Midea P6 Operating instructions

P6 Troubleshooting
Digital display output
Description
▪1P6 indicates compressor A inverter module protection.
▪2P6 indicates compressor B inverter module protection.
▪When a P6 error occurs, a manual system restart is required before the system can resume operation. The cause of a
P6 error should be addressed promptly in order to avoid system damage.
▪All units stop running.
▪Error code is displayed on the main PCB and user interface.
Possible causes
▪Inverter module protection.
▪DC bus low or high voltage protection.
▪MCE error.
▪Zero speed protection.
▪Phase sequence error.
▪Excessive compressor frequency variation.
▪Actual compressor frequency differs from target frequency.
Specific error codes for xH4 inverter module protection
If a P6 error code is displayed, press button SW3 (to No.36 item) until one of the following specific error codes is displayed
on the digital display: xL0, xL1, xL2, xL4, xL5, xL7, xL8, xL9. Refer to Figure 5-4.3 and Table 5-4.1.
Figure 4-4.1: Button SW3 on main PCB

Table 4-4.1: Specific error codes for error xH4
Specific error code1
Content
xL0
Inverter module protection
xL1
DC bus low voltage protection
xL2
DC bus high voltage protection
xL4
MCE error
xL5
Zero speed protection
xL7
Phase sequence error
xL8
Compressor frequency variation greater than 15Hz within one second protection
xL9
Actual compressor frequency differs from target frequency by more than 15Hz protection
Notes:
1. 'x' is a placeholder for the compressor system (compressor and related electrical components), with 1 representing compressor system A and
2 representing compressor system B.
The specific error codes xL0, xL1, xL2 and xL4 cjcled5
n also be obtained from the inverter module LED indicators. If an inverter module error has occurred, LED5 is continuously
on and LED4 flashes. Refer to Figure 5-4.4 and Table 5-4.2.
Figure 4-4.2: LED indicators LED4 and LED5 on main PCB
Table 5-4.2: Errors indicated on LED4/6
LED4/6 flashing pattern
Corresponding error
Flashes 8 times and stops for 1 second, then repeats
xL0 - Inverter module protection
Flashes 9 times and stops for 1 second, then repeats
xL1 - DC bus low voltage protection
Flashes 10 times and stops for 1 second, then repeats
xL2 - DC bus high voltage protection
Flashes 12 times and stops for 1 second, then repeats
xL4 - MCE error

First troubleshooting step
To troubleshoot XP6 errors, first ensure that the DC bus wire is connected correctly. The DC bus wire should run from the N
terminal on the inverter module, through the current sensor (in the direction indicated by the arrow on the current
sensor), and end at the N terminal on the DC filter board.
Figure 4-4.3: DC detection wire connection method
xL0 troubleshooting
Step 1: Check compressor
▪Check that compressor wiring is all connected properly.
▪The normal resistances of the inverter compressor are 0.7-1.5Ω among U V W and infinite between each of U V W
and ground. If any of the resistances differ from these specifications, the compressor has malfunctioned.
Figure 4-4.4: Measuring resistances among compressor
terminals
Figure 4-4.5: Measuring resistances between compressor terminals
and ground
▪If the resistances are normal, go to Step 2.
Step 2: Check inverter module
▪The DC voltage between terminals P1 and N1 should be 1.41 times the local power supply voltage. The DC voltage
between terminals P and N should be 510-580V. If either voltage is not in the normal range, troubleshoot as for xL1 or
xL2 errors. Refer to Part 4, 4.12.7 “xL1/xL4 troubleshooting” or Part 4, 4.12.8 “xL2 troubleshooting”.
▪Disconnect the terminals U, N, W from the inverter compressor. Measure the resistance among terminals P, N, U, V, W.
All the resistances should be infinite. If any of them are not infinite, the inverter module is damaged and should be
replaced.
Inverter module N
terminal
DC bus wire
Current sensor
DC filter board N
terminal

Figure 4-4.6: Inverter module terminals
xL1/xL4 troubleshooting
Step 1: Check inverter module
▪Check the DC voltage between terminals P and N. The normal value is 510-580V. If the voltage is lower than 510V, go
to Step 2.
Figure 4-4.7: Inverter module terminals
Step 2: Check rectifier wiring circuit
▪If the wires are loose, fasten the wires. If the wires are OK, replace the main PCB.
Figure 4-4.8: Rectifier and AC filter board in electric control box
P1
N1
N
U
P
V
W
N
P
Check 3-phase bridge
rectifier wiring
Check AC filter
board wiring

xL2 troubleshooting
Step 1: Check inverter module
▪Check the DC voltage between terminals P and N. The normal value is 510-580V, if the voltage is higher than 580V, go
to Step 2.
Figure 4-4.9: Inverter module terminals
Step 2: Check inverter module
▪Check the voltage between terminals P and N on the capacitor board. The normal value is 510-580V. If the voltage is
not in the normal range, there is a problem with the electrolytic capacitor power supply. Check the power supply for
high or unstable voltage. If the power supply voltage value is normal, then the main PCB has malfunctioned and
needs to be replaced.
Figure 4-4.10: Inverter module terminals
xL8/xL9 troubleshooting
Step 1: Check compressor
▪The normal resistances of the inverter compressor are 0.7-1.5Ω among U V W and infinite between each of U V W
and ground. If any of the resistances differ from these specifications, the compressor has malfunctioned.
▪Refer to Figures 4-4.4 and 4-4.5 in Part 4, 4.12.6 “xL0 troubleshooting”. If the resistance values are normal, go to Step
2.
Step 2: Check compressor and main PCB
▪If there is another unit nearby (either in the same system or another system) that is operating normally, its electric
N
P
P
N

control box can be used to determine whether the xL8/xL9 error is being caused by a compressor fault or a main PCB
fault:
If using another unit in the same system as the unit with the error to perform the test, set it as the master unit
(address 0); if using a unit in another system, use the master unit.
Disconnect the power wires of the compressor referenced in the xL8/xL9 error code.
In the unit that is operating normally, disconnect the power wires that connect a compressor to the electric
control box and use them to connect the compressor with the xL8/xL9 error to the electric control box of the
unit that is operating normally. Ensure that the U, V, W terminals are connected in the right order, and then start
the system that is operating normally.
If the compressor with the xL8/xL9 error runs normally, replace the main PCB of the unit with the xL8/xL9 error
and ensure the wiring is correct; if the compressor with the xL8/xL9 error still does not run normally, it needs to
be replaced. Refer to Part 4, 4.12.10 “Compressor replacement procedure”.
Figure 4-4.11: Connecting compressor to an error-free unit
Unit with error
Unit operating normally
▪If there is no error-free unit nearby:
Replace the main PCB of the unit with the xL8/xL9 error and ensure the wiring is correct. If the compressor with
the xL8/xL9 error runs normally, a fault with the main PCB was causing the xL8/xL9 error; if the compressor with
the xL8/xL9 error still does not run normally, it needs to be replaced. Refer to Part 4, 4.12.10 “Compressor
replacement procedure”.
Compressor replacement procedure
Step 1: Remove faulty compressor and remove
oil
▪Remove the faulty compressor from the outdoor unit.
▪Before removing the oil, shake the compressor so as to not allow
impurities to remain settled at the bottom.
▪Drain the oil out of the compressor and retain it for inspection.
Normally the oil can be drained out from the compressor discharge
pipe. Refer to Figure 4-4.12.
Step 2: Inspect oil from faulty compressor
▪The oil should be clear and transparent. Slightly yellow oil is not an indication of any problems. However, if the oil is
dark, black or contains impurities, the system has problems and the oil needs to be changed. Refer to Figure 5-4.16
for further details regarding inspecting compressor oil. (If the compressor oil has been spoiled, the compressor will
not be being lubricated effectively. The scroll plate, crankshaft and bearings will wear. Abrasion will lead to a larger
load and higher current. More electric energy will get dissipated as heat and the temperature of the motor will
become increasingly high. Finally, compressor damage or burnout will result. Refer to Figure 4-4.13.)
Step 3: Check oil in other compressors in the system
Figure 4-4.12: Draining oil from a compressor
Power line (U, V, W terminals)

▪If the oil drained from the faulty compressor is clean, go to Step 6.
▪If the oil drained from the faulty compressor is only lightly spoiled, go to Step 4.
▪If the oil drained from the faulty compressor is heavily spoiled, check the oil in the other compressors in the system.
Drain the oil from any compressors where the oil has been spoiled. Go to Step 4.
Step 4: Replace oil separator(s) and accumulator(s)
▪If the oil from a compressor is spoiled (lightly or heavily), drain the oil from the oil separator and accumulator in that
unit and then replace them.
Step 5: Check filters(s)
▪If the oil from a compressor is spoiled (lightly or heavily), check the filter between the gas stop valve and the 4-way
valve in that unit. If it is blocked, clean with nitrogen or replace.
Step 6: Replace the faulty compressor and re-fit the other compressors
▪Replace the faulty compressor.
▪If the oil had been spoiled and was drained from the non-faulty compressors in Step 3, use clean oil to clean them
before re-fitting them into the units. To clean, add oil into the compressor through the discharge pipe using a funnel,
shake the compressor, and then drain the oil. Repeat several times and then re-fit the compressors into the units.
Step 7: Add compressor oil
▪Add 2L of oil to the new compressor through the discharge pipe, using a funnel.
▪Add 2L of oil to each of the compressors from which oil was drained in Step 3.
▪Only use FV68H oil. Different compressors require different types of oil. Using the wrong type of oil leads to various
problems.
▪Add additional oil to the accumulators such that the total amount of oil is 4.6L .
Step 8: Vacuum drying and refrigerant charging
▪Once all the compressors and other components have been fully connected, vacuum dry the system and recharge
refrigerant.
Figure 4-4.13: Inspecting compressor oil
This oil is black
-it has been
carbonized
This oil is a little
yellow, but is clear
and transparent and
the condition is
acceptable
This oil is still
transparent but there
are impurities which
may clog the filter

Cloudy or gray
oil indicates
abnormal
system
operation
This oil contains
particles of copper
Table of contents
Popular Microcontroller manuals by other brands

Texas Instruments
Texas Instruments SimpleLink CC3200 Wi-Fi user guide

Qorvo
Qorvo QM33120WDK1 quick start guide
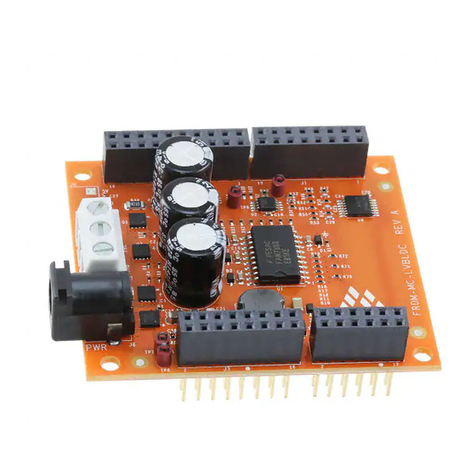
Freescale Semiconductor
Freescale Semiconductor FRDM-MC-LVBLDC user guide

HMS
HMS IXXAT Safe T100 Hardware manual
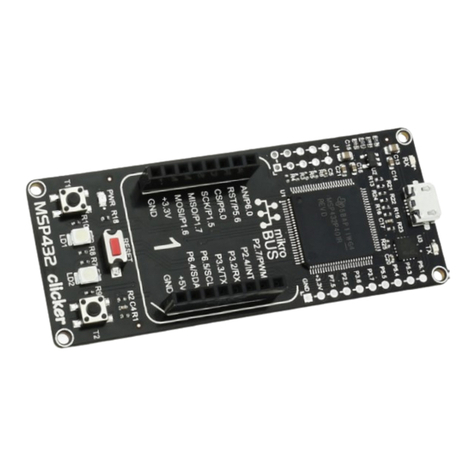
mikroElektronika
mikroElektronika MSP432 clicker user manual
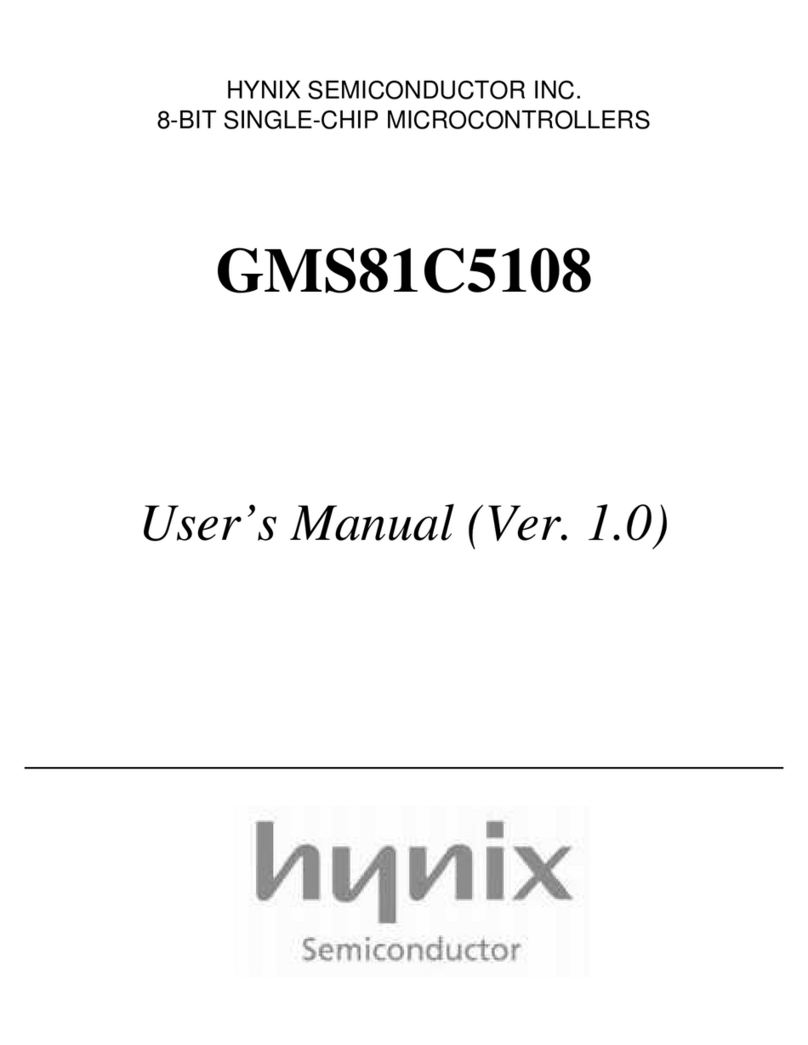
Hynix Semiconductor
Hynix Semiconductor GMS81C5108 user manual
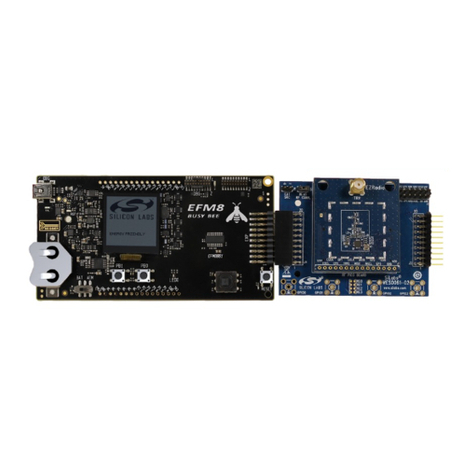
Silicon Laboratories
Silicon Laboratories EFM8 Series Reference manual
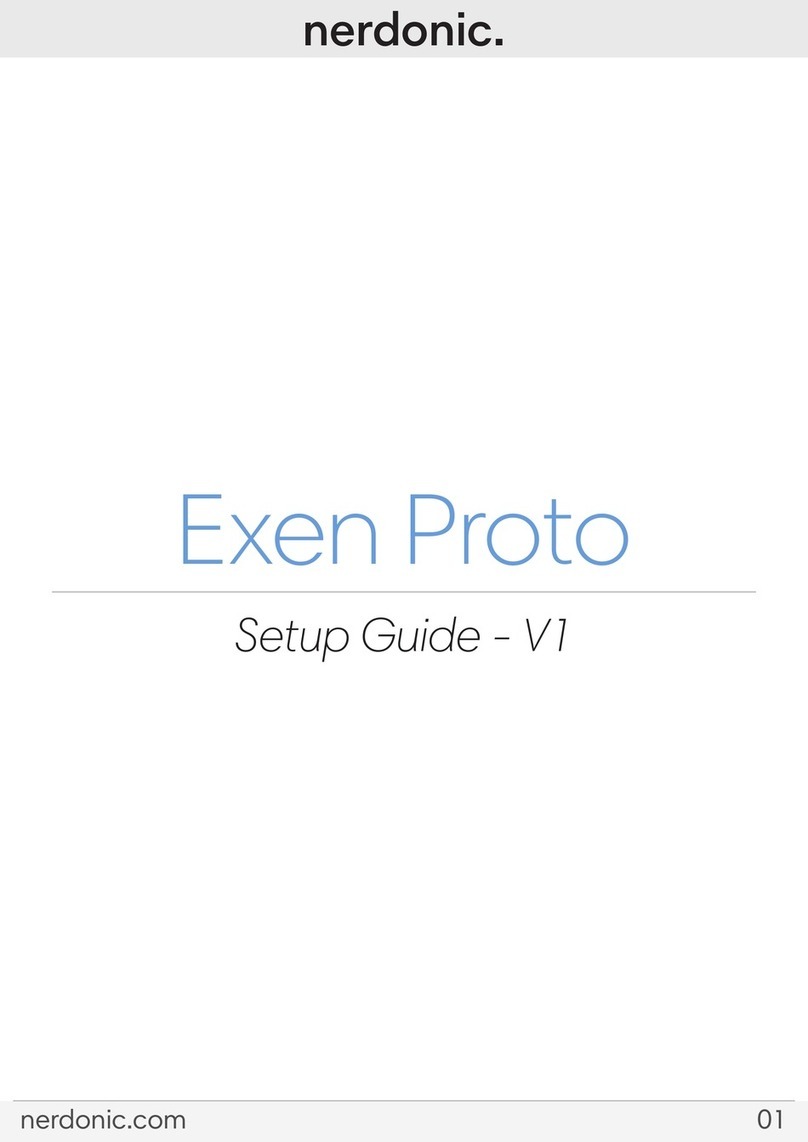
Nerdonic
Nerdonic Exen Proto Setup guide
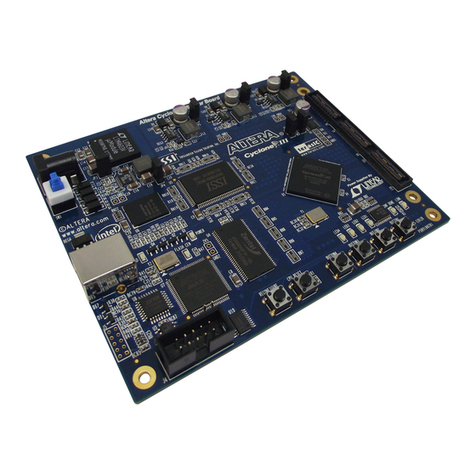
Altera
Altera Cyclone III Getting started guide
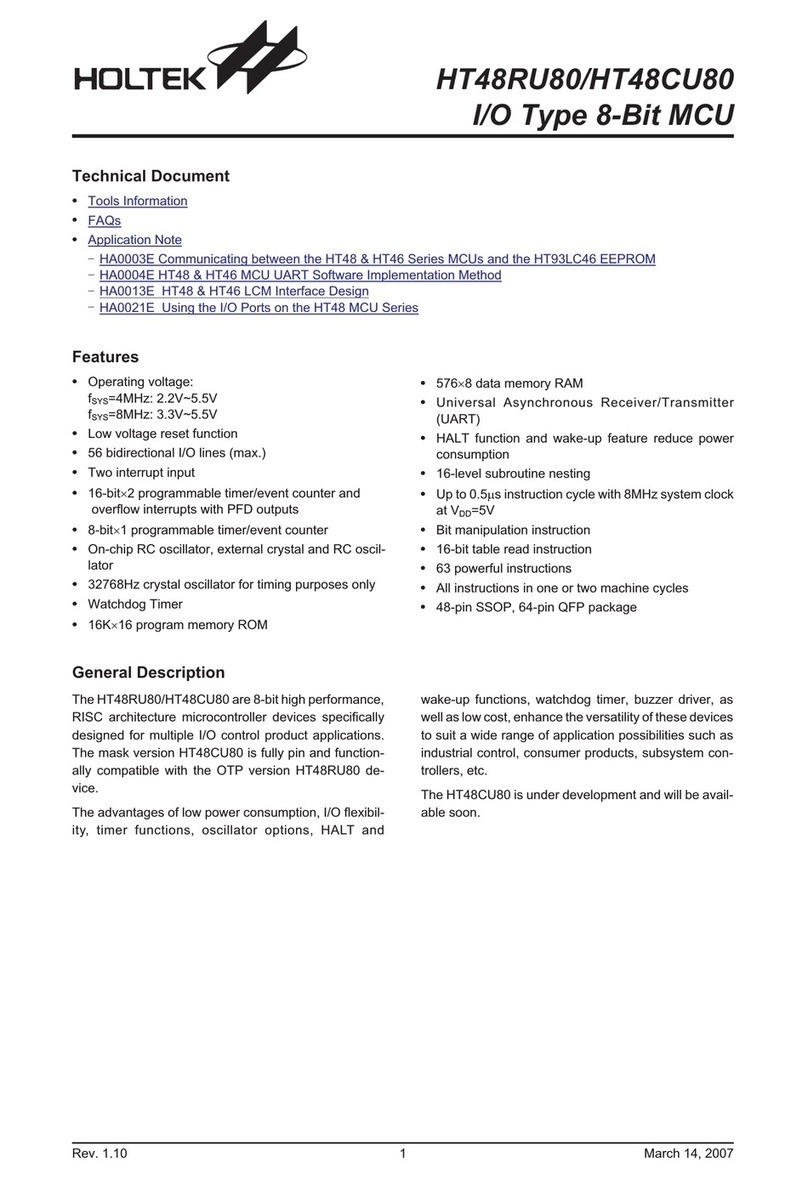
Holtek
Holtek HT48RU80 manual
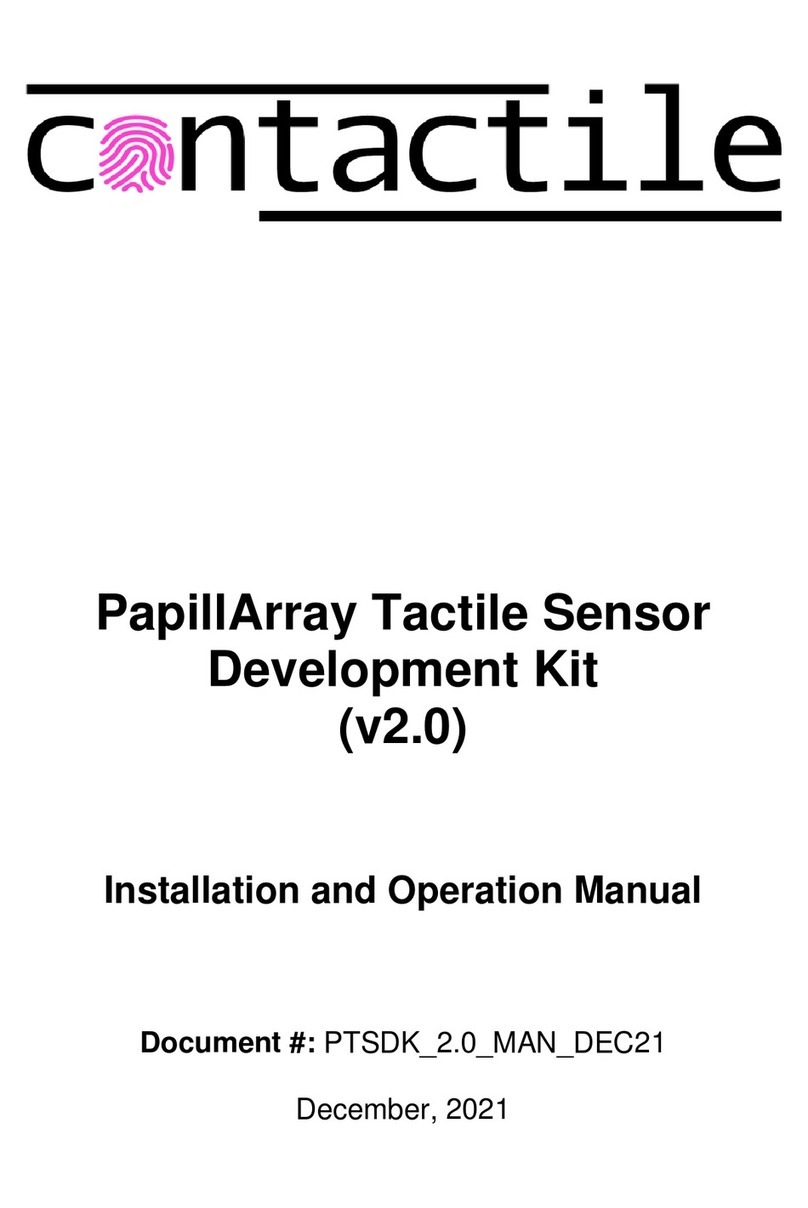
contactile
contactile PapillArray Tactile Sensor Development Kit... Installation and operation manual

Faller
Faller 163701 instruction manual