microSYST MS8347 Parts list manual

COMPETENCE IN
MEASUREMENT
WEIGHT BATCHING CONTROLLER
with Analog Output
and MODBUS RTU ommuni ation
MS8347
V 2.3
TECHNICAL DESCRIPTION
AND
USER MANUAL
PLOVDIV 2020
Document revision 2020-04-07

NCONTENT Стр
I. ORDER CODE 2
II. FE TURES 3
III. DV NT GES 3
IV. DESIGN TION 3
V. TECHNIC L D T 4
VI. FRONT ND B CK P NEL. TERMIN L ND CONNECTION 5
VII. OPER TING MODES 6
VIII. OPER TING GUIDE 8
IX. SYSTEM P R METERS OF THE REGUL TOR 11
X. CTIONS G INST INTERFERENCE 13
XI. COMMUNIC TION - MODBUS RTU 14
I. ORDER CODE
Document revision 2020-04-07
2
MS 8347 - x.x.x.x.x.x.x.x.x.x
Analog output -
4-20mA ISO
K1 K2 K3
AA BA CA
AB BB CB
AD BD CD
- no
- Relay
- Triac
5A/250V
2A / 250V
- OC NPN iso
AF BF CF
U =70V I = 500 mA
CEmax cmax
Power suppl -
220 VАС/50 Hz
MS 8347- 1.R.W.PA.C1 AF.BF.CF.S1.I1.
Communication
- RS485 MODBUS
Displa (6 digits) -
LED 14 mm
Displa color
- Red
Sensor suppl / Sensitivit
.
5 VDC : 1 … 7 mV / V
Example:
Power suppl
PA
-
-
220 V AC / 50 Hz
PB 24 V DC
Sensor suppl / sensitivit
W
- 5 VDC : 1 … 7 mV / V
X - Other
Communication
C0 - No
C1 - RS485 MODBUS RTU
Speed Conversion
S1 - 12 5 mS / 80.0 SPS
S2 - 60.0 mS / 16.7 SPS
Displa ( 6 digit format)
0 - LED 10mm
1 - LED 14 mm
Displa color
R - Red
G - Green
Analog output
I
0 - No
I1 -
2 -
3 -
- Other
0 20 mA
4 20 mA
I 0 10 V
IX
I
Speed Conversion-
12 5 mS/80.0 SPS
Speed Conversion
S1 - 12 5 mS / 80.0 SPS
S2 - 60.0 mS / 16.7 SPS

II. VERSION FEATURES
●MS 8347 is implemented in two hardware variants depending on requirement of conversion speed.
The software supports both. It is necessary in Menu / Parameter / Bit – SYST/rS485/bit6” with
which hardware works the software to be specified. Depending on that the maximum conversion
speed is 12.5 mS /80 SPS – number of measurements per second/ or 60 mS / 16.7 SPS/. In both
variants for greater noise immunity can be operated with 100 mS / 10 SPS /.
●MS 8347 operates as a controller / it controls it's outputs, only if the tare wei ht is less than that of
Calibration / CALL /.
●MS 8347 forms three independent galvanically isolated power supply voltages:
- Power supply of the Measurement circuit
- Power supply of Analogue output and digital inputs.
- Power supply of RS485
●The analogue output signal has insensitivity of the zero about 5 mV, i.e. in zero input indication the
output is about 5 mV ( 0.05% in range 0 ÷ 10 V ) . Above that level the output operates linearly with
accuracy 0.003% FS.
III. ADVANTAGES
●High measurement accuracy – 0.003% FS.
●User selectable measurement speed - up to 80 SPS.
●Galvanic insulation of the measurement part from analogue output, digital inputs and outputs and
from RS485.
●Fast selection of up to 4 sets of parameters by combination of two digital inputs
●utomatic counter of ready doses.
●nalogue output that transmits the input process variable up to 0.003% linearity.
●MODBUS RTU communication by galvanically insulated RS485.
IV. DESIGNATION
MS8347 is suitable for including in dosing or batching systems by weight method. The input signal is
formed by bridge weight sensor which is supplied by the device. The sensitivity and the power supply of
the sensor are hardware fixed and have to be specified in the order code.
The analog output which is galvanically insulated from the input signal transmits the measured
process variable. Most commonly used is uniform signal 0 ÷ 20 m DC; 4 ÷ 20 m DC ; 0÷ 10 V DC which
has to be specified in the order code.
The device has four galvanically insulated from the measurement part digital inputs TARE, ZERO,
S1 and S2 which are designed respectively to tare and reset the measurement, and for selection of
specified in advance set-points.
The controller has three digital outputs, which are user configurable.
Document revision 2020-04-07
3

V. TECHNICAL DATA
Analog input from bridge weight sensor
- power supply / sensitivity of the
sensor
5 V D / 1 ÷ 7 mV/ V
...................................(other)
- measurement accuracy 0.003%
- temperature stability 5 ppm/ °C
- conversion time without software
filter:
- fast / slow conversion
ccording to the configuration of order code
and from SYST/rS485/bit6 menu:
- 12.5 / 100 mS or 60 / 100 mS
- software filters:
arithmetic mean - of 1
level exponential – of 2 level
•rithmetic mean - 1 ÷ 16 measurements ( х10 ms)
•exponential - attenuation % - 0, 50, 75, 88, 94 %
Analogue output, DC 1
- transmitting the measurement 0 ÷ 20 m 4÷ 20 m 0 ÷ 10 V ....................... other
- conversion accuracy 0.003%
- temperature stability 5 ppm/ °C
- output forming time 60ms
- measurement part insulation 1500 V DC for 1 s
Digital inputs 3
Tarе, Zero/Start,
S1, S2-selection set of parameters-2
Low active level NPN to GND iso
minimum time to Tare and Zero tmin= 20 ms
Digital outputs 3
K1, K2, K3
•Relay 250 V C / 5
•Triac 250 V / 2
•NPN OC iso 500 m 70V transistor open collector,
insulated from measurement part, required an external
power supply. Insulation - 1500V DC for 1 s
- output forming time 20 ms
Communi ation MODBUS RTU RS485;
9600 bps; parity non/even; 1 / 2 stop
Power supply
Power supply 220 V C / 50 Hz 80 ÷ 250 V C / 50 ÷ 60 Hz 24 V DC
Display and Keypad
- display range 6 seven segment LED's 14 / or 10/ mm - 99999÷99999
- display format XXXXX, X.XXXX, XX.XXX, XXX.XX XXXX.X
program selectable, by decimal point
- display color red green transparent
- LEDs 4
- keypad Semi sensor keypad
Operating onditions
Operating temperature 0 ÷ 50 °C
Operating relative humidity без кондензация 0 ÷ 80 % rh
Protection class IP 40
Dimensions
Overall dimensions (WxHxL) 96 х 48 х 128 mm
Mounting Panel in hole 90 х 44 mm
Weight Max 400 g
Storage
Storage temperature
Relative humidity
-10 ÷ 70 °C
without condensation 20 ÷ 90 % rh
Document revision 2020-04-07
4

VI. FRONT AND BACK PANEL. TERMINAL AND ELECTRICAL CONNECTION
●In 4-wire onne tion the relevant neighboring terminals 1,2 and 5,6 are shorted.
●The ontroller has four LEDs - К1, К2, LOCK and PROG. К1, К2 and LOCK light when
the respective outputs К1, К2 and К3 are active. The PROG LED light in programming
mode. The PROG LED flashes in B mode with the maximum weight reached if it is not
displayed.
Sele tion of parameter set (Prog 1 ÷ 4) for dosing by the state of external inputs S1, S2 onne ted
to GND iso / terminal 30 / -A tive 0 or off - 1
Input Terminal Prog 1 Prog 2 Prog 3 Prog 4
S1 29 0 0 1 1
S2 28 0 1 0 1
Document revision 2020-04-07
5
SENSOR
1 2 3 4 5 6 7 8 9 10 11 12 13 14 15
30 29 28 27 26 25 24 23 22 21 20 17 16
GND
iso
AOut
S2
S1
Voltage
output Aout
V
Current output
active Aout
+-
mA
Current output
passive AOut
+
-
mA
Vext 9 36 V
External power supply
22
23
2324
19 18
U
UU
+
RELAY
OUTPUT
TRIAC
OUTPUT
NPN OC
insulated
output
Connection of inputs S1,
S2, Tare, Zero/Start in two
and more devices to one
signal source
30
29 28 27 25
30
29 28 27 25
DEVICE 1
DEVICE 2
+
-
-
...
Tare
Zero/
Start
Power supply
of the device
RS-G
A
B
Rs485
RS485
MODBUS RTU
Vexc+
Vref+
Vs+
Vs-
Vref-
Vexc-
In 4-wire connection
terminals 1, 2, and 5, 6
are shorted!

VII. OPERATING MODES
The controller is used as a part of controlling of processes for dosing of materials. Based on
measured input weight three digital and one analog output are formed.
They are supported 4 sets of operating set points(SP):
•Dose 1 / weight of switching K1 “dose 1”
•Dose 2 / weight of switching K2 “dose 2”
•Dose 3 / weight of switching K3 “dose 3”
Selection of one of the four sets when setting the set-points or in operating mode is set by
combination of the inputs S1, S2.
The choice of one of the four sets of parameters in the operating or setting mode is set by a
combination of the status of the inputs S1, S2 see item VI.
Using the parameter “ConFiG” (Confi uration word that defines the functionality of the controller
and represents an inte er, the sum of the values of seven bits) in the system parameters (see item IX), by
setting the value of Bit 7, the corresponding operating mode is selected:
7.1 MODE A - Dispenser / Mixer: “ConFiG” (Bit 7 = 0)
●Declines in the graph are eventual interference or vibrations. If the measured value has reached
a certain set-point the respective output become active and it is active whether the measured
value falls below the set-point. The output is active till the pressing the Stop button, timeout
tOff≠ 0 or reaching the last dose.
fter power supply voltage the device is waiting for start of Zero/Start input. n active level of this
input starts the process. K1 output becomes active. When reaching dose1, K1 becomes inactive and K2
becomes active. When reaching dose1+dose2, K2 becomes inactive and K3 becomes active. When reaching
dose1+dose2+dose3, K3 becomes inactive. Next start – in transition from inactive to active level of
Zero/Start input.
Sequence of switching Start→К1→К2→К3→Stop can not be changed.
The controller gaps one or more stages if the weight at start exceeds their set-points.
The whole process is limited in time by tOff parameter.
Start can be configured (parameter ConFiG) with (Bit 6 = 64) or without (Bit 6 = 0) taring.
It is permissible integration of inputs Tare and Zero/Start with which is obtained taring at
startup.
Start by active level of input Zero/Start when switching on the power supply voltage have to be
weighed against the option “tare at startup”. If the option is active or if inputs Zero/Start and Tare are
Document revision 2020-04-07
6
dose1
dose2
dose3
output K3
K2
K1
tOff
OFF
OFF
OFF
Start
weight
time
MODE А

integrated can be used a pulse not constant input signal to avoid re-tare in power supply failure and
restoration.
On the front panel there is a Start/Stop button which is with analogous function or stops the
process if it is already started.
Inversion of the outputs is possible by parameter ConFiG(Bit 0,Bit 1иBit 2)..
Parameters dose1, 2 and 3 are dosing set-points (for example when mixing various ingredients)
7.2 MODE B - Comparator / The step ontroller /: "ConFiG" (Bit 7 = 128)
7.3
●Declines in the graph are eventual interference or vibrations. Above certain set-point the
respective output become active and it become inactive if the measured value is below the
set-point. At reverse there is no hysteresis.
Parameters dose1, 2 and 3 are switching levels.
fter power supply voltage a normal operating mode is activated. Three digital outputs are
formed.
Output K1 become active exceeding the weight “dose 1” and it become inactive at weight
less than “dose 1”. Its logic of action can be inverted by bit 0 of the “ConFiG” parameter.
Output K2 become active exceeding the weight “dose 1 +dose 2” and it become inactive at
weight less than “dose 1 +dose 2”. Its logic of action can be inverted by bit 1 of the
“ConFiG” parameter.
Output K3 become active exceeding the weight “dose 1 +dose 2 +dose 3” and it become inactive at
weight less than “dose 1 +dose 2 +dose 3”. Its logic of action can be inverted by bit 2 of the
“ConFiG” parameter.
Input Zero/Start has function “reset” of the tare (indications as after calibration)
In this mode the Start/Stop button of the front panel is not used.
7.2.1 MODE B (MAX MODE) - SHOWING MAXIMUM WEIGHT:
It is a sub-mode (MAX MODE) of basic mode B, so the configuration of the unit needs to be done
from parameter “ConFiG” (Bit 7 = 128) to basic mode B and parameter “rS 485” - Confi uration word
(Bit 6 = 64 ) for MAX MODE.
This mode B variant is intended for strength testing. The test consists of loading the test body with a
force / weight from initial PV to fracture or (PV_max).
Document revision 2020-04-07
7
dose1
dose2
dose3
K3
K2
K1
MODE B
{
ON
ON
ON
ON ON
ON
ON
{
{

Status / Event After Power ON After a tive input Start / Zero
Display value PV PV_max
PROG LED flashes It does not light
Cal ulation of PV_max PV_max = 0 PV_max = PV
With Tare input a tive PV_max = 0 PV_max = 0
●The outputs function as in mode B.
●In this mode, the unit always calculates the maximum value in tact with the outputs.
If current PV> PV_max, then PV_max = PV.
●The Prog LED does not light when PV_max is displayed and flashes if PV is displayed.
●The readings can be changed by the START / STOP button on the front panel. It is accompanied by
PV / PV hi messages. This only changes the display and does not affect the accumulated PV max.
●When power is ON PV_max = 0 and the unit displays the current PV measurement.
●For each active Start / Zero input, PV_max assigns a PV value. (PV_max = PV)
●With each tare PV max = 0.
●Tare Input - If used, it must be Zero / Start independent via “ConFiG”, or it will only act after
Zero on the keyboard.
“ConFiG” (Bit 6 = 64 + Bit 7 = 128)=192 - Taring is independent of zeroing.
“ConFiG” (Bit 6 = 0 + Bit 7 = 128)=128, Tare will act after Zero on the keyboard.
Other features:
●Zero from the keyboard does not directly affect PV_max.
●The display filter does not affect the PV max but the other filters does.
●PV_max is available via MODBUS, as well as a bit for the corresponding MAX MODE
configuration (see table). Below
●PV_max is al ulated in all operating modes, but is only displayed in the urrent mode. In
others, it is only available through MODBUS.
VIII. OPERATING GUIDE
The controller supports up to 4 parameter sets with preset assignments of dose_1, dose_2
and dose_3. In the PARAMETER SETTING mode, the parameters for each set are set.
Before starting the dosing process or in the "P R METER SETTING" mode, the desired set
of parameters, namely Prog 1, Prog 2, Prog 3 or Prog 4, is selected using the inputs S1 and S2.
Document revision 2020-04-07
8

8.1. SCREEN MENUS AND BUTTONS FUNCTION
Button Fun tion
Up
By pressin the button to chan e the on-screen menus in the followin sequence :
- Zero – Display the tare value
- Count – Number of doses
- Call – Calibration mode – it can be hidden
- Prog – Parameters setting
- Measure – Current measured value
5 sec. after usin the button, oes back to the main menu.
Left Go back to the main menu – Measure
Enter/Prog
According to currently selected menu this button has following functions:
Cuurent Menu Fun tion
Zero Zero Clearing the current tare
Count Clear Count Clearing the counter
Call Calibration Enter in calibration mode
Prog Programming Enter in parameters setting mode
Enter/Prog
+ Left
Tare in mode – Measure. The buttons pushed and hold up to stop the flashin the
messa e „Tare“.
Function Tarе , Zero and Call can be hidden by “CONFiG” parameter from SYSTEM
PARAMETERS menu
Start/Stop Start/Stop in mode А
8.2 TARE – / with buttons „Enter/Prog + Left” or with digital input /
The device can be tared by ‘Tarе’ input at any time except calibration procedure,
during setting the parameters and during filling for mode A. This also applies to the input
‘Zero/Start’ - clearing of the tare / filling start.
In mode B, for tare there is additional condition to go through 'Zero’ first (indications as
after calibration). This condition can be canceled by parameter in CONFiG. When taring t
he weight measurement starts 1 s after activation of the input and continues 1s. If this weight
is bigger than tArЕHi (% от HiL-t) the operation becomes invalid and flashing
inscription “tArЕEr” appears on the display.
If the button Enter / Prog is pressed at power on (activation of system parameters), tare is
performed unconditionally. If the measured weight> tArEHi message appears "tArEEr" to
power off.
8.3. RESET - Zero for mode В
This function is activated by the digital input or by keypad if this is enabled by the
configuration word “CONFiG”
When activating the respective input the tare value is reset. This function is not active during
calibration, during setting of parameters and during filling for mode A.
Document revision 2020-04-07
9

8.4. CALIBRATION - Call
Before alibration the devi e has to be tared.
Reference weight has to be placed.
llow to establish the value of the display.
Enters “C LIBR TION” mode with button “Enter/Prog” .
Use the arrows to correct the displayed value under placed reference weight.
Press the “Enter/Prog” button to confirm and out of calibration.
Exit from “CALIBRATION” menu is performed automatically also 10 sec. after pressing a
button and the changed value is stored.
8.5. DOSES COUNTER – Count
The controller makes automatic reading of number of switching of К3 and stores them in
nonvolatile memory. The counter is incremented by 1 when the measured weight exceeds the
parameter doSE 3. fter reaching1000000 the counter is reset and continues its work. In the main
menu there is an option to reset the counter (see “Operating guide” point 1)
8.6. SETTING THE DOSING PARAMETERS - Prog
Setting of parameters – mode “Prog”. Changing the parameters is done through “Left” and
“Up” buttons. The current digit for change is shown by flashing dot, using “UP” button the
value is changed and using “Left” button the position of the flashing dot is changed. If the
change of sigh of the number is enabled it is changed when the flashing dot is on leftmost
digit.
doSE1 Dose1 / weight of changing of K1. Dimension and decimal point according to
maximum measured weight and resolution of the sensor.
In mode A it represents a dose, and in mode B – level.
ll features are in effect for the next two set-points.
doSE 2 Weight of changing of K2
doSE 3 Weight of changing of K3
fter setting of “doSE 3”, “End“ appears on the display. When pressing a button other than
“Enter/Prog” proceed to re-setup of set-points. By pressing the “Enter/Prog” exit from
setting mode.
8.7. ERROR MESSAGE
Error Fun tion
“ErrorA” Measurement error. It is necessary the connection of measuring sensor with the device to
be checked. Parameter ErLuvL determines the limit for activation of this message.
“ErrorU” The tare weight together with some of operating set-points exceed the maximum
measured weight by the device.
“tArEEr” Tare weight > t rЕHi (% from HiL-t).
Document revision 2020-04-07
10

IX. SYSTEM PARAMETERS OF THE CONTROLLER
●Available when button Enter/Pro is pressed after power until inscription „Tune“ appears on the
display. After releasing the button “SYSt” appears on the display. After pressing the button
Enter/Pro ” parameters from the following table appear on the display:
Parameter Fun tion Value
A1
Slope of the analog input.
(It is calculated automatically in calibration mode).
Not to be change !
± 99999
( / 1024 )
Point
Position of the decimal point - 4 most significant bits are read, i.e.
allowable values 128, 64, 32, 16 and 0 for :
0.0000, 00.000, 000.00, 0000.0 and 00000
Hi L-t Maximum value of set-points in mode B or their sum in mode A.
It determines the limits when changing them.
tArЕHi
Maximum weight of tare (% of Hi L-t) .
If the weight is above this limit when try to tare appears message TArEEr
up to correct tare and is not perceived start mode A.
0 ÷ 100
Filt D Coefficient of the display filter. * 0.5 0.00 ÷ 1.00
Filt J Threshold of clearing of display filter. * 100 0 ÷ 99999
ConFiG Configuration word. For setup see below. 0 ÷ 255
rS 485 Communication parameters. For setup see below. 0 ÷ 255
Adr rS Modbus address 0 ÷ 255
Flt Ar ** verage filter of the measured weight. * 1 1 ÷ 5
Flt ЕP *** Exponential filter of the measured weight. * 1 1 ÷ 5
Flt J Threshold of reset of the filter as % of the range. * 0.1 0.1 ÷ 100.0
Flt t Time for filter bounce * 0.1 0.00 ÷2.00 s
Hi nE-t Weight corresponding to the upper limit of the analog output range
Aout = ( AP1 * W / Hi nEt+AP0 ) *16
{W –current indication, out – value of the input of D C}
0 ÷ 99999
AP1 Multiplier factor of the analogue output
Not to be
change !
-99999 ÷ 99999
AP0 Coefficient “shift” when forming out -99999 ÷ 99999
ErLeuL Limit of the message Error – measurement error.
When measuring values under these values Error appears on the display.
0 .. 200 х 32
( DC units)
t Off In mode А – time delay for dosing process . Start after set point of first
output. This option is an eled with value 0. 0 ÷ 65535 х 2s
End End. For exit „ Enter/Prog”.
* Recommended values
** The values of the parameter correspond to the following average amounts:
1 – single measurement
2 – 2 consecutive measurements
3 – 4 consecutive measurements
4 – 8 consecutive measurements
5 – 16 consecutive measurements
*** In a larger value of the parameter the filter is deeper.
Document revision 2020-04-07
11

“ConFiG” - Confi uration word - sum of the numbers from chosen options have to be entered
(i.е. Sum of 8 numbers) *
Bit 0 Inversion of К1 output ** NO 0
YES 1
Bit 1 Inversion of К2 output NO 0
YES 2
Bit 2 Inversion of К3 output NO 0
YES 4
Bit 3 Calibration menu “Call”
Enabled 0
Disabled 8
Bit 4 Tare from front panel buttons - T RE Enabled 0
Disabled 16
Bit 5 Tare reset from front panel buttons - ZERO
Enabled 0
Disabled 32
If it is in mode А If it is in mode B
Bit 6 It doesn't tare at start up Tare is possible after reset only 0
It tare at start up Tare is independent of reset 64
Bit 7 Selection of operating mode Mode А 0
Mode B 128
Setting the onfiguration word
Each bit in the configuration word has weight value and in the configuration word have to be
entered sum of the weight values.
•Example for setting of “ConFiG” parameter:
“CONFiG” =0+0+0+8+0+0+64+128=200
Device Confi uration: K1, K2 and K3 without invert; Call menu is disabled; allowed Tara and Zero
via the keyboard, non-resetting tare; MODE B
Changing this values to be done with caution.
Once activated the access it is possible to power off.
When entering setting of system parameters, the outputs are in inactive state (it depends on
inversion options in “ConFiG”).
Normal output – normally open; Inverted – normally closed.
** Inversion of К1 output – example for mode B:
measured weight < doSE 1 Measured weight ≥ doSE 1
normal К1 is inactive К1 is active
inverted К1 is active К1 is inactive
Document revision 2020-04-07
12

“ rS 485” - Configuration word
- sum of the numbers from hosen options have to be entered (i.e. sum of 7 numbers) *
Bit 0 WRITE DIS BLE
(It can be reset by menu of the device only)
NO 0
YES 1
Bit 1 BRO DC ST DIS BLE NO 0
YES 2
Bit 2 EVEN P RITY NO 0
YES 4
Bit 3 2 STOP BITS NO 0
YES 8
Bit 4 DC SPEED – this bit selects the conversion speed - fast / slow HIGH 0
LOW 16
Bit 5
DC TYPE - specifies the type of DC convertor,
which is built-in in the controller.
Wron value stops the measurement !
DS 0
D 32
Bit 6 MAX MODE NO 0
YES 64
X. ACTIONS AGAINST INTERFERENCE
1. Re ommendations for use of onne ting wires
•The able onne ting the sensor to the ontroller has to be shielded. The shield has to be
onne ted to only one end of the able to the ground bus of the power sour e.
•Wires that transmit a similar type of signals can be packed together but if the signals are
different the wires must be separated for prevent electromagnetic interaction.
•When there has to be crossed wires with different types of signals this must be done at an
angle of 90 degrees and a long distance.
•Wires which carry weak signals and wires connecting the sensors to controller must not be
near contactors, motors, generators, radios and wires which carry large currents.
2. Noise suppression by using of built-in filters in the ontroller
•In the controller there are three software filters – average and exponential for the value used
for control functions and another that filters this value before it displayed.
Document revision 2020-04-07
13

XI. MODBUS RTU RS485 COMMUNICATION (option)
The device is MODBUS RTU SL VE with possibility for communication of 9600 bps by
RS485 2WIRE line. In standard performance without using a repeaters, to one line can be connected
up to 32 devices, with repeaters - up to 247. There is an option for a special performance for up to
128 devices without repeaters. In parameters table in column HOLDING REGISTER DDRESS
are presented the addresses of the relevant parameters. Here will be considered other communication
options. There is equality between parameter or operating mode change through the front panel
buttons and change by network – i.e. the device can be influenced simultaneously from both
sources.
IMPLEMENTED MODBUS FUNCTIONS
MODBUS
FUNCTION CTION
01 Reading single bits. /read oils/
03 Reading of HOLDING REGISTERS, /read holding register/
05 Writing single bit, /preset single oil/
06 Writing a single HOLDING REGISTER, / write single register /
10 Writing multiple consecutive HOLDING REGISTERS. /write multiple register/
HOLDING REGISTERS
Label Address Data Show Label Address Data Show
Doze3 10 Long Unsignet AP1 98 Float
//Doze3W2 12 Long Unsignet AP0 100 Float
//Doze3W3 14 Long Unsignet Config 102 MSByte Unsignet
//Doze3W4 16 Long Unsignet DPoint 102 LSByte Unsignet
Doze2 18 Long Unsignet FLT J 103 Integer Unsignet
//Doze2W2 20 Long Unsignet FLT AR 104 MSByte Unsignet
//Doze2W3 22 Long Unsignet FLT EP 104 LSByte Unsignet
//Doze2W4 24 Long Unsignet FLT T 105 LSByte Unsignet
Doze1 26 Long Unsignet Filt Displ 107 LSByte Unsignet
//Doze1W2 28 Long Unsignet Filt Displ J 108 Integer Unsignet
//Doze1W3 30 Long Unsignet T off 111 MSByte Unsignet
//Doze1W4 32 Long Unsignet DEV ID = 5457 126 Integer Unsignet
Slope 82 Float MOD ADR 127 Integer Unsignet
Hi L-t 86 Long Unsignet CNT 208 Long Unsignet
TARE Hi 92 MSByte Unsignet PV 210 Float
ErrLvl 94 MSByte md 212 MSByte Unsignet
HI NET 96 Float
Document revision 2020-04-07
14

COIL ADDRESS
Label Address Label Address
K1 inv 1632 2 STOP BITS 1763
K2 inv 1633 ADC SPEAD 0-HI; 1-LO 1764
K3 inv 1634 ADC TYPE 1765
Disable Clbr 1635 ZARO/START IN 2104
Disable button TARE 1636 K3 2107
Disable button ZERO 1637 K2 2108
TARE in mode B : 1-NO, 0-YES 1638 K1 2109
MODE: 0-A; 1-B 1639 TARE IN 2528
WR DISABLE (ENABLE ONLY FROM 1760 S1 2530
BROADCAST DISABLE 1761 S2 2531
EVEN PARITY 1762
●For MS8347, DEV ID = 5457
●Float parameters are in IEEC754 format.
●For ST RT/STOP and T RE by network „cmd“ parameter is used
- Record of 90 is equivalent to activation of input Start for ~ 50ms
- Record of 150 is equivalent to activation of input Tare for ~ 50ms
- Record of 32 leads to Stop
The value is automatically reset after record of a value.
●Indexes W2,W3 and W4 ….. the relevant parameters, selected by the positions of both
inputs for selecting of set-point S1 and S2.
●The parameter 1 of the device screen is displayed x1024, ie read over the network 1
and the menu of the device would be 1024.
●Calibration in the network is the value of the reference weight is saved in PV.
●The decimal point is decorative and the device doesn't scale. For example 111,22
appears on the display but PV will be written 11122. This is the same for all parameters
with weight dimension.
●The parameters with time dimension also be read as a whole numbers without decimal
point.
●For example 2.23 is readed 223
●The response time of the device is determined by the DC and the mode to be used,
but it can't be < 10 ms.
●When А1=1024 the readings are obtained in DC code respectively 18 bit for DS
and 20 bit for D. 0 mV is the middle of the ran e, and the ne ative value is
displayed 0
●The parameter 0 (offset of the measurement) is service informative. 0 = 0.
Not to be changed!
Document revision 2020-04-07
15

WARRANTY CARD
Warranty Card № : .................................................
Warranty : ................................................. months
Serial number : .................................................
The product is bought by: ..................................................................
with invoice № : ............................../...... ....... 20........
WARRANTY CONDITIONS
The warranty consists of free repair of all manufacturing defects that can occur during the
warranty period. The repair is done by presenting of this warranty ard in the servi e
base with whi h is bought the produ t. The warranty does not cover damage caused by
poor transport, poor storage, incorrect usage, forces of nature, failure to follow instructions
and when others made an attempt to remove the defects. In these cases the defect can only
be removed for a fee.
Service during the warranty period and settlement of claims is done under the current
legislation.
REPAIRS MADE IN THE SERVICE BASE
Service Data of
entry
Order
number Type of the repair Date of
delivery
Performer
of the
repair
Seller: ................... Buyer: .................
Bulgaria, 4000 Plovdiv, 4 Murgash str.
Tel.: (+359 32) 642 519, 640 446 fax: (+359 32) 640 446
www.microsyst.net e-mail: [email protected]
Document revision 2020-04-07
16
Other microSYST Controllers manuals
Popular Controllers manuals by other brands
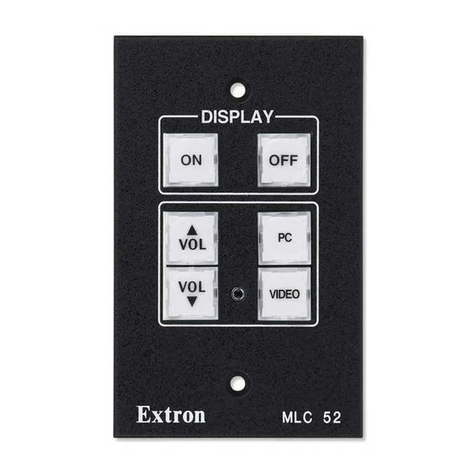
Extron electronics
Extron electronics MEDIALINK MLC 52 Series user manual

Barco
Barco TransForm A Brochure & specs

gefran
gefran GF_LOOPER 3.5” quick start guide
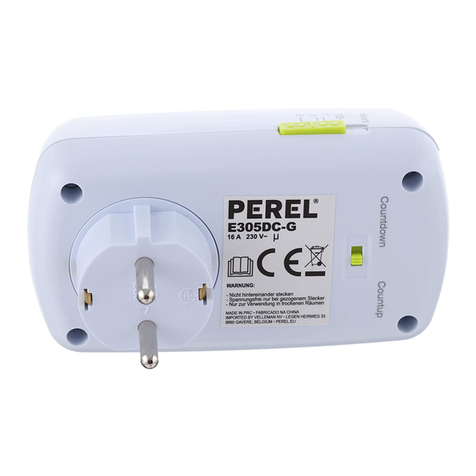
Velleman
Velleman E305DC user manual
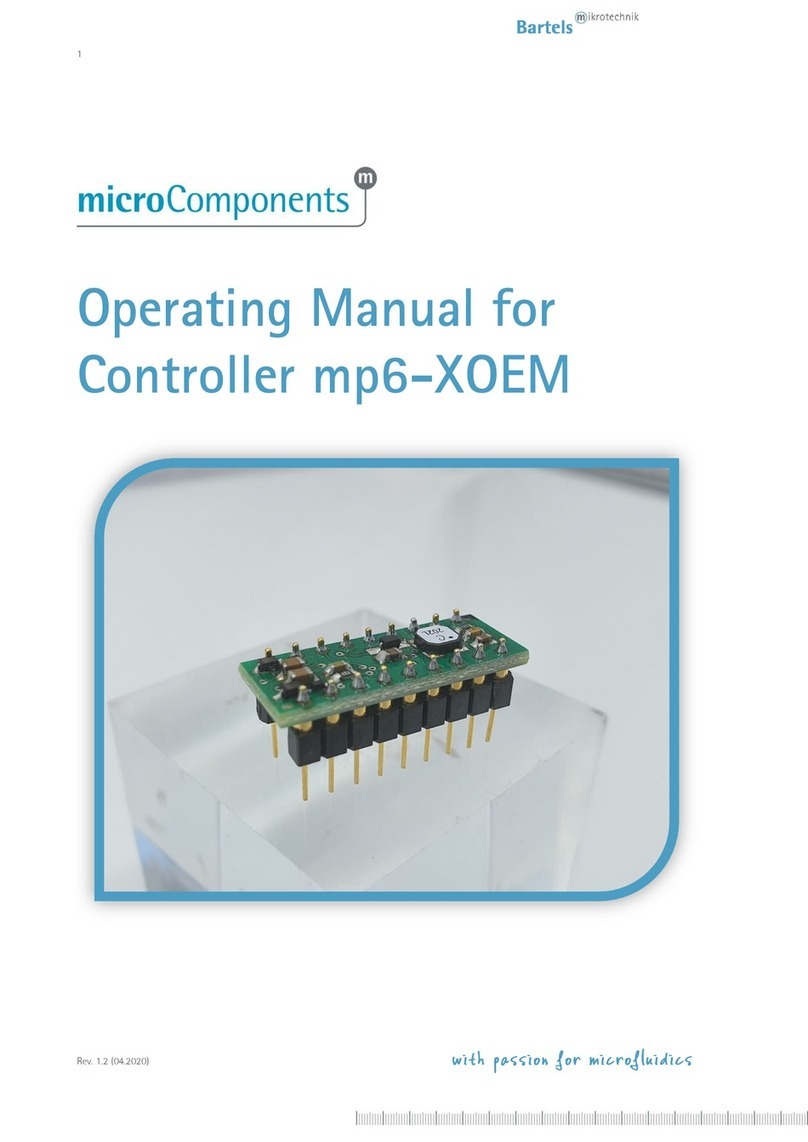
Bartels Mikrotechnik
Bartels Mikrotechnik microComponents mp6-XOEM operating manual
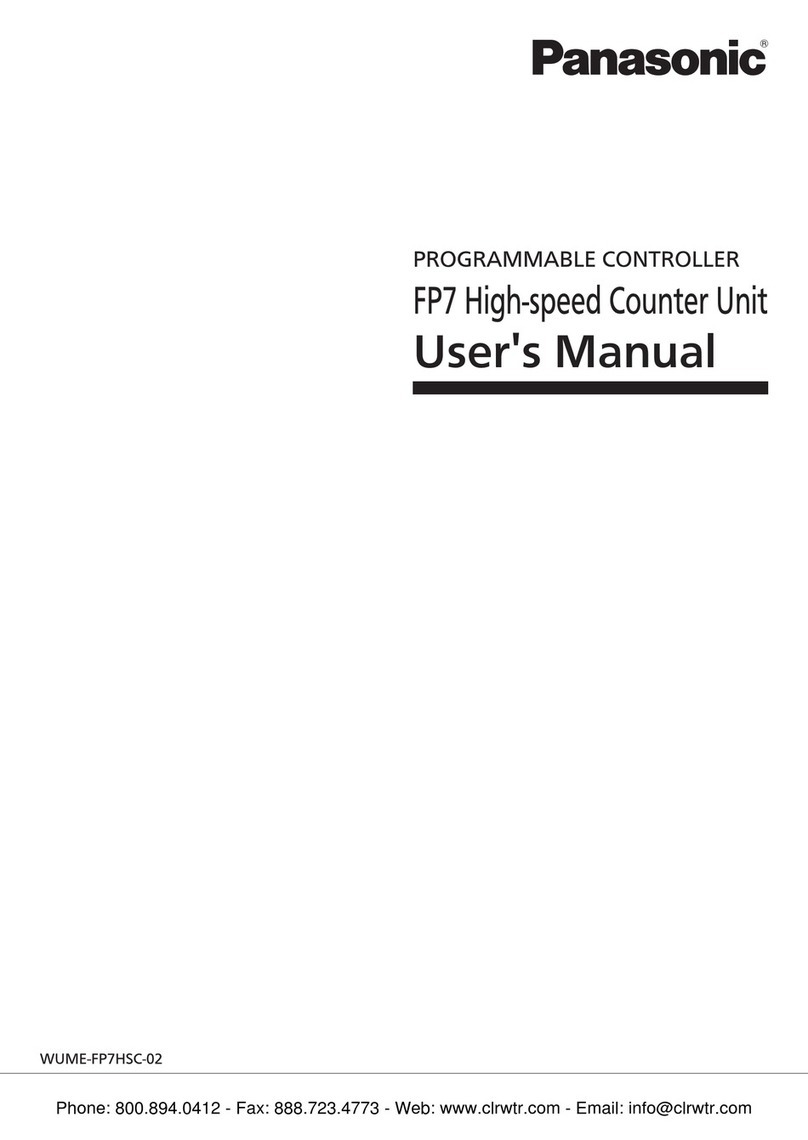
Panasonic
Panasonic FP7 Series user manual
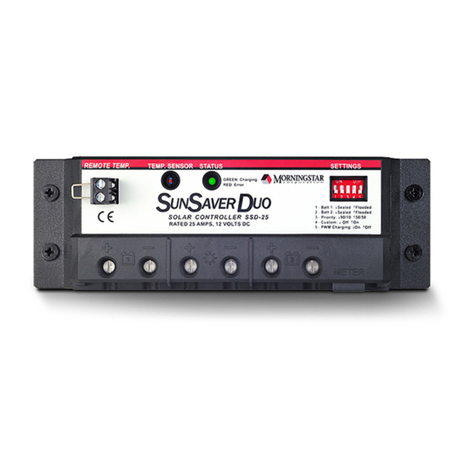
Morningstar
Morningstar SUNSAVER DUO Installation and operation manual

Mitsubishi Electric
Mitsubishi Electric FX3U-ENET user manual
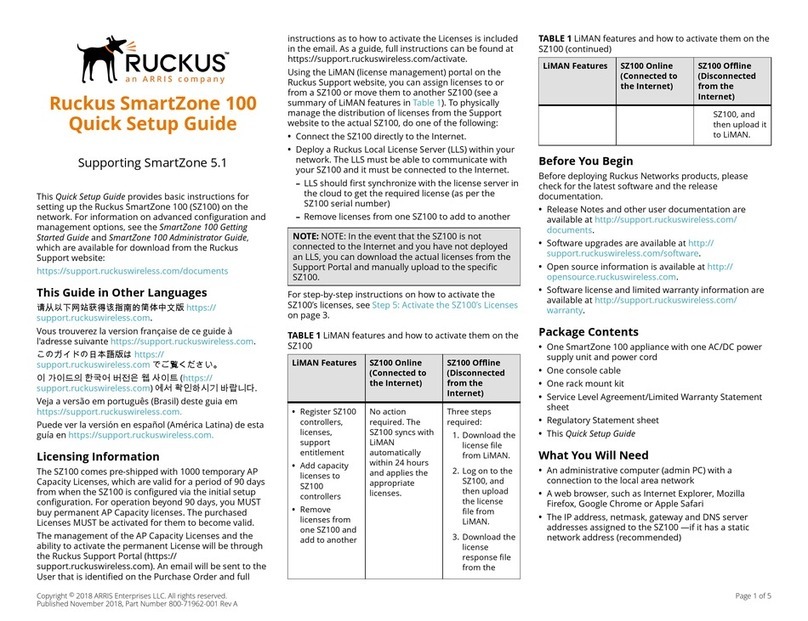
Ruckus Wireless
Ruckus Wireless SmartZone 100 Quick setup guide
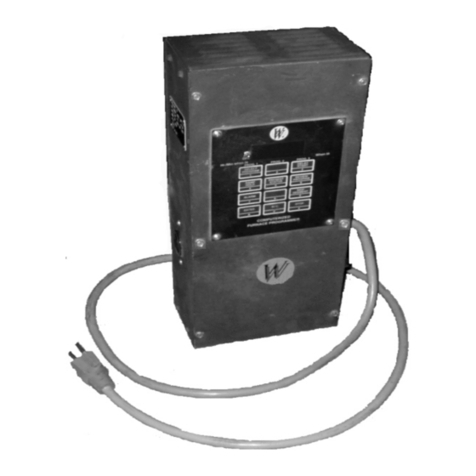
ROMANOFF
ROMANOFF W13 operating instructions
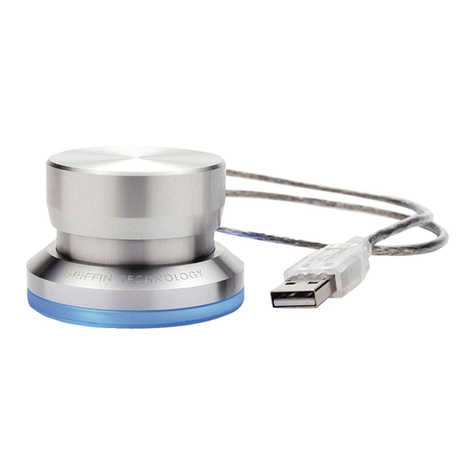
Griffin Technology
Griffin Technology PowerMate quick start guide
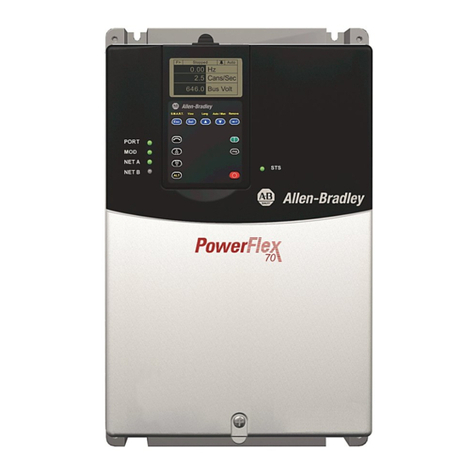
Allen-Bradley
Allen-Bradley PowerFlex 70 user manual