Mouvex Typhon II User guide

OPERATION
MAINTENANCE
SAFETY
TYPHON II
SCREW COMPRESSORS
INSTRUCTIONS 1401-G00 e
Section 1401
Effective October 2018
Replaces February 2016
Original instructions
This Instructions only contains bare shaft machine information.
It is imperative to have in complement the accessories instructions, also the parts list before
installing the equipment.
Your distributor :
Z.I. La Plaine des Isles - F 89000 AUXERRE - FRANCE
Tel. : +33 (0)3.86.49.86.30 - Fax : +33 (0)3.86.49.87.17
WARRANTY :
TYPHON II screw compressors are covered 24 months by warranty within the limits mentioned in our General Sales Conditions. The use of
the BSC3 oil carries our warranty from 24 to 36 months. In case of a use other than that mentioned in the Instructions manual, and without
preliminary agreement of MOUVEX, warranty will be canceled.
20R/30R 13R/15L - 19R22L 20R/30R SAE4

2/16
NT 1401-G00 10 18 TYPHON II e
MOUVEX TRUCK SCREW COMPRESSOR
SAFETY, OPERATION AND MAINTENANCE INSTRUCTIONS
MODEL : TYPHON II
REMARKS :
MOUVEX truck screw-type compressors MUST be installed in sys-
tems designed by qualified personnel. The installation MUST be in
compliance with local standards, national regulations and rules of
safety.
This manual is designed to permit installation and commis-
sioning of MOUVEX truck screw-type compressors and MUST
accompany the compressor.
Maintenance of MOUVEX screw-type compressors must ONLY be
carried out by qualified technicians. This maintenance must meet
local and national standards as well as all safety regulations.
Read this manual, including all instructions and warnings, in
full BEFORE any use of MOUVEX compressors.
Do not remove the warning and use label stickers that are
found on the compressors.
1. OVERALL DIMENSIONS . . . . . . . . . . . . . . . . . . . . . . . . . .4
2. GENERAL DATA . . . . . . . . . . . . . . . . . . . . . . . . . . . . . . . .7
2.1 Principle of operation . . . . . . . . . . . . . . . . . . . . . . . . . .7
2.2 Technical characteristics . . . . . . . . . . . . . . . . . . . . . . . .8
2.3 Operating ranges . . . . . . . . . . . . . . . . . . . . . . . . . . . . .8
3. MULTIPLIER 13R/15L - 19R/22L . . . . . . . . . . . . . . . . . . .11
3.1 Cross-section . . . . . . . . . . . . . . . . . . . . . . . . . . . . . . .11
3.2 Multiplier mounting . . . . . . . . . . . . . . . . . . . . . . . . . . .12
4. USE OF COMPRESSOR . . . . . . . . . . . . . . . . . . . . . . . . . .14
4.1 Lubricant recommendations . . . . . . . . . . . . . . . . . . . .14
4.2 Filling of lubricant . . . . . . . . . . . . . . . . . . . . . . . . . . . .14
4.3 Operation . . . . . . . . . . . . . . . . . . . . . . . . . . . . . . . . . .15
4.4 Starting-up . . . . . . . . . . . . . . . . . . . . . . . . . . . . . . . . .15
5. MAINTENANCE . . . . . . . . . . . . . . . . . . . . . . . . . . . . . . . .16
5.1 Maintenance schedules . . . . . . . . . . . . . . . . . . . . . . .16
5.2 Compressor oil change procedure . . . . . . . . . . . . . . .16
5.3 Troubleshooting . . . . . . . . . . . . . . . . . . . . . . . . . . . . .16
TABLE OF CONTENTS Page
ADDITIONAL DOCUMENTATION
The table below gives the list of instructions in addition
to this central instruction :
TYPHON II
application Instructions Spare parts
list
20R/30R - SAE NT 1401-Q00 PL 1401-Q02
13R/15L - 19R/22L NT 1401-Q00 PL 1401-Q01
DDIC - DDNC NT 1401-R00 PL 1401-R01
LS DDNC NT 1401-W00 PL 1401-W01
Torque limiter NT 1401-B00 PL 1401-Q01
Check and relief valve NT 1401-E00 PL 1401-Q01
Oil cooler NT 1401-AC00 PL 1401-Q01
Definition of safety symbols
This is a SAFETY ALERT SYMBOL.
When you see this symbol on the product, or in the manual,
look for one of the following signal words and be alert to the
potential for personal injury, death or major property damage.
Warns of hazards that WILL cause serious personal injury,
death or major property damage.
Warns of hazards that CAN cause serious personal injury,
death or major property damage.
Warns of hazards that CAN cause personal injury or property
damage.
NOTICE
Indicates special instructions which are very important and
must be followed.
DANGER
WARNING
CAUTION

3/16
NT 1401-G00 10 18 TYPHON II e
SAFETY CHECK LIST
1. Before operating the compressor, ensure the vessel to which the
compressor is connected is certified to withstand the pressure and
/or vacuum produced.
2. Verify adequately sized relief valves have been fitted to protect the
vessel. Do not use solvents or inflammable products for cleaning
the pipelines and the accessories.
3. Gas/air mixtures which are potentially volatile/explosive must not be
introduced or allowed to be introduced into the compressor.
4. All pressure vessel and piping connected to the compressor must
be isolated and in a safe operating condition.
5. Operators should wear ear protection when operating truck mount-
ed compressors.
6. There are components within the compressor of sufficient weight
to cause injury if mishandled. Use proper lifting devices as neces-
sary.
7. Where necessary, this equipment should be grounded to control
static electricity.
8. The temperature of the air leaving the compressor is elevated
above ambient due to air compression. Check that the elevated
temperatures do not adversely affect the product and any material
used in design of the system. Attach clearly marked warning signs
to warn of potentially hot surfaces on the compressor, piping and
accessories which will burn if touched.
9. Mounting of the compressor must be correctly engineered and the
compressor must be properly secured. Refer to the Compressor
Mounting section of this manual.
NOTICE :
MOUVEX COMPRESSORS ARE DESIGNED TO PRODUCE COM-
PRESSED AIR. NOT TO PUMP GASES, LIQUIDS, POWDERS OR
CONDENSATES THOUGH THE COMPRESSOR. TO DO SO WOULD
VOID THE WARRANTY.
LIFTING POINTS :
The compressor can be picked up from underneath to be
transported.
Discharge flanges threads can be used to install a lifting lug
in order to transport the compressor.
WARNING
IT IS IMPERATIVE TO APPLY THE
TRUCK PARKING BRAKE AND TO
BLOCK THE WHEELS BEFORE ANY
INTERVENTION DUE TO RISKS OF
SERIOUS BODILY INJURIES OR PRO-
PERTY DAMAGE.
Hazardous machinery
can cause severe
personal injury or
property damage.
WARNING
CONTENTS OF THE COMPRESSOR,
TANK, PIPING, AND FILTERS COULD
BE HAZARDOUS TO HEALTH.
TAKE ALL NECESSARY PRECAUTIONS
WHEN PERFORMING COMPRESSOR
SERVICE OR MAINTENANCE.
Hazardous or toxic
fluids can cause
serious injury.
CAUTION
COMPRESSOR, PIPING AND ACCES-
SORIES WILL BECOME HOT DURING
OPERATION AND CAN CAUSE SERIOUS
PERSONAL INJURY.
Extreme heat can
cause injury or
property damage.
WARNING
COMPRESSING GASES INTO A VES-
SEL CONTAINING FLAMMABLE OR
EXPLOSIVE GASES OR COMPRESSING
FLAMMABLE OR EXPLOSIVE GASES,
CAN CAUSE PROPERTY DAMAGE,
PERSONAL INJURY OR DEATH.
Hazardous fluids
can cause fire,
serious personal injury
or property damage.
WARNING
FAILURE TO INSTALL ADEQUATELY
SIZED PRESSURE RELIEF VALVE(S)
CAN CAUSE PROPERTY DAMAGE,
PERSONAL INJURY OR DEATH.
Hazardous pressure
can cause
personal injury
or property damage.
WARNING
THE NOISE EMITTED BY WORKING
MOUVEX SCREW COMPRESSOR
CAN BE HIGHER THAN 80 DBA.
THE END USERS MUST USE, WHEN
NECESSARY THE APPROPRIATE
EAR PROTECTIONS. FAILURE TO
WEAR HEAR PROTECTIONS IN
AREAS WHERE THE NOISE IS
HIGHER THAN 80 DBA CAN LEAD TO
PERMANENT BODY DAMAGE.
A loud noise can
cause permanent
body damage.
SAFETY DATA

4/16
NT 1401-G00 10 18 TYPHON II e
20R - 30R
1. OVERALL DIMENSIONS
AJauge d’huile / Oil gauge
BFiltre à huile / Oil filter
CVidange / Draining cap
DContrôle pression refoulement G1/4”
Outlet pressure control G1/4”
EContrôle T° refoulement G1/4”
Outlet T° control G1/4”
FPlaque signalétique / Identification plate
GPrise pression huile / Oil pressure plug
HBouchon 3/4 (pour montage jauge d’huile à droite)
3/4 cap (for right oil gauge installation)
JPrise vitesse G1/4” / Speed control G1/4”
KContrôle pression aspiration G1/4”
Inlet pressure control G1/4”
LContrôle T° aspiration G1/4” / Inlet T° control G1/4”
MBouchon magnétique G3/8” / Magnetic plug G3/8”
20R
30R
Poids / Weight : 143 kg

5/16
NT 1401-G00 10 18 TYPHON II e
1. OVERALL DIMENSIONS (continued)
13R/15L - 19R/22L
13R
19R
15L
22L
Poids / Weight : 173 kg
AJauge d’huile / Oil gauge
BFiltre à huile / Oil filter
CVidange / Draining cap
DContrôle pression refoulement G1/4”
Outlet pressure control G1/4”
EContrôle T° refoulement G1/4”
Outlet T° control G1/4”
FPlaque signalétique / Identification plate
GPrise pression huile / Oil pressure plug
HBouchon 3/4 (pour montage jauge d’huile à droite)
3/4 cap (for right oil gauge installation)
JPrise vitesse G1/4” / Speed control G1/4”
KContrôle pression aspiration G1/4”
Inlet pressure control G1/4”
LContrôle T° aspiration G1/4” / Inlet T° control G1/4”
MBouchon magnétique G3/8” / Magnetic plug G3/8”

6/16
NT 1401-G00 10 18 TYPHON II e
1. OVERALL DIMENSIONS (continued)
20R/30R SAE4
20R
30R
Poids / Weight : 158 kg
AJauge d’huile / Oil gauge
BFiltre à huile / Oil filter
CVidange / Draining cap
DContrôle pression refoulement G1/4”
Outlet pressure control G1/4”
EContrôle T° refoulement G1/4”
Outlet T° control G1/4”
FPlaque signalétique / Identification plate
GPrise pression huile / Oil pressure plug
HBouchon 3/4 (pour montage jauge d’huile à droite)
3/4 cap (for right oil gauge installation)
JPrise vitesse G1/4” / Speed control G1/4”
KContrôle pression aspiration G1/4”
Inlet pressure control G1/4”
LContrôle T° aspiration G1/4” / Inlet T° control G1/4”
MBouchon magnétique G3/8” / Magnetic plug G3/8”

7/16
NT 1401-G00 10 18 TYPHON II e
2. GENERAL DATA
2.1 Principle of operation
The male screw and the female screw mesh and rotate
in opposite directions inside the casing fitted with inlet
and discharge ports.
Rotation generates a volume increase on the inner face
between threads and grooves, which corresponds to
inlet, and a volume reduction on the upper face, which
corresponds to compression.
On the discharge port side, a set of gears synchronizes
the male screw and the female screw. Thus, the screws
are not in contact. The discharged air does not enter in
contact with any friction part and remains clean and free
from particles.
On the drive shaft side, the female screw is driven by a
set of step-up gears.
An oil pump delivers pressurized oil which circulates,
lubricating gears and ball bearings.
Sealing is provided between lubricated parts and the
compression stage by means of labyrinth seals. These
seals do not enter in contact with the shaft and are not
subject to wear.
Thanks to their technology, TYPHON II compressors are
reliable and have a long service life.
TYPHON II compressors need very limited maintenance,
which reduce vehicle downtime.
TYPHON II version 20R, 13R/15L and 19R/22L drive
speed were defined so as to drive it directly through uni-
versal joints from a P.T.O. shaft. TYPHON II compressor
is therefore fitted within the chassis. Thanks to this sys-
tem, the installation is lighter and saves space on the
side of the vehicle for other accessories.
TYPHON II version 30R can be directly driven by an
electric or hydraulic motor, and can be driven by a diesel
motor.
The 20R and 30R versions may be fitted with a SAE4
flange so that they can be mounted on diesel engines.
Our packages are delivered without oil. The use of a
compressor with an oil level that is not located
between the two limits indicated by the gauge can lead
to important property damage and serious injuries.
CAUTION

8/16
NT 1401-G00 10 18 TYPHON II e
2. GENERAL DATA (continued)
0
10
20
30
40
50
60
70
80
0
200
400
600
800
1000
1200
-1-0,500,511,522,5
PUISSANCE/(POWER) kW
DEBIT ASPIRE/(SUCTION FLOW RATE) m3/h
PRESSION REFOULEMENT /(EXHAUST PRESSURE) bar
PRESSION ASPIRATION/(INTAKE PRESSURE) bar
Aspiration/(Suction) : 1 atm , 20°C Mesure débit selon/(Flow measurement) : ISO 5167-2
Characteristics of bare shaft end compressor and direct drive package :
2.2 Technical characteristics
The operating characteristics are given in the indicative
operation conditions : ambient temperature and air inlet
temperature 20°C, atmospheric pressure : 1013 mbars.
2.3 Operating ranges
The operating ranges specified in the § TECHNICAL CHA-
RACTERISTICS give the conditions that must be respected
on mounting and packaging of the TYPHON II compres-
sors, in order to be able to benefit from the guarantees
for these pieces of equipment.
The use of compressors outside of their operating
speed range can lead to property damage or serious
injuries.
TYPHON II 1 2 3 4 5
Speed (rpm) :
13R 780 910 1040 1170 1300
15L 900 1050 1200 1350 1500
19R 1170 1365 1560 1755 1950
20R 1200 1400 1600 1800 2000
22L 1320 1580 1800 2035 2250
30R 1800 2100 2400 2700 3000
Maximum discharge
pressure
(inlet suction air
at 20°C)
2 2,3 2,5 2,5 2,5
CAUTION

9/16
NT 1401-G00 10 18 TYPHON II e
2. GENERAL DATA (continued)
2.3.1 CONDITIONS AT SUCTION
In all cases of use, the compressor inlet suction air must
be filtered in order to eliminate particles bigger than 5 µm.
Compressor functionning under pressure :
The maximum pressure drop at suction must be lower
than 75 mbar.
A clogging indicator device turns red when the filter
needs to be changed.
Vaccum operation (SP version only) :
The maximum vacuum authorised for the intake of the
compressor is -8 bar, since the exhaust is into the
atmosphere. Pressure less than 0,3 bar at the discharge
of the compressor A vacuum breaker must be installed
on the suction circuit in order not to exceed -0,8 bar at
the compressor inlet flange.
The clogging indicator is red during the closed intake
operation. This is normal : after a vaccum operation, the
clogging indicator must be released so it becomes trans-
parent again.
REMINDER :
THE CLOGGING INDICATOR MUST NOT BE RED WHEN
THE COMPRESSOR IS IN PRESSURE OPERATION.
When the compressor is used in vaccum operation,
the temperature of the air that escapes from the
exhaust to the atmosphere may be more than 200°C.
Make sure that the flow of hot air does not cause any
damage to the surrounding elements. If necessary,
provide for protections that prevent operators from
touching the hot parts.
The maximum acceptable temperature at suction as a
function of equipment operating conditions is given in
the § TECHNICAL CHARACTERISTICS.
2.3.2 CONDITIONS AT DISCHARGE
The TYPHON II compressor must be protected by a valve
that protects the compressor against accidental over-
pressure.
See Instructions 1401-E00 MISTRAL B600 TYPHON II
CHECK AND RELIEF VALVE.
Maximum acceptable discharge pressure : see §
TECHNICAL CHARACTERISTICS.
The pressures correspond to the valve opening start
pressure. In a period of 60 seconds, it is acceptable to
have a pressure of 0,2 bar higher when the valve passes
the complete flow rate.
CAUTION
Speed (rpm) :
TYPHON II N-20R 1200 1600 1600 2000
TYPHON II N-30R 1800 2400 2400 3000
TYPHON II N-19R/22L,
driving by shaft 22L 1320 1800 1800 2250
TYPHON II N-19R/22L,
driving by shaft 19R 1170 1560 1560 1950
TYPHON II N-13R/15L,
driving by shaft 15L 900 1200 1200 1500
TYPHON II N-13R/15L,
driving by shaft 13R 780 1040 1040 1300
Discharge pressure
of compressor (bar) 2,0 2,0 2,5 2,5
Maximum inlet temperature
allowable at this pressure (°C) 40 40 40 40

10/16
NT 1401-G00 10 18 TYPHON II e
2.3.3 RECOMMENDED DRIVE CONDITIONS
Our screw compressors can be the object of various
modes of driving, it is however necessary to take care of
the adapted protection systems. Thank you to respect
the following recommendations imperatively.
Operating torque at full speed (Nm)
The transmission lines (universal joint, pulley belt, etc.)
must be sized so as to be able to accept the loads above
and also the starting torque and protected by an appro-
priated system.
It is imperative that the drive shafts be dynamically
balanced.
The non balancing of the drive shafts can lead to
mechanical ruptures that are susceptible of causing
important property damage and/or serious injuries.
The shafts of the motors driving the TYPHON II com-
pressors must be aligned within one angle degree on the
TYPHON II shaft. In the case universal joint drive, the
motor and compressor side shafts must be parallel with-
in one degree. The universal joint plates must be parallel
within one degree. Specific installation conditions : See
Instructions 1401-Q00 DDK BARE SHAFT END FOR TRUCK
INSTALLATION - § PTO SHAFT DRIVE.
Not following the alignment instructions can lead to
mechanical ruptures that may create major property
damage and/or serious injuries.
2.3.4 ACCEPTABLE OIL PRESSURE RANGE
The oil pressure is measured at the tap point located on the
synchromesh gear box (item G on the outline drawings) :
In operation, the surface temperature of a compressor
and parts close to him may reach high temperatures
liable to cause significant burns and inflammation of
materials.
Having the compressor run above its maximal tempe-
rature may lead to serious body injuries or property
damages.
TYPHON II Mini pressure
(bar)
Maxi pressure
(bar)
20R 0,5 3
30R 0,5 4
13R 15L 0,5 3
19R 22L 0,5 4
CAUTION
CAUTION
CAUTION
TYPHON II Pressure (bar)
1,5 2,0 2,5
13R 370 430 510
15L 320 380 440
19R 250 300 350
20R 240 280 330
22L 220 260 300
30R 160 190 220
2. GENERAL DATA (continued)
Recommendations
(1) Type STROMAG PERIFLEX VN must be defined case by case according to the power to transmit, the speed and type of engine.
This device allows to filter the vibrations of the engine which in the long term can generates the rupture of the small pinion shaft
of the compressor.
Driving mode Torque
limiter
Specific rubber
coupling (1) Comments
PTO + Cardan Yes No
Electric motor, direct No No Starting up Star / Triangle
Diesel engine, direct Yes Yes With or without clutch
Pulley/notched belts (synchronous) Yes No
Pulley/not notched belts (asynchronous) No No

11/16
NT 1401-G00 10 18 TYPHON II e
3. MULTIPLIER 13R/15L - 19R/22L
Front view of compressor
3.1 Cross-section

12/16
NT 1401-G00 10 18 TYPHON II e
3.2 Multiplier mounting
Bold references return to marker numbers cross-sections
at the end of the assembly procedure.
Belt pulley packages may not use a multiplier.
To mount a multiplier :
* 13R/15L on a compressor N20R or
* 19R/22L on a compressor N30R,
the following sequence of operations must be respected :
• When the multiplier and the group made up of the
shaft809 with its gears 810 and 811 and inner bearing
rings 808 are delivered separately from the compres-
sor, the screws 830, 835, 836 and 837, the washers
838, the washers 827 and 834, cover 830+832, lipseal
822, the fan and its screw819, as well as the group
made up of the inner ring of the 2 bearings 808, gears
811 and 810 and shaft 809 are delivered packaged
separately. Remove the key 46 and the spacer 831
from the from the drive shaft before starting to assemble.
• Prepare the compressor N20R or N30R from MOUVEX :
- Drain the compressor oil.
- Install the compressor as shown in the photo below,
its body sloping at least 30°.
- If necessary, remove the torque limiter.
- Remove the key 46.
- Remove the screws 50 and the washers 50 A hol-
ding the lid in place 3.
- Remove the lid 3and the seal 59. The shaft will be
held in place as the compressor slopes. If necessa-
ry, use 2 screws M10 to extract the lid.
- Remove from a block the shaft 27, ring 53, circlips 63,
gear 7, a complete roller bearing 68, the inner ring of
the second roller bearing 68. If necessary, use the
tappings M8 found top right and bottom left of the lid
to extract the lid.
- Scrape the Loctite®510* remaining on the joint sur-
face on the compressor side 1.
- Check that the seal 32 is in place on the compressor
body. If necessary, hold it in place using a little grease.
The multiplier may be handled using a lifting ring in the
thread M10 in the multiplier.
• Mount the multiplier on the compressor :
- Mount the headless screw 839.
- To mount the shaft, in particular in the oil pump,
align the oil pump drive recess on the high vertical.
- Firstly, mount in the compressor the group made up
of the shaft 809 fitted with its gears 810 and 811 and
the inner bearing rings 808. Make sure you engage
the shaft pin in the recess of the oil pump 809.
Engage at the end the inner bearing cage 808, screwed
to the shaft, in the bearing 808 inside the compressor.
- Push the outer cage and the roller of the bearing 808
still in the multiplier to the end.
Headless screw 839
mounted
with Loctite®510*
Be careful to the seal 32
(keep it in place)
WARNING
3. MULTIPLIER 13R/15L - 19R/22L (continued)
* Loctite®is a registered trademark.

- Coat the surface for contact between the body and
the multiplier with Loctite®510*.
- Grease the lip joint 822.
- Centre the shaft 809 in the bearing 808 and engage
the lip joint 822, and, in the same movement, engage
the centring between the compressor and the multi-
plier.
- Place Loctite®243* on the short screws 836 and
washers 838 keeping the body of the multiplier in
place 801. Screw at torque 24 Nm + 10%. Start
screwing with the 2 opposite screws, screwed gra-
dually, ckecking that the multiplier drive shafts can
rotate freely.
- Place Loctite®243* on the screws 837 and washers
838 keeping the body of the multiplier in place 801.
Screw at torque 24 Nm + 10%. Check that the multi-
plier drive shafts rotate freely.
- Place Loctite®243* on the screws 835 and rings BS
834 keeping the lid in place 3. Screw at torque 24 Nm
+ 10%.
- Unscrew the screw holding the fan in place 819. Inject
a drop of Loctite®243*. Replace the screw.
- Mount the fan 819 and screw up the relevant screw
to screw it to the shaft 809. NB the fan wings can cut ;
use suitable protection. Wipe off the excess Loctite®*.
- On the cover 820, check the presence of spacers 826
in the sleeves 827.
- If necessary, depending on the drive shaft, change
the shaft position protector 832.
- Put the cover 820 in place.
- Place Loctite®243* on the screws 830 through the
sleeve 827 and the spacer 826 to hold the cover 820
in place. Screw at torque 24 Nm + 10%.
• Engage the spacer 831 on the multiplier drive shaft.
• Mount the key.
• If necessary, replace the torque limiter.
Tightening screw
delivered with the fan
Short
Loctite®510*
13/16
NT 1401-G00 10 18 TYPHON II e
* Loctite®is a registered trademark.
3. MULTIPLIER 13R/15L - 19R/22L (continued)

14/16
NT 1401-G00 10 18 TYPHON II e
The operator should remain nearby the equipment throughout
the use to ensure the proper functioning of the system.
4.1 Lubricant recommendations
MOUVEX BSC3 oil is recommended for 20R and 30R
configuration, whereas it is imperative for 13R/15L and
19R/22L.
A start up oil change has to be made after one week or
10 working hours. Not performing this oil change will void
the warranty.
For the first week or 10 working hours, you can choose
a standard mineral oil.The standard mineral oil grade will
be selected according to the ambient temperature under
which the compressor will be operated :
- Below -10°C. . . . . . . . . . . . . . SAE 10 W 40
- Between -10°C and 30°C . . . SAE 15 W 40
- Above 30°C . . . . . . . . . . . . . . SAE 15 W 50
With BSC3 oil, oil change is recommended every year or
600 working hours that the compressor is equipped with
or without a multiplier.
In case of operations done under minus 25°C, BSC3 oil
viscosity sharply increases and can generate starting
troubles. It will be necessary, in that case, to preheat the
compressor body.
It is also allowed to use oil SAE 5W40 temporarily allowing
to tolerate -35°C.
That implies the following constraints :
• Oil must be replaced every 100 operating hours.
• Imperative return to the BSC3 when the temperature
becomes again positive.
Oils BSC and SAE are miscible; the passage of the one
with the other thus does not imply particular procedure of
cleaning.
Compressors can be used with an external oil cooler in
case of intensive applications (see Instructions 1401-AC00
OIL COOLER SCREW COMPRESSORS MISTRAL B600
TYPHON II).
4.2 Filling of lubricant
Our packages are delivered without oil. The use of a
compressor with an oil level that is not located
between the two limits indicated by the gauge can lead
to important property damage and serious injuries.
The quantity of oil for each compressor is approximately :
• TYPHON II 20R - 30R . . . . . . . . . 6 l
• TYPHON II 13R/15L . . . . . . . . . . 7l
• TYPHON II 19R/22L . . . . . . . . . . 7l
Before starting the system, fill the casing with oil so that
the oil level is set between the min and max value of the
gauge.
NB : A residual volume of 0,5 l of oil may be present inside
the compressor when it leaves the factory.
After filling, the level must under no circumstances
exceed the maximum marker on the oil gauge (the level
is taken after the gauge has been completely screwed
onto the filling tube).
Max level
Min. level
CAUTION
CAUTION
4. USE OF COMPRESSOR

15/16
NT 1401-G00 10 18 TYPHON II e
4.3 Operation
• The compressor must be started with the discharge
valves open.
• When it is started for the first time, check the com-
pressor rotation direction. Also check rotation speed
(refer to § TECHNICAL CHARACTERISTICS).
• The compressor shall be stopped without any coun-
terpressure at discharge.
• At the first start, check that the combinations of rotation
speed and discharge pressure of the compressors
are in conformity with those indicated in § TECHNICAL
CHARACTERISTICS.
Before any equipment startup, it is necessary to
check the coherency between the motor rotation
direction and the compressor operating direction. A
startup with rotation in the wrong direction will lead
to irreversible property damage on the compressors
that is not covered by the guarantee.
During operation, the temperature of the surface of
a compressor and nearby parts can be in the region
of 200°C. The compressor and the parts located
nearby are thus susceptible of provoking serious
burns and property damage. Be careful to not
approach elements that are sensitive to heat and
affix plates informing users that the compressor is
hot, to prevent any risk of burns.
4.4 Starting-up
BEFORE starting compressor, open all air valves neces-
sary to vent the tank and compressor to atmosphere.
Verify there is no possibility of operating at pressure before
compressor reaches correct speed.
Close all valves and proceed to pressurize the tank and
discharge the cargo.
4.4.1 Start-up procedure for manual gear box
• Start the engine and run with standard speed.
• Depress clutch and engage the PTO.
• Release the clutch SLOWLY.
• Set engine speed to give the correct compressor speed.
4.4.2 Shutting down procedure for manual gear
box
• Depress the clutch and disengage the PTO.
• Reduce engine speed to idle.
ALWAYS DISENGAGE THE DRIVE BEFORE SLOWING ENGINE
DOWN.
• Release the clutch.
NOTICE :
COMPRESSOR MUST OPERATE AT FIXED SPEED WITHIN
THECOMPRESSOR MODEL SPEEDLIMITS. SPEED MUST
REMAINCONSTANT THROUGHOUT THE OFF LOADING
OPERATION.
PTO
ON SLOWLY
PTO
OFF
CAUTION
CAUTION
OPEN CLOSE
4. USE OF COMPRESSOR (continued)

16/16
NT 1401-G00 10 18 TYPHON II e
5. MAINTENANCE
5.1 Maintenance schedules
After every cleaning of the truck
Always run the compressor for 15 minutes to remove
any water that inadvertently gets into the piping. DO
NOT fog or introduce anti-corrosive liquids into the com-
pressor to prevent corrosion : Use of liquids in the com-
pressor will cause failure.
After first 10 hours or first week operating
Change the compressor oil and clean the magnetic plugs.
According to the prescriptions of § LUBRICANT RECOM-
MENDATIONS.
Change the compressor oil and clean the magnetic plugs.
Weekly
The compressor should be run for at least 15 minutes to
prevent moisture from collecting inside. This will reduce
the risk of corrosion damage to the compressor and
other equipment in the piping.
Clean the outer surfaces and the compressor cooling
wings, and the multiplier inlet grille. Inspect DAILY if
operating in dirty or severe environment. Check the con-
dition of the inlet filter hose for splits and tears. Replace
or repair as necessary.
Inspect compressor, system piping and components.
Clean or repair as necessary.
Monthly
Check oil level, add the necessary volume if necessary.
Check for cleanliness the breather inside the oil jauge,
clean with an air blower if necessary.
5.2 Compressor oil change procedure
Oil gauge : See § LUBRICANT RECOMMENDATIONS.
Unscrew and remove the oil filter with its seal (marked C
on the outlines drawings). Drip-drain all the oil contained
in the casing.
Carefully clean the oil filter with solvent. Blow out all
impurities with a compressed air blast.
Clean the magnetic plugs (marked M on the outlines
drawings).
After checking that no particles remain in the filter, reins-
tall it making sure that the seal is in good condition. Fill
the compressor. See § FILLING OF LUBRICANT.
5.3 Troubleshooting
See Instructions 1401-Q00 DDK BARE SHAFT END FOR TRUCK
INSTALLATION - § TROUBLESHOOTING.
Seal
Filter
Seal
Seal
Seal
Oil gauge
Magnetic plug Magnetic plug
Blowing direction
CAUTION
THE BLOWING OF OIL GAUGE CAN
CAUSE PERSONNAL INJURY OR PRO-
PERTY DAMMAGE. IT IS MANDATORY
TO CARRY APPROPRIATE PROTEC-
TIONS (GLOVES, GLASSES...) TO AVOID
RISKS OF PERSONNAL INJURY.
Other manuals for Typhon II
1
This manual suits for next models
8
Table of contents
Popular Compressor manuals by other brands
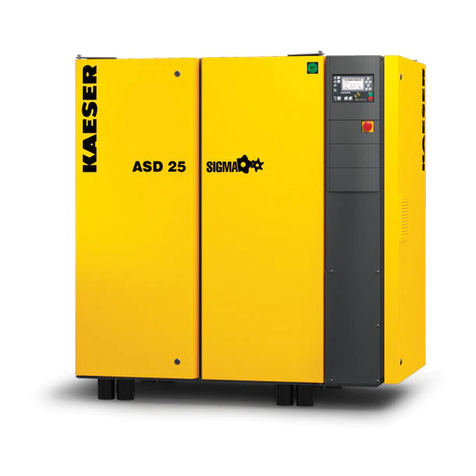
KAESER
KAESER ASD T Series Service manual
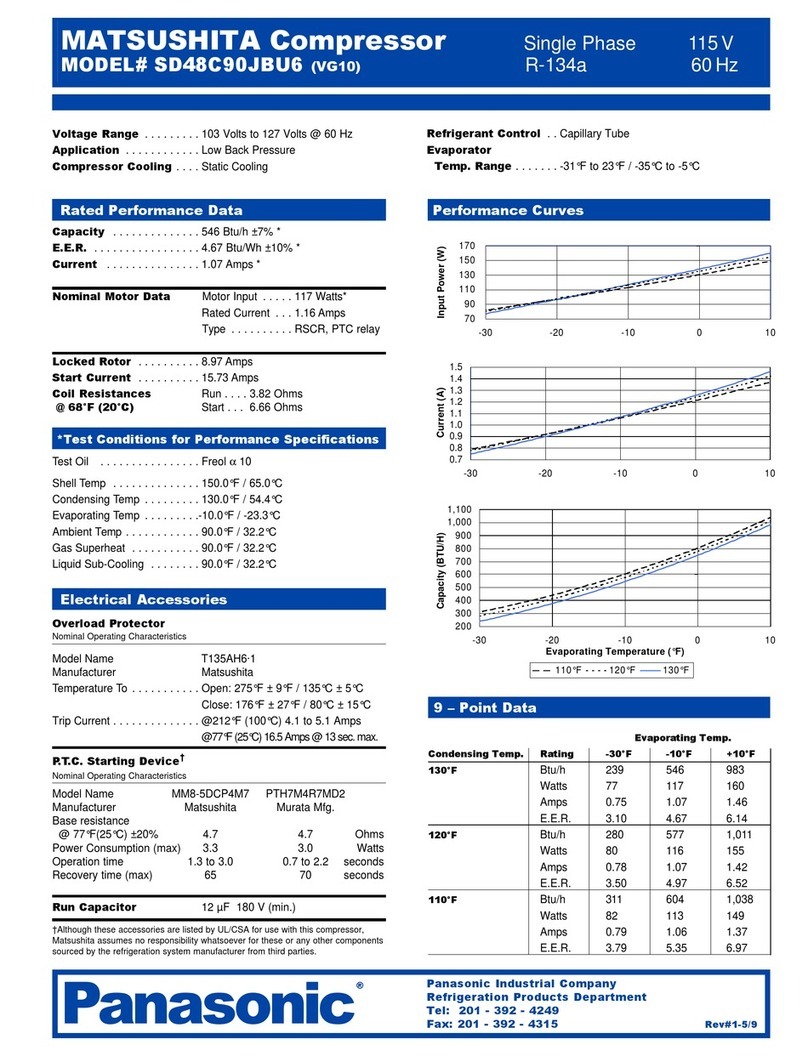
Panasonic
Panasonic Matsushita SD48C90JBU6 Specification sheet
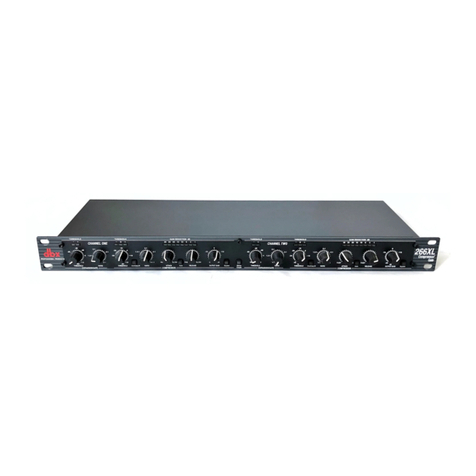
dbx
dbx 266XL Owner's/operator's manual

GreenWorks
GreenWorks 4104107 user manual
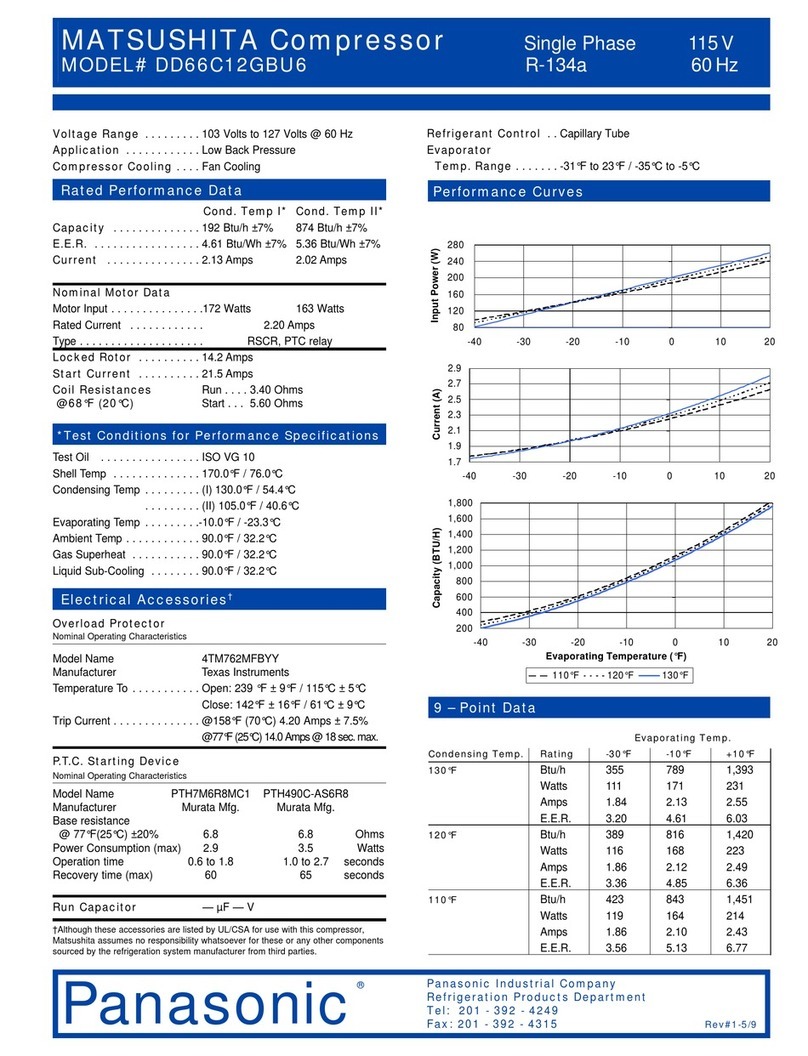
Panasonic
Panasonic Matsushita DD66C12GBU6 Specification sheet
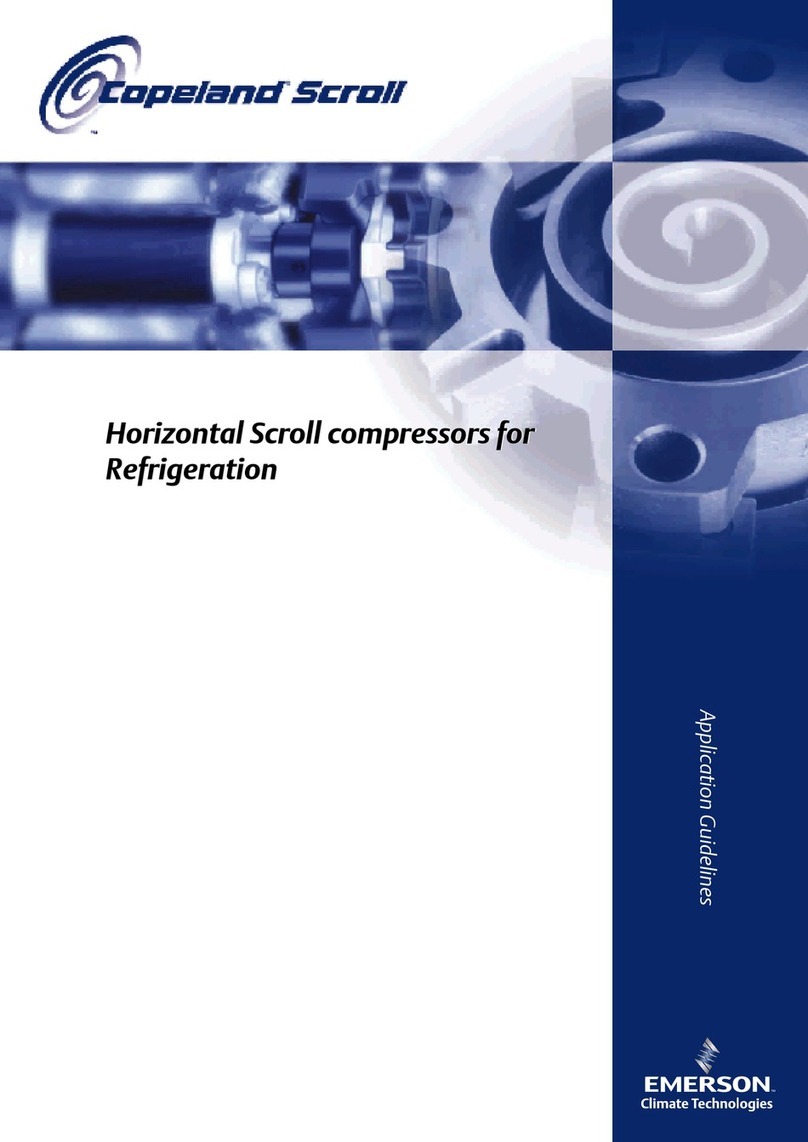
Emerson
Emerson Copeland Scroll Series Application guidelines
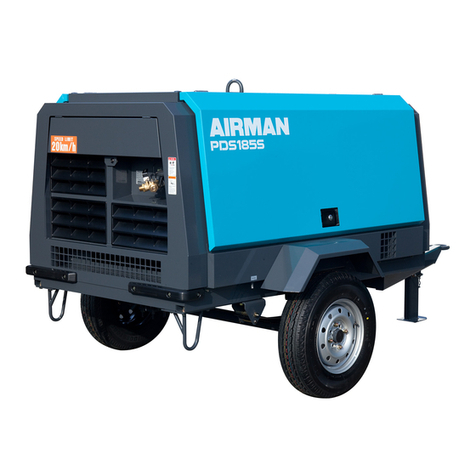
AirMan
AirMan PDS185S-6C2 instruction manual
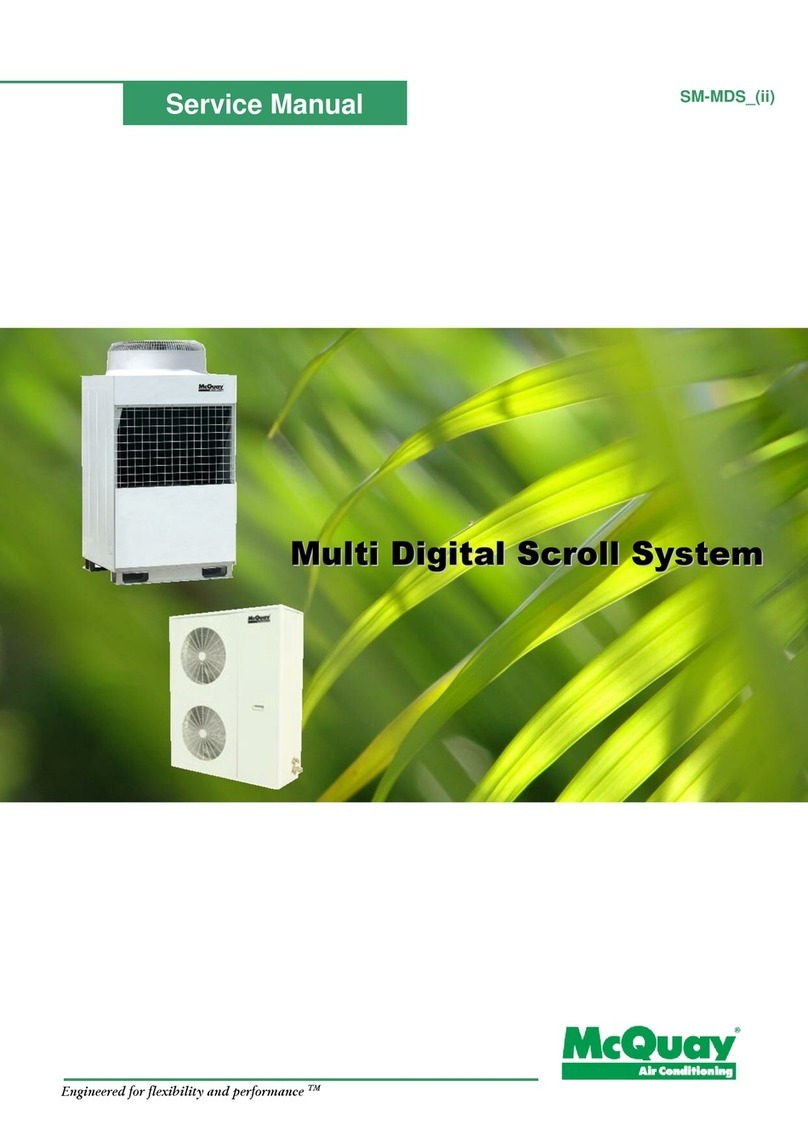
McQuay
McQuay MDS Series Service manual
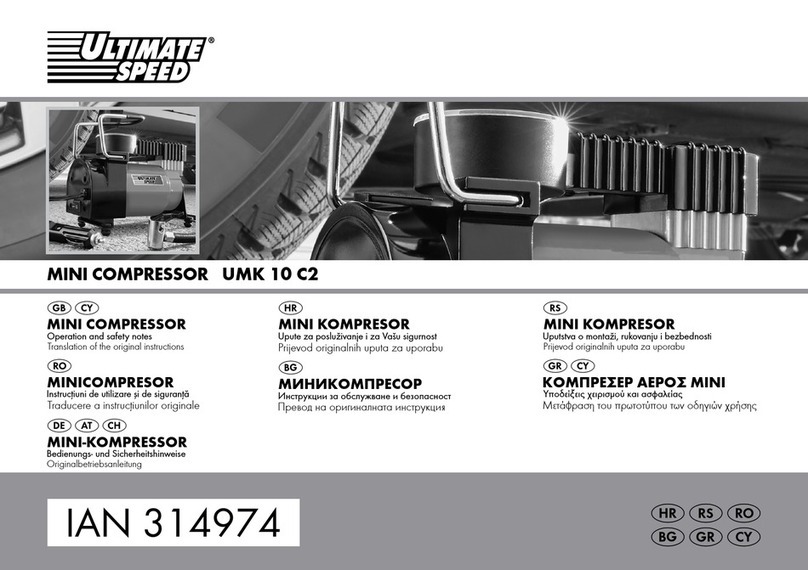
ULTIMATE SPEED
ULTIMATE SPEED UMK 10 C2 Operation and safety notes translation of the original instructions

Scheppach
Scheppach HC 53dc Translation of original instruction manual
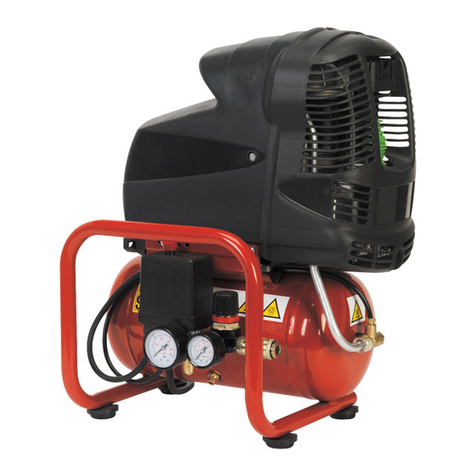
Sealey
Sealey SA0615 instruction manual
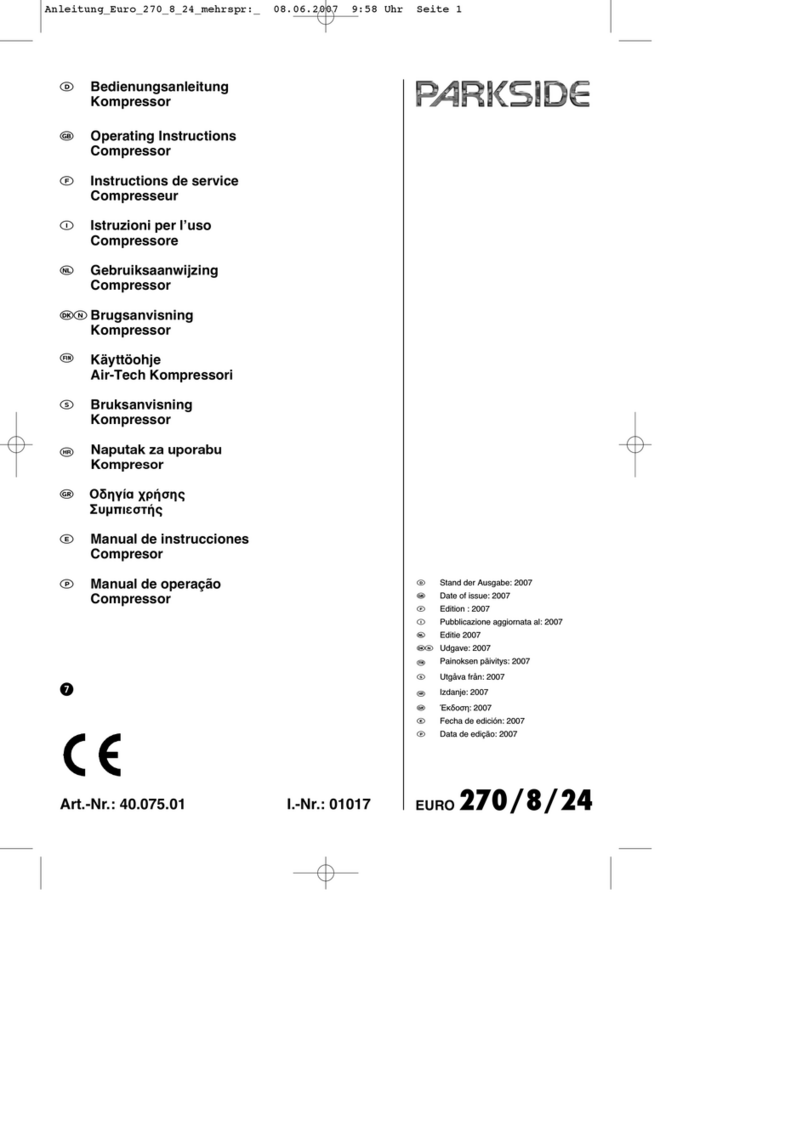
Parkside
Parkside EURO 270/8/24 operating instructions