HMS IXXAT Safe T100 User manual

Hardware Manual / Software Manual
T100 Development Kit
Manual

HMS Technology Center Ravensburg GmbH
Helmut-Vetter-Straße 2
88213 Ravensburg
Germany
Tel.: +49 751 56146-0
Fax: +49 751 56146-29
Internet: www.hms-networks.de
E-Mail: info-ravensburg@hms-networks.de
Support
In case of unsolvable problems with this product please contact HMS in
written form by:
Fax: +49 751 56146-29
E-Mail: support@ixxat.de
Further international support contacts can be found on our webpage
www.ixxat.com/support
Copyright
Duplication (copying, printing, microfilm or other forms) and the electronic
distribution of this document is only allowed with explicit permission of
HMS Technology Center Ravensburg GmbH. HMS Technology Center
Ravensburg GmbH reserves the right to change technical data without
prior announcement. The general business conditions and the regulations
of the license agreement do apply. All rights are reserved.
Registered trademarks
All trademarks mentioned in this document and where applicable third
party registered are absolutely subject to the conditions of each valid
label right and the rights of particular registered proprietor. The absence
of identification of a trademark does not automatically mean that it is not
protected by trademark law.
Document number: 4.01.0300.20100
Version: 1.6 Release

Document history
Date
Version
Change
Editor
24.11.17
1.6
Support of IXXAT Safe T100/FSoE
added. Dynamic non-safe ADI
configuration removed. Flow charts (CIP
Safety IP Address) updated. Cycle Time
attribute described for the first time.
K. Angele

Content
Copyright HMS TC Ravensburg GmbH
3
T100 Development Kit Manual,
Version 1.6
Document history..................................................................................5
Referenced documents ........................................................................5
Abbreviations........................................................................................6
1Overview.........................................................................................7
1.1 Anybus CompactCom objects.............................................10
1.2 Functional Safety Object......................................................11
2Power Supply connection ...........................................................12
3Address Switches........................................................................13
3.1 PROFIsafe F-Address...........................................................13
3.2 CIP Safety IP Address...........................................................14
3.3 FSoE Slave Address.............................................................17
4Enable the Safety module ...........................................................18
4.1 Communication Cycle Time.................................................19
5Non-safe process data handling.................................................20
5.1 PROFINET .............................................................................21
5.2 EtherNet/IP ............................................................................21
5.3 EtherCAT ...............................................................................21
5.4 Non-safe input data ..............................................................22
5.5 Non-safe output data............................................................24
6Network Configuration ................................................................26
6.1 PROFINET (GSDML) .............................................................26
6.2 EtherNet/IP ............................................................................26
6.2.1 Electronic Data Sheet (EDS) .................................................26
6.2.2 Configuration Data String.......................................................26
6.2.3 PLC Configuration in RSLogix Designer (Studio 5000).........27
6.2.3.1 Device Identity and Connections..............................27
6.2.3.2 SCID (Safety Configuration Identifier)......................28
6.2.3.3 Safety Network Number / TUNID.............................29
6.3 EtherCAT (ESI) ......................................................................29
7Fault reset button.........................................................................30
7.1 Manual Fault Reset...............................................................30
7.2 Automatic Fault Reset..........................................................30
8Reset button.................................................................................31

Content
Copyright HMS TC Ravensburg GmbH
4
T100 Development Kit Manual,
Version 1.6
9LED indicators..............................................................................32
9.1 PROFIsafe .............................................................................32
9.2 CIP Safety..............................................................................33
9.3 FSoE ......................................................................................33
10 Safety I/O Connectors..................................................................34
11 Other components.......................................................................35
11.1Jumper...................................................................................35
11.2Switch S1...............................................................................35
11.3Pin Header JP18....................................................................35
11.4JTAG Connector ...................................................................35
11.5RS232 connector JP7...........................................................35
12 Web page......................................................................................36
13 Wiring Diagram ............................................................................37
14 Product Support and Conformity ...............................................43
14.1Support..................................................................................43
14.2Returning hardware..............................................................43
14.3Information on EMC..............................................................43
14.4EC Declaration of Conformity..............................................44
Appendix A –ADI Configuration........................................................45
ADI 1 .............................................................................................45
ADI 2 .............................................................................................46
Appendix B –Firmware Upgrade.......................................................47
Development Kit board................................................................47
Anybus CompactCom..................................................................47
T100 ..............................................................................................47

Referenced documents
Copyright HMS TC Ravensburg GmbH
5
T100 Development Kit Manual,
Version 1.6
Referenced documents
[1] Safety Manual for IXXAT Safe T100
[2] Network Guide Anybus CompactCom 40 PROFINET IRT,
Doc. Id. SCM-1202-023 Rev. 1.4
[3] Network Guide Anybus CompactCom 40 EtherNet/IP,
Doc. Id. SCM-1202-031 Rev. 1.1
[4] Network Guide Anybus Compact Com 40 EtherCAT,
Doc. Id. SCM-1202-034 Rev. 1.4

Abbreviations
Copyright HMS TC Ravensburg GmbH
6
T100 Development Kit Manual,
Version 1.6
Abbreviations
ABCC Anybus CompactCom –Network communication module with a
protocol independent software interface.
ADI Application Data Instances –Instance of an application input or
output module which can be used to exchange data e.g. with a PLC.
CB Carrier Board –Printed circuit board of the DevKit that is the mounting
base for the T100 and the ABCC
DevKit Development Kit –Abbreviation for this product.
EDS Electronic Data Sheet –ASCII text file that describes the
characteristics of a CIP device and is used by software tools for
device and network configuration.
ESI EtherCAT Slave Information (EtherCAT Devices Description) –A XML
file that describes the characteristic of an EtherCAT device. The file is
used by software tools for device and network configuration.
GSDML General Station Description Markup Language –In an XML based
language this file describes the characteristics of a PROFINET
device.
MDP Modular Device Profile - The Modular Device Profile defines a
modeling of structures within in a device. Mainly the object dictionary
structure and corresponding behavior of the entries is defined by the
MDP. The intention is to provide an easy way for master and
configuration tools to handle the devices.
PLC Programmable Logic Controller –A programmable electronic device
used in industrial automation to provide logic and sequencing controls
for machinery.
SCCRC Safety Configuration CRC –CRC that covers the device configuration
data.
SCTS Safety Configuration Time Stamp –Safety related signature that
identifies the revision of the device configuration.
SCID Safety Configuration Identifier –Combination of the SCCRC and the
SCTS used to uniquely identify a configuration.
TUNID Target Unique Network Identifier –Uniquely identifies a device in a
CIP Safety Network.
UTC Coordinated Universal Time –Base for the definition of the SCTS and
the Safety Network Number in the TUNID.

Overview
Copyright HMS TC Ravensburg GmbH
7
T100 Development Kit Manual,
Version 1.6
1 Overview
Figure 1-1: Overview of the T100 Development Kit

Overview
Copyright HMS TC Ravensburg GmbH
8
T100 Development Kit Manual,
Version 1.6
Figure 1-2: Detailed view of the T100 Development Kit

Overview
Copyright HMS TC Ravensburg GmbH
9
T100 Development Kit Manual,
Version 1.6
Number
Name
1
Switch S4
2
Switch S5
3
Switch S6
4
Switch S7
5
Switch S10
6
Switch S1
7
Safe T100
8
Anybus CompactCom
9
24V DC Input
10
Host Processor
11
Board Reset
12
Fault Reset
13
Safe Inputs
14
Safe Outputs
15
Non-Safe Inputs JP16
16
Non-Safe Outputs JP17
17
Status LEDs D1-D8
18
User LEDs D15-D16
19
RAMloader CB Jumper 13
20
RAMloader ABCC Jumper 15
21
JTAG Interface JP19
This manual describes the basic functionality and how to use an Anybus
CompactCom (ABCC) with an IXXAT Safe T100/PS, T100/CS or T100/FSoE
module attached. It also describes how the safe and non-safe functionality of
the Development Kit is implemented and used based on a simple I/O demo
application.
The Development Kit consists of a carrier board (CB) hosting an Anybus
CompactCom, an IXXAT Safe T100/PS, T100/CS or T100/FSoE and a host
application microprocessor. For demonstration purposes the host application
microprocessor runs a simple (non-safe) I/O demo. This demo software is also
initializing the IXXAT Safe T100 module via the ABCC object interface which is
described in more details within this manual.

Overview
Copyright HMS TC Ravensburg GmbH
10
T100 Development Kit Manual,
Version 1.6
Figure 1-3: Development Kit block diagram
For detailed information about the IXXAT Safe T100 module please refer to
the Safety Manual [1].
In the following sections the Anybus CompactCom objects and host
application objects containing information related to functional safety are
described. Please consult the Anybus CompactCom 40 Network Guide ([2] for
PROFINET, [3] for EtherNet/IP, [4] for EtherCAT) for detailed information
regarding these objects.
1.1 Anybus CompactCom objects
The Anybus CompactCom contains the main control and configuration objects
which are necessary to activate and configure the IXXAT Safe T100 operation.
These objects can be accessed via the following object references (indices):
Functional Safety Module Object (11h)
Network Configuration Object (04h)

Overview
Copyright HMS TC Ravensburg GmbH
11
T100 Development Kit Manual,
Version 1.6
1.2 Functional Safety Object
The Functional Safety Object (E8h) is implemented in the host application
processor. It contains information which is relevant for the host application
process.

Power Supply connection
Copyright HMS TC Ravensburg GmbH
12
T100 Development Kit Manual,
Version 1.6
2 Power Supply connection
JP8: 24V DC Input (-15% + 20% according to IEC 61131-2)
and Protective Earth
JP11: Protective Earth
Figure 2-1: Power and Protective Earth connectors

Address Switches
Copyright HMS TC Ravensburg GmbH
13
T100 Development Kit Manual,
Version 1.6
3 Address Switches
3.1 PROFIsafe F-Address
The F-address is the PROFIsafe address on the network which must be
configured from the host application before “Setup complete” of the Anybus
CompactCom module state machine. The F-address is located in instance #21
“F-Address” of the Network Configuration object in the Anybus CompactCom
module and must match the F-address configured in the PLC for the system to
work.
Switches S4 and S5 are used by the Development Kit host application to read
in the value which is then written to the F-Address value attribute. The F-
Address is read considering the two DIP-switches as two bytes with the MSB
given by S4 and the LSB given by S5. If the switch lever is down it is
interpreted as OFF/0, if it is up it is interpreted as 1/ON. The range for a valid
F-Address is between 1 and 65534.
Figure 3-1: Switches S4 and S5 to set the PROFIsafe F-Address
Example: The switches in the figure have the F-address 700 –or 00000010
10111100 in binary –configured.
If the F-address value changes (in this case, someone alters S4
and/or S5) during runtime, the new value must be sent from the
host application to the Anybus CompactCom. As the value is only
sent during startup to the IXXAT Safe T100 it will be used after the
next restart of the system.
MSB
LSB
Highest bit
Lowest bit

Address Switches
Copyright HMS TC Ravensburg GmbH
14
T100 Development Kit Manual,
Version 1.6
3.2 CIP Safety IP Address
CIP Safety devices can optionally determine their IP-address by means of
hardware switches. In the Development Kit host application Switch S5 is used
for this purpose.
Setting Switch S5 to a value between 1 and 254 indicates that the IP address
of the device is determined by this switch (see Figure 3-2). The IP address of
the device is then set to 192.168.1.switch-value. The subnet mask is set to
255.255.255.0. The default gateway is set either to 192.168.1.1 or (to avoid
equality with the IP address) to 0.0.0.0 in case the switch is set to 1.
For switch settings 0 or 255 the IP address is determined by the Anybus
CompactCom module itself (e.g. DHCP, TCP/IP Object attribute, web server,
etc.).
Setting the IP address configuration is done by writing to the Network
Configuration Object (see [3] for details).
For CIP Safety compliant behavior it is necessary to read and evaluate the
switch value during initialization of the Anybus CompactCom module (before
setting the Anybus Object attribute Startup Complete) according to the
example shown in Figure 3-3, but also to continuously sample the switch value
and react on changes. An example for the ongoing switch value evaluation is
shown in Figure 3-4 (“IP Address Change via Switch”).
Additionally the Development Kit host application has to react if the IP address
of the device was changed by network services (e.g. via TCP/IP Object
attribute). An example how to implement this behavior is also shown in Figure
3-4 (“IP Address Change via Network”).
Figure 3-2: Switch S5 to set IP address of the device.
LSB
Highest bit
Lowest bit

Address Switches
Copyright HMS TC Ravensburg GmbH
15
T100 Development Kit Manual,
Version 1.6
INIT==255 OR
INIT==0 ?
FALSE
TRUE
Power-On
DHCP Enabled ?
FALSE
TRUE
Read Switch S5
INIT = S5
Get DHCP Status
(Network Configuration Object 04h
DHCP (Inst#6, Attr#5)
Set IP Address to '1'
(Network Configuration Object 04h)
IP: 192.168.1.1 (Inst#3, Attr#5)
Subnet: 255.255.255.0 (Inst#4, Attr#5)
Gateway: 0.0.0.0 (Inst#5, Attr#5)
DHCP: Disabled (Inst#6, Attr#5)
Set IP Address to 'INIT'
(Network Configuration Object 04h)
IP: 192.168.1.INIT (Inst#3, Attr#5)
Subnet: 255.255.255.0 (Inst#4, Attr#5)
Gateway: 192.168.1.1 (Inst#5, Attr#5)
DHCP: Disabled (Inst#6, Attr#5)
INIT==1 ?
FALSE
TRUE
DeviceIpAddr =
192.168.1.INIT
DeviceIpAddr =
192.168.1.1
DeviceIpAddr =
Value
Get IP Address 'Value'
(Network Configuration Object 04h)
IP (Inst#3, Attr#5)
DeviceIpAddr =
0.0.0.0 (unassigned)
IP Settings valid and
used for communication
Use DHCP
Figure 3-3: Determination of the initial IP-address based on Switch S5

Address Switches
Copyright HMS TC Ravensburg GmbH
16
T100 Development Kit Manual,
Version 1.6
INIT <> NEW ?
TRUE
Set IP Address to 'NEW'
(Network Configuration Object 04h)
IP: 192.168.1.NEW (Inst#3, Attr#5)
Gateway: 192.168.1.1 (Inst#5, Attr#5)
FALSE
NEW ==255 OR
NEW==0 ?
TRUE
Read Switch S5
NEW = S5
Loop
Set IP Address to 'NEW'
(Network Configuration Object 04h)
IP: 192.168.1.NEW (Inst#3, Attr#5)
Set IP Address to 'INIT'
(Network Configuration Object 04h)
IP: 192.168.1.INIT (Inst#3, Attr#5)
NEW==1 ?
FALSE
Set IP Address to '1'
(Network Configuration Object 04h)
IP: 192.168.1.1 (Inst#3, Attr#5)
Gateway: 0.0.0.0 (Inst#5, Attr#5)
TRUE
Get IP Address 'CfgIpAddr'
(Network Configuration Object 04h IP
(Inst#3, Attr#6)
FALSE
Set IP Address to 'DeviceIpAddr'
(Network Configuration Object 04h)
IP: SafetyIpAddr (Inst#3, Attr#5)
Set IP Address to 'CfgIpAddr'
(Network Configuration Object 04h)
IP: CfgIpAddr (Inst#3, Attr#5)
DeviceIpAddr =
'CfgIpAddr'
IpAddrChangedEvt
TRUE
'DeviceIpAddr' ==
0.0.0.0
'CfgIpAddr' <>
'DeviceIpAddr'
TRUE
TRUE
FALSE
FALSE
FALSE
IP Address Change via Switch
IP Address Change via Network
Triggers 'Abort' request to
T100/CS
NEW IP address is used
after restet
Restore INIT IP address
Triggers 'Abort' request
to T100/CS
IP Address change request
during runtime
Restore IP address
IP assigned for the first
time e.g. by DHCP
Triggers 'Abort' request
to T100/CS
Flag set if Ethernet Host Object
(Instance 1, Attr. 16) is written
Figure 3-4: Cyclic check for IP Address changes

Address Switches
Copyright HMS TC Ravensburg GmbH
17
T100 Development Kit Manual,
Version 1.6
3.3 FSoE Slave Address
The FSoE Slave Address is a unique address inside the communication
system which is used to check whether a FSoE Slave is actually addressed.
The FSoE Slave Address must be configured from the host application before
“Setup complete” of the Anybus CompactCom module state machine. The
FSoE Slave Address is located in instance #21 “FSoE Address” of the Network
Configuration object in the Anybus CompactCom module.
Switches S4 and S5 are used by the Development Kit host application to read
in the value which is then written to the FSoE slave address value attribute.
The FSoE Slave Address is read considering the two DIP-switches as two
bytes with the MSB given by S4 and the LSB given by S5. If the switch lever is
down it is interpreted as OFF/0, if it is up it is interpreted as 1/ON. The range
for a valid FSoE Slave Address is between 1 and 65535.
Figure 3-5: Switches S4 and S5 to set the FSoE Slave Address
The FSoE Slave Address is only sent during startup to the IXXAT
Safe T100/FSoE. So changes in the FSoE Slave Address will only
take effect after the next restart of the Development Kit.
MSB
LSB
Highest bit
Lowest bit

Enable the Safety module
Copyright HMS TC Ravensburg GmbH
18
T100 Development Kit Manual,
Version 1.6
4 Enable the Safety module
The host application must enable the safety module by implementing the
Functional Safety Object, and respond with TRUE when a request for the
value of the attribute “Safety enabled” is received during the startup sequence.
More information about the Functional Safety Object can be found in the
Anybus CompactCom PROFINET Network Guide (see [2]) respectively
Anybus CompactCom EtherNet/IP Network Guide (see [3]) respectively
Anybus CompactCom EtherCAT Network Guide (see [4]).
To enable the safety functionality of the IXXAT Safe T100 the host application
needs to respond to the Safety enabled attribute request.
- For PROFIsafe additionally the F-address must be set (see chapter 3.1).
- For CIP Safety additionally the Cycle Time attribute shall be
implemented (see chapter 4.1). Furthermore the host application can
assign the IP address (see chapter 3.2).
- For FSoE additionally the FSoE Slave Address must be set (see chapter
3.3).
All other functional safety related attributes shall be considered as non-safe
status information only.
Switch S6:1 is used by the Development Kit host application to decide if the
safety module shall be enabled or not.
Figure 4-1: Switch S6 with safety functionality enabled.
S6:1
Description
OFF
Safety functionality disabled. Value of DIP-switch has only effect
during start-up.
ON
Safety functionality enabled. Value of DIP-switch has only effect
during start-up.
S6:2 to S6:8 are used for internal tests and should stay in default
position OFF.
S6:1

Enable the Safety module
Copyright HMS TC Ravensburg GmbH
19
T100 Development Kit Manual,
Version 1.6
4.1 Communication Cycle Time
The Cycle Time attribute (#4) configures the communication cycle time
between Anybus CompactCom and IXXAT Safe T100 in milliseconds.
For CIP Safety the host application needs to respond to the Cycle Time
attribute request with a value of 4ms.
When using PROFIsafe or FSoE there is no need to implement this attribute
because the expected value of 2ms is the default value used by Anybus
CompactCom.
Other manuals for IXXAT Safe T100
1
Table of contents
Popular Microcontroller manuals by other brands
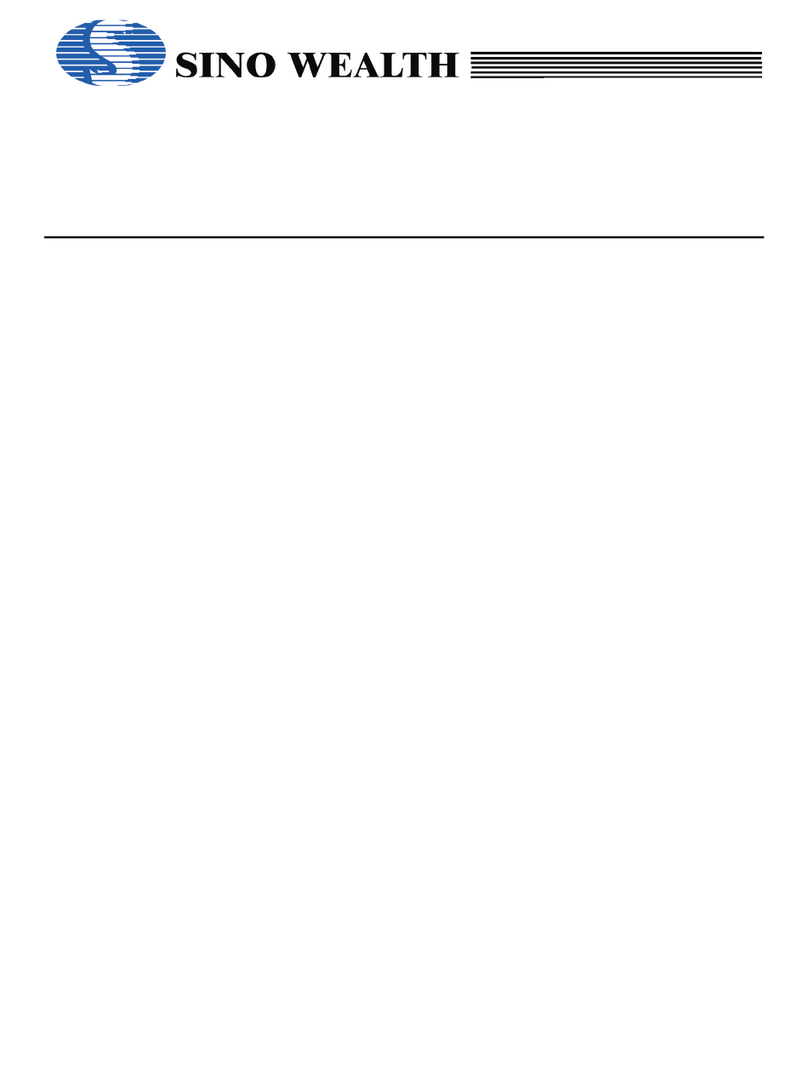
Sino Wealth
Sino Wealth SH79F3281A manual
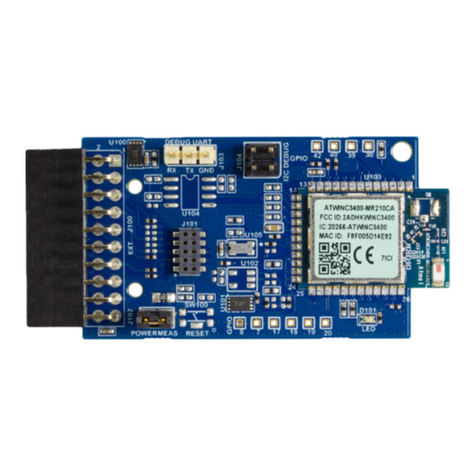
Microchip Technology
Microchip Technology ATWINC3400 user guide
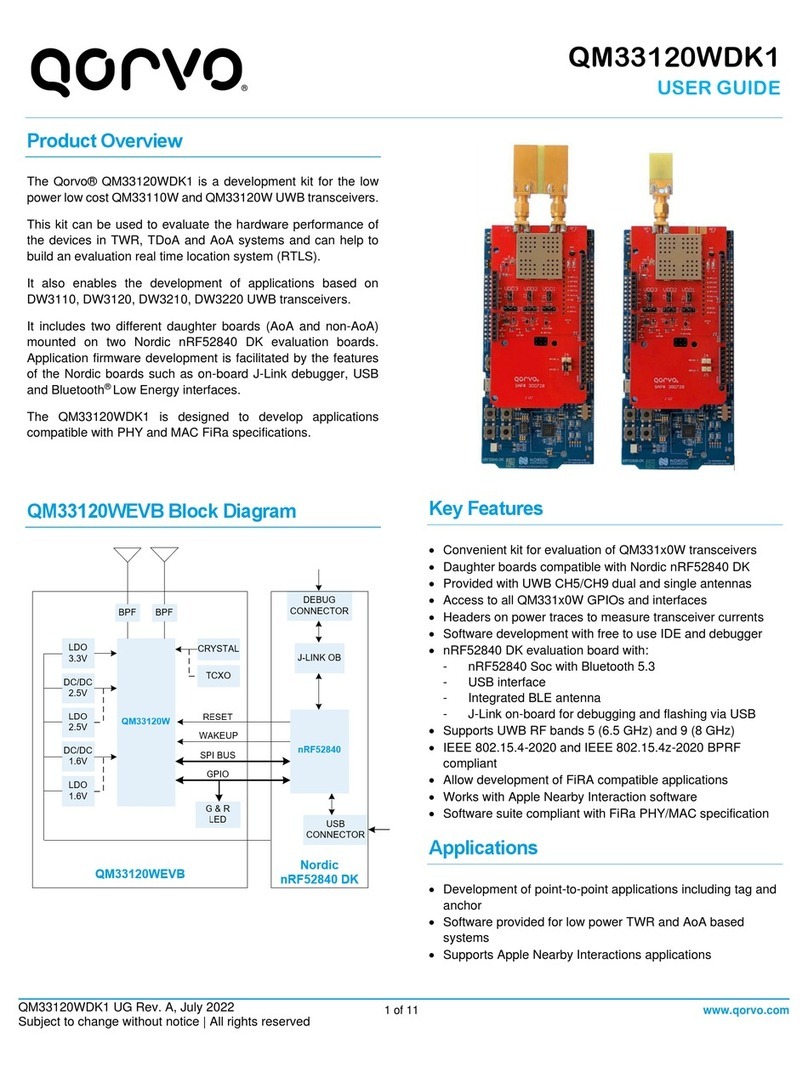
Qorvo
Qorvo QM33120WDK1 user guide
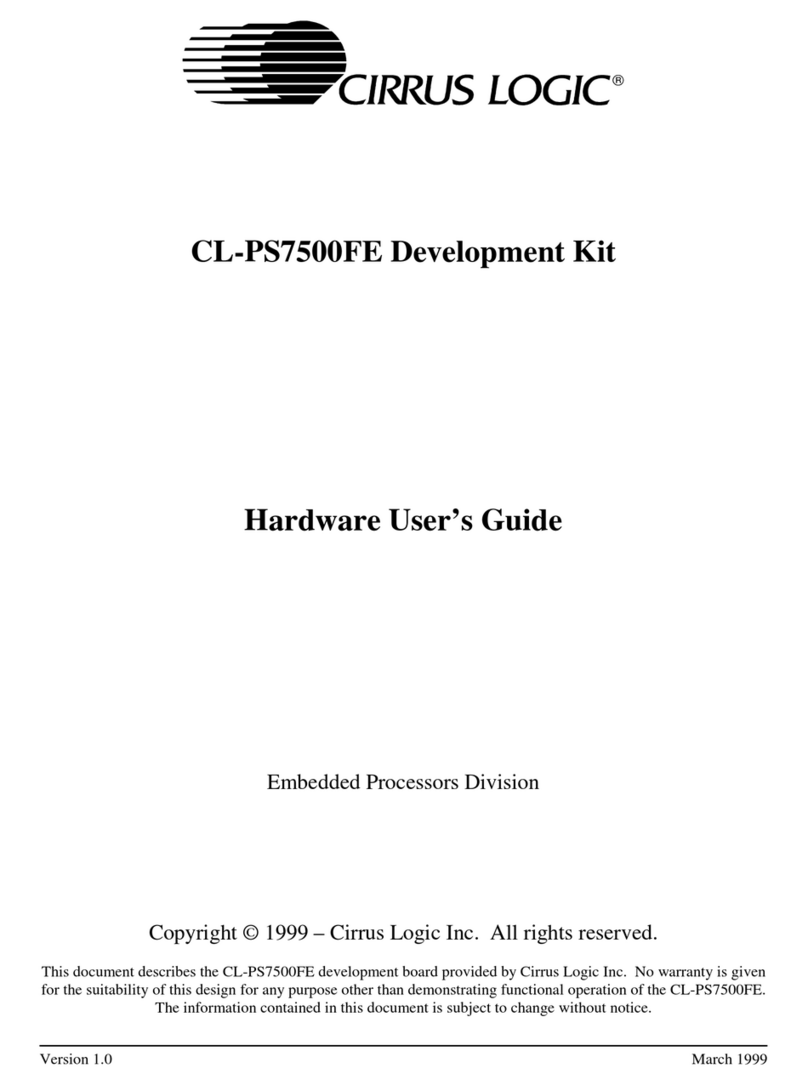
Cirrus Logic
Cirrus Logic CL-PS7500FE Hardware user's guide

SmartNanotubes
SmartNanotubes Smell INSPECTOR Technical manual
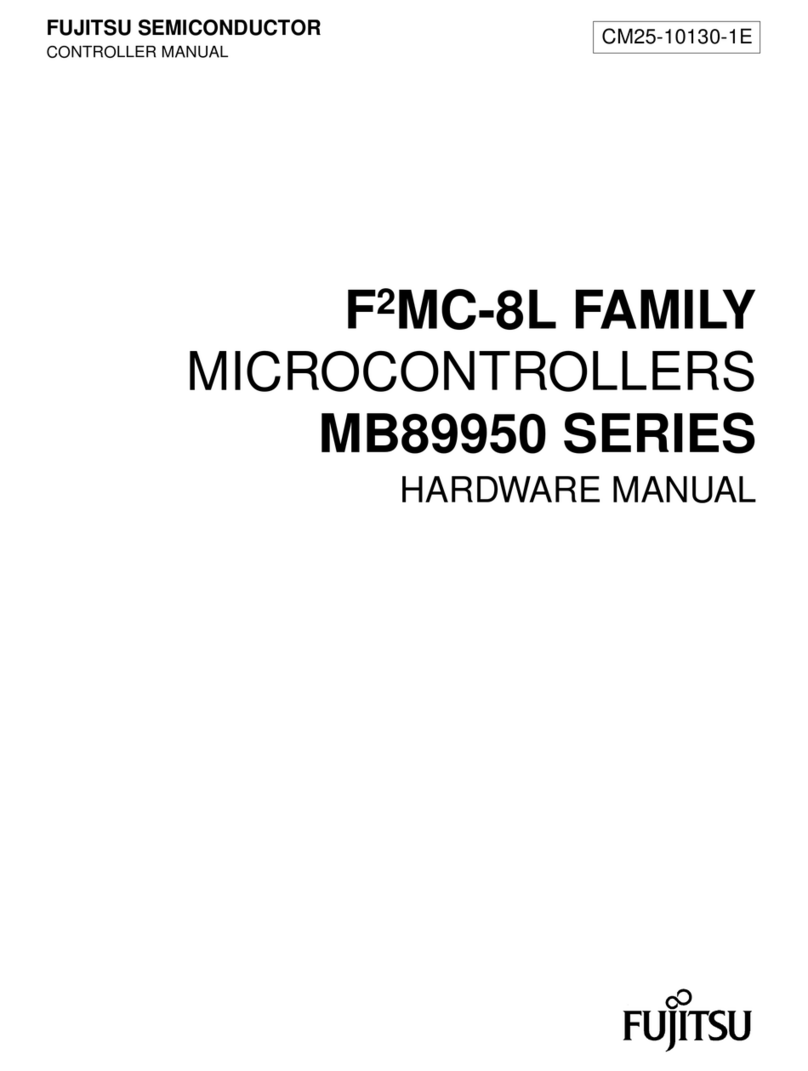
Fujitsu
Fujitsu F2MC-8L Family series Hardware manual