Photonic Universe AN Series User manual

1
MPPT Solar Charge Controller
PTR Tracer AN Series (50A/60A/80A/100A 12V/24V/36V/48V)
User Manual
Models:
PTR5415AN
PTR6415AN
PTR8420AN
PTR10420AN

2

3
Important Safety Instructions
This manual contains important information about the safe installation and
operation of the solar charge controller. Please keep this manual for future
reference.
General Safety Information
Read the full instruction manual before you begin the installation.
There are no parts serviceable by users. Do not disassemble or
attempt to repair the controller.
Mount the controller indoors only. Prevent exposure to the elements,
avoid direct sunlight and high temperatures. Do not allow any contact
with water.
Install the controller in a well-ventilated place to ensure adequate
heat dissipation from the controller’s heat sink which may get hot
during operation.
Install appropriate external fuses / breakers as recommended.
Remove all connections between the controller and the battery / PV
array or disconnect the appropriate fuses / breakers before the
controller is installed.
Power connections must remain tight to avoid excessive heating from
a loose connection.

4

5
Contents
1 General Information.......................................................................................7
1.1 Overview .............................................................................................7
1.2 Characteristics.....................................................................................8
1.3 Included Accessories ..........................................................................9
1.4 Optional Accessories.........................................................................10
2 Installation ...................................................................................................11
2.1 General Installation Notes .................................................................11
2.2 PV Array Requirements.....................................................................11
2.3 Wire Size...........................................................................................13
2.4 Relay Instruction................................................................................14
2.5 Mounting ...........................................................................................16
3 Operation.....................................................................................................21
3.1 Indicator ............................................................................................21
3.2 Button................................................................................................21
3.3 LCD Display ......................................................................................22
3.4 Settings .............................................................................................23
4 Protections, Troubleshooting & Maintenance ..............................................25
4.1 Protections ........................................................................................25
4.2 Troubleshooting.................................................................................27
4.3 Maintenance......................................................................................28
5 Specifications ..............................................................................................29
Annex I Dimensions........................................................................................31

6

7
1 General Information
1.1 Overview
Thank you for choosing this Photonic Universe PTR Tracer AN series MPPT solar charge
controller. Equipped with an advanced MPPT control algorithm, multiphase synchronous
rectification technology (MSRT), dual-core processor, negative common ground and an inbuilt
LCD display, this product is a practical and a high-performing solution for your solar system.
Using the MPPT algorithm, this controller can quickly and accurately track the ideal maximum
power point (MPP) of a photovoltaic array in order to obtain the maximum solar energy output.
This significantly improves the efficiency of the solar system. In addition, the current / power
limiting function and automatic power reduction ensure system longevity and reliability.
With the adaptive three-stage charging mode based on a digital control circuit, PTR Tracer AN
series controllers can effectively prolong the life-cycle of battery and significantly improve the
system performance. The load, utility or generator auto-control relays make it easy to assemble
a hybrid power system.
This solar charge controller features comprehensive electronic self-testing and enhanced
electronic protection functions which allow it to operate safely and help to reduce the risk of
damage to system components resulting from installation errors or system faults.
The isolated RS485 interface with standard MODBUS communication protocol and 5V power
supply supports connection of up to 8 controllers in parallel to expand the system. This port is
also compatible with remote display screens and networking devices for monitoring of the
system in many different applications.
Features:
•Advanced MPPT technology & ultra-fast tracking with efficiency greater than 99.5%
•High quality components for excellent performance & conversion efficiency of up to 98.5%*
•Wide MPP voltage range with multiple-peak detection
•Current limiting function to protect the system against solar inputs greater than the nominal
power
•Four charging programs for lead-acid batteries: Sealed, Gel, Flooded and User-defined
•Battery temperature compensation
•Real-time and recorded energy statistics
•Automatic over-temperature power reduction function
•Supports up to 8 units in parallel to expand the system
•Load relay for control of an external load switch
•Two-stage relay disconnect for better control of load power
•Generator auto-start function
•Isolated RS485 with 5VDC/200mA output for connection to devices with MODBUS protocol
•Monitor system or set parameters using the remote screen (MT50, optional), mobile app or
PC software
•CE certification (LVD EN/IEC62109,EMC EN61000-6-1/3)
* PTR10420AN in a 48V system

8
1.2 Characteristics
❶
-
Charging LED indicator
❿
-
Utility/Generator relay ON
❷
-
SELECT
button
⓫
-
Battery voltage measurement
terminals
(4)
❸
-
Fuse
⓬
-
Load control relay (5)
❹
-
Grounding terminal
⓭
-
Utility/Generator relay OFF
❺
-
Cover screw holes M4
⓮
-
PV terminals (6)
❻
-
PV reverse polarity alarm indicator
⓯
-
Battery terminals (6)
❼
-
Generator and load relay switch (1)
⓰
-
ENTER button
❽
-
Remote Temperature Sensor port (2)
⓱
-
LCD display
❾
-
RS485 comm. port (5VDC/200mA) (3)
⓲
-
Fault LED indicator
(1) Generator and load relay is enabled when the switch is ON;
Generator and load relay is disabled when the switch is OFF.
(2) Connection for a Remote Temperature Sensor (RTS to remotely measure battery
temperature; recommended cable distance is less than 20m.
CAUT ON: f the temperature sensor is short-circuited or damaged, the controller
will charge or discharge at the default temperature setting of 25 °C.
(3) When connecting the controller to external devices, only one of the ports can be used;
when using multiple controllers in parallel, the ports are for cascaded use.

9
(4) Connection for a remote battery voltage measurement cable to measure the battery
voltage accurately; recommended distance less than 20m.
(5) Low Voltage Disconnect Voltage (VLVD point is when the relay will turn off;
Low Voltage Reconnect Voltage (VLVR point is when the relay will turn back on after VLVD
is triggered.
(6) Common negative grounding design.
1.3 Included Accessories
Item
Accessory Model Number
Picture
1 Local temperature sensor RT-MF58R47K3.81A
(2P-3.81mm) 1Pcs
2 Battery voltage measurement
terminal 2P-3.81mm 1Pcs
3 Load control relay terminal 2P-3.81mm 1Pcs
4 Diesel generator relay terminal 2P-3.5mm 2Pcs
CAUT ON: The above accessories may be pre-installed in the related ports.
Please open the controller case when checking they are present.
WARN NG: The Battery voltage measurement terminals (11) and Load control
relay terminals (12) should not be mixed up, otherwise the controller may be damaged.

10
1.4 Optional Accessories
Remote Temperature Sensor
TEMP_VS
(2P-3.81mm)
Detects battery temperature for undertaking temperature compensation of control
parameters, the standard length of the cable is 3m. The TEMP_VS connects to the
port ❽on the controller.
NOTE: If the temperature sensor is short-circuited or damaged, the controller
will be charg
ing
or discharg
ing
at the default temperature 25
º
C
.
USB to RS485 cable
PTR-USB
USB to RS485 converter is used to monitor each controller using Solar Station PC
software. The length of cable is 1.5m. The PTR-USB connects to the RS485 Port on
the controller.
Remote Meter
MT50
MT50 displays various operating data and fault info from the system and allows easy
changing of the settings. The information is displayed on a backlit LCD screen, the
buttons are easy to operate, and the numeric display is clearly readable.
WIFI Serial Adapter
EBOX-WIFI
After the controller is connected with the EBOX-WIFI through a standard Ethernet
cable (parallel cable), the operating status and related parameters of the controller
can be monitored by the mobile app software through WIFI signals.
RS485 to Bluetooth Adapter
eBox-BLE-01
After the controller is connected with the eBox-BLE-01 through the standard
Ethernet cable (parallel cable), the operating status and related parameters of the
controller
can be monitored
by the mobile
app
software through Bluetooth signals.
Logger
eLOG01
After the controller is connected with the eLOG-01 through the RS485
communication cable, it can record the operating data of the controller or monitor the
real-time operating status of the controller via PC software.
PT Adapter
PT-ADP-PORT
Manages and communicates with 2 to 8 controllers in parallel.
Please refer to the user manual of PT adapter for more details.
NOTE:
①
for setting and operation of an accessory, please refer to the accessory’s user manual.
②When you connect the above accessories to the controller, only one of the ports can be used.

11
2 Installation
2.1 General Installation Notes
Before you begin installation please read through the entire installation instructions to
familiarise yourself with the installation steps.
Be very careful when working with batteries, especially flooded lead-acid batteries. Wear
eye protection and have fresh water available to wash with in case of any contact with
battery acid.
Keep the battery away from any metal objects which may cause a short circuit of the battery
terminals.
Explosive battery gases may be released out from the battery during charging, therefore
sufficient ventilation is vital.
This controller has been designed for lead acid batteries, with programs for Gel, Sealed
and Flooded battery types. It also supports a User defined battery type for models of lead
acid batteries that need customised settings. In order to choose the right battery program
and charging voltage for your battery please refer to the battery supplier or manufacturer.
Ventilation is highly recommended when mounting the controller in an enclosure. Never
install the controller in a sealed enclosure with flooded batteries! Battery gases from flooded
batteries may cause corrosion and destroy the controller circuits, as well as increase the
risk of explosion.
Loose power connections and corroded wires may result in high heat that can melt wire
insulation, burn surrounding materials, or even cause fire. Ensure tight connections and use
cable clamps to secure cables and prevent them from unnecessary movement.
Battery connecting cables may be wired to one battery or a bank of batteries. This user
manual always refers to a single battery, but it is implied that the battery connection can be
made to either one battery or a group of batteries in a battery bank.
This model of the solar charge controller allows for the installation of more solar charge
controllers in parallel (all controllers should be identical), connected to the same battery
bank, to achieve a higher charging current. Each controller must have its own solar
panel(s). The battery (bank) should be able to accept combined current from all controllers.
Select the system cables according to 5A per 1 mm2cross-section or less current density in
accordance with this manual and all the appropriate regulations and national guidelines.
2.2 PV Array Requirements
(1) Series connection (string) of PV modules
The maximum number of PV modules which can be connected in series and fed into this solar
charge controller can be calculated according to the open circuit voltage (Voc) of the PV
module and the maximum power point voltage (VMpp) of the controller. The following table is
provided for general guidance only; always refer to the exact parameters of your modules to
make sure they are within the allowed range.

12
Battery
voltage
Max
controller
PV input
36cell
Voc<23V
48cell
Voc<31V
54cell
Voc<34V
60cell
Voc<38V
MAX. Best MAX. Best MAX. Best MAX. Best
12V
150V
4
2
2
1
2
1
2
1
200V
4
2
3
1
2
1
2
1
24V
150V
6
3
4
2
4
2
3
2
200V
6
3
4
2
4
2
3
2
48V
150V
6
5
4
3
4
3
3
3
200V
8
5
5
4
5
3
4
3
Battery
voltage
Max
controller
PV input
72cell, Voc<46V 96cell, Voc<62V Thin-Film
Module
Voc>80V
MAX. Best MAX. Best
12V
150V
2
1
1
1
1
200V 2 1 1 1 1
24V
150V
3
2
2
1
1
200V
3
2
2
1
1
48V
150V
3
2
2
2
1
200V
4
3
2
2
2
NOTE: The above parameter values are calculated under standard test conditions (STC - Standard Test
Conditions): solar irradiance 1000W/m2, module temperature 2 °C, air mass 1. .
(2) PV array maximum power
The MPPT controller has a current/power-limiting function. During the charging process, when
the solar panel current or power exceeds the rated charging current or power, the controller
will automatically limit the charging to the rated level. This protects the charging circuits of the
controller and reduces the risk of damage caused by connection of over-specification PV
modules. The current/power-limiting function operates as follows:
Condition 1:
Actual charging power of PV array ≤Rated charging power of controller
Condition 2:
Actual charging current of PV array ≤Rated charging current of controller
When the controller operates under “Condition 1” or “Condition 2”, it will carry out the
charging as per the actual current or power; at this time, the controller can work at the
maximum power point of PV array.
Condition 3:
Actual charging power of PV array > Rated charging power of controller
Condition 4:
Actual charging current of PV array > Rated charging current of controller
When the controller operates under “Condition 3” or “Condition 4”, it will carry out the
charging as per the rated current or power.
WARNING: When the power of the PV array is greater than the rated charging power,
and the maximum open-circuit voltage of PV array is more than 150V for Tracer**15AN or 200V
for Tracer**20AN (at the lowest environmental temperature), the controller may be damaged.

13
If the PV array power is higher than the nominal rated power of the controller and the controller
has to limit the PV power, the battery charging time will be extended accordingly.
WARNING: The controller will be damaged if a PV array is connected to the controller
PV terminals with the right or reverse polarity and the max PV power is more than
1.5 times the rated controller power!
When the PV array is connected to the controller with either the correct or reverse polarity, the
maximum PV array power must NOT exceed 1.5 times the nominal (rated) controller power.
Please refer to the table below:
Item
Rated
Charge
Current
Rated Charge
Power
Max. PV
Power
Max. PV Open
Circuit
Tracer5415AN 50A
625W/12V
1250W/24V
1875W/36V
2
500
W/
48
V
937.5W/12V
1875W/24V
2812.5W/36V
3750
W/
48
V
150V①
138V②
Tracer6415AN 60A
750W/12V
1500W/24V
2250W/36V
3
0
00
W/
48
V
1125W/12V
2250W/24V
3375W/36V
4500
W/
48
V
Tracer8420AN
80A
1000W/12V
2000W/24V
3000W/36V
4000
W/
48
V
1500W/12V
3000W/24V
4500W/36V
6000
W/
48
V
Tracer10420AN
100A
1250W/12V
2500W/24V
3750W/36V
5000
W/
48
V
1875W/12V
3750W/24V
5625W/36V
7500
W/
48
V
200V①
180V②
①At minimum operating environment temperature
②At 25°C environment temperature
2.3 Wire Size
The wiring and installation methods must conform to all national and local electrical code
requirements.
PV Wire Size
Since PV array output can vary due to the PV module size, connection method or sunlight angle,
the minimum wire size can be calculated based on the maximum current (Isc of PV array.
Please refer to the value of Isc in the PV module specification.
When PV modules are connected in series, the Isc is equal to one PV modules Isc. When PV
modules are connected in parallel, the Isc is equal to the sum of the Isc of all the PV modules.
The Isc of the PV array must not exceed the controller’s maximum PV input current. Please
refer to the table as below:
NOTE: All PV modules in a given array are assumed to be identical.
Model Max. PV input current Max. PV wire size*
PTR5415AN 50A 16mm2/6AWG
PTR
64
15AN
60
A
16
mm
2
/
5
AWG

14
PTR8420AN
80
A
25
mm
2
/
4
AWG
PTR
104
20
AN
100A
35
mm
2
/
2
AWG
*These are the maximum wire sizes that will fit the controller terminals.
CAUT ON: When the PV modules connect in series, the open circuit voltage of the PV
array must not exceed 138V at 25°C environment temperature for Tracer**15AN or 180V for
Tracer**20AN.
Battery Wire Size
The battery wire size must conform to the rated current, the reference size as below:
Model
Rated charge current
Battery wire size
PTR5415AN 50A 16mm2/6AWG
PTR
64
15AN
60
A
16
mm
2
/
5
AWG
PTR8420AN
80
A
25
mm
2
/
4
AWG
PTR10420AN
100A
35
mm
2
/
2
AWG
CAUT ON: The wire size is only for reference. If there is a long distance between the PV
array and the controller or between the controller and the battery, larger wires should be used
to reduce the voltage drop and improve performance.
CAUT ON: The battery cable size recommendations assume that the charge controller
is the only device connected to this cable (no inverter connected to the same cable etc .
2.4 Relay nstruction
Utility/Generator Relay and Load Parameter
Rated Value: 5A/30VDC
Maximum Value: 0.5A/60VDC
1) Control the utility/generator ON/OFF via the utility/generator relay
Utility/Generator start-up Voltage (VON =Under Voltage Warning Voltage (VUVW
Utility/Generator stop Voltage (VOFF = Under Voltage Warning Recover Voltage (VUVWR
Low Voltage Disconnect Voltage (VLVD
Battery Voltage (VBAT
Utility/Generator activates:
VBAT < VON
Utility/Generator deactivates:
VBAT > VOFF
CAUT ON: The VON and VOFF can only be set via the PC software, for the Battery
Control Voltage Parameters refer to chapter 3.4 Settings.

15
2) Control the first and second load disconnection
The controller can disconnect different classes of loads in two stages, leaving the most
important loads connected for longer to allow them to discharge the batteries deeper. In such
case, both generator control relay output and load control relay output of the controller will
need to be used:
-The generator control relay will disconnect the first class of loads earlier and
reconnect later;
-The load control relay will disconnect the second class of loads later (allowing it to
discharge the battery deeper and reconnect earlier.
Parameters to note: Battery Voltage (VBAT ; Under Voltage Warning Voltage (VUVW ; Under
Voltage Warning Recover Voltage (VUVWR ; Low Voltage Disconnect Voltage (VLVD ; Low
Voltage Reconnect Voltage (VLVR
First class of loads disconnection (Utility/Generator Relay, normally closed contact):
VBAT≤VUVW: The Utility/Generator Relay normally closed contact will turn OFF the first load
VBAT≥VUVWR: The Utility/Generator Relay normally closed contact will turn ON the first load
2) Second class of loads disconnection (Load Relay):
VBAT≤VLVD: The Load Relay will turn OFF the second load
VBAT≥VLVR: The Load Relay will turn ON the second load
CAUT ON: For the Battery Control Voltage Parameters refer to the chapter 3.4
Settings.
WARN NG: When the system power is off, the utility/generator relay normally
closed contact is closed, please check that this will not cause problems for your setup.
Refer to the below the diagram:

16
2.5 Mounting
WARN NG: Do not reverse the polarity of the batteries. Reverse polarity will damage
the charge controller permanently. Damage caused by reverse polarity is not covered by
warranty.
WARN NG: Risk of explosion! Never install the controller in a sealed enclosure with
flooded batteries! Do not install in a confined area where battery gas can accumulate.
WARN NG: Risk of electric shock! The solar array high voltage can cause serious
shock or injury. Make use of fuses/breakers for isolation or cover the entire solar array prior to
performing any work on the solar charge controller.
CAUT ON:The controller requires at least 150mm of clearance above and below for
proper air flow. Ventilation is required if mounted in an enclosure.
nstallation steps:
Step 1: Determine the installation location and heat-dissipation space
The controller should be installed in a place that allows sufficient air flow through the heat sink
of the controller and a minimum clearance of 150 mm from the upper and lower edges of the
controller to ensure natural thermal convection. Please see the figure below.
Fix the controller firmly in place to a rigid surface using the mounting holes. Non-combustible
surface is recommended.
CAUT ON: f the controller is to be installed in an enclosed box, it is important to
ensure reliable heat dissipation through the box and ventilation.

17
Step 2:Remove the terminal protective cover
Step3:Connect the battery❶(Left) then the PV❷(Right)
NOTE: Disconnect the system in the reverse order, PV first, then battery second.
WARN NG: Do not reverse the polarity of the batteries. Reverse polarity will damage
the charge controller permanently. Damage caused by reverse polarity is not covered by
warranty.
CAUT ON: While wiring the controller do not turn on the breaker or fuse and make sure
that the leads of "+" and "-" poles are connected correctly.
CAUT ON: A fuse or an over-current circuit breaker with the current rating 1.25 to 2
times the rated current of the controller must be installed on the battery cable with a distance
from the battery not greater than 150 mm.
CAUT ON: If an inverter is to be connected to the system, connect the inverter directly
to the battery.

18
One controller:
Battery
voltage
measuring
cable

19
Multiple controllers:

20
Step 4:Grounding
The PTR Tracer AN series is a common-negative controller. If any negative terminal is grounded,
then both negative terminals of PV and battery will be grounded simultaneously. Grounding
these terminals is not necessary for typical operation, but the grounding terminal on the case
must be grounded. This shields the internal components from electromagnetic interference and
reduces risk of electric shock to the user due to the electrification of the shell.
CAUT ON: For common-negative applications, such as vehicles or boats, it is
recommended to use a common-negative controller. If the common-negative system includes
some common-positive equipment where the positive electrode is grounded, the controller may
be damaged.
Step 5:Connect accessories
Connect the remote temperature sensor cable (Model:
TEMP_VS)
Connect the remote temperature sensor cable to the interface ❽and place
the other end close to or on the battery.
CAUT ON: If the remote temperature sensor is not connected to the controller, the
default setting for battery charging or discharging temperature is 25°C without temperature
compensation.
Connect the remote battery voltage measurement cable
Connect the remote battery voltage measurement cable to the interface ⓫and connect the
other end to the battery terminals.
Connect the accessories for RS485 communication (refer to the accessories list).
Step 6:Power on the controller
Turn on the battery fuse/circuit breaker to power on the controller. Check that the unit powers
on and the fault indicator does not stay lit.
CAUT ON: If the controller is not operating properly or the battery indicator on the
controller shows an abnormality, please refer to 4.2 “Troubleshooting”.
Step 7:Connect the solar array
Turn on the solar circuit breaker to connect the solar panels to the controller. If the solar
panels are exposed to light, check that the controller started charging the battery.
Note that the disconnection should follow the reverse order: disconnect the solar array first,
then disconnect the battery from the controller.
This manual suits for next models
4
Table of contents
Popular Controllers manuals by other brands
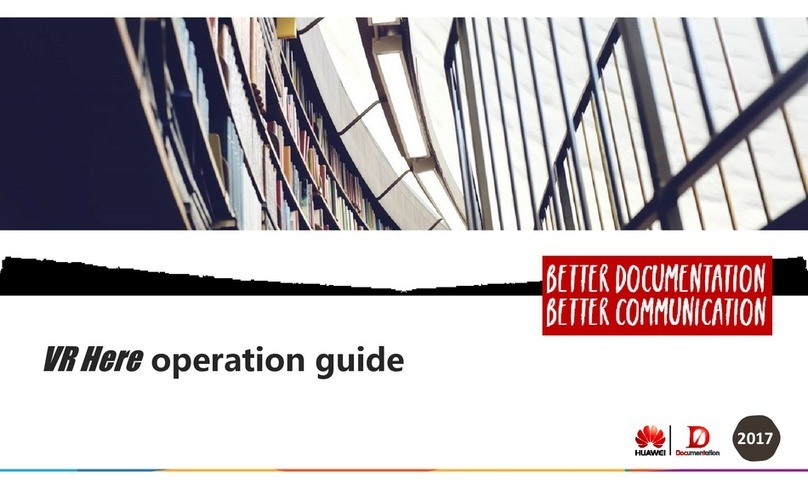
HTC
HTC VIVE Operation guide
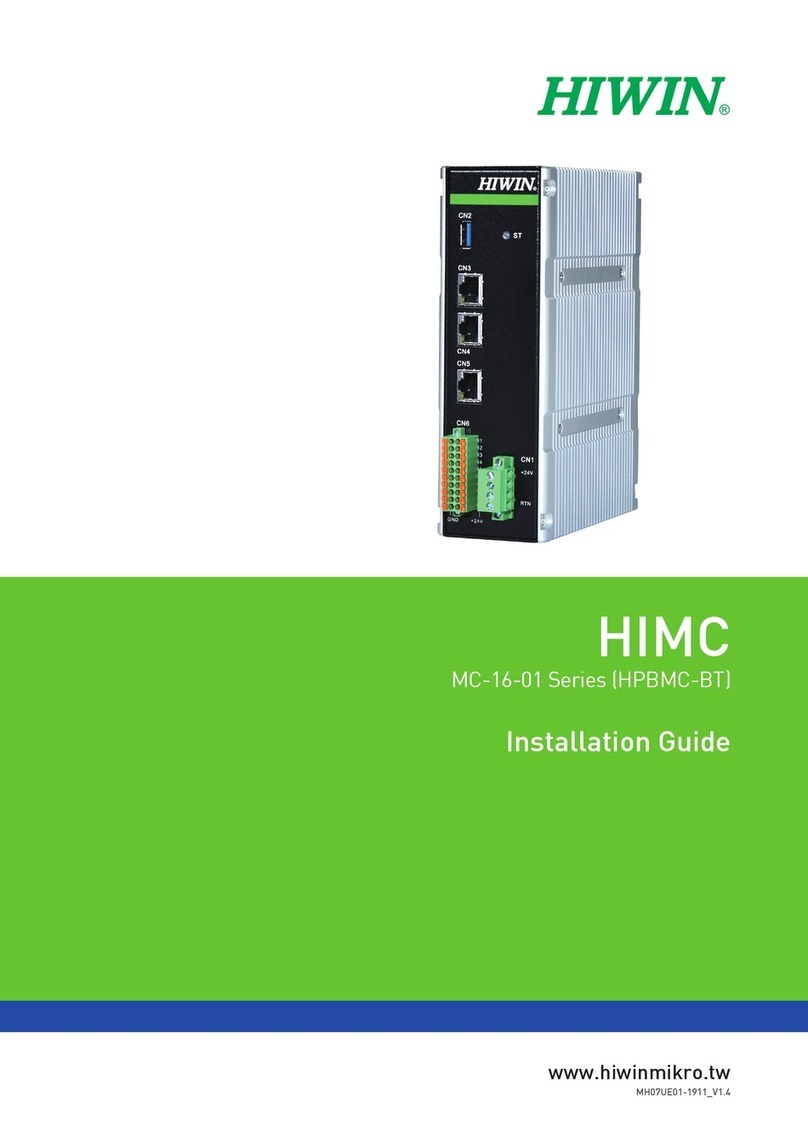
Hiwin
Hiwin HIMC installation guide
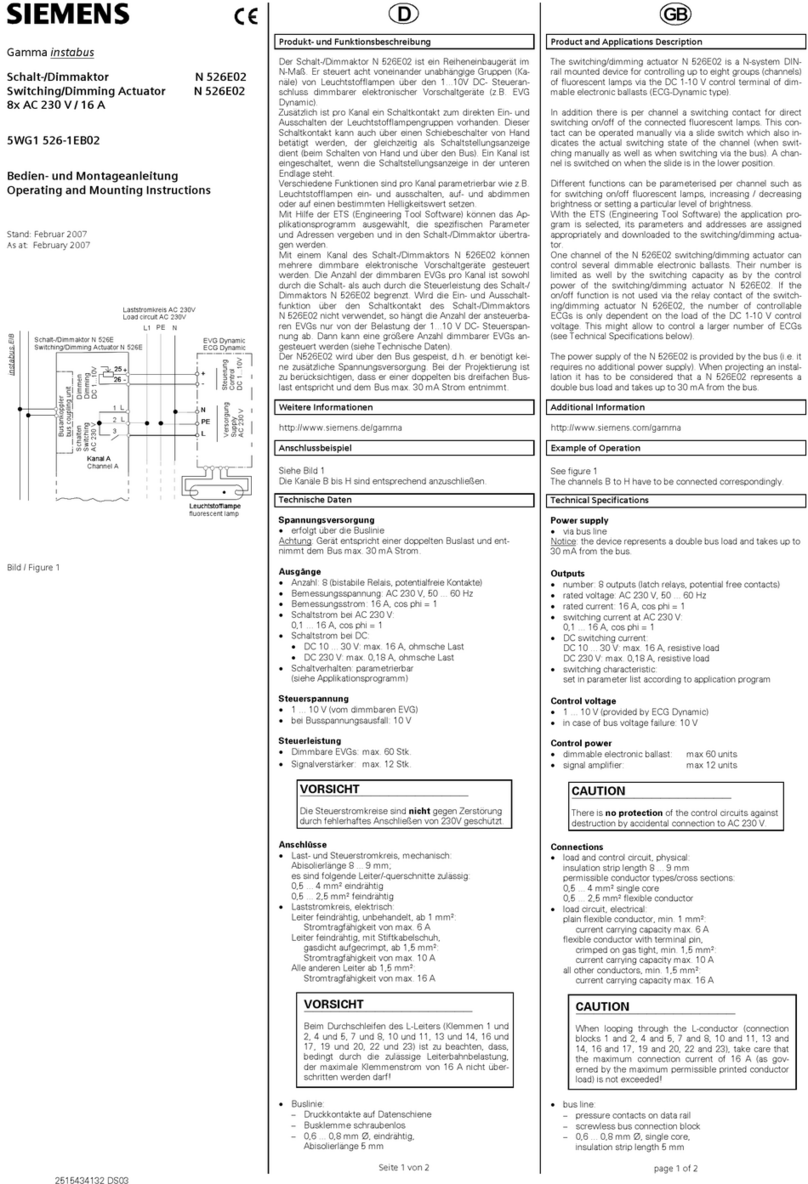
Siemens
Siemens N 526E02 Operating and mounting instructions
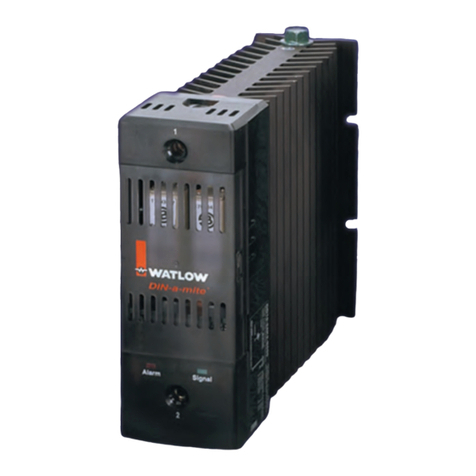
Watlow
Watlow DIN-A-MITE SCR Power Controller Specifications
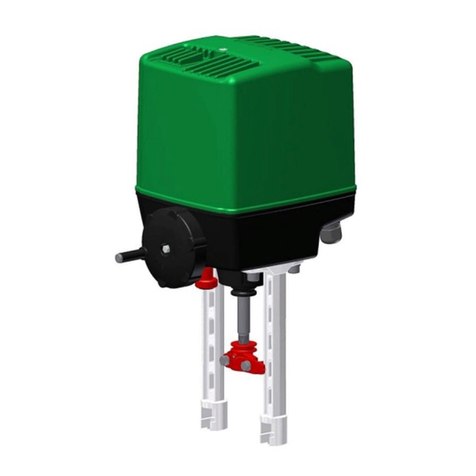
Circor
Circor RTK REact 30 Series Installation and operating instructions
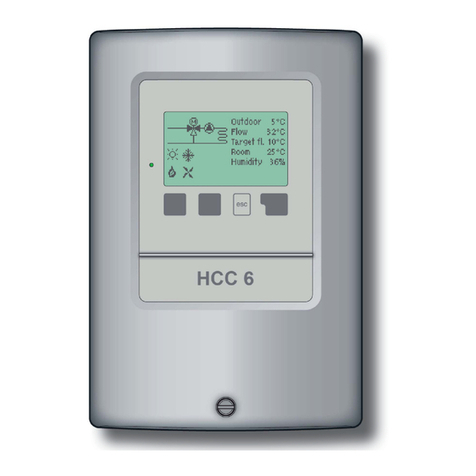
Sorel
Sorel HCC 6 Installation and operating instructions