PMD PMDX-132 User manual

PMDX-132_Manual_10.doc ©2008 Practical Micro Design, Inc. Page 1of 24
17 April 2008 All Rights Reserved
PMDX-132
4-Axis Breakout/Motherboard
for Gecko Stepper Motor Drivers
User’s Manual
Document Revision: 1.0
Date: 17 April 2008
PCB Revision: PCB-466A
Serial Numbers: 23410 and above
PMDX Web: http://www.pmdx.com
9704-D Gunston Cove Rd Phone: +1 (703) 372-2975
Lorton, VA 22079-2366 USA FAX: +1 (703) 372-2977

PMDX-132 User’s Manual PCB Revision: PCB-466A
Document Revision: 1.0 Serial Numbers: 23410 and above
PMDX-132_Manual_10.doc ©2008 Practical Micro Design, Inc. Page 2of 24
17 April 2008 All Rights Reserved
Table of Contents
1.0 Overview....................................................................................................................................3
1.1 Important Safety Information...........................................................................................................................3
1.2 Warranty Summary.............................................................................................................................................3
1.3 Features..................................................................................................................................................................4
1.4 Updates to this Manual......................................................................................................................................4
2.0 Quick Setup Guide ...................................................................................................................4
2.1 Package Contents................................................................................................................................................4
2.2 Assembly steps.....................................................................................................................................................4
2.3 Example Limit Switch Wiring...........................................................................................................................5
2.4 Example Configuration with Daisy-Chained PMDX-122..........................................................................6
3.0 Functional Description and Block Diagrams........................................................................8
3.1 Data Bus.................................................................................................................................................................8
3.2 Control Outputs..................................................................................................................................................8
3.3 Relay Outputs.......................................................................................................................................................9
3.4 Status Inputs........................................................................................................................................................10
3.5 Fault, E-Stop and Motor Disable....................................................................................................................10
3.5.1 Fault Input..................................................................................................................................................11
3.5.2 E-Stop Input...............................................................................................................................................12
3.5.3 Motor Disable Input................................................................................................................................12
3.6 Charge Pump (watchdog)................................................................................................................................12
4.0 Connectors..............................................................................................................................13
4.1 DC (Motor) Power Supply (J1)......................................................................................................................14
4.2 AC Power Supply (J2).......................................................................................................................................14
4.3 Relay Contact Connectors (J3 & J4).............................................................................................................15
4.4 Unregulated Power and Daisy-Chain Output (J5)....................................................................................15
4.5 PC Parallel Port (J6 & J7).................................................................................................................................15
4.6 Status Input Connector (J8)............................................................................................................................17
4.7 Control Output Connector (J9)....................................................................................................................17
4.8 Fault, E-Stop and Motor Disable Connector (J10)....................................................................................18
4.9 Motor Driver Connectors (J11 through J22).............................................................................................18
4.9.1 Disable Signal.............................................................................................................................................19
4.9.2 Step & Direction Signals.........................................................................................................................19
4.9.3 +5V Common...........................................................................................................................................19
4.9.4 Rset Signals.................................................................................................................................................19
4.10 PMDX Expansion Connector (J23)...............................................................................................................19
5.0 Jumpers....................................................................................................................................19
5.1 Output Enable (JP1)..........................................................................................................................................20
5.2 Pin 17 Mode (JP2)..............................................................................................................................................20
5.3 Relay Mode (JP3 and JP4)................................................................................................................................21
5.4 Gecko Step & Direction Common (JP5, JP6, JP7 and JP8)....................................................................21
6.0 Mechanical Specifications......................................................................................................22
7.0 Electrical and Environmental Specifications......................................................................23
Appendix A – Warranty....................................................................................................................24

PMDX-132 User’s Manual PCB Revision: PCB-466A
Document Revision: 1.0 Serial Numbers: 23410 and above
PMDX-132_Manual_10.doc ©2008 Practical Micro Design, Inc. Page 3of 24
17 April 2008 All Rights Reserved
1.0 Overview
This document describes the configuration and operation of the PMDX-132 4-Axis
Breakout/Motherboard. The PMDX-132 interfaces between the parallel port of an IBM-PC style
computer and up to four Gecko stepper driver modules, models G201, G202, G210, G212 and G203V.
This document pertains to the following versions of the PMDX-132:
Circuit Board Revision: PCB-466A (marked on the bottom of the board)
Serial Number Range: 23410 and above
Note that Geckodrive, Inc., the maker of the Gecko stepper motor drives, does not manufacture, sell, or
nor provide technical support for the PMDX-132.
1.1 Important Safety Information
The PMDX-132 is intended for integration by the purchaser into industrial control systems. It is solely
the purchaser's responsibility to assure that the system is configured in a manner consistent with
applicable safety requirements. Practical Micro Design, Inc. does not control how this board is integrated
into the purchaser's system and cannot be responsible for guaranteeing the safety of your system.
The PMDX-132 is not guaranteed to be fail-safe. The system into which the PMDX-132 is installed should
provide fail-safe protection and emergency stop capability.
The PMDX-132 contains circuitry that may be connected to dangerous voltages. Care must be taken that
user cannot come in contact with these voltages. An enclosure that allows for modest ventilation, but
prevents intrusion by operator’s hands and foreign objects, especially conductive byproducts of machining
operations, should be utilized with this board. Interlock switches on power circuits should remove
power when the enclosure is opened.
Automated machine tools, into which the PMDX-132 may be integrated, can cause injury. Precautions
should be taken to assure that operators are trained in their proper operation and safety procedures, and
that they are protected from moving parts that may be under remote control and may move
unexpectedly.
This product may not be used in life support or other critical safety applications.
1.2 Warranty Summary
The PMDX-132 is warranted against failure due to defective parts or workmanship for 90 days from the
date of sale. Refer to Appendix A for complete warranty details.
If you have an item requiring service, please see the support page on the PMDX web site
(http://www.pmdx.com) for return instructions.
The purchaser must pay shipping to return the unit to PMDX. We will ship the repaired unit back to you
via ground transportation at our expense. Repairs are normally completed within 10 business days. See
Appendix A for our complete warranty details.

PMDX-132 User’s Manual PCB Revision: PCB-466A
Document Revision: 1.0 Serial Numbers: 23410 and above
PMDX-132_Manual_10.doc ©2008 Practical Micro Design, Inc. Page 4of 24
17 April 2008 All Rights Reserved
1.3 Features
The PMDX-132 has the following features:
PC Parallel Port:
•Buffers signals to/from the PC parallel port
•Allows use of all 8 data bits, 4 control outputs
and 5 status inputs
•Centronics cable connector uses standard PC
printer cable
•Ribbon header for optional cable to 25-pin
“D” connector or devices with compatible
ribbon connectors such as the SmoothStepper
Status Inputs:
•5 each status inputs w/pull-up resistors
•Status signals are isolated and buffered
•LED indicators for each input
Control Outputs:
•4 each general purpose digital outputs
•2 outputs may also drive relays with N.O and
N.C. terminals
•Outputs are isolated and buffered
•LED indicator for each output
Gecko Stepper Driver Interface:
•4 axes of step and direction
•Driver fault sensing
•Buffers signals to drive step & direction inputs
•Selectable +5V or GND step/dir common
•Wire clamp terminals for the current set
resistors
Power Supply Input:
•120 or 240 VAC input for logic supply
•Separate DC supply input for motor drivers
Special Features:
•Pluggable wire clamp terminal strips for I/O
connections from parallel port status and
control signals
•Support for “charge pump”
•Auxiliary +5V supply output
•Power output for optional fan
•Daisy-chain status signal for sharing
E-Stop/Charge Pump with PMDX-122 boards
1.4 Updates to this Manual
Check the PMDX web site for revisions or updates to this manual (http://www.pmdx.com). The latest
revision of this manual is available on the PMDX-132 page (follow the links from the main page).
2.0 Quick Setup Guide
2.1 Package Contents
Each PMDX-132 ships with the following items:
1 each PMDX-132 circuit board
4 each 4-position plug-on terminal strips (use on the Geckodrive modules, not on the
PMDX-132)
6 each Nylon standoffs, 1-1/4” with 4-40 thread (use to mount the PMDX-132 and Geckodrive
assembly to a heat sink plate)
Note that the PMDX-132 ships without plug-on terminal strips for its connectors (J3, J4, J8, J9 and J10).
You will be re-using the terminal strips from the Gecko stepper driver modules for the PMDX-132
connectors as described below.
2.2 Assembly steps
1. Remove the pluggable terminal strips from each of the Gecko stepper driver modules (these should
be 2 sections of 6-pins each)
2. Install the 6-position terminal strips onto the PMDX-132 connectors J3/J4, J8, J9 and J10. Note that
the connectors J3 and J4 are combined into a single 6-position terminal strip.

PMDX-132 User’s Manual PCB Revision: PCB-466A
Document Revision: 1.0 Serial Numbers: 23410 and above
PMDX-132_Manual_10.doc ©2008 Practical Micro Design, Inc. Page 5of 24
17 April 2008 All Rights Reserved
3. For each Gecko stepper driver module, determine the step/direction common reference required:
•Models G201 and G202 without the G901 step multiplier board require a +5V common.
•Models G210 and G212, and the G201 or G202 with the G901 step multiplier board installed can
be configured for either +5V or GND. Look at the “Input Option Header” jumpers and record
the setting.
•Model G203V requires a GND common reference.
4. Take the results from step (3) above and configure the four PMDX-132 jumpers JP5, JP6, JP7 and JP8
to supply to correct common reference to each Gecko drive. See section 5.4 for more information.
5. For each Gecko stepper driver module, plug the 4-pin terminal strip (supplied with the PMDX-132)
onto the Gecko module’s “Phase A” through “Phase D” terminals.
6. Connect each motor to the 4-pin terminal strips on the Gecko stepper driver module
7. Plug each Gecko stepper driver module onto the connectors on the bottom of the PMDX-132.
8. For each Gecko stepper driver module, install the motor current set resistor in the corresponding 2-
pin terminal strip on the PMDX-132. When looking at the PMDX-132/Geckodrive assembly from
the edge as shown in Figure 1, this would be the green 2-pin terminal strip above and to the right of
each Geckodrive module.
9. Install either (a) an emergency stop switch, or (b) a jumper wire from “E-Stop” to “GND” on
connector J10. See section 3.5.2 for more information.
10. The resulting assembly should look similar to Figure 1.
Figure 1– Sample PMDX-132 and Geckodrive Assembly
2.3 Example Limit Switch Wiring
Mechanical switches, in either “normally open” or “normally closed” configurations, or optical interrupter
switches can be used to provide input signals to the PMDX-132. These switches can act as limit switches,
home indicators or other status information. Since the PMDX-132 provides pull-up resistors on the
status inputs (see section 3.4), mechanical switches can be wired directly to the signal pins on J8 and
ground. Note that the examples below show the signals connected to “pin 11” input. The input signals
may be connected to any of the signal pins on J8.
Normally Closed Switches
The left-hand drawing in Figure 2shows an example of “normally closed” mechanical switches. The
switches are wired in series so that the “normal” case is ground (logic low) going into pin 11 of the PC’s
parallel port. When one or more of the switches open, the pull-up resistor on the PMDX-132 provides a

PMDX-132 User’s Manual PCB Revision: PCB-466A
Document Revision: 1.0 Serial Numbers: 23410 and above
PMDX-132_Manual_10.doc ©2008 Practical Micro Design, Inc. Page 6of 24
17 April 2008 All Rights Reserved
logic high into pin 11 on the PC’s parallel port. Any number of “normally closed” switches may be
connected in series to a single input terminal on the PMDX-132.
Figure 2– Example Switch and Optical Interruptor Configurations
Normally Open Switches
The center drawing in Figure 2shows an example of “normally open” mechanical switches. The switches
are wired in parallel so that the “normal” case is +5V (logic high) going into pin 11 of the PC’s parallel
port (due to the pull-up resistor on the PMDX-132). When one or more of the switches close, a logic
low appears on pin 11 on the PC’s parallel port. Any number of “normally open” switches may be
paralleled onto a single input terminal on the PMDX-132.
Optical Interrupter
The right-hand drawing in Figure 2shows an example of an optical interrupter. This example uses the
“+5V Aux Out” from the PMDX-132 to power the sensor. The output signal is connected as an “open
collector” output between the PMDX-132 input pin and ground. When light from the LED strikes the
sensor, the sensor conducts giving a logic low on pin 11 of the PC’s parallel port. When the LED is
“interrupted”, the transistor stops conducting and the PMDX-132’s pull-up resistor gives a logic high on
pin 11. The same basic operation applies to the “reflective” version of sensor, i.e. when the light from the
LED reflects and strikes the sensor, the sensor outputs a logic “low”.
2.4 Example Configuration with Daisy-Chained PMDX-122
The PMDX-132 can be connected to a PMDX-122 in a daisy-chain configuration. This allows the
PMDX-132’s charge pump, E-Stop and Fault circuitry to enable and disable the PMDX-122’s signals. This
configuration also allows the PMDX-122’s E-Stop input to be used as a general-purpose input.
Figure 3shows a typical daisy-chain configuration. This requires two parallel ports in the PC: one for the
PMDX-132 and a second one for the PMDX-122. The PMDX-132 provides power to the PMDX-122 via
the unregulated “fan power” output on connector J5. The PMDX-122 is shown connected to two optical
encoders, with the data bus direction set to “input to PC”. This is just one example of how the daisy-
chained PMDX-122 can be used. Other uses include having the data bus drive Opto-22 relays. Make sure
to set the PMDX-122’s jumpers according to your configuration.
J8
GND
pin11
+5V
AUX
pin12
pin13
pin15
Three "normally closed"
switches in series.
J8
GND
pin11
+5V
AUX
pin12
pin13
pin15
Three "normally open"
switches in parallel.
J8
GND
pin11
+5V
AUX
pin12
pin13
pin15
Optical Interrupter
(slotted or reflective)

PMDX-132 User’s Manual PCB Revision: PCB-466A
Document Revision: 1.0 Serial Numbers: 23410 and above
PMDX-132_Manual_10.doc ©2008 Practical Micro Design, Inc. Page 7of 24
17 April 2008 All Rights Reserved
Figure 3– PMDX-132 with Daisy-Chained PMDX-122
PHASE A
PHASE B
GND
OPTICAL
ENCODER
+5V
JP6
JP4 JP5 JP2
JP1 JP3
GND
+5V
pin 2-9 COM
not EStop/fault
Outputs Enabled
CP-OK & not EStop/fault
pin 2-9 enable
out
OK
DIR
**
always
normal
pin17out
"OK"
E-Stop Mode
normal
signal only
pin2 pin3 COM pin4 pin5 COM pin8 pin9 COMpin6 pin7 COM
RLY
COM
N/C
N/O
J1 J2 J3 J4 J7
J8
J5
J6
J10
J9
GND
GND
pin11
+5V
AUX
OUT
pin12
pin13
pin15
fault
E-Stop
GND
PWR
Alt In
pin17
pin16
pin14
+5V AUX OUT
J12
J11
PHASE A
PHASE B
GND
OPTICAL
ENCODER
+5V
PMDX-122
(on 2nd parallel port)
E-Stop is a
general purpose
digital input
Data bus direction is
"input to PC" for this example.
Set JP1, JP2 and JP5 according
to your configuration.
fan
pwr
chain PC side
ground
J5J6
PMDX-132
(on 1st parallel port)
Outputs Enabled
CP-OK
not EStop
JP1
pin 17 mode
CP-OK
normal
JP2
K1
JP4
K2
off
pin 8
pin 14 off
pin 9
pin 1
relay mode
JP3
J4 J3J8J9J10

PMDX-132 User’s Manual PCB Revision: PCB-466A
Document Revision: 1.0 Serial Numbers: 23410 and above
PMDX-132_Manual_10.doc ©2008 Practical Micro Design, Inc. Page 8of 24
17 April 2008 All Rights Reserved
3.0 Functional Description and Block Diagrams
3.1 Data Bus
The PC parallel port contains an 8-bit data bus. The PMDX-132 buffers the data bus signals between the
PC and the Gecko stepper drivers. The data bus signals are used as step and direction controls to the
stepper drivers as shown in Table 7on page 16. The output buffers may be disabled via the Fault, E-Stop,
or Motor Disable inputs, as well the Gecko stepper driver’s “Error” output and, optionally, the charge
pump circuit. See sections 3.5 and 3.6 for more information.
Figure 4– Block diagram of data bus (step and direction) signals
3.2 Control Outputs
The control signals are isolated and buffered by the PMDX-132. Each control signal output has a 10K
ohm pull-down resistor paralleled with an LED. The pull-down resistor provides a default “logic low”
when the output buffer is disabled (due to E-Stop, fault, etc.). The LED lights when the output is driven
or pulled high. Two of the control signals (pin 1and pin 14) may also drive the two relays. See section 3.3
for more information.
Enable
Dir
Step
+5V
PC Connector
Buffer
Common
Gecko #1
OK (isolated)
(from charge pump)
(Data0) pin 2
(Data1) pin 3
(Data2) pin 4
(Data3) pin 5
(Data4) pin 6
(Data5) pin 7
(Data6) pin 8
(Data7) pin 9
Dir
Step
Common
Dir
Step
Common
Dir
Step
Common
All referenced to PC ground
Gecko #2
Gecko #3
Gecko #4

PMDX-132 User’s Manual PCB Revision: PCB-466A
Document Revision: 1.0 Serial Numbers: 23410 and above
PMDX-132_Manual_10.doc ©2008 Practical Micro Design, Inc. Page 9of 24
17 April 2008 All Rights Reserved
Figure 5– Block diagram of control signals
3.3 Relay Outputs
Two of the control outputs on the PMDX-132 may drive the on-board relays in addition to being general-
purpose outputs (see section 3.2). PC parallel port pin 1 controls relay K1 via jumper JP3, and pin 14
controls relay K2 via jumper JP4. These two jumpers allow the relays to be disabled when the control
outputs are used as “logic only” outputs. The block diagram below shows the block diagram of one of the
relay circuits. The other circuit is identical but uses the second set of reference designators. See section
5.3 for more information on the jumper settings.
Each relay driver circuit has its own LED (in addition to the LED on the control output section as
described in section 3.2). The relay LED lights when the relay is energized (i.e. the “COM” terminal is
connected to the “N/O” terminal).
Figure 6– Block diagram of relay output signals
**
Each of the four
signals have their
own LED and
pull-down resistor
Enable
2.2K
2
1
3
JP2
PC Connector
Buffer
(~Strobe) pin 1
(~AutoFeed) pin 14
(~Init) pin 16
(~Selelct In) pin 17
I
S
O
L
A
T
E
Enable
Buffer
+5V
10K
Isolated Pin 17
(to charge pump)
OK (from
charge pump)
To JP3 (relay K1 control)
To JP4 (relay K2 control)
J9
+5V
+5V Aux
pin 1
pin 14
pin 16
pin 17
GND
Equipment Ground
PC Ground
** **
** **
**
**
**
**
10K
*
*
*
*
*
Each of the four
input signals have
their own pull-down
resistor Always
Enabled
2
1
3
N/C
COM
N/O
J3 or J4
K1 or K2
Relay
Driver
Disable
JP3 or JP4
Relay
Power
Relay K1 Control
or
Relay K2 Control
(from Control Signal
block diagram)

PMDX-132 User’s Manual PCB Revision: PCB-466A
Document Revision: 1.0 Serial Numbers: 23410 and above
PMDX-132_Manual_10.doc ©2008 Practical Micro Design, Inc. Page 10 of 24
17 April 2008 All Rights Reserved
3.4 Status Inputs
Four of the status signals are available as general-purpose inputs: pins 11, 12, 13 and 15. The fifth status
input on the PC parallel port (pin 10) is connected to the Fault and E-Stop circuitry. See section 3.5, for
more information on this signal. Figure 7shows a block diagram of the status input circuitry.
The “Status Input” LEDs are located next to connector J8, just above each of the pin number labels
(“pin 11”, “pin 12”, “pin 13” and “pin 15”). Each LED is “on” when the corresponding input signal is
driven low.
The status signals are isolated and buffered by the PMDX-132. Each status input has a 2.2K ohm pull-up
resistor in series with an LED. The pull-up resistor provides a default “logic high” when the input is not
connected, and also allows the input to be connected to open-collector drivers or mechanical switches to
ground. The LED lights when the input signal is driven low. The optical isolators further act as a low-pass
filter to remove high-frequency noise from the inputs.
NOTE – Due to logic inside the PC, some status inputs are inverted. This means that a logic
“high” output from the PMDX-132 to the PC’s parallel port is read as a “0” in the
status register. Please refer to technical documentation on the PC parallel port or
your control software for more information.
Figure 7– Block diagram of status signals
3.5 Fault, E-Stop and Motor Disable
The Fault, E-Stop and Motor Disable inputs, along with the Gecko stepper driver’s “Error” signals, provide
ways for external circuitry and the Gecko drivers to enable and disable the operation of the PMDX-132.
The following table summarizes the effects of these signals, as well as the charge pump (see section 3.6).
Figure 8shows a block diagram of the Fault, E-Stop and Motor Disable circuitry.
**
Each of these four signals have
their own LED and pull-up resistor
Enable
2.2K
PC Connector
Buffer
(~Ack) pin 10
(~Busy) pin 11
(Paper End) pin 12
(Select Out) pin 13
I
S
O
L
A
T
E
Enable
Buffer
10K
J8
+5V
+5V Aux
pin 11
pin 12
pin 13
pin 15
GND
Equipment Ground
PC Ground
(~Error) pin 15
+5V
10K
10K
10K
EStop/Fault (isolated)
(from E-Stop and Fault circuit)
Always
Enabled Always
Enabled
**
**
**
**

PMDX-132 User’s Manual PCB Revision: PCB-466A
Document Revision: 1.0 Serial Numbers: 23410 and above
PMDX-132_Manual_10.doc ©2008 Practical Micro Design, Inc. Page 11 of 24
17 April 2008 All Rights Reserved
Condition
(signal asserted) Step/Dir
Ouputs Control Outputs Pin 10 state
(to PC) Motor Current
(see section 3.5.3)
E-Stop Disabled
(tri-state) Disabled
(pull-down resistor) Logic High Enabled
Fault Disabled
(tri-state) Disabled
(pull-down resistor) Logic High Enabled
Gecko Stepper Driver “Error”
Signal Disabled
(tri-state) Disabled
(pull-down resistor) Logic High Enabled
Motor Disable Disabled
(tri-state) Disabled
(pull-down resistor) Logic High Disabled
Charge Pump Failure (only when
jumper JP1 is set to “CP-OK”) Disabled
(tri-state) Disabled
(pull-down resistor) Logic Low Enabled
Table 1– Summary of effects from fault sources
Figure 8– Block diagram of E-Stop, Fault and Motor Diable signals
3.5.1 Fault Input
The Fault input provides an interface for external fault detection circuits. This signal is “active low”,
meaning that a logic “low” indicates a fault condition, and a logic high (or floating) means “all is OK”.
Figure 8shows block diagrams of the Fault input circuitry, and Table 1on page 11 shows the effects of the
Fault signal.
The Fault input can be connected to an external “wired-or” configuration of open-collector status signals
or mechanical switches to ground (switch closed means “fault”). All of the external fault signals should be
tied together and connected to the PMDX-132’s Fault input. The Fault input has a 2.2K ohm pull-up
resistor, so the input may be left unconnected when not used. To indicate a fault condition, drive this
input to ground (via either open-collector or TTL-style drivers or mechanical switches).
Some Gecko stepper drivers implement a “fault output” on pin 7. This signal is “wire OR-ed” with the
PMDX-132’s Fault signal so that the Gecko stepper drivers may also signal a fault condition on the
PMDX-132.
NOTE – The PMDX-132’s Fault signal must be either driven high (+5V) or allowed to float in
order for the motor driver’s step inputs to be enabled and the pin 10 status signal to
the PC parallel port to go low (signaling “OK”). If you do not have any fault detection
circuitry, leave the Fault input unconnected.
J10
Fault*
E-Stop
GND
10K
EStop/Fault
(isolated)
(to status
signal buffer)
2.2K
+5V
+5V
Wired-OR
EStop/Fault*
(active low)
DS10
"EStop Active"
100pF
GND
GND
Gecko
Error
Signals
10K
2.2K
+5V
100pF
I
S
O
L
A
T
E
GND
fan pwr
daisy
2.2K
J5
EStop/Fault*
(to JP1 in the
charge pump)
MotorDisable*

PMDX-132 User’s Manual PCB Revision: PCB-466A
Document Revision: 1.0 Serial Numbers: 23410 and above
PMDX-132_Manual_10.doc ©2008 Practical Micro Design, Inc. Page 12 of 24
17 April 2008 All Rights Reserved
3.5.2 E-Stop Input
The E-Stop input provides an interface for external “emergency stop” circuits (see Figure 8on page 11).
This signal is “active high”, such that a logic “high” tells the system to stop, and a logic low means “all is
OK”. The E-Stop input has a 2.2 Kohm pull-up resistor so that the default condition is “E-Stop”.
The E-Stop input should be connected to an external “normally closed” switch (or group of switches all
wired in series). The external switch(es) should be wired between the E-Stop pin and ground, such that
the switch contacts open to signal an emergency stop condition. If this input is not used, it must be
jumpered to ground. The PMDX-132 provides a 2.2K ohm pull-up resistor on the E-Stop input. This
means that the external emergency stop circuit must be capable of sinking 2.7 mA of current when the
switch contacts are “closed”.
The E-Stop, Fault and Motor Disable inputs are combined (logic “OR”) to drive pin 10 on the PC’s parallel
port and to enable or disable the data bus and control output buffers.
NOTE – The E-Stop signal must be grounded (or driven low) in order for the data bus and
control output buffers to be enabled, and for the pin 10 status signal to the PC
parallel port to go low.
When any or all of the E-Stop (active high), Fault (active low), Motor Disable (active low) inputs, or any of
the Gecko driver’s “error” outputs are asserted, the following actions take place:
•The ACK bit (corresponds to pin 10) in the PC’s status register reads as a “1” (to indicate “E-Stop”)
•The LED labeled “Outputs Enabled” (reference designator DS12, along the right-hand edge of the
board) is “off”
•The Fault daisy-chain output on J5 is tri-stated with a weak (10K ohm) pull-down
•The control outputs are tri-stated with a weak (10K ohm) pull-down
•The relays are de-energized
•The data bus outputs to the Gecko stepper drivers are tri-stated
3.5.3 Motor Disable Input
The Motor Disable input allows external circuitry to place the stepper motors into a “minimum torque”
condition. It does so by overriding the “current set” resistors and setting the motor current to “near”
zero. The amount of holding torque while “disabled” will depend on the motors used. This “disable”
function allows for manual operation of the motors by removing most, but not all of the motor torque.
An emergency stop condition is also signaled when Motor Disable occurs. This disables the step and
direction outputs and any controls (such as spindle power) normally turned on by the outputs. Any
controls that need to operate while in “manual” mode must have a manual override.
This input is active low and has a 2.2 Kohm pull-up resistor so that it may be left unconnected when not
used. To disable the motor drivers, drive this input to ground via open-collector or TTL style drivers or
mechanical switches.
NOTE – The Motor Disable signal must be either driven high (+5V) or allowed to float in
order for the motor driver’s step inputs to be enabled and the pin 10 status signal to
the PC parallel port to go low (signaling “OK”). If you do not have any motor disable
circuitry, leave this input unconnected.
3.6 Charge Pump (watchdog)
The charge pump circuit (also called a watchdog circuit) is designed to disable the PMDX-132 and all
stepper motor drivers when the software running on the PC stops working properly. The charge pump
also keeps the PMDX-132 disabled while the PC starts up (i.e. all outputs are disabled until the PC boots

PMDX-132 User’s Manual PCB Revision: PCB-466A
Document Revision: 1.0 Serial Numbers: 23410 and above
PMDX-132_Manual_10.doc ©2008 Practical Micro Design, Inc. Page 13 of 24
17 April 2008 All Rights Reserved
and the CAD/CAM application software is running). It does this by monitoring pin 17 on the PC parallel
port. When this signal is toggling between high and low, the charge pump is “OK”. When pin 17 stops
toggling, the charge pump is “not OK”. Jumper JP1 determines whether the output from the charge pump
is used to enable and disable the control and data bus output buffers (see section 5.1). See Table 1on
page 11 for a summary of the effects of the charge pump circuit.
This charge pump circuit is designed to work with any software that can toggle pin 17 on the PC parallel
port. If your software does not support this feature, configure jumper JP1 to disable the charge pump
circuit (see section 5.1). See section 7.0, Electrical and Environmental Specifications, for information on
minimum charge pump frequency.
NOTE – The state of the charge pump signal is not reflected in the E-Stop and Fault status that
is output on pin 10 to the PC. This is to prevent “lock up” of the software. Mach2/3
CNC software requires that the Emergency Stop signal not be asserted before it will
start generating the “charge pump” signal.
Figure 9– Block Diagram of Charge Pump signals
4.0 Connectors
The PMDX-132 contains the following connectors. Refer to the following sections for details on the pin-
outs for each connector. For all connectors, pin “1” is the pin closest to the reference designator (i.e. J1
pin 1 is the pin closest to the “J1” text on the circuit board). In addition, all connectors have square pads
on pin 1 (look on the bottom of the circuit board).
2
1
3
JP1
+5V
Isolated Pin 17
(from Control
Signal Input)
Charge
Pump
OK
OK (isolated)
(to Data Bus
enable)
I
S
O
L
A
T
E
EStop/Fault*
(from EStop/Fault)
CP-OK
not EStop
2.2K
+5V
(to control
buffer enable)

PMDX-132 User’s Manual PCB Revision: PCB-466A
Document Revision: 1.0 Serial Numbers: 23410 and above
PMDX-132_Manual_10.doc ©2008 Practical Micro Design, Inc. Page 14 of 24
17 April 2008 All Rights Reserved
Connector Description
J1 DC power supply input for stepper drivers
J2 AC power for logic supply
J3 & J4 Relay contact connections
J5 Fan power output and daisy-chain signal
J6 Centronics 36-pin PC Parallel Port
J7 26-pin ribbon header (alternate connection to PC parallel port)
J8 Status input connections
J9 Control output connections
J10 Fault, E-Stop and Motor Disable connections
J11, J14, J17 &
J20 Current set resistor connections for four Gecko stepper drivers
J12 & J13 Connections to Gecko stepper driver #4 (on the bottom of the board)
J15 & J16 Connections to Gecko stepper driver #3 (on the bottom of the board)
J18 & J19 Connections to Gecko stepper driver #2 (on the bottom of the board)
J21 & J22 Connections to Gecko stepper driver #1 (on the bottom of the board)
J23 PMDX Expansion Connector
Table 2- Summary of PMDX-132 Connectors
4.1 DC (Motor) Power Supply (J1)
J1 is a two-position wire clamp screw terminal for the DC power supply input. This power input is used
solely as the motor power for the Gecko stepper driver modules. An LED (DS11) next to the connector
lights to indicate the presence of DC power.
Pin Number Label Description
1POS Positive DC input terminal
2NEG Negative DC input terminal (does not have to be the same
as the PC’s ground reference)
Table 3– DC Power Connector Pin-Out (J1)
WARNING: The voltage connected to the motor power input must conform with the
Gecko stepper driver specifications. Do not exceed 80 volts DC at the
motor power input to the PMDX-132 board.
The power to each driver is fused and equipped with a 470 uF, 100 volt power filtering capacitor as
recommended by Geckodrive.
The PMDX-132 comes equipped with 5 ampere fast blow fuses. You may replace them with fuses for less
current, but do not increase above 5 amperes, even if the Gecko stepper drivers are set for currents
above 5 amperes. The Gecko stepper drivers will draw less than 5 amperes even when providing 7
amperes to the motors. These fuses are 5mm x 20mm fuses rated for 125 volts minimum.
4.2 AC Power Supply (J2)
J2 is a 3-position wire clamp screw terminal for AC power input. It allows the use of either 120 VAC or
240 VAC mains voltage. This power supply input provides power to everything except the stepper
motor drivers (see section 4.1). An LED next to the connector (DS5) lights to indicate the presence of
regulated +5V DC derived from this AC power supply. Note that this LED may glow dimly if AC power
is removed and the board is connected to the PC’s parallel port, however, the PMDX-132 will not
function correctly unless AC power is supplied.

PMDX-132 User’s Manual PCB Revision: PCB-466A
Document Revision: 1.0 Serial Numbers: 23410 and above
PMDX-132_Manual_10.doc ©2008 Practical Micro Design, Inc. Page 15 of 24
17 April 2008 All Rights Reserved
The PMDX-132 provides its own isolated power for the status inputs (see sections 3.4 and 4.6) and
control outputs (see sections 3.2 and 4.7). Therefore, the AC power supply does not require an external
isolation transformer.
Pin Number Label Description
10V Connection for AC mains NEUTRAL input
2 120
VAC Input for use with 120 VAC mains
(leave as a “no connect” for 240 VAC mains)
3 240
VAC Input for use with 240 VAC mains
(leave as a “no connect” for 120 VAC mains)
Table 4– AC Power Connector Pin-Out (J2)
4.3 Relay Contact Connectors (J3 & J4)
J3 and J4 provide connections to the output relay contacts. These contact ratings are specified in section
7.0. These relays may be controlled by two of the control signals, or they may be disabled, depending on
the configuration of jumpers JP3 and JP4 (see section 5.3).
Pin Number Label Description
1N/O Normally open contact
2COM Common center pole
3N/C Normally closed contact
Table 5– Relay Contact Connector Pin-Out (J3 and J4)
4.4 Unregulated Power and Daisy-Chain Output (J5)
The PMDX-132 provides an unregulated 12 to 16 volt DC power output on J5. This output can be used
to power a fan (24 volt fan running “under speed” is recommended), or to power a companion
PMDX-122 board. Note that this power output (and therefore any connected PMDX-122 boards) share
ground with the PC side of the interface isolation barrier.
Pin Number Label Description
1chain Fault signal output, used to daisy-chain to a PMDX-122
2fan pwr Unregulated power output for fan or PMDX-122
3PC side
ground Ground reference on PC side of the isolation barrier
Table 6– Unregulated Power and Daisy-Chain Connector Pin-Out (J5)
4.5 PC Parallel Port (J6 & J7)
The PMDX-132 provides a Centronics-style connector (J6) for connections to a PC’s parallel port. This
allows the use of a standard PC printer cable. The board also provides a 26-pin ribbon cable header (J7).
This header allows the use of a “ribbon cable to 25-pin “D” connector” adapter cable as an alternative to
the standard PC printer cable and the Centronics connector, or a ribbon cable to devices with a
compatible ribbon connector such as the SmoothStepper.

PMDX-132 User’s Manual PCB Revision: PCB-466A
Document Revision: 1.0 Serial Numbers: 23410 and above
PMDX-132_Manual_10.doc ©2008 Practical Micro Design, Inc. Page 16 of 24
17 April 2008 All Rights Reserved
NOTE – Some printer cables do not have good signal shielding. Some cables also omit some of
the status or control signals (such as “~Auto Feed” and “Select Out”, 25-pin “D”
connector pin numbers 14 and 13, respectively). We recommend using cables that
are listed as IEEE-1284 compliant.
Pin Numbers Direction
PC
(note 1) J6
(note 2) J7
(note 3) PC Signal
Name (relative
to the PC) PMDX-132
Signal Comment
1 1 1 ~Strobe out Output “pin 1” and
relay K1 control Isolated and buffered
output
2 2 3 Data 0 out Dir signal to Gecko #1
3 3 5 Data 1 out Step signal to Gecko #1
4 4 7 Data 2 out Dir signal to Gecko #2
5 5 9 Data 3 out Step signal to Gecko #2
6 6 11 Data 4 out Dir signal to Gecko #3
7 7 13 Data 5 out Step signal to Gecko #3
8 8 15 Data 6 out Dir signal to Gecko #4
9 9 17 Data 7 out Step signal to Gecko #4
Buffered signals from the
PC.
10 10 19 ~Ack in E-Stop, Fault and
Motor Disable See sections 3.5.2 and
3.5.1
11 11 21 Busy in Contact Closure “pin
11”
12 12 23 Paper End in Contact Closure “pin
12”
13 13 25 Select Out
(note 4) in Contact Closure “pin
13”
Isolated and buffered
signals into PC, with
internal pull-up resistors
allowing them to directly
sense switch closures to
ground (pin 6 of J8).
14 14 2 ~Auto Feed out Output “pin 14” and
relay K2 control Isolated and buffered
output
15 32 4 ~Error in Contact Closure “pin
15” See contact closure note
above
16 31 6 ~Init out Output “pin 16” Isolated and buffered
output
17 36 8 ~Select In
(note 4) out Output “pin 17” and
charge pump signal
Isolated and buffered
output, see section 3.6 for
charge pump description.
18 – 25 19-30,
33 10-24
(even) Ground Ground
Table 7- PC Parallel Port Connectors (J6 and J7)
NOTE 1 – The PC Pin number column lists the pin numbers as they would appear on the PC’s
25-pin “D” connector when using a standard printer cable.
NOTE 2 – J6 is the Centronics 36-pin connector on the PMDX-132. Only the Centronics pins
listed in the table above are connected to the PMDX-132. All other pins on the
Centronics connector are not connected to the PMDX-132.
NOTE 3 – J7 is the 26-pin ribbon cable header on the PMDX-132.
NOTE 4 – The “~Select In” and “Select Out” signals are named relative to the printer’s point of
view. That is why the “~Select In” is an output from the PC, and “Select Out” in an input.

PMDX-132 User’s Manual PCB Revision: PCB-466A
Document Revision: 1.0 Serial Numbers: 23410 and above
PMDX-132_Manual_10.doc ©2008 Practical Micro Design, Inc. Page 17 of 24
17 April 2008 All Rights Reserved
The following web sites provide information regarding the PC’s parallel port, including pin-outs, signal
names and useful data for software control of the parallel port:
•IBM PC Parallel Port FAQ and tutorial
http://www.pmdx.com/Resources/parallel-port.html
and
http://et.nmsu.edu/~etti/fall96/computer/printer/printer.html
•General information and lots of links
http://www.lvr.com/parport.htm
•If the previous links do not work, go to http://www.pmdx.com (our main web page), click on the
“handy CNC information” link and then look for the links to parallel port information pages
Note that these web links were accurate as of the printing date of this manual. While we expect that
these two sites will remain available at these addresses, it is possible that they will move or disappear.
4.6 Status Input Connector (J8)
The status input connector provides wire clamp screw terminal connections for all of the PC parallel port
status signals except for pin 10. Pin 10 is used to indicate emergency stop and fault conditions to the PC.
See section 3.5.2 for more information on the emergency stop input.
Pin Number Label Description
1AUX
+5V Auxiliary regulated +5V output (referenced to the isolated
ground provided on pin6 of this connector)
2 11 Status input to PC parallel port pin 11
3 12 Status input to PC parallel port pin 12
4 13 Status input to PC parallel port pin 13
5 15 Status input to PC parallel port pin 15
6GND Ground (isolated from the PC’s ground)
Table 8– Status Input Connector Pin-Out (J8)
4.7 Control Output Connector (J9)
The control output connector provides wire clamp screw terminal connections for all of the PC parallel
port control signals.
Pin
Number Label Description
1AUX
+5V Auxiliary regulated +5V output (referenced to the isolated
ground provided on pin6 of this connector)
2 1 Control output from PC parallel port pin 1
3 14 Control output from PC parallel port pin 14
4 16 Control output from PC parallel port pin 16
5 17 Control output from PC parallel port pin 17 (the signal that also
feeds the PMDX-132’s charge pump circuit, see section 3.6).
6GND Ground (isolated from the PC’s ground)
Table 9– Control Output Connector Pin-Out (J9)

PMDX-132 User’s Manual PCB Revision: PCB-466A
Document Revision: 1.0 Serial Numbers: 23410 and above
PMDX-132_Manual_10.doc ©2008 Practical Micro Design, Inc. Page 18 of 24
17 April 2008 All Rights Reserved
4.8 Fault, E-Stop and Motor Disable Connector (J10)
This connector provides wire clamp screw terminal connections for external E-Stop, Fault, and Motor
Disable functions (see section 3.5).
Pin Number Label Description
1Fault* Fault input (active low)
2GND Ground (isolated from the PC’s ground)
3Estop Emergency Stop input (active high)
4GND Ground (isolated from the PC’s ground)
5MtrDis* Motor Disable input (active low)
6GND Ground (isolated from the PC’s ground)
Table 10 – Control Output Connector Pin-Out (J10)
4.9 Motor Driver Connectors (J11 through J22)
These connectors provide for up to four Gecko Stepper Driver modules. Gecko stepper drivers may be
installed on these sets of connectors in any combination. The only restriction is that the step and
direction signals from the PC’s parallel port are hard wired to specific connectors, as shown in Table 7on
page 16.
Driver Number Motor Power Control Signals Motor Current Set
Gecko #1 J22 J21 J20
Gecko #2 J19 J18 J17
Gecko #3 J16 J15 J14
Gecko #4 J13 J12 J11
Table 11 – Motor Driver Connector Groupings
PMDX-132
Pin Number Gecko
Pin Number Description
1 1 Motor Ground (negative connection)
2 2 Motor Power (positive connection)
Table 12 – Motor Power Connector Pin-Out (J13, J16, J19 & J22)
PMDX-132
Pin Number Gecko
Pin Number Description
1 7 Disable
2 8 Direction
3 9 Step
4 10 +5V common for opto-couplers on the Gecko drivers
5 11 Rset (current setting resistor)
6 12 Rset Gnd (current setting resistor)
Table 13 – Motor Control Signal Connector Pin-Out (J12, J15, J18, and J21)
Pins 3, 4, 5 and 6 of the Gecko stepper motor drivers are wired directly to the motor via a pluggable
terminal strip and do not pass through the PMDX-132 board.

PMDX-132 User’s Manual PCB Revision: PCB-466A
Document Revision: 1.0 Serial Numbers: 23410 and above
PMDX-132_Manual_10.doc ©2008 Practical Micro Design, Inc. Page 19 of 24
17 April 2008 All Rights Reserved
4.9.1 Disable Signal
This signal is not present on every Gecko model, and is not connected on the PMDX-132. The
PMDX-132 implements the “motor disable” function by commanding the motor current to a minimum
value using the current setting resistor terminals (see section 3.5.3 for additional information).
4.9.2 Step & Direction Signals
The step and direction signals are hard-wired to specific motor driver connectors (see Table 7on page
16). These signals are buffered on the PMDX-132. However, they are not optically isolated by the
PMDX-132 because the Gecko stepper driver modules have optical isolation on the step and direction
inputs.
4.9.3 +5V Common
The PMDX-132 provides +5 volts for the Gecko step and direction opto-couplers. Your Gecko stepper
drivers should be jumpered for +5VDC common if equipped with a jumper. The Gecko 201 and 202
drives do not have such a jumper and are always configured for +5VDC common, unless they have the
G901 option board installed (which provides a step multiply function).
4.9.4 Rset Signals
These signals are used to connect a current setting (programming) resistor to the Gecko stepper motor
drivers. The resistors are mounted on the PMDX-132 board and internally connected to these terminals
on the Gecko stepper drivers.
4.10 PMDX Expansion Connector (J23)
Provides power and control signals to PMDX accessory boards such as the PMDX-106 Spindle Speed
Controller.
5.0 Jumpers
The PMDX-132 contains eight 3-pin jumpers that determine various aspects of its behavior. Each jumper
has silk screen labels that describe the function of the jumper, and each possible setting. Each jumper
should have a shorting block installed either between pins 1 and 2, between pins 2 and 3, or on some
jumpers the shorting block can be removed. Figure 10 shows the location of all of the jumpers on the
PMDX-132.

PMDX-132 User’s Manual PCB Revision: PCB-466A
Document Revision: 1.0 Serial Numbers: 23410 and above
PMDX-132_Manual_10.doc ©2008 Practical Micro Design, Inc. Page 20 of 24
17 April 2008 All Rights Reserved
Figure 10 –Jumper Locations
5.1 Output Enable (JP1)
This jumper determines when the PMDX-132 outputs are enabled. This controls all of the outputs: step
and direction (i.e. data bus) and control signals. Figure 10 on page 20 shows the location of this jumper.
Setting Label Description
1 to 2 not
Estop Outputs will be enabled whenever an emergency stop or fault condition does not
exist. The “charge pump” is ignored.
2 to 3 CP-OK Outputs will be enable when “charge pump” is in the OK condition AND no
emergency stop or fault condition exists.
Table 14 – “Output Enable” Jumper Settings (JP1)
5.2 Pin 17 Mode (JP2)
This jumper selects which signal is presented on the “pin 17” terminal on connector J9. Figure 10 on page
20 shows the location of this jumper.
Table of contents
Popular Motherboard manuals by other brands
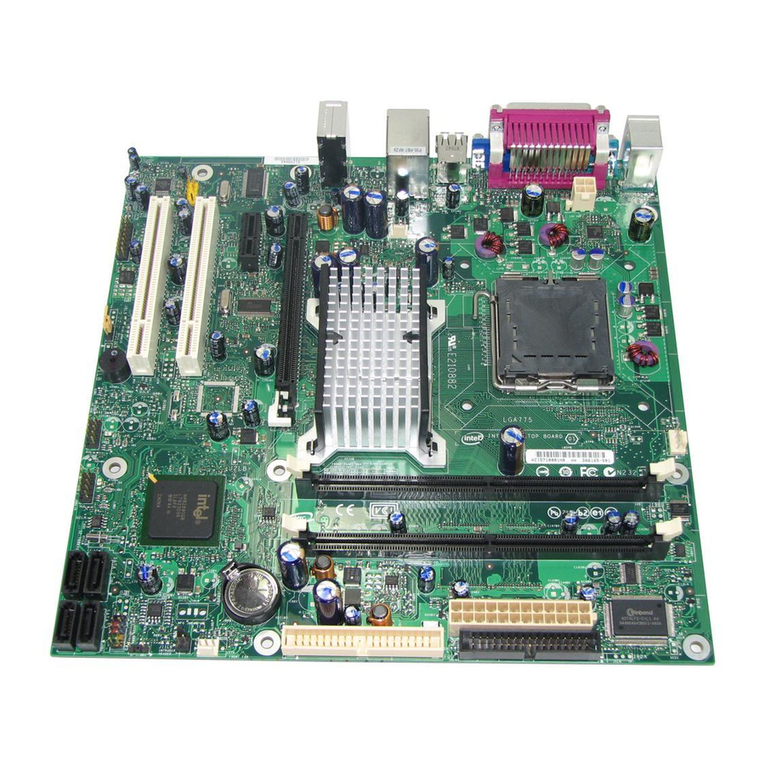
Intel
Intel BLKD946GZISSL - CONROE LGA775 1066 800FSB DR2 A/V Lan SATA mATX 10Pack ACTIVE... Technical product specification
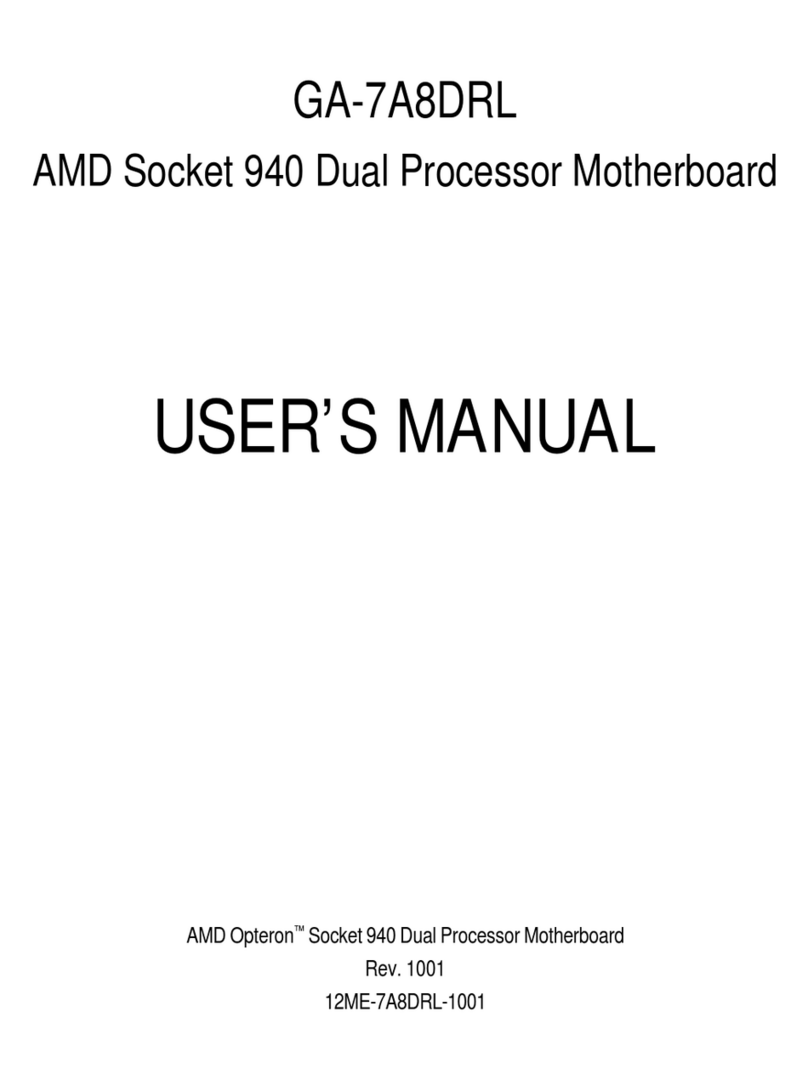
Gigabyte
Gigabyte GA-7A8DRL user manual
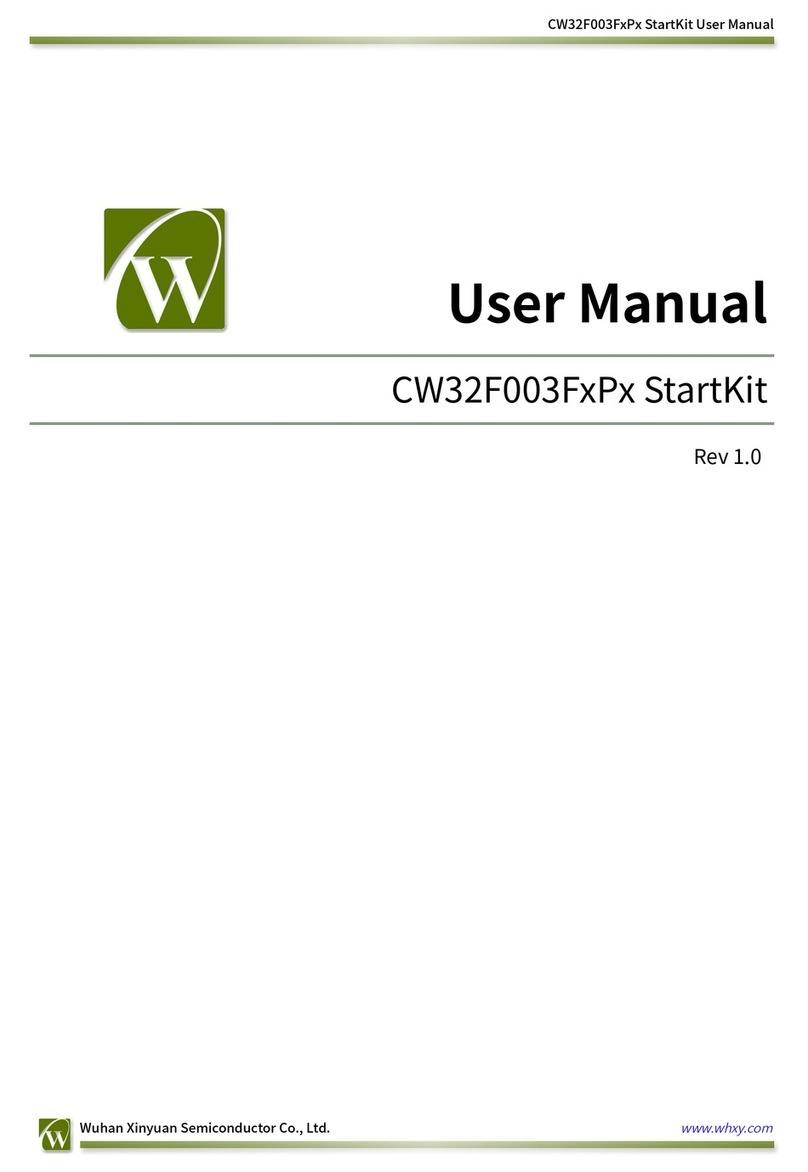
Wuhan Guide
Wuhan Guide CW32F003FxPx StartKit user manual
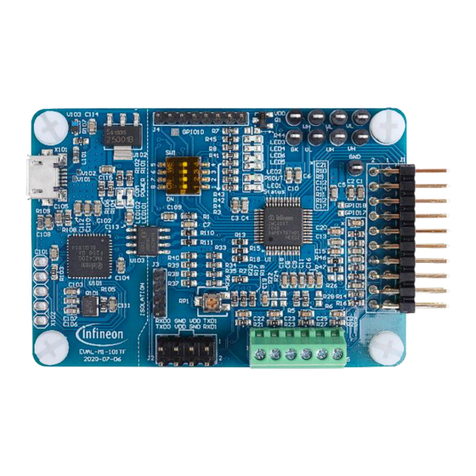
Infineon
Infineon EVAL-M1-101TF user guide

Altera
Altera Stratix III 3SL150 Reference manual
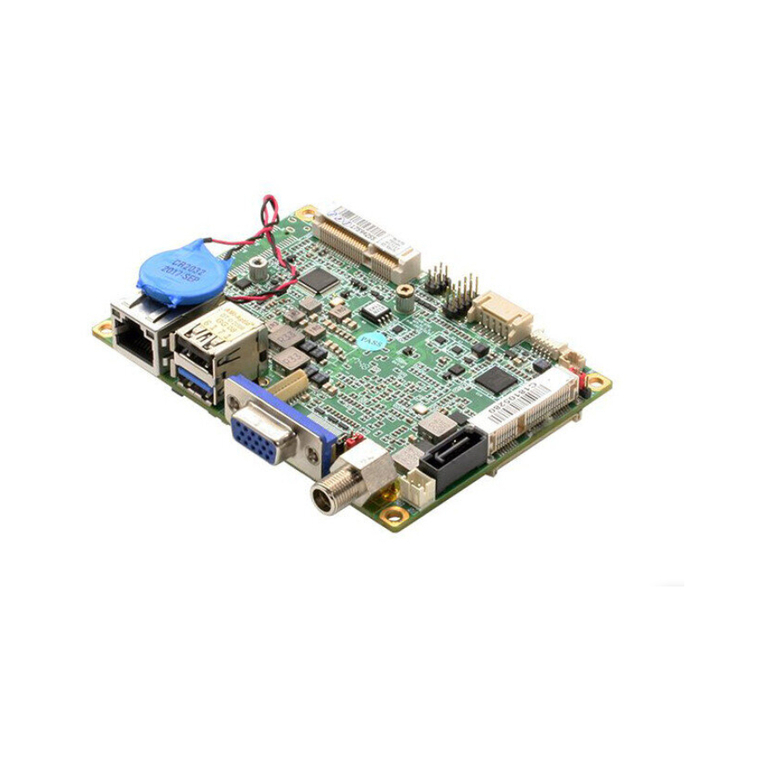
Aaeon
Aaeon PICO-BT01 manual