NI MES-3980 Manual

NI MES-3980
Hardware Installation Guide
First Edition, Sept 2007
P/N: 1802508100110

—1 —
Package Checklist
The NI MES-3980 is shipped with the following items. If any of these items is
missing or damaged, please contact your customer service representative for
assistance.
yNI MES-3980 Switch
yHardware Installation Guide
yCD-ROM with User’s Manual and Windows Utility
yRJ45 to DB9 Console port cable
yProtective caps for unused ports
Features
¾Advanced Industrial Networking Capability
yPlug-n-Play, Redundant Ethernet Ring (recovery time < 300 ms at full
load) and RSTP/STP (IEEE802.1W/D)
yIGMP Snooping and GMRP for filtering multicast traffic from
Industrial Ethernet
ySupports port-based VLAN, IEEE802.1Q VLAN and GVRP protocol to
ease network planning
ySupports QoS-IEEE802.1p/1Q and TOS/DiffServ to increase
determinism
ySupports 802.3ad, LACP for optimum bandwidth utilization
yPort Trunking for optimum bandwidth utilization
yRMON for efficient network monitoring and proactive capability
ySNMP V1/V2c/V3 for different levels of network management security
ySupports IEEE802.1X and https/SSL to enhance network security
¾Designed for IndustrialApplications
yBandwidth management to prevent unpredictable network operation
yPort mirroring for online debugging
yLock port for authorized MAC address access
yDigital inputs to integrate sensors and alarms with IP networks
yAutomatic warning by exception through email, relay output
yAutomatic recovery of IP addresses from connected devices
yLine-swap fast recovery (patent pending)
yRedundant, dual DC power inputs
y-40 to 75°C operating temperature range
yIP30, rugged high-strength case
yDIN-Rail or panel mounting ability

—2 —
Panel Layout
V1, V2 INPUTS: 12-45 VDC
RS-232 CONSOLE
------
ON
OFF
MASTER
COUPLER
TURBO
RING
PWR2
4
3
2
1
PWR2
RELAY2
RELAY1
DI1
DI1
V2-
V2+
I1
V1-
V1+
I2
Top Panel View
1
2
3
4
1
Rear Panel View
2
16
15
15
52
Front Panel View
7
6
8
9
11
10
12
13
14
14
2
M
N
S
AN
NI TIO
RT UT
LA
EN S
NI MES-3980
ManagedEthernetSwitch
MASTER
COUPLER
PWR1
PWR2
FAULT
8
7
6
4
2
5
3
1
1. Grounding screw
2. Terminal block for power input
PWR1/PWR2 and relay output
3. Heat dissipation orifices
4. Console port
5. DIP switches
6. Power input PWR1 LED
7. Power input PWR2 LED
8. Fault LED
9. Master LED
10. Coupler LED
11. TP port’s 100 Mbps LED
12. TP port’s 10 Mbps LED
13. Model Name
14. 10/100BaseT(X) ports
15. Screw hole for wall mounting kit
16. DIN-Rail kit

—3 —
Mounting Dimensions (unit = mm)
Rear View
Side View Front View
DlN-Rail Kit
DlN-Rail
105.00
9.00
0
0
.53
00.531
3.42
73.9377.6465.42
0
0
.53
1
Wall Mounting Kit
10
10
5
7.75 30.50 7.75
3.5
6
6
08
.
6
65
0
.7
5
13.9 18.2 13.9
30.00 15.0
51.3 13.9
80.2
DlN-Rail Kit
7.5 55 7.5
02.72 03.84
DIN-Rail Mounting
The aluminum DIN-Rail attachment plate should already be fixed to the back
panel of the NI MES-3980 when you take it out of the box. If you need to
reattach the DIN-Rail attachment plate, make sure the stiff metal spring is
situated towards the top, as shown in the following figure.
STEP 1:
Insert the top of the DIN-Rail into the
slot just below the stiff metal spring.
STEP 2:
The DIN-Rail attachment unit will
snap into place as shown.
metal
spring
DIN-Rail
metal
spring
DIN-Rail
To remove the NI MES-3980 from the DIN-Rail, simply reverse Steps 1 and 2.

—4 —
Wall Mounting (optional)
For some applications, you will find it convenient to mount the NI MES-3980
on the wall, as shown in the following figures.
STEP 1: Remove the
aluminum DIN-Rail
attachment plate from the NI
MES-3980’s rear panel, and
then attach the wall mount
plates, as shown in the
figures at the right.
⇒
STEP 2:
Mounting the NI MES-3980 on the wall requires 4 screws.
Use the NI MES-3980, with wall mount plates attached, as a
guide to mark the correct locations of the 4 screws. The
heads of the screws should be less than 6.0 mm in diameter,
and the shafts should be less than 3.5 mm in diameter, as
shown in the figure at the right.
6.0 mm
3.5 mm
NOTE Before tightening the screws into the wall, make sure the screw head
and shank size are suitable by inserting the screw into one of the
keyhole-shaped apertures of the Wall Mounting Plates.
Do not screw the screws in completely—leave about 2 mm to allow room for
sliding the wall mount panel between the wall and the screws.
STEP 3: Once the screws are fixed in
the wall, insert the four screw heads
through the large parts of the
keyhole-shaped apertures, and then
slide the NI MES-3980 downwards,
as indicated. Tighten the four screws
for added stability.
Wiring Requirements
WARNING
The power for this product is intended to be supplied by a Listed
Power Unit, with output marked LPS, and rated to deliver 12 to
45 VDC at a maximum of 600 mA.
WARNING
Safety First!
Be sure to disconnect the power cord before installing and/or
wiring your NI MES-3980. Calculate the maximum possible
current in each power wire and common wire. Observe all
electrical codes dictating the maximum current allowable for each
wire size. If the current goes above the maximum ratings, the
wiring could overheat, causing serious damage to your
equipment.

—5 —
You should pay attention to the following important points:
yUse separate paths to route wiring for power and devices. If power wiring
and device wiring paths must cross, make sure the wires are perpendicular
at the intersection point.
yNOTE: Do not run signal or communications wiring, and power wiring
through the same wire conduit. To avoid interference, wires with different
signal characteristics should be routed separately.
yUse the type of signal transmitted through a wire to determine which wires
should be kept separate. The rule of thumb is that wiring that shares similar
electrical characteristics can be bundled together.
yKeep input wiring and output wiring separate.
yIt is strongly advised that you label wiring to all devices in the system,
when necessary.
Grounding the Switch
Grounding and wire routing help limit the effects of noise due to
electromagnetic interference (EMI). Run the ground connection from the
ground screw to the grounding surface prior to connecting devices.
ATTENTION
This product is intended to be mounted to a well-grounded
mounting surface, such as a metal panel.
Wiring the Relay Contact
The NI MES-3980 has two sets of relay output—relay 1 and relay 2. Each
relay contact consists of two contacts of the terminal block on the NI
MES-3980’s top panel. Refer to the next section for detailed instructions on
how to connect the wires to the terminal block connector, and how to attach the
terminal block connector to the terminal block receptor. The meaning of the
two contacts used to connect the relay contacts is illustrated below.
Relay1 Relay2
Relay1 Relay2
The fault circuit will open if:
1. A relay warning event is
triggered, OR
2. The NI MES-3980 is the
Master of this Turbo Ring,
and the Turbo Ring is broken,
OR
3. Start-up failure.
If none of these three conditions
is met, the fault circuit will
remain closed.
Wiring the Redundant Power Inputs
The NI MES-3980 unit has two sets of power inputs—power input 1 and
power input 2. The top two contacts and the bottom two contacts of the 6-pin
terminal block connector on the top panel are used for the NI MES-3980’s two
digital inputs. Top and front views of one of the terminal block connectors are
shown below.

—6 —
PWR1 PWR2
V1- V1+
PWR1
V2- V2+
PWR2
V1- V1+ V2- V2+
Take the following steps to wire
the redundant power inputs:
STEP 1: Insert the
negative/positive DC wires into
the V-/V+ terminals.
STEP 2: To keep the DC wires
from pulling loose, use a small
flat-blade screwdriver to tighten
the wire-clamp screws on the
front of the terminal block
connector.
STEP 3: Insert the plastic
terminal block connector prongs
into the terminal block receptor,
which is located on the NI
MES-3980’s top panel.
ATTENTION
Before connecting the NI MES-3980 to the DC power inputs,
make sure the DC power source voltage is stable.
Wiring the Digital Inputs
The NI MES-3980 unit has two sets of digital inputs, DI 1 and DI 2. Each DI
consists of two contacts of the 6-pin terminal block connector on the NI
MES-3980’s top panel. The remaining contacts are used for the NI
MES-3980’s two DC inputs. Top and front views of one of the terminal block
connectors are shown below.
I1
D2I
I2
D1I
I1I2
D2ID1I
Take the following steps to wire
the digital inputs:
STEP 1: Insert the negative
(ground)/positive DI wires into
the ┴/I1 terminals.
STEP 2: To keep the DI wires
from pulling loose, use a small
flat-blade screwdriver to tighten
the wire-clamp screws on the
front of the terminal block
connector.
STEP 3: Insert the plastic
terminal block connector prongs
into the terminal block receptor,
which is located on the NI
MES-3980’s top panel.

—7 —
10/100BaseT(X) Ethernet Port Connection
The 10/100BaseT(X) ports located on NI MES-3980’s front panel are used to
connect to Ethernet-enabled devices.
Next, we show pinouts for both MDI (NIC-type) ports and MDI-X
(HUB/Switch-type) ports, and also show cable wiring diagrams for
straight-through and cross-over Ethernet cables.
MDI Port Pinouts MDI-X Port Pinouts 8-pin RJ45
Pin Signal Pin Signal
1 Tx+ 1 Rx+
2 Tx- 2 Rx-
3 Rx+ 3 Tx+
6 Rx- 6 Tx-
RJ45 (8-pin) to RJ45 (8-pin) Straight-Through Cable Wiring
Straight-Through Cable
RJ45 Plug Pin 1
Switch Port
RJ45
Connector RJ45
Connecto
r
Tx+
Tx-
Rx+
Rx-
NIC Port
Cable Wiring
3 3
6 6
1 1
2 2
Rx+
Rx-
Tx+
Tx-
RJ45 (8-pin) to RJ45 (8-pin) Cross-Over Cable Wiring
Cross-Over Cable
RJ45 Plug Pin 1
Switch Port
(NIC Port)
RJ45
Connector RJ45
Connector
Tx+
Tx-
Rx+
Rx-
(Rx+)
(Rx-)
(Tx+)
(Tx-)
(Tx+)
(Tx-)
(Rx+)
(Rx-)
Switch Port
(NIC Port)
Cable Wiring
3 1
6 2
1 3
2 6
Rx+
Rx-
Tx+
Tx-
Relay Contact
The NI MES-3980 has two relay contacts located on the top panel. For detailed
instructions on how to connect the relay contact power wires to the two middle
contacts of the 6-contact terminal block connector, see the Wiring the Relay
Contact section. A typical scenario would be to connect the fault circuit to a
warning light located in the control room. The light can be set up to switch on
when a fault is detected.
The Relay Contact has two terminals that form a fault circuit for connecting to
an alarm system. The two wires attached to the fault contacts form an open
circuit when (1) a relay warning event is triggered, (2) the NI MES-3980 is the
Master of this Turbo Ring, and the Turbo Ring is broken, or (3) start-up failure.
If none of these three conditions occur, the fault circuit will be closed.
1
8

—8 —
Turbo Ring DIP Switch Settings
The NI MES-3980 switches are plug-and-play managed redundant Ethernet
switches. The proprietary Turbo Ring protocol was developed by NI to provide
better network reliability and faster recovery time. The recovery time of the NI
Turbo Ring is less than 300 ms-compared to a 3- to 5-minute recovery time for
commercial switches, decreasing the possible loss caused by network failures
in an industrial setting. There are 4 Hardware DIP Switches for Turbo Ring on
the top panel of the NI MES-3980 that can be used to set up the Turbo Ring
easily within seconds.
NOTE If you do not want to use a hardware DIP switch to set up the Turbo
Ring, you can use a web browser, Telnet, or console to disable this
function.
NE MES-3980 DIP Switches
2
1
------
MASTER
COUPLER
TURBO
RING
4
3
The default setting for each DIP Switch is OFF.
The following table explains the effect of setting
the DIP Switches to the ON positions.
DIP Switch Setting Description
------
Serves no function (reserved for future use)
On
Enables the NI MES-3980 to be the Ring Master
in a Turbo Ring topology, and enables the Turbo
Ring break warning. If the NI MES-3980 is the
Master of this Turbo Ring, and the Turbo Ring is
broken, the relay will form an open circuit.
MASTER
Off Disables the NI MES-3980 from being the Ring
Master in a Turbo Ring topology, and disables
the Turbo Ring break warning.
On Enables the Turbo Ring Coupling function. Use
ports 5 and 6 of NI MES-3980 to form the Ring
Coupler path.
COUPLER
Off Disables the Turbo Ring coupling function.
On Enables plug-and-play Turbo Ring redundancy.
Ports 7 and 8 of the NI MES-3980 are used to
form a Turbo Ring.
TURBO
RING
Off Disables the plug-and-play Turbo Ring
redundancy function.
NOTE You must enable the Turbo Ring function first before using the DIP
switch to activate the Master and Coupler functions.

—9 —
NOTE If you do not enable any of the NI MES-3980 switches to be the
Ring Master, the Turbo Ring protocol will automatically choose the
NI MES-3980 with the smallest MAC address range to be the Ring
Master. If you accidentally enable more than one NI MES-3980 to
be the Ring Master, the NI MES-3980 switches will auto-negotiate
to determine which one will be the Ring Master.
LED Indicators
The front panel of the NI MES-3980 contains several LED indicators. The
function of each LED is described in the following table.
LED Color State Description
On Power is being supplied to power input
PWR1
PWR1 AMBER
Off Power is not being supplied to power
input PWR1
On Power is being supplied to power input
PWR2
PWR2 AMBER
Off Power is not being supplied to power
input PWR2
On
When (1) a relay warning event is
triggered, (2) the NI MES-3980 is the
Master of this Turbo Ring, and the Turbo
Ring is broken, or (3) start-up failure
FAULT RED
Off When a relay warning event is not
triggered
On When the NI MES-3980 is the Master of
this Turbo Ring
Blinking When the NI MES-3980 is the Ring
Master of this Turbo Ring and the Turbo
Ring gets disconnected
MASTER GREEN
Off When the NI MES-3980 is not the Master
of this Turbo Ring
On When the NI MES-3980 enables the
coupling function to form a backup path
COUPLER GREEN
Off When the NI MES-3980 is not the Ring
Coupler of this Turbo Ring
On TP port’s 10 Mbps link is active
Blinking Data is being transmitted at 10 Mbps
10M GREEN
Off TP Port’s 10 Mbps link is inactive
On TP port’s 100 Mbps link is active
Blinking Data is being transmitted at 100 Mbps
100M GREEN
Off TP Port’s 100 Mbps link is inactive

—10 —
Auto MDI/MDI-X Connection
The Auto MDI/MDI-X function allows users to connect the NI MES-3980’s
10/100BaseTX ports to any kind of Ethernet device, without needing to pay
attention to the type of Ethernet cable being used for the connection. This
means that you can use either a straight-through cable or cross-over cable to
connect the NI MES-3980 to Ethernet devices.
Specifications
Technology
Standards IEEE802.3, 802.3u, 802.3x, 802.1D, 802.1w, 802.1Q,
802.1p, 802.1X, 802.3ad
Protocols IGMP V1/V2/V3 device, GVRP, GMRP, SNMP
V1/V2c/V3, DHCP Server/Client, BootP, RMON,
TFTP, SNTP, SMTP, RARP
MIB MIB-II, Ethernet-Like MIB, P-BRIDGE MIB,
Q-BRIDGE MIB, Bridge MIB, RSTP MIB, RMON
MIB Group 1,2,3,9
Forwarding and
Filtering Rate 148810 pps
Processing Type Store and Forward
Flow Control IEEE802.3x flow control, back pressure flow control
Interface
RJ45 Ports 10/100BaseT(X) auto negotiation speed, F/H duplex
mode, and auto MDI/MDI-X connection
Console RS-232 (RJ45)
LED Indicators PWR1, PWR2, FAULT, 10M, 100M, MASTER and
COUPLER
Relay Contact Two relay outputs with current carrying capacity of
1A @ 24 VDC
DIP Switches Master, Coupler, Turbo Ring, Reserve
Digital Input Two inputs with the same ground, but electrically
isolated from the electronics
• For state “1”: +13 to +30V
• For state “0”: -30 to +3V
• Max. input current: 8 mA
Power
Input Voltage 12 to 45 VDC, redundant inputs
Input Current (@24V) Max. 0.29A
Connection Two removable 6-pin terminal blocks
Overload Current
Protection Present
Reverse Polarity
Protection Present
Mechanical
Casing IP30 protection, metal case
Dimensions 80.5 ×135 ×105 mm (W ×H ×D)
Weight 1.04 kg

—11 —
Installation DIN-Rail, Wall Mounting (optional kit)
Environment
Operating Temperature -40 to 75°C (-40 to 167°F )
Storage Temperature -40 to 85°C (-40 to 185°F)
Ambient Relative
Humidity 5 to 95% (non-condensing)
Regulatory Approvals
Safety UL60950-1, CSA C22.2 No. 60950-1, EN60950-1,
TÜV
Hazardous Location UL/cUL Class I, Division 2, Groups A, B, C, and D
EMI FCC Part 15, CISPR (EN55022) class A
EMS EN61000-4-2 (ESD), Level 2
EN61000-4-3 (RS), Level 3
EN61000-4-4 (EFT), Level 3
EN61000-4-5 (Surge), Level 3
EN61000-4-6 (CS), Level 3
EN61000-4-8
EN61000-4-11
EN61000-4-12
Operating Shock 15 g, half-sine, 11 ms pulse
Operating Vibration 10 Hz to 150 Hz, 1 rms
Technical Support and Professional
Services
Visit the following sections of the National Instruments Web site at ni.com for
technical support and professional services:
• Support— Online technical support resources at ni.com/support include
the following:
Self-Help Resources— For answers and solutions, visit the
award-winning National Instruments Web site for software drivers and
updates, a searchable KnowledgeBase, product manuals, step-by-step
troubleshooting wizards, thousands of example programs, tutorials,
application notes, instrument drivers, and so on.
Free Technical Support— All registered users receive free Basic
Service, which includes access to hundreds of Application Engineers
worldwide in the NI Discussion Forums at ni.com/forums. National
Instruments Application Engineers make sure every question receives
an answer.
For information about other technical support options in your area, visit
ni.com/services or contact your local office at ni.com/contact.
• Training and Certification— Visit ni.com/training for self-paced training,
eLearning virtual classrooms, interactive CDs, and Certification program
information. You also can register for instructor-led, hands-on courses at
locations around the world.
• System Integration— If you have time constraints, limited in-house
technical resources, or other project challenges, National Instruments
Alliance Partner members can help. To learn more, call your local NI office
or visit ni.com/alliance.

—12 —
• Declaration of Conformity (DoC)— A DoC is our claim of compliance
with the Council of the European Communities using the manufacturer’s
declaration of conformity. This system affords the user protection for
electronic compatibility (EMC) and product safety. You can obtain the DoC
for your product by visiting ni.com/certification.
• Calibration Certificate— If your product supports calibration, you can
obtain the calibration certificate for your product at ni.com/calibration.
If you searched ni.com and could not find the answers you need, contact your
local office or NI corporate headquarters. Phone numbers for our worldwide
offices are listed at the front of this manual. You also can visit the Worldwide
Offices section of ni.com/niglobal to access the branch office Web sites, which
provide up-to-date contact information, support phone numbers, email
addresses, and current events.
Worldwide Technical Support and Product Information
ni.com
National Instruments Corporate Headquarters
11500 North Mopac ExpresswayAustin, Texas 78759-3504USATel: 512 683
0100
Worldwide Offices
Australia 1800 300 800, Austria 43 662 457990-0, Belgium 32 (0) 2 757 0020,
Brazil 55 11 3262 3599, Canada 800 433 3488, China 86 21 5050 9800, Czech
Republic 420 224 235 774, Denmark 45 45 76 26 00, Finland 358 (0) 9 725
72511, France 01 57 66 24 24, Germany 49 89 7413130, India 91 80 41190000,
Israel 972 3 6393737, Italy 39 02 413091, Japan 81 3 5472 2970, Korea 82 02
3451 3400, Lebanon 961 (0) 1 33 28 28, Malaysia 1800 887710, Mexico 01
800 010 0793, Netherlands 31 (0) 348 433 466, New Zealand 0800 553 322,
Norway 47 (0) 66 90 76 60, Poland 48 22 3390150, Portugal 351 210 311 210,
Russia 7 495 783 6851, Singapore 1800 226 5886, Slovenia 386 3 425 42 00,
South Africa 27 0 11 805 8197, Spain 34 91 640 0085, Sweden 46 (0) 8 587
895 00, Switzerland 41 56 2005151, Taiwan 886 02 2377 2222, Thailand 662
278 6777, Turkey 90 212 279 3031, United Kingdom 44 (0) 1635 523545
For further support information, refer to the Cross referenceolor:Blueparatext
appendix. To comment on National Instruments documentation, refer to the
National Instruments Web site at ni.com/info and enter the info code feedback.
© 2007 National Instruments Corporation. All rights reserved.
Table of contents
Other NI Switch manuals
Popular Switch manuals by other brands
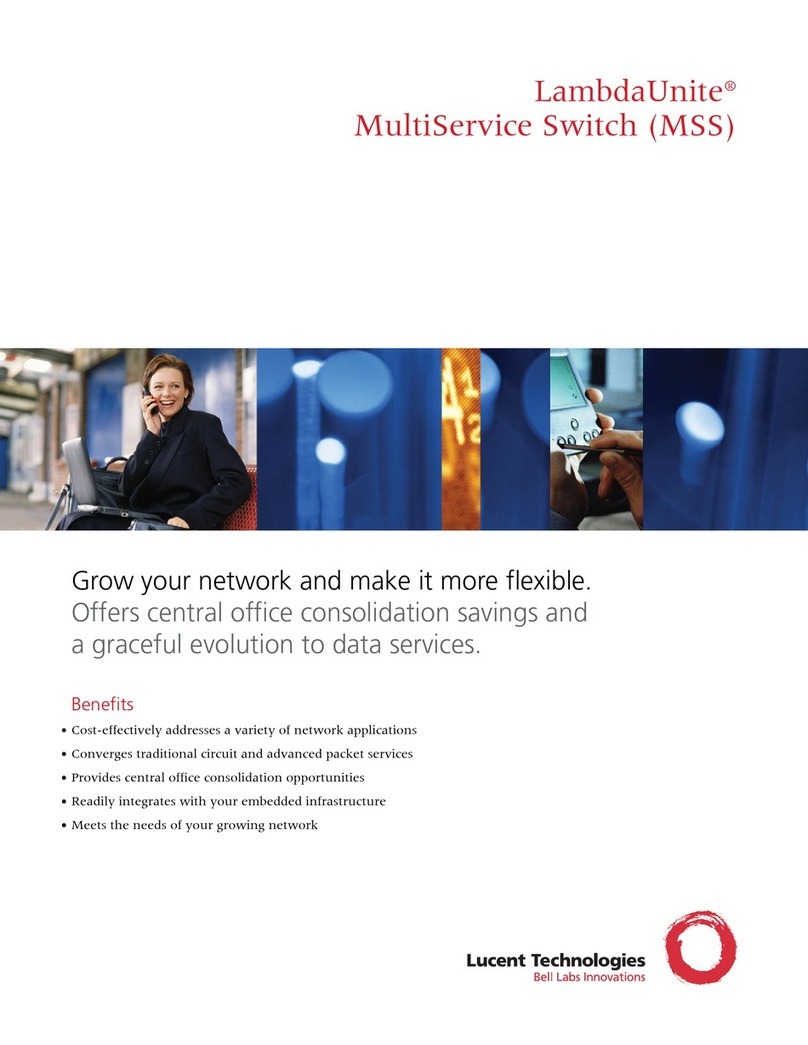
Lucent Technologies
Lucent Technologies LambdaUnite brochure
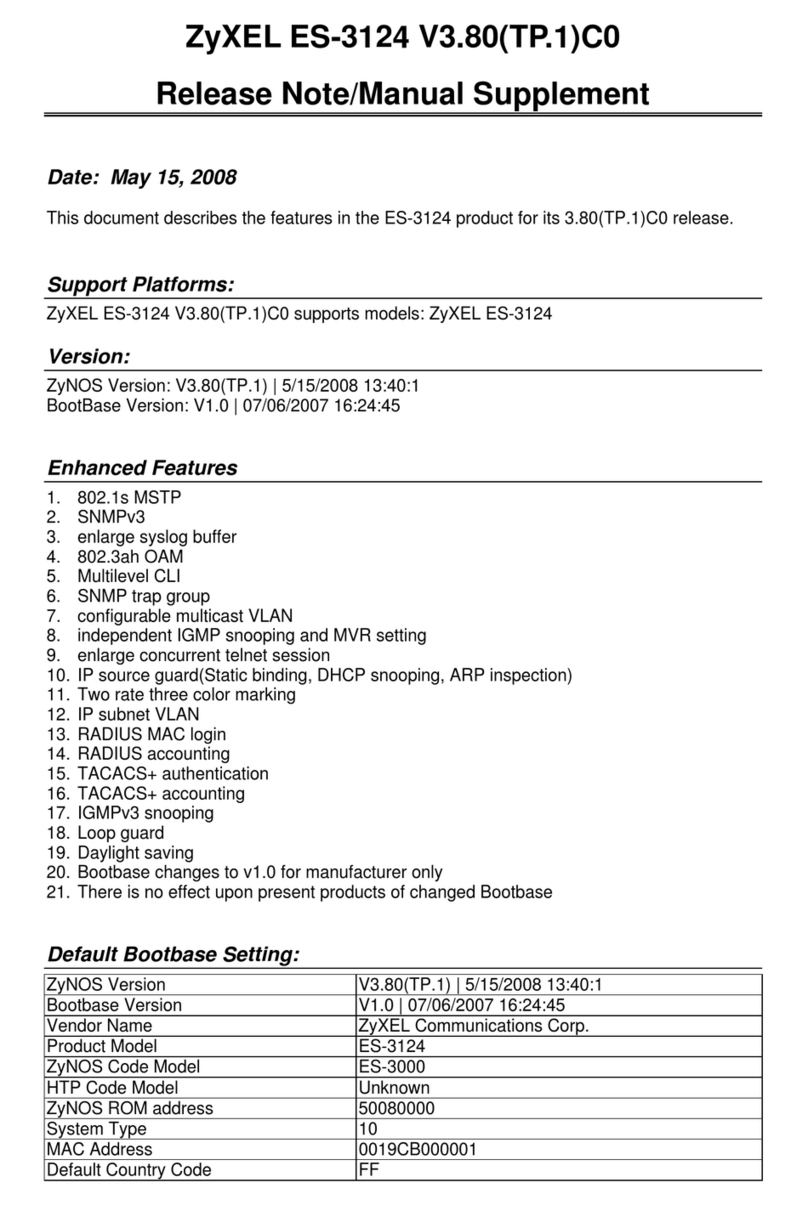
ZyXEL Communications
ZyXEL Communications Dimension ES-3124 release note
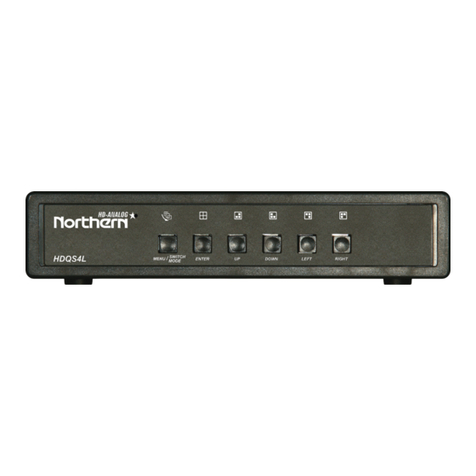
Northern
Northern HDQS4L Installation instructions manual
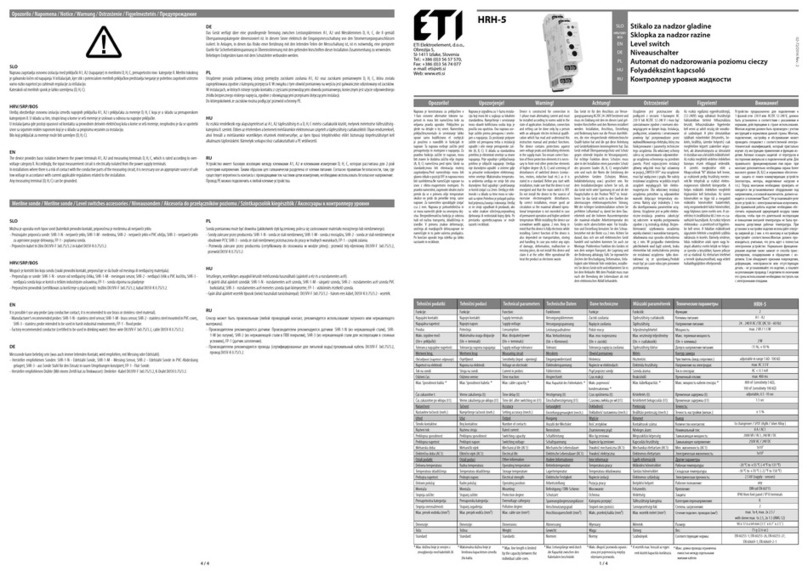
ETI
ETI HRH-5 manual
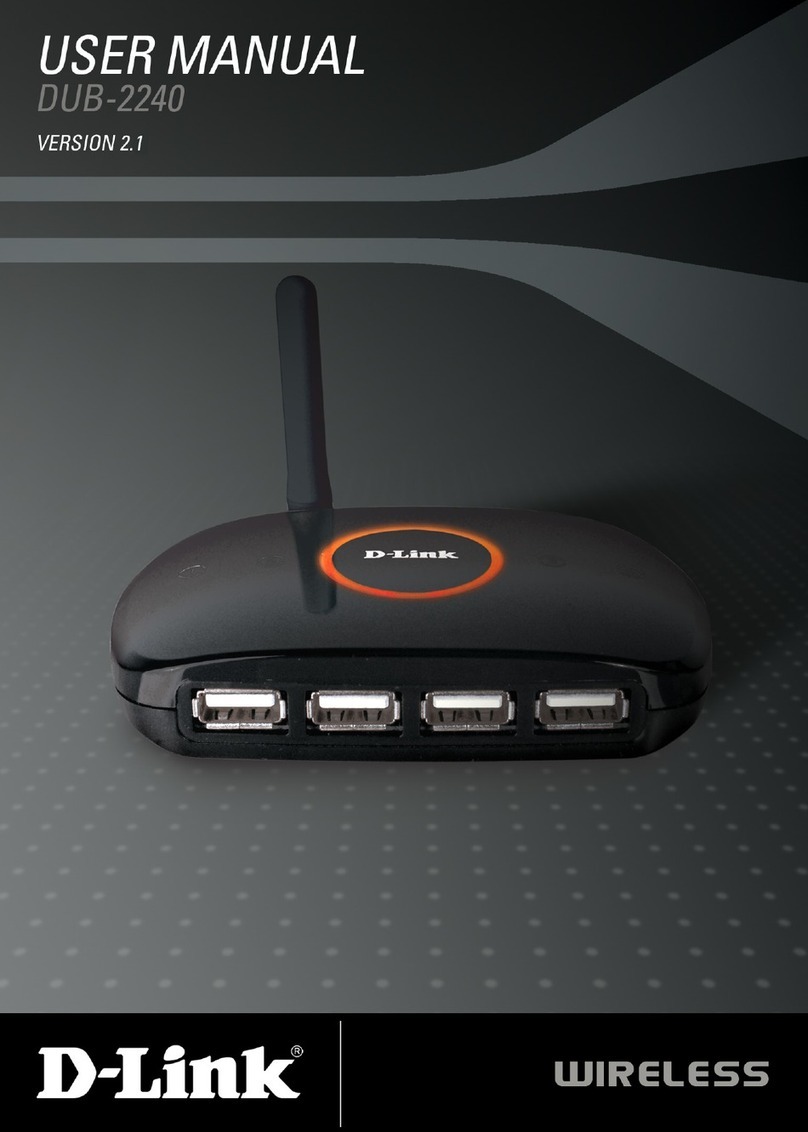
D-Link
D-Link DUB-2240 - Wireless USB Hub user manual
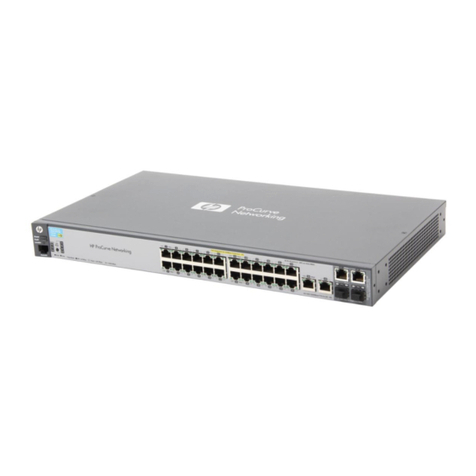
HP
HP ProCurve 2520-24-PoE supplementary guide