Nortech Detection Pty Ltd PD130 How to use

Nortech Detection Pty Ltd
Unit 1, Bldg 5, Forest Central Business Park,
49 Frenchs Forest Road,
Frenchs Forest NSW 2086
PO Box 6011, Frenchs Forest DC, NSW 2086
email: mail@nortechdetection.com.au
web: www.nortechdetection.com.au
Short form User Manual
PD130 Enhanced Vehicle Detector
The PD130 is a single channel microprocessor based detector designed specifically for parking and vehicle access
control application. The PD130 has been designed using the most up-to-date technology in order to meet the
requirements of a vast number of parking applications in terms of operating conditions and options available to the user.
The primary function of the detector is to detect vehicle presence by means of an inductance change caused by the
vehicle passing over a wire loop buried under the road surface.
The detector has been designed for ease of installation and convenience. The various modes are selected by changing
the positions of the switch on the front of the unit.
The switches allow for different loop frequency settings, sensitivity settings and mode settings.
The PD130 provides visual output (LED) on the front of the enclosure and relay changeover contacts are taken on the
11-pin connector at the rear of the enclosure. The LED indicates the power has been applied to the unit, that a vehicle is
present over the loop and if there is a fault on the loop. The Presence relay is fail-safe and will close on a vehicle detect
or in the event of power failure.
In accordance wi
th the manufacturer’s policy of updating and improving product designs, product specification is
subject to change without notice. While every care has been taken with the preparation of this document, no warranty
is offered to the completeness or accuracy of this information.

PD130 Enhanced - User Instructions
Page 2 of 12
1. Table of Contents
1. Table of Contents .......................................................................................................................................... 2
2. User Warnings............................................................................................................................................... 2
3. Principle of Operation.................................................................................................................................... 3
4. Operating Parameters..................................................................................................................................... 3
4.1. Detector Tuning........................................................................................................................................ 3
4.2. Modes of Operation .................................................................................................................................. 3
4.3. Detector Sensitivity................................................................................................................................... 4
4.4. Hardware configuration............................................................................................................................. 4
5. Switch Settings.............................................................................................................................................. 4
5.1.1. Frequency Switch ................................................................................................................................. 4
5.1.2. Sensitivity ............................................................................................................................................ 5
5.1.3. Automatic Sensitivity Boost ................................................................................................................. 5
5.1.4. Filter Mode .......................................................................................................................................... 5
5.1.5. Pulse Relay .......................................................................................................................................... 5
5.1.6. Presence Time...................................................................................................................................... 6
5.1.7. Reset Switch ........................................................................................................................................ 6
5.2. Front Panel Indicators ............................................................................................................................... 6
6. Technical Data .............................................................................................................................................. 6
6.1.1. Functional Data .................................................................................................................................... 6
6.2. Electrical Data .......................................................................................................................................... 7
6.3. Environmental Data .................................................................................................................................. 7
6.4. Mechanical Data ....................................................................................................................................... 7
7. Wiring Connections ....................................................................................................................................... 8
8. Part Numbers................................................................................................................................................. 8
9. Installation Guide .......................................................................................................................................... 9
9.1. Operational Constraints............................................................................................................................. 9
9.1.1. Crosstalk .............................................................................................................................................. 9
9.1.2. Reinforcing .......................................................................................................................................... 9
9.2. Loop and Feeder Specification .................................................................................................................. 9
9.3. Sensing Loop Geometry............................................................................................................................ 9
10. Loop Installation ..........................................................................................................................................10
11. Fault Finding................................................................................................................................................12
12. Warranty ...................................................................................................................................................... 12
13. Sales and Technical support..........................................................................................................................12
2. User Warnings
WARNING: This unit when installed must be correctly earthed!
WARNING: Disconnect power before plugging / unplugging or working on this unit!
WARNING: Installation and service to be undertaken by qualified personnel only!
WARNING: No user serviceable parts are inside.
Warranty is void if unauthorised modifications are made to this unit!
WARNING: Ensure safety to vehicles and personnel at sites where this item is installed to control motorised gates.
Close off access to vehicles and pedestrians before disconnection or making adjustments!
WARNING: Cutting into post tensioned concrete slabs for loop installation can have catastrophic consequences.
As a general rule 30mm is the deepest slot depth allowable in such cases. When any doubt exists the
structural engineer’s approval must be sought prior to commencement of slot cutting.

PD130 Enhanced - User Instructions
Page 3 of 12
3. Principle of Operation
An inductive loop vehicle detector senses the presence of a vehicle over an area defined by a loop of two or more turns
of wire, laid under the road or pavement surface. This loop of wire is connected to the detector by a twisted pair of
wires called a loop feeder.
A vehicle passing over a sensing loop causes a small reduction in the inductance of the loop, which is sensed by the
detector. The sensitivity of the detector is adjustable to accommodate a wide range of vehicle types, as well as different
loop and feeder combinations.
Upon detection of a vehicle passing over the loop the detector operates its output relays, which may be used to indicate
controls associated with the installation.
Figure 4.1 Principle of Operation
4. Operating Parameters
4.1. Detector Tuning
Tuning of the detector is fully automatic. When power is applied to the detector upon installation of the system, or
when a reset is initiated, the detector will automatically tune itself to the loop to which it is connected. The detector
will tune to any loop to inductance range 20 to 1500 microhenries.
This wide range ensures that all loop sizes and feeder combinations will be accommodated in the tuning range of the
detector.
Once tuned, any slow environmental change in loop inductance is fed to a compensating circuit within the detector that
keeps the detector correctly tuned.
4.2. Modes of Operation
The detector has “presence” and “pulse” outputs. The Presence output will be on continuously during the presence of a
vehicle over the inductive loop. The pulse relay outputs a pulse of 150 milliseconds duration on arrival or departure of a
vehicle.
Normally the presence output is available for only a limited time due to the environmental compensation circuitry of the
detector. The detection memory time will be dependent on the change of inductance due to the vehicle over the loop.
The presence time on the limited presence setting will be approximately 1 hour for 3% ∆L/L.
If permanent presence is selected, then the presence output is maintained indefinitely, to the detriment of the
environmental compensation that operates only when the loop is unoccupied.
When set to "pulse on detect" the detector will give a pulse on detection of a vehicle. When set to "pulse on un-detect”
the detector will give a pulse output when the vehicle leaves the loop.
The presence output is known as a fail-safe output. This implies that in the event of a power or loop failure the detector
will give a detect output. The pulse outputs are not fail safe and will not operate if a fault occurs.

PD130 Enhanced - User Instructions
Page 4 of 12
4.3. Detector Sensitivity
Sensitivity of the detection system is dependent on factors such as loop size, number of turns in the loop, feeder length
and the presence of metal reinforcing beneath the loop.
The nature of the application determines the required sensitivity that may be adjusted by means of the sensitivity
switches on the front of the enclosure.
Sensitivity levels of the PD130 have been carefully optimised for parking and vehicle access control applications. The
detection of small unwanted objects such as bicycles and trolleys can be eliminated by selecting lower sensitivity levels
whilst high-bed vehicles and vehicle/trailer combinations will not loose detection by using automatic sensitivity boost
(ASB) option.
ASB operates as follows. When ASB is disabled the undetect level is dependent on the sensitivity setting of the
detector. Hence as the detector is made less sensitive, the undetect level will reduce accordingly. When the ASB is
enabled the undetect level will always be the same irrespective of the sensitivity setting and will be equivalent to the
undetect level when the sensitivity is on maximum setting.
4.4. Hardware configuration
The PD130 Enhanced Vehicle single channel parking detector is designed to be shelf or DIN rail mounted, with the
controls and visual indicators at the front, and wiring at the rear of the enclosure.
The power, loop and relay outputs are all connected to
the single 11-pin plug, which is mounted at the rear of
the enclosure.
Figure 4.1 PD130 Faceplate layout
5. Switch Settings
5.1.1. Frequency Switch
The frequency switches are the lower two switches, switches No. 1 and 2. There are four frequency selections:
SW2 SW1
Off Off - High
On Off - Medium-High
Off On - Medium-Low
On On - Low

PD130 Enhanced - User Instructions
Page 5 of 12
The frequency switches allow the loop to be shifted higher or lower depending on the switch position. The frequency of
the loop is determined by the loop size, and the frequency of the switch simply causes a frequency shift on the loop.
Where more than one detector is used the detectors must be set-up to ensure that there is no cross-talk (interference)
between the detectors. This can be achieved by ensuring that the loops of the two detectors are spaced sufficiently apart
(approximately 2 metres between adjacent edges) and also ensuring that the detectors are set to different frequencies.
As a general rule, the detector connected to the inductive loop with the greatest inductance should be set to operate at
the lowest frequency. Loop inductance increases as loop size, number of turns in the loop and feeder length increases.
5.1.2. Sensitivity
The sensitivity of the detector allows the detector to be selective as to the change of inductance necessary to produce an
output. There are four sensitivity selections and these are set as follows: -
SW4 SW3
Off Off - High
On Off - Medium-High
Off On - Medium-Low
On On - Low
5.1.3. Automatic Sensitivity Boost
Automatic sensitivity boost is a mode that alters the “undetect” level of the detector. This mode is selected by switch
No. 5 on the front of the enclosure and is as follows: -
SW5
Off - Disabled
On - Enabled
Automatic sensitivity boost causes the sensitivity to be boosted to a maximum on detection of a vehicle, and maintained
at this level during the presence of the entire vehicle over the loop. When the vehicle departs the loop and the detection
is lost the sensitivity reverts to the pre-selected level.
5.1.4. Filter Mode
The filter mode is selected with the mode switch No. 6. The filter produces a delay turn-on time of two seconds when a
vehicle occupies the loop. This is to enable unwanted objects (trolleys) to pass over the loop without being detected.
The filter option may be used on any sensitivity setting and is selected as follows: -
SW6
Off - Disabled
On - Enabled
5.1.5. Pulse Relay
The pulse relay may be made to operate on detect (entry) or on “undetect” (exit) of a vehicle. This option is selected
from Switch No. 7 and is configured as follows: -
SW7
Off - Pulse on Detect
On - Pulse on Undetect

PD130 Enhanced - User Instructions
Page 6 of 12
5.1.6. Presence Time
The presence time may be set to permanent presence or to limited presence. See Section 4.1 for details.
The presence mode is set with switch No. 8 and is configured as follows: -
SW8
Off - Limited Presence
On - Permanent Presence
5.1.7. Reset Switch
The detector automatically tunes to the inductive loop connected to it when the power is applied, whether on initial
installation or after any break in power supply. Should it be necessary to re-tune the detector, as may be required after
changing any of the switches or after moving the detector from one installation to another, momentary operation of the
RESET switch will initiate the automatic tuning cycle.
5.2. Front Panel Indicators
While the detector is tuning, the ON (Red) LED will glow and the OUTPUT LED (Green) will extinguish when the
system is tuned. Thereafter, the green LED will flash at a rate of 1 Hz. This is used to indicate the frequency of the loop
to the user. Every flash of the LED is equivalent to 10 kHz. It will stop when the operating frequency is reached. This
operation is also performed whenever the reset button is depressed.
The ON (red) LED will glow permanently to indicate that the unit is functional. The red LED also serves as an optical
interface to the DU100 Diagnostic Unit.
If faults exist with the loop the green LED will come on and flash off at the rate of 2Hz indicating the fault. If the fault
is self-healing the detector will continue to operate but the LED will remain on indicating to the user that a fault has
occurred. The LED will go off for a moment during an “undetect”, indicating this state, thereafter returning on. This
condition can be restored by removing the power or by depressing the reset button.
The green LED will also glow whenever a vehicle is detected passing over the inductive loop.
6. Technical Data
6.1.1. Functional Data
Tuning
Fully Automatic
Self-tuning range 20μH to 1500 μH
Sensitivity Four step switch selectable
High 0.02% ∆L/L
Medium High 0.05 %∆L/L
Medium Low 0.10 %∆L/L
Low 0.50 %∆L/L
Frequency Four step switch selectable
Frequency dependent on loop size
Automatic Sensitivity Boost Switch selectable
Filter Switch selectable 2 second filter
Presence Relay Fail-safe
Presence Time Switch selectable:
Limited presence / Permanent presence
Pulse Relay Switch selectable:
Pulse on detect / Pulse on undetect

PD130 Enhanced - User Instructions
Page 7 of 12
6.2. Electrical Data
6.3. Environmental Data
6.4. Mechanical Data
Pulse Output Duration
150 milliseconds
Response Times 100 milliseconds
Drift Compensation Rate Approx. 1%∆L/L per minute
Visual Indications 1 x Power LED – Red
1 x Channel Status LED - Green
Reset Push button on front of enclosure
Surge protection Loop isolation transformer, gas discharge tubes and Zener
diode clamping on loop input
Power requirements
12 V
-
10% to 24 V +10% (PD134)
230 VAC ± 10% (48 to 62Hz) (PD132)
1.5 VA Maximum @ 230 V
Relay Contact Rating Relays rated - 5 A @ 230 VAC
Factory Option - Opto Isolated 50mA @ 30VDC
Storage T
emperature
-
40° to +80°C
Operating Temperature -40° to +70°C
Humidity Up to 95% relative humidity without condensation
Circuit protection Conformal coating over the PCB and all components
IP Rating IP30
Housing Material
ABS
blend
Mounting Position Shelf or DIN rail mounting
Connections 11-pin Sub-magnal (JEDEC No. B11-88)
Size of Housing 78mm (H) X 41mm (W) X 80mm (D)

PD130 Enhanced - User Instructions
Page 8 of 12
Figure 6.1 PD130 Housing dimension
7. Wiring Connections
11-pin connector wiring
pin colour designation
1 Red Live 230V AC 50/60 Hz
2 Black Neutral OR 12 - 24V AC/DC
3 Grey Pulse Relay Normally Open contact
4 Violet Pulse Relay Common contact
5 Yellow Presence Relay Normally Open contact
6 Brown Presence Relay Common contact
7 Blue Loop Twist this
8 Blue Loop pair
9 Green Earth
10 Pink Presence Relay Normally Closed contact
11 White Pulse Relay Normally Closed contact
8. Part Numbers
Part Number Model Number Description
301FT0101_01 PD132 - Enhanced 230 V ac operation
301FT0122_01 PD134 - Enhanced 12 - 24V ac/dc operation
895FT 0001 DU100 - English Hand Held Diagnostic Unit
301FT0041 Wiring Harness Option - 1 metre plug and harness
CTR119090 DIN Rail Screw terminal base

PD130 Enhanced - User Instructions
Page 9 of 12
9. Installation Guide
Optimum functioning of the detector module is largely dependent on factors associated with the inductive sensor loop
connected to it. These factors include choice of material, loop configuration and correct installation practice. A
successful inductive loop vehicle detection system can be achieved bearing the following constraints in mind, and
strictly following the installation instructions. The detector must be installed in a convenient weatherproof location as
close as possible to the loop.
9.1. Operational Constraints
9.1.1. Crosstalk
When two loop configurations are in close proximity, the magnetic fields of one can overlap and disturb the field of the
other. This phenomenon, known as crosstalk, can cause false detects and detector lock-up.
Crosstalk between adjacent loops operating from different detector modules can be eliminated by:
1. Careful choice of operating frequency. The closer together the two loops, the further apart the frequencies of
operation must be.
2. Separation between adjacent loops. Where possible a minimum spacing of 2 metres between loops should be
adhered to.
3. Adequate twisting of feeder cables (20 twists per metre). Adequate screening if they are routed together with
other electric cables. The cable screen must be earthed at the detector end only.
9.1.2. Reinforcing
The existence of reinforced steel below the road surface has the effect of reducing the inductance, and therefore the
sensitivity, of the loop detection system. Hence, where reinforcing exists 2 turns should be added to the normal loop, as
referred to in section 5.3.
The ideal minimum spacing between the loop and the cable and steel reinforcing is 150mm, although this is not always
practically possible. The slot depth should be kept as shallow as possible, taking care that the feeder remains exposed
after the sealing compound has been applied.
WARNING : Cutting into post tensioned concrete slabs can have catastrophic consequences. As a general rule
30mm is the deepest slot depth allowable in such cases. When any doubt exists the structural engineer’s
approval must be sought prior to commencement.
9.2. Loop and Feeder Specification
The loop and feeder should preferably constitute a single un-joined length of insulated copper conductor, with a
minimum rating 15Amp.
Joints in the loop or feeder are not recommended. Where this is not possible, joints are to be soldered and terminated in
a waterproof junction box. This is extremely important for reliable detector performance.
9.3. Sensing Loop Geometry
Sensing loops should, unless site conditions prohibit, be rectangular in shape and should normally be installed with the
longest sides at right angle to the direction of traffic movement. These sides should ideally be 1 metre apart.

PD130 Enhanced - User Instructions
Page 10 of 12
The length of the loop will be determined by the width of the roadway to be monitored. The loop should reach to
within 300mm of each edge of the roadway.
In general, loops having a circumference measurement in excess of 10 metres should be installed using two turns of
wire, while loops of less than 10 metres in circumference, should have three turns or more. Loops having a
circumference measurement less than 6 metre should have four turns. It is good practice at time of installation to
construct adjacent loops with alternate three and four turn windings.
10. Loop Installation
All permanent loop installations should be installed in the roadway by cutting slots with a masonry cutting disc or
similar devise. A 45° crosscut should be made across the loop corners to reduce the chance of damage that can be
caused to the loop at right angle corners.
NOMINAL SLOT WIDTH: 45mm
NOMINAL SLOT DEPTH : 30mm TO 50mm
A slot must also be cut from the loop circumference at one corner of the loop to the roadway edge to accommodate the
feeder.
A continuous loop and feeder is obtained by leaving a tail long enough o reach the detector before inserting the cable
into the loop slot. Once the required number of turns of wire is wound into the slot around the loop circumference, the
wire is routed again via the feeder slot to the roadway edge. A similar length is allowed to reach the detector and these
two free ends are twisted together to ensure they remain in close proximity to one another (minimum 20 turns per
metre). Maximum recommended feeder length is 100 metres.
It should be noted that the loop sensitivity decreases as the feeder length increases, so ideally the feeder cable should be
kept as short as possible.
The loops are sealed using “quick-set” black epoxy compound or hot bitumen mastic to blend with the roadway surface.
Figure 10.1 Slot details

PD130 Enhanced - User Instructions
Page 11 of 12
Figure 10.2 Adjacent loops connected to different detector modules

PD130 Enhanced - User Instructions
Page 12 of 12
11. Fault Finding
FAULT CAUSED BY REMEDY
Red LED does not glow on power up. If the indicator is off then there
is a fault with the power
connection to the unit.
Check power feed to the unit.
i) Unit cannot tune to the loop
due to faulty loop or feeder
connection.
i) Check loop installation and
connections.
ii) Loop inductance may be too small
or too large.
ii) Re-cut loop as per installation
instructions.
After the initial tune period the
Green LED flashes continuously
(ON for 1 second and OFF for ½
second).
iii) Faulty detector unit. iii) Replace unit.
After tuning, the loop output
LED flashes intermittently and
the relay chatters.
The detector is giving spurious
detects due to:
a) Crosstalk with adjacent detector.
b) Faulty loop or untwisted loop
feeder connection.
c) Electrical interference
a) Change frequency setting on one
unit.
b) Check that the feeders are
correctly connected and adequately
twisted.
c) Isolate sources of nearby electrical
equipment and high voltage cables
12. Warranty
i. A conditional 24-month Warranty is offered on all items covering faulty workmanship or materials.
ii. Warranty is calculated from the unit serial number which incorporates the date of manufacture.
iii. Goods for return under warranty are to be returned to the Company at the customer’s expense.
iv. Goods repaired or exchanged under warranty will be returned to a customer at our expense.
v. Warranty specifically excludes any on site service obligation or liability for any 3rd party equipment
malfunction or damage, and excludes damage by fire, electrocution, accident, misuse, or abuse, or other
cause beyond the normally intended use of the product.
Return Address for warranty items
Nortech Detection Pty Ltd Post : Nortech Detection Pty Ltd
370 – 380 Cambridge Road, P.O. Box 2104
MORNINGTON TAS 7018 HOWRAH TAS 7018
13. Sales and Technical support
Tel: 02-8977 4047
Fax: 02-9475 4742
email: mail@nortechdetection.com.au
website: www.nortechdetection.com.au
Sydney Office hours
08:30 to 17:00 Mon – Friday
Table of contents
Popular Security Sensor manuals by other brands
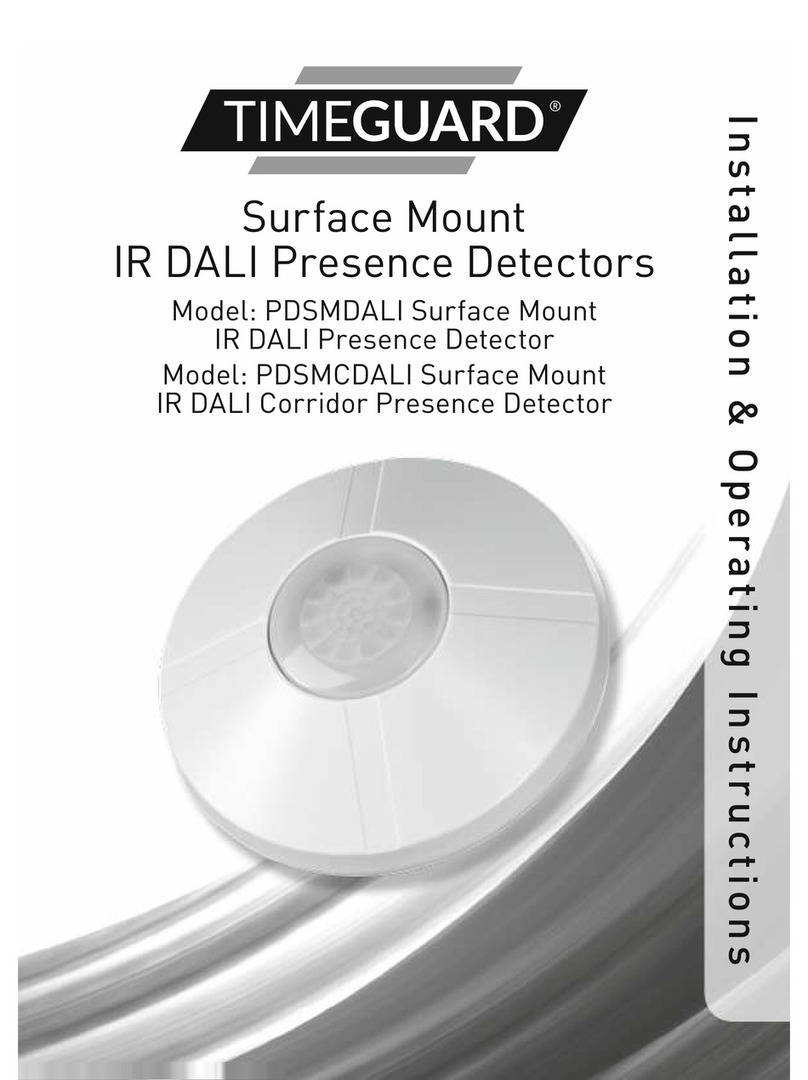
Timeguard
Timeguard PDSMDALI Installation & operating instructions
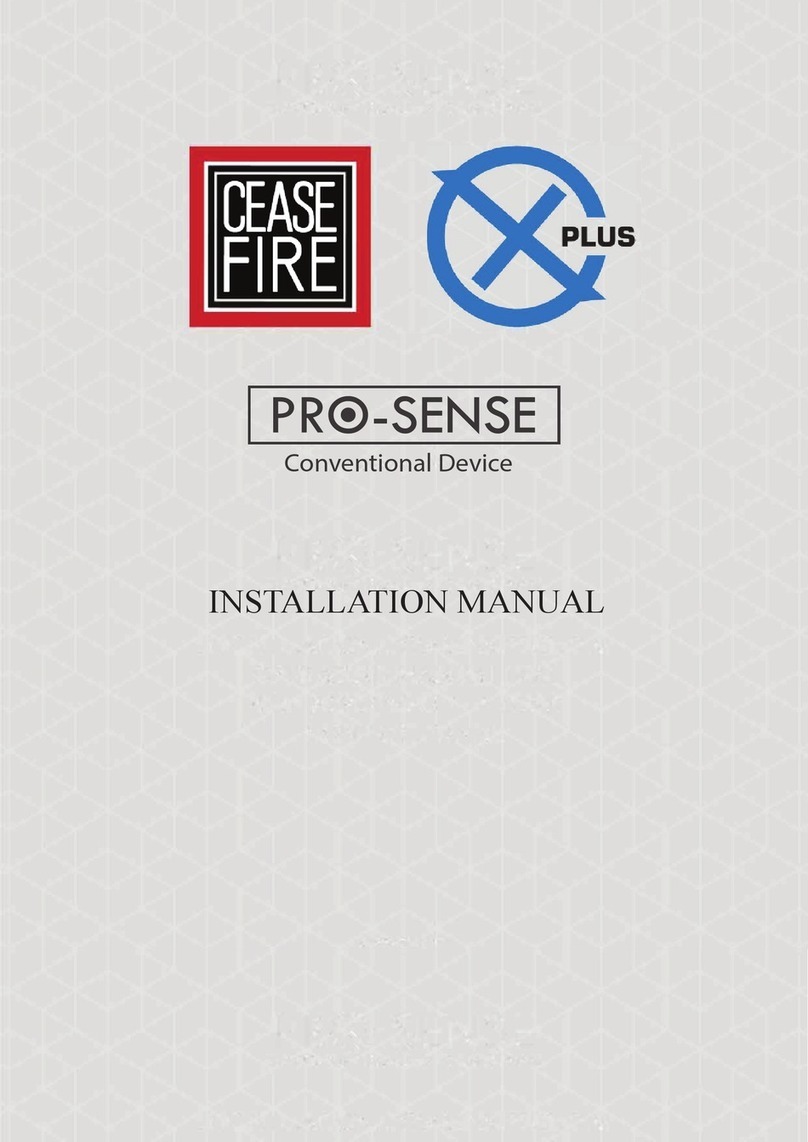
Ceasefire
Ceasefire PRO-SENSE TI-002267 installation guide
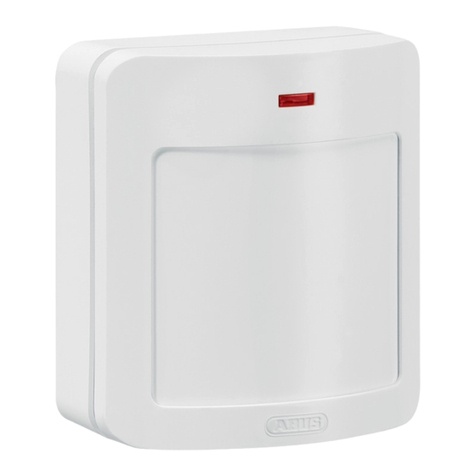
Abus
Abus Secvest 2WAY FU8360 manual
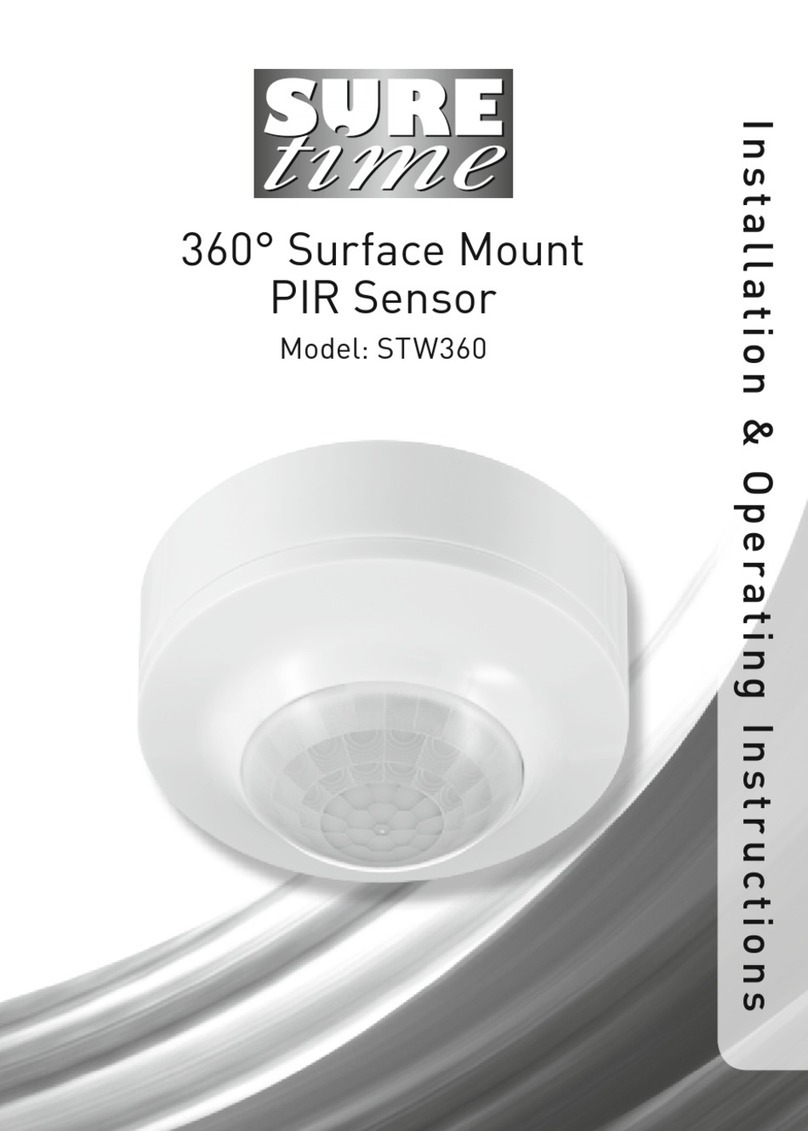
Timeguard
Timeguard Sure Time STW360 Installation & operating instructions
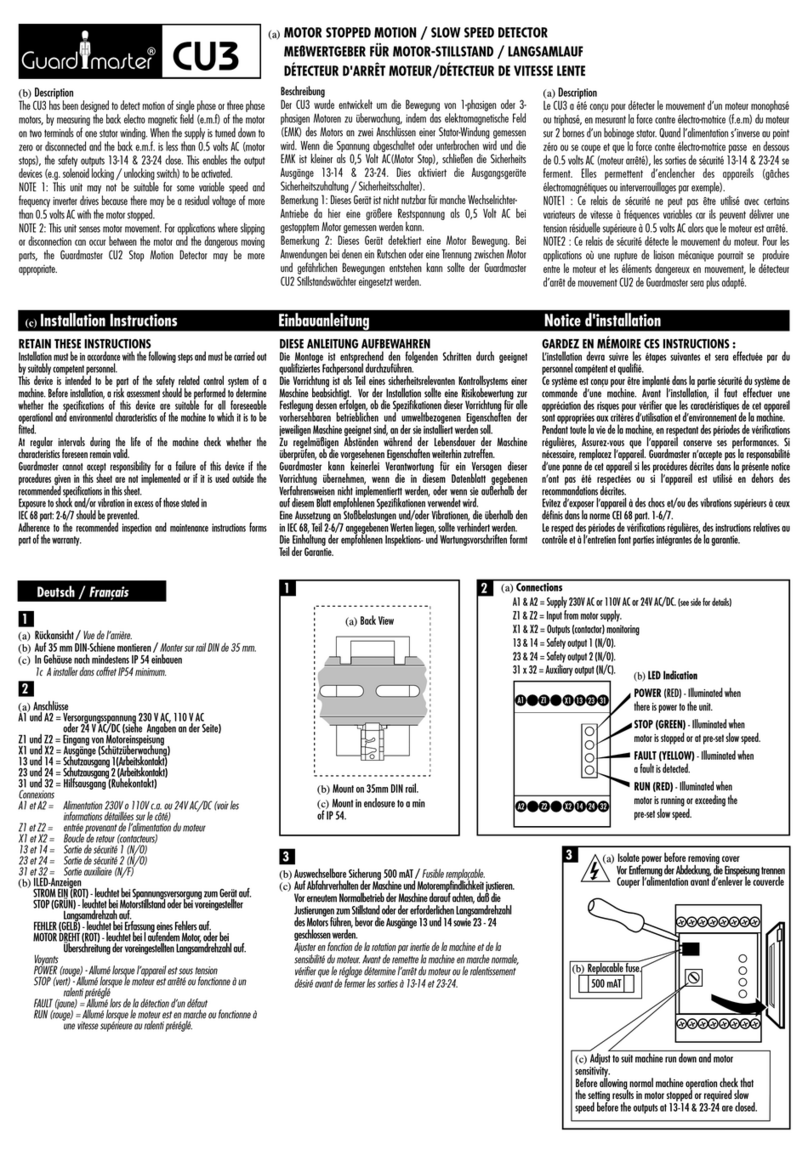
Guard master
Guard master CU3 installation instructions

Heath Zenith
Heath Zenith 5846 manual