Burster 9251 PROFINET Series User manual

OPERATION MANUAL
Fieldbus controller
Model 9251
Manufacturer:
© 2020
burster
präzisionsmesstechnik gmbh & co kg
burster
präzisionsmesstechnik gmbh & co kg
All rights reserved
Talstr. 1-5
Postfach 1432
76593 Gernsbach
Germany
76587 Gernsbach
Germany
Valid from:
December 7, 2020
Tel.: +49 7224 645-0
Fax: +49 7224 645-88
Email: info@burster.de
www.burster.com
4021-BA9251EN-5999-121532

2of 47
Warranty disclaimer
All information in the present documentation was prepared and compiled with great care and reproduced
in accordance with effective control measures. No warranty is provided for freedom from errors. We
reserve the right to make technical changes. The present information as well as the corresponding
technical data can change without notice. Reproduction of any part of this documentation or its
processing or revision using electronic systems is prohibited without the manufacturer's prior written
approval.
Components, devices and measurement sensors made by burster präzisionsmesstechnik (hereinafter
referred to as the “product”) are the result of targeted development and meticulous research. From the
date of delivery, burster provides a warranty for the proper condition and functioning of these products
covering material and production defects for the period specified in the warranty document accompanying
the product. However, burster waives any guarantee or warranty obligations or any additional liability for
consequential damages caused by improper use of the product, in particular the implied guarantee of
success in the market as well as the suitability of the product for a particular purpose. Furthermore,
burster assumes no liability for direct, indirect or incidental damages or for consequential or other
damages arising from the provision and use of the present documentation.

3of 47

4of 47
Contents
1For your safety..................................................................................................................................... 7
1.1 Symbols used in the operating manual ............................................................................................ 7
Signal words......................................................................................................................... 7
Pictograms ........................................................................................................................... 8
1.2 Symbols on the 9251 fieldbus controller .......................................................................................... 8
Conventions used in the operating manual ......................................................................... 8
2Introduction.......................................................................................................................................... 9
2.1 Intended use..................................................................................................................................... 9
2.2 Customer service ............................................................................................................................. 9
Customer service department.............................................................................................. 9
Contact person................................................................................................................... 10
2.3 Download the test certificate .......................................................................................................... 10
2.4 Ambient conditions ......................................................................................................................... 10
Storage conditions ............................................................................................................. 10
Operating conditions .......................................................................................................... 10
Restrictions on use............................................................................................................. 11
Cleaning ............................................................................................................................. 11
2.5 Personnel ....................................................................................................................................... 11
2.6 Contents of pack ............................................................................................................................ 11
2.7 Unpacking....................................................................................................................................... 12
2.8 Warranty ......................................................................................................................................... 12
2.9 Conversions and modifications ...................................................................................................... 12
3Device concept .................................................................................................................................. 13
3.1 Functional scope ............................................................................................................................ 13
3.2 Block diagram and potentials ......................................................................................................... 13
3.3 Versions.......................................................................................................................................... 14
3.4 Power supply.................................................................................................................................. 14
3.5 Available sensors (optional) ........................................................................................................... 14
Sensor technologies (optional) .......................................................................................... 14
3.6 Error indicators ............................................................................................................................... 14
4Controls and connections ................................................................................................................ 15
4.1 Front view ....................................................................................................................................... 15
4.2 Terminal assignment / pin assignment........................................................................................... 16
4.3 Fieldbus status indicator................................................................................................................. 16
4.4 LEDs............................................................................................................................................... 17
4.5 Status LED (normal operation)....................................................................................................... 17
4.6 Grounding and shielding ................................................................................................................ 18

5of 47
4.7 Compatible sensors / inputs........................................................................................................... 18
Voltage measurement / transmitter with voltage output (optional) .................................... 18
4.8 PLC inputs...................................................................................................................................... 18
4.9 PLC outputs.................................................................................................................................... 19
4.10Micro-USB port for configuration.................................................................................................... 19
4.11USB host ........................................................................................................................................ 19
5Using the instrument for the first time............................................................................................ 20
5.1 Installation/removal ........................................................................................................................ 20
6PROFINET .......................................................................................................................................... 21
6.1 Port identification............................................................................................................................ 21
6.2 Planning a PROFINET network ..................................................................................................... 22
6.3 PROFINET fieldbus-specific LED functions................................................................................... 22
6.4 Cyclical data transmission from the 9251 fieldbus controller to the control system ...................... 23
Data packets for data transmission from the 9251 fieldbus controller to the control system
using the “short” method.................................................................................................... 24
Data packets for data transmission from the 9251 fieldbus controller to the control system
using the “extended” method ............................................................................................. 25
Complete data protocol for data transmission from the 9251 fieldbus controller to the
control system using the “short” method............................................................................ 26
Data protocol for data transmission from the 9250 instrumentation amplifier to the control
system using the “short” method ....................................................................................... 26
Data protocol for data transmission from the 9251 fieldbus controller to the control system
using the “extended” method ............................................................................................. 27
Data protocol for data transmission from the 9250 instrumentation amplifier to the control
system using the “extended” method................................................................................. 28
6.5 Cyclical data transmission from the control system to the 9251 fieldbus controller ...................... 29
Controlling the device functions......................................................................................... 29
Data protocol cyclical data for data transmission from the control system to the 9251
fieldbus controller............................................................................................................... 29
Data protocol cyclical data for data transmission from the control system to the 9250
instrumentation amplifier.................................................................................................... 30
6.6 Acyclical data ................................................................................................................................. 30
Data protocol acyclical data 9251 fieldbus controller ........................................................ 31
Data protocol acyclical data 9250 instrumentation amplifier ............................................. 31
7EtherCAT ............................................................................................................................................ 32
7.1 Port identification............................................................................................................................ 33
7.2 EtherCAT fieldbus-specific LED functions ..................................................................................... 33
7.3 EtherCAT PDO – Process Data Objects........................................................................................ 34
Overview of data packets, data transmission from the 9251 fieldbus controller to the
control system.................................................................................................................... 34

6of 47
Data protocol for data transmission from the 9251 fieldbus controller to the control system
35
Data protocol for data transmission from the 9250 instrumentation amplifier to the control
system ................................................................................................................................ 36
Data protocol for data transmission from the control system to the 9251 fieldbus controller
37
Data protocol for data transmission from the control system to the 9250 instrumentation
amplifier.............................................................................................................................. 38
7.4 EtherCAT SDO – Service Data Objects ......................................................................................... 39
Acyclical data 9251 fieldbus controller............................................................................... 39
Acyclical data 9250 instrumentation amplifier module 1.................................................... 39
Acyclical data 9250 instrumentation amplifier module 2.................................................... 40
Acyclical data 9250 instrumentation amplifier module 3.................................................... 40
Acyclical data 9250 instrumentation amplifier module 4.................................................... 41
Acyclical data 9250 instrumentation amplifier module 5.................................................... 41
Acyclical data 9250 instrumentation amplifier module 6.................................................... 41
Acyclical data 9250 instrumentation amplifier module 7.................................................... 42
Acyclical data 9250 instrumentation amplifier module 8.................................................... 42
7.5 EtherCAT error codes .................................................................................................................... 43
8Service offering for the 9251 fieldbus controller ........................................................................... 44
9Technical data.................................................................................................................................... 45
9.1 Electromagnetic compatibility......................................................................................................... 45
Interference immunity......................................................................................................... 45
Interference emission......................................................................................................... 45
10 Accessories available ....................................................................................................................... 46
11 Disposal.............................................................................................................................................. 47

7of 47
1 For your safety
The following symbols on the model 9251 fieldbus controller and in this operation manual warn of
hazards.
1.1 Symbols used in the operating manual
Signal words
The following signal words are used in the operating manual according to the specified hazard
classification.
DANGER
High degree of risk: indicates a hazardous situation which, if not avoided, will result in death or
serious injury.
WARNING
Moderate degree of risk: indicates a hazardous situation which, if not avoided, may result in death or
serious injury.
CAUTION
Low degree of risk: indicates a hazardous situation which, if not avoided, could result in minor or
moderate injury.
NOTICE
Property damage to the equipment or the surroundings will result if the hazard is not avoided.
Note: It is important to heed these safety notices in order to ensure you handle the model 9251
fieldbus controller correctly.
IMPORTANT: Follow the information given in the operating manual.

8of 47
Pictograms
Electric shock hazard
Important, please note
Observe the advice for protecting the model 9251 fieldbus controller.
1.2 Symbols on the 9251 fieldbus controller
Symbol Description
See manual!
It is essential to observe the information and notes in the operation manual for the
model 9251 fieldbus controller.
Follow safety instructions – professional servicing only.
Conventions used in the operating manual
Designation Description
[Text] Operating buttons
“Term” Terms used in the instrument menus

9of 47
2 Introduction
IMPORTANT: Read the operating manual carefully before using the equipment, and keep for future
reference.
2.1 Intended use
DANGER
•Only use the model 9251 fieldbus controller outside of potentially explosive
areas.
•The model 9251 fieldbus controller is not intended as a substitute for safety
devices and protective equipment. Use safety devices and protective equipment.
•The model 9251 fieldbus controller is not intended for use in medical applications
or where people are at risk.
•Do not connect voltages that are higher than the specification allows.
•Not for safety-critical applications.
Intended use is defined as:
•For industrial purposes
•For use in EMC-certified control cabinets
•Use only with grounded top-hat rails
Industry-compatible connection and installation technologies make it easier for the user to adapt and
integrate the unit in existing mechanical and electrical environments. The outstanding measuring quality
makes it ideally suited to use in both development and testing.
Typical applications of the model 9251 fieldbus controller include:
•Factory automation
•Integration of measurement data in a control environment
•Use in test and calibration laboratories
•Measuring and control equipment
2.2 Customer service
Customer service department
For repair inquiries, please telephone our Service department on +49 7224 645-53, or email:
service@burster.de (Germany only). If you are outside Germany, you should contact your burster agent
(see also www.burster.com).
Please have the serial number to hand. The serial number is essential to establishing the definite
technical status of the instrument and providing help quickly. You will find the serial number on the type
plate of the model 9251 fieldbus controller.

10 of 47
Contact person
If you have any questions relating to the model 9251 fieldbus controller, please go directly to burster
präzisionsmesstechnik gmbh & co kg, or if outside Germany, please contact your burster agent (see also
www.burster.com).
Head office
burster präzisionsmesstechnik gmbh & co kg
Talstr. 1-5
76593 Gernsbach
GERMANY
Phone: +49 7224 645-0
Fax: +49 7224 645-88
Email: info@burster.de
2.3 Download the test certificate
You have the option to download the test certificate for your model 9251 fieldbus controller online. To do
this, use the following link https://tinyurl.com/y45kumy6.You can then download the test certificate
directly by entering the serial number.
2.4 Ambient conditions
Storage conditions
The following requirements must be met when storing the model 9251 fieldbus controller:
•Store at temperatures between -25 °C and +70 °C
•The model 9251 fieldbus controller must be packed in clean packaging
•Store in a dry environment
•No condensation
Operating conditions
The following requirements must be met when operating the model 9251 fieldbus controller:
•Indoor operation only
•Maximum altitude 2000 m
•Operate at temperatures between 0 °C and 50 °C
•Humidity: 80% up to +31 °C, decreasing linearly above that temperature to 50% at Tmax, non-
condensing
•Class of protection: 3
•Transient overvoltage category: CAT II
•Supply voltage 11 to 30 V DC
•The mounting rail must be grounded (PE)
Note: Avoid condensation after transportation or storage.

11 of 47
Restrictions on use
DANGER
The model 9251 fieldbus controller is not intended as a substitute for safety devices
and protective equipment.
Use safety devices and protective equipment.
The model 9251 fieldbus controller does not pose a hazard if used within its specification and in
accordance with the safety regulations.
The manufacturer does not accept liability for any personal injury or property damage arising from
misinterpretation of measurement results.
Cleaning
DANGER
Electrical shock hazard
Disconnect the model 9251 fieldbus controller from the power supply before
cleaning.
Disconnect the model 9251 fieldbus controller from the power supply and use a dry cloth to clean the unit.
NOTICE
Do not immerse the model 9251 fieldbus controller in water or hold it under running
water. Do not use strong cleaning agents as these may damage the model 9251
fieldbus controller. Clean the model 9251 fieldbus controller using a slightly damp cloth.
2.5 Personnel
Personnel must be familiar with the relevant regulations. They must follow these regulations. Only trained
personnel who are familiar with the applicable safety regulations are permitted to operate the model 9251
fieldbus controller.
burster is happy to provide your operating personnel with training. To find out more, please look at our
range of services at www.burster.de
2.6 Contents of pack
The following components are supplied:
•Model 9251 fieldbus controller
•Operation manual
•Warranty document
•Test certificate
•Free version of DigiVision configuration and analysis software

12 of 47
2.7 Unpacking
DANGER
Electrical shock hazard
Never switch on the model 9251 fieldbus controller if it shows signs of damage
incurred in transit. Only ever use the model 9251 fieldbus controller under the
conditions specified in this operating manual.
Inspect the model 9251 fieldbus controller for damage. If you suspect that the unit has been damaged
during shipping, notify the delivery company within 72 hours.
The packaging should be retained for examination by a representative of the manufacturer and/or the
delivery company.
The model 9251 fieldbus controller should be shipped only in its original packaging or in packaging
capable of providing an equivalent degree of protection.
2.8 Warranty
burster präzisionsmesstechnik gmbh & co kg provides a manufacturer’s warranty for a period of
24 months after delivery.
Any repairs required during this time will be made without charge. This does not include damage arising
from improper use.
Please note the following when sending the model 9251 fieldbus controller in for repair:
•If there is a problem with the device, please attach a note to the housing of the model 9251
fieldbus controller summarizing the fault.
•Technical specifications subject to change at any time without notice.
We also state explicitly that we do not accept liability for consequential damage.
•The instrument must always be dispatched in suitable packaging.
2.9 Conversions and modifications
Note: The warranty shall be deemed void immediately if you open or dismantle the model 9251
fieldbus controller during the warranty period.
The model 9251 fieldbus controller does not contain any parts that are intended to be serviced by the
user. Only the manufacturer’s own qualified personnel are permitted to open the model 9251 fieldbus
controller.
It is not permitted to make any changes to the model 9251 fieldbus controller without the written
agreement of burster präzisionsmesstechnik gmbh & co kg. burster präzisionsmesstechnik gmbh & co kg
does not accept liability for damages or injury if this condition is disregarded.

13 of 47
3 Device concept
Please refer to the model 9251 fieldbus controller data sheet for full details of dimensions, weight, degree
of protection etc.
3.1 Functional scope
The model 9251 fieldbus controller serves as a bridge between cascadable model 9250 universal
instrumentation amplifiers and Ethernet-based fieldbuses such as PROFINET, EtherCAT and
EtherNet/IP. Up to eight model 9250 instrumentation amplifiers, bus-compatible version, can be
connected to the model 9251 fieldbus controller. The scaled measured values are read simultaneously in
the real-time data of the fieldbus link. A DC standard signal input with voltage range ±10 V can be used
directly on the model 9251 fieldbus controller.
With an update rate of approx. 3.6 kHz, the measured values of the model 9250 instrumentation amplifier
and the internal auxiliary channel in the model 9251 fieldbus controller are written to the process data
array (real-time data) and therefore made available for process data access by the PLC. In addition to the
channel live values, an array of 32 recorded measured values is always available. With the aid of an
additional array counter, the higher-level PLC can record and evaluate a highly dynamic series of
measured values even at a low access rate.
A USB interface is provided for device configuration. The DigiVision PC software (free version at
www.burster.de) enables easy setup and shows the status of all connected model 9250 instrumentation
amplifiers.
Additional functions such as a real-time status of all connected model 9250 instrumentation amplifiers and
the model 9251 fieldbus controller, tare possibilities, peak value recording and smart limit modes enable
the use of the 9250/9251 product bundle in a wide range of measuring tasks in modern industrial
applications.
3.2 Block diagram and potentials
Figure 1: Block diagram model 9251 fieldbus controller
The PLC inputs and outputs, TTL inputs and supply voltage are galvanically isolated from the actual
measurement electronics, and accordingly have their own ground connections. The permissible voltage of
the respective connections to PE is 20 V.
Note: Each module requires a separate supply voltage.

14 of 47
3.3 Versions
Please refer to the data sheet for details of the different versions. You can obtain the latest data sheet
and additional information on the model 9251 fieldbus controller at https://tinyurl.com/y65b5xys or simply
use the QR code below:
Figure 2: QR code for 9251 fieldbus controller
3.4 Power supply
The model 9251 fieldbus controller can be operated with a voltage of 11 to 30 V DC. The maximum
power consumption of the model 9251 fieldbus controller is 3 W.
3.5 Available sensors (optional)
Via the optional voltage input, sensors with a standard signal (0 to ±10 V) can be connected to the model
9251 fieldbus controller.
Sensor technologies (optional)
Symbol Type
Sensors with standard signal (process signal)
3.6 Error indicators
Indicator Error description
Status LED flashing rapidly red
Error after power-on
Sensor supply not available
Internal malfunction
Status LED lights continuously red Input overload
Status LED red flashing rapidly and
LED green flashing slowly
The ADC is not providing measurements because it has
been stopped via the PLC input
Table 1: Error indicators, model 9251 fieldbus controller

15 of 47
4 Controls and connections
4.1 Front view
Figure 3: Front view of model 9251 fieldbus controller
Label Description
1 Fieldbus status indicator
2 Fieldbus ports
3 USB host
4 Status LED
5 Micro-USB port for configuration
6 Internal bus connection e.g. for model 9250 instrumentation amplifier
7 External inputs and outputs
Table 2: Connections on model 9251 fieldbus controller (front view)

16 of 47
4.2 Terminal assignment / pin assignment
Pin Assignment
1 Analog input (±10 V) (optional)
2 Analog input GND
3 Shield
4 Not used
11 Supply voltage 11 to 30 V DC
12 Supply voltage GND
13 PLC input 1
14 PLC input 2
15 PLC output 1
16 PLC output 2
17 PLC supply GND
18 PLC supply +24 V
19 Shield
Table 3: Pin assignment model 9251 fieldbus controller
4.3 Fieldbus status indicator
The fieldbus status indicator on the model 9251 fieldbus controller depends on the chosen version. You
can choose between the different fieldbuses PROFINET, EtherCAT and EtherNet/IP.
See the respective fieldbus section for a detailed description of the status indicators.

17 of 47
4.4 LEDs
LEDs Description
Flashing Lamp test on power-on
“Status” LED Status LED, dual-color LED green and red
OFF Offline
Green Online (RUN)
Table 4: Meaning of LEDs model 9251 fieldbus controller
4.5 Status LED (normal operation)
The status LED is a multi-color LED that tells you the status of the model 9251 fieldbus controller.
Indicator Description
Status LED flashing slowly green Normal measuring mode
Status LED flashing rapidly green Boot phase
Status LED flashing 3x repeatedly red Fieldbus module error: Module not recognized
Status LED flashing 4x repeatedly red Fieldbus module error: Module not supported
Status LED flashing 5x repeatedly red Fieldbus module error: Module not responding
Status LED flashing 6x repeatedly red Fieldbus module error: Module shut down
Status LED flashing 7x repeatedly red Fieldbus module error: Unexpected error
Status LED continuously flashing
slowly red and green Analog input overload
Table 5: Status LED (normal operation) on model 9251 fieldbus controller

18 of 47
4.6 Grounding and shielding
The model 9251 fieldbus controller is grounded via the mounting rail. Use suitable connecting cables for
connecting communication interfaces and for controlling I/O signals. Ideally you should connect sensors
using burster connecting cables and with a minimum length of cable.
We strongly recommend the following:
•In general, keep sensor connecting leads as short as possible.
•When using control lines from remote PLC systems, make sure all the system components are
suitably grounded.
•When using detachable extension leads, make sure the shielding is continuous.
•Spatially separate the signal and power supply lines.
4.7 Compatible sensors / inputs
Voltage measurement / transmitter with voltage output (optional)
Via the optional analog input, transmitters with a voltage output of up to ±10 V can be connected.
•The measuring range is 0 to ±10 V.
•Transmitters having a voltage output of up to ±10 V can be connected like a voltage source.
•The transmitters require a separate power supply.
Connect transmitters as follows:
Figure 4: Transmitter with voltage output
The input range is 0 to ±10 V.
Note: The model 9251 fieldbus controller does not provide supply voltages for transmitters.
4.8 PLC inputs
The model 9251 fieldbus controller optionally (in conjunction with the analog input option) has two
independent PLC inputs to which different functions can be assigned. The PLC inputs are only available
with the optional analog input. Possible functions are:
•Tare
•Reset tare
•Reset limit memory 1 or 2
•Copy input to corresponding output
Note: The PLC inputs are galvanically isolated from the measurement electronics, but not from the
PLC outputs.

19 of 47
4.9 PLC outputs
The model 9251 fieldbus controller optionally (in conjunction with the analog input option) has two
independent PLC outputs to which different functions can be assigned. The PLC outputs are only
available with the optional analog input.
The following functions are possible:
•Dynamic limit threshold under / dynamic limit threshold over:
The output is set as long as the value remains above/below the threshold. If this condition is no
longer fulfilled, the output is cleared (dynamic behavior).
•Static limit threshold under / static limit threshold over:
The output is set as long as the value remains above/below the threshold and stays set even if
this condition is no longer fulfilled. The output can only be reset via a corresponding RESET
signal at the PLC input (static behavior).
•Window mode:
The output is set as long as the measurement signal is between a lower and an upper limit
threshold value. If the signal leaves this range, the output is cleared. If the signal subsequently
fulfills the condition again, the output is set again (dynamic behavior).
Note: The PLC outputs are galvanically isolated from the measurement electronics, but not from the
PLC inputs.
4.10 Micro-USB port for configuration
The model 9251 fieldbus controller has a Micro-USB port for configuration via the free software
DigiVision. The USB interface conforms to USB 2.0 Micro-B.
IMPORTANT: The Micro-USB port is for configuration purposes only. A connected device may cause
interference during measurement operation.
USB interface
The USB interface complies with the USB 2.0 standard and the pin assignment is as usual. The built-in
connector on the model 9251 fieldbus controller is for a USB 2.0 Micro-B plug.
Pin Name
Figure 5: USB Micro-B
1 +5 V
2 Data -
3 Data +
4 ID (not used)
5 GND
4.11 USB host
Note: The USB Type-A port is not currently used.

20 of 47
5 Using the instrument for the first time
DANGER
Electrical shock hazard
•Never switch on the model 9251 fieldbus controller if it shows signs of damage
incurred in transit. Only ever use the model 9251 fieldbus controller under the
conditions specified in this operating manual.
•Only use the model 9251 fieldbus controller outside of potentially explosive
areas.
•Do not connect voltages that are higher than the specification. For the supported
ranges, see the data sheet for the model 9251 fieldbus controller.
5.1 Installation/removal
WARNING
Install the model 9251 fieldbus controller only on a grounded mounting rail in
a grounded control cabinet.
The model 9251 fieldbus controller must be installed on a grounded mounting rail in accordance with DIN
EN 60715 in a grounded control cabinet.
Installation
1 Place the upper edge of the mounting section on the mounting rail.
2 Press the model 9251 fieldbus controller from the front against the mounting rail until it
audibly engages.
3 Pull lightly on the model 9251 fieldbus controller to check it is securely mounted.
Removal
1 Use a screwdriver to release the catch on the bottom of the model 9251 fieldbus controller
from the mounting rail.
2 Tilt the model 9251 fieldbus controller slightly upward, grip its top edge and lift it off the
mounting rail.
Other manuals for 9251 PROFINET Series
1
Table of contents
Other Burster Controllers manuals
Popular Controllers manuals by other brands
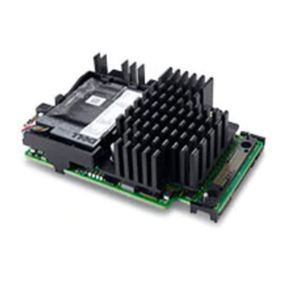
Dell
Dell PowerEdge user guide
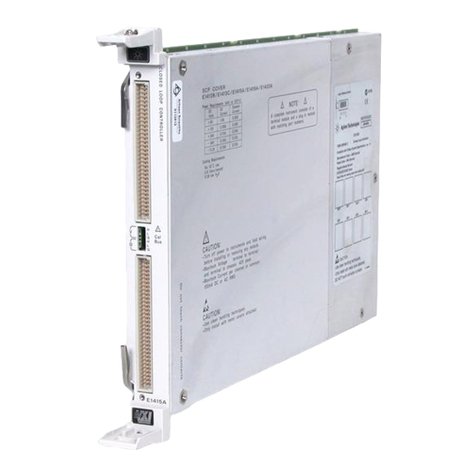
HP
HP VXI 75000 C Series User's and SCPI Programming Manual
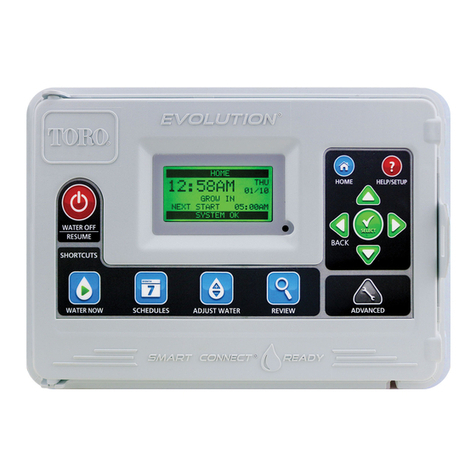
Toro
Toro EVOLUTION Series quick start guide
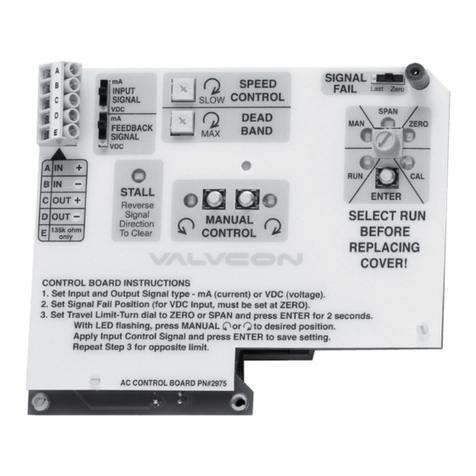
Metso
Metso VALVCON V-Series Installation, maintenance & operating instructions
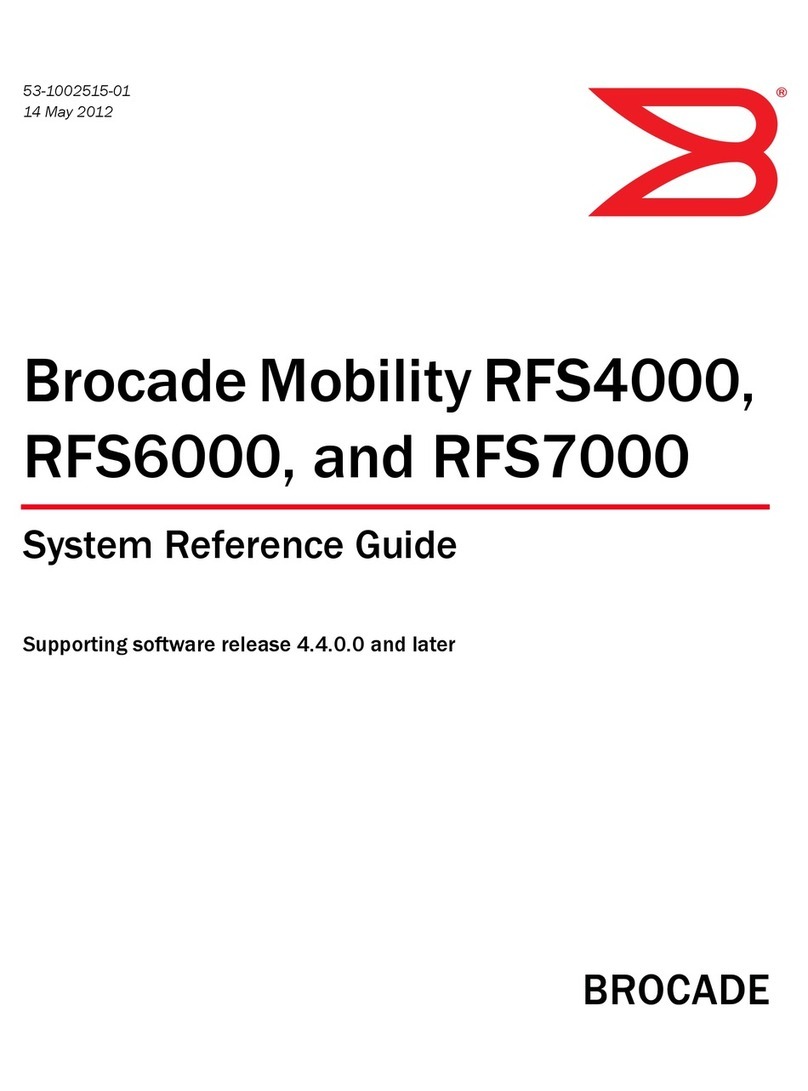
Brocade Communications Systems
Brocade Communications Systems Mobility RFS6000 System reference guide
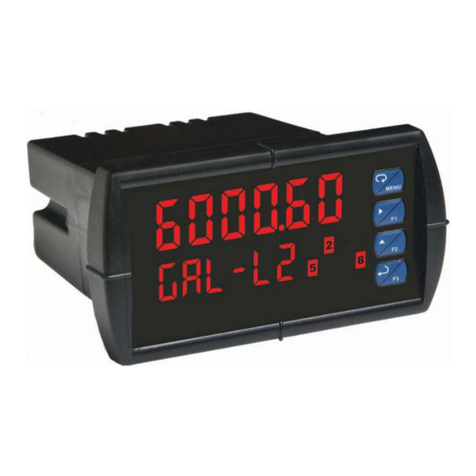
FlowLine
FlowLine DataView LI55 quick start