Mastervolt Whisper 6 User manual

MASTERVOLT
Snijdersbergweg 93
1105 AN Amsterdam
The Netherlands
Tel : +31-20-3422100
Fax: +31-20-6971006
http://www mastervolt com
INSTALLATION MANUAL
V2 October 2004
WHISPER 6 / 8 / 12
6 ULTRA
-3000 / 1500 RPM-
Marine diesel generating set 230V-50Hz
Digital Diesel Control
Art nr 50200361

2October 2004 / WHISPER 6/8/12 & 6 ULTRA / EN
This manual applies to the Mastervolt Whisper 6/8/12 and 6 ULTRA Marine
Diesel Generating set controlled by Digital Diesel Control first launched in April
2004 For earlier models refer to other manuals available on our website: www
mastervolt com
CONTENTS
1 INSTALLATION 3
1 1 Location 3
1 2 Instructions for optimal sound and vibration insulation 3
1 2 1 Steel base plate 3
1 2 2 Further recommendations 3
1 3 Ventilation 3
1 4 Connections 4
1 4 1 Fuel supply 4
1 4 2 Cooling 7
1 4 3 Exhaust system 9
1 4 4 Digital Diesel Control system 12 Volt 12
1 4 5 AC power system 230 Volt (120 Volt) 13
2 INSTALLATION SPECIFICATIONS 15
2 1 Installation table 15
2 2 Commission table 16
2 3 Technical data 17
2 4 Specification of the accessories 17
2 5 Installation materials 18
3 DIAGRAMS AND DRAWINGS 22
3 1 DC wiring diagram 22
3 2 Codes and colors 23
3 3 Wiring diagram electronic governor (optional) 24
3 4 AC wiring diagram Whisper 230V 50Hz 25
3 5 Remote panel dimensions 26
3 6 Whisper 6/8/12 and 6 ULTRA dimensions 27
CONTENTS

EN / WHISPER 6/8/12 & 6 ULTRA / October 2004 3
1 INSTALLATION
To ensure reliability and durability of the equipment, it is
very important that the installation is carried out with the
utmost care and attention To avoid problems, such as
temperature problems, noise levels, vibration, etc the
instructions set out in this manual must be followed and
all installation work must be carried out professionally
1.1 LOCATION
Since Whisper generating sets have extremely compact
dimensions, they can be installed in tight locations Plea-
se consider that even almost maintenance-free machi-
nery must still remain accessible
When selecting the location area to mount the generating
set, make sure there is sufficient room to carry out any
maintenance work The unit must be easily accessible on
the service side and on the distribution side to have ac-
cess to the V-belt
Please also note that in spite of the automatic oil pressu-
re sensor it is still essential that the oil level is checked
regularly
1.2 INSTRUCTIONS FOR OPTIMAL SOUND
AND VIBRATION INSULATION
Position the generating set as low as possible in the
vessel As the generating set already has secured to the
base frame by means of flexible engine mountings, the
frame can be mounted directly to the vessel’s main struc-
ture
1.2.1 S eel base pla e
However to keep resonant vibrations at a minimum, it is
possible to mount the generating set on a solid steel base
plate, approx 20 mm (3/4") weighing approx 60 kg or
50% of the weight of the generating set The engine
draws its inlet combustion air through several holes in the
capsule base Therefore the capsule must be fitted with
sufficient clearance between the capsule underside and
the base plate For the Whisper 6/8-3000rpm a steel
base plate is available with Mastervolt as an optional
accessory (ref fig 12, page 36)
1.2.2 Fur her recommenda ions
Whisper generating sets are standard equipped with a
"GRP" (Glass Reinforced Plastic) sound cover The ca-
nopy has been designed to give an effective sound insu-
lation For optimum sound and vibration dampening, the
following factors should be considered
1 Avoid mounting the generating set in close proximity
to thin walls or floors as that may resonate
2 Sound dampening is extremely poor if the generating
set is mounted on alight weight flimsy surface such
as plywood which will only amplify vibrations If
mounting on a thinner surface cannot be avoided, this
should at least be reinforced with stiffening struts or
ribbing If possible, holes should be drilled or cut
through the surface to help reduce the resonance
Covering the surrounding walls and floors with a
heavy coating plus foam will certainly improve the
situation
3 Never connect the base of the generating set directly
to bulkheads or tanks
1.3 VENTILATION
The generating set normally draws air from the engine
room Engine rooms with natural ventilation must have
vent openings of adequate size and location to enable
the generating set to operate without overheating To
allow an ample supply of air within the temperature limits
of the generating set an opening of at least 100 cm2is re-
quired
A "sealed" engine compartment must have a good
extraction ventilator to maintain reasonable engine room
temperatures High temperature of intake air reduces
engine performance and increases engine coolant tem-
peratures Air temperatures above 40°C reduce the engi-
ne power by 2% for each 5°C of rise To minimise these
effects the engine room temperature must not be more
than 15ºC above the outside ambient air temperature
Apply a combination of ventilators, blowers and air intake
ducting to meet the temperature limit The air inlet ducts
should run to the bottom of the engine room to clear
fumes from the bilge and to circulate fresh air Air outlets
should be at the top of the engine room to remove the
hottest air An engine room blower should be used as an
extraction ventilator to remove air from the engine room
In cases where it is impossible to meet the above mentio-
ned temperature limit by using machine room ventilation,
connections are to be made for an air inlet directly to the
enclosure With these connection the generating set can
be directly connected to an air duct
INSTALLATION

4October 2004 / WHISPER 6/8/12 & 6 ULTRA / EN
INSTALLATION
Air inlets should be louvered, where appropriate, to pro-
tect the engine room and to protect the generating set
from water spray As an extra precaution, the fitting of a
cowl ventilator with dorade box located as high as possi-
ble, is recommended
1.4 CONNECTIONS
The generating set comes supplied with all supply lines
and output cable (i e electric cables, cooling water con-
nections, exhaust, fuel lines etc ) already connected to
the engine and generator The supply lines are fed through
the capsule’s base The connections are marked as shown
in fig 1
All electrical connections, cable types and sizes must
comply to the appropriate national regulations Supplied
cables are rated for ambient temperatures up to 70°C If
the cables are required to meet higher temperature requi-
rements, they must be run through conduits
ATTENTION!
Before working (installation) on the system
read the section safety instructions
1.4.1 Fuel supply
1 FUEL TANK
Fuel tanks should be made of appropriate material
such as (stainless) steel or plastic Steel tanks should
not be galvanised or painted inside Condensation
can occur in metal tanks when temperature changes
Therefore, water accumulates at the bottom of the
tank and provisions should be made for the drainage
of this water
The tank will need a filling connection, a return con-
nection and an air ventilation connection which will
require protection against water entry
Some official regulations do not allow connection
points at the base of the fuel tank; in this instance
connections are to be made at the top of the tank with
internal tubing down to a few cm above the bottom of
the tank
EXHAUST (1)
40 mm REMOTE CABLE (2)
12x0,3 mm2
AC CABLE (3)
FUEL RETURN (6)
16 mm2
BATTERY - (7)
8 mm
FUEL IN (4)
8 mm
16 mm2
BATTERY + (5)
AIRVENT IN (10)
19 mm
AIRVENT OUT (9)
WATER IN (8)
19 mm
19 mm
40 mm
40 mm
EXHAUST (1)
EXHAUST (1)
REMOTE CABLE (2)
AC CABLE (3)
12x0,3 mm2
FUEL RETURN (6)
WATER IN (8)
19 mm
8 mm
BATTERY + (5)
25 mm2
8 mm
FUEL IN (4)
AIRVENT OUT (9)
19 mm
BATTERY - (7)
25mm2
19 mm
AIRVENT IN (10)
Afb. 1.
WHISPER 6/8
WHISPER 12/6 ULTRA

EN / WHISPER 6/8/12 & 6 ULTRA / October 2004 5
2 FUEL LIFT PUMP
The generating set itself is equipped with a fuel lift
pump; therefore the tank can be installed at a lower
level than the generating set The maximum suction
height is 1 m
If the pump has to lift the fuel higher than one meter
an external fuel lift pump must be installed The con-
trol board is already prepared to connect an extra fuel
pump
3 FUEL PIPES
When the tank is above the generating set we recom-
mend to end the return line on the top of the tank
When the return is on the top - in case of a leakage -
the return line cannot overflow because of siphoning
One will only need a fuel cock in the fuel supply line
Fig. 2.
1 Fuel return;
2 Fuel supply;
3 Prefilter / water separator (optional);
5 Fuel tank;
INSTALLATION

6October 2004 / WHISPER 6/8/12 & 6 ULTRA / EN
INSTALLATION
When the tank is below the generating set we recom-
mend to end the return line on the bottom of the tank
(A) below the inlet of the supply line to discharge
under the lowest fuel level This prevents air getting
into the fuel line Here also one need only a fuel cock
in the supply line
Both supply and return fuel pipe lines should be
appropriate material and 8 mm outer diameter tubing
The quality of the tubing of fuel pipes could be sub-
mitted to local regulations depending on the applica-
tion of the vessel
The fuel pipes can be plumbed to the flexible hoses
which are on the generating set and have a connec-
tion to fit to 8 mm pipe This fuel lines fulfils CE
standards and are according to ISO 7840 A2
It is important to avoid bends in the pipes, as they
could trap air bubbles The return pipe should never
be connected to the suction pipe Other consumers of
diesel fuel, such as the propulsion engine and hea-
ters, have to be connected to separate suction and
return pipes
4 FUEL FILTERS
A fine fuel filter is installed which requires maintenan-
ce Mastervolt advises to install an extra fuel filter/
water fuel separator near the fuel tank
Before starting your generating set for the first time
follow the fuel system bleeding procedure in the users
manual
Fig. 3.
1 Fuel return;
2 Fuel supply;
3 Prefilter / water separator (optional);
4 Extra fuel lift pump (optional);
5 Fuel tank

EN / WHISPER 6/8/12 & 6 ULTRA / October 2004 7
1.4.2 Cooling
Intercooling is based on a raw water pump, heat exchan-
ger and water-injected exhaust Cooling liquid in the
internal cooling system is cooled in a heatexchanger by
outboard water (raw water or seawater) After the raw
water is warmed up in the heatexchanger it is dumped
overboard by injecting it in the exhaust
The generating set should have its own sea water
(coolant water) inlet and should not be connected to any
other engine systems A properly installed cooling system
is critical to keep engine temperatures within an accepta-
ble range Ensure that the installation complies to the
following installation instructions
1 THE INTERNAL COOLING SYSTEM
The internal cooling system should be filled with
cooling liquid (Refer to the users manual 2 5 12)
When the engine becomes hot the liquid expands and
the system is pressurised After the pressure becomes
to high the release valve in the filling cap on the
manifold opens and the expanding liquid is pressed
into the expansion tank that is in the delivery Also the
air in the system that is collected at the top of the
manifold is released in this way When the liquid cools
down there will be underpressure An other valve
opens and the liquid is sucked into the manifold again
This system works only when there is enough liquid
initially This has to be checked when commissioning
the generator set By filling up the expansion tank
when necessary there will always be enough liquid in
the system The hose that is in the delivery has to be
connected to the connection on the side of the filling
cap This hose is made of heat resistant plastic and is
not sensitive for kinks
The hose goes through a hole that has to be drilled in
the lower part of the canopy close to the place where
the tank is mounted
The tank has to be placed close to the generator
When it is mounted above the top of the manifold the
liquid in the tank will be drained when the cap on the
manifold is taken off
When keel cooling or radiator cooling is applied the
system will not be pressurised A cap without release
valve should be applied Refer to the special manual
for these applications
2 RAW WATER SUPPLY
For raw water supply the following installation mate-
rials are required: -a skin fitting - a sea cock - a water
strainer - hoses and clamps In order to keep the suc-
tion resistance in the line at a minimum, the sea water
intake system (i e sea cock, tru-hull fitting, inlet filter,
etc ) must have an inner diameter of at least 19 mm
diameter (3/4") The suction hose should be kept as
short as possible Raw water plumbing should avoid
bends as much as possible
1
2
34
5
7
6
Min
24"
60 cm
2"
5 cm
Max
60"
150 cm
Min
24"
60 cm
Fig. 4b. 1 Water level;
2 Water/exhaust separator;
3 Seacock;
4 Waterlock;
5 Air vent;
6 Water strainer;
7 Seacock
Afb. 4a.
INSTALLATION

8October 2004 / WHISPER 6/8/12 & 6 ULTRA / EN
INSTALLATION
Restriction of raw water flow, caused by kinked hoses,
undersized pipes or connections, will reduce the
engine cooling capability This is the main cause for
overheating of an engine
After running the generating set for the first time, check
the coolant flow rate using a stopwatch and by holding
a pail of a known volume under the wet exhaust outlet
The flow rate should be according to the data in the
users manual
3 INSTALLATION OF THROUGH HULL FITTING
It is good practice for yachts to use a hull inlet fitting
with an integrated strainer (water scoop) For propul-
sion engines in motorboats the water scoop is often
mounted against the sailing direction to induce more
water intake for cooling
This should not be done in the case of a
generating set! When ailing at higher
speeds, water will be forced into the inlet
and your generating set will overflow!
On motorboats and on sailing boats the water scoop
for a generating set should be fitted with the opening
faced backwards to prevent water being forced in
during sailing
4 WATER STRAINER
Use an appropriate water strainer with connections of
19 mm (3/4") Install the water strainer in a well ac-
cessible position, (ref to fig 4 - 6) 15 cm above the
waterline
5 SIPHON BREAKER (AIR VENT)
When the point of water injection is below the water-
line, then - when the engine is stopped - there is a
risk that the cooling water may enter the engine as a
result of siphoning To avoid this happening, the ge-
nerating set is designed to accommodate a siphon
breaker (air vent) In the standard delivery the con-
nections are bypassed Hose of 19 mm (3/4") inner
diameter should be used
If the generating set cannot be mounted such that the
bottom of the generating set is placed above the
waterline, an air vent must be installed
Extend the water hose of the by-pass 600 mm above
waterline and install an air vent Ideally, the air vent
should be mounted above the yacht keel center line
(i e to minimize the influence of swaying on the water
intake) The hose of the drain should go downwards
Water must flow out freely; air must flow in freely as
well
Fast motorboats will lay deeper when sailing at large
speed and can cause pressure on the waterinlet This
should be avoided to prevent fleeding the engine
If the air vent is clogged the water hoses
will not be vented when the generating set
has stopped and water can be forced into
the engine This leads to immediate engine
problems and eventually severe damage!
DAMAGE CAUSED BY THE INGRESS OF WATER
INTO THE ENGINE IS NEVER COVERED BY
WARRANTEE.
On the valve is a little hose to drain a little water that
could be spilled from the valve This hose should go
down and may not end under water, because it
should ventilate air into the valve to break the
siphoning
flow direction
sailing direction
WRONG!
thru-vessel inlet
Fig. 5.
Fig. 6.

EN / WHISPER 6/8/12 & 6 ULTRA / October 2004 9
Check the air vent at regular intervals Open, clean
and lubricate the valve as required
1.4.3 Exhaus sys em
Water is injected in the exhaust system of the generating
set In this way the cooling water that has passed the
heat exchanger is mixed with the exhaust gases
Temperature and volume of the gases are thereby
reduced considerably, so that a rubber exhaust hose can
be used and the level of noise is reduced as well
1 STANDARD EXHAUST SYSTEM INSTALLATION
The generating set exhaust system must remain
completely independent and separate from the ex-
haust system of any other engine on board A water
lock prevents the generating set from being flooded
by outside sea water and should be installed as close
to the generating set as possible The lock must be
large enough to hold the entire water volume held in
the hose from the top of the goose neck to the water
lock The water lock must be installed at the lowest
point of the exhaust system (ref to fig 7-1) The ex-
haust hose must have an inner diameter of 40 mm
The exhaust system must be installed so that the
back pressure inside the exhaust does not exceed
0 07 bar (1 psi = 70 cm watercolumn) and total length
from generator to the top of the goose neck or
water/gasseparator does not exceed 3m (10 ft )
(Refer to paragraph 5 4 3 of the users manual
The exhaust hose descends from the capsule to the
water lock Then the hose rises via the "goose neck"
to the through-hull exhaust outlet, situated minimum
50 mm above the water line (ref to fig 7-5 The
"goose neck" must be vertical and situated preferable
along the ship’s keel center line If the generating set
is mounted less than 600 mm (24") above the
waterline, a "goose neck" must be installed to prevent
the engine from overflowing It is recommended to
install an extra muffler close to the through-hull fitting
A
B
Minimal
24"
60 cm
Maximal
60"
150 cm
max length A - B = 10 ft (3 m )
2"
5 cm
Fig. 7.
1 Exhaust water lock;
2 Exhaust outlet muffler;
3 Exhaust line Ø 40 mm;
4 Goose neck
5 Through-hull exhaust outlet Ø 40 mm;
6 Water level
INSTALLATION

10 October 2004 / WHISPER 6/8/12 & 6 ULTRA / EN
INSTALLATION
2 "SUPER SILENT" EXHAUST SYSTEM
In order to reduce the noise level of the generating
set to a minimum, an option to reduce the exhaust
noise further (especially exhaust water splashing) is
an exhaust/water separator The exhaust/water sepa-
rator allows the cooling water to be ejected through a
line (A) separate from the exhaust fumes and also
functions as a goose neck to prevent water from
flooding the engine If the exhaust/water separator is
mounted more than 600 mm above the water level an
additional goose neck is not required
If the through-hull exhaust outlet has to be mounted
far (total length exhaust piping from generator to top
of goose neck (waterseparator) is more than 3 m)
from the generating set, an exhaust/water separator
must definitely be installed The sea water from the
separator must then run down along the shortest pos-
sible path to the through-hull outlet Only after the
exhaust/water separator the exhaust hose may have
alength of over 7,5 m if the exhaust hose diameter is
also increased from 40 mm to 50 mm in order to re-
duce the back pressure (ref to fig 9)
Hohwever watertraps should be avoided as the
fumes still contains water and this should not
accumulate in bents (Refer to fig 8a) An additional
outlet exhaust muffler close to the hull outlet will help
further to reduce noise emission
water
level
max
150 cm
min
60 cm
40 mm
40 mm
40 mm
A
max 10 cm
Fig. 8.
Fig. 8a.

EN / WHISPER 6/8/12 & 6 ULTRA / October 2004 11
A
B
Max. length
A - B = 3 m.
ø 40 mm
ø 40 mm
up to 3 m. ø 40 mm
3-10 m. ø 50 mm
Fig. 9.
Fig. 10.
If the generating set and the exhaust system have
been installed correctly, neighboring boats will not be
disturbed by generating set noise, With the "super
silent" exhaust system, generating set noises are
almost inaudible For optimal noise reduction, the sea
water outlet from the exhaust/water separator (center
outlet on the unit) should be installed below the water
level to eliminate noisy splashing of the effluent sea
water
The through-hull outlet for the exhaust fumes should
not direct the fumes directly toward the water surface
as this will cause excessive noise (ref to fig 10)
Do not direct the outlet directly toward the
water surface
INSTALLATION

12 October 2004 / WHISPER 6/8/12 & 6 ULTRA / EN
INSTALLATION
1.4.4 Digi al Diesel Con rol sys em (12 Vol )
1 DIGITAL DIESEL CONTROL SYSTEM
The electrical control system is standard in 12 Volt
with negative earth Non- earth return is available as
an option for aluminium vessels to prevent corrosion
All electrical wiring has been prepared on the genera-
ting set to the control panel prior to despatch from the
factory The engine is controlled by a very advanced
microprocessor based system: Digital Diesel Control
The “black box” containing the microprocessor is
located on top of the alternator
A local control panel is on the generating set
Remo e con rol
A remote control panel also containing a
microprocessor is in the delivery A 15 m intermediate
8-pole communication cable is in the standard supply
too If necessary an optional longer (max 30 m)
intermediate cable can be connected if the standard
length does not suit the required distance When a
longer distance than 30 m is required, consult the
Mastervolt service department for advice Refer to fig
11
One can mount the control panel after drilling a hole
in the dashboard using the plastic cover Refer to the
dimensional drawing in paragraph 3 5 The panel
without the plastic cover fits the Mastervision modular
panel system
More remote control panels (slave panels) can be put
in parallel by using the modular connectors on the
back of the units As a slave one can use the same
panel offering all functions again It is also possible to
use an old or new type slave panel only to start and
stop the generator
Old type remote panels and system panels can be
connected by means of the green connector
Pay attention to the colour codes as indicated in fig
12 when fitting cable to the green connector Some
software versions in old system panels (supplied
before may 2004) could conflict with the software in
the DDC and an up-date of the software of the
system panel could be necessary When this is the
case consult to the Mastervolt service department for
advice
When using the factory settings, installation is very
simple: just plug the remote cable into the remote and
the generator is ready to use Refer to fig 12
Acous ic alarm or warning lamp
One can connect an external max 150 mAmp relay to
generate an acoustic warning or applying a warning
lamp etc Be aware of polarity as some relays has a
diode inside and should be connected plus to plus en
minus to minus as indicated Refer to fig 12
Au oma ic s ar /s op
Mas ervol canno be held responsible for
damage caused by he una ended running
genera or using he au o-s ar /s op mode or
in erval mode.
Using he au o-s ar /s op (in erval) mode he
genera or can s ar unexpec edly. When working
on he elec rical sys em, he 3 Amp fuse mus be
removed from he con rol panel and he ba ery
plus cable mus be removed from he ba ery.
The Mastervolt Digital Diesel Control system offers
several options for automatic starting and stopping
Fig. 11.
J3
MASTERVOLT
WRP/2
Whisper Remote Panel
TAILORMADE ENERGY
+-
123456789101112
+-
SENSE BAT. 2
12
9
10
11
6
7
8
3
4
5
1
2
REMOTE CABLE
REMOTE CABLE
WARNING RELAY
MAX. 150 mA
BLACK
RED/BLUE
GREY
GREY/PINK
WHITE
BLUE
PURPLE
PINK
YELLOW
BROWN
GREEN
RED
WIRING COLOURS
Fig. 12.

EN / WHISPER 6/8/12 & 6 ULTRA / October 2004 13
Access to this menu and other menus could be
blocked For blocking and setting up this options refer
to the APPENDIX of the DDC users manual
One of these options is to monitor a second battery
(Not being the starter battery) to start the generator
automatically when the voltage of this battery drops
below a certain setting
Other names for this second battery are “auxiliary
battery”, “service battery”, ”users battery” or
“consumers battery” We will refer to this battery as
“the second battery”(BAT2) In some menus the
starter battery could be indicated as “the first battery”
(BAT1)
A sense wire to monitor the second battery should be
connected (Attention polarity!) to the connector on the
back of the remote panel Refer to fig 12 The sense
wires must be connected directly on the second
battery before a main switch and be protected by a 3
Amps fuse
(Monitoring the generator starter battery does not
require an extra sense connection)
Settings
When one want to apply other settings than the
factory settings refer to the DDC users manual,
especially to the APPENDIX
2 STARTER BATTERY
For starting, the Whisper requires a battery with a
capacity of at least 85 Ah The generating set can be
connected with the main engine battery or with its
own battery
We strongly recommend to use a separate battery for
the generating set and to keep the wiring system for
the propulsion engine and the domestic DC supply
system completely separate and individually connec-
ted to separate batteries
However the negative of all the batteries on the
vessel should be interconnected (when on earth) to
avoid difference in the voltage level of the earth on
different places causing trouble to electronic devices
which might be in the system
The above recommendation is not valid for ships
having the starter battery of the propulsion engine or
other auxiliary equipment positive grounded When
this is the case an expert should be consulted
A battery switch may be used to interrupt the positive
connection
The starter battery is charged by the alternator on the
engine An additional battery charger will help to keep
the battery in good condition when the generating set
in not used A battery charger in not included in the
standard supply A high efficiency battery charging
unit can be ordered from Mastervolt which is able to
charge both the ship’s main battery and the starter
battery Also a small charger can be used for the sta-
ter battery only, such s IVO SMART 12/10
3 OTHER RECOMMENDATIONS AND WARNINGS
The battery should be secured for seagoing condi-
tions and the terminals should be insulated For extra
safety the battery can be enclosed in a wooden,
plastic, Fiberglas etc (non metal) box Even when the
earth return system is applied a negative battery ca-
ble should be used and the vessel should not to be
used as a conductor
The battery cables are supplied in a standard length
of 1 5 m, if longer cables are required a larger cross
sectional area should be considered to compensate
for voltage reduction
When two batteries are used in series to provide a 24
INSTALLATION
12V
12V
IVO 12/10
IVO 12/10
AB
230VAC
230VAC
Fig. 11.

14 October 2004 / WHISPER 6/8/12 & 6 ULTRA / EN
INSTALLATION SPECIFICATIOINS
Volt supply system, never take off 12 Volt (starting)
power from one of these batteries This will result in
sever damage to the batteries within short time
Disconnect the battery leads if electrical welding is to
be carried out, otherwise damage will be caused to
the diodes of the alternator
As explosive hydrogen gases are dischar-
ged during charging, the battery should be
located in a well ventilated room Ensure
that the supplied battery cable connectors
are properly fitted and never remove du-
ring or shortly after charging as sparking
can occur, which may ignite the hydrogen
gasses
1.4.5 AC power sys em (230/ Vol )
Before working (installation) on the system
read the sections on safety in the users
manual
Be sure that all electrical installations (including all safety
systems) comply with all required regulations of the local
authorities All electrical safety/shutdown and circuit
breaking system have to be installed onboard as the
generating set itself cannot be equipped with such equip-
ment for every possible variation
The vessel’s power supply system should be suitable
and safe for the AC voltage which is applied and the
power that will be generated Special attention has to be
paid on dividing the system in branches which are fused
individually
It is absolutely essential that each and every circuit in the
on-board electrical system is properly installed by a
qualified electrician
1 FUSE
An input fuse (from the generating set to the system)
should be installed to protect the installed electrical
system
For the Whispers the maximum single phase current
at 230V is 25A (6), 32A (8) or 48A(12)
The fuses must be of the slow reacting type For elec-
trical motors connected to the system, a motor pro-
tection switch must be installed
2 GROUNDING
The AC alternator windings are not grounded
The housing of the alternator and all other metal parts
are grounded
To make a connection between “neutral” and “ground”
could be necessary as part of a specific insulation
failure protection system
Small pleasure craft in Europe is submitted to The
Recreational Craft Directive 94/25/EC The guidelines
of this directive refer to (ISO 13297)
When the installation comply to this standard the
“neutral” and “ground” should be connected on the
generating set by connecting the blue (neutral) wire
with the terminal on which the yellow/green wire is
connected
Warnings:
In all situations the transfer switches between
shore, inverter and generator should switch
both neutral and L1 Of course this is the case
when using a Mastervolt Masterswitch
Be aware that insulation protection systems can be
different for different applications and even within the
ship there could be different standards for different
spaces We did refer to the Recreational Craft Directive
that applies to pleasure craft up to 24 m of length
Sometimes one has to comply with other standards such
as the rules of certification societies like Lloyds Register
of Shipping or Veritas, regulations for the protection of
personal, building legislation, etc It is of the greatest
importance to have expert advice on this issue
For safety reasons connect the main ships ground to
negative point of the generating set start battery When a
ungrounded DC system or positive grounded DC system
is applied the battery negative should not be connected
to then main ships ground
3 CABLE
For the power cable we recommend the use of 3 wire
oil resistant cable with a sufficient cross sectional
area One wire for earth is included For very long ca-
bles it is recommended to apply cables with a larger
cross section than the above mentioned
4 TRANSFER SWITCH
A power source selector switch much be installed
between the generating set and the ship’s electrical
supply system This switch must ensure that all AC
consumers can be switched off at once This switch

2 INSTALLATION
SPECIFICATIONS
2.1 WHISPER 6/8/12/6 ULTRA INSTALLATION
TABLE
1 Install a steel foundation plate between ship’s hull
and generating set, with 4 shock mounts (ref to fig
12) ‘foundation plate’(optional for Whisper 6 / 8)
2 Mount the generating set directly to the foundation
plate
3 Connect the (sea) water inlet to the strainer
4 Connect exhaust system
5 Connect a siphon breaker or ‘air vent’ into cooling cir-
cuit, if necessary
6 Connect ‘fuel supply line’ to the water separator/ fuel
filter
7 Connect ‘fuel return line’ to the fuel tank
8 Connect remote panel (just plug in)
9 Connect the AC cable from the AC box to the power
source selector or masterswitch
10 Connect plus and minus from the 12V starter battery
to the battery cables
11 Install a Mastervolt battery charger (optional)
EN / WHISPER 6/8/12 & 6 ULTRA / October 2004 15
should also be installed to keep the generating set
and shore (grid) power systems separate
Transfer switches - to switch over from shore to ship
or from generating set to inverter - should be well de-
signed to switch over all wires including neutral (and
not only phases or line) and there should be provi-
sions with the aid of timers to prevent relays from
clattering
Mastervolt advises to install a MASTERSWITCH as a
power source selector This works automatically when
the generating set is not running the input remains in
the shore position and as soon as the generating set
is running the masterswitch switches automatically
after 10 seconds delay time over to the generating
set position
INSTALLATION SPECIFICATIONS
Fig. 12.

16 October 2004 / WHISPER 6/8/12 & 6 ULTRA / EN
2.2 COMMISSION TABLE
1 Check if a siphon breaker (air vent) is necessary and
has been installed
2 Open the seawater inlet valve and check all water
connections Check if the strainer is installed above
the seawater level
3 Check if the exhaust system is properly installed
Check maximum lentgh of exhaust hose, diameter of
exhaust hose, position of waterlock, maximum lift
Also check the minimum required height of 600 mm
above sea level of the exhaust loop (goose neck)
4 Open the seawater outlet valve and check all water
connections
5 Check the AC cables and the grounding
6 Check if an AC breaker is installed before or after the
power source selector When there is only a circuit
breaker, use it to disconnect the generating set from
the grid
7 Check all DC connections, check if the battery switch/
circuit breaker is closed
8 Open the fuel valve to bleed the fuel system Check if
there are no air leaks in the fuel supply line, and
check if the lift of the fuel is less than 1 meter Check
if there is no air in the water fuel separator
9 Check if the air intake in the canopy is not blocked
10 Check the oil level and color of the oil
Check the coolant level
11 To bleed the fuel system push the startbutton on the
local control (not on the remote) and hold at least 5
seconds and as long as necessary to bleed the
system
12 Preheat the engine by pushing the glow button for
ten seconds Start the engine by pushing the start
button until the set is running Do not push the start
button longer than 5-10 seconds
13 Check when the generating set is running, the delay
of 5 to 10 seconds in the power source selector
transfer
14 Check voltage and frequency under ‘no load’ condi-
tions
15 Check voltage and frequency under ‘full load’ condi-
tions
16 Check if the battery charger of the generating set is
working (max 14 2 Volt)
17 Close the sound shield and check the noise level
18 Stop the generating set and check the engine again
for leakages of oil, fuel or water
Installation checklist available on our website
Extended commission form available on our website
(www mastervolt com)
INSTALLATION SPECIFICATIONS

EN / WHISPER 6/8/12 & 6 ULTRA / October 2004 17
INSTALLATION SPECIFICATIONS
2.3 INSTALLATION SPECIFICATIONS WHISPER 6/8/12 - 3000 RPM; 6 ULTRA
TECHNICAL DATA
Dimensions wxdxh 6/8: 660x495x550 mm / 12/6 ULTRA:810x525x615
Weight 6/8:178 kg / 12:210 kg / 6 ULTRA: 225 kg
including sound shield
Max operation angle 25°
Remote panel 15 m cable, indicating: Digital Diesel Control system
Battery capacity min 12V, 60 Ah
Fuel consumption 1 5-4 l/hr, load dependent
Lift fuel pump electric driven 12 V DC, max lift 1 m
Cooling indirect cooling
Cooling pump raw water Mastervolt self priming impeller pump, PTO driven, type M
Minimum water supply 9-15 l/min
Crank case lube oil capacity, 6/8:2 4 l + 0 5 oil filter, total 2 9 l ;
12/6 ULTRA:3 6l + 0 5 oil filter total 4 1l
Alternator synchronous brushless, maintenance free water cooled
Voltage regulation 6/8 capacitor, 12/6 ULTRA capacitor + AVR
Output power at 6: 5 2 kW, 230V 50 Hz
power factor cos phi =1 6 ULTRA: 5,7 kW 230V 50Hz
8: 6 4 kW, 230V 50Hz
12: 10 5 kW, 230V 50Hz
Battery charger alternator including regulator (40 Amps)
2.4 SPECIFICATION OF THE ACCESSORIES
Water scoop 3/4” = 19 mm
Inlet valve 3/4" in 19 mm out
Water strainer 19 mm in, 19 mm out
Air vent 19 mm
Inlet suction hose 19 mm
Fuel filter/water separator 30 micron
Fuel inlet and return 8 mm
Exhaust hose in/out Ø 40 mm
Water lock Ø 40 mm
Water/gas separator Ø 40 mm
Anti shock mounts Art nr 50230552
Foundation plate min 60 kg (only 6/8)
Battery charger (optional) IVO SMART 12/10; 12V / 10 Amps, 230V/50Hz

INSTALLATION MATERIALS
18 October 2004 / WHISPER 6/8/12 & 6 ULTRA / EN
2.5 INSTALLATION MATERIALS WHISPER 6/8/12/6 ULTRA
WATER INLET KIT 3/4”(20mm)
no qtt articleno description dimensions
1 1 50230052 Intake strainer 3/4
2 1 50230042 Lever operated ball valve FF 3/4
3 1 50221004 Male hose connection 3/4x20
3 4 50221502 Hose clamps 19-29 mm
5 3 50220056 Outboard cooling water hose 20x28 mm
6 2 50221007 Male hose connection 1/2x20
7 1 50230060 Nickel plated brass intake strainer 1/2
8 1 50230067 Mounting bracket waterstrainer
TOTAL 50230211 WATER INLET KIT 20 mm
AIR VENT KIT 3/4” (20mm)
no qtt articleno description dimensions
4 4 50221502 Hose clamps 19-29 mm
5 3 50220056 Outboard cooling water hose 20x28 mm
11 2 50221031 Bend male type with hose connection 1/2x20
12 1 50221042 TEE fittings 1/2
13 1 50230001 Syphon breaker valve 1/2
14 1 50221001 Male hose connection 3/8x13
15 1 50221521 Hose clamps 12-20 mm
16 1,5 50220055 Outboard cooling water hose 12x18,2 mm
TOTAL 50230212 AIR VENT KIT 20 mm
EXHAUST KIT 40 mm
no qtt articleno description dimensions
21 1 50221481 Hose connector 40 mm
22 5 50221506 Hose clamps 44-56 mm
23 3 50220033 Marine exhaust hose 40 mm inw
24 1 50230071 Waterlock 40 mm
25 1 50230038 Brass through hull fitting hose connection 1 1/4x40
TOTAL 50230203 EXHAUST KIT 40 mm
OPTIONAL INSTALLATION MATERIALS
no qtt articleno description dimensions
21A 1 50201830 Elbow 90 degr adapter exhaust hose 40 mm
22 2 50221506 Hose clamps 44-56 mm
WATER SEPERATOR KIT 40 mm
no qtt articleno description dimensions
22 4 50221506 Hose clamps 44-56 mm
23 2,5 50220033 Marine exhaust hose 40 mm inw
31 1 50221015 Male hose connection 1 1/4 x 40
32 1 50230044 Lever operated ball valve FF 1 1/4
33 1 50230033 Brass through hull fitting 1/1/4x70
34 1 50230080 Water exhaust fumes seperator 40-40-40
35 4 50201121 Vibration mounting 25x30 mm M8
36 4 50211152 Bolt M8x16
37 4 50211465 Nut M8
38 8 50211405 Washer M8
39 8 50211445 Lock washer M8
TOTAL 50230204 WATER SEPERATOR KIT

INSTALLATION MATERIALS
EN / WHISPER 6/8/12 & 6 ULTRA / October 2004 19
FUEL KIT
no qtt articleno description dimensions
41 2 50221203 Straight coupling 8 mm
42 1 50230090 Fuel strainer/water seperator M14x1,5 mm
43 2 50221618 Parallel male stud coupling M14 - 8 mm
44 2 50221644 Reducing male nipple M14-M16 60 gr
45 2 50221615 Hose connection 8 mm
46 2 50221616 Nut coupling M16x1,5 mm
47 1 50221252 Nipple hose pipe 8 mm
48 4 50221522 Hose clamps 10-16 mm
49 2 50221632 Gasket ring 14x20x1,5 mm
TOTAL 50230205 FUEL KIT
OPTINAL INSTALLATION MATERIALS
no qtt articleno description dimensions
50 1 50222020 Copper fuel pipe 6x8 mm
51 1 50220063 Fuel hose 8x16 mm
BATTERY INSTALLATION KIT 85 Ah
no qtt articleno description dimensions
51 1 64000850 Battery 85Ah
52 1 43011030 Battery charger
53 1 68060100 Battery terminal + M8
54 1 68060200 Battery terminal - M8
55 1 68456902 Isolation cap
56 1 68456914 Isolation cap
57 1 79009005 Battery swich 250 Amp
58 4 6503001608 Cable connectors M8x16
58 4 6503002508 Cable connectors M8x25
TOTAL 50230216 BATTERY INSTALLATION KIT 85 Ah
BASE PLATE KIT 6/8 (3000 rpm)
no qtt articleno description dimensions
61 4 50230552 Rubber mountings M12
62 1 50230014 Base plate Whisper 6/8
63 1 50230011 Fastener kit base plate
TOTAL 50230209 BASE PLATE KIT 6/8
RUBBER MOUNTING KIT
no qtt articleno description dimensions
64 1 50230015 Fastener kit rubber mountings
61 4 50230552 Rubber mountings M12
TOTAL 50230217 RUBBER MOUNTING KIT

20 October 2004 / WHISPER 6/8/12 & 6 ULTRA / EN
INSTALLATION MATERIALS
- Fuel kit
- Battery installation kit
- Base plate kit
Whisper 6/8/12/6 ULTRA
Included are all fittings to fit copper pipes
or rubber ful hoses, or both
Other manuals for Whisper 6
12
This manual suits for next models
3
Table of contents
Other Mastervolt Portable Generator manuals
Popular Portable Generator manuals by other brands
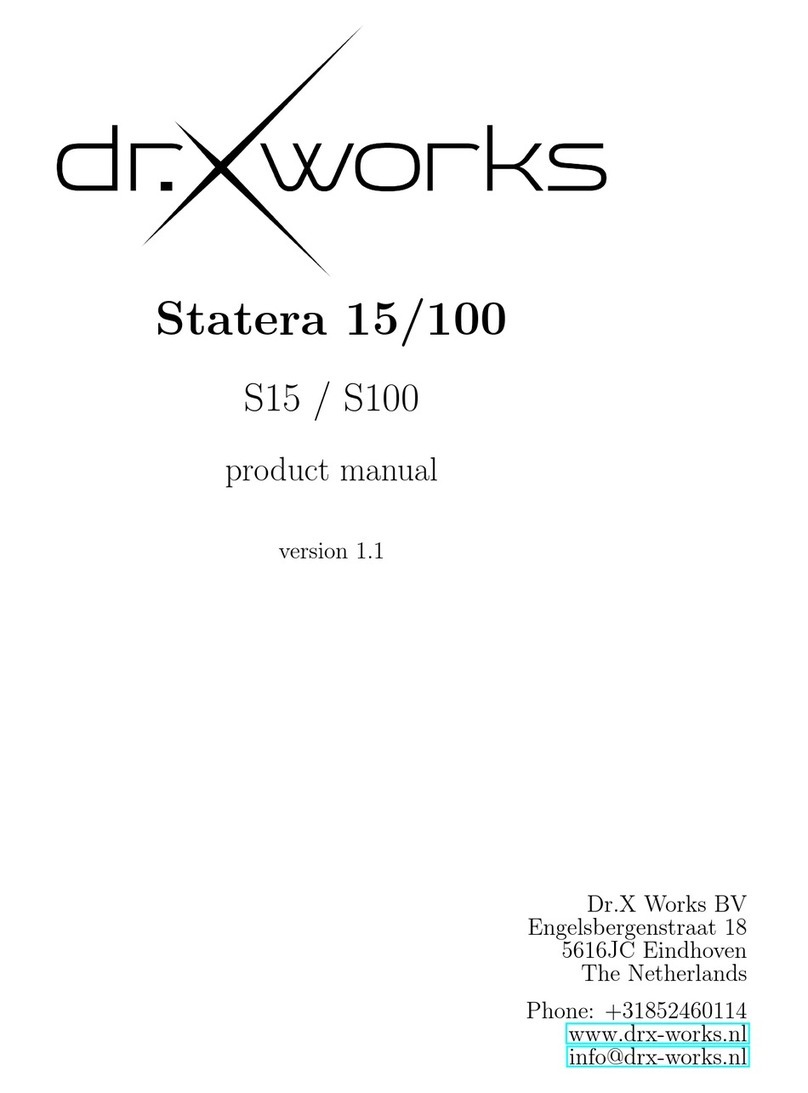
Dr.X Works
Dr.X Works Statera 15/100 product manual
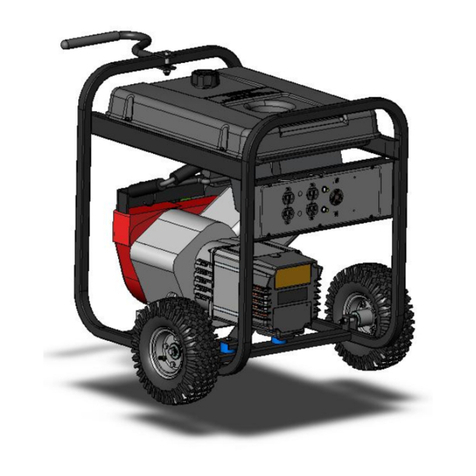
Powermate
Powermate Black Max PM0535001 manual
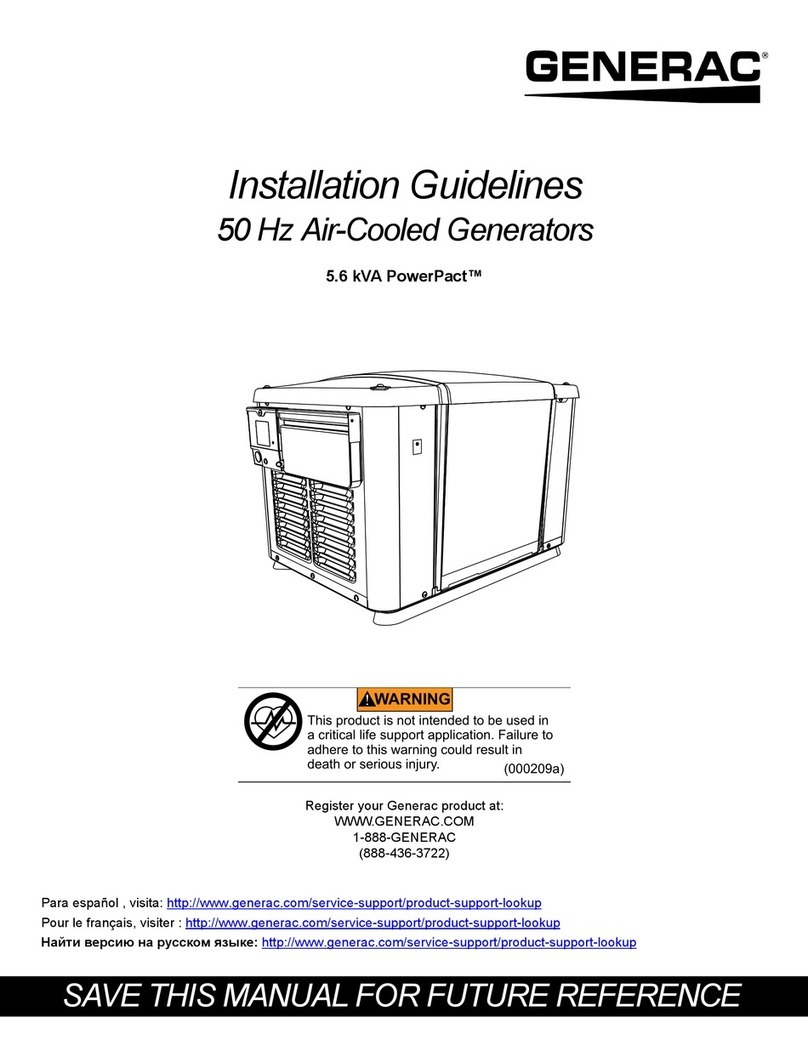
Generac Power Systems
Generac Power Systems PowerPact G0065201 Installation guidelines
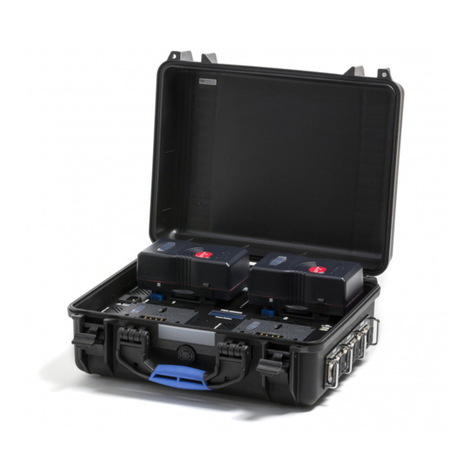
Blueshape
Blueshape Energy inside PWS-RUGGED operating instructions
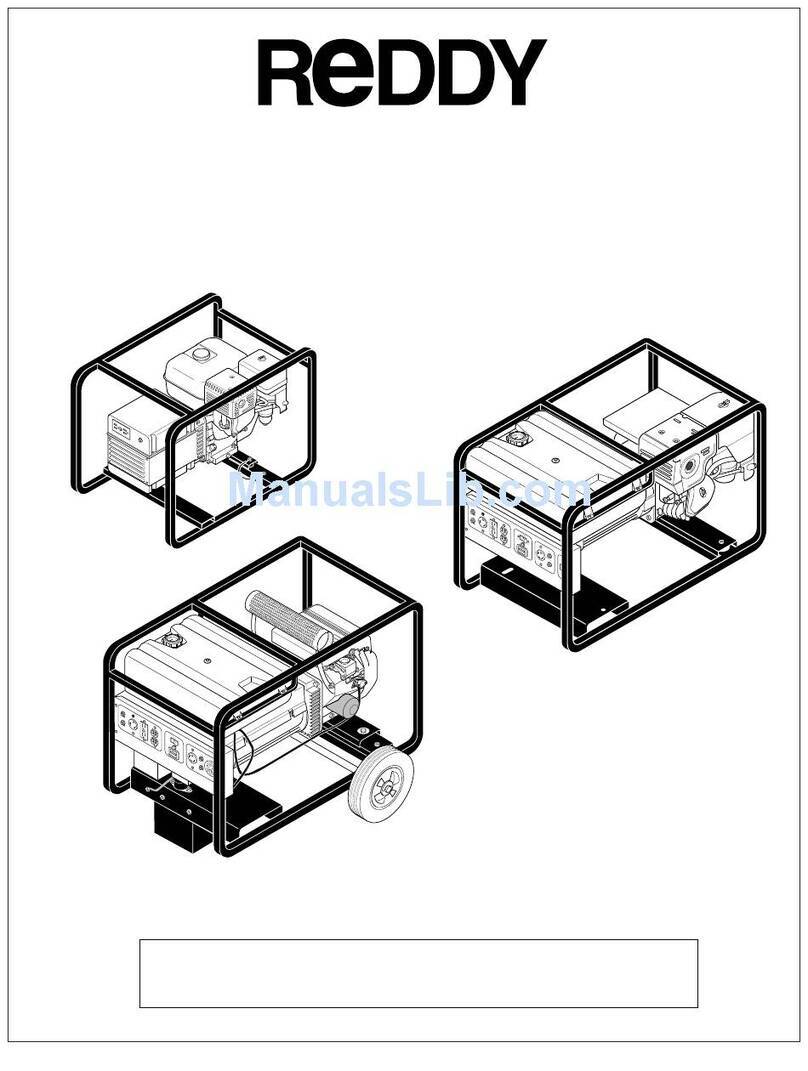
Desa
Desa Reddy RGH3000 OWNER'S OPERATION AND INSTALLATION MANUAL

Black Max
Black Max BM903650R quick start guide