Mercury DS-18 User manual

Mercury Floor Machines, Inc.
New Equipment Warranty
Limited Warranty
Mercury Floor Machines, Inc. warrants new equipment against defects in material and
workmanship under normal use and service to the original purchaser. Any statutory implied
warranties, including any warranty of merchantability or tness for a particular purpose, are
expressly limited to the duration of this written warranty. Mercury Floor Machines, Inc. will not be
liable for any other damages, including but not limited to indirect or special consequential damages
arising out of or in connection with the furnishing, performance, use or inability to use the machine.
This remedy shall be the exclusive remedy of the purchaser. The warranty period is subject to the
conditions stated below.
1-Year Motor, 1-Year Service Labor
Mercury Floor Machines, Inc. warrants electric motors on all Mercury Floor Machines to be free
from defects in material and workmanship, under normal use and service for one (1) year to the
original purchaser. Parts replaced or repaired under this warranty are warranted for the remainder
of the original warranty period. Service labor charges are covered for one (1) year from the date of
purchase, when performed by a Mercury-authorized service provider. Freight charges to and from
this service provider will be covered for ninety (90) days from the purchase date. After this ninety
(90) day period, these freight charges will be paid by the equipment owner. Travel expenses are not
covered.
Wear Items on all Machines
Critical Wear Items - bearings, capacitors, clutches, pulleys, rectiers, relays, switches, wheels,
tires and casters are warranted for manufacturing defects for one (1) year from the purchase date.
Normal Wear Items - belts, brushes, bumpers carbon brushes, cords, nishes, squeegees, actuating
cables and gaskets are warranted for manufacturing defects for ninety (90) days from the purchase
date.
All warranties of motors and associated components will be voided: if the machine is used as
a oor sander; if the machines is serviced by anyone other than a Mercury-authorized service
provider; if the machine is mechanically modied; or if the machine is misused or abused.
The warranty starts on the purchase date by the original purchaser from an authorized Mercury
Floor Machines, Inc. distributor, subject to proof of purchase. The machine must be registered
immediately following its purchase. The machine registration form may be completed online
at www.mercuryoormachines.com/registration.aspx or contact Mercury Floor Machines for a
registration card. If proof of purchase cannot be identied, the warranty start date is ninety (90)
days after the date of sale to an authorized Mercury Floor Machines, Inc. distributor.
Scrub an
Entire Floor
with One
Machine!
Design and Engineering Features:
• Heavy-duty,highqualitycomponentsprepare
oorstoberenishedinhalfthetimecomparedto
conventionalstrippingprocess.
• Chemical-freestrippingusedforrenishingwood
oorsandscrubbing.
• Cleansedgesandcornersineveryroom–nostripper
run-offandnoruinedoorsunderdoors.
• Precisionbalancedweightdistributionforsafe,even
andaggressivecleaningwithlowvibration.
• Largenon-markingwheelsforcleantransportto
protectcompletedareas.
• Safetyenhancedinterlockswitchonhandleleaves
bothhandsconvenientlyincontrol.
• Heavy-dutycomponentsprovidedurableand
dependablescrubbing.
• Nosidetorqueandoperatesinanydirection.
• Ergonomiccarryinghandleoffersoperatorcomfort
andsafetyduringtransport.
• Convenienthandlewithdualswitchleversfor
operationwitheitherhand.
• Totallyenclosedmotorforlessmaintenance.
• Mercury6-QuartBackpackattachmentforquickand
easyclean-up.
• Onlytakesminutesopposedtohoursittakesforan
operatortobecomeacquaintedwithaconventional
rotarymachine.
© 2012 Copy Rights Reserved Mercury Floor Machines, Inc.© 2012 Copy Rights Reserved Mercury Floor Machines, Inc.
Specications
Model No. DS-18
Cleaning Pad Size 12 in. x 18 in.
Motor 1 HP
Voltage/Frequency 120 V / 60 Hz
Orbital Speed 1725 RPM
Power Cable (1) 50-Foot, 14/3-Gauge Safety Power Cord
Sound Level 70 dB
Weight 120 lbs.
Warranty 1-Year Motor, 1-Year Service Labor
One-Touch Dry Scrub
Floor Machine
Model No. DS-18
1 HP, 1725 RPM
Mercury Floor Machines, Inc.
110 South Van Brunt Street
Englewood, NJ 07631
Phone: (201) 568-4606
Toll Free: (888) 568-4606
Fax: (201) 568-7962
www.mercuryoormachines.com

1.0 Safety Instructions
READ THIS MANUAL BEFORE USING THE FLOOR MACHINE. KNOW THE
PROPER OPERATION, CORRECTAPPLICATIONSAND THE LIMITATIONS OF
THIS EQUIPMENT BEFORE USE.
Reduce the Risk of Fire, Electric Shock or
Injury:
• This oor machine is designed for indoor use only. Do
not use outdoors. Do not expose to rain.
• Do not wash the motor with owing water. If the motor
gets wet, seek authorized service.
• Keep the vents on this air-cooled motor free from debris.
Do not operate with the motor covered or with vents
blocked. Do not use this machine as a oor sander.
• Never operate this machine near ammable dusts, liquids
or vapors. Never use ammable solvents as a cleaning
agent. Engine sparks and operating heat can cause re.
• Never handle electrical equipment with wet hands. Never
operate this machine with bare feet.
• Unplug the machine when not in use and when servicing
the equipment. To unplug, grasp the plug not the cord.
• Do not operate a oor machine with damaged handle
controls, cord or plug. If the equipment is not performing
properly, seek repair from a qualied service supplier.
• This machine is constructed with electrical grounding
at the plug. Operate only when connected to a properly
grounded outlet. See section 1.2 for grounding details.
• Prevent electrical cord abuse. Do not close a door on the
cord, drive equipment over it, or run the oor machine
over it. Do not expose the cord to hot surfaces. Do not
lift, pull or carry this oor machine by the cord.
• Never operate the machine over sharp objects that can
be propelled out from under the machine and harm the
operator or damage the oor. Sweep hard oors before
scrubbing or bufng.
• Train your staff in proper use of this machine.
(2) Dry Scrub Floor Machine Dry Scrub Floor Machine (15)
11.0 6-Quart Backpack Parts List
Item No. Description Part No. Qty.
76 6 qt. Backpack Lid - Black BP-6-L-BLK 1
77 Complete 4” Super Flex Hose with 10-0036 2
Cuffs 1-1/2” Diameter
78 HEPADome Filter with Bag Support 10-0219-6 1
79 D.P. Motor 10-0346 1
80 Vacuum Motor Gasket 10-0199 1
81 1-Touch Tank - Red BP-1T-T-Red 1
82 Handle Clamp PVK1-3M 2
83 Bracket Screw B-2 2
84 Spacer for BDP-13A B-65 4
85 Washer B-37 4
86 Cap Screw B-31 4
87 1/4” Flat Washer 10-0015 4
88 Motor Screw 10-0014 4
89 1-Touch Base - Black BP-1T-B-BLK 1
90 6qt.DeectorPlate 10-0016-6 2
91 DeectorScrew 10-0017 1
92 Sound Dampening Band 10-0018 1
93 6 qt. Dual Cell Noise Filter 10-0019-6 1
94 Strain Relief Nut 10-0027-A 1
95 Pigtail Strain Relief 10-0027 1
96 17” Power Cord 10-0026 1
97 On/Off Switch 10-0025 1
98 6 qt. Cloth Bag for 6 qt. Backpack 10-0007-6 1
99 6 qt. Paper Bags/10 Pack 10-0197 0.1
Not Pictured Hose Cuff Straight 10-0155 4
Not Pictured Washer for Rivet 10-0205 10-0204-B 4
Not Pictured Body Rivet for Backpack 10-0205 4
Complete One-Touch Vacuum - Black/Red 70-7000 1

(14) Dry Scrub Floor Machine Dry Scrub Floor Machine (3)
1.1 Electrical Power
Thisoormachineoperatesona13amp,nominal120V,60
HzA.C.powercircuit(motorsmaybecustomwiredatthe
factoryfor220V,50Hzinternationaloperation).Theamp,
hertzandvoltageratingsarelistedonthemotorspeclabel
foundoneachoormachine.Usingvoltagesaboveorbelow
thoseindicatedonthespeclabelwilldamagethemotor.
Alwayscheckyourlocalvoltagerequirements.
1.2 Grounding Instructions
Thisoormachinemustbegroundedwhileinuse
toprotecttheoperatorfromelectricalshock.This
machineisbuiltwitha3-wirecordanda3-prong
grounding-typeplug(Figure1)totaproperly
groundedreceptacle.
Beforeusingthisoormachine,makesurea
properlygrounded,3-holeelectricaloutletis
available.Ifnotavailable,asinsomeolderfacilities,
useanadapterforconnectinga3-prongplugtoa
2-prongreceptacle(Figure2)togroundtheoutlet
chassis.
IMPORTANT: Thisadaptormaynotbeusedin
Canada.
IMPORTANT:Nevercutoffthegroundingprong
foruseina2-prongoutlet.Bydoingso,youhave
cutoffyourprotectionfromelectricalshock.
Neverassumethatall3-holeoutletsareproperly
grounded.Checkbeforeuse.
Neverassumethatanadaptorconnection(asin
Figure2)isproperlygrounded.Checktheoutlet
withagroundfaultinterrupterdevicewhichquickly
indicatesifagroundisconnected.Correctafaulty
groundingbeforeproceeding.
1.3 Extension Cords are Never Recommended
Theoormachineisbuiltwitha50-footsafetypowercordwhichplugsdirectlyintoan
approvedoutlet.Useofanyextensioncord(s)isNEVERRECOMMENDED.
Figure 1
Figure 2
10.0 6-Quart Backpack Schematic Drawing

2.0 Machine Handle
Theoormachineisshippedfromthefactorywiththehandleattached.Noassembly
isrequired.Thefollowinginstructionsdetailhowtoreattachthehandleifthehandle
orpartsneedtobereplaced.Youwillneedtwo(2)7/16”wrenchestocompletethe
assembly.
1. Mount the handle to the chassis:
Slidetheyoke(1)intothehandletube
assembly(2).Alignthetwoverticalholes
ineachpart.Slideayokebolt(8)through
eachholeandsecureayokenut(9)onto
theendofeachbolt.Placetheconnected
yokeandhandletubassemblyintothe
bracketsonthemachinebase(3).Slide
anylonatwasher(5)ontotheyokepin
screw(4).Inserttheyokewithwasherinto
therstbrackethole,thenyokeandout
throughthesecondbrackethole.Slidea
secondnylonatwasher(6)ontotheend
oftheyokepinscrew(7)andtightena
yokenuttotheendoftheyokepinscrew.
2. Mount the support braces on the handle:
Tipthehandleup.Thehandlemounting
collar(10)isdesignedtoslidefreelyup
anddownthehandletube,allowingthe
handletobeadjustedforthecomfortable
operationofallusers.Lineupthemounting
collarwiththeupperholesinthetwo
straighthandlebraces(11).
3. Complete handle assembly:
• Place the curved spacer (13) with a
square hole onto the locking lever shaft
(12). The curve must face the lever.
• From behind the machine, insert the shaft
through the right handle brace (11), the
mounting collar (10) and the left handle
brace.
• Place a spacer (14) on the shaft.
• Place the split washer (12) on the shaft.
• Place the locking wing nut (15) on the
shaft.
• Adjust the wing nut for tightness. When
correctly installed, the collar slides easily
when the cam-engineered locking lever
is “up,” but is rmly xed when the lever
is “down.”
(4) Dry Scrub Floor Machine Dry Scrub Floor Machine (13)
9.0 6-Quart Backpack Troubleshooting Guide
CAUTION: Always disconnect power cord before servicing vacuum.
WARNING: Repairs should only be performed by an authorized service center.
PROBLEM: Loss of vacuum
CAUSE SOLUTION
Cap is damaged Inspect and replace if needed
Faulty vacuum motor Call manufacturer or service center
Full paper bag lter Replace paper lter bag
Clogged hose or wand Remove obstruction
Loose or broken fan Call manufacturer or service center
PROBLEM: Motor is not running
CAUSE SOLUTION
Faulty on/off switch Call manufacturer or service center
Power cord defective Call manufacturer or service center
Loose connection or wiring Call manufacturer or service center
Motor defective Call manufacturer or service center
Blown fuse or tripped circuit breaker Replace fuse or reset circuit breaker
PROBLEM: Dust blowing from vacuum when running
CAUSE SOLUTION
Full paper bag Replace lter bag
Paper lter bag not installed properly Reinstall or replace paper lter bag properly
Cloth lter bag is dirty Clean cloth lter bag
Cloth or paper lter bag is torn Replace

2.1 Attach the Power Cord
Thetriple-wiregroundedpowercordhasbeenfactory-
installedintothehandletube.Aexiblerubbercable
connector(11)isusedtosecuretheplug-inconnections.
Theoormachineshipswiththisconnectormountedon
thecordcomingoutofthehandle(10).
Stretchtheconnectorandslipthemaleconnector(9)
(comingoutofthemotorhousing)throughtheconnector
holeandthenintothefemaleconnector.
Plugtheendofthe50-footpowercordintoagrounded
poweroutlet.Squeezethetriggersonthehandleand
checkforpowertothemotor.
2.2 Install the Pads
Unplugtheoormachine.Lockthehandlein
the“up”positionandtipthemachinebackfully.
First,placethemaroon-coloredStripping
Pad(13)ontotheoor,belowthefootofthe
machine.Next,placetheFillerPad(14)directly
ontopofthemaroon-coloredstrippingpad.
WARNING:TheFillerPadmustbeusedwhen
usingthismachine.TheFillerPadhelpsreach
intodepressionsandvariationsintheoor’s
surface.Also,astheStrippingPadwears,the
FillerPadprotectstheoorfromscratchingby
themachine’sbaseplate.
Tipthemachinetowardsthepadsandmaneuver
themachinesothatthepadsarealigneddirectly
belowofthebottomplate.Placethemachine
baseontothepads,ensuringtheentirestackof
padsaretuckedunderneaththemachinebase,
andtipthemachineintotheuprightposition.
Themachineisnowreadyforoperation.
(12) Dry Scrub Floor Machine Dry Scrub Floor Machine (5)
8.0 6-Quart Backpack Operation Instructions
PREPARATION AND OPERATION. DRY ONLY!
The 6-quart backpack is attached to the oor machine when shipped from the factory. No
assembly is required. This vacuum is equipped with an air-thru motor and is designed for
dry pickup only.
Getting Started:
Make sure your on/off switch is in the OFF position. Remove lid and check to make
sure you have both a cloth lter bag and paper lter bag in place. Secure lid back onto
the vacuum body, tightening securely. Both bags must be used at all times. Any damage
resulting from the lack of using both bags will not be covered under warranty.
To Change Paper Filter Bag:
1. Unscrew lid from body.
2. Remove full paper bag from the tank and dispose of
properly.
3. Take new paper lter bag and set inside cloth lter bag,
expanding it to the sides of the cloth lter bag.
4. Screw lid tightly back onto body.
Cloth Filter Maintenance:
The cloth lter should be inspected and cleaned each time you empty the tank. DO NOT
wash the cloth lter. It could cause shrinkage of the cloth and damage to the gasket.
Simply shake off any dust or loose particles and brush the exposed surface with a soft
bristle brush.

3.0 Operating Tips
• For indoor use only. Sweep abrasive soils before using machine.
• While the pad driver is moving, keep the machine moving to avoid burns on the oor.
3.1 To Start Operation:
• Unlock the handle by raising the locking lever.
• Lower the handle to a comfortable position, typically
waist high.
• Relock the handle by pushing the lever down. NEVER
OPERATE THE MACHINE WITH THE HANDLE
UNLOCKED.
• Hold the machine rmly with both hands when starting
up.
• Push the red safety interlock switch forward to unlock
the dual triggers.
• Squeeze both triggers to power the motor. Once power
is on, either trigger will keep power to the motor.
To stop, release both triggers.
(6) Dry Scrub Floor Machine Dry Scrub Floor Machine (11)
PUSH LOCK
FORWARD SQUEEZE
BOTH TRIGGERS
7.0 Parts List Continued
Item No. Description Part No. Qty.
46 17.875” x 12” Pad with Holes MCPAD 1
47 Aluminum Plate AP-01 1
48 3/8 x 16 x 1 Socaet Head Screw DS-FHS 1
49 Motor Shaft Washer DS-TFWZP 4
50 Motor Shaft Key DS-R59 1
51 Motor Bolt DS-R58 4
52 Rubber Bushing RB-01 8
53 1/4-28 x 51/2” Hex HD Cap Screws DS-HHCS 4
54 Rubber Inner Tower Spacer DS-R23 8
55 Rubber Tower Spacer DS-R22 8
56 Thick Flat Washer DS-FWPS 8
57 Acorn Cap Nits DS-NSAC 4
58 Motor, 1 HP 115/230 V, 60 HZ MOTOR/DRY SCRUB 1
59 Cable Strain Relief G-66P 1
60 Pigtail with Female Outlet G-15ACF 1
61 Twist Lock - Male DS-R63 1
62 Motor Cord DS-R62 1
63 Metal Wire Holder DS-R61 1
64 Motor Bell DS-R64 1
65 Capacitor Box DS-R65 1
66 Motor Capacitor DS-R66 1
67 Capacitor Box Fastener DS-R67 1
68 Machine Base DS-IRONCW 1
69 Flywheel FW-01 1
70 Dry Scrub Bearing DSBR-02 2
71 Bearing Sleeve BS-01 1
72 Rubber Spacer B-5 2
73 5” Rubber Wheel M-260 2
74 Axel B-14 2
75 Dust Ports PVC-Pipe 1 1/2” 2
76 Skirt w/ Brush MCSKIRT 1
77 Thumb Screw B-96 5
78 3/8 Flat Washer B-28 8
79 Nut B-10 2
Not Pictured Filler Pad 42071218 1
Not Pictured Maroon Stripping Pad 40441218 1
Not Pictured 2” Velcro Strips for DS-18 V-CRO Pad 1
3.2 To Store your Machine:
• Lock the handle in the “up” position. Tilt the machine
back onto the transport wheels. Never store the machine
with the pad on the ground.
• Wind the cord around the handles and the bottom cord
hook.
• Inspect and maintain equipment on a regular schedule
for best results.
• Check and clean pads after each operation. Remove soil
and chemical buildup. Replace worn or damaged pads.
• Wash pads and hang to dry.
• Check triggers and switches for proper operation.
• Use air pressure or vacuum to remove dust and debris
from the motor vents.
• Report problems and repair promptly.

(10) Dry Scrub Floor Machine Dry Scrub Floor Machine (7)
3.3 Transport:
Totransportthismachinefromthejanitor’sclosettothe
workarea:
• Lock the handle in the “up” position. Wind the cord
around the handles and the bottom cord hook.
• Tip the machine back onto the transport wheels. Push
or pull the machine by the handle, not by the cord or
any other part of the machine. Travel carefully.
4.0 Troubleshooting
Neveroperatethismachinewhentheequipmentisnotperformingasexpectedorwhen
anypartsarevisiblydamaged.Thecauseandsolutionforsomebasicproblemsare
describedbelow.Whenrepairisneeded,taketheequipmenttoanauthorizedrepair
servicecenter.
4.1 Machine will not Run:
• Circuit breakers are tripped in the building. Check and reset.
• Equipment is unplugged. Check plug at wall and at machine base. Plug in.
• Power cord failure. Test with a working power cord. Lock the handle up and tip the
motor back. Unplug the cord at the motor and plug the motor into your working
power cord.
IMPORTANT: this is just for testing! When you do this, you have removed the
safety handle controls from the circuit and you are sending power directly to the
motor. If the motor now spins, the problem is in the cord of the handle assembly. Seek
authorized repair service.
If the motor still does not work, the problem is either in the male connection at the
motor base or in the motor. Seek authorized repair service.
• Motor sparks or smokes. Seek authorized repair service.
4.2 Electrical Shock to Operator:
• Equipment wiring failure or electrical short in the machine. Seek authorized service.
• Poor grounding or no grounding. Test the outlet with a ground fault interrupter. Retain
certied electrician to inspect and repair grounding. NEVER clip off the ground plug
on your cord.
• Repeated circuit breaking. High amp draw and circuit breaking can be an electrical or
mechanical problem. Seek authorized repair service.
4.3 High Vibration:
• Pads are not centered on the pad driver. Tip machine back and re-center the pad.
• Uneven wear or warp to pad or brushes. Replace.
• Machine chassis is damaged by dropping. Replace.
7.0 Parts List
Item No. Description Part No. Qty.
1 Trigger Pins B-70 2
2 Switch Box Back Cover A-104-S 1
3 Cross Bar Screw B-22 2
4 Safety Interlock Assembly SIA-1 1
5 Handle Tube Screw B-23 2
6 Switch Box Closing Screws B-21 4
7 Strain Relief Clamp - Black M-213 1
8 Black Hand Grip - Red Band M-218-R 2
9 Ground Wire Screw B-68 2
10 Handle Tube Insert M-247 1
11 Handle Tube with Yoke Plated M-206 1
12 Cable Hook Screw B-2 2
13 Cable Hook A-164 1
14 Cam Assembly C-100 1
14a Complete Cam Assembly CCA 1
(Includes 1 each of Drawing Items
#13, 14, 15, 28, 29)
15 Rectangular Hole Cam Washer B-67 1
16 Straight Brace M-233 2
17 Flat Washer B-37 1
18 Split Washer B-39 1
19 Cam Lock Wing Nut B-25 1
20 Sliding Collar A-111 1
21 Cable Grommet B-63 1
22 Black Rubber Cable Connector M-249 1
23 Handle Tube Cable G-16 1
24 PVCAxel Sleeve 1” Diameter DS-PVC SLEEVE 1
25 Hub Caps V0038 2
26 Spring Washer B-51 2
27 9” Axel M-217 1
28 Yoke Bolt B-18A 2
29 Yoke Pin Screw B-14 1
30 Nylon Flat Washers DS-NFW 2
31 Yoke DS-Yoke 1
32 Yoke Nut B10 1
33 Yoke Nut B-19 2
34 50-Ft., 14/3-Gauge Power Cord - Red G-14-50/R 1
35 Switch Mounting Plate G-30-B 1
36 On-off Switch and PlateAssembly G-30-AB 1
37 Insulated Flag Wire Connector G-48 5
38 Switch Plate Wire Screw B-1 2
39 Int. Tooth Lock Washer B-35 1
40 Flat Hex Nut B-33 1
41 Trigger Return Hook Spring G-30-C-T057 1
42 Label - Switchbox 1
43 Switch Box Front A-103 1
44 Wire Nut G-47 1
45 Trigger A-105 2
46 16” Crossbar M-211-A 1
Complete Complete Handle Assy. w/ 50 Ft. Cord - Red M-100-50-R 1

(8) Dry Scrub Floor Machine Dry Scrub Floor Machine (9)
5.0 Handle Schematic Drawing 6.0 Machine Schematic Drawing
Machine Front
Machine Top
Inside Tower
Electrical Box
Table of contents
Other Mercury Floor Machine manuals
Popular Floor Machine manuals by other brands

Tennant
Tennant 8010 Instruction bulletin
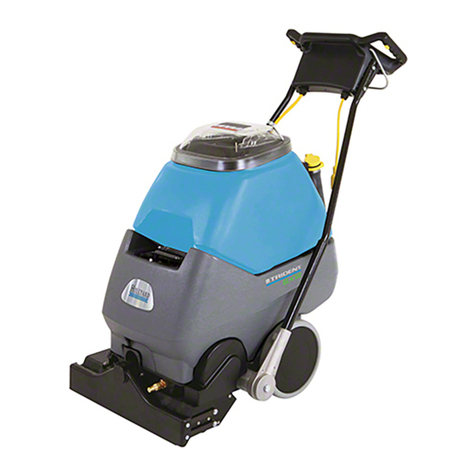
Hillyard
Hillyard TRIDENT EX12 operating instructions
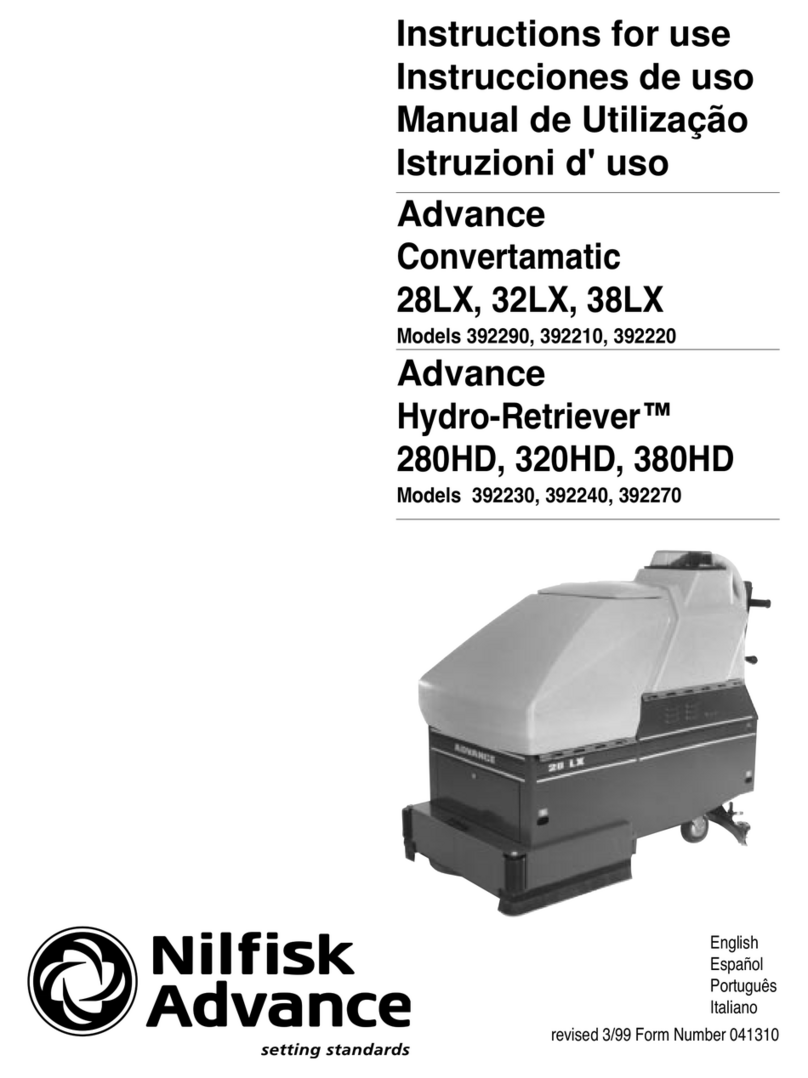
Nilfisk-Advance
Nilfisk-Advance Convertamatic 28LX Instructions for use

Tennant
Tennant 6080E Operator's manual
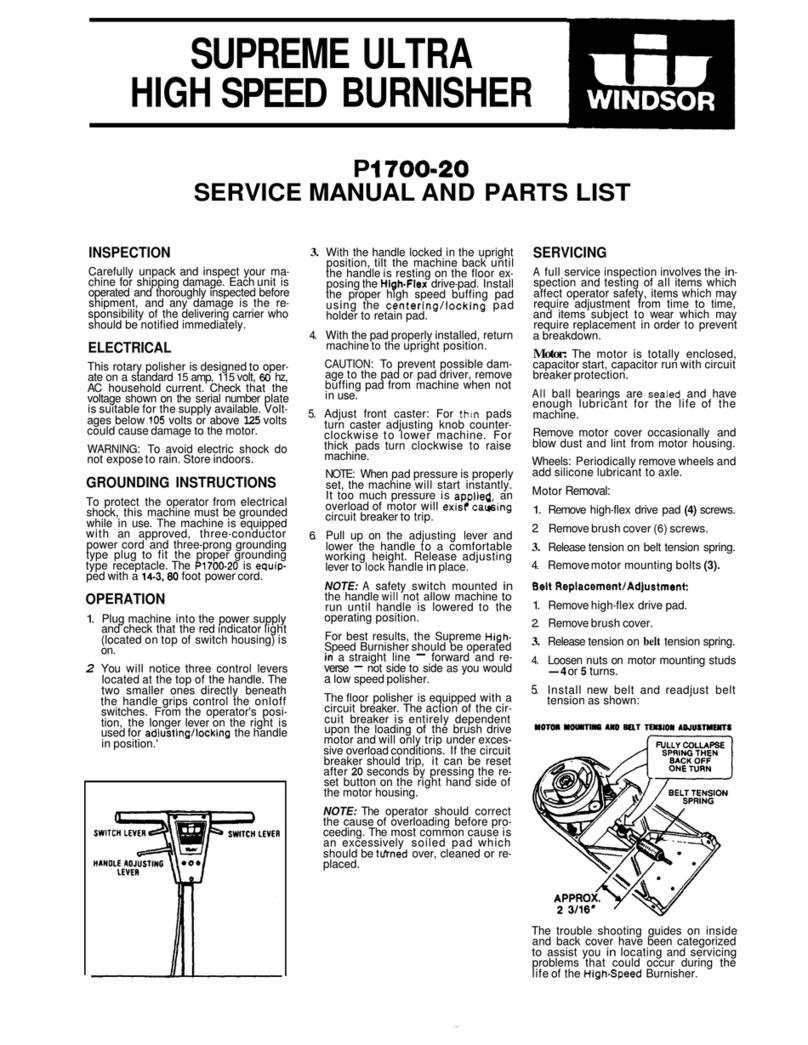
Windsor
Windsor SUPREME ULTRA HIGH SPEED BURNISHER P1700120 Service manual and parts list
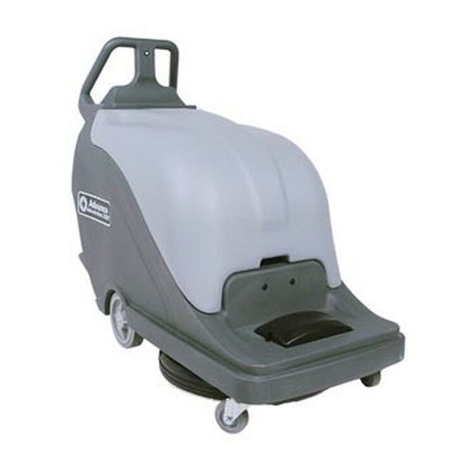
Advance acoustic
Advance acoustic Advolution 20B instruction manual