Parker VRD355 Series User manual

Parker Hannifin GmbH & Co. KG
Hydraulic Controls Division
Gutenbergstr. 38
41564 Kaarst, Germany
Tel.: +49-181 99 44 43 0
Fax: +49-2131-513-230
E-mail: infohcd@parker.com
Copyright © 2003, Parker Hannifin GmbH & Co. KG
Bulletin HY11-AL287-M1/UK
Installation Manual
Series VRD350, VRD355, ABG35S
Digital
Power Amplifier

2
IA VRD UK.INDD RH 02.06
Digital Power Amplifier
Series VRD350 and VRD355Installation Manual
Parker Hannifin GmbH & Co. KG
Hydraulic Controls Division
Note
This document and other information from Parker Hannifin GmbH,
its subsidiaries, sales offices and authorized distributors provide
product or system options for further investigation by users having
technical expertise. Before you select or use any product or system
it is important that you analyse all aspects of your application
and review the information concerning the product or system in
the current product catalogue. Due to the variety of operating
conditions and applications for these products or systems, the
user, through his own analysis and testing, is solely responsible
for making the final selection of the products and systems and
assuring that all performance and safety requirements of the
application are met. The products are subject to change by Parker
Hannifin GmbH at any time without notice.

Digital Power Amplifier
Series VRD350 and VRD355Installation Manual
3
IA VRD UK.INDD RH 02.06
Parker Hannifin GmbH & Co. KG
Hydraulic Controls Division
1. Description and Design 4
1.1. Technical Data 5
1.2. Ordering Code 6
1.3. Connection 7
1.4. Block Diagrams 9
2. Commissioning 12
2.1. Front Panels 12
2.2. Programming 13
2.3. Signal Diagrams 15
2.4. Diagnosis 20
2.5. Parameters 20
3. Function 24
3.1. Command signals 24
3.2. Ramp Function Generators 24
3.3. Offset 25
3.4. Valve Curve Linearisation 25
3.5. Adjustment of Current Gain 25
3.6. Dither 25
3.7. Current Controller 25
3.8. Output Stages 25
3.9. Step Functions 26
3.10. Control Circuits 26
3.11. Zero Point Adjustment 26
3.12. Controller Parameter 27
3.13. Programmable Comparator Function 31
3.14. Serial Interface 32
3.15. ABG35S 32
4. Operating and Error Messages 33
4.1. Enable 33
4.2. Reset Ramp 33
4.3. Malfunction and Error Messages 33
4.4. Comparator Output 34
4.5. Externally selected command signals and directions 34
5. Wiring Diagram of Rear Connector 34
6. Parameter List 35
7. Wiring Diagrams 37
Content Page

4
IA VRD UK.INDD RH 02.06
Digital Power Amplifier
Series VRD350 and VRD355Installation Manual
Parker Hannifin GmbH & Co. KG
Hydraulic Controls Division
1. Description and Design
Applications (general)
Amplifier card for driving proportional directional
valves, pressure and flow control valves. Suitable
for solenoid systems up to 3.5 A. Valves with spool
position feedback, and external closed loop control
circuits (e.g. pressure regulating circuits) can be
implemented with the closed loop control options.
Suitable for use on NC axes, especially where the
requirements for dynamic response and accuracy
are high.
Special Application of VRD355
Amplifier card without the front panel display and
operating elements for cost effective applications
where operation is via a serial interface or ABG35S
(must be ordered separately, No. 23.501 456).
The VRD350 / VRD355 Series is distinguished
by the following Features:
• PWM output stage with programmable current
controller.
• Adjustable parameters for all solenoid types up
to 3.5A.
• Digital setting and display of all parameters.
• High set value and feedback resolution
(<0.05%).
• No temperature or long-term drift.
• Precisely reproducible settings.
• Serial interface on the front panel for remote
parameter setting.
• Simple operation by 4 entry keys and 3-digit
LED display.
• Fault indication by numeric code.
• Variable dither amplitude and frequency.
• Gain for solenoids A and B can be set indepen-
dantly.
• Different valve characteristics are stored
on-board to enable linearisation.
• Set value simulation for simplified commission-
ing.
• Only a unipolar supply voltage is necessary
(24V).
• Internally adjustable time delay of output stages
after applying the enable signal.
• Integrated actual value recording.
• Robust, SMT technology.
Meaning of Symbols
Warning, danger for user.
Attention, possible damage to unit or
other capital assets.
Note, information, key function.
• Differential amplifier input for NC command
signal 0...±10V.
• Additional input for command signal specifica-
tion by 0...±10V.
• Integrated power supply for ±10V symmetrical
to 0V supply, each capable of carrying 10mA.
• 4 recallable command signals.
• “+” and “-”-direction externally set.
• Enable signal for output stages.
• Reset-Ramp for quick reset of ramp function.
• All external input signals for command signals,
direction, enable, reset ramp are electrically
isolated by opto-couplers.
• Status outputs “Error” and “Comparator” are
similarly electrically isolated by opto-couplers.
• Function indication by LEDs on front panel.
• In addition, for simpler commissioning and for
service purposes, test sockets are located on
the front panel for S6 (NC-command signal),
A (feedback value, where available), IA and IB
(Measurement instruments Ri >100kΩ).

Digital Power Amplifier
Series VRD350 and VRD355Installation Manual
5
IA VRD UK.INDD RH 02.06
Parker Hannifin GmbH & Co. KG
Hydraulic Controls Division
General
Design Europe format
Electrical
Supply voltage [V] 18...30, ripple < 5%
Current consumption [A] 3
Power consumption (24V) [VA] 50
Pre-fuse [A] 3.15 quick acting
Inputs
Analogue Feedback value [V] 6 ±2, 600kOhm
Feedback value [V] 7.5 ±2, 600kOhm
Feedback value [V] 0...10, > 10MOhm
Feedback value [V] 0...±10, > 10MOhm
Feedback value [mA] 0...20, 100kOhm
Feedback value [mA] 4...20, 100kOhm
Command value 5/6 [V] 0...±10, > 150kOhm
Digital 0 [V] 0...1
1 [V] 3...30
Outputs
Ext. supply voltage [V] 24 ±10%, ripple <5%
Reference [V] +10, -10, 10mA
Analogue [V] 0...10, 5mA
Digital [mA] 50
Solenoids [A] 0.8 / 2.7 / 3.5
Interfaces
Serial RS 232C
Adjustment range
Min [%] 0...100
Max [%] 0...100
Ramp time [s] 0...39.5
Dither Amplitude [%] 0...30
Frequency [Hz] 0...647, in steps
Zero point [%] -30...+30
Protection class
Industrial protection class IP00
Environment conditions
Temperature [°C] 0...50
Connection
Plug connector DIN 41612, 48pin design type F
Cable dimensions AWG 15 (power supply + solenoid); 20 (all others)
Cable length [m] max 50
Dimensions
Front panel [mm] 50.5 x 128.4, 10TE/3HE
Printed circuit board [mm] 100 x 160
1.1. Technical Data
EN 50081-2 EN 50011
EN 50082-2 EN 61000-4-2 EN 61000-4-3 EN 61000-4-4
EMC

6
IA VRD UK.INDD RH 02.06
Digital Power Amplifier
Series VRD350 and VRD355Installation Manual
Parker Hannifin GmbH & Co. KG
Hydraulic Controls Division
1.2. Ordering Code
Type
Digital
Amplifier for
Proportional
Valves
Module External
Closed
Loop
Solenoid/
Sensor
Type
Sensor
Assignment
Solenoid
Type
Function
* The values for actual value
signals apply to directio-
nal valves.
Design
Series
Assignment Table
1)
without feedback on valve
2) with feedback on valve
VRD
Code Module
350
with front plate
display / and ope-
rating elements
355
without front plate
display / and ope-
rating elements
Code Type
0 controlled
1 regulated
Code Solenoid type
1 0.8A
3 2.7A
5 3.5A
7
2.7A
(RLL-central threa-
ded solenoid)
Code Solenoid / sensor
version
0
Flange solenoids
(or. pos. transdu-
cer with 6V (zero
voltage)
1
Central threaded
solenoids (or
position indicator
with 7.5V null
voltage)
Code Ext. closed loop*
0 without
0 0...±10V
1 4...20mA
2 0...20mA
Code
Sensor assignment
01)
controlled
12)
Flow valves
NG6
22)
Directional valves NG6
32)
Directional valves NG10
42)
Directional valves NG16
52)
Directional valves NG25
62)
Directional valves NG32
71) ext.
closed loop
(DC valves)
81) ext.
closed loop
(press./flow valves)
92)
Directional valve
D91FS
Code Function
- controlled
R regulated
Proportional DC Valves Amplifier card for valves
Type Description Solenoid Size without position
transducer
with position
transducer
w/o pos. transducer,
with ext. closed loop
DC Valves
D*1FW L 10...32 VRD35*-030-00 — VRD35*-130-R7*
D*1FS L 10...25 — VRD35*-130-R*0 —
RLL G09 6 VRD35*-071-00 VRD35*-171-R20 VRD35*-171-R7*
WLL G09 6 VRD35*-031-00 VRD35*-131-R20 VRD35*-131-R7*
WLL — 10 VRD35*-050-00 VRD35*-150-R30 VRD35*-150-R7*
Pressure
Valves
VB — 6 VRD35*-010-00 — VRD35*-110-R8*
VBY — 6...10 VRD35*-010-00 — VRD35*-110-R8*
VMY — 6...10 VRD35*-010-00 — VRD35*-110-R8*
Flow Valves DUR — 6 VRD35*-010-00 VRD35*-110-R10 VRD35*-110-R8*

Digital Power Amplifier
Series VRD350 and VRD355Installation Manual
7
IA VRD UK.INDD RH 02.06
Parker Hannifin GmbH & Co. KG
Hydraulic Controls Division
1.3. Connection
Connect unit in accordance with terminal connec-
tion diagram on page 9. The supply voltage for the
unit at terminals 26bd = 0V and 32bd = + UB is 18V
to 30VDC, residual ripple ≤ 10%.
Output stages are electronically protected against
short circuit and excess current. The amplifiers
should be protected with a quick-acting preliminary
fuse (see technical data). Connection of solenoids
is made at teminals 22bdz and 28bdz for solenoid
A, terminals 24bdz and 30bdz for solenoid B. Ter-
minals bdz are bridged on the amplifier. Connection
should, however, be made to all three terminals on
account of the current carrying capacity.
If no electrical isolation of the logic inputs or outputs
is required, terminal 26bd must be bridged to termi-
nal 2d and terminal 32z to terminal 32bd.
General
Devices from the VRD350/VRD355 series are class
A equipment and thus only suitable for industrial
surroundings.
The distance between a source of interference
(device emitting interference) and an interference
sink (a device under the influence of interference)
is of decisive importance. The interfering field of the
source reduces the greater the distance between
this and the sink. In other words, the closer a device
is placed to a source of interference, the greater the
incidental amplitudes. For this reason, there should
be a minimum gap of 0.25 m between the amplifiers
and strong sources of interference.
The following devices are to be regarded as strong
sources of interference:
• Switching power supply units
• Frequency converters
• Drive modules
• Mains filters with wiring (even if screened)
• AC/DC commutator motors
• Motor cables (even if screened)
• Switched inductances, even when anti-inter-
ference measures have been taken (solenoid
valves, contactors, relays, brakes, etc.)
One of the most common input points is the wiring.
This influence can be minimised. Interfering cables
should therefore be laid at least 0.25m away from
cables susceptible to interference. Parts of the
amplifier wiring may be susceptible to interference
(command signal, actual value, solenoid cables,
etc.). Parallel laying of cables is very critical. The
necessary distance has to be increased if cables
are laid parallel over longer distances (> 10 m).
The influence is least when cables cross, particu-
larly if this is at an angle of 90°. Nor should cables
susceptible to interference ever be laid parallel to
motor cables, in particular over longer distances,
and must always cross these at an angle of 90°.
However, interference can also arise from cables in
the amplifier wiring system, in particular solenoid
cables.
Examples of devices which are particularly sus-
ceptible to interferences:
• Office PC’s
• Sensors with small output voltages
• Proximity switches (capacitive)
• Audio equipment (TV, Hi-Fi, radio, etc.)
• Devices which do not comply with EMC guide-
lines.
The assembly contains electronic
components. Incorrect handling or
operation can lead to damage through
electrostatic discharge (ESD). Only
trained personnel should work with the unit. All
safety instructions must be observed. If the card is
disconnected whilst the power supply is still dam-
age may result. Avoid such actions at all cost.

8
IA VRD UK.INDD RH 02.06
Digital Power Amplifier
Series VRD350 and VRD355Installation Manual
Parker Hannifin GmbH & Co. KG
Hydraulic Controls Division
Special Notes on Wwiring and Electrical Cabi-
net Design
The following rules and tips by no means claim to
be complete. Since various electronic components
are used in a variety of different ambient conditions,
these guidelines only represent a compromise. The
actual design of the wiring also depends on the
interference emission and resistance to jamming
of the individual components.
• Use screened and twisted pairs of cables for
the solenoid connections. The screen must be
earthed (PE) at both ends. The capacity should
be 120pF/m. Cables must be ≥ 1.5mm² for a
length up to 100m and ≥ 2.5mm² for a length
over 100m.
• Digital signal lines are to be connected at both
ends to PE with a good conductivity. Command
signal and actual value connections should have
screened and twisted cables. These analog
signal lines are to be connected to earth at
both ends with a good potential equalisation.
The screen connections should be made over
a large area.
• In environments with great interference, use
doublescreened cables for command signal
and actual value connections. The inner screen
is only earthed at one end, the outer screen at
both ends.
• In the event of low-frequency interferences
on the analog signal lines (measured value
fluctuations), the screen should be connected
at one end. However, a corresponding potential
equalisation is preferred. (See also following
point)
• The reference point for command signal and
actual value signals is analog 0V (terminal 26z).
All setpoint and actual value transmitters are to
be connected to this terminal so as to avoid zero
shifts and incorrect measurements.
• When replacing older devices, the non-fused
earthed conductor (PE) should be connected
to terminal 18d or 18b. If ripple voltages oc-
cur, connect 16b or 20b to PE. In this case the
connection to 18bd must be removed. (But:
preferably make a potential equalisation!)
• Use only cables with a Cu screening grid and
a covering of > 85% whenever possible. Avoid
screening films.
• The screen may not be interrupted along the
entire length of the cable. If contactors, safety
switches, chokes, etc. have to be used in the
wiring, the installation of a metallic housing with
a high HF attenuation may be necessary.
• Screen terminals are to be connected over a
large area to the screen rail.
• The screen rail is to be installed close to the
cable duct in the electrical cabinet.
• The metallic parts of the electrical cabinet
are to be connected with high conductivity on
large areas. Avoid painted surfaces. Make the
desired connection with mechanical aids such
as scratch plates if necessary. The doors are
to be connected to the cabinet via the shortest
possible homogeneous tapes (multiple).
• Solenoid valves, contactors, relays, brakes, etc.,
are to be suppressed directly at the respective
coil. Suitable suppression devices are, for ex-
ample, RC networks, diodes or varistors.
• Analog and digital signal lines should preferably
enter the electrical cabinet from one side.
• Unscreened lines of an electric circuit are to be
twisted.
• Auxiliary wires are to be earthed at both ends.
• Avoid unnecessarily long lines. This keeps the
coupling inductances and capacities small.
• Wiring should preferably not be free in the cabi-
net. Cables, including auxiliary cables, should
be laid as close as possible to mounting plates
and the cabinet housing.
• In the event of an inadequate potential equalisa-
tion between the screen connections, a balanc-
ing conductor > 10 mm² should be laid parallel
to the screen to reduce the screen current. A
multiple connection of the screen to the cabinet
casing and thus PE is generally possible. A mul-
tiple connection of the screen is also permissible
outside the cabinet.
• If filters are fitted, these should be installed
close to the source of interference and with a
good surface contact on the cabinet or mounting
plate.
• If converters are used, converter filters must be
provided. Variable speed motors may have to be
connected using screened lines.
• All further instructions of the converter manu-
facturer are to be observed.

Digital Power Amplifier
Series VRD350 and VRD355Installation Manual
9
IA VRD UK.INDD RH 02.06
Parker Hannifin GmbH & Co. KG
Hydraulic Controls Division
1.4. Block Diagram; Entire System

10
IA VRD UK.INDD RH 02.06
Digital Power Amplifier
Series VRD350 and VRD355Installation Manual
Parker Hannifin GmbH & Co. KG
Hydraulic Controls Division
Feedback Option
(hardware, only with boards for closed loop systems)

Digital Power Amplifier
Series VRD350 and VRD355Installation Manual
11
IA VRD UK.INDD RH 02.06
Parker Hannifin GmbH & Co. KG
Hydraulic Controls Division
Jumper Field for Actual Value Input
Classification of Application Cases
• Voltage input with terminating resistance R =
600kOhm:
Used for all proportional valves with displacement
transducers with mean voltages 6V and 7,5V.
• Voltage input without terminating resistance:
Used for potentiometric transmitter systems in
which the loop current is limited to smal values.
Linearity of the transmitter signal is maintained.
• Current input with load R = 100Ohm:
Used for all sensors with current output 0...20mA
or 4...20mA.
Terminal Connection Diagrams for the Standard
Feedback Transducers for Position-Controlled
Valves
Line socket Connector assignment
WLL NG10
1 - Output
2 - Supply (+24V)
3 - 0V
4 - not used
D*FS, RLL, WLL NG06
1 - Output
2 - Supply (+24V)
3 - 0V
4 - not used
5 - GND
DUR
1 - Output
2 - Supply (+24V)
3 - 0V

12
IA VRD UK.INDD RH 02.06
Digital Power Amplifier
Series VRD350 and VRD355Installation Manual
Parker Hannifin GmbH & Co. KG
Hydraulic Controls Division
2. Commissioning
2.1. Front Panels
Front panels of VRD350 and ABG35S are identical.
The only difference is the plug connector for the
RS232 interface (only with VRD350).
Before switching the supply voltage on,
the electrical wiring must be checked.
Limit switches must be operational
to avoid uncontrolled movements.
Relevant safety regulations must be observed
carefully. Suitable emergency stop measures must
be taken.
Application, Construction and Operation of
ABG35S
The ABG35S plug-in control unit is used in con-
junction with the VRD355 proportional amplifier.
It can easily be plugged in and removed again
when parameters have been set. Combination of
the VRD355 and ABG35S provides the optimum
solution for price sensitive applications together
with ease of operation, especially where a number
of amplifier cards are used e.g. for applications in
production line machines or multi-axis NC ma-
chines. When the ABG35S is removed, unauthor-
ized access to the set parameters is effectively
prevented.
No additional components of any kind are required
for operation of the ABG35S with the amplifier
card.

Digital Power Amplifier
Series VRD350 and VRD355Installation Manual
13
IA VRD UK.INDD RH 02.06
Parker Hannifin GmbH & Co. KG
Hydraulic Controls Division
2.2. Programming
Programming Instructions for U-, S-, P- and E-Values
Select mode
U1, S1, P1 or E1 can be
selected
Select address
Display contents
e.g.: S2
has the value:
Alter contents
First press key “E“, then
press key “M“ simultane-
ously.
For E-values, press key
“M“ twice.

14
IA VRD UK.INDD RH 02.06
Digital Power Amplifier
Series VRD350 and VRD355Installation Manual
Parker Hannifin GmbH & Co. KG
Hydraulic Controls Division
Transfer contents
Value is transfered. The
previously selected address
appears again.
Programming Instructions for H-Values
(Command Signal Simulation)
Select mode
Select mode U1
Select mode H1
First press key "E", then
press key "M" simultane-
ously.
Select address
Display, alter, transfer
contents
Select new address or return to mode U1 with the "M"-key.
Basic Settings
All parameters are preset ex-works according to the
intended application of the amplifier. This setting
depends on the type of amplifier (see also type
code). This basic setting can be recovered from
memory by pressing the 4 keys at the same time up
to 10 seconds after the supply voltage is switched
on. During recovery the display shows “HHH“.
After leaving H mode, auxiliary com-
mand signals are no longer utilized but
remain in the background. They must be
set back to zero after commissioning.
After supply voltage is disconnected, H parameter
settings are lost.
H1 or H2
Same procedure as for U, S and P-values. See
previous page
Setting parameters does not alter the preset values.
Customized parameters are overwritten by the re-
covery operation. Further information on adjusting
the basic settings can be found in the instructions
for the control program PROVRD 350/355.

Digital Power Amplifier
Series VRD350 and VRD355Installation Manual
15
IA VRD UK.INDD RH 02.06
Parker Hannifin GmbH & Co. KG
Hydraulic Controls Division
2.3. Block Diagram; Open Loop Control
(Software functions)
Open loop
Parameter functions:
U-parameter: display of internal measured values
S-parameter: internal command signals and ramps
H-parameter: auxiliary parameters
P-parameter: operating parameters
E-parameter: extended parameters (factory setting)

16
IA VRD UK.INDD RH 02.06
Digital Power Amplifier
Series VRD350 and VRD355Installation Manual
Parker Hannifin GmbH & Co. KG
Hydraulic Controls Division
Closed Loop
(only with boards for closed loop systems)
Closed loop
Parameter functions:
U-parameter: display of internal measured values
S-parameter: internal command signals and ramps
H-parameter: auxiliary parameters
P-parameter: operating parameters
E-parameter: extended parameters (factory setting)

Digital Power Amplifier
Series VRD350 and VRD355Installation Manual
17
IA VRD UK.INDD RH 02.06
Parker Hannifin GmbH & Co. KG
Hydraulic Controls Division
External Closed Loop
(only with boards for closed loop systems)
External closed loop
Parameter functions:
U-parameter: display of internal measured values
S-parameter: internal command signals and ramps
H-parameter: auxiliary parameters
P-parameter: operating parameters
E-parameter: extended parameters (factory setting)
Parameter settings:
E14 ≥ 1→ external closed loop if
E2 = 1→ loop control active without safety function
E2 = 4→ loop control active with safety function

18
IA VRD UK.INDD RH 02.06
Digital Power Amplifier
Series VRD350 and VRD355Installation Manual
Parker Hannifin GmbH & Co. KG
Hydraulic Controls Division
Remote Loop Control
(only with boards for closed loop systems)
Remote loop control, external closed loop E2 = 2
Parameter functions:
U-parameter: display of internal measured values
S-parameter: internal command signals and ramps
H-parameter: auxiliary parameters
P-parameter: operating parameters
E-parameter: extended parameters (factory setting)

Digital Power Amplifier
Series VRD350 and VRD355Installation Manual
19
IA VRD UK.INDD RH 02.06
Parker Hannifin GmbH & Co. KG
Hydraulic Controls Division
Bypass Controller
(only with boards for closed loop systems)
Bypass controller
Parameter functions:
U-parameter: display of internal measured values
S-parameter: internal command signals and ramps
H-parameter: auxiliary parameters
P-parameter: operating parameters
E-parameter: extended parameters (factory setting)

20
IA VRD UK.INDD RH 02.06
Digital Power Amplifier
Series VRD350 and VRD355Installation Manual
Parker Hannifin GmbH & Co. KG
Hydraulic Controls Division
2.4. Diagnosis
Test Sockets
The sockets for IA and IB can be used to measure
the solenoid currents independently. The volt-
age at the socket is roughly proportional to the
solenoid current. The voltage is around 1V at 1A.
At the socket S6 for the sum total of both analog
command signals (SW5 and SW6), the measured
value appears according to the input signals. At
the socket for the actual value (A), the measured
value is proportional to the actual value signal. The
measured value is analogous to display U11.
Internal Diagnostic Parameters (U-Parame-
ters)
Internally computed values can be displayed on the
7-segment display during normal operation and to
aid commissioning and trouble shooting. Values
should be interpreted as voltage or current with a
resolution standardised in the display at 10mV to
9.99V. The relevant position in the software func-
tions can be taken from the block diagrams. For
U1 Command signals
Display
in V
U2 Value after the ramp generator
U3 Value after the linearisation table
U4 Value after amplifier gain adjustment
U5 Signal to solenoid A
U6 Signal to solenoid B
U7 Solenoid A current Display
in mA or A
U8 Solenoid B current
U9 Total current solenoid A + solenoid B
The following values are available in the basic
version:
Further outputs are available with the feedback
option card:
U10
Command signal, reference input variable
Display
in V
U11 Feedback value controlled variable
U12 Control difference (error)
U13 Controller output (correcting variable)
Note
Parameter setting and diagnostics only possible
for VRD355 using ABG35S.
Only trained staff should make pa-
rameter changes. The drive should
be switched off whilst adjusting para-
meters.
2.5. Parameters
S-Parameters
Command signals and ramp times are adjusted by
means of S-Parameters. They may be set during
normal operation and the alteration is immediately
effective.
Display
S1...S4 Command signals as voltage 0...9.99V
S5...S8
Ramp times in seconds
(increment 0.01s) 0...9.99s
(increment 0.1s) 10...39.5s
S5 Ramp from 0 to - (A-Solenoid)
S6 Ramp from - to 0 (A-Solenoid)
S7 Ramp from 0 to + (B-Solenoid)
S8 Ramp from + to 0 (B-Solenoid)
H-Parameters (auxiliary parameters)
Parameters H1 and H2 are used in the commission-
ing phase or in test and measurement sequences
for simple input of command signals (command
signal simulation). This allows a command signal to
be input independent of external inputs (command
signal 5/ command signal 6 or selection of S1 to
S4 and a direction), without requiring additional
external circuitry.
Parameters can be set during operation. Any al-
teration with ⇑ and ⇓ is immediately effective. The
polarity sign shows which of the two output stages
or solenoids the command signal acts on.
Positive sign Solenoid B
Negative sign Solenoid A
All command signals are also additive in the H
mode. This means that when command signals
are input (internally S1 to S4 and externally SW5 to
SW6), these are added to active H-parameters, tak-
ing into account the signs. By switching over from H
1 to H2, or the reverse, it is possible to switch over
to different values - also with opposite sign.
This is only an auxiliary function. Pre-
cise measured values, comparable
with a multimeter, are not possible for
technical reasons.
The enable signal must be present so
that the output stages are active and
current can flow.
This manual suits for next models
2
Table of contents
Other Parker Amplifier manuals
Popular Amplifier manuals by other brands
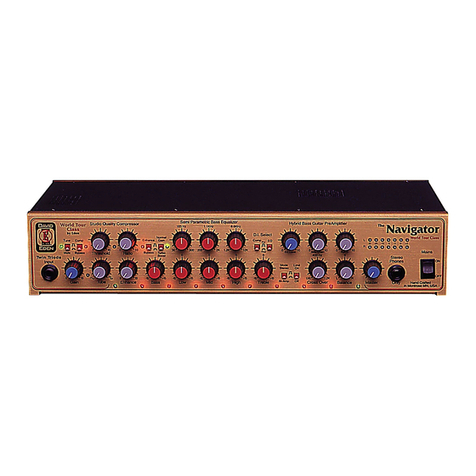
Eden
Eden Navigator WP-100 Operation manual
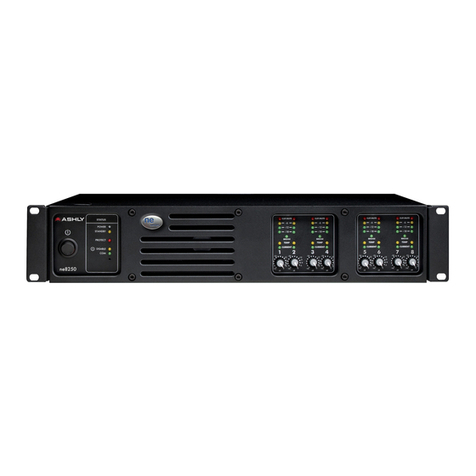
Ashly
Ashly Protea NE8250 Specification sheet
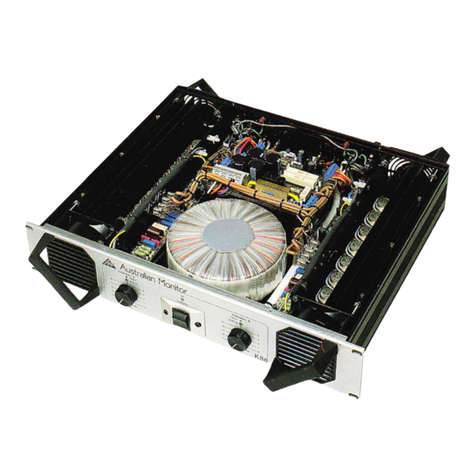
AUSTRALIAN MONITOR
AUSTRALIAN MONITOR K SERIES - brochure

Blue Aura
Blue Aura v40 Blackline manual
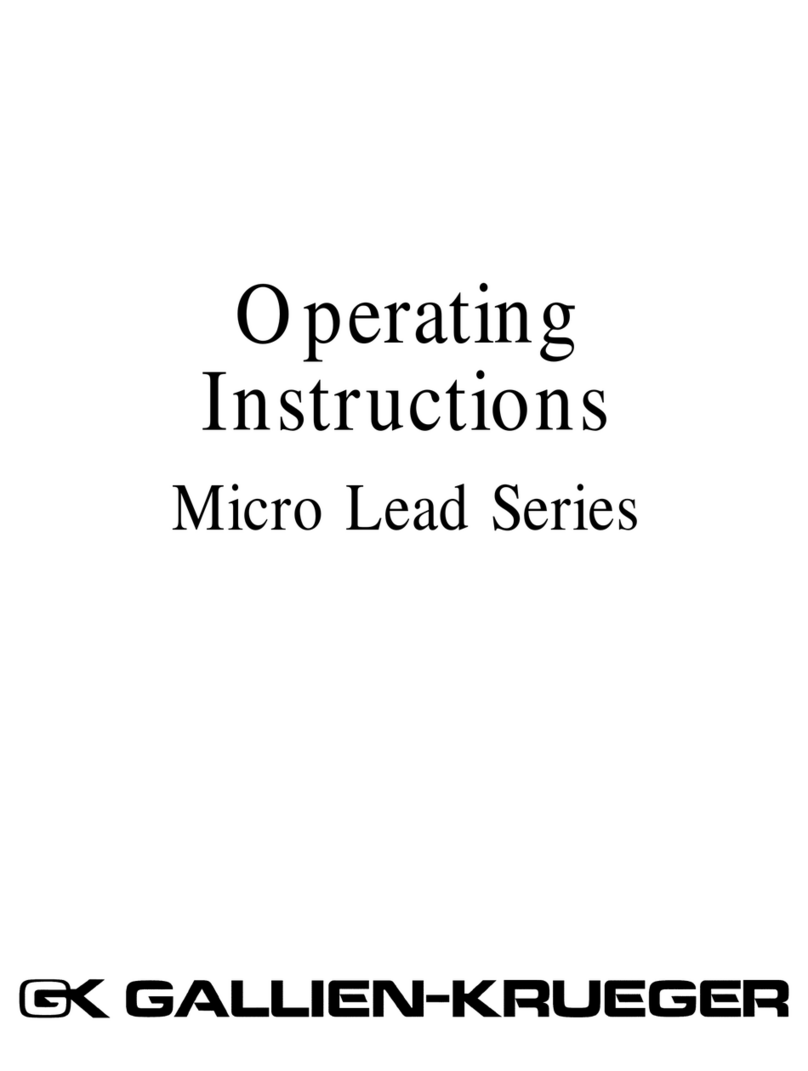
Gallien-Krueger
Gallien-Krueger Micro Lead series operating instructions
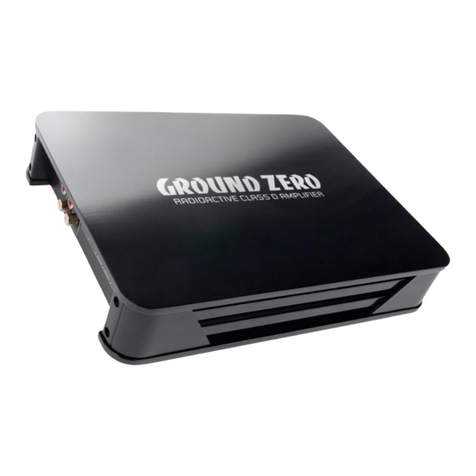
Ground Zero
Ground Zero RADIOACTIVE GZRA 1.600D owner's manual
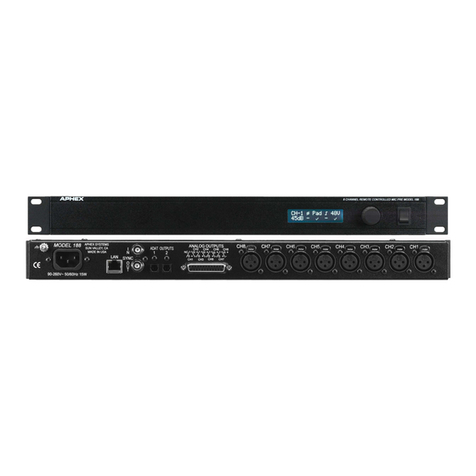
Aphex
Aphex 188 instruction manual
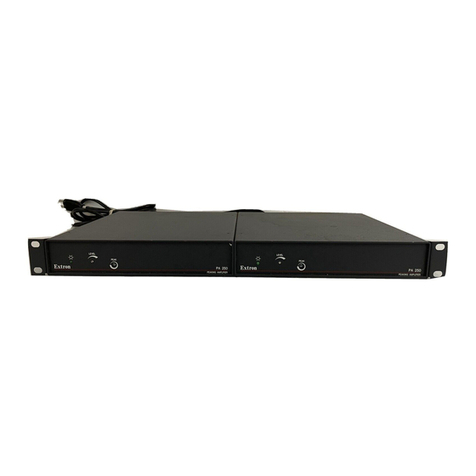
Extron electronics
Extron electronics PA 250 user guide

Carot One
Carot One AUGUSTOLO-TUBE user manual
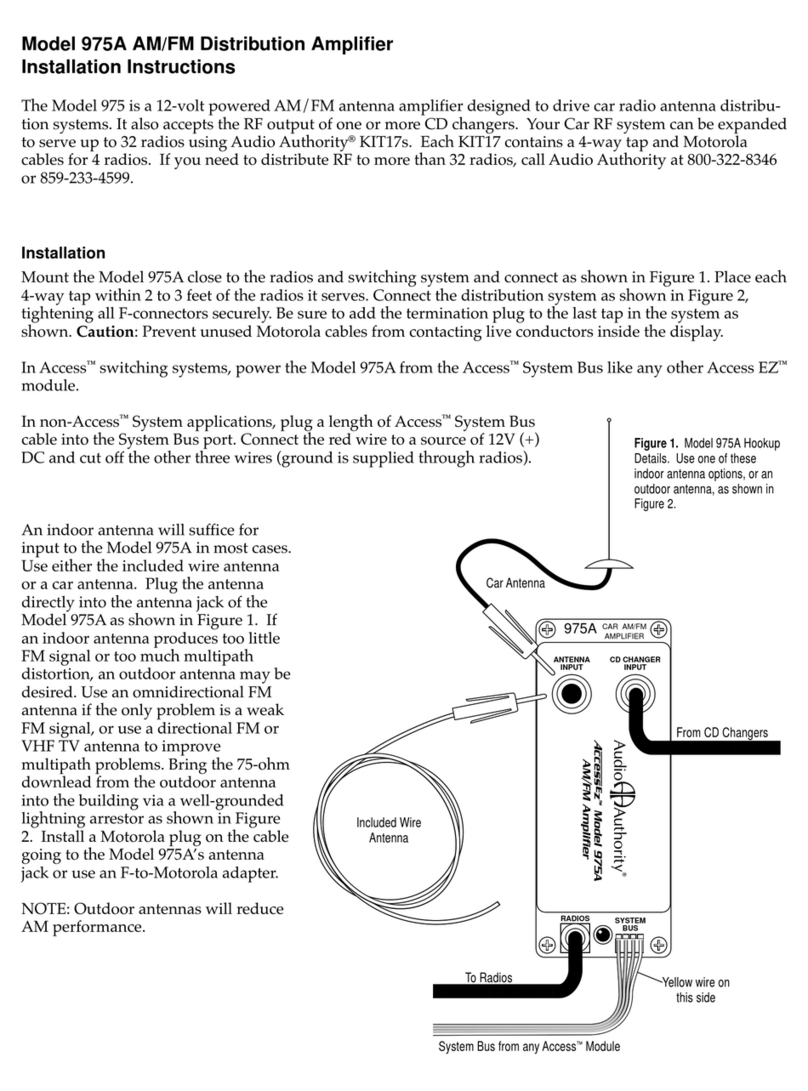
Audio Authority
Audio Authority 975A installation instructions
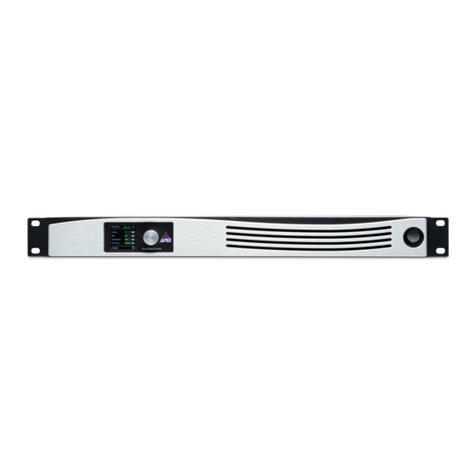
Apex Digital
Apex Digital CloudPower Series Operation manual
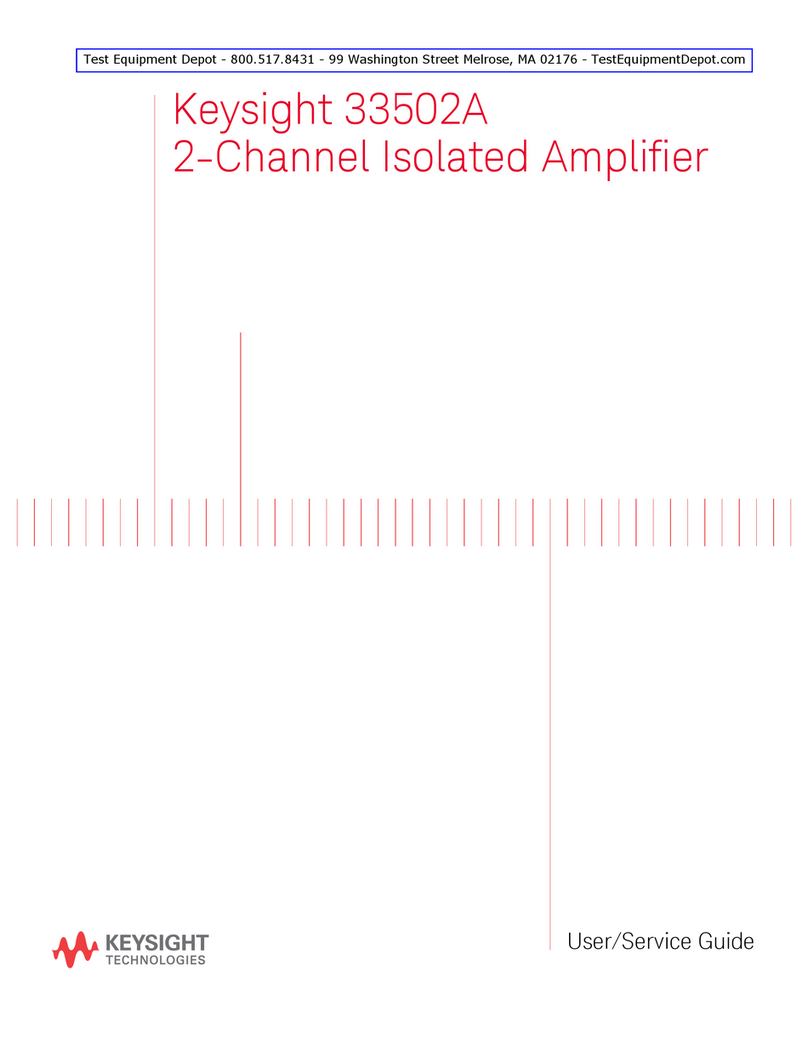
Keysight Technologies
Keysight Technologies 33502A User's & service guide