Mud Buddy HD 23 EFI User manual

HD/HDR
Owner’s Manuel
2020/21
MODELS:
23 EFI | 25 Kohler | 35 CDI | 37 EFI | 40 EFI | 5000 EFI
King of Backwater Motors
www.mudbuddy.com
801-352-8011

Pg. 3………Mounting
Pg. 3………Break In
Pg. 4………Fuel and Storage
Pg. 4………Battery
Pg. 5………Trailering
Pg. 6..…….Oil
Pg. 6………Start Switch
Pg. 7………Starting
Pg. 7………Safety Lanyard
Pg. 8………Shifting
Pg. 9...……Trim Switch
Pg. 9...……Running
Pg. 10.……Handle Bolt Tension
Pg. 10.……Skeg Adjustment
Pg. 11.……Engine & Drive Service
Pg. 12.……Owners Responsibilities
Pg. 13.…...Check Oil
Pg. 14….…Engine RPM
Pg. 15……Owner Service
Pg. 15……Frame Grease
Pg. 16……Drive Greasing
Pg. 16……HDR Transmission Service
Pg. 17……Emissions Control
Pg. 17……Carburetor Adjustments
Pg. 18……How to Adjust Valve Lash
Pg. 19……Belt Tension Adjustment
Pg. 20……Spark Plug Gap
Pg. 20……Inspect Muer
Pg. 20……Change Oil Filter
Pg. 21……Service the Air Filter
Pg. 21……Clean the Air Cooling
System
Pg. 21……Fuel Filter
Pg. 22……Storage – Fuel System
Pg. 24…...Common Replacement
Periods
Pg. 25……Warranties
Pg. 28……Control Box Wiring
Pg. 29……HDR Wire Diagram
Pg. 30……HD Wire Diagram
Pg. 31……HDR 2019 Wire Diagram
Pg. 32……Belt Drive Reverse
Assembly
Pg. 33……Cover Assembly Tall
Reverse
Pg. 34……Handle Assembly
Pg. 35……Clamp Mount Assembly
Pg. 35……Drive Assembly
Pg. 36……Trouble Shooting
Momentary Forward
Bump Switch
Safety Kill Switch
Lanyard -
to be worn at all
times.
Trim Up and Down
HDR – Rear position is reverse gear.
Center position is neutral/start.
Forward position is forward gear.
HD - Center position is neutral/start.
Forward position is forward gear
MUD BUDDY CONTROLS
HD model has forward and neutral.
HDR model has forward, neutral and reverse.
1 2
Table of Contents
Throttle Lever

MOUNTING:
Your motor is shipped with two mounting bolts. Use a
hoist capable of handling 350 pounds to safely lift the
engine from the crate on to the boat.
Align the motor to the center of the boat then mark the
mounting holes and drill using a 3/8” drill bit.
Use silicone to seal the bolt holes. Do not over tighten
the bolts and crush the mount or boat transom.
BREAK IN PROCESS: Very Important
All motors should be broken in over a ve-hour period.
During the rst hour do not run full throttle longer than
two minutes. For the next two hours do not run the
motor at full throttle longer than 15 minutes at a time.
Run the nal two hours by varying the throttle position
every 10 minutes.
Model 5000 requires checking the valve adjustment at ten
hours. This is the owner’s responsibility. (See page 18 for
instructions.)
Change the oil at 10 hours.
FUEL AND STORAGE:
Use Stabil or an equivalent brand fuel additive if you are
storing the engine for more than two weeks.
It is important to use a fuel stabilizer whenever the
engine is not being used for more than two weeks.
There is no warranty on fuel systems and subsequent
damage incurred by improper storage. See page 22-23
for proper motor storage.
For carburetted models, do not use a quick disconnect
fuel hose which can restrict fuel delivery. You can use a
marine primer bulb, however, do not excessively pump
the primer bulb as it can damage the carburetor.
If you are using a front (bow) mounted fuel tank, use a
minimum size 5/16” fuel hose.
Use a minimum of 87 Octane fuel for the 23, 25, 35, 37
and 40 EFI models. The 4400 and 5000 models must use
91 or higher, octane fuel.
BATTERY:
Use a Group 24 or larger battery with at least 550
cranking amps.
If the battery is located in the front of the boat, use
4-gauge battery cable. Your motor is equipped with a 9
foot, 4-gauge wire and 120 amp breaker.
3 4

TRAILERING:
Use over-the-boat strap wrapped around the handle
once, as shown, to tie down the handle so that it does not
bounce while trailering. Failure to follow this advice may
cause damage to the handle, controls and wiring.
Engaging the Travel Lock
The motor is equipped with a travel lock that holds the engine in the
horizontal (up and down) and vertical (left and right position).
To engage, stand on the oil lter side of the engine facing the boat. While
lifting the engine with your left hand, raise the engine upward to line up
the tab on the base plate with the engine mount plate. Push the travel
lock ball inward to lock the engine upward.
You can use the hydraulic trim pump to raise the engine but be careful to
not bend the base plate with excessive lift.
OIL:
Your engine holds approximately 2 quarts of oil. (2.0 qts.
Large Vanguard, 1.83 qts Kohler, 1qt small vanguard)
We ship the engine with oil, however we recommend
checking oil levels before use. Add oil slowly and check
the dipstick with the engine in a level position.
We recommend using a 10W-30 oil or synthetic blend
oil the rst twenty hours during break in. Afterwards we
recommend a synthetic or synthetic blend 10W-30. Use
5W-30 in temperatures lower than 20 degrees to help the
engine start easier.
START SWITCH:
The start key switch is located on the front of the engine.
It has three positions, stop, run and start.
Position 1 - Stop Position 2 - Run Position 3 – Start
(Turn the Key all the way to the
right until engine starts. Key
will return to the run position.)
5 6

STARTING:
Make sure everyone is clear of the propeller. Place the
shift switch in the center neutral position. The engine will
not start with the shift switch in other positions.
For carburetted models, choke the engine during start up
and in cold operating conditions.
The 23 and 35 carburetted models have a choke located
at the front of the engine.
The 4400 BD model choke
is located at the top left
side of the
Mikuni carburetor.
SAFETY LANYARD:
Connect the safety lanyard to your clothing or wrap
around your wrist during operation. The safety lanyard
must be installed properly for the motor to run.
CAUTION – Use the safety lanyard correctly. Failure to do so could
result in injury or death.
SHIFTING:
The HD model has a forward shift position and a center
start position.
The HDR reverse model has a forward gear position, a
center start position and a reverse gear position.
Center – Start/Neutral
Right – Forward
Center – Start/Neutral
Right – ForwardLeft – Reverse
Caution – Ensure the engine is running 1200 RPM or less to ensure
easy shifting, to prevent drive damage and to reduce sudden forward
or reverse motion of the boat which may cause injury or death to the
operator or passengers.
7 8
*Momentary Forward
*Momentary Forward
*Momentary Forward works in neutral position only. Pressing the Momentary Forward
while in reverse, will cause the engine to stop.

TRIM SWITCH:
The trim switch allows you to select the best drive vertical
position. Initially, trim the engine downward to accelerate
and as you pick up speed, trim upward allowing the
propeller to run on the surface for best performance.
Once you set the full speed running height, it is not
necessary to trim the drive downward to stop and take
o.
Left – Down Right - Up
RUNNING:
Take time to learn where all the controls are located on
your Mud Buddy.
IMPORTANT - Place the safety lanyard on your wrist or
clip it to your clothing prior to start.
Start the engine in neutral. Lower the propeller into the
water with the trim control and safely place the motor in
gear. Drive slowly at rst to learn how to steer and
throttle the engine. Trim the drive up and down slowly so
that the propeller is slightly visible above the surface with
a visible water rooster tail.
Rooster Tail
You can lower the drive completely for maximum traction
in mud, ice and thickly vegetated areas. Trim up to clear
logs and rocks.
HANDLE BOLT TENSION:
The handle bolts should be snug, but loose enough to
allow the handle to move up and down. The handle is
designed to oat (freely move up and down) when
driving. If the drive hits a hard object while under power,
the oating handle absorbs the impact, as opposed to
wrenching the handle out of your control.
SKEG ADJUSTMENT:
Depending on the boat design and load, it may be
necessary to adjust the skeg to lessen tiller torque
(excessive push or pull of the handle). However, tiller
torque can also be caused by excessive up or down
position of the drive at full throttle.
The skeg has a small bend closest to the propeller. If
the operator handle is pushing excessively towards you,
increase the bend by adjusting with a large crescent
wrench. Lower the drive and place your knee against the
drive and bend it in small increments. More bend angle
causes the tiller handle to pull away from you. Do not
adjust the skeg with a hammer.
Your motor will run best in
this position. It is not
necessary to trim down
when you stop and resume
travel.
9 10

.
See videos and instructions on the Mud Buddy website at
https://www.mudbuddy.com/resources/tips-and-videos
CAUTION: OWNER’S RESPONSIBILITY
Proper care and maintenance is the responsibility of the
owner. The following items are just some of the actions
an owner should take regularly. Failure to maintain the
drive and engine will result in damage and early part
failure, and can void the product warranty.
- Properly store your engine using fuel stabilizer.
Stale fuel will cause damage to the engine and will result
in dicult starting, poor idle, acceleration and top end
speed. Poor fuel delivery can cause an engine lean
condition and may aect the performance and life of the
engine. (See page 22-23.)
- Always use a fuel stabilizer like Stabil when the
engine is stored for more than two weeks.
- Propeller balance and condition. If a propeller is
worn, damaged or bent, it can vibrate and will cause the
following conditions - Loose bolts, handle vibration,
leaking seals, bearing failure, frame cracking and engine
damage. A unbalanced propeller will cause engine and
frame damage which is not covered by warranty.
- Freezing rain and snow can cause severe
damage to the throttle, trim, shift switch and carburetor.
Store the motor with a cover.
Caution: If you have a frozen cable and thaw it out, the water
in the cable will freeze again during driving and can cause the
throttle to stick open. If the throttle cable freezes, it must be
removed, thawed and pressure lubricated with a silicone based
lubricant to remove the water within the cable. Tape a silicone
pressure can nozzle straw to the end of the cable – spray in
lubricant until the water and lubricant exit the opposite cable
end. Or, remove the cable and soak in WD-40 overnight.
11 12
First 10 Hours
Date Complete _____________
- First Oil Change
*Use 10W-30 regular, synthetic
blend or synthetic oil.
- For performance models (5000):
Check valves, (adjust if
necessary), intake and exhaust
set at .005-.006.
First 20 Hours
Date Complete _____________
- Visually inspect prop.
- Check for loose fuel hose
connection, nuts, bolts and wire
connections.
- Remove clutch cover and visually
inspect transmission and
magnets for excessive wear or
oil leaks.
Every 50 Hours or Annually
Date Complete ____________
- Inspect propeller for wear and
damage.
(Replace immediately if the drive incurs
vibration or if wear exceeds 1/2”).
- Clean or replace air lter.
- Change engine oil and lter.
- Lubricate throttle cable and
throttle lever.
Every 100 hours or Annually
Date Complete ___________
- Replace air lter.
- Replace spark plugs.
- Check for any leaks.
- Grease lower drive tube and
swivel points.
- Check muer and fasteners.
- Clean cooling fans located in
and around the head and
muer area.
- Check valve lash.
- Check engine base bolts and
frame bolts.
- Remove corrosion, touch up
paint, and lubricate wire ends
with silicone spray.
- Replace fuel lter.
- Change oil in the transmission.
- Check belt tension.

- Salt can cause extensive corrosion to the drive and
engine. Ensure the frame is cleaned and lubricated
every time it is run in salt water. Corrosion will cause
nish damage, switch failure, wire shorting, and engine
failure. Remove corrosion on painted surfaces. Matching
paint can be purchased from Backwater Performance
Systems. Use silicone spray protectant on wire
connections.
- Drive seal damage will result in loss of grease level
in the drive and cause bearing damage and early failure.
- Bolts, nuts and other fasteners should be checked
frequently to prevent early drive and engine failure.
- Impacts can cause engine and drive damage. This
includes prop and skeg damage, oil cooler and hose
damage, throttle and kill switch breakage. Severe
impacts can cause carburetor and air lter separation.
Oil Recommendations
We recommend the use of a good quality 10W30 or synthetic blend 5W30 oil
classied for service SF, SG, SH, SJ or higher. Do not use special additives.
CHECK OIL:
Place the engine in a level position for 5 mins. Clean the
oil ll area of any debris. Remove the dipstick and wipe
with a clean cloth. Insert the dipstick fully. Remove the
dipstick and check the oil level. It should be at the top of
the oil level indicator. If low, add oil slowly. Do not
overll. Replace the dipstick.
ENGINE RPM:
The engine idle speed should be set at 1200 RPM or less
to ensure smooth and jolt free shifting. Higher RPMs can
cause damage to the drive and you can lose control of the
engine and cause serious injury or death to the operator
and passengers.
Full throttle engine RPM is set by the propeller size when
run in the water. Use the factory recommended
propellers for your engine size. Normal operating RPM
is from 3800 to 4200 RPM. Carburetted engines are
equipped with a high RPM governor that will cut out the
engine at 4650 RPM. EFI engines ECM’s govern the engine
speed at 4750 RPM. Do not over rev your engine higher
than 4200 when the propeller is out of the water at high
speeds for longer than three minutes – this can cause
excessive heat and damage to the propeller seals and
bearings.
13 14

FRAME GREASING:
Grease swivel assembly ttings annually or every 100
hours with a good quality marine grease available at any
auto parts store. Mercury marine grease is also
acceptable.
Locate and grease the three grease ttings on the
horizontal swivel located under the engine mount and the
single tting on the vertical swivel.
Owner Service: DRIVE GREASING:
Grease annually or every 50 hours with a good quality
marine grease (NLGI 2.5) available at any auto parts store
or on the Excel Boats Online store.
Grease the throttle cable on both ends. Also, spray a wa-
ter resistant silicone spray on the throttle lever. To
prevent cable freezing, remove the cable and soak in WD-
40 for two hours each year.
Locate the drive lubrication zerk screw
located on the drive near the prop.
Remove the pressure release bleed
screw and grease the drive. Grease
until clean grease comes out of the
bleed screw hole. Replace the bleed
screw.
HDR TRANSMISSION SERVICE - EVERY 100 HOURS:
Disconnect the battery cable.
Carefully remove the clutch cover and disconnect the
plug. Locate the two ll/drain screws located on the belt
drive transmission.
Place a shop towel between the belt, below the
transmission to catch oil and any parts that might fall.
Cut a cup in half to catch the oil and drain and replace the
transmission uid with a good quality 10w-30 automotive
grade full synthetic oil.
15 16

Procedure: Remove one of the ll/drain screws
and place it at the 12 o’clock position.
Place the other ll/drain screws at the 6 o-clock
position. Drain the very small amount of oil on to
the shop towel. Replace the drain screw. Using
the Mud Buddy ller syringe, ll the transmission
with 1 1/2 oz. of 10w-30 automotive synthetic
oil. Replace the ller screw. Run the motor and
check for any leaks. Note, if there is excessive oil
on the inside of the transmission cover, locate
and replace the large seal on the transmission
hub.
Reconnect wire and carefully
replace the clutch cover, ensuring
the magnet wires are not pinched
behind the magnets.
EMISSIONS CONTROL:
Maintenance, replacement, or repair of emissions control
devices and systems, may be performed by any engine
repair establishment or qualied individual.
See Emissions Warranty.
CARBURETOR ADJUSTMENT: (Model 35 and 4400BD only)
Never make unauthorized adjustments to the carburetor.
The carburetor was set at the factory to operate
eciently under most conditions. However, if adjustment
is necessary, see a Mud Buddy authorized dealer for
service.
HOW TO ADJUST VALVE LASH (First 10 hours):
Setting Valve Lash or Valve Clearance is important and
should be checked after the rst 10 hours of running, or
earlier if the valves are noisy. (Applies to 4400 & 5000)
If the valve lash is not set to specications, the valves will
not open and close at the correct time, which will cause
power loss and possible head and engine damage. You
will not get the best performance from your motor if the
valve lash is not set correctly. All 4400 & 5000 model valve
lash settings are 0.005 to 0.006 for intake/exhaust.
Other engines are .004 - .006 for intake and .007 - .009 for
exhaust.
Turn the crank shaft/prop counter-clockwise until you
see the valves opening and closing. After the exhaust
valve closes, put your nger over the spark plug hole.
When you feel air coming out (compression stroke) then
turn slowly. Look in the spark plug hole with a ashlight
and turn the shaft until you see the piston rise to its max
point. Turn it just a little bit more till it drops ¼” and then
set the valve clearance (this is ¼” past Top Dead Center -
TDC).
17 18
Disconnect the safety lanyard.
If you disconnect the battery,
you can not engage the clutch.
Set the valves on a cold
engine, remove your valve
covers (10mm wrench), spark
plugs, and engage the clutch
(if you are turning the prop to
turn the crank).

Use a feeler gauge to check/set the clearance. Loosen the
13mm nut on the rocker adjuster on the rocker arm and
use a Torx T40 driver or metric Allen wrench (depending
on your adjuster type) to adjust the clearance. The feeler
gauge should move between the valve and the rocker
arm with resistance. Once the rocker arm clearance is set
at the correct clearance, hold the adjuster and tighten the
13mm nut.
Recheck the clearance to ensure you didn’t move it while
tightening (it may take a few tries to get it right). Repeat
process for remaining valves.
Torque specs: Valve Cover- 70 in. lbs. (8 Nm), Rocker Arm
Adjuster Lock Nut- 70in. lbs. (8 Nm). Recheck valve
clearance after 10 hours and then yearly.
Warning: Make sure the push rod is seated in the rocker
arm cup. If not, this will cause severe engine damage and
is not covered under warranty.
Note - you may re-use the valve cover gaskets, if you carefully
reinstall the covers and see oil leaking after running, order and
install new gaskets.
BELT TENSION ADJUSTMENT: (EVERY 100 HOURS)
Please see the belt tension instructional video for step-by-
step procedures at the Mud Buddy service web page.
https://www.mudbuddy.com/resources/tips-and-videos
SPARK PLUG GAP (100 HOURS):
Check the gap with a feeler gauge. If necessary, reset the
gap to .032 to .035. Install and tighten the spark plug to
the recommended torque.
Specications
Spark Plug Gap .032 to .035 in
Spark Plug Torque 160-inch pounds
INSPECT MUFFLER:
Remove accumulated debris from muer area and
cylinder area. Inspect the muer for cracks, corrosion
and other damage. If damaged, install a replacement
muer.
CHANGING THE OIL FILTER:
All models are equipped with an oil lter. Replace with
every oil change. Use Briggs part number 492932-S or
equivalent.
- Drain the oil from the engine.
- Remove the oil lter.
- Before installing the new lter, clean any dirt o of the
oil lter area and pre-lubricate the lter gasket ring.
- Install and tighten the lter by hand.
- Add oil to the full mark on the dipstick.
- Start and run the engine. Check the oil lter for leaks.
Let cool. Re-check the oil level.
19 20

SERVICE THE AIR FILTER:
Notice - Do not use pressurized air or solvents to clean a stock air
lter.
Remove the pre-cleaner and air lter. Replace the lter
or pre-cleaner if damaged. To loosen debris, gently tap
the air cleaner on a hard surface. For K&N lters, follow
manufacturers cleaning instructions.
CLEAN THE AIR COOLING SYSTEM:
Notice - Do not use high pressure water to clean the engine. Water
could contaminate the fuel system. Use a brush or dry cloth to clean
the engine.
This is an air-cooled engine. Dirt or debris can restrict
airow and cause the engine to overheat resulting in
poor performance and shortened engine life. Use a brush
or dry cloth to remove debris from the intake guard,
cylinder heads and muer area. Inspect and clean the
cooling ns. Loosen the two front panel screws and clean
the area under the panel.
FUEL FILTER:
Use pliers to squeeze the tabs on the fuel lter clamps.
Slide the clamps away from the lter. Carefully remove
the fuel lter and properly dispose of any leaking fuel.
Check the fuel line for any cracks or leaks. Replace if
necessary. Replace the fuel lter with an original
equipment fuel lter. Secure the fuel lter with the hose
clamps. Use Briggs part number 691035 or any good
quality fuel lter 10 micron size or better.
STORAGE – FUEL SYSTEM:
Carburetted Models
Fuel can become stale when stored over 30 days. Stale
fuel causes acid and gum deposits to form in the fuel
system and essential carburetor parts. To keep the fuel
fresh, use a fuel treatment and stabilizer, available at
most automotive stores.
8 Steps For Storing Carburetted Motors
1. Use Fresh Gasoline
2. Add Fuel Stabilizer - Using fresh, treated gasoline will help
clean and protect your engine.
3. Run The Engine For 10-15 Minutes - This will allow that
fresh treated gasoline to work its way through the engine
and hoses, replacing any of the old fuel.
4. Shut O Fuel To The Engine.
5. Run The Engine Until Completely Out Of Fuel - It is
important to store your motor completely empty of fuel.
6. Start Engine With Choke Open Until It No Longer Starts.
7. Perform Routine Maintenance - Now is the perfect time to
do another round of maintenance. Change the spark plugs,
change the air lter, change the fuel lter and change the
oil and oil lter.
8. Disconnect The Battery - This will increase the life of
your battery.
21 22

5 Steps For Storing EFI Motors
1. Fill the Tank With Fresh Gasoline - Many mud motor owners
fail to ll the tank before storing it for the o-season. By
lling your tank with gas, you decrease the chance of
getting air in the tank. Air is bad for your gas tank because
air allows condensation build-up. So, top o your boat
with fresh, treated gasoline.
2. Add Fuel Stabilizer - As you ll your gas tank, combine
it with a fuel stabilizer. Fuel stabilizer additionally helps
prevent build-up. Along with decreasing the chances of
condensation in your tank, this additive protects your fuel
lines, fuel injectors, and carburetors, as well.
3. Run The Engine For 10-15 Minutes - This will allow that
fresh treated gasoline to work its way through the engine
and hoses, replacing any of the old fuel. Do not run engine
dry.
4. Perform Routine Maintenance - Now is the perfect time to
do another round of maintenance. Change the spark plugs,
change the air lter, change the fuel lter and change the
oil and oil lter.
5. Disconnect the battery - This will increase the life of your
battery.
If stored longer than 30 days, the cylinders should be
protected with a cylinder fogging available from marine
stores by injecting the fog in the cylinders through the
spark plug holes. Cylinders that become corroded will
loose compression and void the emissions warranty.
Cover the engine to protect from rain and snow to
prevent corrosion and water from entering the exhaust
outlet.
COMMON SERVICE PARTS & REPLACEMENT PERIOD:
Air Filter - 100 Hours
Fuel Filter - 100 Hours
Oil Filter - 50 Hours
Spark Plug - 100 Hours
Warning – Propeller Balance
A badly worn, damaged or out-of-balance propeller can
cause severe damage to the drive and engine. A bad
propeller will cause signicant vibration in the handle and
lower skeg. Damage caused by a bad propeller is not
covered under our warranty.
23 24

Warranty:
One Year – Frame and Drive All Models
One Year – Models 5000 and 4400 Power Heads
Three Year – Model 23, 25, 35 37 and 40 Power Heads
Five Year – Drive Casting All Models
Manufacturer’s Emissions Warranty Coverage:
If any emission related part on your engine is defective, the part will
be repaired or replaced by Briggs and Stratton or Mud Buddy.
Owner’s Warranty Responsibilities:
As the engine owner, you are responsible for the performance of the
required maintenance listed in your owner’ manual. MUD BUDDY LLC
recommends that you retain all your receipts covering maintenance
on your engine, but MUD BUDDY LLC cannot deny warranty solely for
the lack of receipts or for your failure to ensure the performance of
all scheduled maintenance.
As the engine owner, you should however be aware that MUD
BUDDY LLC may deny warranty coverage of your marine engine or
a part has failed due to abuse, neglect, improper maintenance or
unapproved modications.
You are responsible for presenting your engine to a MUD BUDDY
LLC Service Dealer as soon as a problem exists. The warranty repairs
should be completed in a reasonable amount of time. If you have any
questions regarding your warranty rights and responsibilities, you
should contact a MUD BUDDY LLC Service Representative at
1-801-352-8011.
Manufacturer Emissions Control Warranty Provisions
The following are specic provisions relative to your Emissions
Control Warranty Coverage. It is in addition to the manufacturer
engine warranty for non-regulated engines found in the Operator’s
Manual.
1. Warranted Emission Parts
Coverage under this warranty extends only to the parts listed below
(the emissions control systems parts) to the extent these parts were
present on the engine.
a. Fuel Metering System
- Cold start enrichment system (soft choke)
- Carburetor and internal parts
- Fuel pump
- Fuel line, fuel line ttings, clamps
b. Air induction system
- Intake manifold
- Purge and vent line
c. Ignition System
- Magneto ignition system
d. Miscellaneous items used in the above systems
- Connectors and assemblies
2. Length of Coverage
For a period of three years from date of original purchase, the
manufacturer warrants to the initial owner and each subsequent
purchaser that the engine is free from emission defects in materials
and workmanship that could cause the failure of the warranty part,
and that it is identical in all material respects to the engine described
in the manufacturer’s application for certication. For models 4000,
4400 and 5000 the emissions warranty is 175 hours or one year. The
warranty period begins on the date the engine is originally pur-
chased.
25 26

The warranty on emissions-related parts is as follows:
Any warranted part that is not scheduled for replacement as
required maintenance in the owner’s manual supplied, is warranted
for the warranty period stated above. If any such part fails during the
period of warranty coverage, the part will be repaired or replaced by
the manufacturer at no charge to the owner. Any such part repaired
or replaced under the warranty will be warranted for the remaining
warranty period.
Any warranted part that is scheduled for replacement as required
maintenance in the owner’s manual supplied, is warranted for the
period to the rst scheduled replacement point for that part. If the
part fails prior to the rst scheduled replacement, the part will be
repaired or replaced by the manufacturer at no charge to the
owner. Any such part repaired or replaced under the warranty will be
warranted for the remainder of the warranty period prior to the rst
scheduled replacement point for that part.
Add-ons or modied parts may not be used. The use of any non-ex-
empted add-on or modied parts by the owner will be grounds for
disallowing a warranty claim. The manufacturer will not be liable
to warrant failures of warranted parts caused by the use of a non
exempted add on or modied part.
3. Consequential Coverage
Coverage shall extend to the failure of any engine components
caused by the failure of any warranted emissions part.
4. Claims and Coverage Exclusions
Warranty claims shall be led according to the provisions of the
engine warranty policy. Warranty coverage does not apply to failures
of emission parts that are not original equipment parts or to parts
that fail due to abuse, neglect, or improper maintenance as set forth
in the Mud Buddy LLC engine warranty policy. No liability is accepted
for warranty coverage of failures to emissions parts caused by the
use of add-on or modied parts.
5. High Altitude
Model 4400 BD is equipped with a nonadjustable Mikuni HSR 42mm
carburetor. This engine is not recommended for altitude use of 4000
feet (1219 meters) or above. Contact your dealer if you have
questions.
6. Emissions Label
Look for relevant emissions, date of manufacture, engine family and
the durability period on your engine emissions label located on the
cover side of your engine.
27 28

HDR Wire Diagram
29 30
HD Wire Diagram

A= ACCESSORY
B = BATTERY POWER
G = GROUND
L = LOAD
M = KILL
S = STARTER
RED
YELLOW
BLACK
BROWN
GREY
87a
86
85 87
30
87a
86
85 87
30
87a
86
85 87
30
YELLOW/RED
GREEN
BLUE
BLACK
TRIM
YELLOW/ WHT
STARTER SOLENOID
40A
1
2
3
4
5
6
7
8
9
10
11
12
ECU
BLK/GRN
BLK/GRN
RED/WHT
BLK/GRN
RED/BLU
RED
GRN/WHT
BLU/WHT
YEL/WHT
BLK
BLUE
GREEN
GRY
RED
N.C.
RED/WHT
BLK/GRN
RED/BLU
GRN/WHT
BLU/WHT
YEL/WHT
BLK
BLUE
GREEN
GRY
RED
N.C.
REVERSE
FORWARD
Momentary
FWD
Shift
Switch
GRY
RED
RED/WHT
RED/WHT
YEL/WHT
Trim
RED/BLU
BLUE
GREEN
RED/WHT
BLUE/WHT
GREEN/WHT
AUX/TRIM
ENGINE KILL
TRIM
DOWN
TRIM
UP
IN GEAR PROTECTOIN
20 A
2019 Model year HDR wire diagram
HDR 2019 Wire Diagram BELT DRIVE REVERSE ASSEMBLY
Gen 2
31 32
10 12 511
3
647 13 114
11 2
8
38 TOOTH ASSY STC-534
36 TOOYH ASSY STC-531
INSTALL WITH F-M83 RADIUS KEY (NOT SHOWN)
STC-530
STC-514
STC-533
STC-532
ITEM
NO.
PART NUMBER
QTY.
1
STC-530 Transmission and
Gear Hub assembly
1
2
STC-367 ELECTRIC
CLUTCH -38 TOOTH NO
FLANGE
1
3
STC-375 Planetary Brake
Plate
1
4
STC-382 Snap Ring 5.5
Inch
1
5
STC-396 Washer .4375 SS
1
6
STC-400Planetary End
Cap Insulator
1
7
STC-525 Shaft Seal
90x140x13
1
8
SVC-033 Gearcase Drain
Screw
2
9
SVC-033 GEAR CASE
DRAIN SCREW GASKET
2
10
F-B206 Bolt 7/16-20 X 4
1
11
F-B218 Flat Head Screw
12
12
F-W33 Washer 7/16 L/W ZY
1
13
STC-383 Snap Ring
1
14
STC-410 Seal 2.25 x 1.75 x
.188 1

5
1
3
4
6
87
FOR ZIP TIES TO
HOLD WIRE
ITEM NO.
PART NUMBER
QTY.
1
STC-82 Outdrive Clutch
Cover Tall Reverse
1
3
STC-376 Brake Brake
Magnet
3
4
STC-406 Brake Magnet
Spacer Tube
6
5
STC-403 Magnet 1.42 OD
3
6
F-S69 SCREW 10-32 X 1/4
3
7
STC-474 HDR Cover Harness
Bracket
1
8
F-S18 Screw 10-32 x 0.375"
SS Phillips Pan Head
Machine Screw
3
DO NOT SCALE DRAWING
STC-407
SHEET 1 OF 1
1/15/19
L.THOMAS
B.Hend
UNLESS OTHERWISE SPECIFIED:
SCALE: 1:8
WEIGHT:
REV
DWG. NO.
A
SIZE
TITLE:
NAME
DATE
COMMENTS:
Q.A.
MFG APPR.
ENG APPR.
UPDATED
DRAWN
FINISH
MATERIAL
INTERPRET GEOMETRIC
TOLERANCING PER:
DIMENSIONS ARE IN INCHES
TOLERANCES:
FRACTIONAL
ANGULAR: MACH
BEND
TWO PLACE DECIMAL
.01
THREE PLACE DECIMAL
.005
THE INFORMATION CONTAINED IN THIS
DRAWING IS THE SOLE PROPERTY OF
MUD BUDDY LLC
. ANY REPRODUCTION
IN PART OR AS A WHOLE
WITHOUT THE WRITTEN PERMISSION OF
MUD BUDDY LLC
IS PROHIBITED.
5
4
3
2
1
PROPRIETARY AND CONFIDENTIAL
MUD BUDDY LLC.
COVER ASSEMBLY
TALL REVERSE
A
7
12
11
9
8
4
5
13
ITEM NO.
PART NUMBER
QTY.
4
STC-64 Handle Grip
1
5
CKC-83 Throttle
Handle Assembly
1
7
STC-61 Handle Box
Top Cover
1
8
SVC-064 Trim Switch
Side
1
9
P5- Vandal Resistant,
Sealed, Alternat
action
1
10
STC-61 Handle Box
Back
1
11
STC-393 Toggle Switch
DPDT 15 AMP
1
12
STC-447 Toggle Guard
Handle Box
1
13
EL-180 Tether Kill
Switch
1
DO NOT SCALE DRAWING
STC-507
SHEET 1 OF 1
3/17/20
B.H.
UNLESS OTHERWISE SPECIFIED:
SCALE: 1/8
WEIGHT:
REV
DWG. NO.
A
SIZE
TITLE:
NAME
DATE
COMMENTS:
Q.A.
MFG APPR.
ENG APPR.
CHECKED
DRAWN
FINISH
MATERIAL
INTERPRET GEOMETRIC
TOLERANCING PER:
DIMENSIONS ARE IN INCHES
TOLERANCES:
FRACTIONAL
ANGULAR: MACH
BEND
TWO PLACE DECIMAL
.01
THREE PLACE DECIMAL
.005
THE INFORMATION CONTAINED IN THIS
DRAWING IS THE SOLE PROPERTY OF
MUD BUDDY LLC
. ANY REPRODUCTION
IN PART OR AS A WHOLE
WITHOUT THE WRITTEN PERMISSION OF
MUD BUDDY LLC
IS PROHIBITED.
5
4
3
2
1
PROPRIETARY AND CONFIDENTIAL
MUD BUDDY LLC.
HANDLE ASSEMBLY
HDR 1.5"
COVER ASSEMBLY TALL REVERSE HANDLE ASSEMBLY HDR 1.5
33 34

27
18
21
22
20
23
29
31
28
17
33
11
1
24 11
1
1
13
12
15
510
32
ITEM
NO.
PART NUMBER
QTY.
1
STC-289 Clamp Mount Sub Assembly Sport
Merc
1
2
1-s11 Clamp Mount Sport Merc
1
3
1-S15 Clamp Mount Yoke Left Sport Merc
1
4
1-S16 Clamp Mount Yoke Right Sport
Merc
1
5
STC-126 Travel Lock Barrel
1
6
1-S18 Actuator Yoke Bottom Sport Merc
1
7
F-N11 Nut 1/2-20
2
8
STC-288
1
9
1-S13 Swivel, Inner
1
10
1-S14 Outer Swivel Sport Merc
1
11
STC-111 Swivel Tube
1
12
STC-110 Swivel Tube 7.25
1
13
1-S20 Swivel Tube 2 inch
2
14
1-S17 ACTUATOR YOKE TOP SPORT MERC
1
15
1-S21 Bushing, Actuator (sport merc)
1
16
1-S26 Bumper, Swivel
1
17
1-S22
1
18
F-B114
1
19
STC-239 Clamp Mount Handle Assembly
2
20
STC-29 Clamp Screw
1
21
STC-28 Handle, Clamp Mount
1
22
F-M01 Spring Pin
1
23
STC-27 Cup, Clamp
2
24
SVC 02 merc trim main base
1
25
merc actuator arm
1
26
STC-129 Travel Lock Pin
1
27
STC-125 Travel Lock Ball
1
28
STC-109 Bushing
2
29
F-B75 Bolt 5/8-11 x 9 1/2
1
30
STC-13 Swivel Tube Inner
1
31
F-W13 Washer 5/8 Internal
1
32
F-N84 Nut 5/8-11 Nylock
1
33
1-S24 Quick Release Pin
1
STC-336
SHEET 1 OF 1
SCALE: 1:48
WEIGHT:
REV
DWG. NO.
A
SIZE
TITLE:
THE INFORMATION CONTAINED IN THIS
DRAWING IS THE SOLE PROPERTY OF
MUD BUDDY LLC
. ANY REPRODUCTION
IN PART OR AS A WHOLE
WITHOUT THE WRITTEN PERMISSION OF
MUD BUDDY LLC
IS PROHIBITED.
5
4
3
1
PROPRIETARY AND CONFIDENTIAL
MUD BUDDY LLC.
CLAMP MOUNT
ASSEMBLY SPORT
MERC
7
5
6
1
3
4
17 15 14
12
13
15
10
16
9
11
2
18
ITEM
NO.
PART NUMBER
QTY.
1
STC-418 Top Brace Cav Plate
Assembly 32 inch HDR
1
2
STC-118 Bracket, Right Top Brace
Mount
1
3
STC-119 Bracket, Left Top Brace
Mount
1
4
1-M40 Brace, Mini Lower Bracket
Top 2
5
STC-387 Skeg 32 Inch Drive
Reverse
1
6
STC-416 Skeg Close out Plate
HDR
1
7
STC-417 Drive Sub Assembly 32
Inch Reverse
1
8
F-B04 1/4-28 x 3/4 SHCS SS
1
9
F-B14 3/8-16 X 1 1/4 SS HCS
4
10
F-M05 Retaining Ring Inch
Internal
1
11
F-N06 NUT .375-16 LN
4
12
STC-242 SEAL AND CAP SET
1
13
STC-100 Drive Shaft 32.375
1
14
STC-19 Sleeve, Rear Sleeve
1
15
STC-08 Bearing 6205
4
16
STC-21 Bushing Sleeve Front
1
17
F-N04 .3125-18 NC ZP NYLOCK
NUT
8
18
F-B08 HCS .3125 X 1 SS
8
STC-409
SHEET 1 OF 2
SCALE: 1:24
WEIGHT:
REV
DWG. NO.
SIZE
TITLE:
THE INFORMATION CONTAINED IN THIS
DRAWING IS THE SOLE PROPERTY OF
. ANY REPRODUCTION
IN PART OR AS A WHOLE
WITHOUT THE WRITTEN PERMISSION OF
IS PROHIBITED.
5
4
3
2
1
MUD BUDDY LLC.
DRIVE ASSEMBLY
32" W/OUT DRIVE
DRIVE SPROCET (HDR)
35 36
Troubleshooting
Issue Action Value/ notes Yes NO
Engine
will not
start
Check safety lanyard
Is Shift switch in Neutral
Position?
Adjust to
Neutral
Check the Main circuit Break-
er o Battery
Check Battery Voltage 12.2-13.5 V
Can you hear the fuel pump
initialize when key is turned
to run position
Fuel pump ini-
tialize indicates
ECU is getting
power
System
OK
Check fuel
pump and
connec-
tions
Does The MIL light turn on
when Key is turned to run
position
MIL light Check
ECU or
electrical
connec-
tions to
battery
Trouble
shifting
Forward,
but not
reverse
Check electrical ground connec-
tions coming from belt housing
Look for a loos or corroded connec-
tion at the grounding lug
If shift engages in one
direction but not the
other. The positive
circuit is known good
at least up to the shift
switch.
Tighten
Grounding
lug
Check electrical connector behind
the handle. Position 10 (Red) is for-
ward. Position 11 (Gray is reverse)
Look for contacts not fully seated,
broken or damaged wires
Fix loose
or broken
connec-
tions
Check electrical 2 pin connector
inside the belt housing. Check to
make sure contacts are fully seated
and no broken or damaged wires
cont’d on next pg.

37 38
Forward
or reverse
drops out of
gear while
under power
Check The 20 Amp accessory
power circuit breaker. If breaker
is tripped, Measure current. If
current is over 20 amps. Look for
short circuit. If current is under 20.
Replace breaker.
The circuit breaker
self re-sets when
it cools. A tripped
breaker will inhibit
forward or reverse.
Typical current draw
for forward is 6 amps.
10 for reverse.
Replace
Breaker
or x
electrical
short
Check for loose intermittent
Ground at Grounding lug
No forward
or reverse
Check the Accessory power lug at
the key switch
Accessory power lug
is a red wire spade
connector on the key
switch
Check for voltage at the 20 amp
circuit Breaker
Check all grounding connections at
the grounding lug
Check connections at the handle
and inside belt cover
Best Engine
RPM?
On plane engine RPM
- 4100 to 4300 RPM
Engine
starts, but
has a rough
idle/run
Turn key to ON position, lift pump
sound loud?
Check fuel delivery Next step
Make sure the air lter and fuel
lter are in good shape and there is
no obstructions
Check connections at the battery,
120 AMP Breaker and grounds
Double check the gap between the
CPS and ywheel, reset if necessary
Perform ECM memory reset
Manifold Absolute Pressure sensor (MAP) low voltage
or open
P0107
Manifold Absolute Pressure sensor (MAP) High Voltage P0108
Manifold Air Temperature sensor (MAT) Low Voltage P0112
Manifold Air Temperature Sensor (MAT) High Voltage or
open
P0113
Engine Head Temperature Sensor (EHT) Low Voltage P0117
Engine Head Temperature Sensor (EHT) High voltage or
open
P0118
Throttle Position Sensor(TPS) Low Voltage or open P0122
Throttle Position Sensor (TPS) High Voltage or open P0123
Fuel injector A fault P0201
Fuel Injector B Fault P0202
Fuel Pump Relay Low or open circuit P0231
Fuel Pump Relay High voltage P0232
Crank Shaft Position Sensor (CKP) Noisy Signal P0336 (Reposition sensor)
Crankshaft Position Sensor (CKP) No Signal P0337 (Check wires Reposition sensor)
Ignition Coil A fault P0351
Ignition Coil B fault P0352
Idle Speed Control (IAC) error P0505
System Voltage LOW P0562
System Voltage High P0563
Malfunction Indicator Light (MIL) malfunction P0650
Safety Interrupt Sensor Malfunction P1500
Blink Trouble Codes (Briggs)
Check for error codes ( Briggs)
Turn the key from o to run position 5 times within 5 seconds. End the sequence with the key in
the run position. The Mil light will send a series of Blink codes with 0 being 10 blinks.
Code 061 is the end of the list code. If that is the only code, There are no faults
Clear fault codes (Briggs)
Turn the key from stop to run position 5 times within 5 seconds. End the sequence with the key in
the stop position; wait 10 seconds and start engine, ECM memory will be cleared
This manual suits for next models
11
Table of contents
Other Mud Buddy Engine manuals
Popular Engine manuals by other brands

White
White RE 540 Series Repair instructions
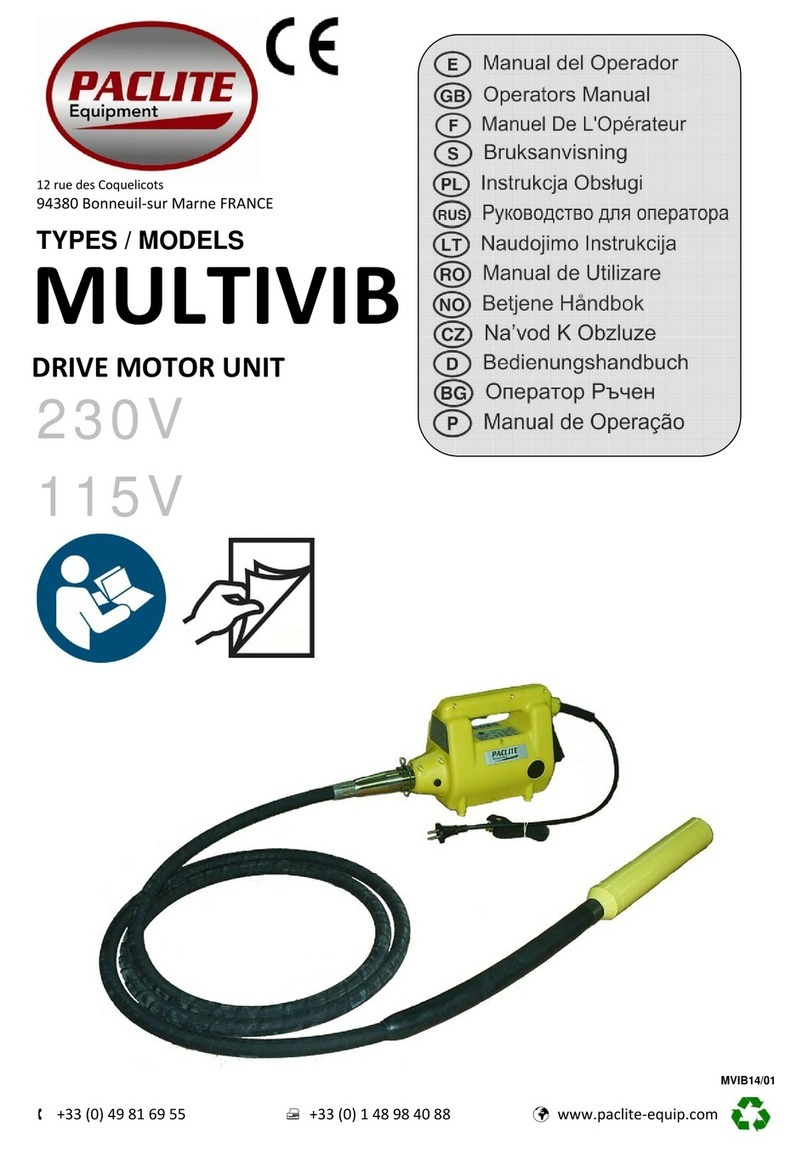
PACLITE Equipment
PACLITE Equipment MULTIVIB Operator's manual
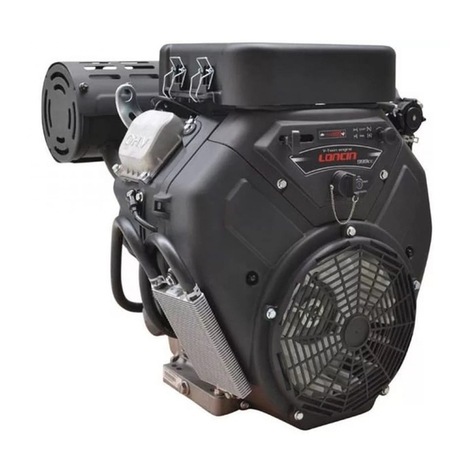
LONCIN
LONCIN 2V90FD owner's manual
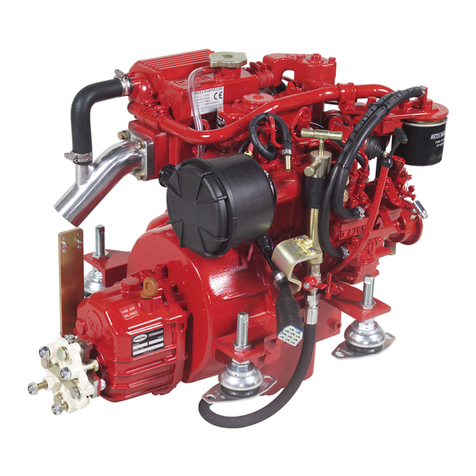
Beta Marine
Beta Marine Beta 10 Operator's maintenance manual
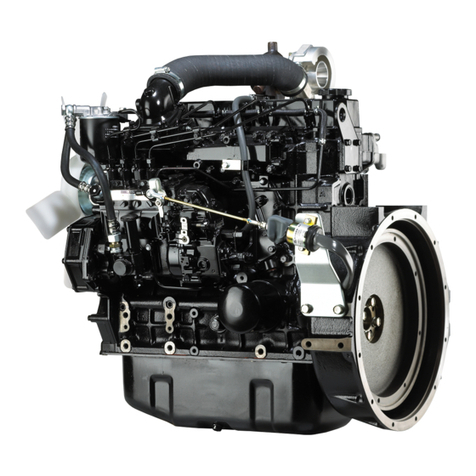
Mitsubishi
Mitsubishi S4S-DT Operation & maintenance manual
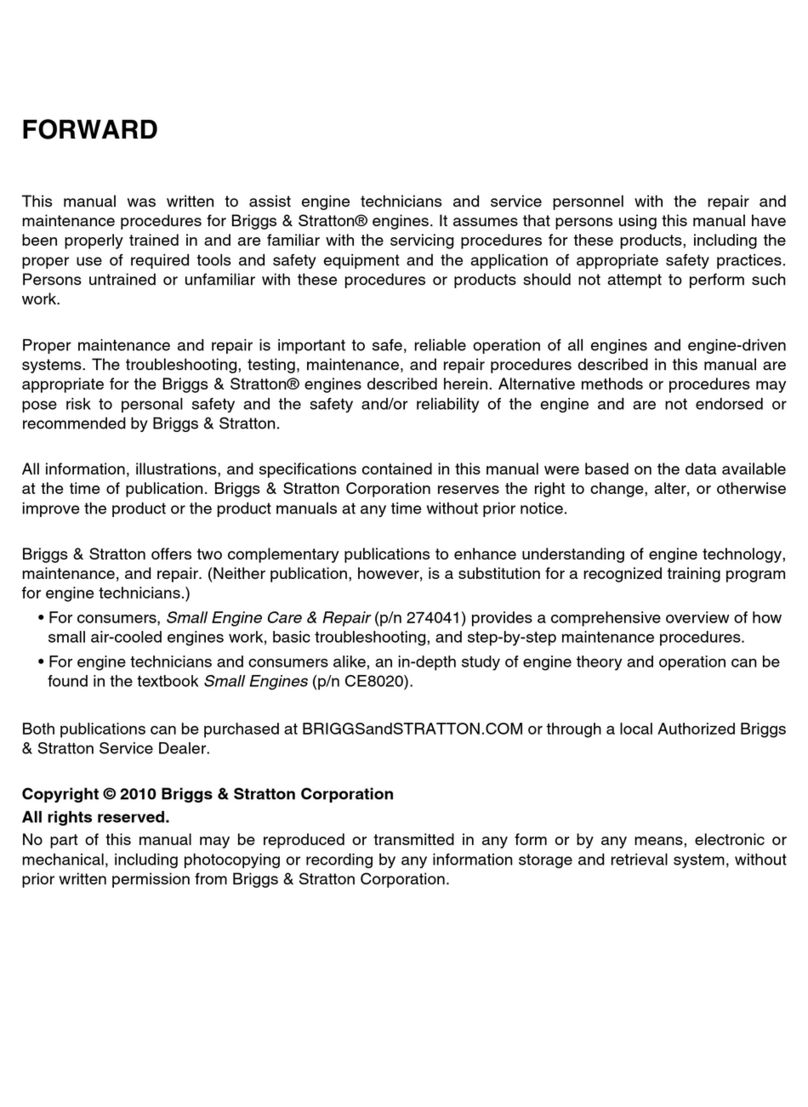
Briggs & Stratton
Briggs & Stratton 090600 manual