Network Technologies Incorporated E - ACDCLM User manual

1
INSTALLATION GUIDE FOR THE
E-ACDCLM
AC & DC Voltage and Current Monitor
INTRODUCTION
The NTI E-ACDCLM AC & DC Voltage and Current Monitor monitors AC and DC voltage sources and current levels when
connected to an E-16D, E-5D or E-2D Server Environment Monitoring System(SYSTEM). The voltage sources can be anything
with a range between -60 to +60VDC or 0-240VAC. Current measurements can be taken on AC and DC loads and with the use
of hall effect sensors (sold separately) loads can be as much as 500A. When connected to a SYSTEM via 18-24AWG CAT5/5e/6
cable (up to 1,000 feet away), the voltage and/or current source(s) can be monitored and the SYSTEM can be configured to alert
users as to variations in the voltage and current levels.
Features:
Detects and monitors up to two voltages, one AC (up to 240VAC)
and the other DC (-60 to +60VDC)
Current measurements (AC and DC) up to 500A using hall-effect
transducers (sold separately)
2 and 4-position screw-terminal connections
Supports 18-24AWG CAT5/5e/6 cable up to 1,000 ft. (305M) (not included)
Includes Mounting Ears
CE certified and RoHS compliant
Powered by E-2D/5D/16D
Dimensions WxDxH (in): 6.2x2.3x1.6
Accuracy and range are transducer-dependent (sold separately).
Compatible with E-FSC Fiber Converter/Extender
oUse to extend sensor up to 1.2 miles (2km) from the ENVIROMUX unit.
INSTALLATION
Mount the E-ACVDCLM using the mounting ears provided. To use the ears, remove the screws securing the ears to the rear of
the E-ACDCLM, turn the ears around, and reapply the screws. Alternatively, secure one ear to holes on the bottom of the unit so
that it can be hung as shown in the image below.
Note: The E-xD must be running
firmware version 2.31 or later in order
to use the E-ACDCLM with it. Refer
to the E-xD manual for firmware
upgrade instructions as needed.

2
To mount multiple E-ACDCLM in close proximity to the E-16D, install an extension rail kit (NTI E-RL-16D - sold separately) and
mount E-ACDCLM as seen in the illustration below.
CONNECTION
Note: To prevent damage to the voltage source or the Sensor Adapter proper polarity must be observed when making
connections.
1. At the “AC VOLTAGE” terminal block, connect an AC voltage source to be monitored between 0 and 240VAC.
Note: The AC connection does not require any specific polarity.
2. At the “DC VOLTAGE” terminal block, connect a -60 to +60VDC voltage source to be monitored to the “Vin“ and “ “ (earth
ground)connections using the removable terminal block.
3. If current sensing is desired, install a hall effect sensor to the AC or DC circuit to be monitored. Then connect the supplied
4-wire cable to the sensor. Connect the 4 wires at the end of the cable to the AC or DC CURRENT TRANSDUCER
(depending upon the type of circuit being sensed) terminals on the E-ACDCLM.
Note: If a hall-effect sensor is installed on a DC circuit and then the sensing cable is connected to the “AC CURRENT
TRANSDUCER” side of the E-ACDCLM, no reading will be displayed for that sensor.
Note: The wire connection terminal block is easily removed from the Sensor Adapter for convenient wire termination.

3
TIP: A single hall effect sensor can be used to measure current at different ranges. By passing a wire through the
sensor loop repeatedly (looping the wire around), the range of the sensor will be divided by the number of times the wire
passes through. For a 100A AC sensor, for example, two passes will reduce it by 100/2 (range of 0-50A), three passes
will reduce it by 100/3 (range of 0-33A), and so on. See example below. If you need to increase the sensitivity of your
sensor, this is a way to do so.
Installation Note: Hall Effect sensors can be rated AC Current-only, DC Current-only, or AC/DC current compatible. Sensors
rated for DC current will include a directional current flow arrow either on the label or on the body of the sensor, indicating that
current flowing in that direction will be reported by the sensor as positive current flow. When installing a hall effect sensor to a DC
circuit, you will want to install it oriented such that the arrow points in the direction you want represented as positive current flow
on the status page for that sensor.
3. Connect a 18-24AWG CAT5/5e/6 patch cable (up to 1,000 feet long) between the “Cat x” port on the E-ACDCLM and an “RJ45
Sensor” port on the SYSTEM. (The use of smaller gauge CATx cabling will result in shorter distances that can be spanned.)
Note: Each row of RJ45 Sensor connectors (1-8 and 9-16) is rated for a combined load of 500mA at 12VDC. Each
E-ACDCLM uses 66mA. When applying sensors, be sure that the total load on each row does not exceed 500mA at
12VDC or failure of the SYSTEM or may result.
4. Configure the SYSTEM to react to changes in the voltage and/or current from the source(s), as desired. See examples on
the following pages.
Positive current flow
indicator

4
CONFIGURATION
When a E-ACDCLM is connected to the ENVIROMUX, the summary page (above) will update with 4 different sensor types, AC
Voltage, AC Current, DC Voltage and DC Current. The sensor is plugged into RJ45 Sensor port #5 in this example. Click on the
Sensor in the Description column (or “View” under Action) and display the status page for each sensor. (Below). In order to better
define the sensor on the Summary Page, in SNMP traps, or in an MIB browser, click on the “Edit” link to open the sensor
configuration page and configure the sensor.

5
Click on the “Configure” button on any Status Page to display the Configuration page for any sensor.
Values shown
here are for a
10Amp hall effect.
A 30A DC voltage
hall effect would
use “-30” and “30”
instead. (for
example)

6
Most of the sensor settings are the same as any other sensor configuration (page 39 of the E-xD manual) but for the AC and DC
Current Sensors there are some differences:
Sensor Settings Description
Associate Sensor Select if the Type “AC Current” or “DC Current” should be replaced by the sensor type to be
entered in the next box
Associated Sensor Type Enter the “Type” of sensor that should be displayed on the summary page and in all alert
communications received regarding this sensor
Associated Sensor Unit Enter between 1 and 3 alphabetical characters. These characters will be used by the
ENVIROMUX to represent the unit of measure reported by the attached sensor. Leaving it
empty will result in an empty string in the reported data.
SNMP Associated Type ID Enter ID value from MIB file if SNMP traps will be used for alert notifications for this sensor (for
more on this, see “SNMP Custom Type ID” below)
Min. Associated Level The minimum range of the units to be associated with the current reading measured from the
attached sensor.
Max. Associated Level The maximum range of the units to be associated with the current reading measured from the
attached sensor.
SNMP Custom Type ID: Use this field if SNMP traps will be used for alert notifications. The Type ID corresponds with a value
defined in the MIB file under “extSensorType” (default value is 32767 for type “Custom”). Place the desired number in this box
that represents the type of sensor to be reported in the MIB browser or SNMP trap.
To define a new type of sensor;
1. open the MIB file,
2. locate the section titled “extSensorType”,
3. assign a description and a number not already in use (in the “SYNTAX” field) to associate with it ,
4. enter the number for the newly defined extSensorType in the SNMP Custom Type ID box.
If the Type ID is left blank, the value “0” will be assigned, which will be reported in the browser and SNMP trap as type
“undefined”.
TECHNICAL SPECIFICATIONS
Description Specification
Polling rate 1Sa/s
AC Voltage Range 600V isolated 0 to 247Vrms
AC Reporting Accuracy 2.5VAC (up to 240VAC)
AC Resolution 0.25VAC
DC Voltage Range Non-isolated -60 to +60V DC
DC Reporting Accuracy 1.2VDC
DC Resolution 0.12VDC
Current Measurement Requires Hall-Effect transducer (sold
separately)
Power Powered by the SYSTEM
Current Draw 12V @ 66mA / 5V @ 8mA
Size (In.) W x D x H 6.2 x 2.3 x 1.6
Regulatory Approvals CE, RoHS
COPYRIGHT
Copyright © 2009-2018 Network Technologies Inc All rights reserved. No part of this publication may be reproduced, stored in a
retrieval system, or transmitted in any form or by any means, electronic, mechanical, photocopying, recording, or otherwise,
without the prior written consent of Network Technologies Inc, 1275 Danner Drive , Aurora, OH 44202.
CHANGES
The material in this guide is for information only and is subject to change without notice. Network Technologies Inc reserves the
right to make changes in the product design without reservation and without notification to its users.
WARRANTY INFORMATION
The warranty period on this product (parts and labor) is two (2) years from date of purchase. Please contact Network
Technologies Inc at (800) 742-8324 or 330-562-7070 for information regarding repairs and/or returns. A return authorization
number is required for all repairs/returns.
MAN250 Revised 4/4/2018
Table of contents
Other Network Technologies Incorporated Measuring Instrument manuals
Popular Measuring Instrument manuals by other brands
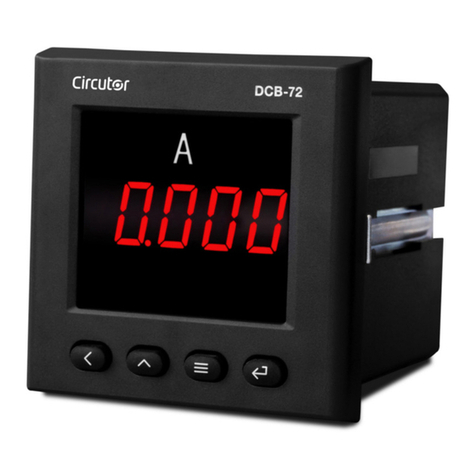
Circutor
Circutor DCB-72 Vac instruction manual
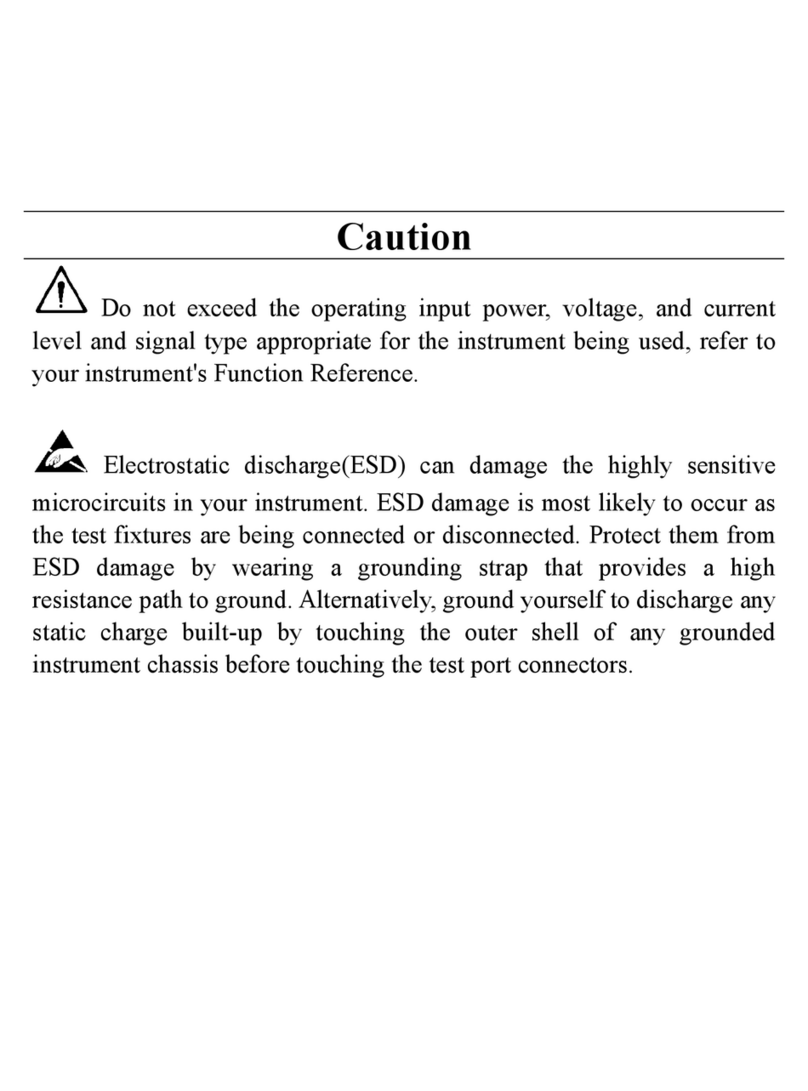
Agilent Technologies
Agilent Technologies E5071C ENA Series installation guide
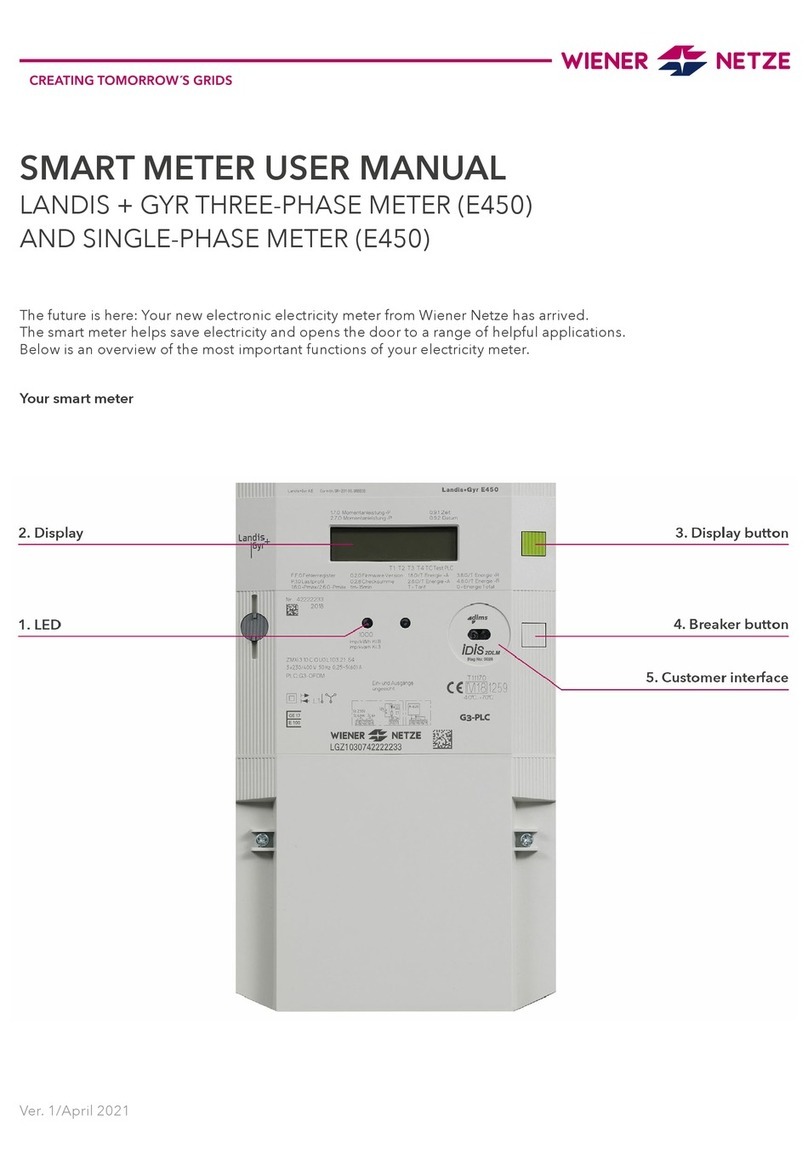
Wiener Netze
Wiener Netze E450 user manual
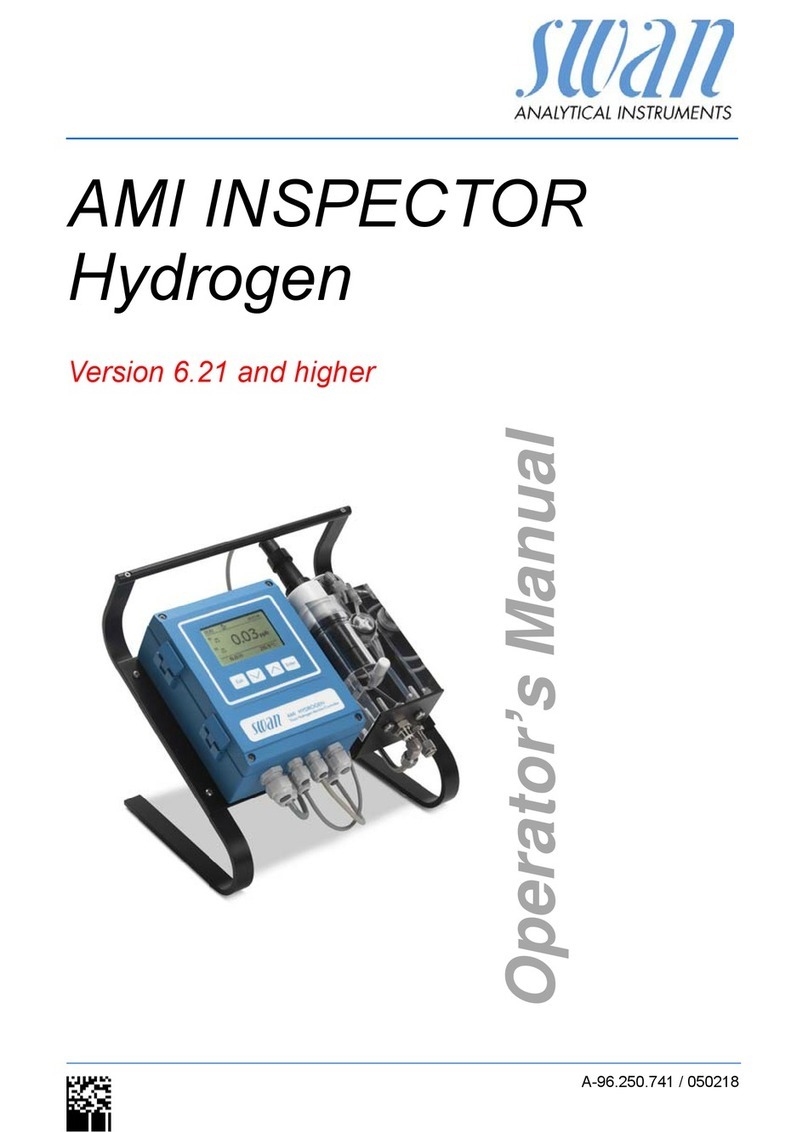
Swan Analytical Instruments
Swan Analytical Instruments AMI INSPECTOR Hydrogen Operator's manual
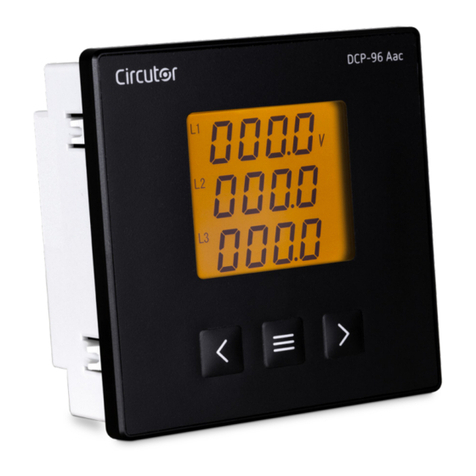
Circutor
Circutor DCP-96 Aac instruction manual
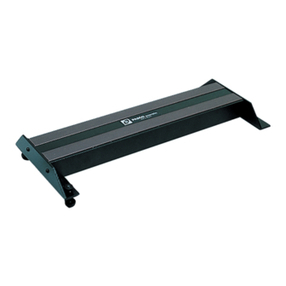
PASCO
PASCO OS-9171 instruction sheet