Pentair Aurora 1070-AP Series Operating instructions

NOTE! To the installer: Please make sure you provide this manual to the owner of the equipment or to the responsible
party who maintains the system.
1070-AP SERIES
HIGH EFFICIENCY CIRCULATOR
INSTRUCTION, INSTALLATION, MAINTENANCE AND REPAIR MANUAL
Part # A-03-333 | © 2012 Pentair Ltd. | 11/19/12

1070-AP SERIES
2
SECTION 2ITEM 1070-AP
DATED NOVEMBER 2012
SUPERCEDES MAY 2010
IMPORTANT NOTE TO INSTALLER:
Read carefully before installing and operating the circulator.
Please leave this manual for the owner’s use.
You are about to install a 1070-AP Series circulator – a high-
efficiency pump from Aurora. 1070-AP Series circulators
are designed for heating and cooling in hydronic, geothermal
or solar systems, circulating water or ethylene or propylene
glycol/water solutions. For pumping domestic (potable) water,
Aurora recommends the use of circulators with bronze body
construction.
The 1070-AP Series circulators are extremely efficient and
quiet and use a state-of-the-art permanently lubricated bearing
system designed for many years of trouble-free operation.
They feature a permanent-split capacitor motor with thermal
protection.
CALIFORNIA PROPOSITION 65 WARNING:
This product and related accessories
contain chemicals known to the State of California to cause
cancer, birth defects or other reproductive harm.
OPERATING LIMITS:
• Maximum operating pressure:
150 psi (1034 kPa)
• Maximum operating temperature:
AllStandardModels–230˚F(110˚C)
ModelsEndingin150–150˚F(65˚C)
• Electrical Rating:
Formodelswith1/6hpmotors:
120V,1Phase,60Hzor208/240V,1Phase,60Hz
For models with 2/5 hp motors:
120V,1Phase,60Hzor
208/240/277V,1Phase,60Hz
When unpacking the circulator, inspect for any damage that
mayhaveoccurredduringtransit.Checkforloose,missingor
damaged parts.
THIS PUMP IS FOR INDOOR USE ONLY.
INSTALLATION:
Before installing the circulator, proper installation practice
recommends a thorough flush of the hydronic system, ensuring
removal of all foreign materials prior to installing the circulator.
Checkthattheflowdirectionofthewaterthroughthehydronic
system matches the arrow on the circulator body. The circulator
is supplied for installation with an up discharge direction.
The 1070-AP Series circulators can be installed to discharge up
or down, horizontally left or right, but the circulator shaft must
remain in the horizontal position. It is recommended that the
circulator be installed such that the terminal box is installed on
the top or side of the motor housing but NOT underneath the
motor housing. The piping can be in a horizontal or vertical run.
Isolation valves should be installed on the discharge and suction
side of the pump to facilitate service.
TERMINAL BOX: If the terminal box is found to
be positioned inconveniently, it can be rotated as required
through 90˚ increments. See examples shown in
“Installation Positions”.
ELECTRICAL WIRING: The electrical wiring must be
installed in strict accordance with the U.S. National Electrical
Code or the Canadian Electrical Code, as well as local codes
and regulations.
a. Electrical installation should be conducted by a qualified
electrician.
b. The motors of 1070-AP Series circulators are designed for
60Hz,1Phase,120Vor240Vserviceonly.(Pleasereferto
the rating label on the circulator’s terminal box to determine
the correct voltage.)
c. Always make sure the electric power is disconnected and
locked out before wiring the circulator.
d. To wire, loosen the screw from the terminal box cover and
remove the screw and cover.
e. Install the appropriate size conduit end to one of the holes
on either side of the terminal box.
f. For 120V models:
• Referring to Diagram 1 on page 2, connect the hot
(black, “L”) and neutral (white, “N”) leads of the supply
wire to the black and white motor leads, respectively,
insidetheterminalbox.Connectthegroundwiretoany
one of the four green ground screws inside the terminal
box(useaminimum18AWGwiresize).
Installation Positions:
Recommended
Optional
Not Recommended

1070-AP SERIES
3
SECTION 2ITEM 1070-AP
DATED NOVEMBER 2012
SUPERCEDES MAY 2010
For 208 / 240 / 277V models:
• Referring to Diagram 2 below, connect the black (“L1”)
and blue (“L2”) leads of the supply wire to the black and
white motor leads, respectively, inside the terminal box.
Connect the ground wire to any one of the four green
ground screws inside the terminal box (use a minimum
18AWGwiresize).
g. Replace the terminal box cover.
The motor is thermally protected for your safety so overload
protection is not necessary. All that is required is a fused
plug or circuit breaker in the power line.
Electrical information can be found on the nameplate of
the motor.
START-UP:
a. Before starting up the circulator, proper installation practice
recommends a thorough flush and draining of the hydronic
system, ensuring removal of all foreign materials. Fill the
system with clean water or glycol solution before starting.
b. Air must be completely vented from the system before
starting up the circulator. If the system is not completely
vented of air and the circulator is allowed to run dry, the
mechanical seal will be damaged.
c. When the system has been completely filled and vented,
only then can the pump be started.
1070-AP Series circulators are fitted with permanently
lubricated ball bearings and DO NOT require lubrication.
Disconnect and lock out the power before servicing.
REPLACEMENT OF PUMP FROM EXISTING
INSTALLATION:
1. If valves have been installed on the suction and discharge
sides of the pump, close them before attempting to remove
the circulator from the system. If no valves have been
installed, it may be necessary to drain the system.
2.For safety, allow water to cool to 100˚F (40˚C) before
draining the system. It is best to leave the drain valve open
while working on the system.
3. Ensure that electric power is disconnected and locked out
before disconnecting the wiring to the circulator. Then,
loosen the screw from the terminal box cover and remove
the screw and cover. Disconnect the supply wires only to
the circulator, leaving the capacitor wires connected.
4. To relieve any residual pressure which may be present in
the pump body, loosen the flange bolts and gently move
the pump body back and forth a bit to allow the pressurized
water to escape.
5. Remove the flange bolts and nuts and then remove the
circulator from the piping.
6.Install the 1070-AP Series circulator where there
will be sufficient room for inspection and service. It is
recommended that isolation valves be installed on both
the suction and discharge sides of the circulator for future
servicing (this eliminates the need for draining the system
when working on the circulator, for example when replacing
the mechanical seal).
7. Install suction and discharge flanges on the pipe ends. The
use of Teflon tape sealer or a high quality thread sealant is
recommended.
8.Pipe strain can be minimized by the use of pipe hangers
near the pump, positioned to support the suction and
discharge piping.
To wire the 1070-AP Series circulator, follow steps c
through g in the “Electrical Wiring” section above, noting
that electrical supply and grounding wires must be rated for
atleast194˚F(90˚C).
PREVENTIVE MAINTENANCE – INSPECTION:
Although Aurora long-life circulators are designed to provide
years of worry-free service, it is good maintenance practice to
inspect the entire hydronic system periodically – including the
1070-AP Series circulator – for potential problems. If there is
any evidence of leakage or damage, repair or replace the pump.
INSTRUCTIONS FOR REPLACING MECHANICAL
SEAL:
(Start by following steps 1 and 2 of section titled
“REPLACEMENT OF PUMP FROM EXISTING
INSTALLATION”.)
)snoitallatsniV772/042/802(2margaiD
)snoitallatsniV021(1margaiD
rofmargaidgniriwlacipyT
rofmargaidgniriwlacipyT
single phase, 120V, 60 Hz power source
a) single phase, 240V, 60 Hz power source, and
b) three phase, 208V / 277V, 60 Hz power source
)snoitallatsniV772/042/802(2margaiD)snoitallatsniV021(1margaiD
rofmargaidgniriwlacipyT
rofmargaidgniriwlacipyT
single phase, 120V, 60 Hz power source
a) single phase, 240V, 60 Hz power source, and
b) three phase, 208V / 277V, 60 Hz power source

1070-AP SERIES
4
SECTION 2ITEM 1070-AP
DATED NOVEMBER 2012
SUPERCEDES MAY 2010
Model
Body:
Cast Iron
(1)
Body:
Bronze
(1)
Flange
Hardware
Kit
(2)
Body
Gasket
(3)
Impeller
(4)
Mechanical
Seal
(5)
Motor
Assembly
120V
(6)
Motor
Assembly
240V
(6)
Motor
Housing
Cap Screw
(7)
1070-AP7
880200-111 880200-141 810120-244
880200-071
880200-033
880200-277
880200-082 880200-182 911117-236
1070-AP8 880200-031
1070-AP9 880200-030
1070-AP10
880200-011 880200-041 810120-204
880200-029
1070-AP11 880200-028
1070-AP12-150
880210-111 880210-141 810120-244 880210-071 880210-035
880210-182 880210-282
911117-152
1070-AP12 880210-082 880210-382
1070-AP13 880200-011 880200-041 810120-204 880200-071 880200-034 880200-082 880200-182 911117-236
1070-AP14-150
880210-111 880210-141
810120-244
880210-071 880210-035
880210-182 880210-282
911117-1521070-AP14 880210-082 880210-382
1070-AP15 880210-411 880210-441
880200-071
880210-037 880210-182 880210-282
1070-AP16 880200-211 880200-241 810120-212 880200-032 880200-082 880210-182 911117-236
1070-AP17 880210-411 880210-441 810120-244 880210-038
880210-182 880210-282 911117-152
1070-AP19
880210-211 880210-241 810120-204
880210-030
1070-AP21 880210-039
1070-AP22 880210-029
1070-AP23 880210-028
1070-AP24 880210-032
1070-AP28
880210-311 880210-341 810120-208
880210-131
1070-AP29 880210-132
1070-AP30 880210-011 80210-041 810120-212 880210-036
1070-AP303 880210-311 880210-341 810120-208 880210-036
1070-AP33 880210-011 80210-041 810120-212
880210-033
1070-AP333 880210-311 880210-341 810120-208
REPLACEMENT PARTS LIST FOR 1070-AP SERIES CIRCULATORS:

1070-AP SERIES
5
SECTION 2ITEM 1070-AP
DATED NOVEMBER 2012
SUPERCEDES MAY 2010
1. Turn off the pump leaving it installed in the line.
2. Ensure electrical power is disconnected and locked out.
3.Close the water supply at the points closest to the pump’s
inlet and outlet.
4. Bleed the water pressure from the pump.
5. Place a pan under the pump to collect the drain water.
6.Whileholdingthemotorbody,unfastenthefourboltsthat
attach the motor to the pump casing (volute). Start with the
two bottom bolts first and remove them, then slowly loosen
the top two bolts. Allow the water to drain from the bottom
of the pump. When the water has finished draining, remove
the two top bolts. Remove the motor straight out from the
volute, being careful of its attached impeller. The motor is
heavy; do not drop it!
7. Locate the snap bushing in the center of the back of the
motor housing and pry it out with a screwdriver. Insert a
straight-blade screwdriver into the snap bushing hole and
into the slot in the end of the motor shaft to lock the rotor.
8.While holding the rotor (step 7), unscrew the plastic
impeller off the motor shaft by hand turning it clockwise
(i.e. opposite to most bolts and nuts!). Place the motor on its
back, with its shaft up.
9. Remove the rotary part of the mechanical seal by gently
pulling it off the shaft. If too tight use two small flat bladed
screwdrivers.Gentlypry itofftheshaftby placing theflat
side of the blades onto opposite sides of the mechanical seal.
10. Remove the stationary part of the seal by gently prying it off
the steel faceplate.
11. Remove any corrosion present on the stainless steel motor
shaft with a nonmetallic brush or scrub pad. Do not use a
wire brush or steel wool.
12. Install the new stationary part of the seal into the faceplate:
first, the rubber cup by firmly pressing it down until it
bottoms, then the ceramic disk. The disk face with a circular
groove should be put against the rubber cup (the visible disk
face should be smooth). Press the disk firmly down until it
too bottoms into the rubber cup. The ceramic disk should be
clean. If needed, wipe it with alcohol and a soft cloth.
13. Install the new rotating part of the seal by gently pushing it,
by hand, onto the shaft (graphite ring first) until its steel cap
stops on the shaft.
Checkthat:
a. The height of the steel cap over the ceramic disk is
between0.33"and 0.35"(8.4mmand8.9 mm). Ifitis
more than 0.35" (8.9 mm), then try pushing it farther
down, carefully, but harder.
b. The graphite disk is pressed against the ceramic disk (by
a spring inside it).
If either (a) or (b) is not happening, then contact
Aurora Pump: phone (630) 859-7000 or e-mail
14. "Lock" again the motor rotor and shaft as per step 7 above,
in order to perform the next step.
15. Fasten the plastic impeller onto the shaft, turning it by hand
counterclockwise until it stops (when it touches the seal's
steel cap). Do not tighten it excessively.
16.Ensure the gasket is properly seated in the pump casing
(volute) gasket groove. Holding the motor body, insert the
impeller straight into the volute. Verify the gasket was not
dislodgedduringinsertionandisstillseatedproperly.Hold
the motor body steady while fastening the four bolts that
attach the motor to the pump casing (volute). Tighten evenly
and diagonally. There should be a small, even gap of about
0.02" (0.5 mm) all around between the motor flange and the
pump casing (volute).
17. Follow the START-UP instructions and check for leaks.

THIS PAGE INTENTIONALLY LEFT BLANK

THIS PAGE INTENTIONALLY LEFT BLANK

WARRANTY
Seller warrants equipment (and its component parts) of its own manufacture against defects in materials and workmanship under normal use
and service for one (1) year from the date of installation or start-up, or for eighteen (18) months after the date of shipment, whichever occurs
first. Seller does not warrant accessories or components that are not manufactured by Seller; however, to the extent possible, Seller agrees to
assign to Buyer its rights under the original manufacturer's warranty, without recourse to Seller. Buyer must give Seller notice in writing of
any alleged defect covered by this warranty (together with all identifying details, including the serial number, the type of equipment, and the
date of purchase) within thirty (30) days of the discovery of such defect during the warranty period. No claim made more than 30 days after
the expiration of the warranty period shall be valid. Guarantees of performance and warranties are based on the use of original equipment
manufactured (OEM) replacement parts. Seller assumes no responsibility or liability if alterations, non-authorized design modifications
and/or non-OEM replacement parts are incorporated If requested by Seller, any equipment (or its component parts) must be promptly
returned to Seller prior to any attempted repair, or sent to an authorized service station designated by Seller, and Buyer shall prepay all
shipping expenses. Seller shall not be liable for any loss or damage to goods in transit, nor will any warranty claim be valid unless the
returned goods are received intact and undamaged as a result of shipment. Repaired or replaced material returned to customer will be
shipped F.O.B., Seller's factory. Seller will not give Buyer credit for parts or equipment returned to Seller, and will not accept delivery of
any such parts or equipment, unless Buyer has obtained Seller's approval in writing. The warranty extends to repaired or replaced parts of
Seller's manufacture for ninety (90) days or for the remainder of the original warranty period applicable to the equipment or parts being
repaired or replaced, whichever is greater. This warranty applies to the repaired or replaced part and is not extended to the product or any
other component of the product being repaired. Repair parts of its own manufacture sold after the original warranty period are warranted for
a period of one (1) year from shipment against defects in materials and workmanship under normal use and service. This warranty applies to
the replacement part only and is not extended to the product or any other component of the product being repaired. Seller may substitute
new equipment or improve part(s) of any equipment judged defective without further liability. All repairs or services performed by Seller,
which are not covered by this warranty, will be charged in accordance with Seller's standard prices then in effect.
THIS WARRANTY IS THE SOLE WARRANTY OF SELLER AND SELLER HEREBY EXPRESSLY DISCLAIMS AND BUYER
WAIVES ALL OTHER WARRANTIES EXPRESSED, IMPLIED IN LAW OR IMPLIED IN FACT, INCLUDING ANY WARRANTIES
OF MERCHANTABILITY OR FITNESS FOR A PARTICULAR PURPOSE. Seller's sole obligation under this warranty shall be, at its
option, to repair or replace any equipment (or its component parts) which has a defect covered by this warranty, or to refund the purchase
price of such equipment or part. Under the terms of this warranty, Seller shall not be liable for (a) consequential, collateral, special or
liquidated losses or damages; (b) equipment conditions caused by normal wear and tear, abnormal conditions of use, accident, neglect, or
misuse of said equipment; (c) the expense of, and loss or damage caused by, repairs or alterations made by anyone other than the Seller; (d)
damage caused by abrasive materials, chemicals, scale deposits, corrosion, lightning, improper voltage, mishandling, or other similar
conditions; (e) any loss, damage, or expense relating to or resulting from installation, removal or reinstallation of equipment; (f) any labor
costs or charges incurred in repairing or replacing defective equipment or parts, including the cost of reinstalling parts that are repaired or
replaced by Seller; (g) any expense of shipment of equipment or repaired or replacement parts; or (h) any other loss, damage or expense of
any nature.
The above warranty shall not apply to any equipment which may be separately covered by any alternate or special warranties.
PERFORMANCE: In the absence of Certified Pump Performance Tests, equipment performance is not warranted or guaranteed.
Performance curves and other information submitted to Buyer are approximate and no warranty or guarantee shall be deemed to arise as a
result of such submittal. All testing shall be done in accordance with Seller's standard policy under Hydraulic Institute procedures.
LIABILITY LIMITATIONS: Under no circumstances shall the Seller have any liability under the Order or otherwise for liquidated
damages or for collateral, consequential or special damages or for loss of profits, or for actual losses or for loss of production or progress of
construction, regardless of the cause of such damages or losses. In any event, Seller's aggregate total liability under the Order or otherwise
shall not exceed the contract price.
ACTS OF GOD: Seller shall in no event be liable for delays in delivery of the equipment or other failures to perform caused by fires, acts of
God, strikes, labor difficulties, acts of governmental or military authorities, delays in transportation or procuring materials, or causes of any
kind beyond Seller's control.
COMPLIANCE WITH LAW: Seller agrees to comply with all United States laws and regulations applicable to the manufacturing of the
subject equipment. Such compliance shall include: The Fair Labor Standards Acts of 1938, as amended; Equal Employment Opportunity
clauses of Executive Order 11246, as amended; Occupational Safety and Health Act of 1970 and the standards promulgated thereunder, if
applicable. Since compliance with the various Federal, State, and Local laws and regulations concerning occupational health and safety,
pollution or local codes are affected by the use, installation and operation of the equipment and other matters over which Seller has no
control, Seller assumes no responsibility for compliance with those laws and regulations, whether by way of indemnity, warranty, or
otherwise. It is incumbent upon the Buyer to specify equipment which complies with local codes and ordinances.
800 Airport Road
North Aurora, Illinois 60542
630-859-7000
www.aurorapump.com
This manual suits for next models
24
Table of contents
Other Pentair Fan manuals
Popular Fan manuals by other brands

ANEMOI
ANEMOI AIRLUX installation manual
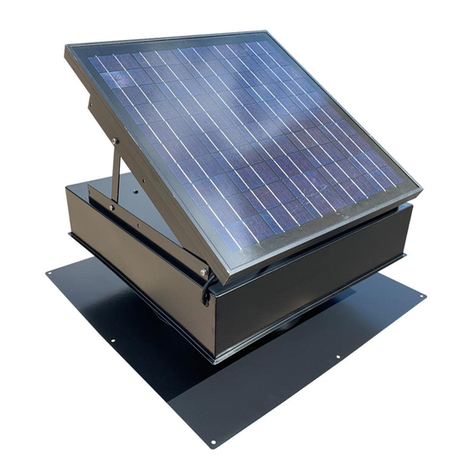
Remington Solar
Remington Solar SF-WF40-BLK manual
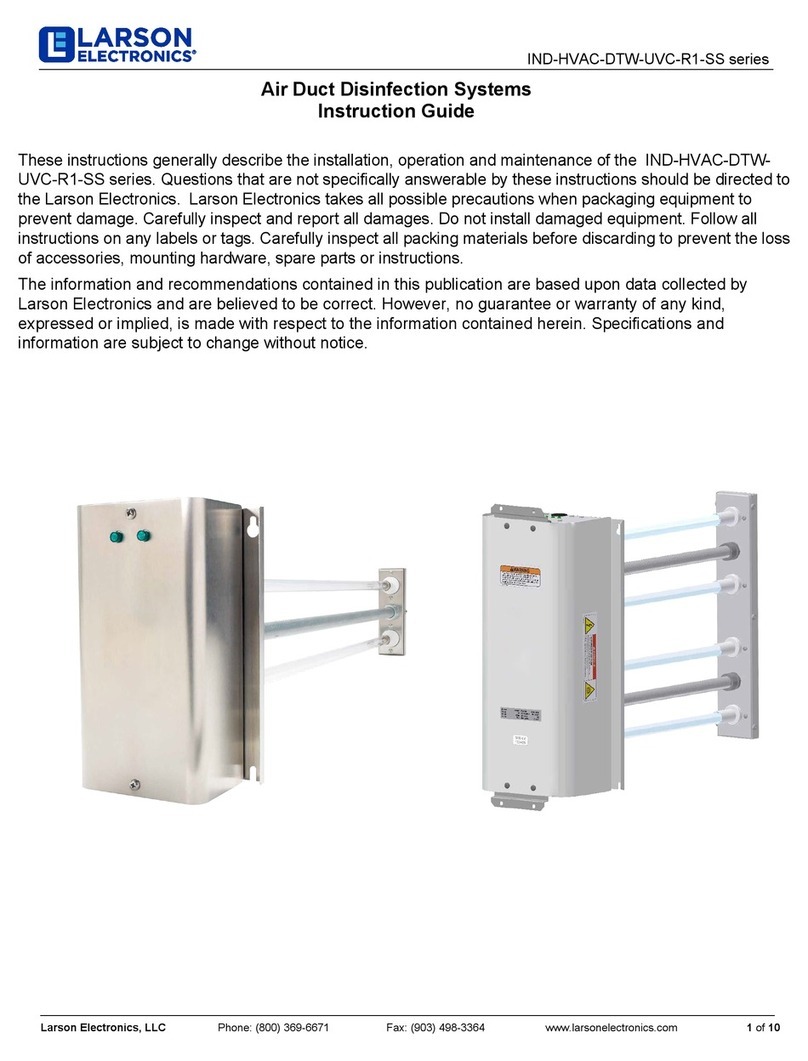
Larson Electronics
Larson Electronics IND-HVAC-DTW-UVC-R1-SS Series Instruction guide

RadonAway
RadonAway RP140 installation instructions

STIEBEL ELTRON
STIEBEL ELTRON LWF FBF 160 Operation and installation

Ruck Ventilatoren
Ruck Ventilatoren EM 100L EC 02 Assembly instruction