Nordberg A2020 User manual

140569
A2020
INSTRUCTION MANUAL
GP Series Cone Crushers
Operator version 3/01

Version 3/01 Page 2/25
TABLE OF CONTENTS
1. General _______________________________________________________________ 4
1.1 Nordberg A2020 ______________________________________________________________4
1.2 User interface ________________________________________________________________4
2. Crusher control ________________________________________________________ 6
2.1 Crusher control display________________________________________________________6
2.2 Selecting operation mode_______________________________________________________6
2.2.1 Manual control mode______________________________________________________________7
2.2.2 Setting control mode ______________________________________________________________7
2.2.3 Load control mode________________________________________________________________8
2.2.4 Feeder control ___________________________________________________________________8
2.2.5 Winter mode ____________________________________________________________________8
2.3 Setting preset values___________________________________________________________8
2.3.1 Setting preset values on Setting control mode___________________________________________8
2.3.2 Setting preset values on Load control mode ____________________________________________8
2.4 Operation data _______________________________________________________________9
2.4.1 Trends _________________________________________________________________________9
2.4.2 Field Data _____________________________________________________________________10
2.5 Alarms_____________________________________________________________________11
2.6 Calibration _________________________________________________________________13
2.6.1 Manual calibration_______________________________________________________________13
2.6.2 Contact calibration_______________________________________________________________14
3. Diagnostics ___________________________________________________________ 14
3.1 Diagnostics display___________________________________________________________14
3.2 Trends _____________________________________________________________________15
3.3 Input and output data ________________________________________________________16
3.4 Starting and stopping crusher__________________________________________________16
3.4.1 Starting lubrication ______________________________________________________________17
3.4.2 Starting crusher _________________________________________________________________18
3.4.3 Starting feeding device ___________________________________________________________18
3.4.4 Stopping feeding device___________________________________________________________18
3.4.5 Stopping crusher ________________________________________________________________19
3.4.6 Stopping lubrication______________________________________________________________19
4. User Setup____________________________________________________________ 19
5. Error/information messages _____________________________________________ 20
5.1 Sensor faults ________________________________________________________________20
5.1.1 Setting ________________________________________________________________________20
5.1.2 Pressure _______________________________________________________________________20
5.1.3 Lubrication oil temperature in tank __________________________________________________21
5.1.4 Crusher lubrication return oil temperature_____________________________________________21
5.1.5 Power_________________________________________________________________________22
5.2 Safety Devices _______________________________________________________________22
5.3 Faults in cables and connectors ________________________________________________23
5.3.1 Crusher control circuit____________________________________________________________23
5.3.2 Feeding device__________________________________________________________________23

Version 3/01 Page 3/25
5.3.3 Lubrication oil heater and cooler control circuits _______________________________________23
5.3.4 Lubrication pump control circuit____________________________________________________23
5.4 System faults________________________________________________________________24
5.5 Error messages concerning software updating and network management _____________24
Appendices
1. Circuit diagrams and connections for A2020
2. Spare parts book

Version 3/01 Page 4/25
Because of the continuous development of the product, the manufacturer reserves a right to alter
the technical specifications written in this manual, without any advance information.
1. General
1.1 Nordberg A2020
The crusher controller A2020 is used for controlling GP and HP crushers. The system
can be installed on fixed and moving plants.
A2020 is a computer system designed for field operation, and it consists of three
decentralised components:
•Display Control Unit (DCU)
•Lubrication Control Module (LCM)
•Process Control Module
1.2 User interface
DCU can be installed either near the crusher or in to the control room. The DCU has
colour display and seven keys which are used for the actual control operations.
Following connections are in the backside of the panel:
•2 x CAN bus
•2 x RS 232
•1 x PS/2 keyboard
•1 x PS/2 mouse
Spare part number
Control keys
Explanation of
control keys
PCMCIA card
under the cover

Version 3/01 Page 5/25
Display screen
The user interface screen is divided into seven windows. The function of the windows is
described below, starting clockwise from the top left corner.
Window 1: Crusher type.
Window 2: Alarms and warnings. The alarm light at left in this window turns red for
alarm and yellow for warning.
Window 3: Operation mode.
Window 4: Preset values.
Window 5: Actual values. At least the values of setting, pressure and power are shown
filtered in the window. The momentary value of capacity is an option.
Window 6: Menu.
Window 7: Main menu. The window specially activated by the user, with different
contents in each screen.
The controlling system starts up when power is switched on. The main menu is always
shown after start-up. The main menu contains the following submenus:
F1: Crusher control. Essential functions for controlling and monitoring the process.
F2: Diagnostics. Monitoring of sensor and actuator condition, diagnostics routines, and
start/stop routines.
F3: System parameters. Device and user parameters.

Version 3/01 Page 6/25
2. Crusher control
2.1 Crusher control display
To enter the crusher control display, press F1 in the main menu. In the crusher control
display you can choose operating mode; preset values; alarm, warning, and event data;
and calibrating functions.
The crusher control screen shows the following functions:
•Arrows describing increasing or decreasing of setting
•Lubrication oil temperature. The temperature may be low (blue), OK (black), or high
(red).
•Running mode messages for discharge conveyor, lubrication, crusher and feeding
device.
2.2 Selecting operation mode
Operation modes: manual control, setting control, and load control.
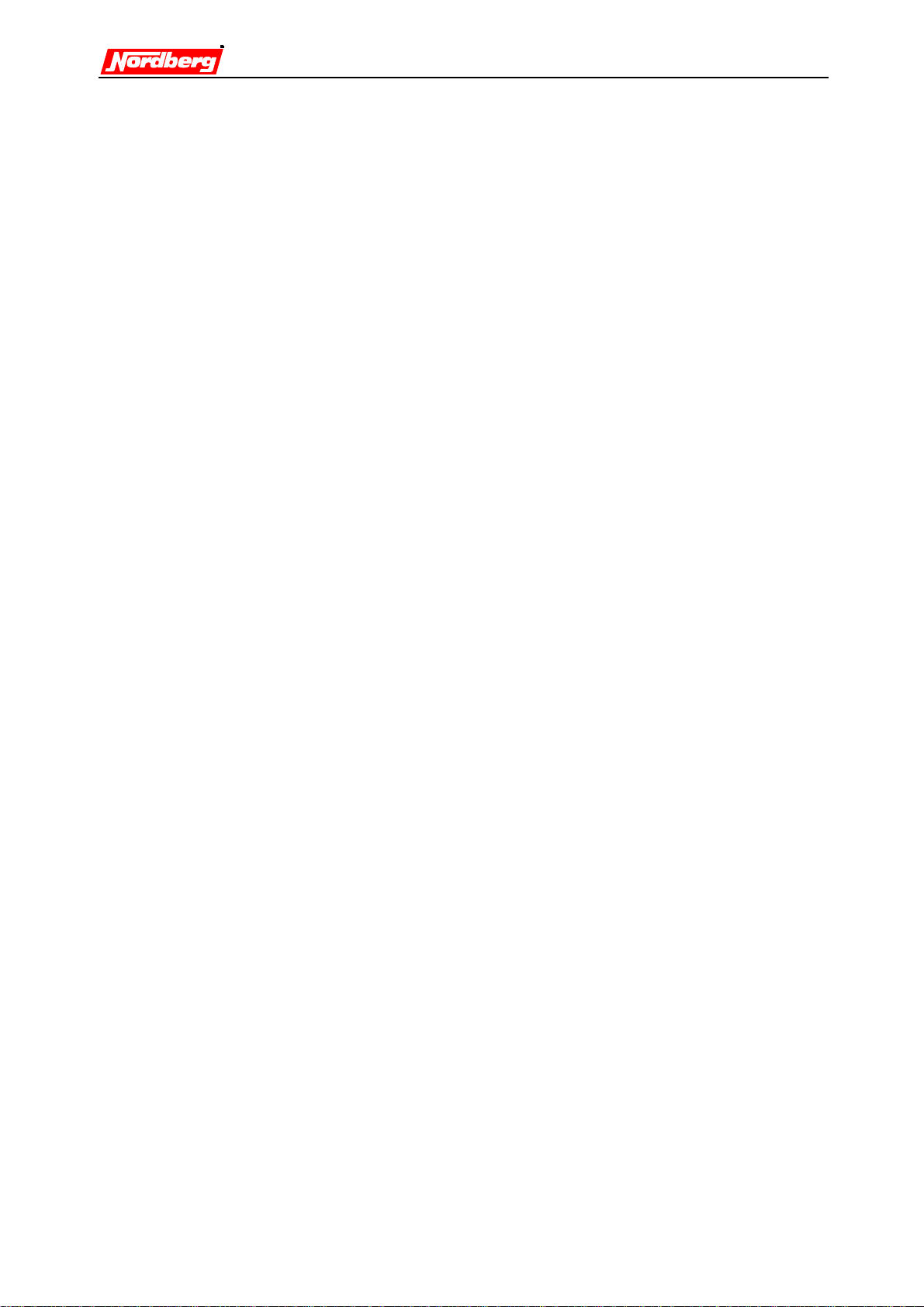
Version 3/01 Page 7/25
2.2.1 Manual control mode
On manual mode crusher can be started and stopped in sequence by using start/stop
push-buttons via Nordberg A2020. Nordberg A2020 goes to manual control mode
when manual control mode is selected by operator or automatically if Nordberg
A2020 system manager does see a loss of DCU <--> PCM/LCM communication for
longer than 2 minutes. Manual control mode may also be forced by system as a result
of serious fault on control modes.
Manual control mode does not require DCU operation and is therefore an operation
mode to secure continuous operations of the crusher even on a DCU breakdown
situation.
NOTE! In case of DCU breakdown or loss of communication no performance
recording is made during the time of breakdown or loss of communication.
All safety limits and interlockings etc. are always operative according to the parameter
setup on manual control mode.
Selecting manual control
•Enter crusher control display (press F1 in main menu).
•Select OP. MODE (press F1).
•Choose the manual control alternative by moving the highlighted line (F5 up, F6
down). F2 gives you more information.
•Accept your choice (press F1).
The selected operation mode is shown in the operating mode window. Press F7 to exit.
2.2.2 Setting control mode
On setting control mode, the crusher controller compares the actual value of setting with
the preset value given. If the preset and actual value difference is bigger than hysteresis
(hysteresis value is set in the configuration), setting is changed until difference is less
than hysteresis value.
If the limit value of maximum pressure or maximum power is exceeded, the controller
increases the setting until the pressure and power values are below maximum limits.
Setting is returned to preset value when pressure and power values are below maximum
value – hysteresis value over 3 seconds.
Selecting setting control mode
•Enter crusher control display (press F1 in main menu).
•Select OP. MODE (press F1). Choose the Setting control mode alternative by moving
the highlighted line (F5 up, F6 down).
•Accept your choice (press F1)
The selected operating mode is shown in the operating mode window. Press F7 to exit.

Version 3/01 Page 8/25
2.2.3 Load control mode
On load control mode, the crusher controller compares the actual pressure and power
values with the preset ones. If the pressure or power actual value is bigger than preset
value + hysteresis (hysteresis values are set in the configuration), setting increases until
actual value is less than preset value + hysteresis value.
If the pressure and power actual values are below preset values – hysteresis, setting
decreases until actual values are above preset values – hysteresis.
Selecting load control mode
•Enter crusher control display (press F1 in main menu).
•Select OP. MODE (press F1). Choose the load control mode alternative by moving
the highlighted line (F5 up, F6 down).
•Accept your choice (press F7).
The selected operating mode is shown in the operating mode window. Press F7 to exit.
2.2.4 Feeder control
Level switch (on/off)
Following actions are valid when level switch is connected and digital level switch is
selected in the configuration:
•If the cavity level is over the maximum limit, feeder is stopped. Feeder is restarted
when level is ok and delay time (counting started after ok signal) is passed. Delay
time can be set in the confuguration.
2.2.5 Winter mode
It is possible to keep the crusher warm when not in operation by selecting winter mode
function. In winter mode the lubrication oil is heated and pumped according to timers and
limits set in configuration.
2.3 Setting preset values
2.3.1 Setting preset values on Setting control mode
•Enter crusher control display (press F1 in main menu).
•Select PR. VALUE (press F2). The preset value window turns yellow.
•Set the desired preset value (F1 increases, F2 decreases in 1 mm increments).
•Accept the preset value (press F3). The preset value window turns grey.
•Press F7 to exit.
2.3.2 Setting preset values on Load control mode
•Enter crusher control display (press F1 in main menu).
•Select PR. VALUE (press F2). The preset value window turns yellow.
•Select pressure (F5) or power (F6) as the preset value to be changed.
•Select the desired preset value (F1 increases, F2 decreases in 0.1 bar or 1 kW
increments).
•Accept the preset value (press F3). The preset value window turns grey.

Version 3/01 Page 9/25
2.4 Operation data
2.4.1 Trends
Trends describe the crusher's actual values. The horizontal axis indicates time and the
vertical axis the actual system value at the specific moment. The time scales you can
choose between are 6 minutes, 60 minutes, 6 hours, and 24 hours.
The vertical axis scales itself automatically to give the most precise view possible. For
example, if the highest power value during the last six minutes has been 182 kW, and the
motor’s maximum power is 250 kW, the screen shows the axis from 0 to 200 kW.
Over each time scale you will have 180 samples. The sample values of longer time scales
are calculated average values of the samples over the shorter time scales. The sampling
times are shown in the table below.
Time scale Sampling period
6 minutes 2 seconds
60 minutes 20 seconds (average of ten 2 second samples)
6 hours 120 seconds (2 minutes - average of six 20 sec. samples)
24 hours 480 seconds (8 minutes - average of four 120 sec. samples)
Reading trends:
•Enter crusher control display (press F1 in main menu).
•Select LOGBOOK (press F3).
•Choose trends (press F1)
•Press F7 to exit.

Version 3/01 Page 10/25
The table below describes the functions of the trend screen:
Key Function Description of function
F1 Setting trend Setting [mm / in]
F2 Power trend Power [kW / hp]
F3 Pressure trend Pressure [bar / psi].
F4 Capacity trend Capacity [mtph / stph] (tons per hour).
F5 Timescale 24 h <-- Changes the time scale shown on the screen.
F6 Timescale --> 6 min Changes the time scale shown on the screen.
F7 Close Exit to production data screen.
2.4.2 Field Data
The data is shown over the past ten days. Production data is registered of the available
measurements. The standard measurements are:
•Setting; average, maximum, and minimum [mm / in]
•Pressure; average and maximum [bar / psi]
•Power; average and maximum [kW / hp]
•Oil temperature; Return oil temperature; average and maximum [_C /_F]
•Capacity; average and maximum with scales connected [tph] (if belt scale is
connected)
•Running time; total and loaded [h]
•Power consumption; total and loaded [MWh]
•Output [tons] (if belt scale is connected)
Data log file is created automatically (at 0:00) every day.

Version 3/01 Page 11/25
Reading field data:
•Enter crusher control display (press F1 in main menu).
•Select LOGBOOK (press F3).
•Choose field data (press F2).
•Press F7 to exit.
Key Function Description of function.
F5 Timescale, day <-- Go over to previous time scale.
F6 Timescale, day --> Go over to next time scale.
F7 Close Exit to Choose production data screen.
2.5 Alarms
A warning is indicated by a yellow and an alarm by a red indicator light. Alarm texts are
also marked with red. You get more information by pressing F1. Messages are
acknowledged by pressing F3.
The following details are stored and displayed in conjunction with an alarm or warning:
•Date and time
•Type; warning or alarm
•Description of alarm
You can browse the messages backwards and forwards with the keys F5 and F6. A list
continuing outside the screen at the bottom is indicated by an arrow (V) at the bottom
right corner of the screen. Correspondingly, a list continuing upwards outside the screen
is indicated by an arrow (/\) at the top right corner.

Version 3/01 Page 12/25
Reading alarm and warning data:
•Enter crusher control display (Press F1 in main menu).
•Select ALARMS (Press F4).
Function keys in alarm mode are as follows:
Key Function Description of function
F1 Select Selects event.
F3 Acknowledge all Acknowledges all events.
F5 Move up Moves cursor upwards on the list.
F6 Move down Moves cursor downwards on the list.
F7 Close Exit to crusher control display.
In the alarm screen you can examine single events by pressing F1. This screen presents
more information, such as setting, pressure, power, etc.
An alarm will be sent if a limit value is exceeded or not reached. An alarm will stop the
device, if necessary. An alarm is often related to the actions of the operator. If a safety
device is triggered, an alarm will follow.
Following additional information is gathered on alarms and warnings:
•Code and point of sending
•Measured values; setting, pressure, and power at the time of alarm
•Operating hours at the time of alarm
•Number of alarms/warnings of this type within operating hours
•Time of first alarm/warning of this type
•Acknowledgement of message; acknowledged events with prefix @
•Lubrication pressure : OK/not OK
•Oil filter: OK/not OK
•Oil temperature: low/OK/high
•Oil flow: on/off
•Oil level: on/off
•Cooler status: on/off
•Heater status: on/off

Version 3/01 Page 13/25
2.6 Calibration
Methods of calibration: manual calibration and contact calibration.
2.6.1 Manual calibration
In manual calibration, the crusher's setting is measured using e.g. a piece of lead. See
crusher’s instruction manual for detailed information about how to perform measuring.
After you have measured the actual setting, do this:
•Enter crusher control display (press F1 in main menu).
•Select Calibration (press F5)

Version 3/01 Page 14/25
•Highlight manual calibration in the menu (F5 up, F6 down).
•Select manual calibration (press F1)
•Feed in new setting (F1 increases, F2 decreases in 0.1 mm / 0.01 inch increments).
•Acknowledge calibration (press F3)
•Press F7 to exit.
2.6.2 Contact calibration
Contact calibration is allowed to do only in fine crushers! In the contact calibration,
the crusher's current setting is checked by running liner against liner.
The start of contact calibration requires that lubrication and crusher are on, feeding
device is off and the crusher is idling. Idling is monitored from pressure and power.
Contact is recognized by the increase of pressure. If liners are very worn, it is not
possible to run them against each other. In such cases the controller interrupts the routine
and gives a warning. You must perform a manual calibration in such case.
Contact calibration:
•Enter crusher control display (Press F1 in main menu).
•Select calibration (Press F5).
•Highlight contact calibration in the menu (F5 up, F6 down).
•Select contact calibration (Press F1).
•Press F1 to start calibration.
•To interrupt calibration, press F2.
•Acknowledge calibration (Press F3).
•Press F7 to exit.
3. Diagnostics
3.1 Diagnostics display
The diagnostic display leads to:
•Trends
•Input and output data
•Start/stop routines
•Alarms/warnings and events

Version 3/01 Page 15/25
3.2 Trends
Reading trends
•Enter main menu.
•Choose Diagn. (press F2).
•Choose trends (press F1)
•Press F7 to exit.
The table below describes the functions of the trend screen:
Key Function Description of function
F1 Tank temperature Oil temperature in the tank [_C /_F].
F2 Return temperature Crusher lubrication return oil temperature [_C / _F].
F4 Load profile This trend is created from values of pressure and power. The
current value of pressure is compared to its maximum value,
and current power value to maximum power value. Higher of
these values is saved to the trend.
For example:
measure actual value max value %
pressure 10 bar 20 bar 50
power 75 kW 250 kW 30
!50% is saved to the trend.
vibration 75% 100% 75
power 150 kW 250 kW 60
!75% is saved.
F5 Timescale
24 h <-- Changes the time scale shown on the screen. The time
alternatives are 24 hours, 6 hours, 60 minutes (1 h), and 6
minutes.

Version 3/01 Page 16/25
F6 Timescale
--> 6 min Changes the time scale shown on the screen. The time
alternatives are 24 hours, 6 hours, 60 minutes (1 h), and 6
minutes.
F7 Close Exit to diagnostics display.
3.3 Input and output data
The diagnostics monitor the condition of sensors and actuators. The system also indicates
the I/O statuses of the control units.
•Enter main menu (Press F7 a sufficient number of times).
•Select diagnostics (Press F2).
•Select I/O status (press F2).
•Press F1 to view next page.
•Press F7 to exit.
The left column on the screen shows the digital inputs. The centre column shows the
outputs. These have either one or zero as their value. The right column presents the
analog inputs.
Detailed information about inputs and outputs can be found on appendix 2.
3.4 Starting and stopping crusher

Version 3/01 Page 17/25
The crusher is started and stopped through the start/stop menu. By selecting F2 in the
main menu you enter the diagnostics display, and from there by pressing F3 to start/stop
menu. The crusher and its auxiliary devices can be started one by one or in the sequence.
When starting in a sequence, the crusher's controller automatically starts the lubrication,
the crusher, and the feeding device in steps while controlling starting conditions for each
device.
3.4.1 Starting lubrication
•Enter diagnostics display (Press F2 in main menu).
•Select start/stop (Press F3).
•Highlight lubrication in the start-stop-sequences menu (F5 up, F6 down).
•Start lubrication (Press F1).
Only the lubrication will start now. During the start, the red OFF on the lubrication line
turns yellow, and then into green ON.
•Press F7 to exit.
Starting conditions for lubrication
•All the safety devices must be OK.
•Oil temperature in the tank has to be warm enough. The starting temperature is set in
system parameters.
•After lubrication has started, the lubrication pressure has to increase during 10
seconds.
•30 seconds after the lubrication is started, the lubrication oil flow has to be ok.
•If the controller can not recognize the oil pressure or flow, controller will stop the
lubrication and give an error message. The delay for recognition is set in system
parameters

Version 3/01 Page 18/25
3.4.2 Starting crusher
•Enter diagnostics display (Press F2 in main menu).
•Select start/stop (Press F3).
•Highlight crusher in the start-stop-sequences menu (F5 up, F6 down).
•Start crusher (press F1).
Lubrication unit and the crusher will start now in sequence. There is a delay between the
startings. During the start, the red Off on the relevant line first turns yellow, and then into
green ON.
•Press F7 to exit.
Starting conditions for crusher
•Crusher may start immediately when oil pressure and flow are ok or there can be time
delay. Time delay is possible to adjust in configuration.
3.4.3 Starting feeding device
•Enter diagnostics display (Press F2 in main menu).
•Select start/stop (Press F3).
•Highlight feeding device in the start-stop-sequences menu (F5 up, F6 down).
•Start feeding device (press F1).
Lubrication unit, crusher, and the feeding device will start now in sequence. There is a
delay between each starting. During the start, the red OFF at the relevant line first turns
yellow, and then into green ON.
•Press F7 to exit.
Starting conditions for feeding device
•Discharging equipment has to be on.
•Material level has to be ok, ie no material in the crusher. (if analog level detector is
connected)
•Level sensor signal must be ok, ie no sensor fault allowed (with analog sensor)
•The crusher must have been running for at least 30 seconds.
3.4.4 Stopping feeding device
•Enter diagnostics display (press F2 in main menu).
•Select start/stop (press F3).
•Highlight feeding device in the start-stop-sequences menu (F5 up, F6 down).
•Stop feeding device (press F2).
The feeding device will stop now. The green ON at the feeding device line first turns
yellow, and then into red OFF.
•Press F7 to exit.

Version 3/01 Page 19/25
3.4.5 Stopping crusher
•Enter diagnostics display (press F2 in main menu).
•Select start/stop (press F3).
•Highlight crusher in the start-stop-sequences menu (F5 up, F6 down).
•Stop crusher (press F2).
Feeding device and the crusher will now stop in sequence. There is a delay between the
stoppings. The green ON at the respective line first turns yellow, and then into red OFF.
•Press F7 to exit.
Stopping conditions for crusher
•The crusher will be stopped after it starts idling.
3.4.6 Stopping lubrication
•Enter diagnostics display (press F2 in main menu).
•Select start/stop (press F3).
•Highlight lubrication in the start-stop-sequences menu (F5 up, F6 down).
•Stop lubrication (press F2).
The feeding device, the crusher, and the lubrication will now stop in sequence. There is a
delay between each stopping. The green ON at the respective line first turns yellow, and
then into red OFF.
•Press F7 to exit.
Stopping conditions for lubrication
•Lubrication will be stopped 30 seconds after the stopping of crusher.
4. User Setup
User Setup contains language selection, selection between metric or imperial units and
possibility to change time/date.

Version 3/01 Page 20/25
Select language
•Enter main menu (Press F7 a sufficient number of times).
•Select system parametres (Press F3).
•Select user setup (Press F1).
•Select language settings (Press F1).
•Highlight desired language (F5 up, F6 down).
•Select language (Press F4).
•Press F7 to exit.
Select metric or imperial units
•Enter main menu (Press F7 a sufficient number of times).
•Select system parametres (Press F3).
•Select user setup (Press F1).
•Change units (Press F2).
•Press F7 to exit.
Change time/date
•Enter main menu (Press F7 a sufficient number of times).
•Select system parameters (Press F3).
•Select user setups (Press F1).
•Select change time/date (Press F3).
•Press F7 to exit.
5. Error/information messages
5.1 Sensor faults
5.1.1 Setting
Minimum setting
•You have reached the mininum allowed closed side setting of the crusher. Setting must
be increased to continue crushing.
Maximum setting
•You have reached maximum allowed setting. Setting must be decreased.
Fault in setting sensor!
•The output of the setting sensor is below working limit. Check the sensor and cables.
Replace if necessary.
Setting sensor ok
•There was a fault in setting sensor, but the sensor has recovered.
5.1.2 Pressure
Maximum pressure reached!
This manual suits for next models
1
Table of contents
Popular Controllers manuals by other brands
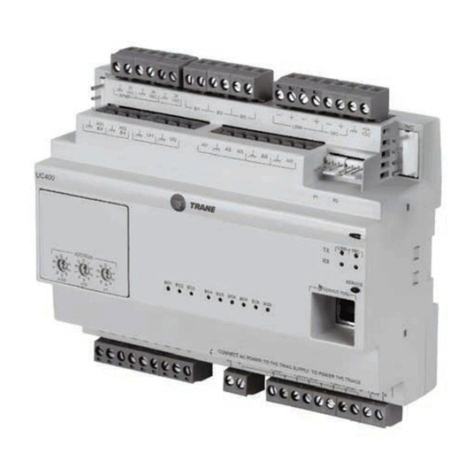
Trane
Trane Tracer UC400 Installation, operation and maintenance
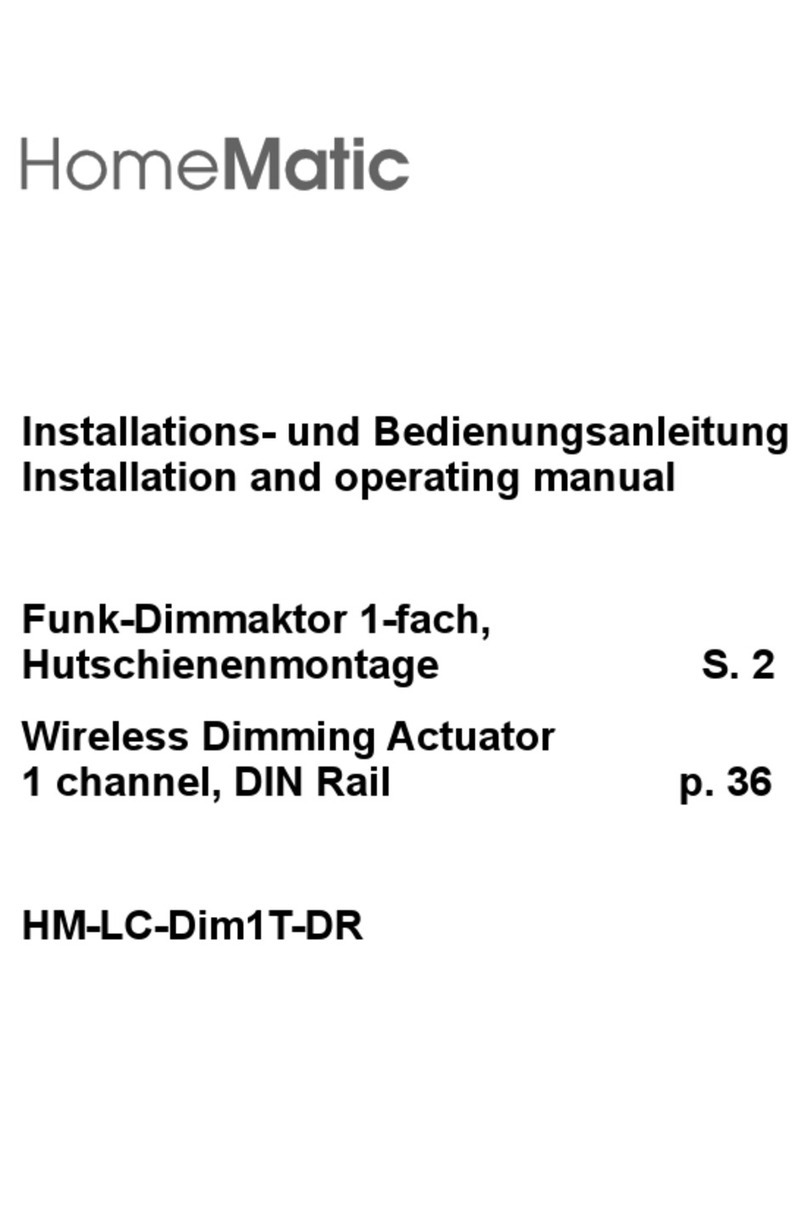
HomeMatic
HomeMatic HM-LC-Dim1T-DR Installation and operating manual
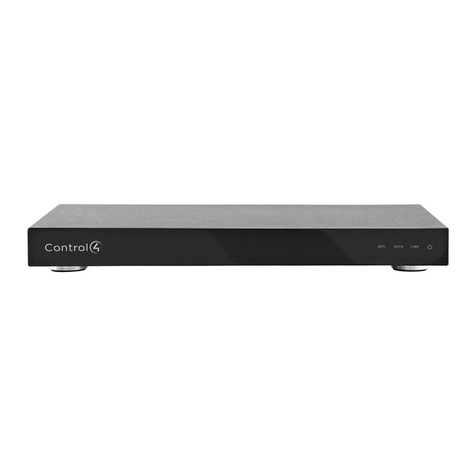
Contro l4
Contro l4 HC-800 installation guide
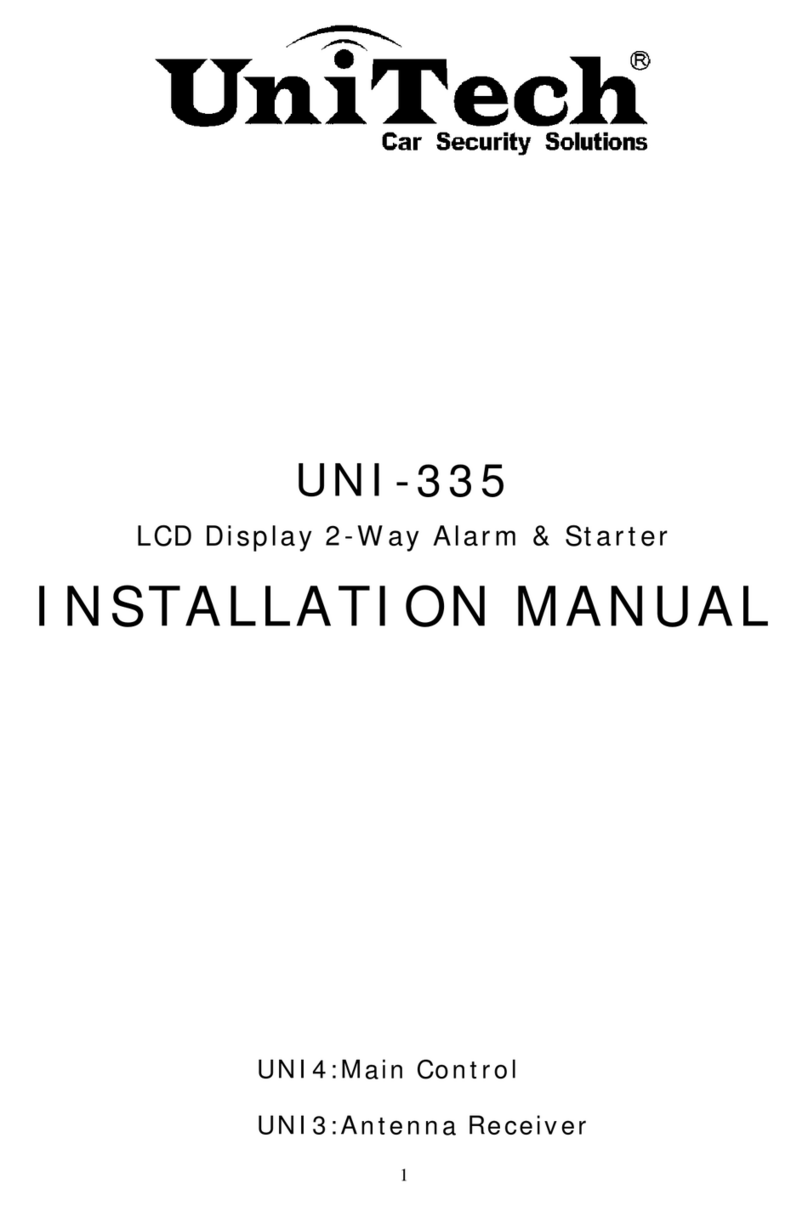
Unitech
Unitech UNI-335 installation manual
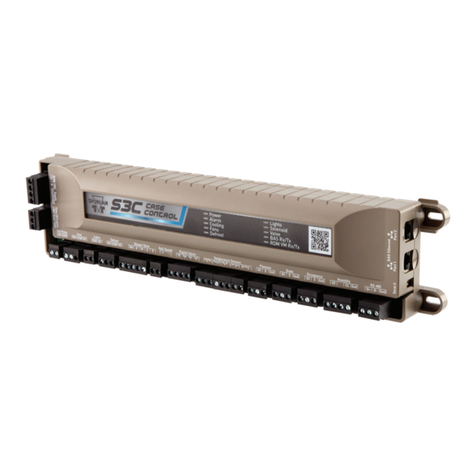
Parker
Parker Sporlan S3C Installation and operation instructions
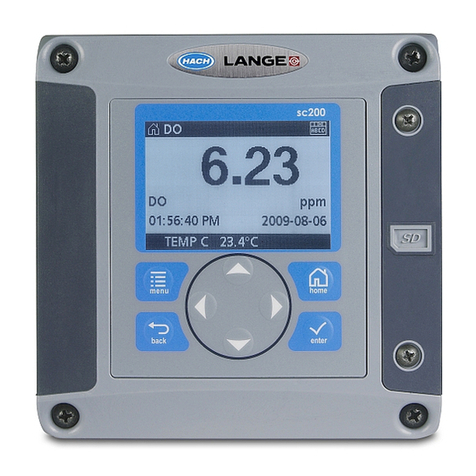
Hach
Hach Polymentron 9500 Basic user manual