PREVOST PNEUMATIC SYSTEM IMPROVEMENT Reference manual

96-14B / Page 1/18
Service Bulletin 96-14B
REVISION : B
VALVE ASSY. #131422 AND #131423 REPLACED BY #131460 IN KIT #141906, #141907
Date: SEPTEMBER 1996
Section: 12
Subject: PNEUMATIC SYSTEM IMPROVEMENT
Application:
Model VIN
XL-40 Converted Coach Shell (M)
Model Year: 1986 - 1990
2P9M33404G1001192 up to 2P9M3340XL1001580 incl.
XL-40 Converted Coach Shell (M)
Model Year: 1990 - 1993
2P9M33405L1001583 up to 2P9M33402P1001739 incl.
XL-40 and XL-45E
Converted Coach Shell (M, ME)
Model Year: 1993 - 1994
2P9E33497P1001741 up to 2P9M3340XR1001832 incl.
XL-40 and XL-45E
Converted Coach Shell (M, ME)
Model Year: 1994 - 1995
2P9M33404R1001857 up to 2P9E33493S1001521 incl.
and
2P9M3340XR1001832.
XL-45 Converted Coach Shell (M5)
Model Year: 1993 - 1996
2P9M33498P1001646 up to 2P9M33490S1001519 incl.
and
2P9M33494S1001524 up to 2PCM3349XT1025774 incl.
DESCRIPTION
On the above-mentioned vehicles, it is possible to improve the airtightness of the vehicle's pneumatic
system. This service bulletin upgrades the pneumatic system in accordance with our current line
specifications.
Note: The existing pneumatic system is safe and this bulletin should be considered as product
improvement instructions.
Modifications are :
♦The logic behind the tag axle unloading and retracting (STEP 1);
♦The increase of the tag axle air springs filling delay before the hydraulic tag axle stabilizer locking (this
modification is applicable only on Mirage M5 vehicles) (STEP 2).
There are kits (materials) at the beginning of step 1. Depending on the vehicle model and VIN, select and
order the appropriate one. There is also a resistor to order (step 2) (only for M5 vehicles).
Proceed as follows to perform modifications.
Before welding is done on the vehicle (Fig. 6), read carefully the general welding procedure.

96-14B / Page 2/18
GENERAL WELDING PROCEDURE
Warning: Park vehicle safely, apply parking brake, stop engine and set battery master switch(es) to the
OFF position prior to working on the vehicle.
1. Welding must be done only by a qualified and experienced person.
2. Always wear the appropriate safety equipment.
3. Weld in clean and well-ventilated area, and always have an appropriate fire extinguisher within your
reach.
4. The following precautions should be taken to protect the electronic control components :
•Cut off battery power (battery master switch) from battery compartment.
•Disconnect wiring harness connectors from ECM (Electronic Control Module). The ECM is mounted
on the starter side of the engine.
•For vehicles equipped with an automatic transmission, disconnect wiring harness connectors from
ECU (Electronic Control Unit). The ECU is located in rear electrical compartment.
•For vehicles equipped with ABS (Anti-Brake System), disconnect wiring harness connectors from
ABS Electronic Control Unit. The ABS Electronic Control Unit is located in the front service
compartment.
•Do not connect welding cables to electronic control components.
5. Thoroughly clean area where welding has to be made.
6. Perform welding.
7. Because of material thickness, it is recommended to use a semi-automatic electric arc welding:
•GMAW (Gaz Metal-Arc Welding) process;
•welding wire conforming to AWS (American Welding Standards) A5.9 specifications;
•308L type welding wire with 0.035" diameter (0,9 mm);
•voltage: 18 volts to 22 volts;
•current: 225 amperes to 250 amperes;
•gas used: T90-H (90% helium, 7,5% argon, 2,5% CO2).
If necessary, with lots of precaution to avoid perforation material, it is possible, but not recommended, to
use a conventional electric arc welding machine, in accordance with the following specifications:
•SMAW (Shield Metal-Arc Welding) process;
•welding rod conforming to AWS (American Welding Standards) A5.9 specifications;
•308L-16 type welding rod 3/16" in diameter (2,4 mm);
•current: 80 amperes to 85 amperes.
9. Allow welding to cool, then remove slag.
10. Reconnect ECM, ECU and ABS electronic control unit mentioned in step 5.

96-14B / Page 3/18
PROCEDURE
Warning: Park vehicle safely, apply parking brake, stop engine and set battery master switch(es) to the
OFF position prior to working on the vehicle.
1. Safely support vehicle at the axle jacking points.
2. Jack vehicle until the tire clears the ground, and place safety supports underneath body.
Caution: Only the recommended jacking points must be used as outlined in Maintenance Manual Section
18,
″
Body
″
or in Operator’s Manual.
3. Exhaust compressed air from accessories and wet air tank by opening drain cock under reservoir. Close
air tank drain cocks.
Note: The wet tank is located under the vehicle before the drive axle. The accessories air tank is located
under the vehicle near the front axle. For more information, refer to maintenance manual, Section 12:
″
Brake
″
, Section 16:
″
Suspension
″
, and to vehicle's pneumatic diagram.
STEP 1 : TAG AXLE UNLOADING AND RETRACTING LOGIC
INVERSION
After this modification, air spring valve pilots must be under pressure to unload the tag axle. When the air
spring valve pilots are under pressure the air exhausts from springs. The lifting air cylinder is activated and
the tag axle raised. At this time, tag axle brakes are not applied, because the tag axle interlocking brake
valve controls (R-12) has no pressure on the controls. In fact, when pressure is applied to air spring valve
pilots to lifting the air cylinder, air flow is reversed by an air valve (inversion valve) and no pressure activates
the tag axle brake valve pilots and consequently, brakes do not apply.

96-14B / Page 4/18
MATERIAL
Kit # 141905 includes the following parts.
Model VIN
M
see
D140162
2P9M33405L1001583 up to 2P9M33402P1001739 incl.
M, ME
see
D140179
2P9E33497P1001741 up to 2P9M3340XR1001832 incl.
Part locations Part No. Description Qty
Fig. 1
item # 32, 33 641375 Elbow, 90°, 3/8 O.D. Tube x 3/8 NPT male 2
Fig. 1 503463 Tube, 3/8″O.D. (green), 4 feet 1
Fig. 1
item #29 501473 Tee, ½ NPT 1
Fig. 1
item #29 641384 Straight fitting, 5/8 O.D. Tube x ½ NPT male 1
Fig. 1 & 7 141861 Inversion valve assy 1
Fig. 1,6 & 7 171993 Inversion valve bracket 1
Fig. 1 391811 Bilingual sticker, control valve lift tag 1
Fig. 1 500613 Adel clip retaining screw 12
Fig. 1 560503 Adel clip ¼ D. 6
Fig. 1 560479 Adel clip 3/8 D. 6
Fig. 1 500625 Valve retaining screw, 1/4-20 X 2″Lg. T.C. hex. head 6
Fig. 1 641034 Sleeve, tube size 5/8″1
Fig. 1 641061 Nut 5/8″1
Fig. 1 641036 Sleeve, tube size 3/8″5
Fig. 1 641059 Nut 3/8″5
Fig. 9 064385 Wiring harness 1
Fig. 9 561626 Tab 1
Fig. 9 561707 Relay 1
Fig. 9 500557 Screw 1
Fig. 9 504637 Cable Tie 6
Note: Material can be obtained through regular channels.

96-14B / Page 5/18
Kit #141906 includes the following parts.
Model VIN
M, ME
see
D140196
2P9M33404R1001857 up to 2P9E33493S1001521 incl.
and
2P9M3340XR1001832.
Part locations Part No. Description Qty
Fig. 2
item # 31 131384 Valve assy N.C. 1
Fig. 2
item 79 131460 Valve assy N.O. 1
Fig. 2
item #32 131460 Valve assy N.O. 1
Fig. 2 141862 Inversion valve assy 1
Fig. 2 171993 Inversion valve bracket 1
Fig. 2
Item #28, 29 641371 Elbow, 90°, 1/4" O.D. Tube x ¼ NPT male 2
Fig. 2
item #33 501473 Tee 1/2" NPT 1
Fig. 2
item #33 641384 Straight fitting 5/8 O.D. Tube x ½ NPT male 1
Fig. 2 503402 Tube 1/4″O.D. (black), 6 feet 2
Fig. 2 503463 Tube 3/8″O.D. (green), 4 feet 1
500613 Adel clip retaining screw 12
560503 Adel clip ¼ D. 6
560479 Adel clip 3/8 D. 6
500625 Valve retaining screw, 1/4-20 X 2″Lg. T.C. hex. head 6
641034 Sleeve, tube size 5/8″1
641061 Nut 5/8″1
641036 Sleeve, tube size 3/8″5
641059 Nut 3/8″5
Fig. 2 391811 Bilingual sticker, control valve lift tag 1
Fig. 9 064385 Wiring harness 1
Fig. 9 561626 Tab 1
Fig. 9 561707 Relay 1
Fig. 9 500557 Screw 1

96-14B / Page 6/18
Fig. 9 504637 Cable Tie 6
Note: Material can be obtained through regular channels.
Kit #141907 includes the following parts.
Model VIN
M5
see
D140204
2P9M33494S1001524 up to 2PCM3349XT1025774 incl.
Part locations Part No. Description Qty
Fig. 3
item #61 131384 Valve assy N.C. 1
Fig. 3
item #60 131460 Valve assy N.O. 1
Fig. 3
item #59 641274
641375
641002
641388
641347
503402
Valve Elbow 90°, 3/8 O.D. Tube x 3/8 NPT male
Elbow Tee, ¼ O.D. Tube x 1/8 NPT male
Elbow Tee, 3/8 O.D. Tube x 3/8 NPT male
Fitting Straight, ¼ O.D. Tube x 3/8 NPT male
Plas. tube
1
1
1
1
1
6"
Fig. 3
item #92 641274
641374
641369
641347
Valve assy N.C.
Elbow 90°, ¼ O.D. Tube x 3/8 NPT male
Elbow 90°, ¼ O.D. Tube x 1/8 NPT male
FP ST #4 x 3/8 PM
1
1
1
2
Fig. 3
item #49 501473 Tee ½ NPT 1
Fig. 3
item #49 641384 Straight fitting, 5/8 OD Tube x ½ NPT male 1
Fig. 3
item #49 501966 Plug, socket Hex. Head ½ NPT 1
Fig. 3
item #50, 51 641371 Elbow 90°, ¼ OD Tube x ¼ NPT male 2
Fig. 3
item #71 641332 Fitting, Straight ¼ O.D. Tube x ¼ NPT male 1
Fig. 3 141861 Inversion valve assy 1
Fig. 3,6 & 7 171993 Inversion valve bracket 1
Fig. 3 503402 Tube 1/4″O.D. (black), 15 feet 1
Fig. 3 503463 Tube 3/8″O.D. (green), 4 feet 1
500613 Adel clip retaining screw 12
560503 Adel clip ¼ D. 6
560479 Adel clip 3/8 D. 6
500625 Valve retaining screw, 1/4-20 X 2″Lg. T.C. hex. head 8
641034 Sleeve, tube size 5/8″1
641061 Nut 5/8″1
641036 Sleeve, tube size 3/8″6
641059 Nut 5/8″6
Fig. 3 391811 Bilingual sticker, control valve lift tag 1

96-14B / Page 7/18
Fig. 9 064385 Wiring harness 1
Fig. 9 561626 Tab 1
Fig. 9 561707 Relay 1
Fig. 9 500557 Screw 1
Fig. 9 504637 Cable Tie 6
Note: Material can be obtained through regular channels.
Kit #141908 includes the following parts.
Model VIN
M
see
D140131
2P9M33404G1001192 up to 2P9M3340XL1001580 incl.
Part locations Part No. Description Qty
Fig. 4 391811 Bilingual sticker, control valve lift tag 1
500613 Adel clip retaining screw 10
560503 Adel clip ¼ D. 6
560479 Adel clip 3/8 D. 4
500625 Valve retaining screw, 1/4-20 X 2″Lg. T.C. hex. head 8
641036 Sleeve, tube size 3/8″6
641059 Nut 3/8″6
Fig. 9 064385 Wiring harness 1
Fig. 9 561626 Tab 1
Fig. 9 561707 Relay 1
Fig. 9 500557 Screw 1
Fig. 9 504637 Cable Tie 6
Note: Material can be obtained through regular channels.

96-14B / Page 8/18
Kit #141909 includes the following parts.
Model VIN
M5
see
D140176
2P9M33498P1001646 up to 2P9M33490S1001519 incl.
Part locations Part No. Description Qty
Fig. 5
item #49 501473 Tee 1
Fig. 5
item #49 641384 Straight fitting, 5/8 O.D. Tube x ½ NPT male 2
Fig. 5
items #50 & 51
641371 Elbow 90º, ¼ O.D. Tube x ¼ NPT male 2
Bloc Manifold 641332 Fitting 1
Fig. 5 141862 Inversion valve 1
Fig. 6 & 7 171993 Inversion valve bracket 1
503402 Tube 1/4″O.D. (black), X 15 feet 2
391811 Bilingual sticker, control valve lift tag 1
500613 Adel clip retaining screw 12
560503 Adel clip ¼ D. 6
560479 Adel clip 3/8 D. 6
500625 Valve retaining screw, 1/4-20 X 2″Lg. T.C. hex.
head 8
Fig. 5
item |#49 641034 Sleeve, tube size 5/8″1
Fig. 5
item #49 641061 Nut 5/8″1
641036 Sleeve, tube size 3/8″5
641059 Nut 3/8″5
Fig. 9 064385 Wiring harness 1
Fig. 9 561626 Tab 1

96-14B / Page 9/18
Fig. 9 561707 Relay 1
Fig. 9 500557 Screw 1
Fig. 9 504637 Cable Tie 6
Note: Material can be obtained through regular channels.
PROCEDURE
Follow instructions on the vehicle's pneumatic diagram (Figure 1 to 5). Then, perform the following lift tag
axle indicator lights modification. Where applicable, perform the following inversion valve installation.
Note : Where ports have to be inverted, replace the sleeves.
Note : Where fittings have to be replaced, use pipe sealant on threads.
FIGURE 1: PNEUMATIC DIAGRAM (REFERENCE DIAGRAM: D140162 OR D140179) 12094

96-14B / Page 10/18
FIGURE 2: PNEUMATIC DIAGRAM (REFERENCE DIAGRAM: D140196) 12095

96-14B / Page 11/18
FIGURE 3: PNEUMATIC SYSTEM (REFERENCE DIAGRAM : D140204) 12096

96-14B / Page 12/18
FIGURE 4: PNEUMATIC SYSTEM (REFERENCE DIAGRAM: D140131) 12097

96-14B / Page 13/18
FIGURE 5: PNEUMATIC SYSTEM (REFERENCE DIAGRAM: D140176) 12098
INVERSION VALVE INSTALLATION
1. Before welding, refer to the general welding procedure in this service bulletin.
2. Locate the inversion valve bracket in rear wheelhousings (Fig. 6). At this position, a tee may be installed
(on all vehicles except M5). Remove the tee.
3. Clean and grind post surface to reasonable flatness before bracket welding.
4. Protect all components (tubes, valves, etc.) from sparks with fireproof material.
5. Weld bracket as per figure 6.
6. Install the inversion valve on the bracket as per (M5 vehicles, fig. 7 or M and Me vehicles, Fig. 8).

96-14B / Page 14/18
FIGURE 6: INVERSION VALVE BRACKET LOCATION 12099
FIGURE 7: INVERSION VALVE INSTALLATION (USED ON FIG. 1,3 & 5) 12100

96-14B / Page 15/18
FIGURE 8: INVERSION VALVE INSTALLATION (USED ON FIG. 2) 12101
LIFT TAG AXLE INDICATOR LIGHTS MODIFICATION
Because the logic behind the tag axle unloading and retracting has been changed, the lift tag axle indicator
lights on the dashboard have to be reversed. Perform the following electrical procedure :
Warning: Park vehicle safely, apply parking brake, stop engine and set battery master switch(es) to the
OFF position prior to working on the vehicle.
1. Open front electrical compartment (Fig. 9).
2. Disconnect wire #115 (blue) from post #35. Connect wire #115 to relay post #85.
3. Add wire #115C, connect one extremity to post #35 and the other extremity to relay post #87A.
4. Add wire #85D, connect one extremity to post #20 and the other extremity to relay post #86.
5. Add wire #0, connect one extremity to post #90 and the other extremity to relay post #30.
6. Install the relay base. Drill a hole to receive the screw (Prévost #500557) that will secure the relay base.
7. Connect relay to its base.
8. Secure wiring harness using cable ties (Prévost #504012).
9. Close the front electrical door.

96-14B / Page 16/18
FIGURE 9: FRONT ELECTRICAL COMPARTMENT 06187

96-14B / Page 17/18
STEP 2 : HYDRAULIC TAG AXLE STABILIZER LOCKING SYSTEM
MODIFICATION (M5 ONLY) (Fig. 10)
Proceed to the following steps to increase the air springs filling delay to 15 seconds before the hydraulic tag
axle stabilizer locking system application. Previous delay was set to 5 seconds.
Note : Perform the following procedure only on M5 vehicles.
MATERIAL
Prévost # Description Qty
562516 Resistor (240 kΩ)1
Note:Material can be obtained through regular channels.
1. Open engine compartment doors, locate electric junction box, then open panel.
2. Replace resistor (Prévost # 562342) by (Prévost # 562216) on R66 relay (Fig. 10).
3. Close electric junction box, then engine compartment rear doors.

96-14B / Page 18/18
FIGURE 10: REAR ELECTRICAL COMPARTMENT 06188
This manual suits for next models
3
Other PREVOST Automobile Part manuals
Popular Automobile Part manuals by other brands
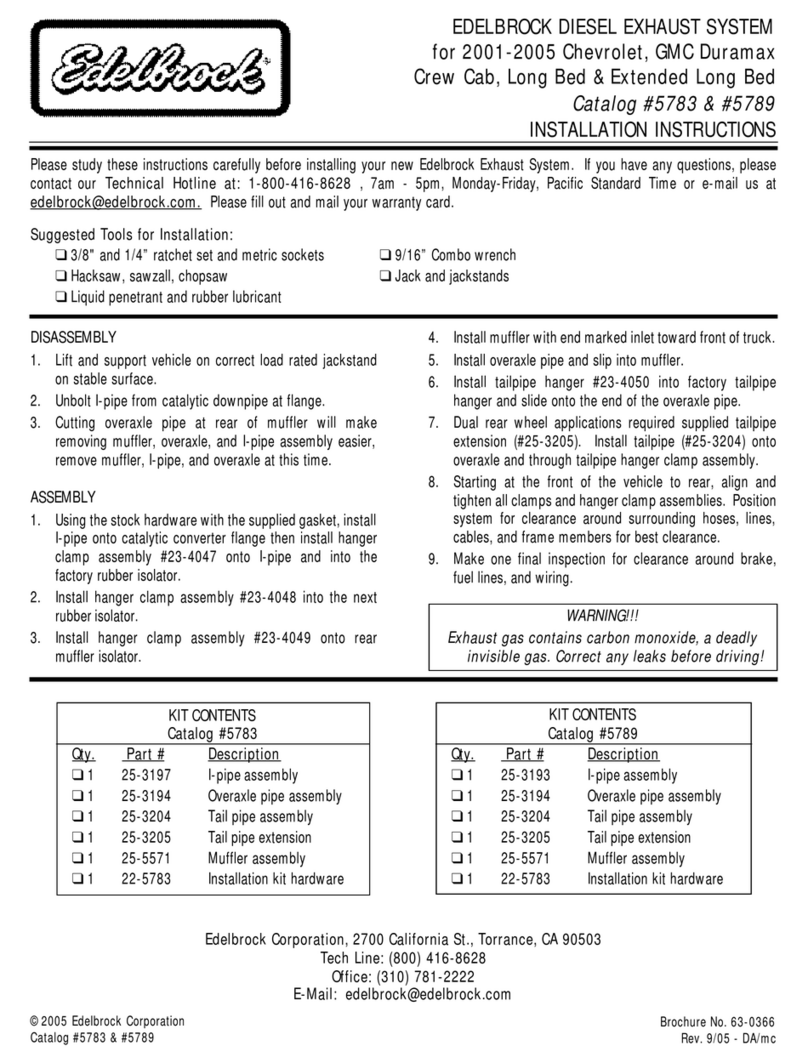
Edelbrock
Edelbrock Chevrolet 5783 installation instructions

BBK
BBK 4009 installation instructions

Russell Corporation
Russell Corporation Honda 599 CB600F installation instructions
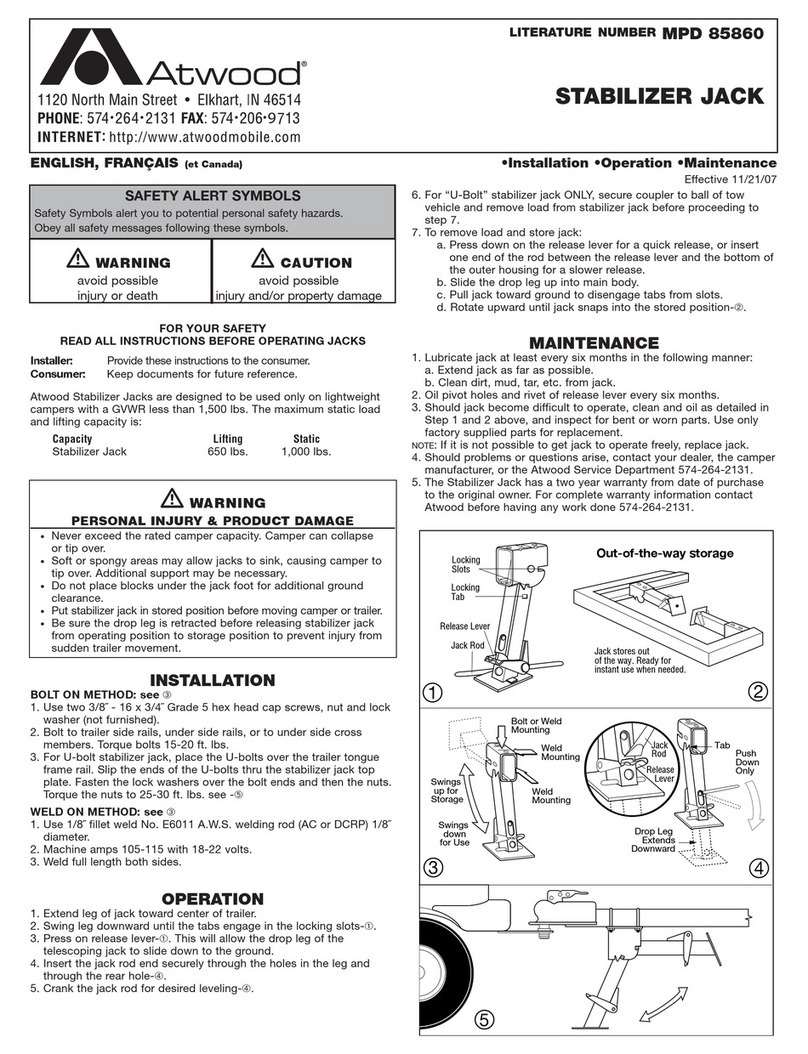
Atwood
Atwood MPD 85860 Installation and operation manual
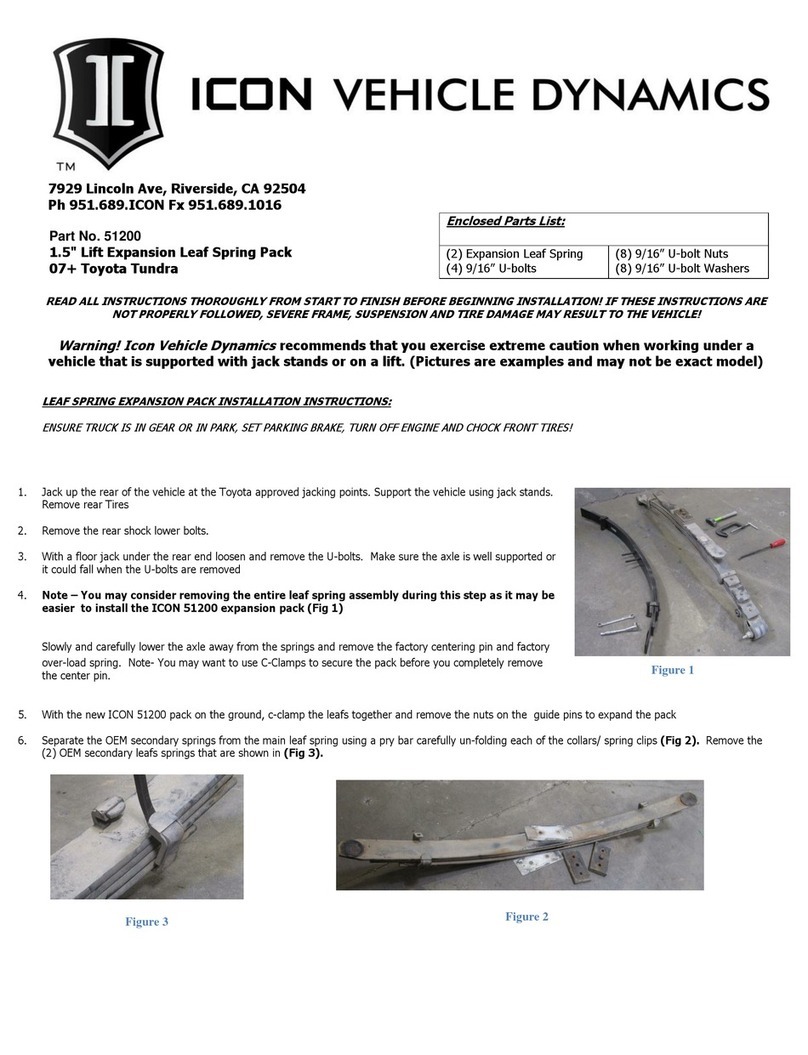
ICON
ICON 51200 instructions
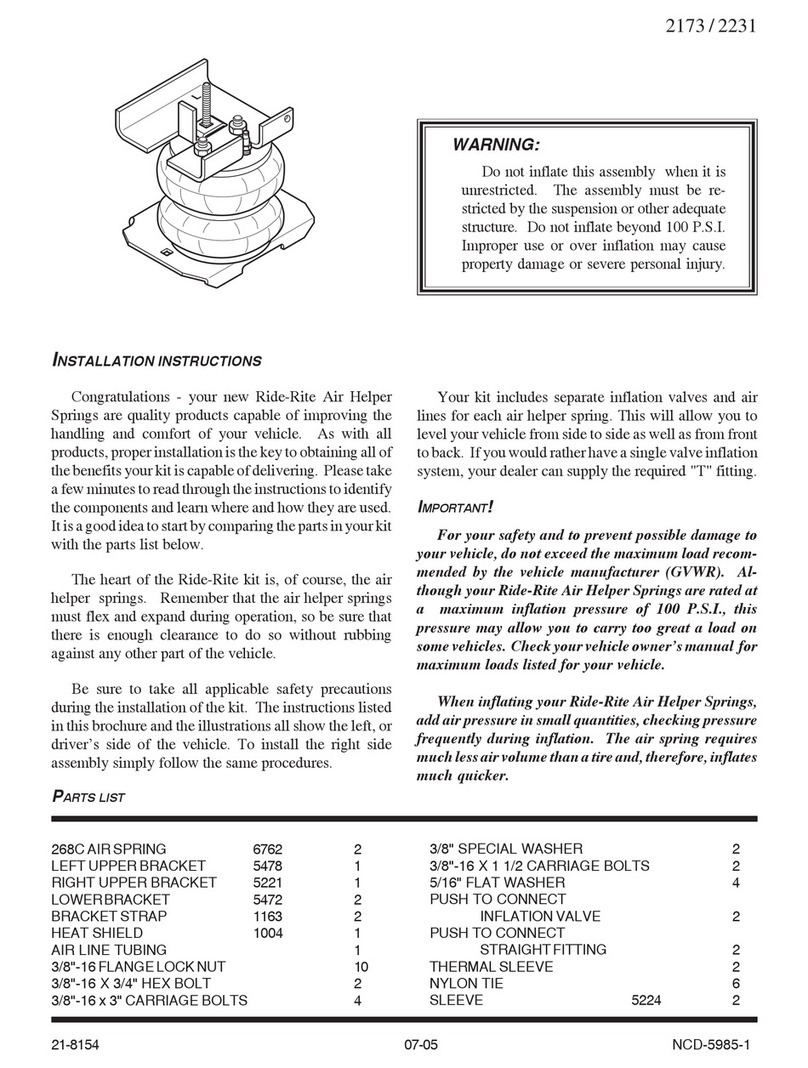
Firestone
Firestone Ride-Rite Air Helper Springs 2173 installation instructions