Mod-tronic APD 1500 Series User manual

Input: 100 Ωto 10,000 ΩBridges, 5 mV to 2000 mV, 1-10 VDC Excitation
Output: Two 8 Amp SPDT Relays
OFactory Set Input Range
ORemovable Plugs for Faster Installation
OInput LoopTracker®and Alarm Status LEDs
OFull 1200 V Isolation
OAlarm Test, Optional Reset Button
QLoad Cell Weighing Systems and Scales
QStrain Gauge Pressure Sensors and Transducers
QTanks, Scales, Extruder Melt Pressure, Crane Loads
Strain Gauge Input Range
Factory configured, specify sensor mV/V rating and mV range
Minimum sensor rating: 5 mV
Maximum sensor rating: 2000 mV
Millivolt range is determined by the sensitivity of the sensor
(mV/V) and the excitation voltage applied.
mV/V sensitivity X excitation voltage = total mV range
Input Impedance
1 MΩminimum
Isolation
Power to input isolation: 1200 V
Common mode protection: 600 VACpor 600 VDC
Excitation Voltage
Factory configured, please specify excitation voltage
Refer to the sensor manufacturer's recommendations.
Excitation: 1 to 10 VDC, 30 mA max.
Fine adjustment: Approximately ±0.25 VDC
Stability: ±0.01% per °C
Designed for one 350 Ω(or greater) sensor
LoopTracker
Variable brightness LED indicates input loop level and status
APD 1500 Relay Output
Dual SPDT Form C contact sets operating in unison
1 setpoint adjustment, 1 deadband adjustment
Standard: HI alarm, non-latching, normal acting
Options: LO alarm, latching, reverse acting
APD 1520 Relay Output
2 independent SPDT Form C contact sets
2 setpoint adjustments, 2 deadband adjustments
Standard: HI/LO alarm, non-latching, normal acting
Options: LO/LO, HI/HI, LO/HI alarms, latching, reverse acting
Relay Contact Ratings
8 A max @ 240 VAC resistive load
External contact protection such as an RC snubber is recom-
mended for inductive loads
Setpoint
12 turn potentiometer adjustable from 0 to 100% of span
Deadband
12 turn potentiometer adjustable from 1 to 100% of span
Response Time
70 milliseconds typical
Output Test/Reset Button
Front button or external contact closure toggles relays to
opposite state when pressed.
Resets relay if latching relay option is ordered.
Ambient Temperature Range and Stability
–10°C to +60°C operating ambient
Better than 0.02% of span per °C
Switching Current (A)
Switching Voltage (V)
0 3 5 10 30 50 100 300 500
8
5
3
1
0.5
0.3
0.1
AC inductive load
(cos f= 0.4) AC resistive
load
DC inductive load
(L/R = 7 ms)
DC resistive
load
Alarm Options—add to end of model number
LAPD 1500 with LO trip. Alarm trips on decreasing signal.
HH APD 1520 with HI/HI trip. Alarms trip at their respective
trip points on increasing signal.
LL APD 1520 with LO/LO trip. Alarms trip at their respective
trip points on decreasing signal.
LH APD 1520 with LO/HI trip. Alarm 1 trips on decreasing
signal. Alarm 2 trips on increasing signal.
HT Latching alarm with push button reset
HP Latching alarm with power-off reset. Module power
must be turned off to reset alarms
RReverse-acting alarms. Relay coils energized in an alarm
condition. No alarm condition with module power off.
UConformal coating for moisture resistance
Accessory—order as separate line item
API BP4 Spare removable 4 terminal plug, black
Strain Gauge Transducer Alarm Trips, Factory Ranged, Isolated APD 1500, APD 1520
Applications
Universal Power
Alarm Status LED
Input LoopTracker LED
Alarm Test Function
Adjustable Deadband
Two 8 Amp SPDT Alarm Relays
Custom Input Ranges
Removable Plugs
File E145968
85-265 VAC, 60-300 VDC
model only
Adjustable Setpoint
Model Input Standard Alarm Configuration Power
APD 1500 Factory ranged, specify
sensor mV/V rating,
mV range, excitation
voltage
Single setpoint dual SPDT relays
HI alarm, non-latching, normal acting
85-265 VAC or 60-300 VDC
APD 1500 D 9-30 VDC or 10-32 VAC
APD 1520 2 setpoints, 2 SPDT relays
HI/LO alarms, non-latching, normal acting
85-265 VAC or 60-300 VDC
APD 1520 D 9-30 VDC or 10-32 VAC
Description
The APD 1500 and APD 1520 accept a strain gauge, bridge, or
load cell input and provide a visual alarm indication and alarm
relay contact outputs.
The input is factory configured to a specific excitation volt-
age and millivolt input range. The input can be configured as
zero-based (i.e., 0 to 20 mV), bipolar (i.e., –30 to +30 mV) for
push-pull applications, or offset (i.e., 5 to 33 mV) to electroni-
cally compensate for deadweights (tare).
The alarm types are factory configured.
Front-accessible potentiometers are used to adjust alarm
setpoint and deadband.
LoopTracker and Alarm Status LEDs
API exclusive features include a LoopTracker LED that varies
in intensity with changes in the process input signal.
A red/green bicolor alarm status LED (two on the APD 1520)
visually indicate alarm status. These LEDs provide a quick
visual picture of your process at all times.
Output Test / Unlatch
The API exclusive Output Test button can be used to verify the
alarm and system operation and also provides the additional
function of unlatching the alarm when the latching option has
been ordered. This feature can be remotely operated.
The output test button greatly aids in saving time during initial
startup and/or troubleshooting.
Dimensions
0.89" W x 4.62" H x 4.81" D
(22.5 x 117 x 122 mm)
Height includes connectors
Housing and Connectors
IP 40, requires installation in panel or enclosure
For use in Pollution Degree 2 Environment
Mount vertically to a 35 mm DIN rail
Four 4-terminal removable connectors, 14 AWG max wire size
Power
85-265 VAC, 50/60 Hz or 60-300 VDC, 2 W maximum
D versions: 9-30 VDC or 10-32 VAC 50/60 Hz, 2 W maximum
Free Factory
I/O Setup!
HHHHHH
HHHHH
HHHHHH
HHHHH
HHHHHH
HHHHH
HHHHHH
HHHHH
HHHHHH
Made in USA
1 2 3 4
5 6 7 8
9 10 11 12
13 14 15 16
1 2 3 4
5 6 7 8
9 10 11 12
13 14 15 16
See Wiring
Diagrams on
Next Page
See Wiring
Diagrams on
Next Page

Precautions
WARNING! All wiring must be performed by a qualified electri-
cian or instrumentation engineer. See diagram for terminal des-
ignations and wiring examples. Consult factory for assistance.
WARNING! Avoid shock hazards! Turn signal input, output,
and power off before connecting or disconnecting wiring, or
removing or installing module.
Précautions
ATTENTION! Tout le câblage doit être effectué par un élec-
tricien ou ingénieur en instrumentation qualifié. Voir le dia-
gramme pour désignations des bornes et des exemples de
câblage. Consulter l'usine pour assistance.
ATTENTION! Éviter les risques de choc! Fermez le signal
d'entrée, le signal de sortie et l'alimentation électrique avant
de connecter ou de déconnecter le câblage, ou de retirer ou
d'installer le module.
Input
The strain gauge input range is factory configured. See the
model/serial number label for input type, range, and options.
Refer to strain gauge manufacturer’s data sheet for wire
color-coding. Polarity must be observed when connecting
inputs. See the wiring diagrams below right.
CAUTION: Never short the excitation terminals together. This
will cause internal damage to the module.
After installation and after all connections are made, the
excitation fine adjust potentiometer may be used to precisely
trim the excitation voltage, if desired.
Alarm Types
Note that the deadband is symmetrical about the setpoint; re-
lay trip and reset points will both change if either the setpoint
or deadband are changed.
High Alarm (default, H, or HH): The alarm relay changes state
when the input signal exceeds the deadband trip point. The relay
resets when the input signal drops below the deadband reset
point. For a high alarm, the trip point is above the reset point.
Low Alarm (L or LL): The alarm relay changes state when the
input signal goes below the deadband trip point. The relay
resets when the input signal exceeds the deadband reset
point. For a low alarm the trip point is below the reset point.
HT: Latching alarm with push button reset
HP: Latching alarm with power-off reset. Module power must
be turned off to reset alarms
R: Reverse-acting alarms. Relay coils energized in an alarm
condition. No alarm condition with module power off.
Relay Output Terminals
See wiring diagrams below right for connections. APD modules
do not provide power to the relay contacts. Inductive loads (mo-
tors, solenoids, contactors, etc.) will greatly shorten relay con-
tact life unless an appropriate RC snubber is installed.
The APD 1500 operates two sets of relays in unison with a
single setpoint. The dual SPDT contact sets are in a Form C
configuration.
The APD 1520 operates two sets of relays independently,
each with its own setpoint. The dual SPDT contact sets are in
a Form C configuration.
Module Power Terminals
Check model/serial number label for module operating volt-
age to make sure it matches available power.
When using DC power, either polarity is acceptable, but for
consistency with similar API products, positive (+) can be wired
to terminal 13 and negative (–) can be wired to terminal 16.
Mounting to a DIN Rail
Install module vertically on a 35 mm DIN rail in a protective
enclosure away from heat sources. Do not block air flow. Al-
low 1" (25 mm) above and below housing vents for air cir-
culation.
1. Tilt front of module downward and position against DIN rail.
2. Clip lower mount to bottom edge of DIN rail.
3. Push front of module upward until upper mount snaps into place.
Removal
1. Push up on the bottom back of the module.
2. Tilt front of module downward to release upper mount
from top edge of DIN rail.
3. The module can now be removed from the DIN rail.
Setup and Calibration
Relay operation is factory configured. See model/serial num-
ber label for relay configurations.
The Setpoint potentiometer allows the operator to adjust the
level at which the alarm is activated. This control is adjustable
from 0 to 100% of the input range.
The Deadband potentiometer allows the alarm trip and reset
window to be adjusted symmetrically about the setpoint from
1 to 100% of the span. This allows the operator to fine tune
the point at which the alarm trips and resets. The deadband
is typically used to prevent chattering of the relays or false
trips when the process signal is unstable or changes rapidly.
To calibrate the alarm section, set the deadband control to the
minimum (counterclockwise). The deadband will be 1.0% of
input span in this case.
Set the signal source to the desired trip point.
Adjust the setpoint control to the point at which the relay
changes state from a non-alarm to an alarm condition.
Turn the deadband potentiometer clockwise for a larger amount
of deadband. The deadband is symmetrical about the setpoint;
both transition points will change as deadband is increased.
Relay set and reset points will both change if the setpoint or
deadband are changed. Alternately set the setpoint and dead-
band until the desired trip and rest points are set.
Output Test Function
When the front test button is depressed it will drive the relays
to their opposite state. A customer-supplied switch connected
to terminals 4 and 8 can also be used to toggle the relays.
When released, the relays will return to their prior states.
This can be used as a diagnostic aid during initial start-up or
troubleshooting, or as a manual over-ride function. The Test
button also resets the relays on models with the HT option.
Operation
The green LoopTracker®input LED provides a visual indication
that a signal is being sensed by the input circuitry of the mod-
ule. It also indicates the input signal strength by changing in
intensity as the process changes from minimum to maximum.
If the LED fails to illuminate, or fails to change in intensity as
the process changes, check the module power or signal input
wiring. Note that it may be difficult to see the LEDs under
bright lighting conditions.
The bicolor alarm LED provides a visual indication of the alarm
status. In all configurations, a green LED indicates a non-alarm
condition and a red LED indicates an alarm condition.
In the normal mode of operation, the relay coil is energized in
a non-alarm condition and de-energized in an alarm condi-
tion. This will create an alarm condition if the module loses
power. For a normal acting, non-latching configuration, the
alarm will activate when the input signal exceeds the setpoint
(HI alarm) or falls below the setpoint (LO alarm), then will
automatically reset when the alarm condition no longer exists.
For a reverse acting alarm, the relay coil is de-energized in a
non-alarm condition and energized in an alarm condition. The
alarm activates when the input signal exceeds the setpoint (HI
alarm) or falls below the setpoint (LO alarm), then automati-
cally resets when the alarm condition no longer exists.
For models with the latching relay option, it will be necessary
to push the Test button or remove power from the module to
reset the alarm, depending on the type of latching option. The
alarm will only reset if the alarm condition no longer exists.
Installation and Setup APD 1500, APD 1520
Module Power
AC or DC +
AC or DC –
1413 15 16
Cu 60/75°C
conductors
14 AWG
max.
1 2 3 4
5 6 7 8
9 10 11 12
13 14 15 16
Input
Relay 1
Power
Relay 2
4 and 8
Relay Test
Test Input
APD 1500
Strain Gauge Input to
Single Alarm Trip
Loop
Tracker
Deadband
Setpoint
Alarm
Test
APD 1520
Strain Gauge Input to
Dual Alarm Trip
Input
Loop
Tracker
Deadband 1
Setpoint 1
Alarm 1
Deadband 2
Setpoint 2
Alarm 2
Sensor
shield wire
(if equipped)
should be
grounded
at one end
only
Sig
–
Sig
+
Strain
Gauge
Exc
–
109 11 12
Exc
+
Relay Wiring APD 1500
NO C NC
21 3 4
65 7 8
NO C NC
Customer-Supplied
Remote Test Switch
NO C NC
21 3 4
65 7 8
NO C NC
Customer-Supplied
Remote Test Switch
RLY 1
RLY 2
Relay Wiring APD 1520
To maintain full isolation avoid com-
bining power supplies in common
with input, output, or unit power.
To avoid damage
to the module,
do not make any
connections to
unused terminals
Wire terminal torque
0.5Nm to 0.6Nm
(4.4 to 5.3 in-lbs)
To maintain full isola-
tion avoid combining
power supplies in
common with input,
output, or unit power.
API maintains a constant effort to upgrade and improve its products.
Specifications are subject to change without notice. See api-usa.com for
latest product information. Consult factory for your specific requirements.
WARNING: This product can expose you to chemicals includ-
ing nickel, which are known to the State of California to cause
cancer or birth defects or other reproductive harm. For more
information go to www.P65Warnings.ca.gov
This manual suits for next models
4
Popular Transducer manuals by other brands
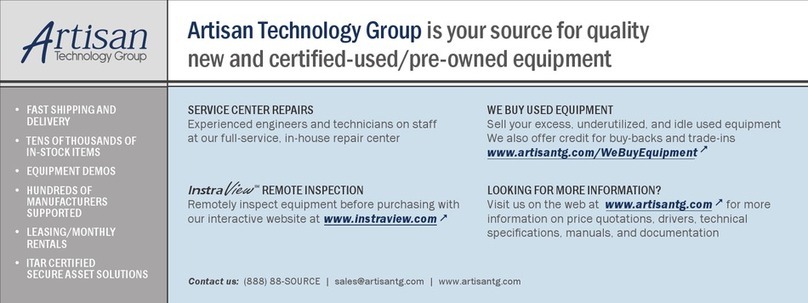
MKS
MKS Baratron 122B instruction manual

Greystone Energy Systems
Greystone Energy Systems LP-S installation instructions

TE Connectivity
TE Connectivity AST46DS operating instructions
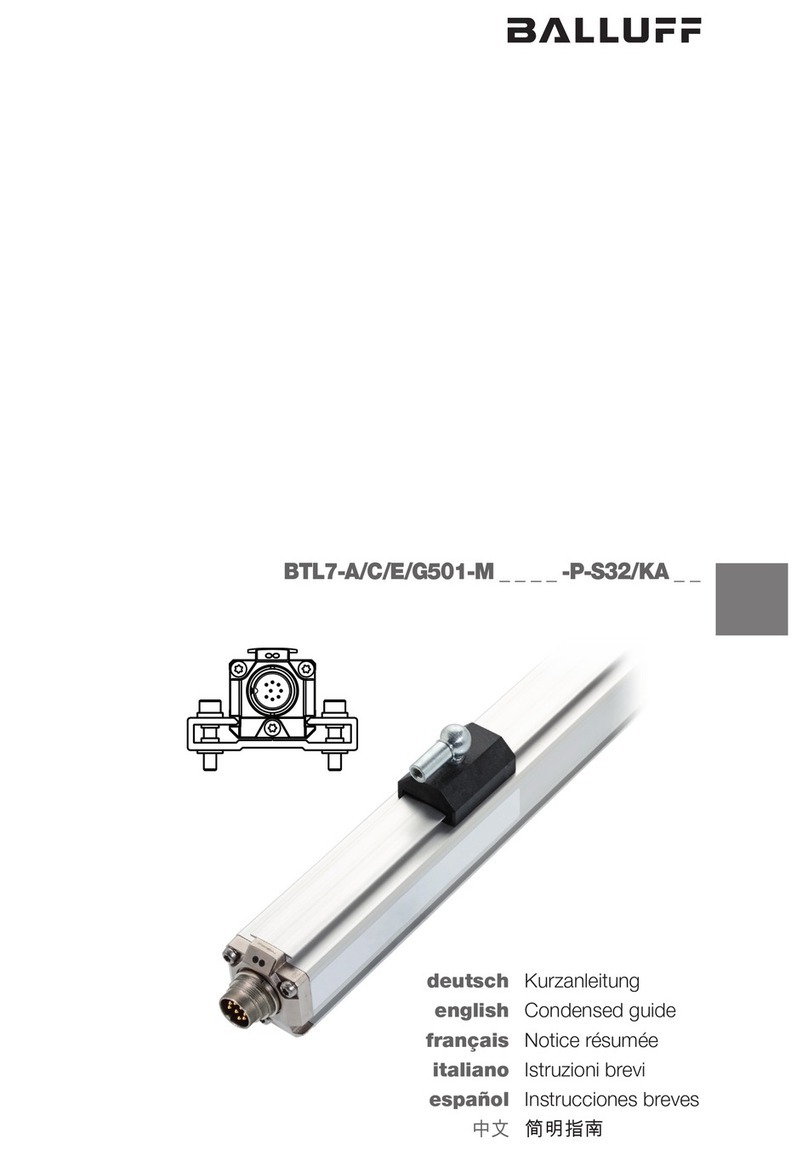
Balluff
Balluff BTL7-A501-M-P-S32/KA Series instruction manual

TR-Electronic
TR-Electronic LMR-70-300 ANA-I+JUSTAGE manual
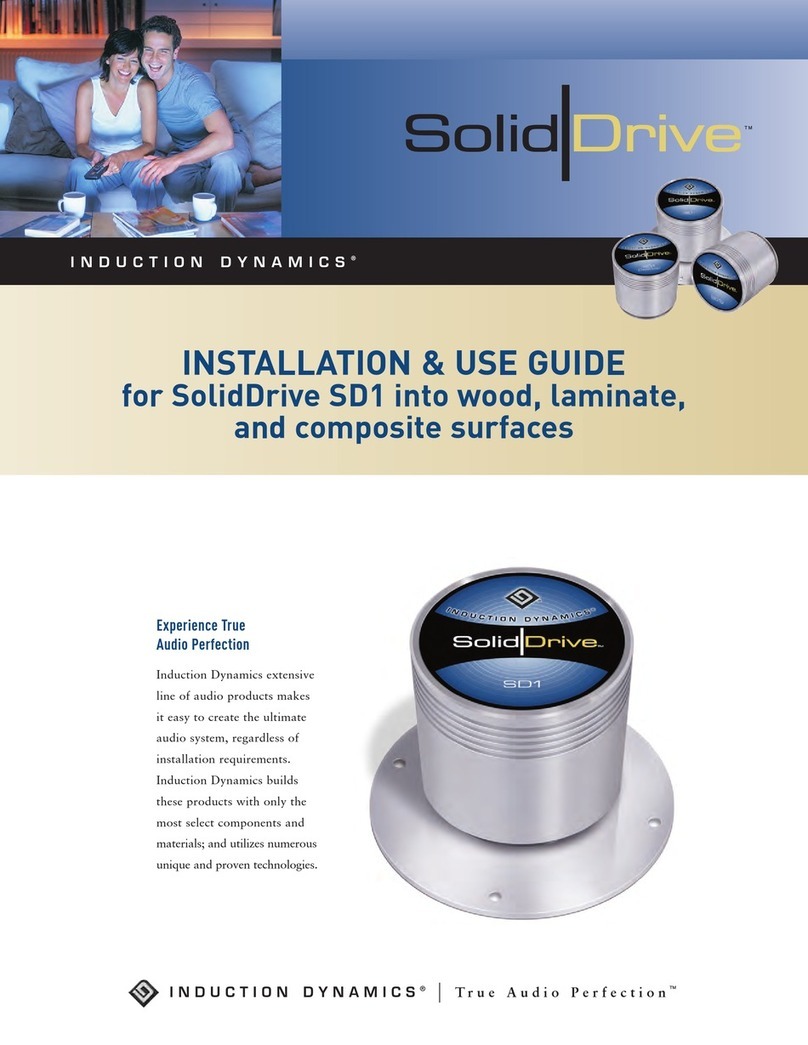
Induction Dynamics
Induction Dynamics SolidDrive SD1 Installation & use guide