Microcyber MS0210 HART User manual

MS0210 HART Temperature Board Set
User Manual
Microcyber Corporation

Caution
1. Please don’t take off/install temperature board set at random.
2. Please check if the power of temperature board set meets the power request in the
User Manual.
Version
V1.3
Disclaimer of Liability
We have reviewed the contents of this publication to ensure consistency with the
hardware and software described. Since variance cannot be precluded entirely, we cannot
guarantee full consistency. However, the information in this publication is reviewed
regularly and any necessary corrections are included in subsequent editions.
Microcyber Corporation 2015
The technical data may change at any time.

Table of Contents
Section 1 Overview....................................................................................................................1
Section 2 Introduction............................................................................................................... 2
2.1 Dimension................................................................................................................... 2
2.2 Hardware Interface......................................................................................................2
2.3 Failure Alarm and Configuration Protection DIP Switch.......................................... 3
2.4 Bus Power Interface.................................................................................................... 3
2.5 Sensor Wiring............................................................................................................. 4
2.6 System Connection..................................................................................................... 4
Section 3 Temperature Board Set Setting.............................................................................5
3.1 Topology Connection..................................................................................................5
3.1.1 (4~20) mA Compatible Mode......................................................................... 5
3.1.2 Networking Mode............................................................................................. 6
3.2 Function Configuration...............................................................................................6
3.2.1 Configuration Environment.............................................................................6
3.2.2 Basic Information Configuration.................................................................... 7
3.2.3 Configuration Information Setting..................................................................7
3.2.4 Sensor Configuration.......................................................................................8
3.2.5 Current Calibration........................................................................................ 10
3.2.6 Variable Monitoring........................................................................................12
Section 4 Adjustment in the Field......................................................................................... 13
4.1 LCD and Button Instruction..................................................................................... 13
4.2 General Adjustment Method.....................................................................................13
4.2.1 List Scan 13
4.2.2 Password Input...............................................................................................13
4.2.3 Function Setting............................................................................................. 13
4.2.4 Data Save 13
4.3 List Function Items................................................................................................... 14
4.4 Description for Special Symbols.............................................................................. 15
Section 5 Maintenance........................................................................................................... 17
Section 6 Technical Specification......................................................................................... 19
6.1 Basic Parameter.........................................................................................................19
6.2 RTD Parameter......................................................................................................... 19
6.3 Thermocouple Parameter..........................................................................................20

Table of Figures
Figure 1 Temperature Board Set Dimension...............................................................................2
Figure 2 Hardware Interface Introduction.................................................................................. 2
Figure 3 Temperature Board Set Sensor Wiring......................................................................... 4
Figure 4 System Connection........................................................................................................4
Figure 5 (4~20) mA Compatible Mode........................................................................................5
Figure 6 Networking Mode......................................................................................................... 6
Figure 7 Basic Information.......................................................................................................... 7
Figure 8 Configuration Information............................................................................................ 8
Figure 9 Sensor Configuration.....................................................................................................9
Figure 10 Current Calibration....................................................................................................11
Figure 11 Variable Monitoring.................................................................................................. 12
Figure 12 Function Switch.........................................................................................................15

Page 1
HART Temperature Board Set | MS0210 |
http://www.microcyber-fieldbus.com
Section 1 Overview
HART temperature board MS0210, using the fieldbus technology, is a new generation of
smart temperature module and it is an indispensable field device for process control. It
can be widely used in the petroleum, chemicals, electricity, and metallurgical industries,
etc.
HART temperature board uses digital technology and it shall match multiple thermal
resistance and thermocouples sensors. It has wide range and simple interface between
field and control room, which reduces the expense of installation, operation and
maintenance.

Page 2
HART Temperature Board Set | MS0210 |
http://www.microcyber-fieldbus.com
Section 2 Introduction
2.1
Dimension
30
M
Φ3
S Z
Unit:mm
56
Figure 1 Temperature Board Set Dimension
2.2
Hardware Interface
The hardware interface of HART temperature board set is shown as Figure 2.
Terminal
Board
P+ P-
Ground
J1 HART Bus
Power Interface
J5 Temperature
Sensor Interface
HART Bus Power
Interface
AL and WP DIP
Switch
Communicatio
n Board
Figure 2 Hardware Interface Introduction
There are 3 main interfaces for HART temperature board set:
Alarm setting (AL) and configuration protection setting (WP) hardware DIP switch;
J1, HART bus power interface (P+ and P-);
J5, temperature sensor connection interface.
22
60
53

Page 3
HART Temperature Board Set | MS0210 |
http://www.microcyber-fieldbus.com
2.3
Failure Alarm and Configuration Protection DIP
Switch
The DIP switch with “AL” is failure alarm current setting and the one with “WP” is
configuration protection setting.
Failure Alarm Setting
HART temperature board set has self-diagnosis function. Once the failure is tested, such
as sensor open circuit, sensor short circuit or AD failure, the board set shall output alarm
current automatically. The alarm current methods depend on the failure alarm current DIP
switch setting of the communication board. When AL DIP switch at OFF position is high
alarm, the alarm current is ≥21.75mA. When AL DIP switch at ON position is low alarm,
the alarm current is ≤3.7mA.
Configuration Protection Setting
HART temperature board set provides configuration protection DIP switch setting. When it
is (DIP switch at ON position) configuration protection, the board set is not allowed to do
any device configuration operation modification. When it is (DIP switch at OFF position)
configuration protection, the board set is allowed to do device configuration operation
modification.
2.4
Bus Power Interface
MS0210 HART temperature board set power and bus share the same a pair of cable and
it is called bus cable. The specific fieldbus cable recommended by IEC61158-2 is
suggested.
Bus cable should not share the same wiring pipe or wiring slot with other devices, and it
shall be away from high-power devices. The bus ends shall be grounded.
There is HART bus power interface for the communication board of HART temperature
board set, and it can be used directly. And there is a terminal board to protect
communication board to protect bus power interface, shown as
Figure 2 Hardware Interface Introduction
Please refer to Section 6.1 “Basic Parameter” for HART bus power voltage and requested
matching resistance in serial.

Page 4
HART Temperature Board Set | MS0210 |
http://www.microcyber-fieldbus.com
2.5
Sensor Wiring
1
2
2-wire 3-wire 4-wire
TC,mV RTD Ω RTD Ω RTD Ω
3
4
Figure 3 Temperature Board Set Sensor Wiring
HART temperature set sensor wiring support 2-wire, 3-wire and 4-wire, shown as Figure 3.
TC represents thermocouple type sensor, mV represent voltage signal, Ω represents
resistive and RTD represents thermal resistive type sensor.
2.6
System Connection
24VDC
HartMPT
Configuration
Software for PC
HART Modem
250Ω
Terminal
Board
HART
Temperatur
e Board Set
Figure 4 System Connection
HART+
HART-
J
1
J
5
+
-

Page 5
HART Temperature Board Set | MS0210 |
http://www.microcyber-fieldbus.com
Section 3 Temperature Board Set
Setting
3.1
Topology Connection
The connection modes of smart transmitter with HART temperature board set can be
divided into 4~20mA compatible mode and networking mode.
3.1.1
(4~20) mA Compatible Mode
HART Interface
Device
4~20mA
Analog
Instrument
Data
Communication
(2-3/s)
Control System or
Other PC Program
Powe
r
Handhel
d
HART
Module
Figure 5 (4~20) mA Compatible Mode
Feature:
1) Connect to upper control system via AI module and HART communication device;
2) Use digital and analog communication;
3) Device address is 0.

Page 6
HART Temperature Board Set | MS0210 |
http://www.microcyber-fieldbus.com
Input/Output
System
HART
Module
3.1.2
Networking Mode
Control System or Other
Master
Handheld
Figure 6 Networking Mode
Feature:
1) Connect to upper control system via HART communication device;
2) Use digital function only and the current is fixed 4mA;
3) Support 64 (polling address is 0~63) devices networking for HART 7.0.
3.2
Function Configuration
HART temperature board set supports Microcyber’s HartMPT Configuration Software and
universal software such HART Organization’s SDC625 for configuration debugging.
Following is an example for HartMPT Configuration Software, including functions:
1) Basic information configuration: configure the basic information of device online,
including tag, address, date, assemble number and so on;
2) Configuration information configuration: configure the configuration information of
device online, including PV range, damp and so on;
3) Sensor info configuration: configure the sensor info of the online device, including type,
wiring, etc.;
4) Current calibration: Can calibrate 4~20mA current of online device, also can set fixed
current output;
5) Variable monitoring: refresh all dynamic variable of selected online device timely and
display trend curve of present device primary value.
3.2.1
Configuration Environment
1) PC with serial port, Windows 2000/Windows XP/Windows 7;
2) HART Modem and serial wire;

Page 7
HART Temperature Board Set | MS0210 |
http://www.microcyber-fieldbus.com
3) Matching resistance 230Ω~550Ω.
3.2.2
Basic Information Configuration
Through basic information dialog, the basic information of the smart transmitter can be
read or modified, including device address, information, description, date, assembly
number, alarm, write protection, manufacturer ID, manufacture, device type, device ID,
long address and version info, shown as Figure 7.
Figure 7 Basic Information
After information modification, click the “Apply” button to download it into device.
1) The address selection range is 0~15;
2) Information can be input 32 characters at most;
3) The maximum length of the description is 16 defined characters;
4) The maximum length of the tag is 8 defined characters;
5) Date range is from the year 1900 to 2155.
6) Assembly number is 6 defined characters at most.
3.2.3
Configuration Information Setting
Through configuration information dialog, the configuration information of smart
transmitter can be read or modified, including displayed device output variable (primary
variable, cold end temperature value, current value and percentage), primary variable info
setting (damp value, unit, upper limit and lower limit) and range calibration, etc., shown as
Figure 8.

Page 8
HART Temperature Board Set | MS0210 |
http://www.microcyber-fieldbus.com
Figure 8 Configuration Information
Damp: range 0~32s
Unit: PV unit modification affects variables related to unit, such as the upper or lower
limit for the range or for the sensor. When you modify the unit, you can’t modify upper
or lower limit for the primary variable range, instead, you should modify them
separately.
The unit can be set as:゜C,゜F,゜R, K, mV, Ohm.
Upper limit of the range: Corresponding to PV value of 20mA output current.
Lower limit of the range: Corresponding to PV value of 4mA output current.
You should press “Apply” to download it into device after the modification.
Set “upper limit of range” with present value: Set the PV as the upper limit of primary
variable range, and keep the lower limit of range the same as previously.
Set “lower limit of range” with present value: Set the PV as the lower limit of primary
variable range, it may probably modify upper limit at the same time.
Set “primary variable zero point” with present value: Set the PV as the primary
variable zero point when the temperature is 0゜C.
3.2.4
Sensor Configuration
You may check the current configuration sensor info (upper limit, lower limit and minimum
span) via sensor info TAB. Also, you may configure the sensor type and wiring with it,

Page 9
HART Temperature Board Set | MS0210 |
http://www.microcyber-fieldbus.com
shown as Figure 9.
Figure 9 Sensor Configuration
Sensor type: Sensor type supported by device, shown as following:
Wiring: It can be set as 2-wire, 3-wire or 4-wire, only effective to RTD.
Sensor Type
Description
0_500R
Resistance, (0 ~ 500) Ω
0_4000R
Resistance, (0 ~ 4000) Ω
CU50
Cu50
CU100
Cu100
PT100
PT100
PT1000
PT1000
100MV
mV voltage signal, range: (-100~100) mV
B_TC
B type thermocouple
E_TC
E type thermocouple
J_TC
J type thermocouple
K_TC
K type thermocouple
N_TC
N type thermocouple
R_TC
R type thermocouple
S_TC
S type thermocouple
T_TC
T type thermocouple

Page 10
HART Temperature Board Set | MS0210 |
http://www.microcyber-fieldbus.com
Cold-end Compensation: It enables or disables thermocouple’s cold-end

Page 11
HART Temperature Board Set | MS0210 |
http://www.microcyber-fieldbus.com
compensation function. When the user is using internal cold-end compensation, the
present cold-end compensation value is internal measurement temperature value.
When the user is using external cold-end compensation, the user may use “external
setting temperature value” to set fixed cold-end compensation value.
Channel status: Display sensor channel status (open circuit, short circuit, etc.)
Sensor channel value: Display original value of sensor channel.
External setting temperature: When external cold-end compensation is set as
“Enable”, the present cold-end compensation value can be set via “external setting
temperature”.
Cold-end compensation temperature: Display present cold-end temperature
compensation value.
R0 correction factor: Correct the sensor’s own error (range 0.9~1.1).
2-wire zero point calibration: When the temperature transmitter is connected to RTD
in 2-wire way, in order to avoid the resistance error in the cable, you should short-
circuit the sensor and execute zero point calibration button.
TC calibration: Factory calibration for thermocouple ranges. (only for manufacturer)
RTD calibration: Factory calibration for thermo resistances ranges. (only for
manufacturer)
Recover to factory default value: Click this, all the data shall be recovered to factory
default status.
Save as factory value: Click this, all the present setting shall be saved as factory
value. Click “Recover to factory”, it shall be recovered to the saved setting.
Recover to factory setting: Click this, all the data shall be recovered to factory status.
If the user has saved factory value, then it shall recover to user’s saved setting.
Otherwise, it shall be recorvered to default factory status.
3.2.5
Current Calibration
The steps of current calibration are shown as following:
1) Connect the loop, an ammeter with the 5 1/2 digit precision should be series-wounded
in the device output loop.
2) Set device rolling address as 0, please refer to basic info configuration. If rolling
address is 0 already, this step can be skipped.
3) Enter current calibration option TAB.
4) Select “current value” as 4mA, when the ammeter is stable, input the value in
ammeter to “adjustment value”, and then click “Apply”.
5) Select “current value” as 20mA, when the ammeter is stable, input the value in
ammeter to “adjustment value”, and then click “Apply”.
6) Select “current value” as blank, makes the device output current as PV value.

Page 12
HART Temperature Board Set | MS0210 |
http://www.microcyber-fieldbus.com
Notes: When the present output current value is high alarm current, the user cannot
calibrate 4mA. When the present output current value is low alarm current, the user
cannot calibrate 20mA.
Configure Current Fixed Output
The user may set fixed current output in current calibration tab. Input the value of the
current the smart transmitter will be fixed on, to “fixed current value”, and click the button
“enter/exit fixed current mode” to enter or exit the mode of fixed current output. The text of
the button can display “exit fixed current mode” and “enter fixed current mode” in turn, to
tell users what to do.
In the run of the HART smart transmitter, compare the value of the primary variable and
range upper/lower limit of the primary variable continuously. When the value of the
primary variable exceeds the range of the primary variable, the smart transmitter will
output fixed current to indicate that the value of the primary variable is exceeded. When it
is over the upper limit, the smart transmitter output fixed current 20.8mA;When it is less
than the lower limit, output is 3.8mA.
Figure 10 Current Calibration
Note: Calibration current and fixed current output functions are only in the moment when
the polling address is 0. It will be at absolute digital communication mode at other polling
addresses, the failure info is “Command Execution Failure”.

Page 13
HART Temperature Board Set | MS0210 |
http://www.microcyber-fieldbus.com
3.2.6
Variable Monitoring
The user is able to refresh all the dynamic variables of the selected device and display
trend curve of present device primary variable via variable monitoring tab. The present
refreshing variables are: PV value, current value, percentage and cold end temperature.
Figure 11 Variable Monitoring

Page 14
HART Temperature Board Set | MS0210 |
http://www.microcyber-fieldbus.com
Section 4 Adjustment in the Field
4.1
LCD and Button Instruction
HART temperature board set has lattice LCD and local button adjustment function, and
the user can do parameter adjustment in local for HART temperature transmitter (HART
temperature board set + sensor + housing).
There are 3 buttons, 【M】,【S】and【Z】.【M】is mode button, in charge of “function
option”, “cursor move” and “confirm”. 【S】and 【Z】are input adjustment buttons, in
charge of “list front/back turn” and “data add and subtract”.
4.2
General Adjustment Method
4.2.1
List Scan
In measurement display mode, press 【M】for lone, to enter function list tab, and then
press 【S】or【Z】to scan the whole function list tab.
4.2.2
Password Input
Press 【S】or【Z】to adjust list as “Fun 01”, and the list is password function, so the user
shall only operate other function if the input password is right. And then the user shall
press 【M】to enter password input status, and the password is “00005”. Press 【S】or
【Z】to adjust the value, and then press 【M】to adjust cursor position, after that, press
【M】to confirm, and then the system shall be return automatically to list scan mode.
4.2.3
Function Setting
In list scan mode, press 【S】or【Z】to choose function to adjust, and press 【M】to enter
function adjustment, after that, press 【M】to confirm and return to list scan mode, and
then go on to adjust following functions.
4.2.4
Data Save
After finishing the function setting, in list scan mode, press 【S】o【r Z】to adjust list as “Fun
99”, and this list is data save confirm function. Press 【M】to enter, 【S】or【Z】to choose
“SAVE”, and then press 【M】to confirm to save. After successful save, the LCD will show
“SUCCESS”. Otherwise, there is “FAILED” is save is not successfully or no modification.
Now the local adjustment functions are finished, the user shall adjust many function items
once, and then adjust to “Fun 99” to save all the data once.

Page 15
HART Temperature Board Set | MS0210 |
http://www.microcyber-fieldbus.com
4.3
List Function Items
Here is the introduction for HART temperature board’s local button operations. With field
adjustment, the user shall adjust PV unit, PV upper limit, PV lower limit, sensor type,
sensor wiring, etc. The supported functions are shown as following:
Notes:
If the sensor type is resistive, there shall be no display for “Fun 25” cold end
compensation function in list.
No.
Parameter
Remarks
01
PASSWORD
Local adjustment, input password: 00005
Save as factory value, input password: 62259
Recover as factory value, input password: 25917
It shall execute as soon as input password for “Save as
factory value” and “Recover as factory”.
03
LOWER
User present value to set PV lower limit, after the setting, the
system shall save automatically, no need to return to “Fun
99” to save manually.
04
UPPER
User present value to set PV upper limit, after the setting, the
system shall save automatically, no need to return to “Fun
99” to save manually.
05
DAMP
0~32 Set damping time 0~32s
06
LRV
Passive setting for PV lower limit
07
URV
Passive setting for PV upper limit
08
ZERO
User present value to set PV zero point
10
FUNCT
Choose PV output function
11
DISPLAY
Set LCD display content
12
UNIT
Set PV unit
22
SENSOR TYPE
Set temperature sensor type
23
SENSOR WIRE
Set RTD wiring: 2/3/4 wire
25
COLD
COMPENSTATE
Thermal couple cold end compensation function option
26
TWO WIRE
CALIBRATION
Resistive type sensor 2 wire zero point calibration
99
SAVE
After the above functions, the user shall execute SAVE
function to finish local adjustment.

Page 16
HART Temperature Board Set | MS0210 |
http://www.microcyber-fieldbus.com
If the sensor type is resistive, and the wiring is not 2-wire, or the sensor type is mV,
Table of contents
Other Microcyber Measuring Instrument manuals
Popular Measuring Instrument manuals by other brands
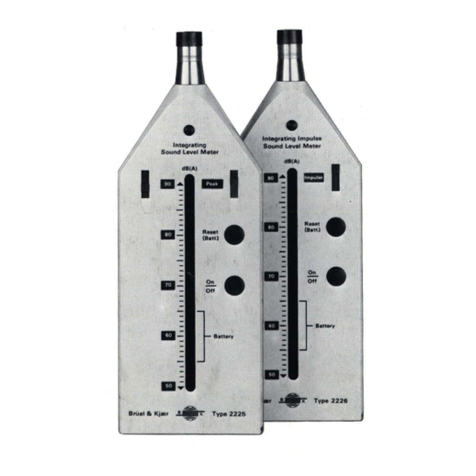
BRUEL & KJAER
BRUEL & KJAER 2225 instruction manual
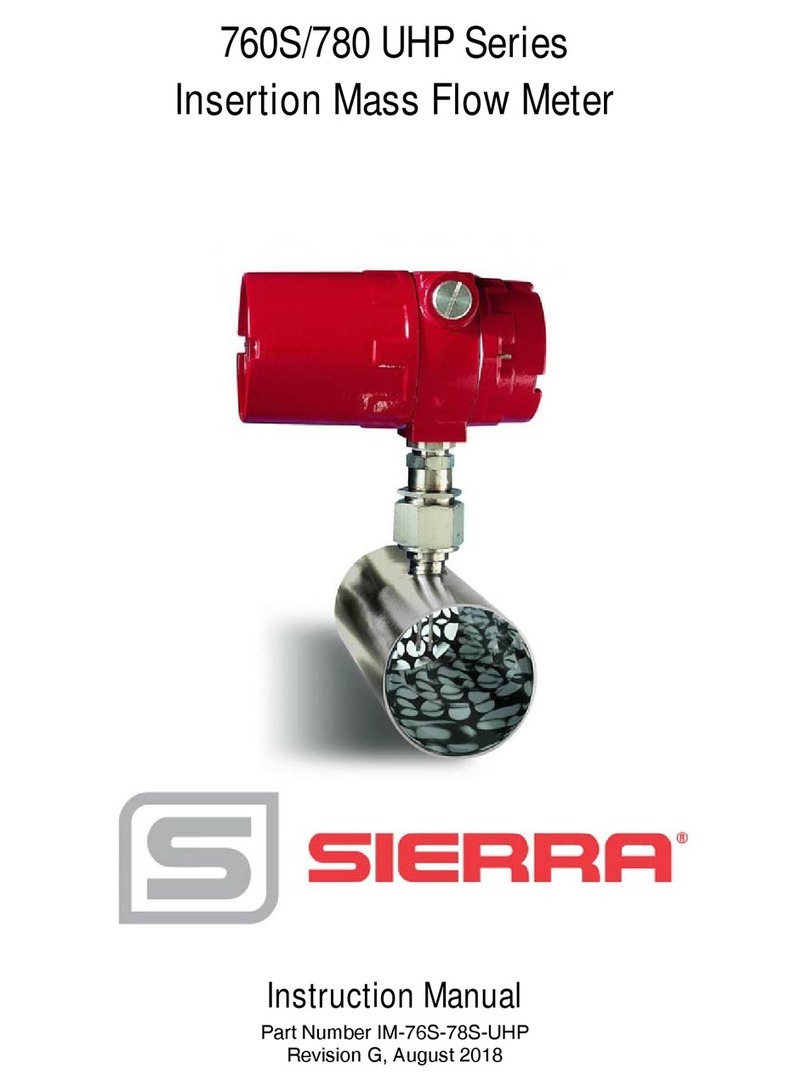
Sierra
Sierra 760S Series instruction manual
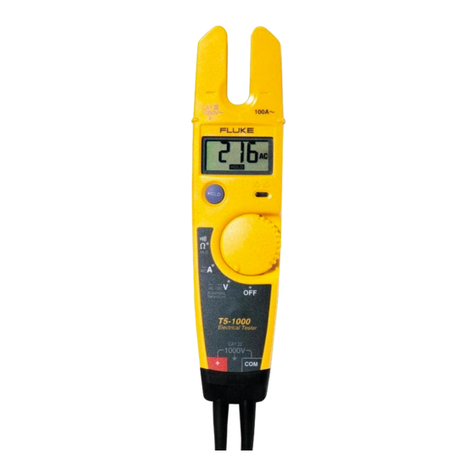
Fluke
Fluke T5-600 Service information
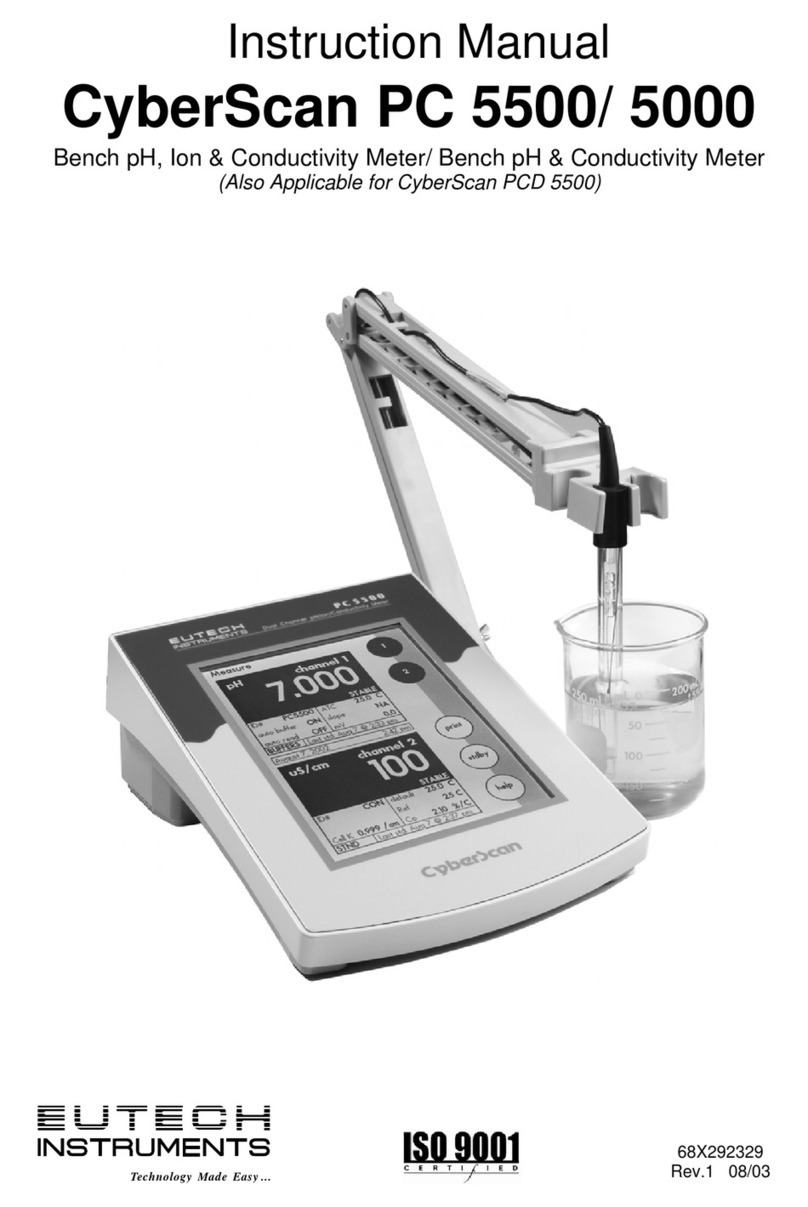
EUTECH INSTRUMENTS
EUTECH INSTRUMENTS CYBERSCAN PC 5000 PHCONDUCTIVITY METER instruction manual
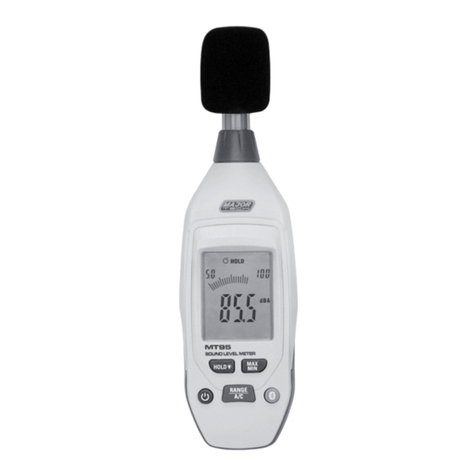
Major tech
Major tech MT95 instruction manual
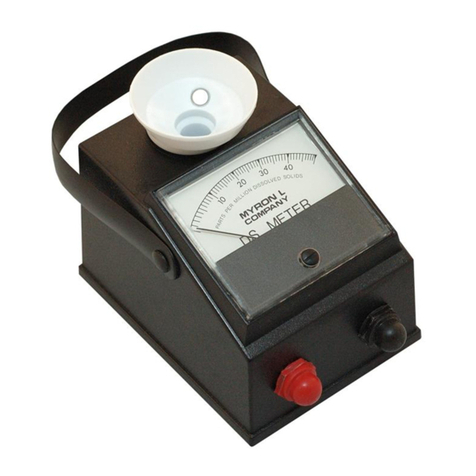
Myron L
Myron L 512T2 Operation instructions