VALCOBABY Vici TCD-3 User manual

Valco Instruments Co. Inc.
Rev 1/20
Thermal Conductivity
Detector
Instruction Manual
Model TCD-3
Valco Instruments Co. Inc.
800 · 367· 8424 sales
713 · 688· 9345 tech
713 · 688· 8106 fax
VICI AG International
Schenkon, Switzerland
Int + 41 · 41 · 925· 6200 phone
Int + 41 · 41 · 925· 6201 fax
North America, South America, and Australia/Oceania contact: Europe, Asia, and Africa contact::

This page intentionally left blank for printing purposes

Table of Contents
Introduction
Description .......................................................................................................................................... 1
Operating Principle...........................................................................................................................1
Operational Overview ..................................................................................................................... 2
Safety Notes and Information....................................................................................................... 3
Symbols......................................................................................................................................3
Installation Category............................................................................................................. 3
Safety ..........................................................................................................................................3
Maintenance.............................................................................................................................3
Components of the Detector System ........................................................................................4
Description of Controls, Indicators,and Connectors ............................................................ 5
Hardware Specifications.................................................................................................................6
System Requirements...............................................................................................................................7
Components Not Included with the Detector System ........................................................ 7
PC System Requirements ............................................................................................................... 7
System Purity ......................................................................................................................................7
GC Column Selection.......................................................................................................................7
Recommended Carrier Gas Purifiers .......................................................................................... 7
Carrier Gas Selection........................................................................................................................8
Installation....................................................................................................................................................9
General Precautions .........................................................................................................................9
Component Dimensions.................................................................................................................9
Detector Mounting.........................................................................................................................10
Vertical Mounting.................................................................................................................10
Horizontal Mounting...........................................................................................................11
Gas Connections..............................................................................................................................11
Installing and Purging the Gas Regulator...............................................................................11
Installing and Purging a Purifer..................................................................................................13
Column Connection .......................................................................................................................13
Referenced Mode .................................................................................................................13
Unreferenced Mode.............................................................................................................13
Packed Columns....................................................................................................................14
Packed Columns with Swagelok®-type Female Nut ................................................14
Capillary Columns ................................................................................................................14
Testing for Leaks ..............................................................................................................................14
Cable Connections..........................................................................................................................15
Heater and Filament Connections..................................................................................15
Data Output Cable(s)...........................................................................................................15
Serial Data Extension Cable..............................................................................................15
Digital I/O Cable (optional) ...............................................................................................15
Power Calbe............................................................................................................................15
Flow Rate Settings ..........................................................................................................................16
Installing the Graphical User Interface (GUI) Software......................................................17
Establishing Communication......................................................................................................17
Initial Bakeout and Equilibration........................................................................................................19
Initial Conditioning.........................................................................................................................19
Temperature Settings ....................................................................................................................19
Balancing the Channels ................................................................................................................20

Table of Contents (continued)
TCD Operation with the Graphical User Interface........................................................................21
Control Screen..................................................................................................................................21
Configuration Screen.....................................................................................................................22
Graph Screen ....................................................................................................................................26
STATUS LED States and Troubleshooting ........................................................................................28
Maintenance..............................................................................................................................................29
Cleaning the Enclosure .................................................................................................................29
Bake Out Procedure........................................................................................................................29
Appendix A: Digital I/O Control..........................................................................................................30
Digital I/O Port..................................................................................................................................30
Digital I/O Connector.....................................................................................................................30
Digital Signal Inputs.......................................................................................................................31
Digital Input Functions..................................................................................................................31
Digital Output Signal .....................................................................................................................31
Appendix B: Basic Control of the TCD via Serial Commands ...................................................32
Establishing Serial Communication..........................................................................................32
Initial Bakeout and Equilibration...............................................................................................33
Initial Conditioning..............................................................................................................33
Temperature Settings..........................................................................................................33
Balancing the Channels ................................................................................................................33
Serial Communication Protocols...............................................................................................34
General Console Port Usage.............................................................................................34
Interface Command Editing .............................................................................................34
Serial Commands ............................................................................................................................35
Appendix C: Heater and Filament Connector Signal Descriptions and
Connection Matrices......................................................................................................................36
Warranty .....................................................................................................................................................37
Detector Performance Log ...................................................................................................................38

1
Introduction
Description
The TCD-3 is designed to operate either as a standalone test unit or as a compo-
nent in a larger chromatographic system. The unit consists of a detector cell and
a controller module, plus the required interconnecting cables.
The detector cell includes two separate filaments,A and B,with outputs designated
as Channel A and Channel B. Cell volume has been minimized to accommodate
capillary column chromatography and optimize the sensitivity of the detector
at low flow rates. (Carrier flow rates of 1 –10 mL/min are recommended for best
sensitivity.)
The controller incorporates the electrometer and temperature controls,with a
status light on the front of the controller to indicate system status. The various
states of this bi-color indicator are listed in Table 2 on page 5, along with an
explanation of the indicated status. Digital control lines are provided for
monitoring system readiness and initiating output channel adjustment routines.
In addition, a serial RS-232 port is available for full unit configuration,control,
and monitoring.
Thermal stability is maintained in the detector to within 0.010°C, producing a
stable,low-noise signal. Two sets of analog output signals are available for each
channel: a 10V output signal (with nominal output signals ranging from -10V to
+10V) and a 1V output signal (with nominal output signals ranging from -1V to
+1V). The two signals are identical, other than the 1:10 voltage scaling. A third
channel, Channel AB,is the referenced or differential output,derived from the
difference of the two filament energy states (i.e., Channel A – Channel B).
Operating Principle
The principal of operation is based on the relative change in the thermal conduc-
tivity of the gas passing across the detector filament as components elute from
the column. Heat is lost continuously by the filament through the carrier gas to
the cell wall of the detector. By measuring the amount of current required to
maintain a constant filament temperature as gases of varying thermal conduc-
tivities cross the filament,a chromatographic signal is produced. This process is
non-destructive of the sample and is concentration dependent.
The TCD-3 is unique in its implementation. Since changes in conductivity are
measured only by the change in current required to keep the filament at a
constant temperature,each of the two filaments can be operated independently
without referencing these changes to a matched filament with reference gas.
This constant temperature provides longer filament life and safeguards it from
the extremely high temperatures and oxidation which can occur with high
concentrations of oxidative or corrosive components. Optional signal referencing
is provided to minimize background variables such as column bleed and
temperature programming.
FILAMENT
A
FILAMENT
B
A
FLOW
INLET
B
FLOW
INLET
OUTLET OUTLET
Figure 1: Unique dual filament design

2
Introduction
Operational Overview
System parameters such as detector cell temperature,filament power levels,
output channel nominal voltage levels, and communication settings must be
entered through the serial communications port. This can be done either with
the included Graphical User Interface (GUI) or by entering direct commands with
a terminal emulator program.
New parameters entered into the TCD-3 are saved in non-volatile memory,
becoming the values referenced the next time the controller is turned on.
Once parameters are stored, the TCD-3 may be operated without a serial port
connection, unless testing criteria change and new parameters must be entered.
By default, these stored settings are implemented immediately when the con-
troller is turned on. However, this default behavior can be altered through serial
port commands. A start-up delay may be added, allowing other system compo-
nents to initialize before the TCD-3 is enabled. Or, the TCD-3 may be configured
to power-up in an idle mode, in which no power is applied to the detector heat-
ing elements until a serial command is received. Refer to “Appendix B: Basic TCD
Operation via Serial Commands” on page 32 for further details on these options.
Once the TCD-3 is enabled, the controller applies power to the detector heaters
until the detector reaches its target temperature setting. The TCD-3 then
monitors the temperature until it is within the minimum accuracy setting for
30 minutes,at which point the system is reported as stable. System stability is
indicated via the controller’s front panel status LED, the READY digital output
signal (available on the rear on the unit), and through the RS-232 communication
port.
After the detector has reached thermal stability (with constant carrier gas flow),
the filament channels of the detector achieve a low-drift,low-noise operational
state. Measurements of the energy states of the detector filaments are avail-
able from the controller’s three analog output channels. Output Channels A
and B reflect the energy state of filaments A and B, respectively.The third analog
output, Channel AB,is a referenced output derived from the difference of the two
filament energy states (i.e., Channel A – Channel B).
Each of these analog signals has a very narrow bandwidth, and is generated as
an offset from a reference voltage. The level of this reference voltage varies, as it
is dependent upon system temperature, filament power, environment,carrier gas,
etc. Because of this variance,the output channels must occasionally be adjusted
so that their signals are within the output limits of the unit. This adjustment
process, which tunes the reference voltage until the differential output signal
level matches the desired voltage, is often referred to as“zeroing”(although the
process can actually be used to adjust the output levels to values other than 0 V).
The zeroing routine should be initiated before each chromatographic test to
correct for any signal drift between tests. The routine should not be executed
until the detector temperature has had adequate time to settle and stabilize. If
the signal is currently out of range, the routine may take up to 10 seconds to
complete. However, once the channel is within the control band, the adjustment
routine should complete within 2 seconds.
Once the TCD-3 system has been properly plumbed, the detector has reached
thermal stability, and the output channels have been“zeroed”, the TCD-3 system
is ready for use.

3
Safety Notes and Information
Symbols
HOT SURFACE
The surface of the detector body may be hot while in operation
(possibly in excess of 250°C). Caution should be observed.
ATTENTION
Refer to the manual.
PROTECTIVE EARTH
This internal connection provides protection against electric
shock from mains voltages and should not be removed.
Installation Category
This equipment has been designed for installation (overvoltage) II, pollution
degree 2. It has been approved for use only in heavy industrial environments and
may not be used in the residential,commercial, or light-industrial environment.
Safety
This instrument has been designed and tested in accordance with the product
safety standard,EN61010. It has left the factory in a safe condition.This instruction
manual contains important information and warnings which must be followed
by the user to ensure safe operation and to retain the instrument in a safe condi-
tion. The case, chassis,and measuring terminals are connected to the protective
earth contact of the power inlet. The instrument operates with a DC power cord
having a protective earthing shield conductor. This shield ring must be connected
to an earth ground,either by direct connection or through the external power
supply module. Any such power supply module must have a mains line plug in-
serted in a socket outlet provided with a protective earth contact. The protective
action must not be negated by the use of an extension cord without a protective
conductor. Use only with an approved mains supply cord having a rating of 2A,
250V, or greater. Do not use this equipment in a manner not specified herein.
Maintenance
The exterior of the instrument should be cleaned regularly with a dusting brush.
If necessary, the casing can be cleaned with a moistened cloth (99% water + 1%
mild detergent). Spirit or petroleum ether can be used to remove greasy dirt.
Any other cleaning agents can attack the plastic and painted surfaces.
Under no circumstances should the cleaning fluid get into the instrument.
Petroleum ether is flammable,and care should be taken in its use.
The detector must be returned to the factory when filament replacement is
required.Call VICI Tech Support for return authorization.
Introduction

4
Components of the Detector System
Components of the detector system are listed in Table 1. Check the contents of
the package(s) to verify that everything is present. Contact the factory if anything
is missing or damaged. (NOTE: Damaged shipments must remain with the original
packaging for freight company inspection.)
Qty Description Product no.
1Detector cell/oven module with nickel-iron filaments TCD3-NIFED
with tungsten-rhenium filaments TCD3-WRED
1Controller unit TCD3-C
1* Power supply, 120w AC/DC,48 V I-25850
1* Power supply cord 115 VAC I-W-17600
230 VAC I-W-17850
3Analog output cables I-25487
1RS-232 cable I-W-RS232-4K
1Digital I/O connector I-T1790124
1Fittings kit TCD3-KIT
Includes: 21/16" zero dead volume union ZU1C
21/16" zero dead volume nut ZN1
21/16" zero dead volume ferrule ZF1
2Fused silica adapter
for 0.8 mm OD capillary column
FS1R.8
* Models TCD3-NIFED-X and TCD3-WRED-X include no power supply or power cord.
They ship with a 48V unterminated power cable with plug, product number I-W-R7B-4.
Introduction
Table 1: Components of TCD3 system
Figure 1: Components of TCD-3 system

5
Description of Controls, Indicators, and Connectors
Front Panel Indicators
1. POWER indicator
This green LED will be illuminated when power is connected to the unit and the
power switch is on (rear panel).
2. STATUS indicator
This LED conveys the status of the TCD-3 system. Table 2 lists the various states
indicated by this LED.
LED mode Explanation
Steady green Detector temperature stable; system ready
Slow green blink Detector cell temperature not yet stable
Red w/ green flash BAUD rate change initiated;waiting for user confirmation
Red/green toggle (fast) Parameter save in progress (do not power-off unit)
Fast red blink Detector cell not found
Fast green blink Auto-zeroing operation in progress
Red/green alternating Auto-zeroing function failure
Green w/ red flash Output channel(s) off scale
Steady red Hardware initialization failure
Table 2: Status indicator explanations
Make sure the ON/OFF switch is in the OFF position
when making power, heater, and filament connections.
Hot-plugging these system elements is not recommended.
3. ON/OFF switch
This is the main power switch for the TCD-3 system. When the switch is in the
OFF position, there is no power to the TCD-3 electronics,detector filaments,and
heater.
Figure 2: Front (left) and rear panels of the TCD-3 controller
Introduction

6
4. 48 VDC connector
The 4' cable from the 48 VDC power supply is plugged into this connector.
5. RS 232 connector
Connect the controller to a PC via a standard DE9 extension cable (M-F). This
DE-9F connector conforms to EIA-232C standard pin-outs for a DCE device.
6. DIGITAL I/O connector
This connector provides three digital inputs and one digital output signal.
Refer to“Appendix A: Digital I/O Control”on page 30.
7. HEATERS connector
The heater cable from the detector mates with this connector.
8. FILAMENTS connector
The filaments cable from the detector mates with this connector.
NOTE: The HEATER and FILAMENTS connectors carry
live voltages, and should only be used with equipment
having no accessible live parts.
9. ANALOG OUT connector
This is normally connected to a data acquisition system or other recording device.
For convenience, full-scale 0 - 1V and 0 - 10V outputs are provided,with an internal
signal reference (-) at zero volts.For best noise performance, the shield (earth)
and signal reference (-) should not be connected together.
Hardware Specifications
Parameter Minimum Nominal Maximum Units Notes
Controller input voltage 44 48 52 V
Controller input current 0.1 1.5 A Vin = 48 Vdc
Input fusing 2.0 A Internal fuse,time delay type
Operating Temperature -10 40 °C
Storage Temperature -25 70 °C
Humidity 0 95 % Non-condensing
Controller weight 1.4 lbs. Without cables
Detector cell weight 3.0 lbs. Standard configuration
Detector temperature ambient 300 °C
Detector pressure 1 1000 psi Working pressure
Heater power 60 W Vin = 48 Vdc
Analog output (1V) -1.2 1.2 V 1V output signal
Analog output (10V) -12 12 V 10V output signal
Analog out impedance 100 Ω
Digital inputs -0.5 5.5 V Internal 4.7kΩpull-up to +5V
Digital input, logic high 2.0 V Minimum logic-high threshold
Digital input, logic low 0.8 V Maximum logic-low threshold
Digital output, voltage -50 50 V Open contacts; maximum volts
Digital output, current -0.5 0.5 A Continuous current rating
Table 3: Hardware specifications
Introduction

7
System Requirements
Components Not Included with the Detector System
• Carriergas(99.999%purityisrecommended)
• Ultrahighpuritygradegaspressureregulatorwithstainlesssteeldiaphragm
(recommended)
• Anyspecialadaptersrequiredforconnectiontothegasregulator
• Flowmeasuringdevice
PC System Requirements
Configuration of the TCD-3 system requires a PC or similar device with a dedicated
asynchronous serial port. This port will operate at 115200 BAUD (8N1).
If the unit will be configured using the console interface,the PC must have terminal
emulation software installed. There are numerous such emulators available for
free on the internet.
If the Graphical User Interface is to be used for system configuration, the PC must
be running the Windows 7/8/10 operating system.
System Purity
Since detection of low concentrations depends in part on the purity of the
carrier, the purest carrier available must be used in order to achieve the lowest
possible detection limit. To maintain carrier purity, extra care must be taken to
assure that the delivery system is clean and free of leaks. Use stainless steel
tubing (cleaned to removed manufacturing solvents) instead of nylon or PTFE
tubing,which can diffuse contaminants into the carrier.
GC Column Selection
Cell volume has been minimized to accommodate capillary, megabore,and
micropacked columns,and to optimize the sensitivity of the detector at low flow
rates. However, standard packed columns may also be used if sensitivity is not an
issue.
Recommended Carrier Gas Purifiers
The Valco Helium Purifier (product number HP2) and Nitrogen Purifier (product
number NP2), which utilize a rare earth gettering alloy to effectively remove
contaminants, are recommended for ppm level analysis of permanent gases.
For other applications,economical and convenient VICI Metronics purifiers are
appropriate.Order the P300-1 for nitrogen, P200-1 for hydrogen,or P100-1 for
helium and other inert carrier gases.

8
Carrier Gas Selection
The detector’s response to a component is based upon the difference between
the thermal conductivities of the component and the carrier gas; the greater the
difference, the greater the response. The table below shows thermal conductivi-
ties for a variety of light gases, given in units of milliwatts per meter per degree
Kelvin. The values listed are given for test conditions at 300°K and 100 kPa.
Gas1
Thermal Conductivity
(mW/m/°K)
Hydrogen 186.6
Helium 155.7
Neon 49.4
Methane 34.4
Oxygen 26.5
Air 26.4
Nitrogen 26.0
Carbon monoxide 25.0
Water 18.6
Argon 17.7
Carbon dioxide 16.8
Table 4: Thermal conductivities of common gases
As an example, note in the table that the thermal conductivity of hydrogen
is 186.6 and helium is 155.7, while nitrogen is only 26.0. Argon is even lower,
at 17.7. Since the largest difference in thermal conductivity yields the best
response,detection of small amounts of hydrogen is better done with argon
or nitrogen carrier than with helium.
However, while nitrogen as a carrier yields excellent response to hydrogen,
the response to oxygen and carbon dioxide is diminished compared to the
levels that could be achieved with helium or hydrogen. Argon would yield
poor response to carbon dioxide and water, but would be adequate for other
components.
There is no absolute“best choice”of carrier gas. For any situation,the choice
must take into account all of the parameters involved:column characteristics,
components of interest and their concentrations,safety considerations,carrier
cost, etc.
System Requirements
1 Harvey,Allan H. & Huber,Marcia L., 06 June 2011,Thermal Conductivity of Gasses, CRC Handbook
of Chemistry and Physics,92nd Ed.,6-240, www.nist.gov/node/599951

9
Installation
The detector is usually mounted on top of the GC column oven.The cord for the
TCD controller is 3 m (10') long (AC cord + desktop supply + power cord); the
detector cable and the signal output are 1.2 m (4') long.
General Precautions
• Donotturntheunitonuntilthecarriergasisowingthroughthedetector.
• Donotshutoffordisconnectthecarriergaswhenthedetectorishot,evenif
the unit is turned off. Turn off the power switch on the back of the controller
and allow the detector to cool down naturally before disconnecting or shut-
ting off the carrier gas.
• Positionthecontrollerunitwherethepowerswitchontherearpanelcanbe
reached easily
Component Dimensions
Figure 3: TCD-3 controller dimensions
4.75"
3.50"
0.56"
FRONT PANEL
(FRONT)
4"
3.67"
3.08"
0.56"
BOTTOM VIEW
0.25"
Figure 4: TCD-3 power supply dimensions

10
Figure 5: TCD-3 detector cell/oven module dimensions
Installation
Detector Mounting
Vertical Mounting
The detector has no particular orientation requirements,but it should have
adequate thermal isolation from the column oven and injection port. Most GCs
have an existing opening which will allow the TCD-3 detector module to sit verti-
cally on top of the column oven with the column inlet extending into the oven.
If an existing detector is being replaced, the TCD-3 can usually be set in its place.
If not, use a drill or chassis punch to make a hole of the proper size,and set the
detector in position.
While trying to match base plate mounting holes to every GC on the market is
impractical, the mounting holes for the TCD-3 have been located so that at least
two of them should align with existing holes on the GC. (Figure 5) Orient the
detector to allow for easy cable and gas connections.The inlet lines installed
into the detector must enter the column oven and permit column connection.
Temperature loss between the column outlet and the detector should be
minimized to prevent possible condensation of the sample.

11
CAUTION: Do not mount the detector near the column
oven cool-down vents.
Horizontal Mounting
Some older GCs have access to the column oven through the side of the GC.
This does not present a problem as far as operation of the TCD-3 is concerned.
Drill a hole at the appropriate location,orient the detector for convenient
connection, and mark the position of the mounting holes. Drill the mounting
holes and secure the detector to the side of the GC with four sheet metal screws
(not supplied).
Gas Connections
When making gas connections, remember these three points:
• Allsurfacesthatcontactthegasstreammustbeglassorstainlesssteel
• Donotusecoppertubingorbrassttings
• Alltubesmustbethoroughlycleanedandbakedbeforeuse.
The instructions below assume that the detector carrier will be supplied from
a nearby cylinder. Since the distance from the carrier supply to the GC will vary
from installation to installation,tubing is not supplied for the supply-to-GC
connection. Consult the VICI catalog or vici.com for any fittings and tubing
required.
The figures on the next page illustrate gas connections for a typical TCD-3
detector system in unreferenced (Figure 6) and referenced (Figure 7) modes.
Installing and Purging the Gas Regulator
1. Make sure the on/off valve on the carrier gas cylinder is completely closed.
Screw the CGA fitting nut of the regulator into the gas cylinder. Go beyond
finger-tight, but do not tighten the nut all the way – some leakage is required
for the purging operation.
2. Turn the output pressure regulating knob completely counterclockwise.
3. Open the cylinder on/off valve slightly and quickly close it again.
4. Adjust the tightness of the regulator connecting nut to allow a pressure
reduction of ~690 kPa/sec (100 psi/sec).With a new bottle, the gauge should
start out at about 14 MPa (2000 psi).
5. When the pressure drops into the 1.4 - 3.4 MPa (200 - 500 psi) range, open the
cylinder on/off valve slightly and quickly close it again.
6. Repeat Step 5 eight or ten times to be certain that all the air is purged. On the
final purge, tighten the regulator connecting nut very securely as the pressure
approaches the 2.1 - 3.4 MPa (300 - 500 psi) range.
7. Open the cylinder valve to pressurize the regulator once again,then close it
and observe the high pressure gauge needle for 15 minutes.If it doesn’t move,
there is no critical leak on the high pressure side of the regulator.
Installation

12
Figure 6: TCD-3 plumbed for operation in unreferenced mode
Figure 7: TCD-3 plumbed for operation in referenced mode (A-B)
CAUTION: Never use leak detecting fluids on any part of
the TCD-3 system.
Installation

13
Installing and Purging a Purifier
1. If the pressure regulator has a 1/8" male cone-type outlet port, install a Valco
1/8" external to 1/16" internal reducer (EZR21); if it has a 1/4" male cone-type
outlet port, install a Valco 1/4" external to 1/16" internal reducer (EZR41). For
other regulator outlet fittings, a wide variety of Valco adapters are available.
2. While keeping the outlet tube capped,remove the cap from the inlet tube
of the Valco helium purifier and insert the tube fitting into the 1/16" reducer
port. Use a 1/4" wrench to turn the nut one-quarter turn past the point where
the ferrule first starts to grab the tubing. Do not remove the fitting. When
made up properly, it should be leak-tight.
3. Turn the output pressure regulating knob clockwise until the gauge registers
345 KPA (50 psi).
4. Allow five minutes for equilibration,then turn the regulating knob all the way
counterclockwise.
5. Observe the needle of the output pressure gauge for 15 minutes. There will
be a slight initial drop, but if it doesn’t move after that,consider that all the
connections are tight.
6. If necessary, use an electronic leak detector to locate any leaks. If a leak
detector is not available,tighten all the fittings (including the output
pressure gauge),and repressurize the system for another test.
7. Uncap the outlet tube of the purifier and purge the system for 15 to 30 minutes
at 60 to 80 mL/min to eliminate air from the purifier getter material.
Column Connection
To prevent detector contamination, it is strongly
recommended that the column be disconnected
from the detector during column bake-out procedures.
Referenced mode
In the referenced mode,the column is connected to the Channel A inlet, and the
carrier gas stream is split and used as a reference in channel B. The gas flow rate
from both channels must be the same (flow balanced). This mode of operation
provides the best baseline stability and the least background noise.
Unreferenced mode
In the unreferenced mode,Channels A and B are used independently. One column
connects to the Channel A inlet, and the other to Channel B. The carrier gas must
be the same for both channels. It is also possible to use only one channel with
the other capped off, as long as the filament temperature control of the unused
channel is set to minimum.
The unreferenced mode has certain limitations. There is a possibility of detector
cross-talk (interference) if compound concentrations exceed 1%. Also,baseline
drift and background noise are greater compared with the referenced mode.
EZR21
Installation

14
To make column connection as convenient as possible, each TCD is shipped with
two Valco 1/16" unions (Product No.B-ZU1C), with nuts and ferrules (Product Nos.
ZN1 and ZF1). Also included are two fused silica adapters (FSR1.8) for use with
.53 mm ID wide bore capillary columns (.8 mm OD). Refer to the information
below to determine the correct Valco fitting for use with other columns.
Packed Columns
A 1/16" packed column requires only the ZU1C which comes with the TCD3. For
1/8" columns, a ZRU21 fitting is required.
Packed Columns with Swagelok®-type Female Nut
The connection of these columns is similar to that for standard packed columns,
but requires a union which adapts the female nut to the Valco fitting.
Capillary Columns
Connection of these columns requires the use of the ZU1C with the appropriate
fused silica adapter. For a .53 mm ID x .8 mm OD column,use the FSR1.8 supplied
with the TCD. For other sizes,use this table to determine the proper adapter:
ZU1C with fused silica adapter
Column size
.32 mm ID x .5 mm OD
.25 mm ID x .4 mm OD
< .2 mm ID
Adapter required
FS1R.5
FS1R.4
FS1R.2
Testing for Leaks
It is critical for the system to be leak-tight,and an additional check at this point
can prevent issues later on. To test for leaks:
1. Ensure that both outlets are capped.
2. Pressurize the entire system with helium to 138 kPa (20 psi).
3. If the system does not hold pressure, check all the fittings with an electronic
helium leak detector. DO NOT use leak detecting liquids.
Installation

15
Cable Connections
Before connecting the any detector cables to the control
module, make sure that the control module power cord
is unplugged and the TCD3 controller power switch is
off. Hot-plugging system elements is not recommended.
NOTE: The HEATER and FILAMENTS connectors carry
live voltages, and should only be used with equipment
having no accessible live parts.
Heater and Filament Connections
The heater and filament connections from the detector to the rear panel of the
controller are made via two cables.(Figure 8) Cable functions are clearly marked
on the detector, as are the connectors are the controller.
After making sure that the controller power cord is not plugged in,connect the
cables to the appropriate connectors on the control module. The cable connectors
should be inserted into the controller sockets until they latch securely into place.
Pin assigments are indicated below.
Data Output Cable(s)
Connect the data output cable(s).The A / B / A-B outputs are typically used with
an integrator or PC-based data acquisition system. Polarities and full scale range
are indicated in Figure 8. Set the recorder (DAQ) for the same voltage scale.
Serial Data Extension Cable
The TCD-3 connects to a PC/laptop via a RS-232C connection. The provided DE-9F
port on the rear panel of the TCD3-C unit uses industry standard (EIA-232-C)
pin-outs for a DCE device. Connect this port to a standard PC serial port using a
standard RS-232C serial data extension cable (male to female).
Digital I/O Cable (optional)
In addition to the serial communication port described above,the TCD-3 controller
also provides digital signals for monitoring and control of the system. Refer to
“Digital I/O Control”on page 30.
Power Cable
Plug the 4' cable from the 48 VDC power supply into the connector labeled 48VDC
on the rear panel of the controller, but do not plug the power supply into the 110
or 230 VAC source.
Installation

16
Figure 8: TCD-3 cable connections
Installation
Flow Rate Settings
Since the TCD-3 is a concentration-dependent detector, the lower the flow rate
through the detector, the higher the sensitivity. Column diameter will determine
the optimum column flow rate.
The microvolume TCD-3 is designed for the lower flow rates typical for capillary
columns,and achieves best sensitivity at rates below 10 mL/min. Since the fila-
ments are maintained at constant temperature, the detector can be operated at
extremely low flow rates (less than 0.5 mL/min) without damage to the filaments.
1. Measure the column flow at the detector’s Channel A out. The optimum flow
rate is in the range of 4 – 20 mL/min,with the actual rate dependent on the
type of column used.
2. Measure the reference gas flow at Channel B out. It should be as close as
possible to the GC column flow. Use a fixed flow restrictor or a good quality
flow controller to match the carrier gas and reference gas flows.
3. Once the flows have been established, connect the 48VDC power supply to the
TCD controller unit,plug it into an appropriate source, and turn the power on
via the rear panel switch.
Table of contents
Popular Security Sensor manuals by other brands
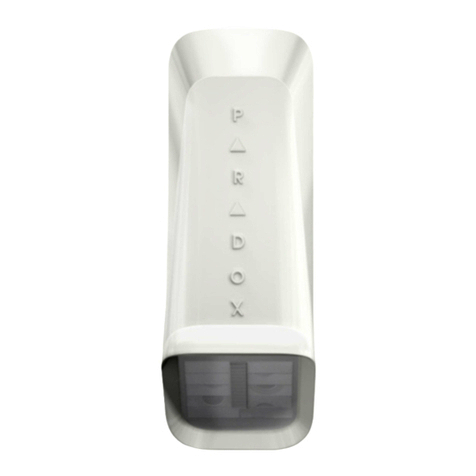
Paradox
Paradox NV35MR installation manual
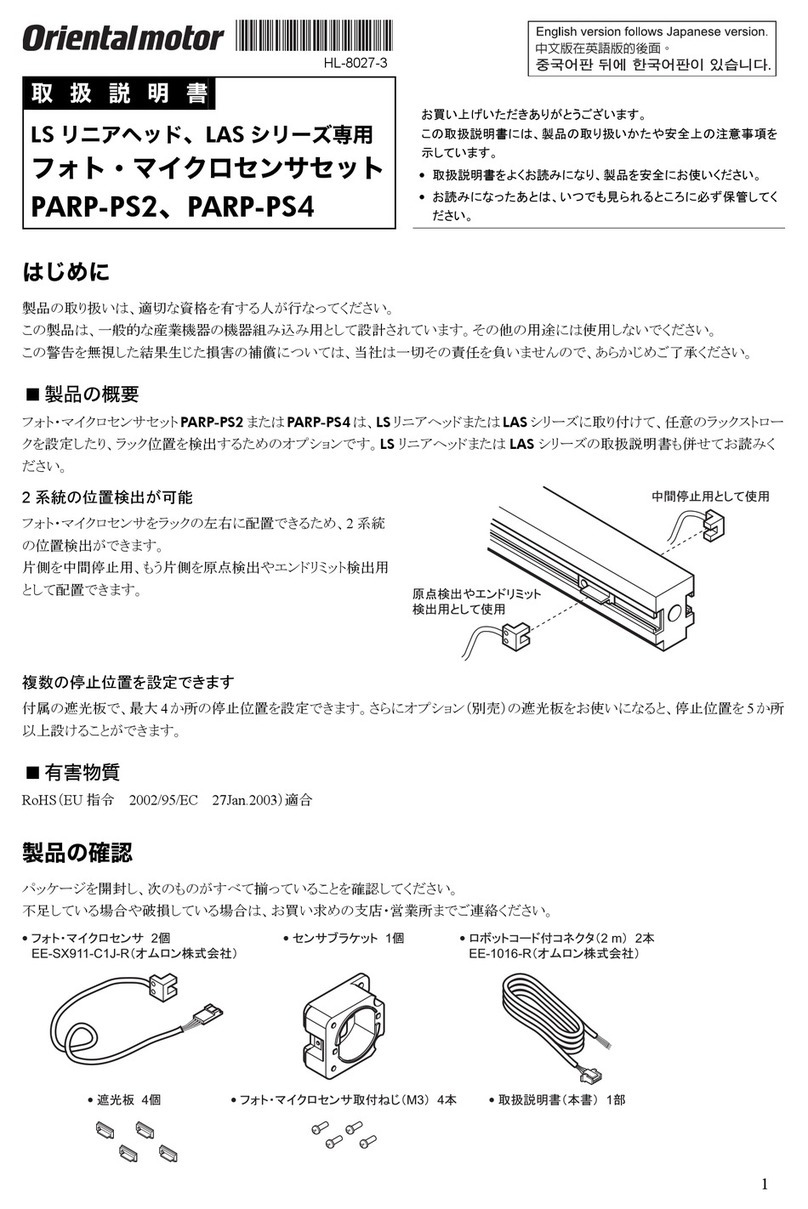
Oriental motor
Oriental motor LS Series operating manual

PROPOINT
PROPOINT 8595258 user manual

L3 Communications
L3 Communications Narda 8950/10 Operation and installation guide
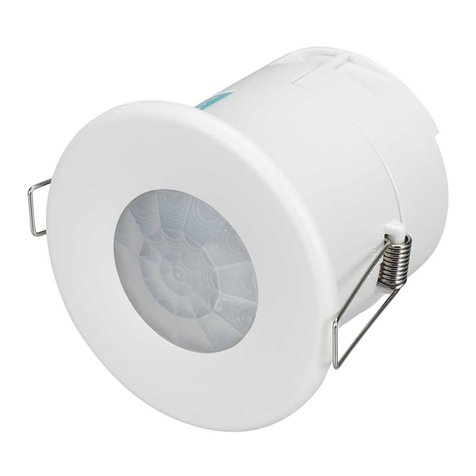
C.P. Electronics
C.P. Electronics EBDSPIR-DD-LV installation guide
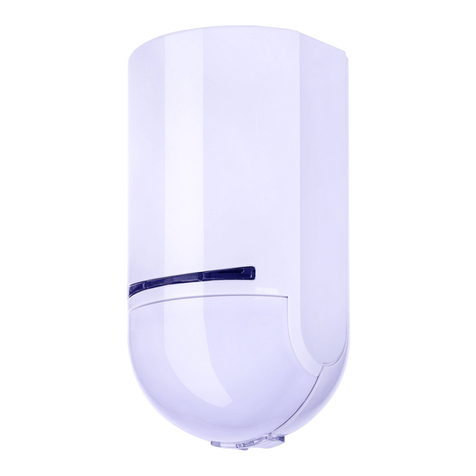
Abus
Abus FUBW50110 Installation instructions and user manual