Orwak 3400 User manual

ORWAK 3400
March 2005
PUBL. NO
4869057-00
Edition 4
OPERATING MANUAL
GB

8
English
SAFETY
Read the operating instructions BEFORE operating the machine.
Our warranty/product responsibility requires that instructions are followed and
that original spare parts and recommended hydraulic oil and lubricants are used.
The user of the machine is responsible for the safety checks and for ensuring that
daily maintenance of the machine is carried out.
The user is responsible for ensuring that any faults are corrected and that neither the
user nor other individuals are exposed to danger.
The owner is responsible for ensuring that national and local laws are complied with
when using the machine.
This symbol means WARNING or DANGER - personal safety instruction!
This machine is designed for ONE MAN OPERATION.
Only the operator is allowed in the machine’s working area.
The machine must not be used if the safety functions (e.g. switches and pro-
tections) have been deactivated, damaged or removed.
Lost or damaged parts must be replaced with original spare parts.
The machine has a high centre of gravity. If the machine needs to be moved,
the press plate must be lowered fully before moving.
Installation, repair and service work may only be performed by qualified and
competent staff, and in accordance with the installation and service instructions.
The machine must not be used by minors.
Never climb on the machine.
SAFETY FEATURES
The machine is equipped with the following safety features:
Upper and lower door switches, which prevent compacting with the doors open.
Covers and protections conceal hydraulic lines and movable machine parts. When
the lower door is opened, the lower door pressure is relieved. Baling is performed
from the side of the machine to keep the operator away from the baling area. The
machine is also equipped with an emergency stop, as well as a main switch that can
be locked to prevent unauthorised use, for example during service and maintenance
or when removing any waste that has become trapped. For the same reason, the
upper door can also be locked with a padlock in the top right corner.
RANGE OF APPLICATION
The machine is a hydraulically operated baler intended for compacting bulky materi-
als such as cardboard, paper and plastic. The material being compacted must be
evenly distributed in the chamber. The machine may only be used in areas that have
a roof, protection against wind and normal lighting.
Materials that are flammable or of an explosive nature, such as pressurised
containers or equivalent which, when exposed to pressure or sparks, could
cause damage, fire or an explosion, must not be compacted in the machine.
Only use straps or string recommended by the machine manufacturer.
TABLE OF
CONTENTS
Safety ........................... 8
Operating instructions... 9
Technical specifications. 10
Dimensional drawing .... 10
Transport ...................... 10
Installation .................... 11
Weekly inspection
and maintenance.......... 12
CE................................. 13
2
3
4
4
4
5
6
7
2

12
34
56
7
89
10
11
13
15
17
18 19 20
21
23
24
25
12
16
OK
22
22
14
9
English
OPERATING INSTRUCTIONS
Mounting the strap
Compaction
Baling
Make sure that the press
plate is lowered.
Open the upper and lower
doors fully.
Place the straps in the
strap holders, pull the straps
through the loops and behind
the pin at the back of the
chamber.
Close the doors.
Run the press plate up.
Open the doors fully.
Fasten the straps with a loop
at the bottom of the chamber.
Place the straps in the strap
slots with the bale tool.
Close the doors.
1
2
3
4
5
6
7
8
9
WARNING!
Only the operator
is allowed in the
machine’s working
area!
Open the upper door.
Place the waste evenly
distributed in the chamber.
Close the upper door
- The start button lights
green.
Press the green start button
for an automatic press cycle.
10
11
12
13
The yellow lamp flashes for
ready bale - the machine is
ready for baling.
Open the upper door.
Pull the straps over the bale.
Cut the straps with the knife.
Close the upper door.
Run the press plate down
using the down arrow. The
press plate automatically
stops in the down position
and keeps the bale UNDER
PRESSURE.
Open the upper and lower
doors FULLY.
Tie the straps.
Check that the end of the
pressure rod on the upper
side of the press plate ends
at the OK arrow.
The operator stands at
the SIDE of the machine,
outside the risk area.
Make sure that nobody is in
the risk area!
Remove the bale by press-
ing the two buttons on the
side of the machine at the
same time.
14
15
16
17
18
19
20
21
22
23
24
25
Mounting the strap
Compaction
Baling
3

A= 2150
B= 2983
C= 2000
D= 1020
E= 1450
F= 570
G= 1108
H= 2278
I= 1065
A= 2150
B= 2783
C= 2000
D= 1020
E= 1450
F= 570
G= 1108
H= 2278
I = 1065
G
E
I
C
B
A
H (with open door)
F
D
-00 (-02, -04)
/+ /+
Min: 1,20 m Min: 1,50 m
/+
- 2150 mm
- 2325 mm
- 1350 Kg
- 1900 Kg
/+
10
TECHNICAL
SPECIFICATIONS
(Valid for 490 3400-00 unless
otherwise indicated)
GENERAL DATA
Total weight: 1,350 kg
Transport height: 2,150 mm
Dimensions: (-02,-04)
Height: 2,983 mm
(2783)
Width: 1,450 mm
Depth: 1,065 mm
Recommended necessary
space installed: (-02,-04)
Height: 2,983 mm
(2783)
Width: 2,650 mm
Depth (door open): 2,878 mm
Bale size:
Height: 1,000 mm
Width: 1,200 mm
Depth: 800 mm
Weight, cardboard: up to 300 kg
Weight, plastic: up to 450 kg
Loading aperture:
Height: 570 mm
Width: 1,200 mm
Noise level: 73 dB (A)
Primer: Anti-corrosive primer.
Topcoat: Two part paint and
powder coat.
ELECTRICAL DATA
Operating power: 3x400 V, 50 Hz
Electric motor: 3 kW
Operating voltage: 24 AC/DC via
transformer
Electrical
connection: 5 pin CEE
plug, 10 A
Protection class: IP 55
HYDRAULIC DATA:
Flow: 25 L/min
Working pressure:
240 bar (3470 psi)
Relief pressure:
240 bar (3470 psi)
Press force:
24 t (240 kN)
Surface pressure: 2.5 kg / cm2
Cycle time total: 41 s.
Piston stroke: (-02,-04)
1,000 mm
(800)
Oil volume: 20.8 L
Recommended hydraulic oil:
+5°C to +60°C:
ISO VG 32-68
below 5°C:
Lubrication Engineering
LE 6520 Monolec hydraulic
mulitgrade SAE 5W-20
DIMENSIONAL DRAWING
TRANSPORT INSTRUCTIONS
English
2
3
4
4
4
5
6
7
4

11
Read through the whole instructions before installing the machine!
If the instructions are not followed, this could result in personal injuries.
(The machine is packaged using recyclable plastic.)
Make sure that nobody except the qualified and competent installation engineer is in the vicinity of the machine during the
installation process! Only one person is allowed to carry out the installation.
The installation must be carried out by an qualified and competent person.
Some steps involve dangerous machine movements. Take every precaution, as there is a great risk of serious crushing injuries.
1: Note the installation dimensions!! The operator must have enough space to be able to stand on the right side of the
machine during baling. The height of the ceiling, the turning radius of the door and sufficient space for service work etc. must also
be considered!
2: Electrical installation: A qualified electrician should only ensure that the correct electrical power according to these instruc-
tions is available for the installation of the machine. The electrician or any other individual must not switch on the current to the
machine or start the machine. This may only be carried out by the qualified and competent installation engineer in accord-
ance with the installation instructions.
3a: Take out 1 bale tool, 2 strap holders and 8 rubber tiles.
b: Place the strap holders in the strap holder mounts and hang the strap hook on the side of the machine
4: Place the machine on the rubber tiles and ensure that it is level.
5: Make sure that the machine’s main switch is set to 0 and that the emergency stop is pressed in.
6: Remove the remote control from the electrical box.
7: Connect the machine to the wall socket.
8: Turn the main switch to 1 and reset the emergency stop button. A white lamp lights up.
9: Dangerous machine movement!! Check the motor’s direction of rotation by briefly pressing the remote control button.
NOTE! If the motor rotates in the wrong direction, call in an electrician to reverse the phases.
10: Dangerous machine movement!! Run the cylinder jerkily up towards the mounting beam by briefly and repeatedly pressing
the remote control button.
11: Screw the cylinders in place from the upper side of the press plate (although do not tighten them until point 15).
12: Angle the hydraulic hoses down and ensure that they are not in contact with any sharp edges. Tighten the hydraulic couplings
on the cylinders.
13: Strap the hydraulic hoses as illustrated.
14a: Run up the press plate using the remote control button until it is approximately 200 mm from the uppermost position.
b: Turn the main switch to 0.
c: Disconnect the remote control by disconnecting the three cables from the logic unit. Tighten the screws on the logic unit again.
Store the remote control in a suitable location, separate from the machine.
When the cylinder has been run up and the installation completed, the remote control must be removed from the electrical
box! If the remote control is not removed, it is possible to bypass the machine’s entire safety system, with a very great risk of
personal injuries as a consequence.
15: Tighten the cylinder screws.
16: Screw the bale indication mount to the beam on the upper side of the machine. Tightening bracket screws seated as delivered
produces maximum bale size.
17: Install the covers.
18: Close the doors.
19a: Turn the main switch to 1.
b: Make sure that the emergency switch is not pressed in.
c: Run up the press plate using the ”up arrow”.
d: The green lamp lights up.
20: Check the oil level when the press plate is in its uppermost position.
When the cylinder has been run up and the installation completed, the remote control must be removed from the electrical
box! If the remote control is not removed, it is possible to bypass the machine’s entire safety system, with a very great risk of
personal injuries as a consequence.
INSTALLATION TEXT FOR THE PICTURES ON THE LAST DOUBLE-PAGE SPREAD
English
5

Hydraulic oil
VG 32-68 <+4°C LE 6520
SAE 5-20
4
1
2
SAE 20
=
=
5
3
>+5°C
0
OFF
12
SAFETY CHECK
- Check the upper and lower door switches: It must not be possible to start the machine if a door(s) is open.
- Check the baling push buttons: It must not be possible to remove the bale from the machine with only one push
button.
- Check that the emergency stop is working.
- Check that the plate that connects the cylinder and the press plate is mounted (see figure 2 above):
If any faults are discovered in the functions listed above, the machine must not be used until it has been repaired by
authorised service personnel.
Service and repairs are only to be performed by qualified and competent staff, and in accordance with the machine
manufacturer’s instructions.
NOTE! During inspection and maintenance, service
work and the removal of trapped waste etc.:
• Always turn the main switch to ”0” and secure it
with a padlock.
• Do not work inside the machine
WEEKLY INSPECTION AND MAINTENANCE
Oil change: Contact the local authorities for advice regarding how to reduce the environmental impact when dealing
with residual oil.
English
6

Sävsjö 2004-12-20
Box 58
S-576 22 Sävsjö, Sweden
Tel: 46-382-15700
Telefax: 46-382-10607
13
4903400-00 - 4903400-99
AB ORWAK
98/37EEC (Machinery Directive)
89/336/EEC, 92/31/EEC, 93/68/EEC (EMC Directive)
73/23/EEC, 93/68/EEC (Low Voltage Directive)
EN 60204-1 (Safety of Machinery - Electrical Equipment of Machines)
EN 61000-6-1 (EMC Immunity for equipment in residential, commercial and light-
industrial environments)
EN 61000-6-2 (EMC Immunity for equipment in industrial environments)
EN 61000-6-3 (EMC Emissions from equipment in residential, commercial and
light-industrial environments)
EN 61000-6-4 (EMC Emissions from equipment in industrial environments)
(EMC technical report has been issued by SP,
Swedish National Testing and Research Institute, Box 857, SE-501 15 BORÅS,
SWEDEN)
to which this declaration relates is in conformity with the following
standards or other normative documents following the provisions of Directive
declares under its sole responsibility that the product model
(serial number specified on the first page)
DECLARATION OF CONFORMITY
We
English
Design manager
7

min. 0,6 m
min. 0,6 m
2,5 mm
Box 58
Sweden
Type Serial No
Product No Date
VHz kW
A
(8x)
A
B
b) OK
0
a)
OK
Check
A )
C )
B )
1
B )
A )
18 mm
10 mm
12 3
45
678
910 11
min. 0,6 m
min. 2983 mm
OK.
OK.
C
A
B
576 22 Sävsjö
B
86
Installation

Max
3 MM!
+
+
-
A )
B )
1
-
12
14) 15
16
20
b)
c) c) c)
C )
D )
0
Q1 2 Q3 1 Q3 2
N1 N2
18
19
~900 mm
2 x
A
B
13
17
OK
24 mm
22 mm
a)
200 mm
MRX x 25
x 4
BRB 5,3
x 4
1
2
4
3
18 mm
10 mm
ca. 150 Nm
87
Installation



AB ORWAK
Box 58
S-576 22 Sävsjö, Sweden
Telephone Telefax www.orwak.com
Table of contents
Other Orwak Garbage Disposal manuals
Popular Garbage Disposal manuals by other brands

Milwaukee
Milwaukee MX FUEL MXF220 Operator's manual
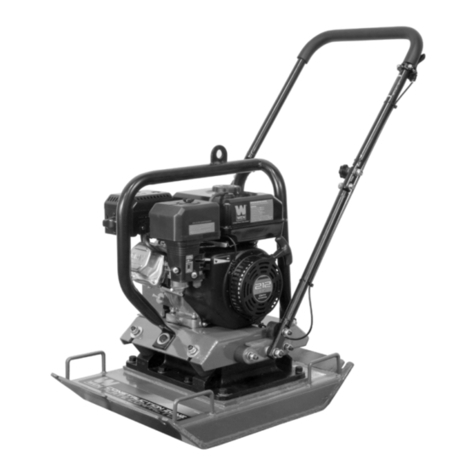
Wen
Wen 56035T instruction manual
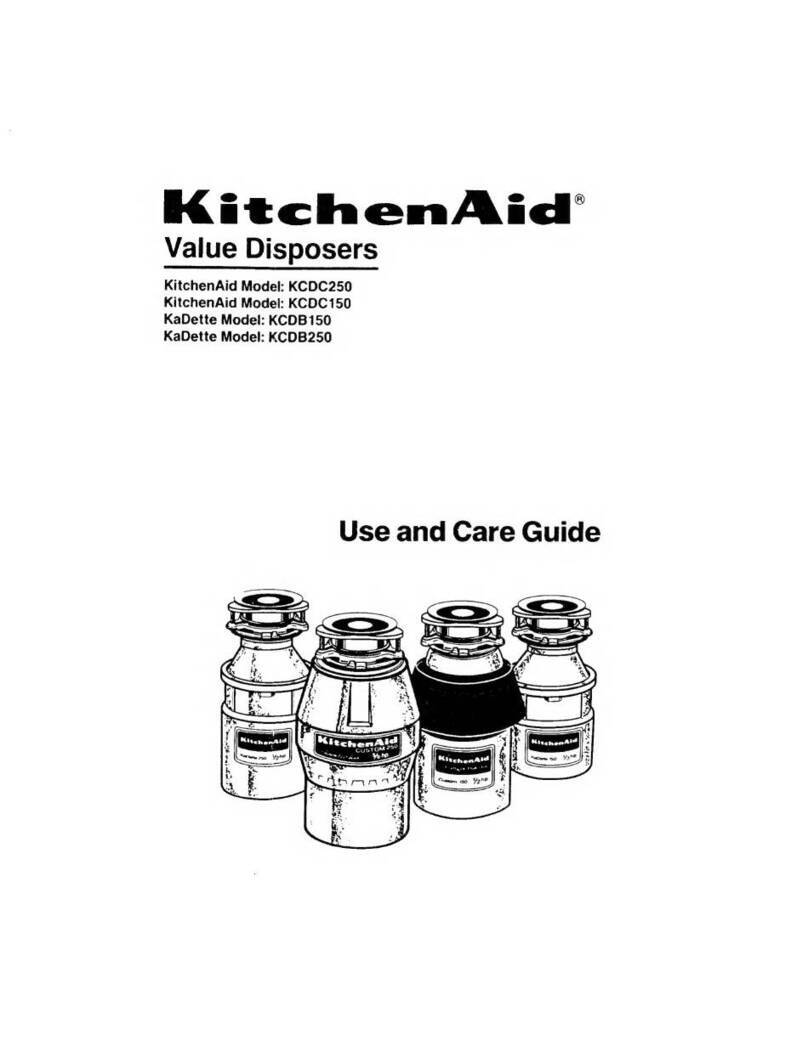
KitchenAid
KitchenAid KCDC250 Use and care guide
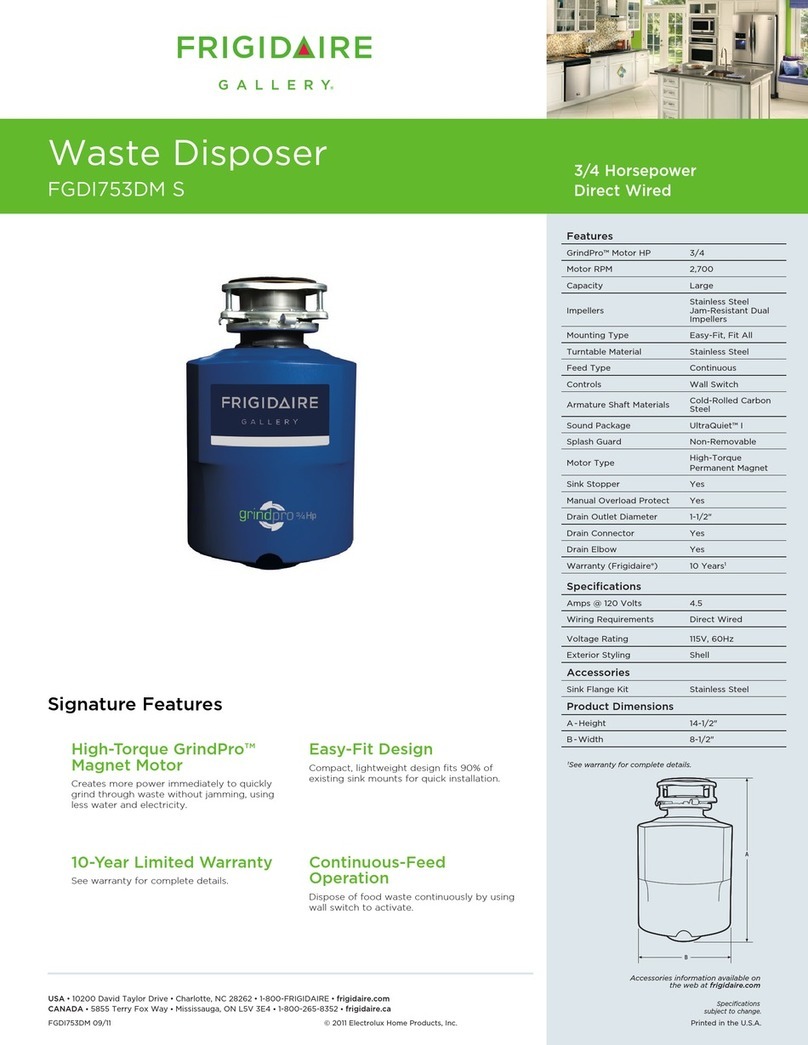
Frigidaire
Frigidaire FGDI753DMS Product specifications
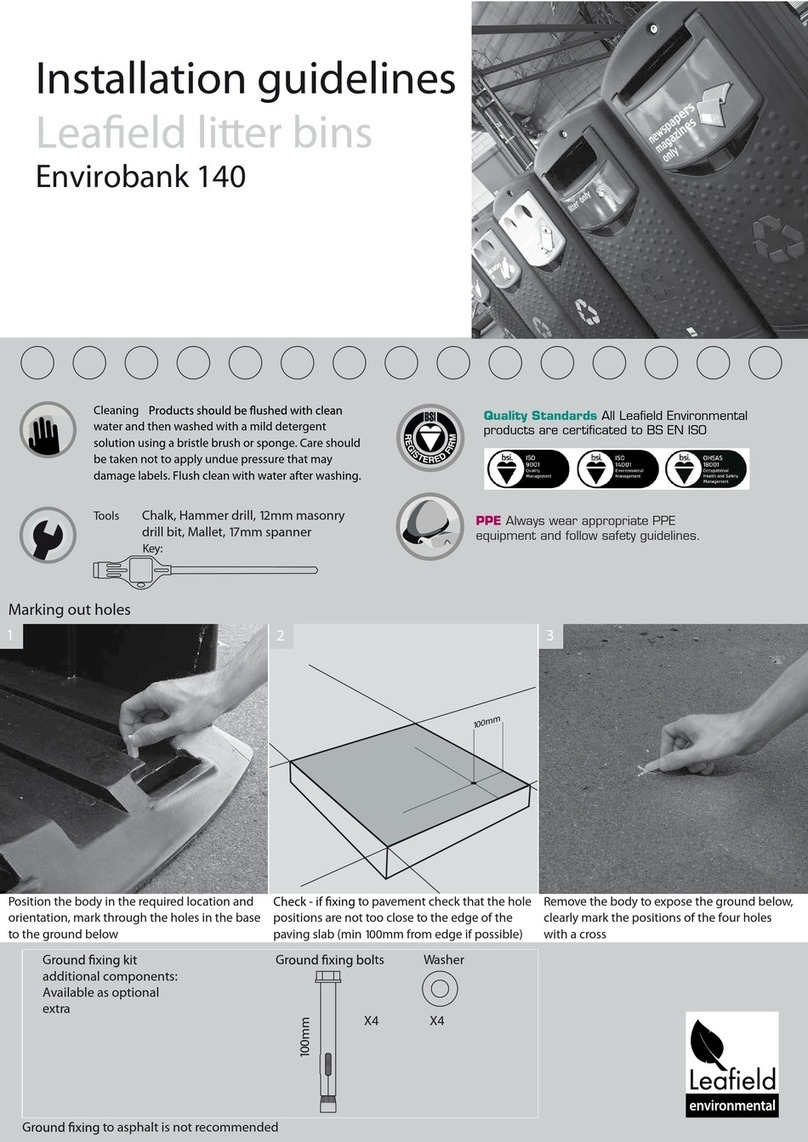
Leafield Environmental
Leafield Environmental Envirobank 140 Installation guidelines
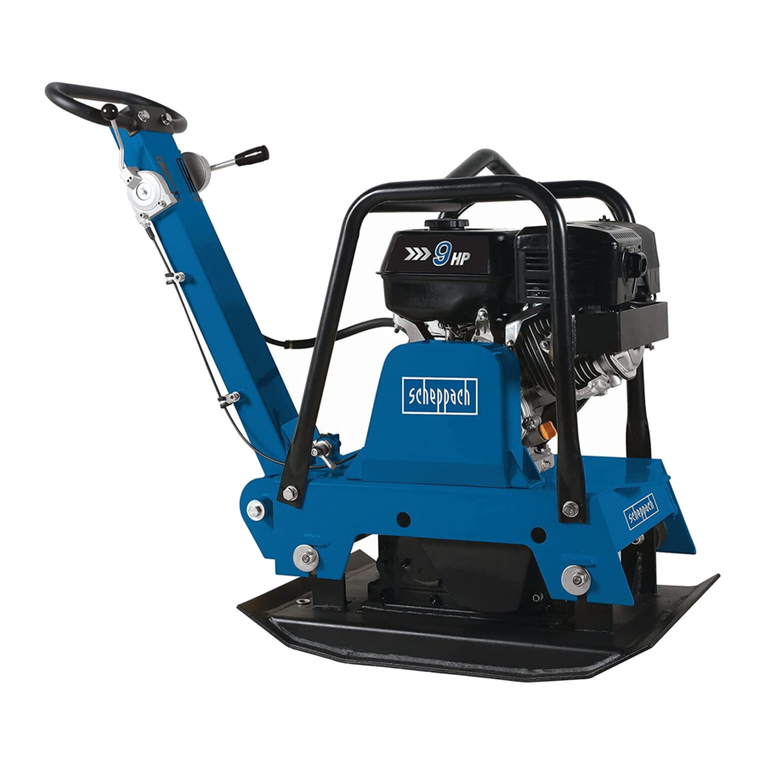
Scheppach
Scheppach HP3000S Translation from the original instruction manual
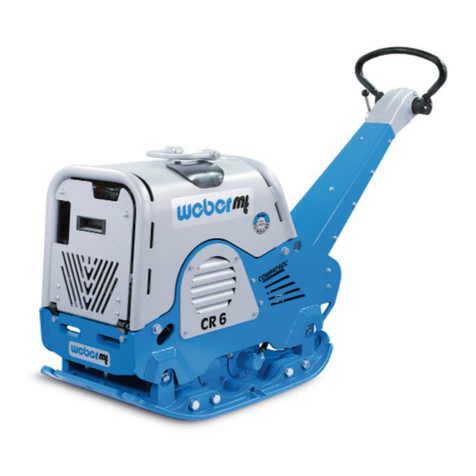
Weber mt
Weber mt CR 6 Operating and maintenance manual

KitchenAid
KitchenAid KCDS075T manual

GE
GE Disposall GFC530T Dimensional information
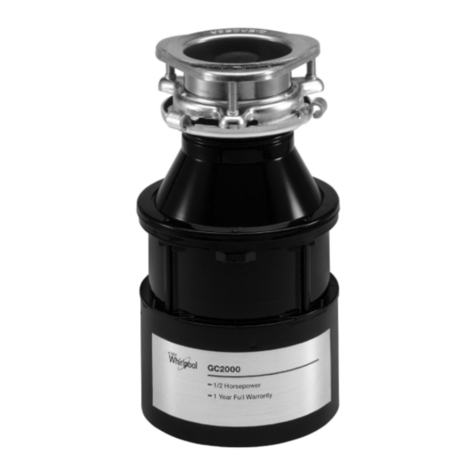
Whirlpool
Whirlpool GC2000XE5 installation instructions
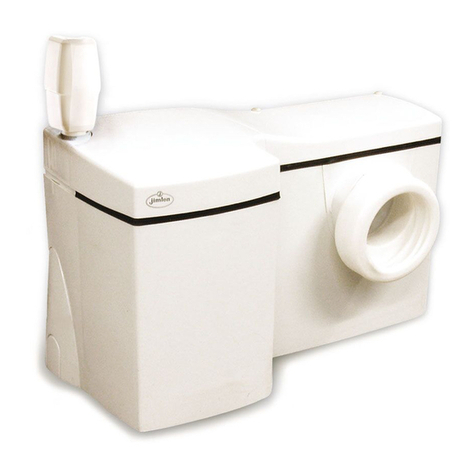
JIMTEN
JIMTEN CICLON L T-604 Maintenance and Instruction Manual

KitchenAid
KitchenAid KBDS100T - NA Batch Feed 1 HP MultiGrind quick guide