AESYS TurboFire II User manual

York-
Shipley
Global
Division
of
AESYS T
ec
hnologie
s,
LLC
TurboFire® II
Burner
INSTALLATION, OPERATION AND
MAINTENANCE MANUAL
AESYS
Techno
l
og
i
es
,
LL
C
693
N
orth
Hill
s R
oad
York, PA 1
7402
Tel:
717-755-
1
08
1
Fax
: 71
7-755-
0
02
0
webs
i
te
:w
ww
.
aesystec
h
.co
m

TurboFire
®
II
Burner
INSTALLATIO
N,
OPERATI
ON AND
MAINTENANCE MANUAL
TABLE OF CONTENTS
FOREWORD
.................................
...
..................................................
SECTION 1: WARNIN
GS
...
...............
...
....
....
..
........................................................ 1
SECTION 2: DESCRIPTJON................................................................................. 2
SECTION 3: INSPECTION & HANDLING ...................................................... 3
INSPEC
TI
O
N·
······
···
·······--··············.............................................. 3
U
NL
OAD
IN
G.................................................................................. 3
SECTION 4: lNSTALLATION................................................................................ 4
SEC
TIONS
:
START·UP
..............
....
...................................................
...
................. 11
PRE S
TART
-UP
CH
ECK
LIST.................................................... 12
START-UP PROCEDURE........................................................... 15
LINKAGE
TEST.............................................................................
16
PILOT TEST...................................................................................
17
MAIN
FLA
METEST (GAS)..........................................................
18
MAIN
FLAME
TEST (OIL)............................................................ 20
MAIN
FLAME
TEST
(LO
W
NO
x PACKAGE)............................ 23
SECT
ION
6:
MAINTENANCE
.........................................................................
..
....
24
DAILY
PROCEDURE.................................................................... 24
WEEKLY
PROCEDURE...............................................................
24
MO
NT
HLY
PROCEDURE............................................................ 25
SEMI-ANNUAL
PROCEDURE .....................................
..
............
25
ANNUAL
PROCEDUR
E.
..
...
.................................................
..
...... 25
SECTION
7:
SERV1CE.
...........................................................................................
26
REFRACTORY REPLACE
MENT
................................................
26
BURNER
SHELL.......................................................................... 26
OIL
NOZZLE
REPAIR...................................................................
27
SECTION 8: TROUBLE SHOOTING .................................................................
28
SECTION 9:
PARTS
LIST.............
..
...........
..
.........................................................
32
APPENDIX
FIRE
TEST REPORT.....................................................................
A-1
BURNER
SPEC
IF
IC
ATIONS ...................................................... A-2
START-UP INSPECT
IO
N FORM................................................ A-3
WARRANTY
CERTIFIC
ATE
.........................................-..............
A-4

Figure 1a.
Figure 1b.
Figure
2.
Figure 3.
Figure
4.
Figure 5.
Figure 6.
Figure 7.
Figure 8.
Figure 9.
Figure 10.
Figure 11.
Figure 12.
Figure 13.
Figure 1
4.
Figure 15.
Figure 16.
Figure 17.
Figure
18
.
Figure 19.
Figu
re
20.
Figure
21
.
Figure 22.
TurboFire® II Burner
LIST OF FIGURES
Page
No
.
General Burner Arrangement.....................................................
..
General Burner Arrangement.....................................................
..
Refractory Insert..............................................................................
Preparing Mounting Flange Area..............................................
..
Refractory Orifice................
.....
........................................................
Preferred Burner Lifting Arrangement.........................................
Alternative Burner Lifting Arrangement....................................
..
Burner Orientation and Insertion..................................................
Retrofrt Gas Train (Main)................................................................
Pressure Tap on Gas Train...........................................................
Typical Linkage Arrangement......................................................
Pilot Gas Train.................................................................................
Oil Nozzle Assembly ...................................................................
..
.
Atomizing
Air
Compressor (
No.2
Fuel Oil)..............................
..
No. 2 Fuel Oil Piping Schemat
ic
..............
..
..................................
Fuel Oil Pump Set (No. 2 Fuel Oil}............................................
..
Scanner Assembly .......................................................................
..
Forced Draft Blower Assembly
..
.................................................
..
Pilot
Gas
Train Assembly............................................................
..
Main Gas Train Schematic (Standard Pressures)....................
Modulation Assembly (Standard}................................................
Control Panel Assembly
(YSHIL-
N/2}.....................................
..
Pilot Assembly Drawing...............................................................
..
4
5
6
7
7
8
8
9
10
15
16
17
27
32
33
34
34
35
35
36
37
38
39

FOREWORD
The vork·Sntpt
ev
packaged boiler has
been
carefullydesigned
and
built in accordance with theBoiler
and Pressure Vessel Code of
the
American Socie
ty
of
Mechanical Engineers and
the
complete
packaged boiler is
li
sted
by
the Underwriter
s'
Laboratory,
Tnc.
Manufacturing operations
are
constantly monitored
byYor
k·Shlpteviospectors and
an
Authorized
National Board commissioned inspector.
The
packaged boiler complies with
the
wr:itten
vorJ<·Shiptey
Quality
Control Procedure
which
has
been
reviewed
and
accepted
by
the authorized agencies
which
control boiler and pressure
vessel
manu
f
acruring.
The packaged boileroperation
is
essentially
autOmatic.
It
does
require proper installation, trained
operators,
and
maintenance
to
provide safeand efficient
lo
ng-life service. This manual, which
is
shipped
with
the
packaged boiler,
pre.sents
inJormarion
which
will
help
the
owner and operators
to
achieve thatle
vel
of
service.
It is
very
imponant that this manual
be
carefully studied and retained in a location where it is
read
il
y available to the
pack
aged boiler
operat
o
rs
fo
r
re
ference at all
times.
ff
tbere are questions, consult
York
-Sh
ipley
before undertaking any unloading, movement,
installation. operation. maintenance, orservice, including
partS
re
placem
e
nt
York-
Sh
ipl
ey}
S
NOT
RE
SP
ONS
IDL
E
FO
R
THE
OVERALL SY
STE
M
DES
I
GN
(
INC
L
UDING
UREEC
Bl
NG
AND ST
ACK
)
~NO
THE
SYS
TE
M'S
PE
RF
OR
MANCE
OR ARIL
ITY
TO
MEET
T
HE
RE
QU
IR
EM
ENTS Of
THE
OW
NER.
DON
L
EE
R
ECOMMENDS
THAT T
HE
OWN
ER
AN
D
/O
R T
HE
I
NSTA
LLER
P
LA
CE
T
HA
T
RE
SP
ONSffi
lLI
TY
W
ITH
A
CO
MP
ET
ENT
ENG
I
NEER.
Treutmem
of
the boiler water
is
nece
ssa
ry
to
prevent excessi
ve
corrosion
of
th
e waterside surfa
ces
of
the
bailee DONLEE. recognizing
the
need
for
specific chemical analysis
of
local water
to
provide proper treatmen
t,
ne
ither prescribes nor recommen
ds
the type
or
amount
of
wa
ter
treatment. The owner sh
al
l engage a com
pe
tent water treating company or consultant
to
recommend
the
proper water rreaanent
and
procedure
of
the boilerwater in question.
The Limited Warranty applying
to
the
packaged boiler
is
included with this manual. Read il
c
ar
e
full
y.
Additional copies
of
this
manual are available
from
tbevork-Sh
l
p
t
e
~iterarure
Departmentfor a fee of
$15.00 perco
py.
The contact address
is:
Yor
k-S
hipl
ey G l
obal
693
No
rth Hills Road
Yo
rk
PA 17402
•
Co
nt
en
ts
of
thisinanual a
re
subj
ec
t
to
c
han
ge
withoul
no
tice.
• Specific perfo
rman
ce
sp
ecifica
ti
ons
will
be
prov
ided
with
the
job quot
at
i
on.

SECTION 1: WARNINGS
Inspect the burner when it arrives at
fts
shipping destinati
on
to identify
and
record any
shipping damage. Reporting this damage
to
the carrier
is
the responsibility of
the
consignee
and SUCH DAMAGE IS NOT C
OV
ERED BY THE
WA
RRANT
Y.
Refer
to
Section 3 for
more details.
If the burner is stored prior
to
installation. it
is
the responsibility of others (not York-Shipley)
to
provide.
the necessary protection from damage due
to
conditions such as:
• Freezing temperatures
• Flooding
Dust and dirt
Falling articl
es.
etc.
SUCH DAMAGE IS NOT COVERED BY THE WARRANTY (see Section 3).
It
Is the owner's responsibility; in cooperation with the installer, to obtain t
he
required
inspections of the installation f
or
compliance with state and local jurisdictional codes
and
requirements and
to
obtain boiler insurance, operati
ng
certification and periodic third-party
inspections during t
he
li
fe
of the burner.
The owner has the responsibility
to
provide qualified and trained operators and to assure t
hat
the burner
is
operated and maintained
to
provfde efficient and safe operati
on
. This
manua
l
provides information
to
assist the owner and operators but is not intended to supplant
thoughtful and diligent dedication
on
the part of the owner and operators
to
this task. The
owner and operators must comply
with
the regulations and requirements of the insurance
carrier, and state and local jurisdictions. Their legal requirements take precedence over
anything included in this manual.
The burner
~:
1i
iizes
combustible fuels and water
or
steam
at
pressures higher than
atmospheric. Industry accepted safety standards are met or exceeded in the desi
gn
and
manufacture of the burner. INSTALLERS AND OPERATORS OF THE BURNER A
RE
WARNED THAT THEIR IMPROPER
OR
CAREL
ES
S ACTIONS CAN
RE
SULT
IN
A
HAZARDOUS CONDITION.
The equipment is not intended for use
in
furnishing temporary heat to the structure
in
which
it
is installed prior to the completion and acceptance of such structure and installation
by
the
owner or other person for whom the entire project
is
being constructed. Therefore, the
warranty
and
warranty service normally issued with respect
to
this equipment will not apply
during
and
a
ft
er
such use.
WHEN SERVICING THE BURNER, DISCONNECT
ALL
POWER SUPPLIES.
Equipment furnished by York-Shipley Global includes various safety, performance,
temperature and operation systems and limits. ANY ACTIONS BY THE PURCHASER,
PURCHASER'S
PERSONNEL
OR
PERSONS ACTING ON PURCHASER
'S
BEHALF WHICH TEND TO NULLIFY
OR
CHANGE SUCH SYSTEMS
OR
LIMITS
WILL
BE
TAKEN
AT
PURCHASER
'S
SOLE RISK AND RESPONSIBILITY AND
WILL
V
OID
York-Shipley Global's
WARRANTY
AND
PERFORMANCE
RESPONSIBILITIES
AND
WILL
RELIEVE
York-Shipley
OF
ALL
LIABILITIES RESULTING THEREFROM.
Secti
on
1 - W
arnings

SECTION 2:
DESCRIPTION
The York-Shipley TurboFire®
II
unit is a packaged burner system consisting
of a burner body, controls, forced draft blower, piping, gas and/or oil train, electric panel and
otheritems. A lifting lug is attached to the burner for handling.
At the request of the purchaser
or
for foreign shipments, certain parts and/or assemblies
may
be
rem
oved from the packaged boiler and shipped separately. Reassembly of these pans
and/or assemblies
is
completely the responsibility of the
pu
rchaser.
Gas, oil, steam and electrical supply power connections need to be made by the installer.
THE CONTROL SYSTEM VOLTAGE FOR THE BURNER IS ALWAYS 120 VOLTS
REGARDLESS OFTHE BOILER VOLTAGE.
The Cyclonic burner differs from existing forced draft burners and its operation is extremely
simple. There are
no
internal baffles, dampers or other appurtenances in the burner.
The high tangential velocity created within the burner causes
an
in
ti
mate mixing of fuel and
air resulting
in
extremely good combustion and low excess air.
This high tangential velocity is maintained throughout the length of the furnace which
increases the convective heat transfer and the residence time of the combustion gases
in
the
furnace resulting
in
the gases exiting
from
the furnace at a relatively
lo
wer temperature than
with conventional burners.
The packaged burner is fire tested at
the
factory priorto shipment. A sample copy ofthe test
report is inclu
ded
in
the APPENDIX.
2 TurboFire®
II
Burner

SECTION
3:
INSPECTION & HANDLING
INSPECTION
York-Ship
l
ey
Global
is
not responsible for damage to the burner and/or
fo
r items
missing during shipment from the factory
to
the shipping destination. RESOLUTION OF
SUCH
CLAIMS AGAINST THE CARRIER
IS
THE RESPONSIBILITY OFTHE CONSIGNEE.
Immediately upon the arrival of the shipment and before. it Is unloaded from the carrier's
vehicle, the consignee
or
his agent shall make a thorough inspection ofthe shipment.
Look
fo
r the following:
• Is the blocking and/or strapping in place and tight?
• Has the unit shifted
on
the carrier's vehicle?
• Are the temperature and pressure gauges and controls in place and undamaged?
• Is the piping to accessories intact and undamaged?
•
Do
the skids and supports show evidence ofstress
or
damage?
• Are the lifting
lu
gs bent or distorted?
• Is the burner dented
or
marred?
• Is there evidence of pilfering?
If there is evidence of damage or items missing, notations of the speciiic damage and/or
missi
ng
items shall
be
made
on
the freight bill and a record of such notations retained by the
consignee. The consignee shall immediately advise the carrier's agent ofthe condition of
the
shipment In writing, demand
an
inspecti
on
of the damage and file the damage claim with
the
carrier.
UNLOADING
The packaged burner is a heavy and bulky piece of equipment which may
be
damaged if it is
not handled properly by skilled persons using special equipment.
Unloading the burner from the carrier's vehicle and/or moving it into position
re
qu
ires skill
and proper equipment and should.not
be
attempted by those who lack the qualifications.
York-Shipley
Glo'?al
recommends that a competent rigger
be
engaged to perform
that task. The consignee should advise the rigger
as
to
the time w
hen
his services will
be
needed
in
order to eliminate charges for delays.
If delays
do
occur, it
is
important
tha
t the burner be protected from the weather, dust, dirt,
pilferage and damage. Panicular attention shall
be
given to protection of electrical items:
controls, motors and wiring.
REFER TO FIGURES 5 & 6 FOR LIFTING INFORMATION.
Se
c
tion
3 -
lnstallatio
n &
Handling
3

SECTION 4:
INSTALLATION
BURNER
INSTALLATION
INSTRUCTIONS
1.
Familiarize yourself with the burnerby studying F
ig
ures 1a and 1b "General Burner
Arrangement."
4
BUR
N
ER
ASSEMBLY
GAS
TRAIN
(PILOT)
BLOWER
A
IR
SWITCH
Figure
1a. General
Burner
Arrangment
TurboFire®
ll
Burner

NOZZLE
ASSCMSL
Y
\OIL)
METER
I
I\'G
VALVe
(OIL)
F
ig
ure
1b.
General
Burn
er
Arrangement
2.
Turn off all electrical power
to
the boiler.
3.
Close
all
natural gas valves.
4. Disconnect and
tag
any electrical, gas
or
oil connections
whi
ch may interfere with the
removal of the existing burner
or
the gas train.
5. Read and follow the instructions for removal
of
the old burner which
we
re
supplied from
the original manufacturer.
Section4 -
Ins
tallation 5

6.
Remove the refractory cylinder
in
to which your old burner was
in
serted. Figure 2
"Refractory
In
sert.·
WARNING:
Your
Turbofire
® II burner may require the installation oi refractory tile.
Consult a
qu
laified TurboFire®
II
technician.
Figure
2. Refractory
Insert
7. Remove any gasketing rope from the mounting flange area
of
the boiler.
6 TurboFire® II Burner

8.
Remove any rust, scale, rope
or
refractory left
in
the firing tube
or
the front mounting
fl
ange area with a wire brush. Figure 3 "Preparing Mounting Flange Area.·
9.
Inspect the refractory orifice located inside the firing tube. The orifice should be
replaced if there are any loose
or
cracked bricks. Figure 4 "Refractory Target."
Fig
ur
e 3.
Prep
ari
ng
Mo
unting
Fl
ange
Ar
ea
Fig
ur
e 4. Refract
or
y Target
NOTE: THE TURBOFIRE®
II
BURNER NORMALLY REQUIRES A REFRACTORY
ORIFICE
IN
THE BOILER MORISON TUBE. CONSULT THE FACTORY
REPRESENTATIVE
FOR
THE PROPER SIZE AND INSTALLATION
INSTRUCTIONS.
WAR
NIN
G: Do not operate your Turbofire®
II
without a properly sized boiler orifice.
Unsafe burner operati
on
will result
Section4 - Installation 7

1o. Place a chain, cable,
or
belt sling rated for a minimum of 2000 lb. around the burner
between the mounting flange on the burner, and the blower. With a properly sized
lifting device, pi
ck
up the burner. Figures 5 and 6 illustrate the preferred and
alternative burner lifiting arrangements.
LIFTING
SUNG
(20
00
LBS. MINIMUM
CAPACITY)
LIFTI
NG
DEV
I
CE
(
2000
LBS. MINIMUM
CAPACITY)
Figure 5. Preferred
Burner
Lifting
Arrangement
LIFTING
DEVICE
(2000
LBS
. MINIMUM
CAP
ACITY)
Figure 6.
Alternative
Burner
Lift
i
ng
Arrangement
8 Tu:cboFire®
II
Burner

11. Rotate the burner
in
the lifting sling
so
that the air inlet of the blower is square to
the
floor. Rgure 7 "BurnerOrientation and Insertion."
NOTE: THE BOILER DESIGN MAY REQUIRE THE TURBOFIRE®
II
BURNER TO
BE
INSTALLED WITH THE BLOWER ABOVE THE BURNER. CONSULT FACTORY
REPRESENTATIVE.
12. liberally spray adhesive onto the front mounting flange area oft
he
boiler.
Wa
it a
few
moments until t
he
adhesive becomes "tacky". Wr
ap
3/8" gasketing rope around the
circumference of the firi
ng
tube two (
2)
times
on
the inside of the mountinq stud
diameter
on
the front cover ofthe boiler.
NOTE: DO NOT USE FIBERGLASS GASKET
13. Slide the burner end head into the firing tube of
th
e boiler. Rotate the burner so that
the mounting flange holes of the burner are aligned with the mounting studs of the
boiler and s
li
de the burner onto the studs. Rgure
7.
518
'
OIAMETEf\
STAAWASHER
5.9.
NUT
(BRASS)
Figure
7.
Burner
Orientation and Insertion
Sect
ion
4.
-Installation 9

14. Screw washers and brass nuts onto the boiler studs.
15. Lower the lifting device
so
that
the
studs support the burner and remove the sling f
rom
around the burner.
16. Tighten
the
brass nuts
on
the studs evenly to seal the burner to t
he
boiler.
CAUTION: Failure to tighten the brass nuts may result
in
a combustion
gas leak and burner overheating.
17. Connect main gas line to gas train connection on TurboFire® II.
See Figure 8 "Retrofit Gas Train (Main)".
18. Have an electrical contractor connect all electrical connections to the gas train and
boiler safety and control switches f
rom
the control panel provided with the burner
exactly as shown
in
the provided wiring diagram.
19. Connect oil (and steam) supp
ly
to the burner.
10
GAS
LINE
CONNECTIO
N COON
(FIELD)
CHARACTERIZED
GAS
VALVE
LOW
PRESSURE
CUT
OUT
SWITCH
Figure
8.
Retrofit Gas Train (Main)
Turbo
Fire®
II
Burner
HIGH
PRESSURE
CUTOUT
SWITCH
GAS
VALVE

SECTION 5: START-UP
Your Tu
rb
oFire® II burner has been tested and adjusted at the
fa
ctory
to
provide
optimum performance and reliability. However, each burner installation is slightly
different and your burner will require some fine tun
in
g and safety checks once it is
installed.
ATTENTION: A
York
-S
h
ip
ley
Global
REPRESENTATIVE
MUST CONDUCT THE PRE-START-UP INSPECTION AND THE
ACTUAL START-UP PROCEDURE.
Section 5-
Start
-u
p 11

PRE
ST
ART-UP CHECK LIST
12
GENERAL
If refractory has been added to the combustion chamber as
part of the installation, is it completely dry, cured, and ready
for firing at full
bo
iler input? 0
Has the proper electrical voltage been connected to the
burner control cabinet
as
shown
on
t
he
burner wiring diagram? 0
Has the burner wiring been checked for completeness and
accuracy? Have 3-phase motors been properly wired and
checked for correct rotation? 0
Are
the
boiler mounted limit controls
such
as
low water cutoffs, high limit
controls, operating controls, modulating controls, etc., properly Installed
and wired? 0
Are
the
boiler controls the right type and adjusted
to
the proper setting
and range for
the
installation? 0
Is
the boiler water supply, including
feed
pumps, properly
connected and is
the
boiler filled with water? 0
Is
sufficient load connected to the boiler
so
that it can
be
fired
continoously
at
full rating? 0
If
the boiler load is not connected, can steam be wasted
so
that the
bo
il
er can
be
fired continuously at full rating without endangering
personnel or equipment? 0
If the installation is a hot water boiler, have the circulating pumps been
completely installed, wired and properly tested to assure proper operation
so
that the burner can
be
fired contifluously at full rating? 0
For new boiler installations, has the boiler been boiled out
in
accordance
with the boiler manufacturer's instructions? 0
Have the boiler breaching connections to the stack been completed
and are they open and unobstructed? 0
Is draft control equipment required and, if so, installed? 0
Have adequate provisions for combustion air been installed? 0
TmboFire®
ll
Burner

Have the persons listed below been notified of the burner start-up date?
0 Owner's Representative?
0 Mechanical Contractor's Representative?
0 Electrical Contractor's Representative?
0 Service Organization's Representative?
0
York-Shipley
Representative?
Is
all specified auxiliary equipment mounted and wired? This may include
outdoor temperature controls, oil flow switches, space thermostats,
water flow switches, motorized combustion air louvers, etc. 0
GAS FIRING
Are
all gas train components installed and have they been
properly selected, sized and assembled? 0
Have properly sized vent lines been installed on all gas train components
whi
ch
require venting? This includes such items
as
pressure regulators,
normally open vent valves, diaphragm valves,
lo
w and hi
gh
gas pressure
switches, etc. 0
Have gas train piping and components been tested and proven gas
ti
ght?_
0
Have the gas lines been purged? 0
Is the proper gas pressure available
at
the
in
letto the controls which
meets the requirement shown on the burner material list? 0
OIL FIRING
Is the oil tank installed and filled with the proper type and
grade of fuel oil
as
required by the burnermaterial list?
-------
0
Is the proper oil pressure, temperature and viscosity available
at the inlet to the controls which meets the requirements shown
on the burner fire test report and/or oil system sheet?
_______
_ 0
Have oil supply and return
li
nes been properly sized to meet
the maximum pumping capacity of the pump and has the system
been purged and proven leak proof?
-------------
- 0
Section 5 • Start
-u
p 13

SIGNATURE
OF
INSPECTOR($)
(Name) (Date)
(Name) (Date)
(Name) (Date)
(Name) (Date)
(Name) (Date)
14
Turbo
F
ir
e®
II
Burner

S
TAR~UP
PROCEDURE
STEP
1:
Tighten all electrical, conduit, air, steam and fuel lines.
STEP 2: Set the natural gas
li
ne
pressure taken at the beginning of the gas train
to
the
value
li
sted in t
he
burner fire test report, by adjusting the natural gas regulator.
Figure 9 "Pressure
Tap
on Gas T
ra
in"
• Connect manometer
to
gas pressure
tap
.
• Place oxygen analyzer in boiler stack.
FI.StiOLE
TV&ING
Figu
re
9. Pr
e9'Su
re Tap on Gas
Tr
ain
STEP
3:
Read the Fireye E100,
(o
r YS-7000 if so equipped) Flame Control Manual
NOTE: THE FIREYE E100
OR
Y-S 7000 SYSTEM, WHICH IS USED ON YOUR
TURBOFIRE®
II
BURNER, PROVIDES FLAME SUPERVISION AND
SEQUENCING FUNCTIONS. YOU SHOULD BE THOROUGHLY FAMI
LIAR
WITH ALL
OF
THEIR
FUNC
T
IO
NS AND FEATURES BEFORE ATTEMPTING
THE START-UP PROCEDURE.
STEP 4: Tum on electrical power to the boilerat the main boiler room electric pa
nel.
Section 5 - Start-up 15

S
TE
P 5: LIN
KAGE
TEST
Procedure:
1.
Tighten all linkage nuts located
on
all
li
nkage rods.
2.
With
the flame controller
in
the check mode
and
all fuel manual valves open except
the manual valve located closest
to
the
burner (Figure 10), place the boiler ON/OFF
switch
in
the ON position. (The ON/OFF
sWitch
is located
on
the side of the burner
control panel).
NOTE: THE BLOWER WILL NOT START
UN
LE
SS
THE LOW GAS PRESSURE
SWITCH
(I
F EQUIPPED) '
IS
RESET.
The blower should start and the
li
nkage should begin to move.
Re
peat Step 2 several times to assure proper linkage movement.
3. Watch the linkage arrangement
as
it
mo
ves up and
do
w
n.
1 6
The fuel valves, air damper,
lin
kage
ro
ds and modulation motor should all move
with a smooth act
io
n with
no
binding.
The
fuel valves and air damper should
not bind at the FULL OPEN orCLOSED
pos
ition.
CAMPER
CC"'TRRL
AAV.
\
MOOUlATlON
t.OTOR
MET'El11NG
VALVE
(OIL)
JACI<SHAFT
BRACKET
BliT"TEAFL
Y
VALVE
{AIR)
Fig
ur
e 10. Typical Li
nk
age
Ar
rangement
Turbo
Fire®
II
Bum
er
Popular Burner manuals by other brands

baltur
baltur TBG 35 ME Instruction manual for installation, use and maintenance
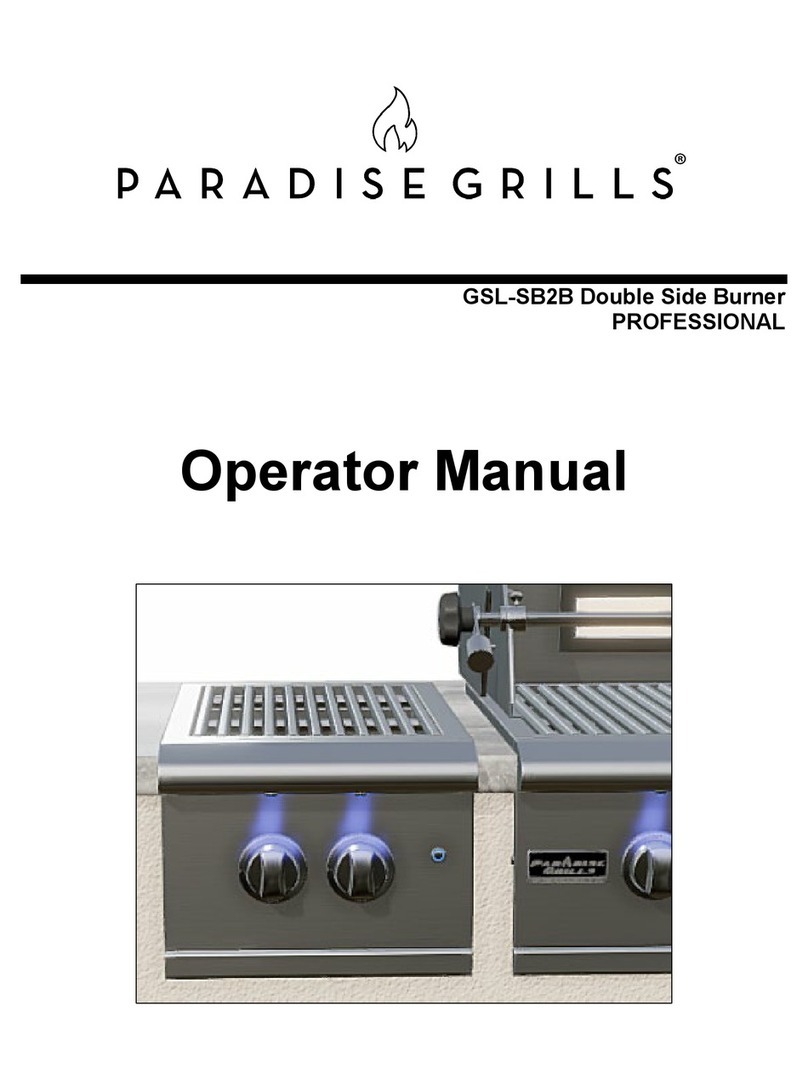
PARADISE GRILLS
PARADISE GRILLS GSL-SB2B Operator's manual
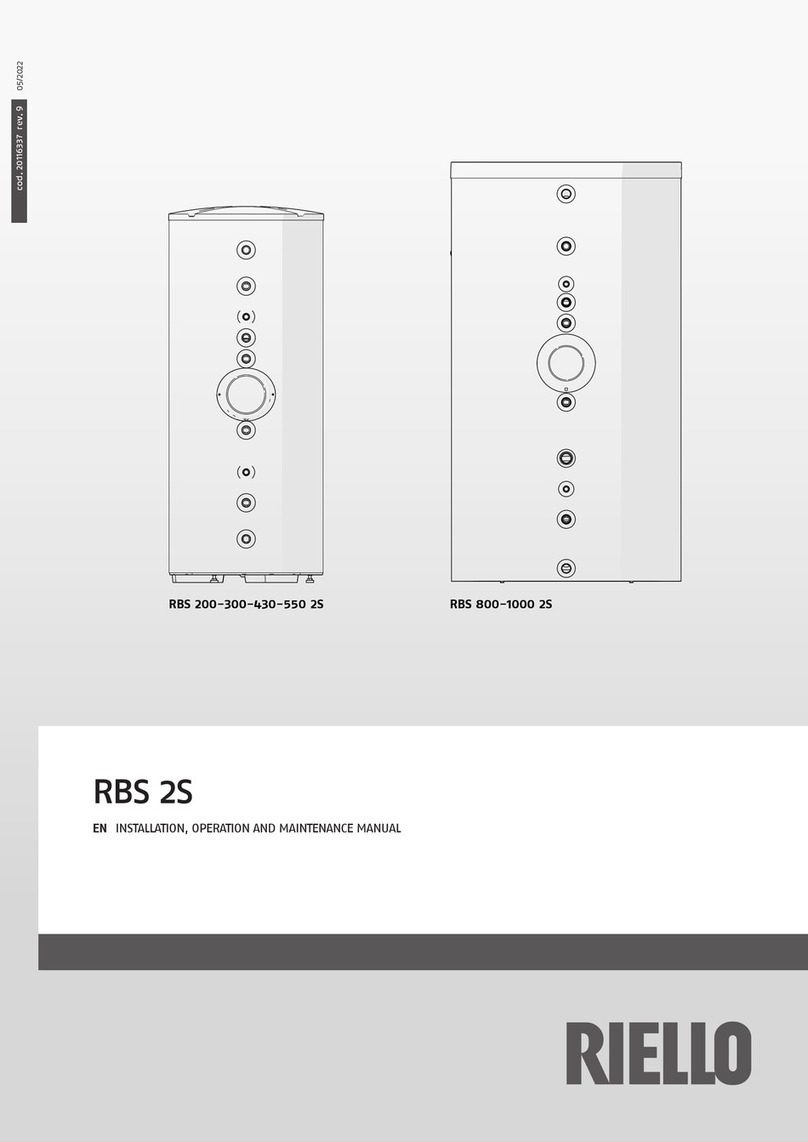
Riello
Riello RBS 200 2S Installation, operation and maintenance manual

Coyote
Coyote C1SBLP install guide
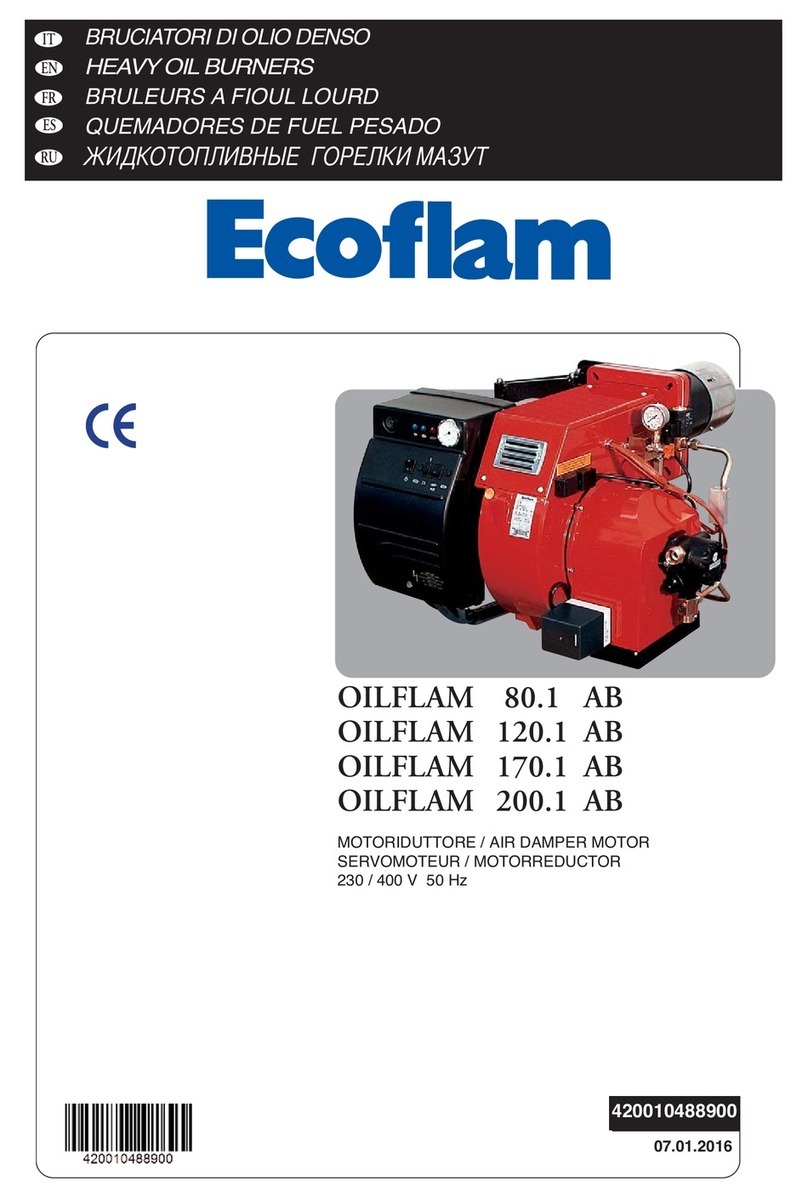
Ecoflam
Ecoflam OILFLAM 80.1 AB manual

Riello
Riello G5K Installation, use and maintenance instructions
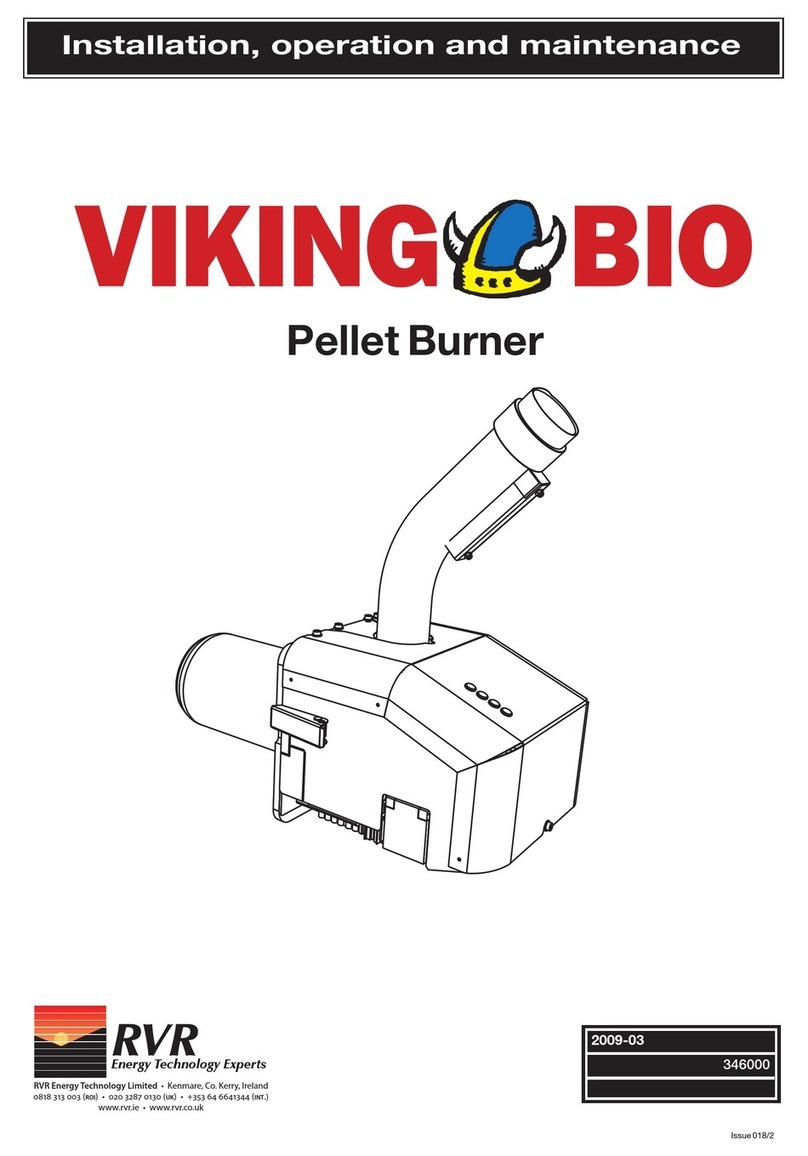
RVR Solar
RVR Solar Varmebaronen Viking BIO Installation, operation and maintenance
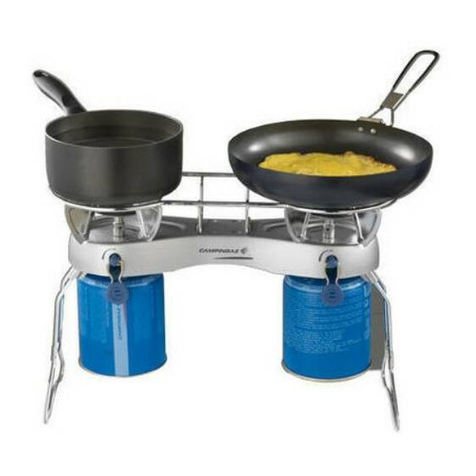
Campingaz
Campingaz CAMPING DUO PLUS CV manual
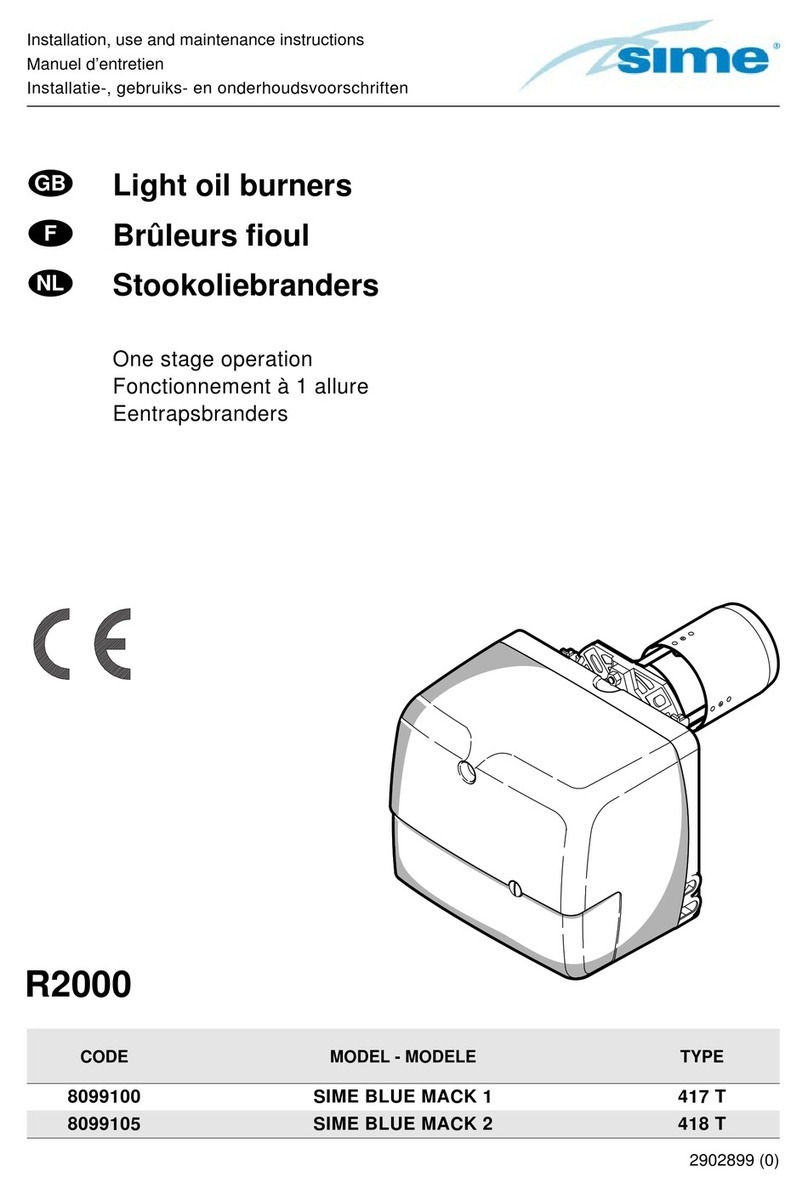
Sime
Sime SIME BLUE MACK 1 Installation, use and maintenance instructions
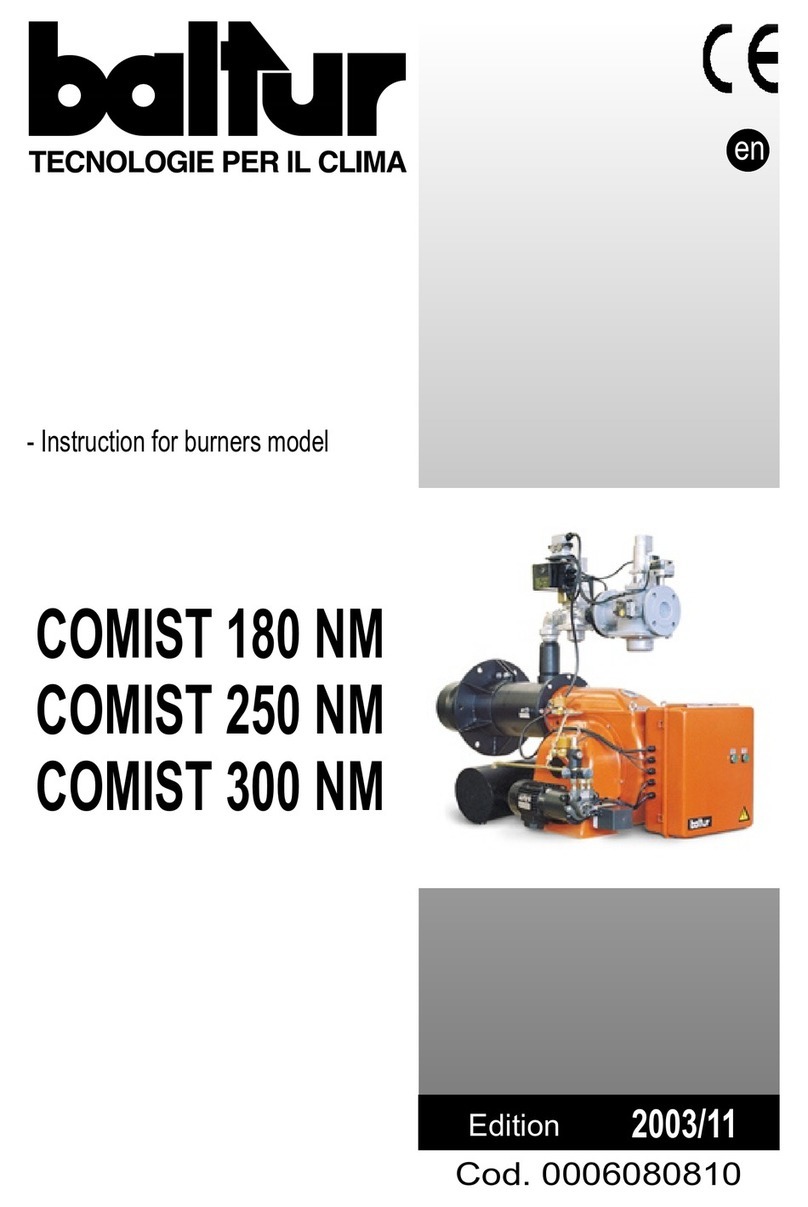
baltur
baltur COMIST 180 NM instructions

Riello
Riello RX 500 S PV manual
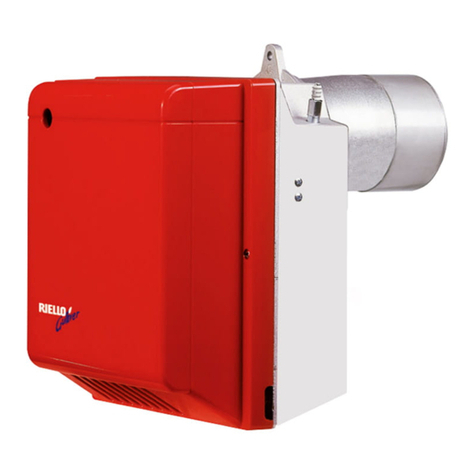
Riello
Riello Gulliver RG4D Installation, use and maintenance instructions