NSD Varlimit VS-212DN User manual

U S E R ' S M A N U A L
V S -212D N
NSP-Z2004-7


6. Operation
- Do not change the controller's function switch settings during the
operation; otherwise, it will cause injury.
- Do not approach the machine after instantaneous power failure
has been recovered.
Doing so may result in injury if the machine starts abruptly, it will
cause injury.
- Be sure to check that the power supply specifications are correct;
otherwise, it may caused controller failure.
- Be sure to provide an external emergency stop circuit so that
operation can be stopped with power supply terminated immediately.
- Be sure to conduct independent trial runs for the controller before
mounting the controller to the machine;
otherwise, it may cause injury.
- When an error occur, be sure to eliminate the cause, ensure
safety, and reset the error before restarting operation;
otherwise, it may cause injury.
7. Maintenance And Inspection
- Do not disassemble, remodel, or repair the unit;
otherwise, it will cause electric shock, fire, and unit malfunction.
- The capacitor of the power line deteriorates through prolonged use.
We recommended that the capacitor be replaced every five years
to prevent secondary damage.
8. Disposal
- Be sure to handle the controller as industrial waste while
disposing of it.
1. Handling Precautions
- Do not touch components inside of the controller;
otherwise, it will cause electric shock.
- Do not damage the cable by applying excessive load, placing
heavy objects on it, or clamping;
otherwise, it will cause electric shock or fire.
DANGER
- Turn the power supply OFF before wiring, transporting, and inspecting
the controller; otherwise, it may cause electric shock.
- Provide an external safety circuit so that the entire system
functions safely even when the controller is faulty.
- Connect the grounding terminal of the controller;
otherwise, it may case electric shock or malfunction.
- Do not use the controller in the following places; water splashes,
the atmosphere of the corrosion, the atmosphere of the flammable
vapor, and the side of the combustibility.
Doing so may result in fire or the controller may become faulty.
- Be sure to use the controller and the ABSOCODER sensor in the
environment designated by the general specifications in the manual.
Failure to do so may result in electric shock, fire, malfunction or unit
failure.
- Be sure to use the specified combination of the ABSOCODER
sensor, controller and sensor cable; otherwise, it may cause fire or
controller malfunction.
CAUTION
2. Storage
CAUTION
- Do not store the controller in a place exposed to water, or toxic
gas and liquid.
- Be sure to store the controller in designed temperature and humidity
range, and do not exposed to direct sunlight.
- Be sure to consult with NSD when the controller is stored for long
periods.
- Do not hold the cable or shaft of ABSOCODER sensor during
transport; otherwise, it will cause injury or controller malfunction.
CAUTION
3. Transport
Thank you very much for purchasing our product.
Before operating this product, be sure to carefully read this manual so that
you may fully understand the product, safety instructions and precautions.
- Please submit this manual to the operators actually involved in operation.
- Please keep this manual in a handy place.
Symbol Meaning
DANGER
Incorrect handling may cause a hazardous situation that
will result in moderate injury or physical damage.
Incorrect handling may cause a hazardous situation that
will result in death or serious injury.
Instructions accompanied by a symbol may also result in serious
damage or injury. Be sure to follow the all instructions accompanied by the symbol.
Graphic Symbols
Symbol Meaning
Indicates prohibited items.
Indicates items that must be performed to.
This product is not designed to be used under any situation affecting human
life. When you are considering to use this product for special purposes such as
medical equipment, aerospace equipment, nuclear power control systems,
traffic systems, and etc., please consult with NSD.
This product is designed to be used under the industrial environments categorized
in Class A device.
The supplier and user may be required to take appropriate measures.
CAUTION
CAUTION
Application Limitation
4. Installation
- Do not step on the ABSOCODER sensor or place heavy objects on
the controller; otherwise, it will cause injury.
- Do not block the exhaust port or allow any foreign matter to enter
the controller; otherwise, it will cause fire or unit failure.
- Be sure to secure the controller and ABSOCODER sensor with the
provided brackets; otherwise, it may cause malfunction, injury, or
drop.
- Be sure to secure the specified distance between the main body
and the control panel or other equipments; otherwise, it may cause
malfunction.
5. Wiring
- Be sure to secure the terminal block firmly; otherwise, it may have
risk of fire.
- Be sure to mount the terminal cover provided with the controller,
before supplying the power, starting operation after the installation,
and wiring; otherwise, it may cause electric shock.
- Be sure to keep the sensor cable, control cable, and communication
cable at least 300 mm away from the main circuit and power line;
otherwise it may cause injury or malfunction.
- Be sure to connect all cables correctly; otherwise, it may cause injury
or controller malfunction.
- Be sure to firmly connect the external I/O connectors and sensor
connectors; otherwise, it may cause incorrect inputs and outputs or
injury.
CAUTION
CAUTION
(Please read this safety guide carefully before operation)
GENERAL SAFETY RULES
DANGER
CAUTION
CAUTION
CAUTION
Signal Words
Safety precautions in this guide are classified into DANGER and CAUTION.

Revision History
* The Document No. appears at the upper right of this manual's cover page.
Document No.
Date
Revision Description
NSP-Z2004
11, Mar., 2002
1st Edition
Japanese document: ZEF003800201
NSP-Z2004-1
6, Feb., 2006
2nd Edition
Japanese document: ZEF003800201
NSP-Z2004-2 1, Feb., 2008 3rd Edition
Japanese document: ZEF003800201
NSP-Z2004-3
8, Jan., 2014
4th Edition
Japanese document: ZEF003800202
NSP-Z2004-4 18, Nov., 2014 5th Edition
Japanese document: ZEF003800203
NSP-Z2004-5
4, June, 2015
6th Edition
Japanese document: ZEF003800204
NSP-Z2004-6
23, Mar., 2016
7th Edition
Japanese document: ZEF003800205
NSP-Z2004-7 8, Mar., 2019 8th Edition
Japanese document: ZEF003800206

CONTENTS
1. OVERVIEW .................................................................................................. 1-1
1.1 Features .................................................................................................. 1-2
1.2 Definitions .................................................................................................. 1-3
2. SPECIFICATIONS ......................................................................................2-1
2.1 General Specifications ..........................................................................2-1
2.2 Performance Specifications ............................................................. 2-1
2.3External Input / Output Specifications .................................................2-2
2.4Terminal Block Input / Output Specifications .....................................2-3
2.5DeviceNet Specifications ..........................................................................2-3
2.6ABSOCODER Sensor ..........................................................................2-4
2.7Extension Cable Specifications ............................................................. 2-4
3. DeviceNet .................................................................................................. 3-1
3.1 Control Panel Settings ......................................................................... 3-1
3.2 Control Panel Display ......................................................................... 3-2
3.3 Interface .................................................................................................. 3-3
3.3.1 OUT Data Format (Consumed Connection) ........................ 3-3
3.3.2 IN Data Format (Produced Connection) .................................... 3-4
3.3.3 Error Codes ......................................................................... 3-5
3.4 Signal Explanations ......................................................................... 3-5
3.4.1 Command Bit ......................................................................... 3-5
3.4.2 Status Bits ......................................................................... 3-6
3.5 Buffer Memory List ......................................................................... 3-7
3.5.1 Manual Mode Input/Output Status Reading ........................ 3-15
3.5.2 Error Code Reading ............................................................. 3-15
3.5.3 Function Selection (Parameter Writing) .................................... 3-15
3.5.4 Sequence Mode Selection Writing .................................... 3-15
3.5.5 Sequence Mode Answerback Reading .................................... 3-16
3.5.6 Sensor Binary Current Position Value Reading ........................ 3-16
3.5.7 Scaling Binary Current Position Value Reading ........................ 3-16
3.5.8 Speed Output Reading ............................................................. 3-17
3.5.9 Hold Current Position Reading .................................................3-18

3.5.10 Preset Value Writing for Current Position Preset Input ............3-18
3.5.11 Current Position Preset ‘Input Disabled’ Setting (Writing) ............3-18
3.5.12 Target Stop Position Writing .................................................3-19
3.5.13 Forward/Reverse Stop Zone After Learning Function (Reading) ... 3-19
3.5.14 Speed Limit Writing ............................................................. 3-19
3.5.15 Buffer Memory Selection For Positioning Pattern Data (Writing) ... 3-19
3.5.16 Medium-Speed Zone Writing .................................................3-19
3.5.17 Low-Speed Zone Writing ............................................................. 3-20
3.5.18 FWD/RVS Stop Zone Writing ................................................. 3-20
3.5.19 In-Position Zone Writing ............................................................. 3-20
3.5.20 Limit Switch Output Status Reading .................................... 3-20
3.5.21 Program No. Answerback Reading .................................... 3-21
3.5.22 Limit Switch “Output Disabled” Setting (Writing) ........................ 3-21
3.5.23 Program No. Setting (Writing) ................................................. 3-21
4. Function List .................................................................................................. 4-1
4.1 Current Position Detection Function .................................................4-2
4.2 Positioning Function ......................................................................... 4-3
4.3 Limit Switch Output Function ............................................................. 4-4
4.4 Nomenclature ......................................................................................4-5
4.5 Explanation of Displays ......................................................................... 4-5
4.5.1 System LEDs ......................................................................... 4-5
4.5.2 DeviceNet monitor LEDs (MS, NS) .................................... 4-5
4.5.3 Monitor Display ......................................................................... 4-6
4.6 Explanation of I/O ......................................................................................4-7
4.6.1 Terminal Block I/O ............................................................. 4-7
4.6.2 Connector I/O ......................................................................... 4-7
5. Operations .................................................................................................. 5-1
5.1 Operating Sequence (Flowchart) ............................................................. 5-1
5.2 Changing Saved Data ......................................................................... 5-2
5.3 Connecting External Wiring ............................................................. 5-3
5.3.1 Wiring precautions ............................................................. 5-3
5.3.2 Connecting The External Power Supply .................................... 5-3
5.4 ABSOCODER Sensor Installation Precautions .................................... 5-4
5.4.1 Installation of MRE series ABSOCODER sensor ........................ 5-4
5.4.2 Precautions when connecting ABSOCODER sensor ............ 5-4

6. Current Position Detection Function ............................................................. 6-1
6.1 Pre-Operation Setting Sequence ............................................................. 6-2
6.2 Initial Setting ...................................................................................... 6-3
6.3 Initial Setting List ......................................................................................6-3
6.3.1 Sensor selection/sensor rotation direction setting ........................ 6-4
6.3.2 Decimal point position setting .................................................6-4
6.3.3 Scale length and minimum current position value setting ............6-5
6.3.4 Current position value setting ................................................. 6-6
6.4 Parameter Settings ......................................................................... 6-7
6.5 Parameter Setting List ......................................................................... 6-8
6.5.1 Permissible current position change amount setting ............ 6-8
6.5.2 Permissible correction amount setting .................................... 6-8
6.5.3 Current position preset value setting .................................... 6-9
6.5.4 Speed gate time and speed sampling time ........................ 6-12
6.6 Sequence Program Sample ............................................................. 6-13
6.6.1 Initial Settings ......................................................................... 6-13
6.6.2 Parameter Settings ............................................................. 6-15
6.6.3 Program for current position monitor display ........................ 6-17
6.6.4 Program for error code readout and reset ........................ 6-18
7. Positioning Function ......................................................................................7-1
7.1 Explanation of positioning functions .................................................7-3
7.1.1 Unidirectional positioning .................................................7-3
7.1.2 Positioning speed switching format .....................................7-4
7.1.3 Positioning speed stepping format .....................................7-5
7.1.4 Control timing ......................................................................... 7-6
7.1.5 Starting operation from stop zone .....................................7-8
7.1.6 Simple learning function ............................................................. 7-9
7.1.7 JOG operation ......................................................................... 7-10
7.1.8 Operation when detection range is exceeded ........................ 7-12
7.1.9 Current position presetting during positioning operation ............7-14
7.1.10 Operation error ......................................................................... 7-15

7.2 Positioning Function and Operation Sequence .....................................7-16
7.3 Initial Settings ......................................................................................7-17
7.4 Parameter Settings ......................................................................... 7-17
7.5 Parameter List ......................................................................................7-18
7.5.1 Selection of positioning format .....................................7-18
7.5.2 Designation of positioning direction .....................................7-19
7.5.3 Designation of overshoot amount .....................................7-19
7.5.4 Designation of medium-speed zone,
low-speed zone, stop zone, and In-position zone ........................ 7-19
7.5.5 Designation of upper and lower limits .....................................7-19
7.5.6 Start from stop zone setting ................................................. 7-19
7.5.7 Timer settings ......................................................................... 7-20
7.6 Sequence Program Sample ............................................................. 7-21
7.6.1 Initial settings and parameter settings .................................... 7-21
7.6.2 Program for positioning function .................................................7-21
7.6.3 Program for JOG operation .................................................7-23
8. Limit Switch Output Function ..........................................................................8-1
8.1 Pre-Operation Setting Sequence .................................................8-3
8.2 Initial Settings ......................................................................................8-4
8.3 Parameter Settings ..........................................................................8-4
8.4 Parameter List ......................................................................................8-5
8.4.1 Number of protected channels ................................................. 8-5
8.4.2 Offline output status setting
– TEST, INIT, PRM and PRGM mode ........................ 8-5
8.4.3 Offline output status setting – RUN mode ........................ 8-5
8.5 Limit Switch Data setting ..........................................................................8-6
8.5.1 Data setting ..........................................................................8-6
8.5.2 Data setting for program No. 0 .................................................8-8
8.5.3 Writing program Nos. 1-8 ................................................. 8-9
8.5.4 Reading program Nos. 1-8 .................................................8-9

8.6 Sequence Program Sample ............................................................. 8-10
8.6.1 Initial settings and parameter settings .................................... 8-10
8.6.2 Program for limit switch output function .................................... 8-10
8.6.3 Program for limit switch output function (Program No. 0) ............8-12
8.6.4 Writing program to program Nos. 1-8 .................................... 8-17
8.6.5 Reading program from program Nos. 1-8 .................................... 8-21
9. TROUBLESHOOTING ......................................................................................9-1
9.1 Error Code List ......................................................................................
9-1
10. DIMENSIONS .................................................................................................. 10-1
10.1 VS-212DN ......................................................................................10-1
10.2 External setting unit VS-T62 and cable VS-C1S62-2 ........................ 10-2
10.3 External setting unit VS-T62B and cable VS-C62B-2 ........................ 10-3
10.4 ABSOCODER sensor ..........................................................................10-4
10.5 Extension Cable ......................................................................................10-6
11. CE MARKING .................................................................................................. 11-1
11.1 EMC Directives ......................................................................................11-1
11.2 EMC Directive and Standards ............................................................. 11-1
11.3 Low Voltage Directive ..........................................................................11-1
11.4 Restrictions ......................................................................................11-1
Reference 1: Statement of Conformance
Reference 2: Attribute Lists

1-1
1. OVERVIEW
This manual describes the VS-212DN specifications and the operation and programming procedures
when the VS-212DN is used together with DeviceNet.
Designed to replace limit switches, the VS-212DN unit features a rotary position sensor which detects the
machine's position. The detected position is then compared with the setting position value, and the
appropriate motor control signals are output accordingly.
The VS-212DN is equipped with the ABSOCODER rotary position sensor. The ABSOCODER features a
magnetic position detection format, and can be used in place of mechanical cam switches, proximity
switches, and limit switches, etc.
This sensor can be used for automatic control of conveyance systems, press machines, and assembly
machines, etc., where position detection is required. Moreover, the VS-212DN permits ABSOCODER
sensors to be connected to 2 axes for simultaneous 2-axes control.
The VS-212DN is used in conjunction with DeviceNet. DeviceNet is a system which permits position and
control data exchanges with a master unit such as a programmable logic controller (hereafter referred to
as "PLC"), etc.
Because all settings can be specified in DeviceNet, an external setting unit is not required.
(If an external setting unit is needed, the VS-T62 or VS-T62B should be used. VS-T62B is the successor
model to VS-T62.)

1-2
1.1 Features
The VS-212DN has the following features:
(1) Absolute position detection:
Rotational position is detected by an absolute position detection format. Even when a power outage,
etc., occurs, the correct address of the ABSOCODER sensor's current position will be instantly detected
when power is turned back ON.
(2) High resolution:
The 32-turn rotary-type ABSOCODER sensor (MRE Series) offers a resolution factor of 4096 divisions
per 1 turn of the sensor shaft. The resolution factor for a 64-turn rotary-type ABSOCODER sensor is
half the amount given above. Refer to Item 2.6 ABSOCODER sensor for details regarding the relationship
between the number of turns and the resolution. Such high resolution results in high-precision ON/OFF
signal outputs and positioning.
(3) High-speed response:
The VS-212DN ON/OFF signal and motor control outputs are not affected by the PLC's scan time.
These output signals are executed within 4ms after position detection occurs.
(4) Current position preset function:
If a positional discrepancy occurs between the machine's position and the ABSOCODER sensor's
position, the current position can be preset to the desired value by external input. The current position
can also be preset from the PLC via the buffer memory.
(5) Current position hold function:
By detecting the leading edge (OFF→ON) of the current position preset input (external connector), the
current position is stored in the buffer memory and held.
(6) Speed detection function:
The sensor's rotation speed is constantly monitored. The detected value (change in position per
specified time) is stored in the buffer memory for data communication with the PLC CPU as sensor
binary or as r/min..
(7) Unidirectional positioning format:
Regardless of the existing positional relationship between the current position and the target stop
position, positioning is always executed from the same direction. If the target stop position lies in the
opposite direction, position overshooting will occur, with positioning the being executed from the
prescribed direction. Unidirectional positioning reduces error resulting from backlash, etc.
(8) Joint use of positioning function and limit switch output function:
Output of the designated limit switch output signals is possible while positioning is being executed
toward the target stop position.
(9) Two speed control formats:
Either of two speed control formats can be used for the positioning operation:
o Speed switching format in which low-speed/high-speed signal switching occurs.
o Speed stepping format in which a series of low-speed/medium-speed/high-speed changes occur.
(10) Extension of positioning pattern data:
The desired item of positioning pattern data; medium-speed zone, low-speed zone, stop zone, or
In-position zone can be changed via the buffer memory. The stop zone data can be changed separately
for forward direction and reverse direction.
(11) Positioning command speed limit function:
Some limitation can be applied to speed command output for positioning via the buffer memory.
(12) Highly accurate positioning by simple learning function:
If a positional discrepancy occurs between the target position and the current position upon completion
of positioning, the discrepancy will be automatically corrected when positioning is next carried out.

1-3
1.2 Definitions
(1) ABSOCODER
ABSOCODER is the generic name given to the NSD-developed position sensor which detects
rotational/linear displacement, speed, and acceleration, using an absolute position detection format
with a digital (or analog) output.
The ABSOCODER sensor consists of two main components:
The sensor, where displacement is detected by the change in magnetic resistance, and the converter,
where the sensor’s output signal (when an AC excitation signal has been applied to the sensor) is
converted into absolute date.
The converter for Multi-turn type ABSOCODER sensor is built-in to the VS-212DN.
(2) UNIDIRECTIONAL POSITIONING
Positioning toward the target stop position is always executed from a single direction. When
positioning is required in the opposite direction, the target stop position will be overshot, and
positioning will then occur from the prescribed direction (U-turn is made). The unidirectional positioning
format is useful in reducing stop position errors caused by backlash, etc.
(3) IN-POSITION ZONE
During the positioning operation, there may be a slight discrepancy between the point where
positioning ends and the target stop position. At such times, a judgement is required to determine
whether the discrepancy is within a permissible limit. The 'In-position zone' setting is a +/- value to
determine 'in position'. If the positional discrepancy in within the In-position zone, the 'In-Position'
signal output will occur.
(4) OVERSHOOT AMOUNT
This refers to the amount by which the target stop position is overshot before a U-turn is made during
unidirectional positioning.
(5) PROTECTED CHANNEL (LIMIT SWITCH OUTPUT FUNCTION)
This refers to a switch output channel where the switch output ON/OFF setting cannot be changed
during the course of normal operations.
In order to make setting changes at such a channel, its protected status must be cancelled by
designating the 'number of protected channels' setting as '0' in the [PRM] (parameter) mode.
(6) SENSOR SHAFT ROTATION DIRECTION
Depending on the direction in which the ABSOCODER sensor shaft rotates, the position data value will
increase or decrease. For the VS-212DN, two position data areas are available, one for detecting in
the CW direction, and one for detecting in the CCW direction.
For multi-turn type ABSOCODER sensor (MRE series), the following will apply:
o Current position value in the CW direction:
Position data value will increase when the sensor
shaft rotates CW (viewed from shaft direction).
o Current position value in the CCW direction:
Position data value will increase when the sensor
shaft rotates CCW (viewed from shaft direction).

1-4
(7) SCALE LENGTH
This refers to the maximum distance over which the ABSOCODER sensor can execute absolute
detection. The scale length can be designated in units which match the machine's travel amount (mm,
inches, degrees, etc.). For multi-turn type ABSOCODER sensors (MRE Series), the scale length will be
the machine's travel amount which corresponds to the prescribed number of sensor shaft turns (32, 64,
128, 160, 256, 320).
Example:
When a 32-turn MRE Series sensor is linked to a machine which moves 10 mm per each sensor shaft
revolution, and when the minimum setting unit of machine's drive unit is 0.01 mm, the scale length
would be as follows:
Actual detection distance = 10 mm/turn ×32 turns = 320 mm
Scale length (L) = Actual detection distance/Minimum setting unit Or, L = 320/0.01 = 32000
Important
Absolute detection of the current position is possible only within the detection range.
If this range is exceeded, the current position value will immediately change by the amount
of the entire scale length.
Therefore, it is essential that the machine's travel range not exceed the scale length.
(8) MINIMUM CURRENT POSITION VALUE
This is the minimal value of the scale length which can be displayed. This value can be designated as
desired within the following range: -99999 to [1000000 - scale length].
Example:
Given the same conditions as those described in the 'Scale Length' item above, and with the actual
minimum position value of the machine detection range being -10 mm, the following will apply:
Minimum current position value (K) = actual minimum position value/minimum setting unit
Or, K = -10/0.01 = -1000

1-5
(9) CURRENT POSITION VALUE
This value indicates where the machine is currently positioned within the machine detection range.
This can be expressed in two ways: By a sensor binary current position value, or by a scaling binary
current position value.
(a)Sensor binary current position value:
With this format, a digital output of '0' will occur (in response to the ABSOCODER sensor's input
signal) when the machine is at the 'minimum current position value' position designated at item 8
above. All subsequent machine positions are then output as values relative to that '0' point.
ABSOCODER sensor detection ranges: 0-131071 (0-1FFFF #)
(b)Scaling binary current position value:
With this format, the scaling binary value (indicating the machine's current position) is converted
into the appropriate unit (inch/mm) value. The 'minimum current position value' is then added,
with the result being expressed as a binary value:
Scaling binary value = Scale length/131072×sensor binary value+ minimum current position value
Example:
With position detection executed by a 32-turn MRE sensor with a scale length of 32000, minimum
current position value of -1000, the scaling binary value will be as shown below when the
machine's actual position is at the 150 mm point:
The scaling binary value at the 150 mm position will be as follows:
32000/131072×65536 + (-1000) = 15000
(10) STOP ZONE
This is the distance between the target stop position and the point where the motor is switched OFF
(and the brake applied) when positioning is being executed. The stop zone can be designated as
desired in the PRM (parameter) mode.
(11) BRAKE RELEASE
This is the output signal which releases the brake in positioning systems where the motor is equipped
with a brake.
(12) FWD/RVS
For the VS-212DN system, the current position value increases in the FWD (forward) direction and
decreases in the RVS (reverse) direction.
(13) SIMPLE LEARNING FUNCTION
If a positional discrepancy occurs between the target position and the current position upon
completion of positioning, the discrepancy will be automatically corrected when positioning is next
carried out.

2-1
2. SPECIFICATIONS
2.1 General Specifications
Item
Specifications
Power supply voltage
24 VDC
±
10
%
(Including ripples)
Current consumption 0.5A or less
Insulation resistance
20 M
Ω
or more between the external power terminal and enclosure (tested by
500VDC meg-ohmmeter)
Withstand voltage 500 VAC 60 Hz for 1 minute between external DC terminals and enclosure
Vibration resistance
20 m/s2
・
10 to 500 Hz, 10 cycles of 5 minutes in 3 directions.
(Conform to JIS C 0040 standard)
Ambient temperature
0 to 55
℃
Ambient humidity
20 to 90
%
RH
(
no freezing)
Ambient atmosphere
Free of corrosive gases and excessive dust
Ground
Must be securely grounded (ground resistance of 100 ohm or less)
Construction
Book-self type within enclosure
Dimensions(mm)
37.5 (W)
×
130 (D)
×
250 (H)
Mass
Approx. 1.3 kg
2.2 Performance Specifications
Item Specifications
Position detection format Absolute detection
Number of position detection axes 2 axes
Number of divisions [4096 divisions×32 turns] to [409.6 divisions×320 turns]
Limit switch
output
function
Number of programs
9
Program No.0 (Data is not held when power is OFF)
Program No.1-8 (Data is held when power is OFF)
Number of multi-dogs 10 dogs/channel
Number of channels 16 channels/axis (DeviceNet I/O)
Data setting method
Positioning
function
Control format
Unidirectional positioning (Bidirectional positioning when ‘overshoot
amount’ is set to “0”.
Target position setting
method
DeviceNet I/O
Number of output
channels for positioning
pattern data
1 pattern/axis
Number of output
channels for positioning
signal output (CH/axis)
8 channels/axis
Minimum setting units 0.00001
Current position value setting function Current position value setting, current position preset setting
JOG operation function via DeviceNet I/O
Sampling time
2ms
Response
time
Limit switch output 4ms (max. response delay time due to internal processing without
including communication time)
Current position output

2-2
2.3 External Input / Output Specifications
Input specifications
Output specifications
Item
specifications
Item
specifications
Number of Input
Current position preset:
2 points
×
2 axes
Number of Output
Positioning output:
8 points
×
2 axes
Isolation format Photo-coupler Isolation format Photo-coupler
Rated input voltage (V)
12 VDC
24VDC
Rated input voltage (V)
12/24 VDC
Rated input current (mA)
4
10
Load voltage range used (V)
10.2 to 30 VDC
Input voltage range (V)
10.2 to 30 VDC
Max. load current (mA)
100
ON voltage (V)
10 VDC or more
Max. rush current (A)
0.4 (10 ms or less)
OFF voltage (V)
4 VDC or less
Current leakage when OFF (mA)
0.1 or less
Max. voltage drop when ON(V)
0.5 (at 100 mA)
Response time (ms)
OFF
→
ON
0.04 (with input
voltage of 24V)
Response time (ms)
OFF
→
ON
0.04 (when load current
is 100 mA)
ON
→
OFF
0.2 (with input
voltage of 24V)
ON
→
OFF
0.2 (when load current is
100 mA)
Common connection
1 common for 4 points
(Common terminal:
B1,B2)
Common connection 1 common for 16 points
(Common terminal: A1,A2)
External cable
connection format Connector connection (24 pins connector:FCN-361J024-AU/FCN-360C024-B:Fujitsu)
Compatible wire size
0.3 mm
2
I/O
Pin
No.
Signal Name
Using ‘speed switching’ format
Using ‘speed stepping’ format
Axis 1
Output
B12
Forward
Forward/low-speed
B11
Reverse
Reverse/low-speed
B10
High-speed
High-speed
B9
Low-speed
Medium-speed
B8
Brake release
Brake release
B7
In-position
In-position
B6
Positioning in progress
Positioning in progress
B5
Operation error
Operation error
Input
B4
Current position preset input 1
Current position preset input 1
B3
Current position preset input 2
Current position preset input 2
Axis 2
Output
A12
Forward
Forward/low-speed
A11
Reverse
Reverse/low-speed
A10
High-speed
High-speed
A9
Low-speed
Medium-speed
A8
Brake release
Brake release
A7
In-position
In-position
A6
Positioning in progress
Positioning in progress
A5
Operation error
Operation error
Input
A4
Current position preset input 1
Current position preset input 1
A3
Current position preset input 2
Current position preset input 2
B1,B2
12/24DVC
12/24 DVC
A1,A2
0V
0V
o I/O circuit o Pin arrangement

2-3
2.4 Terminal Block Input / Output Specifications
Input specifications
Output specifications
Item
specifications
Item
specifications
Number of Input
Stop Input:
1 point
×
2 axes
Number of Output
Ready output:
1 point
×
2 axes
Isolation format Photo-coupler Isolation format Photo-coupler
Rated input voltage (V)
24VDC
Rated input voltage (V)
24 VDC
Rated input current (mA)
10
Load voltage range used (V)
21.6 to 30 VDC
Input voltage range (V)
21.6 to 30 VDC
Max. load current (mA)
100
ON voltage (V)
10 VDC or more
Max. rush current (A)
0.4(10 ms or less)
OFF voltage (V)
4 VDC or less
Current leakage when OFF (mA)
0.1 or less
Max. voltage drop when ON(V)
0.5 (at 100 mA)
Response time (ms)
OFF
→
ON
0.04 (with input
voltage of 24V)
Response time (ms)
OFF
→
ON
0.04 (when load
current is 100 mA)
ON
→
OFF
0.2 (with input
voltage of 24V)
ON
→
OFF
0.2 (when load current
is 100 mA)
Common connection Power supply and shared common
o Internal Circuit
2.5 DeviceNet Specifications
Items
Specifications
DeviceNet specifications
Volume
Ⅰ-
Release2
,
Volume
Ⅱ-
Release2
Vendor name
NSD Corporation
(
230
)
Device profile name
Generic Device
(
0
)
Product name
VS-212DN
(
2120
)
Network current consumption
75mA or less
Connector type
Open-plug
Isolated physical layer
Yes
LEDs supported
MS(Module), NS(Network)
MAC ID setting
Dip switch
Communication baud rates setting
Dip switch
Communication baud rates supported
125kbps, 250kbps, 500kbps
Predefined master/slave connection setting
Group 2 only server
UCMM supported
No
Fragmented explicit messaging supported
Yes
I/O message supported
POLD I/O
Output from master unit to VS-212DN: 8 bytes
Output from VS-212DN to master unit: 8 bytes

2-4
2.6 ABSOCODER Sensor
(1) Multi-turn type ABSOCODER sensor:
o Multi-turn type MRE
Item
Specifications
Model
MRE-
□
32SP062
G64SP062
G128SP062
G160SP062
G256SP062
G320SP062
Number of turns
32
64
128
160
256
320
Divisions/Turn
4096
2048
1024
819.2
512
409.6
Mass (kg)
1.5
1
Moment of inertia (kg
・
m2)
6.7
×
10-6
3.9
×
10-6
Starting torque (N
・
m)
4.9
×
10-2 or less
Permissible shaft
load (N)
Radial
98
Thrust
49
Permissible mechanical speed(r/min)
3600
Bearing Life (at 3600r/min)
3
×
104Hr
1.5
×
104Hr
Ambient
temperature
Operating (
℃
)
-20 to +60
Storage (
℃
)
-30 to +90
Vibration resistance
2.0
×
102m/s2 , 200Hz , up/down 4h, forward/back 2h,
conforms to JIS D1601 standard
Shock resistance
4.9
×
103m/s2, 0.5ms , up/down/forward/back
×
3 times each,
conforms to JIS C5026 standard
Protection rating
IP52f conforms to JEM 1030 standard
Max. cable
Length (m)
Standard cable: 4P-S
100
Robotic cable: 4P-RBT
40
70
IMPORTANT
An ABSOCODER sensor should be selected which has a ABSOCODER detection range (distance
over which absolute position detection is possible) which exceeds the machine’s travel amount.
ABSOCODER sensor’s detection range
Machine travel range
2.7 Extension Cable Specifications
Item Specifications
Model 4P-S-□4P-RBT-□
Cable type Standard cable Robotic cable
Operating temperature range -5 to +60℃
Characteristics Extensible for long distance Superior flexibility; ideal for moving components
Insulator Irradiated, formed polyethylene ETFE plastic (resin)
Sheath Polyvinyl chloride (PVC) mixture
Color
Gray
Black

3-1
3. DeviceNet
VS-212DN operates as a "group 2 only" slave module for FA field networks. Therefore, VS-212DN requires
a master module for communication with the PLC DeviceNet. Using such a DeviceNet communication
module enables the PLC to control VS-212DN as a regular I/O unit.
For details regarding operation of the DeviceNet communication module and the DeviceNet communication
setting procedures, refer to the manufacturer's manual.
It is also possible to use DeviceNet devices available from PLC manufacturers, etc., to enable reading
and writing in the VS-212DN buffer memory. Contact NSD if a file (EDS file) is required which defines
the control data used by the DeviceNet devices.
3.1 Control Panel Settings
The VS-212DN control panel is equipped with switches for node address and baud rate setting.
(1) Specify a node address setting of 0 to 63. Be sure that duplicate node addresses (same as address for
another module) are not specified.
[Ex] If node address = 5: Set 1 (SW6) and 4 (SW4) to ON.
(2) Baud rate setting
Baud rate
SW7
SW8
500kbps ON OFF
250kbps OFF ON
125kbps
OFF
OFF
*Note ON ON
*Note: This combination is prohibited.
(3) PLC selection switch (SW 1) setting
When Rockwell Automation’s master unit is connected to the VS-212DN unit, SW 1 on the VS-212DN
rear panel should be set to ‘ON’ side.

3-2
3.2 Control Panel Display
VS-212DN is equipped with 2 LED lamps (MS and NS) which serve as DeviceNet status indicators.
The "MS" indicator shows the module status, and the "NS" indicator shows the network status.
MS Indicator
LED Status VS-212DN Status Description
OFF No power No power is being supplied.
Green ON Normal Normal operation is in progress.
Green blinking No setting Configuration is not completed or is incorrect.
Red blinking Minor error Recovery is possible by changing a setting, etc.
Red ON Non-recovery error
VS-212DN recovery from this error is not possible.
Replacement is required.
Green/red blinking Self-diagnosis VS-212DN self-diagnosis is in progress.
NS Indicator
LED Status VS-212DN Status Description
OFF No power or offline
No power is being supplied to the VS-212DN. Online status is not
established. ("MS" minor error, etc.)
Green blinking Online/disconnected VS-212DN is not recognized by master unit.
Green ON Online/connected VS-212DN is recognized by master unit.
Red blinking
Minor
communication error
Recovery is possible by changing a setting, etc.
Red ON Critical error
Error which disables network communications.
(Duplicate node addresses, circuit malfunction, etc.)
Green/red blinking VS-212DN communication failure.
Other Errors
LED Status Description
Orange (simultaneous red and green) MS,
NS lamps are both ON
VS-212DN power voltage drop detected.
MS and NS red ON A DeviceNet CPU watchdog timer error has occurred.
MS red ON, NS orange ON
Watchdog timer error has occurred at both the DeviceNet CPU and the
control CPU.
MS red ON, NS unchanged
(communication enabled)
A watchdog timer error has occurred at the control CPU.
MS orange ON, NS unchanged
(communication enabled)
Communication error has occurred at the control CPU and at the
DeviceNet CPU. Recovery is possible by clearing the communication
error status.
Table of contents
Popular Controllers manuals by other brands
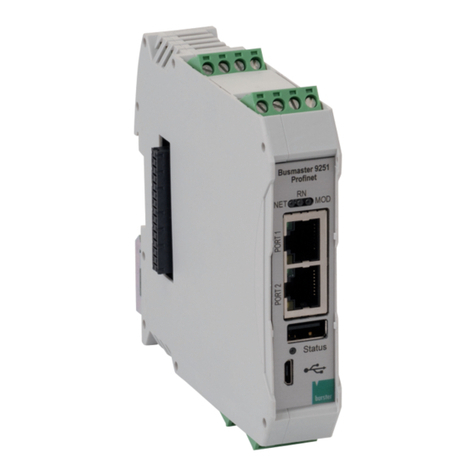
Burster
Burster 9251 PROFINET Series Operation manual
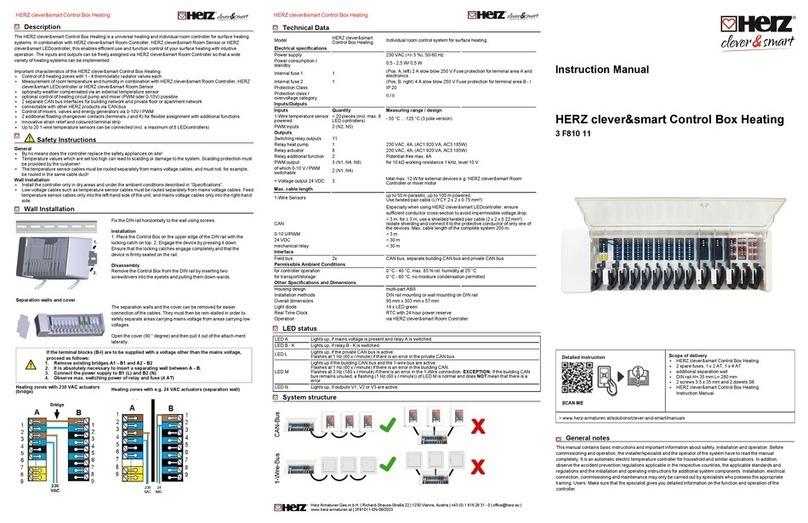
Herz
Herz clever&smart Control Box Heating instruction manual
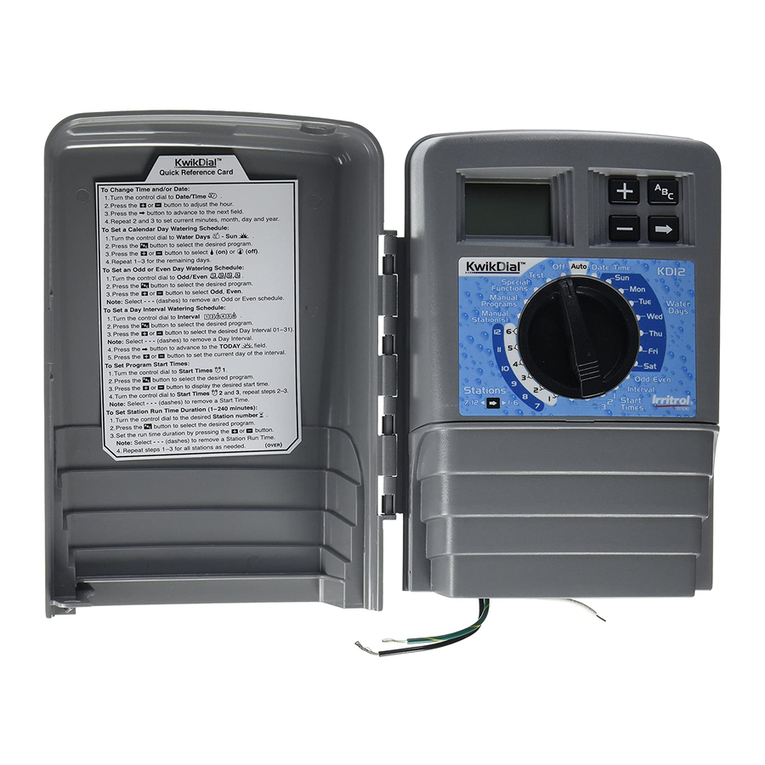
Irritrol
Irritrol KwikDial user guide
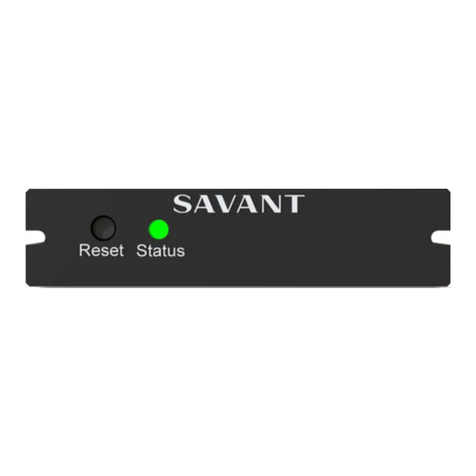
Savant
Savant SmartControl SSC-W02R Quick reference guide
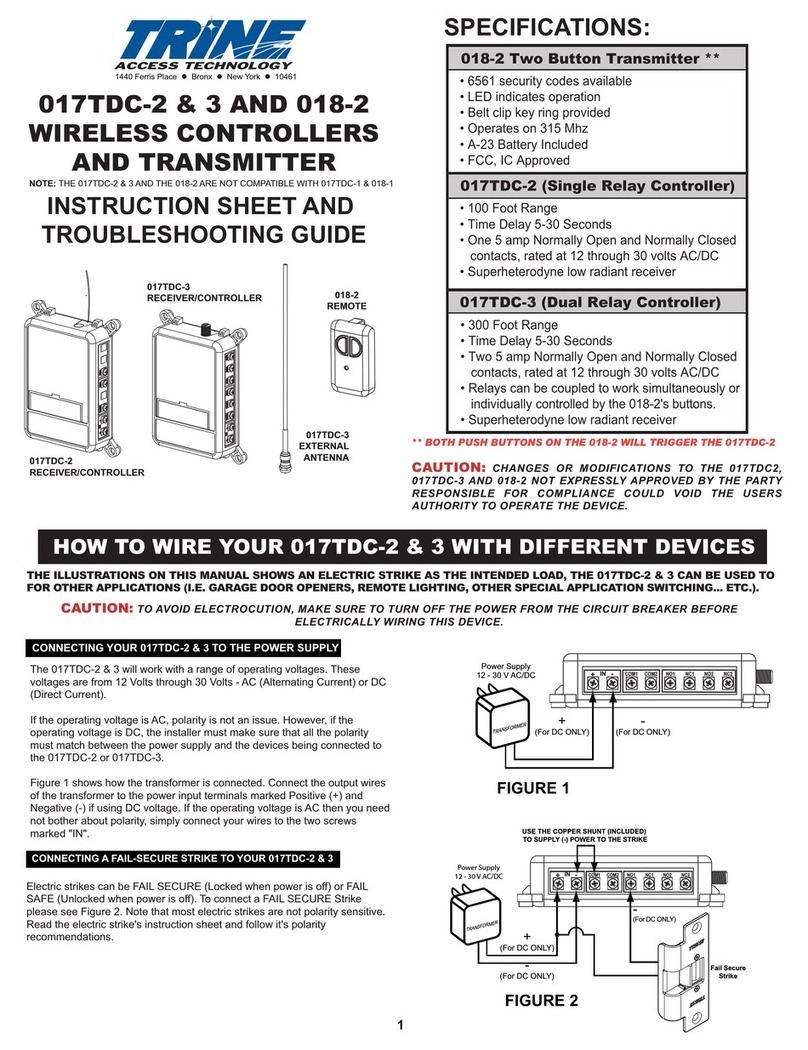
Trine
Trine 017TDC-2 Instruction sheet and troubleshooting guide
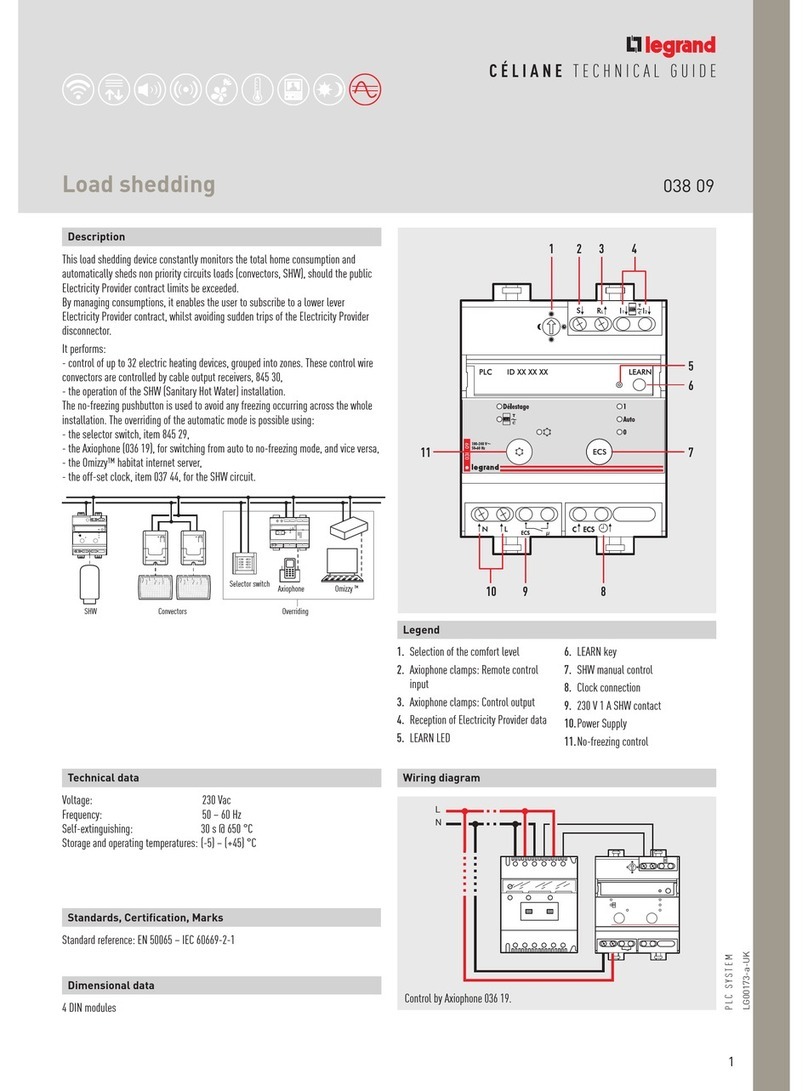
LEGRAND
LEGRAND 038 09 Technical guide
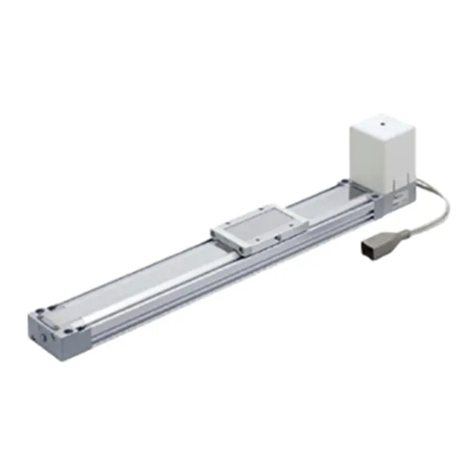
SMC Networks
SMC Networks LEFS Series Operation manual
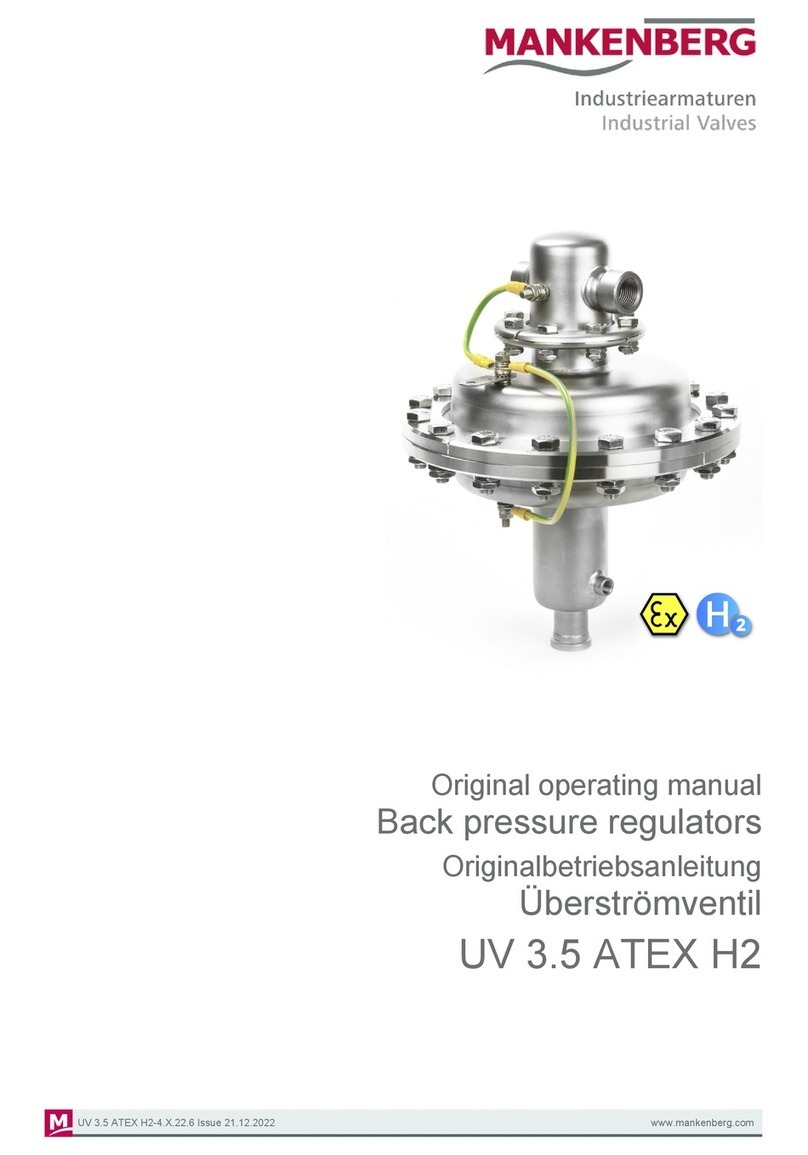
Mankenberg
Mankenberg UV 3.5 ATEX H2 Original operating manual
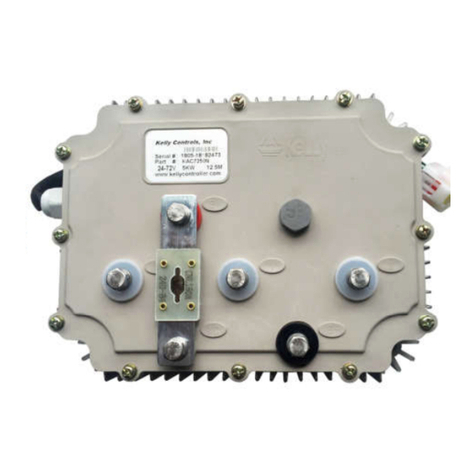
Kelly
Kelly KLS Series user manual
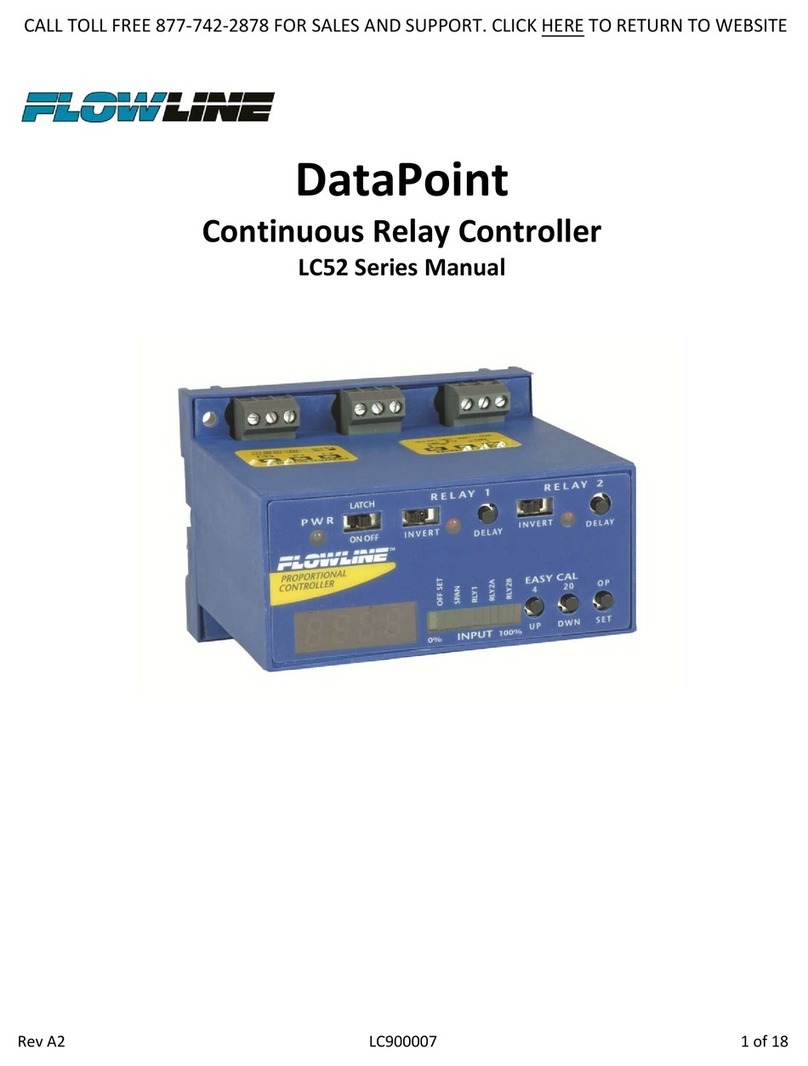
FlowLine
FlowLine DataPoint LC52 Series manual
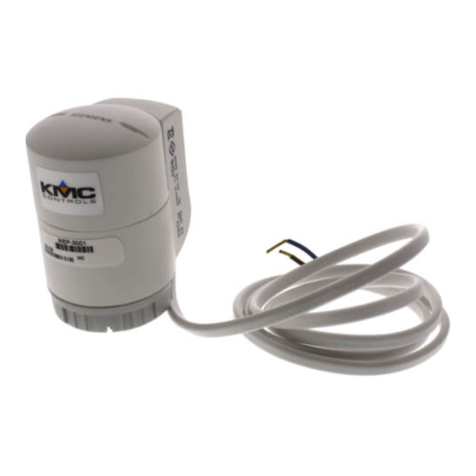
KMC Controls
KMC Controls MEP-3001 Installation and operation guide
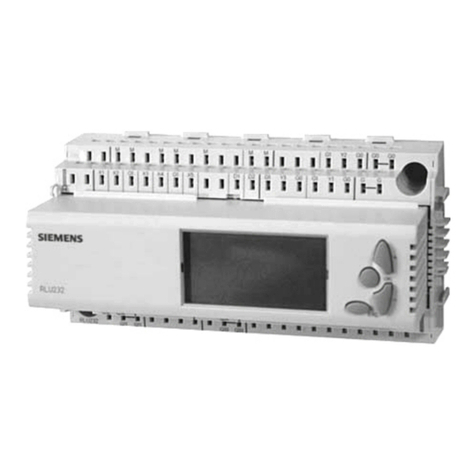
Siemens
Siemens Synco 200 Basic documentation