OMEGA AIR B-DRY Series User manual

Installation and operating
manual
Please read the following instructions carefully before installing the product. Trouble free
and safe operating of the product can only be guaranteed if recommendations and
conditions stated in this manual are respected.
B-DRY adsorption dryer series

2

Index
1 GENERAL INFORMATION ............................................................................................................................... 5
1.1
D
EVICE
I
NFORMATION
........................................................................................................................................ 5
1.2
S
UPPLIER
I
NFORMATION
..................................................................................................................................... 5
1.
B
ASICS
............................................................................................................................................................ 5
1.4
A
DSORPTION
D
RYERS
......................................................................................................................................... 6
1.5
A
DSORPTION
.................................................................................................................................................... 6
1.6
A
PPROPRIATE
U
SE
............................................................................................................................................. 6
2 SAFETY INSTRUCTIONS .................................................................................................................................. 7
3 TECHNICAL DATA ......................................................................................................................................... 10
.1
C
OMPONENTS
................................................................................................................................................. 10
.2
S
PECIFICATIONS
............................................................................................................................................... 11
4 DESCRIPTION OF OPERATION ...................................................................................................................... 14
5 CONTROLLER ............................................................................................................................................... 1
5.1
S
TATUS
S
CREEN
............................................................................................................................................... 17
5.2
D
EW
-
POINT
M
ONITORING
................................................................................................................................ 18
5.
T
IMES
........................................................................................................................................................... 19
5.4
D
RAIN
........................................................................................................................................................... 20
5.5
M
ANUAL
S
ELECTION OF
F
IXED
C
YCLE
.................................................................................................................. 21
5.6
LCD
D
IAGRAM
................................................................................................................................................ 22
5.7
S
TAND
-
BY
...................................................................................................................................................... 2
5.7.1 LCD Diagram for Stand-by Feature ..................................................................................................... 24
5.8
P
ARAMETER
S
ETTINGS
...................................................................................................................................... 25
5.8.1 LCD Diagram of Parameter settings ................................................................................................... 27
5.9
U
PDATING AND
R
EPROGRAMMING
..................................................................................................................... 28
5.10
E
LECTRICAL
S
CHEME
&
S
ENSOR
C
ONNECTION
..................................................................................................... 1
5.11
D
ATA
L
OGGING
.............................................................................................................................................
5.12
R
EMOTE
A
CCESS
........................................................................................................................................... 4
EFFICIENCY CONSIDERATIONS ..................................................................................................................... 38
7 TRANSPORTATION ...................................................................................................................................... 39
8 STORAGE ..................................................................................................................................................... 40
9 INSTALLATION ............................................................................................................................................. 41
9.1
G
ENERAL
I
NSTALLATION
R
EQUIREMENTS
.............................................................................................................. 41
9.2
I
NSTALLATION
L
AYOUT
...................................................................................................................................... 42
9.
I
NSTALLATION
P
ROCEDURE
................................................................................................................................ 44
10 COMMISSIONING ...................................................................................................................................... 45
10.1
P
RESSURIZATION
........................................................................................................................................... 45
10.2
O
PENING
O
UTLET
V
ALVE
................................................................................................................................ 46
10.
S
TART
-
UP
.................................................................................................................................................... 46
11. DECOMMISSION ....................................................................................................................................... 47
12 MAINTENANCE .......................................................................................................................................... 48
12.1
D
RYER
O
PERATION
I
NSPECTION
................................................................................................................... 50
12.2
C
OMPLETE
D
RYER
I
NSPECTION
.................................................................................................................... 50
12.
F
ILTER
E
LEMENTS
R
EPLACEMENT
................................................................................................................. 50
12.4
E
XPANSION
S
ILENCERS
R
EPLACEMENT
.......................................................................................................... 50
12.5
C
ONTROL
V
ALVE
R
EPLACEMENT
(L
OWER
B
LOCK
) ................................................................................................ 51

4
12.6
C
HECK
V
ALVE
R
EPLACEMENT
(U
PPER
B
LOCK
) ................................................................................................ 52
12.7
A
DSORBENT
R
EPLACEMENT
........................................................................................................................ 5
12.8
D
EW
-
POINT
S
ENSOR
C
ALIBRATION
.................................................................................................................... 54
13 TROUBLESHOOTING .................................................................................................................................. 55
1 .1
C
ONTROLLER
T
URNS
OFF ............................................................................................................................... 55
1 .2
H
IGH
P
RESSURE
D
ROP
.................................................................................................................................... 55
13.2.1 nadequately Dimensioned Compressor and Dryer .......................................................................... 55
13.2.2 The Downstream System is Oversized .............................................................................................. 56
13.2.3 Oil in the Adsorption Dryer ............................................................................................................... 56
13.2.4 Dryer Connected to the System in the Opposite Way ....................................................................... 56
13.2.5 Control Valves Malfunction .............................................................................................................. 57
13.2.6 Clogged Pre-filter and/or After-filter ................................................................................................ 57
13.2.7 ncreased Purge Flow ........................................................................................................................ 57
1 .
H
IGH
O
UTLET
D
EW
-
POINT
.............................................................................................................................. 58
13.3.1 Underdiemnsioned Adsorption Dryer .............................................................................................. 58
13.3.2 Liquid Water in the Towers ............................................................................................................... 58
13.3.3 Oil in the Towers ............................................................................................................................... 59
13.3.4 Tower Fails to Depressurise .............................................................................................................. 59
1 .4
P
IPING
L
EAK
................................................................................................................................................. 60
14 WARRANTY EXCLUSION ............................................................................................................................. 0
15 MAINTENANCE RECORD ............................................................................................................................ 1

5
1 General Information
1.1 Device Information
Please fill in the fields accordingly. Correct information enables proper and efficient
maintenance of the device, selection of spare parts and technical support.
1.2 Supplier Information
1.3 Basics
Compressed air contains contaminants such as water, oil and particulates which must be
removed or reduced to the acceptable level based on specific application requirements.
Standard ISO857 -1 specifies air purity/quality classes for these contaminants. Humidity
(water vapor content) is expressed in the terms of Pressure Dew Point (PDP) where Dew point
is the temperature at which air is 100% saturated with moisture. When the temperature of
the air reduces to or below the dew point, condensation will occur. Reduction of water
content down to pressure dew point + °C is usually achieved with refrigerant dryers while for
lower pressure dew points adsorption (also called desiccant) dryers are typically used.
Adsorption dryer model:
Serial number:
Year of production:
Commissioning date:
Type of towers:
Left tower serial number:
Right tower serial number:
Name:
Address:
Telephone/Fax:
e-mail:

6
1.4 Adsorption Dryers
Typical applications for the adsorption dryers are outdoor installations where the risk of
freezing occurs and applications with high quality requirements in terms of air dryness (PDP <
+ °C) such as the process air in process industry (food and beverage, pharmaceutical,
electronic, chemical, …).
The most common adsorption dryers are heatless regeneration adsorption dryers due to their
simplicity reliability and relatively low investment costs.
1.5 Adsorption
Adsorption is a process where specific molecules adhere to the surface of a highly porous solid
(adsorbent/desiccant) by electrostatic and molecular forces. The adsorbent is normally
formed in sphere form beads. Process of adsorption takes place while air flows through
column filled with the beads. Rate of adsorption depends on several factors (type of
adsorbent, relative humidity, inlet temperature, contact time, face velocity) and therefore
adsorption process is usually set/optimized for every individual application.
1.6 Appropriate Use
B-DRY series desiccant dryers are intended for highly efficient drying of compressed
air. This appliance must be used only for the purpose for which it was specifically
designed. All other uses are to be considered incorrect.
Specifically:
•Desiccant dryer can only be used for “GROUP 2” fluids (PED 2014/68/EU).
•Desiccant dryer can not be used for explosive, toxic, flammable, corrosive and “GROUP
1” fluids (PED 2014/68/EU).
Warning: internal corrosion can seriously reduce the safety of installation: check it during
maintenance.
The manufacturer will under no circumstances be responsible for any damage resulting from
improper, incorrect or unreasonable use.
Use genuine spare parts only. Any damage or malfunction caused by the use of non-genuine
parts is not covered by Warranty or Product Liability.

7
2 Safety Instructions
Improper handling of compressed air systems/equipment and electric installations
/ equipment may result in serious injury or death
Improper handling (transportation, installation, use/operation, maintenance) of B-
DRY series dryer may result in serious injury or death. As a result of improper
handling damage or reduced performance can occur.
The relevant safety at work and accident prevention regulations, plus operating
instructions, shall apply for operating the adsorption dryer. The adsorption dryer
has been designed in accordance with the generally recognized rules of
engineering. It complies with the requirements of directive 2014/68/EU concerning
pressure equipment.
Ensure that installation complies with local laws for operation and routine testing
of pressure equipment at the place of installation.
Operator/user of the adsorption dryer should make himself familiar with the
function, installation and start-up of the unit.
All the safety information is always intended to ensure your personal safety. If you are not
experienced in such systems please contact your local representative or manufacturer of the
dryer for help.

8
•Before any kind of work on the dryer make sure that it is depressurized (additional to
dryer this also refers to nearest upstream and downstream part of installation) and
disconnected from power supply.
•Do not exceed maximum operating pressure or operating temperature range (see
dryer and vessel type plate; Picture 1).
•The permissible working temperatures and pressures for the adsorption dryer add-on
parts are given under Technical data for those add-ons. Maximum temperature and
pressure for assembled system is the lowest of any individual part.
•It is necessary to ensure that the adsorption dryer is equipped with the corresponding
safety and test devices to prevent the permissible operating parameters from being
exceeded.
•Ensure that the adsorption dryer is not subject to vibrations that could cause fatigue
fractures.
•Adsorption dryer is not to be subjected to mechanical stresses.
•The medium used may not have any corrosive components that could attack the
materials of the adsorption dryer in a way that is not permitted. Do not use the
adsorption dryer in hazardous areas with potentially explosive atmospheres.
•All installation and maintenance work on the adsorption dryer may only be carried out
by trained and experienced specialists.
•It is forbidden to carry out any kind of work on the adsorption dryer, including welding
and constructional changes, etc.
•Depressurize the system before carrying out the installation work.
•Wear respiratory protective equipment when working with the molecular sieve.
Molecular sieve is a crumbling material that is producing fine dust which can cause
respiratory complications if inhaled in sufficient quantities.
•Ensure that the molecular sieve does not come into contact with the liquid water.
Unused molecular sieve in liquid water produces thermal energy that can cause the
water to boil and can inflict serious burns.
•At manipulation with adsorbent some amount of adsorbent can stay on the floor. In
case of adsorbent on the floor be extremely careful and immediately clean the floor to
prevent injuries due to fall on slippery surface.
•Ensure that adsorption dryer is installed as specified and without any stresses.
•Use original spare parts only.

9
•Use the device for the intended purpose only.
•Centre of gravity is positioned relatively high meaning there is a risk of tilting the dryer,
which can cause serious injury or even death.
•For transportation please check and follow local regulations for lifting and transporting
heavy objects.
•Note that dryer can only be lifted using lifting lugs on the top of each vessel or with
forklift in case if it is firmly positioned on an appropriately sized pallet.
•Do not climb on the dryer.
•Do not use water to extinguish fire on the dryer or surrounding objects.
•Wear proper personal safety equipment (earplugs, earmuffs, safety goggles, safety
helmet, safety gloves, safety shoes…).
Picture 1: Location of vessel typeplate and dryer typeplate
Vessel typeplate
Dryer typeplate

10
3 Technical Data
3.1 omponents
Picture 2: Components
Note: The adsorption dryer displayed on the pictures of this manual is B-DRY 1000 (left=front
view, right=rear view)
1. Vessel 1 (filled with adsorbent)
2. Vessel 2 (filled with adsorbent)
. Lower valve block
4. Upper valve block
5. Controller
6. Inlet filter
7. Outlet filter
8. Adsorbent discharge connection
9. Strainer
10. Expansion silencer
11. Solenoid valve
12. Purge line
1 . Manometer
14. Dew point sensor (optional)
1 2
8
10
11
5
1 4
12
6
7
8
9
14

11
3.2 Specifications
SIZES
Model Conn.
IN &
OUT
(5)
Inlet flow
[Nm
/h]
( )
Outlet
flow
[Nm
3
/h]
(4)
A
[mm]
B
[mm]
C
[mm]
Mass
[kg]
Volum
e
[l]
Transient
pressure
Δp [bar]
Allowabl
e stress
reversals
B-DRY 110 G /4” 110 86,0 719 422 1657 140 20 1 10
6
B-DRY 150 G 1” 150 117,5 707 422 1897 156 25 1 10
6
B-DRY 200 G 1” 200 157,0 707 471 1664 196 6 1 10
6
B-DRY 250 G 1” 260 204,0 707 471 1914 2 6 45 1 10
6
B-DRY 00 G 1” 20 251,0 860 5 5 1742 274 57 1 10
6
B-DRY 400 G 1 ½” 410 21,5 854 5 5 1989 295 70 1 10
6
B-DRY 600 G 1 ½” 590 462,5 854 671 2051 92 102 1 10
6
B-DRY 800 G 2” 770 60 ,5 1059 701 2080 507 1 4 1 10
6
B-DRY 1000 G 2” 1000 784,0 1052 701 2140 597 164 1 10
6
( )
Refers to 1bar(a) and 20°C at 7 bar operating pressure , inlet temperature 5°C and pressure dew point at
outlet -40°C
(4)
Outlet flow refers to typical assumption during regeneration phase for operating at nominal inlet flow
conditions. Outlet flow includes average air losses of approximately 17, %.
(5)
Refers to inlet and outlet filter housing.

12
TECHNICAL PARAMETERS
Operating pressure 4 – 16 bar
Operating temperature 1,5°C to 60°C
Pressure dew points -40°C (-25, -70)
Voltage, Frequency 2 0V, 50/60Hz
Power consumption <60W
Protection class (controller) IP 65
Noise level (at 1m distance) Normally up to 100dB(A)
Filter (inlet)* Super fine coalescing; residual oil cont. <0,01mg/m ;
0,01µm
Filter (outlet) Dust filter; 1µm
Input for stand-by STANDARD
Dew point dependent control OPTIONAL
*If dryer is supplied without inlet filter compressed air class 1 (ISO 875 -1) for solid particles and oil should be
provided to the inlet of the dryer.
DRYER RATING ACCORDING TO ISO8573-1
Solid particles
(1)
Water
(1),(2)
Oil
(1)
2 1- 1
(1)
Typical result based on standard configuration and nominal operating conditions
(2)
Depending on the specific design, class 2 when operated at nominal operating conditions.
MATERIALS
Columns, construction, support Steel
Column inner protection /
Column and construction outer protection Epoxy painted
Desiccant support screen (strainer) Stainless steel
Valves Brass, aluminium
Sealings NBR
Fittings, Screws, plugs INOX, brass, steel (zinc plated)
Lubricant Shell cassida grease RLS 2
Outside protection Powder paint coated (Epoxy-polyester base)
Desiccant 80% Molecular sieve 4A, 20% Silica gel
PRESSURE EQUIPMENT DIRECTIVE
PED 2014/ 8/EU (Fluid group 2)
B-DRY 110 to B-DRY 00 ategory 2, Module H
B-DRY 400 to B-DRY 1000 Category , Module H

1
CORRECTION FACTORS
To calculate the correct capacity of a given filter based on actual operating conditions, multiply the nominal
flow capacity by the appropriate correction factor(s).
CORRECTED CAPACITY = NOMINAL FLOW CAPACITY x C
OP
x C
OT
x C
D
OPERATING PRESSURE
[bar] 2 4 5 6 7 8 9 10 11 12 1 14 15 16
[psi] 29 44 58 72 87 100 115 1 0 145 160 174 189 20 218 2 2
C
OP
0, 8 0,5 0,6 0,75 0,88 1 1,1 1,25 1, 8 1,50 1,6 1,75 1,88 2,00 2,1
OPERATING TEMPERATURE DEW POINT
[°C] 25 0 5 40 45 50 55 60 [°C] -25 -40 -70
[F] 77 86 95 104 11 122 1 1 140 [F] -1 -40 94
C
OT
1 1 1 0,97 0,87 0,80 0,64 0,51 C
D
1,1 1 0,7
Technical datasheet is available. For additional technical specification contact the
manufacturer.

14
4 Description of Operation
Adsorption dryer is intended for removal of water vapor from the inlet compressed air in order
to reach a desired dew point at the outlet.
During normal operation of the adsorption dryer the non-dried compressed air enters the
adsorption dryer through the inlet and passes through the appropriate inlet control valve into
a tower (pressure vessel filled with adsorbent) where the process of adsorption is in progress.
In the tower the air passes the molecular sieve which removes the water vapor content
through the process of adsorption. After leaving the tower the dried compressed air leaves
the adsorption dryer through the outlet.
If a process of regeneration is underway in the second tower then part of the dried air is lead
through a nozzle into the tower where the regeneration is in progress. There the air that has
been dried and heated through the process of adsorption expands after leaving the nozzle and
passes the molecular sieve. Through the process of desorption the water vapor content gets
released from the molecular sieve and is carried by the air through the appropriate release
control valve after which it is discharged from the system.
After a set time (in case of dew point dependent control adsorption time can be up to 2 hours)
the adsorption in the first tower is stopped and the control valves are run through a sequence
that pressurizes both towers and starts the adsorption in second tower and regeneration in
the first tower.
Time of regeneration is constant and does not change. The dried air used for regeneration is
released which means that while the regeneration is in progress the adsorption dryer operates
at a lower efficiency. In most operating conditions the adsorption process can run for a longer
time than the time that is needed to regenerate the tower. Consequently although times of
regeneration and adsorption can be equal, in most operating conditions it is more economical
that the adsorption time is longer since such operation can greatly increase the efficiency of
the adsorption dryer.
B-DRY adsorption dryers can operate in fixed cycle mode or in energy saving dew point
dependent cycle mode. In fixed cycle mode length of cycle is normally 10min. In dew point
dependent cycle mode length of cycle is automatically adjusted and can be up to 2 hours.
If the compressed air station shuts down, a stand-by signal is received or the adsorption dryer
gets disconnected from the power supply both adsorption dryer inlet control valves open
while both release control valves are closed so the air can flow from inlet through the towers
to the outlet. After the start signal is received or power returns the adsorption dryer continues
where it has stopped.
* For more information contact your supplier.

15

16
5 Controller
The B-DRY adsorption dryer series controller in combination with tower pressure manometers
and the outlet dew-point sensor enables complete monitoring of the adsorption dryer
operation. The controller PLC includes a LCD display interface with buttons that enables the
technical expert to examine/change settings and operating parameters of the system.
Typically information such as operating mode and pressure dew point are displayed on the
main screen. Additionally the controller has a stand-by input, electronic drain control output
and alarm/warning output. Press ↓ and ↑ to move through the menu screens. Use OK to
confirm or ESC to go back.
Picture of the controller and controller housing

17
5.1 Status Screen
To access the controller interface open the transparent cover on the controller housing. The
interface on the PLC block has four buttons and can display the information in four lines. To
move through the menu, press the up and down buttons. To enter a sub-menu or confirm an
action press right. To go back press left.
The first screen shows the system status. At the start-up of the dryer the controller is
initializing. This phase lasts a few seconds.
I N I T I A L I S I N G
When the B-DRY adsorption dryer is in the FIXED CYCLE MODE it is operating with fixed
adsorption-regeneration cycles.
When the B-DRY adsorption dryer is in the PDP VARIABLE CYCLE SAVING MODE it is operating
in a dew-point dependent energy saving mode with variable adsorption-regeneration cycles.
When the B-DRY adsorption dryer is in the STAND-BY mode the adsorption-regeneration
cycles are stopped for as long as there is a STAND-BY signal on INPUT I1 (→for more
information see chapter 5. ).
A
D
S
R
E
G
F
I
X
E
D
M
O
D
E
0
0
: 0
0 h
A
D
S R
E
G
V
A
R
I A
B
L E
M
O
D
E
0
0 : 0
0
h

18
5.2 Dew-point Monitoring
If the dew-point sensor is connected it is possible to monitor the current dew-point. The outlet
dew-point sensor is connected to the PLC controller analogue INPUT I7/A1 (0…10VDC, -
100…+20°C) and enables the PLC to adjust the adsorption time of the adsorption-regulation
cycle in order to reach a set dew-point. The adsorption time is adjusted in such a way that the
desired dew-point is reached with a maximum possible adsorption time. A high adsorption to
regeneration time ratio means that a smaller percentage of dried air has been used for
regeneration resulting in higher efficiency of adsorption dryer system operation.
It is possible to check the current outlet dew-point measurement on the PLC controller display
by moving through the menus to the DEW-POINT SENSOR screen. When in STATUS SCREEN
press ↓ to proceed to the DEW-POINT SENSOR screen. If the sensor is connected then the set
and current dew-point will be displayed. The third line of the screen shows the set dew-point.
The fifth line of the screen shows the current measured dew-point.
Example of DEW-PO NT SCREEN
In case of dew-point sensor malfunction, the dew-point rising above the set alarm dew-point
or if the dew-point sensor has been unplugged the DEW-POINT SENSOR OFF status will be
displayed on the DEW-POINT SENSOR screen and alarm/warning output OUTPUT Q (Q2 on
the input/output module) will be set to OFF (logical 0).
The alarm dew-point can be set in the SETTINGS menu. →See 5.8 Parameters Settings.
S T A N D - B Y
D E
W
- P
O
I N
T
S e
t P
D
P
:
- 4
0 °
C
t
d
M
e
a s
u
r e
d P
D
P
:
- 4
1 °
C
t
d
D
E
W
- P O
I
N
T
S E
N S
O
R O
F
F

19
5.3 Times
The CYCLE TIMES SCREEN shows the set adsorption, current adsorption, regulation and
current regeneration times. In the first line (ADS) represents the set adsorption time. The
second line (T) represents the current time of adsorption. The third line (REG) and the fourth
line (T) represent the set regeneration time and the current time of regeneration.
The WORKING HOURS AND CYCLES screen displays the total working hours of the adsorption
dryer and the total number of adsorption-regeneration cycles. One adsorption-regeneration
cycle consists of two adsorption-regeneration half-cycles.
A D S 5 m
T = 0 0 : 0 0 h
R E G 0 0 : 0 4 h
T = 0 0 : 0 0 h
W
O
R
K
H
O
U
R
S
0
C Y C
L E
S
1

20
5.4 Drain
The B-DRY adsorption dryer controller has an option to control the drain through the RELAY
OUTPUT Q5 (Q1 on the input/output module).
The DRAIN screen displays the drain activation interval time (Inter) and its duration (Durat).
Interval and duration times can be modified in the controller settings (→see 5.7 Parameter
Settings).
D
R
A
I N
( Q
5
) :
I n
t e
r 1
0 : 0
0
m
D
u
r a
t 0
1 : 0
0
s
This manual suits for next models
9
Table of contents
Other OMEGA AIR Dryer manuals
Popular Dryer manuals by other brands

Mediclinics
Mediclinics M04AB Installation and operating manual

Amica
Amica WTK 14312 W operating instructions
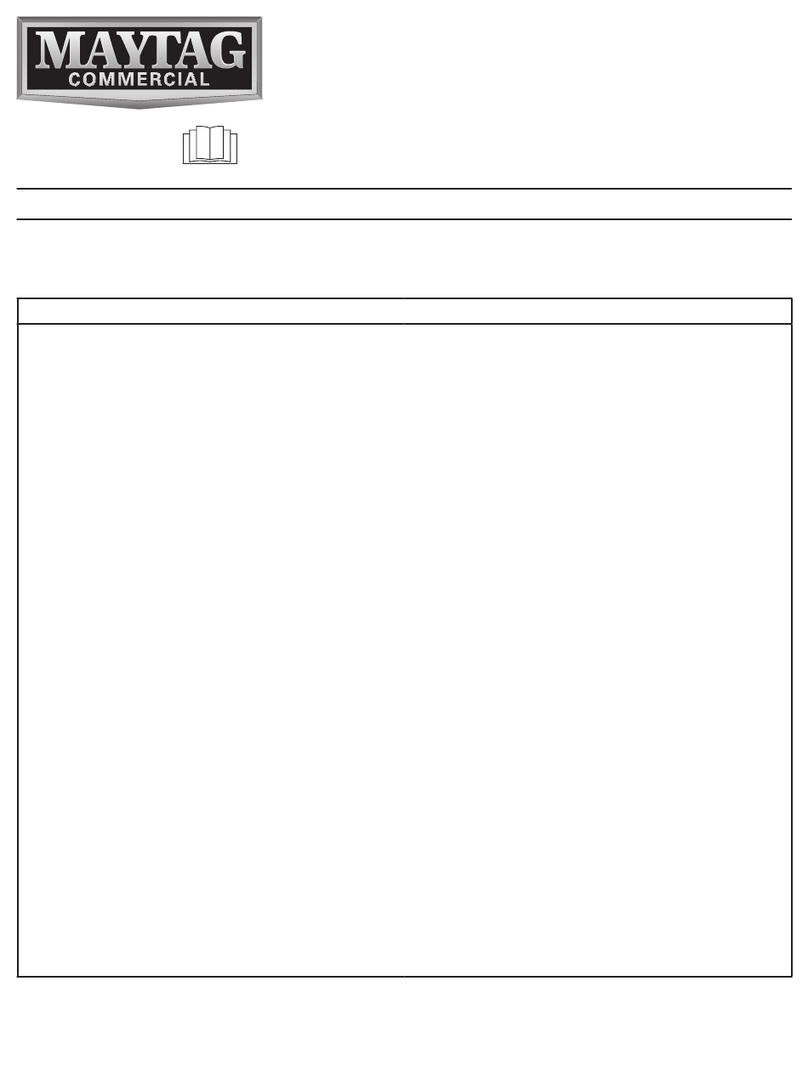
Maytag
Maytag MDE28PD User instructions
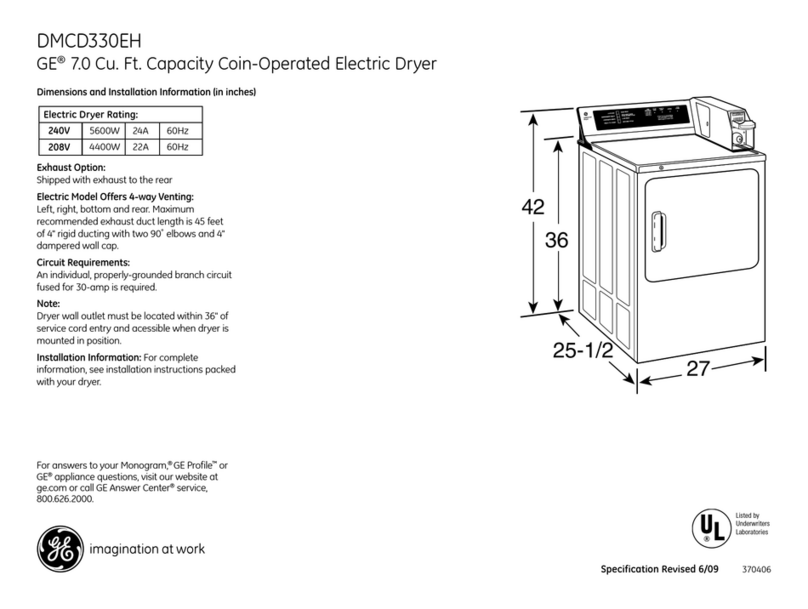
GE
GE DMCD330EH Dimensions and installation information

Nofer
Nofer THIN Instruction manual and installation guide
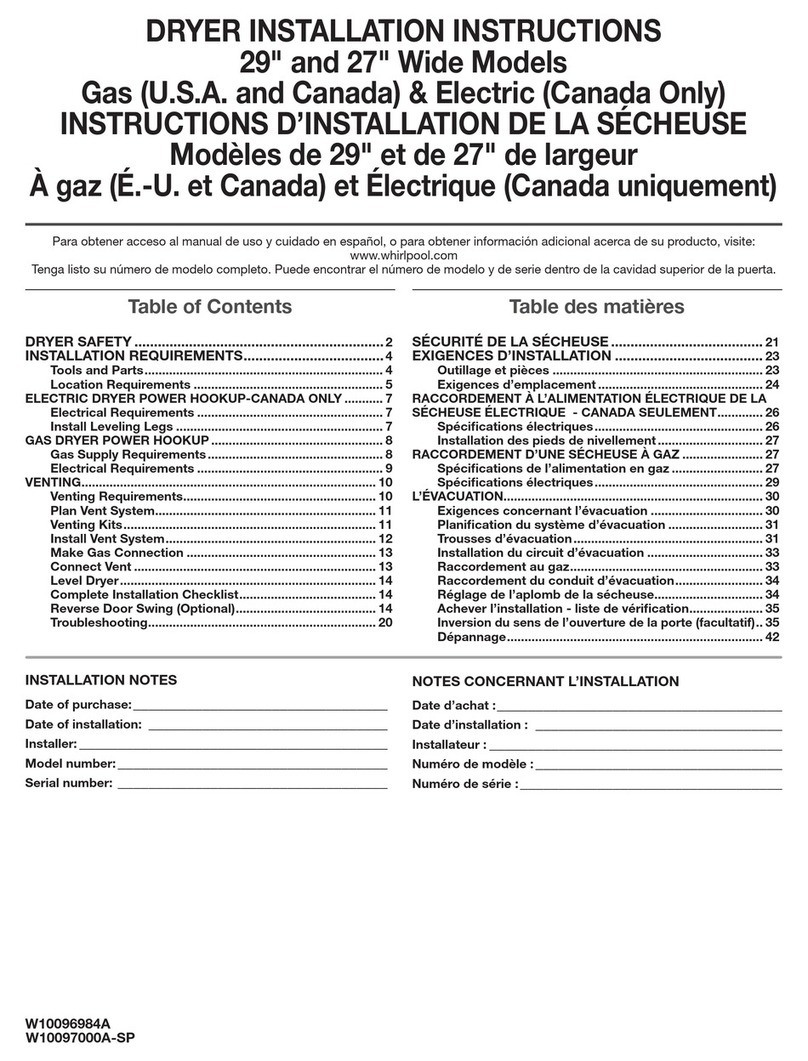
Whirlpool
Whirlpool W10096984A installation instructions

Bosch
Bosch WQG242AE User manual and installation instructions
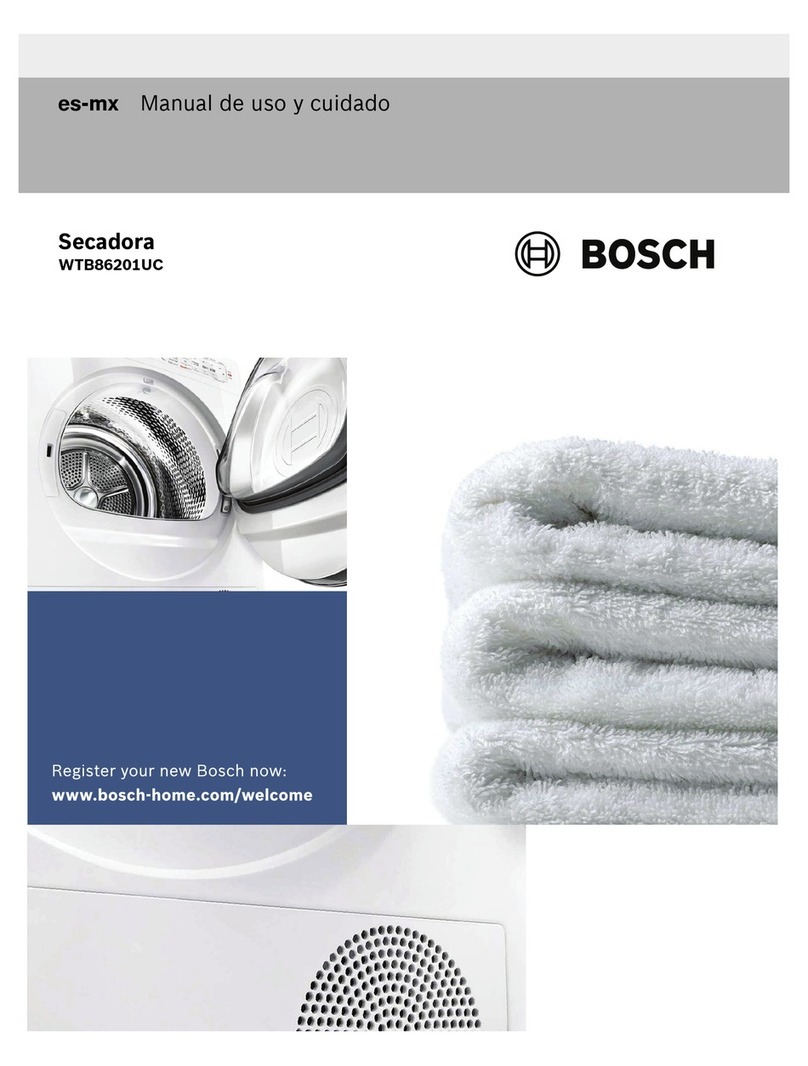
Bosch
Bosch WTB86201UC Instructions for use

Beko
Beko TR530 user manual
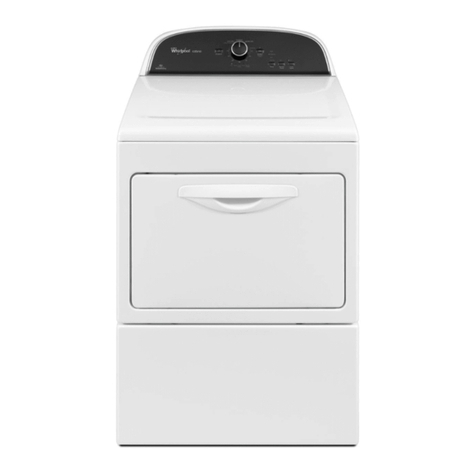
Whirlpool
Whirlpool WED5500BW Installation

Miele professional
Miele professional PT 8337 Operating and installation instructions
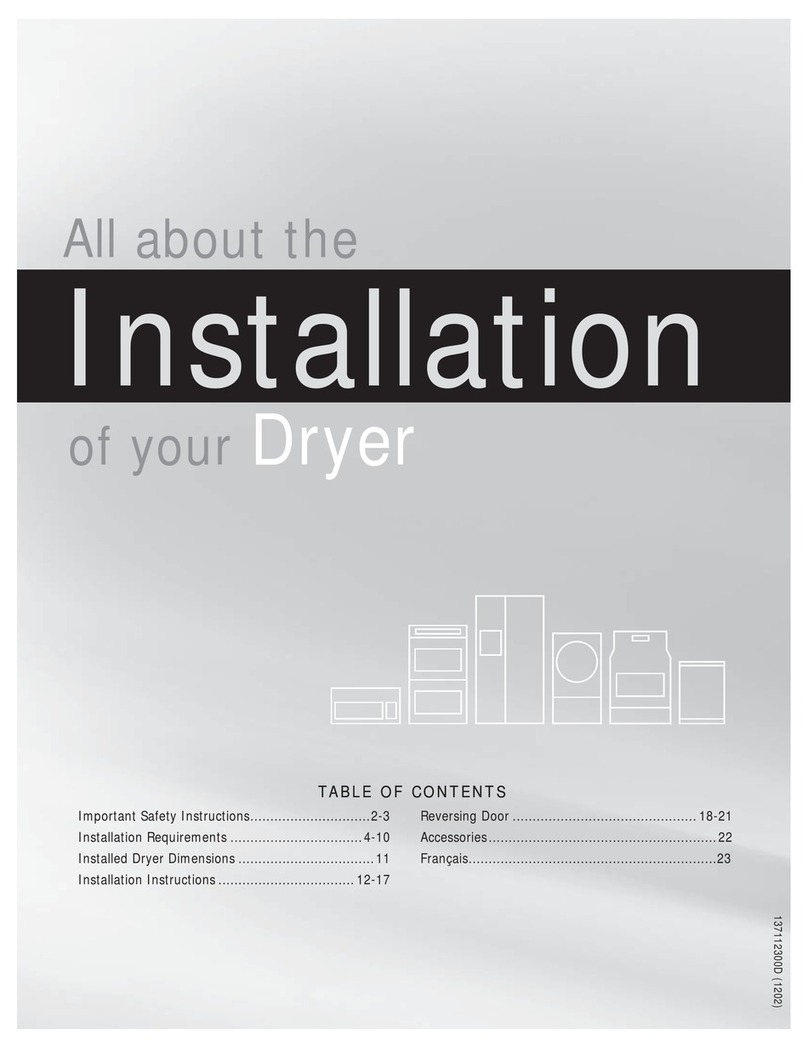
Frigidaire
Frigidaire 137112300B installation instructions