Moog 903 User manual

Moog Inc., Components Group, Halifax Operations
Focal Technologies Corporation
77 Frazee Avenue
Dartmouth, Nova Scotia, Canada B3B 1Z4
Tel: 902-468-2263 • Fax: 902-468-2249
Application Note
This document is the property of Focal Technologies Corporation, and may not be neither copied, reproduced or otherwise dealt with nor its
contents communicated to others except in accordance with written instructions received from Focal Technologies Corporation.
700-0290-00 Rev. 1 Page 1 of 6
INITIAL CHECKS
• Ensure cards installed and configured as per installation drawing. (Note: in a 16HP medium speed, high density
system, the FMB is furthest right and the HDB-TX card must be installed in the slot adjacent to the FMB).
• Ensure correct input power is supplied and verify the primary fuse is not open.
• Fuses: each module and card have fuse protection. Ensure there are no input power supply issues or incorrect
connector wiring before replacing fuses. Several spare kits are available for fuses, e.g. 903-8022-18.
• Verify the proper fuse type and value and location per the User's Guide appendices.
• Ensure voltage rail levels are acceptable using either the diagnostics software or a voltmeter.
• Ensure external fibers and bushings are clean and have low optical loss. (May be verified with diagnostic
software or an optical power meter.)
• Ensure optical output power levels are sufficient at the FMB front panels with an optical power meter:
• Typically Console FMB 1550nm downlink output power should be -6 dBm or better and Remote FMB 1310nm
uplink output power should be -6 dBm or better. Refer to your Model 903 User's Guide for more details on
output power specifications.
• Ensure receiver power at the FMB front panel is acceptable, typically between -8 dBm and -26 dBm. Excessive
receive power will cause errors or possibly even damage the receiver and low receive power will cause errors or
link faults. In general, bench testing should be conducted with a 5-10 dB optical attenuator.
REVIEW SETTINGS
• Cards should be shipped from Focal in the default configuration for the specific system. Shunt terminals are 2-
pin or 3-pin; pin 1 is typically designated with a square pad or silk-screened ‘1’.
• DIP switches are set either on (1) or off (0). Circuit 1 is the leftmost switch when reading the text on the switch.
• Mode settings should generally match on remote and console cards, except AIB-MS900, AIB-ARCNET, and
AIB-HYDRO.
• FMB DIP switch settings should not normally be changed. When troubleshooting an older card with a DIP
switch, switch the DIP switch back and forth a few times to ensure there is a good, stable contact.
USING DIAGNOSTIC SOFTWARE
• Check for acceptable voltage levels (screen LEDs).
• Check acceptable temperature, remote and console (both should be less than +70C).
• Check for uplink/downlink errors (<= 1 error per hour typical).
• Verify expected optical levels (transmitted and received) with fiber optic power meter.
• Verify flux budget with VOAT (Variable Optical Attenuator), per user's guide.
• Observe strip chart for unusual power fluctuations in the optical link.
• Verify losses of video sync.
• Log diagnostics files for long term monitoring.
• When new FMBs are installed, the software may need to be recalibrated for optical readings. (OK if within 2 dB).
MODEL 903 EVALUATING AND TROUBLE-SHOOTING GUIDE
Doc. No.
700-0290-00
Revision:
1
Date:
2006 March 01

Moog Inc., Components Group, Halifax Operations
Focal Technologies Corporation
77 Frazee Avenue
Dartmouth, Nova Scotia, Canada B3B 1Z4
Tel: 902-468-2263 • Fax: 902-468-2249
Application Note
This document is the property of Focal Technologies Corporation, and may not be neither copied, reproduced or otherwise dealt with nor its
contents communicated to others except in accordance with written instructions received from Focal Technologies Corporation.
700-0290-00 Rev. 1 Page 2 of 6
MOST COMMON VIDEO PROBLEMS
• Improper impedance matching (75 ohms) or missing ground connection
• Video signal “too hot”, i.e. >> 1 Vpp nominal. (Camera outputs may be set to drive long copper cables.)
• RG-179 OK but attenuates at higher frequencies, so limit to a few meters or use RG-59 for long runs
• Isolation required, e.g. Deerfield Labs transformer (grounding problems between camera, mux, monitor)
• Wrong jumper settings on video card for composite versus S-video (Y/C) and RGB (see user's guide).
• Anti-piracy protection on VCR tapes or DVDs during testing (e.g. Macrovision)
MOST COMMON DATA PROBLEMS
• Improper RS-485 auto sense settings (refer to manual for proper settings)
• AIB plug-ins not installed in proper orientation or socket, or different card types used in remote and console end.
• Incorrect RS-485 polarity: Focal standard is negative pin is inverting and RS-485 biased with 619 ohm pull
up/down resistors plus optional 120 ohm terminator. When the two-wire polarity is correct, the red receive LED
is typically on less often then when the wires are reversed.
• No or poor terminations: terminators and impedance controlled cable is needed at high data rates (> 500 kbps).
• Poor cabling or grounding: Use twisted pairs for differential serial links. Verify proper grounding and shielding.
• AIB switch settings: Incorrect or default settings need to be changed.
• RS-422 Cross-over: Pins 1, 2 (Mux Rx) and 3, 4 (Mux Tx) are the same at both ends. Hence RS-422 coming
into the mux on pins 1/2 at one end will exit the mux at the other end on pins 3/4 for the corresponding channel.
• MS900 AIB settings: Jumper on AIB must be set one way for the remote and the opposite way for the console.
• ARCNET AIB settings: Mux and sonar settings must match, per manual.
MOST COMMON OPTICAL PROBLEMS
• Bad or contaminated connections (excessive loss and/or back reflection) cause 80% of all link problems.
• Excessive fiber bends or damaged cables cause excessive optical loss, particularly at 1550 nm.
• Insufficient fiber bandwidth, particularly in multi-mode fiber, can cause intermittent problems on long cables.
• Optical overload (not enough attenuation) during bench tests can cause link faults or errors.
• Dust contamination from bushings or connectors not being covered (especially turrets) can cause link faults.
• Mixed multimode/singlemode fiber jumpers (orange/gray vs yellow jackets) cause optical faults.
FIBER HANDLING GUIDELINES
• Never use the fiber to pick up or support the weight of the device to which it is attached.
• Do not exceed the minimum bend radius (typically 1" for many loops, 0.5" for single half loops).
• Never clamp down on fiber. For example, when securing the fiber to a PCB, do not use a tight string, clamps or
any mechanical mean to tightly bind the fiber. Local stress on the fiber increases loss and may break the fiber.
Hard epoxies should also be avoided when securing fibers on a PCB.
• Follow ESD guidelines for handling electrostatic sensitive devices, such as cards with electro-optical devices.
• Clean all optical connectors (tips and barrels), bushings, adapters, and attenuators before use.
• Momentary violations of bend radius or excessive lateral pressure may significantly reduce the long term
reliability of fiber, even if it appears undamaged. When in doubt, do not use the fiber.
• Always use dust caps on bushings, turrets and connectors, especially on turrets.
• Ensure connectors are well secured in the bushing and are not side loaded.

Moog Inc., Components Group, Halifax Operations
Focal Technologies Corporation
77 Frazee Avenue
Dartmouth, Nova Scotia, Canada B3B 1Z4
Tel: 902-468-2263 • Fax: 902-468-2249
Application Note
This document is the property of Focal Technologies Corporation, and may not be neither copied, reproduced or otherwise dealt with nor its
contents communicated to others except in accordance with written instructions received from Focal Technologies Corporation.
700-0290-00 Rev. 1 Page 3 of 6
The following is a table outlining possible problems, symptoms, and solutions for Model 903:
SYMPTOM POSSIBLE PROBLEM POTENTIAL SOLUTION
Non-functioning optical cable/damaged or
dirty connector Change optical cable
Clean optical connections
Optical loss is too high Reduce optical loss
Unit(s) not powered Apply power to modules
No link ready lights
One or both FMBs in wrong configuration Configure both the same (e.g. MS/HS)
Cable not connected to console FMB
Cable not straight connection (DTE-DCE) Install "straight through" RS-232 Cable
(EL-E0017)
No diagnostics
Program not installed or properly started Run 903-0406-00 VDM.exe and press
START button (see software manual).
Improper channel configuration (also see no
link lights). Improper wiring of WAGO
connector. (RED LED = Data into Mux;
GREEN LED = Data out of Mux)
Reference appropriate manual section
for data board configuration & wiring of
WAGO connector
Data I/O board not connected at the remote
end (903-HD only) Install ribbon cable at J5 of both HDB-
TX and DATA IO boards
No data and/or no
data LEDs
Non-working data daughtercard Replace daughtercard
No Video Improper channel configuration (see also no
link lights)
Reference appropriate manual section
for video and high density board
configuration
No video sync lights
at console No video source at remote end Plug camera into appropriate remote
video channel.
Console module
voltage reading low
PSU internal 110/220 VAC selector switch
(bottom side of cassette) may be set
incorrectly (default is 110 VAC)
Set switch to appropriate AC input
voltage (110 or 220 VAC)
Noisy video Partial LINK observable in diagnostics Inspect / clean / replace optical cable
system. Ensure valid ground connection
on video cables.
Very bright video Video signal input is too large Ensure video input is 1.0Vpp
DIAGNOSTIC LEDS
• PSU LEDs are on solid if +5, +12, -12 VDC rails are valid.
• AIB-4 Data Direction LEDs: Red = Receive (into front panel); Green = Go (from front panel). A lit red LED at
one end of the system should have corresponding lit green LED at the other end of the system.
• Only on during the space state (TTL = 0) and off during the mark state (TTL = 1); data activity is indicated by the
flashing or brightness of the LED. Idle signals are usually in the mark state (TTL = 1, LED = off)
• FMB-VTX Link LED is on with valid downlink frames, including synchronization frames.
• FMB-VRX Line LED is on with valid uplink frames, including synchronization frames.
• FMB Video Activity LEDs (on with sync pulse present on each video channel)
• Ethernet LEDs (on with valid link and/or collision)

Moog Inc., Components Group, Halifax Operations
Focal Technologies Corporation
77 Frazee Avenue
Dartmouth, Nova Scotia, Canada B3B 1Z4
Tel: 902-468-2263 • Fax: 902-468-2249
Application Note
This document is the property of Focal Technologies Corporation, and may not be neither copied, reproduced or otherwise dealt with nor its
contents communicated to others except in accordance with written instructions received from Focal Technologies Corporation.
700-0290-00 Rev. 1 Page 4 of 6
CARD DIAGNOSTIC LEDS:
CARD LED STATUS – NORMAL OPERATION CONDITION
Fiber Multiplexer Boards Green LED “Link” indicator between the Console and Remote Modules
Ethernet Cards
Green RJ-45 port LED: ON = valid link, FLASHING = data activity
Yellow RJ-45 port LED: ON = full duplex link, FLASHING = data collisions
Green Panel LED ("T"): ON = data received from backplane (10 Mbps EIB only)
Red Panel LED ("R"): ON = data sent to backplane (10 Mbps EIB only)
AIB-4, DIB-232, DIB-485
Cards
Two LEDs for each channel indicate the presence of a signal transmitted or
received:
Green LED (“T”): ON = data being transmitted out of card front panel
Red LED (“R”): ON = data being received into card front panel
Non-digital i/o cards (e.g. AIB-MS900) or blank sockets force both LEDs on.
Remote Module Data I/O
(903-HD Only)
Two LEDs for each channel indicate the presence of a signal transmitted or
received:
Green LED ("T”): ON = data being transmitted out of i/o box
Red LED (“R”): ON = data being received into i/o box
Red power switch located on the front of the console system indicates presence
of AC power.
Power Supply Green LEDs on PSU front panel indicate corresponding output voltage levels are
OK. Flickering or dim LEDs indicates power problems on the rails.
FMB LINK READY LEDS (FMB FRONT PANEL):
LED STATUS CONDITION POTENTIAL SOLUTION
Both LEDs On Normal operating condition
(Valid uplink/downlink established) OK
LED Flickering Insufficient flux budget Verify optical power budget with VOAT.
One LED On Insufficient optical power or optical
frame mismatch.
Re-establish synchronization. Replace FMB that
has the unlit LED if received optical power is OK.
Check FMB DIP switch settings per Manual.
Both LEDs Off Problem with optics between remote
and console modules Bad connector: clean all optical connections.
Bad fiber: bypass fiber sections with jumpers.

Moog Inc., Components Group, Halifax Operations
Focal Technologies Corporation
77 Frazee Avenue
Dartmouth, Nova Scotia, Canada B3B 1Z4
Tel: 902-468-2263 • Fax: 902-468-2249
Application Note
This document is the property of Focal Technologies Corporation, and may not be neither copied, reproduced or otherwise dealt with nor its
contents communicated to others except in accordance with written instructions received from Focal Technologies Corporation.
700-0290-00 Rev. 1 Page 5 of 6
Model 903 Console showing the location of the “Link Ready” LED.
CARD HANDLING GUIDELINES
• Use ESD protection as appropriate. Ensure unit is powered down when removing or installing cards, as the
system is not “hot swappable”.
• Unscrew both captured front panel screws, but leave a few threads on upper screw to prevent “popping out”.
• Pull on card until backplane connector unmates. Undo the upper screw completely and withdraw the card
slowly, especially if it is an optical card or adjacent to the FMB to avoid snagging fibers.
• Do not subject fibers to excessive bends, even momentarily.
• Ensure any re-mated optical connectors are cleaned immediately prior to remating. (Even clean connectors will
accumulate dirt if left uncovered.)
• Transport cards in ESD safe bags or boxes.
• Ensure AIB plug-in modules are installed with their alignment dots matching the dots on the AIB motherboard.

Moog Inc., Components Group, Halifax Operations
Focal Technologies Corporation
77 Frazee Avenue
Dartmouth, Nova Scotia, Canada B3B 1Z4
Tel: 902-468-2263 • Fax: 902-468-2249
Application Note
This document is the property of Focal Technologies Corporation, and may not be neither copied, reproduced or otherwise dealt with nor its
contents communicated to others except in accordance with written instructions received from Focal Technologies Corporation.
700-0290-00 Rev. 1 Page 6 of 6
GENERAL HANDLING AND FAILURE REPORTING GUIDELINES
• Use a spare card and see if that fixes the problem.
• Verify the problem on other cards or channels, if possible.
• Note card part number and serial number, as well as PO number, if possible.
• Confirm whether the problem appeared during installation or well after successful installation, i.e. did the
problem occur with no changes to a previously working system?
• Log a diagnostics file, if relevant, and email it to Focal. Diagnositcs files include all optical measurements,
temperature, voltage levels, video syncs, and errors detected. Ensure the log file is configured properly per the
software users manual. (The various log fields may be enabled/disabled and the logging frequency may be
changed from the one second default.)
FOCAL SERVICE AND SUPPORT
It is recommended that damaged cards or cards/systems that the fault cannot be found in using the above guide be
returned to Focal.
• Request a RMA # from Focal (Tel: 902-468-2263) and complete a return product form.
• Provide key information, such as a description of the problem, the part number of the board, how long the board
has been in service, any attempted fixes, and the urgency for repair.
• Ensure packaging is secure and ESD safe.
• Typical assessment response is 3 days after receipt of product.
Other manuals for 903
1
Table of contents
Other Moog Multiplexer manuals
Popular Multiplexer manuals by other brands

Comnet
Comnet Value FVR81 Series Installation and operation manual

ConLAB
ConLAB RTM-8 Operation and calibration manual
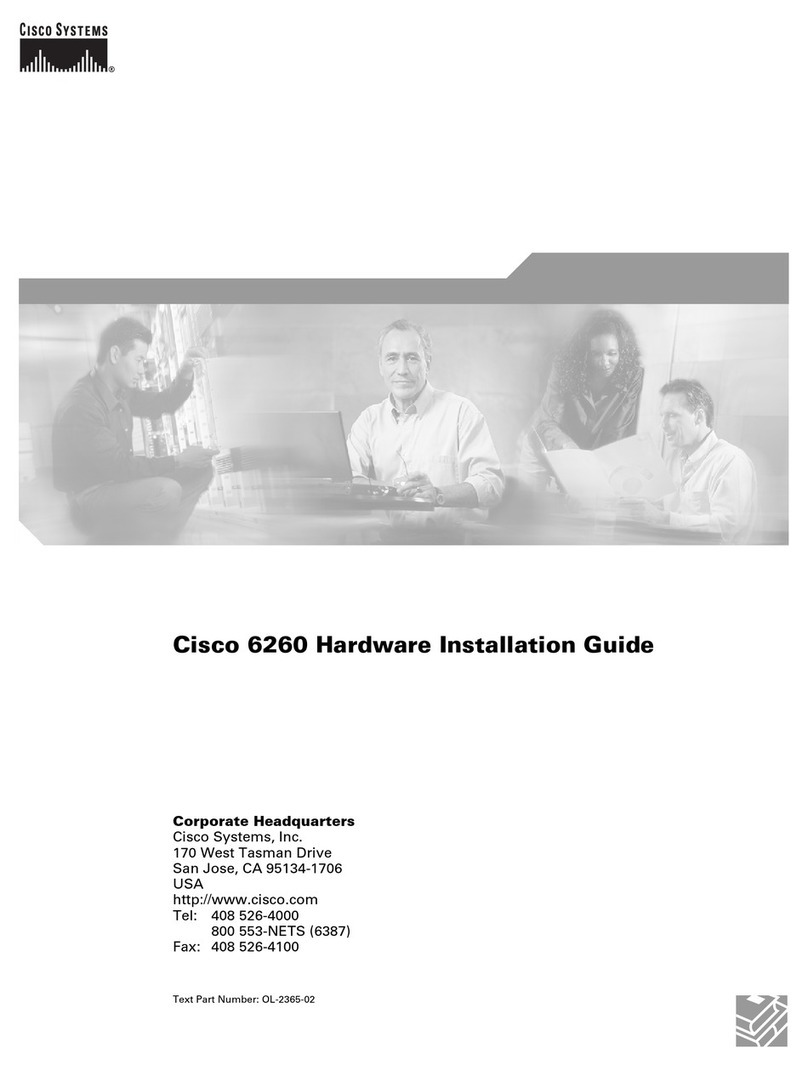
Cisco
Cisco 6260 installation guide
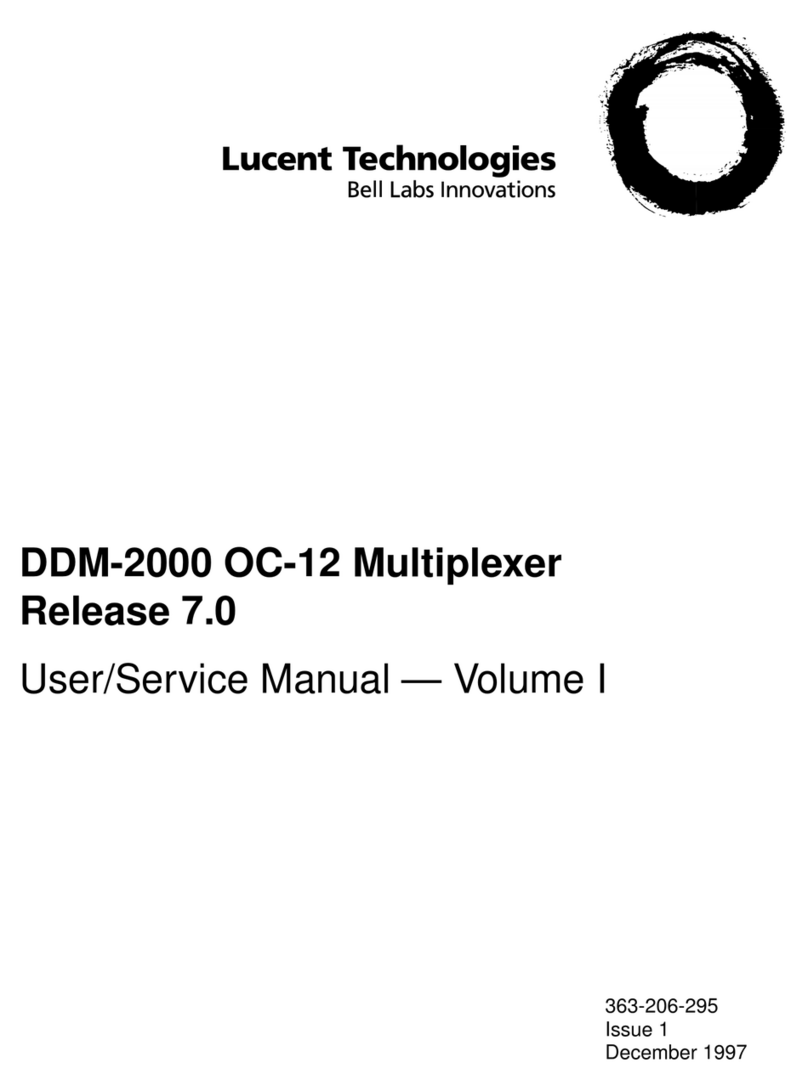
Lucent Technologies
Lucent Technologies DDM-2000 OC-12 User & service manual
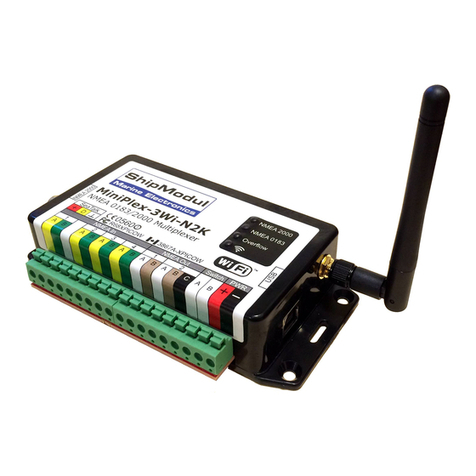
ShipModul
ShipModul MiniPlex-3 Series Firmware Guide
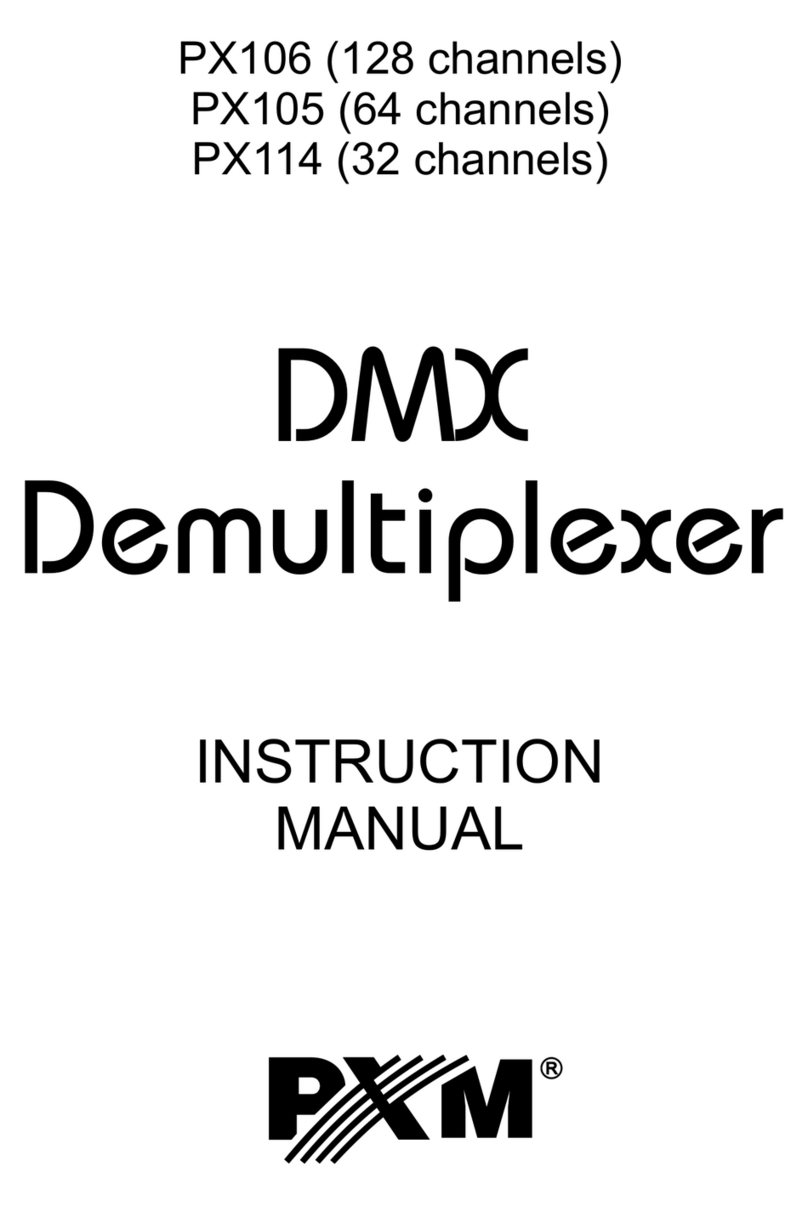
PXM
PXM PX106 instruction manual