nuair HA Series Manual

Please file in Service Binder
6197 083 - 03 04/2023
Nu-Air HA Series
Installation, Service and
Operating Instructions
for use by heating contractor
Nu-Air HA Series
Hydronic forced air handler
Product may not be exactly as shown
Read and save these instructions
for future reference.
IMPORTANT

Nu-Air HA Installation, Service and Operating
6197 083 - 03
2
Safety, Installation and Warranty Requirements
Safety
2
Please ensure that these instructions are read and understood before commencing installation. Failure to comply with
the instructions listed below and details printed in this manual can cause product/property damage, severe personal
injury, and/or loss of life. Ensure all requirements below are understood and fulfilled (including detailed information
found in manual subsections).
WARNING
Follow the maintenance schedule of the air handler
contained in this manual.
Product documentation
Read all applicable documentation before commencing
installation. Store documentation near air handler in a
readily accessible location for reference in the future
by service personnel.
uFor a listing of applicable literature,
please see section entitled “Important
Regulatory and Installation Requirements”.
Warranty
Information contained in this and related
product documentation must be read
and followed. Failure to do so renders
the warranty null and void.
Licensed professional heating contractor
The installation, adjustment, service and maintenance
of this equipment must be performed by a licensed
professional heating contractor.
uPlease see section entitled
“Important Regulatory and Installation
Requirements”.
Advice to owner
Once the installation work is complete, the heating
contractor must familiarize the system operator/
ultimate owner with all equipment, as well as safety
precautions/requirements, shutdown procedure, and
the need for professional service annually before the
heating season begins.
Operating and service documentation
It is recommended that all product documentation such as
parts lists, operating and service instructions be handed
over to the system user for storage. Documentation is to
be stored near air handler in a readily accessible location
for reference by service personnel.
WARNING
Inhaling of fiberglass wool materials is a possible cancer
hazard. These materials can also cause respiratory, skin
and eye irritation.
Fiberglass wool materials
WARNING
Appliance materials of construction, may contain toxic
or harmful substances which can cause serious injury
or loss of life and which are known to the State of
California to cause cancer, birth defects and other
reproductive harm. Always use proper safety clothing,
respirators and equipment when servicing or working
nearby the appliance.
The state of California has listed the airborne fibers of
these materials as a possible cancer hazard through
inhalation. When handling these materials, special care
must be applied.
First aid measures
- If eye contact occurs, flush eyes with water to
remove dust. If symptoms persist, seek medical
attention.
- If skin contact occurs, wash affected areas gently
with soap and warm water after handling.
Suppliers of fiberglass wool products recommend the
following precautions be taken when handling these
materials:
- Avoid breathing fiberglass dust and contact with
skin and eyes.
- Use NIOSH approved dust/mist respirator.
- Wear long-sleeved, loose fitting clothing, gloves
and eye protection.
- Wash work clothes separately from other clothing.
Rinse washer thoroughly.
- Operations such as sawing, blowing, tear-out and
spraying may generate airborne fiber concentration
requiring additional protection.

3
6197 083 - 03
Nu-Air HA Installation, Service and Operating
Safety
General Information
Product Description
Installation
Page
Safety, Installation and Warranty Requirements..............2
Product documentation...........................................2
Warranty...............................................................2
Licensed professional heating contractor...................2
Advice to owner....................................................2
Operating and service documentation.......................2
Fiberglass wool materials........................................2
First aid measures..................................................2
About these Installation Instructions..............................5
Necessary Tools.........................................................5
Important Regulatory and Installation Requirements........6
Codes..................................................................6
Instructing the system user...................................6
Initial start-up........................................................6
Working on the equipment......................................6
Technical literature................................................6
Introduction...............................................................7
Components................................................................7
Features......................................................................8
Equipment Selection and Sizing.....................................9
Compatibility Charts.....................................................9
BeforeSet-up..............................................................12
Minimum Clearances...................................................12
Dimensions.............................................................13
Pressure Drop........................................................14
Installation...............................................................14
Installation Examples.................................................15
Proper Piping Practice................................................16
Connecting to the Heating System..............................17
Panels.....................................................................18
Opening the Air Handling Unit....................................18
Rotating the Heating Coil.......................................19
Ductwork................................................................21
Installing the Filter Rack........................................22
Accessing the Connection Board...............................22
Viessmann Vitodens 100 B1HE, B1KE Wiring..............23
Viessmann Vitodens 200 B2HE Wiring........................24
Viessmann HO1B Control Wiring...............................25
External Heat Demand via Switching Contact...............25
Controller Logic........................................................26
Freeze Protection Temperature....................................27
Control Inputs.........................................................27
Outputs...................................................................27
Electrical.................................................................28
Power Supply..........................................................29
Quick Check.............................................................30
Table of Contents

Nu-Air HA Installation, Service and Operating
6197 083 - 03
4
Startup
Operation
Service
Additional Information
Page
Startup Procedure....................................................31
Air handler LED Indications.........................................31
Closing the Connection Board.....................................32
Closing the Air Handler Unit.......................................32
Normal Operation......................................................34
Troubleshooting.......................................................35
Service and Maintenance...........................................36
System Layout 1......................................................37
System Layout 2......................................................38
System Layout 3......................................................39
System Layout 4......................................................40
System Layout 5......................................................41
System Layout 6......................................................42
System Layout 7......................................................43
System Layout 8......................................................44
System Layout 9......................................................45
System Layout 10....................................................46
Electrical Connections................................................47
Blower Speed Adjustment..........................................48
Performance HA 6018..............................................48
Performance HA 8524..............................................49
Performance HA 9836..............................................50
Technical Data.........................................................51
Parts List.................................................................52
Table of Contents

5
6197 083 - 03
Nu-Air HA Installation, Service and Operating General Information
About these Installation Instructions
Take note of all symbols and notations intended to draw attention to potential hazards or important
product information.
CAUTION
Cautions draw your attention to the presence of potential
hazards or important product information.
WARNING
Warnings draw your attention to the presence of potential
hazards or important product information.
u
IMPORTANT
uIndicates an imminently hazardous situation which,
if not avoided, could result in death, serious injury or
substantial product/property damage.
uIndicates an imminently hazardous situation which,
if not avoided, may result in minor injury or product/
property damage.
uHelpful hints for installation, operation or maintenance
which pertain to the product.
uThis symbol indicates to note additional information
uThis symbol indicates that other instructions must be
referenced.
Necessary Tools
Testing/analysis equipment
(Use only calibrated equipment)
HMultimeter to measure 0 - 230V, 0 - 12A AC and
0-100 mA DC
HManometer to measure air pressure 0 to 11 "w.c.
(accurately) (or a non-electric Magnehelic® manometer
may also be utilized)
Cleaning supplies
HPlastic hand brush
HRags
Special items
HPipe joint sealant

Nu-Air HA Installation, Service and Operating
6197 083 - 03
6
Important Regulatory and Installation Requirements
General Information
Codes
In Canada all electrical wiring is to be done in accordance
with the latest edition of CSA C22.1 Part 1 and/or local
codes. In the U.S. use the National Electrical Code ANSI/
NFPA 70. The heating contractor must also comply with
both the Standard for Controls and Safety Devices for
Automatically Fired Boilers, ANSI/ASME CSD-1, and
the Installation Code for Hydronic Heating Systems,
CSA B214-01, where required by the authority having
jurisdiction.
Instructing the system user
The installer of the system is responsible to ensure the
system operator/ultimate owner is made familiar with the
system functioning, its activation, and its shut-down.
The following topics must be covered:
- Proper system operation sequence.
- Explain the equipment.
- Demonstrate an emergency shut-down, what to do
and what not.
- Explain that there is no substitute for proper
maintenance to help ensure safe operation.
Initial start-up
Initial start-up must be performed by a qualified heating
contractor. Proper completion of the Maintenance Record
by the heating contractor is also required.
Working on the equipment
The installation, adjustment, service, and maintenance of
this air handler must be done by a licensed professional
heating contractor who is qualified and experienced in
the installation, service, and maintenance of hot water
heating equipment. There are no user serviceable parts
on the air handler.
Please carefully read this manual prior to attempting
start-up, maintenance or service. Any warranty is null
and void if these instructions are not followed.
For information regarding Viessmann System Technology
componentry, please reference documentation of the
respective product.
We offer frequent installation and service seminars to
familiarize our partners with our products. Please inquire.
Ensure main power supply to equipment, the heating
system, and all external controls have been deactivated.
Take precautions in all instances to avoid accidental
activation of power during service work.
The completeness and functionality of field supplied
electrical controls and components must be verified by
the heating contractor. These include low water
cut-offs, flow switches (if used), staging controls,
pumps, motorized valves, air vents, thermostats, etc.
Technical literature
Literature for the Nu-Air HA air handler:
- Technical Data Manual
- Installation, Service, and Operating Instructions
- Instructions of Viessmann products utilized and installed
- Installation codes mentioned in this manual
Leave all literature at the installation site and advise the
system operator/ultimate owner where the literature
can be found. This product comes with several safety
instruction labels attached. Do not remove!

7
6197 083 - 03
Nu-Air HA Installation, Service and Operating
Introduction
The Nu-Air HA series air handlers are to be used in
conjunction with Viessmann boilers.
The automatic adjustments are made in heating as well
as cooling. This minimizes selecting an oversized heating
appliance just to accommodate the cooling load.
The Nu-Air HA series is always the right size.
Components
Cabinet
All cabinets have a tough, durable powder coat finish
on heavy gauge aluminum.
Heating coils
All heating coils are copper and assembled using no lead
solder. High density aluminum fins provide maximum heat
transfer for small coil surface.
Fan and motor
Constant speed EC (Electronically Commutated) Motor.
Pump exercise function
120VAC pump output, controlled by the Nu-Air HA
including 24 hr. pump exerciser to eliminate stagnant
water, and prevent the pump from seizing.
Zone control logic
Integrated zone control to control up to 3 zones. Zone 1
lead logic prevents simultaneous heat and cool calls.
Legend
AHydronic supply/return connections
BHydronic heating coil
CConnections for up to 3 thermostats (for 3 zones and
outputs for 3 zone dampers
DAcoustic sound reduction insulation
EBlower motor and controls
Product Description
The Nu-Air HA hydronic air handler is designed to
maximize performance and comfort in residential or light
commercial applications. Smart control systems within the
air handler allows extraction of maximum heat by allowing
condensing high efficiency heat sources to work at their
maximum efficiency while providing ultimate comfort with
unmatched performance.
A
A
E
B
C
D

Nu-Air HA Installation, Service and Operating
6197 083 - 03
8
Product Description
Features
Pump exercise function
If the pump has not run in the previous 24 hours, the
control will turn the pump on for 1 minute to flush the
lines and heating coil. This will help ensure that the water
lubricated pump does not seize during long periods of
inactivity.
Freeze protection
Should the air handler be installed in an area where the
ambient temperature may fall below freezing, propylene
glycol, up to 50% maximum concentration, should be
added into the hydronic heating system to protect against
damage.
Condenser Lockout/Freeze Protection
The air handler is equipped with a condenser lockout /
freeze protection sensor to help prevent any damage to
the heating coil from a freeze up. In any mode, heating,
cooling or standby, when the heating coil temperature
is 37°F (3°C) or lower the air handler will energize the
pump relay and boiler switch and open the A/C interlock,
turning off the condenser unit.

9
6197 083 - 03
Nu-Air HA Installation, Service and Operating
Equipment Selection and Sizing
Proper sizing of systems components is crucial for proper
operation;
1. Obtain room by room heat loss and/or heat gain
2. Determine heating water temperature
3. Determine duct layout
Make sure a proper room-by-room heat loss and heat
gain for the dwelling is calculated using Manual J, HRAI,
ASHRAE or other approved sizing method.
Boiler supply
water temperature
120°F
(49°C)
25.0 MBH
(7.4 kW)
140°F
(60°C)
35.0 MBH
(10.3 kW)
160°F
(71°C)
46.0 MBH
(13.5 kW)
180°F
(82°C)
56.0 MBH
(16.4 kW)
Viessmann Boiler Model
Vitodens 100 B1HE-85 a a a a
Vitodens 100 B1HE-120 a a a a
Vitodens 100 B1HE-150 a a a a
Vitodens 100 B1HE-199 a a a a
Vitodens 100 B1KE-120 a a a a
Vitodens 100 B1KE-199 a a a a
Vitodens 222 B2TB-125 a a a a
Vitodens 200 B2HA-285 a a a a
Vitodens 200 B2HA-311 a a a a
Vitodens 200 B2HA-352 a a a a
Vitodens 200 B2HA-399 a a a a
Vitodens 200 B2HA-530 a a a a
Vitodens 200 B2HE-85 a a a a
Vitodens 200 B2HE-120 a a a a
Vitodens 200 B2HE-150 a a a a
Vitodens 200 B2HE-199 a a a a
Vitocrossal 300 CU3A-94 a a a a
Vitocrossal 300 CU3A-125 a a a a
Vitocrossal 300 CU3A-160 a a a a
Vitocrossal 300 CU3A-199 a a a a
Compatibility Charts
Air handler model HA 6018
Product Description
Note: Compatibility charts are based on an entering air temperature of 70°F (21°C), airflow rate of 700 cfm,
and a heating water supply flow rate of 5 gpm (1136 L/h) (at the temperatures specified above), additional
settings are possible, please refer to charts starting on page 48.
Compatibility charts do not take into consideration systems using additional heat emitters, DHW load etc.
Ensure the boiler selected meets all of the system requirements for loads generated by additional components.
It is the responsibility of the system designer to ensure proper sizing and equipment selection.

Nu-Air HA Installation, Service and Operating
6197 083 - 03
10
Compatibility Charts (continued)
Product Description
Air handler model HA 8524
Note: Compatibility charts are based on an entering air temperature of 70°F (21°C), airflow rate of 900 cfm,
and a heating water supply flow rate of 7 gpm (1590 L/h) (at the temperatures specified above), additional
settings are possible, please refer to charts starting on page 48.
Compatibility charts do not take into consideration systems using additional heat emitters, DHW load etc.
Ensure the boiler selected meets all of the system requirements for loads generated by additional components.
It is the responsibility of the system designer to ensure proper sizing and equipment selection.
Boiler supply
water temperature
120°F
(49°C)
34.0 MBH
(10.0 kW)
140°F
(60°C)
49.0 MBH
(14.4 kW)
160°F
(71°C)
63.0 MBH
(18.5 kW)
180°F
(82°C)
78.0 MBH
(23.0 kW)
Viessmann Boiler Model
Vitodens 100 B1HE-85 a a a --
Vitodens 100 B1HE-120 a a a a
Vitodens 100 B1HE-150 a a a a
Vitodens 100 B1HE-199 a a a a
Vitodens 100 B1KE-120 a a a a
Vitodens 100 B1KE-199 a a a a
Vitodens 222 B2TB-125 a a a a
Vitodens 200 B2HA-285 a a a a
Vitodens 200 B2HA-311 a a a a
Vitodens 200 B2HA-352 a a a a
Vitodens 200 B2HA-399 a a a a
Vitodens 200 B2HA-530 a a a a
Vitodens 200 B2HE-85 a a a --
Vitodens 200 B2HE-120 a a a a
Vitodens 200 B2HE-150 a a a a
Vitodens 200 B2HE-199 a a a a
Vitocrossal 300 CU3A-94 aaa --
Vitocrossal 300 CU3A-125 a a a a
Vitocrossal 300 CU3A-160 a a a a
Vitocrossal 300 CU3A-199 a a a a

11
6197 083 - 03
Nu-Air HA Installation, Service and Operating
Air handler model HA 9836
Compatibility Charts (continued)
Product Description
Note: Compatibility charts are based on an entering air temperature of 70°F (21°C), airflow rate of 1200 cfm,
and a heating water supply flow rate of 7 gpm (1590 L/h) (at the temperatures specified above), additional
settings are possible, please refer to charts starting on page 48.
Compatibility charts do not take into consideration systems using additional heat emitters, DHW load etc.
Ensure the boiler selected meets all of the system requirements for loads generated by additional components.
It is the responsibility of the system designer to ensure proper sizing and equipment selection.
Boiler supply
water temperature
120°F
(49°C)
44.0 MBH
(13.0 kW)
140°F
(60°C)
63.0 MBH
(18.5 kW)
160°F
(71°C)
83.0 MBH
(24.4 kW)
180°F
(82°C)
102.0 MBH
(30.0 kW)
Viessmann Boiler Model
Vitodens 100 B1HE-85 a a -- --
Vitodens 100 B1HE-120 a a a --
Vitodens 100 B1HE-150 a a a a
Vitodens 100 B1HE-199 a a a a
Vitodens 100 B1KE-120 a a a --
Vitodens 100 B1KE-199 a a a a
Vitodens 222 B2TB-125 a a a --
Vitodens 200 B2HA-285 a a a a
Vitodens 200 B2HA-311 a a a a
Vitodens 200 B2HA-352 a a a a
Vitodens 200 B2HA-399 a a a a
Vitodens 200 B2HA-530 a a a a
Vitodens 200 B2HE-85 a a -- --
Vitodens 200 B2HE-120 a a a --
Vitodens 200 B2HE-150 a a a a
Vitodens 200 B2HE-199 a a a a
Vitocrossal 300 CU3A-94 a a -- --
Vitocrossal 300 CU3A-125 a a a --
Vitocrossal 300 CU3A-160 a a a a
Vitocrossal 300 CU3A-199 a a a a

Nu-Air HA Installation, Service and Operating
6197 083 - 03
12
Installation
Before Set-up
Recommended minimum service clearances
For typical Nu-Air HA installation, it is recommended to
install the air handler with the clearances shown in the
illustration.
Before placing Nu-Air HA in its installation location,
ensure all necessary accessories are installed.
Minimum Clearances
CAUTION
The air handler must be installed in such a way that
electrical components are protected from water (spraying,
splashing, etc.) during operation and service.
a - 24 in. (610 mm)
b - 0 in. (0 mm)
These dimensions reflect the recommended service
clearance for the air handler only, ensure adequate clearance
is left for the installation of ducting, piping and electrical
connections. Ensure to leave adequate clearance for
ductwork, plumbing and electrical connections, with zero
clearance between the air handler unit and ducting being
acceptable.
The Nu-Air HA requires 0 in. (0 mm) clearance to
combustibles.

13
6197 083 - 03
Nu-Air HA Installation, Service and Operating
Top view
Front view Side view
Installation
Dimensions
IMPORTANT
The maximum ambient temperature must not exceed
104ºF (40ºC).
Legend
AHydronic supply connection
BHydronic return connection
Note: The Nu-Air series of handlers are supplier with push
connect to NPT thread adaptor fittings to simplify the
installation process.
d
e
c
f
g
a
b
h
A
B
HA 6018 HA 8524 HA 9836
a in.
(mm)
19a
(487)
21a
(539)
21a
(539)
b in.
(mm)
22c
(575)
22c
(575)
22c
(575)
c in.
(mm)
29
(737)
31b
(800)
31b
(800)
d in.
(mm)
3b
(89)
3c
(93)
3c
(93)
e in.
(mm)
6a
(156)
6a
(160)
6a
(160)
f in.
(mm)
4a
(104)
2a
(53)
2a
(53)
g in.
(mm)
15a
(383)
19a
(485)
19a
(485)
h in.
(mm)
23c
(600)
23c
(603)
23c
(603)

Nu-Air HA Installation, Service and Operating
6197 083 - 03
14
The Nu-Air HA can be suspended by securing straps to
the corners of the enclosure (field supplied).
Install the air handler with the door screwed in place to
avoid distortion of the cabinet. The installing contractor
must ensure that suspension materials are sized and
installed to provide sufficient support to the air handler
and connected accessory fittings and materials.
Note: System layout examples are provided starting on
page 37 of these instructions.
Installation
The contractor shall adhere to all local, state and national
code requirements pertaining to the installation of this
equipment.
The Nu-Air HA series air handler can be mounted in
most directions. Upflow, downflow, horizontal left and
horizontal right. An adequately sized drain pan and drain
connection must be installed under the appliance.
This appliance shall not be installed in a non conditioned
space where the potential may exist for the appliance and
or water lines and drain line to freeze.
Installation
Pressure Drop
Flow Rate GPM (L/h) 3 (681) 4 (908) 5 (1135) 7 (1590)
Pressure Drop HA 6018
Ft of Head (mbar) 1.6 (48) 2.7 (81) 4.1 (123) --
Pressure Drop HA 8524 / 9836
Ft of Head (mbar) -- 1.3 (39) 1.9 (57) 3.6 (108)
Pumps are field supplied, consideration can be given to
the following pump models, based on system design
criteria:
Grundfos UPS 15-58FC
Taco 0015e3
Bell & Gossett Ecocirc 20-18F

15
6197 083 - 03
Nu-Air HA Installation, Service and Operating
Installation Examples
Installation
Note: Field selected suspension materials must be sized
by installing contractor so as to be of sufficient
strength to support air handler weight of 150 lbs.
(68 kg) and connected accessory fittings and
materials.
CAUTION
Return air openings shall not be installed in back panel.
For an installation over a finished space
A field fabricated auxiliary drain pan with drain pipe is
required to prevent damage by overflow due to blocked
condensate drain.
You cannot install the air handler on it’s back or
suspended with front cover facing down.
IMPORTANT Air Handler Mounting
The air handler can be installed in up flow, down flow and
left or right horizontal applications.
Install the air handler with the door in place to make sure
the cabinet remains square. Flip the unit for down flow
applications so that the top of the unit is now the bottom.
No modification is required for any configuration.
CAUTION
Use any of the existing screw holes in the cabinet
when using straps. If the existing screw is too short for
securing a mounting strap, a longer screw should be
used provided care is taken not to damage any internal
components. Product warranty does not cover any
damage or claims resulting from damage from longer
screws or from the unit being improperly suspended.
The cabinet is designed so that the return air can be
located on either side of the cabinet. Position the filter rack
so that the filter is readily accessible.

Nu-Air HA Installation, Service and Operating
6197 083 - 03
16
Installation Examples (continued)
Installation
Vertical installation
The A/C coil is installed in the downstream air flow of the
Nu-Air HA air handler.
IMPORTANT
A field fabricated auxiliary drain pan with drain pipe is
required in all configurations.
Return air
Supply air
A/C coil
Air
Filter
Air
Filter
A/C
Coil
Supply air
Return air
Vertical installation
The A/C coil is installed in the upstream air flow of the
Nu-Air HA air handler.
Support piping by proper suspension method.
Piping must not rest on or be supported by the air handler.
Use moderate amount of dope.
2 imperfect threads
Leave 2 threads bare
Proper Piping Practice
This section constitutes an overview only! Refer to
subsequent sections for detailed information on individual
piping connections.
Use an approved pipe sealant or Teflon tape when
connecting the following installation fittings.
This air handler is supplied with push connect to NPT
threaded adaptors to simplify the installation process.

17
6197 083 - 03
Nu-Air HA Installation, Service and Operating Installation
Air handler piping
Depending on the boiler selected and system design it may
be required to use a primary, secondary piping arrangement
to de-couple the flow through the boiler from the flow
through the air handler. Refer to the system layout examples
starting on page 37.
Boiler
Follow the instructions provided with the boiler for
installation and start-up of the boiler. Make sure the boiler
is turned off during air handler installation and service.
Ensure system has been filled, and all air is purged from
the system before turning on the boiler.
Duct work
All duct designs must be designed to conform with HRAI
Manuals “J” and “D” or local codes and requirements.
To minimize fan noise in the living space, it is recommended
that the first six feet of supply and return air duct be lined
with acoustic insulation.
Return and supply air duct work should be the same size as
the air handler openings up to the first branch, fitting or
transition.
Install a ½ in sediment faucet or ball valve for use as
a drain/purge valve. The drain valve must be located
downstream of the pump and check valve, and upstream
of the isolation valve. With this arrangement, any air
trapped in the system can easily be flushed out following
the instructions in the Start-up & Troubleshooting sections.
Installing isolation valves facilitates ease of servicing.
Following the flushing procedures in the start-up
section will ensure that there is no air in the system
after initial set-up.
Follow recommendations supplied by the manufacturer
of the boiler.
The heating coil of the Nu-Air HA series air handlers are
further equipped with vent and drain plugs at the highest
and lowest points.
Connecting to the Heating System
Legend
AAir vent
BDrain
For more details, refer to the boiler Installation
and Service Instructions.
AB

Nu-Air HA Installation, Service and Operating
6197 083 - 03
18
1. Remove the front panel retaining screws and set
aside.
2. Pull the front panel straight out to remove.
Installation
Opening the Air Handler Unit
Panels
The cabinet is designed so that the return air can be
located on either side of the cabinet.
Position the filter rack so that the filter is readily accessible.
A filter is not included.
Supply air connection
Return air
connection
(left or right side)
Knock outs for routing
electrical connections
(left or right side)
IMPORTANT
The air handler is shipped with a blower retaining bracket,
this bracket must be removed prior to installation of the
air handler.

19
6197 083 - 03
Nu-Air HA Installation, Service and Operating
Rotating the Heating Coil
Installation
1. Remove the upper side panels and set aside.
2. Cut the zipties holding the thermistor, and move the
thermistor out of the way.
3 Unscrew and remove the outer top panel and set
aside.
4. Unscrew and remove the inner top panel and set a
side.
5. Remove the heating coil and set aside.
1.
3.
4.
2.
5.

Nu-Air HA Installation, Service and Operating
6197 083 - 03
20
Rotating the Heating Coil (continued)
Installation
5. Rotate the heating coil 1808horizontally.
Do Not flip vertically.
8. Reinstall the heating coil, and reattach the thermistor
to the heating water supply port of the heating coil
with a zip tie.
7.
8.
6. Remove the retaining brackets and reposition them as
shown.
6.
Front
This manual suits for next models
3
Table of contents
Popular Air Handler manuals by other brands
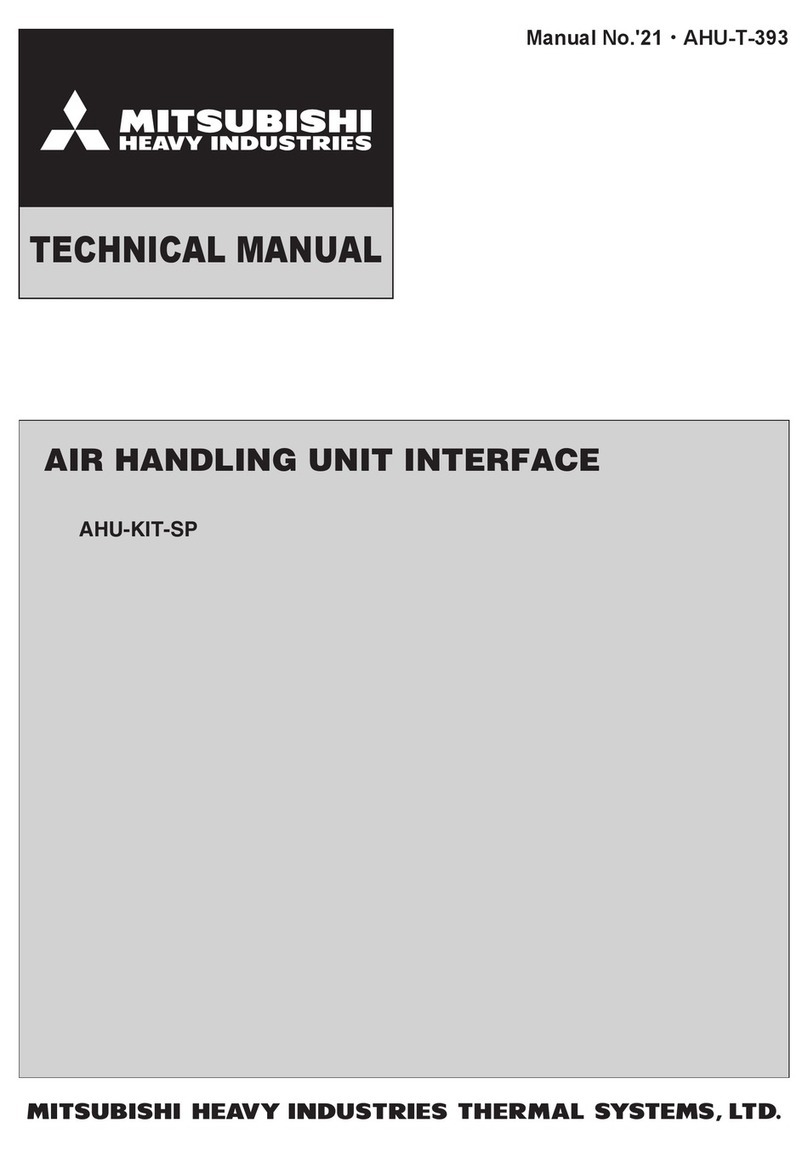
Mitsubishi Heavy Industries
Mitsubishi Heavy Industries AHU-KIT-SP Technical manual
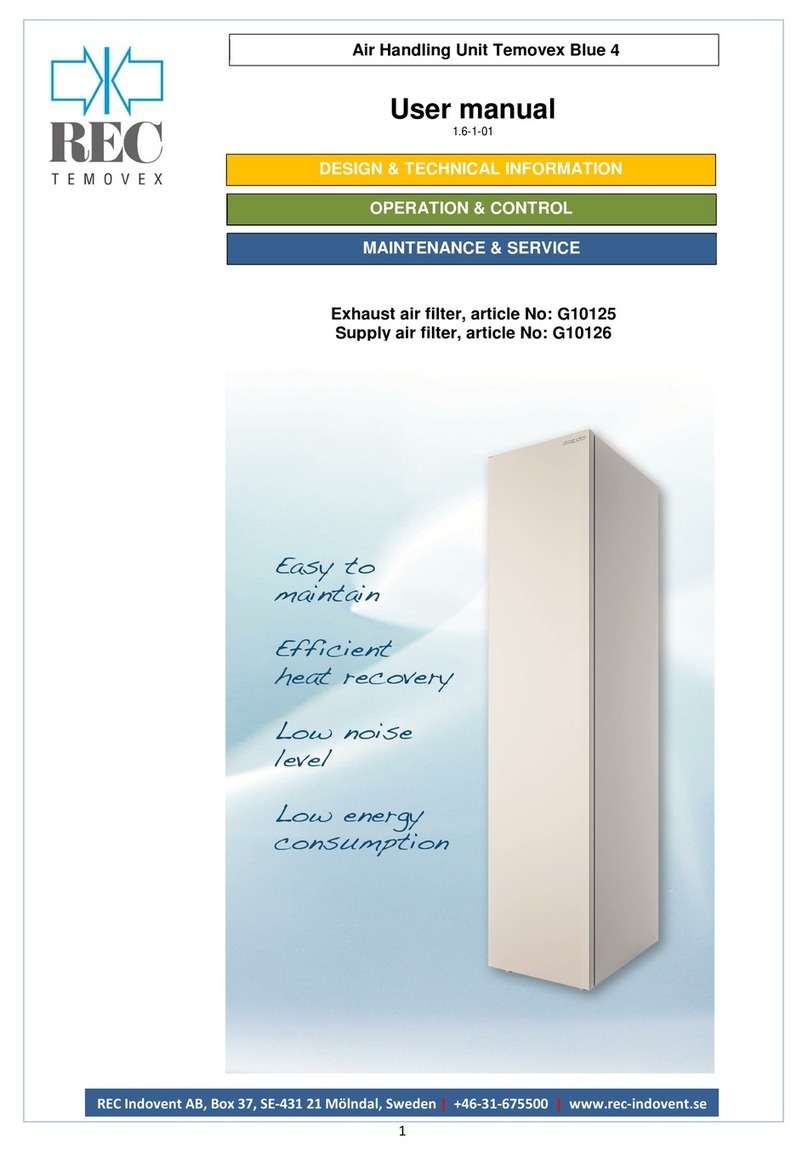
Rec Temovex
Rec Temovex G10125 user manual
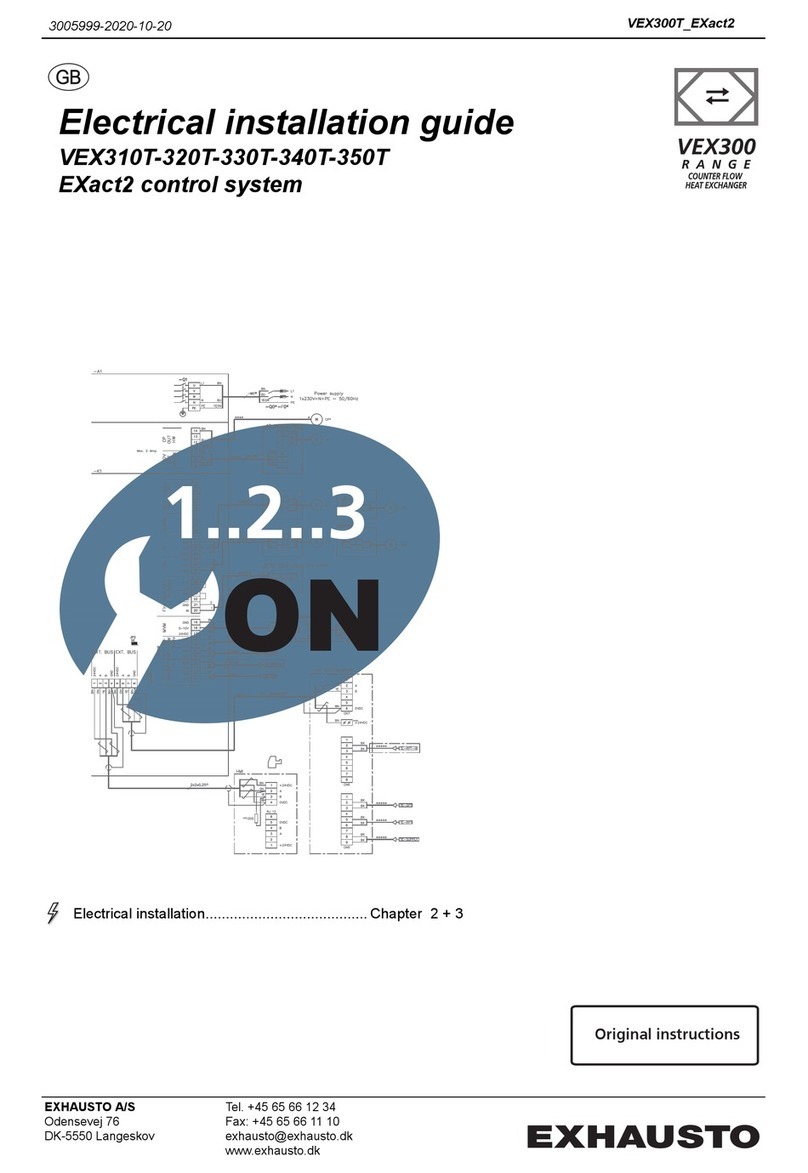
Exhausto
Exhausto VEX300 Series Electrical installation guide
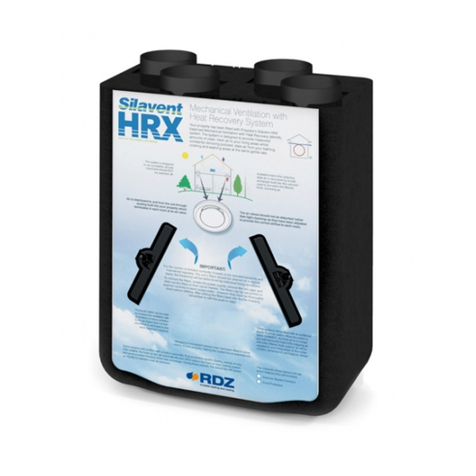
RDZ
RDZ SILAVENT HRXD Technical installation manual
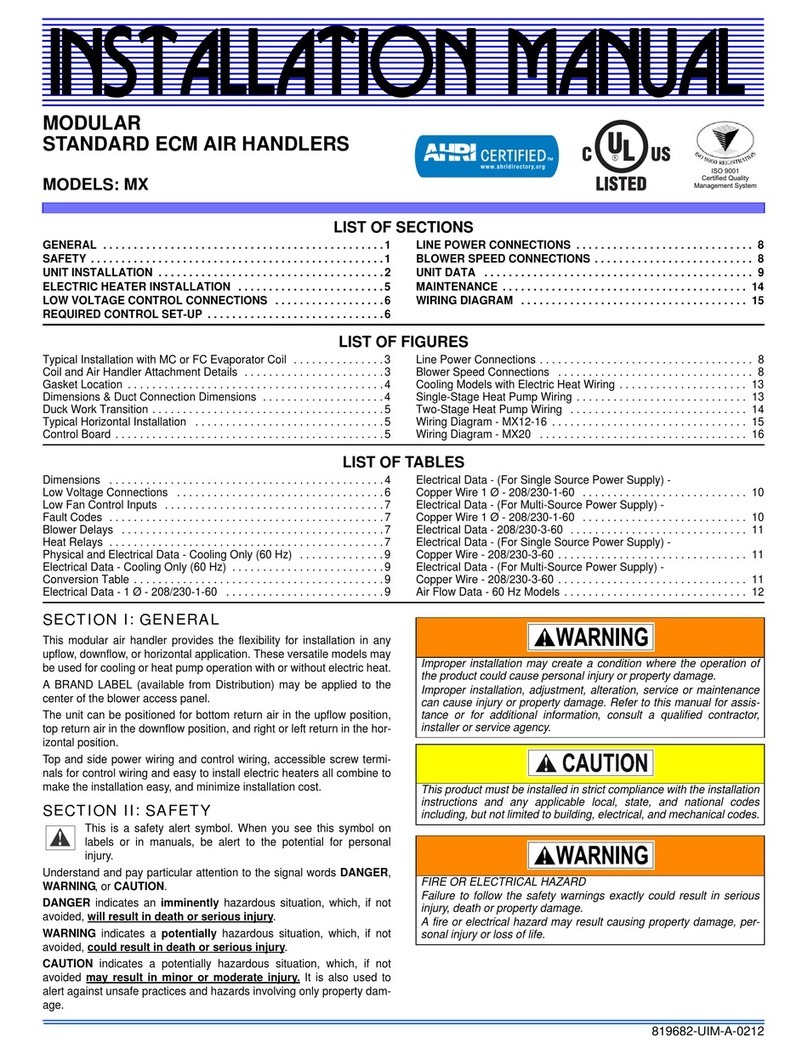
York
York MX Series installation manual
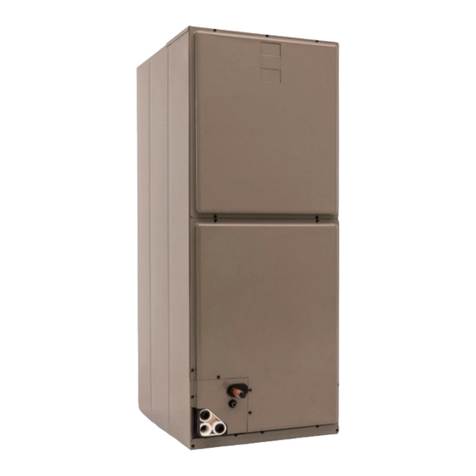
Johnson Controls
Johnson Controls MAHP18B21S Installation and maintenance manual
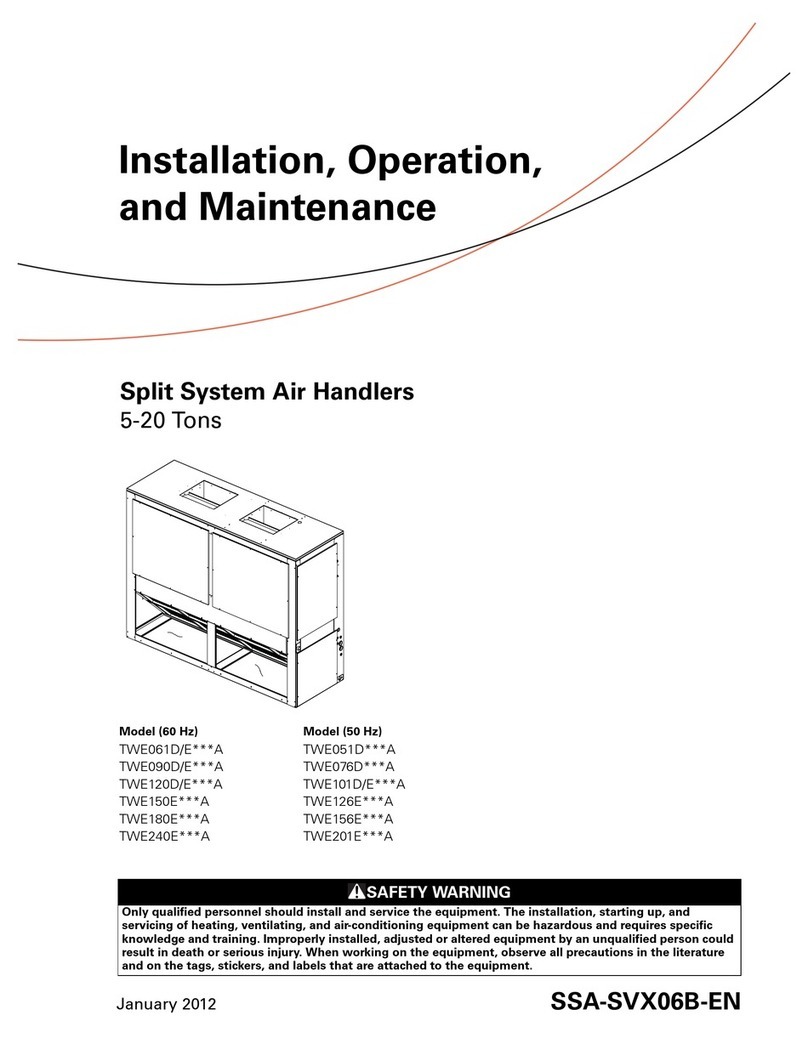
Ingersoll-Rand
Ingersoll-Rand twe065e13fa1 Installation, operation and maintenance

IV Produkt
IV Produkt Envistar Top Assembly instructions
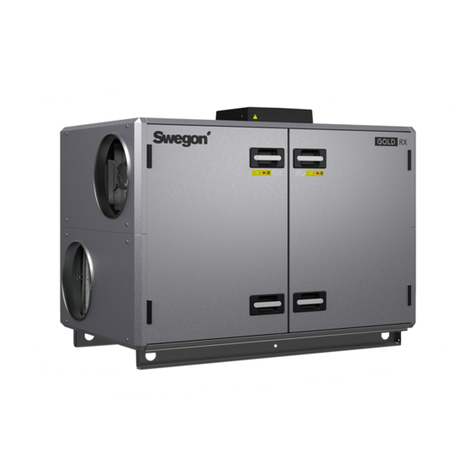
Swegon
Swegon GOLD series Function guide
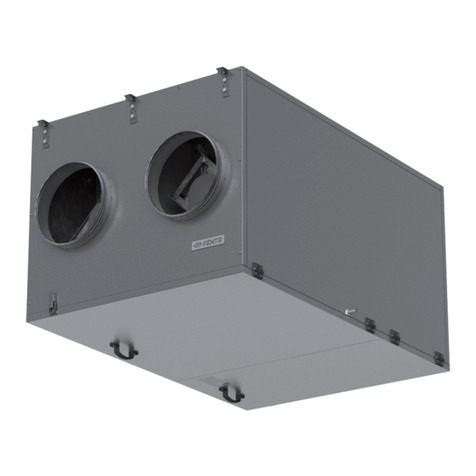
Vents
Vents VUT 3000 PE EC user manual
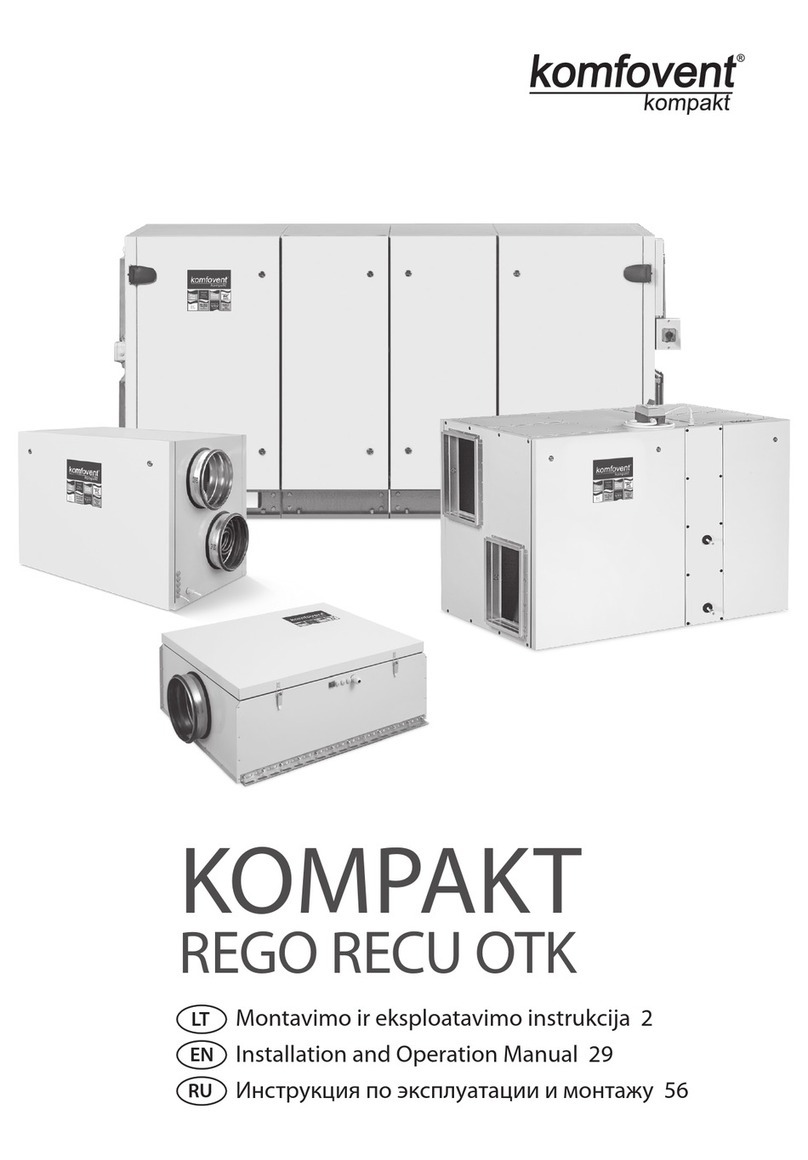
Komfovent
Komfovent KOMPAKT REGO Series Installation and operation manual
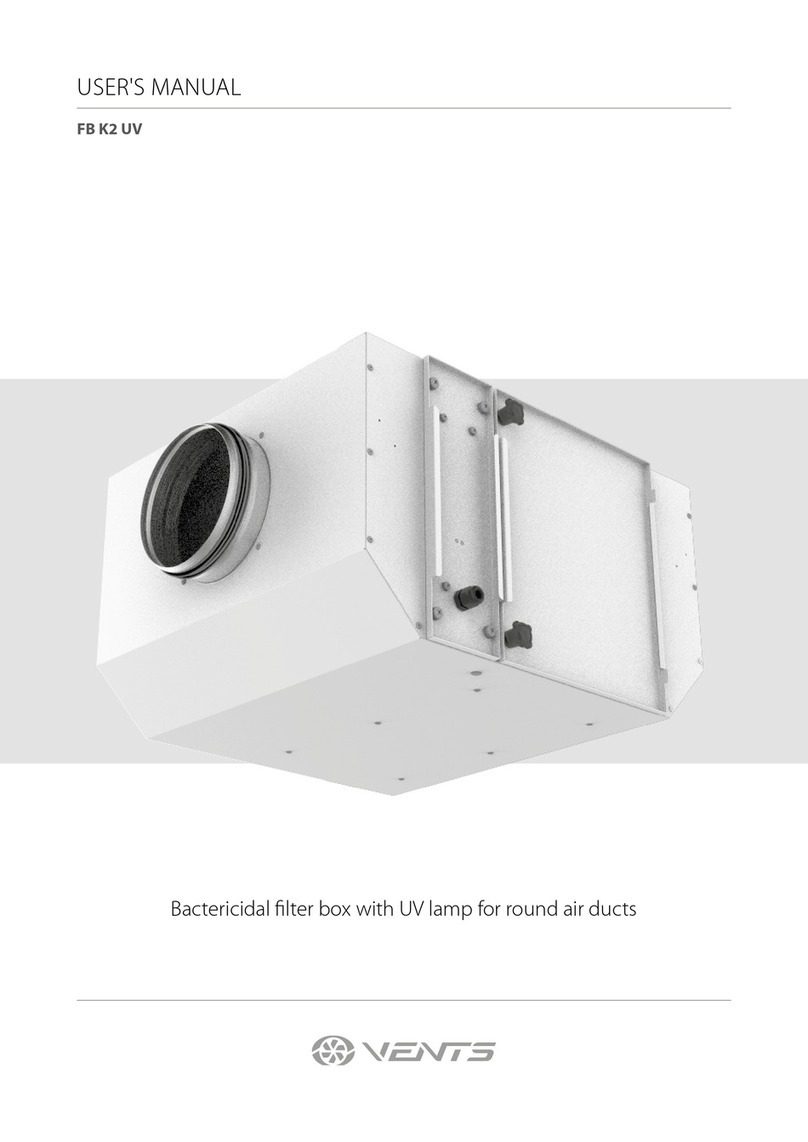
Vents
Vents FB K2 UV user manual