Packard Ec Max User manual

Electronically Commutated Motor
Wiring Manual
R: 0
G: 105
B: 62
#00693e
GREEN SPECS
R: 0
G: 0
B: 0
#000000
BLACK SPECS
FONT: Arial Bold
®

packardonline.com | 800.334.17692
Table of Contents
Safety Considerations 3
Application Guide 4, 5, 6, 7, 8
Operational Characteristics 9, 10, 11, 12
Diagnostics, Maintenance & Warranty 13
Specications 14

packardonline.com | 800.334.1769 3
Safety Considerations
Safety
Symbols
The following denitions are used a safety considerations on EC Max and in
this manual. Please read and observe all of these safety concerns.
Installation and service of this motor should be attempted only by trained service
technicians familiar with EC Max instructions and training manual.
EC Max is a multi-purpose replacement indoor blower motor. Proper wiring is
critical to provide proper operation and maintain the proper operation of all safeties
built into the HVAC system.
Always disconnect the main power from the unit being serviced before making any
wiring connections to EC Max. It is also a good practice to conrm that the power
is o with a meter.
EC Max is a multi-volt capable motor. Read all instructions and install the proper
jumper for the line voltage before applying power to this motor.
Use of the wires provided in this kit is recommended. Should additional wires be
needed, use equivalent size wire gauge and rated insulation.
Improper installation, adjustment, alternation, service, maintenance, or use can
cause explosion, re, electrical shock, or other conditions which may cause
personal injury, death, or property damage. Consult a qualied installer, service
agency, or your distributor or branch for information or assistance. The qualied
installer or agency must use the supplied or recommended parts when installing
or servicing this product.
Warning indicates
a hazardous situation which, if
not avoided, could result in
death or serious injury.
Caution indicates
a hazardous situation which, if not
avoided, could result in minor or
moderate injury.
This motor should be installed in accordance with accepted practices and
installation instructions, and in compliance with all national and local codes.
CAUTION
WARNING
CAUTION
WARNING
CAUTION
WARNING
CAUTION
WARNING
CAUTION
WARNING
CAUTION
WARNING
CAUTION
WARNING

packardonline.com | 800.334.17694
Application Guide
EC Max can be used in the following applications
• Residential and light commercial HVAC split system (Air Handler and Fossil Fuel
Furnace) units and Package Units;
• Indoor direct drive blower motors;
• Replace original equipment PSC (Permanent Split Capacitor) induction motors;
• Replace original equipment Constant Torque ECM (Electronically Commutated
Motor) such as the genteq X13 and Endura Pro, or similar model motors with
24vac speed taps.
EC Max is not compatible with the following applications
• HVAC systems that were originally supplied with Constant Airow ECM also
known as Variable Speed such as genteq models 2.0, 2.3, 2.5, 3.0 and Eon;
• Outdoor fan motors;
• Belt drive motors.
NOTE: In this manual, there are two sets of instructions. One for replacing PSC motors and
one for replacing Constant Torque ECM. Please make sure to use the correct instructions
for the motor you are replacing to prevent damage to the motor.
NOTE: The EC Max is mounted using a belly band mount. The mount is not provided. If the
replaced motor used a belly band and was a NEMA 48 Frame motor, the original belly band
canbeusedontheECMax.However,itisnotrecommendedtouseatorsionexmounton
the ¾ and 1 Hp rated motors.
For 46013 and 46012 use TFM55 for mounting.
For 46034 and 46001 use A60048 for mounting.
The following items are supplied with this motor
• Harness – the same harness is used for all
applications;
• Voltage Plugs;
◦ One for 115vac (white)
◦ One for 230vac (yellow)
• Optional jumper wires and extra terminals;
• Optional Y-adapter;
• Installation manual.
Use of included wiring harness
is required for proper motor
installation.
NOTE

packardonline.com | 800.334.1769 5
Using EC Max to replace PSC (Permanent Split Capacitor) induction motors.
• Install motor in HVAC system using a belly band mount.
• Select the voltage plug that matches the voltage rating of the replaced motor.
Install the voltage plug. Connect the harness plugs to the motor.
White Voltage Plug
115vac Systems
Yellow Voltage Plug
230vac Systems
• HIGH VOLTAGE POWER CONNECTIONS
◦Note: The Black and White HIGH VOLTAGE POWER wires are taped together and
aggedforidentication.
◦ Connect the Black HIGH VOLTAGE POWER wire to a L1 line voltage power
source that is continuously powered when the unit disconnect is closed
◦ Connect the White HIGH VOLTAGE POWER wire to a Neutral (115vac
systems) or L2 (230vac systems) that is continuously powered when the
unit disconnect is closed.
• HIGH VOLTAGE SIGNAL CONNECTION
◦Note:TheBlackandRedHIGHVOLTAGESIGNALwiresaretapedtogetherandagged
foridentication.
◦ Connect the Black (HV1) HIGH VOLTAGE SIGNAL wire to all of the motor
output terminals from the HVAC board (or fan relay) including Heat, Cool
and Continuous Fan (if applicable) that were previously connected to the
PSC motor. Use the supplied jumper wires and terminals or wire nut all
together.
◦ Insulate the Red (HV2) HIGH VOLTAGE SIGNAL wire with a wire nut.
• LOW VOLTAGE SIGNAL CONNECTIONS
◦Note:AllLOWVOLTAGESIGNALwiresaretapedtogetherandaggedfor
identication.
◦ Connect the Blue LOW VOLTAGE SIGNAL wire to the thermostat common
terminal or directly to the common side of the 24vac transformer.
◦ Connect the speed desired for HEAT to thermostat (W) and the speed
desired for COOL (including A/C or Heat Pump systems) to thermostat (Y).
• NOTE:
◦After completing all connections, the technician should operate the system in
alldemandmodesmeasuringairowusingindustrybestpractices.Toadjust
theairow,changethespeedselectionconnectedtotheappropriatethermostat
terminal.
◦If the system has a Continuous Fan selection at the thermostat, this demand
will energize the motor through the fan relays to energize the Black (HV1) HIGH
VOLTAGE SIGNAL input which will operate the motor at the default continuous fan
speed. This speed is approximately 200 rpm slower than the LOW speed from the
LOW VOLTAGE SIGNAL CONNECTIONS. If a higher continuous fan speed is desired,
connect any unused speed selection to thermostat terminal (G).

packardonline.com | 800.334.17696
Using EC Max to replace PSC (Permanent Split Capacitor) induction motors.

packardonline.com | 800.334.1769 7
Using EC Max to replace Constant Torque ECM with 24vac speed taps.
• Install motor in HVAC system using a belly band mount.
• Select the voltage plug that matches the voltage rating of the replaced motor.
Install the voltage plug. Connect the harness plugs to the motor.
White Voltage Plug
115vac Systems
Yellow Voltage Plug
230vac Systems
• HIGH VOLTAGE POWER CONNECTIONS
◦Note: The Black and White HIGH VOLTAGE POWER wires are taped together and
aggedforidentication.
◦ Connect the Black HIGH VOLTAGE POWER wire to a L1 line voltage power
source that is continuously powered when the unit disconnect is closed.
◦ Connect the White HIGH VOLTAGE POWER wire to a Neutral (115vac
systems) or L2 (230vac systems) that is continuously powered when the
unit disconnect is closed.
◦Note: These wires can be connected to the same terminals the Constant Torque ECM
used for line voltage inputs.
• HIGH VOLTAGE SIGNAL CONNECTION
◦Note:TheBlackandRedHIGHVOLTAGESIGNALwiresaretapedtogetherandagged
foridentication.
◦ Connect the Red (HV2) HIGH VOLTAGE SIGNAL wire to a L1 line voltage
power source that is continuously powered when the unit disconnect is
closed. This wire can be connected to the same L1 source as the Black
HIGH VOLTAGE POWER wire in the previous step.
◦ Insulate the Black (HV1) HIGH VOLTAGE SIGNAL wire with a wire nut.
◦Note: This wire can be connected to the same terminal as the L1 HIGH VOLTAGE
POWER connection in the previous step.
• LOW VOLTAGE SIGNAL CONNECTIONS
◦Note:AllLOWVOLTAGESIGNALwiresaretapedtogetherandaggedfor
identication.
◦ Connect the Blue LOW VOLTAGE SIGNAL wire to the (C) terminal used by
the motor that was removed or to the thermostat common terminal or to
the common side of the 24vac transformer.
◦ Connect the speed desired for HEAT to the 24vac HEAT terminal and the
speed desired for COOL (including A/C or Heat Pump systems) to the
24vac COOL Terminal used by the motor that was removed.
◦ If the system has a 24vac Continuous Fan terminal connect any unused
speed to this terminal if desired.
• NOTE:
◦After completing all connections, the technician should operate the system in all
demandmodesmeasuringairowusingindustrybestpractices.Toadjustthe
airow,changethespeedselectionconnectedtotheappropriatedemandterminal.

packardonline.com | 800.334.17698
Using EC Max to replace Constant Torque ECM.

packardonline.com | 800.334.1769 9
Operational Characteristics
The Black and White HIGH VOLTAGE POWER wires provide the power to operate the
electronics in the motor control and the power to operate the motor. These
inputs are required to operate the motor but cannot turn the motor on by
themselves.
The Black or Red HIGH VOLTAGE SIGNAL wires select the mode of operation.
◦ When replacing PSC motors the Black wire (HV1) is energized from the fan
relay(s). This creates the “ON” command for the motor. When the Black
wire is de-energized from the fan relay(s) the motor will turn o. The level
of output (speed) is determined by the LOW VOLTAGE SIGNAL wires. The
Red wire (HV2) is not used in this conguration.
◦ When replacing Constant Torque ECM the Red wire (HV2) is energized with
continuous line voltage power. This input is required to operate the motor
but cannot turn the motor on by itself. When the Red wire is energized,
the LOW VOLTAGE SIGNAL wires provide both the “ON/OFF” command
for the motor and determine the output level (speed).
The LOW VOLTAGE SIGNAL wires provide the speed selection to the motor. These
are 24vac inputs.
◦The low voltage signal inputs are programmed with a hierarchy. If more
than one input is energized at the same time, the higher tap value (speed
value) will be operated. Multiple taps can be energized at the same time
without damaging the motor.
◦The optional Y-adapter is provided to allow multiple thermostat
connections to the same speed without back feeding to each other.
For example, if same speed is desired for multiple thermostat demands.
◦ IMPORTANT NOTE: The Y-adapter will only work properly on the Low and Med-Hi
speed taps.
◦NOTE: The Y- adapter is only needed when replacing PSC motors where
the thermostat demands are used to energize the speed taps of the EC
Max. When replacing Constant Torque ECM with 24vac speed taps, any
speed can be connected to multiple fan relay outputs from the HVAC
system control board or fan relay(s).

packardonline.com | 800.334.176910
Using EC Max to replace PSC (Permanent Split Capacitor) induction motors.
• Example connection using the optional Y-adapter when replacing PSC motors.
Using EC Max to replace Constant Torque ECM.
• Example connection of one speed to multiple fan relay outputs from the HVAC
system control board or fan relay(s).

packardonline.com | 800.334.1769 11
Rotation is determined automatically the rst time the motor is operated. It
is important to operate the motor for the rst time in the HVAC system. Do
not bench test the motor. The rst time the motor is operated the following
sequence should be recognized:
• The motor will run very slowly in CW rotation (lead end) for approximately 15
seconds then stop.
• The motor will run very slowly in CCW rotation (lead end) for approximately
15 seconds.
• The motor will then either:
◦increase speed (related to the speed selection energized) at the current
CCW rotation if that is the direction it has selected;
◦or stop, reverse to CW rotation and increase speed to CW rotation.
◦Once the motor speeds up, the direction the motor is operating is the
direction it has selected. It will now start and run in this direction the rest
of its life. It will never perform this function again. If this is not the correct
direction it can be reversed.
Changing the rotation of the motor after it has selected a rotation using the
process above is accomplished with the following steps.
• Turn o the power to the HVAC system.
• Leave the HIGH VOLTAGE POWER wires connected
• Connect both the Black and Red (HV1 & HV2) HIGH VOLTAGE SIGNAL
WIRES to the same L1 source as the Black HIGH VOLTAGE POWER wire.
• Leave the Blue LOW VOLTAGE SIGNAL wire connected to 24vac common.
• Disconnect all the LOW VOLTAGE SIGNAL speed wires from the motor to the
HVAC system controls.
• Connect the White (Low Speed) LOW VOLTAGE SIGNAL wire only to the
thermostat (R) terminal or directly to 24vac side of the transformer.
• Restore power to the HVAC system. There is no need for a thermostat
demand. Set a stop watch for 1 minute.
• After 1 minute, turn o the power to the HVAC system and restore all wires to
the desired conguration for the application.
• The next time the motor is energized it will operate in the opposite direction.

packardonline.com | 800.334.176912
Wiring diagram for changing the rotation of the motor.
Using EC Max to replace PSC (Permanent Split Capacitor) induction motors.
Wiring diagram for changing the rotation of the motor.
Using EC Max to replace Constant Torque ECM.

packardonline.com | 800.334.1769 13
Diagnostics
If the motor will not operate (turn on at any speed) see the information in the
previous section related to Operational Characteristics and conrm the motor
has the proper line voltage and 24vac inputs needed to operate.
To reverse the rotation of the motor, see the information in the previous section
related to Operational Characteristics (pg 11).
Maintenance
The EC Max motor is permanently lubricated and requires no maintenance.
Diagnostics, Maintenance & Warranty
1. All items sold by Packard, Inc. are warranted against defects in
workmanship or materials under normal use for a period of one (1) year.
Products are covered for up to a maximum of two (2) years from the
manufacturer’s date code on the product or one year after installation,
whichever comes first.
2. No warranty is made as to the fitness of vendor’s products for a
purpose. Buyer acknowledges that it alone has determined that the
goods purchased will suitably meet the requirements of their intended
use. In no event will Packard be liable for consequential, incidental or
other damages.
3. For products other than those listed below, please MAIL the original
nameplate (label or sticker) for each item. Copies of labels will NOT be
accepted. Please do NOT fax or email labels!
4. A reason for failure MUST be provided for each item on the warranty
claim.
5. Credits are NOT to be taken by customer until merchandise or original
nameplate has been received by Packard, Inc. and credit is issued.
6. Credit will be issued upon verification of purchase history for ORIGINAL
labels dated within manufacturing date code requirements.
7.Do not field scrap products until credit has been issued.
8. In the event Packard or the manufacturer requires evaluation of warranty
items, Packard will issue a return authorization form. Do not return
warranty items unless requested.
9. Please contact Packard Warranty for these products prior to mailing
claims.
Warranty

packardonline.com | 800.334.176914
Specications
Voltage Ratings
• 115VAC (white voltage plug) allowable range 90-132VAC
• 230VAC (yellow voltage plug) allowable range 180-264VAC
Horsepower Ratings 1/3, 1/2, 3/4 & 1
FLA Ratings
• 1/3 Hp = 5.0/3.0
• 1/2 Hp = 6.7/4.0
• 3/4 Hp = 8.2/4.9
• 1 Hp = 11.0/6.7
RPM Rating 1075
Speeds (see chart below for estimated RPM values)
• 4 speeds (LOW, MED-LOW, MED-HI & HI)
Rotation CW or CCW (automatically congured)
Bearing Ball
Ambient Rating 40°C
Enclosure Open Air Over (OAO)
Frame size and dimensions NEMA 48 Frame (5.6” diameter) see diagram
below for DIM A & B
• 1/3 Hp (DIM A = 11.26), (DIM B = 6.34)
• 1/2 Hp (DIM A = 11.26”), (DIM B = 6.34”)
• 3/4 Hp (DIM A = 12.76”, (DIM B = 7.84”)
• 1 Hp (DIM A = 12.76”), (DIM B = 7.84”)
Shaft .5” x 5” (4.5” single at)
Mounting Belly band (not supplied)
Harness Lead length 48”
UL Recognized Component
4kV surge protection
SPEED (RPM) RATINGS.
NOTE: ACTUAL RPM WILL
VARY DEPENDING ON LOAD.
HI = 1075 RPM
MED-HI = 1000 RPM
MED LOW = 925 RPM
LOW = 850 RPM

packardonline.com | 800.334.1769 15

Customer Service
800.334.1769
customerser[email protected]
Corporate Headquarters and Main Distribution Center
2700 Barrett Lakes Blvd. NW, Suite 100, Kennesaw, GA 30144
Distribution Centers
2570 N. Shadeland Ave. Suite 103, Indianapolis, IN 46219
6151 W. Erie St., Chandler AZ 85226
Packard supplies to wholesale distribution only.
PACKARDONLINE.COM
This manual suits for next models
4
Table of contents
Other Packard Engine manuals
Popular Engine manuals by other brands
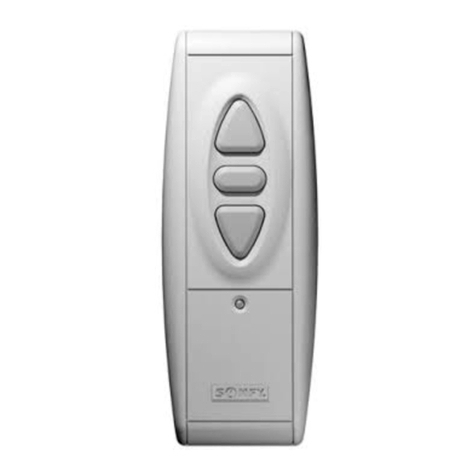
SOMFY
SOMFY LIGHTING OUTDOOR RTS Quick programming guide
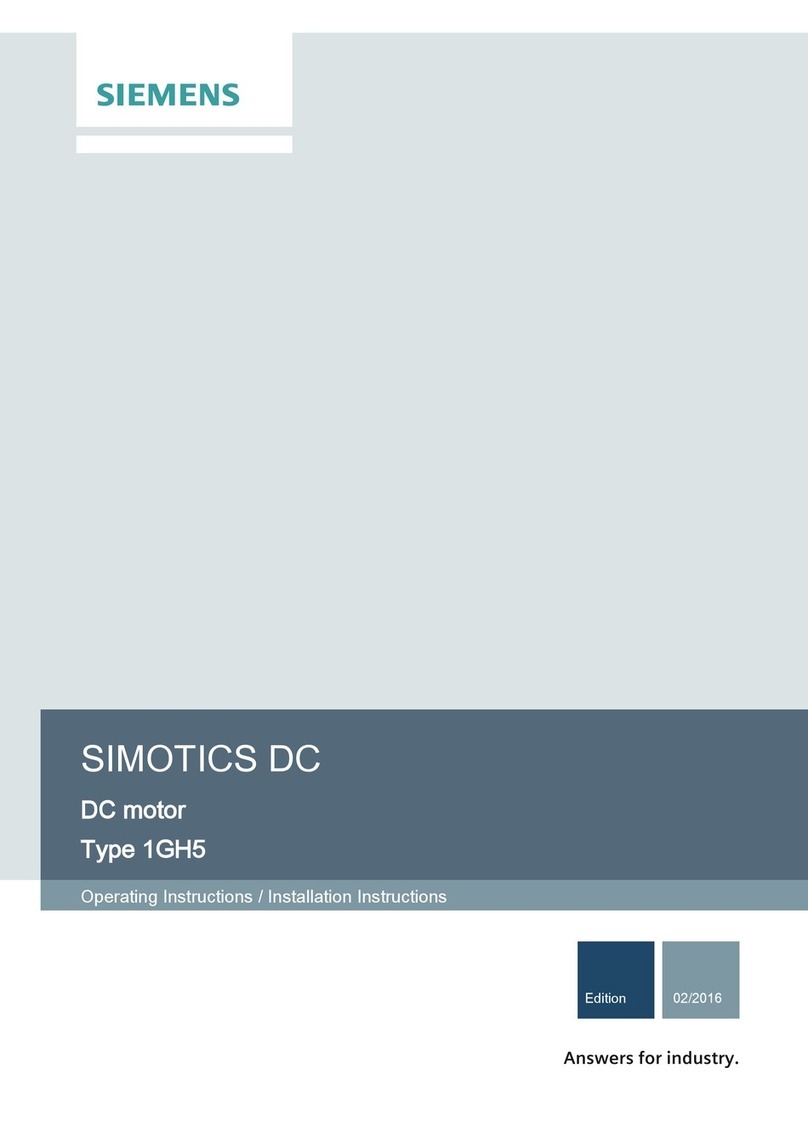
Siemens
Siemens SIMOTICS DC 1GH5 Operating and installation instructions
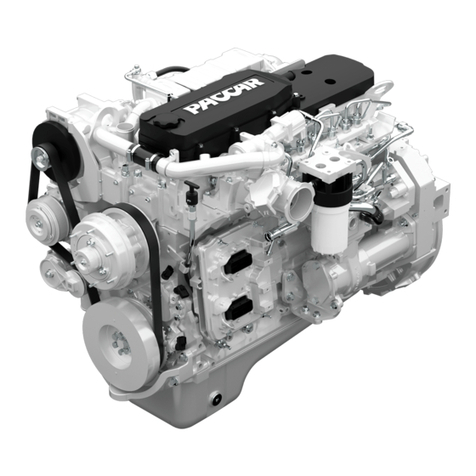
Paccar
Paccar PX-7 Operator's manual

Fiamma
Fiamma Polar White 07930-01P Installation and usage instructions

Robin America
Robin America EH722 EFI parts manual
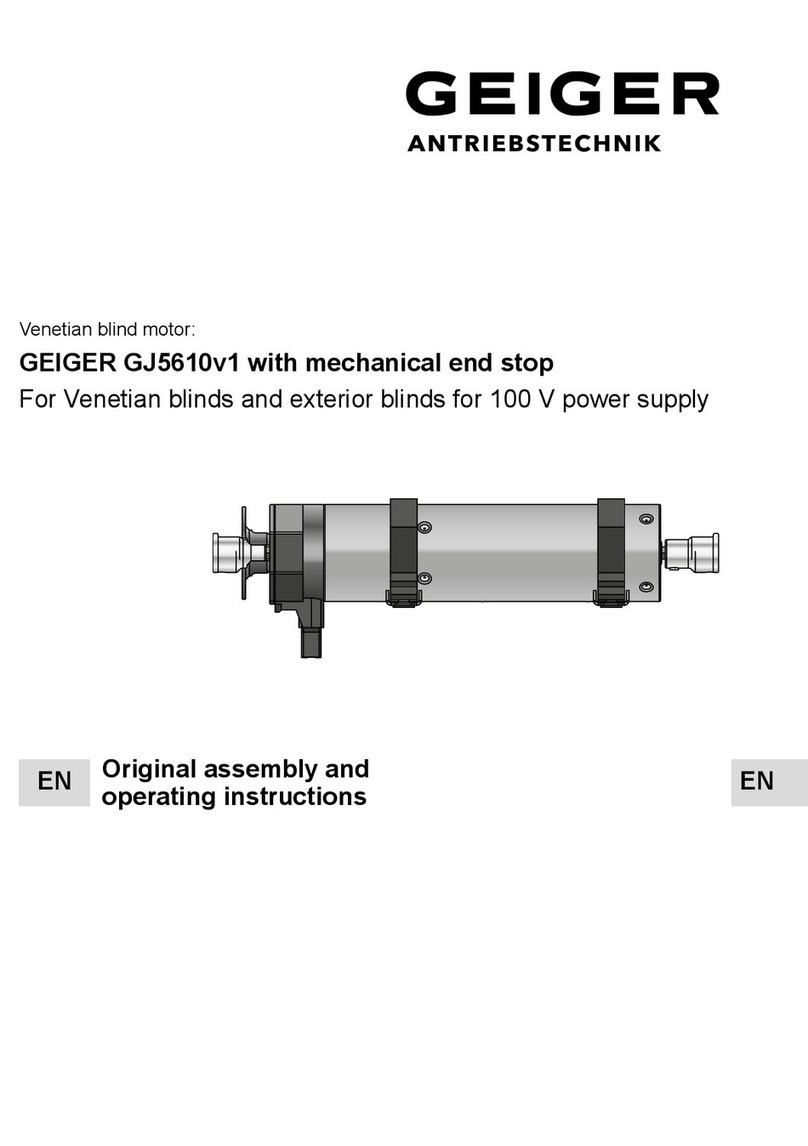
GEIGER
GEIGER GJ5610v1 Assembly and operating instructions