Mitek RoofTracker III Reference manual

MACHINERY DIVISION
MiTek Machinery Division
301 Fountain Lakes Industrial Drive
St. Charles, MO 63301
Phone: 800-523-3380
Fax: 636-328-9218
www.mitek-us.com
SERVICE BULLETIN
Affected machinery:
RoofTracker III™ roller press
Document:
SB203 rev. B
Title:
Electrical & Software Updates for
Reset Button & Deceleration Changes
Distribution:
All customers
Part # and Rev. SB203 rev. B
Print Date 1 July 2020
Effectivity Frame #s
333, 335, 337-451
Revision Date 29 June 2020
Revised By A. McIntire
Orig. Release Date 5 December 2019
Created By R. Tucker
Approved By M. Kanjee

SB203
ORIGINAL INSTRUCTIONS 2
Purpose and Scope
MiTek has applied software and wiring changes to the RoofTracker III to make daily
operation more efficient and convenient. These changes eliminate the need to press and
hold the Reset button to move the gantry head in the opposite directions when the safety
circuit detects an obstruction. Please upgrade your software as soon as possible and return
the parts indicated to MiTek.
Once the software update is complete, machines with laser scanners will exhibit a faster
deceleration when the scanner detects an obstacle, resulting in a smoother stop and
reduced wear and tear on machine components.
IMPORTANT: Returning Parts
An RGA document is enclosed in your kit to return the two memory devices. Please
package them in a way that they will not be damaged during shipment. Thank you!
Overview
The parts included in the kits are shown below. Please make sure all parts are present
before starting this procedure.
Figure 1: Parts in SB203KITs
Contact MiTek Automation Solution Customer Service
immediately upon completing this procedure, and we will
arrange for Fedex to pickup the package.
[email protected] or 800-523-3380
Quantity Kit Voltage Description Part #
1
208V
Memory module programmed for VFD
509791-505
230V 509791-506
460V 509791-507
575V 509791-508
1 - Memory cassette programmed for safety
controller
94019
4 ft - Wire, 18 AWG (for jumpers) 508003
16 ft - Wire, 16 AWG (for signal wires) 508870
1 sheet - Blank labels for new wires 694060
1 - Service bulletin document SB203
1 - RGA document for returning memory
devices
N/A
1 - Printed electrical schematic 90635 rev. H

SB203
ORIGINAL INSTRUCTIONS 3
Before beginning the procedure, gather the supplies listed here:
If you have any questions, call MiTek Machinery Division Customer Service
at 1-800-523-3380.
Wire strippers/cutters Slotted screwdriver Marker
Lockout/tagout device Phillips screwdriver T-20 Torx tool
Wooden T for safety test (see page 12)

SB203
ORIGINAL INSTRUCTIONS 4
Procedure
Electrical Lockout/Tagout Procedure
Procedure for Working Either on a Machine Inside the Machine’s Main
Electrical Enclosure or in the Electrical Transmission Line to the Machine
Before opening the main electrical enclosure or attempting to repair or replace an
electrical transmission line, lockout/tagout the machine properly. Follow your company’s
approved lockout/tagout procedures, which should include, but are not limited to, the steps
here.
1. Engage an E-stop on the machine.
2. If you have a Wizard PDS® operator
station mounted to the gantry head, turn
that computer off now.
3. Turn the machine’s disconnect switch to
the Off position. This is usually required to
open the main electrical enclosure’s door.
4. Shut the power to the machine off at the
machine’s power source, which is usually
an electrical service entry panel on the
facility wall. One example of a locked-out
power source panel is shown in Figure 2.
5. Attach a lock and tag that meets OSHA
requirements for lockout/tagout to the
electrical service entry panel.
6. Wait 20 seconds for the VFD to discharge
any remaining power.
7. Open the door to the enclosure to which
you need access. Using a multimeter,
verify that the power is off.
!WARNING
ELECTROCUTION HAZARD.
All electrical work must be performed by a qualified electrician.
Verify that all power to the machine has been turned off and follow
approved lockout/tagout safety procedures before performing any
maintenance.
If it is absolutely necessary to troubleshoot an energized
machine, follow NFPA 70E for proper procedures and person
protective equipment.
Figure 2: Lockout/Tagout on
the Power Source Panel

SB203
ORIGINAL INSTRUCTIONS 5
Pneumatic System Lockout/Tagout Procedure
!WARNING
MOVING PARTS CAN CRUSH AND CUT.
Always verify that power to the machine has been turned off and
follow approved lockout/tagout procedures.
!WARNING
HIGH PRESSURE HAZARD.
Bleed pneumatic lines before performing any maintenance on the
system.
Working on pressurized lines may cause injury.

SB203
ORIGINAL INSTRUCTIONS 6
Replacing the VFD Memory Module
The VFD must have a new program for the intended changes to take place.
1. Remove the VFD cover. Depending on the VFD model, it can be removed in one
of two ways:
• Insert a screwdriver into the notch at the bottom-center of the cover, OR
• Remove the screws securing the cover.
2. With power locked out, remove the old VFD memory module and return it using
these steps:
a) Place latch in Unlock position and pull out gently on the memory module.
b) Follow the instructions on page 2 to return the memory module to MiTek.
c) On the new memory module, push the tab as shown in Figure 3 to extend the
points out, and place the memory module into its slot.
3. Place the latch in Lock position.
Figure 3: Replacing the VFD Memory Module
Unlock
position
for removal.
Lock position
for securing
in place.
Push tab down
to extend points
for connection
to occur.

SB203
ORIGINAL INSTRUCTIONS 7
Replacing the Safety Controller Memory Cassette
The safety controller must have a new program for the changes to take place.
Figure 4: Enclosure Overview & Safety Controller Steps
Installing the Memory Cassette into the Safety Controller
1. With the power locked out, locate the safety controller shown in Figure 4 and
verify that the DIP switch 4 is in the off (left) position.
2. Remove the old memory cassette from the safety controller and follow the
instructions on page 2 to return it to MiTek.
3. Insert the new memory cassette into the safety controller.
VFD Screen
VFD Main
Relays
Extension
Module
FIO-01
DIP
switch
4 in left
position.
Safety
Controller
memory casette
VFD
Memory
Module
230-volt enclosure shown. 460-volt enclosure may vary slightly.

SB203
ORIGINAL INSTRUCTIONS 8
4. With the main enclosure door open, remove the lock and tag from the gantry
head’s power source. Turn on the machine’s disconnect switch at the 3-phase
fuses to restore power to the gantry head. All components are now powered.
5. Press the push-switch shown in Figure 5
for at least two seconds. The MC
indicator light should flash yellow and
the input terminal lights should flash in a
repeated sequence to indicate that the
program has finished downloading to the
safety controller.
6. After the terminal input lights start
flashing in sequence, cycle power at the
machine’s disconnect switch.
After you cycle power, you may proceed
after:
• The MS indicator light turns green.
• The LOCK indicator light turns yellow.
Figure 6: Do NOT Continue if Indicators Look Like This
!WARNING
ELECTROCUTION HAZARD.
All components have electrical power during these next steps.
All electrical work must be performed by a qualified electrician.
If it is absolutely necessary to troubleshoot an energized
machine, follow NFPA 70E for proper procedures and person
protective equipment.
If the lights look like Figure 6, there is a password issue and the procedure
cannot be completed. Contact MiTek immediately at the number on page 2.
Figure 5: Push-Switch
Indicator
Lights
Hold
push-switch
for 2 sec.
Si5
illuminated
illuminated

SB203
ORIGINAL INSTRUCTIONS 9
Rewiring for Software Change Compatibility
Some minor wiring changes must be made for the machine to accept the program changes.
1. Lockout/tagout out as previously described on page 4, and locate the VFD in the
main electrical enclosure. It is shown on page 10.
2. Make the wiring changes according to Figure 7. All supplies needed are included.
3. Gently tug on newly installed wires to ensure they are securely attached.
4. Reinstall the VFD cover.
Figure 7: Wire Connection Points
It is easiest to connect the wires by removing the terminal block,
connecting the wires, then putting the terminal block back in place.
TIP: 16-gauge wires are larger in diameter than 18-gauge wires.
JUMPER A
Wire: 18 AWG cut as needed
Label: T1
Connect:
Ext. Relay LT, terminal 2 to
Ext Relay RT, terminal 2
shares terminals with existing wires
Jumper A
Jumper B
Main
Relays
R13 JUMPER B
Wire: 18 AWG cut as needed
Label: T1
Connect:
Ext. Relay RT, terminal 2 to
Main Relay R13
shares terminals with existing wires
SIGNAL WIRE S17
Wire: 16 AWG cut as needed
Label: SI7
Connect:
Ext. Relay LT, terminal 1 to
Safety Controller SI7
Signal Wire SI7 Signal Wire SI8
SIGNAL WIRE S18
Wire: 16 AWG cut as needed
Label: SI8
Connect:
Ext. Relay RT, terminal 1 to
Safety Controller SI8
Continue on to see proper
routing of signal wires
Ext Relay LT Ext Relay RT

SB203
ORIGINAL INSTRUCTIONS 10
Termination Points for Signal Wires
Wire Routing
460-volt enclosure shown.
230-volt enclosure may
vary slightly.
VFD
Figure 8: Routing the Wires
to the Safety Controller

SB203
ORIGINAL INSTRUCTIONS 11
Setting the Supply Voltage
1. With the 3-phase electrical enclosure door open, restore power to the machine.
2. Look at the VFD screen through the viewer slot in the door for errors.
If Fault 5093 appears on the VFD screen, cycle the power again to clear the fault.
3. If the VFD displays Warning A6A6, perform these steps to set the correct supply
voltage:
a) Press the Left Selector to
select Hide, and the
display will change
screens.
b) Choose Select
Parameter.
c) Arrow to 95 and select it.
d) Arrow to 01 and select it.
e) Arrow to the appropriate
voltage according to
Table 1 and select it.
f) Press Back until you
reach Exit, and select it.
4. Close all enclosure doors.
!WARNING
ELECTROCUTION HAZARD.
All components have electrical power during these next steps.
All electrical work must be performed by a qualified electrician.
If it is absolutely necessary to troubleshoot an energized
machine, follow NFPA 70E for proper procedures and person
protective equipment.
Left
Selector
Figure 9: VFD Interface
Table 1: Supply Voltage Settings
Machine
Voltage
Supply Voltage
Setting
208 208-240
230 208-240
415 380-415
460 500
575 525-600

SB203
ORIGINAL INSTRUCTIONS 12
Test for Safety and Proper Operation
1. Test that the gantry head E-stop scanner activates the E-stop when an obstacle is
in its path. Even if the machine seems to be working fine, the E-stop capabilities
must be tested! We suggest using a wooden T as described in the RoofTracker III
equipment manual.
2. If it does not E-stop properly, contact MiTek Automation Solutions Customer
Service immediately and do not attempt to use the machine. Lockout/tagout the
machine until the issue is resolved.
3. Perform all additional safety tests from the safety chapter of the RoofTracker III
manual to verify that the gantry head operates correctly.
New Operating Method
Reset Button
Upon the completion of this service bulletin, the gantry head controls will operate
differently. When the gantry head is traveling in either direction, if the scanner observes an
obstacle in the direction it is traveling, it will slow down, then stop before reaching the
obstruction. Movement in the opposite direction from the obstacle is unaffected. With the
obstacle detected, you can move the gantry head in the opposite direction without pressing
the Reset button to allow you to safely remove the obstacle.
Beacon Light
• The light blinks yellow (amber) when the machine is running.
•NEW! The light turns off when ONE scanner is tripped, letting you know the
gantry head can move in only the direction opposite of what it was just traveling.
• The light blinks red when an E-stop pushbutton is activated or when BOTH
scanners are tripped.
• The light is green when ready to operate.
New Schematics
New electrical schematics came with this kit. Replace your old schematics with these
updated pages so maintenance personnel are always working from the correct set.
END OF SERVICE BULLETIN
!WARNING
CRUSH HAZARD!
The success of the procedures performed must be verified as
described in the Safety Test section of the equipment manual.
Not testing properly could result in an E-stop failing to stop the
machine.
Table of contents
Other Mitek Power Tools manuals
Popular Power Tools manuals by other brands
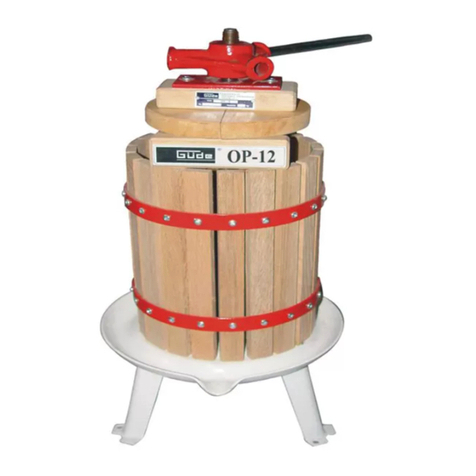
Gude
Gude OP 6 Translation of original operating instructions
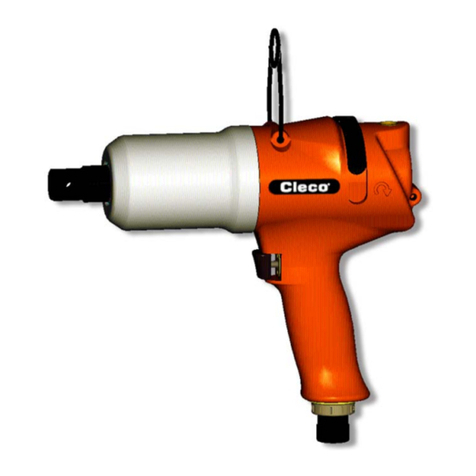
Cleco
Cleco 140PTHC Series instruction manual

HSS Hire
HSS Hire Hire Shops 631 Operating & safety guide
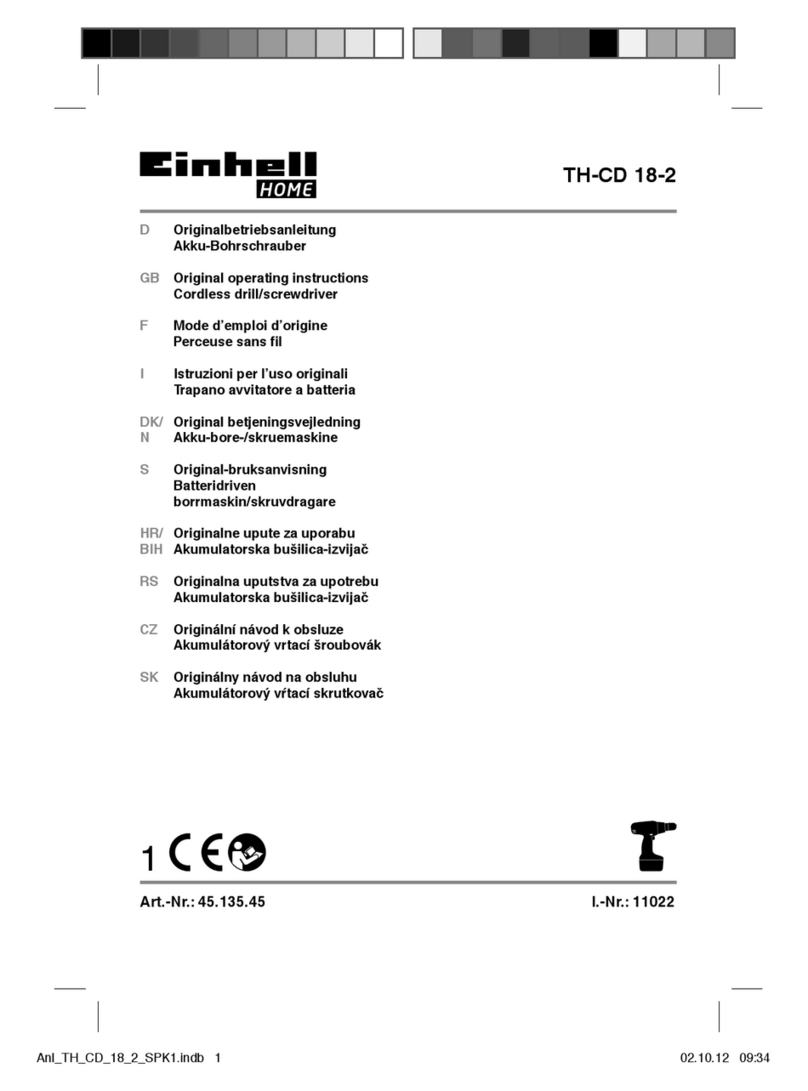
EINHELL HOME
EINHELL HOME TH-CD 18-2 Original operating instructions
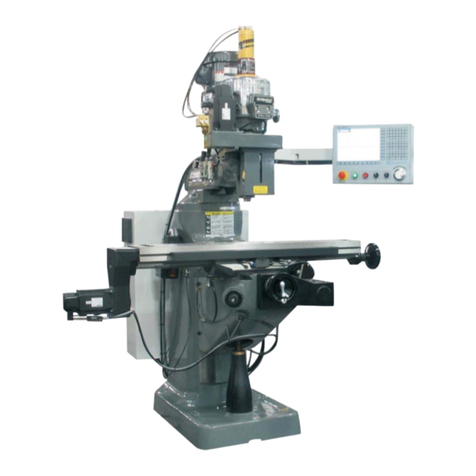
Hardinge
Hardinge Bridgeport EZ Vision Installation, Maintenance, and Parts Manual
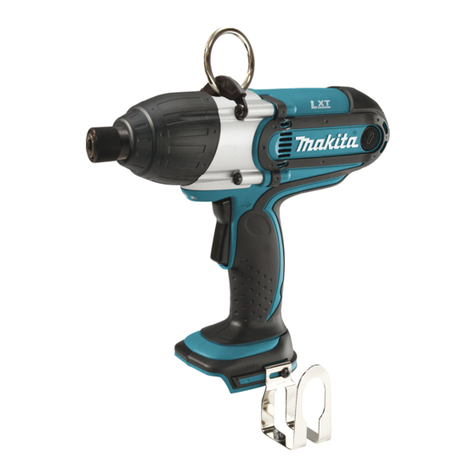
Makita
Makita XWT01Z instruction manual