NoiseKen ISS-7650 User manual

INSTRUCTIONMANUAL
AUTOMOTIVE TRANSIENT
SURGE SIMULATOR
MODEL
ISS-7650
Noise Laboratory Co., Ltd.
Edition 2.00
AEJ00339-00E-1-E

NOTICE
•
The contents of this instruction manual (the “Manual”) are subject to change without
prior notice.
•
No part of the Manual may be reproduced or distributed, in any form or by any means,
without the authorization of Noise Laboratory Co., Ltd. (the “Company”).
•
The contents of the Manual have been thoroughly examined. However, if you find
any problems, misprints, or missing information, please feel free to contact our sales
agent who you purchased our product from.
•
The Company assumes no responsibility for any loss or damage resulting from
improper usage, failure to follow the Manual, or any repair or modifications of this
product undertaken by a third party other than the Company or the agent authorized by
the Company.
•
The Company assumes no responsibility for any loss or damage resulting from
remodeling or conversion solely undertaken by the user.
•
Please note that the Company cannot be held responsible for any consequences
arising from the use of this product.
•
Product names and business names referred to in the Manual are generally
trademarks or registered trademarks of third parties. Those trademarks have nothing to
do with the Company. ® and TM are not always referred to in this manual.

- 1 -
1. IMPORTANT SAFETY PRECAUTIONS
The following instructions are very important for safe handling of ISS-7650 (the “Unit”).
Read them carefully before use.
1. Do not use the Unit near flammable materials or fire sources. When used,
there is a risk of fire due to pulses, etc.
2. Any person with medical electronics such as a heart pacemaker is not to
operate the Unit. And, do not enter the test area while the Unit is operating.
3. To avoid electric shock, be sure that the power of the Unit, the power source,
and the device under test ("DUT") are all turned OFF, and make sure there is
no residual voltage before making any connections.
4. A number of safety recommendations are listed in the later chapter "BASIC
SAFETY PRECAUTIONS". Be sure to read them before test environment
settings, connecting and testing.
5. A powerful magnetic field is generated by the Unit at the time of pulse
output. Give careful consideration to your testing environment to use the
Unit.
6. Do not touch AC power voltage switch terminals or external output terminals.
There is a risk of electric shock.

- 2 -
Memorandum

- 3 -
2. APPLICATION FORM FOR INSTRUCTION MANUAL
We place an order for an instruction manual.
Model: ISS-7650
Serial No.:
Applicant:
Company name:
Address:
Department:
Person in charge:
Tel No.:
Fax No.
Cut off this page “APPLICATION FORM FOR INSTRUCTION
MANUAL” from this volume and keep it for future use with
care.
When an INSTRUCTION MANUAL is required, fill in the above Application Form
and mail or fax it to the following sales department of our company.
To: Noise Laboratory Co., Ltd.
1-4-4 Chiyoda Chuo-ku Sagamihara City,
Kanagawa Pref., 252-0237 Japan
Tel: +81-(0)42-712-2051 Fax: +81-(0)42-712-2050
Cut
line

- 4 -
Memorandum

- 5 -
3. CONTENTS
1. IMPORTANT SAFETY PRECAUTIONS.......................................................................................1
2. APPLICATION FORM FOR INSTRUCTION MANUAL................................................................3
3. CONTENTS ...................................................................................................................................5
4. PREFACE......................................................................................................................................6
5. BASIC SAFETY PRECAUTIONS.................................................................................................7
5-1.
S
YMBOLS OF
H
AZARD
........................................................................................................... 7
5-2.
B
ASIC
S
AFETY
I
NSTRUCTIONS
............................................................................................... 7
5-3.
L
OSS OF
W
ARNING
L
ABEL
..................................................................................................... 8
6. MAIN FEATURES .........................................................................................................................9
6-1.
D
ISTINCTIVE
F
EATURES
........................................................................................................ 9
6-2.
S
CHEMATIC
C
IRCUIT
D
IAGRAM OF THE
U
NIT
........................................................................ 10
6-3.
R
EGARDING
DC
I
NJECTION
C
IRCUIT
.................................................................................... 11
6-4.
R
EGARDING
ISO
7637-2
(S
ECOND EDITION
2004-06-15).................................................... 13
7. PART NAMES AND FUNCTIONS..............................................................................................15
8. TEST PROCEDURES .................................................................................................................22
8-1.
P
RE
-O
PERATION
C
HECK
..................................................................................................... 22
8-2.
V
ARIOUS
S
ETTINGS
............................................................................................................ 23
8-3.
S
TARTING AND
F
INISHING
T
EST
........................................................................................... 24
9. REMOTE CONTROLLING BY PC..............................................................................................26
9-1.
P
REPARATION
..................................................................................................................... 26
9-2.
H
ARDWARE
S
ETUP
............................................................................................................. 26
9-3.
I
NSTALLING THE
S
OFTWARE
................................................................................................ 27
9-4.
I
NSTALLING
R
EMOTE
C
ONTROL
S
OFTWARE
......................................................................... 27
9-5.
I
NSTALLING
S
ERIAL
P
ORT
D
RIVERS
(A
T THE TIME OF
S
TAND
-
ALONE
U
SE
)............................. 27
9-6.
U
SING
R
EMOTE
C
ONTROL
S
OFTWARE
................................................................................. 27
9-7.
T
URNING
O
FF THE
R
EMOTE
C
ONTROL
S
OFTWARE AND THE
U
NIT
......................................... 27
10. SPECIFICATIONS.....................................................................................................................28
10-1.
S
PECIFICATIONS
C
OMMON TO
P
ULSE
5
A
/
5
B
..................................................................... 28
10-2.
P
ULSE
5
A
......................................................................................................................... 29
10-3.
P
ULSE
5
B
......................................................................................................................... 29
11. WAVEFORM VERIFICATION...................................................................................................30
12. ACCESSORIES.........................................................................................................................32
13. OPTIONS...................................................................................................................................33
14. WARRANTY..............................................................................................................................34
15. MAINTENANCE.........................................................................................................................36
16. NOISE LABORATORY SUPPORT NETWORK.......................................................................37

- 6 -
4. PREFACE
ThankyouverymuchforpurchasingISS-7650(the"Unit").Pleasereadthisinstructionmanual(the
"Manual")thoroughlypriortouseoftheUnitinordertoattainthemaximumandsafeuseofthe
Unit.
RemoteControlSoftwaretocontroltheUnitbyaPCisalsoattached.
When you control the
Unit through the software, please read the instruction manual of Remote Control
Software thoroughly in addition to the Manual to ensure safety and correct procedures
The Manual will let you operate ISS-7650 safely and make the most use of it if you
strictly follow the operational procedures and the safety instructions.
Keep the Manual handy whenever you operate ISS-7650.

- 7 -
5. BASIC SAFETY PRECAUTIONS
5-1. Symbols of Hazard
This sign indicates the presence of "dangerous voltage/current" that may endanger
persons.
This sign indicates "handle with care".
Refer to the Manual to protect human bodies and devices.
This sign indicates a protective ground terminal.
This sign indicates a connection to FG (steel case).
5-2. Basic Safety Instructions
1. The Unit is grounded by the three line AC cord with a grounding conductor. To avoid
electric shock, be sure to insert it to an outlet with a ground terminal.
【
【【
【
Precautions regarding connection and use
】
】】
】
2. Use the AC cord which matches the source voltage, as the shape of the AC cord differs
depending on the source voltage.
【
【【
【
Precautions regarding connection and use
】
】】
】
3. When changing fuses, choose the same melt off type and rating. Also, be sure to unplug
the AC chord before changing fuses.
【
【【
【
Precautions regarding use and safety
】
】】
】
4.
Do not supply the Unit with voltage or overload beyond the specification range. The Unit
may be damaged if this is not obeyed.
【
【【
【
Precautions regarding connection and use
】
】】
】
5. Use the input and output cables which meet the current and power capacity
requirements.
【
【【
【
Precautions regarding connection and use
】
】】
】
Indication of Warning
The following warning indication is placed on
the upper left of the rear-panel of the Unit, and
alerts a risk of electric shock.

- 8 -
6. Before connecting the Unit, turn OFF the DC power source and the Unit, and make sure
that there is no residual voltage. Connect each cable securely. Nonobservance may cause
electric shock or damage to the internal parts of the Unit and connected devices.
【
【【
【
Precautions regarding bodily injury and connection
】
】】
】
7. When a protective cover, etc. of the Unit is removed for connection to the Unit, be sure to
place the protective cover before supplying electricity. There is a risk of short circuiting or
electric shock.
【
【【
【
Precautions regarding connection and use
】
】】
】
8. Use accessories and optional items supplied by the Company to ensure safe operation.
【
【【
【
Precautions regarding connection and use
】
】】
】
9. Do not open the Unit's cover, as voltages are generated within the Unit's enclosure,
【
【【
【
Precautions regarding bodily injury
】
】】
】
10. Do not block any ventilation openings of the Unit.
【
【【
【
Precautions regarding environment
】
】】
】
11. Do not utilize or store the Unit under extremely high or low temperature
environment.
(Operating environment
:
::
:
23
℃±
℃±℃±
℃±
5
℃
℃℃
℃
/ Operating Humidity Range
:
::
:
25 - 75 %)
【
【【
【
Precautions regarding environment
】
】】
】
12. Do not use the Unit under high humidity or dusty conditions.
【
【【
【
Precautions regarding environment
】
】】
】
13. Should condensation form, fully dry the Unit before usage.
【
【【
【
Precautions regarding environment
】
】】
】
14. Do not wipe the body of the Unit with solvents such as lacquer thinner or alcohol. When
the Unit gets dirty, wipe it with a detergent moistened fabric etc.
【
【【
【
Precautions regarding use
】
】】
】
15. Do not use the Unit near flammable materials or fire sources. When used, there is a risk
of fire due to electric discharge, etc.
【
【【
【
Precautions regarding bodily injury and environment
】
】】
】
16. The Company and its sales agent assume no responsibility for any bodily injury, loss,
damage or resultant damage arising from derelict misuse of the Unit on the part of the
user.
【
【【
【
Precautions regarding bodily injury, use, environment, and connection
】
】】
】
17. Should the necessity of services such as repair, maintenance, or internal calibration
arise, leave them to qualified service personnel only.
【
【【
【
Precautions regarding use and safety
】
】】
】
18. The Unit has a heavy load. Install it in the place possessing adequate strength. When
moving the Unit, confirm the safety of the surrounding area, and more than one person
should move it. Use casters etc. to fix the Unit after moving. Moving or falling down of
the Unit may cause injuries.
【
【【
【
Precautions regarding use and safety
】
】】
】
5-3. Loss of Warning Label
1. If the warning label is peeled off and missing or it gets dirty, replace it with a new one for safety.
2. If the warning label is lost, order a new one from our sales agent or the Technical Service Center of
the Company.

- 9 -
6. MAIN FEATURES
6-1. Distinctive Features
Capable of performing tests of Test Pulse 5a/5b in accordance with ISO/DIS
7637-2.2(2002-07-16), ISO/DIS 7637-2.3 (2003-05-20), and ISO7637-2 (Second edition
2004-06-15).
Capable of detailed configuration of output wave voltage, pulse width, and device resistance.
・
Pulse 5a output voltage is variable from 20V to 200V in steps of 0.5V.
・
Pulse 5b output voltage is variable from 10.0V to 40.0V in steps of 0.1V.
・
Pulse widths of 40ms, 100ms, 200ms, 350ms, 400ms.
・
Output resistance Ri is variable from 0.5
Ω
to 8.0
Ω
in steps of 0.5
Ω
.
Capable of producing Pulse 5b clipped waveform without externally attaching a zener diode.
Pulse 5b clipped waveform is pre-eminent in evenness.
The maximum DUT (Device Under Test) capacity is 60V 30A.
Capable of selecting DC injection methods (See Figure 2).
Capable of performing tests under harsher conditions than the Standards (to max 999 repetitions
in sequence).
A buzzer begins to ring 5 seconds before pulse output.
The waveform at the time of 2
Ω
connection with output terminals(ISO Standard Annex D)is
ensured.
Allows oscilloscope observation of the current waveform flowing into DUT. Current and voltage
waveforms can be examined at the same time with an oscilloscope because the current monitor
output circuit is floating off from SG and FG. Voltage waveform is measurable from DC.
Output terminals are the electric shock free safety plugs which protect against electric shock.
Compatible with AC Input driving voltage of 100V, 110V, 120V, 200V, 220V, and 240V by a
jumper switch on the rear panel.
Capable of creating test conditions not limited to the Standards by utilizing optional Remote
Control Software. Also capable of running user defined sequential tests (sequence) combining
various test settings.
Capable of noise unsusceptible stable transmissions by using an optional Optical Interface Unit
and Remote Control Software for the purpose of communication between ISS-7650 and the PC
(when used standalone without mounting to a rack),
An optional ISS-7690 is capable of integrated pulse output when the Unit is installed onto
System Rack ISS-7602 (Optional). The optional 50A type ISS-7690 can expand DUT capacity to
60V max, 50A max.

- 10 -
6-2. Schematic Circuit Diagram of the Unit
The schematic circuit diagram of the Unit is shown in Figure 1. The basic action is that the
charge collected in capacitor C flows through internal resistance Ri and DUT connected between
Output Terminals HOT-GND, and return to C when SW is turned ON.
Figure 1 Schematic Circuit Diagram
・
Output resistance Ri is the sum of R1 and direct current resistance R0 of L.
・
When Pulse 5b is selected, ZD is connected and the waveform clipped at configured voltage
will be output. ZD mounts the circuitry that has functions equivalent to a zener diode.
・
Current Monitor Output lets you measure the current flowing to DUT. Current and voltage
waveforms can be examined at the same time with an oscilloscope because the current
monitor output circuit is floating off from SG and FG.
・
You can select either serial or parallel DC Injection. An example of waveform output is
shown in Figure 2. By short-circuiting D3, SG and FG electric potential becomes the same,
and allows more stable waveform output.
・
DC input is controlled by DC ON/OFF Switch. Take caution, as the input DC voltage is
output to the Output Terminals when the switch is ON.
(
In compliance with ISO Standards
)
Figure 2
DC Injection Method

- 11 -
6-3. Regarding DC Injection Circuit
For the purpose of ISO complied serial injection, short circuit Serial and COM of DC Injection in
Figure 1. To input DC, DC source is connected to DC INPUT. The following explains the pulse
current flow in this state referring to the figure below.
C
L
R2
R1
0Ω~7.5Ω
10V~40V
SHORT:5b0.5Ω
R0 Ri=R0+R1
SURGE OUTPUT
GND
+
-
DC INPUT
G
SG
HOT
Current Monitor Output
SW
ZD
D1
D3
D2
G
DC Power Supply
EUT
Surge Current 150A max
N B
Figure 3
DC Input Serial Injection
1.
When SW contactor is connected, the charge stored in capacitor flows through the
circuit as pulse current.
2.
Pulse current going out of HOT Terminal flows through DUT to GND Terminal.
3.
As SG electric potential is the same as DC input, pulse current is not able to flow
through D3 and flows to the bottom of the schematic circuit and reaches Negative
Terminal of DC INPUT.
4.
Pulse current is output from the positive Terminal of DC Power Supply.
5.
Pulse current will eventually return to the capacitor.
At this point, pay attention to DC Power Supply current-carrying capacity. Pulse current fluctuates
depending on DUT impedance and the Unit settings, and it can reach up to 150A. Because of this,
it is recommended that tests be performed with DC Power Supply which can manage this much
current flow. Note that DC Power Supply may be destroyed if tests are performed by low capacity
DC Power Supply.
When DC Power Supply contains an over current protection circuit, the circuit might work. But it
may result in reduction of DC Power Supply output voltage, and may cause deviation of injected
pulse waveform voltage + DC voltage from the Standards. An example follows.

- 12 -
The Unit setting (Pulse 5b) is as follows;
Uss
:
40.0V Us
:
200V
Ri
:
1
Ω
td
:
400ms
The injection method is serial.
Connecting the external DC Supply (with the maximum 60A over current protection circuit) to DC
Input Terminal with the voltage of 27V, the two figures below gives the waveform difference
between the open Output Terminal and 0.9
Ω
load.
Figure 4
DC Serial Injection Waveforms (left: Output Open, right: Output 0.9
Ω
ΩΩ
Ω
Load)
When the output is open (Figure 4 left), no current flows through output HOT-GND and DC Power
Supply, DC Supply outputs +40V.
When output is 0.9
Ω
(Figure 4 right) with the pulse voltage 40V and DC Supply voltage 27V, the
current flowing into DC Power Supply makes (40 + 27) / 0.9
≒
74.4(A), which exceeds the current
capacity 60A of DC Supply. The waveform shows that the DC Source over current protection circuitry
is working and dropping the voltage. As 40V is injected onto the decreased voltage, the output
voltage is lowered.
To correct this problem, change DC Power Supply to a battery or change injection method to parallel
injection.
DC Source Voltage (27V)
Output Voltage (Pulse
+
DC)

- 13 -
6-4. Regarding ISO 7637-2 (Second edition 2004-06-15)
ISO7637-2 (Second Edition 2004-06-15) specifies the standard relevant to the transient pulse
simulator for in-vehicle devices. This standard specifies the configurations of the test, the pulse
voltage waveforms, the testing voltage level and the testing environment, etc. The Unit is capable
of performing tests in accordance with this standard. The schematic test setup is excerpted from
the standard and shown below. For details, be sure to refer to the ISO Standards.
a)Pulse adjustment
8
1
2
3
65
74
Figure 5
Test Configuration (For Pulse Veification)
When verifying the Unit waveform, do not connect DUT to output and leave the output open. Turn
DC LINE ON (Circuit Breaker is also ON), short circuit DC INPUT
+
and
-
terminals with the
accessory Short Lead Cable (for Waveform Verification), and set the injection to serial injection.
The standards for the output waveform under this condition is shown below. The standards for
Pulse 5a with 2
Ω
connected to Output Terminals is specified in Annex D. The parameters are
also given.
The standard provides the following;
(1)
Pulse 5a Output Open (Top of Table 1
)
(2)
Pulse 5a Output with 2
Ω(
Annex D
)
(Bottom of Table 1)
(3)
Pulse 5b Output Open (Table 2, td is the same as td of Pulse 5a Output Open)
The current flow changes dramatically compared with Pulse 5a Output Open, and td always
changes when zener diode is connected to the Unit output as shown in Figure 5, This standard
contains inconsistency, and it is not possible to realize the waveform (3) specified in the
standard under the Figure 5 configuration. A test set-up other than a zener diode connection to the
output must be used to output waveform satisfying (3).
The Unit is designed according to Figure 5 configuration, which models the conditions of real
vehicles. Please note td shown in Table 2 cannot be realized for this reason.

- 14 -
Pulse 5a Waveform Standard (ISO 7637-2 (Second edition 2004-06-15))
td
tr
U
s
10%
90%
0V
U
A
Figure 6
Pulse 5a Waveform
Table 1
Pulse 5a Parameters
Parameters
12V
System
24V
System
Output
Open
Us
65V~87V
123V~174V
Ri 0.5
Ω
~4
Ω
1
Ω
~8
Ω
t
d
40ms~400ms
100ms~350ms
t
r
10ms
–
5ms/+0ms
10ms
–
5ms/+0ms
Annex D
Us 50V
±
10V 100V
±
20V
td 200ms
±
40ms 175ms
±
35ms
t
r
Not Specified
Not speci
fied
Annex D Requirements
・
12V System (UA=0V, td=400ms, Ri=2
Ω
, Us=100V, Output=2
Ω
Load)
・
24V System (UA=0V, td=350ms, Ri=2
Ω
, Us=200V, Output=2
Ω
Load)
Pulse 5b Waveform Standard (ISO7 637-2 (Second edition 2004-06-15))
td
tr
U
s
10%
90%
0V
U
①
②
U
s
s
A
Figure 7
Pulse 5b Waveform
Table 2
Pulse 5b Parameters
Parameter
12V
System
24V
System
Us
65V~87V
123V~174V
Uss
As specified by customer
T
d
Same as uns
up
pressed value
①
Unsuppressed (Us)
②
Suppressed (Uss)

- 15 -
7. PART NAMES AND FUNCTIONS
Unit (ISS-7650)
Figure 8 Front View
Figure 9
Rear View
②
Power
Switch
①
Control
Panel
⑦
DC Input
Terminals
⑥
DC Injection Method
Selection Terminals
③
Current Monitor
Output
④
Output Terminal
HOT Side
⑤
Output Terminal
GND Side
⑨
Ventilation
Holes
⑩
AC Input
(with
Internal Fuse)
⑪
Protective
Conductor
Terminal
⑫
AC Input Voltage Selection
Terminals
⑮
Communication
Terminals
⑰
Interlock Terminal
⑬
Ventilation Fan
⑧
Circuit Breaker
Warning Lamp
Terminal
⑯
External Output
Port

- 16 -
①
Control Panel
The “Control Panel” lets you set local settings.
Figure 10
Control Panel
A Us / Uss Display
The “Us / Uss Display” displays either Us or Uss value. It shows Us value when P5a is
chosen. It shows Uss value when P5b is chosen and “FUNCTION F” is not lit, and it shows
Us when P5b is chosen and “FUNCTION F” is lit. When START Button is pressed, the
monitor forcefully displays Us ( P5a) or Uss ( P5b). (FUNCTION light is unlit). As shown in
Figure 6 and Figure 7, Us for Pulse 5a is the actual output voltage, and Uss for Pulse 5b is
the actual clipping voltage. Also, Us value for Pulse 5b is the virtual open voltage.
Therefore, Us for both Pulse 5a and Pulse 5b gives the same waveform, and the Unit
shows the value in conjunction with the waveform. When Ri is 0.5
Ω
or td is 40ms, the
maximum voltage of Us is 100V. To set it above 101V, set Ri larger than 1
Ω
and td larger
than 100ms.
B COUNT / Ri Display
The “COUNT / Ri Display” displays either COUNT or Ri value. It shows COUNT when
FUNCTION is not lit and Ri when lit. When START Button is pressed, (FUNCTION light
goes off and) the monitor forcefully displays COUNT. COUNT is the number of sequential
output under the same setting. It can be set from the minimum 1 to the maximum 999.
Every time a pulse is output during testing, this value will decrease by 1 indicating the
remaining number of pulse out put. When the remaining count becomes “0,” the test is
complete, and the Unit enters STOP mode. Ri is the Unit’s output resistance. It can be set
from 0.5
Ω
to 8.0
Ω
in steps of 0.5
Ω
, but Us of Pulse 5a or Pulse 5b must be below 100V
to set it to 0.5
Ω
.
A
Us / Uss Display
B
COUNT / Ri Display
C
INTERVAL / td Display
D
UP / DOWN Buttons
E
SELECT Button
F
FUNCTION Button
H
DC LINE Button
K
Warning Lamp
G
Pulse 5a / 5b Buttons
I
START Button
J
STOP Button

- 17 -
C INTERVAL / td Display
The “INTERVAL / td Display” displays either INTERVAL or td value. It shows INTERVAL
when FUNCTION is not lit and td when lit. When START Button is pressed, (FUNCTION
light goes out and) the monitor forcefully displays INTERVAL, and it counts down the time
remaining for pulse output every second.
INTERVAL is the time from START to actual pulse output. It can be set between the
minimum 30s to the maximum 999s. In repetition tests, it is the interval between
successive pulse output. For example, if INTERVAL is set to 30s and COUNT is set to 3,
the outputs will be timed as shown in Figure 11.
Figure 11
Pulse Output Timing
D UP / DOWN Buttons
The “UP / DOWN Buttons” raise or lower the value displayed in the currently selected
display. Keeping holding the button down will accelerate the value increment/decrement.
Even if you try to set the value beyond the allowable range, it stops at the moment it
reaches the limit.
E SELECT Button
The “SELECT Button” lets you select one of the three row displays. The selected display
repeats blinking. Every time the button is pressed, the selected row will change from row1
→
row 2
→
row 3
→
row 1.
F FUNCTION Button
The “FUNCTION Button” lets you change the displays as follows:
When this button is not lit, the values displayed for P5a are from the top Us, COUNT, and
INTERVAL. When it is lit, the display will be no display, Ri, and td.
When this button is not lit, the values displayed for P5b are from the top Uss, COUNT, and
INTERVAL. When it is lit, the displays are Us, Ri, and td.
When START Button is pressed, FUNCTION Button lamp goes off, and the displays are
forcefully changed to Us (Uss for P5b), COUNT, and INTERVAL. During START mode,
holding down this button will light the lamp and “no display (Us for P5b), Ri, td” values can
be confirmed.
G P5a Button, P5b Button
The “P5a Button, P5b Button” let you switch the output waveform between Pulse 5a and
Pulse 5b. The waveform of the lit button will be output. ZD in Figure 1 is connected when
START Button is pressed while P5b Button is lit. ZD is not connected in STOP mode even
if P5b button is blinking.
START Pulse 1 Pulse 2 Pulse 3
30s 30s 30s

- 18 -
H DC LINE Button
The “DC LINE Button” serves as the switch to control DC output, and moves the DC
ON/OFF electromagnetic contactor in Figure 1. It is OFF immediately after the Power
Switch is turned ON. When the button is turned ON, externally input DC is output from the
HOT output terminal. It works independently of the START Button. You can also turn the
button off in START mode (ON
→
OFF). In this case, the Unit will go into STOP mode,
which is identical to “STOP Button I” pressing.
I START Button
By pressing the “START Button” for 1 second, the Unit will go into START mode keeping
the current settings. When the test is finished or stopped by the STOP button, 5 seconds
of electricity purge time is pre-set, and all the displays are kept lit. When you keep pressing
this button for 1 second during the electricity purge, the Unit will go into standby mode, and
will return to START mode after the purge is complete. Other buttons are functional during
the purge time (except standby mode), and you can modify the settings.
J STOP Button
The “STOP Button” lets you stop START mode (incl. standby mode). At this time, the Unit
will return to STOP mode without outputting pulses from the Output Terminals. As STOP
Button does not work with DC output , DC output is not turned OFF. Turn DC Output
OFF with DC LINE Button.
K Warning Lamp
The “Warning Lamp” turns ON when DC LINE is ON during STOP mode. Be aware that
DC is output from the Output Terminals while the Warning Lamp is ON. Also, it blinks while
the capacitor is charging, and will return to the pre-START mode when charge/discharge is
complete (See the table below).
Table 3
Warning Lamp status
START
/
STOP DC LINE ON/OFF Display
STOP Mode DC LINE OFF Unlit
DC LINE ON Lit
START Mode DC LINE OFF Blink
DC LINE ON Blink
②
Power Switch
The “Power Switch” powers the Unit. When flipped to the right, the power turns ON, and
settings will be displayed on the control panel. The power turns OFF when flipped to the left.
③
Current Monitor Output
The “Current Monitor Output” lets you monitor current flowing to DUT. The current waveform at
10mV/Acan be observed by connecting BNC cable to the oscilloscope and setting input
resistance to 1M
Ω
.An offset current exists in the output. With compensating the offset current
to the 0A as the reference, measure the difference.
Table of contents
Other NoiseKen Switch manuals
Popular Switch manuals by other brands
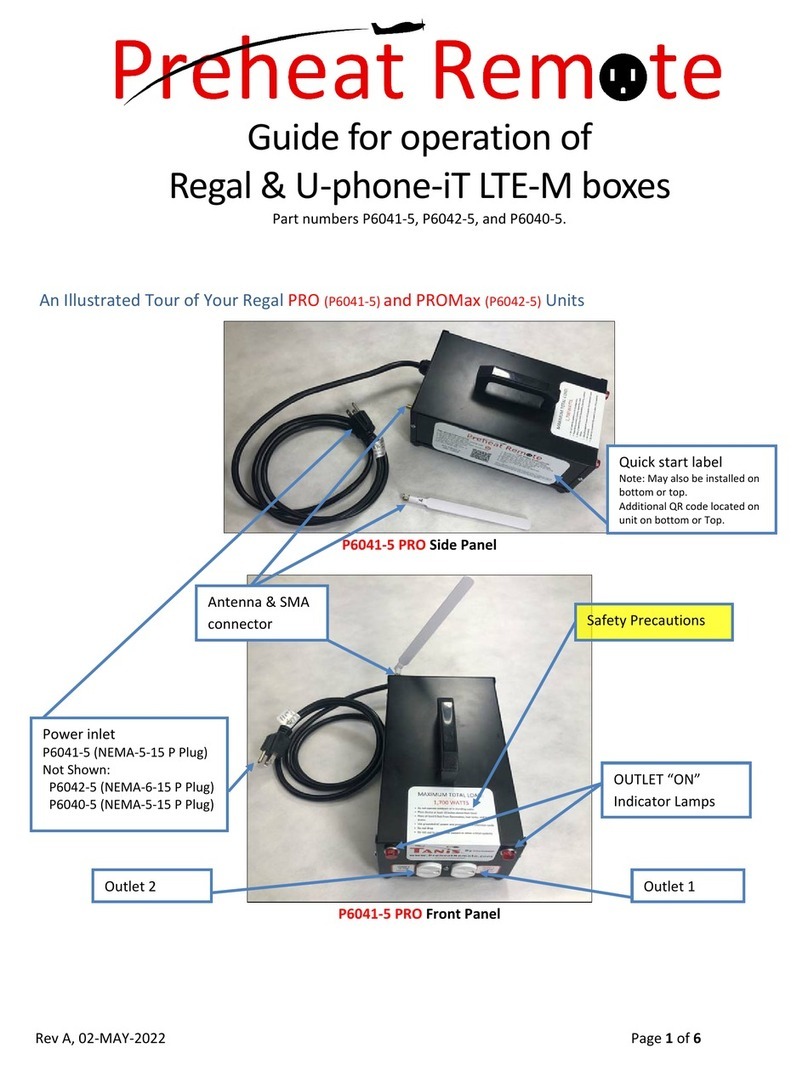
Tanis Technologies
Tanis Technologies Preheat Remote Regal PRO Operation guide
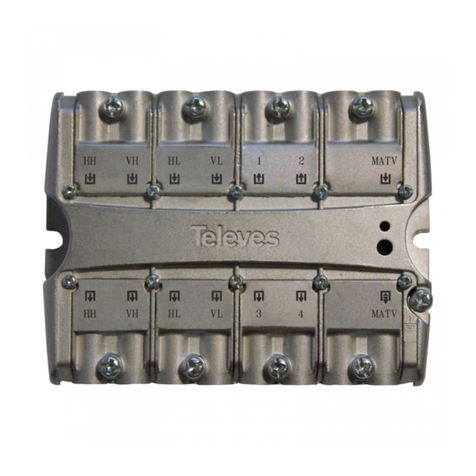
Televes
Televes EasyF user manual
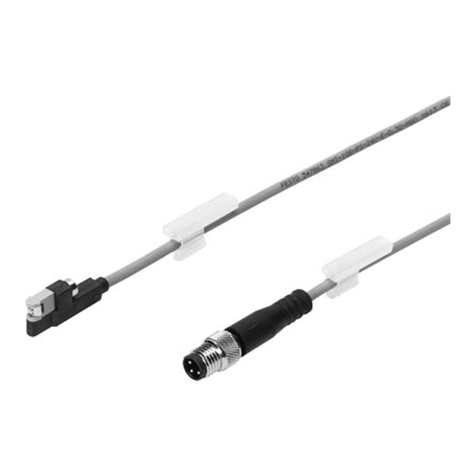
Festo
Festo SMT-10G-...-24V Series manual

steute
steute Ex 61 Mounting and wiring instructions
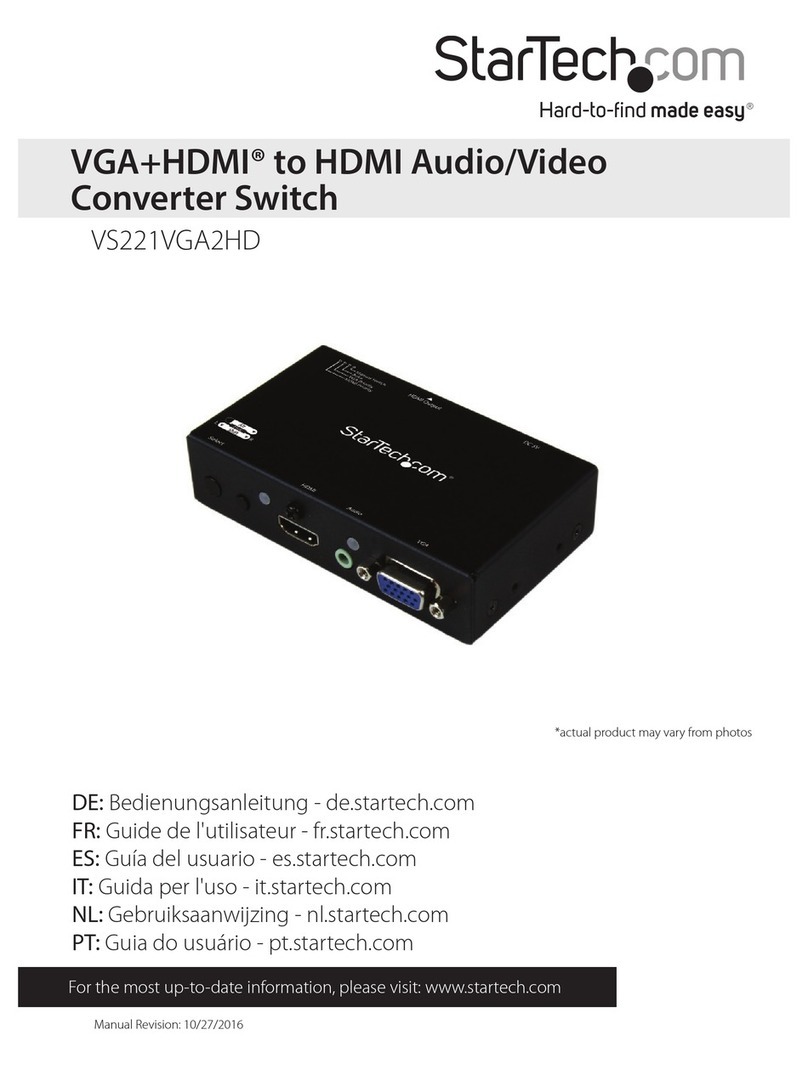
StarTech.com
StarTech.com VS221VGA2HD user guide
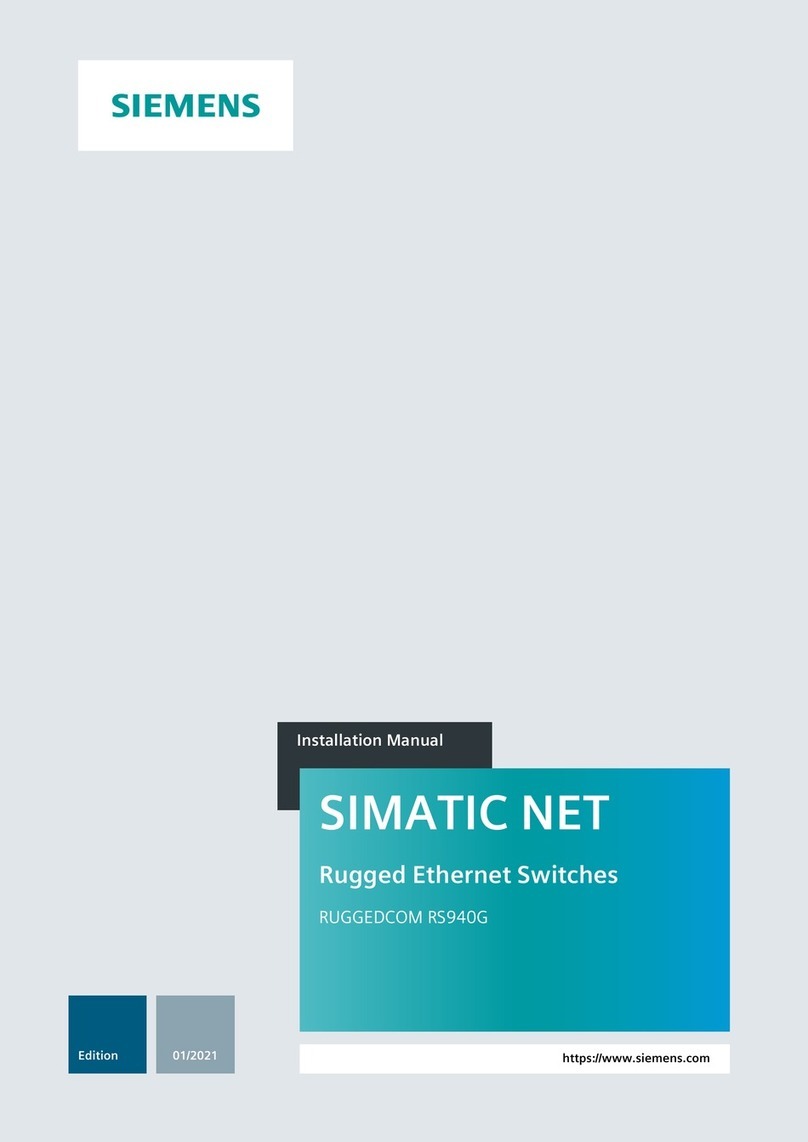
Siemens
Siemens SIMATIC NET RUGGEDCOM RS940G installation manual