METALSAWZ MZ STANDARD Series Operating instructions

INTRODUCTION TO “METALSAWZ” BANDSAWS
MANUFACTURING METALSAWZ PAGE 03
INSTRUCTIONS AND SAFETY PRECAUTIONS
SAFETY PRECAUTIONS
SAFETY DECALS AND SAFETY PROCEDURES PAGE 04
PREPARING THE SAW UPON RECEIPT
MAINTENANCE PRECAUTIONS PAGE 08
CONTROLS AND OPERATIONS
START-UP AND OPERATION PAGE 10
INSTALLATION PROCEDURES PAGE 10
CONTROL PANEL AND OPERATION PAGE 11
INITIAL OPERATION PAGE 12
GUIDE POST HEIGHT ADJUSTMENT PAGE 13
VISE ADJUSTMENT PAGE 13
MITER CUTTING PAGE 14
BLADE REPLACEMENT PAGE 15
COOLANT PUMP SERVICE PAGE 17
AUTOMATIC SHUT OFF SWITCH (OPTIONAL) PAGE 18
SPRAY MIST COOLING (OPTIONAL) PAGE 19
SPECIFICATIONS PAGE 21
MAINTENANCE ADJUSTMENTS
BLADE CHIP BRUSH ADJUSTMENT PAGE 24
BAND WHEEL TRACKING ADJUSTMENT PAGE 24
CARRIAGE TRACKING ADJUSTMENT PAGE 25
VISE ALIGNMENT PAGE 26
GUIDE POST ALIGNMENT ADJUSTMENT PAGE 27
BAND GUIDE BLOCK ADJUSTMENT PAGE 28
BAND GUIDE BEARING OR CARBIDE (OPTIONAL) ADJUSTMENT PAGE 30
PARTS LIST
PARTS EXPLOSION PAGE 32
SCHEMATICS
ELECTRICAL SCHEMATIC PAGE 42
HYDRAULIC SCHEMATIC MZ PAGE 43
HYDRAULIC SCHEMATIC MZS PAGE 44
HYDRAULIC SCHEMATIC MZHD PAGE 45
HYDRAULICS
HYDRAULICS SAFETY PAGE 46
HYDRAULICS TROUBLESHOOTING PAGE 47

2
BANDSAW BLADE FAQS
FACTORS THAT AFFECT CUTTING PAGE 48
TOOTH SELECTION PAGE 48
BLADE BREAK-IN PAGE 37
BAND SPEED PAGE 49
FEED PRESSURE PAGE 39
VISE LOADING AND BEAM STRENGTH PAGE 50
BLADE BRUSH PAGE 51
CUTTING OIL PAGE 52
MATERIAL/BLADE LIFE PAGE 52
EXCLUSIVE “POWERSTRIKE” ACTION PAGE 53
BLADE PROPLEM SOLVING
BLADE SPEED CHART
TERMS AND CONDITIONS OF LIMITED WARRANTY

3
INTRODUCTION TO
“METALSAWZ”
BAND SAW MACHINES
MANUFACTURING METALSAWZ
MetalSawz have been manufactured to operate with the same quality, efficiency and tolerances of
machines that cost up to two times the price. The simplicity of the MetalSawz design will allow it to work
well beyond its anticipated useful life. Only standard “off the shelf” components have been used to
facilitate repair and replacement.
Adjustments are accessible and easily done. With proper use the saw will give years of service and
expand the capabilities of your shop. This manual outlines the operations, adjustment and safety
procedures.
It is very important that you familiarize yourself with this manual before you
begin operation of the saw.
MZ STANDARD SERIES
WITH MZS PACKAGE
WITH MZHD PACKAGE

4
INSTRUCTIONS
AND
SAFETY PRECAUTIONS
INDUSTRIAL MACHINERY CAN BE DANGEROUS!
READ THE SAFETY MESSAGES BOTH IN THIS MANUAL AND POSTED ON THE MACHINE. A
THOROUGH KNOWLEDGE OF THE OPERATION OF THIS MACHINE AND THE HAZARDS IT
PRESENTS IS YOUR BEST PROTECTION AGAINST INJURY!
MetalSawz Inc. has made every effort to eliminate potential dangers in its equipment
through careful design and guarding. This equipment has the potential to cause serious
injury or death if not operated and maintained properly.
---------------------------------------------------------------------

5
SAFETY

6
A CAREFUL AND KNOWLEDGABLE OPERATOR IS THE BEST INSURANCE
AGAINST AN ACCIDENT.
PERSONAL SAFETY PRECAUTIONS
QUALIFIED PERSONNEL must make all electrical connections
. (“Entela” evaluates our product for
electrical safety and conformity.)
DO NOT operate the saw before reading the entire manual and familiarizing yourself with the location,
function, and safety precautions of the machine.
NEVER allow anyone unfamiliar or untrained to operate the machine.
NEVER place any part of your body near a moving saw blade.
KEEP guards and shields in place and in good working order.
USE EXTREME CARE when making adjustments.
MACHINERY PRECAUTIONS
The caution decal is located on the front top blade cover of the machine and must remain legible. Should it
become damaged we will replace it free of charge.
CAUTION
TO AVOID POTENTIAL HAZARDS, OBSERVE THE FOLLOWING PRECAUTIONS WHEN OPERATING OR SERVICING
THIS MACHINE.
ALWAYS WEAR SAFETY GLASSES.
ALWAYS USE YOUR EMPLOYER PROVIDED SAFETY EQUIPMENT.
ALWAYS WEAR GLOVES WHEN HANDLING SAW BLADE.
ALWAYS ADJUST GUIDE POST HEIGHT TO WORKPIECE AND REMOVE LOOSE ITEMS FROM TABLE BEORE
STARTING MACHINE.
ALWAYS REPLACE BAND WHEEL COVER AND SKIRT DOOR AFTER INSTALLING NEW BLADE.
ALWAYS KEEP FINGERS AND HANDS AWAY FROM MOVING SAW BLADE AND VISE.
ALWAYS STOP MACHINE BEFORE REACHING INTO THE WORK AREA.
ALWAYS AVOID CONTACT WITH COOLANT, ESPECIALLY THE EYES.
ALWAYS USE A HOOK OR RAKE TO REMOVE DEBRIS FROM TABLE.
ALWAYS MAINTAIN PROPER BLADE GUIDE BEARING CLEARANCE.
ALWAYS BE AWARE OF PROPER BAND SPEED AND FEED PRESSURE SETTINGS.
ALWAYS USE VISE PROPERLY.
ALWAYS LOCK OUT POWER WHEN UNATTENDED.
ALWAYS DISCONNECT POWER BEFORE REMOVING COVERS TO SERVICE MACHINE.
ALWAYS REFER TO DATA CHARTS SUPPLIED BY BLADE MANUFACTURERS FOR PROPER SELECTION OF
BLADE, SPEED AND FEED FOR THE TYPE AND SIZE OF THE MATERIAL YOU ARE CUTTING.
NEVER WEAR JEWELRY OR LOOSE CLOTHING WHILE OPERATING MACHINE.
NEVER SAW UNKNOWN MATERIAL.
NEVER SAW A WELD OR A TORCH CUT EDGE.
NEVER OPERATE WITH SAFETY SHIELDS REMOVED.
NEVER ALLOW DEBRIS TO BUILD UP UNDER SAW OR IN COOLANT SUMP.
NEVER RUN THE MACHINE WITHOUT A THOROUGH UNDERSTANDING OF ITS OPERATION.
NEVER LOAD, UNLOAD STOCK OR REMOVE CUT PARTS FROM MACHINE WHILE THE BLADE IS
RUNNING.

7
CONTROLS, OPERATION
AND MAINTENANCE OF
“METALSAWZ”
MZ1832S
(MODEL SHOWN)

8
PREPARING THE SAW UPON RECEIPT:
1. Remove steel shipping brackets located at rear.
i. Small bracket –frame to carriage
ii. Large bracket –column to carriage
iii. Reinstall limit switch dog if equipped.
2. Fill hydraulic oil tank with between 20 and 25 gallons “Noco” AWS32 hydraulic oil or equivalent.
3. Do not run saw dry (without coolant). The coolant pump automatically runs when the saw starts.
4. Place coolant pan under the saw while head is in tilt position.
5. Have a qualified electrician connect the saw to a disconnect switch.
6. Grease all grease fittings on band wheel bearings and pivot points.
7. Familiarize yourself thoroughly with this instruction manual, particularly all safety points.
MAINTENANCE PRECAUTIONS:
1. Observe blade tension recommendations and use sharp blades. (Dull blades are dangerous and
hard on equipment). Should you use excessive blade tension you will decrease wheel-bearing life.
2. Observe hydraulic oil reservoir level and change filter every 200 hours or when contaminated under
normal conditions or sooner under extreme conditions.
3. Periodically clean off chips and debris on the underside of carriage and grease moving parts.
4. Read your manual.
CONTROLS AND OPERATIONS
(SEE FIGURE 1)
ITEM DESCRIPTION
1MAIN POWER SWITCH
2FEED PRESSURE GAUGE
3APPROACH SPEED CONTROL VALVE
4FEED PRESSURE CONTROL VALVE
5COOLANT FLOW CONTROL VALVE
6CARRIAGE FEED CONTROL VALVE
7HYDRAULIC HEAD TILT SELECTOR VALVE (“S” and “HD” MODELS ONLY)
8BAND SPEED CONTROL VALVE
9VISE ASSEMBLY
10 FRONT VISE JAW (standard left hand shown)
11 FIXED VISE JAW
12 BLADE GUIDE POST
13 HEAD TILT ANGLE INDICATOR
14 HEAD TILT LOCK (not shown)
15 HEAD TILT SCREW (not shown)
16 FRONT BLADE SHIELD
17 POST HEIGHT ADJUSTMENT CLAMP HANDLE
18 FIXED UPPER WHEEL GUARD
19 HINGED UPPER WHEEL GUARD
20 REAR BLADE SHIELD
21 C –FRAME ASSEMBLY
22 CARRIAGE FEED CYLINDER GUARD
23 CARRIAGE ASSEMBLY
24 AUTOMATIC SHUT-OFF SWITCH (IF EQUIPED)
25 ELECTRIC BOX
26 MOTOR AND HYDRAULIC PUMP ASSEMBLY
27 COOLANT TRAY HANDLE
28 COOLANT RECOVERY TRAY
29 COOLANT SUMP PUMP
30 LEVELLING BOLTS
31 REMOVEABLE SIDE PANELS
32 VISE PRESSURE ADJUSTMENT (“S” and “HD” MODELS ONLY)
33 VISE PRESSURE GAUGE (“S” and “HD” MODELS ONLY)
34 VISE PRESSURE VALVE (“S” and “HD” MODELS ONLY)

9
SAW CONTROLS
(FIGURE 1)
22
31

10
START-UP AND OPERATION
INSTALLATION PROCEDURES
NOTE: This machine has been set-up and tested prior to shipping, but due to the vibrations and stresses of
shipping the following procedures should be completed to ensure proper installation.
IMPORTANT!
TO MEET HIGHWAY TRANSPORT REGULATIONS THIS MACHINE IS SHIPPED WITHOUT HYDRAULIC OIL. FILL
HYDAULIC OIL TANK WITH BETWEEN 20 AND 25 GALLONS OF “NOCO” AWS32 HYDRAULIC OIL (OR
EQUIVALENT) BEFORE STARTING THE MACHINE.
“FAILURE TO COMPLY WILL VOID THE LIMITED WARRANTY.”
1. Remove carriage and frame brackets. Re-install limit switch dog if so equipped.
(Fig. 2, items 1 and 2)
(Figure 2)
2. With a level placed on the top of the saw frame, adjust leveling screws
(item 30 Fig. 1)
so that the frame
is approximately 1/16” lower in the back than the front. With the level placed on the width of the saw and
using the leveling screws, level the frame across the width. When you are finished the saw frame should
be level across the width
.
The frame should have no twist.
2. Remove carriage bearing covers
left and right side
(Fig. 2, item 3
). This exposes carriage-bearing rolls. All
(4) of these bearings should be touching the saw rails
.
If they are not touching the rails they can be
adjusted by loosening the nut on the outside of the carriage and turning the eccentric bolt on the inside
of the carriage until the bearing contacts the saw rails. Two (2) eccentrics are placed opposite each
other at 90 degrees at the back of the carriage.
4. Have a qualified electrician make electrical connection at this time to a disconnect switch.
5. Check all controls & operations
(Fig. 3)
with the carriage feed lever
(Fig. 3, item 7)
in the NEUTRAL position
and the band speed valve set at 60 FPM
(Fig. 3, item 8), jog the start/stop buttons (Fig.3, Items 1&2)
to
check band wheel rotation. The band saw blade should be rotating in the downward direction.
6. Crank tilt handle on standard model or with the tilt selector valve (“S” and “HD” packages only) in tilt
position and using the carriage feed valve, tilt the head 30 degrees left with the head now in the tilt
position, next place sump pump (
Fig. 1, item 27)
in sump at the rear of the coolant tray.
7. Fill with required cutting fluid until the fluid is well over the top of the sump pump (approximately 14
gallons of mixed coolant).
8. Move coolant tray into position. Head must be tilted to position tray.
9. Grease four-wheel bearings and two head pivot points with a good quality heavy-duty grease.
YOUR METALSAWZ IS NOW READY FOR OPERATION.

11
CONTROL PANEL AND OPERATION
(Figure 3)
(Figure 3A) (Figure 3B)
(Figure 3 and 3a and 3b “S” and “HD” packages only)
CONTROL PANEL
1. Start Button: Starts all electrical circuits, as well as the hydraulic and coolant pumps.
2. Stop Button: Shuts off all electrical circuits.
3. Feed Pressure Gauge: Displays current feed pressure.
4. Approach Speed Valve: Unlock lock nut. Turning valve counterclockwise increases approach speed,
turning clockwise decreases approach speed.
5. Feed Pressure Valve: Unlock lock nut. Turning valve counterclockwise reduces feed pressure, turning
clockwise increases feed pressure.
FEEDFEEDCUTTING
PRESSURERATEFLUID

12
6. Coolant Flow Valve: Turning valve counterclockwise reduces coolant flow, turning clockwise increases
coolant flow.
7. Carriage Feed Valve: Pushing lever away from you returns carriage to rear of machine. Pulling lever
toward you engages the cutting stroke. The middle position is referred to as
neutral in this manual.
8. Band Speed Valve: To adjust, unlock lock nut and set to desired band speed.
9. Tilt Selector Valve: (“S” and “HD” packages only) Toggle this valve and use Carriage Feed Valve
(Fig. 3, item 7)
to adjust head tilt angle. Be sure to loosen head tilt lock prior to
adjusting and to return selector valve to original position when done. (Leaving
head tilt lock “finger tight” generally reduces vibration during head travel.)
10. Hydraulic Vise Valve: (“S” and “HD” packages only) Pushing lever away from you closes hydraulic
vises. Pulling lever toward you opens the vises. The middle position is referred to
as neutral in this manual.
11. Vise Pressure Valve: (“S” and “HD” packages only) To adjust vise pressure, unlock lock nut and set
to desired pressure.
12. Vise Pressure Gauge: (“S” and “HD” packages only) Displays current vise pressure.
13. Hydraulic Lift Arm: (“HD” packages only) Operates hydraulic lift guide arm up or down so you can
adjust blade guides as close to material as possible for best blade life.
INITIAL OPERATION
1. Open approach speed valve (counter clockwise) approximately one turn.
2. Press START button to start machine. Check to make sure motor is running in the right direction, as
indicated by the arrow on the hydraulic pump. Allow hydraulic oil to warm up before operation.
WARNING! NEVER LEAN AGAINST OR PLACE FINGERS, HANDS OR ANY PART OF THE BODY NEAR MOVING
PARTS. FAILURE TO FOLLOW THESE RULES MAY RESULT IN PERSONAL INJURY OR DEATH.
3. Move carriage lever to the CUT position.
4. Adjust feed pressure valve until carriage moves freely, but not forcefully; gauge should read between 40
and 60 psi.
5. Ensure nothing is obstructing the cutting path.
6. Adjust approach speed valve so carriage is advancing at a rate of approximately 2 to 3 inches per
minute. (Use a scale and stop watch to obtain cutting speed).
7. If saw feed rate is excessive, adjust by closing approach speed valve. If rate needs to be faster, and
opening the approach speed valve does not help, increase feed pressure by approximately 10 psi on
the gauge with the feed pressure valve.
8. Move carriage lever to the RETURN position until rear limit is reached, then move to NEUTRAL.
9. Adjust coolant flow valve until desired flow is achieved.
NOTE: These settings are safe for most conditions and materials and are stated here as an initial
guideline. For maximum blade life be sure to consult the back of this manual or your blade supplier’s
blade speed and pitch recommendation chart.

13
As a general rule:
Set feed pressure between 70 to 110 psi on gauge (green area on gauge decal), for most cutting
applications.
The slower the approach speed the higher the feed pressure.
The faster the approach speed the lower the feed pressure.
GUIDE POST HEIGHT ADJUSTMENT
The guidepost should be adjusted as close to the work piece as possible to maintain cutting accuracy. Too
much space between the work piece and the blade guide can cause a non-square cut. To adjust, loosen
post height adjustment clamp, reposition post and re-tighten clamp.
Make sure adequate lubricant is
applied before moving!
On machines equipped with the optional “Hydraulic Guide Arm”, (standard on HD models) simply move
guide arm lever forward or backward to lift or lower guide arm.
MANUAL AND HYDRAULIC DUAL VISES
WARNING! FOR PERSONAL SAFETY, THE VISE MUST BE FULLY OPERATIONAL. IF WORKPIECE IS NOT
ADEQUATELY CLAMPED, PERSONAL INJURY OR DAMAGE TO THE MACHINE MAY OCCUR.
1. Position work piece against the back of the Rear Vise Jaw
(Fig.4, item 1).
2. Push Vise Ram
(Fig.4, item 2)
forward stopping Front Vise Jaw
(Fig. 4, item 3) ¼”
away from work piece.
3. Pull Vise Lock Lever
(fig 4, item 4)
backward with firm, but not overly strenuous force. Only a relatively
slight force is required to adequately clamp work piece.
4. Vise may be moved to the second or third position
(item 5)
for cutting depths greater than 7.5 inches by
lifting up vise clamp on swivel and positioning the pin in the desired pinhole.
5. For “S” and “HD” models with hydraulic vises, pull lever and set adjustable vise pressure insuring that
adequate pressure is applied to hold the material but not too much to crush thin wall tubing etc.
(Figure 4)

14
MITER CUTTING
1. Loosen head tilt lock
(Fig 5, item 1)
and turn head tilt screw crank
(Fig 5, item 2)
for adjusting cut to
desired angle. Re-clamp head tilt lock. For operation of the hydraulic tilt on “S” and “HD” Packages
(Fig 5, item 3)
refer to MANUAL CONTROLS AND OPERATION.
NOTE: Ensure manual or hydraulic blade guidepost maintains adequate clearance above vise
and work piece when adjusting head angle.
(Figure 5)

15
BLADE REPLACEMENT
1. Open hinged upper wheel guard and loosen front blade guard; push forward. Remove skirt door.
2. Loosen old band by turning band tension bolt
(Fig.6, item 1)
clockwise.
3. Slip old band out of blade guide bearing, remove from band wheels and discard.
WARNING! BAND SAW BLADES ARE SHARP. ALWAYS WEAR GLOVES WHEN HANDLING NEW OR USED
BLADES. UNSAFE PRACTICES COULD RESULT IN PERSONAL INJURY IF PROPER PRECAUTIONS
ARE NOT TAKEN.
4. Examine new blade to ensure teeth are oriented properly. Place new band around wheels.
5. Tighten band tension bolt (counterclockwise) enough to keep band from slipping off wheels when
twisting into guide bearings.
6. Twist band and slip into upper and lower guide bearing sets simultaneously.
WARNING! ALWAYS REPLACE COVER WHEN TENSIONING BAND. A DEFECTIVE BAND COULD BREAK AND IF
UNRESTRAINED, COULD CAUSE SEVERE LACERATIONS.
7. Tighten band tension bolt until spring bolster
(Fig. 6A, item 2)
and tension gauge bar
(Fig. 6A, item 3)
are level. This factory-preset position will give the band a tension of approx. 17,000 p.s.i. It is
recommended to use 17,000 to 19,000 psi. If the saw is run for prolonged periods at very high tension
be prepared to replace band wheel bearings more frequently. ANY ADJUSTMENT OF THE TENSION TO
MORE THAN 19,000 LBS. BY BANDSAW BLADE VENDORS WILL VOID THE WARRANTY!
8. Follow blade manufacturers recommendations for break-in procedures.
(Figure 6A)

16
ALWAYS CHECK THESE POINTS BEFORE INSTALLING A NEW
WELDED BAND ON YOUR METALSAWZ.
1. Check for misalignment on the weld either from side to side or top to bottom. (Figure 6B)
2. Check for proper tooth match particularly on a variable pitch tooth blade, for example; a six tooth
should follow a 5 tooth on a 5-8 variable pitch blade.
3. Look at the annealing pattern; is the heat pattern even across the width of the blade?
4. Was all the weld flash removed from both sides of the band?
5. Is there still weld flash in the gullet?
6. Was the tooth damaged during the gullet grinding operation?
(Figure 6B)
Any of the above factors could lead to premature blade failure.
GOOD TOOTH MATCH
PROPER ALIGNMENT
TWISTED SIDE TO SIDE
MISALIGNMENT
BAD TOOTH MATCH
TOP AND BOTTOM
MISALIGNMENT

17
METALSAWZ COOLANT PUMP
The Little Giant model #2E-N pump must be run submerged. The pump should be placed in an upright
position. The volute must always be in a flooded condition; that is, always under the liquid level.
Do not attempt to restrict the intake side of these pumps. Restricting the intake may cause damage to the seal
and may starve the pump.
Do not let the unit run dry (without liquid). It is designed to be cooled by pumping fluid. You may damage
the seal and the motor may fail if the pump is allowed to run dry.
If the unit is going to be idle for a period of time, follow the cleaning instructions outlined in the next section. Do
not let the unit freeze in the wintertime. This may cause cracking or distortion that may destroy the unit.
SERVICE INSTRUCTIONS
MAKE CERTAIN THE UNIT IS DISCONNECTED FROM THE POWER SOURCE BEFORE
ATTEMPTING TO SERVICE OR REMOVE ANY COMPONENT!
This unit is permanently lubricated. Oiling is not required. Do not, in any case, open the sealed portion of the unit
or remove housing screws. The power cord on these units cannot be replaced. In case of damage the whole
unit must be replaced.

18
(OPTIONAL) AUTOMATIC SHUT-OFF SWITCH (depth of cut)
1. Loosen locking handle
(Fig. 7, item 1)
on switch.
2. Advance carriage to desired shut-off position.
3. Move switch to location where actuator angle
(Fig 7, item 2)
toggles the switch arm
(Fig. 7 item 3).
4. Tighten lock screw.
5. To return carriage after shut-off, move carriage feed lever to the return position and press the start button.
(Figure 7)

19
(OPTIONAL) METALSAWZ SPRAY MIST COOLING SYSTEM
COOLANT MIXTURE:
Fill container with clean fresh coolant mixture at 20 or 30 to 1. We recommend a synthetic coolant concentrate. Do
not use coolants that separate or settle out, as they tend to clog the liquid line or nozzle. DO NOT use any hazardous
or flammable solutions in the unit. Deviations from these proportions may be necessary per your application. One
gallon of mixture generally can provide approximately 14 hours of spray per nozzle.
AIR CONNECTION:
Attach the shop air line to the end of the valve body. You will need to supply a 1/8” pipe thread fitting to the end of
your air hose. Usual shop line pressure of 80 to 125 PSI is ideal. The cooling effect of the expanding air is greater with
higher line pressures and therefore air regulators should not be used. The air volume should be regulated only by the
air control needle valve on the top of the valve body.
LIQUID CONTROL:
The liquid control assembly adjusts the amount of liquid in the mist from zero to maximum. Liquid volume is changed
without changing the air valve setting.
USE:
Open the air control and the liquid control. Allow sufficient time for the coolant to be drawn from the tank to the
nozzle. As the units operate on the siphon principle, there is no pressure in the container. Adjust the liquid volume as
needed.
NOZZLE LOCATION:
Maximum cooling will result when the mist is applied at the point of contact between the cutting edge of the tool
and the work. Never point the nozzle to spray on the chips.
NOZZLES:
The nozzles supplied with your unit are made to very close tolerances. DO NOT drill, file, or tamper with the nozzle tip.
They cannot be repaired.
AIR & COOLANT LINES:
The red tube is the airline. The clear tube is the liquid line. The unit will not work if these lines are reversed.
CLOGGED COOLANT LINES:
Should the coolant line become clogged (usually due to use of unclean mixture), place your thumb and forefinger
tightly over the tip of the nozzle. This forces air down the coolant line and pick-up tube back into the container. IF
frequent clogging occurs, the tank should be completely cleaned and refilled with fresh mixture. If you are unable to
unclog the poly tubing, it can be replaced, thereby saving the braided line.
MAGNET NOZZLE HOLDERS:
The magnet assembly makes it possible to apply mist cooling where permanent installations are not required or
wanted.

20
MAINTENANCE:
Clean the container periodically with a bleach type mixture.
Clean container before adding new coolant.
Use only fresh clean coolant each time.
Use only enough coolant to do the job since stagnant coolant will set off fungal & bacterial activity in the tank.
Protect air & coolant lines from damage and kinks.
Install nozzle as close to the work as possible.
This manual suits for next models
1
Table of contents
Popular Saw manuals by other brands
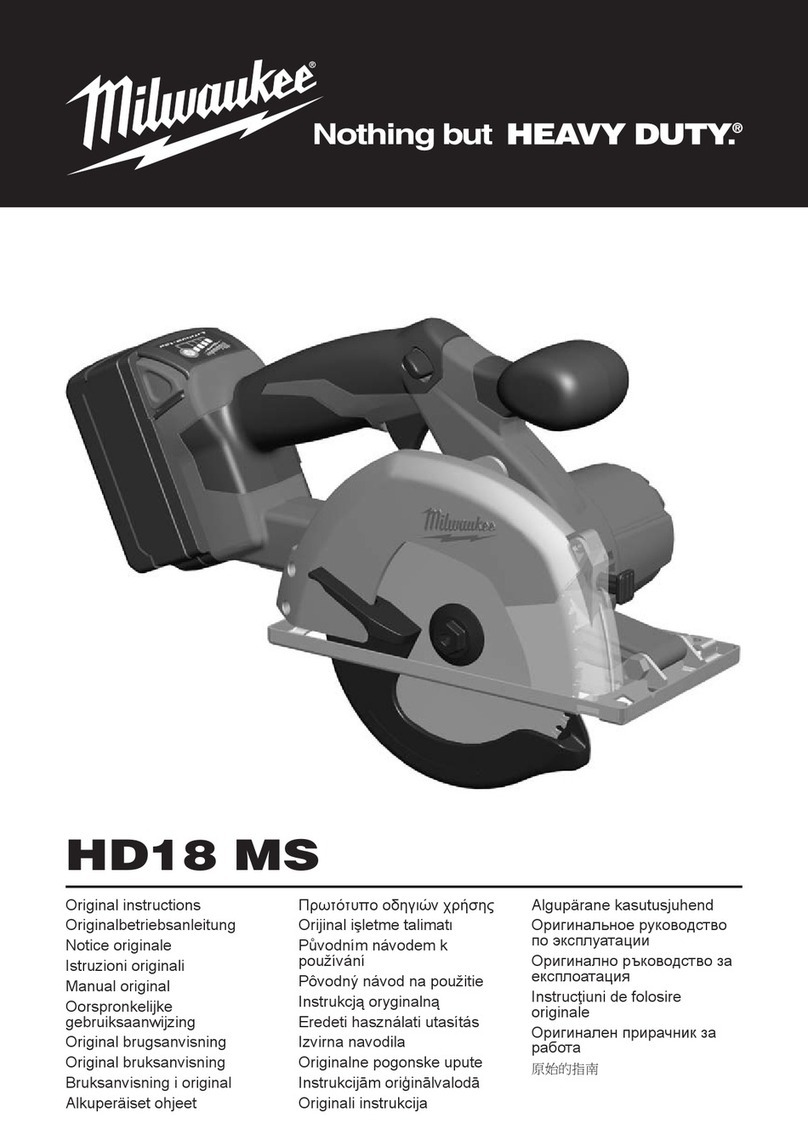
Milwaukee
Milwaukee HD18 MS Original instructions

Ferm
Ferm MSM1021 Original instructions
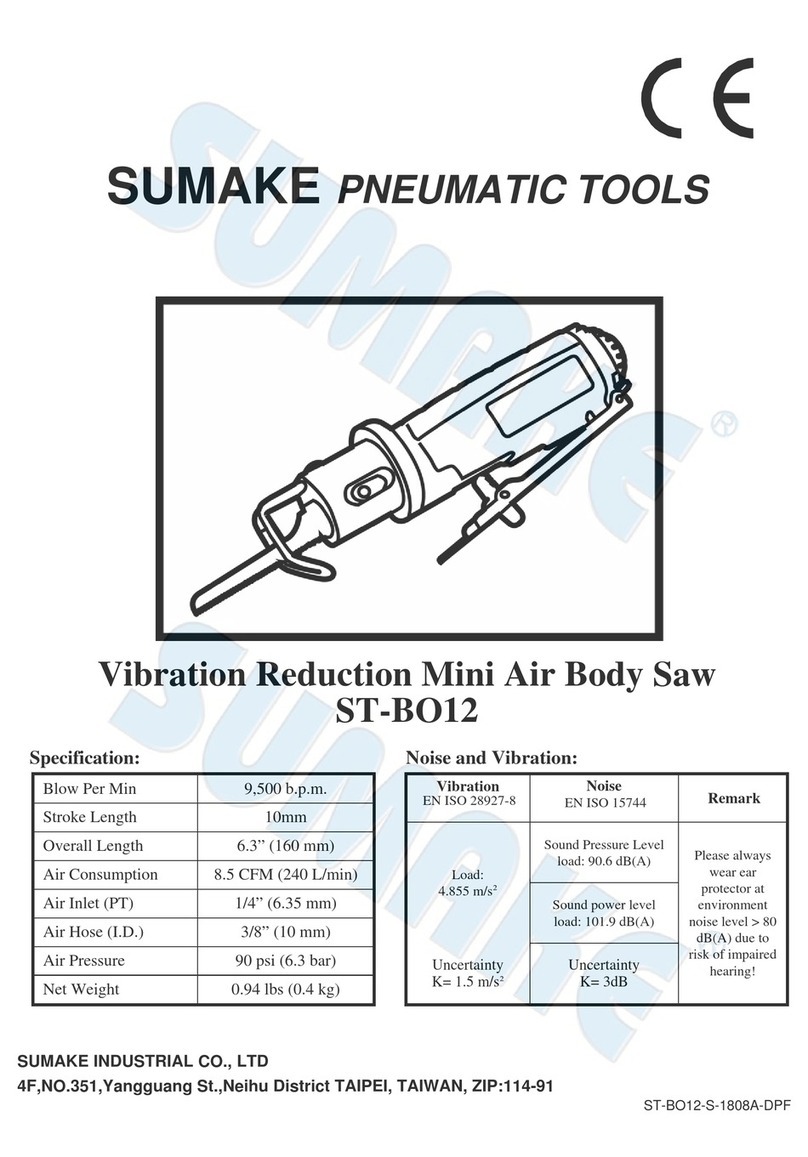
Sumake
Sumake ST-BO12 quick start guide

Barranca Diamond
Barranca Diamond HP18-24 Owner's manual & parts list

HOLZMANN MASCHINEN
HOLZMANN MASCHINEN TK305 user manual
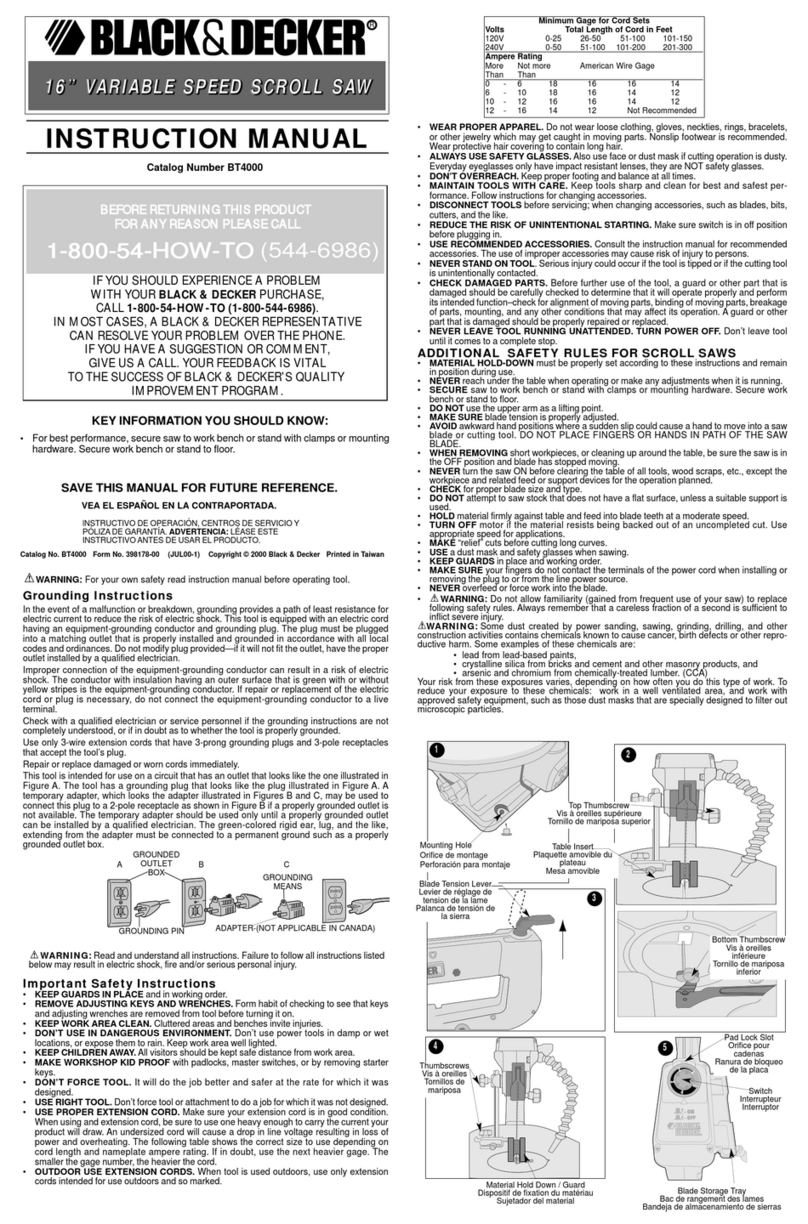
Black & Decker
Black & Decker 398178-00 instruction manual