.2.3.
5. Fig 6.2 shows the location of flue cleaning plug situated inside the top exhaust chamber which is above the
top baffle board.
6. Push this plug upwards to release from the steel plate and then slide it towards the front of the firebox.
7. This will enable to drop and collect all the chimney dirt into bottom combustion chamber without removing
the main flue pipe.
8. Once chimney sweep operation is complete, clean the top exhaust chamber properly and pull the flue
cleaning plug back in place. Ensure that it seals the circular cutout correctly.
Fig 6.2
6.2.4 Cleaning the Heat Exchanger
Though the ceramic block arrests most of the fly ash, some fine ash particles will enter heat exchanger and
condense as soot over the period.
9. Carry out this procedure after completing procedures given in 6.2.2 and 6.2.3.
10. Close the bottom combustion chamber door
11. Remove the rear access panel
12. Remove the heat exchanger cover plate (Refer Fig 6.3)
13. Insert a long wire brush through this opening to clean the outer surface of all the tubes
14. All the ash will fall at the base of the heat exchanger.
15. Open the bottom combustion chamber door to remove the ash
16. Screw back the heat exchanger cover plate and the rear access panel once both chambers are cleaned.

15
Fig 6.3
6.2.4 Cleaning Combustion Chambers
After cleaning flue and heat exchanger, clean both the top and the bottom combustion chambers
17. Using a metal pan and a brush collect the ash and dispose of at a safe place.
18. Inspect both chamber and then put back all the boards in both the top and the bottom chambers
19. Place bottom injector by orienting with the tab on the base plate (Refer Fig 6.4)
20. Place top injector and lock it into tab of bottom injector.
21. Make sure the injectors are sitting flat in stepped bottom bricks and the orientation of rods is front to back.
22. At the end, put ceramic block and make sure it is pushed correctly at the rear.
Fig 6.4

16
7.0 Cromwell Replacement Parts
Some parts of Cromwell burner are considered consumable. These parts will wear out or degrade over time.
The life of these parts will vary upon
23. How frequently the fire is used
24. Type of fuel. Some species of wood fuel are harsher than others.
Following items are considered as consumables:
Boards & Bricks
25. Set for Top Combustion Chamber
26. Set for Bottom Combustion Chamber
27. Ceramic Block
Seals
28. Top Door Seal
29. Bottom Door Seal
Downdraft Injector
30. Top Downdraft Injector
31. Bottom Downdraft Injector
Glass
32. Top Chamber Ash Glass
33. Top Combustion Door Glass
34. Bottom Combustion Door Glass
Other Spare Parts/Kits available
35. Top / Bottom Door Handle Kit
36. Damper Handle Kit
37. Damper
These consumable parts should be replaced as soon as they show signs of wear. Running your burner with
worn or broken parts may result in reduced output, increase in fuel consumption, and even can damage the
firebox or other vital parts of the burner. We highly recommend frequent visual check of these consumables
and other parts of the burner. Refer Fig 6.1 & Fig 7.1 for schematic of Insulation Board layout and other
Cromwell parts.
Part Description
Part Description
1
Top Combustion Chamber
9
Damper Plate
2
Top Combustion Chamber Door Complete
1
0
Down Draft Injector Top
3
Top Door Handle
1
1
Down Draft Injector Bottom
4
Bottom Combustion Chamber
1
2
Bottom Front Panel
5
Bottom Combustion Chamber Door Complete
1
3
Top Plate
6
Bottom Door
Handle
14
Rear Panel
7
Top Chamber Ash Glass
15
Rear Access Panel
8
Damper Handle
16 Flue Cleaning Plug
Fig 7.1

17
8.0 Problem Solving
Problem
Reason for Problem
Solution
Dark, dirty film on
door glass
Burning wet or green firewood OR
Leaking door seals.
Ensure only dry seasoned wood is used.
As per new air plan, it is an offence in the
Environment Canterbury region to burn wood
with greater than 25% moisture.
Check door and glass seals. Your Masport
Dealer can help with this.
To remove dirty film try following:
1. Burn with damper open for 30 minutes.
2. Try to clean glass with damp news paper and
ash when fire has completely cooled down
3. Try using non-caustic oven cleaner
Caution: Do not scrub using steel products or
abrasive material, as it can leave scratch marks
on the glass and damage printing on the glass.
Occasional puffs of
smoke entering the
room while fuel
loading
There could be not enough flue draft due
to insufficient flue height in relation to your
roofline, trees, or other high obstacles
near your home, which can cause a down
draft.
The fuel will eventually ignite and when it
does so, the build up of gasses will cause
a pressurisation forcing smoke into the
room.
Cromwell burner has mechanical interlock that
prevents opening of top combustion door unless
damper is opened. After switching damper
handle from “OPEN” to “CLOSE” position, wait for
30~45 seconds before you open the top
combustion chamber door.
This is usually a problem when the wind is
coming from one direction and requires an
experienced installer to remedy, by either
extending your flue height or fitting an anti down
draft flue cowl.
The down draft flame
is pulsing or puffing
when damper is
switched to ’CLOSE’
position
This is likely to happen when firing the
burner from cold start.
Not enough embers around the downdraft
injector or loading of excessive fuel during
start up can be the reasons.
Open the damper for 1~2 min and close it.
Open the damper and then the top combustion
chamber door and using rake, level the ember
bed. Particularly leaving good embers around
the downdraft injector
Poor performance of
the fire or Smoke
entering room due to
extreme negative
pressure in the house
This is when the air circulates down from
the chimney towards the interior of the
house which is at negative pressure.
Energy efficiency practices and new
building code rules are making our houses
increasingly airtight. This makes the
house’s energy efficient but also makes
them more sensitive to negative pressure
when air is exhausted from the house.
This can be because of large extraction
fans which cause extreme negative
pressure in the house when they are
operating.
This negative pressure works against flue
system draft. In severe cases, the
negative pressure in the house overcomes
the flue system draft and the appliance
begins to spill smoke, especially when a
fire is started or when it dies down to
coals. Also, it can starve fire from air
needed resulting in poor performance.
To prevent this extreme negative pressure, open
a window approximately 6mm to allow
combustion air to enter the room.

18

19
GLEN DIMPLEX WARRANTY REGISTRATION
CROMWELL ULTRA LOW EMISSION BURNER
Thank you for purchasing a Masport Fire. We ask you to complete the following information and
return to the Glen Dimplex Warranty Registration Department on following address:
New Zealand : P O Box 58473, Botany, Manukau 2163, Auckland
Australia : Unit 1, 21 Lionel Road, Mount Waverley, Victoria 3149
Mr / Mrs / Miss / Ms Name: _______________________________________________
Address: ________________________________________________________________
_________________________ Post Code: ___________________________
Telephone: _________________________ Fax: ________________________________
Email ________________________________________________________________
Model: _________________________ Serial Number: ________________________
Retailer: _________________________ Purchase Date: ________________________
Price: ________________________________________________________________
Installed By: _________________________ Date Installed: _________________________
We at Glen Dimplex strive to provide you with quality products and have continuous product
development program. To help achieve our objectives to our mutual benefit we would welcome
your feedback on the following questionnaire.
Question
Please tick appropriate remark
1.General presentation of Product
□
Excellent
□
Good
□
Ok
□
Needs to Improve
2.Styling and Looks
□Excellent
□Good
□Ok
□Needs to Improve
3.Packaging
□Excellent
□Good
□Ok
□Needs to Improve
4.Is documentation easy to follow
and informative?
□Excellent
□Good
□Ok
□Needs to Improve
5.Fixtures & Fittings (Loose parts)
□In order
□Items missing
□Needs to Improve
6.Do you currently own Masport or
Dimplex product?
□Yes
□No
Which? -
7.Why did you decide on Masport?
(tick one or more options)
□Knew this brand
□Suggested by Friend
□
Dealer
r
ecommended
□
Better Price
□Performance
□Features
8.Other Comments
Privacy Act Notice: the owner named on the Warranty Registration consents and agrees that Glen Dimplex may retain and use
the information in this warranty card, including details about the owner for marketing and development purposes. The owner
also agrees that Glen Dimplex may also share purposes with [intended recipients of such information]. In accordance with the
New Zealand Privacy Act 1993 and the Australian Privacy Act 1988, the owner shall have the right to request the correction of,
as well as inspect, all personal information held by Glen Dimplex on that owner.
------------------------------------------------------------------------------------------------------------------------------
Please cut and mail this completed form within 30 days of installation to your
Glen Dimplex Warranty Registration Department at the above address
Cut Here Cut Here Cut Here

20
Table of contents
Other Masport Burner manuals
Popular Burner manuals by other brands
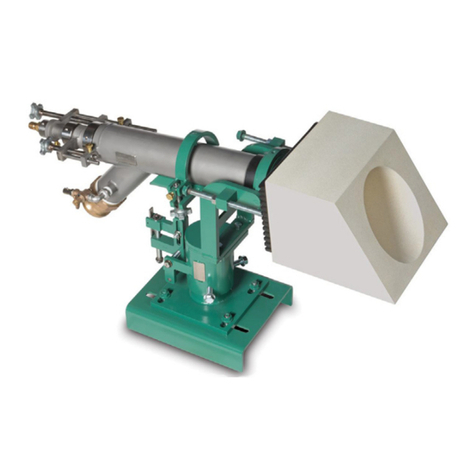
Eclipse
Eclipse BrightFire 200 series operating instructions
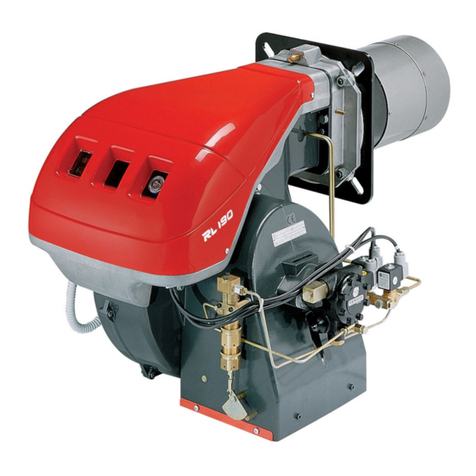
Riello
Riello RL 190 Installation, use and maintenance instructions
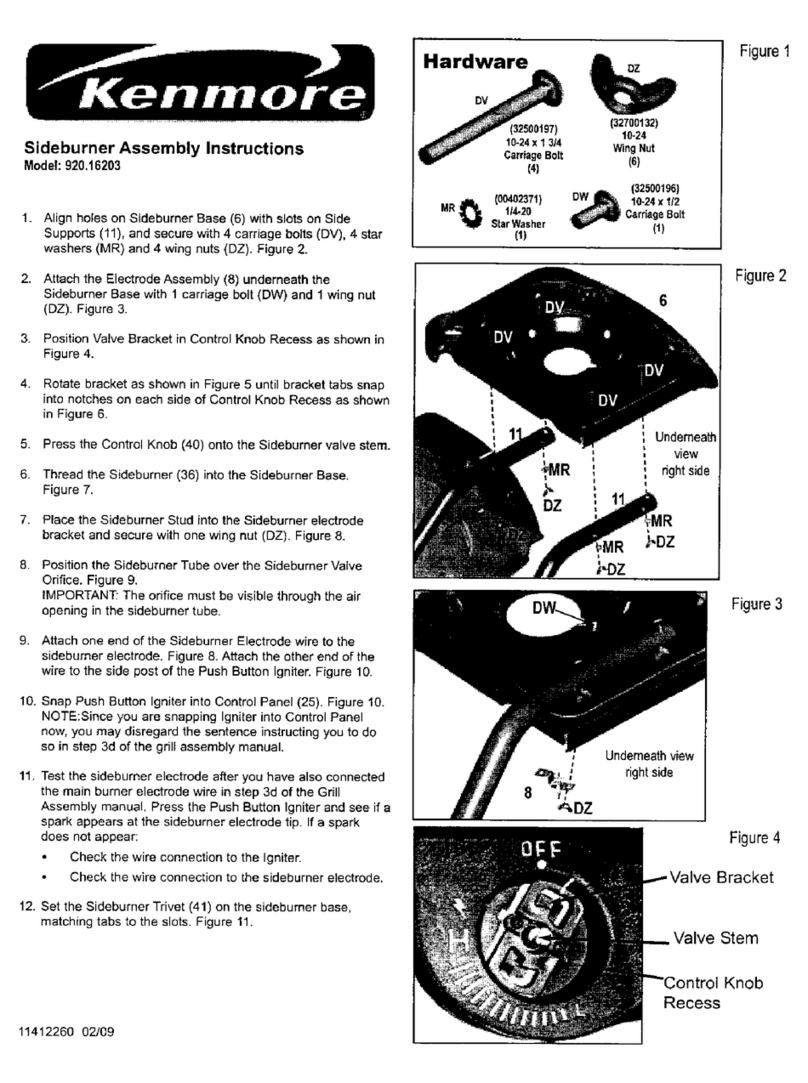
Kenmore
Kenmore 920.16203 Assembly instructions
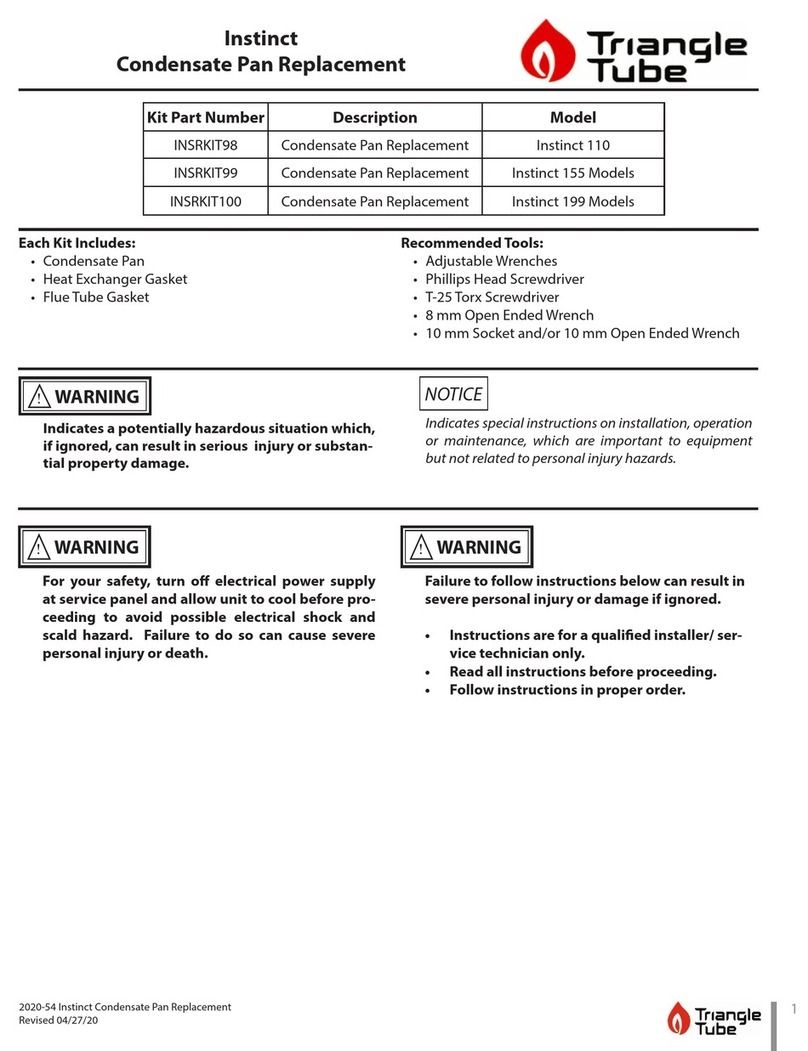
TriangleTube
TriangleTube INSRKIT98 manual

Town & Country Fireplaces
Town & Country Fireplaces TC54.NG04C2 instructions
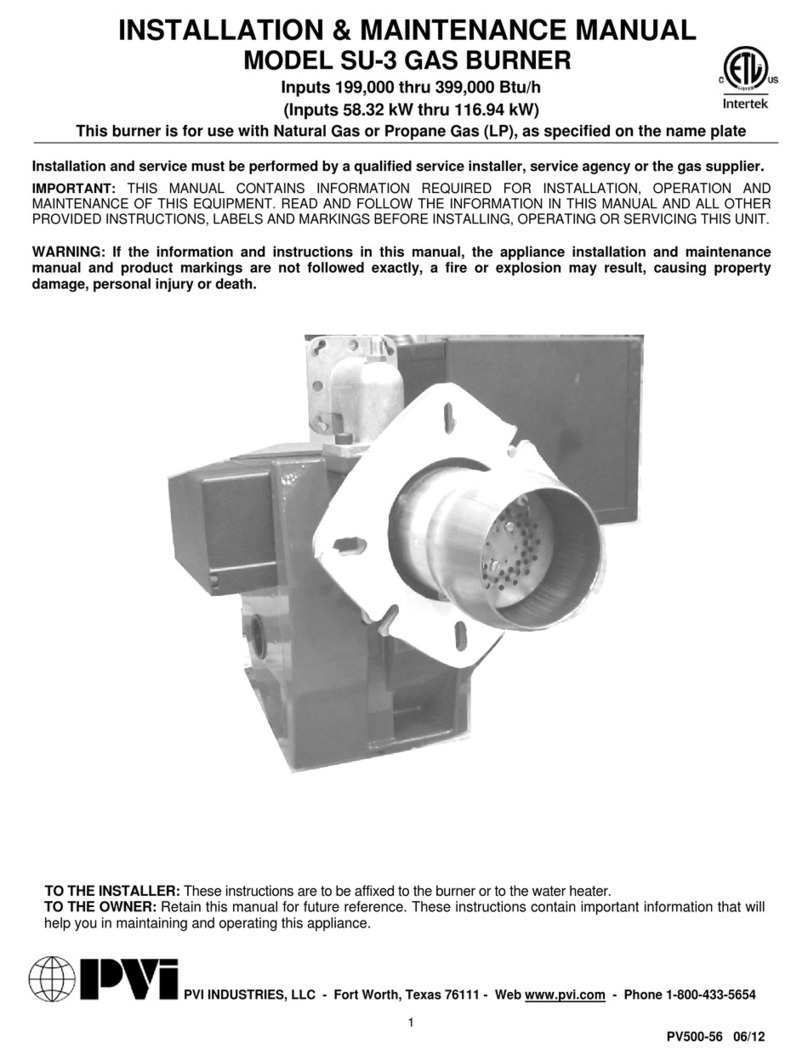
PVI Industries
PVI Industries SU-3 Installation & maintenance manual

Warmington
Warmington SG 700 installation instructions
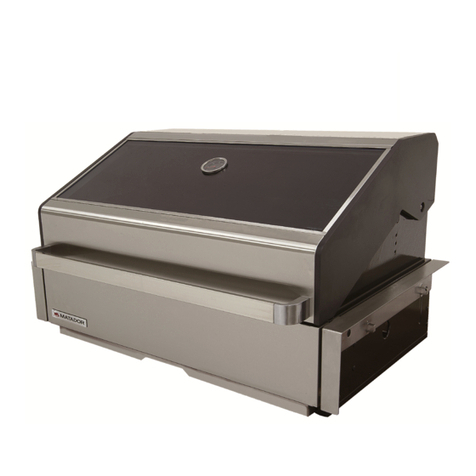
Matador
Matador HS - 19FBI400 instruction manual

elco
elco P2.190 L-Z/LMO operating instructions
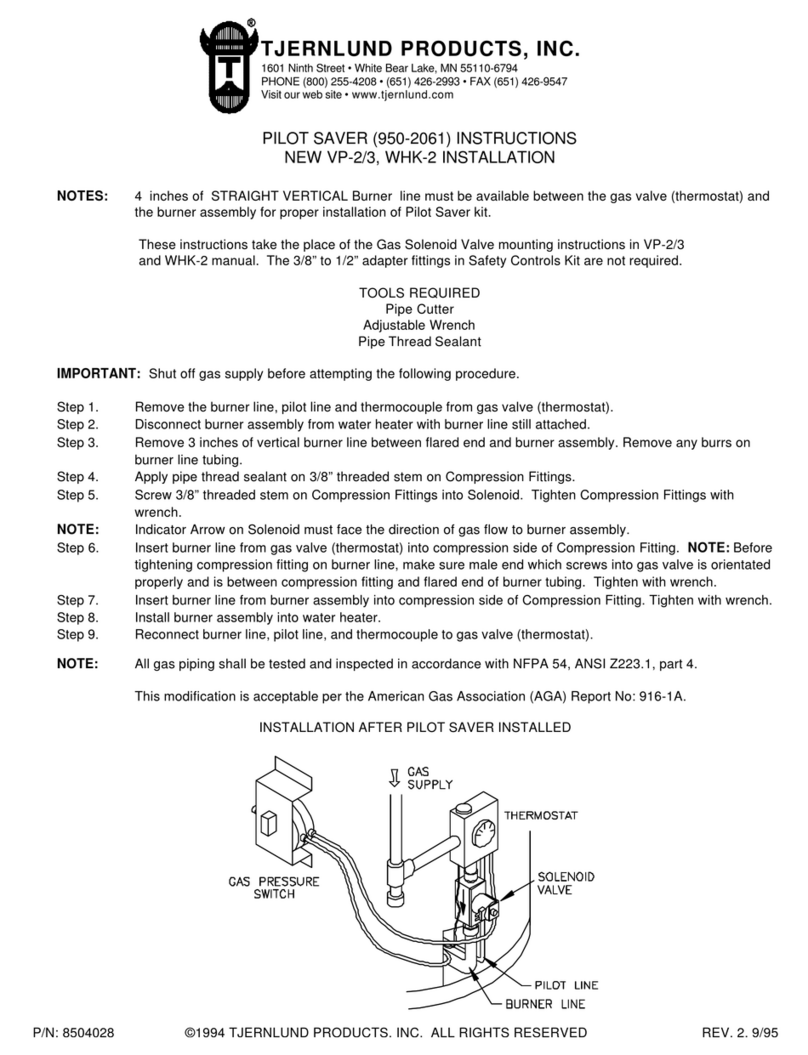
TJERNLUND
TJERNLUND VP-2, VP-3 8500567 0702 installation instructions

Fisher & Paykel
Fisher & Paykel DCS PBE1 installation guide
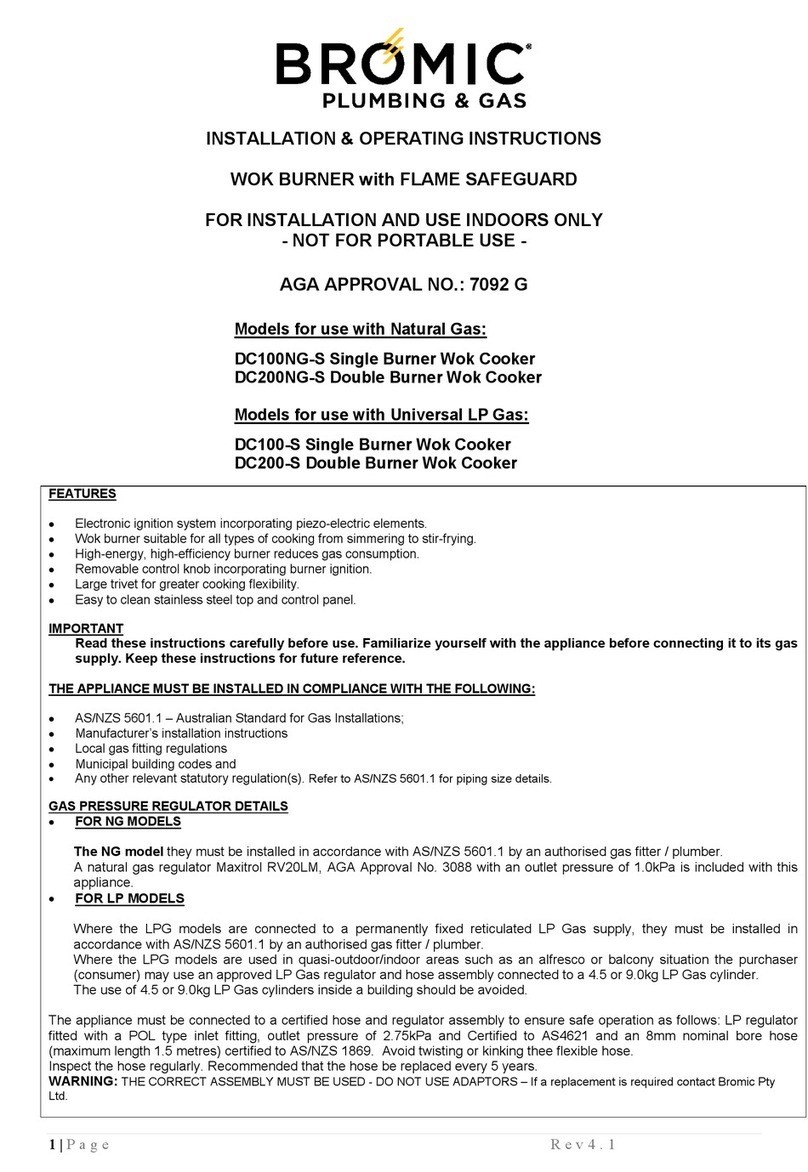
Bromic Heating
Bromic Heating DC100NG-S Installation & operating instructions