NXP Semiconductors AN13125 Installation and operating instructions

AN13125
IW416 Design Guide
Rev. 1 — 26 May 2021 Application note
Document information
Information Content
Keywords Power supply, clock source, reset, host interface, RF interface, PCB layout,
PCB stackup
Abstract Provides design guidelines for IW416 device.

NXP Semiconductors AN13125
IW416 Design Guide
Rev Date Description
v.1 20210526 Initial version
Revision history
AN13125 All information provided in this document is subject to legal disclaimers. © NXP B.V. 2021. All rights reserved.
Application note Rev. 1 — 26 May 2021
2 / 33

NXP Semiconductors AN13125
IW416 Design Guide
1 Overview
This document provides design guidelines for NXP IW416 device. The IW416 is a highly
integrated Wi-Fi® 4 (2.4 GHz/5 GHz) and Bluetooth® 5.1 single-chip solution.
The IW416 is available in two package options – QFN and WLCSP.
NXP releases reference designs to provide examples on how to design a PCB using the
device. We strongly recommend follow these design guidelines closely. Please contact
your NXP representative to schedule a design review and discuss design options.
Note: In the following sections, the IW416 may be referred to as “Wireless SoC”
AN13125 All information provided in this document is subject to legal disclaimers. © NXP B.V. 2021. All rights reserved.
Application note Rev. 1 — 26 May 2021
3 / 33

NXP Semiconductors AN13125
IW416 Design Guide
2 Power supply
2.1 Power supply overview
Table 1 lists the power supplies.
Supply Description Typical value
VCORE Core power supply 1.05 V
AVDD18 Analog power supply 1.8 V
VPA Wi-Fi PA power supply 2.2 V
VIO Digital I/O power supply 1.8 V or 3.3 V
VIO_SD SDIO power supply 1.8 V or 3.3 V
VIO_RF RF power supply 1.8 V or 3.3 V
Table 1. Power supplies
A “2-wire” power management interface is used to lower the core voltage to reduce
power consumption in sleep mode. The power management interface uses two control
signals, DVSC1 and DVSC0, to dynamically adjust the voltage level from the power
management IC (PMIC). Under normal operation, the core voltage level is 1.05 V. In
sleep mode, the core voltage is dropped to 0.8 V.
The following sections describe PMIC solutions from MPS, NXP, and Marvell
manufacturers:
•MPS: MP2182, MP2162A, MP8904
•Marvell 88PG823
•NXP PM823
AN13125 All information provided in this document is subject to legal disclaimers. © NXP B.V. 2021. All rights reserved.
Application note Rev. 1 — 26 May 2021
4 / 33

NXP Semiconductors AN13125
IW416 Design Guide
2.2 Power supply using MPS PMICs
Figure 1 shows a simplified block diagram using the MPS MP2182, MP2162A and
MP8904. Two control signals, DVSC1 and DVSC0, are used to control the core voltage
level. Table 2 shows the part numbers.
Figure 1. Power supply by MPS PMICs
Manufacturer Part number
MPS BUCK: MP2162AGQH-C867-Z
MPS BUCK: MP2182GTL-C867-Z
MPS BUCK: MP8904DD-C867-LF-Z
Table 2. MPS PMICs part numbers
AN13125 All information provided in this document is subject to legal disclaimers. © NXP B.V. 2021. All rights reserved.
Application note Rev. 1 — 26 May 2021
5 / 33

NXP Semiconductors AN13125
IW416 Design Guide
2.3 Power supply using NXP PM823 or Marvell 88PG823
Figure 2 shows a simplified block diagram using the NXP PM823 or Marvell 88PG823
(QFN). Two control signals, DVSC1 and DVSC0, are used to control the core voltage
level. Table 3 shows the part numbers.
Figure 2. Power supply by 88PG823 (QFN)
Manufacturer Part number
Marvell QFN package option: 88PG823-xx-NPD2C000
Marvell WLCSP package option: 88PG823-xx-CBK2-T
NXP QFN package option: PM823HN/A0CHP
NXP WLCSP package option: PM823UK/A0CZ
Table 3. Marvell and NXP PMICs part numbers
2.4 Power-up sequence requirements
All the power rails must meet correct power-up sequence. Refer to IW416 data sheet.
AN13125 All information provided in this document is subject to legal disclaimers. © NXP B.V. 2021. All rights reserved.
Application note Rev. 1 — 26 May 2021
6 / 33

NXP Semiconductors AN13125
IW416 Design Guide
2.5 PCB layout guidelines
Refer to the following PCB layout guidelines for power supply.
•Follow the PMIC schematic/layout exactly. Any deviation must be reviewed with PMIC
vendor Applications Engineer.
•Use power planes (layer) and polygons to lower the power impedance.
•Use decoupling capacitors with low ESR
•Place the power vias and ground vias as close as possible to the decoupling
capacitors, as shown in Figure 3.
Figure 3. Power vias and ground vias
•Ensure each power pin has its own decoupling capacitor. Place the decoupling
capacitors as close as possible to the power pin.
•The power from source to the power pin should go through the decoupling network
before connecting to the power pin. As shown in Figure 4
Figure 4. Example of power trace outing to power pin
AN13125 All information provided in this document is subject to legal disclaimers. © NXP B.V. 2021. All rights reserved.
Application note Rev. 1 — 26 May 2021
7 / 33

NXP Semiconductors AN13125
IW416 Design Guide
•There is a decoupling capacitor for each power pin and a bulk capacitor for each rail.
Place the decoupling capacitor as close as possible to the power pin, then place the
bulk capacitor. Figure 5 shows an example where C9 is the decoupling capacitor for K5
pin. In this example, place C9 as close as possible to K5 pin, and place C58 close to
C9.
Figure 5. Decoupling capacitor and bulk capacitor placements
•Do not place any analog power plane (trace) as ring and loop in the layout. Figure 6
shows the correct top layer (left hand side of the figure) and the incorrect top layer
(right hand side). In the correct top layer, there is no loop on the AVDD18 net.
Figure 6. Power plane without loop
AN13125 All information provided in this document is subject to legal disclaimers. © NXP B.V. 2021. All rights reserved.
Application note Rev. 1 — 26 May 2021
8 / 33

NXP Semiconductors AN13125
IW416 Design Guide
3 Clock source
Two main clock sources are available: a crystal, and an external oscillator. An optional
sleep clock is also available for low power mode.
3.1 Crystal
In a typical application, a 26 MHz or 40 MHz crystal is used as a reference clock source.
We recommend to select a crystal with ±10 ppm at 25°C and ±10 ppm over the operating
temperature range. For detailed crystal specifications, refer to IW416 data sheet.
Figure 7 shows the crystal connections. The internal capacitor in the Wireless SoC is
used to tune the crystal frequency. External loading capacitors are typically not needed.
Figure 7. Typical crystal circuit
PCB layout guidelines for the crystal
Refer to the following guidelines for the crystal:
•Place the crystal close to the device and keep it as far away as possible from the RF
side of the device and high frequency signal traces such as SDIO, PCIe, or USB.
•Keep XTAL_IN and XTAL_OUT traces far from any noisy or switching signal, at a
distance of at least ten times the substrate height.
AN13125 All information provided in this document is subject to legal disclaimers. © NXP B.V. 2021. All rights reserved.
Application note Rev. 1 — 26 May 2021
9 / 33

NXP Semiconductors AN13125
IW416 Design Guide
•Keep XTAL_IN and XTAL_OUT traces as short as possible, as shown in Figure 8.
Figure 8. Crystal PCB layout
•Make sure XTAL_IN and XTAL_OUT traces are referenced to the solid ground plane in
the second layer.
•Place the ground guard with ground stitching vias around the XTAL_IN and XTAL_OUT
traces, as shown in Figure 8.
•To minimize the reference clock signals, cut out all internal metal planes under the
crystal and keep the last ground plane as the reference plane.
AN13125 All information provided in this document is subject to legal disclaimers. © NXP B.V. 2021. All rights reserved.
Application note Rev. 1 — 26 May 2021
10 / 33

NXP Semiconductors AN13125
IW416 Design Guide
3.2 External oscillator
Figure 9 shows the typical application circuit for an external oscillator.
Figure 9. External oscillator circuit
An external 26 MHz external oscillator may be used as reference clock source. If using
an external oscillator, make sure its frequency accuracy meets the ±20 ppm IEEE
specification over the operating temperature range of the product. Refer to IW416 data
sheet for the oscillator requirement specification.
PCB layout guidelines for the external oscillator
•Follow the external oscillator vendor's recommendations for the layout.
•Place the oscillator as far as possible from the Wireless SoC RF side.
•Keep the clock trace as short as possible.
•Ground the guard trace with the ground via around the clock trace.
3.3 Sleep clock
An optional external sleep clock may be used to further reduce the power consumption in
sleep mode.
Note the following:
•The external sleep clock frequency is 32.768 kHz.
•The external sleep clock usage is optional
•If an external sleep clock is not used, it is recommended to leave the SLP_CLK_IN pin
floating.
AN13125 All information provided in this document is subject to legal disclaimers. © NXP B.V. 2021. All rights reserved.
Application note Rev. 1 — 26 May 2021
11 / 33

NXP Semiconductors AN13125
IW416 Design Guide
4 Reset
4.1 Reset overview
Power on reset (POR) is triggered when the correct power up sequence is followed.
Refer to IW416 data sheet for details on power up sequence requirements.
The PDn signal is used to reset the Wireless SoC. On the NXP reference design, the
PDn signal is pulled up to VIO to meet the power-up sequence requirements. The PDn
pin may be connected to a reset signal from the host CPU. Refer to IW416 data sheet for
further details on PDn usage.
4.2 Reset strap configuration
It is critical to set the reset configuration pins correctly at reset to ensure the proper
configuration for the Wireless SoC. Refer to IW416 data sheet for details on the
configuration pins and host configuration options.
4.3 PCB layout guidelines
•Do not route PDn signal next to a large switching signal or on the edge of the PCB to
avoid EMI affecting the reset signal, as shown in Figure 10.
•The pull-up resistor on the external reset signal is placed close to PDn pin.
Figure 10. PDn signal trace routing
AN13125 All information provided in this document is subject to legal disclaimers. © NXP B.V. 2021. All rights reserved.
Application note Rev. 1 — 26 May 2021
12 / 33

NXP Semiconductors AN13125
IW416 Design Guide
5 Host interface
Table 4 lists the supported host interfaces.
Wi-Fi Bluetooth
SDIO 3.0 UART
Table 4. Wi-Fi and Bluetooth host interfaces
5.1 SDIO interface
The SDIO interface has the following characteristics:
•SDIO v3.0 is backward compatible with SDIO v2.0 HOST. SDIO 3.0 is recommended
for maximum throughput.
•For SDIO clock running at 25 MHz (SDR12) and 50 MHz (SDR25), VIO_SD must be
3.3V.
For SDIO clock running at > 50 MHz (SDR50 and DDR50), VIO_SD must be 1.8V.
•SDIO clock (SD_CLK) supports up to 208 MHz clock speed
•The required pull up for SDIO interface on SD_CMD, and SD_D[3:0] signals should be
provided by the host. The pull up value is between 10 kΩ to 100 kΩ according to SDIO
v3.0 specifications.
•Series damping resistors may be needed to help with signal integrity issues. When
extending the SDIO signals through ribbon cable, series resistors of 75 Ω are
recommended to reduce the undershoot/overshoot due to long trace run and cable
impedance mismatch.
Figure 11 shows the SDIO interface connection to the host processor.
Figure 11. SDIO interface connection to host processor
AN13125 All information provided in this document is subject to legal disclaimers. © NXP B.V. 2021. All rights reserved.
Application note Rev. 1 — 26 May 2021
13 / 33

NXP Semiconductors AN13125
IW416 Design Guide
PCB layout guidelines for SDIO interface
Refer to the following PCB layout guidelines for SDIO interface:
•SDIO signals are routed with 50(±10%) ohm impedance
•Route the SDIO signals as far away as possible from the RF trace
•Route all SDIO signal lines entirely over a solid ground plane. Avoid splits and voids on
an adjacent layer.
•Keep the same length for all SDIO signal traces and as short as possible.
•Place the ground plane along with SDIO signals with stitch vias as shown in Figure 12.
Figure 12. Place ground between SDIO signals with ground stitch vias
•Avoid routing power supply traces under or above SDIO signal traces. If SDIO signal
traces are routed on one of the inner layers, then make sure to shield them by having
solid ground above and below SDIO traces.
•The bend trace routing should be smooth with a large radius rather than of 90 degree
with a sharp edge, as shown in Figure 13.
Figure 13. Bend trace routing
AN13125 All information provided in this document is subject to legal disclaimers. © NXP B.V. 2021. All rights reserved.
Application note Rev. 1 — 26 May 2021
14 / 33

NXP Semiconductors AN13125
IW416 Design Guide
5.2 UART interface
Figure 14 shows a typical application circuit for the UART interface.
Figure 14. UART host interface connections
AN13125 All information provided in this document is subject to legal disclaimers. © NXP B.V. 2021. All rights reserved.
Application note Rev. 1 — 26 May 2021
15 / 33

NXP Semiconductors AN13125
IW416 Design Guide
6 RF interface
The NXP reference designs for the Wireless SoC show the front-end configurations
currently supported by NXP. It is recommended to discuss your desired front-end
configuration with your NXP representative and have your design reviewed by NXP.
6.1 RF front-end for QFN package
The QFN package can be used in single and dual antenna applications. In a dual
antenna application, one antenna is for Wi-Fi and the other antenna is for Bluetooth. In a
single antenna application, the antenna is shared between Wi-Fi and Bluetooth.
Figure 15 shows the typical front-end topology for a two-antenna application. Use
discrete low pass filters (LPF) to ensure the rejection of out-of-band emissions. LPF
components also act as impedance matching circuits between the wireless SoC pin
and the diplexer part on the PCB. For maximum power transfer in RF, the input/output
impedance needs to match 50 Ω.
Figure 15. RF front-end for two antenna application
AN13125 All information provided in this document is subject to legal disclaimers. © NXP B.V. 2021. All rights reserved.
Application note Rev. 1 — 26 May 2021
16 / 33

NXP Semiconductors AN13125
IW416 Design Guide
Figure 16 shows the filter circuit for Wi-Fi 2.4 GHz path.
Figure 16. Discrete LPF on Wi-Fi 2.4GHz RF path
Figure 17 shows the filter circuit for Bluetooth path.
Figure 17. Discrete LPF on Bluetooth RF path
For two antenna applications and where simultaneous 2.4 GHz Wi-Fi and Bluetooth
transmission is possible, note the following recommendations:
•To reduce the impact of mutual interference, provide at least 30 dB isolation between
the two antennas
•Keep the antenna gain to a minimum, outside the 2.4 and 5 GHz bands
•In applications where the antenna isolation is limited, the transmit power level for the
Bluetooth radio may need to be reduced. The transmit power level depends on various
system design factors such as antenna gain and isolation.
AN13125 All information provided in this document is subject to legal disclaimers. © NXP B.V. 2021. All rights reserved.
Application note Rev. 1 — 26 May 2021
17 / 33

NXP Semiconductors AN13125
IW416 Design Guide
Figure 18 shows the typical front-end topology for a single-antenna application. An
external SPDT switch is required to combine the 2.4 GHz Wi-Fi and Bluetooth transmit/
receive paths. Use discrete low pass filters (LPF) to ensure the rejection of out-of-band
emissions. LPF components also act as impedance matching circuits between the
wireless SoC pin and the diplexer part on the PCB. For maximum power transfer in RF,
the input/output impedance needs to match 50 Ω. Refer to Figure 16 for the filter circuit
on Wi-Fi 2.4 GHz path.
Figure 18. RF Front-end for single antenna application
Table 5 lists the recommended RF front-end components.
RF component Manufacturer Part number
Diplexer TDK DPX166000DT-8093A1
SPDT switch SKYWORKS SKY13323-378LF
Discrete LPF on Wi-Fi 2.4 GHz path — L = 2.1 nH ± 0.1 nH (0201), C = 0.6 pF (0201)
Discrete LPF on Bluetooth path — C= 1.6 pF (0201), L = 3.3 nH ± 0.1 nH (0201), C
= 1.6 pF (0201)
Table 5. Recommended RF front-end components
AN13125 All information provided in this document is subject to legal disclaimers. © NXP B.V. 2021. All rights reserved.
Application note Rev. 1 — 26 May 2021
18 / 33

NXP Semiconductors AN13125
IW416 Design Guide
6.2 RF front-end for WLCSP package
Similar to QFN package, WLCSP package can also be configured as single or dual
antenna front-end application. WLCSP package requires an external RF SPDT switch on
5 GHz Wi-Fi path to provide additional rejection to out-of-band emissions. The following
RF front-end components must be used to reduce out-of-band emissions.
•RF SPDT switch on Wi-Fi 5 GHz path
•Bandpass-bandpass structure diplexer
Figure 19 shows a typical front-end topology for dual antenna applications.
Figure 19. RF front-end with dual antenna applications
Use discrete low pass filters (LPF) to ensure the rejection of out-of-band emissions. LPF
components also act as impedance matching circuits between the wireless SoC pin
and the diplexer part on the PCB. For maximum power transfer in RF, the input/output
impedance needs to match 50 Ω. Refer to Figure 16 for filter circuit on Wi-Fi 2.4 GHz path
and Figure 17 for the filter circuit on Bluetooth path.
AN13125 All information provided in this document is subject to legal disclaimers. © NXP B.V. 2021. All rights reserved.
Application note Rev. 1 — 26 May 2021
19 / 33

NXP Semiconductors AN13125
IW416 Design Guide
Figure 20 shows the circuit diagram for SPDT switch on Wi-Fi 5 GHz path.
Figure 20. Circuit diagram for SPDT switch on Wi-Fi 5 GHz path
Table 6 shows the list of recommended RF front-end components.
RF component Manufacturer Part number
Diplexer TDK DPX166000DT-8193A1
SPDT switch SKYWORKS SKY13323-378LF
Discrete LPF on Wi-Fi 2.4 GHz path — L = 2.1 nH ± 0.1 nH (0201), C = 0.6 pF (0201)
Discrete LPF on Bluetooth path — C= 1.6 pF (0201), L = 3.3 nH ± 0.1 nH (0201), C
= 1.6 pF (0201)
Table 6. Recommended RF front-end components
AN13125 All information provided in this document is subject to legal disclaimers. © NXP B.V. 2021. All rights reserved.
Application note Rev. 1 — 26 May 2021
20 / 33
Table of contents
Other NXP Semiconductors Power Supply manuals
Popular Power Supply manuals by other brands

Redarc
Redarc DPS1225 manual
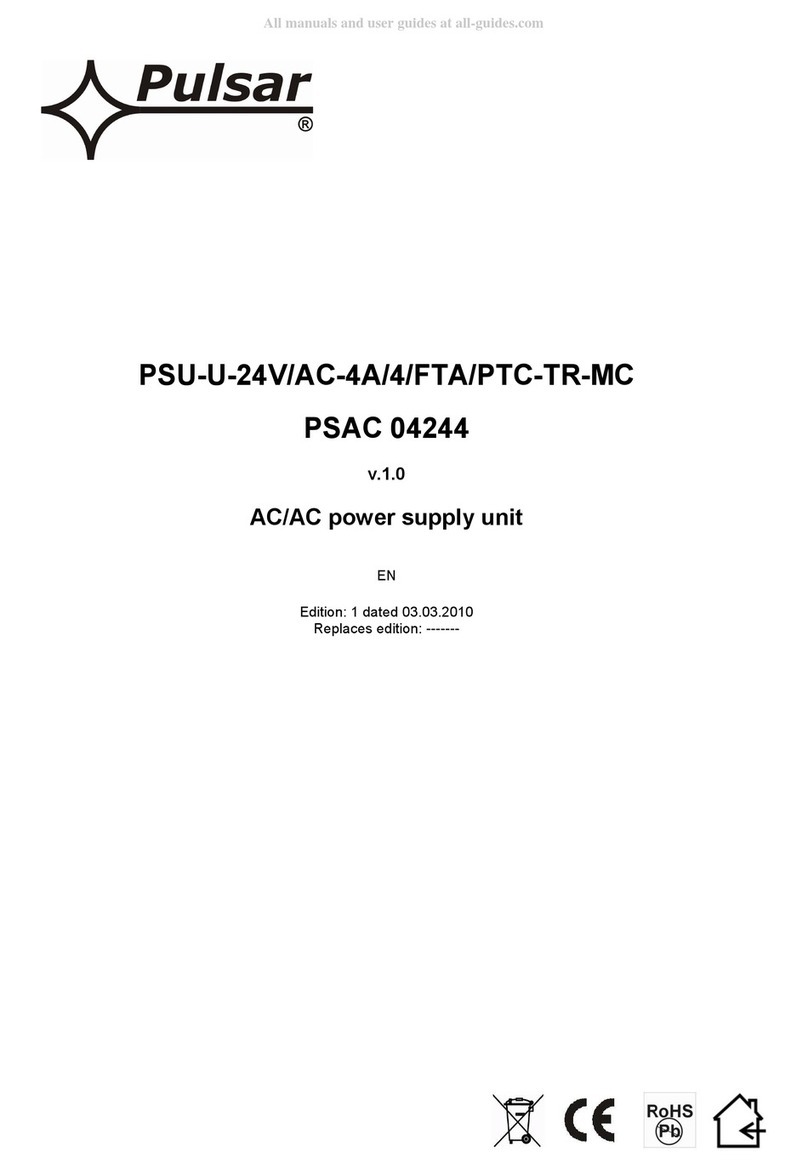
Pulsar
Pulsar PSU-U-24V/AC-4A/4/FTA/PTC-TR-MC manual
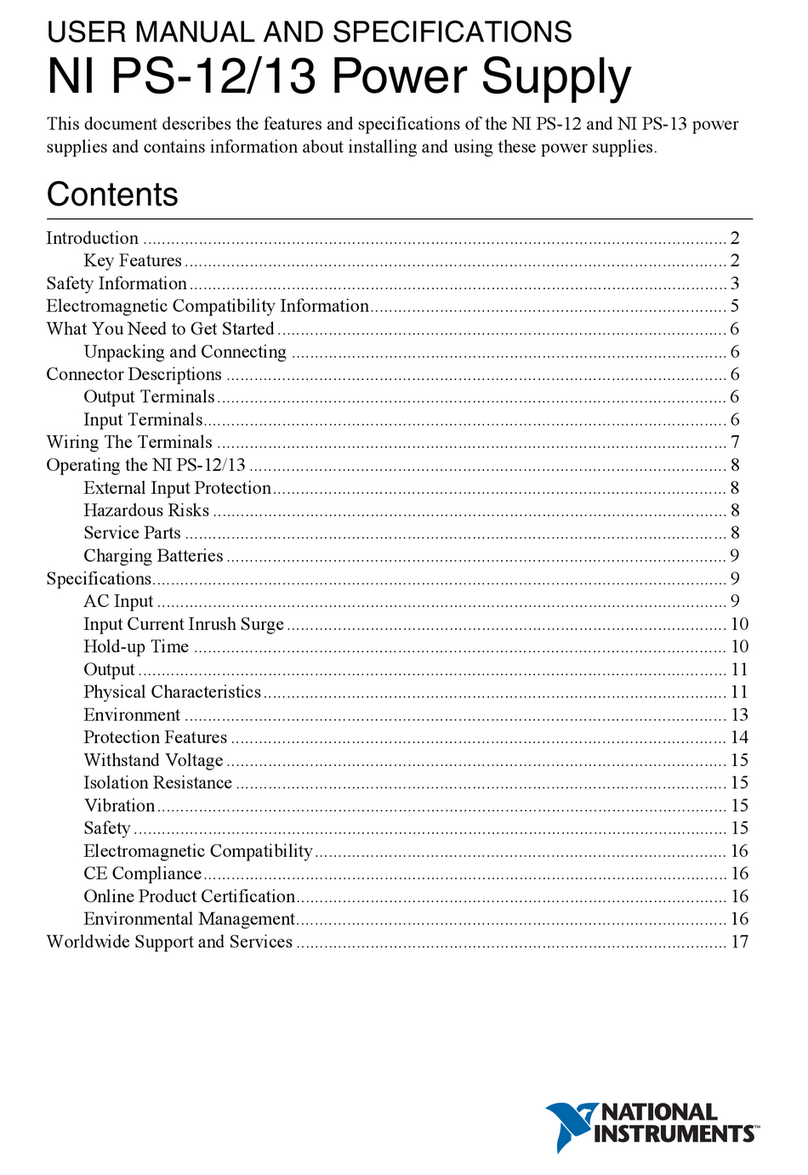
National Instruments
National Instruments NI PS-13 User manual and specifications
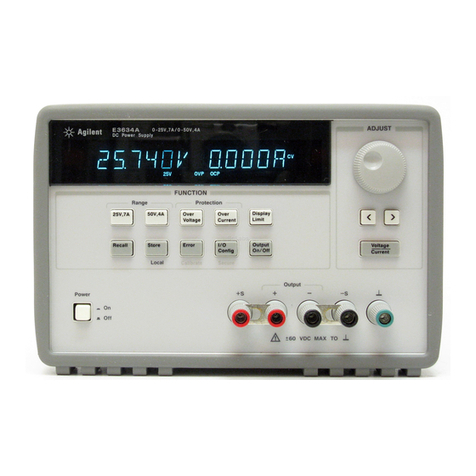
HP
HP E3633A user guide
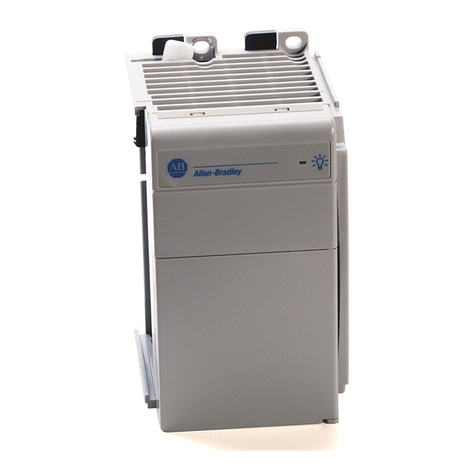
Allen-Bradley
Allen-Bradley 1769-PA2K installation instructions

Rockwell Automation
Rockwell Automation Allen-Bradley 1606-XLE240EDRZ SER B installation instructions